The 89 Most Common Symbols On Your Car’s Dashboard
- Updated: March 21, 2024
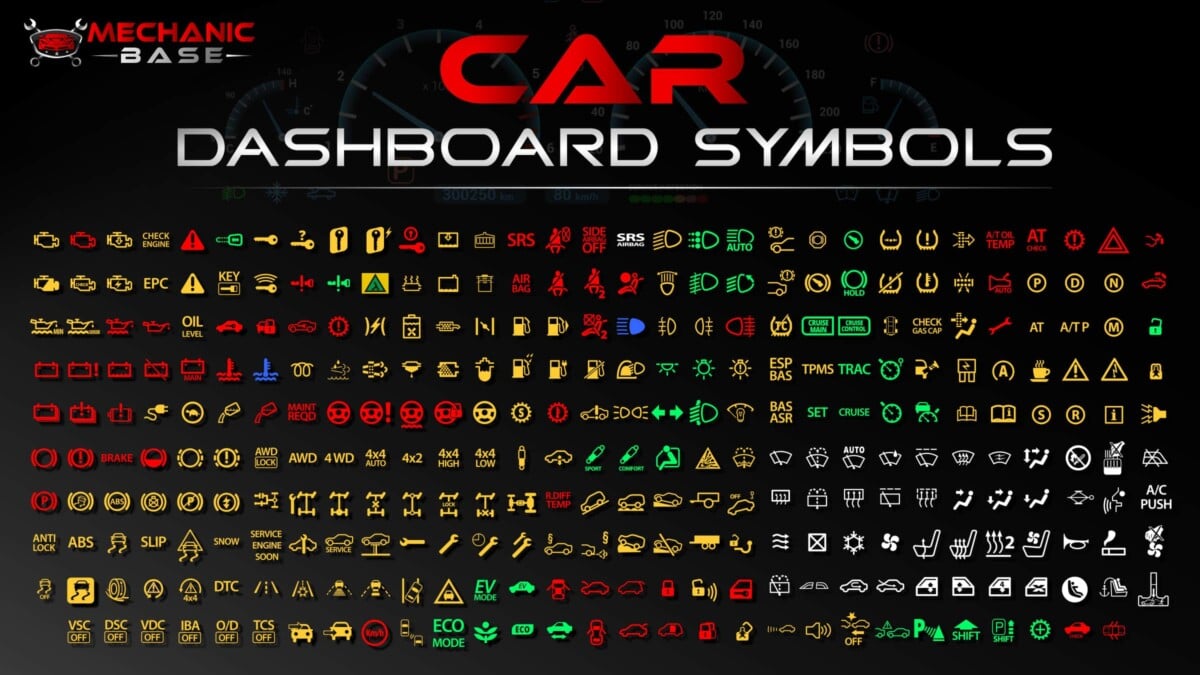
We’re all familiar with that moment of uncertainty when a warning light flashes on our car’s dashboard. It leaves us scrambling for the manual, attempting to decipher what the illuminated symbol signifies.
In this article, we will guide you through the top 89 most common car dashboard symbols and their meanings, empowering you with knowledge for the next time a warning light appears. By recognizing what these lights indicate, you can sidestep expensive repairs in the future.
Some dashboard symbols and warning lights are more common than others. Some are specific to certain car brands, while others will be seen on most car models on the market. We will begin by showing you the most common dashboard symbols that can be found in most car brands.
Here is a list of the dashboard symbols, and you can click on each name to get more information about the specific warning light.
Engine & Emission
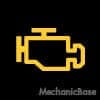

1. Check Engine Light
A Check Engine light indicates an issue with the engine or the emissions. It can be shown either as an engine symbol or as plain text reading “Check Engine”. Read More
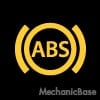
2. Anti-lock Braking System
An ABS light indicates there is an issue with your anti-lock brakes or Anti-lock braking system (ABS). Read more
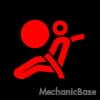
3. Airbag Indicator
An airbag light means that there is an issue with the airbag system. The airbags will not deploy in an accident with the light on. Read more
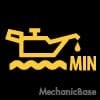
4. Oil Level Warning Light
A yellow oil level warning light indicates a low engine oil level. The oil level should be checked as soon as possible. Most likely due to an oil leak.
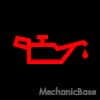
5. Oil Pressure Warning
A red oil pressure light indicates low oil pressure in the engine. Your engine should be switched off immediately to avoid damage when the oil pressure warning light shows. Read more
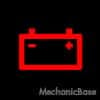
6. Battery Charge Warning
A battery charge warning symbol means that the generator is not charging the battery properly and that your engine is at risk of shutting down due to low battery capacity. Read more
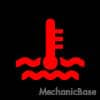
7. Coolant Temperature Warning Light
An engine temperature warning light means that the engine coolant temperature is high and that the engine should be turned off immediately to avoid further damage. Read more
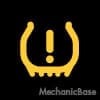
8. Tire Pressure Warning Light
A tire pressure warning light indicates low air pressure in one or more tires. It can also be caused by a faulty or uncalibrated tire pressure sensor. Read more
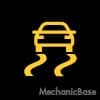
9. Traction Control/ESP Light
An ESP or Traction control light indicates an issue with the traction control system. Your traction control system will not work when the light is on, and this can be dangerous. Read More
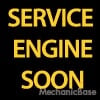
10. Service Engine Soon
A Service Engine Soon message indicates minor trouble with the engine or low fluid levels. Read more
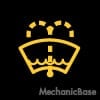
11. Low Washer Fluid Light
A washer fluid symbol means that the windshield washer fluid level is low or has incorrect measurements.
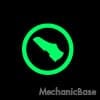
12. Automatic Shift Lock Symbol
An automatic shift lock symbol indicates the brake pedal is not pressed. The car will not start, and the shifter won’t move out of Park.
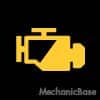
13. Reduced Engine Power
A Reduced engine power car light means that there is an issue with the engine and the power is reduced to protect the engine. Read more
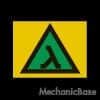
14. Lambda Warning Light
A lambda warning light indicates there is an issue with the air-fuel mixture or an issue with the oxygen sensors. This light is more common in older car models.
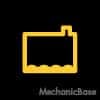
15. Low Coolant Indicator
A low coolant warning light indicates there is a low coolant level in the coolant reservoir or an issue with the coolant level sensor. Check for leaks around the radiator, radiator cap , coolant hoses, or water pump.
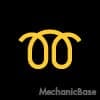
16. Glow Plug Indicator (Diesel)
A glow plug symbol indicates there is an issue with the glow plugs or the glow plug control system.
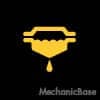
17. Fuel Filter Level Warning
A fuel filter level warning light means that the water-trap in the fuel level is full and needs to be emptied.
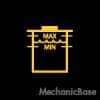
18. Power Steering Level Symbol
A power steering level warning light indicates the power steering fluid level is low, or there is an issue with the level sensor.
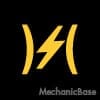
19. Electronic Throttle Control Light
An electronic throttle control (ETC) warning light indicates there is an issue with the engine’s electronic throttle body or the system.
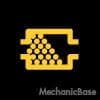
20. Particle Filter Warning (Diesel)
A diesel particulate filter warning light indicates there is an issue with the diesel particulate filter system (DPF), or that the particle filter is full and needs regeneration or replacement.
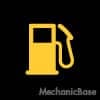
21. Low Fuel Level
A low fuel level symbol means that the fuel tank level is low or that there is an issue with the fuel level measuring system. There could also be an arrow, indicating which side your gas cap is on.
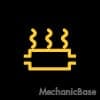
22. Catalytic Converter Warning
A catalytic converter warning light indicates there is an issue with the catalytic converter control system, or the catalytic converter is damaged.
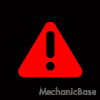
23. Master Warning Light
A master warning light normally shows up together with another warning light and means that there is an issue with your car. Let a mechanic take a look.
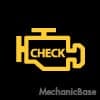
24. Blinking Engine Light
A blinking or flashing engine light indicates there is an issue with your engine ongoing right now. A flashing light is normally triggered by a misfiring engine. Read more.
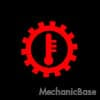
25. Transmission Temperature Warning
A transmission temperature warning light indicates the transmission temperature is too high, or there is an issue with the temperature measurement.

26. Traction Control Off
The traction control off symbol means that the traction control is manually switched off.
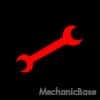
27. Powertrain Fault
A powertrain fault symbol indicates there is an issue with the powertrain or drivetrain system, like the 4WD or AWD system, for example.
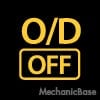
28. Overdrive Off indicator
An overdrive off symbol means that the automatic transmission overdrive system is switched off. Read more
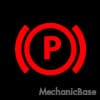
29. Parking Brake Light
A parking brake warning light indicates the parking brake is engaged, or there is an issue with the parking brake system
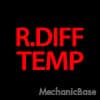
30. Differential Temperature Warning
A differential temperature warning light indicates the differential temperature is too high, or there is an issue with the measurement system.
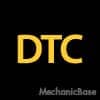
31. DTC Warning Light
A DTC warning light means that there is an issue with the BMW traction control system.
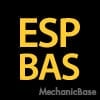
32. ESP BAS
An ESP BAS warning light indicates an issue with the electronic stability program or brake assist program.
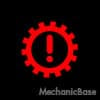
33. Automatic Gearbox Warning
An automatic gearbox warning indicates an issue with the automatic transmission or the system controlling it.
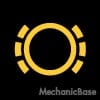
34. Brake Pad Warning
A Brake pad warning light means that the front or rear brake pads are worn and need to be replaced.
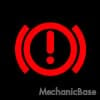
35. Brake Warning Light
A brake warning light indicates an issue with the brake system. This should be checked immediately because you may lose your brakes otherwise.
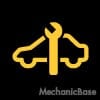
36. Service Vehicle Soon
A service vehicle soon symbol indicates there is an issue with the ABS, traction control, or electric suspension system.
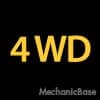
37. 4WD Engaged Indicator
A 4WD engaged symbol means that the four-wheel-drive system is engaged.
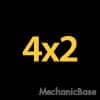
38. 2WD Engaged Indicator
A 2WD engaged symbol indicates the 4WD system is switched off and the car is sending power to two wheels only.
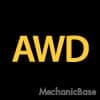
39. All Wheel Drive (AWD/4WD)
An All Wheel Drive symbol indicates that the AWD or 4WD system is engaged.
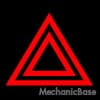
40. Hazard Lights On
A hazard lights symbol means that the hazard lights are turned on.
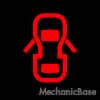
41. Door Ajar Symbol
A door ajar symbol indicates that one of the doors is open or there is an issue with the door switch system.
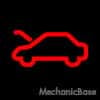
42. Hood Open
A hood open symbol indicates that the hood is not closed properly. It is very dangerous to drive with a hood that is not secured at higher speeds.
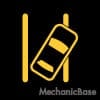
43. Lane Departure Warning
A lane departure warning light indicates the vehicle is moving out from the lane without signaling
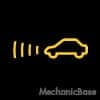
44. Forward Collision Warning
A forward-collision warning light means that there is a potential collision detected.
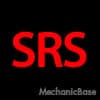
45. SRS Light
An SRS warning light indicates there is an issue with the airbag or supplemental restraint system. Read more
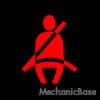
46. Seatbelt Indicator
A seatbelt symbol indicates one or more seat belts are not closed or there is an issue with the system. Check both the driver and passenger sides and the rear seats on some car models.
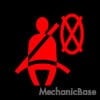
47. Side Airbag Warning Light
A side airbag warning light indicates the side airbags are turned off or there is an issue with the side airbags.
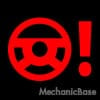
48. Power Steering Warning Light
A power steering warning light means that there is an issue with the power steering system
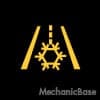
49. Icy Road Warning Light
An icy road warning light indicates the outside temperature is cold and that there is a risk of an icy road. Slow down!
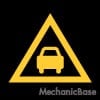
50. Distance Warning
A distance warning indicates the front radar detected that your vehicle is too close to the car in front or is being approached too quickly.
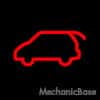
51. Bonnet Open
A bonnet open symbol means that the bonnet is not closed properly, or there is an issue with the bonnet lock switch.

52. Headlight Range Control
A headlight range control warning light indicates there is an issue with the headlight range control system
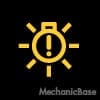
53. Exterior Light Fault
An exterior light warning light indicates an issue with one or more exterior lights, usually faulty light bulbs.
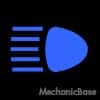
54. Highbeam Light Indicator
A high beam light symbol means that the high beam lights are turned on
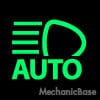
55. Auto High Beam Lights
An auto high beam lights symbol means that the auto high beam system is turned on
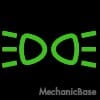
56. Position Light Indicator
A position light symbol will turn on when the headlights are switched off and the position lights are on
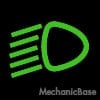
57. Low Beam Indicator Light
A low beam light symbol is turned on when the low beam headlights are turned on
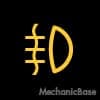
58. Front Fog Lights On
A front fog light symbol is illuminated when the front fog lights are turned on.
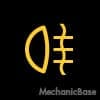
59. Rear Fog Light On
A rear fog light symbol is illuminated when the rear fog lights are turned on.
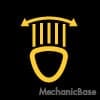
60. Turn Lights Warning Symbol
A turn light warning symbol indicates that there is an issue with the headlight’s turn-light system.
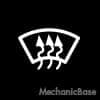
61. Windshield Defrost Indicator
A windshield defrost symbol indicates that the windshield defroster is turned on.
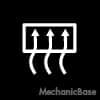
62. Rear Window Defrost
A rear window defrost symbol means that the rear window’s defroster is turned on.
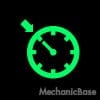
63. Cruise Control On Indicator
A green cruise control symbol indicates the cruise control is switched on and engaged.
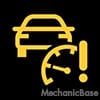
64. Cruise Control Warning
A cruise control warning symbol indicates there is an issue with the cruise control or throttle control system.
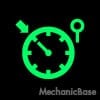
65. Cruise Control Speed Limiter
A cruise control speed limiter symbol means that the cruise control system will limit the max speed.
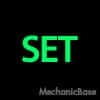
66. Cruise Control SET Indicator
A “SET” symbol indicates that the cruise control is set to a fixed speed and trying to hold the speed.
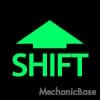
67. Shift Up Indicator
A shift up symbol indicates that it’s time to shift up to a higher gear.
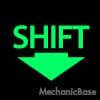
68. Shift Down Indicator
A shift down symbol means that it’s time to shift down to a lower gear.
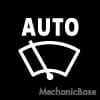
69. Auto Windshield Wiper
An auto windshield wiper symbol indicates that the auto wiper system is turned on.
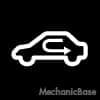
70. Recirculated Cabin Air
A recirculated cabin air symbol indicates that the car will recirculate the air inside the car instead of taking air from the outside of the car
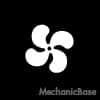
71. Heater Blower Fan On
A heater blower fan symbol means that the blower motor is turned on.
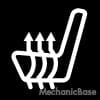
72. Heated Seats On
A heated seat symbol indicates that one or more seats’ heating system is turned on.
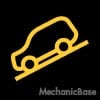
73. Hill Descent Control
A hill descent control symbol indicates that the hill descent system is turned on and will limit the car’s speed while going downhill.
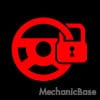
74. Steering Lock Warning Light
A steering lock warning light means that there is an issue with the steering lock or that the car key is not recognized

75. Brake Fluid Level Warning
A brake fluid level warning indicates that the brake fluid level is too low, or there is an issue with the measurement system.
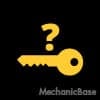

76. Key Not in Vehicle Indicator
A Key Not in Vehicle symbol indicates the car’s immobilizer system can’t reach or recognize your car key.
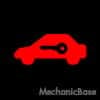
77. Immobilizer Indicator
An immobilizer symbol means that it can’t reach or recognize your car key, or there is an issue with the immobilizer system.
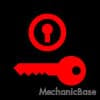
78. Ignition Switch Warning
An ignition switch warning symbol indicates that there is an issue with the ignition switch system.
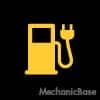
79. Low Electric Battery Charge
A low electric battery charge symbol indicates that it’s time to charge your electric vehicle’s battery.
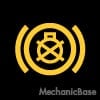
80. Brake Lights Warning
A brake light warning light indicates that the brake lights are not working.
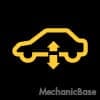
81. Air Suspension Warning
An air suspension warning symbol means that there is an issue with the air suspension system.
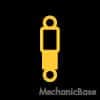
82. Suspension Warning Light
A suspension warning light shows up when there is a malfunction with the electric suspension system.
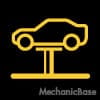
83. Car on Ramp Mode
A car on ramp mode warning symbol turns on when the car’s tires are raised up in the air or when the repair mode is activated.
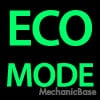
84. ECO Mode On Indicator
An ECO Mode on symbol indicates that the Economy system is turned on. Read more
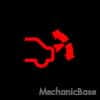
85. Rear Spoiler Warning
A rear spoiler warning light indicates that there is a malfunction in the rear spoiler electric system
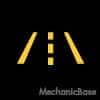
86. Lane Assist
A green lane assist symbol indicates that the lane assist system is turned on.
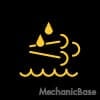
87. Exhaust Fluid (Diesel)
An exhaust fluid warning light means that the exhaust fluid (AdBlue) level is low in your diesel car.
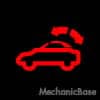
88. Convertible Roof Warning Light
A Convertible Roof Warning Light indicates that the convertible roof system is opening or closing.
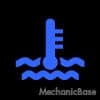
89. Blue Coolant Temp Light
A blue engine temperature symbol means that the engine is still cold and you should drive carefully.
- Toyota Dashboard Lights
- Lexus Warning Lights
Categories: General , Warning Lights
Related Posts
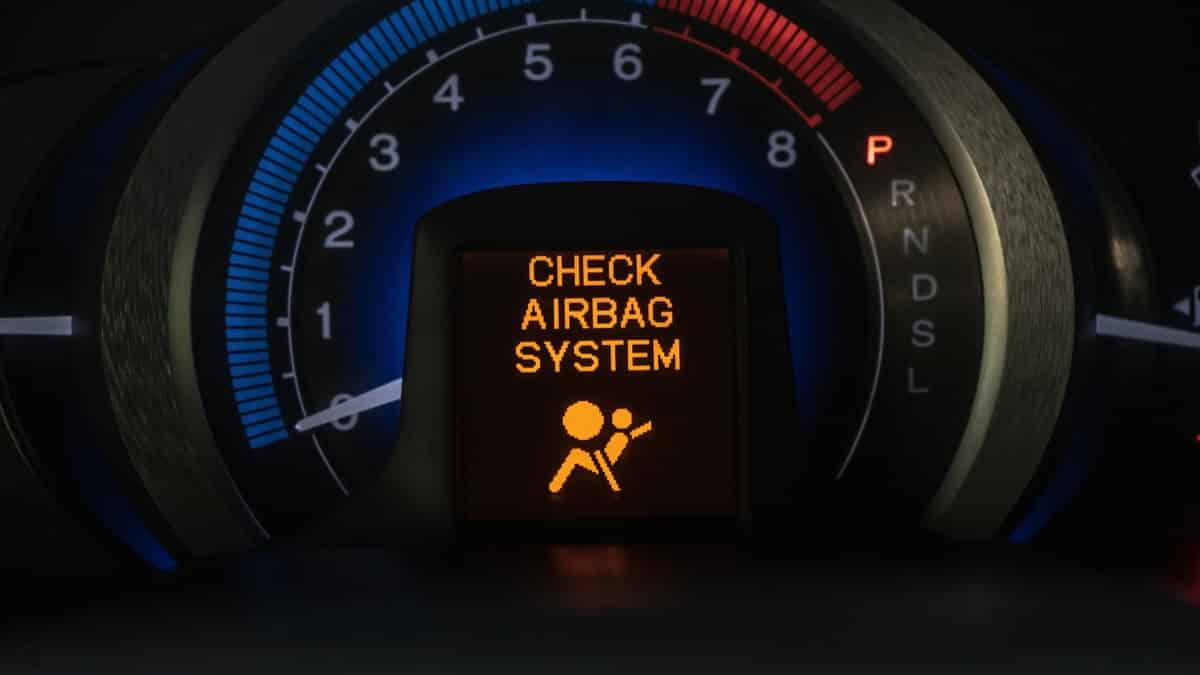
Latest Posts
- The Best & Worst Years Of Ford Explorer
- Best & Worst Years Of Toyota Corolla
- Best & Worst Years of Toyota RAV4
- When Should Your Child Switch To A Forward-Facing Car Seat?
- The Best & Worst Years Of Toyota Camry
- I Accidentally Put Premium Gas In My Car, What To Do?
Attention! Your ePaper is waiting for publication!
By publishing your document, the content will be optimally indexed by Google via AI and sorted into the right category for over 500 million ePaper readers on YUMPU.
This will ensure high visibility and many readers!
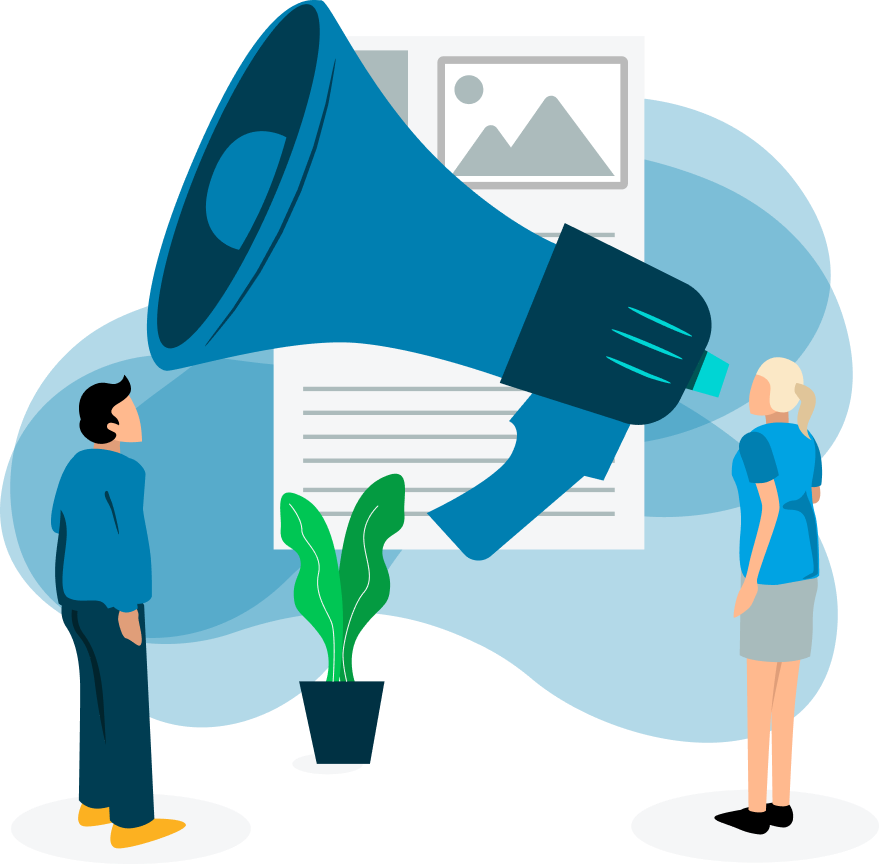
Your ePaper is now published and live on YUMPU!
You can find your publication here:
Share your interactive ePaper on all platforms and on your website with our embed function
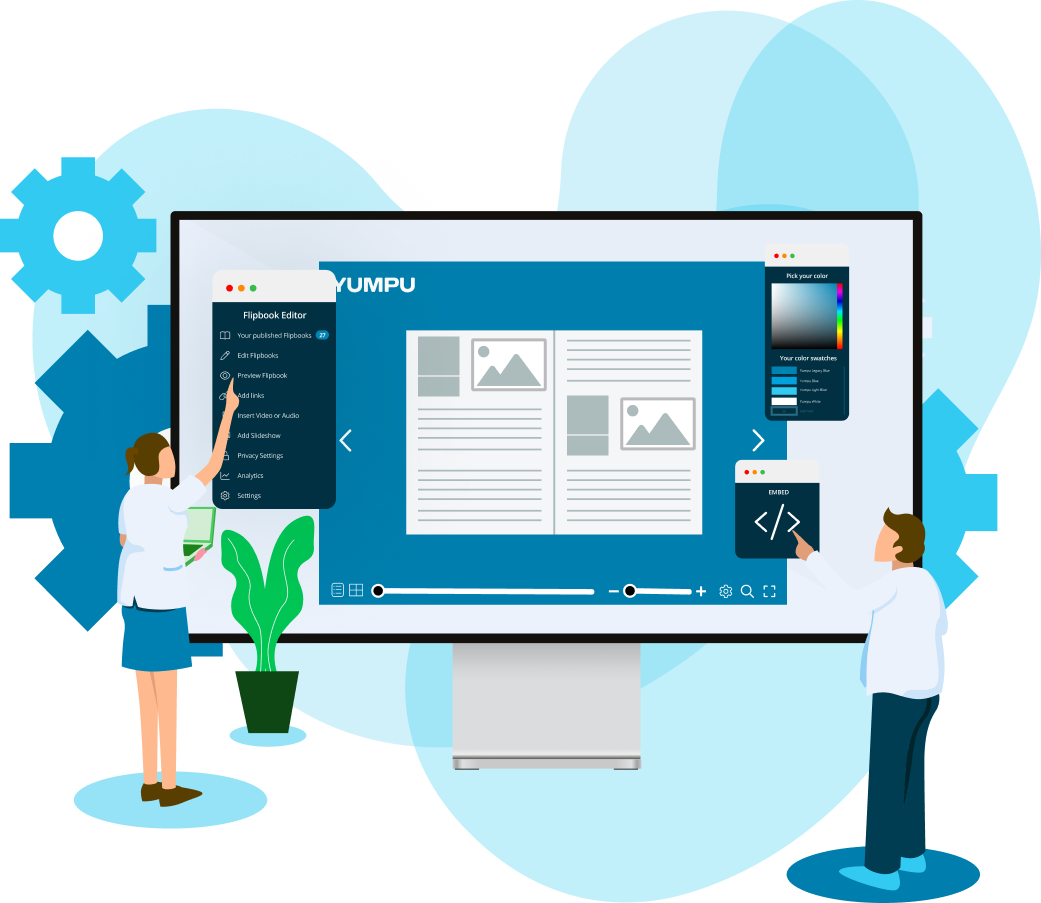
Foton Workshop Manual - View (CS2)
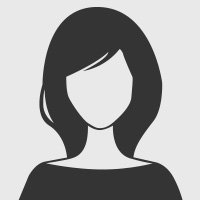
Create successful ePaper yourself
Turn your PDF publications into a flip-book with our unique Google optimized e-Paper software.
POWERED BY<br />
WCRKSHCP manuaL
VOLUME 1<br />
FOTON WORKSHOP MANUAL - VIEW (<strong>CS2</strong> / C2)<br />
Table of Contents<br />
Edition: January 2013 01 INTRODUCTION 07<br />
Printed: February 2013 02 PREPARATION 43<br />
Publication: FWSM-201301 03 SERVICE SPECIFICATIONS 83<br />
Location: China 04 DIAGNOSTICS 123<br />
© 2013 Beiqi <strong>Foton</strong> Motor Co., Ltd<br />
All right reserved. No part of this service manual may<br />
be reproduced or stored in a retrieval system, or<br />
transmitted in any form, or by any means, electronic,<br />
mechanical, photo-copying, recording or otherwise,<br />
without the prIor written permission of <strong>Foton</strong>.<br />
VOLUME 2 689<br />
04 DIAGNOSTICS (RHD) 691<br />
Pg.<br />
05 VEHICLE MAINTENANCE 1203<br />
11A ENGINE CONTROL SYSTEM 1263<br />
12A FUEL SYSTEM 1327<br />
13A EMISSION CONTROL 1355<br />
14A INTAKE AIR 1365<br />
15A ENGINE MECHANICAL 1383<br />
16A EXHAUST SYSTEM 1465<br />
17A COOLING SYSTEM 1477<br />
18A LUBRICATION SYSTEM 1503<br />
19A IGNITION SYSTEM 1525<br />
20A STARTING AND CHARGING 1533<br />
VOLUME 3 1567<br />
11B ENGINE CONTROL SYSTEM 1569<br />
12B FUEL SYSTEM 1617<br />
13B EMISSION CONTROL 1669<br />
14B INTAKE AIR 1681<br />
15B ENGINE MECHANICAL 1703<br />
16B EXHAUST SYSTEM 2019<br />
17B COOLING SYSTEM 2035<br />
18B LUBRICATION SYSTEM 2065<br />
19A IGNITION SYSTEM 2091<br />
20B STARTING AND CHARGING 2103<br />
21 SUPERCHARGER 2139<br />
VOLUME 4 2157<br />
11C ENGINE CONTROL SYSTEM 2159<br />
12C FUEL SYSTEM 2171<br />
13C EMISSION CONTROL 2193<br />
14C INTAKE AIR 2199<br />
15C ENGINE MECHANICAL PART 2207<br />
16C EXHAUST SYSTEM 2233<br />
17C COOLING SYSTEM 2241<br />
18C LUBRICATION SYSTEM 2261<br />
20C STARTING AND CHARGING 2271<br />
VOLUME 5 2299<br />
31-32 SUSPENSION SYSTEM 2301<br />
33 TYRE AND WHEEL 2339<br />
34 AXLE AND PROPELLER SHAFT 2351<br />
35-36 BRAKING SYSTEMS 2405<br />
41 TRANSMISSION 2465<br />
42 CLUTCH 2543<br />
51 STEERING COLUMN 2565<br />
52 POWER STEERING 2589<br />
61 HEATER AND AIR CONDITIONING 2625<br />
62 SUPPLEMENTAL RESTRAINT SYSTEM 2713<br />
63 SEAT BELT 2733<br />
64 LIGHTING 2757<br />
65 WIPER AND WASHER 2787<br />
66 AUDIO SYSTEM 2809<br />
71 WIRING 2825<br />
81 COMMUNICATION SYSTEM 3219<br />
82 WINDSHIELDS, MIRRORS & GLASS 3235<br />
83 INSTRUMENT PANEL 3259<br />
84 SEATS 3277<br />
85 DOOR LOCKS 3303<br />
86 SLIDING ROOF 3325<br />
87 DOORS AND ENGINE HOOD 3335<br />
88 EXTERIOR AND INTERIOR TRIM 3357<br />
91 VEHICLE CONTROL SYSTEM 3395
WORKSHOP MANUAL - VIEW <strong>CS2</strong> / C2<br />
V O L U M E 1<br />
01 INTRODUCTION 07<br />
02 PREPARATION 43<br />
03 SERVICE SPECIFICATIONS 83<br />
04 DIAGNOSTICS 123
INTRODUCTION<br />
HOW TO USE THIS MANUAL........................................................... 01-1<br />
GENERAL INFORMATION.......................................................... 01-1<br />
IDENTIFICATION INFORMATION..................................................... 01-6<br />
VEHICLE IDENTIFICATION NUMBER (VIN) .............................. 01-6<br />
SERIAL NUMBER (SN) ............................................................... 01-7<br />
REPAIR INSTRUCTION..................................................................... 01-8<br />
PRECAUTION.............................................................................. 01-8<br />
VEHICLE LIFT AND SUPPORT LOCATIONS........................... 01-16<br />
HOW TO TROUBLESHOOT............................................................ 01-18<br />
GENERAL INFORMATION........................................................ 01-18<br />
HOW TO PROCEED WITH TROUBLESHOOTING .................. 01-20<br />
ELECTRONIC CIRCUIT INSPECTION PROCEDURE ............. 01-29<br />
TERMS ............................................................................................. 01-33<br />
ABBREVIATIONS USED IN THIS MANUAL ............................. 01-33<br />
01<br />
HOW TO USE THIS MANUAL<br />
GENERAL INFORMATION<br />
INTRODUCTION - HOW TO USE THIS MANUAL<br />
01-1<br />
1. GENERAL DESCRIPTION.<br />
(a) Carrying out operations described in this manual in the correct sequence may help you improve the<br />
quality and efficiency during servicing.<br />
(b) Generally, service operations can be separated in the following 3 main processes:<br />
• Diagnosis<br />
• Removal / Installation, Replacement, Disassembly / Assembly, (On-vehicle) Inspection and Adjustment<br />
• Final Inspection<br />
(c) This manual includes the 1st process of “Diagnosis” (Refer to “Chapter 04 diagnostics”) and the 2nd<br />
process of “Removal / Installation, Replacement, Disassembly / Reassembly, (On-vehicle) Inspection<br />
and Adjustment”, but the 3rd process of “Final Inspection” is not included.<br />
(d) The following essential operations are not written in this manual. However, these operations must be<br />
performed in actual situations.<br />
• Clean a removed part when necessary<br />
• Visual check<br />
2. INDEX.<br />
(a) An alphabetical INDEX section is provided at the end of this chapter as a reference to help you to<br />
understand these abbreviation meaning.<br />
3. PREPARATION.<br />
(a) Special service tools (SST) and special service materials (SSM) may be required depending on the servicing<br />
situation. Be sure to use SST and SSM when they are required and follow the correct operation<br />
sequence. A list of SST and SSM is in the “Chapter 02 preparation”.<br />
4. SERVICING PROCEDURES.<br />
(a) According to chapter content, the components’ illustration is added into chapters.<br />
01-2<br />
(b)<br />
The components’ illustration shows the all parts relationship in the same assy. A table following the<br />
illustration lists the name of each part.<br />
Example:<br />
01-3<br />
(c) If installation is performed in the reverse order of removal, only important points will be described.<br />
(d) In this manual, only items with important points are described in the procedure and the illustration<br />
shows what and where we can do. In the explanations, details of the operational method, standard<br />
value and notices are listed.<br />
(e) Some illustrations in this manual for similar vehicle models may be the same. In this case, some details<br />
in illustration may be different from the actual vehicle.<br />
(f) The procedures are presented in a step-by-step format:<br />
• The illustration shows what to do and where to do it.<br />
• The task title tells us what to do.<br />
• The explanation text tells us how to perform the task and includes other information such as<br />
specifications, service notice and warnings.<br />
01-4<br />
5. SERVICE SPECIFICATIONS.<br />
(a) Specifications are presented in bold type throughout the manual. You never have to leave the servicing<br />
to look for the specifications. The specifications can also be found in the “Chapter 03 service<br />
specifications” for quick reference.<br />
6. TERM DEFINITIONS.<br />
WARNING<br />
CAUTION<br />
NOTE<br />
Indicates the possibility of injury to you or other persons.<br />
Indicates the possibility of damage to the components being<br />
repaired and the equipments being operated.<br />
Provides additional information to help you perform the servicing<br />
efficiently.<br />
7. INTERNATIONAL SYSTEM OF UNITS.<br />
(a) The units used in this manual comply with the International System of Units (SI UNIT) standard.<br />
Torque: 30 N•m<br />
01-5<br />
8. APPLICABLE VEHICLES.<br />
Series<br />
Steering<br />
Wheel<br />
Engine Transmission Model Examples<br />
BJ6549B1PDA-AA 6549B1PDA-AAZA09<br />
6549BDPDA-AAZA01<br />
F2.8 038J2 BJ6549BDPDA-AA<br />
6549BDPDA-AAZ001<br />
BJ6549B1PDA-3<br />
6549B1PDA-03ZA01<br />
widebody<br />
longshaft<br />
LHD<br />
4JB1T ZM001AJD<br />
BJ6549B1PDA-1 6549B1PDA-01ZA05<br />
BJ6549B1PDA-2 6549B1PDA-02ZA02<br />
6549B1PXA-EEZA03<br />
BJ6549B1PXA-EE<br />
4G69<br />
ZM001AD<br />
549B1PXA-EEZA08<br />
BJ6549BDPXA-EE 6549BDPXA-EEZA01<br />
ZM011D BJ6549B1PXA-2 6549B1PXA-02ZA02<br />
F2.8 038J2<br />
BJ6549B1PDA-RA 6549B1PDA-RAZA01<br />
BJ6549B1PDA-R2 6549B1PXA-R2ZA03<br />
RHD<br />
ZM001AJD BJ6549B1PXA-RE 6549B1PXA-REZA02<br />
ZM011D BJ6549B1PXA-R2 6549B1PXA-R2ZA01<br />
4JB1T ZM001AJD BJ6549B1PDA-R1 6549B1PDA-R1ZA01<br />
01-6<br />
INTRODUCTION - IDENTIFICATION INFORMATION<br />
IDENTIFICATION INFORMATION<br />
VEHICLE IDENTIFICATION NUMBER (VIN)<br />
1. VEHICLE IDENTIFICATION NUMBER (VIN).<br />
(a) The Vehicle Identification Number (VIN) is stamped on the vehicle identification number label and<br />
vehicle certification plate as shown in the illustration.<br />
• Vehicle identification number label: Can be found through the windshield at front left corner of the<br />
instrument panel.<br />
• Vehicle certification plate: Can be found after turning over the front vehicel hood.<br />
01-7<br />
SERIAL NUMBER (SN)<br />
1. FINAL DRIVE SERIAL NUMBER.<br />
(a) The final drive serial number is stamped on the rear axle<br />
welding housing.<br />
2. PROPELLER SHAFT SERIAL NUMBER.<br />
(a) The propeller shaft serial number is stamped on the propeller<br />
shaft tube.<br />
01-8<br />
INTRODUCTION - REPAIR INSTRUCTION<br />
REPAIR INSTRUCTION<br />
PRECAUTION<br />
1. BASIC REPAIR NOTE.<br />
(a) Notes on operation.<br />
1 Protection<br />
2 Safe operation<br />
• Be sure to wear a clean uniform.<br />
• Be sure to wear hat and safety shoes.<br />
• Perform safty inspection each other, when 2 or more persons servicing<br />
togehter.<br />
• When working with the engine running, pay attention to the ventilation<br />
of the workshop.<br />
• In case of operating on high temperature parts, rotating, moving and<br />
vibrating parts, protective clothing is necessary and pay attention not<br />
to burn or injury yourself.<br />
• When jacking up the vehicle, be sure to support the vehicle at correct<br />
position and use safe jack.<br />
• When lifting up the vehicle, use a safe and standard equipment.<br />
3<br />
Preparation of tools and<br />
measuring gauge<br />
• Before starting the servicing, prepare a tool stand, SST, gauge, oil,<br />
shop rag and new parts for replacement.<br />
01-9<br />
4<br />
Removal and installstion,<br />
disassembly and assembly<br />
operations<br />
5 Removed parts<br />
• Diagnose problems with a thorough understanding of the trouble<br />
phenomenon and perform effective operations.<br />
• Before removing the parts, check the assembly for general condition:<br />
deformation and damage.<br />
• When the part structure is complicated, take a note or make match<br />
marks so as not to make mistakes that affect the function of the parts.<br />
• Clean and wash the removed parts if necessary, and assemble them<br />
after a thorough inspection.<br />
• Place the removed parts in the correct order to avoid mixing up or<br />
making them dirty.<br />
• As for non-reusable parts such as gasket, O-rings, and self lock nut,<br />
replace them with new one following the instruction of manual.<br />
• Put the old parts into a box and show them to the customer.<br />
(b) Jacking up and supporting vehicle.<br />
• Be carefully when jacking up and supporting the vehicle. Be sure to lift and support the vehicle at the<br />
proper locations. (Refer to “Chapter 01 introduction - repair instruction, vehicle lift and support<br />
locations”)<br />
(c) Precoated part.<br />
• Precoat removed parts like bolts, nuts, etc. that are coated with sealant at the factory.<br />
• If a precoated part is retightened, loosened or caused to move in any way, it must be recoated with the<br />
sealant.<br />
• When reusing precoated parts, clean the old sealant and dry the part with compressed air. Then apply<br />
the specified sealant to the bolts, nut or threads.<br />
• Sometimes, it is necessary to leave the installed precoated parts for a specified time until the sealant<br />
hardens.<br />
(d) Gasket.<br />
• If necessary, use a sealer or new gasket to prevent leakage.<br />
(e) Bolts, nuts and screws.<br />
• Always tighten the bolts, nuts and screws at the specified torque with a torque wrench.<br />
Perform the torque check with the lower limit value of the torque tolerance.<br />
01-10<br />
(f) Fuse.<br />
• When replacing a fuse, make sure the amperage rating of new fuse is correct. The amperage rating of<br />
new fuse should be the same as old fuse, neither more nor less.<br />
Illustration Symbol Part Name<br />
Fuse<br />
Circuit Breaker<br />
01-11<br />
(g) Clips.<br />
• The removal and installation methods of typical clips used in body parts are shown in the below table.<br />
If the clip is damaged during the servicing, replace with a new one.<br />
Shape (Example)<br />
Removal / Installation<br />
01-12<br />
(h) Removal and installation of vacuum hoses.<br />
• To disconnect the vacuum hoses, pull the hoses by<br />
holding at the end, not at the middle of hose.<br />
• When disconnecting vacuum hoses, use tags to identify<br />
where they should be reconnected.<br />
• After performing the servicing, check carefully whether<br />
the hoses are connected properly.<br />
• When using a vacuum gauge, never force the hose onto<br />
a connector . Always use a adapter to connect hose. The<br />
stretched hose may cause leakage.<br />
01-13<br />
(i) Torque when using a torque wrench with extension tool.<br />
• In case of tightening with a torque wrench which has an<br />
extended length by combining the torque wrench with<br />
SST or extension tool, if you tighten until the reading of<br />
the torque wrench reaches the specified torque value,<br />
the actual value becomes excessive.<br />
• In this manual, only the specified torque is described. In<br />
case of using SST or an extension tool, calculate the<br />
reading of the torque wrench by the following formula.<br />
• Formula: T’ = T × L2 / (L1 + L2)<br />
T’ Reading of torque wrench (N·m)<br />
T<br />
Torque (N•m)<br />
L1<br />
L2<br />
Length of SST or extension tool (mm)<br />
Length of torque wrench (mm)<br />
2. ELECTRONIC CONTROL.<br />
(a) Disconnection and connection of battery terminal.<br />
• Before performing electrical operations, disconnect the<br />
battery negative terminal cable firstly so as to prevent<br />
burnt-out damage by short.<br />
• Disconnect the battery terminal completely without twist<br />
after turning off all switches.<br />
• When the negative (-) terminal cable is disconnected from<br />
the battery, the memory of the clock and audio system will<br />
be cleared. So before servicing, record the necessary data<br />
of the clock and audio system. After servicing, reset the<br />
clock and audio system.<br />
(b) Handling of electronic parts.<br />
• Do not open the cover or case of the module. If the IC<br />
terminals are touched, the IC may be destroyed by static<br />
electricity.<br />
• To disconntect electronic connectors, pull the connector,<br />
not the wire harness.<br />
01-14<br />
• Do not drop electronic components, such as sensors or<br />
relays. If they are dropped on a hard floor, they should be<br />
replaced.<br />
• When cleaning the engine with steam, protect the<br />
electronic components, air filter and emission-related<br />
components from water.<br />
• Never use an impact wrench to remove or install<br />
temperature switches or temperature sensors.<br />
• When checking the wire harness connector, insert the<br />
tester probe carefully to prevent terminals from bending.<br />
• After replacing electronic components, always perform<br />
function check.<br />
3. REMOVAL AND INSTALLATION OF FUEL CONTROL PARTS.<br />
(a) Place for removing and installing of fuel system parts.<br />
• Work in a place with good air ventilation and without anything flammable such as welder, grinder, drill,<br />
electric motor or stove in the surroundings.<br />
• Never work in a place such as a pit or nearby a pit, as there is a place that vaporized fuel is filled in.<br />
(b) Removing and installing of fuel system parts.<br />
• Prepare a fire extinguisher before starting the servicing.<br />
• For prevention of static electricity, connect the fuel changer, vehicle and fuel tank to ground and keep<br />
floor dry to prevent slipping.<br />
• Never use any electric equipment like an electric motor or a working light, as they may cause sparks or<br />
high temperature.<br />
• Never use an iron hammer, as it may cause sparks.<br />
• Dispose the shop rag without any fuel deposit.<br />
4. REMOVAL AND INSTALLATION OF ENGINE INTAKE PARTS.<br />
If any metal chips are into the inlet pass, this may get a bad effect to the engine and turbocharger.<br />
(a)<br />
When removing and installing the inlet system parts,<br />
wrap the opening of engine intake system with clean rag<br />
or tape.<br />
When installing the inlet system parts, check that there is<br />
no mixing of metal chips.<br />
01-15<br />
5. HANDLING OF HOSE CLAMPS.<br />
(a) Before removing the hose, record the depth of the inserting<br />
portion and the old clamp position in order to reinstall it<br />
correctly.<br />
(b) If deformation or dent is found, replace it with a new one.<br />
(c) In case of reusing the hose, install the clamp on the hose<br />
where it has a clamp track.<br />
(d) For a spring type clamp, adjust it by applying force to the<br />
arrow mark direction after the installation.<br />
6. FOR VEHICLES EQUIPPED WITH CATALYTIC CONVERTER.<br />
If large amount of unburned fuel flows into the converter, it may cause overheating and a fire hazard.<br />
To prevent this, observe the following precautions.<br />
(a) Use only unleaded gasoline (gasoline vehicles).<br />
(b) Avoid running the engine at idle speed for more than 20 minutes.<br />
(c) Avoid a spark jump test.<br />
• Perform a spark jump test only when absolutely necessary. Perform this test as quickly as possible.<br />
• While testing, never race the engine.<br />
(d) Avoid a prolonged engine compression measurement. This operation must be performed as quickly as<br />
possible.<br />
(e) Do not run the engine when the fuel tank is nearly empty. This may cause the engine to misfire and<br />
damage the catalytic converter.<br />
01-16<br />
VEHICLE LIFT AND SUPPORT LOCATIONS<br />
1. NOTICE ABOUT VEHICLE CONDITION WHEN JACKING UP.<br />
(a) According to rules, the vehicle must be unloaded when jacking up. Never jack up or lift up the vehicle<br />
with things of heavy weight loading.<br />
(b) When removing any parts of heavy weight like the engine and transmission, the center of gravity of the<br />
vehicle will be changed. Place a balance weight in vehicle so as to keep it from rolling, or support the<br />
vehicle with jack at the position of specification.<br />
2. NOTICE FOR USING JACK AND 4 POSE LIFT.<br />
(a) Follow the instruction in this manual for a safety operation.<br />
(b) Do not damage tires or wheels with a pry bar.<br />
(c) Park the vehicle on a flat road with applying parking brake.<br />
(d) Shift in the reverse position.<br />
(e) Using a wheel stopper, fix the vehicle.<br />
(f) Jack up the vehicle using a jack with rubber attachment.<br />
Be sure to jack up the vehicle at the correct support location.<br />
01-17<br />
(g) Lift the vehicle up by using a 4 pose lift with rubber attachment.<br />
Be sure to lift up the vehicle at the correct support location.<br />
01-18<br />
INTRODUCTION - HOW TO TROUBLESHOOT<br />
HOW TO TROUBLESHOOT<br />
There are many electronic controlled systems in the vehicle. In general, electronic controlled system is considered<br />
to be very complex and require a high level of technical knowledge and expert skill to troubleshoot.<br />
However, the fact is that if you check the circuits one by one, troubleshooting of these systems is not complex.<br />
If you have adequate understanding of the system and basic knowledge of electricity, the problem can be<br />
accurately found out and comfirmed.<br />
This manual is designed based on the above principle to help service technicians perform accurate and<br />
effective troubleshooting.<br />
The troubleshooting procedures are described on the following chapter.<br />
System<br />
Engine Control System<br />
Anti-lock Brake System<br />
Audio System<br />
Supplemental Restraint System<br />
Heater And Air Conditioning System<br />
Lighting System<br />
Wiper And Washer<br />
Multimedia System<br />
Auxiliary Power<br />
Horn System<br />
Reverse Radar System<br />
Power Windows<br />
Outside Mirror<br />
Defrost System<br />
Instrument Cluster<br />
Power Door Locks<br />
Sliding Roof<br />
Reference<br />
Chapter 04 diagnostics - engine control system-4G69<br />
Chapter 04 diagnostics - engine control system-ISF2.8<br />
Chapter 04 diagnostics - engine control system-4JB1T<br />
Chapter 04 diagnostics - anti-lock brake system<br />
Chapter 04 diagnostics - audio system<br />
Chapter 04 diagnostics - supplemental restraint system<br />
Chapter 04 diagnostics - heater and air condition system<br />
Chapter 04 diagnostics - light system<br />
Chapter 04 diagnostics - wiper and washer<br />
Chapter 04 diagnostics - multimedia system<br />
Chapter 04 diagnostics - auxiliary power<br />
Chapter 04 diagnostics - horn system<br />
Chapter 04 diagnostics - reverse radar system<br />
Chapter 04 diagnostics - power windows<br />
Chapter 04 diagnostics - outside mirrors<br />
Chapter 04 diagnostics - defrost system<br />
Chapter 04 diagnostics - instrument cluster<br />
Chapter 04 diagnostics - power door locks<br />
Chapter 04 diagnostics - Sliding Roof<br />
01-19<br />
FOR USING HAND-HELD TESTER<br />
• Before using the tester, be sure to read thoroughly the tester operating manual.<br />
• Connect the tester to the diagnosis wire harness connector and turn the ignition switch to “ON”<br />
position. If the tester can not communicate with the module, there is a problem on the vehicle<br />
side or tester side.<br />
• If the communication is normal when the tester is connected to another vehicle, inspect the<br />
diagnosis data link or module power circuit of the vehicle.<br />
• If the communication is still impossible when the tester is connected to another vehicle, the<br />
problem is probably in the tester itself, so perform the self test procedures described in the<br />
“Tester Operating <strong>Manual</strong>”.<br />
01-20<br />
HOW TO PROCEED WITH TROUBLESHOOTING<br />
• Here, only the basic procedures are shown.<br />
• Carry out troubleshooting in accordance with the procedures on the following pages.<br />
• Details are provided in Chapter 04 diagnostics, showing the most effective methods for each<br />
circuit.<br />
• Confirm the troubleshooting procedures firstly for the relevant circuit before servicing.<br />
1. VEHICLE VISITED TO WORKSHOP<br />
2. CUSTOMER PROBLEM ANALYSIS<br />
Ask the customer about the conditions and environment that the problem occurred.<br />
3. SYMPTOM CONFIRMATION AND DTC (INCLUDING DATA STREAM) CHECK<br />
(c)<br />
(d)<br />
Check the battery positive voltage.<br />
Voltage: 11 ~ 14 V (Engine stopped)<br />
Visually check the wire harness, connectors and fuses for open and short, etc.<br />
Warm up the engine to the operating temperature.<br />
Confirm the problem symptoms and conditions and check for DTCs according to the related chart.<br />
Does the DTC display?<br />
YES > Go to next step.<br />
NO > Go to step 5.<br />
4. DTC CHART<br />
(a) Check the results obtained in step 3, then confirm the inspection procedures for the system or the part<br />
which should be checked with the DTC chart.<br />
Go to step 6 directly.<br />
5. PROBLEM SYMPTOMS TABLE<br />
Check the results obtained in step 3, then confirm the inspection procedures for the system or the part<br />
which should be checked with the problem symptoms table.<br />
6. CIRCUIT INSPECTION OR PARTS INSPECTION<br />
(a) Inspect the circuit or parts according to results obtained in step 4 and 5.<br />
(b) Confirm the circuil or parts which should be repaired.<br />
7. REPAIR<br />
(a) Perform adjustment, repair or replacement according to the results obtained in step 6.<br />
8. CONFIRMATION TEST<br />
After servicing, confirm that the problem has been solved.<br />
If the problem does not recur, perform a confirmation test under the same conditions and enviroment<br />
that vehicle fault occurred at the first time.<br />
9. END<br />
01-21<br />
CUSTOMER PROBLEM ANALYSIS<br />
• In troubleshooting, the problem symptoms must be confirmed accurately, meaning that all<br />
preconceptions must be set aside in order to make an accurate judgement.<br />
• Before comfirmation the problem symptoms, it is very important to ask the the customer about<br />
some detail information of problems.<br />
• The following 5 items are important points in the problem analysis.<br />
What?<br />
When?<br />
Where?<br />
Under what conditions?<br />
How did it happen?<br />
Vehicle model, system name<br />
Date, time, occurrence frequency<br />
Road conditions<br />
Running conditions, driving conditions, weather conditions<br />
Problem symptoms<br />
• Past problems and the repair history which are thought to be unrelated may be useful in some<br />
cases. Therefore, as much information as possible should be gathered and its relationship with<br />
the problem symptoms should be correctly ascertained for use as reference in troubleshooting.<br />
01-22<br />
SYMPTOM CONFIRMATION AND DTC (INCLUDING DATA STREAM) CHECK<br />
The diagnosis system in vehicle has various functions.<br />
• The first function is the Diagnostic Trouble Code (DTC) checking. We could check out stored<br />
fault in the module memory.<br />
• Another function is the Input Signal Check, which checks whether the signals from various<br />
switches are sent to the module correctly.<br />
By using these check functions, it is possible to quickly find potential problem areas and<br />
troubleshooting can be performed effectively.<br />
System System Description DTC Signal Check Data Stream Symptom<br />
Engine Control System ○ ○ ○ ○ ○<br />
Anti-lock Brake System ○ ○ - - ○<br />
Supplemental Restraint<br />
○ ○ - - ○<br />
Heater And Air Conditioning - - - - ○<br />
Lighting System - - - - ○<br />
Wiper And Washer - - - - ○<br />
Multimedia System - - - - ○<br />
Auxiliary Power - - - - ○<br />
Horn System - - - - ○<br />
Reverse Radar System ○ - - - ○<br />
Power Windows - - - - ○<br />
Outside Mirror - - - - ○<br />
Defrost System ○ - - - ○<br />
Instrument Cluster - - - - ○<br />
Power Door Locks - - - - ○<br />
Sliding Roof ○ - - - ○<br />
01-23<br />
In the DTC checking, it is very important to determine whether the problem indicated by the DTC is current<br />
fault or stored fault. In addition, during the problem symptom confirmation, a step must be taken<br />
whether the malfunction indicated by the DTC is directly related to the problem symptom or not. For this<br />
reason, the DTC should be checked before problem confirmation. If missing this step, it may result in<br />
unnecessary troubleshooting for systems which are operating normally. It will cause more difficult to<br />
detect the problem area or repair irrelevant areas. Therefore, always follow the procedures in the<br />
correct order and perform the DTC check.<br />
A flow chart showing how to proceed with troubleshooting with the DTC checking is shown below. This<br />
flow chart shows how to use the DTC checking effectively. Throughout this chart flow, we can know<br />
how to process the DTC troubleshooting and the troubleshooting of problem symptoms table.<br />
1. DTC CHECK<br />
2. RECORD AND CLEAR THE DTC<br />
If a fault code is displayed in the initial DTC checking, it indicates that a trouble may have occurred in<br />
a wire harness or connectors in the past. Therefore, check the wire harness and connectors. (Refer to<br />
“Chapter 01 introduction - how to troubleshoot, electronic circuit inspection procedure”)<br />
3. SYMPTOM CONFIRMATION<br />
Do the problem symptoms still exist?<br />
4. SIMULATION TEST WITH THE METHODS OF SYMPTOM SIMULATION (Refer to “Chapter 01<br />
introduction - how to troubleshoot, how to proceed with troubleshooting”)<br />
5. DTC CHECK AGAIN<br />
Does DTC display?<br />
YES > Proceed with DTC chart.<br />
NO > Go to next step.<br />
6. SYMPTOM CONFIRMATION<br />
Does any symptom exist?<br />
NO > The system is normal.<br />
7. PROCEED WITH PROBLEM SYMPTOMS TABLE<br />
The problem beyond the DTC system ability. The fault code displayed in the DTC is either a past<br />
problem or a secondary problem.<br />
8. END<br />
01-24<br />
SYMPTOM SIMULATION<br />
• The most difficult case in troubleshooting is when no symptoms occurs. In such cases, be sure<br />
to carry out a thorough customer problem analysis. Then simulate the same or similar<br />
conditions and enviroment in which the customer’s vehicle was and when the problem<br />
occurred. No matter how much experience and skill a technician has. If he troubleshoot the<br />
problem without the direction, he will tend to miss some important things during servicing and<br />
make some mistakes, which will lead to a standstill.<br />
• For example, for a problem which only occurs when the engine is cold, or for a problem which<br />
occurs due to vibration caused by the road during driving, etc., the problem can never be found<br />
out when the engine is hot or when the vehicle is stopped. Since enviroment problem like<br />
vibration, heat or moisture which is difficult to reproduce, the symptom simulation tests<br />
introduced here are effective measures that the external causes are applied to the vehicle in a<br />
stationary condition.<br />
1. IMPORTANT POINTS IN THE SYMPTOM SIMULATION TEST:<br />
(a) In the symptom simulation test, the problem symptoms should be confirmed and the problem area or<br />
parts must also be found. So, before starting simulation test, connect hand-held tester into the vehivle<br />
firstly in order to reduce the range of testing.<br />
(b) After the step aboved, carry out the symptom simulation test, judging whether the circuit being tested is<br />
defective or normal and also confirming the problem symptoms at the same time. Refer to the problem<br />
symptoms table of each system, find out the possible causes of the problem.<br />
2. VIBRATION METHOD: When vibration seems to be<br />
the major cause.<br />
(a) Part and sensor.<br />
• Apply slight vibration with your finger to the part or the<br />
sensor and check whether the malfunction occurs.<br />
Apply strong vibration to relays may result in open.<br />
(b) Connectors.<br />
• Lightly shake the connector vertically and horizontally.<br />
(c) Wire harness.<br />
• Lightly shake the wire harness vertically and horizontally.<br />
The connector joint is the major area that should be checked<br />
thoroughly.<br />
01-25<br />
3. HEAT METHOD: If the problem seems to occur when<br />
the temperature is higher.<br />
(a) Heat the component that is possible cause of the malfunction<br />
with a hair dryer or similar object. Check it if the malfunction<br />
occurs.<br />
• Never heat the components to more than 60 ℃ to<br />
prevent from being damaged.<br />
• Never apply heat directly to the module.<br />
4. WATER SPRINKLING METHOD: When the malfunction<br />
seems to occur on a rainy day or in high-humidity.<br />
(a) Sprinkle water on the vehicle and check whether the<br />
malfunction occurs.<br />
• Never spray water directly on the engine hood. Spray a<br />
mist of water on the radiator front surface to change the<br />
temperature and humidity.<br />
• Never spray water directly on the electronic components.<br />
• If a vehicle is subject to water leakage, the leaking water<br />
may damage the module. When testing a vehicle for<br />
water leakage problem, this factor must be considered.<br />
5. HIGH ELECTRICAL LOAD METHODS: If the malfunction seems to occur when electrical load is<br />
excessive.<br />
(a) Turn on all the electrical equipment including the heater blower, headlights, rear windows defrost, etc.<br />
and check whether the malfunction occurs.<br />
01-26<br />
DTC CHART<br />
Take the engine control system as an example, inspection procedures are shown in the illustration below.<br />
The chart indicates the DTCs of the engine control system and lists the corresponding troubleshooting<br />
procedures. It will be more effective and accurate to proceed with troubleshooting in accordance with the<br />
inspection procedures listed in the chart.<br />
01-27<br />
PROBLEM SYMPTOMS TABLE<br />
The problem symptoms table indicates the suspect circuits or parts for each problem symptom, as shown in<br />
the illustration below. Using this table to troubleshoot the problem when the problem is occuring but no DTC<br />
displayed. The number in the table indicates the procedures of troubleshooting.<br />
When the problem is not detected by the diagnostic system even though the problem symptoms is<br />
present, it may be that the problem is occuring beyond the detection range of the dignostic system.<br />
01-28<br />
CIRCUIT INSPECTION<br />
How to read and use each page is shown below.<br />
01-29<br />
ELECTRONIC CIRCUIT INSPECTION PROCEDURE<br />
1. BASIC INSPECTION.<br />
(a) Resistance measuring condition.<br />
• Unless special instruction, all resistance is measured at an ambient temperature of 20 ℃ .<br />
• The resistance may be out of the specifications when measured at high temperature (such as the<br />
engine is hot). So measurements should be performed when the engine is cooled down.<br />
(b) Handling of connectors.<br />
• When disconnecting the connector, press the connector<br />
in the direction of engagement and remove the lock by<br />
lightly pressing the lock claw.<br />
• When removing the connector, do not pull the wire harness<br />
but pull the connector.<br />
• Make sure there is no deformation, damage or missing<br />
terninals before connecting the connector.<br />
• The connector with a lock should be inspected until hearing<br />
a “click”.<br />
• When checking the connector with a mutimeter, be sure<br />
to check it from the backside (wire harness side) of the<br />
connector by using a mini test lead.<br />
• As a water proof connector can not be checked from<br />
the backside, check it by a connecting the adapter.<br />
• Do not damage the terminals when moving the inserted<br />
tester needle.<br />
(c) Connector checking points.<br />
Check when the connector is connected:<br />
• Hold the connector and check the inserting condition and<br />
locking efficiency (engaged condition).<br />
Check when the connector is disconnected:<br />
• Pull the wire harness lightly and check the connector for<br />
missing terminal, terminal crimping condition and core<br />
wire break.<br />
• Check visually for any rust, metal chips, water and bent<br />
terminals.<br />
01-30<br />
Check the contact pressure of the terminal:<br />
• Prepare a spare male terminal and insert it into a female<br />
terminal. Check the engaged condition and sliding.<br />
Always use a gold-plated male terminal to test a gold-plated<br />
female terminal.<br />
(d) Repair method of connector terminal.<br />
• If there is dirty on the contact point, clean the contact<br />
point by using an air gun or shop rag. However, never<br />
polish the contact point using sand paper as the plating<br />
may come off.<br />
• In case of abnormal contact pressure, replace the female<br />
terminal. However, if a male terminal is gold-plated (gold<br />
colour), use a gold-plated female termina. If it is silverplated<br />
(silver colour), use a silver-plated female terminal.<br />
(e) Handling of wire harness.<br />
• When removing the wire harness, check the position of<br />
the wire harness and clamps before servicing, reinstall it<br />
• Never twist, pull or loosen the wire harness.<br />
• Never allow the wire harness to cross a area of high-temperature,<br />
rotating, moving, vibrating or sharp (edge of the<br />
panel, tip of the screw, etc.) part.<br />
• When installing parts, never let the wire harness be interfered.<br />
• Never cut or break the cover of the wire harness. If it is<br />
cut or broken, replace it or repair it with electrical tape.<br />
2. CHECK OPEN CIRCUIT.<br />
(a) For the open circuit shown in the illustration, perform a<br />
resistance check in step (b) or voltage check in step (c)<br />
to comfirm fault.<br />
01-31<br />
(b) Check the resistance.<br />
• Disconnect connector A & C and measure the resistance<br />
between them.<br />
Resistance: < 2 Ω<br />
Measure the resistance while lightly shaking the wire harness<br />
vertically and horizontally.<br />
For this circuit:<br />
The resistance between terminal 1 of connector A and terminal<br />
1 of connector C: ≥ 1 MΩ<br />
The resistance between terminal 2 of connecor A and terminal 2<br />
of connector B: < 2 Ω<br />
Therefore, the cause is an open circuit between terminal 1 of<br />
connector A and terminal 1 of connector C.<br />
• Disconnect connector B and measure the resistance<br />
between the connectors.<br />
1 of connector B1: < 2 Ω<br />
The resistance between terminal 1 of connector B2 and terminal<br />
connector B2 and terminal 1 of connector C.<br />
(c) Check the voltage.<br />
• An open circuit which voltage is applied can be checked by<br />
conducting a voltage check.<br />
• For the open circuit which each connector is still connected<br />
shown in the illustration, measure the voltage orderly<br />
between ground and terminal 1 of connector A at the ECU 5<br />
V output terminal, terminal 1 of connector B and terminal 1 of<br />
connector C.<br />
The voltage between terminal 1 of connector A and ground: 5 V<br />
The voltage between terminal 1 of connector B and ground: 5 V<br />
The voltage between terminal 1 of connector C and ground: 0 V<br />
Therefore, the cause is an open circuit in the wire harness<br />
between terminal 1 of connector B and terminal 1 of connector<br />
C.<br />
01-32<br />
3. CHECK SHORT CIRCUIT.<br />
(a) For the short circuit shown in the illustration, perform a<br />
resistance check in step (b) to locate the section.<br />
between terminal 1 and 2 of connector A and ground.<br />
Resistance: ≥ 1 MΩ<br />
Measure the resistance while lightly shaking the wire<br />
harness vertically and horizontally.<br />
The resistance between terminal 1 of connector A and ground: < 2<br />
Ω<br />
The resistance between terminal 2 of connector A and ground: ≥ 1<br />
MΩ<br />
Therefore, the cause is an short circuit between terminal 1 of<br />
• Disconnect connector B and measure the resistance between<br />
terminal 1 of connector A and B2 and ground.<br />
The resistance between terminal 1 of connector A and ground: ≥ 1 MΩ<br />
The resistance between terminal 1 of connector B2 and ground: < 2 Ω<br />
Therefore, the cause is a short circuit between terminal 1 of<br />
INTRODUCTION - TERMS<br />
01-33<br />
TERMS<br />
ABBREVIATIONS USED IN THIS MANUAL<br />
A/C<br />
Abbreviations<br />
Air Conditioning<br />
Meaning<br />
A/F<br />
ABS<br />
ACC<br />
ASSY<br />
BAT<br />
B-joint<br />
BTDC<br />
CKP<br />
Air-fuel Ratio<br />
Accessory<br />
Assembly<br />
Battery<br />
Ball Joint<br />
Before Top Dead Center<br />
Crankshaft Position<br />
CMP<br />
Camshaft Position<br />
DLC3 Data Link Connector 3<br />
DTC<br />
Diagnostic Trouble Code<br />
ECM<br />
Engine Control Module<br />
ECT<br />
ECU<br />
EFI<br />
EGR<br />
EVAP<br />
GEN<br />
GND<br />
HO2S<br />
HVAC<br />
IAT<br />
ISC<br />
KS<br />
LSP<br />
MAF<br />
MIL<br />
MWP<br />
No.<br />
O2S<br />
Engine Coolant Temperature<br />
Engine Control Unit<br />
Engine Fuel Injection<br />
Exhaust Gas Recirculation<br />
Evaporative Emission<br />
Generator<br />
Ground<br />
Heated Oxygen Sensor<br />
Heater And Air Conditioning<br />
Intake Air Temperature<br />
Idle Speed Control<br />
Knock Sensor<br />
Load Sensing Proportioning<br />
Mass Air Flow<br />
Malfunction Indicator Lamp<br />
Max Working Pressure<br />
Number<br />
Oxygen Sensor<br />
01-34<br />
OBD<br />
PCV<br />
RCM<br />
RPM<br />
SFI<br />
SRS<br />
SSM<br />
SST<br />
TC<br />
TPS<br />
U-joint<br />
On-Board Diagnostic<br />
Positive Crankcase Ventilation<br />
Restraint Control Module<br />
Revolutions Per Minute<br />
Sequential Multiport Fuel Injection<br />
Special Service Materials<br />
Special Service Tools<br />
Turbocharger<br />
Throttle Position Sensor<br />
Universal Joint<br />
PREPARATION<br />
DIAGNOSTICS................................................................................... 02-1<br />
PREPARATION ........................................................................... 02-1<br />
ENGINE CONTROL SYSTEM............................................................ 02-3<br />
PREPARATION ........................................................................... 02-3<br />
FUEL .................................................................................................. 02-4<br />
PREPARATION ........................................................................... 02-4<br />
EMISSION CONTROL........................................................................ 02-5<br />
PREPARATION ........................................................................... 02-5<br />
INTAKE AIR ....................................................................................... 02-6<br />
PREPARATION ........................................................................... 02-6<br />
ENGINE MECHANICAL..................................................................... 02-7<br />
PREPARATION ........................................................................... 02-7<br />
EXHAUST......................................................................................... 02-10<br />
PREPARATION ......................................................................... 02-10<br />
COOLING ......................................................................................... 02-11<br />
PREPARATION ......................................................................... 02-11<br />
LUBRICATION ................................................................................. 02-12<br />
PREPARATION ......................................................................... 02-12<br />
STARTING AND CHARGING .......................................................... 02-14<br />
PREPARATION ......................................................................... 02-14<br />
FRONT SUSPENSION..................................................................... 02-15<br />
PREPARATION ......................................................................... 02-15<br />
REAR SUSPENSION ....................................................................... 02-16<br />
PREPARATION ......................................................................... 02-16<br />
TIRE AND WHEEL........................................................................... 02-17<br />
PREPARATION ......................................................................... 02-17<br />
AXLE AND PROPELLER SHAFT.................................................... 02-18<br />
PREPARATION ......................................................................... 02-18<br />
BRAKE ............................................................................................. 02-21<br />
PREPARATION ......................................................................... 02-21<br />
PARKING BRAKE............................................................................ 02-22<br />
PREPARATION ......................................................................... 02-22<br />
TRANSMISSION .............................................................................. 02-23<br />
PREPARATION ......................................................................... 02-23<br />
CLUTCH ........................................................................................... 02-25<br />
PREPARATION ......................................................................... 02-25<br />
STEERING COLUMN....................................................................... 02-26<br />
PREPARATION ......................................................................... 02-26<br />
POWER STEERING......................................................................... 02-27<br />
PREPARATION ......................................................................... 02-27<br />
HEATER AND AIR CONDITIONING................................................ 02-28<br />
PREPARATION ......................................................................... 02-28<br />
SEAT BELT...................................................................................... 02-30<br />
PREPARATION ......................................................................... 02-30<br />
WIPER AND WASHER .................................................................... 02-31<br />
PREPARATION ......................................................................... 02-31<br />
WINDSHIELD/SIDE WINDOW GLASS/REAR VIEW MIRROR....... 02-32<br />
PREPARATION ......................................................................... 02-32<br />
INSTRUMENT PANEL/INSTRUMENT............................................. 02-33<br />
PREPARATION ......................................................................... 02-33<br />
02<br />
SEAT ................................................................................................ 02-34<br />
PREPARATION ......................................................................... 02-34<br />
DOOR LOCKS.................................................................................. 02-35<br />
PREPARATION ......................................................................... 02-35<br />
DOORS............................................................................................. 02-36<br />
PREPARATION ......................................................................... 02-36<br />
VEHICLE CONTROL SYSTEM........................................................ 02-37<br />
PREPARATION ......................................................................... 02-37<br />
PREPARATION - DIAGNOSTICS<br />
02-1<br />
DIAGNOSTICS<br />
RECOMMENDED TOOLS<br />
Collective Intellegence Scan Tool<br />
ENGINE CONTROL SYSTEM<br />
Digital Multimeter<br />
Test Lead Set<br />
ANTI-LOCK BRAKE SYSTEM<br />
SUPPLEMENTAL RESTRAINT<br />
SYSTEM<br />
HEATER AND AIR<br />
CONDITIONING SYSTEM<br />
LIGHTING SYSTEM<br />
WIPER AND WASHER<br />
MULTIMEDIA SYSTEM<br />
AUXILIARY POWER<br />
HORN SYSTEM<br />
REVERSE RADAR SYSTEM<br />
POWER WINDOWS<br />
OUTSIDE MIRROR<br />
DEFROST SYSTEM<br />
INSTRUMENT CLUSTER<br />
POWER DOOR LOCKS<br />
SLIDING ROOF<br />
19A<br />
Torque Wrench -<br />
EQUIPMENT<br />
Oscilloscope -<br />
02-2<br />
Item Capacity Specification<br />
Thread sealant - 3M No.4171 or equivalent<br />
PREPARATION - ENGINE CONTROL SYSTEM<br />
FUEL INJECTION SYSTEM<br />
IGNITION SYSTEM<br />
SENSOR<br />
ACTUATOR<br />
02-3<br />
02-4<br />
PREPARATION - FUEL<br />
FUEL<br />
Needle Nose Plier<br />
FUEL PRESSURE REGULATOR<br />
Hydraulic Jack<br />
FUEL TANK ASSY<br />
Torque Wrench<br />
FUEL FITER ASSY<br />
FUEL PUMP REMOVER<br />
FUEL PUMP<br />
Fuel injector leakage tester -<br />
Grease - -<br />
EMISSION CONTROL<br />
PREPARATION - EMISSION CONTROL<br />
Air Blow Gun<br />
02-5<br />
VAPER CANISTER<br />
CANISTER CONTROL SOLENOID<br />
VALVE<br />
02-6<br />
INTAKE AIR<br />
PREPARATION - INTAKE AIR<br />
Sealant - <strong>Foton</strong> sealant<br />
PREPARATION - ENGINE MECHANICAL<br />
02-7<br />
ENGINE MECHANICAL<br />
Camshaft Pulley Spanner Wrench<br />
CAMSHAFT TIMING PULLEY<br />
Cylinder Cover Bolt Spanner<br />
CYLINDER COVER BOLT<br />
Crankshaft Front Oil Seal Guide<br />
CRANKSHAFT FRONT OIL SEAL<br />
Crankshaft Front Oil Seal Installer<br />
Hydraulic Tappet Adjuster Leakage<br />
Tester<br />
HYDRAULIC TAPPET ADJUSTER<br />
Hydraulic Tappet Adjuster Keeper<br />
Hydraulic Tappet Adjuster Wiring<br />
Camshaft Oil Seal Installer<br />
CAMSHAFT OIL SEAL<br />
Pin For Belt Gear<br />
Oil Pan Remover<br />
OIL PAN<br />
02-8<br />
Valve Spring Compressor<br />
VALVE AND INTERRELATED<br />
PARTS<br />
Valve Oil Seal Installer<br />
VALVE OIL SEAL<br />
Crankshaft Rear Oil Seal Installer<br />
CRANKSHAFT REAR OIL SEAL<br />
Crankshaft Pulley Puller<br />
CRANKSHAFT TIMING PULLEY<br />
Piston Disassembling and<br />
Assembling Tool<br />
PISTON<br />
Flywheel Holder<br />
FLYWHEEL<br />
Snap Ring Plier -<br />
ENGINE ASSY<br />
Feeler Gauge -<br />
CLAMP<br />
02-9<br />
V-block -<br />
Coolant 10 L <strong>Foton</strong> long life coolant<br />
Engine oil<br />
gasoline<br />
diesel<br />
4 L<br />
5 ~ 5.5 L<br />
Temperature -25 ~ 30 ℃<br />
Temperature -20 ~ 40 ℃<br />
Temperature -30 ~ 30 ℃<br />
Temperature -20 ~ 30 ℃<br />
SL 10W-30<br />
SL 15W-40<br />
SL 5W-30<br />
CF-4 or above, 15W-40<br />
CF-4 or above, 15W-30<br />
02-10<br />
PREPARATION - EXHAUST<br />
EXHAUST<br />
Feeler Gauge<br />
EXHAUST MANIFOLD<br />
Exhaust pipe sealant - <strong>Foton</strong> sealant<br />
PREPARATION - COOLING<br />
02-11<br />
COOLING<br />
Radiator Cap Tester<br />
COOLANT RESERVOIR<br />
Thermometer<br />
THERMOSTAT<br />
Steam cleaner -<br />
02-12<br />
PREPARATION - LUBRICATION<br />
LUBRICATION<br />
Oil Filter Wrench<br />
OIL FILTER<br />
Engine Oil Pressure Switch<br />
Remover<br />
ENGINE OIL PRESSURE SWITCH<br />
Rubber Hammer<br />
Planometer -<br />
02-13<br />
02-14<br />
STARTING AND CHARGING<br />
PREPARATION - STARTING AND CHARGING<br />
GENERATOR<br />
STARTER<br />
Dial Indicator<br />
Vernier Caliper<br />
Puller<br />
Soldering Gun<br />
Snap Ring Plier<br />
Belt Tension Gauge -<br />
Battery Charger -<br />
Discharge Tongs -<br />
PREPARATION - FRONT SUSPENSION<br />
02-15<br />
FRONT SUSPENSION<br />
Wheel alignment instrument -<br />
Tire changer -<br />
Tire dynamic balancer -<br />
02-16<br />
PREPARATION - REAR SUSPENSION<br />
REAR SUSPENSION<br />
Spring Scale -<br />
PREPARATION - TIRE AND WHEEL<br />
02-17<br />
TIRE AND WHEEL<br />
Tire Pressure Gauge<br />
Tire inflater -<br />
Balance block - -<br />
02-18<br />
PREPARATION - AXLE AND PROPELLER SHAFT<br />
AXLE AND PROPELLER SHAFT<br />
TIRE<br />
PROPELLER SHAFT SPLINE<br />
DRIVE AXLE SIDE GEAR<br />
Hammer<br />
Brass Bar<br />
PROPELLER SHAFT U-JOINT<br />
CENTER SUPPORT BEARING<br />
FRONT AXLE HUB GREASE CAP<br />
REAR AXLE HUB BEARING<br />
STEERING KNUCKLE<br />
DIFFERENTIAL PINION SHAFT<br />
Micrometer Calipers<br />
CROSS SPIDER<br />
FRONT AXLE HUB BEARING<br />
DRIVE PINION<br />
CROWN GEAR<br />
DIFFERENTIAL PINION<br />
PINION FLANGE<br />
OUTPUT FLANGE<br />
PROPELLER SHAFT END YOKE<br />
AXLE SHAFT BEARING<br />
DRIVING GEAR BEARING<br />
Grease Gun<br />
02-19<br />
Spring Scale<br />
FRONT AXLE HUB STARTING<br />
TORQUE<br />
REAR AXLE HUB STARTING<br />
COTTER PIN<br />
CENTER SUPPORT BEARING OIL<br />
SEAL<br />
OUTPUT FLANGE OIL SEAL<br />
DRIVE PINON OIL SEAL<br />
Tapeline<br />
REAR AXLE BACK LASH<br />
Allen Wrenchs (Key) -<br />
FINAL DRIVE ASSY<br />
DRIVE AXLE SIDE GEAR THRUST<br />
WASHER<br />
DIFFERENTIAL PINION THRUST<br />
DRIVE PINION ADJUSTING SHIM<br />
DRIVE PINION STARTING<br />
Propeller dynamic balancer -<br />
Vice -<br />
Press machine -<br />
02-20<br />
Red lead - -<br />
Grease<br />
propeller shaft U-joint<br />
center support bearing<br />
front axle hub<br />
axle shaft<br />
output flange oil seal<br />
drive pinion oil seal<br />
-<br />
Lithium base grease No.2<br />
Final drive oil 2.5 L GL-5 80W/90<br />
Sealant<br />
ouput flange<br />
crown gear<br />
differential bearing<br />
LOCTITE 204<br />
PREPARATION - BRAKE<br />
02-21<br />
BRAKE<br />
FRONT BRAKE DISK<br />
REAR BRAKE DRUM<br />
REAR BRAKE SHOE<br />
Nipper Plier<br />
WHEEL BRAKE CYLINDER<br />
BRAKE PAD<br />
BRAKE MASTER CYLINDER<br />
FRONT AXLE HUB<br />
REAR AXLE HUB<br />
FRONT AXLE HUB OIL SEAL<br />
REAR AXLE HUB OIL SEAL<br />
AXLE SHAFT<br />
Brake fluid - V3/V4<br />
02-22<br />
PREPARATION - PARKING BRAKE<br />
PARKING BRAKE<br />
FRONT PARKING BRAKE PULL<br />
CABLE ASSY<br />
REAR PARKING BRAKE PULL<br />
CABLE ASSY LH<br />
CABLE ASSY RH<br />
PREPARATION - TRANSMISSION<br />
02-23<br />
TRANSMISSION<br />
SYNCHRONIZER ASSY<br />
COUNTER SHAFT WASHER<br />
RETURN SPRING<br />
REVERSE IDLER GEAR SHAFT<br />
OUTPUT SHAFT<br />
INPUT SHAFT WASHER<br />
INPUT SHAFT ASSY<br />
OUTPUT SHAFT ASSY<br />
SHIFT MECHANISM<br />
GEARSHIFT FORK<br />
OUTPUT FRONT BEARING<br />
OUTPUT MIDDLE BEARING<br />
OUTPUT REAR BEARING<br />
02-24<br />
Transmission fluid 2 L GL-4 75W/90<br />
Grease - Mitsubishi No.0101011<br />
Sealant -<br />
Mitsubishi No.997740<br />
3M No.4170<br />
PREPARATION - CLUTCH<br />
02-25<br />
CLUTCH<br />
CLUTCH DISK<br />
CLUTCH COVER<br />
CLUTCH MASTER CYLINER ASSY<br />
02-26<br />
STEERING COLUMN<br />
PREPARATION - STEERING COLUMN<br />
OFF TRACK<br />
Allen Wrenchs (Key)<br />
HORN SWITCH ASSY<br />
STEERING WHEEL TURNING<br />
FORCE<br />
STEERING PROPELLER SHAFT<br />
U-JOINT<br />
POWER STEERING<br />
PREPARATION - POWER STEERING<br />
02-27<br />
Steering fluid 1.2 L ATF - Ⅲ<br />
Grease power steering box - QL-5 80W/90<br />
Sealant low-pressure hose - -<br />
02-28<br />
PREPARATION - HEATER AND AIR CONDITIONING<br />
HEATER AND AIR CONDITIONING<br />
Manifold Gauge<br />
REFRIGERANT<br />
COMPRESSOR<br />
Service Hoses<br />
Service Coupler<br />
3-way Joint<br />
Service Tank<br />
Vacuum Pump Connector<br />
Refrigerant Leakage Tester<br />
Eyes Protecter -<br />
ENVIRONMENT TEMPERATURE<br />
Thermistance Type Thermometer<br />
OUTLET TEMPERATURE<br />
Belt Tension Gauge<br />
PULLEY<br />
02-29<br />
Refrigerant Recovery / Recycling<br />
Station<br />
(With this device, vacuum pump is<br />
not required.)<br />
Vacuum Pump<br />
Refrigerant<br />
front and rear A/C<br />
only front A/C<br />
850 ± 25 g<br />
700 ± 25 g<br />
R-134a<br />
Compressor oil 180 ml -<br />
02-30<br />
SEAT BELT<br />
PREPARATION - SEAT BELT<br />
PREPARATION - WIPER AND WASHER<br />
02-31<br />
02-32<br />
PREPARATION - WINDSHIELD/SIDE WINDOW GLASS/REAR VIEW MIRROR<br />
WINDSHIELD/SIDE WINDOW GLASS/REAR VIEW MIRROR<br />
Scraper<br />
WINDSHIELD<br />
SIDE WINDOW<br />
REAR WINDOW<br />
Suction Cup<br />
Knife<br />
Sealer Gun<br />
Protective Tape - -<br />
Block - -<br />
Plastic Paper - -<br />
Steel Wire - -<br />
Nylon Cord - -<br />
Adhesive Tape - -<br />
Primer - Reactive polyester primer, black<br />
Sealant - Polyurethane sealant, black<br />
PREPARATION - INSTRUMENT PANEL/INSTRUMENT<br />
INSTRUMENT PANEL/INSTRUMENT<br />
02-33<br />
Allen Wrenchs (key) -<br />
Pry -<br />
02-34<br />
PREPARATION - SEAT<br />
SEAT<br />
Needle Nose Plier -<br />
DOOR LOCKS<br />
PREPARATION - DOOR LOCKS<br />
02-35<br />
DOOR LOCK CORE<br />
Grease - Lithium base grease No.2<br />
02-36<br />
PREPARATION - DOORS<br />
DOORS<br />
DOOR<br />
VEHICLE CONTROL SYSTEM<br />
PREPARATION - VEHICLE CONTROL SYSTEM<br />
02-37<br />
IGNITION SWITCH ASSY<br />
MEMO<br />
SERVICE SPECIFICATIONS<br />
SPECIFIED TORQUE FOR SPECIFICATION BOLTS...................... 03-1<br />
ENGINE CONTROL SYSTEM............................................................ 03-2<br />
SERVICE DATA........................................................................... 03-2<br />
TORQUE SPECIFICATION ......................................................... 03-3<br />
FUEL .................................................................................................. 03-4<br />
SERVICE DATA........................................................................... 03-4<br />
TORQUE SPECIFICATION ......................................................... 03-4<br />
EMISSION CONTROL........................................................................ 03-5<br />
TORQUE SPECIFICATION ......................................................... 03-5<br />
ENGINE MECHANICAL..................................................................... 03-6<br />
SERVICE DATA........................................................................... 03-6<br />
TORQUE SPECIFICATION ......................................................... 03-9<br />
INTAKE AIR ..................................................................................... 03-10<br />
SERVICE DATA......................................................................... 03-10<br />
TORQUE SPECIFICATION ....................................................... 03-10<br />
EXHAUST......................................................................................... 03-11<br />
SERVICE DATA......................................................................... 03-11<br />
TORQUE SPECIFICATION ....................................................... 03-11<br />
COOLING ......................................................................................... 03-12<br />
SERVICE DATA......................................................................... 03-12<br />
TORQUE SPECIFICATION ....................................................... 03-12<br />
LUBRICATION ................................................................................. 03-13<br />
TORQUE SPECIFICATION ....................................................... 03-13<br />
IGNITION.......................................................................................... 03-14<br />
SERVICE DATA......................................................................... 03-14<br />
TORQUE SPECIFICATION ....................................................... 03-14<br />
STARTING AND CHARGING .......................................................... 03-15<br />
SERVICE DATA......................................................................... 03-15<br />
TORQUE SPECIFICATION ....................................................... 03-16<br />
FRONT SUSPENSION..................................................................... 03-17<br />
SERVICE DATA......................................................................... 03-17<br />
TORQUE SPECIFICATION ....................................................... 03-17<br />
REAR SUSPENSION ....................................................................... 03-18<br />
TORQUE SPECIFICATION ....................................................... 03-18<br />
TIRE AND WHEEL........................................................................... 03-19<br />
SERVICE DATA......................................................................... 03-19<br />
TORQUE SPECIFICATION ....................................................... 03-19<br />
AXLE AND PROPELLER SHAFT.................................................... 03-20<br />
SERVICE DATA......................................................................... 03-20<br />
TORQUE SPECIFICATION ....................................................... 03-21<br />
BRAKE ............................................................................................. 03-23<br />
SERVICE DATA......................................................................... 03-23<br />
TORQUE SPECIFICATION ....................................................... 03-23<br />
PARKING BRAKE............................................................................ 03-24<br />
TORQUE SPECIFICATION ....................................................... 03-24<br />
TRANSMISSION .............................................................................. 03-25<br />
SERVICE DATA ........................................ 03-25<br />
TORQUE SPECIFICATION .............................. 03-26<br />
CLUTCH ........................................................................................... 03-27<br />
SERVICE DATA......................................................................... 03-27<br />
03<br />
TORQUE SPECIFICATION ....................................................... 03-27<br />
STEERING COLUMN....................................................................... 03-28<br />
SERVICE DATA......................................................................... 03-28<br />
TORQUE SPECIFICATION ....................................................... 03-28<br />
POWER STEERING ......................................................................... 03-29<br />
SERVICE DATA......................................................................... 03-29<br />
TORQUE SPECIFICATION ....................................................... 03-30<br />
HEATER AND AIR CONDITIONING................................................ 03-31<br />
SERVICE DATA......................................................................... 03-31<br />
TORQUE SPECIFICATION ....................................................... 03-31<br />
SEAT BELT ...................................................................................... 03-32<br />
TORQUE SPECIFICATION ....................................................... 03-32<br />
LIGHTING......................................................................................... 03-33<br />
TORQUE SPECIFICATION ....................................................... 03-33<br />
WIPER AND WASHER .................................................................... 03-34<br />
TORQUE SPECIFICATION ....................................................... 03-34<br />
SEAT ................................................................................................ 03-35<br />
TORQUE SPECIFICATION ....................................................... 03-35<br />
DOORS............................................................................................. 03-36<br />
SERVICE DATA......................................................................... 03-36<br />
TORQUE SPECIFICATION ....................................................... 03-36<br />
EXTERIOR AND INTERIOR TRIM................................................... 03-37<br />
TORQUE SPECIFICATION ....................................................... 03-37<br />
VEHICLE CONTROL SYSTEM........................................................ 03-38<br />
TORQUE SPECIFICATION ....................................................... 03-38<br />
SERVICE SPECIFICATIONS - SPECIFIED TORQUE FOR SPECIFICATION BOLTS<br />
03-1<br />
SPECIFIED TORQUE FOR SPECIFICATION BOLTS<br />
The range of the tightening torques listed in the following table have already contained the error of the<br />
used tools.<br />
Thread Standard<br />
Torque (N·m)<br />
Grade 8.8 Grade 10.9<br />
M5 9 ~ 11 12 ~ 14<br />
M8<br />
M8 × 1<br />
M10<br />
M10 × 1.25<br />
M10 × 1<br />
M12<br />
M12 × 1.5<br />
M12 × 1.25<br />
M14<br />
M14 × 1.5<br />
M16<br />
M16 × 1.5<br />
M18<br />
M18 × 1.5<br />
M20<br />
M20 × 1.5<br />
21 ~ 25<br />
22 ~ 27<br />
41 ~ 51<br />
45 ~ 55<br />
46 ~ 56<br />
73 ~ 89<br />
75 ~ 92<br />
78 ~ 96<br />
122 ~ 149<br />
126 ~ 154<br />
182 ~ 222<br />
199 ~ 243<br />
243 ~ 285<br />
287 ~ 336<br />
389 ~ 456<br />
396 ~ 465<br />
29 ~ 35<br />
32 ~ 39<br />
58 ~ 71<br />
63 ~ 77<br />
65 ~ 79<br />
105 ~ 128<br />
106 ~ 130<br />
113 ~ 138<br />
160 ~ 195<br />
178 ~ 218<br />
247 ~ 290<br />
265 ~ 311<br />
380 ~ 437<br />
397 ~ 457<br />
486 ~ 548<br />
540 ~ 596<br />
03-2<br />
SERVICE SPECIFICATIONS - ENGINE CONTROL SYSTEM<br />
SERVICE DATA<br />
GASOLINE ENGINE (4G69)<br />
ECT sensor resistance 0 ℃<br />
20 ℃<br />
40 ℃<br />
80 ℃<br />
5.1 ~ 6.5 KΩ<br />
2.1 ~ 2.7 KΩ<br />
0.9 ~ 1.3 KΩ<br />
0.26 ~ 0.36 KΩ<br />
Engine idle speed Standard 750 ± 50 RPM<br />
Idle air control motor coil resistance<br />
Standard 28 ~ 33 Ω ( 20 ℃)<br />
TPS resistance Standard 3.5 ~ 6.5 Ω ( 20 ℃)<br />
IAT resistance 0 ℃<br />
5.3 ~ 6.7 KΩ<br />
2.3 ~ 3.0 KΩ<br />
1.0 ~ 1.5 KΩ<br />
0.30 ~ 0.42 KΩ<br />
CKP resistance Standard 560 Ω ± 10% ( 20 ℃)<br />
Upstream HO2S resistance<br />
Downstream HO2S resistance<br />
Terminal 3 and 4 2.5 ~ 4.5 Ω ( 20 ℃)<br />
Canister solenoid valve Standard 19 ~ 22 Ω ( 20 ℃)<br />
DIESEL ENGINE (ISF2.8)<br />
Coolant temperature sensor (ECT) resistance - 10 ℃<br />
0 ℃<br />
100 ℃<br />
9.397 Ω<br />
5.986 Ω<br />
2.500 Ω<br />
1.175 Ω<br />
0.323 Ω<br />
0.186 Ω<br />
TPS(APPS1)<br />
TPS(APPS2)<br />
Fully opened<br />
Fully closed<br />
0.72 ~ 0.74 V<br />
3.95 V<br />
0.36 ~ 0.37 V<br />
1.97 V<br />
CKP resistance Standard 860 Ω ± 86 Ω ( 20 ℃)<br />
03-3<br />
TORQUE SPECIFICATION<br />
Part Tightened<br />
N•m<br />
ECM × Body 19.6<br />
ECT sensor × Engine cylinder block 20 ~ 25<br />
Idle air control valve × Throttle body 20 ~ 25<br />
TPS × Throttle body 1.7 ~ 2.6<br />
MAP sensor / IAT sensor × Intake manifold -<br />
CKP sensor × flying wheel housing -<br />
Upstream HO2S × Exhaust pipe 40 ~ 60<br />
Downstream HO2S × Exhaust pipe 40 ~ 60<br />
Ignition control module -<br />
Canister solenoid valve x engine bracket -<br />
Odometer sensor × Transmission -<br />
EGR temperature sensor × Engine cylinder block -<br />
Preheat plug -<br />
EGR vacuum regulator -<br />
EGR cooling tube -<br />
Inlet solenoid valve -<br />
03-4<br />
SERVICE SPECIFICATIONS - FUEL<br />
Gasoline engine fuel pressure<br />
Ignition switch ON<br />
Engine idling<br />
Ignition switch OFF<br />
Diesel engine fuel pressure -<br />
Injector electric power parameter<br />
Peak current<br />
Holding current<br />
resistance<br />
Fuel pump filling quantity Standard -<br />
Rear Fuel tank bracket × Fuel tank 41 ~ 51<br />
Fuel hose board retaining bolt × Body 41 ~ 51<br />
Fuel level sensor & bracket assy × Fuel tank 60 ~ 70<br />
Fuel pump × Fuel tank 60 ~ 70<br />
Gasoline engine fuel filter belt bolt 21 ~ 25<br />
Gasoline fuel fliter -<br />
Diesel filter hand pump bolt -<br />
High-pressure tube -<br />
High-pressure tube × Injector -<br />
Injector plate retaining bolt<br />
1st step<br />
2nd step<br />
Lower-pressure filter bracket bolt -<br />
SERVICE SPECIFICATIONS - EMISSION CONTROL<br />
Diesel engine EGR valve × EGR cooling pipe -<br />
Diesel engine EGR valve × Exhaust pipe -<br />
Vacuum regulator bolt Diesel 9 ~ 11<br />
03-5<br />
03-6<br />
GASOLINE ENGINE(4G69)<br />
ENGINE ASSY 4G69<br />
SERVICE SPECIFICATIONS - ENGINE MECHANICAL<br />
Type<br />
Four cylinder in-line, water cooling, four stroke, EFI<br />
Cylinder 4<br />
Combustion chamber<br />
Displacement<br />
Bore<br />
Stroking<br />
Maximum torque<br />
Rated power<br />
Pent-roof combustion chamber<br />
2.378 L<br />
87 mm<br />
100 mm<br />
200 N·m<br />
96 KW (5250 r / min)<br />
Compression ratio 10:1<br />
Lubrication system<br />
Fuel pump type<br />
Water pump type<br />
Pressure, splash compound<br />
Gear type<br />
Centrifugal vane wheel type<br />
TIMING BELT<br />
Tensioner ejector pin herniation amount Standard 12 mm<br />
Tensioner ejector pin displacement ( force 98 ~ 196N)<br />
Standard<br />
≤ 1 mm<br />
ROCKER ARM/ROCKER SHAFT<br />
Rocker arm inner diameter -<br />
Rocker shaft diameter -<br />
Clearance<br />
HYDRAULIC ADJUSTER/VALVE PUSH ROD<br />
Limit<br />
Run-out of push rod Limit -<br />
Hydraulic adjuster external diameter Standard -<br />
Hydraulic adjuster hole diameter Standard -<br />
Fit clearance<br />
CAMSHAFT<br />
Cam height Intake Standard<br />
Exhaust<br />
37.39 mm<br />
36.89 mm<br />
36.83 mm<br />
36.33 mm<br />
03-7<br />
1st camshaft journal Standard -<br />
2nd camshaft journal Standard -<br />
3rd camshaft journal Standard -<br />
4th canshaft journa Standard -<br />
5th camshaft journal Standard -<br />
1st canshaft bearing bore Standard -<br />
2nd canshaft bearing bore Standard -<br />
3rd canshaft bearing bore Standard -<br />
4th canshaft bearing bore Standard -<br />
5th canshaft bearing bore Standard -<br />
axial clearance between thrust plate and 1st camshaft<br />
journal thrust surface<br />
Camshaft run-out Limit -<br />
CYLINDER HEAD<br />
Cylinder head gasket surface flatness Limit 0.2 mm<br />
Edge thickness Intake Standard<br />
1.0 mm<br />
0.5 mm<br />
1.2 mm<br />
0.7 mm<br />
Valve rod diameter<br />
6.0 mm<br />
Crest clearance between valve rod and guide<br />
Intake<br />
0.02 mm ~ 0.05 mm<br />
0.1 mm<br />
0.03 mm ~ 0.07 mm<br />
0.15 mm<br />
Inclination valve Standard 45° ~ 45.5°<br />
Valve rod length Intake Standard<br />
112.30 ~ 111.80 mm<br />
114.11 ~ 113.61 mm<br />
Valve stem guide hole<br />
Oversize 0.05 mm<br />
11.05 mm ~ 11.068 mm<br />
11.25 mm ~ 11.268 mm<br />
11.50 mm ~ 11.518 mm<br />
Valve height Intake Standard<br />
112.30 mm<br />
111.8 mm<br />
114.11 mm<br />
113.61 mm<br />
VALVE SPRING<br />
03-8<br />
Free height<br />
Pre-loading force/operation height km/mm<br />
Center line<br />
51.0 mm<br />
50.0 mm<br />
27.2 Kg/44.2 mm<br />
≤ 2°<br />
4°<br />
Valve spring elastic Standard -<br />
Clearance between piston ring and groove side<br />
Clearance No.1 ring Standard<br />
No.2 ring<br />
Oil ring<br />
0.02 ~ 0.06 mm<br />
0.25 ~ 0.35 mm<br />
0.8 mm<br />
0.40 ~ 0.55 mm<br />
0.1 ~ 0.4 mm<br />
Piston pin bore diameter Standard 22.0 mm<br />
Piston pin outer diameter Standard -<br />
Piston pin bore and piston pin clearance Standard -<br />
piston pin wear limit -<br />
Connecting rod and piston pin clearance Standard -<br />
Depressing force<br />
Depressing temperature<br />
Axial clearance of connecting rods<br />
CRANKSHAFT<br />
Axial clearance of crankshaft<br />
7500 ~ 17500 N<br />
Room temperature<br />
0.1 ~ 0.25 mm<br />
0.4 mm<br />
0.05 ~ 0.18 mm<br />
0.25 mm<br />
Clearacne between main journal and main bearing<br />
0.20 ~ 0.040 mm<br />
Main journal diameter Standard 56.982 ~ 57.000 mm<br />
CYLINDER BLOCK<br />
Upper surface flatness<br />
Upper surface grinding limit<br />
0.05 mm<br />
0.2 mm<br />
03-9<br />
Cylinder hole diameter<br />
Clearance between piston and cylinder Standard 0.020 ~ 0.04 mm<br />
Timing belt cover<br />
Down cover<br />
Middle cover<br />
Upper cover<br />
11<br />
18 ~ 26<br />
Crankshaft pulley (timing) 165<br />
Crankshaft pulley (damping) 25<br />
Rockshaft retaining bolt 31<br />
Valve - chamber cover bolt 4<br />
Camshaft thrust plate 19<br />
Oil pump driving shaft 55<br />
Camshaft pulley 90<br />
Cylinder head assy Step 1<br />
Step 2<br />
Step 3<br />
Connecting rod cap Step 1<br />
78<br />
20<br />
180°<br />
90° ~ 100°<br />
Rear engine block cover 11<br />
Flywheel bolt 135<br />
Crankshaft bearing cap 25<br />
03-10<br />
SERVICE SPECIFICATIONS - INTAKE AIR<br />
Compressor blade and compressor case clearance<br />
Minimum -<br />
Turbocharger rotor axial clearance<br />
Engine cover -<br />
Intake air pipe retaining bolt -<br />
Intake air filter cover bolt -<br />
Intake air filter assy 21 ~ 25<br />
Air straining box bolt -<br />
Air grille bolt -<br />
Intake air manifold bolt -<br />
Throttle body bolt 15 ~ 25<br />
Intake air filter assy -<br />
Exhaust manifold × Turbocharge -<br />
Exhaust pipe × Turbocharge -<br />
Turbocharge oil outlet pipe -<br />
Turbocharge oil inlet pipe -<br />
Intake air connect pipe × Intake manifold -<br />
Intake pipe × EGR -<br />
SERVICE SPECIFICATIONS - EXHAUST<br />
03-11<br />
Exhaust manifold and cylinder block cover flatnes<br />
Front exhaust pipe × Exhaust manifold 41 ~ 51<br />
Front exhaust pipe × Catalytic converter 41 ~ 51<br />
Middle exhaust pipe bolt 41 ~ 51<br />
Muffer × Rear exhaust pipe 41 ~ 51<br />
Exhaust manifold bolt 41 ~ 51<br />
Heat shield 10 ~ 14<br />
Exhaust pipe retaining belt bolt -<br />
Catalytic converter × Exhaust manifold 41 ~ 51<br />
Exhaust manifold bolt -<br />
Exhaust pipe × EGR -<br />
Heat shield -<br />
03-12<br />
SERVICE SPECIFICATIONS - COOLING<br />
Cooling system outlet temperature -<br />
Thermostat valve opening temperature 80 ~ 84 ℃<br />
Thermostat valve lift 8 mm ( At 95 ℃ )<br />
Coolant drain plug -<br />
Coolant filling pipe bolt -<br />
Fan cover upper support bolt 9 ~ 11<br />
Fan cover lower support bolt 9 ~ 11<br />
Coolant reservior bolt 21 ~ 25<br />
Thermostat housing bolt 21 ~ 25<br />
Cooling fan(electrical) bolt 9 ~ 11<br />
Water pump pulley bolt<br />
Gasoline<br />
Diesel<br />
14<br />
Water pump bolt 14<br />
SERVICE SPECIFICATIONS - LUBRICATION<br />
03-13<br />
Drain plug 34 ~ 45<br />
Oil pan 6 ~ 7<br />
Oil strainer bolt 19<br />
Oil filter 13 ~ 15<br />
Drain plug 35 ~ 45<br />
Oil pan -<br />
Oil filter bracket bolt -<br />
Oil pump -<br />
Oil filter 25 ~ 30<br />
Cooler pipe x Oil filter bracket -<br />
03-14<br />
SERVICE SPECIFICATIONS - IGNITION<br />
IGNITION<br />
Spark plug gap<br />
1.1 mm<br />
Spark plug 25<br />
Ignition coil 24<br />
SERVICE SPECIFICATIONS - STARTING AND CHARGING<br />
03-15<br />
Nominal voltage<br />
12 V<br />
Rated current -<br />
Rotation revolution -<br />
Power -<br />
Rotation mode<br />
Polarity<br />
Work mode<br />
Generator rotor coil resistance<br />
Generator rotor diameter<br />
clockwise<br />
Negative ground<br />
continuous rated type<br />
3 ± 0.5 Ω<br />
14.2 mm ~ 14.4 mm<br />
12.8 mm<br />
Pinion-to-stopper clearance Standard 0.5 mm ~ 2.0 mm<br />
Starter commutator run-out<br />
Starter commutator diameter<br />
≤ 0.05 mm<br />
0.10 mm<br />
29.4 mm<br />
28.4 mm<br />
Brush attrition value Limit 7.0 mm<br />
REGULATOR<br />
Type -<br />
Regulation voltage -<br />
Voltage -<br />
Output power -<br />
Direction of rotation -<br />
Battery rated voltage -<br />
03-16<br />
Regulator -<br />
Generator bracket bolt 20 ~ 24<br />
Generator retaining bolt 20 ~ 24<br />
Generator cable nut -<br />
Generator lock bolt 20 ~ 24<br />
Starter pulley bolt -<br />
Starter shell bolt 8 ~ 10<br />
Magnetic switch bolt 8 ~ 10<br />
Magnetic coil nut 14 ~ 16<br />
Starter × Battery cable 18 ~ 20<br />
Starter retaining bolt 68 ~ 72<br />
Battery plate × Body 16 ~ 18<br />
Battery hold down -<br />
Battery cable -<br />
FRONT WHEEL ALIGNMENT<br />
SERVICE SPECIFICATIONS - FRONT SUSPENSION<br />
Front toe-in 2±2 mm (8′±8′)<br />
03-17<br />
Front wheel camber -0°20′±45′ (Difference between left and right ≤ 30′)<br />
Kingpin inclination 13°05′±45′ (Difference between left and right ≤ 30′)<br />
Kingpin caster 2°35′±45′ (Difference between left and right ≤ 30′)<br />
Front shock absorber × Body 30<br />
Front shock absorber × Lower control arm assy 80 ~ 90<br />
Torsion bar × Frame<br />
Rating nut<br />
Locking nut<br />
75 ~ 85<br />
120 ~ 130<br />
Upper control arm assy × Frame 170 ~ 200<br />
Upper control arm ball joint × Upper control arm assy 110 ~ 115<br />
Upper control arm assy × Torsion bar 100 ~ 110<br />
Lower control arm assy × Frame 180 ~ 220<br />
Lower control arm ball joint × Lower control arm assy 110 ~ 120<br />
Stabilizer bar link × Stabilizer bar 40 ~ 60<br />
Stabilizer bar bracket × Frame 110 ~ 130<br />
Strut rod × Lower control arm assy 110 ~ 120<br />
Strut rod × Frame 105 ~ 125<br />
03-18<br />
SERVICE SPECIFICATIONS - REAR SUSPENSION<br />
Rear shock absorber × Anchor plate 60 ~ 80<br />
Rear shock absorber × Frame 55 ~ 65<br />
Shackle pin upper bolt 110 ~ 115<br />
Shackle pin lower bolt 125 ~ 130<br />
Leaf spring pin nut 110 ~ 120<br />
U-bolt nut 85 ~ 105<br />
TIRE PRESSURE<br />
SERVICE SPECIFICATIONS - TIRE AND WHEEL<br />
03-19<br />
195R15C-104S<br />
Front tire<br />
Rear tire<br />
Spare tire<br />
350 KPa<br />
400 KPa<br />
420 KPa<br />
Wheel nut 90 ~ 120<br />
03-20<br />
SERVICE SPECIFICATIONS - AXLE AND PROPELLER SHAFT<br />
PROPELLER ASSY<br />
Propeller tube outer diameter × Thickness<br />
φ 63.5 ×2.5 mm<br />
Operating torque Maximum 1600 N·m<br />
Angle without interference Maximum -<br />
Dynamic unbalance Maximum 20 g.cm (3200 r/min)<br />
Propeller radial run-out<br />
0.3 mm<br />
Clearance between tube yoke and transmission output<br />
shaft spline<br />
Cross spider journal<br />
Clearance between needle bearing and yoke<br />
0 mm (Interferencefit)<br />
Clearance between cross spider and needle bearing -<br />
Axial clearance of cross spider -<br />
AXLE HUB<br />
Back lash<br />
Deviation<br />
Primal rotating force<br />
REAR AXLE<br />
Rear wheel track<br />
Front<br />
Rear<br />
1650 mm<br />
Back lash -<br />
Number of drive pinion teeth 10<br />
Number of crown gear teeth 39<br />
Final ratio 3.9<br />
DIFFERENTIAL ASSY<br />
Crown gear deviation -<br />
Crown gear back lash -<br />
03-21<br />
Contact area between drive pinion and crown gear<br />
Length<br />
Width<br />
Center of the tooth surface. The distance away from<br />
small end ≥ 2 mm<br />
≥ 60% tooth length<br />
≥ 60% tooth width<br />
Drive axle side gear and pinion back lash -<br />
Drive axle side gear clearance -<br />
Radial clearance between differential pinion and pinion<br />
shaft<br />
Radial clearance between drive axle side gear and differential<br />
case<br />
Thickness of drive axle side gear thrust washer<br />
Thickness of differential pinion thrust washer<br />
Pinion flange back lash -<br />
Pinion flange deviation -<br />
Drive pinion primal rotating force -<br />
Final drive pinion flange × Propeller shaft 70 ~ 79<br />
Center support bearing bracket × Frame 60 ~ 70<br />
End yoke retaining bolt -<br />
Front axle hub × Front brake disc 50 ~ 60<br />
Rear wheel brake cylinder × brake tube 21 ~ 24<br />
Steering knuckle × Upper control arm joint 110 ~ 115<br />
Steering knuckle × Lower control arm assy 110 ~ 115<br />
Lower control arm joint × Lower control arm 110 ~ 120<br />
Tie rod × Steering knuckle arm 84 ~ 100<br />
Final drive drain plug -<br />
Final drive filler cap -<br />
Final drive vent plug -<br />
Main retard assy × Final drive assy -<br />
Crown gear × Differential case -<br />
03-22<br />
Differential bearing cap × Differential case -<br />
Pinion nut<br />
Minimum<br />
Increment<br />
Maximum<br />
13<br />
SERVICE SPECIFICATIONS - BRAKE<br />
03-23<br />
BRAKE PEDAL<br />
Height Standard 148 mm<br />
Free play Standard 5 ~ 10 mm<br />
FRONT BRAKE<br />
Thickness of front brake pad<br />
Thickness of front brake disk<br />
Front brake disk run-out<br />
REAR BRAKE<br />
Thickness of rear brake shoe<br />
Brake drum inside diameter<br />
Clearance between rear brake drum and brake shoe<br />
16 ~ 16.1 mm<br />
8 mm<br />
28 ± 0.1 mm<br />
0.03 mm<br />
5 mm<br />
1.5 mm<br />
254 ~ 254.2 mm<br />
Front disk brake caliper bleeding plug 8 ~ 13<br />
Rear wheel brake cylinder bleeding plug 9 ~ 11<br />
Brake master cylinder bolt 20 ~ 26<br />
Brake master cylinder tube connector 21 ~ 24<br />
Front brake disk x front wheel hub 50 ~ 70<br />
Front wheel hub x knuckle 85 ~ 120<br />
Front disk brake caliper mounting bolt 30 ~ 35<br />
Front disk brake caliper bolt 90 ~ 110<br />
Front disk brake caliper fluid tube connector 21 ~ 24<br />
Rear wheel cylinder brake fluid tube connector 21 ~ 24<br />
Rear wheel brake cylinder assy 8 ~ 13<br />
Speed sensor -<br />
ABS pipe connector 21 ~ 24<br />
03-24<br />
SERVICE SPECIFICATIONS - PARKING BRAKE<br />
Parking brake front part assy -<br />
Parking brake swinging arm bracket -<br />
Transmission fluid<br />
SERVICE SPECIFICATIONS - TRANSMISSION<br />
Zomax<br />
Aisin<br />
2.0 L<br />
2.4 L<br />
03-25<br />
1st gear ratio<br />
2nd gear ratio<br />
4.452<br />
3.83<br />
2.398<br />
2.33<br />
3rd gear ratio<br />
1.414<br />
1.436<br />
4th gear ratio 1.000<br />
5th gear ratio<br />
Reverse gear ratio<br />
0.802<br />
0.789<br />
4.473<br />
4.22<br />
Odometer gear ratio (Driven gear / driving gear) Zomax<br />
19/6<br />
32/10<br />
Input shaft gear bearing axial clearance<br />
Output shaft radial run-out<br />
Output shaft journal<br />
A<br />
B<br />
C<br />
D<br />
Axial clearance between od-r synchronizer ring and<br />
gear<br />
Axial clearance between 4th synchronizer ring and<br />
Axial clearance between 3rd synchronizer ring and<br />
Axial clearance between 2nd synchronizer ring and<br />
Axial clearance between 1st synchronizer ring and<br />
Radial clearance between 1st synchronizer ring and<br />
1.0 ~ 1.6 mm<br />
1.0 ~ 2.0 mm<br />
03-26<br />
Clearance between od-r synchronizer sleeve and<br />
gearshift fork<br />
Clearance between 3rd-4th synchronizer sleeve and<br />
Clearance between 1st-2nd synchronizer sleeve and<br />
Drain plug<br />
35 ~ 45<br />
29.8 ~ 44.6<br />
Transmission operation mechanism × Body -<br />
Transmission lifting lug × Transmission 41 ~ 51<br />
Transmission assy × Engine<br />
42.2 ~ 53.9<br />
78 ~ 96 (M6 × 1.25)<br />
45 ~ 55 (M6 × 1.25)<br />
Odometer sensor × Transmission assy -<br />
Backup lamp switch × Transmission assy -<br />
Gear shift connecting rod × Transmission assy 22 ~ 28<br />
Gear select connecting rod × Transmission assy 22 ~ 28<br />
Filler cap<br />
Front bearing retainer × Transmission assy<br />
17 ~ 22<br />
Output shaft rear bearing baffle × Transmission assy<br />
Reverse idler gear shaft plate × Transmission assy<br />
15 ~ 20<br />
Lever housing assy × Transmission assy 14 ~ 26<br />
Extension housing sub-assy × Transmission assy 26 ~ 48<br />
Clutch housing × Transmission assy 16 ~ 21<br />
SERVICE SPECIFICATIONS - CLUTCH<br />
03-27<br />
CLUTCH PEDAL<br />
Height Standard 165 mm<br />
Push rod play Standard 26.4 mm<br />
Clutch disk thickness<br />
Width of diaphragm spring<br />
Height of diaphragm spring<br />
Clutch disk run-out<br />
Flywheel run-out<br />
Limit -<br />
Bleeding plug -<br />
Clutch pedal lock nut 17 ~ 21<br />
Clutch pedal pin nut -<br />
Clutch master cylinder nut 20 ~ 26<br />
Clutch master cylinder fluid tube connector 21 ~ 24<br />
Clutch slave cylinder fluid tube connector 21 ~ 24<br />
Clutch slave cylinder bolt -<br />
Clutch cover bolt 25<br />
03-28<br />
VEHICLE<br />
SERVICE SPECIFICATIONS - STEERING COLUMN<br />
Steering radius Minimum 5.75 m<br />
Off track (30 m,40 Km/h)<br />
STEERING WHEEL<br />
Left<br />
Right<br />
< 2 m<br />
< 1 m<br />
Diameter -<br />
Free play ± 15°<br />
Turning force<br />
Engine stopped<br />
< 200 N<br />
< 45 N<br />
Clearance between cross spider and bearing<br />
≤ 0.15 mm<br />
Steering wheel nut 40 ~ 50<br />
Steering column assy 29 ~ 35<br />
Main retard assy 29 ~ 35<br />
Steering propeller shaft assy × Steering column assy 29 ~ 35<br />
Steering propeller shaft assy × Steering box 29 ~ 35<br />
Steering box 108 ~ 125<br />
SERVICE SPECIFICATIONS - POWER STEERING<br />
03-29<br />
STEERING PUMP BELT<br />
Deflection 5.5 ~ 8.5 mm (98 N)<br />
STEERING FLUID<br />
Operating temperature - 40 ~ 120 ℃<br />
Pressure<br />
Engine idling, valve closed<br />
Engine idling, valve open, steering wheel at lock position<br />
10±0.5 MPa<br />
≤ 10.5 Mpa<br />
Pressure difference<br />
Vavle open, engine running at 1000 and 3000 r/min -<br />
STEERING BOX<br />
Weight -<br />
Number of rack teeth -<br />
Number of pinion teeth -<br />
Module -<br />
Gear ratio -<br />
Rotating angle of rack shaft -<br />
Gross rotating turn of pinion -<br />
Pitch circle of pinion -<br />
Radial run-out of rack -<br />
03-30<br />
Power steering line connector -<br />
Steering box 108 ~ 128<br />
Steering box × Steering propeller shaft assy 29 ~ 35<br />
Steering tie rod × Steering knuckle arm 84 ~ 100<br />
SERVICE SPECIFICATIONS - HEATER AND AIR CONDITIONING<br />
AMOUNT OF COMPRESSOR OIL<br />
03-31<br />
Replace compressor<br />
Replace all pipes<br />
Replace evaporator<br />
Compressor has 180 ml oil, no need added<br />
40 ~ 60 ml<br />
10 ml<br />
Replace condenser<br />
Replace pipes<br />
Gas leakage<br />
Pressure of low side<br />
Pressure of high side<br />
No leakage<br />
Leakage<br />
ON<br />
OFF<br />
5 ml<br />
No need added<br />
80 ml<br />
0.15 ~ 0.25 MPa<br />
1.37 ~ 2.37 MPa<br />
Φ9 aluminium tube, M16×1.5 thread 12 ~ 15<br />
Φ12 aluminium tube, M22×1.5 thread 20 ~ 26<br />
Φ16 aluminium tube, M24×1.5 thread 30 ~ 35<br />
Front evaporator and heater assy bolt -<br />
03-32<br />
SERVICE SPECIFICATIONS - SEAT BELT<br />
Driver / assistant driver seat retractor × Body 50 ~ 55<br />
Driver / assistant driver seat belt lower anchor × Body 50 ~ 55<br />
SERVICE SPECIFICATIONS - LIGHTING<br />
03-33<br />
LIGHTING<br />
Front combination lamp × Frame 2 ~ 3<br />
Rear combination lamp × Frame 2 ~ 3<br />
03-34<br />
SERVICE SPECIFICATIONS - WIPER AND WASHER<br />
Front wiper assy nut -<br />
Rear wiper assy nut -<br />
Front wiper motor with link assy bolt 6 ~ 8<br />
Rear wiper motor with link assy bolt 6 ~ 8<br />
SERVICE SPECIFICATIONS - SEAT<br />
03-35<br />
Driver seat assy bolt 45 ~ 55<br />
Assistant driver seat assy bolt 45 ~ 55<br />
Passenger seat assy bolt 45 ~ 55<br />
03-36<br />
SERVICE SPECIFICATIONS - DOORS<br />
FRONT DOOR<br />
Flatness<br />
SLIDING DOOR<br />
REAR HATCH<br />
Up<br />
From up to down of A pillar<br />
Other<br />
Down<br />
5.5 mm<br />
-2 ~ 0 mm<br />
0 mm<br />
6 mm<br />
10 mm<br />
Flatness -<br />
Front door hinge bolt 28 ~ 32<br />
Front door lock catch screw 28 ~ 32<br />
Sliding door hinge bolt 28 ~ 32<br />
Sliding door concave limiting device bolt 28 ~ 32<br />
Rear hatch bolt 28 ~ 32<br />
Rear hatch concave limiting device bolt 28 ~ 32<br />
SERVICE SPECIFICATIONS - EXTERIOR AND INTERIOR TRIM<br />
EXTERIOR AND INTERIOR TRIM<br />
Sunvisor hook bolt 6 ~ 8<br />
Floor trim strip screw 6 ~ 8<br />
Front bumper assy bolt 6 ~ 8<br />
Rear bumper assy bolt 6 ~ 8<br />
Front wiper bolt 6 ~ 8<br />
03-37<br />
03-38<br />
SERVICE SPECIFICATIONS - VEHICLE CONTROL SYSTEM<br />
Ignition switch assy bolt -<br />
ENGINE CONTROL SYSTEM............................................................ 04-1<br />
PRECAUTION.............................................................................. 04-1<br />
LOCATION................................................................................... 04-4<br />
HOW TO DIAGNOSTICS ANALYSE........................................... 04-6<br />
DIAGNOSTIC HELP - INTERMITTENT FAULT .......................... 04-9<br />
BASIC SERVICE PROCEDURE................................................ 04-11<br />
TERMINALS OF ECM................................................................ 04-12<br />
DIAGNOSTIC SYSTEM............................................................. 04-17<br />
READING AND ERASING DIAGNOSTIC<br />
TROUBLE CODE (DTC)........................................................... 04-19<br />
CAPTURING DATA ................................................................... 04-21<br />
FAIL - SAFE CHART.................................................................. 04-22<br />
DATA STREAM LIST/ACTIVE TEST......................................... 04-24<br />
DIAGNOSTIC TROUBLE CODE CHART.................................. 04-28<br />
DTC DIAGNOSTIC .................................................................... 04-33<br />
PROBLEM SYMPTOMS TABLE................................................ 04-60<br />
ENGINE SYMPTOM DIAGNOSTIC........................................... 04-61<br />
ANTI - LOCK BRAKE SYSTEM....................................................... 04-98<br />
PRECAUTION............................................................................ 04-98<br />
LOCATION............................................................................... 04-100<br />
ABS MODULE CONNECTOR ................................................. 04-101<br />
DIAGNOSTIC TROUBLE CODE CHART................................ 04-102<br />
PROBLEM SYMPTOMS TABLE.............................................. 04-104<br />
PRE - CHECK.......................................................................... 04-105<br />
POWER SUPPY VOLTAGE HIGH OR LOW........................... 04-107<br />
SOLENOID VALVES AND VALVES RELAY FAILURE........... 04-108<br />
PUMP MOTOR FAILURE ........................................................ 04-112<br />
WHEEL SPEED SENSOR SIGNAL FAULT ............................ 04-118<br />
ABS CONTROL IS UNREASONABLE .................................... 04-122<br />
ABS SYSTEM IS INOPERATIVE............................................. 04-125<br />
SUPPLEMENTAL RESTRAINT SYSTEM ..................................... 04-129<br />
PRECAUTION.......................................................................... 04-129<br />
LOCATION............................................................................... 04-130<br />
RESTRAINT CONTROL MODULE (RCM)<br />
CONNECTOR PIN................................................................... 04-131<br />
DIAGNOSTIC TROUBLE CODE CHART................................ 04-133<br />
PROBLEM SYMPTOMS TABLE.............................................. 04-134<br />
8102 - POWER SUPPLY VOLTAGE LOW.............................. 04-135<br />
8201 - DRIVER AIRBAG FAULT - HIGH RESISTANCE ......... 04-139<br />
8202 - DRIVER AIRBAG FAULT - LOW RESISTANCE.......... 04-139<br />
8203 - DRIVER AIRBAG CIRCUIT SHORT TO GROUND...... 04-141<br />
8211 - CO - PILOT SIDE AIRBAG FAULT - HIGH<br />
RESISTANCE .......................................................................... 04-145<br />
8212 - CO - PILOT SIDE AIRBAG FAULT - LOW<br />
RESISTANCE ......................................................................... 04-145<br />
8213 - CO - PILOT SIDE AIRBAG CIRCUIT<br />
SHORT TO GROUND.............................................................. 04-148<br />
8214 - CO - PILOT SIDE AIRBAG CIRCUIT<br />
SHORT TO BATTERY............................................................. 04-150<br />
SRS WARNING LIGHT IS INOPERATIVE .............................. 04-154<br />
04<br />
HEATER AND AIR CONDITIONING SYSTEM.............................. 04-156<br />
PRECAUTION.......................................................................... 04-156<br />
BASIC INSPECTION ............................................................... 04-157<br />
LOCATION............................................................................... 04-158<br />
PROBLEM SYMPTOMS TABLE.............................................. 04-159<br />
A/C SYSTEM IS INOPERATIVE.............................................. 04-162<br />
FRONT BLOWER MOTOR IS INOPERATIVE ........................ 04-166<br />
REAR EVAPORATOR MOTORS ARE INOPERATIVE........... 04-172<br />
FRONT AIR FLOW IS INSUFFICIENT .................................... 04-178<br />
REAR AIR FLOW IS INSUFFICIENT....................................... 04-182<br />
NO COOLING FROM FRONT A/C SYSTEM .......................... 04-184<br />
NO COOLING FROM REAR A/C SYSTEM............................. 04-191<br />
REAR HEATER IS INOPERATIVE OR<br />
INSUFFICIENT HEATING ....................................................... 04-195<br />
LIGHTING SYSTEM ....................................................................... 04-202<br />
PRECAUTION.......................................................................... 04-202<br />
BASIC INSPECTION ............................................................... 04-203<br />
LOCATION............................................................................... 04-204<br />
PROBLEM SYMPTOMS TABLE.............................................. 04-206<br />
LO - BEAM HEADLAMP IS INOPERATIVE (ONE SIDE) ........ 04-212<br />
HI - BEAM HEADLAMP IS INOPERATIVE (ONE SIDE) ......... 04-218<br />
HI - BEAM HEADLAMPS ARE INOPERATIVE<br />
(BOTH SIDES) ........................................................................ 04-220<br />
LO - BEAM AND HI - BEAM HEADLAMPS ARE<br />
INOPERATIVE (ONE SIDE) .................................................... 04-224<br />
ALL HEADLAMPS ARE INOPERATIVE .................................. 04-227<br />
FRONT FOG LAMPS ARE INOPERATIVE ............................. 04-233<br />
FRONT FOG LAMPS ARE ALWAYS ON ................................ 04-238<br />
REAR FOG LAMPS ARE INOPERATIVE................................ 04-241<br />
REAR FOG LAMPS ARE ALWAYS ON .................................. 04-246<br />
ALL FOG LAMPS ARE INOPERATIVE ................................... 04-249<br />
HAZARD WARNING LAMPS ARE INOPERATIVE (TURN SIGNAL<br />
LAMPS ARE NORMAL) ........................................................... 04-256<br />
TURN SIGNAL LAMPS ARE INOPERATIVE (HAZARD WARNING<br />
LAMPS ARE NORMAL) ........................................................... 04-260<br />
HAZARD WARNING AND TURN SIGNAL LAMPS ARE INOPERA-<br />
TIVE ......................................................................................... 04-264<br />
TURN SIGNAL LAMPS ARE INOPERATIVE (ONE SIDE)...... 04-272<br />
HAZARD WARNING LAMPS ARE ALWAYS ON .................... 04-275<br />
ALL STOP LAMPS ARE INOPERATIVE ................................. 04-277<br />
STOP LAMP IS INOPERATIVE (ONE SIDE) .......................... 04-282<br />
HIGH - MOUNTED STOP LAMP IS INOPERATIVE................ 04-284<br />
BACK - UP LAMP IS INOPERATIVE(ONE SIDE) ................... 04-286<br />
BACK - UP LAMPS ARE INOPERATIVE (BOTH SIDES) ....... 04-288<br />
IGNITION SWITCH ILLUMINATION IS INOPERATIVE .......... 04-293<br />
CENTRAL DOME LIGHT IS INOPERATIVE ........................... 04-296<br />
AIR PURIFIER LAMP IS INOPERATIVE ................................. 04-301<br />
STEP LAMP ARE INOPERATIVE ........................................... 04-304<br />
TRUNK LAMP IS INOPERATIVE ............................................ 04-307<br />
FRONT DOME LIGHT IS INOPERATIVE................................ 04-310<br />
ALL INTERIOR ILLUMINATION LAMPS ARE<br />
INOPERATIVE ........................................................................ 04-314<br />
INSTRUMENT CLUSTER ILLUMINATION IS<br />
NOT INOPERATIVE ................................................................ 04-319<br />
DIAGNOSIS SWITCH ILLUMINATION IS<br />
NOT INOPERATIVE ................................................................ 04-322<br />
CIGARETTE LIGHTER ILLUMINATION IS<br />
NOT INOPERATIVE ............................................................... 04-324<br />
A/C CONTROL PANEL ILLUMINATION IS<br />
NOT INOPERATIVE ................................................................ 04-326<br />
RADIO ILLUMINATION IS NOT INOPERATIVE ..................... 04-328<br />
REAR BLOWER FORWARD SWITCH ILLUMINATION IS<br />
NOT INOPERATIVE ................................................................ 04-330<br />
DOME LIGHT SWITCH ILLUMINATION IS<br />
NOT INOPERATIVE ............................................................... 04-332<br />
OUTSIDE MIRROR DEFROSTER SWITCH ILLUMINATION IS<br />
NOT INOPERATIVE ................................................................ 04-334<br />
HEADLAMP DIMMER SWITCH ILLUMINATION IS<br />
NOT INOPERATIVE ............................................................... 04-336<br />
REAR WINDOW DEFROSTER SWITCH ILLUMINATION IS<br />
NOT INOPERATIVE ................................................................ 04-338<br />
INSTRUMENT DIMMER SWITCH ILLUMINATION IS<br />
NOT INOPERATIVE ............................................................... 04-340<br />
HAZARD WARNING SWITCH ILLUMINATION IS<br />
NOT INOPERATIVE ............................................................... 04-342<br />
WIDTH LAMPS IS NOT INOPERATIVE.................................. 04-344<br />
TAIL LAMPS ARE INOPERATIVE........................................... 04-347<br />
LICENSE LAMP IS INOPERATIVE ......................................... 04-350<br />
WIDTH LAMPS TAIL LAMPS AND LICENSE<br />
LAMP ARE INOPERATIVE..................................................... 04-352<br />
WIPER AND WASHER .................................................................. 04-356<br />
PRECAUTION.......................................................................... 04-356<br />
LOCATION............................................................................... 04-357<br />
BASIC INSPECTION ............................................................... 04-358<br />
PROBLEM SYMPTOMS TABLE.............................................. 04-359<br />
WIPERS ARE INOPERATIVE - WINDSHIELD........................ 04-361<br />
WIPERS ARE INOPERATIVE AT<br />
LOW SPEED - WINDSHIELD.................................................. 04-367<br />
HIGH SPEED - WINDSHIELD ................................................ 04-369<br />
WIPERS ARE INOPERATIVE IN INTERMITTENT MODE - WIND-<br />
SHIELD .................................................................................... 04-371<br />
WASHER PUMP IS INOPERATIVE - WINDSHIELD............... 04-374<br />
WHEN THE WIPER SWITCH IS OFF, THE WIPER BLADE DOES<br />
NOT RETRACT........................................................................ 04-378<br />
WIPER IS INOPERATIVE - REAR WINDOW.......................... 04-381<br />
WASHER PUMP IS INOPERATIVE - REAR WINDOW .......... 04-387<br />
AUDIO SYSTEM............................................................................. 04-392<br />
PRECAUTION.......................................................................... 04-392<br />
LOCATION............................................................................... 04-393<br />
BASIC INSPECTION ............................................................... 04-394<br />
PROBLEM SYMPTOMS TABLE.............................................. 04-395<br />
RADIO DOES NOT WORK...................................................... 04-396<br />
RADIO RECEPTION IS POOR................................................ 04-400<br />
POOR SOUND QUALITY....................................................... 04-401<br />
SPEAKER DOES NOT WORK ................................................ 04-402<br />
AUXILIARY POWER...................................................................... 04-406<br />
LOCATION............................................................................... 04-406<br />
PROBLEM SYMPTOMS TABLE.............................................. 04-407<br />
CIGARETTE LIGHTER IS INOPERATIVE .............................. 04-408<br />
INSPECTION PROCEDURE ................................................... 04-409<br />
12V POWER SUPPLY OUTPUT SOCKET IS<br />
INOPERATIVE ......................................................................... 04-411<br />
HORN SYSTEM.............................................................................. 04-415<br />
LOCATION............................................................................... 04-415<br />
PROBLEM SYMPTOMS TABLE.............................................. 04-416<br />
HORN IS INOPERATIVE ......................................................... 04-417<br />
INSPECTION PROCEDURE ................................................... 04-418<br />
HORN IS ALWAYS ON............................................................ 04-422<br />
REVERSE RADAR SYSTEM ......................................................... 04-424<br />
PRECAUTION.......................................................................... 04-424<br />
LOCATION............................................................................... 04-425<br />
SYSTEM DESCRIPTION......................................................... 04-426<br />
PROBLEM SYMPTOMS TABLE.............................................. 04-428<br />
REVERSE RADAR SYSTEM IS INOPERATIVE AT ALL ........ 04-429<br />
REVERSE RADAR SYSTEM IS OPERATIVE WHEN THE SHIFT LE-<br />
VER IS OUT OF REVERSE POSITION .................................. 04-434<br />
REVERSE RADAR SYSTEM IS INOPERATIVE WITHIN SPECIFIED<br />
DISTANCE (BACK - UP LAMP IS NORMAL) ......................... 04-436<br />
REVERSE RADAR SYSTEM IS OPERATIVE BUT THERE IS NO<br />
OBSTACLE BEHIND VEHICLE ............................................... 04-439<br />
BUZZER IS INOPERATIVE OR OPERATIVE INCORRECTLY WITH-<br />
IN SPECIFIED DISTANCE (DISPLAYER IS NORMAL) .......... 04-442<br />
DISPLAYER IS INOPERATIVE WITHIN SPECIFIED DISTANCE<br />
(BUZZER IS NORMAL)............................................................ 04-445<br />
POWER WINDOWS ....................................................................... 04-448<br />
PRECAUTION.......................................................................... 04-448<br />
LOCATION............................................................................... 04-449<br />
DOOR CONTROL SWITCH PIN.............................................. 04-450<br />
WINDOW CONTROL SWITCH RH PIN .................................. 04-451<br />
CENTRAL LOCKING CONTROLLER ASSY A PIN................. 04-452<br />
BASIC INSPECTION ............................................................. 04-453<br />
PROBLEM SYMPTOMS TABLE.............................................. 04-454<br />
ALL POWER WINDOWS ARE INOPERATIVE ....................... 04-456<br />
FRONT POWER WINDOW LH IS INOPERATIVE .................. 04-461<br />
FRONT POWER WINDOW LH DOES NOT OPEN................. 04-464<br />
FRONT POWER WINDOW LH DOES NOT CLOSE............... 04-466<br />
FRONT POWER WINDOW RH IS INOPERATIVE (USE DOOR CON-<br />
TROL SWITCH) ....................................................................... 04-468<br />
FRONT POWER WINDOW RH IS INOPERATIVE (USE WINDOW<br />
CONTROL SWITCH RH) ......................................................... 04-470<br />
OUTSIDE MIRROR ........................................................................ 04-473<br />
LOCATION............................................................................... 04-473<br />
TERMINALS OF OUTSIDE MIRROR SWITCH....................... 04-474<br />
BASIC INSPECTION ............................................................... 04-475<br />
PROBLEM SYMPTOMS TABLE.............................................. 04-476<br />
MIRRORS ARE INOPERATIVE (BOTH SIDES) ..................... 04-477<br />
A SINGLE MIRROR IS INOPERATIVE ................................... 04-480<br />
MIRROR ADJUSTMENT UP/DOWN IS INOPERATIVE ......... 04-483<br />
MIRROR ADJUSTMENT LEFT/RIGHT IS INOPERATIVE...... 04-485<br />
DEFROSTER SYSTEM .................................................................. 04-487<br />
LOCATION............................................................................... 04-487<br />
SYSTEM DESCRIPTION......................................................... 04-489<br />
BASIC INSPECTION ............................................................... 04-490<br />
PROBLEM SYMPTOMS TABLE.............................................. 04-491<br />
REAR WINDOW DEFROSTER IS INOPERATIVE................. 04-492<br />
OUTSIDE MIRROR DEFROSTER IS INOPERATIVE............ 04-497<br />
INSTRUMENT CLUSTER .............................................................. 04-502<br />
PRECAUTION.......................................................................... 04-502<br />
LOCATION............................................................................... 04-503<br />
INSTRUMENT CLUSTER INFORMATION.............................. 04-504<br />
TERMINALS OF INSTRUMENT CLUSTER ............................ 04-507<br />
BASIC INSPECTION ............................................................... 04-510<br />
PROBLEM SYMPTOMS TABLE.............................................. 04-511<br />
MALFUNCTION IN SPEEDOMETER...................................... 04-513<br />
MALFUNCTION IN TACHOMETER ........................................ 04-515<br />
MALFUCTION IN FUEL GAUGE / LOW FUEL WARNING LIGHT<br />
NEVER OR ALWAYS ON........................................................ 04-517<br />
MALFUCTION IN ENGINE COOLANT<br />
TEMPERATURE GAUGE........................................................ 04-520<br />
ENGINE OIL PRESSURE WARNING LIGHT<br />
NEVER / ALWAYS ON ........................................................... 04-523<br />
SEAT BELT WARNING LIGHT<br />
NEVER / ALWAYS ON ........................................................... 04-526<br />
PARKING BRAKE INDICATOR LIGHT<br />
NEVER / ALWAYS ON ........................................................... 04-530<br />
POWER DOOR LOCKS................................................................. 04-533<br />
PRECAUTION.......................................................................... 04-533<br />
LOCATION............................................................................... 04-534<br />
CENTRAL LOCKING CONTROLLER ASSY A........................ 04-535<br />
CENTRAL LOCKING CONTROLLER ASSY B........................ 04-536<br />
BASIC INSPECTION ............................................................... 04-537<br />
PROBLEM SYMPTOMS TABLE.............................................. 04-538<br />
THE FUNCTION OF POWER DOOR LOCKS IS<br />
INOPERATIVE (USING THE KEY).......................................... 04-539<br />
ONE DOOR IS INOPERATIVE (USING THE KEY)................. 04-543<br />
DOOR DOES NOT OPEN / CLOSE (USING<br />
THE REMOTE KEY) ................................................................ 04-545<br />
SLIDING ROOF SYSTEM .............................................................. 04-548<br />
LOCATION............................................................................... 04-548<br />
SYSTEM DESCRIPTION......................................................... 04-549<br />
TERMINALS OF MAIN COMPONENTS.................................. 04-550<br />
BASIC INSPECTION ............................................................... 04-551<br />
PROBLEM SYMPTOMS TABLE.............................................. 04-552<br />
SLIDING ROOF SYSTEM IS INOPERATIVE.......................... 04-553<br />
1. POWER OFF.<br />
DIAGNOSTICS - ENGINE CONTROL SYSTEM<br />
04-1<br />
• The battery negative cable must be disconnected first before removing or installing any electric<br />
appliance and when tools or facilities will touch the exposed terminals. It should be connected<br />
eventually. This will prevent person injured and vehicle damaged.<br />
• The ignition switch must be OFF without any special descriptions.<br />
The ignition and illuminatioin switches must be OFF before disconnecting or connecting the battery<br />
negative cable (the semiconductor maybe damaged without doing that).<br />
Do not leave the key in the vehicle in case the doores are locked before disconnecting the battery negative<br />
cable for the vehicle equipped with remote control central lock.<br />
2. RESET THE ODOMETER AND CLOCK IF DISCONNECTING THE COMBINATION INSTRUMENT<br />
BATTERY NEGATIVE CABLE.<br />
The total course will not be reset.<br />
3. THE SAVING DATA SETTING WILL LOST IF DISCONNECTING THE BATTERY NEGATIVE CABLE.<br />
After connecting the battery negative cable, the audio system shoud be reset.<br />
4. EXPRESSIONS OF IGNITION SWITCH<br />
Switch Type Ignition Switch (position) Ignition Switch (condition)<br />
Ignition switch off LOCK Off<br />
Expression<br />
Ignition switch on (IG) ON On (IG)<br />
Ignition switch on (ACC) ACC On (ACC)<br />
Engine start START Start<br />
5. PRECAUTIONS FOR OVERHAULING THE ENGINE CONTROL SYSTEM FAILURE.<br />
(a) Do not disconnect power circuit while engine is running at high speed in case the instantaneous overvoltage<br />
damage the ECM and sensors.<br />
(b) The ECM should be disconnected when welding on the vehicle body. It is special attention that performing<br />
the repair work beside the ECM or sensors.<br />
(c) The system will resume its normal state temporarily or competely by removing and reinstalling the suspicious<br />
faulty components when the connector terminals or the installing state of the components go<br />
out of order.<br />
(d) The high impedance type multimeter should be used to the test except the especial description of the<br />
procedure in place of the traditional analogue types multimeter.<br />
(e) Don’t check any electric appliance connecting the ECM with a test light.<br />
(f) Never connect the negative and positive battery cables wrong. The battery negative cable must be<br />
grounded.<br />
04-2<br />
(g) ECM and sensors must be kept from moisture. No permission damaging the seal device of ECM and<br />
sensors and washing them more.<br />
(h) Prevent human body static electricity from damaging ECM: The operator body must be grounded when<br />
operator checks ECM or replace chips.<br />
(i) In order to identifying the faulty position, we must check the vehicle condition while vehicle goes out of<br />
order. For example, we check the faults through the DTC. We record these faults states before<br />
disconnecting every connector or removing and installing components.<br />
(j) We must remove and install ECM, actuators and independent sensors when the ignition switch is OFF<br />
unless there is additional specification in the checking procedure.<br />
(k) If the removed and installed ECM, actuators and sensors are to be reinstalled, the system should be<br />
checked after completing installation. Using the special diagnosis tool to check DTC.<br />
(l) Check the ECM connector terminals with a multimeter.<br />
• Connect the small probing pin to the probe of a multimeter.<br />
• Check voltage value of terminals referring to the inspection sheet by back probing ECM connectors<br />
(m) When diagnosis, the ignition switch turns “ON” and the connectors are disconnected. DTC of the other<br />
system will be set. After diagnosis, confirm DTC in all systems.Turn the ignition switch “LOCK” when<br />
the connectors are connected and disconnected.<br />
(n) The test probe must not be probed in wire harness. This will reduce the waterproofness. And it also<br />
cause corrossion. Using the test wire, wire connector, measure wire harness and so on.<br />
(o) Check the common connectors when they are in connection status by probing terminals in the wire<br />
harness. If the connector is too small to check, do not force inserting.<br />
(p) If check the common connectors when they are not in connection status (check male connectors):<br />
• Do not short terminals circuit by using a probe. This will damage the interior circuit in ECM.<br />
• The system to be checked and other system will store DTC when they aren’t in connecting status.<br />
(q) If check the common connectors when they are not in connection status (check female connectors):<br />
• Use the special tools to check wire harness.<br />
(r) We shall have a short harness or connectors without taking cautions by wrong insertion. This will<br />
damage wire harness, sensor, ECM and other components So we must carefully handle when<br />
checking.<br />
(s) Do not check with the list order.<br />
• If the check results are different from the standard value, then check related sensors, actuators and<br />
wire harness. Repair or replace if necessary.<br />
• Check with the voltage meter again after repairing or replacing. Confirm if the faults have been<br />
eliminated.<br />
(t) Check resistance and continuity between terminals of ECM with multimeter.<br />
• Ignition switch: OFF<br />
• Disconnect ECM harness connector.<br />
(u) Ground inspection.<br />
• Ground connections are very important to the proper operation of electrical and electronic circuits.<br />
Ground connections are often exposed to moisture, dirt and other corrosive elements. The corrosion<br />
(rust) can become an unwanted resistance. This unwanted resistance can change the way a circuit<br />
works.<br />
• Electronically controlled circuits are very sensitive to proper grounding. A loose or corroded ground can<br />
drastically affect an electronically controlled circuit. A poor or corroded ground can easily affect the<br />
circuit. Even when the ground connection looks clean, there can be a thin film of rust on the surface.<br />
• When inspecting a ground connection follow these rules:<br />
04-3<br />
1 Remove Bolt (Screw)<br />
2<br />
Inspect Mating Surface For Tarnish,<br />
Dirt, Rust, Etc. Clear As Required To<br />
Assure Good Contact.<br />
3 Reinstall Bolt (Screw) Securely<br />
(e)<br />
(f)<br />
Remove the ground bolt or screw.<br />
Inspect all mating surfaces for tarnish, dirt, rust, etc.<br />
Clean as required to assure good contact.<br />
Reinstall bolt or screw securely.<br />
Inspect for “add - on” accessories which may be interfering with the ground circuit.<br />
If several wires are crimped into one ground eyelet terminal, check for improper crimps. Make<br />
sure all of the wires are clean, securely fastened and providing a good ground path. If multiple<br />
wires are cased in one eyelet, make sure no ground wires have excess wire insulation.<br />
04-4<br />
LOCATION<br />
1 Injector<br />
2 Throttle Body<br />
3 Spark Plug<br />
4 Idle Air Control Motor<br />
5<br />
Engine Coolant Temperature (ECT)<br />
Sensor<br />
6 Knock Sensor<br />
7 Crankshaft Position (CKP) Sensor<br />
9<br />
Manifold Absolute Pressure/Intake Air<br />
Temperature (MAP/IAT) Sensor<br />
10 Ignition Control Module<br />
11 Fuel Pressure Regulator<br />
12 PCV Valve<br />
13 Inlet Fuel (From Fuel Pump)<br />
Outlet Fuel (Return Back To Fuel<br />
Tank)<br />
8 Vehicle Speed Sensor<br />
04-5<br />
1 Diagnosis Link Connector (DLC)<br />
2 Brake Lamp Switch<br />
3 Instrument Cluster<br />
4 Accelerator Pedal<br />
5 Muti - media<br />
04-6<br />
HOW TO DIAGNOSTICS ANALYSE<br />
Use diagnostic scan tool to diagnose vehicle.<br />
1. VEHICLE INTO REPAIR SHOP<br />
2. COLLECT AND ANALYSE CUSTOMER’S SYMPTOM<br />
3. CONNECT THE DIAGNOSTIC SCANNER TO DLC3<br />
4. CHECK DTC AND DATA FREEZE - FRAME DATA<br />
5. ERASE DTC<br />
6. VISUAL CHECK<br />
7. CONFIRM FAULT SYMPTOM<br />
Check result (if engine can not start,check following first)<br />
Result<br />
Proceed To<br />
Fault present Step 9<br />
Normal Step 8<br />
8. SIMULATE FAULT SYMPTOM<br />
9. CHECK IF DTC PRESENT<br />
Check result<br />
DTC present<br />
Next step<br />
10. REFER TO DTC TABLE<br />
YES > Go to step 13.<br />
Normal Step 11<br />
04-7<br />
11. BASIC CHECK<br />
Fault can not be confirmed<br />
Fault can be confirmed Step 16<br />
12. REFER TO SYMPTOM TABLE<br />
Fault can be confirmed circuit<br />
Fault can be confirmed part Step 15<br />
13. CHECK ECM POWER SUPPLY CIRCUIT<br />
14. CHECK ELECTRIC CIRCUIT<br />
Fault can be confirmed Step 17<br />
15. CHECK INTERMITTENT FAULT<br />
YES > Go to step 17.<br />
16. CHECK PARTS<br />
17. CONFIRM FAULT<br />
18. ADJUST OR REPAIR<br />
19. PERFORM CONFIRMATION TEST<br />
YES > END.<br />
04-8<br />
THE MAIN POINTS OF REPAIRING BURNED FUSE OUT<br />
DTC cause by burned fuse.<br />
(a) Remove the burned fuse. Check the resistance between<br />
the load side and ground where the fuse burned. Turn off<br />
all the switch that connecting to the fuse. If the resistance<br />
is almost zero, the switch and the load components<br />
circuit must be shorted somewhere. If the resistance is<br />
not zero, there is no circuit for short. But the temporaly<br />
shorted circuit also will cause the fuse burning.<br />
(b) The shortage caused by following:<br />
• Clipped harness<br />
• Damaged harness<br />
• Water seep into connection<br />
• Operation<br />
1 Battery<br />
2 Fuse<br />
3 Load switch<br />
4 Burned fuse<br />
5 Short position<br />
04-9<br />
DIAGNOSTIC HELP - INTERMITTENT FAULT<br />
If an intermittent fault exists, perform diagnosis as follow:<br />
• Intermittent incidents may occur. In many cases, the malfunction resolves itself (the part or<br />
circuit function returns to normal without intervention). It is important to realize that the<br />
symptoms described in the customer's complaint often do not recur on (1st trip) DTC visits.<br />
Realize also that the most frequent cause of intermittent incidents occurrences is poor<br />
electrical connections. Because of this, the conditions under which the incident occurred may<br />
not be clear. Therefore, circuit checks made as part of the standard diagnostic procedure may<br />
not indicate the specific malfunctioning area.<br />
• In this case, the maintenance staff must find out the situation in detail from the customer, ask<br />
the car owner for the details of driving conditions, weather conditions, frequency of occurrence<br />
and symptom of failure, take analysis and simulate the same or similar conditions and<br />
environment, then, determine if the symptom of failure is caused by vibration, temperature or<br />
other factors. No matter how experienced the maintenance staff are, how skilled their technique<br />
is, if analyzing the failure without checking, they would certainly neglect some important factors<br />
during repairing which causes wrong speculation and the repair work will take an indirect route<br />
or can’t go forward. The following checking will help to find out this kind of failure.<br />
1. VIBRATION METHOD.<br />
(a) Connector: Shake the connector lightly in vertical or<br />
horizontal directions, check if the wiring harness<br />
connector connecting the connector and corresponding<br />
parts is loose, the terminal is dirty, rusty, worn or bended<br />
and if the connection is loose because of the terminal<br />
extension.<br />
(b) Harness: Shake the harness lightly in vertical or<br />
horizontal directions, thoroughly check the harness<br />
breakaway condition in the connector connecting<br />
vibration section and engine/cab instruments.<br />
(c) Relay, part and sensor: Pat the sensor, relay and part<br />
considered as the failure cause lightly with hands, check<br />
them for failure, don't hit the relay with force, otherwise<br />
the relay may be open.<br />
04-10<br />
2. HEATING METHOD.<br />
(a) If one doubtful region is considered to cause a failure, heat the part which is the most possible cause of<br />
failure with an electric blower or the like to check if the failure occurs.<br />
Don’t heat to over 60℃ (the heating temperature should be in the limit of touching the part with hands);<br />
don’t heat the control module.<br />
3. SPRAYING METHOD.<br />
(a) If the failure is considered to occur in rainy day or wet weather, spray water to the vehicle to check if the<br />
failure occurs.<br />
• Don’t spray water to the engine directly to cool the engine, sprinkle water on the front face of<br />
radiator to change the temperature and humidity indirectly.<br />
• Don’t spray water on electronic parts directly.<br />
• Please take extra care to sprinkle water on vehicle leaking water.<br />
4. ELECTRIC APPLIANCE CONNECTED FULLY METHOD.<br />
(a) If the failure is possible to be caused by electric overload, connect all electrical loads, including the<br />
heater blower, the headlamps and the rear - window defroster, to check if the failure occurs. The trouble<br />
location or failure part must be found out while the symptom is confirmed during the failure symptom<br />
simulation test. To do this, narrow the range of circuit which is possible to failure based on the symptom<br />
of failure before starting the test and the pre - connection of connectors, then carry out the symptom<br />
simulation test and judge if the circuit tested is normal. When a puzzling failure occurs, make full use of<br />
troubleshooting and diagnostic code list for fault analysis and diagnosis to narrow the failure range and<br />
find out the trouble location quickly. This method is very practical and effective.<br />
5. DATA FLOW CAPTURE WITH DIAGNOSTIC SCANNER.<br />
(a) Use the function of data flow capture on the diagnostic scanner. When seeing the data flow on the<br />
diagnostic scanner, make the rated data status to simulate the fault conditions based on the freeze -<br />
frame on the diagnostic scanner.<br />
6. OSCILLOSCOPE METHOD.<br />
(a) Using the oscilloscope, capture waveform can be more helpful to find intermittent malfunction.<br />
7. OTHER METHODS.<br />
(a) Before replacing ECM of other electronic control modules in part replacing method, take full diagnosis<br />
for other external causes; ECM or other electronic control modules are expensive products with high<br />
reliability.<br />
When replacing and testing possible damaged ECM or control modules, install the possible damaged<br />
ECM or control modules on a failure - free vehicle for testing; Don’t install new control modules on a<br />
failed vehicle for testing to avoid damaging the control modules.<br />
04-11<br />
BASIC SERVICE PROCEDURE<br />
1. CHECK BATTERY VOLTAGE<br />
Check when engine stops or ignition switch is OFF.<br />
More than 11V<br />
Less than 11V<br />
Charge or change battery<br />
2. CHECK IF THE ENGINE STARTS<br />
Is the check result normal?<br />
NO > Go to fault symptom chart.<br />
3. CHECK FILTER<br />
NO > Replace or clean filter.<br />
4. CHECK IDLE SPEED<br />
5. CHECK FUEL PRESSURE<br />
NO > Eliminate fuel pressure fault, and go to next step.<br />
6. CHECK IGNITION<br />
YES > Go to fault symptom chart.<br />
NO > Eliminate ignition system fault.<br />
04-12<br />
TERMINALS OF ECM<br />
ECM TERMINAL DEFINITION<br />
Terminal No. Terminal Description Color Terminal No. Terminal Description Color<br />
1 Ignition control L 43 - -<br />
2 Ground B 44 Main relay control G - W<br />
3 Ground B 45 - -<br />
4 Ignition control G 46 - -<br />
5 - - 47<br />
6 Injector 1 L - W 48<br />
Upstream oxygen<br />
signal +<br />
Downstream oxygen<br />
7 Injector 3 L - P 49 ECT sensor + W - B<br />
8 Injector 2 L - V 50 - -<br />
9 Pump relay control G 51 Vehicle speed input W - G<br />
10 A/C low voltage output L 52 ECT sensor - W - R<br />
Crankshaft position<br />
sensor -<br />
P 53 - -<br />
12 SVS R - B 54 Air pressure MAP L - Y<br />
13 - - 55 - -<br />
14 - - 56 - -<br />
15 - - 57 - -<br />
16 - - 58 Knock sensor power O - V<br />
17 High fan control W - B 59 Accelerator sensor +<br />
18 Vehicle speed R - W 60 - -<br />
W<br />
O<br />
04-13<br />
19 MIL G - B 61 - -<br />
20 Idle control high A G - Br 62 - -<br />
21 Idle control low A G - Y 63 - -<br />
22 - - 64 EVAP control W - Y<br />
23<br />
24<br />
Heated downstream<br />
oxygen sensor -<br />
Heated upstream<br />
Y - H 65 Low fan control Y<br />
L - R 66<br />
Air temperature/<br />
pressure power<br />
25 Injector 4 L - O 67 ECU continued power W - L<br />
26 A/C MP IN R - W 68 ECU IG power B - G<br />
27 Throttle position signal V - G 69 - -<br />
28 - - 70 Sensor power SB<br />
29 - - 71 Air temperature L - W<br />
30<br />
sensor +<br />
31 - - 73<br />
O 72 - -<br />
Upstream/downstream<br />
oxygen sensor signal -<br />
32 - - 74 Sensor ground Br - R<br />
33 - - 75 ECU K signal R - L<br />
34 - - 76<br />
pressure signal -<br />
35 - - 77 - -<br />
36 - - 78 - -<br />
SB<br />
Br - R<br />
37 Knock signal W - B 79 A/C request Y - B<br />
38 - - 80 - -<br />
39 - - 81 - -<br />
40 - -<br />
41 Idle control high B Y - P<br />
42 Idle control low B Br - Y<br />
13.<br />
04-14<br />
CHECK ECM TERMINAL WITH MULTIMETER<br />
The normal standard voltage of per terminal as follow “normal condition”. The table also points out the<br />
check condition<br />
Terminal No. Terminal Description Detection Condition Specified Condition<br />
6 No.1 Injector<br />
8 No.2 Injector<br />
7 No.3 Injector<br />
25 No.4 Injector<br />
20 Idle air control motor loop A<br />
41 Idle air control motor loop B<br />
Idle: depress accelerator suddenly<br />
Engine: warm condition, start<br />
engine<br />
Voltage: 11 ~ 14 V<br />
Voltage: 0 ~ 3 V<br />
9 Pump relay<br />
64 EVAP solenoid<br />
Ignition switch: ON<br />
Engine: idle<br />
Engine: warm condition, 3000 RPM<br />
Battery voltage<br />
0 ~ 3 V<br />
1 Ignition control: (1 - 4) Engine: 3000 RPM 0.3 ~ 3.0 V<br />
4 Ignition control: (2 - 3) Engine: 3000 RPM 0.3 ~ 3.0 V<br />
68 Continuity power supply<br />
Ignition switch:<br />
79 A/C request signal Engine running, depress A/C switch -<br />
26 A/C feed back signal Engine running, depress A/C switch -<br />
19 MIL Ignition switch: OFF → ON 0 ~ 3 V<br />
44 Main relay<br />
Ignition switch: OFF<br />
Heated upstream oxygen<br />
sensor<br />
Engine: warm condition, idle<br />
Engine: 5000 RPM<br />
Heated downstream oxyge<br />
IAT: 0 ℃<br />
3.2 ~ 3.8 V<br />
66 IAT sensor Ignition switch: ON<br />
IAT: 20 ℃<br />
IAT: 40 ℃<br />
IAT: 80 ℃<br />
2.3 ~ 2.9 V<br />
1.5 ~ 2.1 V<br />
0.4 ~ 1.0 V<br />
04-15<br />
47 Upstream oxygen sensor Engine: warm condition, 2000 RPM 0.1 ~ 0.9 V<br />
48 Downstream oxygen sensor Engine: warm condition, 2000 RPM About 100 mV<br />
49 ECT sensor Ignition switch: ON<br />
ECT: 20 ℃<br />
ECT: 40 ℃<br />
1.3 ~ 1.9 V<br />
70 TPS Ignition switch: ON<br />
ECT: 80 ℃ 0.3 ~ 0.9 V<br />
TPS: idle 0.3 ~ 1.0 V (0 %)<br />
Open widely 4.5 ~ 5.5 V (100 %)<br />
51 VSS<br />
30 CKP sensor<br />
Move forward slowly<br />
Start motor<br />
Idle<br />
0 ~ 5 V (repeat)<br />
0.4 ~ 4.0 V<br />
1.5 ~ 2.5 V<br />
3 Ground - 0 V<br />
04-16<br />
CHECK ECM HARNESS - SIDE TERMINAL WITH A MULTIMETER<br />
Standard normal resistance and continuity as follow:<br />
No. Item Normal Condition (20 ℃ )<br />
1 No.1 injector<br />
2 No.2 injector<br />
3 No.3 injector<br />
13 ~ 16 Ω<br />
4 No.4 injector<br />
5 Idle air control motor loop A, B terminal<br />
6 Idle air control motor loop C, D terminal<br />
28 ~ 33 Ω<br />
7 EGR solenoid valve 36 ~ 44 Ω<br />
8 EVAP solenoid valve 36 ~ 44 Ω<br />
9 ECM ground Continuity<br />
10 Heated oxygen sensor About 12 Ω<br />
5.3 ~ 6.7 Ω<br />
11 IAT sensor<br />
2.3 ~ 3.0 Ω<br />
1.0 ~ 1.5 Ω<br />
0.30 ~ 0.42 Ω<br />
5.1 ~ 6.5 Ω<br />
12 ECT sensor<br />
2.1 ~ 2.7 Ω<br />
0.9 ~ 1.3 Ω<br />
0.26 ~ 0.36 Ω<br />
04-17<br />
DIAGNOSTIC SYSTEM<br />
1. The failure of engine electric control system is<br />
divided into 2 classes:<br />
First is lighting MIL lamp (1); When the instrument MIL<br />
lamp lights, based on relevant requirements of national<br />
rules, it needs to be treated immediately, otherwise the<br />
system will limit the speed of the engine so as to affect<br />
the normal operating of vehicle.<br />
The other is lighting SVS lamp (2), indicating that the<br />
system fails and needs to be repaired in time.<br />
The failures of both classes should be checked with<br />
diagnostic scanner or special equipment with corresponding<br />
functions.<br />
The following matters should be noted during the engine running and service processes.<br />
2. The lighting of SVS lamp and MIL lamp is controlled by ECM; The special lighting of SVS lamp<br />
and MIL lamp after and before starting are described below:<br />
(a) For system without failure, the ignition switch is turned ON, the MIL lamp lights on, SVS lamp lights and<br />
then goes out (system self - checking). The SVS lamp and MIL lamp are off after engine starting and<br />
stalling.<br />
(b) For system with failure, the ignition switch is turned ON, the MIL lamp lights on, the SVS lamp is off and<br />
then lights on after self - checked; After engine starting, if the SVS lamp in failure class is defined as<br />
lighting on mode, the SVS lamp will light on after the requirements for SVS lamp lighting are met; if the<br />
MIL lamp in failure class is defined as lighting on mode, the SVS lamp will light on after the<br />
requirements for MIL lamp lighting are met; After engine stalling, the ignition switch is turned OFF and<br />
goes out after process (90s for the longest).<br />
3. If an engine failure that may involve the fuel injection system - electronic controlled is to be<br />
diagnosed and cleared, first determine if the failure is related with the fuel injection system -<br />
electronic controlled. If the engine fails but the malfunction indicator lamp doesn't light, the failure<br />
is unrelated to the electronic control system generally.<br />
The diagnostic trouble codes record and data related<br />
with sensors and actuators in ECM can be read by<br />
KT600 diagnostic scanner. Additional, the actuator can<br />
be positive driven by the scan tool under specified<br />
conditions.<br />
04-18<br />
DLC - data link connector.<br />
ECM communicate with DLC.<br />
Terminals in DLC arrange according to standard.<br />
Terminal No. Name Check Result<br />
4 Ground Less than 1 Ω<br />
5 Ground Less than 1 Ω<br />
6 Diagnostic signal<br />
Pulse signal (When<br />
commnicate)<br />
7<br />
Diagnostic<br />
communication K<br />
16 Battery positive 9 ~ 14 V<br />
ENGINE CONTROL SYSTEM SELF - DIAGNOTIC ITEM<br />
• Connect the diagnostic scanner cable to DLC. Turn<br />
the ignition switch ON. Try to open it. If displayed<br />
error communication on screen, then the diagnostic<br />
scanner faults .<br />
• If the diagnostic scanner communicates with other<br />
vehicle normally, then check the DLC on the original<br />
vehicle.<br />
Check Item<br />
2 Main Relay<br />
3 Fuel Pump<br />
4 Ignition Coil<br />
5 Oxygen Sensor<br />
6 EVAP Solenoid<br />
7 Knock Sensor<br />
9 Poor Accelerator Sensor<br />
10 CKP Sensor<br />
11 Throttle Position Sensor<br />
12 ECT Sensor<br />
13 MAP/IAT Sensor<br />
04-19<br />
READING AND ERASING DIAGNOSTIC TROUBLE CODE (DTC)<br />
The troubles are tested and determined by the engine control system and stored in the Engine Control<br />
Module (ECM); the system troubles can be current or history.<br />
Current troubles: Exist in ECM currently. For example: The circuit of Engine Coolant Temperature<br />
(ECT) sensor is open. The current troubles must be repaired. Otherwise, they can’t be erased from<br />
memory.<br />
(b) History troubles: Have two storage types.<br />
• The trouble has been repaired and actual trouble has disappeared, but the memory hasn’t been erased<br />
from ECM.<br />
• The trouble occurred once and didn’t exist, but it is possible to occur again. For example: Poor contact<br />
of conducting wire. As the stored troubles are not current ones, it’s unnecessary to repair them before<br />
erased from the memory, or it can be processed referring to the trouble - shooting methods for<br />
intermittent malfunction.<br />
• If the battery voltage is too low and the trouble code can’t be output normally from ECM, the<br />
battery voltage must be tested before checking and the voltage should not be less than 11 V.<br />
• When the battery or ECM connectors are disconnected, the trouble code stored in ECM will be<br />
erased.<br />
• Before connecting or disconnecting KT600 scan tool, be sure to confirm the ignition switch is in<br />
OFF (LOCK) position.<br />
• Using the KT600 collective intelligence scan tool, read DTC.<br />
• Using the KT600 scan tool, perform the reading DTC procedure below:<br />
(a) Check and confirm the following conditions:<br />
• The throttle is closed.<br />
• Turn A/C switch OFF.<br />
• Shift transmission in neutral.<br />
(b) Turn the ignition switch OFF.<br />
(c) Connect the KT600 scan tool to the Data Link Connector<br />
(DLC) - use the most current software available.<br />
(d) Turn the ignition switch ON.<br />
(e) Select the item, read dtc.<br />
(f) Check DTC and data stream. After recording, delete it (If<br />
DTC cannot be deleted, then perform the diagnosis<br />
procedure refering to “Diagnostics trouble code check”.<br />
Repair faults ).<br />
(g) Start engine and warm it to normal operating temperature.<br />
(h) Under one of the condition, run engine to MIL ON:<br />
• Simulate DTC setting condition.<br />
• Simulate the customer’s description.<br />
• Simulate the scan tool freeze data.<br />
(i) Use the scan tool to read the DTC in ECM.<br />
04-20<br />
(j)<br />
If there are DTCs, but the data stream is normal or the<br />
function is good, then refer to the diagnostics help. If there<br />
are DTCs, but the stream is abnormal or the function is not<br />
good, then perform diagnosis procedure refering to<br />
“Diagnostics trouble code chart”.<br />
• Use the scan tool to delete DTCs. As soon as DTC is detected, ECM will record the vehicle and<br />
driving conditions as the type of freeze stream. When eliminating faults, the catching function<br />
will help to confirm the condition of the fault, such as warm condition, stop condition and lean<br />
or rich A/F ration and other data.<br />
• DTC setting condition:<br />
(a) Engine speed<br />
(b) VSS<br />
(c) ECT sensor<br />
(d) MAP sensor<br />
(e) Barometric sensor<br />
(f) IAT sensor<br />
(g) TPS<br />
(h) EVAP<br />
(i) Fuel pressure adjustment<br />
(j) A/C switch<br />
THE WAY OF CLEAR DTC<br />
1. Using the scan tool, clear DTC:<br />
(a) Turn the ignition switch OFF.<br />
(b) Connect the KT600 scan tool to the Data Link Connector (DLC) - use the most current software<br />
available.<br />
(c) Turn the ignition switch ON.<br />
(d) Select the item, clear DTC.<br />
04-21<br />
CAPTURING DATA<br />
Once DTC is captured and stored, ECM records the vehicle and driving conditions information as a<br />
form of rated data. During troubleshooting, the rated data can help determine if the vehicle was<br />
running or parked, and data of other sensors and actuators has been recorded when the trouble<br />
occurred.<br />
If the DTC is detected but the trouble can’t reappear, confirm the freeze - frame rated data. ECM records<br />
the engine condition in form of freeze - frame data at regular intervals. The diagnostic scanner can be<br />
used to read several sets of freeze - frame data respectively. KT600 diagnostic scanner provides<br />
powerful random data flow help function. Select read data flow function menu in engine system, enter<br />
the data flow testing result display interface, click “?Help” button to eject the following windows:<br />
• Driving Record Playback<br />
• Calculator<br />
• Data Range Reference<br />
• Data Capture<br />
• Data Comparisons<br />
• Data Flow Settings<br />
• Data/Waveform Display<br />
• Driving Recorder Menu<br />
The data can be used to simulate the vehicle conditions as the failure occurs. It also can help<br />
determine the cause of trouble and judge if it’s temporary fault. When the engine is running with<br />
trouble, select the menu items, read data flow (Click “?Help”)\Data Capture\Click Record\(Click<br />
“?Help”)\Data Comparisons.<br />
04-22<br />
FAIL - SAFE CHART<br />
When the DTC listed below is detected, the ECM enters fail - safe mode and the MIL lights up.<br />
Number Item Control Contents Period Of Fault<br />
2 Relay<br />
3 Fuel pump<br />
4 Ignition coil<br />
5 Oxygen sensor<br />
6 EVAP solenoid valve<br />
7 KS<br />
8 VSS<br />
9 IAT sensor<br />
• The MIL light will turn on.<br />
• Unstable idle.<br />
• Lack of engine power.<br />
• Poor acceleration.<br />
• Engine will not start.<br />
• Plugged injector.<br />
• System is out of work.<br />
• Can not start engine.<br />
• Noisy fuel pump operation.<br />
• Poor fuel economy.<br />
• Excessive exhaust emissions.<br />
• Weak spark.<br />
• Sluggish acceleration.<br />
• Poor driving capability.<br />
• The engine base fuel closed - loop control self - learning will be shut<br />
off.<br />
• The engine idle air control self - learning will be shut off.<br />
• Unstable idle or high idle.<br />
• The engine produces an engine knock.<br />
• Overheated engine.<br />
• Internal engine damage.<br />
• The engine RPM will be limited.<br />
• No VSS diaplay.<br />
• The IAT is equal to ECT.<br />
04-23<br />
10 Poor accelerator sensor<br />
11 CKP sensor<br />
12 TPS<br />
13 ECT sensor<br />
14 MAP/IAT sensor<br />
• Misfire.<br />
• Rough engine operation.<br />
• Engine is hard to start.<br />
• The engine RPM will be limited after the engine starts.<br />
• The highest RPM is less than 3800 RPM.<br />
• No ignition signal to the ECM.<br />
• The tachometer does not work.<br />
• Engine hard to start when cold.<br />
• Engine hard to start when hot.<br />
• If the sensor circuit is shorted to power, the engine will run under the<br />
default values.<br />
• The temperature gauge indicates too high.<br />
• The temperature gauge indicates too low.<br />
• The cooling fan operates continuously on high speed.<br />
• The high temperature warning lamp will flash when the instrument<br />
panel indicates low temperature.<br />
04-24<br />
DATA STREAM LIST/ACTIVE TEST<br />
1. DATA STREAM LIST.<br />
• Through reading the data stream displayed on scan tool sreen, we can check the sensor,<br />
actuator and switch data value but not removing any components. As the first step, this way is<br />
the best way to short diagnosis period .<br />
• The following arranged the data stream under the normal condition. It only offers to reference.<br />
Don’t judge a component normal or not only depend on these value.<br />
READ DATA STREAM PROCEDURE<br />
Start the engine and warm it to normal operating temperature.<br />
Turn the ignition switch OFF.<br />
Connect the KT600 scan tool to the Data Link Connector (DLC) - use the most current software<br />
Turn the ignition switch ON.<br />
Select the item, read data sream.<br />
The table below lists the data found in inspection items at different states by the KT600 in “DATA LIST”<br />
items.<br />
• If no concrete specification of idle condition, the shift selector lever is in neutral position. The A/C and<br />
accessories switch are in the OFF position.<br />
• Injector driving time means time is taken by crankshaft at speed of less than 250 RPM and power<br />
supply voltage of 11 V.<br />
• For new vehicle (within operation distance of 500 km), sometimes injector driving time is 10% more<br />
than standard time.<br />
• For new vehicle (within operation distance of 500 km), sometimes step length of stepper motor is more<br />
30 steps than standard step length.<br />
04-25<br />
Displayed Item Check Item Specified Condition<br />
Oxygen sensor<br />
• Engine: Warm<br />
• A/F: Mixture is made<br />
leaner when decelerating<br />
richer when accelerating<br />
Engine suddenly decelerate<br />
from 4000 RPM<br />
Engine suddenly accelerate<br />
≤ 0.2 V<br />
0.6 ~ 1 V<br />
• Check A/F with oxygen<br />
Engine: Idle<br />
≤ 0.4 V<br />
2500 RPM 0.6 ~ 1 V<br />
MAP sensor<br />
IAT sensor<br />
• ECT: 80 ~ 95 ℃<br />
• Lamp and all other<br />
accessorie: OFF<br />
• Transmission: Neutral<br />
• Ignition switch: ON<br />
• Or engine is running<br />
Engine: Idle -<br />
2500 RPM -<br />
IAT: - 20 ℃ - 20 ℃<br />
IAT: 0 ℃ 0 ℃<br />
IAT: 20 ℃ 20 ℃<br />
IAT: 40 ℃ 40 ℃<br />
IAT: 80 ℃ 80 ℃<br />
Engine: Idle 0.3 ~ 1 V (0%)<br />
TP open slowly<br />
Increase proportionally<br />
Wide open<br />
4.5 ~ 5.5 V<br />
Power supply Ignition switch: ON System voltage<br />
Ignition switch<br />
Engine: Stop<br />
Engine: Start<br />
ECT sensor<br />
ECT: - 20 ℃ - 20 ℃<br />
ECT: 0 ℃ 0 ℃<br />
ECT: 20 ℃ 20 ℃<br />
ECT: 40 ℃ 40 ℃<br />
ECT: 80 ℃ 80 ℃<br />
Altitude: 0 m<br />
101 kPa<br />
Barometric sensor<br />
Altitude: 600 m<br />
Altitude: 1200 m<br />
95 kPa<br />
88 kPa<br />
Altitude: 1800 m<br />
81 kPa<br />
A/C switch<br />
(Turn A/C switch ON, A/C<br />
compressor works)<br />
A/C switch: OFF<br />
A/C switch: ON<br />
04-26<br />
ECT: 0 ℃<br />
60 ~ 90 ms<br />
Injector<br />
Engine: Running<br />
30 ~ 5 ms<br />
ECT: 80 ℃<br />
6.7 ~ 10.1 ms<br />
• Accessorie: OFF<br />
2.2 ~ 3.4 ms<br />
2500 RPM 1.9 ~ 3.1 ms<br />
Engine runs at high speed<br />
suddenly<br />
Increase<br />
Ignition coil • Engine: Warm<br />
2 ~ 18 BTDC<br />
2500 RPM 27 ~ 47 BTDC<br />
Idle air control<br />
motor<br />
• Engine: Idle<br />
• A/C works<br />
A/C switch: OFF → ON<br />
2 ~ 25 steps<br />
A/C relay<br />
Engine: Warm and idle<br />
Not activate (Compressor<br />
clutch does not work)<br />
Activate (Compressor<br />
clutch works)<br />
• Engine: Running<br />
• Tachometer: Connection<br />
Compare the values read<br />
from tachometer and KT600<br />
respectively<br />
The same<br />
ECT: - 20 ℃<br />
1275 ~ 1475 RPM<br />
CKP sensor<br />
1225 ~ 1425 RPM<br />
1100 ~ 1300 RPM<br />
950 ~ 1150 RPM<br />
650 ~ 850 RPM<br />
2. ACTIVE TEST.<br />
The active test function for us to check the sensor, actuator and switch data value but not removing<br />
any components. We can use the scan tool to perform the test. As the first step, this way is the best<br />
way to short diagnosis period.<br />
The displayed data stream when performing the active test.<br />
(d) Select the item, actice test.<br />
(e) Refer to the following chart, perform the active test. The following chart is the item which in the<br />
“ACTIVE TEST” of the KT600 scan tool.<br />
(f) When performing the function of the “ACTIVE TEST”, if there is fault phenomenon, check and repair.<br />
04-27<br />
(g)<br />
(h)<br />
(i)<br />
After repairing, using the KT600 to perform again.<br />
Clear DTC.<br />
Disconnect KT600 scan tool.<br />
Restart engine to perform test. Confirm the faults has been eliminated.<br />
Displayed Item Test Component Control Area Diagnosis Remark<br />
MIL Control MIL ON/OFF -<br />
EVAP EVAP solenoid valve ON/OFF -<br />
Fuel pump relay Fuel pump relay ON/OFF -<br />
Low fan Control low fan ON/OFF -<br />
High fan Control high fan ON/OFF -<br />
A/C relay Shut off A/C relay ON/OFF -<br />
Idle air control motor Control idle motor steps - -<br />
Idle air control motor Control idle motor speed - -<br />
Idle control motor reset Control Idle motor reset - -<br />
Ignition advance angle Ignition advance angle - -<br />
Gear signal learn 58X learn - -<br />
Injector (A/B/C/D) Shut off fuel injection ON/OFF -<br />
BLM learn - - -<br />
BLM reset - - -<br />
Fuel open control Open control - -<br />
Inspect catalysator at idle Check catalysator at idle - -<br />
Oxygen sensor response Oxygen sensor response - -<br />
04-28<br />
DIAGNOSTIC TROUBLE CODE CHART<br />
Note<br />
If a malfunction code is displayed during the DTC check in the check mode, check the harness or connectors<br />
for the codes listed in the table below. For details of each code, refer to the DTC chart<br />
DTC No. DTC Definition Trouble Area<br />
P0106<br />
P0107<br />
P0108<br />
P0112<br />
P0113<br />
P0117<br />
P0118<br />
P0122<br />
P0123<br />
P0131<br />
MAP / TPS Rationality<br />
MAP Circuit Low Voltage or Open<br />
MAP Circuit High Voltage<br />
IAT Circuit Low Voltage or Open<br />
IAT Circuit High Voltage<br />
Coolant Circuit Low Voltage<br />
Coolant Circuit High Voltage<br />
Throttle Position Low Voltage<br />
Throttle Position High Voltage<br />
Front Oxygen Sensor Short Low<br />
• MAP sensor<br />
• Open or short in MAP sensor harness or<br />
connectors<br />
• ECM<br />
• Short in MAP sensor harness or connectors<br />
• IAT sensor<br />
• Short in IAT sensor harness or connectors<br />
• Open or short in IAT sensor harness or<br />
• ECT sensor<br />
• Short in ECT sensor harness or connectors<br />
• Open or short in ECT sensor harness or<br />
• Throttle position sensor<br />
• Open or short in throttle position sensor<br />
harness or connectors<br />
• Short in throttle position sensor harness or<br />
• Upstream oxygen sensor<br />
• Short in upstream oxygen sensor harness or<br />
04-29<br />
P0132<br />
Front Oxygen Sensor Short High<br />
P0133<br />
Front Oxygen Sensor slow response<br />
• Open or short in upstream oxygen sensor<br />
• Upstream oxygen sensor heater<br />
• Relay<br />
• Air induction system<br />
• Fuel pressure<br />
• Injector<br />
P0134<br />
Front Oxygen Sensor Inadequate<br />
Activeness Or Open<br />
• Open in upstream oxygensensor harness or<br />
P0135<br />
Front Oxygen Heater Fault<br />
• Upstream oxygen heater<br />
• Open or short in upstream oxygen heater<br />
P0137<br />
Rear Oxygen Sensor Short Low<br />
• Open or short in downstream oxygen sensor<br />
P0138<br />
Rear Oxygen Sensor Short High<br />
• Downstream oxygen sensor<br />
P0140<br />
Rear Oxygen Sensor Inadequate<br />
• Open in downstream oxygen sensor harness<br />
or connectors<br />
P0141<br />
Rear Oxygen Heater Fault<br />
• Downstream oxygen heater<br />
• Open or short in downstream oxygen heater<br />
04-30<br />
P0171<br />
P0172<br />
P0201<br />
P0202<br />
P0203<br />
P0204<br />
P0230<br />
P0300<br />
Fuel Trim BLM Learn Too Lean<br />
Fuel Trim BLM Learn Too Rich<br />
Injector 1 Circuit Diagnostic<br />
Injector 2 Circuit Diagnostic<br />
Injector 3 Circuit Diagnostic<br />
Injector 4 Circuit Diagnostic<br />
Fuel Pump Relay Fault<br />
The Engine Misfire Fault<br />
• Injector blockage<br />
• Open or short in oxygen sensor circuit<br />
• Oxygen sensor<br />
• Injector leak or blockage<br />
• Engine coolant temperature sensor<br />
• Gas leakage in exhaust system<br />
• Open or short in oxygen sensor harness or<br />
• Injector 1<br />
• Injector A harness or connectors<br />
• Injector 2<br />
• Injector 3<br />
• Injector 4<br />
• Pump relay<br />
• Pump relay harness or connectors<br />
• Open or short in engine wire<br />
• Ignition system<br />
• Compression pressure<br />
• Valve timing<br />
• PCV hose connection<br />
• PCV hose<br />
04-31<br />
P0324<br />
Knock System Fault<br />
• Knock sensor<br />
• Knock sensor harness or connectors<br />
P0325<br />
P0335<br />
Knock Sensor Fault<br />
CKP Sensor Circuit No Signal<br />
• Open or short in CKP sensor harness or<br />
P0336<br />
CKP Sensor Circuit Noisy Signal<br />
• CKP sensor<br />
• Open or short in CKP sensorharness or<br />
P0351 EST Output #1<br />
P0352 EST Output #2<br />
• Ignition coil 1 harness or connectors<br />
• Ignition coil 1<br />
• Ignition coil 2 harness or connectors<br />
• Ignition coil 2<br />
P0420<br />
P0443<br />
P0480<br />
P0481<br />
P0502<br />
P0506<br />
P0507<br />
Catalyst failure<br />
Purge Solenoid Diagnostic<br />
Fan 1 Fault<br />
Fan 2 Fault<br />
Vehicle Speed Sensor No Signal<br />
Idle Speed Control - Low RPM<br />
Idle Speed Control - High RPM<br />
• Catalyst harness or connectors<br />
• Catalyst<br />
• Purge solenoid diagnostic harness or<br />
connectors open or short<br />
• Purge solenoid diagnostic<br />
• Fan1<br />
• Fan 1 harness or connectors<br />
• Fan 2<br />
• Fan 2 harness or connectors<br />
• Vehicle speed sensor<br />
• Vehicle speed sensor harness or connectors<br />
• Idle motor<br />
• Idle control vale<br />
• Idle motor harness or connectors<br />
04-32<br />
P0562<br />
P0563<br />
P0645<br />
P0650<br />
P0685<br />
P1167<br />
P1171<br />
P1336<br />
P1391<br />
P1392<br />
P1393<br />
P1659<br />
Voltage Low Diagnostics<br />
Voltage High Diagnostics<br />
A/C clutch output circuit fault<br />
Malfunction Indicator Lamp Fault<br />
Main Power Relay Fault<br />
Front Oxygen Sensor Signal Rich in<br />
fuel<br />
Front Oxygen Sensor Signal Lean In fuel<br />
TEC Not Learned<br />
G Sensor Rationality<br />
G sensor short low<br />
G Sensor Short High<br />
SVS Light Fault<br />
• Battery<br />
• Generator<br />
• Power supply harness or connectors<br />
• A/C clutch<br />
• A/C clutch harness or connectors<br />
• Malfunction indicator lamp<br />
• Malfunction indicator lamp harness or<br />
• Main Power Relay<br />
• Main Power Relay harness or connectors<br />
• Engine hood main relay<br />
• Upstream oxygen heater and main relay<br />
• CKP sensor is not installed<br />
• Accelarator<br />
• Short in accelarator harness or connectors<br />
• SVS Light harness or connector<br />
• Instrument Panel<br />
04-33<br />
DTC DIAGNOSTIC<br />
P0107 - MAP CIRCUIT LOW VOLTAGE OR OPEN<br />
P0108 - MAP CIRCUIT HIGH VOLTAGE<br />
P0112 - IAT CIRCUIT LOW VOLTAGE OR OPEN<br />
P0113 - IAT CIRCUIT HIGH VOLTAGE<br />
DESCRIPTION<br />
MT20U2 adopted speed - density air measurement method to check the air intake volume into the engine so<br />
as to control the fuel injection pulse width for the precise control of engine power output. Meanwhile, this<br />
system adopted intake pressure cylinder determination technology and the intake air sensor is installed near<br />
the inlet opening of cylinder 4 intake manifold. At the moment when the throttle is opened, there will be one<br />
instantaneous pressure drop at the sensor, of which the value is about 1 kPa. When the ECM detected and<br />
received this instantaneous pressure drop, the ECM will determine the compression upper dead center signal<br />
after software diagnosis treatment (its functions is similar with the camshaft position sensor of traditional<br />
electric injection system, also referred as phase sensor).<br />
WIRING DIAGRAM<br />
04-34<br />
DTC No. DTC Definition DTC Detection Condition Trouble Area<br />
MAP sensor circuit low<br />
voltage or open<br />
• No TPS faults<br />
• ECM detects that the MAP<br />
input signal is less than<br />
acceptable value<br />
• MAP sensor loose connector<br />
• Open or short in MAP sensor<br />
signal circuit<br />
• Short circuit in MAP sensor<br />
• Open circuit in MAP sensor<br />
5V circuit<br />
• Open in MAP sensor ground<br />
circuit<br />
MAP sensor circuit high<br />
voltage<br />
input signal is higher than<br />
• Short in MAP sensor signal<br />
• Short in MAP sensor 5V<br />
power circuit<br />
IAT sensor circuit low<br />
• Ignition switch: ON.<br />
• 60 seconds since the ignition<br />
switch is turned “ON”, or after<br />
engine starts.<br />
• Sensor output voltage has<br />
continued to be 0.2 V or lower<br />
(corresponding to an intake air<br />
temperature of 125 ℃ or<br />
lower) for 4 seconds.<br />
• Short in IAT sensor 5 V<br />
reference circuit<br />
IAT sensor circuit high<br />
continued to be 4.6 V or<br />
higher (corresponding to an<br />
intake air temperature of - 45<br />
℃ or lower) for 4 seconds.<br />
• Open in IAT sensor 5 V<br />
• While performing electrical diagnosis & testing, assure the ECM ground good contact.<br />
• While performing electrical diagnosis & testing, always refer to the electrical schematics for<br />
specific circuitand component information.<br />
• While performing electrical diagnosis & testing, look for broken, bent, pushed out or corroded<br />
• If any DTC is detected, using the scan tool, select the item, read data stream.<br />
04-35<br />
INSPECTION PROCEDURE<br />
1. READ VALUE AND DTC OF SCAN TOOL<br />
With the KT600 scan tool, perform the DTC confirming procedure.<br />
Perform the reading data stream procedure.<br />
Read IAT value displayed on the KT600 scan tool.<br />
Displayed DTC And Pressure Proceed To Malfunction<br />
• P0108<br />
• About 45 kPa (or 4 V)<br />
Next step Short to voltage<br />
• P0107<br />
• P0107 or P0108<br />
• Pressure normal<br />
Diagnostic help<br />
Open or short to ground<br />
Check for intermittent problems<br />
YES > Go to diagnostic help for checking intermittent problems.<br />
NO > If there an open or short circuit, go to next step.<br />
2. CHECK HARNESS AND CONNECTOR (INTAKE AIR TEMPERATURE PRESSURE SENSOR -<br />
GROUND)<br />
Disconnect the E006 intake air temperature pressure sensor.<br />
(d) Measure the voltage according to the value in the table<br />
below.<br />
Standard voltage<br />
Tester Connection<br />
E006 (2) - Ground<br />
Specified Condition<br />
5.0 ± 0.25 V<br />
NO > Repair or replace harness or connector.<br />
04-36<br />
3. CHECK HARNESS AND CONNECTOR (INTAKE AIR TEMPERATURE PRESSURE SENSOR -<br />
ECM)<br />
Disconnect the E001 ECM connector.<br />
(d) Measure the resistance according to the value in the<br />
table below.<br />
Standard resistance (check for open)<br />
E001 (76) - E006 (4)<br />
E001 (71) - E006 (3)<br />
< 2 Ω<br />
4. CHECK MAP SIGNAL<br />
(b) Disconnect the E006 intake air temperature pressure sensor.<br />
(c) Start engine.<br />
E006(2) - Ground • Idle: 5.0 ± 0.25 V<br />
E006(4) - Ground<br />
• Idle: 1.3 V<br />
• No load condition, opening<br />
throttle slowly: 1.3 V<br />
• Open quickly: 4 V, then return<br />
back to 1.5 V<br />
04-37<br />
5. CHECK HARNESS AND CONNECTOR (INTAKE AIR TEMPERATURE PRESSURE SENSOR -<br />
(e) Measure the voltage according to the value in the table<br />
E006 (4) - Ground<br />
0 V<br />
YES > Replace the ECM.<br />
04-38<br />
P0117 - COOLANT CIRCUIT LOW VOLTAGE<br />
P0118 - COOLANT CIRCUIT HIGH VOLTAGE<br />
1 Electric Appliance Connector<br />
2 Cabinet<br />
3 NTC Resistance<br />
This sensor is one Negative Temperature Coefficient (NTC) thermistance, of which the resistance will reduce<br />
following the increasing of the temperature in non - linear relation. When the coolant temperature is low, the<br />
resistance in the thermistor increases. When the temperature is high, theresistance drops. The variations in<br />
resistance are reflected in the voltage output from the sensor.<br />
The ECM monitors the sensor voltage and uses this value to calculate the engine coolant temperature.<br />
Engine cooling<br />
temperature sensor circuit<br />
low voltage<br />
• 60 seconds since the ignition switch is<br />
turned “ON” or after engine starts<br />
• Sensor output voltage has continued to be<br />
0.2 V or lower (corresponding to an intake<br />
airtemperature of 145 ℃ or higher) for 4<br />
seconds<br />
• Short in ECT<br />
sensor circuit<br />
high voltage<br />
4.6 V or higher (corresponding to an<br />
intakeair temperature of - 45 ℃ or lower)<br />
for 4 seconds<br />
• Open or short in<br />
04-39<br />
• If the ECM detects the DTC P0117 or P0118, it operates the fail–safe function in which the engine<br />
coolant temperature is assumed to be a default value. At the same time, with the ignition switch<br />
ON, the cooling fans will operate at high speed. The fail–safe function will not untill the ECM<br />
detects the acceptance condition.<br />
• If any DTC is detected, using the scan tool, select the item, read the data stream.<br />
Displayed Temperature<br />
Malfunction<br />
- 40 °C Open circuit<br />
140 °C Short circuit<br />
Read sensor value displayed on the KT600 scan tool.<br />
Display DTC And Temperature Proceed To Malfunction<br />
• P0118<br />
• - 40 °C<br />
• P0117<br />
• 140 °C or more<br />
• P0117 or P0118<br />
• 80°C - 100°C<br />
Step 5<br />
Open or short to power<br />
Short to ground<br />
NO > If there is an open circuit, go to next step.<br />
If there is a short circuit, go to step 5.<br />
2. READ VALUE OF KT600 SCAN TOOL<br />
Disconnect the E010 ECT sensor connector<br />
Connect terminals 1 and 2 of the engine coolant temperature sensor connector E010 on the wire<br />
harness side.<br />
Select the item, read data stream.<br />
Read ECT value displayed on the KT600 scan tool.<br />
Temperature value: ≥ 140 °C<br />
04-40<br />
YES > Replace engine coolant temperature sensor, clear the DTC.<br />
3. CHECK HARNESS AND CONNECTOR (COOLANT TEMPERATURE SENSOR - GROUND)<br />
Disconnect the E010 coolant temperature sensor.<br />
E010 (1) - Ground<br />
4.5 ~ 5.0 V<br />
4. CHECK HARNESS AND CONNECTOR (COOLANT TEMPERATURE SENSOR - ECM)<br />
Disconnect the E001 ECM.<br />
E010 (2) - E001 (52)<br />
YES > Replace the coolant temperature sensor.<br />
04-41<br />
P0122 - THROTTLE POSITION LOW VOLTAGE<br />
P0123 - THROTTLE POSITION HIGH VOLTAGE<br />
MT20U2 Throttle Position Sensor (TPS) is used to provide throttle angle, angle speed and engine idle position<br />
information to the ECM, based on which the ECM can obtain the engine load information, operating mode<br />
(such as start, idle, reverse towing, partial load, full load) and acceleration & deceleration information. This<br />
sensor is of three - line type and the ECM will check the throttle open extent by monitoring the voltage<br />
variation.<br />
Throttle position low<br />
• 60 seconds since the ignition switch<br />
is turned “ON”, or after engine starts<br />
• Sensor output voltage has continued<br />
to be 0.2V or lower for 4 seconds<br />
• TPS failed or maladjusted<br />
• Open or short in TPS circuit<br />
Throttle position<br />
• Setting the closed throttle position<br />
switch ON, the sensor output<br />
voltage has continued to be 2 V or<br />
higher for 4 seconds<br />
• Short in TPS circuit<br />
04-42<br />
Using the KT600 scan tool, perform the DTC confirming procedure.<br />
Read TPS value displayed on the KT600 scan tool.<br />
Read TPS signal data displayed on the KT600 scan tool<br />
Displayed DTC And Voltage Proceed To Malfunction<br />
• P0122 ( < 0.2 V) Step 4 Short to voltage<br />
• P0123 ( > 2 V) Next step Open or short to ground<br />
• P0122 or P0123<br />
• TPS signal is normal<br />
NO > If there is an open or short circuit, go to next step.<br />
2. CHECK HARNESS AND CONNECTOR (THROTTLE POSITION SENSOR - GROUND)<br />
Disconnect the E009 throttle position sensor.<br />
Measure the voltage according to the value in the table<br />
E009 (1) - Ground<br />
04-43<br />
3. CHECK THROTTLE POSITION SENSOR SIGNAL<br />
(a) Turn the ignition switch ON.<br />
(b) Jump wire at terminals 2 and 3 of the E009 TPS connector.<br />
(c) Perform reading sensor data stream procedure with scan tool.<br />
Voltage value: 4 V<br />
YES > Go to step 5.<br />
4. CHECK HARNESS AND CONNECTOR (THROTTLE POSITION SENSOR - ECM)<br />
Measure the resistance according to the value in the<br />
E009 (2) - E001 (74)<br />
5. CHECK HARNESS AND CONNECTOR (THROTTLE POSITION SENSOR - GROUND)<br />
E009 (3) - Ground<br />
YES > Replace the throttle position sensor.<br />
04-44<br />
P1167 - FRONT OXYGEN SENSOR SIGNAL RICH IN FUEL<br />
P1171 - FRONT OXYGEN SENSOR SIGNAL LEAN IN FUEL<br />
P0131 - FRONT OXYGEN SENSOR SHORT LOW<br />
P0132 - FRONT OXYGEN SENSOR SHORT HIGH<br />
P0133 - FRONT OXYGEN SENSOR RESPONSE<br />
P0134 - FRONT OXYGEN SENSOR OPEN<br />
P0135 - FRONT OXYGEN SENSOR HEATER FAULT<br />
1 Air<br />
2 Case<br />
3 Solid electrolyte<br />
4 Platinum electrode<br />
5 Heater<br />
6 Lining<br />
7 Exhaust gas<br />
8 Rich<br />
9 Air/fuel ratio<br />
10 Lean<br />
04-45<br />
The Engine Control Module (ECM) supplies a voltage of about 450 mV between the ECM terminals 62 and 6.<br />
The oxygen sensor varies the voltage within a range of about 1V if the exhaust is rich, down to about 0.1 V if<br />
the exhaust is lean. The oxygen sensor is like an open circuit and produces no voltage when it is below 360 ℃<br />
. An open oxygen sensor circuit or a cold oxygen sensor causes open - loop operation.<br />
Front oxygen sensor<br />
short low<br />
• The engine controls system<br />
is in closed loop<br />
• The engine speed is below<br />
6000 RPM<br />
feedback voltage has<br />
continued to be 0.07 V or<br />
lower at least 40 seconds<br />
• Upstream oxygen<br />
• Short in upstream<br />
oxygen sensor<br />
short high<br />
continued to be 4.8 V or<br />
higher for at least 0.2<br />
open<br />
continued to be between<br />
0.42 ~ 0.48 V<br />
• Open in upstream<br />
response<br />
• DTC P0135、 P01167 are<br />
not set<br />
heater fault<br />
• P1171DTC P0133、P01167<br />
are not set<br />
04-46<br />
signal rich in fuel<br />
• DTC P01171、 P0133 are<br />
signal lean in fuel<br />
DIAGNOSIC HELP<br />
• Normal scan tool voltage varies between 0.1 to 1.0 V while in closed - loop.<br />
• Check oxygen sensor harness, maybe the oxygen sensor is not well installed. It touch the exhaust pipe.<br />
• Check if there is intermittent ground existent between ECM and oxygen sensor.<br />
• Perform an injector balance test. Check if the lean mixture was caused by injector blocking.<br />
• The vacuum leaking of crankcase cause lean mixture.<br />
• The out air enter into exhaust pipe and through the oxygen sensor by the leaking of exhaust manifold<br />
wsaher.<br />
04-47<br />
Read oxygen sensor value displayed on the KT600 scan tool.<br />
Engine runs at idle.<br />
P0131 ( < 0.21 V) Step 6 Short to ground<br />
P0132 ( > 4.8 V) Step 7 Short to power<br />
P0134 (0.42 V ~ 0.48 V ) Next step Open<br />
2. CHECK HARNESS AND CONNECTOR (FRONT OXYGEN SENSOR - ECM)<br />
Disconnect the E007 front oxygen sensor.<br />
E007 (1) - E007 (2)<br />
0.45 V<br />
YES > Replace the front oxygen sensor.<br />
3. CHECK HARNESS AND CONNECTOR (FRONT OXYGEN SENSOR - GROUND)<br />
E007 (2) - Ground<br />
04-48<br />
4. CHECK HARNESS AND CONNECTOR (FRONT OXYGEN SENSOR - ECM)<br />
E007 (2) - E001 (47)<br />
E007 (1) - E001 (73)<br />
5. CHECK HARNESS AND CONNECTOR (FRONT OXYGEN SENSOR - GROUND)<br />
Standard resistance (check for short)<br />
E007 (1) - Ground<br />
≥ 1MΩ<br />
04-49<br />
6. CHECK HARNESS AND CONNECTOR (FRONT OXYGEN SENSOR - GROUND)<br />
E007 (4) - Ground<br />
7. CHECK HARNESS AND CONNECTOR (FRONT OXYGEN SENSOR - ECM)<br />
Standard resistance(check for open)<br />
E007 (3) - E001 (24)<br />
04-50<br />
8. CHECK HARNESS AND CONNECTOR (FRONT OXYGEN SENSOR - GROUND)<br />
E007 (3) - Ground<br />
04-51<br />
P0335 - CRANKSHAFT POSITION SENSOR CIRCUIT NO SIGNAL<br />
P0336 - CRANKSHAFT POSITION SENSOR CIRCUIT NOISY SIGNAL<br />
1 Shielded cable<br />
2 Permanent magnet<br />
3 Sensor case<br />
4 Mounting bracket<br />
5 Soft magnet iron core<br />
6 Coil<br />
7 Air clearance<br />
The 58X reference signal is produced by the Crankshaft Position (CKP) sensor. The Engine Control Module<br />
(ECM) uses the 58X reference signal to calculate engine RPM and CKP. The ECM constantly monitors the<br />
number of pulses on the 58X reference circuit and compares them to the number of MAP signal being<br />
received. If the ECM receives and incorrect number of pulses on the 58X reference circuit, DTC P0336 will be<br />
set.<br />
04-52<br />
CKP sensor circuit<br />
noisy signal<br />
• ECM received no or<br />
error signal<br />
• CKP loose connector<br />
• Open or short in CKP sensor<br />
CKP sensor circuit no<br />
signal<br />
• ECM received no signal<br />
04-53<br />
1. READ VALUE AND DTC USING SCAN TOOL<br />
Read CKP sensor value displayed on the KT600 scan tool.<br />
Using scan tool, perform the CKP sensor waveform confirming procedure.<br />
2. CHECK CKP SIGNAL USING THE OSCILLOSCOPE<br />
Using the oscilloscope, check the CKP sensor waveform.<br />
3. CHECK HARNESS AND CONNECTOR (CRANKSHAFT POSITION SENSOR - ECM)<br />
Disconnect the E008 crankshaft position sensor.<br />
E008 (1) - E001 (30)<br />
E008 (2) - E001 (11)<br />
04-54<br />
4. CHECK HARNESS AND CONNECTOR (CRANKSHAFT POSITION SENSOR - GROUND)<br />
(c) Measure the resistance according to the value in the<br />
E008 (3) - Ground<br />
5. CHECK CRANKSHAFT POSITION SENSOR<br />
Replace the CKP sensor with a known good one.<br />
(b) Using the oscilloscope, check the CKP sensor waveform.<br />
YES > Replace the crankshaft position sensor.<br />
6. CHECK HARNESS AND CONNECTOR (CRANKSHAFT POSITION SENSOR - GROUND)<br />
• Standard resistance (check for short)<br />
E008 (1) - Ground<br />
04-55<br />
7. CHECK HARNESS AND CONNECTOR (CRANKSHAFT POSITION SENSOR - GROUND)<br />
8. CHECK CKP SENSOR SIGNAL PLATE<br />
Check for a problem such as scrap, dirt, foreign body<br />
and loose with the 58X CKP signal plate and signal<br />
tooth.<br />
Check the mounting clearance of the CKP sensor.<br />
Clearance: 0.3 ~ 1.5 mm<br />
9. Is the check result normal?<br />
NO > Remove any foreign obstacles, clean 58X signal tooth. If there is fault present, replace 58X signal<br />
plate.<br />
04-56<br />
P0324 - KNOCK SYSTEM FAULT<br />
P0325 - KNOCK SENSOR FAULT<br />
Item<br />
1 1 ms\DIV<br />
The Knock Sensor (KS) system is used to detect engine detonation, allowing the Engine Control Module<br />
(ECM) to retard ignition control spark timing based on the KS signal being received. The KS produces an AC<br />
signal. The KS signal’s amplitude and frequency depend upon the amount of knock being experienced. The<br />
ECM contains a non - replaceable knock filter module called a Signal - to - noise Enhancement Filter (SNEF)<br />
module. This filter module in the ECM determines whether knock is occurring by comparing the signal level on<br />
the KS circuit with the voltage level on the noise channel. The noise channel allows the ECM to reject any false<br />
knock signal by knowing the amount of normal engine mechanical noise present. Normal engine noise varies<br />
depending on engine speed and load. When the ECM determines that an abnormally low noise channel<br />
voltage level is being experienced, DTC P0324 & P0325 will be set.<br />
04-57<br />
Knock system fault<br />
• ECT is higher than 80 ℃<br />
• Engine RPM is higher than<br />
2,500 RPM<br />
• ECM detect that the KS<br />
signal is out of the range<br />
• KS loose connector<br />
• Open or short in KS circuit<br />
Knock sensor fault<br />
• The knock sensor voltage is<br />
below 0.2 V<br />
• Short in KS circuit<br />
04-58<br />
1. READ VALUE OF KT600 SCAN TOOL<br />
Driving vehicle, read knock sensor value displayed on the KT600 scan tool.<br />
Result: Feed back value change<br />
YES > Check intermittent problems.<br />
2. CHECK HARNESS AND CONNECTOR (KNOCK SENSOR - ECM)<br />
Disconnect the E001 knock sensor connector.<br />
E011 (1) - E001 (58)<br />
E011 (2) - E001 (37)<br />
3. CHECK HARNESS AND CONNECTOR (KNOCK SENSOR - GROUND)<br />
E011 (1) - Ground<br />
E011 (2) - Ground<br />
≥ 1 MΩ<br />
04-59<br />
4. CHECK HARNESS AND CONNECTOR (KNOCK SENSOR - GROUND)<br />
Connect the E001 ECM connector.<br />
5 V<br />
YES > Replace the knock sensor.<br />
04-60<br />
Use the table below to help you find the cause of the problem. The numbers indicate thepriority of the likely<br />
cause of the problem. Check each part in order. If necessary, replace these parts.<br />
ENGINE CONTROL SYSTEM SYMPTOM<br />
Symptom<br />
Check Order<br />
Communication with KT600 is impossible KT600 failed to communicate with ECM. 1<br />
Starting<br />
Idling stability (Improper idling)<br />
Idling stability (Engine stalls)<br />
Driving<br />
Engine cranks, but will not start. 2<br />
When engine is cold, it starts difficultly, body shock. 3<br />
Unstable idle (Rough idle, hunting). 4<br />
Idle speed is high (Improper idle speed). 5<br />
When the engine is cold, it stalls (At idle). 6<br />
The engine stalls when accelerating. 7<br />
Accelerated reaction is slow, acceleraton<br />
disturbance.<br />
Poor acceleration capability. 9<br />
8<br />
ENGINE CONTROL SYSTEM SYMPTOM DESCRIPTION<br />
Idling stability<br />
(Improper idling)<br />
(Engine stalls)<br />
Failed to start<br />
Hard starting<br />
Hunting<br />
Incorrect idle speed<br />
Engine will stall when it is cold (Idle)<br />
Engine stalls when moving<br />
Accelerated reaction is slow,<br />
acceleraton disturbance<br />
Poor acceleration capability<br />
The starter is used to crank the engine, but there is<br />
no combustion within the cylinders, and the engine<br />
does not start.<br />
Engine starts after cranking a while.<br />
Engine speed does not remain constant.<br />
The engine does not idle at the usual correct speed.<br />
Engine stall easily when ECT is low after it start for<br />
a while.<br />
The engine stalls when the accelerator pedal is<br />
depressed.<br />
Hesitation is the delay in response of the vehicle<br />
speed that occurs when the accelerator is<br />
depressed in order to accelerate from the speed at<br />
which the vehicle is now traveling or a temporary<br />
drop in vehicle speed during such acceleration.<br />
Serious hesitation is called “sag”.<br />
Poor acceleration is the inability to obtain an<br />
acceleration corresponding to the degree of throttle<br />
opening (Even though acceleration is smooth) or<br />
the inability to reach maximum speed.<br />
04-61<br />
ENGINE SYMPTOM DIAGNOSTIC<br />
• Some symptom diagnostics require visual and outer inspection. Perform these inspections<br />
first. These inspection can select a problem that needn’t check deeply. And it can save the<br />
expensive time.<br />
• Inquiry customer about the fault after taking over vehicle:<br />
(a) The first time when the faults appear.<br />
(b) The engine temperature when the faults appear.<br />
(c) The vehicle roadhaul.<br />
(d) The road which the customer usually drives.<br />
(e) The vehicle maintenace log.<br />
(f) The vehicle maintenace record.<br />
(g) Is there any aftermarket retrofit device on vehicle? After the inspection, the checking time will be<br />
shorted.<br />
• Perform the primary inspection.<br />
(a) Confirm the engine MIL is normal. If it is not good, repair it first.<br />
(b) Confirm that no DTC exists in the ECM. If DTC exists, refer to the DTC chart to eliminate it.<br />
(c) With the scan tool to inspect the engine control system hot data stream. And confirm them in the normal<br />
range.<br />
(d) Confirm the fault and the reason.<br />
(e) When repairing the vehicle, confirm the repair record.<br />
• Visual inspection.<br />
(a) Check the fuel system for any fuel leakage.<br />
(b) Check the vacuum system for any broken, kinked or incorrectly linked vacuum pipes or hoses.<br />
(c) Check the intake air pipe for being jammed, leaking, or damaged.<br />
(d) Check the ignition system for any broken or aging spark plug wires and verify the engine firing order is<br />
correct.<br />
(e) Check the engine ground cable and verify a clean and tight connection.<br />
(f) Check the sensors and actuators electrical connectors and verify good contact and tight connection.<br />
• The carbon deposits in the back of the valve will cause the poor engine acceration, unsteady<br />
idling, starting difficulty in cold temperature, ect.<br />
• Valve, carbon deposits in the combustion chamber.<br />
Determined by the ECI (Electronic Controlled Injection) engine control features, the cylinder carries out<br />
the fuel injection first and then the ignition at each running. The ignition is cut off immediately the engine<br />
is shut off, but the petrol injected in this running cycle can’t be recovered and is attached on the intake<br />
valve and the combustion chamber wall. The petrol is volatile, but the waxes and colloids in the petrol<br />
remain. In the long term, the waxes and colloids become thick and hard after repeatedly heated, so the<br />
carbon deposits are formed. If the engine burns oil or the filled petrol quality is poor and with many<br />
impurities, the valve carbon deposits are more severe and the formation rate is faster. As the carbon<br />
deposit structure is similar to the sponge, after the valve carbon deposits are formed, part of fuel<br />
injected into the cylinder every time will be attached, making the air - fuel mixture strength actually into<br />
the cylinder thin, which causes poor engine running, difficult starting, rough idling, poor accelerating,<br />
backfire during emergency fueling, exhaust exceeding the standards, consumption increasing and<br />
other abnormal symptoms. If the carbon deposits are more severe, they may lead to improperly sealed<br />
valve, and the cylinder can't work without cylinder pressure, or even the valve is adhered and can’t<br />
return. Now the motion interference occurs between the valve and the piston which would damage the<br />
engine finally.<br />
04-62<br />
• Carbon deposits in the intake manifold.<br />
As the running of each piston in the whole engine is not synchronous, when the engine is shut off,<br />
some intake valves in some cylinders can’t be fully closed, the unburned fuel evaporates and is<br />
oxidized continuously thus to form some softer black carbon deposits in the intake pipe, especially at<br />
the rear of the throttle valve. On the one hand, the carbon deposits make the intake pipe wall coarse;<br />
the air forms a spiral vortex at the coarse section, affecting the air intake effect and the quality of air -<br />
fuel mixture. On the other hand, the carbon deposits block the idling aisle, making the idling speed<br />
control device clamped or exceeding its regulation range, leading to low idling speed and rough idling.<br />
• If the carbon deposit in the cylinder is too much, usually it will cause the high pressure. But the<br />
vehicle has more mileage, there is much more carbon deposit in the cylinder. Because of the<br />
wear, the cylinder pressure will decline. So it is not the good way to judge if there is the carbon<br />
deposit in the cylinder . The good way is:<br />
(a) With the electronic endoscopy.<br />
(b) Inspect the feedback voltage.<br />
(c) Disassembly way.<br />
• It’s a gradual process from the carbon deposit formation to aggregation and to affecting engine<br />
normal running. When the engine cold starting is hard and the idling is rough, it shows that the<br />
carbon deposits are quite serious, if further it will cause misfire and cylinder fuel cut, until the<br />
engine unable to start. When the cold starting is hard, check the engine at once, clean the valve<br />
carbon deposits in time after removing other factors to avoid damage caused by removing the<br />
cylinder cover.<br />
• Should pay attention to the following for the danger of the carbon deposit:<br />
(a) Fill with the high quality gasoline.<br />
(b) Don’t idle long.<br />
(c) Run at high speed usually.<br />
04-63<br />
COMMUNICATION WITH KT600 IS IMPOSSIBLE<br />
Symptom Diagnosic Logic Suspect Area<br />
Communication with KT600 is<br />
impossible<br />
1. READ VALUE OF SCAN TOOL<br />
• No power supply<br />
• Open in the harness of ECMand<br />
scan tool KT600<br />
• ECM power supply<br />
• Open in the harness of ECM and<br />
(b) Connect the KT600 scan tool to the Diagnostic Link Connector (DLC) - use the most current software<br />
available, press the POWER key to start the KT600.<br />
(d) Using scan tool, select the item, read data stream.<br />
(e) Using the KT600 scan tool, read data stream displayed on the screen.<br />
Whether the ECM data stream can be read?<br />
2. CHECK DLC COMMUNICATION K<br />
(b) Disconnect the E001ECM connector.<br />
(c) Check the continuity between the data link connector M002 terminal 7 - ECM connector terminal 75.<br />
Resistance:< 2 Ω<br />
(d) Using the multimeter, check the continuity between the data link connector M002 terminal 7 and<br />
ground.<br />
Resistance:≥ 1 MΩ<br />
(e) Turn the ignition switch ON, using the multimeter, check the voltage between data link connector M002<br />
terminal 7 and ground.<br />
Voltage: 0 V<br />
04-64<br />
ENGINE CRANKS, BUT WILL NOT START<br />
Symptom Condition Diagnosic Logic Suspect Area<br />
Engine cranks, but will not<br />
start<br />
• Engine run normally<br />
• Battery is normal<br />
• MIL is normal<br />
• No phenomenon of<br />
burning when cranking<br />
the engine<br />
• Spark plugs are fouled<br />
defective<br />
• No supply of fuel to the<br />
combustion chamber<br />
is defective<br />
• Cylinder pressure is<br />
not normal<br />
• Malfunction of the<br />
ignition system<br />
• Malfunction of the fuel<br />
pump system<br />
injector<br />
• Leakage or<br />
malfunction of intake<br />
air system<br />
If the engine can’t be started with starting symptom, it shows the ignition system, fuel system and<br />
control system don’t fully lose the functions even though work normally. The cause of this starting<br />
failure is nothing but may be that the high tension sparks are too weak, the ignition is improper, the air/<br />
fuel mixture is too thin or thick, or the cylinder pressure is too low. In general, first check the ignition<br />
system, then the air intake system, the fuel system, the control system, the engine cylinder pressure at<br />
last.<br />
1. INSPECTION MIL AND DTC<br />
(a) Using the KT600 scan tool, perform the reading DTC procedure.<br />
Is the DTC present?<br />
2. VISUAL INSPECTION<br />
(a) Perform the visual inspection.<br />
Is the inspection result normal?<br />
NO > Eliminate the exterior problems.<br />
3. CHECK THE SECONDARY IGNITION SYSTEM<br />
(a) Perform the following to test the secondary ignition system:<br />
• Disconnect the injector fuse.<br />
• Remove any of the 4 spark plugs.<br />
• Connect the spark plug to spark plug wire.<br />
• Ground the spark plug on the cylinder block.<br />
• Crank the engine to test the secondary ignition system with the spark plugs removed.<br />
Normal result: A strong blue spark visible is at each spark plug while cranking the engine<br />
YES > Go to step 6.<br />
04-65<br />
4. CHECK THE SECONDARY IGNITION SYSTEM<br />
(a) Check ignitioin coil resistance, and clear connector terminals.<br />
(b) Check whether there is carbon deposit in plug, carbon tracking, residual current in insulating ceramics<br />
cause of crack, clearance, burned in the positive and negative. And clear the plug.<br />
NO > Clear, replace the faulty components.<br />
5. CHECK IGNITION SPARK PLUG WIRE<br />
(a) Using multimeter, check resistance of the ignition spark wire.<br />
Resistance: ≥ 4 kΩ<br />
NO > Replace the ignition spark wire.<br />
6. CHECK CKP SENSOR<br />
(a) Using scan tool, select the item, read data stream.<br />
(b) Read the displayed CKP sensor value. It should be within the specified value.<br />
NO > Check whether the sensor installion is correct.<br />
7. CHECK THE THROTTLE BODY<br />
(a) Depress the accelerator slightly.<br />
(b) Check whether the engine can start.<br />
Can the engine start?<br />
YES > Check throttle body and idle air path. Clear the carbon deposit. Disconnect the idle air control motor<br />
connector, Check whether there is 12 V. And the resistance value is 28 ~ 33Ω when the temperature is<br />
20 ℃ . Check whether the idle air control motor is clip. If necesasary, repair or replace it.<br />
The carbon and grease beside the throttle and air path change the cross section of the idle air path. It<br />
makes the ECM control the idle air impossilly. And it will cause the A/F too lean or too rich. The<br />
borning will not be normal. And the usual reasons of unnormal borning are: carbon and grease, grease<br />
beside the throttle air path, carbon and grease with the idle air control motor.<br />
8. CHECK ECT SENSOR AND MAP/IAT SENSOR<br />
(a) Check whether the installation of the MAP/IAT is normal.<br />
(b) Check whether the MAP/IAT sensor is dirty.<br />
(c) Using scan tool, select the item, read data stream.<br />
(e) Read the displayed ECT and MAP/IAT sensor value. It should reach the specified value.<br />
NO > Repair or replace the harness or connector.<br />
04-66<br />
9. CHECK THE FUEL SYSTEM CIRCUIT<br />
(b) Check whether the pump relay and pump operate normally.<br />
10. CHECK THE FUEL SYSTEM PRESSURE<br />
(a) Release the fuel system pressure. (Refer to “Chapter 12A fuel system - precaution”)<br />
(b) Check the fuel system pressure. (Refer to “Chapter 12A fuel system - precaution”)<br />
NO > Repair or replace the fuel system parts and harness:<br />
• If the pressure is higher than 350 kPa, check the return pipe:<br />
(1) If the return pipe is bent or twisted, repair or replace it.<br />
(2) If the return pipe is normal, replace the pressure regulator.<br />
• If the pressure is less than 350 kPa, turn the ignition switch ON, make the pump operate, check<br />
the pressure again:<br />
(1) If the pressure can be established, go to step 12.<br />
(2) If the pressure cannot be established, go to step 13.<br />
11. CHECK INJECTOR<br />
(a) Disconnect the injector connector.<br />
(b) Remove the injector and fuel rail assy.<br />
(c) Apply 12 V battery voltage to the injector directly.<br />
(d) Check whether every injector can spray even and standard quantity gasline.<br />
If the spraying condition is not normal just as the “cylindrical growth”, or the spraying quantity is not<br />
equal much more under the same condition (more than 5 ml), then replace the injector.<br />
When check the fuel system:<br />
• Place a “Caution - No inflammable” symbol inside the operation area.<br />
• Never smoke while servicing the vehicle.<br />
• Service vehicles in well - ventilated areas and avoid ignition sources.<br />
• Release fuel system pressure before servicing fuel system components.<br />
YES > Go to step14.<br />
NO > Clear the injector. Check the injector operation condition again. If not OK, replace it. Confirm the fault is<br />
not present. If not OK, go to next step.<br />
04-67<br />
12. CHECK FUEL SYSTEM RETURN<br />
(a) Using the fuel return blocker, clamping the return pipe, make the system fuel can not return.<br />
(b) Check whether the system pressure can establish again quickly.<br />
YES > Replace the fuel pressure regulation.<br />
NO > Repair or replace the fuel supply pipe, pump or injector.<br />
13. CHEKC FUEL SYSTEM SUPPLY<br />
Check whether the input pipe leakage or block.<br />
Running the engine, Check connectors for fuel leaks as following:<br />
(b) Turn the ignition switch ON (Do not start the engine). Apply pressure on the fuel pipe. Check whether<br />
fuel leaks at fuel pipe connection.<br />
YES > Repair or replace the inlet fuel pipe.<br />
NO > Replace fuel pump.<br />
14. CHECK CYLINDER PRESSURE<br />
(a) Perform the cylinder compression pressure test. The standard as following:<br />
• Per cylinder pressure: 1270 kPa<br />
• Per cylinder limit: 880 kPa<br />
• Per cylinder difference limit: less than 25%<br />
YES > Go to step16.<br />
15. CHECK ENGINE VALVE - TIMING<br />
(a) Check whether the engine valve - timing gear mark is aligned, damaged. And the belt is loose. Whether<br />
the jumping over teeth exists.<br />
NO > Perform the valve timing align operation.<br />
16. CHECK ENGINE MECHANISM<br />
(a) Perform the engine mechanism inspection:<br />
• Check the cylinder with the endoscopy.<br />
• Inspect the feedback voltage.<br />
• Disassembly the engine inner faults.<br />
NO > Repair the engine inner mechanism faults.<br />
04-68<br />
ENGINE STARTS DIFFICULTILY WHEN IT IS COLD<br />
Engine starts difficultily<br />
when it is cold (idle)<br />
• Engine runs normally<br />
• It needs several times<br />
for engine starts<br />
successfully when it is<br />
cold<br />
1. A/F is not correct<br />
2. Carbon deposit at<br />
valve<br />
3. Operation condition is<br />
not equal between<br />
every cylinder<br />
4. ECT sensor is fault<br />
5. Others:<br />
• MAP/IAT sensor<br />
• Idle step motor<br />
• Fuel quality<br />
• Supply fuel system<br />
• Leakage of the inlet<br />
system<br />
• Cylinder compression<br />
pressure<br />
• Engine management<br />
Hard engine starting refers to that the starter is able to drive the engine to run in normal speed with<br />
clear starting symptom, but the engine only run after continuous starting or the starter driving for a<br />
long time. For the failure of hard starting, determine whether the occurrence is in cold starting or hot<br />
starting, or both of them. The cause of this failure is from the fuel injection system generally. Check it<br />
in the following method.<br />
1. CHECK ENGINE MIL AND DTC<br />
YES > Refer to DTC chart. Perform the diagnostic procedure.<br />
2. CHECK THE VISUAL INSPECTION<br />
(b) Check following after opening the engine hood:<br />
• Air filter.<br />
• Leakage of the intake manifold.<br />
3. CHECK BATTERY<br />
(a) Check the battery voltage when cranking the engine.<br />
Battery voltage: ≥ 9.6 V<br />
NO > Charge or replace battery.<br />
04-69<br />
4. CHECK STARTER<br />
(a) Check whether the starter or the starter circuit exist fault.<br />
5. CHECK CKP SENSOR<br />
(b) Read the displayed CKP sensor value.<br />
6. CHECK ECT SENSOR<br />
(b) With the multimeter to check the ECT sensor or feedback voltage. (or with a 1.5 kΩ resistance, replace<br />
the ECT sensor. Start engine. If OK, it means that the ECT sensor isnot normal).<br />
NO > Replace the ECT sensor.<br />
7. CHECK MAP SENSOR<br />
(a) Check MAP sensor after starting engine successfully.<br />
Pressure value: 35 ~ 55 kPa<br />
NO > Eliminate the leakage of intake system.<br />
8. CHECK THROTTLE BODY<br />
(a) Depress the accelerator slightly. Start egnine.<br />
NO > Go to step 10.<br />
makes the ECM control the idle air impossilly. And it will cause the A\F too lean or too rich. The borning<br />
will not be normal. And the usual reasons are: carbon and grease, grease beside the throttle air<br />
path, carbon and grease with the idle air controlmotor.<br />
9. CHECK IDLE AIR CONTROL MOTOR<br />
(a) Disconnect the idle air control motor connector. Check whether there is 12 V. And the resistance value<br />
is 28 ~ 33 Ω when the temperature is 20 ℃ .<br />
(b) Remove the idle air control motor to test:<br />
• Check expansion of the idle air control motor when turning the ignition switch ON.<br />
• Check whether the idle air control motor can move when turning the ignition switch OFF.<br />
04-70<br />
NO > Repair or replace the idle control motor.<br />
10. CHECK ECT SENSOR AND MAP/IAT SENSOR<br />
(d) Turn the ignition switch ON. Read the displayed ECT and MAP/IAT sensor value.<br />
NO > Replace the MAP/IAT sensor.<br />
11. CHECK THE FUEL SYSTEM PRESSURE<br />
(a) Release the fuel system pressure.<br />
(b) Check the fuel system pressure.<br />
12. CHECK INJECTOR<br />
(a) Remove the injector connector.<br />
If the spraying condition isnot normal just as the “cylindrical growth”, or the spraying quantity is not<br />
YES > Go to step15.<br />
NO > Clean the injector. Check the injector operation condition again. If not OK, replace it. Confirm the fault<br />
isnot present. If not OK, go to next step.<br />
04-71<br />
13. CHECK FUEL SYSTEM RETURN<br />
Using the fuel return blocker, and clamping the return pipe, make the system fuel not return.<br />
Check whether the system pressure can establish again quickly.<br />
14. CHEKC FUEL SYSTEM SUPPLY<br />
Check whether the input pipe leaks or block.<br />
(b) Turn the ignition switch ON (not crank the engine). Apply pressure on the fuel pipe. Check whether fuel<br />
leakage at fuel pipe connection.<br />
15. CHECK THE SECONDARY IGNITION SYSTEM<br />
YES > Go to step18.<br />
16. CHECK THE SECONDARY IGNITION SYSTEM<br />
(b) Check whether there is carbon deposit in plug, carbon tracking,residual current in insulating ceramics<br />
17. CHECK IGNITION SPARK PLUG WIRE<br />
(a) With multimeter, check resistance of the ignition spark wire.<br />
Resistance:≥ 4 kΩ<br />
04-72<br />
18. CHECK CYLINDER PRESSURE<br />
YES > Go to step 20.<br />
19. CHECK ENGINE VALVE - TIMING<br />
(a) Check whether the engine valve - timing gear mark is aligned, damaged and the belt is loose.<br />
NO > Perform the valve timing align operation or replace the timing belt.<br />
20. CHECK ENGINE MECHANISM<br />
• Disassembly the engine.<br />
• Clear the carbon deposit or remove and check the engine cylinder head.<br />
• Check valves, carbon deposit of manifold. For example: the clearance between the cylinder and the<br />
piston ring. The leakage of the cylinder gasket, and loose of the valve guides, carbon deposit of the<br />
valve.<br />
04-73<br />
UNSTABLE IDLE<br />
Unstable idle (Rough idle,<br />
hunting)<br />
The engine cannot keep<br />
stability<br />
• The ignition system,<br />
air - fuel.<br />
• Air ratio<br />
• IAC motor<br />
is too low<br />
• Malfunction of air - fuel<br />
ratio control system<br />
• Malfunction of the IAC<br />
• Poor compression<br />
• Drawing air into intake<br />
The unstable idle is the usually faulty. It has many kinds of types. It includes unstable, misfire, etc.<br />
When performing the diagnosis and elimination, should analyse according to the specific symptom.<br />
YES > Refer to DTC chart. Perform the diagnosis procedure.<br />
(b) Check after opening the engine hood:<br />
(c) Inspect the engine operating condition.<br />
(d) Inspect the tachometer if the pointer deviates the idle target value.<br />
(e) Inspect if the idle trembles is normal or load reasons, such as: A/C, lighting, push the lever into gear,<br />
turn the steering wheel, etc.<br />
(f) Check the vacuum system for any broken, kinked or incorrectly linked vacuum pipes or hoses.<br />
(g) Check whether the exhaust pipe emit black smoke.<br />
(h) Check whether there is unburned petrol fumes.<br />
(i) Check whether the throttle cable is adjusted to be appropriate.<br />
3. CHECK THE THROTTLE AND IDLE CONTROL MOTOR<br />
(a) Check throttle body and idle air path. Clear the carbon deposit and greasy dirt.<br />
(b) Start engine and runs at idle.<br />
(c) Using scan tool, select the item, active test.<br />
(d) Perform the idle air control motor test.<br />
• When the scan tool control the rotation of expansion of the idle air control motor, the engine RPM<br />
changes from high to low in synchronism (touching the idle air control motor, can feel vibration).<br />
04-74<br />
(e) Disconnect the idle air control motor connector, Check whether there is 12 V. And the resistance value is<br />
28 ~ 33 Ω when the temperature is 20 ℃ . Check whether the idle air control motor is clip. If necesasary,<br />
repair or replace it.<br />
(f) Remove the idle air control motor . Connect the connector:<br />
• Check whether the idle air control motor can extend - retract when turning the switch off.<br />
• Check whether the idle air control motor can move when turning the ignition switch on.<br />
NO > Repair or replace idle control motor.<br />
4. CHECK ENGINE IGNITION SYSTEM<br />
(a) Engine runs at idle speed.<br />
(b) Brennschluss one by one.<br />
(c) Inspect if the idle speed changes.<br />
It is better that use the active test function of the scan tool to perform the brennschluss test. If without<br />
the scan tool or the scan tool wirhout the function, the brennschluss period shoul not be too long, if<br />
not, the Three Way Catalytic Converter (TWC) will be damaged.<br />
(d) When brennschluss every cylinder, the same RPM should decline obviously or the same vibration.<br />
YES > Go to step12.<br />
5. CHECK THE SECONDARY IGNITION SYSTEM<br />
• Connect the spark plug to spark plug wire. Ground the spark plug on the cylinder block.<br />
• Start the engine to test the secondary ignition system with the spark plugs removed.<br />
normal result: A strong blue spark visible is at each spark plug while cranking the engine<br />
YES > Go to step 8.<br />
6. CHECK THE SECONDARY IGNITION SYSTEM<br />
(a) Check secondary ignition wire resistance. And clear the connector terminals.<br />
NO > Replace the faulty components.<br />
04-75<br />
7. CHECK IGNITION SPARK PLUG WIRE<br />
With multimeter, check resistance of the ignition spark wire.<br />
8. CHECK THE INJECTOR<br />
(a) Using scan tool, select the item, active test.<br />
(b) Perform the injector active test.<br />
(c) Check whether the same engine RPM decline obviously and shortly in synchronism (touching the injector,<br />
can feel vibration, or with the voice - tool, touch the injector, the action voice should be hearded).<br />
NO > Repair, clear or replace harness or connectors. Every injector can spray even and standard quantity<br />
gasoline. If not OK, replace it.<br />
If the spraying condition isnot normal just as the “cylindrical growth”, or the 4 injectors spraying quantity<br />
is not equal much more under the same condition (more than 5 ml), then replace the injector.<br />
9. CHECK THE FUEL SYSTEM PRESSURE<br />
04-76<br />
10. CHECK FUEL SYSTEM RETURN<br />
Using the fuel return blocker and clamping the return pipe, make the system fuel not return.<br />
11. CHEKC FUEL SYSTEM SUPPLY<br />
Check connectors for fuel leakage as following:<br />
(b) Turn the ignition switch ON (Do not start the engine).<br />
(c) Apply pressure on the fuel pipe.<br />
(d) Check whether fuel leaks at fuel pipe connection.<br />
12. CHECK INTAKE AND EXHAUST SYSTEM<br />
(d) Check the sensors and actuators electrical connectors and verify good contact and tight connection.<br />
(e) Check the PCV valve.<br />
(f) Check whether the EVAP system leakage.<br />
(g) Checkif the fuel pressure regulator vacuum pipe broken, kinked or crack.<br />
(h) Check whether the Three - Way Catalytic Converter (TWC) is blocked.<br />
(i) Check whether the throttle body gasket leakage.<br />
(j) Check whether the intake manifold gasket leakage.<br />
NO > Repair or replace the faulty components.<br />
13. CHECK MAP/IAT SENSOR<br />
(a) Check whether the installation of the MAP/IAT is normal?<br />
(b) Remove the MAP/IAT sensor.<br />
(c) Check whether the MAP/IAT sensor is dirty.<br />
(e) Read the scan tool displaied MAP/IAT sensor data stream value.<br />
(f) With the 3 kinds of the basic types: idle tets, accerlerate suddenlly test and blocked test in exhaust<br />
system. Test the vaccum rate in the intake manifold.<br />
NO > Clear and reinstall or repair. If not OK, go to step 15.<br />
04-77<br />
14. CHECK OXYGEN SENSOR<br />
(a) Engine idle.<br />
(b) Inspect the displayed scan tool data stream.<br />
(c) When the temperature is normal after the engine enter into the closed - loop control, inspect if the<br />
oxygen sensor operate normally.<br />
Oxygen Sensor Normal Value: 0 ~ 1 V. Change 5 ~ 8 times in 10 seconds periodically.<br />
NO > Replace xoygen sensor harness or connector.<br />
15. CHECK CYLINDER PRESSURE<br />
• Per cylinder pressure: 1270 kPa.<br />
• Per cylinder limit: 880 kPa.<br />
• Per cylinder difference limit: less than 25%.<br />
YES > Go to step17.<br />
16. CHECK ENGINE VALVE - TIMING<br />
17. CHECK ENGINE MECHANISM<br />
(b) Check the cylinder with the endoscopy.<br />
(c) Inspect the feedback voltage.<br />
(d) Disassembly the engine inner faults.<br />
(e) Clear the carbon deposit or remove and check the engine cylinder head.<br />
(f) Check valves, carbon deposit of manifold. For example: the clearance between the cylinder and the<br />
04-78<br />
IDLE IS TOO HIGH<br />
Idle is too high (The<br />
engine does not idle at the<br />
usual correct speed)<br />
Engine idle speed too<br />
high<br />
The cause is probably that the<br />
intake air volume during idle<br />
is too great<br />
• Malfunction of the Idle<br />
air control motor<br />
throttle body<br />
• Inspect the engine operating condition.<br />
• Inspect the tachometer if the pointer deviates the idle target value.<br />
• Inspect if the idle trembles is normal or load reasons, such as: A/C, lighting, push the lever into gear,<br />
• Check the vacuum system for any broken, kinked or incorrectly linked vacuum pipes or hoses.<br />
• Check whether the exhaust pipe emit black smoke.<br />
• Check whether there is unburned petrol fumes.<br />
• Check whether the throttle cable is adjusted to be appropriate.<br />
3. CHECK THE ACCELERATOR PEDAL<br />
(a) Check whether the accelerator pedal cable blocked.<br />
NO > Adjust or replace the accelerator cable.<br />
4. CHECK RELATED ACCESSORIES<br />
(a) Check EVAP.<br />
(b) Check the fuel pressure vacuum regualtor.<br />
(c) Check whether the PCV vacuum pipe installation is reliable.<br />
(d) Check whether the braking system vacuum booster pipe installation is reliable.<br />
NO > Adjust or replace.<br />
04-79<br />
5. CHECK IDLE<br />
(b) Gear in N position.<br />
(c) Depress brake pedal.<br />
(d) Inspect if the idle speed is too high.<br />
NO > Go to step 7.<br />
6. CHECK THE VACUUM BOOSTER<br />
(a) Blocking the vacuum pipe, inspect if the idle become normal.<br />
NO > Repair or replace the vacuum booster.<br />
7. CHECK PCV VALVE<br />
(a) Clipping the PCV vacuum pipe, inspect if the idle become normal.<br />
(b) Check whether the PCV valve clip. If the opening degree is normal.<br />
NO > Replace PCV valve.<br />
8. CHECK IDLE AIR CONTROL MOTOR<br />
(a) Start engine and runs at idle.<br />
(b) Using scan tool, select the item, active test.<br />
(c) Perform the idle air control motor test:<br />
• Disconnect the idle air control motor connector, Check whether there is 12 V. And the resistance value is<br />
28 - 33 Ω when the temperature is 20 ℃ .<br />
(d) Remove the idle air control motor to test:<br />
NO > Replace the idle control motor.<br />
9. CHECK THE INTAKE SYSTEM<br />
(a) Check the vacuum system for any broken, kinked or incorrectly linked vacuum pipes or hoses.<br />
(b) Check the intake air pipe for being jammed, leaking, or damaged.<br />
NO > Repair or replace vacuum pipes.<br />
04-80<br />
(a) Check whether the installation of the MAP/IAT sensor is normal?<br />
(d) Turn the ignition switch ON. Read the displayed ECT and MAP/IAT value. It should be within the specified<br />
value.<br />
YES > Go to step13.<br />
NO > Repair or replace related components of fuel system.<br />
YES > Replace the injector washer.<br />
NO > Clean or replace the injectpor.<br />
04-81<br />
WHEN THE ENGINE IS COLD, IT STALLS<br />
When the engine is cold,<br />
it stalls (At idle)<br />
The cause is probably<br />
that the air/fuel mixture is<br />
inappropriate when the<br />
engine is cold, or that the<br />
intake air<br />
volume is insufficient.<br />
that the intake air volume<br />
during idle is too great<br />
• Check whether the exhaust pipe emit black smoke. Check whether there is unburned petrol fumes.<br />
3. CHECK THE THROTTLE AND IDLE AIR CONTROL MOTOR<br />
makes the ECM control the idle air impossilly. And it will cause the A/F too lean or too rich. The borning<br />
(b) Start engine and run at idle.<br />
(d) Perform the idle air control motor test:<br />
(e) When the scan tool control the rotation of expansion of the idle air control motor, the engine RPM<br />
04-82<br />
(f) Disconnect the idle air control motor connector, Check whether there is 12 V. And the resistance value is<br />
28 - 33 Ω when the temperature is 20 ℃ . Check whether the idle air control motor is clip. If necesasary,<br />
NO > Clean, repair or replace idle control motor.<br />
4. CHECK THE ECT SENSOR<br />
(a) Check the resistance accord with the standard:<br />
20 ℃ : 2.1 ~ 2.7 kΩ<br />
80 ℃ : 0.26 ~ 0.36 kΩ<br />
(b) Using scan tool, select the item, read the data stream.<br />
5. CHECK THE IAT SENSOR<br />
20 ℃ : 2.3 ~ 3.0 kΩ<br />
80 ℃ : 0.3 ~ 0.42 kΩ<br />
NO > Replace the IAT sensor.<br />
6. CHECK THE INJECTOR<br />
gasline. If not OK, replace it.<br />
04-83<br />
7. CHECK THE FUEL SYSTEM PRESSURE<br />
Release the fuel system pressure.<br />
YES > Go to step 10.<br />
(1) If the pressure can be established, go to step 8.<br />
(2) If the pressure cannot be established, go to step 9.<br />
8. CHECK FUEL SYSTEM RETURN<br />
(a) Using the fuel return blocker and clamping the return pipe, make the system fuel not return.<br />
9. CHEKC FUEL SYSTEM SUPPLY<br />
Check connectors for fuel leaks as following:<br />
YES > Repair or replace the intake fuel pipe.<br />
NO > Replace the fuel pump.<br />
10. CHECK CYLINDER PRESSURE<br />
YES > Go to step 12.<br />
04-84<br />
11. CHECK ENGINE VALVE - TIMING<br />
NO > Perform the valve timing align operation or replace timing belt.<br />
12. CHECK ENGINE MECHANISM<br />
NO > Repair the engine mechanism faults.<br />
04-85<br />
THE ENGINE STALLS WHEN ACCELERATING<br />
The engine stalls when<br />
accelerating<br />
the accelerator pedal is<br />
depressed<br />
• Poor power when starting<br />
• Malfunction of the Idle air<br />
control motor<br />
• Malfunction of the throttle<br />
body<br />
• Malfunction of the injector<br />
• Malfunction of the ignition<br />
Start in idling mode: Put into gear without pressing the accelerator pedal, disengage the clutch and<br />
start the engine. This moment, as the throttle valve is closed and the idling electric shock is closed,<br />
ECM considers it as the idling mode. The control of idling mode is a cruise control without any load<br />
signal, namely a steady speed control that the engine is controlled in target speed range. Speed -<br />
raising control is done if with load signal. During starting, the load signal is input into ECM, the later<br />
raises the engine speed, enhances the dynamic property and keeps the idling from the effect of load.<br />
This moment the starting is smoothly and hard to be shut off generally. If the starting is wobbled and<br />
easy to be shut off and the speed falls in idling mode, find the causes from the idling control.<br />
04-86<br />
(e) Disconnect the idle air control motor connector, Check whether there 12 V exists. And the resistance value<br />
is 28 - 33 Ω when the temperature is 20 ℃ . Check whether the idle air control motor is clip. If necesasary,<br />
(f) Remove the idle air control motor. Connect the connector:<br />
NO > Clear, repair or replace idle control motor.<br />
04-87<br />
4. CHECK THROTTLE POSITION<br />
With the scan tool, check whether the throttle is normal.<br />
(b) Check whether the throttle open degree is normal when depressing the accelerator pedal.<br />
NO > Adjust the throttle position.<br />
5. CHECK THE LOAD SIGNAL<br />
(a) Check whether the gear signal is sent to ECM.<br />
(b) Check whether the A/C signal is sent to ECM.<br />
(c) Check whether the load signal is sent to ECM.<br />
6. CHECK THE IGNITION SYSTEM<br />
(b) Cut off spark plug wire one by one.<br />
It is better that use the active test function of the scan tool to perform the cutoff test. If without the<br />
scan tool or the scan tool wirhout the function, the brennschluss period shoul not be too long, if not,<br />
the TWC will be damaged.<br />
7. CHECK THE SECONDARY IGNITION SYSTEM<br />
04-88<br />
8. CHECK THE SECONDARY IGNITION SYSTEM<br />
Check secondary ignition wire resistance. And clean the connector terminals.<br />
9. CHECK IGNITION SPARK PLUG WIRE<br />
10. CHECK THE INJECTOR<br />
NO > Repair or replace injector<br />
If the spraying condition is not normal just as the “cylindrical growth”, or the 4 injectors spraying<br />
quantity is not equal much more under the same condition (more than 5 ml), then replace the injector.<br />
04-89<br />
NO > Repair or replace the fuel supply pipe, pump, injector.<br />
leaks at fuel pipe connection.<br />
YES > Go to step 16.<br />
• Clear the carbon deposit or remove and check the engine cylinder head. Check valves, carbon deposit<br />
of manifold. For example: the clearance between the cylinder and the piston ring. The leakage of the<br />
cylinder gasket, and loose of the valve guides, carbon deposit of the valve.<br />
04-90<br />
ACCELERATED REACTION IS SLOW, ACCELERATON DISTURBANCE<br />
Accelerated reaction is<br />
slow, acceleraton<br />
disturbance<br />
When the accelerator is<br />
depressed in order to<br />
accelerate from the<br />
speed, the vehicle is now<br />
traveling or a temporary<br />
drop in vehicle speed<br />
during such acceleration.<br />
that ignition system, air -<br />
fuel mixture or<br />
compression pressure is<br />
• Malfunction of fuel<br />
supply system<br />
3. CHECK THE AIR FILTER<br />
(a) Check whether the air filter dirty, grease and blocked.<br />
NO > Clean or replace the air filter.<br />
4. CHECK IDLE<br />
Start engine and runs at idle.<br />
Check whether the idle speed is normal.<br />
04-91<br />
NO > Refer to the symptom chart, eliminate the problems.<br />
5. CHECK MAP/IAT SENSOR<br />
(e) Read the scan tool displayed MAP/IAT sensor data stream value.<br />
6. CHECK TPS<br />
(b) With the analogue mulitimeter to check TPS resistance (resistance should be continuity).<br />
(c) Refer to engine DTC chart.<br />
NO > Repair or replace the throttle position sensor.<br />
7. CHECK FUEL SYSTEM PRESSURE<br />
(1) If the pressure can be established, go to step 9.<br />
(2) If the pressure cannot be established, go to step 10.<br />
8. CHECK INJECTOR<br />
04-92<br />
YES > Go to step 11.<br />
NO > Repair or replace the injector.<br />
9. CHECK FUEL SYSTEM RETURN<br />
NO > Repair or replace the fuel supply pipe, pump and injector.<br />
10. CHEKC FUEL SYSTEM SUPPLY<br />
(b) Turn the ignition switch ON (not crank the engine).<br />
(d) Check whether fuel leakage at fuel pipe connection.<br />
11. CHECK EXHAUST SYSTEM<br />
(a) Check the exhaust system and Three - Way Catalytic Converter (TWC).<br />
(b) Check whether the exhaust pipe blocked with the exhaust pressure meter.<br />
NO > Replace or clean the exhaust system.<br />
12. CHECK CYLINDER PRESSURE<br />
YES > Go to step 14.<br />
04-93<br />
13. CHECK ENGINE VALVE - TIMING<br />
(a) Check whether the engine valve - timing gear mark is aligned, damaged. And the belt is loose.<br />
14. CHECK ENGINE MECHANISM<br />
• Disassembly the engine faults.<br />
YES > Repalce the ECM.<br />
04-94<br />
POOR ACCELERATION<br />
Poor Acceleration<br />
Poor acceleration is the<br />
inability to obtain an<br />
acceleration corresponding<br />
to the degree of throttle<br />
opening (even though<br />
acceleration is smooth) or<br />
the inability to reach<br />
maximum speed<br />
Defective ignition system,<br />
abnormal air - fuel ratio, poor<br />
compression, etc are<br />
suspected.<br />
• Poor acceleration<br />
• Clogged exhaust<br />
(a) Using the KT600 scan tool, perform the reading DTC procedure. (Refer to ”Chapter 04 engine control<br />
system - read and clear DTC”)<br />
2. CHECK VISUAL INSPECTION<br />
3. CHECK THROTTLR POSITION SENSOR<br />
(b) With the analogue mulitimeter to check throttle position sensor resistance (resistance should be<br />
continuity).<br />
04-95<br />
4. CHECK MAP/IAT SENSOR<br />
5. CHECK THE FUEL SYSTEM PRESSURE<br />
(1) If the pressure can be established, go to step 7.<br />
(2) If the pressure cannot be established, go to step 8.<br />
6. CHECK INJECTOR<br />
YES > Go to step 9.<br />
NO > Clean or replace the injector.<br />
04-96<br />
7. CHECK FUEL SYSTEM RETURN<br />
(a) Using the fuel return blocker and clamping the return pipe, make the system fuel not return. Check<br />
whether the system pressure can establish again quickly.<br />
8. CHEKC FUEL SYSTEM SUPPLY<br />
9. CHECK THE SECONDARY IGNITION SYSTEM<br />
10. CHECK THE SECONDARY IGNITION SYSTEM<br />
04-97<br />
11. CHECK IGNITION SPARK PLUG WIRE<br />
04-98<br />
DIAGNOSTICS - ANTI - LOCK BRAKE SYSTEM<br />
ANTI - LOCK BRAKE SYSTEM<br />
1. ELECTRONIC CONTROL.<br />
(a). Before removing or installing any electrical device, please disconnect the negative cable to<br />
prevent damage to the device or personal injury.<br />
(b).<br />
Make sure ignition switch is OFF if no specific instructions.<br />
If equipped with central locking, do not leave ignition switch in the car before disconnecting the<br />
battery negative cable.<br />
2. REMOVE INSTRUMENT CLUSTER OR DISCONNECT THE NEGATIVE CABLE WILL RESULT IN<br />
LOSS OF DATA.<br />
Total odometer will not be cleared.<br />
3. WHEN THE BATTERY TERMINAL IS REMOVED, ALL THE MEMORIES OF THE CLOCK, RADIO,<br />
DTCS, ETC. WILL BE ERASED. SO BEFORE REMOVING IT, CHECK THEM AND NOTE THEM<br />
DOWN.<br />
When service is finished, reset the clock and audio systems.<br />
4. EXPRESSIONS OF IGNITION SWITCH.<br />
5. NOTES ABOUT ANTI - LOCK BRAKE SYSTEM.<br />
(a) The system will resumes its normal state temporarily or competely by removing and reinstalling the<br />
suspicious faulty components when the connector terminals or the installing state of the components go<br />
(b) In order to identify the faulty position, we must check the vehicle condition while vehicle goes out of<br />
order. For example, we check the faults through the DTC. And we record these fault states before<br />
(c) The sensor and ABS module can be removed or installed with the ignition switch in OFF position.<br />
(d) After repairing the anti - lock brake system is completed, check the ABS warning light.<br />
(e). Never use the multimeter to measure the terminal of ABS module.<br />
(f). The ABS system must be repaired by technicians trained and mastered maintenance<br />
skills, and only use original parts for replacement.<br />
(g). Before repairing the ABS system, if there are some failures with mechanical braking<br />
system, must be excluded. Such as:<br />
• Brake system noise.<br />
• Brake pedal is excellent.<br />
• Brake pedal or vehicle vibration when pressing pedal.<br />
04-99<br />
• Vehicle deviation.<br />
• Parking brake system failure.<br />
(h). ABS control module (refer to the ABS electronic control unit and hydraulic control unit, not<br />
including brake lines, sensors ,etc.) can only be replaced as assembly, can not be<br />
overhauled or part replacement / swap.<br />
(i). The following two cases show that ABS system failure is detected:<br />
• Turn the ignition switch On, the system self - test is completed, but the warning light<br />
is on.<br />
• The warning light is always on when driving the vehicle.<br />
The driver can stop the vehicle conventionally, but it should be as far as possible to reduce the<br />
braking force to prevent the wheels from locking. Warning lamp lights need to be careful driving<br />
and immediately to the authorized service station overhaul to prevent more failures occurred,<br />
resulting in a traffic accident.<br />
(j). Pay attention to the following points when connect the ABS system connector:<br />
• Turn the igintion OFF before disconnecting ABS wiring harness and connector.<br />
• Ensure that the connector dry and clean, to avoid any foreign objects to enter.<br />
• ABS harness connector is installed in place, must be in the horizontal direction and<br />
a vertical direction to avoid damage to the connectors.<br />
(k). Ensure proper connection when connectiong the ABS system pipes. ABS control module<br />
can not detect that the brake lines are connected properly or not. The error connection<br />
may lead to a serious accident. Connecting the brake lines, must be in compliance with<br />
the ABS assembly on the mark:<br />
• MC1: Brake line 1 connected to the brake master cylinder.<br />
• MC2: Brake line 2 connected to the brake master cylinder.<br />
• FL: Brake line connected the wheel cylinders FL.<br />
• FR: Brake line connected the wheel cylinders FR.<br />
• RL: Brake line connected the wheel cylinders RL.<br />
• RR: Brake line connected the wheel cylinders RR.<br />
(l). There are noise with ABS system in the following cases:<br />
• Vehicle power or start the engine, it will produce a short sound of "Om", this is a<br />
normal phenomenon with the sound of the ABS self - check..<br />
• There will be sound when ABS system work properly, mainly reflected in the<br />
following:<br />
1) Sound made by ABS hydraulic unit motor, solenoid valve and the reflux pump.<br />
2) Sound caused by brake pedal rebounding.<br />
3) Emergency brake caused the crash of the suspension and the body.<br />
04-100<br />
1 Front Brake Pipe RH<br />
2 ABS Control Module<br />
3 Front Brake Pipe LH<br />
4 Rear Brake Pipe LH<br />
5 Rear Brake Pipe RH<br />
04-101<br />
ABS MODULE CONNECTOR<br />
No. Wiring Color Difinition<br />
1 R ABS motor power input<br />
2 - -<br />
3 Y - R EBD warning ligh output<br />
4 L Front sensor signal RH<br />
5 - -<br />
6 R - L Dinostic connector K<br />
7 - -<br />
8 W Front sensor signal LH<br />
9 - -<br />
10 - -<br />
11 - -<br />
12 - -<br />
13 W - B ABS motor ground<br />
14 - -<br />
15 - -<br />
16 G<br />
17 P<br />
Front sensor power<br />
suppy RH<br />
Rear sensor power<br />
18 L - G Rear sensor signal LH<br />
19 B<br />
suppy LH<br />
20 - -<br />
21 - -<br />
22 - -<br />
23 - -<br />
24 - -<br />
25 R - W<br />
ABS solenoid valve<br />
power suppy input<br />
26 - -<br />
27 Y - G ABS warning ligh output<br />
28 R - W ABS - IG input<br />
29 LG Rear sensor signal RH<br />
30 G - W Brake signal<br />
31 Y - W<br />
32 - -<br />
33 - -<br />
34 - -<br />
35 - -<br />
36 - -<br />
37 - -<br />
38 W - B ECU ground<br />
04-102<br />
If a malfunction code is displayed during the DTC checking, check the circuit listed below. For details<br />
of each code, turn to the relevant troubleshooting page in the DTC chart.<br />
DTC No.<br />
C190004<br />
C190104<br />
C100004<br />
C101008<br />
C006B06<br />
C003108<br />
C003200<br />
C00A000<br />
C00A100<br />
C00A900<br />
C003408<br />
C003500<br />
C00A200<br />
C00A300<br />
C00AA00<br />
C003708<br />
C003800<br />
C00A400<br />
C00A500<br />
C00AB00<br />
C003A08<br />
C003B00<br />
C00A600<br />
C00A700<br />
C00AC00<br />
ECU Power Suppy High<br />
ECU Power Suppy Low<br />
Detection Item (DTC Definition)<br />
ECU Malfunction (Hardware, Central Controller Error)<br />
ECU Malfunction (Software Error)<br />
Abs Control Is Unreasonable (Controling Time Too Long)<br />
Front Wheel Speed Sensor LH Output Signal Malfunction: Beyond The Scope Of Loss,<br />
Noise, Intermittent Interruption<br />
Front Wheel Speed Sensor LH Wiring Malfunction: Open<br />
Front Wheel Speed Sensor LH Wiring Malfunction: Short For Ground<br />
Front Wheel Speed Sensor LH Wiring Malfunction: Short For Power Suppy<br />
Front Wheel Speed Sensor LH Malfunction: Unknow<br />
Front Wheel Speed Sensor RH Output Signal Malfunction: Beyond The Scope Of Loss,<br />
Front Wheel Speed Sensor RH Wiring Malfunction: Open<br />
Front Wheel Speed Sensor RH Wiring Malfunction: Short For Ground<br />
Front Wheel Speed Sensor RH Wiring Malfunction: Short For Power Suppy<br />
Front Wheel Speed Sensor RH Malfunction: Unknow<br />
Rear Wheel Speed Sensor LH Output Signal Malfunction: Beyond The Scope Of Loss,<br />
Rear Wheel Speed Sensor LH Wiring Malfunction: Open<br />
Rear Wheel Speed Sensor LH Wiring Malfunction: Short For Ground<br />
Rear Wheel Speed Sensor LH Wiring Malfunction: Short For Power Suppy<br />
Rear Wheel Speed Sensor LH Malfunction: Unknow<br />
Rear Wheel Speed Sensor RH Output Signal Malfunction: Beyond The Scope Of Loss,<br />
Rear Wheel Speed Sensor RH Wiring Malfunction: Open<br />
Rear Wheel Speed Sensor RH Wiring Malfunction: Short For Ground<br />
Rear Wheel Speed Sensor RH Wiring Malfunction: Short For Power Suppy<br />
Rear Wheel Speed Sensor RH Malfunction: Unknow<br />
04-103<br />
C109904<br />
C001004<br />
C001104<br />
C001404<br />
C001504<br />
C001804<br />
C001904<br />
C001C04<br />
C001D04<br />
C109504<br />
C002004<br />
C007208<br />
Wheel Speed Sensor Group Malfunction (Wheel Speed Sensor Interchangeable, Each<br />
Of The Wheel Speed Difference Is Too Large, Wheel Speed Sensors Fault)<br />
Front Inlet Hydraulic Valve LH Failure<br />
Front Outlet Hydraulic Valve LH Failure<br />
Front Inlet Hydraulic Valve RH Failure<br />
Front Outlet Hydraulic Valve RH Failure<br />
Rear Inlet Hydraulic Valve LH Failure<br />
Rear Outlet Hydraulic Valve LH Failure<br />
Rear Inlet Hydraulic Valve RH Failure<br />
Rear Outlet Hydraulic Valve RH Failure<br />
Valve Relay Failure<br />
Reflux Pump Motor Failure<br />
Valve Group Failure (Overheating Protection Signal Is Invalid, Hardw Is Damaged)<br />
04-104<br />
Use the table below to help you find the cause of the problem. The numbers indicate the priority of the likely<br />
Symptom Suspect Area Reference<br />
1. Brake pipe leakage,<br />
breakage, etc.<br />
2. Lack of brake fluid -<br />
3. Differential fault<br />
Chapter 34 axle and propeller shaft - differential<br />
assy, check and adjustment<br />
4. Front brake fault Chapter 35 brake - front brake, overhaul<br />
5. Rear brake fault Chapter 35 brake - rear brake, overhaul<br />
ABS is inoperative.<br />
6. Hydraulic regulator assembly<br />
fault<br />
7. Parking light switch fault<br />
8. Brake fluid level sensor fault<br />
9. Brake switch fault<br />
10. Speed sensor fault<br />
11. Stop valve fault<br />
12. Pressure relief valve fault<br />
13. ABS module power supply<br />
14. ABS module ground fault<br />
Chapter 04 diagnostics - instrument cluster,<br />
ABS warning light is inoperative/always on<br />
Chapter 04 diagnostics - anti - lock brake system,<br />
ABS system is inoperative<br />
15. ABS module fault -<br />
04-105<br />
PRE - CHECK<br />
Before diagnosis of the ABS system, check the ABS system failure and easily accessible<br />
components first, visual inspection can quickly determine fault, and thus do not need to do further<br />
diagnosis.<br />
1. CHECK TIRE.<br />
(a). Make sure that the vehicle only install the<br />
recommended size tires and wheels. coaxial style<br />
of tire tread depth must be the same. Specific tire<br />
models, refer to the vehicle owner's manual for<br />
details.<br />
2. CHECK THE ABS HYDRAULIC MODULATOR, BRAKE PIPES AND CONNECTIONS<br />
FOR LEAKING.<br />
3. CHECK ABS SYSTEM FUSES TO ENSURE THAT THE FUSES ARE NOT BURNED,<br />
AND THE MODEL IS CORRECT. ABS SYSTEM HAS THREE FUSES:<br />
• Pump motor fuse (40A)<br />
• Solenoid valve fuse (25A)<br />
• Electronic control unit Fuse (5A)<br />
4. CHECK THE BATTERY VOLTAGE, DETECT WHETHER THE BATTERY TERMINAL<br />
CORROSION OR LOOSE. ABS SYSTEM NORMAL OPERATING VOLTAGE RANGE IS<br />
9.3V - 16.8V.<br />
5. CHECK ABS GROUND.<br />
(a). Check ABS grounding point is loose. The<br />
location is changed or not.<br />
ABS ground has good sealing, in order to avoid<br />
water and moisture in capillary (siphon) effect<br />
through wiring harness of channel infiltration ABS<br />
control module, which cause function failure.<br />
04-106<br />
6. VISUAL INSPECTION OF THE FOLLOWING<br />
ELECTRICAL COMPONENTS:<br />
(a).<br />
ABS system harness and connectors of the<br />
related components are properly connected, to be<br />
pinched or cut or not.<br />
Harness routing is too close to high - voltage or<br />
high - current devices, such as high - voltage or<br />
parts, generators, motors or stereo amplifier.<br />
The high voltage or high current device may cause<br />
the circuit to generate the induced noise, and<br />
thereby interfere with the normal working of the<br />
(c). ABS parts are sensitive to electromagnetic<br />
interference (EMI). Suspected intermittent fault,<br />
check the aftermarket installation of anti - theft<br />
device, lights, or whether the mobile phone is not<br />
installed correctly.<br />
7. IF THE ABS NOISE IS TOO LARGE, IT MAY BE CAUSED BY THE FOLLOWING<br />
REASONS:<br />
(a). Loosening of ABS assembly with bracket.<br />
(b). Loosening of ABS bracket and body.<br />
(c). ABS plastic bracket washer missing or damaged.<br />
04-107<br />
POWER SUPPY VOLTAGE HIGH OR LOW<br />
DIAGNOSTIC TROUBLE CODE:<br />
C190004; C190104<br />
CONDITIONS OF FAULT SETTING<br />
It will be caused failure by one of the following conditions are met when the supply voltage of the<br />
ECU:<br />
(1) Voltage is lower than 4.5V when starting engine.<br />
(2) Voltage is lower than 7.7V or higher than 16.8V when ignition switch is ON.<br />
(3) Voltage is between 7.7V to 9.2V when vehicle speed is higher than 6km/h.<br />
1. PERFORM PRE - CHECK STEPS<br />
NO > Repair or replace related components.<br />
2. INSPECT BATTERY<br />
(a). Turn the ignition switch ON.<br />
(b). Measure the battery voltage.<br />
NO > Repair or replace battery.<br />
3. ABS CONTROL MODULE CROSS - VALIDATION<br />
(a). Turn the ignition switch OFF.<br />
(b). Remove the ABS actuator. (Refer to “Chapter 35 brake - abs actuator, replacement”)<br />
(c). Install the removed ABS to another known vehicle with the same model. (Ensure that ABS<br />
connectors are securely installed without connecting pipes when vehicle was driven. )<br />
(d). Start the engine and to ensure that the vehicle speed is not lower than 20km/h, so that the<br />
ABS dynamic self - check.<br />
YES > Replace ABS module.<br />
NO > Replace the ABS actuator.<br />
04-108<br />
SOLENOID VALVES AND VALVES RELAY FAILURE<br />
C001004; C001104; C001404; C001504; C001804; C001904; C001C04; C001D04; C109504;<br />
(1) Valves power supply failure. (Power supply short for ground or ground open.)<br />
(2) Solenoid valve temperature is too high. (Overheating protection)<br />
(3) Solenoid valve is shorted. (Fuse)<br />
(4) Actuating the corresponding solenoid valve, but no feedback.<br />
(5) Solenoid valve failure.<br />
(6) Valves relay failure.<br />
POSSIBLE CAUSE<br />
(1) Solenoid valve short for power supply or ground, circuit open.<br />
(2) Fuses failure.<br />
(3) Overheating protection (Solenoid valve long working hours, common in vacuum filling and<br />
offline detection)<br />
(4) ABS damaged<br />
1. DETECT THE OCCASIONAL FAULT OF SYSTEM<br />
(b). Disconnect the battery negative cable.<br />
(c). Vehicle was allowed to stand for 5 minutes.<br />
(d). Connect the negative battery cable.<br />
YES > System is normal .<br />
2. PERFORM PRE - CHECK STEPS<br />
04-109<br />
3. READ DTC AND DATA ON THE DIAGNOSTIC TOOL<br />
Selecte diagnostic mode in the disgnostic tool and read data stream.<br />
Detect vehicle speed displayed on the instrument panel and diagnostic tool when vehicle<br />
is running, and compare whether they are consistent.<br />
If speedmeter display shows the speed value and the diagnostic value of error within ± 10%, it belongs<br />
to the normal range.<br />
YES > Clear the DTC(s).<br />
4. INSPECT FUSE<br />
Disconnect the battery negative cable.<br />
(b). Inspect the ABS valve fuse in battery<br />
compartment junction box (A001): 25 A.<br />
(c). Inspect the ABS IG fuse in battery compartment<br />
junction box (A001): 5 A.<br />
NO > Replace the fuse.<br />
5. ABS CONTROL MODULE CROSS - VALIDATION<br />
connectors are securely installed without connecting pipes when vehicle was driven.)<br />
ABS dynamic self - check<br />
04-110<br />
6. CHECK HARNESS AND CONNECTOR (ABS VALVE FUSE - GROUND)<br />
Measure the voltage according to the value(s) in<br />
the table below.<br />
ABS valve fuse - Ground<br />
7. CHECK HARNESS AND CONNECTOR (ABS IG FUSE - ABS MODULE)<br />
Remove the ABS IG fuse (5A) in the battery compartment junction box.<br />
Disconnect the A009 ABS module connector.<br />
(c).<br />
Measure the resistance according to the value(s)<br />
in the table below<br />
ABS IG fuse - A009 (28)<br />
04-111<br />
8. CHECK HARNESS AND CONNECTOR (ABS VALVE FUSE - ABS MODULE)<br />
Remove ABS valve fuse (25A) in the battery compartment junction box.<br />
ABS valve fuse - A009 (25)<br />
YES > Replace ABS MODULE.<br />
04-112<br />
PUMP MOTOR FAILURE<br />
(1) Pump motor is overloaded with work, the temperature is too high. (Overheat protection)<br />
(2) Reflux pump motor relay work over 60ms, reflux pump monitoring is still not detected voltage<br />
signal.<br />
(3) Reflux pump motor relay did not work, reflow pump monitoring detected voltage exceeds<br />
2.5s.<br />
(4) Reflux pump motor relay stops working and the reflux pump monitoring detected voltage<br />
does not drop.<br />
(1) Pump motor is poorly grounded.<br />
(2) System overheating protection.<br />
(3) Pump motor power supply is not normal(Fuse, battery terminal)<br />
(4) Pump motor relay failure.<br />
(5) Pump motor failure.<br />
YES > System is normal<br />
04-113<br />
If speedmeter display shows the speed value and the diagnostic value of error within ±<br />
10%, it belongs to the normal range.<br />
Inspect the ABS pump fusible link in battery<br />
compartment junction box (A001): 40 A.<br />
Inspect the ABS IG fuse in battery compartment<br />
04-114<br />
6. CHECK HARNESS AND CONNECTOR (ABS PUMP FUSIBLE LINK - GROUND)<br />
ABS pump fusible link -<br />
04-115<br />
8. CHECK HARNESS AND CONNECTOR (ABS PUMP FUSIBLE LINK - ABS MODULE)<br />
ABS valve fuse - A009 (1)<br />
04-116<br />
WHEEL SPEED SENSOR CIRCUIT FAULT<br />
C003200; C00A000; C00A100; C00A900; C003500; C00A200; C00A300; C00AA00; C003800;<br />
C00A400;C00A500; C00AB00; C003B00; C00A600; C00A700; C00AC00; C109904<br />
(1) ECU detects wheel speed sensor signal wire is shorted to ground.<br />
(2) Wheel speed sensor circuit open.<br />
(1) Wheel speed sensor circuit is disconnected, patch loosening, fracture.<br />
(2) Wheel speed sensor signal circuit and the power suppy circuit is connected in reverse.<br />
(3) Signal circuit is shorted to ground.<br />
(4) Damage to the sensor head or connector pins.<br />
2. READ DTC AND DATA ON THE DIAGNOSTIC TOOL<br />
(d).<br />
Remove the ABS actuator. (Refer to “Chapter 35 brake - abs actuator, replacement”)<br />
Install the removed ABS to another known vehicle with the same model. (Ensure that ABS<br />
Start the engine and to ensure that the vehicle speed is not lower than 20km/h, so that the<br />
04-117<br />
4. CHECK HARNESS AND CONNECTOR (WHEEL SPEED SENSOR - GROUND)<br />
Disconnect the A010 front wheel speed sensor connector.<br />
(d). Measure the resistance according to the value(s)<br />
A010 (1) - Ground<br />
A010 (2) - Ground<br />
5. CHECK HARNESS AND CONNECTOR (WHEEL SPEED SENSOR - ABS MODULE)<br />
A010 (1) - A009 (8)<br />
A010 (2) - A009 (19)<br />
04-118<br />
WHEEL SPEED SENSOR SIGNAL FAULT<br />
C003108; C00A900; C003408; C00AA00; C003708; C00AB00; C003A08; C00AC00; C109904<br />
1. ECU detects wheel speed sensor signal circuit is shorted to power supply.<br />
2. ECU detects wheel speed sensor power supply circuit is shorted to ground.<br />
3. Wheel speed sensor signal is not normal.<br />
1. Wheel speed sensor circuit is disconnected, patch loosening, fracture.<br />
2. Wheel speed sensor signal circuit is shorted to power supply.<br />
3. Wheel speed sensor power supply is shorted to ground.<br />
4. The ring gear is not installed, missing teeth, dirty dust and installed incorrectly.<br />
5. The gap between the sensor and the ring is too large.<br />
6. The wheel speed sensor is subjected to the external magnetic field interference. (Wheel or<br />
axle is not demagnetization)<br />
7. The wheel speed sensor fault.<br />
8. The number of teeth of the ring gear error.<br />
9. Tire size does not meet specifications<br />
10. ECU is damaged.<br />
2. INSPECT WHEEL SPEED SENSOR<br />
Raise the vehicle.<br />
04-119<br />
(c). Inspect whether the ABS speed sensor<br />
installation is correct or not.<br />
(e).<br />
(f).<br />
Inspect whether the ABS speed sensor connector<br />
is loose or not.<br />
Inspect whether the ABS speed sensor tightening<br />
bolt is loose or not.<br />
Remove ABS speed sensor to inspect whether<br />
the speed sensor is damaged or the surface is<br />
dirty.<br />
NO > Replace wheel speed sensor.<br />
4. INSPECT WHEEL SPEED SENSOR INSTALLATION<br />
(a). Position the front wheel speed sensor RH<br />
properly.<br />
Installation bolts are tightened properly, the sensor<br />
installation position should be flat.<br />
04-120<br />
5. INSPECT WHEEL SPEED SENSOR TIP<br />
Remove the front wheel speed sensor.<br />
(b). Check wheel speed sensor tip.<br />
No scratches or foreign objects on the sensor tip.<br />
6. INSPECT WHEEL SPEED SENSOR ROTOR<br />
Check the sensor serrations.<br />
No scratches, missing teeth or foreign objects.<br />
If foreign object is attached, please remove it. After<br />
reassembling, check the output voltage.<br />
NO > Replace the wheel speed sensor rotor.<br />
7. CHECK HARNESS AND CONNECTOR (WHEEL SPEED SENSOR - GROUND)<br />
04-121<br />
8. CHECK HARNESS AND CONNECTOR (WHEEL SPEED SENSOR - ABS MODULE)<br />
04-122<br />
ABS CONTROL IS UNREASONABLE<br />
ABS received continuous working instruction (more than 1 minute).<br />
(1) Continued brake on ice.<br />
(2) Wheel speed difference is too large.<br />
3. INSPECT WHEEL SPEED SENSOR INSTALLATION<br />
04-123<br />
Inspect whether ABS speed sensor installation is<br />
correct or not.<br />
Position front wheel speed sensor RH properly.<br />
4. INSPECT WHEEL SPEED SENSOR TIP<br />
04-124<br />
5. INSPECT WHEEL SPEED SENSOR ROTOR<br />
6. ABS CONTROL MODULE CROSS - VALIDATION<br />
7. CHECK HARNESS AND CONNECTOR (ABS MODULE - GROUND)<br />
A009 (13) - Ground<br />
A009 (38) - Ground<br />
04-125<br />
ABS SYSTEM IS INOPERATIVE<br />
WIRING DIAGRAM (<br />
04-126<br />
1. INSPECT FUSE<br />
Inspect ABS valve fuse in battery compartment<br />
junction box (A001): 25 A.<br />
Inspect the stop lamp switch fuse in engine room<br />
junction box (A002): 15 A.<br />
2. INSPECT BACK - UP LAMP SWITCH<br />
Disconnect the A025 stop lamp switch connector.<br />
Inspect the stop lamp switch according to the<br />
value(s) in the table below.<br />
Condition<br />
Release stop<br />
lamp switch<br />
Press stop lamp<br />
switch<br />
Specified<br />
1 - 2 ≥ 1 MΩ<br />
1 - 2 < 2 Ω<br />
NO > Replace stop lamp switch.<br />
3. CHECK HARNESS AND CONNECTOR (ABS MODULE - GROUND)<br />
04-127<br />
4. CHECK ABS MODULE POWER SUPPLY<br />
ABS IG fuse - Ground<br />
ABS pump fusible link - Ground<br />
5. CHECK HARNESS AND CONNECTOR (STOP LAMP FUSE - STOP LAMP SWITCH)<br />
04-128<br />
in the table below.<br />
Stop lamp fuse - A025 (2)<br />
6. CHECK HARNESS AND CONNECTOR (ABS MODULE - STOP LAMP SWITCH)<br />
A009 (30) - A025 (1)<br />
DIAGNOSTICS - SUPPLEMENTAL RESTRAINT SYSTEM<br />
04-129<br />
SUPPLEMENTAL RESTRAINT SYSTEM<br />
• Fail to carry out the service operations in the correct sequence could cause the supplemental<br />
restraint system to unexpectedly deploy during servicing. It may lead to a serious accident.<br />
Furthermore, if a mistake is made in servicing the supplemental restraint system, it is possible<br />
that the SRS will fail to operate when requiring. Before servicing (including removal or<br />
installation of parts, inspection or replacement), be sure to read the following items carefully.<br />
Then follow the correct procedure described in this manual.<br />
• Work must be started after 90 seconds from the time that the ignition switch is turned to the<br />
”LOCK” position and the negative (–) terminal cable is removed from the battery. (The<br />
supplemental restraint system is equipped with a back–up power source, so if work is started<br />
within 90 seconds after disconnecting the negative (–) terminal cable from the battery, the SRS<br />
may deploy.<br />
• Do not directly expose the horn switch assy to hot air or flames.<br />
• Malfunction symptoms of the supplemental restraint system are difficult to confirm, so the<br />
diagnostic trouble codes (DTC) become the most important source of information when<br />
troubleshooting. When repair the supplemental restraint system, always check the diagnostic<br />
trouble codes (DTC) before disconnecting the battery.<br />
• After completion of maintenance work,be sure to erase diagnostic trouble code (s) (DTC);If<br />
diagnostic trouble code (s) (DTC) can’t be erased,replace the restraint control module.Check for<br />
diagnostic trouble code (s) (DTC) again.<br />
• Even in case of a minor collision where the SRS does not deploy, the horn switch assy and<br />
restraint control module should be inspected.<br />
• Before repairing, remove the driver airbag and restraint control module if shocks are likely to be<br />
applied to the airbag and module during repairing.<br />
• Never use SRS related parts from another vehicle. If necessary, replace with new parts.<br />
• Never disassemble and repair the horn switch assy.<br />
• If the horn switch assy has been dropped, or if there are cracks, dents or other defects in the<br />
case, bracket or connector, replace them with new ones.<br />
• Use the multimeter with high impedance (10 kW/V minimum) for troubleshooting of an electrical<br />
• Information labels are attached to the SRS components. Follow the instructions on the notices.<br />
• After working on the supplemental restraint system is completed, check the SRS warning light.<br />
• When the negative (–) terminal cable is disconnected from the battery, memory of the clock and<br />
audio systems will lost. So, before starting work, make a record of the memorized contents in<br />
each memory system. Then, when work is finished, reset the clock and audio systems as<br />
before. To avoid erasing the memory in each memory system, never use a back–up power<br />
supply from another battery.<br />
04-130<br />
1 Restraint Control Module (RCM)<br />
2 Instrument Cluster<br />
3 Driver Airbag<br />
4 Clock Spring<br />
5 Passenger Airbag<br />
6 Driver Side Fuse Box<br />
7 Co - pilot Side Junction Box<br />
8 Ignition Switch<br />
04-131<br />
RESTRAINT CONTROL MODULE (RCM) CONNECTOR PIN<br />
Terminal No. Wiring Color Definition<br />
1 - -<br />
3 - -<br />
4 - -<br />
5 B - O Power Supply<br />
6 W - B Ground<br />
7 B - Y SRS Warning Light<br />
8 - -<br />
9 R - L Diagnosis K<br />
10 Y Airbag +<br />
11 Y - B Airbag -<br />
13 G - B Airbag +<br />
14 G - R Airbag -<br />
16 - -<br />
17 - -<br />
18 - -<br />
19 - -<br />
25 - -<br />
04-132<br />
27 - -<br />
28 - -<br />
29 - -<br />
30 Y Collision Output Interface<br />
04-133<br />
If a malfunction code is displayed during the DTC check, check the circuit listed. For details of each<br />
code, turn to the relevant troubleshooting page in the DTC chart.<br />
DTC No. Detection Item (DTC Definition) Trouble Area<br />
8101 Power supply voltage high<br />
8102 Power supply voltage low<br />
8201 Driver airbag fault - high resistance<br />
8202 Driver airbag fault - low resistance<br />
8203 Driver airbag circuit short to ground<br />
8204 Driver airbag circuit short to battery<br />
• Charging system<br />
• Power source circuit<br />
• Wire harness<br />
• Fuse<br />
• Ignition switch<br />
• Driver airbag circuit<br />
• Driver airbag<br />
• Clock spring<br />
• Restraint control module<br />
8211<br />
8212<br />
8213<br />
8214<br />
Co - pilot side airbag fault - High<br />
Co - pilot side airbag fault - Low<br />
Co - pilot side airbag circuit short to<br />
ground<br />
battery<br />
• Passenger airbag circuit<br />
• Passenger airbag<br />
8610 ACU internal error • Restraint control module<br />
04-134<br />
• If there is no DTC,but supplemental restraint system isn’t normal ,use the table below to check<br />
the circuit.<br />
• Before replacement of restraint control module (RCM) and instrument cluster,turn the ignition<br />
switch OFF,and disconnect the battery negative cable.<br />
• Use the table below to help you find the cause of the problem. The numbers indicate the priority<br />
of the likely cause of the problem. Check each part in order. If necessary, replace these parts.<br />
1. SRS warning light circuit -<br />
SRS warning light is<br />
always on<br />
2. Instrument Cluster<br />
3. Restraint control module<br />
Chapter 83 instrument panel - instrument cluster<br />
, replacement<br />
Chapter 62 supplemental restraint system -<br />
RCM , replacement<br />
inoperative<br />
04-135<br />
8102 - POWER SUPPLY VOLTAGE LOW<br />
CIRCUIT DESCRIPTION<br />
DTC No. DTC Detecting Condition Trouble Area<br />
8102<br />
With vehicle speed at 3 km/h or more, ignition<br />
switch terminal voltage is 10V or below for 10<br />
sec or longer.<br />
04-136<br />
1. CHECK RESTRAINT CONTROL MODULE<br />
Disconnect the negative cable from the battery, and wait at least for 90 seconds.<br />
Disconnect the A027 restraint control module connector.<br />
Connect the battery negative cable.<br />
(e) Measure the voltage according to the value (s) in the<br />
A027 (5) - Ground<br />
YES > Replace restraint control module.<br />
2. INSPECT FUSE (Co - pilot Side Junction Box)<br />
Measure the voltage according to the value (s) in the<br />
Airbag fuse (10A) - Ground<br />
NO > Go to step 4.<br />
04-137<br />
3. CHECK HARNESS AND CONNECTOR (AIRBAG FUSE - RESTRAINT CONTROL MODULE)<br />
Measure the resistance according to the value (s) in the<br />
Airbag fuse (10A) - A027 (5)<br />
04-138<br />
4. CHECK HARNESS AND CONNECTOR (IGNITION SWITCH - AIRBAG FUSE)<br />
Disconnect the I009 ignition switch connector.<br />
I009 (2) - Airbag fuse (10A)<br />
I009 (2) - Ground<br />
YES > Replace ignition switch assy.<br />
04-139<br />
8201 - DRIVER AIRBAG FAULT - HIGH RESISTANCE<br />
8202 - DRIVER AIRBAG FAULT - LOW RESISTANCE<br />
8201<br />
8202<br />
• Short circuit between airbag plus wire harness and<br />
airbag negative wire harness.<br />
• Open circuit between airbag plus wire harness and<br />
• Driver airbag malfunction<br />
• Clock spring malfunction<br />
• Restraint control module malfunction<br />
04-140<br />
1. INSPECT CLOCK SPRING AND DRIVER AIRBAG<br />
Disconnect the I014 clock spring connector.<br />
Relace clock spring and driver airbag.<br />
Connect the battery negative cable.Turn the ignition switch ON.<br />
Dose the systerm work correctly?<br />
YES > Relace clock spring and driver airbag.<br />
2. CHECK HARNESS AND CONNECTOR (CLOCK SPRING - RESTRAINT CONTROL MODULE)<br />
A027 (10) - I014 (3)<br />
A027 (11) - I014 (4)<br />
I014 (3) - Ground<br />
I014 (4) - Ground<br />
04-141<br />
8203 - DRIVER AIRBAG CIRCUIT SHORT TO GROUND<br />
8203<br />
• Short circuit in airbag wire harness (to<br />
ground)<br />
04-142<br />
A027 (10) - Ground<br />
A027 (11) - Ground<br />
04-143<br />
8204 - DRIVER AIRBAG CIRCUIT SHORT TO BATTERY<br />
8204<br />
battery)<br />
04-144<br />
1. CHECK HARNESS AND CONNECTOR (RESTRAINT CONTROL MODULE - CLOCK SPRING)<br />
2. INSPECT CLOCK SPRING AND DRIVER AIRBAG<br />
Does the system work correctly?<br />
NO > Replace restraint control module.<br />
04-145<br />
8211 - CO - PILOT SIDE AIRBAG FAULT - HIGH RESISTANCE<br />
8212 - CO - PILOT SIDE AIRBAG FAULT - LOW RESISTANCE<br />
airbag negative wire harness<br />
• Passenger airbag malfunction<br />
04-146<br />
1. INSPECT PASSENGER AIRBAG<br />
Disconnet the I035 passenger airbag connector.<br />
Replace passenger airbag.<br />
YES > Replace passenger airbag.<br />
2. CHECK HARNESS AND CONNECTOR (PASSENGER AIRBAG - RESTRAINT CONTROL<br />
MODULE)<br />
A027 (13) - I035 (1)<br />
A027 (14) - I035 (2)<br />
04-147<br />
I035 (1) - Ground<br />
I035 (2) - Ground<br />
04-148<br />
8213 - CO - PILOT SIDE AIRBAG CIRCUIT SHORT TO GROUND<br />
04-149<br />
2. CHECK HARNESS AND CONNECTOR (PASSENGER AIRBAG - RESTRAINT CONTROL MODULE)<br />
A027 (13) - Ground<br />
A027 (14) - Ground<br />
04-150<br />
8214 - CO - PILOT SIDE AIRBAG CIRCUIT SHORT TO BATTERY<br />
04-151<br />
2. CHECK HARNESS AND CONNECTOR (RESTRAINT CONTROL MODULE - PASSENGER<br />
AIRBAG)<br />
04-152<br />
SRS WARNING LIGHT IS ALWAYS ON<br />
04-153<br />
1. CHECK HARNESS AND CONNECTOR (INSTRUMENT CLUSTER - RESTRAINT CONTROL<br />
Disconnect the I003 instrument B connector.<br />
A027 (7) - Ground<br />
2. INSPECT INSTRUMENT CLUSTER<br />
Disconnect the I002 instrument A connector.<br />
Replace instrument cluster.<br />
Does the instrument cluster work correctly?<br />
YES > Replace instrument cluster.<br />
04-154<br />
SRS WARNING LIGHT IS INOPERATIVE<br />
04-155<br />
I003 (B27) - A027 (7)<br />
Replace instrument cluster,and keep the I003 instrument connector disconnecting.<br />
Connect Pin B27 of the I003 instrument B connector to ground.<br />
04-156<br />
DIAGNOSTICS - HEATER AND AIR CONDITIONING SYSTEM<br />
HEATER AND AIR CONDITIONING SYSTEM<br />
1. DO NOT DEPOSIT REFRIGERANT IN AN ENCLOSED AREA OR NEAR AN OPEN FLAME.<br />
2. ALWAYS WEAR SAFETY GOGGLES.<br />
3. AVOID CONTACTING WITH LIQUID REFRIGERANT R - 134A.<br />
If liquid refrigerant is in your eyes or on your skin:<br />
(f) Wash the area with lots of cold water.<br />
(g) Apply clean petroleum jelly to the skin.<br />
(h) Immediately go to a hospital or see a physician for professional treatment.<br />
4. DO NOT HEAT CONTAINER OR EXPOSE THE CONTAINER TO OPEN FLAME.<br />
5. DO NOT DROP DOWN CONTAINER OR APPLY PHYSICAL SHOCKS TO IT.<br />
6. DO NOT OPERATE COMPRESSOR WITHOUT ENOUGH REFRIGERANT IN REFRIGERANT<br />
SYSTEM.<br />
(a) If there is not enough refrigerant in A/C system, oil lubrication will be insufficient and the compressor<br />
may be damaged.<br />
7. DO NOT OPEN HIGH PRESSURE MANIFOLD VALVE WHILE COMPRESSOR IS OPERATING.<br />
(a) Open and close only the low pressure valve.<br />
If the high pressure valve is opened, refrigerant flowing in the reverse direction will cause the charging<br />
cylinder to rupture.<br />
8. BE CAREFUL NOT TO OVERCHARGE SYSTEM WITH REFRIGERANT.<br />
(a) If refrigerant is overcharged, it will cause problems such as insufficient cooling, poor fuel economy,<br />
engine overheating, etc.<br />
9. DO NOT OPERATE ENGINE AND COMPRESSOR WITH NO REFRIGERANT.<br />
10. EXPRESSIONS OF IGNITION SWITCH.<br />
04-157<br />
BASIC INSPECTION<br />
Step Condition Action<br />
1<br />
Check the refrigerant.<br />
• Open the cap of release valve.<br />
• Press the release valve.<br />
Yes<br />
No<br />
Go to next step<br />
Charge the refrigerant system<br />
Check the A/C switch.<br />
• Start the engine.<br />
• Press the A/C switch.<br />
• Check the A/C switch.<br />
Go to problem symptoms table<br />
Check the A/C clutch field coil.<br />
• check the A/C clutch field coil.<br />
Check compressor belt.<br />
• Check compressor belt.<br />
Check the compressor.<br />
• Check the compressor cluth for noisy.<br />
6<br />
Check the condenser.<br />
• Check the dirt between the condenser<br />
and radiator.<br />
Clear the dirt or repalce the condenser<br />
Check pressure A/C liquid line.<br />
• Check the line for inhibition or leakage.<br />
Replace or reroute the pressure A/C liquid<br />
line<br />
04-158<br />
1 Rear Blower Forward Switch<br />
2 A/C Switch<br />
3 Blower Control Knob<br />
4 Temperature Control Knob<br />
04-159<br />
1. Fuse -<br />
A/C system is inoperative<br />
2. Relay -<br />
3. Wire harness -<br />
Front blower motor is inoperative<br />
3. A/C control panel<br />
4. Front blower control module<br />
5. Front blower motor<br />
Chapter 61 heater and air<br />
conditioning - multi - media and A/C<br />
controller assy, replacement<br />
conditioning - front blower control<br />
module, replacement<br />
conditioning - front A/C blower,<br />
replacement<br />
6. Wire harness -<br />
Top evaporator blower motors are<br />
3. Top evaporator blower switch<br />
4. Top evaporator blower resistor<br />
5. Rear blower forward switch<br />
6. A/C control panel<br />
conditioning - top evaporator blower<br />
switch, replacement<br />
resistor, replacement<br />
Chapter 83 instrument panel -<br />
dashboard assy, replacement<br />
7. Wire harness -<br />
04-160<br />
Front air flow is insufficient<br />
1. A/C control panel<br />
2. Front blower control module<br />
3. Front blower motor<br />
4. Front A/C vent duct<br />
conditioning - front A/C vent duct ,<br />
5. Wire harness -<br />
Rear air flow is insufficient<br />
1. Rear A/C blower switch<br />
2. Top evaporator blower resistor<br />
conditioning - rear A/C blower<br />
No cooling from front A/C system<br />
3. A/C compressor<br />
4. A/C control panel<br />
5. Refrigerant<br />
6. Triple pressure switch<br />
7. Front evaporator thermistor<br />
conditioning - compressor, overhaul<br />
conditioning - refrigerant<br />
conditioning - A/C pressure switch,<br />
conditioning - front evaporator<br />
thermistor, replacement<br />
8. Wire harness -<br />
04-161<br />
1. Top evaporator temperature<br />
conditioning - top evaporator<br />
temperature sensor, replacement<br />
No cooling from rear A/C system<br />
2. Rear A/C solenoid valve<br />
conditioning - rear A/C shut off<br />
solenoid valve, replacement<br />
3. Relay -<br />
Rear heater is inoperative or insufficient<br />
heating<br />
3. Rear heater blower switch<br />
4. Rear heater solenoid valve<br />
5. Rear heater motor<br />
conditioning - rear heater blower<br />
conditioning - rear heater solenoid<br />
valve, replacement<br />
conditioning - rear heater blower,<br />
overhaul<br />
04-162<br />
A/C SYSTEM IS INOPERATIVE<br />
04-163<br />
04-164<br />
Inspect the A/C fuse (15A) in driver side junction box<br />
(I001).<br />
2. CHECK HARNESS AND CONNECTOR ( A/C CUT OFF RELAY - GROUND)<br />
Remove A/C cut off relay.<br />
Measure the voltage according to the value(s) in the<br />
A/C cut off relay (30) - Ground<br />
04-165<br />
3. CHECK HARNESS AND CONNECTOR ( A/C CUT OFF RELAY - GROUND)<br />
Standard voltage (check for a short to battery)<br />
A/C cut off relay (85) - Ground<br />
04-166<br />
FRONT BLOWER MOTOR IS INOPERATIVE<br />
04-167<br />
Inspect the front blower fusible link (30A) in Co-pilot<br />
Junction Box (A003).<br />
Inspect the A/C controller fuse (7.5A) in Driver Side<br />
Junction Box (I001).<br />
2. INSPECT FRONT BLOWER RELAY<br />
Remove the front blower relay.<br />
Inspect the front blower relay according to the value(s) in<br />
Standard resistance:<br />
Condition Tester Connection Specified Condition<br />
Constant 85 - 86 Continuity<br />
Apply battery<br />
voltage to<br />
terminal 85<br />
and 86<br />
30 - 87 < 2 Ω<br />
NO > Replace the front blower relay.<br />
3. INSPECT FRONT BLOWER CONTROL MODULE<br />
Disconnect the I025 front blower control module connector.<br />
Replace the front blower control module with a new one.<br />
04-168<br />
YES > Replace the front blower motor resistor.<br />
4. INSPECT FRONT BLOWER MOTOR<br />
(a) Disconnect the battery negative cable.<br />
(b) Disconnect the A028 front blower motor connector.<br />
(c) Replace a new front blower motor.<br />
YES > Replace the front blower motor.<br />
5. CHECK HARNESS AND CONNECTOR (FRONT BLOWER RELAY - FRONT BLOWER )<br />
Disconnect the A028 front blower motor connector.<br />
Measure the resistance according to the value(s) in the<br />
Front blower relay (30) - A028 (1)<br />
6. CHECK HARNESS AND CONNECTOR (FRONT BLOWER - FRONT BLOWER CONTROL<br />
Disconnect the A027 front blower connector.<br />
04-169<br />
A028 (2) - I025 (4)<br />
7. CHECK HARNESS AND CONNECTOR (FRONT BLOWER CONTROL MODULE - GROUND)<br />
Disconnect the I025 blower control module connector.<br />
I025 (8) - Ground<br />
8. CHECK HARNESS AND CONNECTOR (FRONT BLOWER CONTROL MODULE - A/C CONTROL<br />
PANEL)<br />
Disconnect the I021 A/C control panel connector.<br />
04-170<br />
I025 (2) - I021 (35)<br />
I025 (3) - I021 (28)<br />
9. CHECK HARNESS AND CONNECTOR (FRONT BLOWER RELAY - A/C CONTROL PANEL)<br />
Remove front blower relay.<br />
Disconnect the I020 A/C control panel connector.<br />
Front blower relay (86) - I020 (8)<br />
10. CHECK HARNESS AND CONNECTOR ( A/C CONTROL PANEL - GROUND)<br />
04-171<br />
I020 (10) - Ground<br />
I020 (19) - Ground<br />
11. CHECK HARNESS AND CONNECTOR ( A/C CONTROL PANEL - GROUND)<br />
I020 (18) - Ground<br />
I020 (20) - Ground<br />
YES > Replace A/C control panel ( Multi - media and A/C controller assy).<br />
04-172<br />
REAR EVAPORATOR MOTORS ARE INOPERATIVE<br />
04-173<br />
Inspect the rear A/C fusible link (30A) in Co - pilot<br />
2. INSPECT REAR A/C RELAY<br />
Remove the rear A/C relay.<br />
NO > Replace the rear A/C relay.<br />
04-174<br />
3. INSPECT REAR BLOWER FORWARD SWITCH<br />
Disconnect the I023 rear blower forward switch connector.<br />
Inspect the rear blower forward switch according to the<br />
Position Tester Connection Specified Condition<br />
Release 2 - 5 ≥ 1 ΜΩ<br />
Press 2 - 5 < 2 Ω<br />
NO > Replace the rear blower forward switch.<br />
4. INSPECT TOP EVAPORATOR BLOWER SWITCH<br />
Disconnect the L005 top evaporator blower switch connector.<br />
Inspect the top evaporator blower switch according to the<br />
I<br />
II<br />
III<br />
1 - 2<br />
3 - 4<br />
3 - 5<br />
3 - 6<br />
NO > Replace the top evaporator blower switch.<br />
5. INSPECT TOP EVAPORATOR BLOWER RESISTOR<br />
Disconnect the L003 top evaporator blower resistor connector.<br />
Replace a new top evaporator blower resistor.<br />
YES > Replace the top evaporator blower resistor .<br />
04-175<br />
6. CHECK HARNESS AND CONNECTOR (REAR A/C RELAY - GROUND)<br />
Turn the ignition switch ON and press the I023 rear blower forward switch.<br />
Rear A/C relay (30) - Ground<br />
7. CHECK HARNESS AND CONNECTOR (REAR A/C RELAY - TOP EVAPORATOR BLOWER<br />
SWITCH)<br />
Remove rear A/C relay.<br />
Rear A/C relay (86) - L005 (2)<br />
04-176<br />
8. CHECK HARNESS AND CONNECTOR (TOP EVAPORATOR BLOWER SWITCH - GROUND)<br />
L005 (1) - Ground<br />
L005 (3) - Ground<br />
9. CHECK HARNESS AND CONNECTOR (TOP EVAPORATOR BLOWER RESISTOR - TOP<br />
EVAPORATOR BLOWER SWITCH)<br />
L003 (1) - L005 (6)<br />
L003 (2) - L005 (5)<br />
L003 (3) - L005 (4)<br />
10. CHECK HARNESS AND CONNECTOR ( REAR A/C RELAY - LEFT/RIGHT BLOWER)<br />
Disconnect the L001 left blower connector.<br />
Disconnect the L002 right blower connector.<br />
04-177<br />
Rear A/C relay (87) - L001 (1)<br />
11. CHECK HARNESS AND CONNECTOR ( LEFT/RIGHT BLOWER - TOP EVAPORATOR BLOWER<br />
RESISTOR)<br />
Remove the L003 top evaporator blower resistor connector.<br />
L001 (2) - L003 (1)<br />
L002 (2) - L003 (1)<br />
YES > Replace left or right blower.<br />
04-178<br />
FRONT AIR FLOW IS INSUFFICIENT<br />
04-179<br />
1. INSPECT FRONT BLOWER MOTOR RESISTOR<br />
Replace the front blower control moduler with a new one.<br />
YES > Replace the front blower control module.<br />
2. CHECK THE HARNESS AND CONNECTOR (FRONT BLOWER - FRONT BLOWER CONTROL<br />
Disconnect the A028 front blower connector.<br />
3. CHECK HARNESS AND CONNECTOR (FRONT BLOWER CONTROL MODULE - GROUND)<br />
I025 (1) - Ground<br />
04-180<br />
4. CHECK HARNESS AND CONNECTOR (FRONT BLOWER CONTROL MODULE - A/C CONTROL<br />
5. CHECK HARNESS AND CONNECTOR ( A/C CONTROL PANEL - GROUND)<br />
04-181<br />
6. CHECK HARNESS AND CONNECTOR ( A/C CONTROL PANEL - GROUND)<br />
04-182<br />
REAR AIR FLOW IS INSUFFICIENT<br />
04-183<br />
1. INSPECT TOP EVAPORATOR BLOWER SWITCH<br />
NO > Replace the rear evaporator blower switch.<br />
2. CHECK HARNESS AND CONNECTOR (TOP EVAPORATOR BLOWER RESISTOR - TOP<br />
YES > Replace top evaporator blower resistor.<br />
04-184<br />
NO COOLING FROM FRONT A/C SYSTEM<br />
04-185<br />
04-186<br />
1. INSPECT COMPRESSOR RELAY<br />
Remove the compressor relay.<br />
NO > Replace the compressor relay<br />
2. CHECK HARNESS AND CONNECTOR (COMPRESSOR RELAY - GROUND)<br />
Compressor relay (30) - Ground<br />
Compressor relay (85) - Ground<br />
04-187<br />
3. CHECK HARNESS AND CONNECTOR (COMPRESSOR - GROUND)<br />
Disconnect the E013 compressor connector.<br />
Start the engine, turn A/C switch on.<br />
E013 (1) - Ground<br />
YES > Replace the compressor.<br />
4. CHECK HARNESS AND CONNECTOR (COMPRESSOR RELAY - ENGINE ELECTRONIC CON-<br />
TROL MODULE(4G69) / ENGINE ECM(ISF2.8) )<br />
Disconnect the C016 blower switch connector.<br />
Compressor relay (86) - A036 (48)<br />
Compressor relay (86) - E001 (10)<br />
5. INSPECT TRIPLE PRESSURE SWITCH<br />
Disconnect the V017 triple pressure switch connector.<br />
04-188<br />
Inspect the triple pressure switch according to the<br />
V017 (1) - V017 (4)<br />
V017 (2) - V017 (3)<br />
NO > Replace the triple pressure switch.<br />
6. CHECK HARNESS AND CONNECTOR (TRIPLE PRESSURE SWITCH - ENGINE ELECTRONIC<br />
CONTROL MODULE(4G69) / ENGINE ECM(ISF2.8) )<br />
V017 (4) - E001 (79)<br />
V017 (3) - E001 (26)<br />
V017 (4) - A036 (27)<br />
V017 (3) - A036 (11)<br />
7. CHECK HARNESS AND CONNECTOR (TRIPLE PRESSURE SWITCH - A/C CONTROL PANEL)<br />
04-189<br />
V017 (2) - I020 (9)<br />
YES > Go to next step for 4G69, go to step 9 for ISF2.8.<br />
8. CHECK HARNESS AND CONNECTOR (TRIPLE PRESSURE SWITCH - GROUND)(4G69)<br />
V017 (2) - Ground<br />
9. CHECK HARNESS AND CONNECTOR (TRIPLE PRESSURE SWITCH - ENGINE ECM)(ISF2.8)<br />
Disconnect the A036 engine ECM connector.<br />
V017 (2) - A036 (29)<br />
04-190<br />
10. INSPECT FRONT EVAPORATOR THERMISTOR<br />
Disconnect the I026 front evaporator thermistor connector.<br />
Inspect the front evaporator thermistor according to the<br />
Check Condition<br />
Specified Condition (KΩ)<br />
2 ℃ 14.5 ~ 15.2<br />
5 ℃ 12.5 ~ 13.0<br />
10 ℃ 9.7 ~ 10.3<br />
15 ℃ 7.6 ~ 8.1<br />
20 ℃ 6.1 ~ 6.4<br />
25 ℃ 4.8 ~ 5.1<br />
NO > Replace the front evaporator thermistor.<br />
11. CHECK HARNESS AND CONNECTOR (FRONT EVAPORATOR THERMISTOR - A/C CONTROL<br />
Inspect the resistance according to the value(s) in the<br />
I026 (1) - I021 (29)<br />
I026 (2) - I021 (33)<br />
04-191<br />
NO COOLING FROM REAR A/C SYSTEM<br />
04-192<br />
1. INSPECT TOP EVAPORATOR TEMPERATURE SENSOR<br />
Disconnect the L004 top evaporator temperature sensor connector.<br />
Inspect the top evaporator temperature sensor according<br />
to the value(s) in the table below.<br />
NO > Replace the top evaporator temperature sensor.<br />
2. CHECK HARNESS AND CONNECTOR (REAR A/C RELAY - REAR A/C SOLENOID VALVE)<br />
Disconnect the N003 rear A/C solenoid valve connector.<br />
When ignition switch turns ON, press the top evaporator blower switch.<br />
N003 (1) - Ground<br />
04-193<br />
3. CHECK HARNESS AND CONNECTOR (REAR A/C SOLENOID VALVE - A/C CONTROL PANEL)<br />
N003 (2) - I021 (36)<br />
4. CHECK HARNESS AND CONNECTOR (REAR A/C SOLENOID VALVE - GROUND)<br />
Standard resistance<br />
N003 (2) - Ground<br />
YES > Replace rear A/C solenoid valve.<br />
04-194<br />
5. CHECK HARNESS AND CONNECTOR (REAR A/C RELAY - A/C CONTROL PANEL)<br />
Rear A/C relay (86) - I020 (1)<br />
04-195<br />
REAR HEATER IS INOPERATIVE OR INSUFFICIENT HEATING<br />
04-196<br />
Inspect the rear heater fuse (15A) in Co - pilot Junction<br />
Box (A003).<br />
2. INSPECT REAR HEATER RELAY<br />
Remove the rear heater relay.<br />
Inspect the rear heater relay according to the value(s) in<br />
NO > Replace the rear heater relay.<br />
04-197<br />
3. INSPECT WATER VALVE RELAY<br />
Remove the water valve relay.<br />
Inspect the water valve relay according to the value(s) in<br />
NO > Replace the water valve relay.<br />
4. INSPECT REAR HEATER BLOWER SWITCH<br />
Disconnect the A007 rear heater blower switch connector.<br />
L<br />
M<br />
H<br />
NO > Replace the rear heater blower switch.<br />
04-198<br />
5. CHECK HARNESS AND CONNECTOR (REAR HEATER RELAY / WATER VALVE RELAY -<br />
GROUND )<br />
Remove the rear blower relay and water valve relay.<br />
When ignition switch turns ON, press the rear blower forward switch.<br />
Rear heater relay (85) - Ground<br />
Water valve relay (85) - Ground<br />
6. CHECK HARNESS AND CONNECTOR (REAR HEATER BLOWER SWITCH - REAR BLOWER<br />
RELAY/WATER VALVE REALY)<br />
Remove the rear blower relay.<br />
A007 (2) - Rear heater relay (86)<br />
A007 (2) - Water valve relay (86)<br />
04-199<br />
7. CHECK HARNESS AND CONNECTOR (REAR HEATER BLOWER SWITCH - GROUND)<br />
A007 (3) - Ground<br />
A007 (1) - Ground<br />
8. CHECK HARNESS AND CONNECTOR (REAR HEATER SOLENOID VALVE - GROUND)<br />
Disconnect the P001 rear heater solenoid valve connector.<br />
When ignition switch turns ON, press the rear heater blower switch.<br />
P001 (1) - Ground<br />
04-200<br />
9. CHECK HARNESS AND CONNECTOR (REAR HEATER SOLENOID VALVE - GROUND)<br />
P001 (2) - Ground<br />
YES > Replace rear heater solenoid valve.<br />
10. CHECK HARNESS AND CONNECTOR ( REAR HEATER RELAY - REAR HEATER MOTOR )<br />
Disconnect the P002 rear heater motor connector.<br />
When ignition switch turns ON, press the rear heater forward switch and rear heater blower switch.<br />
P002 (2) - Ground<br />
04-201<br />
11. CHECK HARNESS AND CONNECTOR ( REAR HEATER MOTOR - REAR HEATER BLOWER<br />
P002 (4) - A007 (4)<br />
P002 (1) - A007 (5)<br />
P002 (3) - A007 (6)<br />
YES > Replace rear heater motor.<br />
04-202<br />
DIAGNOSTICS - LIGHTING SYSTEM<br />
1. PRECAUTION FOR USING BATTERY DURING INSPECTION.<br />
(a) While using the battery during inspection, do not bring the positive and negative tester probes too close<br />
to each other as a short circuit may occur.<br />
2. PRECAUTION FOR HEADLIGHT BULB REPLACEMENT.<br />
(a) If even a thin film of oil is left on the surface of the halogen light, the bulb may be damaged because the<br />
light will burn at a higher temperature.<br />
(b) Handle any halogen light with great care. Dropping, hitting or damaging the bulb, in any way, may result<br />
in exploding and shattering because the internal pressure is high.<br />
(c) Always prepare a new bulb for immediate replacement. While replacing the bulb, the lens may attract<br />
dust and moisture if removed from the vehicle for too long.<br />
(d) Always use a bulb of the same wattage for replacement.<br />
(e) Firmly reinstall the socket after bulb replacement. The lens may become cloudy or the light cavity may<br />
fill with water through the gaps around the socket.<br />
3. EXPRESSIONS OF IGNITION SWITCH.<br />
04-203<br />
Check the battery voltage.<br />
• The voltage should not be below 12 V.<br />
Charge or replace battery. Refer to “Chapter<br />
20A/20B starting and charging - battery,<br />
replacement”<br />
Check the LO - beam lamps.<br />
• Turn the ignition switch ON.<br />
• Check the LO - beam lamps.<br />
Check the HI - beam lamps.<br />
Check the turn signal lamps.<br />
Check the hazard lamps.<br />
Check the Indoor Lamps.<br />
Check harness and connector<br />
04-204<br />
04-205<br />
1 Front Combination Lamp Assy LH<br />
2 Front Fog Lamp Assy LH<br />
3 Front Combination Lamp Assy RH<br />
4 Front Fog Lamp Assy RH<br />
5 Rear Combination Lamp Assy LH<br />
6 High - mounted Stop Lamp Assy<br />
7 License Lamp Assy<br />
8 Rear Combination Lamp Assy RH<br />
04-206<br />
LO - beam headlamp is<br />
inoperative (One side)<br />
2. Wire harness -<br />
LO - beam headlamps are<br />
inoperative (Both sides)<br />
HI - beam headlamp is<br />
4. Combination switch<br />
Chapter 64 lighting - combination switch,<br />
HI - beam headlamps are<br />
3. Combination switch<br />
4. Wire harness -<br />
LO - beam and HI - beam<br />
headlamps are inoperative<br />
(One side)<br />
1. Bulb(s)<br />
Chapter 64 lighting - front combination Lamp<br />
assy, replacement<br />
1. Fuse<br />
(Both sides)<br />
4. Bulb(s)<br />
Front fog lamps are<br />
2. Combination switch<br />
3. Bulb(s)<br />
Chapter 64 lighting - front fog lamp assy,<br />
4. Relay -<br />
04-207<br />
Front fog lamps are always<br />
on<br />
1. Combination switch<br />
2. Front fog lamp relay -<br />
Rear fog lamps are<br />
Chapter 64 lighting - rear combination Lamp<br />
Rear fog lamps are always<br />
2. Rear fog lamp relay -<br />
All fog lamps are<br />
Hazard warning lamps are<br />
inoperative (Turn signal<br />
lamps are normal)<br />
2. Hazard warning switch -<br />
urn signal lamps are<br />
inoperative (Hazard<br />
warning lamps are normal)<br />
3. Hazard warning switch -<br />
Hazard warning and turn<br />
signal lamps are<br />
3. Flasher -<br />
04-208<br />
5. Combination switch<br />
Turn signal lamps are<br />
2. Bulb(s)<br />
1. Hazard warning switch -<br />
2. Flasher -<br />
All stop lamps are<br />
2. Stop lamp switch<br />
Chapter 35 brake - brake pedal,<br />
Chapter 64 lighting - high - mounted stop<br />
lamp assy, replacement<br />
Stop lamp is inoperative<br />
High - mounted stop lamp<br />
is inoperative<br />
Back - up lamps are<br />
inoperative(Both sides)<br />
Back - up lamp is<br />
2. Back - up lamp switch<br />
Chapter 41 transmission - transmission<br />
(yanchengzhongma ZM001), replacement<br />
(tangshanaixin), replacement<br />
04-209<br />
Ignition switch illumination<br />
Central dome light is<br />
Air purifier lamp is<br />
1. Bulb(s) -<br />
2. Central locking controller<br />
assy<br />
Chapter 64 lighting - rear combination lamp,<br />
Chapter 85 door locks - alarm controller,<br />
Chapter 64 lighting - middle dome light assy,<br />
Chapter 64 lighting - step lamp assy,<br />
Step lamp are inoperative<br />
3. Middle door lamp switch<br />
RH<br />
Trunk lamp is inoperative<br />
Front dome light is<br />
3. Rear hatch lock assy -<br />
Chapter 64 lighting - front dome light assy,<br />
All interior illumination<br />
lamps are inoperative<br />
Instrument cluster<br />
illumination is not<br />
2. Instrument cluster<br />
Chapter 83 instrument - instrument cluster,<br />
04-210<br />
Diagnosis switch<br />
wiring diagram<br />
1. Diagnosis switch -<br />
2. Wire harness<br />
Cigarette lighter<br />
1. Cigarette Lighter<br />
Chapter 66 audio system - electric device<br />
accessories, replacement<br />
A/C control panel<br />
Rear blower forward switch<br />
Radio illumination is not<br />
Dome light switch<br />
Outside mirror defroster<br />
switch illumination is not<br />
Headlamp dimmer switch<br />
Rear window defroster<br />
Instrument dimmer switch<br />
Hazard warning switch<br />
WIdth lamps is not<br />
Tail lamps are inoperative<br />
1. Rear blower forward switch -<br />
1. Radio<br />
1. Dome light switch -<br />
1. Outside mirror defroster<br />
1. Headlamp dimmer switch -<br />
1. Rear window defroster<br />
1. Instrument dimmer switch -<br />
Chapter 61 heater and air conditioning -multi -<br />
media And Air - condition Controler Assy,<br />
Chapter 66 audio system - multi - media And<br />
air - condition controler Assy, replacement<br />
Chapter 64 lighting - front combination lamp<br />
LH, replacement<br />
Chapter 64 lighting - rear combination lamp<br />
04-211<br />
License lamp is inoperative<br />
Width lamps tail lamps and<br />
license lamp are<br />
Chapter 64 lighting - licence lamp assy,<br />
04-212<br />
LO - BEAM HEADLAMP IS INOPERATIVE (ONE SIDE)<br />
04-213<br />
• This inspection procedure is an example of lo - beam headlamp LH, lo - beam headlamp RH inspection<br />
procedure is similar.<br />
1. INSPECT BULB<br />
Disconnect the V003 headlamp LH connector.<br />
Replace the headlamp LH bulb.<br />
Does the lo - beam headlamp LH work correctly?<br />
YES > Replace the headlamp LH bulb.<br />
2. CHECK HARNESS AND CONNECTOR (LO - BEAM LH FUSE - HEADLAMP LH)<br />
Lo - beam LH fuse (7.5A) - V003 (3)<br />
V003 (3) - Ground<br />
YES > Replace Lo - beam LH fuse (7.5A) in driver side junction box (I001).<br />
04-214<br />
LO - BEAM HEADLAMPS ARE INOPERATIVE (BOTH SIDES)<br />
04-215<br />
1. INSPECT HEADLAMP BULBS BOTH LH AND RH<br />
Disconnect the V006 headlamp RH connector.<br />
Replace headlamp bulb RH.<br />
Do both lo - beam headlamps work correctly?<br />
YES > Replace headlamp Bulbs both LH and RH.<br />
2. INSPECT LO - BEAM RELAY<br />
Remove lo - beam relay in driver side junction box (I001).<br />
Inspect lo - beamheadlamp relay according to the<br />
Normal<br />
Apply battery voltage to<br />
terminals 85 and 86<br />
85 - 86 breakover<br />
30 - 87<br />
NO > Replace lo - beamheadlamp relay.<br />
04-216<br />
3. INSPECT COMBINATION SWITCH (LIGHT)<br />
Disconnect the I012 combination switch (light) connector.<br />
Inspect the combination switch according to the value(s)<br />
Set the lo - beam headlamp<br />
switch to OFF<br />
switch to ON<br />
8 - 11<br />
NO > Replace the combination switch.<br />
4. CHECK HARNESS AND CONNECTOR (LO - BEAM RELAY - COMBINATION SWITCH (LIGHT))<br />
Lo - beam Relay (86) - I012 (8)<br />
04-217<br />
5. CHECK HARNESS AND CONNECTOR (LO - BEAM FUSES BOTH LH AND RH, LO - BEAM<br />
HEADLAMPS BOTH LH AND RH)<br />
Lo - beam fuse RH (7.5A) - V006 (3)<br />
V006 (3) - Ground<br />
YES > Replace lo - beam headlamp fuse (7.5A) both LH and RH in driver side fuse box (I001).<br />
04-218<br />
HI - BEAM HEADLAMP IS INOPERATIVE (ONE SIDE)<br />
04-219<br />
• This inspection procedure is an example of hi - beam headlamp LH, hi - beam headlamp RH inspection<br />
Does hi - beam headlamp LH work correctly?<br />
2. CHECK HARNESS AND CONNECTOR (HI - BEAM LH FUSE - HEADLAMP LH)<br />
Hi - beam LH fuse (10A) - V003(2)<br />
V003 (2) - Ground<br />
YES > Replace Hi - beam LH Fuse(10A) in driver side junction box (I001).<br />
04-220<br />
HI - BEAM HEADLAMPS ARE INOPERATIVE (BOTH SIDES)<br />
04-221<br />
Replace headlamp Bulb RH.<br />
Do both hi - beam headlamps work correctly?<br />
2. INSPECT HI - BEAM RELAY<br />
Remove hi - beam relay in driver side junction box (I001).<br />
Inspect hi - beamheadlamp relay according to the<br />
value(s) in the table below<br />
Connection<br />
Namal<br />
85 - 86 Breakover<br />
NO > Replace hi - beam relay.<br />
Disconnect the i012 combination switch (light) connector.<br />
04-222<br />
Set the hi - beam headlamp<br />
9 - 11<br />
4. CHECK HARNESS AND CONNECTOR (HI - BEAM RELAY - COMBINATION SWITCH (LIGHT))<br />
hi - beam relay (86) - I012 (9)<br />
04-223<br />
5. CHECK HARNESS AND CONNECTOR (HI - BEAM FUSES BOTH LH AND RH, HI - BEAM<br />
HEADLAMPS BOTH LH AND RH )<br />
Hi - beam LH fuse (10A) - V003 (2)<br />
Hi - beam RH fuse (10A) - V006 (2)<br />
V006 (2) - Ground<br />
YES > Replace hi - beam fuses both LH and RH in driver side box (I001).<br />
04-224<br />
LO - BEAM AND HI - BEAM HEADLAMPS ARE INOPERATIVE (ONE<br />
SIDE)<br />
04-225<br />
• This inspection procedure is an example of hi - beam headlamp and lo - beam headlamp LH, hi - beam<br />
headlamp and lo - beam headlamp RH inspection procedure is similar.<br />
2. CHECK HARNESS AND CONNECTOR (HEADLAMP LH - GROUND)<br />
V003 (1) - Ground<br />
3. CHECK HARNESS AND CONNECTOR (HI - BEAM FUSE AND LOW - BEAM FUSE LH -<br />
HEADLAMP LH)<br />
04-226<br />
Hi - beam LH fuse (10 A) - V003 (2)<br />
Lo - beam LH fuse (7.5 A) - V003 (3)<br />
YES > Replace hi - beam fuse and lo - beam fuse LH in driver side junction box (I001).<br />
04-227<br />
ALL HEADLAMPS ARE INOPERATIVE<br />
04-228<br />
Inspect the headlamp fuse (20A) in driver side junction<br />
box (I001).<br />
2. CHECK HARNESS AND CONNECTOR (COMBINATION SWITCH (LIGHT) - GROUND)<br />
I012 (11) - Ground<br />
04-229<br />
in the table below..<br />
4. INSPECT HEADLAMP BULBS BOTH LH AND RH<br />
Does both headlamp hulbs work correctly?<br />
YES > Replace headlamp bulbs both LH and RH.<br />
5. CHECK HARNESS AND CONNECTOR (HEADLAMP BOTH LH AND RH - GROUND)<br />
V006 (1) - Ground<br />
04-230<br />
6. INSPECT HI - BEAM RELAY AND LO - BEAM RELAY<br />
30 - 87 ≥ 1 MΩ<br />
NO > Replace relays.<br />
7. CHECK HARNESS AND CONNECTOR (HI - BEAM RELAY AND LO - BEAM RELAY -<br />
COMBINATION SWITCH)<br />
04-231<br />
Hi - beam relay (86) - I012 (9)<br />
Lo - beam relay (86) - I012 (8)<br />
8. CHECK HARNESS AND CONNECTOR (HI - BEAM FUSE AND LO - BEAM FUSE BOTH LH AND<br />
RH - HEADLAMP BOTH LH AND RH)<br />
04-232<br />
Lo - beam RH fuse (7.5A) - V006 (3)<br />
YES > Replace hi - beam fuse (10A) and lo - beam fuse (7.5A) both LH and RH in the driver side junction box<br />
04-233<br />
FRONT FOG LAMPS ARE INOPERATIVE<br />
04-234<br />
Inspect front fog lamp fuse (15 A) in driver side junction<br />
YES > Go to step 3.<br />
2. CHECK HARNESS AND CONNECTOR (FRONT FOG LAMP RELAY - FRONT FOG LAMP)<br />
Remove front fog relay in driver side junction box (I001).<br />
Disconnect the C001 front fog lamp LH connector.<br />
Disconnect the C002 front fog lamp RH connector.<br />
Disconnect the I002 instrument cluster A connector.<br />
C001 (1) - Ground<br />
YES > Replace the fuse.<br />
NO > Repair or replace harness or connector,and replace the fuse.<br />
04-235<br />
3. INSPECT FRONT FOG LAMP BULBS<br />
relace front fog lamp bulb LH.<br />
relace front fog lamp bulb RH.<br />
YES > Replace front fog lamp bulb both LH and RH.<br />
4. INSPECT COMBINATION SWITCH (LIGHT)<br />
Disconnect the I012 combination switch connector.<br />
Set the front fog lamp<br />
2 - 4 < 2 Ω<br />
2 - 4 ≥ 1 MΩ<br />
5. CHECK HARNESS AND CONNECTOR (FRONT FOG LAMP RELAY - COMBINATION SWITCH<br />
(LIGHT))<br />
Remove front fog lamp relay in driver side junction box (I001).<br />
04-236<br />
Front fog lamp relay (86) - I012 (2)<br />
6. CHECK HARNESS AND CONNECTOR (FRONT FOG LAMP RELAY - FRONT FOG LAMP)<br />
Front fog lamp relay (87) - C001 (1)<br />
Front fog lamp relay (87) - C002 (1)<br />
04-237<br />
7. CHECK HARNESS AND CONNECTOR (FRONT FOG LAMP - GROUND)<br />
C001 (2) - Ground<br />
C002 (2) - Ground<br />
YES > Replace front fog lamp relay.<br />
04-238<br />
FRONT FOG LAMPS ARE ALWAYS ON<br />
04-239<br />
1. INSPECT COMBINATION SWITCH (LIGHT)<br />
2. CHECK HARNESS AND CONNECTOR (FRONT FOG LAMP RELAY - COMBINATION SWITCH)<br />
I012 (2) - Ground<br />
04-240<br />
3. CHECK HARNESS AND CONNECTOR (FRONT FOG LAMP RELAY - FRONT FOG LAMP)<br />
(b) Remove front fog lamp relay in driver side junction box (I001).<br />
(c) Connect the battery negative cable, check the wire harness for short to power supply.<br />
The front fog lamps should not light.<br />
04-241<br />
REAR FOG LAMPS ARE INOPERATIVE<br />
04-242<br />
Inspect rear fog lamp fuse (10A) in driver side junction<br />
2. CHECK HARNESS AND CONNECTOR (REAR FOG LAMP RELAY - REAR FOG LAMP)<br />
Remove rear fog lamp relay in driver side junction box (I001).<br />
Disconnect the F006 rear combination lamp LH connector.<br />
Disconnect the G001 rear combination lamp RH connector.<br />
Disconnect the I003 instrument cluster B connector.<br />
F006 (5) - Ground<br />
04-243<br />
Set the rear foglamp<br />
3 - 4 < 2 Ω<br />
3 - 4 ≥ 1 MΩ<br />
4. CHECK HARNESS AND CONNECTOR (REAR FOG LAMP RELAY - COMBINATION SWITCH (LIGHT))<br />
Rear fog lamp relay (86) - I012 (3)<br />
04-244<br />
5. CHECK HARNESS AND CONNECTOR (REAR FOG LAMP - GROUND)<br />
F006 (2) - Ground<br />
G001 (2) - Ground<br />
6. INSPECT REAR FOG LAMP BULBS<br />
Replace rear fog lamp bulb LH.<br />
Replace rear fog lamp bulb RH.<br />
YES > Replace rear fog lamp bulb both LH and RH.<br />
04-245<br />
7. CHECK HARNESS AND CONNECTOR (REAR FOG LAMP RELAY - REAR FOG LAMP LH)<br />
Rear fog lamp relay (87) - F006 (5)<br />
Rear fog lamp relay (87) - G001 (5)<br />
YES > Replace rear fog lamp relay.<br />
04-246<br />
REAR FOG LAMPS ARE ALWAYS ON<br />
04-247<br />
2. CHECK HARNESS AND CONNECTOR (REAR FOG LAMP RELAY - COMBINATION SWITCH)<br />
I012 (3) - Ground<br />
04-248<br />
3. CHECK HARNESS AND CONNECTOR (REAR FOG LAMP RELAY - REAR FOG LAMP)<br />
(b) Remove rear fog lamp relay in driver side junction box (I001).<br />
The rear fog lamps should not light.<br />
04-249<br />
ALL FOG LAMPS ARE INOPERATIVE<br />
04-250<br />
Inspect the front fog lamp fuse (15 A) in driver side junction<br />
Inspect the rear fog lamp fuse (10 A) in driver side junction<br />
YES > Go to step 4.<br />
NO > If front fog lamp fuse (15 A) is damage,go to next step.<br />
If rear fog lamp fuse (10 A) is damage,go to step 3.<br />
If both front and rear fog lamp fuses are damage,go to step 2 and step 3.<br />
04-251<br />
4. CHECK HARNESS AND CONNECTOR (COMBINATION SWITCH (LIGHT) - GROUND)<br />
I012 (4) - Ground<br />
04-252<br />
5. INSPECT COMBINATION SWITCH (LIGHT)<br />
Set the front foglamp<br />
2 - 4<br />
6. NSPECT BOTH FRONT AND REAR FOG LAMP RELAYS.<br />
Remove rear fog relay in driver side junction box (I001).<br />
Inspect relays according to the value(s) in the table<br />
below.. .<br />
• Front fog lamp relay and rear fog lamp relay have<br />
same pins.<br />
• Both relays shoud be measured.<br />
04-253<br />
7. CHECK HARNESS AND CONNECTOR (FRONT FOG LAMP RELAY AND REAR FOG LAMP<br />
RELAY - COMBINATION SWITCH (LIGHT))<br />
8. CHECK HARNESS AND CONNECTOR (FRONT AND REAR FOG LAMP RELAY - FRONT FOG<br />
LAMP LH AND RE ,REAR FOG LAMP LH AND RH)<br />
04-254<br />
9. CHECK HARNESS AND CONNECTOR (FRONT FOG LAMP LH AND REAR FOG LAMP LH AND<br />
RH - GROUND)<br />
04-255<br />
YES > Replace all fog lamp bulbs.<br />
04-256<br />
LAMPS ARE NORMAL)<br />
04-257<br />
Inspect the hazard warning fuse (15A) in driver side<br />
junction box (I001).<br />
2. CHECK HARNESS AND CONNECTOR (HAZARD WARNING FUSE - HAZARD WARNING SWITCH)<br />
Disconnect the I006 hazard warning switch connector.<br />
I006 (8) - Ground<br />
3. CHECK HARNESS AND CONNECTOR (HAZARD WARNING SWITCH - FLASHER)<br />
Disconnect the I034 flasher connector.<br />
04-258<br />
I006 (6) - I034 (3)<br />
4. CHECK HARNESS AND CONNECTOR (HAZARD WARNING FUSE - HAZARD WARNING SWITCH)<br />
Hazard warning fuse (15A) - I006 (8)<br />
5. CHECK HARNESS AND CONNECTOR (HAZARD WARNING SWITCH - ALL TURN SIGNAL LAMPS)<br />
Disconnect the V004 front turn signal lamp LH connector.<br />
Disconnect the V008 front turn signal lamp RH connector.<br />
04-259<br />
I006 (5) - V004 (2)<br />
I006 (5) - F006 (4)<br />
I006 (4) - V008 (2)<br />
I006 (4) - G001 (4)<br />
YES > Replace hazard warning switch.<br />
04-260<br />
04-261<br />
Inspect the turn signal fuse (10A) in driver side junction<br />
2. CHECK HARNESS AND CONNECTOR (TURN SIGNAL FUSE - HAZARD WARNING SWITCH)<br />
I006 (10) - Ground<br />
3. INSPECT COMBINATION SWITCH (TURN SIGNAL SWITCH)<br />
Disconnect the I012 combination switch (turn signal switch) connector.<br />
04-262<br />
Inspect combination switch (turn signal switch) according<br />
Turn the turn signal<br />
switch OFF<br />
Set turn signal switch to<br />
LEFT<br />
RIGHT<br />
6 - 5<br />
6 - 7<br />
4. CHECK HARNESS AND CONNECTOR (TURN SIGNAL FUSE - HAZARD WARNING SWITCH)<br />
Turn signal fuse (10A) - I006 (10)<br />
5. CHECK HARNESS AND CONNECTOR (FLASHER - COMBINATION SWITCH (TURN SIGNAL SWITCH))<br />
04-263<br />
I034 (3) - I012 (6)<br />
6. CHECK HARNESS AND CONNECTOR (COMBINATION SWITCH (TURN SIGNAL SWITCH) - ALL<br />
TURN SIGNAL LAMPS)<br />
I012 (5) - V004 (2)<br />
I012 (5) - F006 (4)<br />
I012 (7) - V008 (2)<br />
I012 (7) - G001 (4)<br />
04-264<br />
HAZARD WARNING AND TURN SIGNAL LAMPS ARE INOPERATIVE<br />
04-265<br />
NO > If hazard warning fuse (15A) is damage, go to next step.<br />
If turn signal fuse (10A) is damage,go to step 3.<br />
If both hazard warning fuse (15A) and turn signal fuse (10A) are damge,go to step 2 and step 3.<br />
≥ 1 ΜΩ<br />
3. CHECK HARNESS AND CONNECTOR (TURN SIGNAL FUSE - HAZARD WARNING SWITCH)<br />
04-266<br />
4. CHECK HARNESS AND CONNECTOR (HAZARD WARNING SWITCH - FLASHER)<br />
I034 (2) - Ground<br />
5. INSPECT HAZARD WARNING SWITCH<br />
Inspect the hazard warning switch according to the<br />
Set hazard warning<br />
switch ON<br />
7 - 10<br />
7 - 8<br />
6 - 5 - 4<br />
04-267<br />
NO > Relace hazard warning switch.<br />
6. CHECK HARNESS AND CONNECTOR (FLASHER - GROUND)<br />
I034 (1) - Ground<br />
7. CHECK HARNESS AND CONNECTOR (HAZARD WARNING SWITCH - FLASHER)<br />
I006 (7) - I034 (2)<br />
8. CHECK HARNESS AND CONNECTOR (HAZARD WARNING SWITCH - HAZARD WARNING FUSE<br />
AND TURN SIGNAL FUSE)<br />
04-268<br />
I006 (8) - Hazard warning fuse (15A)<br />
I006 (10) - Turn signal fuse (10A)<br />
9. INSPECT FLASHER<br />
Replace flasher.<br />
YES > Replace flasher.<br />
10. CHECK HARNESS AND CONNECTOR (FLASHER - COMBINATION SWITCH)<br />
04-269<br />
11. INSPECT COMBINATION SWITCH<br />
12. CHECK HARNESS AND CONNECTOR (TURN SIGNAL LAMP - GROUND)<br />
04-270<br />
V004 (1) - Ground<br />
V008 (1) - Ground<br />
13. CHECK HARNESS AND CONNECTOR (HAZARD WARNING SWITCH - ALL TURN SIGNAL LAMPS)<br />
04-271<br />
14. CHECK HARNESS AND CONNECTOR (COMBINATION SWITCH (TURN SIGNAL SWITCH) - ALL<br />
YES > Replace 4 turn signal lamp bulbs.<br />
04-272<br />
TURN SIGNAL LAMPS ARE INOPERATIVE (ONE SIDE)<br />
04-273<br />
• This inspection procedure is an example of turn signal lamp LH, turn signal lamp RH inspection<br />
1. INSPECT COMBINATION SWITCH<br />
If only one turn signal lamp is not bright,over this step.<br />
Disconnect the I012 combination switch(turn signal lamp) connector.<br />
• If only turn signal lamps LH is not bright,measure 6 -<br />
5.<br />
• If only turn signal lamps RH is not bright,measure 6 -<br />
7.<br />
2. CHECK HARNESS AND CONNECTOR (COMBINATION SWITCH (TURN SIGNAL SWITCH) - TURN<br />
SIGNAL LAMP)<br />
• If only front turn signal lamps LH is not bright,step d isn’t performed.<br />
• If only rear turn signal lamps LH is not bright,step c isn’t performed.<br />
(b) Disconnect the I012 combination switch(turn signal lamp) connector.<br />
(c) Disconnect the V004 front turn signal lamp LH connector.<br />
(d) Disconnect the F006 rear combination lamp LH connector.<br />
04-274<br />
• If only front turn signal lamps LH is not bright,measure<br />
I012 (5) - V004 (2) only.<br />
• If only rear turn signal lamps LH is not bright,measure<br />
I012 (5) - F006 (4) only.<br />
3. CHECK HARNESS AND CONNECTOR (TURN SIGNAL LAMP - GROUND)<br />
• If only front turn signal lamps LH is not bright,step c isn’t performed.<br />
• If only rear turn signal lamps LH is not bright,step b isn’t performed.<br />
(b) Disconnect the V004 front turn signal lamp LH connector.<br />
(c) Disconnect the F006 rear combination lamp LH connector.<br />
YES > Replace turn signal lamp bulb(s).<br />
V004 (1) - Ground only.<br />
F006 (2) - Ground only.<br />
04-275<br />
HAZARD WARNING LAMPS ARE ALWAYS ON<br />
04-276<br />
1. INSPECT HAZARD WARNING SWITCH<br />
NO > Replace hazard warning switch.<br />
2. CHECK HARNESS AND CONNECTOR (HAZARD WARNING SWITCH - TURN SIGNAL LAMP)<br />
Connect the battery negative cable,check the wire harness for shot to ground,hazard warning lamp is<br />
shoud not be bright.<br />
04-277<br />
ALL STOP LAMPS ARE INOPERATIVE<br />
04-278<br />
Inspect the stop lamp fuse (15A) in engine room junction<br />
box(A002).<br />
2. CHECK HARNESS AND CONNECTOR (BRAKE LAMP FUSE - STOP LAMP SWITCH)<br />
A025 (2) - Ground<br />
3. CHECK HARNESS AND CONNECTOR (STOP LAMP SWITCH - STOP LAMP)<br />
Disconnect the U002 high - mounted stop lamp connector.<br />
04-279<br />
F006 (3) - Ground<br />
4. INSPECT STOP LAMP SWITCH<br />
Inspect the stop lamp switch according to the value(s) in<br />
Set stop lamp switch OFF 1 - 2 ≥ 1 MΩ<br />
Set stop lamp switch ON 1 - 2 < 2 Ω<br />
5. CHECK HARNESS AND CONNECTOR ( BRAKE LAMP FUSE - STOP LAMP SWITCH)<br />
04-280<br />
Stop lamp fuse (15A) - A025 (2)<br />
6. CHECK HARNESS AND CONNECTOR (STOP LAMP SWITCH - STOP LAMP)<br />
A025(1) - F006 (3)<br />
A025(1) - G001(3)<br />
A025(1) - U002 (2)<br />
04-281<br />
7. CHECK HARNESS AND CONNECTOR (STOP LAMP - GROUND)<br />
U002 (1) - Ground<br />
YES > Replace stop lamp bulbs.<br />
04-282<br />
STOP LAMP IS INOPERATIVE (ONE SIDE)<br />
04-283<br />
• This inspection procedure is an example of stop lamp LH, stop lamp RH inspection procedure is similar.<br />
1. CHECK HARNESS AND CONNECTOR (REAR COMBINATION LAMP - GROUND)<br />
2. CHECK HARNESS AND CONNECTOR (STOP LAMP SWITCH - REAR COMBINATION LAMP)<br />
A025 (1) - F006 (3)<br />
YES > Replace stop lamp bulb.<br />
04-284<br />
HIGH - MOUNTED STOP LAMP IS INOPERATIVE<br />
04-285<br />
1. CHECK HARNESS AND CONNECTOR (HIGH - MOUNTED STOP LAMP - GROUND)<br />
2. CHECK HARNESS AND CONNECTOR (STOP LAMP SWITCH - HIGH - MOUNTED STOP LAMP)<br />
A025 (1) - U002 (2)<br />
YES > Replace high - mounted stop lamp bulb.<br />
04-286<br />
BACK - UP LAMP IS INOPERATIVE(ONE SIDE)<br />
04-287<br />
• This inspection procedure is an example of back - up lamp LH, back - up lamp RH inspection procedure<br />
is similar.<br />
Check harness and connector (back - up lamp - ground)<br />
3. CHECK HARNESS AND CONNECTOR (BACK - UP LAMP SWITCH - BACK - UP LAMP)<br />
Disconnect the A021 back - up lamp switch connector.<br />
A021 (2) - F006 (6)<br />
YES > Replace back - up lamp bulb.<br />
04-288<br />
BACK - UP LAMPS ARE INOPERATIVE (BOTH SIDES)<br />
04-289<br />
Inspect the back - up lamp fuse (10A) in driver side<br />
2. CHECK HARNESS AND CONNECTOR (BACK - UP LAMP FUSE - BACK - UP LAMP SWITCH)<br />
A021 (1) - Ground<br />
04-290<br />
F006 (6) - Ground<br />
4. INSPECT BACK - UP LAMP SWITCH<br />
Inspect the back - up lamp switch according to the<br />
Set back - up lamp<br />
NO > Replace back - up lamp switch.<br />
04-291<br />
5. CHECK HARNESS AND CONNECTOR (BACK - UP LAMP FUSE - BACK - UP LAMP SWITCH)<br />
Back - up lamp (10A) - A021<br />
(1)<br />
6. CHECK HARNESS AND CONNECTOR (BACK - UP LAMP SWITCH - BACK - UP LAMP)<br />
A021 (2) - G001 (6)<br />
04-292<br />
7. CHECK HARNESS AND CONNECTOR (BACK - UP LAMP - GROUND)<br />
YES > Replace back - up lamp bulbs.<br />
04-293<br />
IGNITION SWITCH ILLUMINATION IS INOPERATIVE<br />
04-294<br />
1. INSPECT IGNITION SWITCH ILLUMINATION LAMP.<br />
Disconnect the I010 ignition switch illumination connector.<br />
Replace ignition switch illumination lamp.<br />
YES > Replace ignition switch illumination lamp.<br />
2. CHECK HARNESS AND CONNECTOR (DOME LIGHT FUSE - IGNITION SWITCH ILLUMINATION)<br />
Dome light fuse (10A) - I010 (1)<br />
04-295<br />
3. CHECK HARNESS AND CONNECTOR (IGNITION SWITCH ILLUMINATION - CENTRAL LOCKING<br />
CONTROLLER ASSY)<br />
Disconnect the I008 central locking controller assy connector.<br />
I010 (2) - I008 (B1)<br />
4. CHECK HARNESS AND CONNECTOR (CENTRAL LOCKING CONTROLLER ASSY - GROUND)<br />
I008 (B10) - Ground<br />
YES > Replace central locking controller asssy.<br />
04-296<br />
CENTRAL DOME LIGHT IS INOPERATIVE<br />
04-297<br />
04-298<br />
1. CHECK HARNESS AND CONNECTOR (DOME LIGHT FUSE - CENTRAL DOME LIGHT)<br />
Disconnect the F004 central dome light connector.<br />
Dome light fuse (10A) - F004 (1)<br />
If central dome light can’t be contrled by door lamp switch,over<br />
this step.<br />
If central dome light can be contrled by door lamp switch,over<br />
2. CHECK HARNESS AND CONNECTOR (CENTRAL DOME LIGHT - DOME LIGHT SWITCH AND<br />
MIDDLE DOOR LAMP SWITCH RH)<br />
• If central dome light can be contrled by door lamp switch,perform this step.<br />
• If central dome light can’t be contrled by door lamp switch,over this step ,perform the next step.<br />
(b) Disconnect the F004 central dome light connector.<br />
(c) Disconnect the G003 middle door lamp switch RH connector.<br />
04-299<br />
F004 (3) - I018 (5)<br />
F004 (2) - G003 (1)<br />
YES > Replace central dome light assy.<br />
3. CHECK HARNESS AND CONNECTOR (CENTRAL DOME LIGHT - DOME LIGHT SWITCH)<br />
Disconnect the I018 dome light switch connector.<br />
F004 (2) - I018 (5)<br />
4. INSPECT DOME LIGHT SWITCH<br />
Turn the dome light switch ON.<br />
If the dome light switch has no problem,it should be bright.<br />
NO > Replace dome light switch.<br />
04-300<br />
5. CHECK HARNESS AND CONNECTOR (DOME LIGHT SWITCH - GROUND)<br />
I018 (2) - Ground<br />
04-301<br />
AIR PURIFIER LAMP IS INOPERATIVE<br />
04-302<br />
04-303<br />
1. CHECK HARNESS AND CONNECTOR (DOME LIGHT FUSE - AIR PURIFIER LAMP)<br />
Disconnect the F007 air purifier connector.<br />
Dome light fuse (10A) - F007 (1)<br />
2. CHECK HARNESS AND CONNECTOR (AIR PURIFIER LAMP - DOME LIGHT SWITCH AND<br />
Disconnect the G003 middle door lamp switch RH connector.<br />
F007 (3) - I018 (5)<br />
F007 (2) - G003 (1)<br />
YES > Replace air purifier.<br />
04-304<br />
STEP LAMP ARE INOPERATIVE<br />
04-305<br />
1. INSPECT STEP LAMP<br />
Disconnect the N002 step lamp connector.<br />
Replace step lamp bulb.<br />
Connect the battery negative cable,trun the middle door lamp switch RH ON.<br />
YES > Replace step lamp bulb.<br />
2. CHECK HARNESS AND CONNECTOR (dome light FUSE - STEP LAMP)<br />
dome light fuse (10A) - N002 (1)<br />
04-306<br />
3. CHECK HARNESS AND CONNECTOR (STEP LAMP - MIDDLE DOOR LAMP SWITCH RH)<br />
N002 (2) - G003 (1)<br />
YES > Replace middle door lamp switch RH.<br />
04-307<br />
TRUNK LAMP IS INOPERATIVE<br />
04-308<br />
1. INSPECT TRUNK LAMP<br />
Disconnect the J003 trunk lamp connector.<br />
Replace trunk lamp bulb.<br />
Connect the battery negative cable,turn rear hatch lock assy - switch ON.<br />
YES > Replace trunk lamp bulb.<br />
2. CHECK HARNESS AND CONNECTOR (DOME LIGHT FUSE - TRUNK LAMP)<br />
Dome light fuse (10A) - J003 (1)<br />
3. CHECK HARNESS AND CONNECTOR (TRUNK LAMP - REAR HATCH LOCK ASSY - SWITCH)<br />
Disconnect the J001 rear hatch lock assy - switch connector.<br />
04-309<br />
J003 (2) - J001 (1)<br />
4. CHECK HARNESS AND CONNECTOR (REAR HATCH LOCK ASSY - SWITCH - GROUND)<br />
J001 (2) - Ground<br />
YES > Replace rear hatch lock assy - switch.<br />
04-310<br />
FRONT DOME LIGHT IS INOPERATIVE<br />
04-311<br />
04-312<br />
1. CHECK HARNESS AND CONNECTOR (DOME LIGHT FUSE - FRONT DOME LIGHT)<br />
Disconnect the battery negative cable.front dome light<br />
Disconnect the F001 front dome light connector.<br />
Dome light fuse (10A) - F001 (1)<br />
Dome light fuse (10A) - F001 (2)<br />
2. CHECK HARNESS AND CONNECTOR (FRONT DOME LIGHT - GROUND,FRONT DOOR LAMP<br />
DIODE LH,FRONT DOOR LAMP SWITCH RH,INSTRUMENT CLUSTER)<br />
Disconnect the A029 front door lamp diode LH connector.<br />
Disconnect the A024 front door lamp switch rh connector.<br />
F001 (4) - A029 (1)<br />
F001 (4) - A024 (1)<br />
04-313<br />
F001 (4) - I002 (A30)<br />
F001 (3) - Ground<br />
YES > Replace front dome light assy.<br />
04-314<br />
ALL INTERIOR ILLUMINATION LAMPS ARE INOPERATIVE<br />
04-315<br />
04-316<br />
1. INSPECT LAMPLET RELAY<br />
Remove lamplet relay in driver side junction box (I001).<br />
Inspect lamplet relay according to the value(s) in the<br />
table below<br />
Normal 85 - 86 Breakover<br />
NO > Replace lamplet relay.<br />
2. CHECK HARNESS AND CONNECTOR (LAMPLET RELAY - COMBINATION SWITCH)<br />
remove lamplet relay in driver side junction box (I001).<br />
Lamplet relay (86) - I012 (13)<br />
04-317<br />
3. CHECK HARNESS AND CONNECTOR (COMBINATION SWITCH (LIGHT) - GROUND)<br />
I012 (10) - Ground<br />
inspect lamplet fuse (7.5A) in driver side junction box<br />
inspect switch lighting fuse (7.5A) in driver side junction<br />
YES > Replace the combination switch.<br />
04-318<br />
5. CHECK HARNESS AND CONNECTOR (LAMPLET FUSE - INSTRUMENT CLUSTER)<br />
I002 (A6) - Ground<br />
NO > Repair or replace harness or connector,and go to next step.<br />
6. CHECK HARNESS AND CONNECTOR (SWITCH LIGHTING FUSE - INTERIOR LAMPS)<br />
(k)<br />
(l)<br />
Disconnect the I004 headlamp dimmer switch connector.<br />
Disconnect the I005 instrument dimmer switch connector.<br />
Disconnect the I016 rear window defroster switch connector.<br />
Disconnect the I017 outside mirror defroster switch connector.<br />
Disconnect the I033 cigarette lighter connector.<br />
Disconnect the I031 radio A connector.<br />
Disconnect the I021 A/C control panel B connector.<br />
Disconnect the I019 diagnosis switch connector.<br />
(m)<br />
I006 (2) - Ground<br />
04-319<br />
INSTRUMENT CLUSTER ILLUMINATION IS NOT INOPERATIVE<br />
04-320<br />
Inspect lamplet fuse (7.5A) in driver side junction box<br />
2. CHECK HARNESS AND CONNECTOR (LAMPLET FUSE - INSTRUMENT CLUSTER)<br />
04-321<br />
3. CHECK HARNESS AND CONNECTOR (INSTRUMENT CLUSTER - GROUND)<br />
I002 (A19) - Ground<br />
4. CHECK HARNESS AND CONNECTOR (LAMPLET FUSE - INSTRUMENT CLUSTER)<br />
Lamplet fuse (7.5A) - I002 (A6)<br />
YES > Replace Instrument Cluster.<br />
04-322<br />
DIAGNOSIS SWITCH ILLUMINATION IS NOT INOPERATIVE<br />
04-323<br />
1. CHECK HARNESS AND CONNECTOR (DIAGNOSIS SWITCH - GROUND)<br />
I019 (1) - Ground<br />
2. CHECK HARNESS AND CONNECTOR (SWITCH LIGHTING FUSE - DIAGNOSIS SWITCH)<br />
Switch lighting fuse (7.5A) - I019 (3)<br />
YES > Replace diagnosis switch.<br />
04-324<br />
CIGARETTE LIGHTER ILLUMINATION IS NOT INOPERATIVE<br />
04-325<br />
1. CHECK HARNESS AND CONNECTOR (CIGARETTE LIGHTER - GROUND)<br />
I033 (1) - Ground<br />
2. CHECK HARNESS AND CONNECTOR (SWITCH LIGHTING FUSE - CIGARETTE LIGHTER)<br />
Switch lighting fuse (7.5A) - I033 (3)<br />
YES > Replace cigarette lighter.<br />
04-326<br />
A/C CONTROL PANEL ILLUMINATION IS NOT INOPERATIVE<br />
04-327<br />
1. CHECK HARNESS AND CONNECTOR (A/C CONTROL PANEL - GROUND)<br />
Disconnect the I020 A/C control panel A connector.<br />
2. CHECK HARNESS AND CONNECTOR (SWITCH LIGHTING FUSE - A/C CONTROL PANEL)<br />
Switch lighting fuse (7.5A) - I021 (32)<br />
YES > Replace A/C control panel.<br />
04-328<br />
RADIO ILLUMINATION IS NOT INOPERATIVE<br />
04-329<br />
1. CHECK HARNESS AND CONNECTOR (RADIO - GROUND)<br />
I031 (A8) - Ground<br />
2. CHECK HARNESS AND CONNECTOR (SWITCH LIGHTING FUSE - RADIO)<br />
Switch lighting fuse (7.5A) - I031 (A3)<br />
YES > Raplace radio.<br />
04-330<br />
REAR BLOWER FORWARD SWITCH ILLUMINATION IS NOT INOP-<br />
ERATIVE<br />
04-331<br />
1. CHECK HARNESS AND CONNECTOR (REAR BLOWER FORWARD SWITCH - GROUND)<br />
I023 (1) - Ground<br />
2. CHECK HARNESS AND CONNECTOR (SWITCH LIGHTING FUSE - REAR BLOWER FORWARD<br />
Switch lighting fuse (7.5A) - I023 (3)<br />
YES > Replace rear blower forward switch.<br />
04-332<br />
DOME LIGHT SWITCH ILLUMINATION IS NOT INOPERATIVE<br />
04-333<br />
1. CHECK HARNESS AND CONNECTOR (DOME LIGHT SWITCH - GROUND)<br />
I018 (1) - Ground<br />
2. CHECK HARNESS AND CONNECTOR (SWITCH LIGHTING FUSE - DOME LIGHT SWITCH)<br />
Switch lighting fuse (7.5A) - I018 (3)<br />
YES > Replace dome light switch.<br />
04-334<br />
OUTSIDE MIRROR DEFROSTER SWITCH ILLUMINATION IS NOT<br />
INOPERATIVE<br />
04-335<br />
1. CHECK HARNESS AND CONNECTOR (OUTSIDE MIRROR DEFROSTER SWITCH - GROUND)<br />
I017 (1) - Ground<br />
2. CHECK HARNESS AND CONNECTOR (SWITCH LIGHTING FUSE - OUTSIDE MIRROR DEFROSTER<br />
Switch lighting fuse (7.5A) - I017 (3)<br />
YES > Replace outside mirror defroster switch.<br />
04-336<br />
HEADLAMP DIMMER SWITCH ILLUMINATION IS NOT INOPERA-<br />
TIVE<br />
04-337<br />
1. CHECK HARNESS AND CONNECTOR (HEADLAMP DIMMER SWITCH - Ground)<br />
I004 (6) - Ground<br />
2. CHECK HARNESS AND CONNECTOR (SWITCH LIGHTING FUSE - HEADLAMP DIMMER SWITCH)<br />
Switch lighting fuse (7.5A) - I004 (3)<br />
YES > Replace headlamp dimmer switch.<br />
04-338<br />
REAR WINDOW DEFROSTER SWITCH ILLUMINATION IS NOT<br />
04-339<br />
1. CHECK HARNESS AND CONNECTOR (REAR WINDOW DEFROSTER SWITCH - GROUND)<br />
I016 (1) - Ground<br />
2. CHECK HARNESS AND CONNECTOR (SWITCH LIGHTING FUSE - REAR WINDOW DEFROSTER<br />
Switch lighting fuse (7.5A) - I016 (3)<br />
YES > Replace rear window defroster switch.<br />
04-340<br />
INSTRUMENT DIMMER SWITCH ILLUMINATION IS NOT INOPERA-<br />
04-341<br />
1. CHECK HARNESS AND CONNECTOR (INSTRUMENT DIMMER SWITCH - GROUND)<br />
I005 (6) - Ground<br />
2. CHECK HARNESS AND CONNECTOR (SWITCH LIGHTING FUSE - INSTRUMENT DIMMER SWITCH)<br />
Switch lighting fuse (7.5A) - I005 (3)<br />
YES > Replace instrument dimmer switch.<br />
04-342<br />
HAZARD WARNING SWITCH ILLUMINATION IS NOT INOPERATIVE<br />
04-343<br />
1. CHECK HARNESS AND CONNECTOR (HAZARD WARNING SWITCH - GROUND)<br />
I006 (3) - Ground<br />
2. CHECK HARNESS AND CONNECTOR (SWITCH LIGHTING FUSE - HAZARD WARNING SWITCH)<br />
Switch lighting fuse (7.5A) - I006 (2)<br />
04-344<br />
WIDTH LAMPS IS NOT INOPERATIVE<br />
04-345<br />
1. CHECK HARNESS AND CONNECTOR (WIDTH LAMPS - GROUND)<br />
• If only width lamp LH is not bright,step c isn’t performed.<br />
• If only width lamp RH is not bright,step b isn’t performed.<br />
(b) Disconnect the V002 front position lamp LH connector.<br />
(c) Disconnect the V007 front position lamp RH connector.<br />
V002 (1) - Ground<br />
V007 (1) - Ground<br />
• If only width lamp LH is not bright,measure V002 (1) -<br />
Ground onlyl.<br />
• If only width lamp RH is not bright,measure V007 (1) -<br />
Ground only.<br />
2. CHECK HARNESS AND CONNECTOR (LAMPLET FUSE - WIDTH LAMPS)<br />
04-346<br />
Lamplet fuse (7.5A) - V002 (2)<br />
Lamplet fuse (7.5A) - V007 (2)<br />
NIOTE<br />
• If only width lamp LH is not bright,measure lamplet<br />
fuse (7.5A) - V002 (2) only.<br />
• If only width lamp RH is not bright,measure lamplet<br />
fuse (7.5A) - v007 (2) only.<br />
YES > Replace width lamp bulbs.<br />
04-347<br />
TAIL LAMPS ARE INOPERATIVE<br />
04-348<br />
1. CHECK HARNESS AND CONNECTOR (TAIL LAMPS - GROUND)<br />
• If only tail lamp LH is not bright,step c isn’t performed.<br />
• If only tail lamp RH is not bright,step b isn’t performed.<br />
(b) Disconnect the F006 rear combination lamp LH connector.<br />
(c) Disconnect the G001 rear combination lamp RH connector.<br />
• If only tail lamp LH is not bright, measure F006 (2) -<br />
• If only tail lamp RH is not bright,measure G001 (2) -<br />
2. CHECK HARNESS AND CONNECTOR (LAMPLET FUSE - TAIL LAMPS)<br />
04-349<br />
Lamplet fuse (7.5A) - F006 (1)<br />
Lamplet fuse (7.5A) - G001 (1)<br />
• If only tail lamp LH is not bright, measure Lamplet<br />
Fuse (7.5A) - F006 (1) only.<br />
• If only tail lamp RH is not bright,measure Lamplet<br />
Fuse (7.5A) - G001 (1) only.<br />
YES > Replace tail lamp bulbs.<br />
04-350<br />
LICENSE LAMP IS INOPERATIVE<br />
04-351<br />
1. CHECK HARNESS AND CONNECTOR (LICENSE LAMP - GROUND)<br />
Disconnect the J004 license lamp connector.<br />
J004 (2) - Ground<br />
2. CHECK HARNESS AND CONNECTOR (LAMPLET FUSE - LICENSE LAMP)<br />
Lamplet fuse (7.5A) - J004 (1)<br />
YES > Replace license lamp bulbs.<br />
04-352<br />
WIDTH LAMPS TAIL LAMPS AND LICENSE LAMP ARE INOPERA-<br />
04-353<br />
Inspect the lamplet fuse (7.5A) in driver side junction box<br />
2. CHECK HARNESS AND CONNECTOR (LAMPLET FUSE - LAMPLET)<br />
Disconnect the V002 front position lamp LH connector.<br />
Disconnect the V007 front position lamp RH connector.<br />
V002 (2) - Ground<br />
04-354<br />
3. INSPECT LAMPLET RELAY<br />
4. CHECK HARNESS AND CONNECTOR (LAMPLET RELAY - COMBINATION SWITCH (LIGHT))<br />
Remove the lamplet relay in driver side junction box (I001).<br />
lamplet relay (86) - I012 (13)<br />
04-355<br />
5. CHECK HARNESS AND CONNECTOR (COMBINATION SWITCH (LIGHT) - GROUND)<br />
04-356<br />
DIAGNOSTICS - WIPER AND WASHER<br />
1. EXPRESSIONS OF IGNITION SWITCH.<br />
Ignition Switch (position)<br />
LOCK<br />
START<br />
Ignition Switch (condition)<br />
Ignition switch off<br />
Ignition switch on (IG)<br />
Ignition switch on (ACC)<br />
Engine start<br />
2. POWER OFF.<br />
Before removing or installing any electrical device, please disconnect the nagative battery cable to<br />
04-357<br />
1 Front Wiper Arm Assy LH 2 Front Wiper Arm Assy RH<br />
1 Rear Wiper Arm Assy 2 Rear Wiper Blade Assy<br />
04-358<br />
• The voltage should be above 12 V.<br />
Check the wiper motor in HIGH position.<br />
• Set the wiper and washer switch in HIGH<br />
position.<br />
Does the wiper motor operate in high mode?<br />
Check the wiper motor in LOW position.<br />
• Set the wiper and washer switch in LOW<br />
Does the wiper motor operate in low mode?<br />
Check the wiper motor in INT position.<br />
• Set the wiper and washer switch in INT<br />
Does the wiper motor operate in intermittent<br />
mode?<br />
Check wiper and washer switch<br />
04-359<br />
Wipers are inoperative - windshield<br />
2. Wiper and washer switch<br />
3. Windshield wiper motor<br />
Chapter 51 steering column -<br />
combination switch, replacement<br />
Chapter 65 wiper and washer -<br />
wiper motor, replacement<br />
Wipers are inoperative at low speed<br />
- windshield<br />
1. Windshield wiper motor<br />
Wipers are inoperative at high<br />
speed - windshield<br />
Wipers are inoperative in<br />
intermittent mode - windshield<br />
Washer pump is inoperative -<br />
windshield<br />
1. Wiper and washer switch<br />
2. Windshield wiper motor<br />
When the wiper and washer switch<br />
is OFF, the wiper blade does not<br />
retract<br />
Wiper is inoperative - rear window<br />
1. Rear window wiper motor<br />
04-360<br />
Wiper is inoperative in intermittent<br />
mode - rear window<br />
3. Wire harness<br />
1. Washer pump - rear window -<br />
Washer pump is inoperative - rear<br />
window<br />
04-361<br />
WIPERS ARE INOPERATIVE - WINDSHIELD<br />
04-362<br />
Inspect the windshield wiper fuse in driver side junction<br />
box (I001): 15 A.<br />
2. CHECK HARNESS AND CONNECTOR ( FRONT WIPER FUSE - WINDSHIELD WIPER)<br />
Disconnect the V011 windshield wiper assy connector.<br />
Front wiper fuse - V011(2)<br />
Go to next step.<br />
04-363<br />
3. CHECK HARNESS AND CONNECTOR (FRONT WIPER FUSE - COMBINATION SWITCH)<br />
Disconnect the I013 combination switch (wiper and washer control) connector.<br />
Front wiper fuse - I013 (8)<br />
4. CHECK HARNESS AND CONNECTOR (FRONT WIPER FUSE - FRONT WASHING RESERVOIR<br />
MOTOR)<br />
Disconnect the V010 front washing reservoir motor connector.<br />
Front wiper fuse - V010 (2)<br />
04-364<br />
5. INSPECT RELAY IG2<br />
Pull out the relay IG2.<br />
Inspect relay IG2.<br />
terminal 30 and<br />
87<br />
NO > Replace relay IG2.<br />
6. CHECK HARNESS AND CONNECTOR (WINDSHIELD WIPER - GROUND)<br />
Disconnect the V011 windshield wiper connector.<br />
Windshield wiper(V011) -<br />
04-365<br />
7. CHECK HARNESS AND CONNECTOR (COMBINATION SWITCH - WINDSHIELD WIPER)<br />
Disconnect the I013 combination switch connector.<br />
I013(7) - V011(1)<br />
I013(9) - V011(4)<br />
I013(6) - V011(3)<br />
8. INSPECT WINDSHIELD WIPER<br />
Remove the windshield wiper assy.<br />
Inspect the windshield wiper in high mode.<br />
terminal 4 and 5<br />
4 - 5<br />
Windshield wiper<br />
high - speed operation<br />
Inspect windshield wiper in low mode<br />
terminal 1 and 5<br />
1 - 5<br />
low - speed operation<br />
NO > Repair or replace windshield wiper.<br />
04-366<br />
9. CHECK HARNESS AND CONNECTOR (COMBINATION SWITCH - GROUND)<br />
I013(5) - Ground<br />
YES > Replace combination switch.<br />
04-367<br />
WIPERS ARE INOPERATIVE AT LOW SPEED - WINDSHIELD<br />
04-368<br />
Inspect combination switch (wiper and washer control)<br />
according to the value(s) in the table below.<br />
Set the wiper and washer<br />
switch to LOW<br />
8 - 7 ≥ 1 MΩ<br />
8 - 7 < 2 Ω<br />
2. CHECK HARNESS AND CONNECTOR (COMBINATION SWITCH - WINDSHIELD WIPER)<br />
Standard resisance<br />
YES > Replace windshield wiper.<br />
04-369<br />
WIPERS ARE INOPERATIVE AT HIGH SPEED - WINDSHIELD<br />
04-370<br />
Disconnect the V013 combination switch (wiper and washer control) connector.<br />
switch to HIGH<br />
8 - 9 ≥ 1 MΩ<br />
8 - 9 < 2 Ω<br />
Measure the resisitance according to the value(s) in the<br />
I013 (9) - V011(4)<br />
04-371<br />
SHIELD<br />
04-372<br />
1. INSPECT WINDSHIELD WIPER<br />
Inspect the windshield wiper in INT mode.<br />
voltage to terminal<br />
3 and 5<br />
Battery(+) - 3<br />
Battery( - ) - Ground<br />
Front washing<br />
reservoir motor<br />
operates at low<br />
speed<br />
NO > Replace the windshield wiper.<br />
2. CHECK HARNESS AND CONNECTOR ( COMBINATION SWITCH - GROUND)<br />
I013 (5) - Ground<br />
Is the inspecrtion result normal?<br />
04-373<br />
3. CHECK HARNESS AND CONNECTOR (WINDSHIELD WIPER - GROUND)<br />
V011 (5) - Ground<br />
4. CHECK HARNESS AND CONNECTOR (WINDSHIELD WIPER - COMBINATION SWITCH)<br />
I013 (6) - V011 (3)<br />
I013 (7) - V011 (1)<br />
04-374<br />
WASHER PUMP IS INOPERATIVE - WINDSHIELD<br />
04-375<br />
Inspect the front wiper fuse in driver side junction box<br />
(I001): 15 A.<br />
2. INSPECT COMBINATION SWITCH<br />
switch to WASH<br />
4 - 5 ≥ 1 MΩ<br />
4 - 5 < 2 Ω<br />
04-376<br />
3. CHECK HARNESS AND CONNECTOR (DRIVER SIDE JUNCTION CONNECTOR - FRONT WASHER<br />
PUMP)<br />
Disconnect the V010 front washer pump connector.<br />
Driver side junction connector(87)<br />
- V010 (2)<br />
4. CHECK HARNESS AND CONNECTOR (COMBINATION SWITCH - FRONT WASHER PUMP)<br />
V010 (1) - I013 (4)<br />
04-377<br />
5. CHECK HARNESS AND CONNECTOR (COMBINATION SWITCH - GROUND)<br />
YES > Replace the front washer pump.<br />
04-378<br />
WHEN THE WIPER SWITCH IS OFF, THE WIPER BLADE DOES NOT<br />
RETRACT<br />
04-379<br />
5 - 7 < 2 Ω<br />
5 - 7 ≥ 1 MΩ<br />
2. CHECK HARNESS AND CONNECTOR (COMBINATION SWITCH - WINDSHIELD WIPER )<br />
04-380<br />
3. CHECK HARNESS AND CONNECTOR (COMBINATION SWITCH - WINDSHIELD WIPER)<br />
V011(3) - I013 (6)<br />
YES > Repair or replace windshield wiper.<br />
04-381<br />
WIPER IS INOPERATIVE - REAR WINDOW<br />
04-382<br />
Set the rear wiper and<br />
washer switch to ON<br />
2 - 5 ≥ 1 MΩ<br />
2 - 5 < 2 Ω<br />
2. INSPECT FUSE<br />
Inspect the rear wiper fuse in driver side junction box<br />
(I001): 10 A.<br />
04-383<br />
3. CHECK HARNESS AND CONNECTOR (DRIVER SIDE JUNCTION CONNECTOR - COMBINATION<br />
Disconnect rear wiper relay connector.<br />
Rear wiper relay(86) - I013 (2)<br />
NO > Replace fuse.<br />
4. CHECK HARNESS AND CONNECTOR (DRIVER SIDE JUNCTION CONNECTOR - REAR WIPER)<br />
Rear wiper relay(86) - U001 (2)<br />
04-384<br />
5. INSPECT REAR WIPER RELAY<br />
Disconnect rear wiper relay.<br />
Constant 30 - 87a < 2 Ω<br />
Constant 85 - 86 < 2 Ω<br />
terminal 85 and 86<br />
30 - 87a ≥ 1 MΩ<br />
30 - 87 Continuity<br />
NO > Repair or replace rear wiper relay.<br />
6. INSPECT RELAY<br />
Disconnect relay IG2.<br />
NO > Repair or replace relay.<br />
04-385<br />
7. CHECK HARNESS AND CONNECTOR (REAR WIPER RELAY - REAR WIPER)<br />
Rear wiper relay (30) - U001<br />
(4)<br />
8. CHECK HARNESS AND CONNECTOR (REAR WIPER RELAY - REAR WIPER)<br />
04-386<br />
9. CHECK HARNESS AND CONNECTOR (REAR WIPER - GROUND)<br />
Disconnect the U001 rear wiper relay connector.<br />
U001(3) - Ground<br />
YES > Replace the rear wiper.<br />
04-387<br />
WASHER PUMP IS INOPERATIVE - REAR WINDOW<br />
04-388<br />
Set rear wiper and<br />
washer switch to<br />
SART<br />
5 - 2 < 2 Ω<br />
5 - 2 ≥ 1 MΩ<br />
04-389<br />
3. CHECK HARNESS AND CONNECTOR (REAR WIPER FUSE - REAR WASHING RESERVOIR<br />
Disconnect the V009 rear washing reservoir motor connector.<br />
Rear wiper fuse (87) - V009 (2)<br />
4. CHECK HARNESS AND CONNECTOR (REAR WIPER RELAY - COMBINATION SWITCH)<br />
Disconnect the I001 rear wiper relay connector.<br />
Rear wiper relay (86) - I013 (2)<br />
04-390<br />
5. INSPECT RELAY<br />
6. CHECK HARNESS AND CONNECTOR (DRIVER SIDE JUNCTION CONNECTOR - GROUND)<br />
Disconnect rear relay IG2.<br />
Junction connector - Ground<br />
04-391<br />
7. CHECK HARNESS AND CONNECTOR (COMBINATION SWITCH - GROUND)<br />
8. CHECK HARNESS AND CONNECTOR ( REAR WASHING RESERVOIR MOTOR - COMBINATION<br />
V009(1) - I013(3)<br />
YES > Repair or replace rear washing reservoir motor.<br />
04-392<br />
DIAGNOSTICS - AUDIO SYSTEM<br />
AUDIO SYSTEM<br />
1. IT IS FORBIDDEN TO REFIT THE AUDIO SYSTEM.<br />
2. THE RADIO WAVE BANDS USED IN RADIO BROADCASTING ARE AS FOLLOWS.<br />
Radio wave AM FM<br />
Modulation method Amplitude modulation Frequency modulation<br />
Designation AM1 AM2 FM1 FM2 FM3<br />
Frequency 522 ~ 1620 KHz 87.5 ~ 108 MHz<br />
3. POWER OFF.<br />
(a) Before removing or installing any electrical device, please disconnect the negative battery cable to<br />
prevent the device damage or personal injury.<br />
(b) Ignition switch must be off if no specific instructions.<br />
04-393<br />
1 Rear Speaker Assy RH<br />
2 Rear Speaker Assy LH<br />
3 Radio Assy<br />
4 Front Speaker Assy RH<br />
3 Front Speaker Assy LH<br />
04-394<br />
• The voltage should be above 12V.<br />
Check radio antenna.<br />
• Check whether the antenna is pulled out<br />
and pulled out to end.<br />
• Check whether the antenna is covered<br />
with obstacles.<br />
• Check whether the antenna is bended or<br />
deformation.<br />
Repair or replace the radio antenna assy.<br />
Check radio.<br />
• Press the radio power button, check<br />
whether the radio work well.<br />
Check speaker.<br />
• Set the radio volume level above 5 VOL,<br />
check whether the speaker sounds.<br />
Check the radio broadcasting signal.<br />
Move the vehicle to the place where the<br />
signal is strong.<br />
04-395<br />
Radio does not work<br />
3. Radio Chapter 66 audio system - radio system, replacement<br />
1. Setting impropriety Chapter 04 diagnositics - audio system, radio reception poor<br />
Radio reception is poor<br />
2. Radio broadcasting<br />
Chapter 04 diagnositics - audio system, radio reception poor<br />
3. Antenna malfunction Chapter 04 diagnositics - audio system, radio reception poor<br />
4. Radio Chapter 66 audio system - radio system, replacement<br />
1. Setting impropriety Chapter 04 diagnositics - audio system, sound quality poor<br />
Poor sound quality<br />
Chapter 04 diagnositics - audio system, sound quality poor<br />
3. Antenna malfunction Chapter 04 diagnositics - audio system, sound quality poor<br />
4. Speaker Chapter 04 diagnositics - front speaker assy, replacement<br />
5. Radio Chapter 66 audio system - radio system, replacement<br />
1. Setting impropriety<br />
Chapter 04 diagnositics - audio system, speaker does not<br />
work<br />
Speaker does not work<br />
2. Speaker Chapter 04 diagnositics - front speaker assy, replacement<br />
04-396<br />
RADIO DOES NOT WORK<br />
04-397<br />
Check Radio ACC fuse (7.5 A) in junction box (I001).<br />
Check Radio fuse (10 A) in junction box (I001).<br />
NO > If the dome light fuse is blown, go to next step.<br />
If the radio & cigarette fuse is blown, go to step 3.<br />
2. CHECK HARNESS AND CONNECTOR (RADIO - GROUND)<br />
(b) Disconnect the radio connector.<br />
Do not drop the radio.<br />
A7 - Ground<br />
04-398<br />
3. CHECK HARNESS AND CONNECTOR (RADIO - GROUND)<br />
A4 - Ground<br />
4. CHECK HARNESS AND CONNECTOR (RADIO FUSE - RADIO)<br />
Radio fuse (10 A) - A4<br />
04-399<br />
5. CHECK HARNESS AND CONNECTOR (RADIO ACC FUSE - RADIO)<br />
Radio ACC fuse(15 A) - A4<br />
6. CHECK HARNESS AND CONNECTOR (RADIO - GROUND)<br />
A8 - Ground<br />
YES > Replace radio.<br />
04-400<br />
RADIO RECEPTION IS POOR<br />
1. CHECK RADIO SETTING<br />
Press the radio power button.<br />
Adjust the volume level above 5 VOL.<br />
Turn the button and search the radio station.<br />
Check whether the radio setting is correct?<br />
NO > Reset the radio.<br />
2. CHECK THE RADIO BROADCASTING SIGNAL<br />
Move the vehicle to the place where the signal is strong.<br />
Check whether the radio reception is good?<br />
YES > System is normal.<br />
• There is great difference in the size of the service area for AM, FM monaural, and FM stereo<br />
broadcasting. Thus it may happen that FM broadcast cannot be received even though AM comes in<br />
very clearly. Not only does FM stereo have the smallest service area, but also it picks up static and<br />
other types of interference most easilly.<br />
• AM broadcasts are susceptible to other types of interference, especially at night. This is because AM<br />
radio waves bounce off the ionosphere at night. These radio waves then interfere with the signals from<br />
the same transmitter that reach the vehicle’s antenna directly.<br />
• When a signal from broadcast transmitter antenna bounces off Mountains, tall buildings or other<br />
obstruction, it will interfere with the signal that is received directly.<br />
3. CHECK RADIO ANTENNA<br />
Check whether the antenna is pulled out to the end.<br />
Check whether the antenna is bended or deformation.<br />
Check whether the antenna is breakage.<br />
Check whether the antenna connnector is intalled correct.<br />
Adjust and check the radio antenna. Is the check result normal?<br />
YES > Repair or replace the radio antenna.<br />
NO > Replace the radio.<br />
04-401<br />
POOR SOUND QUALITY<br />
4. CHECK SPERKER<br />
Remove the speaker. (Refer to “Chapter 66 audio system - front speaker assy, replacement”)<br />
Check whether the speaker is around with obstacles.<br />
Check whether the speaker cone diaphragm accumulates dust.<br />
Check the speaker cone diaphragm for damage.<br />
Replace the old speaker with a troubleprool one and check the system.<br />
Check whether the radio sound quality is good?<br />
YES > Repair or replace the speaker.<br />
04-402<br />
SPEAKER DOES NOT WORK<br />
04-403<br />
3. CHECK HARNESS AND CONNECTOR (RADIO - SPEAKER)<br />
Disconnect the speaker connector.<br />
B3 - H001 (1)<br />
H001 (2) - B4<br />
04-404<br />
4. CHECK HARNESS AND CONNECTOR (RADIO - SPEAKER)<br />
B5 - D001 (1)<br />
D001 (2) - B6<br />
5. CHECK HARNESS AND CONNECTOR (RADIO - SPEAKER)<br />
B2 - G002 (2)<br />
G002 (1) - B1<br />
04-405<br />
6. CHECK HARNESS AND CONNECTOR (RADIO - SPEAKER)<br />
B7 - F0025(1)<br />
F005 (2) - B8<br />
7. CHECK SPEAKER<br />
Check the speaker for damage.<br />
YES > Replace the speaker.<br />
04-406<br />
DIAGNOSTICS - AUXILIARY POWER<br />
1 Cigarette Ligter 2 12V Power supply output socket<br />
04-407<br />
Cigarette Ligter is<br />
12V Power supply<br />
output socket is<br />
8. Fuse -<br />
9. Relay -<br />
10.Wire harness -<br />
1. Relay -<br />
2. Fuse -<br />
04-408<br />
CIGARETTE LIGHTER IS INOPERATIVE<br />
04-409<br />
Inspect the cigarette lighter fuse in body junction box<br />
(I001):15 A.<br />
2. CHECK HARNESS AND CONNECTOR (CIGARETTE LIGHTER - GROUND)<br />
I033 (2) - Ground<br />
04-410<br />
3. CHECK HARNESS AND CONNECTOR (CIGARETTE LIGHTER FUSE - CIGARETTE LIGHTER)<br />
Cigarette lighter fuse - I033 (2)<br />
4. CHECK HARNESS AND CONNECTOR (CIGARETTE LIGHTER - GROUND)<br />
YES > Replace the cigarette lighter.<br />
04-411<br />
12V POWER SUPPLY OUTPUT SOCKET IS INOPERATIVE<br />
04-412<br />
(b) Inspect the IG2 fuse in body junction box (I001):15 A .<br />
(c) Inspect the power fuse in body junction box (I001):40 A .<br />
2. INSPECT HORN RELAY<br />
Remove the IG2 relay.<br />
Inspect IG2 relay.<br />
NO > Replace horn relay.<br />
04-413<br />
3. CHECK HARNESS AND CONNECTOR (INSTRUMENT FUSE - IG2 FUSE)<br />
Disconnect the IG2 relay.<br />
IG2 (40A) - Instrument fuse(60A)<br />
4. CHECKHARNESS AND CONNECTOR (POWER FUSE - 12V POWER SUPPLY OUTPUT SOCKET<br />
FUSE)<br />
Disconnect I015 12V power supply output socket.<br />
Power fuse (15A) - I015(2)<br />
04-414<br />
5. CHECK HARNESS AND CONNECTOR (12V POWER SUPPLY OUTPUT SOCKET FUSE - GROUNUD)<br />
I015(1) - Ground<br />
YES > Replace 12V power supply output socket.<br />
DIAGNOSTICS - HORN SYSTEM<br />
04-415<br />
1 Horn Switch<br />
2 Alt Horn<br />
3 Bass Horn<br />
04-416<br />
6. Horn fuse -<br />
7. Horn relay -<br />
Horn is inoperative<br />
8. Horn switch<br />
9. Clock spring<br />
10.Horn<br />
Chapter 51 steering column - steering wheel,<br />
Chapter 81 communication system - horn,<br />
11.Wire harness -<br />
1. Horn relay -<br />
Horn is always on<br />
2. Horn switch<br />
4. Center Door Lock Controller -<br />
04-417<br />
HORN IS INOPERATIVE<br />
04-418<br />
(b) Inspect the horn fuse in body junction box (I001):15 A.<br />
NO > Replace the horn fuse.<br />
Remove the horn relay.<br />
Inspect horn relay.<br />
04-419<br />
3. CHECK HARNESS AND CONNECTOR (HORN RELAY - CENTRAL LOCKING CONTROLLER B<br />
ASSY)<br />
Disconnect the I008 central locking controller B connector.<br />
I008 (B4) - Horn relay(86)<br />
4. INSPECT CENTRAL LOCKING CONTROLLER B ASSY<br />
(b) Disconnect the battery negative cable.<br />
(c) Replace the central locking controller B. (Refer to“Chapter 82 Windshiel window glass rearview mirror<br />
- power window, replacement”)<br />
(d) Connect the battery negative cable.<br />
(e) Turn the ignition switch ON.<br />
Does the horn sound?<br />
YES > Repair or replace central locking controller B.<br />
5. CHECK HARNESS AND CONNECTOR (HORN RELAY - CLOCK SPRING)<br />
Disconnect the horn relay connector.<br />
Disconnect the clock spring connector.(Refer to“Chapter 62 Supplemental Restraint System - clock<br />
spring, replacement”)<br />
04-420<br />
Horn relay (86) - I014(2)<br />
6. INSPECT CLOCK SPRING<br />
Replace the clock spring. (Refer to“Chapter 62 Supplemental<br />
Restraint System - clock spring, replacement”)<br />
YES > Repair the clock spring.<br />
7. INSPECT HORN SWITCH<br />
Remove the horn switch. (Refer to“Chapter 51 steering column - steering wheel, replacement”)<br />
Check the horn switch for corrosion or damaged pins.<br />
Replace the horn switch. (Refer to“Chapter 51 steering column - steering wheel, replacement”)<br />
Press the horn switch.<br />
YES > Repair or replace the horn switch.<br />
04-421<br />
8. CHECK HARNESS AND CONNECTOR (HORN RELAY - HORN)<br />
Disconnect the V014 alt horn connector.<br />
Disconnect the V013 bass horn connector..<br />
Standard resistance (check for open).<br />
Horn relay - V013(1)<br />
Horn relay - V014(1)<br />
9. CHECK HARNESS AND CONNECTOR (HORN - GROUND)<br />
Disconnect the V013 alt horn connector.<br />
V014(2) - Ground<br />
V013(2) - Ground<br />
YES > Replace horn.<br />
04-422<br />
HORN IS ALWAYS ON<br />
04-423<br />
1. INSPECT HORN RELAY<br />
(b) Remove the horn relay.<br />
2. INSPECT CLOCK SPRING<br />
Replace clock spring. (Refer to“Chapter 62 Supplemental<br />
(c) Connect the battery negative cable.<br />
3. INSPECT HORN SWITCH<br />
(a) Remove the horn switch. (Refer to“Chapter 51 steering column - steering wheel, replacement”)<br />
(b) Check the horn switch for corrosion or damaged pins.<br />
(c) Replace the horn switch. (Refer to“Chapter 51 steering column - steering wheel, replacement”)<br />
(d) Press horn switch.<br />
YES > Replace the horn.<br />
NO > Replace the horn switch.<br />
04-424<br />
DIAGNOSTICS - REVERSE RADAR SYSTEM<br />
1. UNDER THE FOLLOWING CONDITIONS, THE DETECTION FUNCTION MAY NOT FUNCTION<br />
PROPERLY:<br />
(e) The sensor is covered with foreign matter, such as mud or snow (detection function returns to normal<br />
when the sensor is cleaned).<br />
(f) The sensor is frozen (detection function returns to normal when the temperature of the sensor is going<br />
high).<br />
(g) The sensor is covered with a hand.<br />
(h) In very cold weather where a malfunction display appears, the sensor may not be able to detect<br />
obstacles.<br />
2. THE DETECTION RANGE MAY BE AFFECTED BY THE FOLLOWING CONDITIONS:<br />
(a) The sensor is covered with foreign matter, such as mud or snow.<br />
(b) The vehicle is in an excessively hot or cold area.<br />
3. UNDER THE FOLLOWING CONDITIONS, A DETECTION ERROR MAY OCCUR:<br />
(a) Driving on a bumpy road, an unpaved road, or in tall grass.<br />
(b) Ultrasonic waves from items such as another vehicle's horn, motorcycle engine sounds, a large<br />
vehicle's air brake sound, or another vehicle's sonar are transmitted near the vehicle.<br />
(c) It is raining heavily or the sensor comes into contact with water (sprayed).<br />
(d) The vehicle is tilted at a large angle.<br />
(e) The vehicle is equipped with a commercial fender pole or a wireless mechanism antenna.<br />
(f) The sensor is covered with foreign matter, such as mud or snow.<br />
(g) The vehicle is moving toward a high curb or the corner of a pointed object.<br />
4. THE SENSOR CANNOT DETECT SOME OBJECTS SUCH AS THE FOLLOWING:<br />
(a) Thin objects, such as wires and ropes.<br />
(b) Materials that absorb ultrasonic waves, such as cotton, snow, etc.<br />
(c) Objects with sharp edges.<br />
(d) Short objects.<br />
(e) Tall, overhanging objects.<br />
5. OTHER NOTICES:<br />
(a) The sensor cannot detect objects directly under the bumper. (The sensor may detect low objects and<br />
thin poles, and then lose track of the objects.)<br />
(b) The sensor may not be able to detect obstacles that are too close to the sensor.<br />
(c) The sensor may not be able to detect obstacles if it is dropped or subjected to a strong impact.<br />
04-425<br />
Audio (Multi - media And Air - condition<br />
Controler Assy)<br />
2 Reverse Radar Control Unit<br />
3 Reverse Radar Sensor<br />
4 Camera<br />
04-426<br />
SYSTEM DESCRIPTION<br />
1. GENERAL.<br />
This system uses ultrasonic sensors to send ultrasonic waves. The reverse radar sensors receive the<br />
echo. The reverse radar control unit then informs the driver of the distance between the sensors and<br />
the obstacles as well as their positions by indicating them on the combined display and by clearance<br />
warning buzzer.<br />
2. FUNCTION OF COMPONENTS.<br />
Components<br />
Reverse radar sensor<br />
Clearance warning buzzer<br />
Audio (multi - media and air<br />
- condition controler assy)<br />
Reverse radar control unit<br />
Camera<br />
Back - up lamp switch<br />
Function<br />
Detects the distance between the vehicle and an obstacle.<br />
Sounds from the buzzer to motify the driver for the distance between the vehicle<br />
and the obstacle.<br />
Displays the location of the obstacle and the approximate distance between the<br />
vehicle and the obstacle,and image in rear of vehicle.<br />
1. Judges the approximate distance between the vehicle and the obstacle based<br />
on the signals from the reverse radar sensor.<br />
2. Sounds the clearance warning buzzer.<br />
Shoot image information.<br />
Sends the back - up signal to the reverse radar control unit.<br />
3. DETECTION RANGE OF REVERSE RADAR SENSOR.<br />
(a) Detection range of reverse radar sensor (both sides).<br />
Detection range of reverse radar sensor (middle).<br />
4. DISTANCE TO AN OBSTACLE, FREQUENCY AND MODE OF CLEARANCE WARNING BUZZER.<br />
NO. DISTANCE MODE FREQUENCY<br />
A 90 - 150 cm Long & Intermittent 1 Hz<br />
04-427<br />
B 60 - 90 cm Short & Intermittent 2 Hz<br />
C 40 - 60 cm Rapid & Intermittent 4 Hz<br />
D 40 ± 5 cm Continual Continual<br />
5. TERMINALS OF REVERSE RADAR CONTROL UNIT PIN.<br />
Terminal No. Wiring Color Terminal Description<br />
1 B - R Power supply<br />
3 W - R Radar power supply<br />
4 R - W Reverse radar central sensor RH<br />
6 L - B Vehicle speed signal<br />
7 R - G Reverse radar sensor LH<br />
8 R - B Reverse radar central sensor LH<br />
9 Y Parking signal<br />
11 B Sensor ground<br />
13 - -<br />
15 R - L Reverse radar sensor RH<br />
16 W - B Ground<br />
04-428<br />
Reverse radar system is<br />
inoperative at all<br />
2. Reverse radar control unit<br />
3. Back - up lamp switch<br />
Chapter 81 communication system - reverse<br />
radar, replacement<br />
operative when the shift<br />
lever is out of reverse<br />
position<br />
1. Reverse radar sensor<br />
everse radar system is<br />
inoperative within specified<br />
distance (Back - up lamp is<br />
normal)<br />
operative but there is no<br />
obstacle behind the vehicle<br />
Buzzer is inoperative or<br />
operative incorrectly within<br />
specified distance (<br />
displayer is normal)<br />
Display is inoperative<br />
within specified distance<br />
(Back - up lamp is<br />
1. Displayer Chapter 81 communication system - multi -<br />
media and air - condition controler<br />
assy,replacement<br />
2. Camera Chapter 81 communication system - astern<br />
image, replacement<br />
04-429<br />
REVERSE RADAR SYSTEM IS INOPERATIVE AT ALL<br />
04-430<br />
Inspect back - up lamp fuse (10A) in driver side junction<br />
Disconnect the I028 reverse radar control unit connector.<br />
3. INSPECT BACK - UP LAMP SWITCH<br />
04-431<br />
1 - Ground<br />
2 - Ground<br />
NO > Replace back - up lamp switch and fuse.<br />
4. CHECK HARNESS AND CONNECTOR (BACK - UP LAMP SWITCH - REVERSE RADAR<br />
CONTROL UNIT)<br />
A021 (2) - Ground<br />
5. CHECK HARNESS AND CONNECTOR (REVERSE RADAR CONTROL UNIT - GROUND)<br />
I028 (16) - Ground<br />
04-432<br />
6. INSPECT BACK - UP LAMP SWITCH<br />
Inspect back - up lamp switch according to the value(s)<br />
condition<br />
Set shift lever in reverse<br />
Set shift lever out of<br />
reverse position<br />
1 - 2 ≥ 1 ΜΩ<br />
NO > Replace back - up lamp.<br />
7. CHECK HARNESS AND CONNECTOR (BACK - UP LAMP FUSE - BACK - UP LAMP SWITCH)<br />
Back - up lamp fuse (10A) - A021 (1)<br />
04-433<br />
8. CHECK HARNESS AND CONNECTOR (BACK - UP LAMP SWITCH - REVERSE RADAR<br />
A021 (2) - I028 (1)<br />
YES > Replace reverse radar control unit.<br />
04-434<br />
REVERSE RADAR SYSTEM IS OPERATIVE WHEN THE SHIFT<br />
LEVER IS OUT OF REVERSE POSITION<br />
04-435<br />
1. INSPECT BACK - UP LAMP SWITCH<br />
2. CHECK HARNESS AND CONNECTOR (BACK - UP LAMP SWITCH - REVERSE RADAR<br />
I028 (1) - Ground<br />
04-436<br />
DISTANCE (BACK - UP LAMP IS NORMAL)<br />
04-437<br />
1. INSPECT REVERSE RADAR SENSOR<br />
Disconnect the R001 Reverse Radar Sensor LH connector.<br />
Disconnect the R002 Reverse Radar Central Sensor LH connector.<br />
Disconnect the R003 Reverse Radar Central Sensor RH connector.<br />
Disconnect the R004 Reverse Radar Sensor RH connector.<br />
Replace reverse radar sensor.<br />
Set the shift lever in reverse position.<br />
Does reverse radar system work correctly?<br />
YES > Replace reverse radar sensor.<br />
2. CHECK HARNESS AND CONNECTOR (REVERSE RADAR CONTROL UNIT - REVERSE RADAR<br />
SENSOR)<br />
I028 (7) - R001 (1)<br />
I028 (11) - R001 (2)<br />
I028 (8) - R002 (1)<br />
I028 (11) - R002 (2)<br />
04-438<br />
I028 (4) - R003 (1)<br />
I028 (11) - R003 (2)<br />
I028 (15) - R004 (1)<br />
I028 (11) - R004 (2)<br />
04-439<br />
OBSTACLE BEHIND VEHICLE<br />
04-440<br />
Turn the ignition switch OFF..<br />
04-441<br />
04-442<br />
BUZZER IS INOPERATIVE OR OPERATIVE INCORRECTLY WITHIN<br />
SPECIFIED DISTANCE (DISPLAYER IS NORMAL)<br />
04-443<br />
04-444<br />
04-445<br />
(BUZZER IS NORMAL)<br />
04-446<br />
1. CHECK HARNESS AND CONNECTOR (BACK - UP LAMP SWITCH - CAMERA)<br />
Disconnect the J005 camera connector.<br />
A021 (2) - J005 (2)<br />
2. CHECK HARNESS AND CONNECTOR (CAMERA - RADIO)<br />
Disconnect the I029 radio connector.<br />
J005 (3) - I029 (1)<br />
J005 (4) - I029 (2)<br />
04-447<br />
3. CHECK HARNESS AND CONNECTOR (CAMERA - GROUND)<br />
J005 (1) - Ground<br />
4. INSPECT CAMERA<br />
Replace the camera.<br />
Does displayer work correctly?<br />
YES > Replace the camera.<br />
04-448<br />
DIAGNOSTICS - POWER WINDOWS<br />
(a) Before removing or installing any electrical device, please disconnect the negative cable from battery to<br />
To prevent locking the key in the vehicle, do not leave the key in the vehicle when disconnecting the<br />
negative battery cable.<br />
3. DISCONNECTING THE NEGATIVE BATTERY CABLE WILL RESET BOTH THE TRIP ODOMETER<br />
AND THE CLOCK TO ‘0’.<br />
The total odometer can not be reset to ‘0’.<br />
4. THE AUDIO SYSTEM WILL LOSE STORED MEMORY DATA IF THE NEGATIVE BATTERY CABLE<br />
IS DISCONNECTED.<br />
After reconnecting the negative battery cable, the audio system will need to be reset.<br />
04-449<br />
1 Central Locking Controller<br />
2 Door Control Switch<br />
4 Window Control Switch RH<br />
5 Glass Lift Motor RH<br />
3 Glass Lift Motor LH<br />
04-450<br />
DOOR CONTROL SWITCH PIN<br />
Terminal No. Wiring Color Description<br />
1 L - B Door control switch LH (date)<br />
2 L Door control switch LH (clock)<br />
3 L - Y Window control switch RH<br />
4 P - L Window control switch RH<br />
5 L - G Window control switch RH<br />
6 W - B Grond<br />
9 G - R Lamplet illumination<br />
04-451<br />
WINDOW CONTROL SWITCH RH PIN<br />
1 L - G Door control switch<br />
3 P - L Door control switch<br />
4 L - Y Door control switch<br />
04-452<br />
CENTRAL LOCKING CONTROLLER ASSY A PIN<br />
1 W - B Ground<br />
4 G Power window motor LH<br />
5 R Power window motor LH<br />
6 R - L Power window motor RH<br />
7 G - R Power window motor RH<br />
8 W - L Window control power input<br />
11 Y Collision signal<br />
14 R Door - status<br />
15 L - B Door control switch LH (date)<br />
16 L Door control switch LH (clock)<br />
17 W - L Vehicle speed signal<br />
18 R - B Ignition switch<br />
04-453<br />
• The battery voltage should be over than<br />
12 V.<br />
Charge or replace the battery. Refer to<br />
“Chapter 20A starting and charging -<br />
battery”.<br />
Check the front power window motor LH.<br />
• Push or pull the front window switch LH to<br />
operate the fornt window LH open and<br />
close.<br />
Check power window auto open operation.<br />
operate the fornt window LH auto open.<br />
Check power window motor RH.<br />
operate the fornt window RH open and<br />
• ush or pull the front window switch RH to<br />
Replace power window motor.<br />
04-454<br />
Use the table below to help you to find the cause of the problem. The numbers indicate the priority of the likely<br />
All power windows are<br />
inoperative.<br />
1. Power, ground circuits<br />
2. Door control switch<br />
3. Power window motor LH and<br />
Chapter 20A starting and charging - battery,<br />
Chapter 20B starting and charging - battery,<br />
Chapter 82 windshield/windowglass/rear view<br />
mirror - power window, replacement<br />
Front power window<br />
LH is inoperative.<br />
3. Central Locking Controller<br />
4. Power window motor LH<br />
LH does not open.<br />
1. Door control switch<br />
2. Central Locking Controller<br />
LH does not close.<br />
RH is inoperative (use<br />
door control switch).<br />
3. Window control switch RH<br />
04-455<br />
window control switch<br />
RH).<br />
4. Power window motor RH<br />
1. Window control switch RH<br />
3. Power window motor RH<br />
04-456<br />
ALL POWER WINDOWS ARE INOPERATIVE<br />
04-457<br />
Inspect the power window fusible link (20 A) in driver<br />
side junction box (I001).<br />
2. CHECK HARNESS AND CONNECTOR (DOOR CONTROL SWITCH - GROUND)<br />
Disconnect the D005 door control switch connector.<br />
Disconnect the I007 central locking controller assy A connector.<br />
D005 (12) - Ground<br />
3. INSPECT DOOR CONTROL SWITCH<br />
Replace door control switch.<br />
04-458<br />
Does power window work correctly?<br />
YES > Replace door control switch.<br />
4. CHECK HARNESS AND CONNECTOR (POWER WINDOW FUSIBLE LINK - DOOR CONTROL<br />
Power window fusible link (20A) - D005 (12)<br />
5. CHECK HARNESS AND CONNECTOR (POWER WINDOW FUSIBLE LINK - CENTRAL LOCKING<br />
CONTROLLER ASSY A)<br />
Power window fusible link (20A) - I007 (A8)<br />
04-459<br />
6. CHECK HARNESS AND CONNECTOR (DOOR CONTROL SWITCH - GROUND)<br />
D005 (6) - Ground<br />
7. CHECK HARNESS AND CONNECTOR (DOOR CONTROL SWITCH - CENTRAL LOCKING CONTROLLER<br />
ASSY A)<br />
D005 (1) - I007 (A15)<br />
D005 (2) - I007 (A16)<br />
04-460<br />
8. INSPECT POWER WINDOW MOTOR LH AND RH<br />
Disconnect the D002 power window motor LH connector.<br />
Disconnect the H002 power window motor RH connector.<br />
Replace power window motor LH and RH.<br />
YES > Replace power window motor LH and RH.<br />
9. CHECK HARNESS AND CONNECTOR (CENTRAL LOCKING CONTROLLER ASSY A - POWER<br />
WINDOW MOTOR LH AND RH)<br />
I007 (A4) - D002 (2)<br />
I007 (A5) - D002 (1)<br />
I007 (A6) - H002 (2)<br />
I007 (A7) - H002 (1)<br />
YES > Replace central locking controller assy.<br />
04-461<br />
FRONT POWER WINDOW LH IS INOPERATIVE<br />
04-462<br />
1. INSPECT DOOR CONTROL SWITCH<br />
2. CHECK HARNESS AND CONNECTOR (DOOR CONTROL SWITCH - CENTRAL LOCKING<br />
3. INSPECT POWER WINDOW MOTOR LH<br />
Replace power window motor LH.<br />
04-463<br />
4. CHECK HARNESS AND CONNECTOR (CENTRAL LOCKING CONTROLLER ASSY A - POWER<br />
WINDOW MOTOR LH)<br />
04-464<br />
FRONT POWER WINDOW LH DOES NOT OPEN<br />
04-465<br />
2. CHECK HARNESS AND CONNECTOR (DOOR CONTROL SWITCH - CENTRAL LOCKING CONTROLLER<br />
04-466<br />
FRONT POWER WINDOW LH DOES NOT CLOSE<br />
04-467<br />
04-468<br />
TROL SWITCH)<br />
04-469<br />
Does power window RH work correctly?<br />
2. CHECK HARNESS AND CONNECTOR (CENTRAL LOCKING CONTROLLER ASSY A - POWER<br />
WINDOW MOTOR RH)<br />
3. INSPECT POWER WINDOW MOTOR RH<br />
Replace power window motor RH.<br />
Does power windou RH work correctly?<br />
YES > Replace power window motor RH.<br />
NO > Replace central locking controller assy.<br />
04-470<br />
CONTROL SWITCH RH)<br />
04-471<br />
1. INSPECT WINDOW CONTROL SWITCH<br />
Disconnect the H004 window control switch RH connector.<br />
Replace window control switch RH.<br />
YES > Replace window control switch RH.<br />
2. CHECK HARNESS AND CONNECTOR (WINDOW CONTROL SWITCH RH - DOOR CONTROL SWITCH)<br />
H004 (1) - D005 (5)<br />
H004 (3) - D005 (4)<br />
H004 (4) - D005 (3)<br />
04-472<br />
4. INSPECT POWER WINDOW MOTOR RH<br />
5. CHECK HARNESS AND CONNECTOR (CENTRAL LOCKING CONTROLLER ASSY A - POWER<br />
DIAGNOSTICS - OUTSIDE MIRROR<br />
04-473<br />
1 Outside Mirror Assy LH<br />
3 Outside Mirror Remote Control Switch<br />
2 Outside Mirror Assy RH<br />
04-474<br />
TERMINALS OF OUTSIDE MIRROR SWITCH<br />
OUTSIDE MIRROR SWITCH<br />
1 L - R<br />
Left Outside Mirror Left And Right<br />
Adjust Input<br />
3 L - Y<br />
Right Outside Mirror Left And Right<br />
Adjust Output<br />
4 G - R Outside Mirror Switch Power Input<br />
5 R - Y Outside Mirror -<br />
7 R<br />
8 R - L<br />
Left Outside Mirror Up And Down<br />
Right Outside Mirror Up And Down<br />
04-475<br />
Yes Go to step 2<br />
Check the outside mirror.<br />
• Adjust the outside mirror LH and the outside<br />
mirror RH.<br />
Replace the outside mirror. Refer to “Chapter<br />
82 windshield - outside mirror, replacement”<br />
04-476<br />
Use the table below to help you find the cause of the problem. The numbers indicate the probability of the<br />
6. Fuse -<br />
Mirrors are inoperative (Both sides)<br />
7. Outside mirror defrost switch<br />
Chapter 85 door lock - front door<br />
lock - replacement<br />
A single mirror is inoperative<br />
1. Outside mirror defrost switch<br />
2. Outside mirror<br />
Chapter 82 windshield - outside<br />
mirror, replacement<br />
Mirror adjustment UP/DOWN is<br />
2. Outside mirror motor<br />
Mirror adjustment LEFT/RIGHT is<br />
04-477<br />
MIRRORS ARE INOPERATIVE (BOTH SIDES)<br />
04-478<br />
Inspect the radio & ACC fuse (7.5 A) in body junction<br />
box(I001).<br />
2. CHECK HARNESS AND CONNECTOR (RADIO & ACC FUSE - OUTSIDE MIRROR REMOTE<br />
CONTROL SWITCH)<br />
Remote the radio & ACC fuse.<br />
Disconnect the D004 outside mirror remote control switch connector.<br />
Radio & ACC fuse (7.5A) -<br />
D004 (4)<br />
04-479<br />
3. CHECK HARNESS AND CONNECTOR (OUTSIDE MIRROR REMOTE CONTROL SWITCH -<br />
D004 (6) - Ground<br />
YES > Replace the outside mirror remote control switch.<br />
04-480<br />
A SINGLE MIRROR IS INOPERATIVE<br />
04-481<br />
• This inspection procedure is an example of outside mirror assy LH, outside mirror assy RH inspection<br />
procedure are similar.<br />
1. INSPECT OUTSIDE MIRROR REMOTE CONTROL SWITCH<br />
Inspect outside mirror remote control switch according to<br />
the value(s) in the table below.<br />
1 - 6<br />
Outside<br />
Mirror LH<br />
4 - 1<br />
5 - 6<br />
4 - 7<br />
7 - 6<br />
NO > Replace outside mirror remote control switch.<br />
2. CHECK HARNESS AND CONNECTOR (OUTSIDE MIRROR REMOTE CONTROL SWITCH -<br />
OUTSIDE MIRROR LH)<br />
Disconnect the D003 outside mirror connector.<br />
D003 (6) - D004 (7)<br />
D003 (4) - D004 (5)<br />
04-482<br />
D003 (5) - D004 (1)<br />
YES > Replace the outside mirror assy.<br />
04-483<br />
MIRROR ADJUSTMENT UP/DOWN IS INOPERATIVE<br />
04-484<br />
the value(s) in the table below<br />
NO > Replace the outside mirror remote control switch.<br />
YES > Replace the outside mirror assy LH.<br />
04-485<br />
MIRROR ADJUSTMENT LEFT/RIGHT IS INOPERATIVE<br />
04-486<br />
Outside Mirror LH<br />
DEFROSTER SYSTEM<br />
DIAGNOSTICS - DEFROSTER SYSTEM<br />
04-487<br />
04-488<br />
1 Rear Window Defroster<br />
2 Outside Mirror Assy<br />
3 Rear Window Defroster Switch<br />
4 Outside Mirror Defrost Switch<br />
04-489<br />
1. GENERAL<br />
The defroster system consist of rear window defroster and outside mirror defroster(outside mirror assy).<br />
The heating element is the electric heating wire which are integrated in the rear window glass and both<br />
outside mirror glasses and defog the glasses quickly. The rear window defroster switch and outside<br />
mirror defrost switch are integrated on the centre switch panel in the instrument panel and can be operated<br />
separately. When each switch is pressed, the indicator lamp in the switch illuminates to indicate<br />
that the defroster is operating.<br />
2. FUNCTION OF MAIN COMPONENTS<br />
Component<br />
Description<br />
Rear window defroster relay<br />
Outside mirror defrost relay<br />
Outside mirror (outside mirror defroster)<br />
Receives rear defrost control signals from rear window<br />
defrost switch and supplies power to rear window<br />
defroster.<br />
Receives defrost control signal from outside mirror<br />
defrost switch and supplies power to both outside mirror.<br />
Receives power from Rear window defroster relay and<br />
heats defroster.<br />
Receives power from outside mirror defrost relay and<br />
04-490<br />
Check battery voltage.<br />
Check ignition switch.<br />
• The ignition switch should work correctly.<br />
Repair or replace ignition switch. Refer to<br />
“Chapter 91 vehicle control system - assy,<br />
removal & installation and disassembly &<br />
reassembly”<br />
Check fuse.<br />
• Check fuse.<br />
Check rear window defroster switch.<br />
• Press the rear window defroster switch.<br />
• The rear window defrost switch should<br />
work correctly.<br />
Check outside mirror defrost switch.<br />
• Press the outside mirror defrost switch.<br />
• The outside mirror defrost switch should<br />
Check rear window defroster.<br />
• The rear window defrost grid should work<br />
Check outside mirror defroster.<br />
• The outside mirror defroster should work<br />
Yes Go to step 6<br />
Replace rear window defroster switch. Refer<br />
to “Chapter 83 instrument panel - dashboard,<br />
Yes Go to step 7<br />
Yes -<br />
Replace rear window defrost grid. Refer to<br />
“chapter 82 Windshield - windshield,<br />
04-491<br />
2. Rear window defrost relay -<br />
Rear window defroster system is<br />
3. Rear window defrost switch<br />
instrument cluster, replacement<br />
4. Rear window defrost grid<br />
Chapter 82 Windshield - rear window<br />
glass, replacement<br />
2. Outside mirror defrost relay -<br />
Outside mirror defroster system is<br />
3. Outside mirror defrost switch<br />
4. Outside mirror defroster<br />
04-492<br />
REAR WINDOW DEFROSTER IS INOPERATIVE<br />
04-493<br />
Inspect the rear defroster fuse (25 A) in Co - pilot<br />
Inspect the outside mirror defrost fuse (7.5 A) in Co - pilot<br />
NO > If the rear defroster fuse or outside mirror defrost fuse is blown, replace the fuse.<br />
2. INSPECT REAR DEFROSTER RELAY<br />
Remove the rear defroster relay.<br />
Inspect the rear defroster relay according to the value(s)<br />
NO > Replace the rear defroster relay.<br />
04-494<br />
3. INSPECT REAR WINDOW DEFROSTER SWITCH<br />
Inspect the rear window defroster switch according to the<br />
NO > Replace the rear window defroster switch.<br />
4. CHECK HARNESS AND CONNECTOR (REAR WINDOW DEFROSTER SWITCH - GROUND)<br />
I016 (2) - Ground<br />
5. CHECK HARNESS AND CONNECTOR (REAR DEFROSTER RELAY - REAR WINDOW DEFROSTER<br />
04-495<br />
Rear defroster relay (85) - I016 (5)<br />
6. CHECK HARNESS AND CONNECTOR (REAR DEFROST RELAY - GROUND)<br />
Remove the rear defrost relay.<br />
Rear defrost relay (86) - Ground<br />
04-496<br />
7. CHECK HARNESS AND CONNECTOR ( REAR DEFROST HEATING WIRE - GROUND)<br />
Disconnect the S001 rear defrost heating wire connector.<br />
Turn rear window defroster switch ON.<br />
S001 (1) - Ground<br />
8. CHECK HARNESS AND CONNECTOR ( REAR DEFROST HEATING WIRE - GROUND)<br />
Disconnect the T001 rear defrost heating wire connector.<br />
T001 (1) - Ground<br />
YES > Replace the rear defrost heating wire.<br />
04-497<br />
OUTSIDE MIRROR DEFROSTER IS INOPERATIVE<br />
04-498<br />
NO > If the outside mirror defrost fuse is blown, replace the fuse.<br />
Remove the outside mirror defrost relay.<br />
NO > Replace the outside mirror defrost relay.<br />
04-499<br />
3. INSPECT OUTSIDE MIRROR DEFROST SWITCH<br />
Disconnect the I017 outside mirror defrost switch connector.<br />
Inspect the outside mirror defrost switch according to the<br />
NO > Replace the outside mirror defrost switch.<br />
4. CHECK HARNESS AND CONNECTOR (OUTSIDE MIRROR DEFROST SWITCH - GROUND)<br />
I017 (2) - Ground<br />
04-500<br />
5. CHECK HARNESS AND CONNECTOR (OUTSIDE MIRROR DEFROST RELAY - OUTSIDE MIRROR<br />
DEFROST SWITCH)<br />
Disconnect the I017 rear window defrost switch connector.<br />
Rear defrost relay (85) - I017 (5)<br />
6. CHECK HARNESS AND CONNECTOR (OUTSIDE MIRROR DEFROST RELAY - GROUND)<br />
Outside mirror defrost relay (86) - Ground<br />
04-501<br />
7. CHECK HARNESS AND CONNECTOR (OUTSIDE MIRROR DEFROST RELAY - OUTSIDE MIRROR<br />
ASSY LH/RH )<br />
Disconnect the D003 outside mirror assy LH/ H003 outside mirror assy RH connector.<br />
Outside mirror defrost relay (87) - D003(3)<br />
Outside mirror defrost relay (87) - H003(3)<br />
8. CHECK HARNESS AND CONNECTOR (OUTSIDE MIRROR ASSY LH/RH - GROUND )<br />
D003(2) - Ground<br />
H003(2) - Ground<br />
YES > Replace outside mirror assy LH/ outside mirror assy RH.<br />
04-502<br />
DIAGNOSTICS - INSTRUMENT CLUSTER<br />
(a) Before removing or installing any electrical device, please disconnect the negative battery cable to prevent<br />
damage to the device or personal injury.<br />
(b) Make sure ignition switch off if no specific instructions.<br />
2. DISCONNECTING THE NEGATIVE BATTERY CABLE WILL RESET BOTH THE TRIP ODOMETER<br />
AND THE CLOCK TO ‘ 0 ’.<br />
The total odometer can not be reset to ‘ 0 ’.<br />
3. THE AUDIO SYSTEM WILL LOSE STORED MEMORY DATA IF THE NEGATIVE BATTERY CABLE<br />
Switch Type Ignition Switch (position) Engine (condition)<br />
04-503<br />
1 Instrument Cluster<br />
2 Speedometer Sensor<br />
3 Fuel Level Sensor<br />
4 Coolant Temperature Sensor<br />
04-504<br />
INSTRUMENT CLUSTER INFORMATION<br />
GAUGES<br />
No Content Description<br />
1 Speedometer The fuel gauge indicates the approximate fuel level in the tank.<br />
6 Fuel Gauge<br />
12 ECT Gauge<br />
15 Tachometer<br />
Receving signal from coolant temperature indicator, the ECT<br />
gauge indicates the engine coolant temperature.<br />
Receiving signal from the ECM, the tachometer indicates<br />
engine revolutions per minute (RPM).<br />
According to the signal received from the speedometer sensor,<br />
the speedometer indicates the vehicle running speed.<br />
04-505<br />
WARNING / INDICATOR LIGHTS<br />
2 Lamplet indicator light<br />
Lamplet indicator light turns on when lamplet is on and receive<br />
lamplet relay signal.<br />
Engine coolant fluid level<br />
warning light<br />
Engine coolant fluid level warming light turns on when engine<br />
coolant level is lower than specification.<br />
Left turn signal/hazard<br />
indicator light<br />
5 Seat belt warning light<br />
Left turn signal/hazard indicator light flashes when the turn<br />
signal switch or hazard switch is activated.<br />
Seat belt warning light turns on when receiving the seat belt<br />
warning signal.<br />
Engine coolant<br />
temperature indicator light<br />
Engine coolant temperature indicator light will illuminate when<br />
engine coolant temperature is between - 20 ℃ ~ 110 ℃ .<br />
8 Fuel level warning light<br />
9 High beam indicator light<br />
10 Door ajar warning light<br />
11 Brake warning light<br />
13 SRS warning light<br />
Fuel level warning light turns on when fuel level lower than<br />
specified level.<br />
High beam indicator light turns on when high beam is on and<br />
receive headlamp relay signal.<br />
Door ajar warning light turns on when receiving the door ajar<br />
Brake warning light turns on when receiving signals from parking<br />
brake switch or brake fluid level sensor.<br />
SRS warning light will turn on when SRS is detected malfunction.<br />
16<br />
Right turn signal/hazard<br />
Parking brake indicator<br />
light<br />
Right turn signal/hazard indicator light flashes when the turn<br />
Parking Brake indicator light turns on when receiving signals<br />
from parking brake switch.<br />
17 ABS warning light Warning light will turn on when ABS is detected malfunction.<br />
18 EBD warning light<br />
The ABS will illuminate EBD warning light when EBD is<br />
detected malfunction.<br />
19<br />
Engine oil pressure<br />
Engine oil pressure indicator light turns on according to the<br />
signal from engine oil pressure warning switch.<br />
20 Charging warning light Charging warning light turns on when charging system is fault.<br />
21 Malfunction indicator light<br />
The ECM will turn on malfunction indicator light when engine<br />
electronic control system is detected malfunction.<br />
22<br />
25<br />
26<br />
Rear fog lamp indicator<br />
Front fog lamp indicator<br />
SVS indicator light<br />
(Gasoline)<br />
Vacuum warning light<br />
(Diesel)<br />
Rear fog lamp indicator light receive the rear fog lamp relay<br />
signal and turns on when rear fog lamp switch is pressed.<br />
Front fog lamp indicator light receive the front fog lamp relay<br />
signal and turns on when front fog lamp switch is pressed.<br />
SVS indicator light will be illuminated when the ECM detect<br />
general malfunctions. It will be always on until faults resolved.<br />
Vacuum warning light turns on when receiving the vacuum<br />
04-506<br />
LIQUID CRYSTAL DISPLAY<br />
Odometer Display driving distance and can not be reset to “0”.<br />
Clock<br />
Display time and can be reset.<br />
04-507<br />
TERMINALS OF INSTRUMENT CLUSTER<br />
Terminals No. Wiring Color Description<br />
A1 B - L Instrument Power<br />
A2 - -<br />
A3 R Door Lamp Indicator<br />
A4 - -<br />
A5 - -<br />
I002<br />
A6 V - W Lamplet Signal Input<br />
A7 LG Front Fog Lamp Indicator<br />
A8 L Vehicle Speed Output<br />
A9 W - L Vehicle Speed Output<br />
A10 L - B Vehicle Speed Output<br />
A11 - -<br />
04-508<br />
A12 - -<br />
A13 W - G Speed Signal Input<br />
A14 B Lighting Pwm Signal<br />
A15 W - R Door Open Indicator<br />
A16 R Instrument Power Output<br />
A17 - -<br />
A18 - -<br />
A19 W - B Instrument A Ground<br />
A20 R - B Instrument Ground<br />
A21 - -<br />
A22 - -<br />
A23 V Fuel Sensor + Output<br />
A24 Y - B Engine Stop Light<br />
A25 - -<br />
A26 B Vacuum Level Alarm + Input<br />
A27 G - Y Preheat Indicator<br />
A28 BR Engine Maintenance<br />
A29 - -<br />
A30 R - W Front Door Open Indicator<br />
A31 B - W Seat Belt Warning<br />
A32 G - Y Left Turn Indicator<br />
B1 - -<br />
B2 - -<br />
B3 - -<br />
I003<br />
B4 - -<br />
B5 - -<br />
B6 Y Instrument Parking Brake Light<br />
B7 V - B Coolant Level Sensor + Output<br />
B8 - -<br />
04-509<br />
B9 B - W Seat Belt Alarm + Output<br />
B10 V - W Speed Input<br />
B11 - -<br />
B12 - -<br />
B13 - -<br />
B14 - -<br />
B15 - -<br />
B16 Y - G Water Temperature Gauge Sensor<br />
B17 - -<br />
B18 - -<br />
B19 - -<br />
B20 Y - G ABS Fault Light Signal Input<br />
B21 R - Y Rear Fog Lamp Indicator<br />
B22 L - Y Engine Oil Pressure Warning Light<br />
B23 L - W Engine Failure Warning Input<br />
B24 Y - R EBD Warning Light Signal Input<br />
B25 P - L Instrument Charging Indicator Input<br />
B26 - -<br />
B27 B - Y Airbag Warning Lamp Signal Input<br />
B28 R - W Brake Fluid Sensor + Output<br />
B29 - -<br />
B30 W - B Instrument B Ground<br />
B31 R - G High Beam Indicator<br />
B32 G - B Right Turn Indicator<br />
04-510<br />
Do not perform basic inspection until engine temperature reaches the specified value. If on - road test<br />
is needed, must have at least two people to perform the test.<br />
Step Conditions Action<br />
• The battery voltage should above 12 V.<br />
Check tachometer.<br />
• Connect hand - held tester, reading the engine<br />
rotating speed data.<br />
• Reading engine rotating speed data with 1000 ~<br />
2000 r/min and 3000 ~ 6000 r/min.<br />
• The variation of error in ± 100 ~ 200 r/min,± 150<br />
~ 300 r/min.<br />
Check speedometer.<br />
• Connect hand - held tester, reading the vehicle<br />
speed data.<br />
• Reading vehicle speed data with 20 ~ 100 Km/h,<br />
120 Km/h and 140 Km/h.<br />
• The variation of error in + 5, + 6, + 7 Km/h.<br />
• The pointer should be without jump when vehicle<br />
is at constant speed or constant acceleration.<br />
Tire wear and incorrect tire pressure will lead<br />
inaccurate data.<br />
Yes Go to step 2.<br />
Charge or replace the battery.<br />
Refer to “Chapter 20A starting<br />
and charging - battery”.<br />
Yes Go to step 3.<br />
Go to the problem symptoms<br />
table.<br />
Yes Go to step 4.<br />
Check engine oil pressure warning light.<br />
• Engine oil pressure warning light should be illuminated.<br />
• After engine starts, engine oil pressure warning<br />
light should go off.<br />
04-511<br />
Malfunction in speedometer<br />
Malfunction in tachometer<br />
Malfunction in fuel gauge<br />
Malfunction in ECT gauge<br />
MIL never/always on<br />
SRS warning light never/<br />
ABS warning light never/<br />
Engine oil pressure warning<br />
light never/always on<br />
1. Speedometer sensor<br />
2. Speedometer circuits<br />
3. Speedometer<br />
1. CKP sensor<br />
2. Tachometer circuits<br />
3. Tachometer<br />
1. Fuel level sensor<br />
2. Fuel gauge circuits<br />
3. Fuel gauge<br />
1. Engine coolant temperature<br />
2. ECT gauge circuits<br />
3. ECT gauge<br />
1. Engine electronic<br />
control system<br />
2. Malfunction indicator<br />
light circuits<br />
3. Instrument cluster<br />
1. SRS warning light<br />
2. SRS warning light circuits<br />
1. ABS system<br />
2. ABS warning light circuits<br />
1. Engine oil pressure<br />
2. Engine oil pressure<br />
warning light circuits<br />
Chapter 04 diagnostics - instrument cluster, malfunction<br />
in speedometer<br />
in tachometer<br />
in fuel gauge<br />
in ECT gauge<br />
Chapter 04 diagnostics - gasoline engine control<br />
system, diagnostic trouble code chart<br />
Chapter 04 diagnostics - diesel engine control system,<br />
diagnostic trouble code chart<br />
Chapter 04 diagnostics - SRS system, problem<br />
symptoms table<br />
problem symptoms table<br />
Chapter 04 diagnostics - supplemental restraint system,<br />
engine oil pressure warning light never/always<br />
04-512<br />
Seat belt warning light never/<br />
Parking Brake indicator light<br />
never/always on<br />
Turn signal/hazard indicator<br />
High beam indicator light<br />
1. Seat belt warning<br />
2. Seat belt waring<br />
switch circuits<br />
1. Parking brake switch<br />
2. Parking brake circuits<br />
3. instrument cluster<br />
1. Fuses<br />
3. Hazard switch<br />
4. Turn signal/hazard<br />
indicator light circuits<br />
5. Instrument cluster<br />
3. High beam indicator<br />
4. Instrument cluster<br />
seat belt warning light never/always on<br />
parking brake indicator light never/always on<br />
Chapter 04 diagnostics - lighting, problem symptoms<br />
table (If exterior turn signal/hazard lights are<br />
normal, repair turn signal/hazard indicator light circuits<br />
for an open or replace the instrument cluster)<br />
table (If exterior high light are normal, repair<br />
high beam indicator light circuits for an open or<br />
replace the instrument cluster)<br />
04-513<br />
MALFUNCTION IN SPEEDOMETER<br />
04-514<br />
1. CHECK HARNESS AND CONNECTOR (SPEEDOMETER SENSOR - GROUND)<br />
Disconnect the A020 speedometer sensor connector.<br />
A020 (1) - Ground<br />
2. CHECK HARNESS AND CONNECTOR (INSTRUMENT CLUSTER - SPEEDOMETER SENSOR)<br />
Disconnect the I002 instrument cluster connector.<br />
I002 (A13) - A020 (3)<br />
3. INSPECT SPEEDOMETER SENSOR<br />
Remove the speedometer sensor.<br />
Use a good sensor replacement<br />
YES > Replace the instrument cluster.<br />
NO > Replace the speedometer sensor.<br />
04-515<br />
MALFUNCTION IN TACHOMETER<br />
04-516<br />
An abnormal running engine will lead the tachometer pointer instable.<br />
Check if the engine has normal start.<br />
YES > Go to step 1.<br />
NO > Refer to “Chapter 04 diagnostics - gasoline engine control system, problem symptoms table”<br />
1. CHECK HARNESS AND CONNECTOR (INSTRUMENT CLUSTER - ECM)<br />
Disconnect the E001(4G69) / A036(ISF2.8) ECM connector.<br />
I002 (A8) - E001(51)<br />
I002 (A8) - A036(E28)<br />
2. CHECK HARNESS AND CONNECTOR<br />
Start the engine until the engine temperature reaches to normal condition.<br />
Measure the pulse signal between the instrument cluster<br />
connector I002, pin A8 and ground.<br />
Pulse signal: Appr 33.3 Hz (1000 r / min)<br />
04-517<br />
NEVER OR ALWAYS ON<br />
04-518<br />
• Turn the ignition switch ON and ensure fuel tank have enough fuel (more than 1/4 in fuel tank).<br />
• Fuel level warning light will be illuminated when fuel level sensor resistance greater than 96 ± 2.5 Ω.<br />
• Fuel level warning light will turn off when fuel level sensor resistance smaller than 96.5 ± 4 Ω.<br />
1. INSPECT FUEL LEVEL SENSOR<br />
Disconnect the A022 fuel level sensor connector.<br />
Measure the resistance between the fuel level sensor<br />
A022 pin 2 and pin 3.<br />
Remove the fuel level sensor and measure the resistance<br />
following the table below.<br />
Position Empty Warn threshold 1/4 1/2 3/4 Full<br />
Resistance(Ω)<br />
150 ± 2.5 120 ± 2.5 95 ± 2.5 74 ± 2.5 54 ± 2.5 30 ± 2.5<br />
NO > Replace the fuel level sensor..<br />
2. CHECK HARNESS AND CONNECTOR (FUEL LEVEL SENSOR - GROUND)<br />
A022 (2) - Ground<br />
04-519<br />
3. INSPECT FUEL LEVEL SENSOR<br />
A022 (3) - Ground<br />
NO > Replace the fuel level sensor.<br />
4. CHECK HARNESS AND CONNECTOR (INSTRUMENT CLUSTER - FUEL LEVEL SENSOR)<br />
Disconnect the I002 instrument cluster connectors.<br />
Disconnect the A022 fuel level sensor connectors.<br />
Measure the resistanceaccording to the value(s) in the<br />
I002 (A23) - A022 (3)<br />
04-520<br />
MALFUCTION IN ENGINE COOLANT TEMPERATURE GAUGE<br />
04-521<br />
• Ensure engine coolant level within specified value.<br />
• Ensure engine coolant temperature normal.<br />
1. INSPECT ECT INDICATOR<br />
(b) Remove ECT indicator.<br />
Whenever remove the ECT indicator, ensure the engine is cold (Engine coolant temperature lower than<br />
40 ℃ ).<br />
(c) Measure the ECT sensor resistance following the table below.<br />
Temperature ( ℃ ) 40 72 105 120<br />
Resistance (Ω) 287.4 ± 30 98 ± 13.5 33 ± 2 21<br />
NO > Replace the ECT indicator.<br />
2. CHECK HARNESS AND CONNECTOR (ECT INDICATOR - GROUND)<br />
Disconnect the E012 (4G69) / E037 (ISF2.8) ECT indicator connector.<br />
E012 (1) - Ground<br />
E037 (1) - Ground<br />
YES > Replace the ECT indicator.<br />
04-522<br />
3. CHECK HARNESS AND CONNECTOR (INSTRUMENT CLUSTER - ECT INDICATOR)<br />
Disconnect the I003 instrument cluster connector.<br />
I003 (B16) - E012 (1)<br />
I003 (B16) - E037 (1)<br />
04-523<br />
ENGINE OIL PRESSURE WARNING LIGHT NEVER / ALWAYS ON<br />
04-524<br />
• When turning the ignition switch ON, the engine oil pressure warning light will turn on.<br />
• Engine oil pressure warning light will turn off after engine starts.<br />
If the engine oil pressure warning light is always on after engine starts. Do not shut off engine immediately.<br />
Check oil level, if oil level is out of specification, it needs to be repaired first.<br />
Check if engine oil pressure warning light is always on or never.<br />
YES > (Always on) Go to step 1.<br />
NO > (Never on) Go to step 3.<br />
1. INSPECT ENGINE OIL PRESSURE WARNING LIGHT<br />
Disconnect the A023 (4G69) / E036 (ISF2.8) engine oil pressure switch connector.<br />
Check if the engine oil pressure warning light turns off.<br />
YES > Replace the engine oil pressure switch.<br />
2. CHECK HARNESS AND CONNECTOR (ENGINE OIL PRESSURE SWITCH - GROUND)<br />
Standard resistance (check for short<br />
A023 (1) - Ground<br />
E036 (1) - Ground<br />
04-525<br />
3. CHECK HARNESS AND CONNECTOR (INSTRUMENT CLUSTER - ENGINE OIL PRESSURE<br />
Standard resistance (check for open<br />
I003 (B22) - A023 (1)<br />
I003 (B22) - E036 (1)<br />
04-526<br />
SEAT BELT WARNING LIGHT NEVER / ALWAYS ON<br />
04-527<br />
• Seat belt warning light will turn on.<br />
• Seat belt warning light will turn off when seat belt is fastened.<br />
Check if seat belt warning light always or never on.<br />
1. INSPECT SEAT BELT WARNING LIGHT<br />
Disconnect the O001 the seat belt warning switch connector.<br />
Check if the seat belt warning light turns off.<br />
YES > Replace the seat belt warning switch.<br />
2. CHECK HARNESS AND CONNECTOR (SEAT BELT WARNING SWITCH - GROUND)<br />
Disconnect the O001 seat belt warning switch connector.<br />
O001 (1) - Ground<br />
04-528<br />
3. CHECK HARNESS AND CONNECTOR (SEAT BELT WARNING SWITCH - GROUND)<br />
O001 (2) - Ground<br />
4. INSPECT SEAT BELT WARNING SWITCH<br />
insert seat belt<br />
buckle<br />
O001 (1) - O001 (2)<br />
NO > Replace the seat belt warning switch.<br />
04-529<br />
5. CHECK HARNESS AND CONNECTOR (INSTRUMENT CLUSTER - SEAT BELT WARNING<br />
Disconnect the O001seat belt warning switch connector.<br />
I002 (A31) - O001 (1)<br />
04-530<br />
PARKING BRAKE INDICATOR LIGHT NEVER / ALWAYS ON<br />
04-531<br />
• Fix four tires.<br />
• Pull and release the parking brake.<br />
Check if parking brake indicator light always/never on.<br />
NO > (Never on) Go to step 2.<br />
1. INSPECT PARKING BRAKE INDICATOR LIGHT<br />
Release the parking brake.<br />
Disconnect the A026 parking brake switch connector.<br />
Check if the parking brake light turns off.<br />
YES > Replace the parking brake switch.<br />
Disconnect the I003 instrument cluster.<br />
A026 (1) - O003 (B6)<br />
04-532<br />
3. CHECK HARNESS AND CONNECTOR (PARKING BRAKE SWITCH - GROUND)<br />
A026 (1) - Ground<br />
DIAGNOSTICS - POWER DOOR LOCKS<br />
04-533<br />
Off<br />
On (ACC)<br />
On (IG)<br />
Start<br />
To prevent the key locked in the vehicle, do not leave the key in the vehicle when disconnecting the<br />
(b) If no specific instructions, the ignition switch must be off.<br />
3. Disconnecting the negative battery cable will reset both the trip odometer data and the clock to<br />
‘ 0 ’.<br />
The total odometer data can not be reset to ‘ 0 ’.<br />
4. The audio system will lose stored memory data if the negative battery cable is disconnected.<br />
04-534<br />
1 Front Door Lock Assy LH<br />
4 Right Side Sliding Door Lock Assy<br />
5 Rear Hatch Lock Assy<br />
3 Front Door Lock Assy RH<br />
04-535<br />
CENTRAL LOCKING CONTROLLER ASSY A<br />
2 R Lock Output<br />
3 G Unlock Output<br />
4 G Driver Side Window Down Output<br />
5 R Driver Side Window Up Output<br />
6 R - L Co - pilot Side Window Down Output<br />
7 G - R Co - pilot Side Window Up Output<br />
8 W - L Window Control Power Input<br />
9 L - O Key Lock Input<br />
10 L - R Key Unlock Input<br />
11 Y Collision Signal Input<br />
12 G - Y Left Turn Light Signal<br />
13 G - B Right Turn Light Signal<br />
14 R Door Lamp Indicator<br />
15 L - B Left Door Assy Switch (Data) Output<br />
16 L Left Door Assy Switch (Clock) Output<br />
17 W - L Vehicle Speed Signal<br />
18 R - B Ignition Switch<br />
04-536<br />
CENTRAL LOCKING CONTROLLER ASSY B<br />
1 W - R Ignition Switch Illumination Control<br />
2 W - L Front Left Door Open Signal Output<br />
3 R Central Locking Spare Power<br />
4 G - R Horn<br />
6 O - L To Engine Hood Switch Output<br />
7 V - W Lamplet Forget To Turn Off Hints<br />
8 O - B Key Detection Switch<br />
10 W - B Ground<br />
04-537<br />
• The battery voltage should be above 12V.<br />
“Chapter 20A starting and charging - battery”<br />
Check basic function<br />
• Using the key in driver‘s door cylinder to<br />
lock, all doors should be locked.<br />
unlock, all doors should be unlocked.<br />
Yes Go to step 3<br />
Go to problem symptoms table.<br />
Check remote control function<br />
• When all doors are closed, using the<br />
remote key to lock the doors, all doors<br />
should be locked.<br />
remote key to unlock the doors, all doors<br />
should be unlocked.<br />
Replace the remote key.<br />
04-538<br />
cause of the problem. Check each part in order. If necessary, replace these parts<br />
The function of power door locks<br />
is inoperative (using the key)<br />
One door is inoperative (using<br />
the key)<br />
Door does not open / close<br />
(using the remote key)<br />
2. Power door lock control unit<br />
3. Harness<br />
1. Harness<br />
2. Door lock actuator<br />
3. Power door lock control unit<br />
1. Power door lock control unit<br />
2. Harness<br />
3. Door lock actuator<br />
4. Remote key<br />
5. Remote keyless entry receiver<br />
Chapter 04 diagnostics - power door<br />
locks, the function of power door locks is<br />
inoperative (using the key)<br />
locks, one door is inoperative (using the<br />
key)<br />
locks, door does not open / close (using<br />
the remote key)<br />
04-539<br />
THE FUNCTION OF POWER DOOR LOCKS IS INOPERATIVE<br />
(USING THE KEY)<br />
04-540<br />
• Before operating this inspection procedure, make sure the door open warning light is operating normally.<br />
• If the door open warning light is inoperative, repair it. Refer to “Chapter 04 diagnostics - instrument<br />
cluster, problem symptoms table”<br />
Inspect the central locking fuse (20A) in driver side<br />
2. CHECK HARNESS AND CONNECTOR (CENTRAL LOCKING FUSE - CENTRAL LOCKING CONTROLLER<br />
Disconnect the I008 central locking controller assy B connector.<br />
Central locking fuse (20 A) - I008 (B3)<br />
04-541<br />
3. CHECK HARNESS AND CONNECTOR (CENTRAL LOCKING CONTROLLER ASSY - GROUND)<br />
I007 (A1) - Ground<br />
4. CHECK HARNESS AND CONNECTOR (CENTRAL LOCKING CONTROLLER ASSY - FRONT<br />
DOOR LOCK ASSY LH)<br />
Disconnect the D006 front door lock assy LH connector.<br />
I007 (A9) - D006 (9)<br />
I007 (A10) - D006 (10)<br />
04-542<br />
5. CHECK HARNESS AND CONNECTOR (FRONT DOOR LOCK ASSY LH - GROUND)<br />
D006 (7) - Ground<br />
6. INSPECT FRONT DOOR LOCK ASSY LH<br />
Replace a new front door lock assy LH.<br />
YES > Replace the front door lock assy LH.<br />
7. CHECK CENTRAL LOCKING CONTROLLER ASSY<br />
Disconnect the I007 central locking controller assy connector.<br />
Use key to unlock A2 - A3 Battery voltage<br />
Use key to lock A3 - A2 Battery voltage<br />
YES > Repair or replace harness or connector.<br />
NO > Replace the central locking controller assy.<br />
04-543<br />
ONE DOOR IS INOPERATIVE (USING THE KEY)<br />
04-544<br />
• This inspection procedure is an example of front door LH, other doors inspection procedure are similar<br />
1. INSPECT FRONT DOOR LOCK ASSY LH<br />
Remove the front door inner guard board LH.<br />
Remove the front door water - proof film LH.<br />
Use key to unlock 4 - 1 Battery voltage<br />
Use key to lock 1 - 4 Battery voltage<br />
NO > Replace the front door lock assy LH.<br />
2. CHECK HARNESS AND CONNECTOR (CENTRAL LOCKING CONTROLLER ASSY - FRONT DOOR<br />
LOCK ASSY LH)<br />
I007 (A2) - D006 (4)<br />
I007 (A3) - D006 (1)<br />
YES > Replace the central locking controller assy.<br />
04-545<br />
DOOR DOES NOT OPEN / CLOSE (USING THE REMOTE KEY)<br />
04-546<br />
1. INSPECT REMOTE KEY<br />
Check the remote key battery. If the battery voltage is low, change the battery. If the problem is also<br />
exist, replace the remote key.<br />
YES > Replace the battery or remote key.<br />
04-547<br />
3. CHECK HARNESS AND CONNECTOR (CENTRAL LOCKING FUSE - CENTRAL LOCKING CONTROLLER<br />
ASSY )<br />
Disconnect the I007 central locking controller assy B connector.<br />
(c) Measure the resistance according to the value(s) in the<br />
central locking fuse (20 A) - I008 (8)<br />
4. CHECK HARNESS AND CONNECTOR<br />
Use remote key to<br />
lock<br />
unlock<br />
A2 - A3<br />
A3 - A2<br />
04-548<br />
SLIDING ROOF SYSTEM<br />
DIAGNOSTICS - SLIDING ROOF SYSTEM<br />
1 Sliding Roof Assy<br />
2 Sliding Roof Control Motor<br />
3 Sliding Roof Control Switch<br />
4 Sliding Roof ECU<br />
04-549<br />
This system has the following functions:<br />
<strong>Manual</strong> slide open and close.<br />
Auto slide open and close.<br />
Sliding roof control motor<br />
and sliding roof drive<br />
gear sub - assembly<br />
Sliding roof control<br />
module<br />
Sliding roof control module sends the signal to sliding roof control motor. The sliding<br />
roof control motor is then actived. Sliding roof control module controls sliding roof<br />
motor to rotate forward and backward.<br />
Sliding roof control switch sends the signal to sliding roof control module. The sliding<br />
roof control module analyses the signal and sends it to sliding roof control motor.<br />
3. SYSTEM OPERATION<br />
The sliding roof has the following features:<br />
<strong>Manual</strong> slide open<br />
and close<br />
Auto slide open and<br />
close<br />
This function enables sliding roof to open (or close) when OPEN/CLOSE switch is pressed<br />
without release. Sliding roof stops as soon as the switch is released.<br />
This function enables sliding roof to fully open (or close) when OPEN/CLOSE switch is<br />
pressed and immediately released.<br />
04-550<br />
TERMINALS OF MAIN COMPONENTS<br />
SLIDING ROOF CONTROL MODULE<br />
1 R<br />
Sliding roof ECU power supply<br />
input<br />
2 G Sliding roof control switch<br />
3 W - B To Sliding roof ECU<br />
4 R - B Sliding roof ECU - ACC input<br />
5 Y Sliding roof control switch<br />
6 - -<br />
04-551<br />
Charge or replace battery. Refer to<br />
“Chapter 20A/20B starting and charging -<br />
battery, replacement”<br />
Check the sliding roof opening operation.<br />
• Press the “OPEN” button.<br />
Does the sliding roof work correctly?<br />
Check the sliding roof closing operation.<br />
• Press the “CLOSE” button.<br />
Replace the sliding roof. Refer to “Chapter 86<br />
sliding roof - sliding roof assy, replacement”<br />
04-552<br />
Sliding roof system is inoperative<br />
3. Sliding roof control switch<br />
4. Sliding roof ECU<br />
5. Sliding rail<br />
6. Sliding roof control motor<br />
Chapter 86 sliding roof - sliding roof<br />
04-553<br />
SLIDING ROOF SYSTEM IS INOPERATIVE<br />
04-554<br />
Inspect the sliding roof fuse (15 A) and cigarette lighter<br />
fuse(15 A) in driver side junction box (I001).<br />
NO > Replace the sliding roof fuse or cigarette lighter fuse.<br />
2. INSPECT SLIDING ROOF CONTROL SWITCH<br />
Disconnect the F003 sliding roof control switch connector.<br />
Replace sliding roof control switch with a new one.<br />
YES > Replace the sliding roof control switch.<br />
3. INSPECT SLIDING ROOF CONTROL MOTOR<br />
Disconnect the sliding roof control motor connector.<br />
Replace sliding roof control motor with a new one.<br />
YES > Replace the sliding roof control motor.<br />
4. CHECK HARNESS AND CONNECTOR (SLIDING ROOF CONTROL SWITCH - GROUND)<br />
04-555<br />
F003 (3) - Ground<br />
F003 (2) - Ground<br />
5. CHECK HARNESS AND CONNECTOR (SLIDING ROOF ECU - GROUND)<br />
Disconnect the F002 sliding roof ECU connector.<br />
F002 (1) - Ground<br />
F002 (4) - Ground<br />
6. CHECK HARNESS AND CONNECTOR (SLIDING ROOF CONTROL SWITCH - SLIDING ROOF<br />
ECU)<br />
F002 (2) - F003 (4)<br />
F002 (5) - F003 (1)<br />
04-556<br />
7. CHECK HARNESS AND CONNECTOR (SLIDING ROOF ECU/SLIDING ROOF CONTROL SWITCH<br />
- GROUND)<br />
F002 (3) - Ground<br />
F003 (5) - Ground<br />
YES > Replace the sliding roof ECU.<br />
ABBREVIATIONS USED IN THIS MANUAL(TERMS) ................01-33<br />
ABS CONTROL IS UNREASONABLE(ANTI-LOCK<br />
BRAKE SYSTEM) ......................................................................04-122<br />
ABS MODULE CONNECTOR(ANTI-LOCK<br />
BRAKE SYSTEM) ......................................................................04-101<br />
(LIGHTING SYSTEM) ................................................................04-301<br />
(LIGHTING SYSTEM) ................................................................04-227<br />
ALL INTERIOR ILLUMINATION LAMPS ARE INOPERATIVE(LIGHT-<br />
ING SYSTEM)............................................................................04-314<br />
(POWER WINDOWS) ................................................................04-456<br />
(LIGHTING SYSTEM) ................................................................04-277<br />
ANTI-LOCK BRAKE SYSTEM .....................................................04-98<br />
AUDIO SYSTEM ........................................................................04-392<br />
AUXILIARY POWER..................................................................04-406<br />
AXLE AND PROPELLER SHAFT .................................... 02-18, 03-20<br />
(LIGHTING SYSTEM) ................................................................04-326<br />
A/C SYSTEM IS INOPERATIVE(HEATER AND AIR CONDITIONING<br />
SYSTEM) ...................................................................................04-162<br />
BASIC INSPECTION(DEFROSTER SYSTEM) .........................04-490<br />
BASIC INSPECTION(HEATER AND AIR CONDITIONING<br />
SYSTEM) ...................................................................................04-157<br />
BASIC INSPECTION(INSTRUMENT CLUSTER)......................04-510<br />
BASIC INSPECTION(OUTSIDE MIRROR) ...............................04-475<br />
BASIC INSPECTION(POWER DOOR LOCKS) ........................04-537<br />
BASIC INSPECTION(WIPER AND WASHER)..........................04-358<br />
BASIC SERVICE PROCEDURE(ENGINE<br />
CONTROL SYSTEM)...................................................................04-11<br />
BRAKE ............................................................................. 02-21, 03-23<br />
IN SPECIFIED DISTANCE (DISPLAYER IS NORMAL)<br />
(REVERSE RADAR SYSTEM) ..................................................04-442<br />
CAPTURING DATA(ENGINE CONTROL SYSTEM)...................04-21<br />
(LIGHTING SYSTEM) ................................................................04-296<br />
(LIGHTING SYSTEM) ................................................................04-324<br />
(AUXILIARY POWER) ...............................................................04-408<br />
CLUTCH........................................................................... 02-25, 03-27<br />
COOLING......................................................................... 02-11, 03-12<br />
DATA STREAM LIST/ACTIVE TEST(ENGINE<br />
CONTROL SYSTEM)...................................................................04-24<br />
DEFROSTER SYSTEM .............................................................04-487<br />
(LIGHTING SYSTEM) ................................................................04-322<br />
INDEX<br />
(ORGNIZED ALPHABETICALLY)<br />
DIAGNOSTIC HELP - INTERMITTENT FAULT(ENGINE CONTROL<br />
SYSTEM)....................................................................................... 04-9<br />
DIAGNOSTIC SYSTEM(ENGINE CONTROL SYSTEM)............ 04-17<br />
DIAGNOSTIC TROUBLE CODE CHART(ENGINE<br />
CONTROL SYSTEM) .................................................................. 04-28<br />
DIAGNOSTIC TROUBLE CODE CHART(SUPPLEMENTAL<br />
RESTRAINT SYSTEM) ............................................................. 04-133<br />
DIAGNOSTICS.............................................................................. 02-1<br />
(LIGHTING SYSTEM) ............................................................... 04-332<br />
DOOR LOCKS............................................................................. 02-35<br />
DOORS ............................................................................ 02-36, 03-36<br />
DTC DIAGNOSTIC(ENGINE CONTROL SYSTEM) ................... 04-33<br />
E<br />
(HOW TO TROUBLESHOOT)..................................................... 01-29<br />
EMISSION CONTROL ......................................................... 02-5, 03-5<br />
ENGINE CONTROL SYSTEM ....................................02-3, 03-2, 04-1<br />
ENGINE MECHANICAL ....................................................... 02-7, 03-6<br />
ENGINE SYMPTOM DIAGNOSTIC ............................................ 04-61<br />
EXHAUST......................................................................... 02-10, 03-11<br />
EXTERIOR AND INTERIOR TRIM.............................................. 03-37<br />
F<br />
FAIL-SAFE CHART(ENGINE CONTROL SYSTEM) .................. 04-22<br />
(LIGHTING SYSTEM) ............................................................... 04-310<br />
(LIGHTING SYSTEM) ............................................................... 04-238<br />
(LIGHTING SYSTEM) ............................................................... 04-233<br />
(POWER WINDOWS) ............................................................... 04-466<br />
(POWER WINDOWS) ............................................................... 04-461<br />
FRONT SUSPENSION..................................................... 02-15, 03-17<br />
FUEL .................................................................................... 02-4, 03-4<br />
G<br />
GENERAL INFORMATION(HOW TO TROUBLESHOOT) ......... 01-18<br />
GENERAL INFORMATION(HOW TO USE THIS MANUAL) ........ 01-1<br />
TIVE(LIGHTING SYSTEM) ....................................................... 04-264<br />
(LIGHTING SYSTEM) ............................................................... 04-275<br />
HAZARD WARNING SWITCH ILLUMINATION IS NOT INOPERA-<br />
(LIGHTING SYSTEM) ............................................................... 04-342<br />
(LIGHTING SYSTEM) ............................................................... 04-336<br />
HEATER AND AIR CONDITIONING................................ 02-28, 03-31<br />
HEATER AND AIR CONDITIONING SYSTEM ......................... 04-156<br />
HI-BEAM HEADLAMP IS INOPERATIVE<br />
(ONE SIDE)(LIGHTING SYSTEM)........................................... 04-218<br />
HORN IS ALWAYS ON(HORN SYSTEM) ................................ 04-422<br />
HORN IS INOPERATIVE(HORN SYSTEM).............................. 04-417<br />
HORN SYSTEM ........................................................................ 04-415<br />
HOW TO DIAGNOSTICS ANALYSE(ENGINE<br />
CONTROL SYSTEM) .................................................................... 04-6<br />
(HOW TO TROUBLESHOOT)..................................................... 01-20<br />
HOW TO TROUBLESHOOT ....................................................... 01-18<br />
HOW TO USE THIS MANUAL ...................................................... 01-1<br />
J<br />
IDENTIFICATION INFORMATION................................................ 01-6<br />
IGNITION..................................................................................... 03-14<br />
(LIGHTING SYSTEM) ............................................................... 04-293<br />
INSTRUMENT CLUSTER ......................................................... 04-502<br />
(LIGHTING SYSTEM) ............................................................... 04-319<br />
TIVE(LIGHTING SYSTEM) ....................................................... 04-340<br />
INSTRUMENT PANEL/INSTRUMENT........................................ 02-33<br />
INTAKE AIR........................................................................ 02-6, 03-10<br />
LICENSE LAMP IS INOPERATIVE(LIGHTING SYSTEM)........ 04-350<br />
LIGHTING.................................................................................... 03-33<br />
LIGHTING SYSTEM.................................................................. 04-202<br />
LO-BEAM AND HI-BEAM HEADLAMPS ARE INOPERATIVE<br />
(ONE SIDE)(LIGHTING SYSTEM)............................................ 04-224<br />
LO-BEAM HEADLAMP IS INOPERATIVE (ONE SIDE)(LIGHTING<br />
SYSTEM)................................................................................... 04-212<br />
LOCATION ................................................................................ 04-473<br />
LOCATION(ANTI-LOCK BRAKE SYSTEM).............................. 04-100<br />
LOCATION(AUDIO SYSTEM)................................................... 04-393<br />
LOCATION(AUXILIARY POWER) ............................................ 04-406<br />
LOCATION(DEFROSTER SYSTEM)........................................ 04-487<br />
LOCATION(ENGINE CONTROL SYSTEM).................................. 04-4<br />
LOCATION(HEATER AND AIR CONDITIONING SYSTEM) .... 04-158<br />
LOCATION(HORN SYSTEM) ................................................... 04-415<br />
LOCATION(INSTRUMENT CLUSTER) .................................... 04-503<br />
LOCATION(LIGHTING SYSTEM) ............................................. 04-204<br />
LOCATION(OUTSIDE MIRROR) .............................................. 04-473<br />
LOCATION(POWER DOOR LOCKS) ....................................... 04-534<br />
LOCATION(POWER WINDOWS) ............................................. 04-449<br />
LOCATION(SLIDING ROOF SYSTEM) .................................... 04-548<br />
LOCATION(SUPPLEMENTAL RESTRAINT SYSTEM)............ 04-130<br />
LOCATION(WIPER AND WASHER)......................................... 04-357<br />
LUBRICATION ................................................................. 02-12, 03-13<br />
MALFUCTION IN FUEL GAUGE / LOW FUEL WARNING LIGHT NEV-<br />
ER OR ALWAYS ON(INSTRUMENT CLUSTER) ..................... 04-517<br />
MALFUNCTION IN TACHOMETER(INSTRUMENT<br />
CLUSTER)................................................................................. 04-515<br />
MIRROR ADJUSTMENT LEFT/RIGHT IS INOPERATIVE(OUTSIDE<br />
MIRROR)................................................................................... 04-485<br />
MIRROR ADJUSTMENT UP/DOWN IS INOPERATIVE(OUTSIDE<br />
MIRROR)................................................................................... 04-483<br />
N<br />
NO COOLING FROM REAR A/C SYSTEM(HEATER AND AIR CON-<br />
DITIONING SYSTEM) ............................................................... 04-191<br />
ONE DOOR IS INOPERATIVE (USING THE KEY)(POWER DOOR<br />
LOCKS)......................................................................................04-543<br />
OUTSIDE MIRROR ...................................................................04-473<br />
INOPERATIVE(LIGHTING SYSTEM)........................................04-334<br />
P<br />
PARKING BRAKE.............................................................02-22, 03-24<br />
POWER DOOR LOCKS ............................................................04-533<br />
POWER STEERING .........................................................02-27, 03-29<br />
POWER WINDOWS ..................................................................04-448<br />
PRE - CHECK(ANTI-LOCK BRAKE SYSTEM) .........................04-105<br />
PRECAUTION(ANTI-LOCK BRAKE SYSTEM)...........................04-98<br />
PRECAUTION(AUDIO SYSTEM)..............................................04-392<br />
PRECAUTION(HEATER AND AIR<br />
CONDITIONING SYSTEM) .......................................................04-156<br />
PRECAUTION(INSTRUMENT CLUSTER)................................04-502<br />
PRECAUTION(LIGHTING SYSTEM) ........................................04-202<br />
PRECAUTION(POWER DOOR LOCKS) ..................................04-533<br />
PRECAUTION(POWER WINDOWS) ........................................04-448<br />
PRECAUTION(REPAIR INSTRUCTION) ......................................01-8<br />
PRECAUTION(REVERSE RADAR SYSTEM) ..........................04-424<br />
PRECAUTION(SUPPLEMENTAL RESTRAINT SYSTEM) .......04-129<br />
PRECAUTION(WIPER AND WASHER)....................................04-356<br />
PREPARATION(AXLE AND PROPELLER SHAFT)....................02-18<br />
PREPARATION(BRAKE).............................................................02-21<br />
PREPARATION(CLUTCH) ..........................................................02-25<br />
PREPARATION(COOLING) ........................................................02-11<br />
PREPARATION(DIAGNOSTICS) ..................................................02-1<br />
PREPARATION(DOOR LOCKS).................................................02-35<br />
PREPARATION(DOORS)............................................................02-36<br />
PREPARATION(EMISSION CONTROL).......................................02-5<br />
PREPARATION(ENGINE CONTROL SYSTEM)...........................02-3<br />
PREPARATION(ENGINE MECHANICAL) ....................................02-7<br />
PREPARATION(EXHAUST)........................................................02-10<br />
PREPARATION(FRONT SUSPENSION)....................................02-15<br />
PREPARATION(FUEL)..................................................................02-4<br />
PREPARATION(HEATER AND AIR CONDITIONING) ...............02-28<br />
PREPARATION(INSTRUMENT PANEL/INSTRUMENT)............02-33<br />
PREPARATION(INTAKE AIR).......................................................02-6<br />
PREPARATION(LUBRICATION).................................................02-12<br />
PREPARATION(PARKING BRAKE) ...........................................02-22<br />
PREPARATION(POWER STEERING)........................................02-27<br />
PREPARATION(REAR SUSPENSION) ......................................02-16<br />
PREPARATION(SEAT BELT) .....................................................02-30<br />
PREPARATION(SEAT) ...............................................................02-34<br />
PREPARATION(STARTING AND CHARGING)..........................02-14<br />
PREPARATION(STEERING COLUMN)......................................02-26<br />
PREPARATION(TIRE AND WHEEL) ..........................................02-17<br />
PREPARATION(TRANSMISSION) .............................................02-23<br />
PREPARATION(VEHICLE CONTROL SYSTEM) .......................02-37<br />
PREPARATION(WINDSHIELD/SIDE WINDOW GLASS/REAR VIEW<br />
MIRROR) .....................................................................................02-32<br />
PREPARATION(WIPER AND WASHER)....................................02-31<br />
PROBLEM SYMPTOMS TABLE(ANTI-LOCK<br />
BRAKE SYSTEM)......................................................................04-104<br />
PROBLEM SYMPTOMS TABLE(DEFROSTER SYSTEM) .......04-491<br />
PROBLEM SYMPTOMS TABLE(ENGINE<br />
CONTROL SYSTEM) ..................................................................04-60<br />
PROBLEM SYMPTOMS TABLE(HEATER AND AIR<br />
CONDITIONING SYSTEM) .......................................................04-159<br />
PROBLEM SYMPTOMS TABLE(INSTRUMENT CLUSTER)....04-511<br />
PROBLEM SYMPTOMS TABLE(OUTSIDE MIRROR) .............04-476<br />
PROBLEM SYMPTOMS TABLE(POWER DOOR LOCKS) ......04-538<br />
PROBLEM SYMPTOMS TABLE(SLIDING ROOF SYSTEM) ...04-552<br />
PROBLEM SYMPTOMS TABLE(SUPPLEMENTAL RESTRAINT<br />
SYSTEM) ...................................................................................04-134<br />
R<br />
(LIGHTING SYSTEM) ................................................................04-328<br />
RADIO RECEPTION IS POOR(AUDIO SYSTEM) ....................04-400<br />
(ENGINE CONTROL SYSTEM)...................................................04-19<br />
ERATIVE(LIGHTING SYSTEM).................................................04-330<br />
(LIGHTING SYSTEM) ................................................................04-241<br />
REAR SUSPENSION....................................................... 02-16, 03-18<br />
REAR WINDOW DEFROST ER IS INOPERATIVE<br />
(DEFROSTER SYSTEM)...........................................................04-492<br />
REAR WINDOW DEFROSTER SWITCH ILLUMINATION IS NOT IN-<br />
OPERATIVE(LIGHTING SYSTEM) ...........................................04-338<br />
REPAIR INSTRUCTION ................................................................01-8<br />
(SUPPLEMENTAL RESTRAINT SYSTEM)...............................04-131<br />
REVERSE RADAR SYSTEM.....................................................04-424<br />
REVERSE RADAR SYSTEM IS INOPERATIVE AT ALL(REVERSE<br />
RADAR SYSTEM)......................................................................04-429<br />
S<br />
SEAT................................................................................ 02-34, 03-35<br />
SEAT BELT...................................................................... 02-30, 03-32<br />
SERIAL NUMBER (SN)(IDENTIFICATION INFORMATION) ........01-7<br />
SERVICE DATA(AXLE AND PROPELLER SHAFT) ...................03-20<br />
SERVICE DATA(BRAKE) ............................................................03-23<br />
SERVICE DATA(CLUTCH)..........................................................03-27<br />
SERVICE DATA(COOLING)........................................................03-12<br />
SERVICE DATA(DOOR)..............................................................03-36<br />
SERVICE DATA(EMISSION CONTROL) ......................................03-6<br />
SERVICE DATA(ENGINE CONTROL SYSTEM) ..........................03-2<br />
SERVICE DATA(EXHAUST) .......................................................03-11<br />
SERVICE DATA(FRONT SUSPENSION) ...................................03-17<br />
SERVICE DATA(FUEL) .................................................................03-4<br />
SERVICE DATA(HEATER AND AIR CONDITIONING)...............03-31<br />
SERVICE DATA(IGNITION) ........................................................03-14<br />
SERVICE DATA(INTAKE AIR) ....................................................03-10<br />
SERVICE DATA(POWER STEERING) .......................................03-29<br />
SERVICE DATA(STARTING AND CHARGING) .........................03-15<br />
SERVICE DATA(STEERING COLUMN) .....................................03-28<br />
SERVICE DATA(TIRE AND WHEEL)..........................................03-19<br />
SERVICE DATA(TRANSMISSION) .............................................03-25<br />
SLIDING ROOF SYSTEM..........................................................04-548<br />
SPECIFIED TORQUE FOR SPECIFICATION BOLTS..................03-1<br />
STARTING AND CHARGING .......................................... 02-14, 03-15<br />
STEERING COLUMN ...................................................... 02-26, 03-28<br />
STEP LAMP ARE INOPERATIVE(LIGHTING SYSTEM) ..........04-304<br />
(LIGHTING SYSTEM) ................................................................04-282<br />
SUPPLEMENTAL RESTRAINT SYSTEM .................................04-129<br />
SYSTEM DESCRIPTION(DEFROSTER SYSTEM) ..................04-489<br />
SYSTEM DESCRIPTION(REVERSE RADAR SYSTEM)..........04-426<br />
SYSTEM DESCRIPTION(SLIDING ROOF SYSTEM)...............04-549<br />
TAIL LAMPS ARE INOPERATIVE(LIGHTING SYSTEM)..........04-347<br />
TERMINALS OF INSTRUMENT CLUSTER(INSTRUMENT CLUS-<br />
TER)...........................................................................................04-507<br />
(OUTSIDE MIRROR) .................................................................04-474<br />
TERMS.........................................................................................01-33<br />
THE FUNCTION OF POWER DOOR LOCKS IS INOPERATIVE (US-<br />
ING THE KEY)(POWER DOOR LOCKS).................................. 04-539<br />
TIRE AND WHEEL ........................................................... 02-17, 03-19<br />
TORQUE SPECIFICATION(AXLE AND PROPELLER SHAFT) . 03-21<br />
TORQUE SPECIFICATION(BRAKE) .......................................... 03-23<br />
TORQUE SPECIFICATION(CLUTCH)........................................ 03-27<br />
TORQUE SPECIFICATION(COOLING)...................................... 03-12<br />
TORQUE SPECIFICATION(DOOR) ........................................... 03-36<br />
TORQUE SPECIFICATION(EMISSION CONTROL) ........... 03-5, 03-9<br />
TORQUE SPECIFICATION(ENGINE CONTROL SYSTEM) ........ 03-3<br />
TORQUE SPECIFICATION(EXHAUST) ..................................... 03-11<br />
TORQUE SPECIFICATION(EXTERIOR AND INTERIOR TRIM)03-37<br />
TORQUE SPECIFICATION(FRONT SUSPENSION) ................. 03-17<br />
TORQUE SPECIFICATION(FUEL) ............................................... 03-4<br />
TORQUE SPECIFICATION(HEATER AND AIR<br />
CONDITIONING)......................................................................... 03-31<br />
TORQUE SPECIFICATION(IGNITION) ...................................... 03-14<br />
TORQUE SPECIFICATION(INTAKE AIR) .................................. 03-10<br />
TORQUE SPECIFICATION(LIGHTING) ..................................... 03-33<br />
TORQUE SPECIFICATION(LUBRICATION) .............................. 03-13<br />
TORQUE SPECIFICATION(PARKING BRAKE)......................... 03-24<br />
TORQUE SPECIFICATION(POWER STEERING) ..................... 03-30<br />
TORQUE SPECIFICATION(REAR SUSPENSION).................... 03-18<br />
TORQUE SPECIFICATION(SEAT BELT)................................... 03-32<br />
TORQUE SPECIFICATION(SEAT)............................................. 03-35<br />
TORQUE SPECIFICATION(STARTING AND CHARGING) ....... 03-16<br />
TORQUE SPECIFICATION(STEERING COLUMN) ................... 03-28<br />
TORQUE SPECIFICATION(TIRE AND WHEEL)........................ 03-19<br />
TORQUE SPECIFICATION(TRANSMISSION)........................... 03-26<br />
TORQUE SPECIFICATION(VEHICLE CONTROL SYSTEM) .... 03-38<br />
TORQUE SPECIFICATION(WIPER AND WASHER) ................. 03-34<br />
TRANSMISSION .............................................................. 02-23, 03-25<br />
TRUNK LAMP IS INOPERATIVE(LIGHTING SYSTEM)........... 04-307<br />
LAMPS ARE NORMAL)(LIGHTING SYSTEM) ......................... 04-260<br />
WASHER PUMP IS INOPERATIVE - REAR WINDOW(WIPER AND<br />
WASHER).................................................................................. 04-387<br />
WASHER PUMP IS INOPERATIVE - WINDSHIELD(WIPER AND<br />
WASHER).................................................................................. 04-374<br />
VEHICLE CONTROL SYSTEM........................................ 02-37, 03-38<br />
VEHICLE IDENTIFICATION NUMBER (VIN)(IDENTIFICATION IN-<br />
FORMATION)................................................................................ 01-6<br />
VEHICLE LIFT AND SUPPORT LOCATIONS(REPAIR INSTRUC-<br />
TION)........................................................................................... 01-16<br />
NOT RETRACT(WIPER AND WASHER) ................................. 04-378<br />
WIDTH LAMPS IS NOT INOPERATIVE(LIGHTING SYSTEM) 04-344<br />
TIVE(LIGHTING SYSTEM) ....................................................... 04-352<br />
WINDSHIELD/SIDE WINDOW GLASS/REAR<br />
VIEW MIRROR............................................................................ 02-32<br />
WIPER AND WASHER .......................................02-31, 03-34, 04-356<br />
(WIPER AND WASHER) ........................................................... 04-381<br />
WIPERS ARE INOPERATIVE - WINDSHIELD(WIPER AND WASH-<br />
ER) ............................................................................................ 04-361<br />
WIPERS ARE INOPERATIVE AT HIGH SPEED - WINDSHIELD(WIP-<br />
ER AND WASHER) ................................................................... 04-369<br />
WIPERS ARE INOPERATIVE AT LOW SPEED - WINDSHIELD(WIP-<br />
ER AND WASHER) ................................................................... 04-367<br />
SHIELD(WIPER AND WASHER) .............................................. 04-371<br />
V O L U M E 2<br />
DIAGNOSTICS(RHD)<br />
HOW TO DIAGNOSTICS ANALYSE........................................... 04-5<br />
DIAGNOSTIC HELP - INTERMITTENT FAULT .......................... 04-8<br />
BASIC SERVICE PROCEDURE................................................ 04-10<br />
TERMINALS OF ECM................................................................ 04-11<br />
DIAGNOSTIC SYSTEM............................................................. 04-16<br />
READING AND ERASING DIAGNOSTIC TROUBLE CODE<br />
(DTC) ......................................................................................... 04-18<br />
CAPTURING DATA ................................................................... 04-20<br />
FAIL-SAFE CHART.................................................................... 04-21<br />
DATA STREAM LIST/ACTIVE TEST......................................... 04-23<br />
DIAGNOSTIC TROUBLE CODE CHART.................................. 04-27<br />
DTC DIAGNOSTIC .................................................................... 04-32<br />
PROBLEM SYMPTOMS TABLE................................................ 04-58<br />
ENGINE SYMPTOM DIAGNOSTIC........................................... 04-59<br />
ANTI-LOCK BRAKE SYSTEM......................................................... 04-96<br />
PRECAUTION............................................................................ 04-96<br />
ABS MODULE CONNECTOR ................................................... 04-98<br />
DIAGNOSTIC TROUBLE CODE CHART.................................. 04-99<br />
PROBLEM SYMPTOMS TABLE.............................................. 04-101<br />
PRE - CHECK.......................................................................... 04-102<br />
POWER SUPPY VOLTAGE HIGH OR LOW........................... 04-104<br />
SOLENOID VALVES AND VALVES RELAY FAILURE........... 04-105<br />
PUMP MOTOR FAILURE ........................................................ 04-109<br />
WHEEL SPEED SENSOR CIRCUIT FAULT........................... 04-113<br />
WHEEL SPEED SENSOR SIGNAL FAULT ............................ 04-115<br />
ABS CONTROL IS UNREASONABLE .................................... 04-119<br />
ABS SYSTEM IS INOPERATIVE............................................. 04-122<br />
SUPPLEMENTAL RESTRAINT SYSTEM ..................................... 04-126<br />
PRECAUTION.......................................................................... 04-126<br />
RESTRAINT CONTROL MODULE (RCM) CONNECTOR<br />
PIN ........................................................................................... 04-127<br />
DIAGNOSTIC TROUBLE CODE CHART................................ 04-129<br />
PROBLEM SYMPTOMS TABLE.............................................. 04-130<br />
8101 - POWER SUPPLY VOLTAGE HIGH ............................. 04-131<br />
8102 - POWER SUPPLY VOLTAGE LOW.............................. 04-131<br />
8201 - DRIVER AIRBAG FAULT - HIGH RESISTANCE ......... 04-133<br />
8202 - DRIVER AIRBAG FAULT - LOW RESISTANCE.......... 04-133<br />
8203 - DRIVER AIRBAG CIRCUIT SHORT TO GROUND...... 04-135<br />
8204 - DRIVER AIRBAG CIRCUIT SHORT TO BATTERY ..... 04-137<br />
RESISTANCE .......................................................................... 04-139<br />
8213 - CO - PILOT SIDE AIRBAG CIRCUIT SHORT TO<br />
GROUND ................................................................................. 04-141<br />
8214 - CO - PILOT SIDE AIRBAG CIRCUIT SHORT TO<br />
BATTERY ................................................................................ 04-143<br />
SRS WARNING LIGHT IS ALWAYS ON ................................. 04-145<br />
SRS WARNING LIGHT IS INOPERATIVE .............................. 04-147<br />
HEATER AND AIR CONDITIONING SYSTEM.............................. 04-149<br />
PRECAUTION.......................................................................... 04-149<br />
BASIC INSPECTION ............................................................... 04-150<br />
PROBLEM SYMPTOMS TABLE.............................................. 04-151<br />
A/C SYSTEM IS INOPERATIVE.............................................. 04-153<br />
FRONT BLOWER MOTOR IS INOPERATIVE ........................ 04-157<br />
FRONT AIR FLOW IS INSUFFICIENT .................................... 04-163<br />
NO COOLING FROM FRONT A/C SYSTEM .......................... 04-167<br />
REAR HEATER IS INOPERATIVE OR INSUFFICIENT<br />
HEATING ................................................................................. 04-174<br />
LIGHTING SYSTEM ....................................................................... 04-181<br />
PRECAUTION.......................................................................... 04-181<br />
BASIC INSPECTION ............................................................... 04-182<br />
LOCATION............................................................................... 04-183<br />
PROBLEM SYMPTOMS TABLE.............................................. 04-185<br />
LO - BEAM HEADLAMP IS INOPERATIVE (ONE SIDE) ........ 04-191<br />
LO - BEAM HEADLAMPS ARE INOPERATIVE<br />
(BOTH SIDES) ......................................................................... 04-193<br />
HI - BEAM HEADLAMP IS INOPERATIVE (ONE SIDE) ......... 04-197<br />
(BOTH SIDES) ......................................................................... 04-199<br />
LO - BEAM AND HI - BEAM HEADLAMPS ARE INOPERATIVE<br />
(ONE SIDE)............................................................................. 04-204<br />
ALL HEADLAMPS ARE INOPERATIVE .................................. 04-207<br />
FRONT FOG LAMPS ARE INOPERATIVE ............................. 04-213<br />
FRONT FOG LAMPS ARE ALWAYS ON ................................ 04-218<br />
REAR FOG LAMPS ARE INOPERATIVE................................ 04-221<br />
REAR FOG LAMPS ARE ALWAYS ON .................................. 04-226<br />
ALL FOG LAMPS ARE INOPERATIVE ................................... 04-229<br />
LAMPS ARE NORMAL) ........................................................... 04-236<br />
LAMPS ARE NORMAL) ........................................................... 04-240<br />
TIVE ......................................................................................... 04-245<br />
TURN SIGNAL LAMPS ARE INOPERATIVE (ONE SIDE)...... 04-254<br />
HAZARD WARNING LAMPS ARE ALWAYS ON .................... 04-258<br />
ALL STOP LAMPS ARE INOPERATIVE ................................. 04-260<br />
STOP LAMP IS INOPERATIVE (ONE SIDE) .......................... 04-265<br />
HIGH - MOUNTED STOP LAMP IS INOPERATIVE................ 04-267<br />
BACK - UP LAMP IS INOPERATIVE(ONE SIDE) ................... 04-269<br />
BACK - UP LAMPS ARE INOPERATIVE (BOTH SIDES) ....... 04-271<br />
IGNITION SWITCH ILLUMINATION IS INOPERATIVE .......... 04-275<br />
CENTRAL DOME LIGHT IS INOPERATIVE ........................... 04-278<br />
AIR PURIFIER LAMP IS INOPERATIVE ................................. 04-283<br />
STEP LAMP ARE INOPERATIVE ........................................... 04-286<br />
TRUNK LAMP IS INOPERATIVE ............................................ 04-288<br />
FRONT DOME LIGHT IS INOPERATIVE................................ 04-291<br />
ALL INTERIOR ILLUMINATION LAMPS ARE INOPERATIVE 04-295<br />
INSTRUMENT CLUSTER ILLUMINATION IS NOT IN<br />
OPERATIVE............................................................................. 04-300<br />
DIAGNOSIS SWITCH ILLUMINATION IS NOT<br />
INOPERATIVE ......................................................................... 04-303<br />
CIGARETTE LIGHTER ILLUMINATION IS NOT<br />
INOPERATIVE......................................................................... 04-305<br />
A/C CONTROL PANEL ILLUMINATION IS NOT<br />
INOPERATIVE......................................................................... 04-307<br />
RADIO ILLUMINATION IS NOT INOPERATIVE ..................... 04-309<br />
REAR BLOWER FORWARD SWITCH ILLUMINATION IS NOT IN-<br />
OPERATIVE ............................................................................ 04-311<br />
DOME LIGHT SWITCH ILLUMINATION IS NOT<br />
INOPERATIVE......................................................................... 04-313<br />
INOPERATIVE......................................................................... 04-315<br />
TIVE ......................................................................................... 04-317<br />
INSTRUMENT DIMMER SWITCH ILLUMINATION IS NOT INOPER-<br />
ATIVE....................................................................................... 04-319<br />
TIVE ......................................................................................... 04-321<br />
WIDTH LAMPS IS NOT INOPERATIVE.................................. 04-323<br />
TAIL LAMPS ARE INOPERATIVE........................................... 04-325<br />
LICENSE LAMP IS INOPERATIVE ......................................... 04-328<br />
TIVE ......................................................................................... 04-330<br />
WIPER AND WASHER .................................................................. 04-334<br />
PRECAUTION.......................................................................... 04-334<br />
BASIC INSPECTION ............................................................... 04-334<br />
PROBLEM SYMPTOMS TABLE.............................................. 04-336<br />
WINDSHIELD........................................................................... 04-338<br />
WIPERS ARE INOPERATIVE - WINDSHIELD........................ 04-339<br />
WIPERS ARE INOPERATIVE AT LOW SPEED -<br />
WINDSHIELD........................................................................... 04-344<br />
WIPERS ARE INOPERATIVE AT HIGH SPEED -<br />
WINDSHIELD........................................................................... 04-345<br />
SHIELD .................................................................................... 04-346<br />
WASHER PUMP IS INOPERATIVE - WINDSHIELD............... 04-348<br />
NOT RETRACT........................................................................ 04-351<br />
REAR WINDOW ...................................................................... 04-353<br />
WASHER PUMP IS INOPERATIVE - REAR WINDOW .......... 04-358<br />
AUDIO SYSTEM............................................................................. 04-361<br />
PRECAUTION.......................................................................... 04-361<br />
BASIC INSPECTION ............................................................... 04-362<br />
PROBLEM SYMPTOMS TABLE.............................................. 04-363<br />
RADIO DOES NOT WORK...................................................... 04-364<br />
RADIO RECEPTION IS POOR................................................ 04-368<br />
POOR SOUND QUALITY....................................................... 04-369<br />
SPEAKER DOES NOT WORK ................................................ 04-370<br />
AUXILIARY POWER...................................................................... 04-374<br />
PROBLEM SYMPTOMS TABLE.............................................. 04-374<br />
CIGARETTE LIGHTER IS INOPERATIVE .............................. 04-375<br />
12V POWER SUPPLY OUTPUT SOCKET IS INOPERATIVE 04-378<br />
HORN SYSTEM.............................................................................. 04-382<br />
PROBLEM SYMPTOMS TABLE.............................................. 04-382<br />
HORN IS INOPERATIVE......................................................... 04-383<br />
HORN IS ALWAYS ON............................................................ 04-389<br />
REVERSE RADAR SYSTEM ......................................................... 04-391<br />
PRECAUTION.......................................................................... 04-391<br />
SYSTEM DESCRIPTION......................................................... 04-392<br />
PROBLEM SYMPTOMS TABLE.............................................. 04-394<br />
REVERSE RADAR SYSTEM IS INOPERATIVE AT ALL ........ 04-395<br />
VER IS OUT OF REVERSE POSITION .................................. 04-400<br />
DISTANCE (BACK-UP LAMP IS NORMAL) ........................... 04-402<br />
OBSTACLE BEHIND VEHICLE ............................................... 04-405<br />
IN SPECIFIED DISTANCE (DISPLAYER IS NORMAL) .......... 04-408<br />
(BUZZER IS NORMAL)............................................................ 04-411<br />
POWER WINDOWS ....................................................................... 04-414<br />
PRECAUTION.......................................................................... 04-414<br />
DOOR CONTROL SWITCH PIN.............................................. 04-415<br />
WINDOW CONTROL SWITCH LH PIN ................................... 04-416<br />
CENTRAL LOCKING CONTROLLER ASSY A PIN................. 04-417<br />
BASIC INSPECTION .............................................................. 04-418<br />
PROBLEM SYMPTOMS TABLE.............................................. 04-419<br />
ALL POWER WINDOWS ARE INOPERATIVE ....................... 04-421<br />
FRONT POWER WINDOW RH IS INOPERATIVE .................. 04-427<br />
FRONT POWER WINDOW LH DOES NOT OPEN................. 04-430<br />
FRONT POWER WINDOW LH DOES NOT CLOSE............... 04-432<br />
FRONT POWER WINDOW RH IS INOPERATIVE (USE DOOR<br />
CONTROL SWITCH) ............................................................... 04-434<br />
FRONT POWER WINDOW LH IS INOPERATIVE (USE WINDOW<br />
CONTROL SWITCH RH) ......................................................... 04-436<br />
OUTSIDE MIRROR ........................................................................ 04-439<br />
TERMINALS OF OUTSIDE MIRROR SWITCH....................... 04-439<br />
BASIC INSPECTION ............................................................... 04-440<br />
PROBLEM SYMPTOMS TABLE.............................................. 04-441<br />
MIRRORS ARE INOPERATIVE (BOTH SIDES) ..................... 04-442<br />
A SINGLE MIRROR IS INOPERATIVE ................................... 04-445<br />
MIRROR ADJUSTMENT UP/DOWN IS INOPERATIVE ......... 04-448<br />
MIRROR ADJUSTMENT LEFT/RIGHT IS INOPERATIVE...... 04-450<br />
OUTSIDE MIRROR DEFROSTER SYSTEM................................. 04-452<br />
SYSTEM DESCRIPTION......................................................... 04-452<br />
BASIC INSPECTION ................................... 04-453<br />
OUTSIDE MIRROR DEFROSTER IS INOPERATIVE............ 04-455<br />
INSTRUMENT CLUSTER .............................................................. 04-461<br />
PRECAUTION.......................................................................... 04-461<br />
LOCATION............................................................................... 04-462<br />
INSTRUMENT CLUSTER INFORMATION.............................. 04-463<br />
LIQUID CRYSTAL DISPLAY ................................................... 04-465<br />
TERMINALS OF INSTRUMENT CLUSTER ............................ 04-466<br />
BASIC INSPECTION ............................................................... 04-469<br />
PROBLEM SYMPTOMS TABLE.............................................. 04-470<br />
MALFUNCTION IN SPEEDOMETER ...................................... 04-472<br />
MALFUNCTION IN TACHOMETER ........................................ 04-474<br />
NEVER OR ALWAYS ON ........................................................ 04-476<br />
MALFUCTION IN ENGINE COOLANT TEMPERATURE<br />
GAUGE .................................................................................... 04-479<br />
ENGINE OIL PRESSURE WARNING LIGHT NEVER / ALWAYS<br />
ON............................................................................................ 04-482<br />
SEAT BELT WARNING LIGHT NEVER / ALWAYS ON.......... 04-485<br />
PARKING BRAKE INDICATOR LIGHT NEVER / ALWAYS<br />
ON............................................................................................ 04-489<br />
POWER DOOR LOCKS................................................................. 04-492<br />
PRECAUTION.......................................................................... 04-492<br />
CENTRAL LOCKING CONTROLLER ASSY A........................ 04-493<br />
CENTRAL LOCKING CONTROLLER ASSY B........................ 04-494<br />
BASIC INSPECTION ............................................................... 04-495<br />
PROBLEM SYMPTOMS TABLE.............................................. 04-496<br />
(USING THE KEY)................................................................... 04-497<br />
ONE DOOR IS INOPERATIVE (USING THE KEY)................. 04-502<br />
DOOR DOES NOT OPEN / CLOSE (USING THE<br />
REMOTE KEY) ........................................................................ 04-504<br />
DIAGNOSTICS(RHD) - ENGINE CONTROL SYSTEM<br />
3. THE SAVING DATA SETTING WILL LOST IF DISCONNECTING THE BATTER NEGATIVE CABLE.<br />
Inspect for “add-on” accessories which may be interfering with the ground circuit.<br />
If several wires are crimped into one ground eyelet terminal, check for improper crimps.<br />
Make sure all of the wires are clean, securely fastened and providing a good ground path.<br />
If multiple wires are cased in one eyelet, make sure no ground wires have excess wire<br />
insulation.<br />
4. CHECK DTC AND DATA FREEZE-FRAME DATA<br />
If one doubtful region is considered to cause a failure, heat the part which is the most possible cause of<br />
heater blower, the headlamps and the rear-window defroster, to check if the failure occurs. The trouble<br />
of failure before starting the test and the pre-connection of connectors, then carry out the symptom<br />
diagnostic scanner, make the rated data status to simulate the fault conditions based on the freezeframe<br />
on the diagnostic scanner.<br />
ECM or control modules on a failure-free vehicle for testing; Don’t install new control modules on a<br />
7 Injector 3 L - P 49 ECT sensor + W - R<br />
10 A/C low voltage output L 52 ECT sensor - W - B<br />
16 - - 58 Knock sensor signal B - W<br />
17 High fan control W - B 59 Accelerator sensor + Br - G<br />
19 MILL G - B 61 - -<br />
L-R 66<br />
37 Knock power O - V 79 A/C request Y - B<br />
38 - 80 - -<br />
39 - 81 - -<br />
40 -<br />
0.3 ~ 0.9 V<br />
CHECK ECM HARNESS-SIDE TERMINAL WITH A MULTIMETER<br />
diagnostic scanner or special equipment with<br />
corresponding functions.<br />
then goes out (system self-checking). The SVS lamp and MIL lamp are off after engine starting and<br />
then lights on after self-checked; After engine starting, if the SVS lamp in failure class is defined as<br />
3. If an engine failure that may involve the fuel injection system-electronic controlled is to be<br />
diagnosed and cleared, first determine if the failure is related with the fuel injection systemelectronic<br />
controlled. If the engine fails but the malfunction indicator lamp doesn't light, the failure<br />
The diagnostic trouble codes record and data related with sensors and actuators in ECM can be read<br />
by KT600 diagnostic scanner. Additional, the actuator can be positive driven by the scan tool under<br />
specified conditions.<br />
DLC- data link connector.<br />
• Connect the diagnostic scanner cable to DLC. Turn the ignition switch ON. Try to open it. If<br />
displayed error communication on screen, then the diagnostic scanner faults .<br />
• If the diagnostic scanner communicates with other vehicle normally, then check the DLC on the<br />
original vehicle.<br />
ENGINE CONTROL SYSTEM SELF-DIAGNOTIC ITEM<br />
erased from the memory, or it can be processed referring to the trouble-shooting methods for<br />
(c) Connect the KT600 scan tool to the Data Link Connector (DLC) - use the most current software<br />
(f) Check DTC and data stream. After recording, delete it (If DTC cannot be deleted, then perform the<br />
diagnosis procedure refering to “Diagnostics trouble code check”. Repair faults ).<br />
(j) If there are DTCs, but the data stream is normal or the function is good, then refer to the diagnostics<br />
help. If there are DTCs, but the stream is abnormal or the function is not good, then perform diagnosis<br />
procedure refering to “Diagnostics trouble code chart”.<br />
If the DTC is detected but the trouble can’t reappear, confirm the freeze-frame rated data. ECM records<br />
the engine condition in form of freeze-frame data at regular intervals. The diagnostic scanner can be<br />
used to read several sets of freeze-frame data respectively. KT600 diagnostic scanner provides<br />
FAIL-SAFE CHART<br />
When the DTC listed below is detected, the ECM enters fail-safe mode and the MIL lights up.<br />
• The engine base fuel closed-loop control self-learning will be shut<br />
• The engine idle air control self-learning will be shut off.<br />
ECT: -20 ℃<br />
(g) After repairing, using the KT600 to perform again.<br />
(h) Clear DTC.<br />
(i) Disconnect KT600 scan tool.<br />
(j) Restart engine to perform test. Confirm the faults has been eliminated.<br />
DFCO<br />
Front Oxygen Sensor Signal Lean In PE<br />
MT20U2 adopted speed-density air measurement method to check the air intake volume into the engine so as<br />
to control the fuel injection pulse width for the precise control of engine power output. Meanwhile, this system<br />
adopted intake pressure cylinder determination technology and the intake air sensor is installed near the inlet<br />
opening of cylinder 4 intake manifold. At the moment when the throttle is opened, there will be one<br />
intake air temperature of -45<br />
following the increasing of the temperature in non-linear relation. When the coolant temperature is low, the<br />
intakeair temperature of -45 ℃ or lower) for<br />
4 seconds<br />
• If the ECM detects the DTC P0117 or P0118, it operates the fail–safe function in which the<br />
engine coolant temperature is assumed to be a default value. At the same time, with the ignition<br />
switch ON, the cooling fans will operate at high speed. The fail–safe function will not untill the<br />
ECM detects the acceptance condition.<br />
-40 °C Open circuit<br />
(a) Start the engine and warm it to normal operating temperature.<br />
(b) With the KT600 scan tool, perform the DTC confirming procedure.<br />
(c) Read sensor value displayed on the KT600 scan tool.<br />
(d) Read sensor value displayed on the KT600 scan tool.<br />
E010 (2) - Ground<br />
E010 (1) - E001 (52)<br />
sensor is of three-line type and the ECM will check the throttle open extent by monitoring the voltage variation.<br />
P1167 - FRONT OXYGEN SENSOR SIGNAL RICH IN DFCO<br />
P1171 - FRONT OXYGEN SENSOR SIGNAL LEAN IN PE<br />
. An open oxygen sensor circuit or a cold oxygen sensor causes open-loop operation.<br />
signal rich in dfco<br />
signal lean in pe<br />
• Normal scan tool voltage varies between 0.1 to 1.0 V while in closed-loop.<br />
ECM contains a non-replaceable knock filter module called a Signal-to-noise Enhancement Filter (SNEF)<br />
Disconnect the E011 knock sensor connector.<br />
injected into the cylinder every time will be attached, making the air-fuel mixture strength actually into<br />
the air forms a spiral vortex at the coarse section, affecting the air intake effect and the quality of air-fuel<br />
mixture. On the other hand, the carbon deposits block the idling aisle, making the idling speed control<br />
device clamped or exceeding its regulation range, leading to low idling speed and rough idling.<br />
• Service vehicles in well-ventilated areas and avoid ignition sources.<br />
15. CHECK ENGINE VALVE-TIMING<br />
(a) Check whether the engine valve-timing gear mark is aligned, damaged. And the belt is loose. Whether<br />
19. CHECK ENGINE VALVE-TIMING<br />
(a) Check whether the engine valve-timing gear mark is aligned, damaged and the belt is loose.<br />
air-fuel.<br />
• Compression<br />
pressure is too low<br />
• Malfunction of air-fuel<br />
• Check whether the idle air control motor can extend-retract when turning the switch off.<br />
can feel vibration, or with the voice-tool, touch the injector, the action voice should be hearded).<br />
(h) Check whether the Three-Way Catalytic Converter (TWC) is blocked.<br />
(c) When the temperature is normal after the engine enter into the closed-loop control, inspect if the<br />
16. CHECK ENGINE VALVE-TIMING<br />
11. CHECK ENGINE VALVE-TIMING<br />
• Malfunction of air-fuel ratio<br />
signal, namely a steady speed control that the engine is controlled in target speed range. Speedraising<br />
control is done if with load signal. During starting, the load signal is input into ECM, the later<br />
• Inspect if the idle trembles is normal or load reasons, such as: A\C, lighting, push the lever into gear,<br />
Check throttle body and idle air path. Clear the carbon deposit and greasy dirt.<br />
(a) With the scan tool, check whether the throttle is normal.<br />
(a) Check secondary ignition wire resistance. And clean the connector terminals.<br />
that ignition system, airfuel<br />
mixture or<br />
(b) Check whether the idle speed is normal.<br />
Disconnect the injector connector.<br />
Remove the injector and fuel rail assy.<br />
Apply 12 V battery voltage to the injector directly.<br />
Check whether every injector can spray even and standard quantity gasline.<br />
(a) Check the exhaust system and Three-Way Catalytic Converter (TWC).<br />
13. CHECK ENGINE VALVE-TIMING<br />
(a) Check whether the engine valve-timing gear mark is aligned, damaged. And the belt is loose.<br />
abnormal air-fuel ratio, poor<br />
DIAGNOSTICS(RHD) - ANTI-LOCK BRAKE SYSTEM<br />
(a) Before removing or installing any electrical device, please disconnect the negative cable to prevent<br />
(b) Make sure ignition switch is OFF if no specific instructions.<br />
5. NOTES ABOUT ANTI-LOCK BRAKE SYSTEM.<br />
(d) After repairing the anti-lock brake system is completed, check the ABS warning light.<br />
(e) Never use the multimeter to measure the terminal of ABS module.<br />
(f) The ABS system must be repaired by technicians trained and mastered maintenance skills, and only<br />
use original parts for replacement.<br />
(g) Before repairing the ABS system, if there are some failures with mechanical braking system, must be<br />
excluded. Such as:<br />
(h) ABS control module (refer to the ABS electronic control unit and hydraulic control unit, not including<br />
brake lines, sensors ,etc.) can only be replaced as assembly, can not be overhauled or part<br />
replacement / swap.<br />
(i) The following two cases show that ABS system failure is detected:<br />
• Turn the ignition switch On, the system self-test is completed, but the warning light is on.<br />
The driver can stop the vehicle conventionally, but it should be as far as possible to reduce the braking force to<br />
prevent the wheels from locking. Warning lamp lights need to be careful driving and immediately to the<br />
authorized service station overhaul to prevent more failures occurred, resulting in a traffic accident.<br />
(j) Pay attention to the following points when connect the ABS system connector:<br />
• ABS harness connector is installed in place, must be in the horizontal direction and a vertical direction<br />
to avoid damage to the connectors.<br />
(k) Ensure proper connection when connectiong the ABS system pipes. ABS control module can not<br />
detect that the brake lines are connected properly or not. The error connection may lead to a serious<br />
accident. Connecting the brake lines, must be in compliance with the ABS assembly on the mark:<br />
(l) There are noise with ABS system in the following cases:<br />
• Vehicle power or start the engine, it will produce a short sound of "Om", this is a normal phenomenon<br />
with the sound of the ABS self-check..<br />
• There will be sound when ABS system work properly, mainly reflected in the following:<br />
ABS solenoid valve power<br />
suppy input<br />
28 R - W ABS-IG input<br />
Rear sensor power suppy<br />
LH<br />
Front sensor power suppy<br />
Front Wheel Speed Sensor LH Output Signal Malfunction: Beyond The Scope Of Loss, Noise,<br />
Intermittent Interruption<br />
Front Wheel Speed Sensor RH Output Signal Malfunction: Beyond The Scope Of Loss, Noise,<br />
Rear Wheel Speed Sensor LH Output Signal Malfunction: Beyond The Scope Of Loss, Noise,<br />
Rear Wheel Speed Sensor RH Output Signal Malfunction: Beyond The Scope Of Loss, Noise,<br />
Wheel Speed Sensor Group Malfunction (Wheel Speed Sensor Interchangeable, Each Of The<br />
Wheel Speed Difference Is Too Large, Wheel Speed Sensors Fault)<br />
Chapter 04 diagnostics - anti-lock brake system,<br />
Before diagnosis of the ABS system, check the ABS system failure and easily accessible components first,<br />
visual inspection can quickly determine fault, and thus do not need to do further diagnosis.<br />
(a) Make sure that the vehicle only install the recommended<br />
size tires and wheels. coaxial style of tire tread depth<br />
must be the same. Specific tire models, refer to the<br />
vehicle owner's manual for details.<br />
2. CHECK THE ABS HYDRAULIC MODULATOR, BRAKE PIPES AND CONNECTIONS FOR<br />
LEAKING.<br />
3. CHECK ABS SYSTEM FUSES TO ENSURE THAT THE FUSES ARE NOT BURNED, AND THE<br />
MODEL IS CORRECT. ABS SYSTEM HAS THREE FUSES:<br />
4. CHECK THE BATTERY VOLTAGE, DETECT WHETHER THE BATTERY TERMINAL CORROSION<br />
OR LOOSE. ABS SYSTEM NORMAL OPERATING VOLTAGE RANGE IS 9.3V - 16.8V.<br />
(a) Check ABS grounding point is loose. The location is<br />
changed or not.<br />
(b) ABS ground has good sealing, in order to avoid water<br />
and moisture in capillary (siphon) effect through wiring<br />
harness of channel infiltration ABS control module, which<br />
cause function failure.<br />
ABS system harness and connectors of the related<br />
components are properly connected, to be pinched or cut<br />
or not.<br />
Harness routing is too close to high-voltage or highcurrent<br />
devices, such as high-voltage or parts,<br />
generators, motors or stereo amplifier.<br />
The high voltage or high current device may cause the<br />
circuit to generate the induced noise, and thereby interfere<br />
with the normal working of the circuit.<br />
(c) ABS parts are sensitive to electromagnetic interference<br />
(EMI). Suspected intermittent fault, check the<br />
aftermarket installation of anti-theft device, lights, or<br />
whether the mobile phone is not installed correctly.<br />
7. IF THE ABS NOISE IS TOO LARGE, IT MAY BE CAUSED BY THE FOLLOWING REASONS:<br />
(a) Loosening of ABS assembly with bracket.<br />
(b) Loosening of ABS bracket and body.<br />
(c) ABS plastic bracket washer missing or damaged.<br />
It will be caused failure by one of the following conditions are met when the supply voltage of the ECU:<br />
(3) Voltage is between 7.7V to 9.2V when vehicle speed is higher than 6km / h.<br />
1. PERFORM PRE-CHECK STEPS<br />
(b) Measure the battery voltage.<br />
3. ABS CONTROL MODULE CROSS-VALIDATION<br />
(b) Remove the ABS actuator. (Refer to “Chapter 35 brake - abs actuator, replacement”)<br />
(c) Install the removed ABS to another known vehicle with the same model. (Ensure that ABS connectors<br />
are securely installed without connecting pipes when vehicle was driven. )<br />
(d) Start the engine and to ensure that the vehicle speed is not lower than 20km / h, so that the ABS<br />
dynamic self-check.<br />
C001004; C001104; C001404; C001504; C001804; C001904; C001C04; C001D04; C109504; C007208<br />
(3) Overheating protection (Solenoid valve long working hours, common in vacuum filling and offline detection)<br />
(c) Vehicle was allowed to stand for 5 minutes.<br />
(d) Connect the negative battery cable.<br />
2. PERFORM PRE-CHECK STEPS<br />
(a) Selecte diagnostic mode in the disgnostic tool and read data stream.<br />
(b) Detect vehicle speed displayed on the instrument panel and diagnostic tool when vehicle is running,<br />
and compare whether they are consistent.<br />
Inspect the ABS valve fuse in battery compartment<br />
junction box (Z048): 25 A.<br />
Inspect the ABS IG fuse in battery compartment junction<br />
box (Z048): 5 A.<br />
5. ABS CONTROL MODULE CROSS-VALIDATION<br />
are securely installed without connecting pipes when vehicle was driven.)<br />
dynamic self-check<br />
6. CHECK HARNESS AND CONNECTOR (ABS VALVE FUSE- GROUND)<br />
Disconnect the Z062 ABS module connector.<br />
ABS IG fuse - Z062 (28)<br />
ABS valve fuse - Z062 (25)<br />
(2) Reflux pump motor relay work over 60ms, reflux pump monitoring is still not detected voltage signal.<br />
(3) Reflux pump motor relay did not work, reflow pump monitoring detected voltage exceeds 2.5s.<br />
(4) Reflux pump motor relay stops working and the reflux pump monitoring detected voltage does not drop.<br />
Detect vehicle speed displayed on the instrument panel and diagnostic tool when vehicle is running,<br />
(b) Inspect the ABS pump fusible link in battery<br />
compartment junction box (Z048): 40 A.<br />
6. CHECK HARNESS AND CONNECTOR (ABS PUMP FUSIBLE LINK- GROUND)<br />
ABS valve fuse - Z062 (1)<br />
Disconnect the Z059 front wheel speed sensor connector LH.<br />
Z059 (1) - Ground<br />
Z059 (2) - Ground<br />
Z059 (1) - Z062 (8)<br />
Z059 (2) - Z062 (19)<br />
(1) ECU detects wheel speed sensor signal circuit is shorted to power supply.<br />
(2) ECU detects wheel speed sensor power supply circuit is shorted to ground.<br />
(3) Wheel speed sensor signal is not normal.<br />
(2) Wheel speed sensor signal circuit is shorted to power supply.<br />
(3) Wheel speed sensor power supply is shorted to ground.<br />
(4) The ring gear is not installed, missing teeth, dirty dust and installed incorrectly.<br />
(5) The gap between the sensor and the ring is too large.<br />
(6) The wheel speed sensor is subjected to the external magnetic field interference. (Wheel or axle is not<br />
demagnetization)<br />
(7) The wheel speed sensor fault.<br />
(8) The number of teeth of the ring gear error.<br />
(9) Tire size does not meet specifications<br />
(10) ECU is damaged.<br />
Inspect whether the ABS speed sensor installation is<br />
Inspect whether the ABS speed sensor connector is<br />
loose or not.<br />
Inspect whether the ABS speed sensor tightening bolt is<br />
Remove ABS speed sensor to inspect whether the<br />
speed sensor is damaged or the surface is dirty.<br />
Position the front wheel speed sensor RH properly.<br />
Check wheel speed sensor tip.<br />
If foreign object is attached, remove it. After reassembling,<br />
check the output voltage.<br />
Disconnect the Z059 front wheel speed sensor connector.<br />
6. ABS CONTROL MODULE CROSS-VALIDATION<br />
7. CHECK HARNESS AND CONNECTOR (ABS MODULE- GROUND)<br />
Z062 (13) - Ground<br />
Z062 (38) - Ground<br />
(c) Inspect the ABS pump fusible link in battery<br />
Inspect the stop lamp switch fuse in engine room junction<br />
box (Z063): 15 A.<br />
2. INSPECT BACK-UP LAMP SWITCH<br />
Disconnect the Z006 stop lamp switch connector.<br />
3. CHECK HARNESS AND CONNECTOR (ABS MODULE- GROUND)<br />
Stop lamp fuse - Z006 (2)<br />
Z062 (30) - Z006 (1)<br />
DIAGNOSTICS(RHD) - SUPPLEMENTAL RESTRAINT SYSTEM<br />
8101 - POWER SUPPLY VOLTAGE HIGH<br />
1. INSPECT FUSE (Co - pilot Side Junction Box)<br />
2. CHECK HARNESS AND CONNECTOR (AIRBAG FUSE - RESTRAINT CONTROL MODULE)<br />
Disconnect the Z044 restraint control module connector.<br />
Z044 (5) - Ground<br />
Disconnect the Z012 clock spring connector.<br />
Z044 (10) - Z012 (3)<br />
Z044 (11) - Z012 (4)<br />
Z012 (3) - Ground<br />
Z012 (4) - Ground<br />
Z044 (10) - Ground<br />
Z044 (11) - Ground<br />
Disconnet the Z040 passenger airbag connector.<br />
Z044 (13) - Z040 (1)<br />
Z044 (14) - Z040 (2)<br />
Z040 (1) - Ground<br />
Z040 (2) - Ground<br />
Z044 (13) - Ground<br />
Z044 (14) - Ground<br />
Disconnect the Z002 instrument B connector.<br />
Z044 (7) - Ground<br />
Disconnect the Z003 instrument A connector.<br />
Z002 (B27) - Z044 (7)<br />
Replace instrument cluster,and keep the Z002 instrument connector disconnecting.<br />
Connect Pin B27 of the Z002 instrument B connector to ground.<br />
DIAGNOSTICS(RHD) - HEATER AND AIR CONDITIONING SYSTEM<br />
8. DO NOT DEPOSIT REFRIGERANT IN AN ENCLOSED AREA OR NEAR AN OPEN FLAME.<br />
9. ALWAYS WEAR SAFETY GOGGLES.<br />
10. AVOID CONTACTING WITH LIQUID REFRIGERANT R-134A.<br />
11. DO NOT HEAT CONTAINER OR EXPOSE THE CONTAINER TO OPEN FLAME.<br />
12. DO NOT DROP DOWN CONTAINER OR APPLY PHYSICAL SHOCKS TO IT.<br />
13. DO NOT OPERATE COMPRESSOR WITHOUT ENOUGH REFRIGERANT IN REFRIGERANT<br />
(a) If there is not enough refrigerant in the A/C system, oil lubrication will be insufficient and the<br />
compressor may be damaged.<br />
14. DO NOT OPEN HIGH PRESSURE MANIFOLD VALVE WHILE COMPRESSOR IS OPERATING.<br />
15. BE CAREFUL NOT TO OVERCHARGE SYSTEM WITH REFRIGERANT.<br />
16. DO NOT OPERATE ENGINE AND COMPRESSOR WITH NO REFRIGERANT.<br />
17. EXPRESSIONS OF IGNITION SWITCH.<br />
conditioning - multi-media and A/C<br />
Inspect the A/C fuse (15 A) in driver side junction box<br />
(Z043).<br />
Junction Box (Z043).<br />
(b) Disconnect the Z020 front blower control module connector.<br />
(c) Replace the front blower control module with a new one.<br />
(b) Disconnect the Z019 front blower motor connector.<br />
Disconnect the Z019 front blower motor connector.<br />
Front blower relay (30) - Z019 (1)<br />
Disconnect the Z019 front blower connector.<br />
Disconnect the Z020 front blower control module connector.<br />
Z019 (2) - Z020 (4)<br />
Disconnect the Z020 blower control module connector.<br />
Z020 (8) - Ground<br />
Disconnect the Z017 A/C control panel connector.<br />
Z020 (2) - Z017 (35)<br />
Z020 (3) - Z017 (28)<br />
Disconnect the Z023 A/C control panel connector.<br />
Front blower relay (86) - Z023 (8)<br />
Z023 (10) - Ground<br />
Z023 (19) - Ground<br />
Z023 (18) - Ground<br />
Z023 (20) - Ground<br />
YES > Replace A/C control panel ( Multi-media and A/C controller assy).<br />
(c) Replace the front blower control moduler with a new one.<br />
2. CHECK HARNESS AND CONNECTOR (FRONT BLOWER - FRONT BLOWER CONTROL<br />
Z020 (1) - Ground<br />
table below..<br />
Disconnect the V031 triple pressure switch connector.<br />
(c) Inspect the triple pressure switch according to the<br />
V031 (1) - V031 (4)<br />
V031 (2) - V031 (3)<br />
V031 (4) - E001 (79)<br />
V031 (3) - E001 (26)<br />
V031 (4) - A036 (27)<br />
V031 (3) - A036 (11)<br />
V031 (2) - Z023 (9)<br />
V031 (2) - Ground<br />
V031 (2) - A036 (29)<br />
Disconnect the Z039front evaporator thermistor connector.<br />
Z039(1) - Z017 (29)<br />
Z039(2) - Z017 (33)<br />
Inspect the rear heater fuse (15A) in Co-pilot Junction<br />
Box (Z043).<br />
Disconnect the Z047 rear heater blower switch connector.<br />
Z047 (2) - Rear heater relay (86)<br />
Z047 (2) - Water valve relay (86)<br />
Z047 (3) - Ground<br />
Z047 (1) - Ground<br />
P002 (4) - Z047 (4)<br />
P002 (1) - Z047 (5)<br />
P002 (3) - Z047 (6)<br />
DIAGNOSTICS(RHD) - LIGHTING SYSTEM<br />
Disconnect the V020 headlamp LH connector.<br />
Lo - beam LH fuse (7.5A) - V020 (3)<br />
V020 (3) - Ground<br />
YES > Replace Lo - beam LH fuse (7.5A) in co-pilot side junction box (Z043).<br />
Disconnect the V022 headlamp RH connector.<br />
Remove lo - beam relay in co-pilot side junction box (Z043).<br />
terminals 86 and 85<br />
86 - 85 breakover<br />
87 - 30<br />
Disconnect the Z011 combination switch (light) connector.<br />
Lo - beam Relay (85) - Z011 (10)<br />
Lo - beam fuse RH (7.5A) - V022 (3)<br />
V022 (3) - Ground<br />
YES > Replace lo - beam headlamp fuse (7.5A) both LH and RH in driver side fuse box (Z043).<br />
Hi - beam LH fuse (10A) - V020(2)<br />
V020 (2) - Ground<br />
YES > Replace Hi - beam LH Fuse(10A) in co-pilot side junction box (Z043).<br />
Inspect the headlamp fuse (20A) in co-pilot side junction<br />
box (Z043).<br />
3. INSPECT HI - BEAM RELAY<br />
Remove hi - beam relay in co-pilot side junction box (Z043).<br />
Inspect Hi - beamheadlamp relay according to the<br />
9 - 7<br />
5. CHECK HARNESS AND CONNECTOR (HI - BEAM RELAY - COMBINATION SWITCH (LIGHT))<br />
hi - beam relay (86) - Z043 (9)<br />
6. CHECK HARNESS AND CONNECTOR (HI - BEAM FUSES BOTH LH AND RH, HI - BEAM<br />
(d) Measure the resistance according to the value(s) in the<br />
Hi - beam LH fuse (10A) - V020 (2)<br />
Hi - beam RH fuse (10A) - V022 (2)<br />
V022 (2) - Ground<br />
YES > Replace hi - beam fuses both LH and RH in driver side box (Z043).<br />
V020 (1) - Ground<br />
Hi - beam LH fuse (10 A) - V020 (2)<br />
Lo - beam LH fuse (7.5 A) - V020 (3)<br />
YES > Replace hi - beam fuse and lo - beam fuse LH in co-pilot side junction box (Z043).<br />
1. CHECK HARNESS AND CONNECTOR (COMBINATION SWITCH (LIGHT) - GROUND)<br />
Z011 (11) - Ground<br />
2. INSPECT COMBINATION SWITCH (LIGHT)<br />
10 - 7<br />
3. INSPECT HEADLAMP BULBS BOTH LH AND RH<br />
4. CHECK HARNESS AND CONNECTOR (HEADLAMP BOTH LH AND RH - GROUND)<br />
V022 (1) - Ground<br />
5. INSPECT HI - BEAM RELAY AND LO - BEAM RELAY<br />
86 - 85 Breakover<br />
6. CHECK HARNESS AND CONNECTOR (HI - BEAM RELAY AND LO - BEAM RELAY -<br />
Hi - beam relay (86) - Z011 (9)<br />
Lo - beam relay (85) - Z011 (10)<br />
7. CHECK HARNESS AND CONNECTOR (HI - BEAM FUSE AND LO - BEAM FUSE BOTH LH AND<br />
Lo - beam RH fuse (7.5A) - V022 (3)<br />
8. INSPECT FUSE<br />
YES > Replace hi - beam fuse (10A) and lo - beam fuse (7.5A) both LH and RH in the co-pilot side junction<br />
NO > Replace headlamp fuse (20A) and lo - beam fuse (7.5A) both LH and RH in the co-pilot side junction<br />
Inspect front fog lamp fuse (15 A) in co-pilot side junction<br />
Remove front fog relay in co-pilot side junction box (Z043).<br />
Disconnect the Z003 instrument cluster A connector.<br />
Disconnect the Z011 combination switch connector.<br />
3 - 1 < 2 Ω<br />
3 - 1 ≥ 1 MΩ<br />
Remove front fog lamp relay in co-pilot side junction box (Z043).<br />
Front fog lamp relay (86) - Z011 (3)<br />
Z011 (3) - Ground<br />
(b) Remove front fog lamp relay in co-pilot side junction box (Z043).<br />
Inspect rear fog lamp fuse (10A) in co-pilot side junction<br />
Remove rear fog lamp relay in co-pilot side junction box (Z043).<br />
Disconnect the F012 rear combination lamp LH connector.<br />
Disconnect the G004 rear combination lamp RH connector.<br />
Disconnect the Z002 instrument cluster B connector.<br />
F012 (5) - Ground<br />
2 - 1 < 2 Ω<br />
2 - 1 ≥ 1 MΩ<br />
Rear fog lamp relay (86) - Z011 (2)<br />
F012 (2) - Ground<br />
G004 (2) - Ground<br />
Rear fog lamp relay (87) - F012 (5)<br />
Rear fog lamp relay (87) - G004 (5)<br />
Z011 (2) - Ground<br />
(b) Remove rear fog lamp relay in co-pilot side junction box (Z043).<br />
Inspect the front fog lamp fuse (15 A) in co-pilot side<br />
junction box (Z043).<br />
Inspect the rear fog lamp fuse (10 A) in co-pilot side<br />
Z011 (1) - Ground<br />
3 - 1<br />
2 - 1<br />
Remove rear fog relay in co-pilot side junction box (Z043).<br />
Inspect the hazard warning fuse (15A) in co-pilot side<br />
2. CHECK HARNESS AND CONNECTOR (HAZARD WARNING FUSE - FLASHER)<br />
Disconnect the Z007 flasher connector.<br />
Z007(1) - Ground<br />
3. CHECK HARNESS AND CONNECTOR (FLASHER - HAZARD WARNING SWITCH)<br />
Disconnect the Z034 hazard warning switch connector.<br />
Z007 (7) - Z034 (8)<br />
4. CHECK HARNESS AND CONNECTOR (HAZARD WARNING FUSE - FLASHER)<br />
Hazard warning fuse (15A) - Z007 (1)<br />
5. CHECK HARNESS AND CONNECTOR (HAZARD WARNING SWITCH - GROUND)<br />
Z034 (7) - Ground<br />
6. INSPECT HAZARD WARNING SWITCH<br />
YES > Replace the flasher.<br />
Inspect the turn signal fuse (10A) in co-pilot side junction<br />
2. CHECK HARNESS AND CONNECTOR (TURN SIGNAL FUSE - COMBINATION SWITCH (TURN<br />
SIGNAL SWITCH))<br />
Disconnect the Z011 combination switch (turn signal switch) connector.<br />
Z011 (12) - Ground<br />
3. CHECK HARNESS AND CONNECTOR (COMBINATION SWITCH (TURN SIGNAL SWITCH) - FLASHER)<br />
Z007 (12) - Ground<br />
Z007 (5) - Ground<br />
4. INSPECT COMBINATION SWITCH (TURN SIGNAL SWITCH)<br />
12 - 11<br />
12 - 13<br />
5. CHECK HARNESS AND CONNECTOR (TURN SIGNAL FUSE - COMBINATION SWITCH (TURN SIGNAL<br />
SWITCH))<br />
Turn signal fuse (10A) - Z011 (12)<br />
6. CHECK HARNESS AND CONNECTOR (FLASHER - COMBINATION SWITCH (TURN SIGNAL SWITCH))<br />
Z007 (5) - Z011 (11)<br />
Z007 (12) - Z011 (13)<br />
3. CHECK HARNESS AND CONNECTOR (TURN SIGNAL FUSE - COMBINATION SWITCH (TURN<br />
4. CHECK HARNESS AND CONNECTOR (COMBINATION SWITCH (TURN SIGNAL SWITCH) - FLASHER)<br />
5. CHECK HARNESS AND CONNECTOR (FLASHER - GROUND)<br />
Z007 (8) - Ground<br />
6. INSPECT FLASHER<br />
7. INSPECT HAZARD WARNING SWITCH<br />
NO > Relace hazard warning switch,and go to step 11.<br />
8. CHECK HARNESS AND CONNECTOR (HAZARD WARNING SWITCH - FLASHER)<br />
Z034 (8) - Z007 (7)<br />
NO > Repair or replace harness or connector, and go to step 11.<br />
9. CHECK HARNESS AND CONNECTOR (HAZARD WARNING SWITCH - GROUND)<br />
NO > Repair or replace harness or connector,and go to step 11.<br />
10. CHECK HARNESS AND CONNECTOR (HAZARD WARNING FUSE - FLASHER)<br />
11. CHECK HARNESS AND CONNECTOR (TURN SIGNAL FUSE - COMBINATION SWITCH (TURN SIGNAL<br />
12. CHECK HARNESS AND CONNECTOR (FLASHER - COMBINATION SWITCH (TURN SIGNAL SWITCH))<br />
YES > Replace the combination switch (turn signal switch) .<br />
13. CHECK HARNESS AND CONNECTOR (TURN SIGNAL LAMP - GROUND)<br />
Disconnect the V021 front turn signal lamp LH connector.<br />
Disconnect the V025 front turn signal lamp RH connector.<br />
V021 (1) - Ground<br />
V025 (1) - Ground<br />
Z007 (4) - V021 (2)<br />
Z007 (9) - F012 (4)<br />
Z007 (10) - V025 (2)<br />
Z007 (2) - G004 (4)<br />
Disconnect the Z011 combination switch(turn signal lamp) connector.<br />
• If only turn signal lamps LH is not bright,measure 12<br />
- 11.<br />
• If only turn signal lamps RH is not bright,measure 12<br />
- 13.<br />
2. CHECK HARNESS AND CONNECTOR (FLASHER - COMBINATION SWITCH (TURN SIGNAL SWITCH))<br />
3. INSPECT FLASHER<br />
4. CHECK HARNESS AND CONNECTOR (FLASHER - TURN SIGNAL LAMP)<br />
(b) Disconnect the Z007 flasher connector.<br />
(c) Disconnect the V021 front turn signal lamp LH connector.<br />
(d) Disconnect the F012 rear combination lamp LH connector.<br />
Z007 (4) - V021 (2) only.<br />
Z007 (9) - F012 (4) only.<br />
5. CHECK HARNESS AND CONNECTOR (TURN SIGNAL LAMP - GROUND)<br />
V021 (1) - Ground only.<br />
F012 (2) - Ground only.<br />
7 - 8 ≥ 1 MΩ<br />
2. CHECK HARNESS AND CONNECTOR (HAZARD WARNING SWITCH - FLASHER)<br />
Z034 (8) - Ground<br />
3. CHECK HARNESS AND CONNECTOR (FLASHER - TURN SIGNAL LAMP)<br />
Connect the battery negative cable,check the wire harness for shot to power supply, hazard warning<br />
lamp is shoud not be bright.<br />
box(Z063).<br />
Z006 (2) - Ground<br />
F012 (3) - Ground<br />
Stop lamp fuse (15A) - Z006 (2)<br />
Z006(1) - F012 (3)<br />
Z006(1) - G004(3)<br />
Z006(1) - U002 (2)<br />
Z006 (1) - F012 (3)<br />
Z006 (1) - U002 (2)<br />
Disconnect the Z056 back - up lamp switch connector.<br />
Z056 (2) - F012 (6)<br />
Inspect the back - up lamp fuse (10A) in co-pilot side<br />
Z056 (1) - Ground<br />
F012 (6) - Ground<br />
Back - up lamp (10A) - Z056<br />
Z056 (2) - G004 (6)<br />
Disconnect the Z014 ignition switch illumination connector.<br />
Dome light fuse (10A) - Z014 (1)<br />
Disconnect the Z008 central locking controller assy connector.<br />
Z014 (2) - Z008 (B1)<br />
Z008 (B10) - Ground<br />
Disconnect the F010 central dome light connector.<br />
Dome light fuse (10A) - F010 (1)<br />
(b) Disconnect the F010 central dome light connector.<br />
(c) Disconnect the F014 middle door lamp switch RH connector.<br />
Disconnect the Z031 dome light switch connector.<br />
F010 (3) - Z031 (5)<br />
F010 (2) - F014 (1)<br />
F010 (2) - Z031 (5)<br />
Z031 (2) - Ground<br />
Disconnect the F011 air purifier connector.<br />
Dome light fuse (10A) - F011 (1)<br />
Disconnect the F014 middle door lamp switch RH connector.<br />
F011 (3) - Z031 (5)<br />
F011 (2) - F014 (1)<br />
Disconnect the Z055 step lamp connector.<br />
dome light fuse (10A) - Z055 (1)<br />
Z055 (2) - F014 (1)<br />
Disconnect the F009 front dome light connector.<br />
Dome light fuse (10A) - F009 (1)<br />
Dome light fuse (10A) - F009 (2)<br />
DIODE RH,FRONT DOOR LAMP SWITCH RH,INSTRUMENT CLUSTER)<br />
Disconnect the Z073 front door lamp diode RH connector.<br />
Disconnect the Z046 front door lamp switch LH connector.<br />
F009 (4) - Z073 (1)<br />
F009 (4) - Z046 (1)<br />
F009 (4) - Z003 (A30)<br />
F009 (3) - Ground<br />
Remove lamplet relay in co-pilot side junction box (Z043).<br />
87 - 30 < 2 Ω<br />
remove lamplet relay in co-pilot side junction box (Z043).<br />
Lamplet relay (86) - Z011 (5)<br />
Z011 (8) - Ground<br />
inspect lamplet fuse (7.5A) in co-pilot side junction box<br />
inspect switch lighting fuse (7.5A) in co-pilot side junction<br />
Z003 (A6) - Ground<br />
Disconnect the Z033 headlamp dimmer switch connector.<br />
Disconnect the Z032 instrument dimmer switch connector.<br />
Disconnect the Z024 outside mirror defroster switch connector.<br />
Disconnect the Z022 rear blower forward switch connector.<br />
Disconnect the Z030 cigarette lighter connector.<br />
Disconnect the Z025 radio A connector.<br />
Disconnect the Z017 A/C control panel B connector.<br />
Disconnect the Z029 diagnosis switch connector.<br />
Z034 (2) - Ground<br />
Inspect lamplet fuse (7.5A) in co-pilot side junction box<br />
Z003 (A19) - Ground<br />
Lamplet fuse (7.5A) - Z003<br />
(A6)<br />
Z029 (1) - Ground<br />
Switch lighting fuse (7.5A) - Z029 (3)<br />
Z030 (1) - Ground<br />
Switch lighting fuse (7.5A) - Z030 (3)<br />
Disconnect the Z023 A/C control panel A connector.<br />
Switch lighting fuse (7.5A) - Z017 (32)<br />
Z025 (A8) - Ground<br />
Switch lighting fuse (7.5A) - Z025 (A3)<br />
Z022 (1) - Ground<br />
Switch lighting fuse (7.5A) - Z022 (3)<br />
Z031 (1) - Ground<br />
Switch lighting fuse (7.5A) - Z031 (3)<br />
Z024 (1) - Ground<br />
Switch lighting fuse (7.5A) - Z024 (3)<br />
Z033 (6) - Ground<br />
Switch lighting fuse (7.5A) - Z033 (3)<br />
Z032 (6) - Ground<br />
Switch lighting fuse (7.5A) - Z032 (3)<br />
Z034 (3) - Ground<br />
Switch lighting fuse (7.5A) - Z034 (2)<br />
(b) Disconnect the V019 front position lamp LH connector.<br />
(c) Disconnect the V024 front position lamp RH connector.<br />
V019 (1) - Ground<br />
V024 (1) - Ground<br />
• If only width lamp LH is not bright,measure V019 (1) -<br />
• If only width lamp RH is not bright,measure V024 (1) -<br />
Lamplet fuse (7.5A) - V019 (2)<br />
Lamplet fuse (7.5A) - V024 (2)<br />
fuse (7.5A) - V019 (2) only.<br />
fuse (7.5A) - V024 (2) only.<br />
(b) Disconnect the F012 rear combination lamp LH connector.<br />
(c) Disconnect the G004 rear combination lamp RH connector.<br />
• If only tail lamp LH is not bright, measure F012 (2) -<br />
• If only tail lamp RH is not bright,measure G004 (2) -<br />
Lamplet fuse (7.5A) - F012 (1)<br />
Lamplet fuse (7.5A) - G004 (1)<br />
Fuse (7.5A) - F012 (1) only.<br />
Fuse (7.5A) - G004 (1) only.<br />
Inspect the lamplet fuse (7.5A) in co-pilot side junction<br />
Disconnect the V019 front position lamp LH connector.<br />
Disconnect the V024 front position lamp RH connector.<br />
V019 (2) - Ground<br />
Remove the lamplet relay in co-pilot side junction box (Z043).<br />
lamplet relay (86) - Z011 (5)<br />
DIAGNOSTICS(RHD) - WIPER AND WASHER<br />
1. EXPRESSIONS OF IGNITION SWITCH<br />
2. POWER OFF<br />
(a) Before removing or installing any electrical device, please disconnect the nagative battery cable to<br />
Does the wiper motor operate in high<br />
Does the wiper motor operate in low<br />
Does the wiper motor operate in<br />
intermittent mode?<br />
box (Z043): 15 A.<br />
NO > If the fuse blows,check the line to normal after replacing the fuse.<br />
Disconnect the V030 windshield wiper assy connector.<br />
Front wiper fuse - V030(3)<br />
Disconnect the Z013 combination switch (wiper and washer control) connector.<br />
Front wiper fuse - Z013 (3)<br />
Disconnect the V028 front washing reservoir motor connector.<br />
Front wiper fuse - V028 (2)<br />
5. CHECK HARNESS AND CONNECTOR (WINDSHIELD WIPER - GROUND)<br />
Disconnect the V030 windshield wiper connector.<br />
V030(6) - Ground<br />
6. CHECK HARNESS AND CONNECTOR (COMBINATION SWITCH - WINDSHIELD WIPER)<br />
Disconnect the Z013 combination switch connector.<br />
Z013(4) - V030(1)<br />
Z013(2) - V030(4)<br />
Z013(5) - V030(2)<br />
7. INSPECT WINDSHIELD WIPER<br />
Inspect the windshield wiper.<br />
Windshield wiper lowspeed<br />
operation<br />
Windshield wiper highspeed<br />
Motor does not<br />
8. CHECK HARNESS AND CONNECTOR (COMBINATION SWITCH - GROUND)<br />
Z013(6) - Ground<br />
(c) Inspect combination switch (wiper and washer control)<br />
V030(1) - Z013(4)<br />
YES > Check windshield wiper, replace windshield wiper if necessary.<br />
2 - 3 ≥ 1 MΩ<br />
2 - 3 < 2 Ω<br />
(d) Measure the resisitance according to the value(s) in the<br />
Z013 (2) - V030(4)<br />
(c) Inspect the windshield wiper in INT mode.<br />
2 and 5<br />
Battery(+) - 2<br />
Battery(-) - Ground<br />
Z013 (6) - Ground<br />
3. CHECK HARNESS AND CONNECTOR (WINDSHIELD WIPER- GROUND)<br />
V030 (5) - Ground<br />
Z013 (5) - V030 (2)<br />
Z013 (4) - V030 (1)<br />
6 - 7 ≥ 1 MΩ<br />
6 - 7 < 2 Ω<br />
2. CHECK HARNESS AND CONNECTOR (DRIVER SIDE JUNCTION CONNECTOR - FRONT<br />
WASHER PUMP)<br />
Disconnect the V028 front washer pump connector.<br />
3. CHECK HARNESS AND CONNECTOR (COMBINATION SWITCH - FRONT WASHER PUMP)<br />
V028 (1) - Z013 (7)<br />
4. CHECK HARNESS AND CONNECTOR (COMBINATION SWITCH - GROUND)<br />
YES > Check the front washer pump, replace the front washer pump if necessary.<br />
switch to other position<br />
3. CHECK HARNESS AND CONNECTOR ( COMBINATION SWITCH - WINDSHIELD WIPER)<br />
V030(2) - Z013 (5)<br />
(Z043): 10 A.<br />
NO > If the fuse blows, check the line to normal after replacing the fuse<br />
9 - 6 ≥ 1 MΩ<br />
9 - 6 < 2 Ω<br />
Rear wiper relay(85) - Z013 (9)<br />
Rear wiper relay(87) - U001 (2)<br />
Constant 85 - 86 90Ω<br />
Apply 12V voltage to<br />
6. CHECK HARNESS AND CONNECTOR (REAR WIPER RELAY - REAR WIPER)<br />
8. CHECK HARNESS AND CONNECTOR ( REAR WIPER - GROUND)<br />
YES > Check the rear wiper, Replace the rear wiper if necessary.<br />
NO > If the fuse blows, check the line to wiring after replacing the fuse.<br />
Disconnect the V029 rear washing reservoir motor connector.<br />
Rear wiper fuse (30)- V029 (2)<br />
Disconnect the Z043 rear wiper relay connector.<br />
Rear wiper relay (85) - Z013<br />
(9)<br />
6. CHECK HARNESS AND CONNECTOR ( REAR WASHING RESERVOIR MOTOR - COMBINATION<br />
V029(1) - Z013(8)<br />
DIAGNOSTICS(RHD) - AUDIO SYSTEM<br />
Check Radio ACC fuse (7.5 A) in junction box (Z043).<br />
Check Radio fuse (10 A) in junction box (Z043).<br />
(b) Disconnect the Z025 radio connector.<br />
Z025(A7) - Ground<br />
Z025 (A4) - Ground<br />
Radio fuse (10 A) - Z025 (A4)<br />
Radio ACC fuse(15 A) - Z025 (A4)<br />
H006 (1) - Z026 (B3)<br />
H006 (2) - Z026 (B4)<br />
D011 (1) - Z026(B5)<br />
D011 (2) - Z026(B6)<br />
G005 (2) - Z026 (B2)<br />
G005 (1) - Z026 (B1)<br />
F013(1) - Z026 (B7)<br />
F013 (2) - Z026 (B8)<br />
DIAGNOSTICS(RHD) - AUXILIARY POWER<br />
(Z043):Refer to “Circuit Guidance” document “the front<br />
passenger side fuse box” fuse F35.<br />
Z030 (2) - Ground<br />
Cigarette lighter fuse - Z030 (2)<br />
Inspect the IG2 fuse in body junction box (Z043):Refer to<br />
“Circuit Guidance” document “the front passenger side<br />
fuse box” fuse F19.<br />
(c) Inspect the power fuse in body junction box<br />
passenger side fuse box” fuse F49.<br />
NO > If the fuse blows, check the line to normal after replacing the fuse.<br />
Constant 85 - 86 90 Ω<br />
Apply 12V<br />
4. CHECK HARNESS AND CONNECTOR (POWER FUSE - 12V POWER SUPPLY OUTPUT SOCKET<br />
Disconnect Z018 12v power supply output socket.<br />
Power fuse (15A) - Z018(2)<br />
5. CHECK HARNESS AND CONNECTOR (12V POWER SUPPLY OUTPUT SOCKET FUSE - GRO-<br />
NUD)<br />
Z018(1) - Ground<br />
YES > Replace 12v power supply output socket.<br />
DIAGNOSTICS(RHD) - HORN SYSTEM<br />
(b) Inspect the horn fuse in body junction box (Z043):15 A.<br />
Disconnect the Z008 central locking controller B connector.<br />
Z008 (B4) - Horn relay(86)<br />
Horn relay (86) - Z012(2)<br />
Disconnect the V027 alt horn connector.<br />
Disconnect the V026 bass horn connector..<br />
Horn relay - V026(1)<br />
Horn relay - V027(1)<br />
Disconnect the V026 alt horn connector.<br />
V027(2) - Ground<br />
V026(2) - Ground<br />
(b) Replace the clock spring. (Refer to“Chapter 62<br />
Supplemental Restraint System - clock spring,<br />
replacement”)<br />
DIAGNOSTICS(RHD) - REVERSE RADAR SYSTEM<br />
Audio (multi-media and aircondition<br />
controler assy)<br />
Back-up lamp switch<br />
Sends the back-up signal to the reverse radar control unit.<br />
3. Back-up lamp switch<br />
distance (Back-up lamp is<br />
(Back-up lamp is normal)<br />
1. Displayer Chapter 81 communication system - multi-media<br />
and air-condition controler assy,replacement<br />
Inspect the back-up lamp fuse (10 A) in co-pilot side<br />
2. CHECK HARNESS AND CONNECTOR (BACK-UP LAMP FUSE - BACK-UP LAMP SWITCH)<br />
Disconnect the Z056 back-up lamp switch connector.<br />
Disconnect the Z042 reverse radar control unit connector.<br />
3. INSPECT BACK-UP LAMP SWITCH<br />
NO > Replace back-up lamp switch and fuse.<br />
4. CHECK HARNESS AND CONNECTOR (BACK-UP LAMP SWITCH - REVERSE RADAR CONTROL<br />
UNIT)<br />
Z056 (2) - Ground<br />
Z042 (16) - Ground<br />
6. INSPECT BACK-UP LAMP SWITCH<br />
Inspect the back-up lamp switch according to the<br />
NO > Replace back-up lamp.<br />
7. CHECK HARNESS AND CONNECTOR (BACK-UP LAMP FUSE - BACK-UP LAMP SWITCH)<br />
Back-up lamp fuse (10A) - Z056 (1)<br />
8. CHECK HARNESS AND CONNECTOR (BACK-UP LAMP SWITCH - REVERSE RADAR CONTROL<br />
Z056 (2) - Z042 (1)<br />
1. INSPECT BACK-UP LAMP SWITCH<br />
(c) Inspect the back-up lamp switch according to the<br />
NO > Replace back-up lamp switch.<br />
2. CHECK HARNESS AND CONNECTOR (BACK-UP LAMP SWITCH - REVERSE RADAR CONTROL<br />
Z042 (1) - Ground<br />
DISTANCE (BACK-UP LAMP IS NORMAL)<br />
Turn the ignition switch OFF.。<br />
Z042 (7) - R001 (1)<br />
Z042 (11) - R001 (2)<br />
Z042 (8) - R002 (1)<br />
Z042 (11) - R002 (2)<br />
Z042 (4) - R003 (1)<br />
Z042 (11) - R003 (2)<br />
Z042 (15) - R004 (1)<br />
Z042 (11) - R004 (2)<br />
1. CHECK HARNESS AND CONNECTOR (BACK-UP LAMP SWITCH - CAMERA)<br />
Z056 (2) - J005 (2)<br />
Disconnect the Z028 radio connector.<br />
J005 (3) - Z028 (1)<br />
J005 (4) - Z028 (2)<br />
DIAGNOSTICS(RHD) - POWER WINDOWS<br />
1 L - B Door control switch (date)<br />
2 L Door control switch (clock)<br />
3 L - Y Window control switch LH<br />
4 P - L Window control switch LH<br />
5 L - G Window control switch LH<br />
WINDOW CONTROL SWITCH LH PIN<br />
4 G Power window motor RH<br />
5 R Power window motor RH<br />
6 R - L Power window motor LH<br />
7 G - R Power window motor LH<br />
14 R Door-status<br />
Check power window motor LH.<br />
• Push or pull the front window switch RH to<br />
RH is inoperative.<br />
RH does not open.<br />
RH does not close.<br />
3. Window control switch LH<br />
LH is inoperative (use<br />
LH).<br />
1. Window control switch LH<br />
3. Power window motor LH<br />
side junction box (Z043).<br />
Disconnect the H010 door control switch connector.<br />
Disconnect the Z009 central locking controller assy A connector.<br />
H010 (12) - Ground<br />
Power window fusible link (20A) - H010 (12)<br />
Power window fusible link (20A) - Z009 (A8)<br />
H010 (6) - Ground<br />
7. CHECK HARNESS AND CONNECTOR (DOOR CONTROL SWITCH - CENTRAL LOCKING<br />
H010 (1)- Z009 (A15)<br />
H010 (2)- Z009 (A16)<br />
Disconnect the H007 power window motor LH connector.<br />
Disconnect the D007 power window motor RH connector.<br />
Disconnect the H007 power window motor RH connector.<br />
Disconnect the D007 power window motor LH connector.<br />
Z009 (A4) - H007 (2)<br />
Z009 (A5) - H007 (1)<br />
Z009 (A6) - D007 (2)<br />
Z009 (A7) - D007 (1)<br />
FRONT POWER WINDOW RH IS INOPERATIVE<br />
Does power window LH work correctly?<br />
Does power windou LH work correctly?<br />
YES > Replace power window motor LH.<br />
Disconnect the D009 window control switch LH connector.<br />
Replace window control switch LH.<br />
YES > Replace window control switch LH.<br />
2. CHECK HARNESS AND CONNECTOR (WINDOW CONTROL SWITCH LH - DOOR CONTROL SWITCH)<br />
D009 (1) - H010 (5)<br />
D009 (3) - H010 (4)<br />
D009 (4) - H010 (3)<br />
4. INSPECT POWER WINDOW MOTOR LH<br />
DIAGNOSTICS(RHD) - OUTSIDE MIRROR<br />
5 R - Y Outside Mirror-<br />
6 W -B Ground<br />
Inspect the radio & ACC fuse (10 A) in Co-pilot junction<br />
box(Z043).<br />
Remove the radio & ACC fuse.<br />
Disconnect the H009 outside mirror remote control switch connector.<br />
Radio & ACC fuse (10A) -<br />
H009 (4)<br />
H009 (6) - Ground<br />
Disconnect the D008 outside mirror connector.<br />
D008 (6) - H009 (7)<br />
D008 (4) - H009 (5)<br />
D008 (5) - H009 (1)<br />
DIAGNOSTICS(RHD) - OUTSIDE MIRROR DEFROSTER SYSTEM<br />
OUTSIDE MIRROR DEFROSTER SYSTEM<br />
The outside mirror defroster system consists of heating wires, switch, relay, fuse, indicator and wiring<br />
harness. The heating element is the electric heating wire which are integrated in both outside mirror<br />
glasses and defog the glasses quickly. The outside mirror defrost switch is integrated on the centre<br />
switch panel on the instrument panel. When the switch is pressed, the indicator lamp in the switch<br />
illuminates to indicate that the defroster is operating.<br />
OUTSIDE MIRROR DEFROSTER WIRING DIAGRAM<br />
Inspect the outside mirror defrost fuse (7.5 A) in Co-pilot<br />
Junction Box (Z043), refer to “HOW TO USE MANUAL”<br />
in WIRING chapter to identify the fuse.<br />
NO > If the outside mirror defrost fuse is blown, prior to replacing the fuse, inspect the wiring harness.<br />
2. INSPECT OUTSIDE MIRROR DEFROST RELAY<br />
Remove the outside mirror defrost relay (refer to “HOW TO USE MANUAL” in WIRING chapter to<br />
identify the relay).<br />
Disconnect the Z024 outside mirror defrost switch connector.<br />
4. CHECK HARNESS AND CONNECTOR (OUTSIDE MIRROR DEFROST SWITCH CONNECTOR -<br />
POWER SUPPLY)<br />
Z024 (2) - Ground<br />
5. CHECK HARNESS AND CONNECTOR (OUTSIDE MIRROR DEFROST RELAY - OUTSIDE<br />
MIRROR DEFROST SWITCH)<br />
Rear defrost relay (85) - Z024 (5)<br />
Turn ignition switch OFF..<br />
Turn ignition switch ON.<br />
Outside mirror defrost relay (30) - Ground<br />
7. CHECK HARNESS AND CONNECTOR (OUTSIDE MIRROR DEFROST RELAY - GROUND)<br />
8. CHECK HARNESS AND CONNECTOR (OUTSIDE MIRROR DEFROST RELAY - OUTSIDE<br />
MIRROR ASSY LH/RH )<br />
Disconnect the D008 outside mirror assy LH/ H008 outside mirror assy RH connector.<br />
Outside mirror defrost relay (87) - D008(3)<br />
Outside mirror defrost relay (87) - H008(3)<br />
9. CHECK HARNESS AND CONNECTOR (OUTSIDE MIRROR ASSY LH/RH - GROUND )<br />
D008(2) - Ground<br />
H008(2) - Ground<br />
DIAGNOSTICS(RHD) - INSTRUMENT CLUSTER<br />
engine coolant temperature is between -20 ℃ ~ 110 ℃ .<br />
Terminals No Wiring Color Description<br />
Z003<br />
Z002<br />
Do not perform basic inspection until engine temperature reaches the specified value. If on-road test is<br />
needed, must have at least two people to perform the test.<br />
• Connect hand-held tester, reading the engine<br />
• Connect hand-held tester, reading the vehicle<br />
(b) Disconnect the Z057 speedometer sensor connector.<br />
Z057 (1) - Ground<br />
Disconnect the Z003 instrument cluster connector.<br />
Disconnect the Z057 speedometer sensor connector.<br />
Z003 (A13) - Z057 (3)<br />
Install a new speedometer sensor.<br />
Z003 (A8) - E001(51)<br />
Z003 (A8) - Z072(E28)<br />
connector Z003, pin A8 and ground.<br />
Disconnect the Z067 fuel level sensor connector.<br />
Z067 pin 2 and pin 3.<br />
NO > Replace the fuel level sensor.。<br />
Z067 (2) - Ground<br />
Z067 (3) - Ground<br />
Disconnect the Z003 instrument cluster connectors.<br />
Disconnect the Z067 fuel level sensor connectors.<br />
Z003 (A23) - Z067 (3)<br />
Disconnect the Z002 instrument cluster connector.<br />
Z002 (B16) - E012 (1)<br />
Z002 (B16) - E037 (1)<br />
Disconnect the Z078 (4G69) / E036 (ISF2.8) engine oil pressure switch connector.<br />
Z078 (1) - Ground<br />
Z002 (B22) - Z078 (1)<br />
Z002 (B22) - E036 (1)<br />
Disconnect the Z070 the seat belt warning switch connector.<br />
Disconnect the Z070 seat belt warning switch connector.<br />
Z070 (1) - Ground<br />
Z070 (2) - Ground<br />
Z070 (1) - Z070 (2)<br />
Disconnect the Z070seat belt warning switch connector.<br />
Z003 (A31) - Z070 (1)<br />
Disconnect the Z045 parking brake switch connector.<br />
Disconnect the Z002 instrument cluster.<br />
Z045 (1) - Z002 (B6)<br />
Z045 (1) - Ground<br />
DIAGNOSTICS(RHD) - POWER DOOR LOCKS<br />
6 R - L Co-pilot Side Window Down Output<br />
7 G - R Co-pilot Side Window Up Output<br />
Inspect the central locking fuse (20 A) in driver side<br />
2. CHECK HARNESS AND CONNECTOR (CENTRAL LOCKING FUSE - CENTRAL LOCKING<br />
Disconnect the Z008 central locking controller assy B connector.<br />
Central locking fuse (20 A) - Z008 (B3)<br />
Z009 (A1) - Ground<br />
Disconnect the H011 front door lock assy LH connector.<br />
Z009 (A9) - H011 (9)<br />
Z009 (A10) - H011 (10)<br />
H011 (7) - Ground<br />
Disconnect the Z009 central locking controller assy connector.<br />
Remove the front door water-proof film LH.<br />
Disconnect the D010 front door lock assy LH connector.<br />
2. CHECK HARNESS AND CONNECTOR (CENTRAL LOCKING CONTROLLER ASSY - FRONT<br />
Z009 (A2) - D010 (4)<br />
Z009 (A3) - D010 (1)<br />
3. CHECK HARNESS AND CONNECTOR (CENTRAL LOCKING FUSE - CENTRAL LOCKING<br />
CONTROLLER ASSY )<br />
Disconnect the Z009 central locking controller assy B connector.<br />
central locking fuse (20 A) - Z008 (8)<br />
VEHICLE MAINTENANCE<br />
MAINTENANCE SCHEDULE............................................................. 05-1<br />
PRECAUTION.............................................................................. 05-1<br />
MAINTENANCE CONTENT AND SCHEDULE IN GENERAL<br />
CONDITION................................................................................. 05-3<br />
INSPECTION...................................................................................... 05-8<br />
CHECK THE ELECTRICAL SYSTEM WORKING<br />
CONDITION................................................................................. 05-8<br />
CHECK THE BATTERY............................................................... 05-9<br />
CHECK THE AIRBAG................................................................ 05-10<br />
CHECK SEAT BELT .................................................................. 05-11<br />
CHECK PARKING BRAKE, BRAKE PEDAL ............................. 05-13<br />
CHECK DOOR LIMIT, DOOR LOCK AND DOOR HINGE ........ 05-14<br />
CHECK AND CLEAN WINDSHIELD FLUME ............................ 05-16<br />
CHECK ENGINE COMPARTMENT PARTS.............................. 05-17<br />
CHECK TIMING BELT............................................................... 05-18<br />
CHECK ACCESSORY BELT..................................................... 05-20<br />
CHECK THE TIE ROD BALL HEAD AND DUST COVER......... 05-21<br />
CHECK AND TIGHTEN THE CHASSIS BOLT REFER<br />
TO THE PRESCRIBED TORQUE ............................................. 05-22<br />
CHECK HEADLIGHTS............................................................... 05-23<br />
CHECK WINDSHIELD WIPERS, CLEANING DEVICE ............. 05-24<br />
CHECK CHASSIS...................................................................... 05-26<br />
CHECK SUSPENSION COMPONENTS ................................... 05-27<br />
CHECK SUSPENSION BALL JOINT AND DUST COVER........ 05-28<br />
CHECK STEERING FLUID LEVEL............................................ 05-29<br />
CHECK BRAKING SYSTEM...................................................... 05-30<br />
CHECK THE BRAKE DISC, BRAKE DRUM AND BRAKE<br />
FRICTION PLATE...................................................................... 05-31<br />
CHECK TIRES........................................................................... 05-32<br />
CHECK EXHAUST SYSTEM..................................................... 05-33<br />
CHECK COOLANT LEVEL........................................................ 05-34<br />
CHECK THE ENGINE OIL LEVEL (4G69) ................................ 05-35<br />
CHECK THE ENGINE OIL LEVEL (ISF2.8)............................... 05-36<br />
REPLACEMENT............................................................................... 05-37<br />
REPLACE AIR FILTER ELEMENT............................................ 05-37<br />
REPLACE AIR CONDITIONER FILTER ELEMENT.................. 05-38<br />
REPLACE ENGINE OIL (4G69)................................................. 05-40<br />
REPLACE OIL FILTER (4G69).................................................. 05-42<br />
REPLACE ENGINE OIL (ISF2.8)............................................... 05-44<br />
REPLACE OIL FILTER (ISF2.8) ................................................ 05-46<br />
REPLACE SPARK PLUG (4G69) .............................................. 05-48<br />
REPLACE FUEL FILTER ASSEMBLY (4G69) .......................... 05-50<br />
REPLACE FUEL FILTER ELEMENT (ISF2.8)........................... 05-51<br />
REPLACE COOLANT................................................................ 05-52<br />
REPLACE BRAKE FLUID.......................................................... 05-54<br />
REPLACE GEARBOX LUBRICATING OIL................................ 05-56<br />
REPLACE REAR MAIN REDUCER GEAR OIL......................... 05-57<br />
REPLACEMENT ........................................................................ 05-57<br />
05<br />
VEHICLE MAINTENANCE -<br />
MAINTENANCE SCHEDULE<br />
VEHICLE PRECAUTION<br />
MAINTENANCE ATTENTION<br />
05-1<br />
1. SAFETY INFORMATION<br />
(a) Maintenance project preparation.<br />
• Operators shall wear labor insurance shoes, working gloves, goggles, etc if necessary.<br />
• To ensure that the work site is ventilation and clean, tools and instruments are putted in good order,<br />
keep a fire extinguisher when needed.<br />
• Check the safety status of the instrument and equipment using, such as check lifting machine jack, etc.<br />
• Check the safety operation condition of the vehicle driving, ensure that the maintenance can be carried<br />
out smoothly.<br />
(b) Notes in the maintenance process.<br />
• Before driving into the Lift frame, ensure that there is enough distance between the vehicle bottom and<br />
sides with Lift frame, avoid scratch.<br />
• Before lifting the vehicle, ensure the vehicle weight does not exceed the lift rated load.<br />
• When lifting the vehicle, you should select the correct lifting point.<br />
• In the process of lifting vehicle, not allowed to start the engine and shift into gear when the driving<br />
wheel touches the ground. Otherwise the operator and vehicle are in danger.<br />
• Operator should strictly observe all safety rules and user rules in the maintenance process. Otherwise<br />
the operator and vehicle are in danger.<br />
• Replacement parts and consumption goods, to use the Beiqi <strong>Foton</strong> automobile Co. LTD. approved<br />
products, to ensure the safety and performance of the vehicle.<br />
(c) Notes after maintenance.<br />
• After the completion of maintenance, road test must be carried out. Special attention should be paid to<br />
the braking system and the occupant protection system inspection.<br />
• Vehicle should be cleared the failure messages in memory before transferred to the customer.<br />
2. PLANNING ISSUES<br />
(a) Planned maintenance interval, depends on the odometer or time interval, whichever comes first. Such<br />
as the schedule shows.<br />
(b) The next maintenance interval should be equal to the last maintenance interval.<br />
(c) Maintenance intervals of the various components refer to the maintenance schedule.<br />
(d) Some parts are particularly important in the maintenance objects. Hose if there is aging or damage<br />
should be replaced immediately. Please note, rubber hose is aging with time, this causing swelling,<br />
bruising or cracking.<br />
(e) Once the off-road passing through sand, mud or water, please check the following parts, and according<br />
to the conditions for maintenance or repair.<br />
• Brake pad and brake drum.<br />
• Brake pad and brake disc.<br />
• Brake pipeline and rubber hose.<br />
• Oil and working fluid used for transmission, transfer case and differential mechanism.<br />
• Air Filter elements.<br />
05-2 VEHICLE MAINTENANCE - MAINTENANCE SCHEDULE<br />
MAINTENANCE CONDITION<br />
1. IN DAILY CONDITIONS, THE VEHICLE NEEDS ACCORDING TO THE ORDINARY MAINTENANCE<br />
PERIOD TO THE IMPLEMENTATION OF THE MAINTENANCE.<br />
2. IF THE VEHICLE IS MAINLY IN THE FOLLOWING ANY ONE OR MORE SPECIAL CIRCUMSTANCES<br />
DRIVING, SOME OF THE PROJECTS MUST BE IMPLEMENTED MAINTENANCE MORE FREQUENTLY<br />
(REFER TO HARSH OPERATION CONDITION).<br />
Road condition:<br />
• Drive on rough, muddy or dissolve snow road.<br />
• Drive on dusty road.<br />
• Drive on saline road.<br />
(b) Driving condition:<br />
• Drag the tail car, use camping frame or roof supporter.<br />
• Repeat within 8 kilometers of the short-range travel, and temperatures below 0 ℃ .<br />
• Vehicle which long term to long distance running at idle or low speed, such as the police car, taxi or<br />
house-to-house delivery truck.<br />
• Often continuous running at very high speed over 2 hours (Traveling at a rate of 80% of the maximum<br />
speed)<br />
The Content Involves Behind “4g69” Is Gasoline Engine Code,"2.8”and “4jb1t” Are Diesel Engine<br />
Codes.<br />
05-3<br />
MAINTENANCE CONTENT AND SCHEDULE IN GENERAL CONDI-<br />
TION<br />
4G69 GASOLINE ENGINE REGULAR INSPECTION AND REPAIR PARTS LIST:<br />
The projects are made clear distance and time (by the month), Check whichever comes first.<br />
I: Inspection, correction, or necessary replacement; R: Replacement, handling or lubrication; L: Lubrication;<br />
Empty: N/A.<br />
Interval (The odometer reading and the number of months of whichever comes first)<br />
Month - 3 6 9 12 15 18 21 24 27 30 33 36 39 42 45 48<br />
Odometer<br />
reading ×1000<br />
km<br />
The internal inspection of the engine compartment<br />
Check belt for crack,<br />
flying chip, wear, and<br />
adjust its tension<br />
1 5 10 15 20 25 30 35 40 45 50 55 60 65 70 75 80<br />
I I I I I I I I I<br />
Engine timing belt R R R R R R R R<br />
Check the crankcase<br />
system is normal or not<br />
(Including the crankcase<br />
ventilation air filter<br />
element)<br />
I I I I<br />
Replace the spark plugs R R R R<br />
Check the radiator hoses<br />
for damage, correct<br />
connection<br />
Check the engine<br />
cooling fluid level<br />
Replace engine cooling<br />
fluid<br />
Check whether the air<br />
filter clogging or damage<br />
Other iinspection<br />
Chang<br />
e the<br />
oil<br />
e<br />
filter<br />
General<br />
Harsh<br />
I I I I I I I I<br />
I I I I I I I I I I I I I I I I<br />
5000 kilometers for the first time, since then every 5000 km or 3 month intervals<br />
The replacement mileage with general conditions of use<br />
Repla<br />
ce the<br />
Replace the air filter I I I R I I I R I I I R I I I R<br />
Check the engine idle<br />
05-4 VEHICLE MAINTENANCE - MAINTENANCE SCHEDULE<br />
ventilation hose<br />
ISF2.8 SERIES DIESEL ENGINE PARTS OF PERIODIC INSPECTION AND<br />
REPAIR LIST<br />
Odomete<br />
r reading<br />
×1000<br />
Check belt for crack, flying<br />
chip, wear, and adjust its<br />
tension<br />
Check the engine cooling<br />
fluid level<br />
I I I I I I I I I I I I I I I I I<br />
Check whether the air filter<br />
clogging or damage<br />
Other inspection<br />
Replace<br />
engine oil<br />
Replace oil<br />
diesel filter<br />
Replace air<br />
R Every 20,000 km or every 12 months<br />
R Every 10,000 km<br />
R 10,000 km for the first time, since then every 20,000 km or every 12 months<br />
R 5,000 km, since then every 10000 km or every 6 months<br />
Timing belt<br />
Change every 80,000 km (drain the cooling liquid before disassembly, must use E049377000009 locating bolt in<br />
Installation and adjustment, refer to maintenance manual)<br />
05-5<br />
4JB1T SERIES DIESEL ENGINE PARTS OF PERIODIC INSPECTION AND<br />
I: Check the fluid level, tighten or adjust, replace if necessary; R: replace or lubricate; Empty: N/A.<br />
Month — 3 6 9 12 15 18 21 24 27 30 33 36 39 42 45 48<br />
reading<br />
×1000 km<br />
tension.<br />
Replace engine timing belt<br />
R Every 100,000 km<br />
ventilation control system<br />
ventilation air filter element)<br />
I Every 5,000 km or every 3 months<br />
R Every 5,000 km or every 3 months<br />
The replacement mileage with general condition<br />
R 2,000 km, check for the first time, since then replace every 10,000 km<br />
R 5,000 km for the first time, since then every 10,000 km or every 6 months<br />
Check the engine idle I I I I I I I I I<br />
05-6 VEHICLE MAINTENANCE - MAINTENANCE SCHEDULE<br />
CHASSIS AND ELECTRICAL COMPONENTS OF PERIODIC INSPECTION AND<br />
I:Check the fluid level, tighten or adjust, replace if necessary; R:replace or lubricate; Empty: N/A.I ★:Inspection<br />
Chassis parts<br />
Brake pedal and hand<br />
brake<br />
Brake lining and brake<br />
drum<br />
Brake pipe and brake hose I I I I I I I I I<br />
Brake fluid (Including clutch<br />
oil)<br />
I I I I I I I I R I I I I I I I R<br />
Power steering fluid I I I I I I I I I I I I I I I I<br />
<strong>Manual</strong> transmission oil I I I R I I I R<br />
Main reducer and<br />
differential oil<br />
Steering wheel, steering<br />
linkage, steering<br />
I I I R I R<br />
Ball joint and dust cover I I I I I I I I I I I I I I I I<br />
Front and rear suspension<br />
Four wheel alignment I I I I<br />
Tire and pressure I I I I I I I I I I I I I I I I<br />
Drive shaft connected<br />
components<br />
Drive shaft sliding fork R R R R R R R R R R R R R R R R<br />
Wheel bearing and ball pin<br />
grease<br />
I R I R I R I R<br />
Exhaust pipe, silencer I I I I I I I I<br />
Electric system<br />
Light. horn I I I I I I I I I I I I I I I I<br />
Air conditioning system and<br />
refrigerant<br />
SSRS Airbag<br />
First inspection at 120 months after licensed, since than every 24 months<br />
Battery I I I I I I I I I I I I I I I<br />
Clutch pedal I I I I I I I I I I I I I I I I I<br />
Wheel nut<br />
Tighten the wheel nuts at the specified torque, check every 5,000 km or 1,000 km.<br />
HARSH CONDITION MAINTENANCE PERIODIC TABLE<br />
05-7<br />
According to the driving conditions listed in the following table, maintain the project which should<br />
be increase the maintenance frequency (project not listed refer to general condition maintenance<br />
periodic table).<br />
A-1:Driving on rough, muddy or dissolve snow sections<br />
□ Check the brake friction lining and<br />
□ Check the brake pads and brake disc<br />
□ Check the brake line and the hose<br />
□ Check the steering wheel, steering<br />
linkage and gear box oil<br />
□ Replace wheel bearing grease<br />
□ Check front and rear suspension<br />
Every 10,000 km or 6 months<br />
Every 5,000 km or 3 months<br />
The first 1, 000 km, then every 10, 000 km or 6 months<br />
Every 20,000 km or 12 months<br />
□ Tighten chassis and body connection<br />
bolt and nut<br />
A-2:Driving on much dust sections.<br />
□ Check the air filter element<br />
□ Check the brake linings and brake<br />
B-1:Vehicle which long term to long distance running at idle or low speed, such as the police<br />
car, taxi or house-to-house delivery truck<br />
B-2:Often continuous running at very high speed over 2 hours (Traveling at a rate of 80% of the<br />
maximum speed)<br />
□ Replace differential gear oil<br />
05-8 VEHICLE MAINTENANCE - INSPECTION<br />
INSPECTION<br />
CHECK THE ELECTRICAL SYSTEM WORKING CONDITION<br />
• Check the brightness and working conditions of front combination lamps, fog lamp, turn signal<br />
lamp, warning flashes, rear combination lamp, rear fog lamp, backup light and parking lamp.<br />
• Check the working condition of the interior lighting.<br />
• Check the working condition of buzzer, control unit, center tunnel, all switch in dashboard and<br />
horn.<br />
• Check the condition of power window, exterior mirror and central control door lock.<br />
• Check the radio reception conditions and interference immunity, and check the speaker.<br />
CHECK THE BATTERY<br />
05-9<br />
• Keep the battery cable clean and firm installation is benefit to the battery using performance<br />
and life.<br />
• When fastening the battery cable, pay attention to the battery cable installed correctly and<br />
firmly. Otherwise may affect appliances use and battery life.<br />
1. OPEN THE BATTERY CABLE COVER.<br />
2. CHECK THE BATTERY.<br />
(a) Check the battery shell and cable whether they are<br />
corrosion or fracture. Replace it if necessary.<br />
(b) Shaking battery cable to check whether installation is<br />
firm.<br />
(c) If discover the battery positive cable is not fixed firmly.<br />
Disconnect the battery negative cable first. Tighten<br />
battery positive cable. Reinstall the fastening battery<br />
negative cable nut.<br />
3. CHECK THE BATTERY POWER DISPLAY LAMP<br />
COLOR.<br />
(a) If it displays blue, that indicate the battery is good.<br />
(b) If it displays white, that indicate the battery is in low level,<br />
charge the battery.<br />
(c) If it displays red, that indicate battery electrolyte<br />
shortage, replace the battery.<br />
05-10 VEHICLE MAINTENANCE - INSPECTION<br />
CHECK THE AIRBAG<br />
• No paste or add items on Airbag shell, forbidden to damage or hinder the airbag shell. To<br />
ensure the normal function of the airbag, remind the user.<br />
• Airbag housing is only allowed to use a dry or slightly damp cloth to clean.<br />
CHECK DRIVER SIDE AIRBAG<br />
1. DRIVER SIDE AIRBAG IS LOCATED IN THE<br />
CENTRAL POSITION OF THE STEERING WHEEL,<br />
VISUAL INSPECTION OF PLASTIC SHELL IS INTACT.<br />
CHECK ASSISTANT DRIVER SIDE AIRBAG<br />
1. ASSIATANT DRIVER SIDE AIRBAG IS LOCATED ON<br />
THE GLOVE BOX OF THE VICE CAB, VISUAL<br />
INSPECTION OF PLASTIC SHELL IS INTACT.<br />
CHECK SEAT BELT<br />
05-11<br />
• Check the safety belt completely pulled out of the belt automatic rewind device.<br />
• Check the safety belt is dirty. Clean with neutral soap liquid if necessary.<br />
1. CHECK THE BELT STRAP FOR THE FOLLOWING<br />
DAMAGE, REPLACE IT IF NECESSARY.<br />
(a) The seat belt fracture, torn or abrasion.<br />
The webbing edge is torn down.<br />
Traces of cigarette burns.<br />
One side of the webbing edge is deformation or the seat<br />
belt edge is wavy.<br />
05-12 VEHICLE MAINTENANCE - INSPECTION<br />
2. CHECK THE SEAT BELT LOCK.<br />
Force quickly pulled down the safety belt to check<br />
whether the safety belt lock locking sensitive,replace it,<br />
if can’t be lock fast.<br />
3. CHECK ORIENTED BUCKLE AND LOCK TONGUE.<br />
(a) Check oriented buckle shell for deformation, shedding<br />
and dehiscence, replace it if necessary.<br />
Check the lock tongue for deformation and dehiscence,<br />
replace it if necessary.<br />
Insert the lock tongue into the oriented buckle. Check the<br />
lock tongue can be locked, after cross-checks more than<br />
5 times, the lock tongue once failed to lock in the<br />
oriented buckle, should be replaced.<br />
05-13<br />
CHECK PARKING BRAKE, BRAKE PEDAL<br />
1. CHECK THE PARKING BRAKE, BRAKE PEDAL.<br />
(a) Check the parking brake is flexible, handle pull strength<br />
is normal or not, whether the cable is worn, repair it if<br />
necessary.<br />
Check whether the brake pedal is loose, whether the free<br />
stroke is normal, repair it if necessary.<br />
Free stroke:1 ~ 3 mm<br />
2. ROAD TEST, CHECK THE WORK CONDITION OF THE PARKING BRAKE AND BRAKE PEDAL,<br />
MAINTAIN IT IF NECESSARY.<br />
05-14 VEHICLE MAINTENANCE - INSPECTION<br />
CHECK DOOR LIMIT, DOOR LOCK AND DOOR HINGE<br />
1. CHECK THE DOOR LIMIT.<br />
Check the door limit is in good work condition. Apply<br />
grease to the activity place if lacking of the lubrication.<br />
2. CHECK THE DOOR LOCK, INSURANCE BUTTON,<br />
CHILD SAFETY LOCK.<br />
Lock the door, check the insurance button works normal<br />
Press down the insurance button, then close the door,<br />
the insurance button will upspring to prevent false lock<br />
the door.<br />
Switch the child safety lock from OFF to ON. The child<br />
safety lock locking. In this case the door can only be<br />
opened from the outside.<br />
3. CHECK THE LOCK CORE.<br />
Insert the key into the lock.<br />
Rotate the key left and right, the lock core should be able<br />
to rotate smoothly.<br />
05-15<br />
4. CHECK THE ENGINE HATCH AND REAR HATCH.<br />
(a) Continuously open and close the engine hatch to check<br />
whether the hinge catching, Apply grease to the activity<br />
place if lacking of the lubrication.<br />
Check the rear hatch closed, check the rear hatch look.<br />
Continuously open and close the rear hatch to check<br />
whether the hydraulic pole catching. Apply grease to the<br />
activity place if lacking of the lubrication.<br />
05-16 VEHICLE MAINTENANCE - INSPECTION<br />
CHECK AND CLEAN WINDSHIELD FLUME<br />
1. OPEN THE ENGINE HATCH.<br />
2. CHECK WINDSHIELD FLUME WHETHER HAS<br />
IMPURITIES OR CLOGGED.<br />
3. CHECK THE SEALING STRIP FOR DAMAGE.<br />
4. CLOSE THE ENGINE HATCH.<br />
05-17<br />
CHECK ENGINE COMPARTMENT PARTS<br />
• Troubles once detected should be checked immediately<br />
• Replenish loss fluid timely, exclude leakage in pipes.<br />
2. CHECK THE FOLLOWING CATHETER, HOSE AND LAYUP FOR LEAKS, DAMAGE AND AGING.<br />
CHECK THE INTERSPACE BETWEEN THE PIPELINE AND THE BODY IS REASONABLE.<br />
ADJUST OR REPLACE IF NECESSARY.<br />
(a) Fuel system.<br />
(b) Air conditioning system pipeline and cooling system pipeline.<br />
(c) Brake equipment and pipeline.<br />
05-18 VEHICLE MAINTENANCE - INSPECTION<br />
CHECK TIMING BELT<br />
1. TURN THE IGNITION SWITCH OFF.<br />
2. REMOVE THE RETAINING BOLT ON THE TIMING<br />
BELT FRONT COVER. TAKE DOWN THE TIMING<br />
BELT FRONT COVER.<br />
3. CHECK THE TIMING BELT HAS THE FOLLOWING SITUATION, REPLACE IT IF NECESSARY:<br />
• Water or grease adhere to the timing belt can reduce the services life of the belt. If the timing<br />
belt with oil and heavy polluted, do not wash, need to change a new one.<br />
• If the timing belt with traces of oil pollution, should check engine if there is oil leakage.<br />
Inspect the timing belt back rubber for signs of aging and<br />
glistening.<br />
Cracks and stripping in the canvas.<br />
Cracks in the back rubber.<br />
Cracks in the grooves.<br />
Cracks in the side of the belt.<br />
Inspect the timing belt for abnormal abrasion in the side<br />
of the belt.<br />
Timing belt for abnormal abrasion.<br />
Teeth missing from the belt.<br />
05-19<br />
4. INSTALL THE TIMING BELT FRONT COVER,<br />
TIGHTEN BOLTS.<br />
Torque:18 ~ 26N•m<br />
05-20 VEHICLE MAINTENANCE - INSPECTION<br />
CHECK ACCESSORY BELT<br />
2. OPEN THE ENGINE HATCH.<br />
3. CHECK THE ACCESSORY BELT WHETHER THERE<br />
IS A FRACTURE, AGING, ETC. REPLACE IT IF<br />
NECESSARY.<br />
• Water or grease adhere to the belt can reduce the services life of the belt. If the belt with oil and<br />
heavy polluted, do not wash, needs to change a new one.<br />
• If the belt with traces of oil pollution, should check engine if there is oil leakage.<br />
05-21<br />
CHECK THE TIE ROD BALL HEAD AND DUST COVER<br />
1. LIFT THE VEHICLE.<br />
2. SLOSHING THE TIE ROD, SHOULD FEEL NO GAP.<br />
3. CHECK THE TIE ROD BALL HEAD FIXED NUT IS<br />
FIRMLY.<br />
4. CHECK THE TIE ROD DUST COVER AND BALL<br />
HEAD RUBBER FOR DAMAGE. IF THERE IS ANY<br />
DAMAGE, REPLACE IT WITH A NEW ONE.<br />
05-22 VEHICLE MAINTENANCE - INSPECTION<br />
CHECK AND TIGHTEN THE CHASSIS BOLT REFER TO THE PRE-<br />
SCRIBED TORQUE<br />
Pay attention to prevent dust, sand and other debris falling into the eyes when looking up to the<br />
chassis.To tighten the chassis bolts do wear a helmet and gloves and other safety measures.<br />
1. TURN OFF ALL ELECTRICAL APPLIANCES AND IGNITION SWITCH.<br />
2. LIFT THE VEHICLE.<br />
3. CHECK ALL CHASSIS FASTENING BOLTS AND NUTS FOR TIGHTNESS AND CORROSION.<br />
4. RE-TIGHTEN ALL FASTENING BOLTS AND NUTS REFER TO SPECIFIED TORQUE.<br />
05-23<br />
CHECK HEADLIGHTS<br />
1. PREPARATION FOR HEADLIGHTS INSPECTION:<br />
(a) Park vehicle on a flat road.<br />
(b) The driver sitting in the car (or with weight 73 kg), and more than half of the fuel store in the fuel tank.<br />
(c) Tire pressure is normal.<br />
(d) Headlight internal structure normal.<br />
2. CHECK THE HEADLIGHTS:<br />
(a) Check the headlight assembly for damage and replace if necessary.<br />
(b) Test headlight function. Bulbs burnt out should be replaced. Headlight regulating function is normal or<br />
not.<br />
(c) Check whether there is water vapor in the headlight, or other foreign material.<br />
(d) If the headlight irradiation deviates from the normal range, required to adjust the headlight. (Refer to<br />
“Chapter 64 Lighting-LF combination lamp assembly, adjustment”)<br />
05-24 VEHICLE MAINTENANCE - INSPECTION<br />
CHECK WINDSHIELD WIPERS, CLEANING DEVICE<br />
1. CHECK THE WINDSHIELD WIPER BLADE LIMIT POSITION:<br />
• Check the wiper blade should be located in the rest position, adjust if necessary.<br />
• Wiper arm tightening torque:18 ~ 21N•m.<br />
The driver's side.<br />
• The distance between the wiper blade rubber and the<br />
lower edge of the windscreen is 30mm.<br />
• If necessary, move and adjust the wiper arm.<br />
(b) The front passenger side.<br />
lower edge of the windscreen is 45mm。<br />
2. REPLACE WIPER BLADE.<br />
(a) Place the wiper arm in the maintenance position. Push<br />
the locking button of the wiper blade. Remove the wiper<br />
blade down.<br />
(b) Install wiper blade. Make sure locking button located in<br />
the lock position.<br />
(c) Turn on the ignition switch and operate the wiper arm in<br />
a short-term, stop the windshield wipers back at the<br />
automatic stop position.<br />
3. CHECK THE WINDSHIELD WASHER FLUID.<br />
(a) The windshield washer fluid level should be apart from<br />
the opening about 10cm, add if inadequate.<br />
The windshield washer fluid is consumable liquid. Please<br />
check regularly.<br />
05-25<br />
4. Check the windshield spray.<br />
(a) The washer fluid sprays on windshield within the range<br />
shown in the illustration.<br />
If the point which the washer fluid sprays on windshield is<br />
not in right position, adjust washer nozzle.<br />
05-26 VEHICLE MAINTENANCE - INSPECTION<br />
CHECK CHASSIS<br />
2. CHECK THE FUEL LINE, BRAKE FLUID LINE FOR LEAKS.<br />
3. CHECK THE BOTTOM COVER, WHEEL COVER AND SIDE BEAM IF THERE IS DAMAGE.<br />
4. VISUAL CHECK THE EXHAUST PIPE LIFTING LUG FOR AGEING AND INSTALLATION FIRMLY.<br />
05-27<br />
CHECK SUSPENSION COMPONENTS<br />
2. CHECK ALL CONNECTING BUSHING FOR AGING OR DAMAGE.<br />
3. TIGHTEN ALL CONNECTING BOLTS AND NUTS BY SPECIFIED TORQUE.<br />
4. CHECK EACH CONNECTING PARTS FOR DEFORMATION AND CRACK.<br />
5. CHECK SHOCK ABSORBER FOR OIL LEAKAGE. CHECK DUST COVER FOR DAMAGE.<br />
05-28 VEHICLE MAINTENANCE - INSPECTION<br />
CHECK SUSPENSION BALL JOINT AND DUST COVER<br />
1. CHECK UPPER ARM BALL JOINT DUST COVER FOR<br />
DAMAGE. IF THERE IS ANY DAMAGE, REPLACE IT<br />
WITH A NEW ONE.<br />
2. CHECK LOWER ARM BALL JOINT DUST COVER FOR<br />
05-29<br />
CHECK STEERING FLUID LEVEL<br />
1. PARK VEHICLE ON A FLAT ROAD.<br />
2. TURN IGNITION SWITCH OFF.<br />
3. TURN FRONT WHEELS TO STRAIGHT POSITION.<br />
4. OPEN THE ENGINE HATCH.<br />
5. UNSCREW POWER STEERING RESERVOIR FILLER<br />
CAP.<br />
6. CHECK THAT THE FLUID LEVEL IS WITHIN THE<br />
RANGE OF MAX AND MIN, ADJUST THE FLUID IF<br />
Steering fluid:ATF- Ⅲ<br />
7. TIGHTEN THE POWER STEERING RESERVOIR<br />
FILLER CAP.<br />
8. CLOSE THE ENGINE HATCH.<br />
05-30 VEHICLE MAINTENANCE - INSPECTION<br />
CHECK BRAKING SYSTEM<br />
• Only use the brake fluid <strong>Foton</strong> approved.<br />
• Brake fluid can not mixed with other liquid, otherwise it may damage the braking system line<br />
and endanger vehicle.<br />
• Decide whether to add brake fluid according to the wear pattern of braking friction plate.<br />
2. CHECK THE BRAKE FLUID RESERVOIR LEVEL.<br />
(a) When braking friction plate wear close to the limit, brake fluid level should be partial to the lowest line.<br />
(b) When braking friction plate wear little, brake fluid level should be partial to the highest line.<br />
3. CHECK THE FOLLOWING PARTS WHETHER HAVE DAMAGE AND LIQUID LEAKAGE:<br />
(a) Brake master cylinder.<br />
(b) Brake booster.<br />
(c) Brake caliper.<br />
(d) Braking line.<br />
4. CHECK THE CLEARANCE OF BRAKE HOSE AND BODY, IT SHOULD BE APPROPRIATE. CHECK<br />
BRAKE HOSE IF IT IS ABRADED, CHECK WHETHER BRAKE LINE INTERFACE AND FIXED<br />
INSTALLATION IS FIRMLY.<br />
05-31<br />
CHECK THE BRAKE DISC, BRAKE DRUM AND BRAKE FRICTION<br />
PLATE<br />
If the brake disc, brake drum and brake friction plate thickness wear to limit, must inform the customer,<br />
replace it.<br />
1. CHECK FRONT BRAKE DISC AND THE BRAKE FRICTION PLATE.<br />
(a) Remove front wheel. (Refer to “Chapter 33 tire and wheel - front tire and wheel, replacement”)<br />
(b) Measuring braking friction plate (without rear panel) and<br />
brake disc thickness.<br />
• Standard thickness for brake friction plate (without<br />
rear panel) is: 12mm, limit thickness is: 2mm.<br />
• Standard thickness for brake disc is: 22mm, limit<br />
thickness is: 21mm.<br />
(c) Install the front wheel. (Refer to “Chapter 33 tire and wheel - front tire and wheel, replacement”)<br />
2. CHECK THE REAR BRAKE DRUM AND BRAKE FRICTION PLATE.<br />
(a) Remove rear wheel.<br />
brake drum thickness.<br />
rear panel) is: 7.5mm, limit thickness is: 2.5mm.<br />
• Standard thickness for brake drum is: Φ295mm, limit<br />
thickness is: Φ296mm.<br />
Install the rear wheel (Refer to “Chapter 33 tire and wheel - front tire and wheel, replacement”)<br />
05-32 VEHICLE MAINTENANCE - INSPECTION<br />
CHECK TIRES<br />
When found tire wear to limit or damaged which affect the safe driving, must inform the customer,<br />
change the tire.<br />
1. CHECK THE TIRE ROLLING SURFACE AND SIDE WALL IS DAMAGE OR FOREIGN BODY,<br />
CHECK SIDE WALL IS LOOSE POROUS, INCISION AND FOREIGN BODY PIERCING.<br />
2. CHECK WHETHER THE TIRE ROLLING SURFACE WEAR IS UNILATERAL, IF UNILATERAL<br />
WEAR IS SERIOUS, NEED TO ADJUST BY FOUR-WHEEL LOCATION.<br />
3. CHECK THE TIRE TREAD DEPTH (INCLUDING<br />
SPARE TIRE), ENSURE TREAD GROOVE DEPTH<br />
THAN WEAR MARK THICKNESS, THE SIDE OF THE<br />
TIRE TRIANGLE WEAR MARK MUST NOT WEAR<br />
OUT.<br />
The minimum tread depth is: 1.6mm.<br />
4. Check and adjust tire inflation pressure (including spare tire):<br />
wheel specification Front wheel Rear wheel Spare wheel<br />
195R15C-106R 350 kPa 400 kPa 400 kPa<br />
05-33<br />
CHECK EXHAUST SYSTEM<br />
In the exhaust system operation, pay attention to prevent scalding.<br />
2. CHECK FRONT AND REAR EXHAUST PIPE, THE SILENCER, THE OXIDATION CATALYST SHELL<br />
IF THERE IS ANY BREAKAGE.<br />
3. CHECK IF THE EXHAUST SYSTEM CONNECTION BETWEEN COMPONENTS LEAKS.<br />
4. CHECK THE LIFTING LUGS WHETHER AGEING OR FRACTURE.<br />
05-34 VEHICLE MAINTENANCE - INSPECTION<br />
CHECK COOLANT LEVEL<br />
• In the cooling system operation, pay attention to prevent water and heat steam scalding.<br />
• Can only use the cooling fluid <strong>Foton</strong> approved.<br />
2. WAIT UNTIL THE ENGINE COOLING TO ROOM TEMPERATURE.<br />
3. OPEN THE ENGINE HATCH.<br />
4. CHECK COOLANT LEVEL LINE, LIQUID LEVEL<br />
SHOULD BE IN MIN AND MAX (ENGINE IS ALREADY<br />
COOLING DOWN).<br />
5. PUT DOWN THE ENGINE HATCH.<br />
05-35<br />
CHECK THE ENGINE OIL LEVEL (4G69)<br />
1. PARK THE VEHICLE ON A FLAT ROAD.<br />
2. PREHEAT THE ENGINE TO NORMAL OPERATING TEMPERATURE.<br />
3. TURN THE IGNITION SWITCH OFF.<br />
4. WAIT FOR ABOUT 3 MINUTES.<br />
5. OPEN THE ENGINE HATCH.<br />
6. PULL OUT OIL SCALE SLOWLY.<br />
7. CHECK THE ENGINE OIL LEVEL, LEVEL SHOULD<br />
BE IN OIL SCALE MARK RANGE.<br />
8. CHECK THE ENGINE OIL, IF OIL IS DIRTY OR THINNED, DEBUGGING AND REPLACE ENGINE<br />
OIL.<br />
9. PUT BACK THE OIL SCALE.<br />
10. PUT DOWN THE ENGINE HATCH.<br />
05-36 VEHICLE MAINTENANCE - INSPECTION<br />
CHECK THE ENGINE OIL LEVEL (ISF2.8)<br />
3. TURN OFF THE IGNITION SWITCH.<br />
BE IN THE SCOPE OF OIL SCALE MARK RANGE.<br />
REPLACEMENT<br />
05-37<br />
REPLACE AIR FILTER ELEMENT<br />
1. REPLACE AIR FILTER ELEMENT.<br />
(a) Remove the 4 air filter fixed buckle from the vehicle<br />
bottom.<br />
(b) Open the air filter lower cover, remove the air filter.<br />
Air filter is made of paper material, if necessary, can use the<br />
high pressure air gun to clean air filter from internal to<br />
external. don't rinse the air filter by water.<br />
(c) Clean or replace the air filter.<br />
2. INSTALL AIR FILTER LOWER COVER AND FASTEN<br />
THE BUCKLE.<br />
When install air filter lower cover, ensure that install air<br />
filter in the right direction, then fasten the buckle.<br />
05-38 VEHICLE MAINTENANCE - REPLACEMENT<br />
REPLACE AIR CONDITIONER FILTER ELEMENT<br />
1. REMOVE THE GLOVE BOX.<br />
2. REMOVE THE AIR FILTER DECORATIVE COVER.<br />
(a) Press on both sides of the lock. take down the decorative<br />
cover.<br />
3. EXTRACT AIR-CONDITIONING FILTER.<br />
4. INSTALL AIR-CONDITIONING FILTER.<br />
Install the air conditioning filter in accordance with the marked<br />
direction at filter lateral.<br />
05-39<br />
5. INSTALL THE AIR FILTER DECORATIVE COVER,<br />
AND LOCK INTO TO THE CORRECT POSITION.<br />
6. INSTALL THE GLOVE BOX.<br />
05-40 VEHICLE MAINTENANCE - REPLACEMENT<br />
REPLACE ENGINE OIL (4G69)<br />
1. START ENGINE AND ENSURE ENGINE COOLANT TEMPERATURE WITHIN 80 ~ 90 ℃ .<br />
2. TURN IGNITION SWITCH OFF AND WAIT FOR 10 MINUTES.<br />
3. OPEN ENGINE COMPARTMENT COVER.<br />
(a) Loosen the driver seat clamp.<br />
(b) Turn over the driver seat and open engine compartment<br />
4. OPEN OIL FILLER CAP.<br />
5. RAISE AND SUPPORT VEHICLE.<br />
6. REMOVE OIL DRAIN PLUG.<br />
(a) Drain engine oil.<br />
• The engine oil maybe hot, be careful, avoid personal<br />
injury.<br />
• Prolonged and repeated contact with engine oil will<br />
cause the skin fat to be removed, resulting in dry<br />
skin, allergies and dermatitis. In addition, used<br />
engine oil contains potentially harmful pollutants<br />
which may cause skin cancer. Therefore, the skin<br />
must be protected in appropriate methods and with<br />
cleaning equipment.<br />
• Using a special container, collect or dispose used oil<br />
as required.<br />
7. REPLACE WITH NEW DRAIN PLUG GASKET AND<br />
TIGHTEN PLUG.<br />
Torque: 34 ~ 45 N.m<br />
05-41<br />
8. LOWER VEHICLE.<br />
9. FILL ENGINE OIL.<br />
Engine oil: 4 L<br />
The Specification of engine oil allowed only is 10W-30 ,15W-40 or SL level as well as 5W-30 (GB11121)<br />
oil used in winter of North China.<br />
10. INSTALL OIL FILLER CAP.<br />
11. PARK THE VEHICLE ON LEVEL GROUND AND START ENGINE UNTIL IT IS WARM. CHECK AND<br />
ENSURE THERE IS NO OIL LEAKAGE.<br />
12. TURN IGNITION SWITCH OFF AND WAIT FOR 10 MINUTES.<br />
13. CHECK OIL LEVEL.<br />
(a) Pull out oil dipstick and wipe it clean .<br />
(b) Insert oil dipstick and pull it out to ensure oil level is<br />
within the range as shown in the figure.<br />
14. PUT DOWN DRIVER SEAT AND LOCK IT.<br />
05-42 VEHICLE MAINTENANCE - REPLACEMENT<br />
REPLACE OIL FILTER (4G69)<br />
Without special circumstances, the oil filter should be replaced with engine oil to avoid oil pollution<br />
and keep engine normal operation.<br />
2. OPEN ENGINE COMPARTMENT COVER.<br />
3. OPEN OIL FILLER CAP.<br />
4. RAISE AND SUPPORT VEHICLE.<br />
5. DRAIN ENGINE OIL. (Refer to “Chapter 18A lubrication - engine oil, replacement”)<br />
6. USING SPECIAL TOOL TO REMOVE OIL FILTER.<br />
7. CLEAN THE CONNECT SURFACE OF OIL FILTER AND OIL FILTER BRACKET.<br />
8. APPLY OIL TO O-RING OF NEW OIL FILTER.<br />
05-43<br />
9. TIGHTEN OIL FILTER BY HAND UNTIL O-RING TOUCHES<br />
OIL FILTER BRACKET. USE A SUITABLE TOOL TO<br />
TIGHTEN OIL FILTER.<br />
Torque: 13 ~ 15 N•m<br />
10. TIGHTEN DRAIN PLUG.<br />
Torque: 34 ~ 45 N•m<br />
11. LOWER VEHICLE.<br />
12. OPEN OIL FILLER CAP AND FILL ENGINE OIL TO SPECIFIED LEVEL.<br />
13. INSTALL OIL FILLER CAP.<br />
14. PARK THE VEHICLE ON LEVEL GROUND AND START ENGINE UNTIL IT IS WARM.<br />
15. CHECK AND ENSURE THERE IS NO OIL LEAKAGE.<br />
16. TURN THE IGNITION SWITCH OFF AND WAIT FOR 10 MINUTES.<br />
17. PULL OUT OIL DIPSTICK TO ENSURE OIL LEVEL IS BETWEEN “MAX” MARK AND “MIN”<br />
MARK.<br />
05-44 VEHICLE MAINTENANCE - REPLACEMENT<br />
REPLACE ENGINE OIL (ISF2.8)<br />
1. PARK VEHICLE IN LEVEL ROAD, SLOWLY PULL OUT OIL DIPSTICK, AND CHECK OIL LEVEL,<br />
OIL LEVEL MUST BE LOCATED WITHIN THE OIL DIPSTICK MARK.<br />
2. CHECK OIL WITHOUT EXCESSIVE POLLUTION, NO PETROL AND LIQUID MIXED. THERE MUST<br />
HAVE ENOUGH CONCENTRATIONS AND VISCOSITY.<br />
3. START ENGINE AND ENSURE ENGINE COOLANT TEMPERATURE WITHIN 80 ~ 90 ℃ .<br />
5. LIFT THE VEHICLE.<br />
The engine oil maybe hot, be careful, avoid personal injury.<br />
7. USING A SPECIAL CONTAINER, COLLECT OR DISPOSE USED OIL AS REQUIRED.<br />
8. REPLACE A NEW DRAIN PLUG GASKET AND TIGHTEN<br />
DRAIN PLUG.<br />
Torque: 35 ~ 45 N.m<br />
9. LOWER VEHICLE.<br />
10. FILL ENGINE OIL.<br />
Engine oil: 5 ~ 5.5 L<br />
The specification of engine oil is CH - 4 level or above (15W-40 in summer and 15W-30 in winter).<br />
11. INSTALL OIL FILLER CAP.<br />
12. PARK THE VEHICLE ON LEVEL GROUND AND START ENGINE UNTIL IT IS WARM.<br />
13. CHECK OIL FILTER OR OTHER PART AND ENSURE THERE IS NO OIL LEAKAGE.<br />
14. TURN IGNITION SWITCH OFF.<br />
05-45<br />
15. AFTER 8 ~ 10 MINUTES, PULL OUT OIL DIPSTICK TO<br />
ENSURE OIL LEVEL IS BETWEEN “MAX” MARK AND<br />
“MIN” MARK.<br />
05-46 VEHICLE MAINTENANCE - REPLACEMENT<br />
REPLACE OIL FILTER (ISF2.8)<br />
2. OPEN ENGINE COMPARTMENT COVER AND THEN OPEN OIL FILLER CAP.<br />
3. RAISE AND SUPPORT THR VEHICLE.<br />
4. REMOVE OIL DRAIN PLUG AND DRAIN ENGINE OIL.<br />
Be careful, the engine oil maybe hot.<br />
5. USING A SPECIAL CONTAINER, COLLECT OR DISPOSE USED OIL AS REQUIRED.<br />
6. USING SPECIAL TOOL, REMOVE OIL FILTER.<br />
7. CLEAN THE SURFACE BETWEEN OIL FILTER AND OIL FILTER BRACKET.<br />
9. FILL CLEAN OIL INTO OIL FILTER.<br />
05-47<br />
10. TIGHTEN OIL FILTER BY HAND UNTIL O-RING TOUCHES<br />
OIL FILTER BRACKET. USING SUITABLE TOOL, TIGHTEN<br />
OIL FILTER.<br />
Torqure: 25 ~ 30 N•m<br />
11. TIGHTEN DRAIN PLUG.<br />
12. LOWER VEHICLE.<br />
13. FILL ENGINE OIL TO SPECIFIED LEVEL.<br />
14. INSTALL OIL FILLER CAP.<br />
15. START ENGINE AND RUN FOR 5 MINUTES WITH THE VEHICLE PARKING ON LEVEL GROUND.<br />
16. CHECK OIL FILTER AND ENSURE THERE IS NO OIL LEAKAGE.<br />
17. TURN IGNITION SWITCH OFF.<br />
18. AFTER 8 ~ 10 MINUTES, PULL OUT OIL DIPSTICK TO<br />
05-48 VEHICLE MAINTENANCE - REPLACEMENT<br />
REPLACE SPARK PLUG (4G69)<br />
1. TURN IGNITION SWITCH OFF.<br />
Loosen the driver seat clamp.<br />
Turn over the driver seat and open engine compartment<br />
3. REMOVE AIR INTAKE HOSE. (Refer to “Chapter 14A intake air - intake air hose, replacement”)<br />
4. REMOVE SPARK PLUG WIRE.<br />
(a) Pull out spark plug wire by slightly turning.<br />
5. REMOVE SPARK PLUG..<br />
(a) Using special socket tool ,remove spark plug.<br />
(b) Take spark plug out.<br />
6. INSTALL SPARK PLUG.<br />
(a) Using special socket tool, tighten spark plug.<br />
Torque: 25 N•m<br />
Install the spark plug, tightening torque to meet the<br />
technical specifications of <strong>Foton</strong>. Don’t screw it too loose<br />
or too tight to avoid leakage or damage to the spark plug<br />
and Spark plug holes.<br />
05-49<br />
7. INSTALL SPARK PLUG WIRE.<br />
(a) Place spark plug wire on the corresponding position<br />
according to the sequence as shown on igniton module.<br />
(b) Install spark plug wire.<br />
A click can be heard to confirm the spark plug wire is<br />
installed properly.<br />
8. INSTALL INTAKE HOSE. (Refer to “Chapter 14A intake air- intake air hose, replacement”)<br />
9. PUT DOWN DRIVER SEAT AND LOCK IT.<br />
10. START ENGINE AND CONFIRM IT IS IN GOOD CONDITION.<br />
05-50 VEHICLE MAINTENANCE - REPLACEMENT<br />
REPLACE FUEL FILTER ASSEMBLY (4G69)<br />
1. RELEASE FUEL PRESSURE. (Refer to “Chapter 12A fuel - fuel system, fuel system pressure<br />
release process”)<br />
2. RAISE AND SUPPORT THE VEHICLE.<br />
3. REMOVE THE FUEL FILTER.<br />
(a) Disconnect quick connector from both sides of fuel filter.<br />
• Depress the tab on both sides of quick connector,<br />
slide out the connector slowly. Do not pull excessively<br />
to prevent quick connector from damaging.<br />
• Keep the connecting portion clean and avoid damage<br />
and foreign materials, cover them completely with<br />
plastic bags or something similar.<br />
Loosen fuel filter mounting band retaining bolt.<br />
Remove fuel filter.<br />
4. INSTALL NEW FUEL FILTER.<br />
Follow the arrow on the fuel filter when install the fuel filter.<br />
(a) Install fuel filter and tighten the mounting band bolt.<br />
Torque: 21 ~ 25 N•m<br />
(b) Connect both sides quick connector.<br />
Connect fuel tube quick connectors until a click was heard,<br />
then pull the quick connector to check quick connectors<br />
are secured.<br />
5. LOWER THE VEHICLE.<br />
6. CHECK FUEL LINES.<br />
(a) When ignition switch is on, fuel pump will apply fuel pressure to fuel lines. inspect if there is fuel<br />
leakage from pipe connection.<br />
(b) Start engine and rev it up and check there are no fuel leakage at the fuel system tube and hose<br />
connections.<br />
05-51<br />
REPLACE FUEL FILTER ELEMENT (ISF2.8)<br />
1. DIESEL FILTER ASSY DESCRIPTION.<br />
(a) ISF2.8 Engine have a maintainable cylinder-type diesel<br />
filter which contains a integrated WIF sensor and fuel<br />
heater. The diesel filter is located between fuel pump and<br />
tank.<br />
2. RELEASE FUEL PRESSURE. (Refer to “Chapter 12B fuel - fuel system, fuel system pressure<br />
3. REPLACE DIESEL FILTER. (Refer to CUMMINS ISF SERIES ENGINE SERVICE MANUAL )<br />
• If draining water is required frequently, it means that fuel is not qualified or there is water in fuel<br />
tank. Please drive the vehicle to service station for repair.<br />
• In order to ensure fuel clean, in strict accordance with maintenance requirement to operate fuel<br />
filter sechudle maintenance. Replacement cycle: 15,000 km.<br />
4. CHECK AFTER INSTALLATION.<br />
(a) After installation, turn ignition switch on and check the fuel gauge’s conditions in instrument panel. Start<br />
engine and check there are no fuel leakage at the diesel system tube and hose connections.<br />
05-52 VEHICLE MAINTENANCE - REPLACEMENT<br />
REPLACE COOLANT<br />
Do not open the reservior cap when the engine is hot. Coolant temperature should be reduced to 50 ° C<br />
(120 ° F) below, remove the radiator cap. Otherwise, the cooling liquid or vapor emitting heat may<br />
cause personal injury.<br />
1. COOL ENGINE TO NORMAL INDOOR TEMPERATURE.<br />
2. OPEN RESERVOIR CAP TO RELEASE PRESSURE<br />
BY TURN IT COUNTERCLOCKWISE.<br />
Wrap a thick cloth around the reservior cap. Slowly turn it a<br />
quarter of a turn to release built-up pressure. Then turn it all<br />
the way.<br />
3. RAISE AND SUPPORT THE VEHICLE.<br />
4. REMOVE RADIATOR DRAIN PLUG AND DRAIN<br />
COOLANT.<br />
Using a suitable container, hold the coolant. if not to be<br />
used, dispose of them according to the regulations .<br />
5. CHECK ENGINE COOLANT.<br />
(a) Check drained engine coolant for contaminants such as rust, corrosion or discoloration.<br />
(b) If contaminated, flush the engine cooling system.<br />
6. FLUSH ENGINE COOLING SYSTEM.<br />
(a) Install and tighten radiator drain plug.<br />
Always clean coolant drain plug and replace O-ring with new one.<br />
(b) Fill radiator and reservoir with water and reinstall reservior cap.<br />
(c) Run the engine and warm it up to normal operating temperature.<br />
(d) Rev the engine two or three times under no-load.<br />
(e) Stop the engine and wait until it cools down.<br />
(f) Drain water from the cooling system.<br />
(g) Repeat the precedure above until clear water begins to drain from radiator<br />
7. ADD ENGINE COOLANT.<br />
(a) Install radiator drain plug.<br />
(b) Slowly fill the radiator with ”FOTON Long-effective coolant”.<br />
Standard volume: 13.5 L<br />
(c) Push the radiator inlet/outlet hose several times, check the coolant level. If coolant is at the low level ,<br />
fill the coolant.<br />
05-53<br />
(d) Install the radiator cap and coolant reservoir cap.<br />
(e) Start and warm the engine until the cooling fan at high speed.<br />
(f) Stop the engine and check the coolant level.<br />
(g) Check the coolant level in reservoir. If necessary, add the coolant to specified position.<br />
The air in cooling system can be bled automatically.<br />
05-54 VEHICLE MAINTENANCE - REPLACEMENT<br />
REPLACE BRAKE FLUID<br />
Brake fluid damages painted surfaces and irritates skin. If brake fluid is spilled on any painted surfaces<br />
or skin, wash it off immediately with water.<br />
1. FILL THE FLUID RESERVOIR WITH BRAKE FLUID.<br />
Brake fluid: DOT 3 or DOT 4 brake fluid<br />
Brake fluid damages painted surfaces and irritates skin. If<br />
brake fluid is spilled on any painted surfaces or skin, wash<br />
it off immediately with water.<br />
2. BLEED BRAKE MASTER CYLINDER ASSY.<br />
(a) Tighten tubing joint nut fitting brake tube to brake master<br />
cylinder.<br />
If the brake cylinder has been removed or if the brake fluid<br />
reservoir assy becomes empty, bleed the air from the<br />
master cylinder assy.<br />
Rapidly depress the brake pedal and hold it.<br />
Loosen tubing joint nut separately, bleed the air and<br />
fluid,then tighten tubing joint nut immediately.<br />
Repeat steps (b) and (c) 3 or 4 times until all the air in the<br />
fluid has been bled out.<br />
05-55<br />
3. BLEED BRAKE LINE.<br />
(a) Connect the hose to the bleeder plug of rear wheel brake<br />
(b) Rapidly depress the brake pedal several times, then<br />
loosen the bleeder plug.<br />
(c) When brake fluid stops flowing, tighten the bleeder plug,<br />
then release the brake pedal.<br />
Torque: 9 ~ 11 N•m<br />
(d) Repeat steps (b) and (c) 3 or 4 times until all the air in the<br />
Connect the hose to the bleeder plug of front disk brake<br />
caliper.<br />
Rapidly depress the brake pedal several times, then<br />
When brake fluid stops flowing, tighten the bleeder plug,<br />
Torque: 8 ~ 13 N•m<br />
Repeat steps (f) and (g) 3 or 4 times until all the air in the<br />
Repeat the above procedures to bleed the air out of the<br />
brake line for each wheel.<br />
Sequence Of Brake Line Bleeding(sit in driver seat): Rear<br />
RH - Rear LH - Front RH - Front LH<br />
4. CHECK FLUID LEVEL IN BRAKE FLUID RESERVOIR.<br />
(a) Check the fluid level and fill the fluid reservoir with brake<br />
fluid if necessary.<br />
05-56 VEHICLE MAINTENANCE - REPLACEMENT<br />
REPLACE GEARBOX LUBRICATING OIL<br />
1. REMOVE DRAIN PLUG BY DOWNSIDE AND DRAIN<br />
TRANSMISSION FLUID COMPLETELY. TIGHTEN DRAIN<br />
PLUG.<br />
Torque: 35 ~ 45 N•m<br />
• Keep vent plug unblocked and loosen the filler plug<br />
before draining fluid. In order to drain transmission<br />
fluid completely, drain the fluid when it is hot.<br />
• Use special container for transmission fluid when<br />
draining.<br />
2. REMOVE FILLER PLUG AND FILL TRANSMISSION<br />
FLUID. THEN TIGHTEN FILLER PLUG.<br />
CAUTIONN<br />
• According to demand, fill transmission fluid GL- 4<br />
75W/90 for 2.0 L.<br />
• Do not mix different kind of transmission fluid.<br />
• Parking the vehicle on the levelground when<br />
checking fluid level. The fluid level must be flush<br />
with lower edge of oil filler.<br />
05-57<br />
REPLACE REAR MAIN REDUCER GEAR OIL<br />
1. PRECAUTION. (Refer to “Chapter 34 axle and propeller shaft - rear axle, precaution”)<br />
2. DRAIN FINAL DRIVE OIL.<br />
(a) Remove the vent plug.<br />
Using a wrench, remove the drain plug.<br />
Drain the final drive oil completely.<br />
Use a container to collect final drive oil when performing<br />
this operation.<br />
Using a wrench, install the drain plug.<br />
GASOLINE ENGINE CONTROL SYSTEM.....................................11A-1<br />
PRECAUTION............................................................................ 11A-1<br />
SYSTEM OVERVIEW................................................................ 11A-2<br />
INTRODUCTION TO SYSTEM FUNCTION .............................. 11A-6<br />
BASIC PRINCIPLE .................................................................... 11A-8<br />
MAIN COMPONENTS ............................................................. 11A-13<br />
SYSTEM COMPONENTS DESCRIPTION.............................. 11A-14<br />
ENGINE CONTROL MODULE (ECM) ...........................................11A-15<br />
PRINCIPLE .............................................................................. 11A-15<br />
REPLACEMENT ...................................................................... 11A-16<br />
ENGINE COOLANT TEMPERATURE SENSOR...........................11A-18<br />
PRINCIPLE .............................................................................. 11A-18<br />
OVERHAUL ............................................................................. 11A-19<br />
THROTTLE BODY .........................................................................11A-21<br />
THROTTLE BODY CLEANING................................................ 11A-21<br />
THE FIXED SPEED ADJUSTING SCREW (SAS)<br />
ADJUSTMENT......................................................................... 11A-22<br />
BASIC IDLE SPEED ADJUSTMENT....................................... 11A-23<br />
OVERHAUL ............................................................................. 11A-24<br />
IDLE AIR CONTROL MOTOR .......................................................11A-28<br />
PRINCIPLE .............................................................................. 11A-28<br />
ON-VEHICLE INSPECTION .................................................... 11A-29<br />
OVERHAUL ............................................................................. 11A-30<br />
THROTTLE POSITION SENSOR (TPS)........................................11A-32<br />
PRINCIPLE .............................................................................. 11A-32<br />
ON-VEHICLE INSPECTION .................................................... 11A-33<br />
OVERHAUL ............................................................................. 11A-34<br />
MANIFOLD ABSOLUTE PRESSURE/INTAKE<br />
TEMPERATURE SENSOR ............................................................11A-36<br />
PRINCIPLE .............................................................................. 11A-36<br />
ON-VEHICLE INSPECTION .................................................... 11A-37<br />
OVERHAUL ............................................................................. 11A-38<br />
KNOCK SENSOR...........................................................................11A-40<br />
PRINCIPLE .............................................................................. 11A-40<br />
OVERHAUL ............................................................................. 11A-41<br />
CKP SENSOR ................................................................................11A-43<br />
PRINCIPLE .............................................................................. 11A-43<br />
OVERHAUL ............................................................................. 11A-44<br />
UPSTREAM OXYGEN SENSOR ...................................................11A-46<br />
PRINCIPLE .............................................................................. 11A-46<br />
ON-VEHICLE INSPECTION .................................................... 11A-47<br />
OVERHAUL ............................................................................. 11A-48<br />
DOWNSTREAM OXYGEN SENSOR.............................................11A-49<br />
PRINCIPLE .............................................................................. 11A-49<br />
ON-VEHICLE INSPECTION .................................................... 11A-50<br />
OVERHAUL ............................................................................. 11A-51<br />
CANISTER SOLENOID VALVE.....................................................11A-52<br />
PRINCIPLE .............................................................................. 11A-52<br />
ON-VEHICLE INSPECTION .................................................... 11A-53<br />
OVERHAUL ............................................................................. 11A-54<br />
11A<br />
VEHICLE SPEED SENSOR ...........................................................11A-57<br />
PRINCIPLE ..............................................................................11A-57<br />
ON-VEHICLE INSPECTION ....................................................11A-58<br />
OVERHAUL .............................................................................11A-59<br />
IGNITION CONTROL MODULE.....................................................11A-60<br />
PRINCIPLE ..............................................................................11A-60<br />
OVERHAUL .............................................................................11A-61<br />
ENGINE CONTROL SYSTEM -<br />
GASOLINE ENGINE CONTROL<br />
GASOLINE ENGINE CONTROL SYSTEM<br />
11A-1<br />
1. GASOLINE ENGINE CONTROL SYSTEM PRECAUTION.<br />
(a) Power off.<br />
• The battery negative cable must be disconnected at first before removing or installing any electric<br />
appliance and when tools or facilities will touch the exposed terminals. It should be connected eventually.<br />
This will prevent injured person and vehicle damage.<br />
• The ignition switch must be off without any special descriptions.<br />
The ignition and illumination switches must be shut off before removing or installing the battery<br />
negative cable (the semiconductor may be damaged without doing that).<br />
(b) Please do disassembly, assembly and testing in accordance with the provisions introduced in this<br />
manual during maintenance.<br />
(c) Clear off the sundries on the mounting surface with a sealant scraper or a wire brush and confirm the<br />
sealing face is level and smooth and no greasy dirt on it before the installation. Don’t forget to remove<br />
the sealant on the mounting hole, the threaded hole and the thread.<br />
(d) Tighten the fixing bolts with prescribed torque during installing the sensors, actuators or other parts.<br />
(e) The high impedance type digital multimeter should be used to the test except the especial description<br />
of the procedure in place of the traditional analogue types multimeter.<br />
(f) The oxygen sensor can not contact with water or other liquids.<br />
(g) When installing or carrying the sensor, ensure it not damaged. Any shock or drop may cause great<br />
damage to its performance.<br />
(h) Battery voltage is low or starter failure, not long time starting the engine, so as not to damage the<br />
catalytic converter.<br />
(i) Do not use the needle puncture method to inspect system signal of wire harness.<br />
(j) Fuel pump can not operate for a long time without gasoline, also it can not run in the air.<br />
(k) Because most electric sprayed parts are un-repairable, after confirming the part is damaged, replace it<br />
as necessary.<br />
(l) The system should use anti-type spark plugs and high-voltage, non-resistant phenotype will not only<br />
release high-voltage spark plug and interference wave, but also effect the ignition coil driver module in<br />
the ECM.<br />
(m) ECM can’t be disassembled for test and maintenance.<br />
11A-2 ENGINE CONTROL SYSTEM -<br />
SYSTEM OVERVIEW<br />
1. INTRODUCTION.<br />
The electrically controlled Multi-point Injection (MPI) engine control systems – BJ491EQ – take DELPHI<br />
MT20U2 Engine Control Module (ECM) as the control center and measure various working parameters of the<br />
engine through various sensors mounted on different components of the engine. Then the fuel injection<br />
quantity is controlled precisely via the control injector according to the preset control program in the ECM,<br />
which enables the engine to obtain the mixture with optimal concentration under various working conditions. In<br />
addition, with the control program in the ECM, the electrically controlled fuel injection system can also enable<br />
the functions of start-up enrichment, warm-up enrichment, acceleration enrichment, full-load enrichment,<br />
deceleration dilution, forcible idle cutoff, automatic idle speed control etc, which meets the requirements for<br />
mixture under special working conditions of the engine and enables the engine to obtain good fuel economy<br />
and emission while enhancing the functional performance of the vehicle. In addition, ECM has some fault<br />
diagnosis modes which can simplify the fault location.<br />
2. ENGINE CONTROL SYSTEM FUNCTION.<br />
Knock control<br />
Mileage memory<br />
Over voltage pretection<br />
Fuel pump control<br />
Canister solenoid valve control<br />
ECM control function<br />
Idle air control motor control<br />
Totally main power relay control<br />
A/C, coolant water box fan control<br />
Direct ignition<br />
Closed-loop control multi-point squence fuel injection (MAP sensor pressure<br />
judgement)<br />
Intake pressure speed-density method air measurement<br />
Trouble self-diagnosis function<br />
3. ECM CONTROL STRUCTURE.<br />
11A-3<br />
11A-4 ENGINE CONTROL SYSTEM -<br />
4. ENGINE CONTROL SYSTEM DIAGRAM.<br />
1 Intake<br />
2 Air Filter<br />
3 Idle Air Control Motor<br />
4 Throttle Position Sensor (TPS)<br />
5 Canister Solenoid Valve<br />
6 Canister<br />
7 Fuel Pressure Regulation<br />
8 To Fuel Box<br />
Positive Crankshift Ventilation (PCV)<br />
Valve<br />
10<br />
11 From Fuel Pump<br />
12 Injector<br />
13 Coolant Temperature Sensor<br />
14 Crankshaft Position Sensor<br />
15 Upstream Oxygen Sensor<br />
16 Downstream Oxygen Sensor<br />
17 Three-Way Catalyst (TWC)<br />
11A-5<br />
5. ENGINE CONTROL SYSTEM MAIN COMPONENTS DISTRIBUTION GRAPHIC.<br />
14 Outlet Fuel (Return Back To Fuel Tank)<br />
11A-6 ENGINE CONTROL SYSTEM -<br />
INTRODUCTION TO SYSTEM FUNCTION<br />
1. IDLE SPEED CONTROL.<br />
(a) Idle speed control function refers to system control of engine speed with the throttle valve closed. The<br />
system makes the actual speed consistent with the target idle speed by controlling idle parameters.<br />
(b) The system applies the idle air control motor and realizes high precision idle speed control.<br />
2. AIR METERING OF SPEED-DENSITY METHOD (INTAKE MANIFOLD PRESSURE/ TEMPERATURE<br />
SENSOR).<br />
With intake temperature sensor and intake manifold pressure sensor, ECM calculates and defines the<br />
air quantity entering the cylinder. Furthermore, ECM allows air/fuel ratio to meet the requirements of<br />
various working conditions by controlling the fuel supply.<br />
3. CYLINDER DETECTION SEQUENCE CONTROL.<br />
In order to realize engine sequence control, the system applies intake pressure cylinder detection<br />
technology. The intake pressure sensor is installed near the air inlet of the intake manifold for 4<br />
cylinders. At the moment, when the inlet valve opens, there is an instantaneous pressure drop of which<br />
the value is around 1 kPa at the sensor. ECM detects the instantaneous pressure drop. After receiving<br />
the signal, ECM identifies compression Top Dead Centre (TDC) signal through the software analysis<br />
and processing.<br />
4. CLOSED LOOP CONTROL.<br />
The system applies closed loop control for the engine fuel supply and idle speed. The advantage of<br />
closed loop control is that the system effectively eliminates the difference between the system and<br />
relevant mechanical parts due to the manufacture and usage wear, which enhances the integrated<br />
coherence of the whole vehicle and reduces the emission.<br />
5. GROUPING CONTROL.<br />
The system divides the engine cylinders into two groups of 1-4 and 2-3 which control the ignition<br />
respectively. The grouping control optimizes and simplifies the system structure. Ignition timing and fuel<br />
injection control (crankshaft position sensor) systems determine crankshaft position and measure<br />
engine speed according to 58X gear signal, which controls the engine ignition and fuel injection timing<br />
precisely. The opening and closing of the power transistor control the continuity of the primary current in<br />
the ignition coils. The ignition timing control is aimed to obtain the optimal ignition time so as to meet<br />
the requirements of various working conditions of the engine. ECM determines the ignition time<br />
according to the engine speed, intake vacuum degree, engine cooling water temperature and<br />
atmospheric pressure.<br />
11A-7<br />
6. SELF-DIAGNOSIS.<br />
(a) The system fault self-diagnosis is an essential function for the engine control system. When one or<br />
several parts in the system operate abnormally, the system will inform the vehicle owner to perform<br />
necessary check and repair timely with fault indicator lamp ON. When the fault occurs, the system can<br />
also control the engine operation with temporary emergency mode, so as to ensure the owner can drive<br />
the vehicle to repair.<br />
(b) When certain sensor and actuator is detected abnormal, the engine fault inspection lamp turns on to<br />
remind the driver.<br />
(c) When certain sensor and actuator is detected abnormal, the fault code corresponding to the fault will be<br />
exported.<br />
(d) RAM data related to the sensor and actuator in ECM can be read by fault diagnostic apparatus. In<br />
addition, in certain situation, the actuator can be forcibly driven.<br />
7. OVERVOLTAGE PROTECTION.<br />
When the voltage of the charging system is too high caused by the fault, the system will go to the<br />
protection status to restrict the engine speed to avoid the ECM damage.<br />
8. AIR CONDITIONING COMPRESSOR CONTROL.<br />
When the A/C switch is on, the system will receive a A/C request signal and make preparations for<br />
operating the A/C system based on engine working condition. And then switch on the A/C compressor.<br />
The system will switch on or switch off the A/C according to the protection demand for air-conditioner.<br />
To ensure the power output and protect the engine, the system will cut off the A/C system under<br />
specified working condition.<br />
9. THREE-WAY CATALYTIC CONVERTER.<br />
The function of three-way catalytic converter is to convert harmful exhaust gas from the engine to<br />
harmless gas to exhaust to the atmosphere. The internal structure of three-way catalytic converter<br />
applies the cellular pipeline design. The cellular pipeline wall has precious metal coating on it, including<br />
palladium, rhodium, platinum etc, which acts as catalytic reaction media. The three-way catalytic<br />
converter will cause 3% - 5% of the power consumption to the engine.<br />
10. OVERHEAT SYSTEM PROTECTION FUNCTION FOR THE THREE-WAY CATALYTIC CONVERTER.<br />
The system predicts the rising trend of the engine exhaust temperature according to actual working<br />
condition of the engine and reduces the engine combustion temperature by timely controlling the air/<br />
fuel ratio, so as to protect the three-way catalytic converter.<br />
11. CONTROL OF THE COOLING FAN.<br />
(a) The vehicle is equipped with a silicon oil fan and an electronic fan.<br />
(b) Electrical fan control function: ECM determines to switch on various fans according to the engine<br />
coolant temperature. ECM also judges the temperature meets the condition for switching on the airconditioner<br />
or not, so as to reduce the engine internal power consumption accordingly..<br />
11A-8 ENGINE CONTROL SYSTEM -<br />
BASIC PRINCIPLE<br />
1. PRINCIPLE OF START CONTROL.<br />
(a) When turning the ignition switch on, the fuel pump will stop after running for 1.5 seconds.<br />
(b) When the engine starts to rotate, the fuel pump will start to operate after ECM detected 2 valid 58X<br />
signals.<br />
(c) The fuel pump stops operating 0.8 seconds after the engine speed disappears (the analogue signal is<br />
easy to be disturbed).<br />
(d) Pre-injection: The pre-injection only injects once during the normal start process (if the fuel is absorbed<br />
by the carbon deposition, the mixture dilutes, which makes it difficult to start).<br />
(e) Preliminary stage for starting: The intake manifold internal pressure is displayed as ambient<br />
atmospheric pressure. After the throttle valve closed, ECM specifies a fixed parameter according to the<br />
start temperature.<br />
(f) During the start process, the fuel injection quantity varies according to the change of the engine coolant<br />
temperature. The ignition advance angle also adjusts continually and changes with the engine coolant<br />
temperature, the intake air temperature and the engine speed.<br />
(g) End of the start process: When the engine speed exceeds 600 RPM, the start working condition ends.<br />
2. PRINCIPLE OF FUEL INJECTION CONTROL.<br />
(a) ECM controls the injector driving time and the injection timing, which enables the engine to obtain the<br />
mixture with optimal air/fuel ratio under various working conditions.<br />
(b) Each cylinder is equipped with an injector at the air inlet. The fuel pump in the fuel tank pumps out the<br />
fuel and delivers the fuel to the fuel high pressure rail. The fuel pressure regulator keeps the injection<br />
pressure stable. The injector injects the fuel directly to the air passage of each cylinder. During each<br />
working cycle (when the crankshaft rotates twice) of the cylinder, each cylinder injects the fuel once (the<br />
injection sequence is 1 - 3 - 4 - 2). This injection type is called as sequential injection.<br />
(c) When the engine operates under cold or high-load condition, ECM performs open loop control to supply<br />
dense mixture, so as to keep good performance. When the engine operates under the normal working<br />
condition (medium or small load), ECM performs closed loop control via the signal fedback by oxygen<br />
sensor to obtain optimal air/fuel ratio, which enables the three-way catalytic converter to get the optimal<br />
purifying effect.<br />
(d) Inject pulse width control<br />
A/F modify<br />
Signal Input ECM Control Output<br />
Closed loop feedback modify<br />
Intake manifold absolute pressure<br />
Air charging temperature<br />
Air charging efficiency<br />
Self-learning modify<br />
Power supply modify<br />
Exhaust cycle<br />
Accelerate deepen<br />
Decelerate fuel reduction<br />
Decelerate fuel cut<br />
Injector parameter<br />
Calculate fuel charge<br />
Inject pulse width<br />
3. CONTROL SIGNAL DESCRIPTION<br />
Modified Item<br />
Content<br />
11A-9<br />
Air/fuel ratio<br />
Closed loop feedback<br />
correction<br />
• Start air/fuel ratio.<br />
• Air/fuel ratio while engine is running.<br />
• Air/fuel ratio at low engine coolant temperature.<br />
• Air/fuel ratio at normal engine coolant temperature.<br />
• Theoretical air/fuel ratio.<br />
• Enriched air/fuel ratio.<br />
• Overheat protection air/fuel ratio.<br />
• Control the actual air/fuel ratio around the theoretical air/fuel ratio via the<br />
feedback signal from the oxygen sensor.<br />
Intake manifold pressure • Read directly via the MAP mounted on the intake manifold.<br />
Self-learning • Modify the engine internal slow change due to long time operation.<br />
Power voltage<br />
• When the battery voltage changes, the voltage modification can ensure the<br />
correct fuel injection quantity.<br />
Acceleration enrichment<br />
Deceleration dilution<br />
Deceleration cutoff<br />
• When ECM detects the intake manifold pressure and the opening value of the<br />
throttle valve increases greatly, the fuel injection quantity is increased to avoid<br />
the engine mixture dilutes momentarily, so as to improve the power<br />
performance.<br />
• When the system detects the vehicle is under deceleration status, it controls<br />
the fuel cutoff to reduce the emission and fuel consumption.<br />
• When the engine speed is above the setting value, fuel cutoff starts.<br />
• When a fault occurs in the ignition system, the fuel cuts off.<br />
Fuel injection parameter • It provides the relation between the engine and the fuel injection quantity.<br />
(a) Modification for the engine mixture:<br />
• Partial load control of the engine is closed loop fuel control at the normal working temperature. Then<br />
the system modifies fuel injection quantity via ECM according to the feedback voltage signal from the<br />
oxygen sensor, so as to adjust the mixture concentration to around the theoretical air/fuel ratio, which<br />
ensures the conversion efficiency of the harmful emission gas by the three-way catalytic converter<br />
reaches the optimal status while ensuring good fuel economy.<br />
• When the engine operates with full-load within the normal working temperature range, it applies the<br />
open loop fuel control. At this time, in order to ensure the engine obtains the optimal power output, the<br />
system will control the fuel injection quantity with a thick air/fuel ratio. Furthermore, with the premise<br />
that no engine knock occurs, the engine will increase the ignition advance angle moderately.<br />
• The system will also control the exhaust gas temperature using the exhaust gas temperature<br />
mathematical model established during calibration, so as to protect the engine and the three-way<br />
catalytic converter. The system determines the full-load condition of the engine according to the signal<br />
supplied by the throttle valve position sensor. When the throttle valve opening is above 80% ~ 90%, the<br />
system considers the engine goes to the full-load status. When the driver presses the accelerator pedal<br />
to accelerate the vehicle, the system will increase the fuel injection quantity moderately to ensure the<br />
power demand when the engine accelerates. The increased fuel injection quantity goes a direct<br />
proportion with the changing rate of the throttle valve opening. When accelerating, ECM will retard the<br />
ignition advance angle moderately, then recover step by step. The aim is to avoid impacting to the drive<br />
train because the torque increases too rapid when the engine accelerates sharply.<br />
11A-10 ENGINE CONTROL SYSTEM -<br />
• When the acceleration working condition is near the engine full-load, the system will automatically<br />
switch off the A/C system temporarily, so as to ensure the engine power output well when accelerating.<br />
Whatever the situation, when the engine speed exceeds the highest speed specified in the system, the<br />
system will cut off the fuel supply to restrict the speed increasing, so as to protect the engine and avoid<br />
the vehicle skidding. When the engine speed returns within specified in the system, the system will<br />
restore the fuel supply immediately.<br />
4. PRINCIPLE OF IGNITION CONTROL.<br />
(a) Start: The engine applies a fixed ignition advance angle when starting, which allows the gas in the<br />
cylinder to ignite and provide the positive torque. When the engine speed increases to certain speed,<br />
ECM caculates the ignition advance angle according to the input signal.<br />
(b) Ignition advance angle control.<br />
ECT modify<br />
IAT modify<br />
Elevation modify<br />
Idle modify<br />
Signal Modify ECM Output Control<br />
Main ignition angle<br />
Decelerate fuel reduction modify<br />
Accelerate modify<br />
Accelerate deepen modify<br />
A/C modify<br />
Calculate ignition advance angle<br />
Ignition advance angle<br />
(c) Main ignition advance angle: When the engine temperature reaches the normal value, the main ignition<br />
angle with the throttle valve opening is usually the minimum ignition angle at the optimal torque point.<br />
When the throttle valve closes, the ignition angle should be reduced to obtain the idle speed stability.<br />
(d) Correction of the ignition advance angle:<br />
• Acceleration correction: When the vehicle accelerates, ECM detects the knock and corrects the ignition<br />
advance angle until the knock disappears. Furthermore, it is also used to reduce the engine speed<br />
fluctuation caused by the drive train torsion.<br />
• Power enrichment correction: To obtain better power and torque near the exterior feature point, the air/<br />
fuel ratio is enriched to the thinnest air/fuel ratio with the best torque.<br />
• Deceleration cutoff correction: When the deceleration cutoff exits, correct the ignition advance angle to<br />
get a stable transition.<br />
• A/C correction: Switch off the A/C when the engine is idle. Correct the ignition advance angle, which<br />
allows the speed to get a stable transition.<br />
5. PRINCIPLE OF IDLE CONTROL.<br />
(a) Idle control:<br />
• Control the air flow in the bypass of the throttle valve according to the idle condition and the engine idle<br />
load to maintain the idle speed at the optimal speed. According to the engine coolant temperature and<br />
the A/C load, ECM drives the IAC motor to make the engine operate under the preset target idle speed.<br />
In addition, when the engine operates at idle speed, turn on or turn off the A/C switch. The IAC motor<br />
will regulate the air flow in the bypass according to the engine load to avoid idle speed unstable .<br />
11A-11<br />
Calculate the target idle speed.<br />
Basic target idle speed<br />
Input ECM Output Control<br />
Voltage compensation<br />
Vehicle speed compensation<br />
Fan compensation<br />
Calculate target idle speed<br />
Target idle speed<br />
Headlamp compensation<br />
A/C compensation<br />
Deceleration adjustment<br />
• Voltage compensation: When the voltage is below 12V, the system will automatically increase the target<br />
idle speed to increase the electrical energy production of the generator.<br />
• A/C compensation: Switch on the A/C when parking the vehicle at idle speed. To compensate the<br />
power loss of the compressor, the target idle speed increases by 150 RPM.<br />
• Headlamp compensation: After switching on the low beam, the target idle speed increases by 50 RPM<br />
to compensate the electricity loss.<br />
• Fan compensation: When the coolant temperature increases and the fan operates, the idle speed<br />
increases by 50 RPM to compensate the electricity loss for the fan operation.<br />
(c) Idle speed control parameters:<br />
• Control of idle air flow.<br />
• Control of fuel injection quantity.<br />
• Control of ignition timing.<br />
(d) Idle speed design control timing:<br />
• Calibration of idle stability.<br />
• Calibration of acceleration working condition.<br />
• Calibration of deceleration working condition.<br />
• Deceleration cutoff.<br />
• Calibration for the fuel supply under engine transient transition working condition.<br />
• Calibration of constant speed driving.<br />
• Calibration of increasing and reducing the mechanical and electricity load.<br />
(e) Decisive factors for the target idle speed:<br />
• When the coolant temperature is low, the system provides a high target idle speed to accelerate the<br />
warm-up.<br />
• When the additional load (e.g. various electrical appliances such as the headlamp, A/C, cooling fan<br />
etc.) opens, the system will raise the idle speed to compensate the increased load and keep the idle<br />
speed stable.<br />
11A-12 ENGINE CONTROL SYSTEM -<br />
6. PRINCIPLE OF CARBON CANISTER SOLENOID VALVE CONTROL.<br />
(a) Used for controlling the air flow of carbon canister cleaning. The carbon canister is controlled by ECM<br />
sending the duration and frequency for the electrical impulse (duty cycle) through integrated<br />
computation according to a series of signals including engine load, engine coolant temperature, and<br />
engine speed etc. When too much gasoline vapor is accumulated in the activated carbon canister, it will<br />
cause the gasoline leakage, which pollutes the environment. Therefore, the effect of carbon canister<br />
solenoid valve is to open at the proper time to allow the excess gasoline vapor to enter the intake pipe<br />
after mixing with the air sufficiently in the carbon canister to involve in the combustion.<br />
(b) The carbon canister will not work in the following conditions:<br />
• During a period after the cold start of the engine.<br />
• When the cooling water temperature is low.<br />
• During the engine idle operation period.<br />
• During the engine big load period.<br />
• When the important sensors of the system have fault.<br />
MAIN COMPONENTS<br />
11A-13<br />
11A-14 ENGINE CONTROL SYSTEM -<br />
SYSTEM COMPONENTS DESCRIPTION<br />
Component Summary Quantity Function<br />
ECM 16 bit CPU 1<br />
Upstream oxygen sensor With heated 1<br />
Downstream oxygen sensor With heated 1<br />
MAP sensor Piezoelectric type 1<br />
ECM optimization control system<br />
depends on the sensor signal.<br />
Check oxygen concentration in<br />
exhaust.<br />
ECM judges whether the TWC is<br />
good comparing the upstream with<br />
downstream oxygen sensor signal.<br />
Check the air inlet quantity and<br />
BTDC.<br />
CKP sensor Magnetron induction coil type 1 Check CKP and engine RPM.<br />
Injector 4 hole type 4<br />
Inject fuel depends on the sensor<br />
Idle air control motor Electromagnetic coil type 1 Control air inlet.<br />
Carbon solenoid valve Electromagnetic type 1<br />
Control the exhaust depending on<br />
the digital pulse wave from ECM.<br />
3- lines type carbon film<br />
resistor sliding indicator<br />
1 Check the open of throttle.<br />
ECT sensor NTC thermal resistance type 1 Check ECT.<br />
IAT sensor NTC thermal resistance type 1 Check IAT.<br />
Vehicle speed sensor Hall effect type 1 Check vehicle speed.<br />
Ignition coil Electromagnetic coil type 1 Ignite mixed gas.<br />
Fuel pump Electromagnetic type pump 1<br />
Supply the enough pressure fuel<br />
for system.<br />
ENGINE CONTROL MODULE (ECM)<br />
PRINCIPLE<br />
11A-15<br />
1. ECM DESCRIPTION.<br />
(a) ECM is the electric engine control center with the micro<br />
processor as the core that having sensor signal input<br />
interface and the executor drive circuit. The ECM<br />
receives and treats the engine status signal that inputted<br />
from all sensors, sends control signal to the executor to<br />
drive the engine running in accordance with the preset<br />
procedures so as to make the engine run under best<br />
status, ensure good power capability, fuel economy and<br />
exhaust capability.<br />
(b) Normal operating voltage: 9 ~ 16V.<br />
(c) Overvoltage protection: +24V/-12V < 60 s.<br />
(d) ECM has self-protection function. It may result the<br />
ignition failure during repair and it will resume normal<br />
after replacement of ECM. In fact, the ECM doesn’t get<br />
damaged, but just self-protection mode. ECM will<br />
resume normal after certain time period.<br />
11A-16 ENGINE CONTROL SYSTEM - ENGINE CONTROL MODULE (ECM)<br />
2. DISCONNECT BATTERY NEGATIVE CABLE.<br />
When disconnecting or connecting the battery cables, please first turn off the ignition switch and<br />
lighting switch and completely loosen the cable nut. Do not pry up the cable when peforming these<br />
operations.<br />
3. REMOVE ECM MODULE.<br />
(a) Pull passenger seat forward.<br />
(b) Lift the covering behind the assistant driver seat , loosen<br />
the ECM locking knob.<br />
(c) Remove the ECM cover.<br />
Depress the connector locking tab, pull the latch upward<br />
to the end .<br />
Disconnect ECM connector.<br />
After disconnecting the connector, keep the connection<br />
away from dirt, water and other foreign materials.<br />
Remove 4 ECM mounting bolts.<br />
Remove ECM.<br />
11A-17<br />
• Disconnect battery negative cable first, wait at least<br />
1 minute, then remove ECM.<br />
• Take care not to impact ECM while removing the<br />
ECM.<br />
• Keep ECM away water during operation.<br />
• Be careful of the terminals of ECM.<br />
4. INSTALL ECM.<br />
Tighten 4 ECM mounting bolts.<br />
Torque: 19.6 N•m<br />
Pay attention to electrostatic protection when installation.<br />
Connect ECM connector.<br />
Pull the connector upward, be sure that it is installed in<br />
place properly .<br />
Install ECM cover and tighten the ECM cover locking<br />
knob.<br />
Cover the covering and push passenger seat back to its<br />
original position.<br />
5. CONNECT BATTERY NEGATIVE CABLE.<br />
11A-18 ENGINE CONTROL SYSTEM -<br />
ENGINE COOLANT TEMPERATURE<br />
ENGINE COOLANT TEMPERATURE SENSOR<br />
1. ENGINE COOLANT TEMPERATURE DESCRIPTION.<br />
(a) The Engine Coolant Temperature (ECT) sensor uses a<br />
thermistor to control the signal voltage to the Engine<br />
Control Module (ECM).<br />
(b) This ECT sensor is a 2-line type. Normally a 1-line type is<br />
to provide coolant temperature signal to the instrument.<br />
OVERHAUL<br />
11A-19<br />
2. OPEN THE ENGINE HOOD AND REMOVE THE<br />
COOLANT RESERVOIR PRESSURE CAP.<br />
Do not open the reservoir cap when the engine is hot. Such<br />
as coolant temperature should be reduced to 50 ° C (120 ° F)<br />
below, remove the reservoir cap. Otherwise, the cooling<br />
liquid or vapor emitting heat may cause personal injury.<br />
Drain coolant. (Refer to “Chapter 17A cooling - coolant,<br />
precaution”)<br />
3. RAISE THE VEHICLE, LOOSEN COOLANT DRAIN<br />
PLUG AT THE BOTTOM OF RADIATOR , THEN DRAIN<br />
Using a suitable container, collect the coolant. If do not<br />
reuse, dispose of coolant according to the local laws.<br />
4. REMOVE ECT SENSOR.<br />
(a) Loosen the clamp and remove the hose.<br />
Disconnect ECT connnector.<br />
Remove ECT sensor.<br />
• Clear the installation surface after removing.<br />
• Clear the sensor hole after removing.<br />
• Clear the thread of sensor after removing.<br />
.<br />
11A-20 ENGINE CONTROL SYSTEM -<br />
5. CHECK ECT SENSOR.<br />
(a) Dip the sensing part of ECT sensor into hot water. Using<br />
the multimeter, measure resistance of the sensor.<br />
(b) If the check result is not OK, replace it with a new one.<br />
0 ℃ 9098 ~ 9700 Ω<br />
10 ℃ 5494 ~ 5822 Ω<br />
20 ℃ 3420 ~ 3602 Ω<br />
30 ℃ 2184 ~ 2296 Ω<br />
Don’t let the water go into terminals. After checking, dry the<br />
sensor.<br />
6. INSTALL ECT SENSOR.<br />
(a) Install ECT sensor.<br />
Apply sealant to thread. The specified sealant: 3M NUT<br />
LOCKING PART or the equivalent.<br />
(b) Connect ECT sensor connector .<br />
Attach the hose and tighten the clamp.<br />
7. FILL COOLANT. (Refer to “Chapter 17A cooling - coolant, precaution”)<br />
8. CHECK COOLING SYSTME FOR COOLANT LEAKAGE.<br />
THROTTLE BODY<br />
THROTTLE BODY CLEANING<br />
1. CLEANING STEPS.<br />
(a) Start the engine and warm it up until the coolant is heated to 80 ℃ or higher. then stop the engine.<br />
(b) Remove the air intake hose from the throttle body.<br />
(c) Plug the bypass passage inlet (arrow) of the throttle body.<br />
Do not allow cleaning solvent to enter the bypass passage.<br />
11A-21<br />
Spray cleaning solvent into the valve through the throttle<br />
body intake port and leave it for approximately five<br />
minutes.<br />
Start the engine, accelerate it several times and then idle<br />
it for about one minute. if the idle speed becomes<br />
unstable (or if the engine stalls) due to the bypass<br />
passage being plugged, slightly open the throttle valve to<br />
keep the engine running.<br />
If the throttle valve deposits are not removed, repeat<br />
steps d and e.<br />
Unplug the bypass passage inlet.<br />
Connect the air intake hose.<br />
Use the scan tool to erase any diagnostic trouble code.<br />
Adjust the basic idle speed.<br />
If the engine hunts while idling after adjustment of the basic<br />
idle speed, keep the battery negative cable disconnected<br />
for 10 seconds or more, and then reconnect it and run the<br />
engine at idle for about 10 minutes after the engine is<br />
warmed up.<br />
11A-22 ENGINE CONTROL SYSTEM - THROTTLE BODY<br />
THE FIXED SPEED ADJUSTING SCREW (SAS) ADJUSTMENT<br />
1. SINCE FIXED SAS IS ADJUSTED AT FACTORY, PLEASE DO NOT ADJUST “FIXED SAS” IN<br />
NORMAL CASES UNLESS IT IS NECESSARY.<br />
2. IF “FIXED SAS” IS ROTATED RANDOMLY, PLEASE RE-ADJUST ACCORDING TO THE<br />
FOLLOWING STEPS:<br />
Loosen the tension of the acceleration cable.<br />
Loosen the "fixed SAS” lock nut.<br />
Turn the idle switch counterclockwise until the throttle<br />
valve closes.<br />
Screw the “fixed SAS” clockwise until the point (i.e. the<br />
position when throttle is started to be opened) of throttle<br />
rail is reached.<br />
Keep the “fixed SAS” from moving when tightening the<br />
lock nut.<br />
Adjust the acceleration cable tension.<br />
11A-23<br />
BASIC IDLE SPEED ADJUSTMENT<br />
1. THE STANDARD IDLE SPEED HAS BEEN ADJUSTED WITH THE SPEED ADJUSTING SCREW<br />
(SAS) BY THE MANUFACTURER, AND THERE SHOULD BE NO NEED FOR RE-ADJUSTMENT.<br />
2. IF THE ADJUSTMENT HAS BEEN CHANGED BY MISTAKE, THE IDLE SPEED MAYBE COME TOO<br />
HIGH OR TOO LOW WHEN LOADS A/C, DEFOGGER, ETC. ARE PLACED ON THE ENGINE. IF<br />
THIS OCCURS, ADJUST BY THE FOLLOWING PROCEDURE.<br />
If make the adjustment, it should be made after confirming that the spark plugs, the injectors, the idle<br />
air control motor, compression, etc., are all normal.<br />
(a) Place the car in good condition before the inspection and adjustment.<br />
(c) Connect the scan tool to the Data Link Connector (DLC).<br />
(d) Start the engine and run at idle speed.<br />
(e) Check the idle speed.<br />
Standard value: 750 ± 50 RPM<br />
• The engine speed may be 20 to 100 RPM lower than indicated above for a new vehicle, but this<br />
is normal and no adjustment is necessary.<br />
• If the engine stalls or the engine speed is low even though the vehicle has been driven<br />
approximately 500 km (300 mile) or more, it is probable that deposits are adhered to the throttle<br />
valve, clean it.<br />
If it is not within the standard value range, turn the Speed<br />
Adjusting Screw (SAS) to make the necessary adjustment.<br />
If SAS gets to bottom completely, the idle speed is still more<br />
than standard value, then check if “fixed SAS” was rotated.<br />
If yes, re-adjust “fixed SAS”.<br />
• Turn the ignition switch OFF.<br />
• Disconnect the scan tool.<br />
• Start the engine again and let it idle for about 10 minutes.<br />
Check that the idling condition is normal.<br />
11A-24 ENGINE CONTROL SYSTEM - THROTTLE BODY<br />
2. LOOSEN COOLANT DRAIN PLUG AT THE BOTTOM OF<br />
RADIATOR , THEN DRAIN COOLANT.<br />
(b) Rotate the driver seat and open engine compartment<br />
4. REMOVE AIR INTAKE HOSE. (Refer to “Chapter 14A intake air - intake air hose, replacement”)<br />
5. REMOVE THROTTLE BODY.<br />
(a) Disconnect IAC connector.<br />
Disconnect TPS connector.<br />
11A-25<br />
Loosen accelerator cable locking nut on the throttle body<br />
and remove accelerator cable.<br />
Remove 2 preheating hoses from throttle body.<br />
Remove 4 throttle body mounting bolts.<br />
(f) Remove throttle body.<br />
Check the seal gasket between throttle body and intake<br />
manifold for damage and replace it as necessary.<br />
11A-26 ENGINE CONTROL SYSTEM - THROTTLE BODY<br />
6. REMOVE AIR INTAKE HOSE. (Refer to “Chapter 14A intake air - intake air hose, replacement”)<br />
7. INSTALL THROTTLE BODY.<br />
(a) Tighten 4 throttle body mounting bolts .<br />
Torque:15 ~ 25 N•m<br />
Connect 2 preheating hoses to throttle body.<br />
Connect idle air control motor connector.<br />
Connect TPS connector.<br />
11A-27<br />
Install accelerator cable and keep cable at the proper<br />
tension, then tighten the locking nut.<br />
8. INSTALL AIR INTAKE HOSE. (Refer to “Chapter 14A intake air - intake air hose, replacement”)<br />
9. PUT DOWN ENGINE COMPARTMENT COVER AND LOCK IT.<br />
10. FILL COOLANT. (Refer to “Chapter 17A cooling - coolant, replacement”)<br />
11A-28 ENGINE CONTROL SYSTEM - IDLE AIR CONTROL MOTOR<br />
IDLE AIR CONTROL MOTOR<br />
1. IDLE AIR CONTROL MOTOR DESCRIPTION.<br />
(a) The idle air control motor is essentially one micro motor.<br />
since the motor will revolve in various directions when<br />
the motor coil is supplied with current in various<br />
directions. The motor revolution shaft will drive the<br />
moving of the leading screw so as to control the open<br />
extent of the valve indirectly. ECM will send the<br />
digitalized square wave signal to control the positive<br />
rotation and the reverse rotation of the motor so as to<br />
control the stroke of the idle air control motor.<br />
11A-29<br />
ON-VEHICLE INSPECTION<br />
1. OPERATING SOUND INSPECTION.<br />
(a) Check that coolant temperature of engine is below 20 ℃ .<br />
If coolant temperature of engine is above 20 ℃ , remove the harness connector of engine coolant temperature<br />
sensor, and use the less than 20 ℃ sensor for connection.<br />
(b) Check that when ignition switch is changed into the ON position (do not start engine), the operating<br />
sound of the IAC motor can be heard over the IAC motor.<br />
(c) If an operating sound can be heard, check the IAC motor drive circuit. If the circuit is good, a defective<br />
IAC motor or ECM is suspected.<br />
2. CHECK ENGINE RPM.<br />
(c) Connect the scan tool to the Data Link Connector (DLC) - use the most current software available.<br />
(e) Select the item ,perform the idle air control motor test.<br />
(f) When the scan tool control the rotation of expansion of the IAC motor, the engine RPM changes from<br />
high to low in synchronism (vibration can be felt when touching the IAC motor).<br />
(g) If it is not OK, check IAC motor control harness or connector. If harness or connector is OK, check IAC<br />
motor or ECM.<br />
3. CHECK IDLE AIR CONTROL MOTOR STEPS.<br />
(e) Select the item .”<br />
Displayed Item Detection Condition Specified Condition<br />
Idle air control motor<br />
• Accessories: OFF<br />
• Transmission: N<br />
• Engine: idle<br />
• A/C turns ON, A/C<br />
should works<br />
If it is not OK, check idle air control motor, harness, connector or ECM.<br />
Add 10 ~ 70 steps<br />
11A-30 ENGINE CONTROL SYSTEM - IDLE AIR CONTROL MOTOR<br />
3. REMOVE IDLE AIR CONTROL MOTOR.<br />
(a) Disconnect idle air control motor connector.<br />
Remove 2 idle air control motor retaining bolts.<br />
Remove idle air control motor.<br />
• Clear surface after removing.<br />
• Clear the path of the idle.<br />
11A-31<br />
4. CHECK IDLE AIR CONTROL MOTOR COIL RESISTANCE.<br />
(a) Connect special tool (for test).<br />
(b) Check resistance between terminal A and B of idle air<br />
control motor connector.<br />
Standard resistance: 28 ~ 33 Ω (20 ℃ )<br />
(c) Check resistance between terminal C and D of idle air<br />
(d) If it is not OK, replace it with a new one.<br />
5. INSTALL IDLE AIR CONTROL MOTOR.<br />
(a) Install idle air control motor and tighten 2 idle air control<br />
motor retaining bolts.<br />
• Do not apply any axially type of force to press or pull<br />
out the axle.<br />
• The axle must be in the place of the retreating before<br />
the idle air control motor being installed into the<br />
throttle body.<br />
• After removing battery or ECM, perform the idle air<br />
control motor self-learning.<br />
6. THE IAC MOTOR SELF-LEARNING.<br />
(a) Turn the ignition switch OFF, do not start at once. After 5 seconds, start it again.<br />
7. PUT DOWN ENGINE COMPARTMENT COVER AND LOCK IT.<br />
11A-32 ENGINE CONTROL SYSTEM - THROTTLE POSITION SENSOR (TPS)<br />
THROTTLE POSITION SENSOR (TPS)<br />
1. THROTTLE POSITION SENSOR DESCRIPTION.<br />
Throttle Position Sensor (TPS) is used to provide throttle<br />
angle, angle speed and engine idle position information<br />
to the ECM. Based on this the ECM can obtain the<br />
engine load information, operating mode (such as start,<br />
idle, reverse towing, partial load and full-load) and<br />
acceleration & deceleration information. This sensor is of<br />
3-line type and the ECM will check the throttle open<br />
extent by monitoring the voltage variation.<br />
The throttle position sensor is comprised of carbon film<br />
resistance and slide indicator.<br />
The sensor slide indicator connects with the throttle and<br />
rotates following the shaft. When the throttle open extent<br />
changes following the accelerator pedal, the position of<br />
the slide indicator will also change on the carbon film<br />
resistance, at that moment the resistance output will also<br />
change, which reflects the open extent of the throttle<br />
indirectly.<br />
11A-33<br />
1. START THE ENGINE AND WARM IT TO NORMAL OPERATING TEMPERATURE.<br />
2. TURN THE IGNITION SWITCH OFF.<br />
3. CONNECT THE SCAN TOOL TO THE DATA LINK CONNECTOR (DLC) - USE THE MOST<br />
CURRENT SOFTWARE AVAILABLE.<br />
4. TURN THE IGNITION SWITCH ON.<br />
5. SELECT THE ITEM BELOW.<br />
• Engine stop<br />
Idle position 0.3 ~ 1 V (0%)<br />
Open throttle slowly<br />
Directly proportional with<br />
the open degree<br />
Open widely 4.5 ~ 5.5 V (100%)<br />
6. IF IT IS NOT OK, CHECK TPS, HARNESS CONNECTORS AND ECM.<br />
11A-34 ENGINE CONTROL SYSTEM - THROTTLE POSITION SENSOR (TPS)<br />
3. REMOVE TPS.<br />
(a) Disconnect TPS connector.<br />
Remove 2 TPS retaining bolts.<br />
Remove TPS.<br />
Clear the surface after removing.<br />
11A-35<br />
4. CHECK TPS RESISTANCE.<br />
(a) Measure the resistance between termal 1 and termal 2 of<br />
(a) Measure the resistance between termal 2 and termal 3 of<br />
Terminal 1 and 2 • Resistance: 3.5 ~ 6.5 Ω (20 ℃ )<br />
Terminal 1 and 3 or<br />
Terminal 2 and 3<br />
• Open throttle from idle position to<br />
open wide.The output value is<br />
proportional change to the open<br />
degree.<br />
If the resistance is out of the range and the value<br />
changes unsteadily, replace it.<br />
5. INSTALL TPS.<br />
(a) Install TPS and tighten 2 TPS retaining bolts.<br />
6. PUT DOWN ENGINE COMPARTMENT COVER AND LOCK IT.<br />
11A-36 ENGINE CONTROL SYSTEM -<br />
MANIFOLD ABSOLUTE PRESSURE/<br />
INTAKE TEMPERATURE SENSOR<br />
MANIFOLD ABSOLUTE PRESSURE/INTAKE TEMPERA-<br />
TURE SENSOR<br />
1. MANIFOLD ABSOLUTE PRESSURE/INTAKE TEMPERATURE<br />
SENSOR DESCRIPTION.<br />
(a) The engine control system adopted speed-density air<br />
measurement method to check the air intake volume into<br />
the engine so as to control the fuel injection pulse width<br />
for the precise control of engine power output.<br />
Meanwhile, this system adopted intake pressure cylinder<br />
determination technology and the intake air sensor is<br />
installed near the inlet opening of cylinder 4 intake<br />
manifold. At the moment when the throttle is opened,<br />
there will be one instantaneous pressure drop at the<br />
sensor, of which the value is about 1 kPa. When the<br />
ECM detected and received this instantaneous pressure<br />
drop. The ECM will determine the compression upper<br />
dead center signal after software diagnosis treatment.<br />
(b) Intake air temperature sensor is a Negative Temperature<br />
Coefficient (NTC) of resistance, with the intake air<br />
temperature increases resistance decreases, the engine<br />
ECM contrast through the internal circuitry to detect an<br />
intake air temperature changes.<br />
11A-37<br />
• Engine: running<br />
IAT: -20 ℃ -20 ℃<br />
6. TURN DIGITAL MULTIMETER TO VOLTAGE RANGE.<br />
CHECK VOLTAGE OF MAP SENSOR BETWEEN<br />
TERMINAL A OR D AND GROUND.<br />
(a) When engine runs at idle, terminal 3 is 5 V, terminal 4 is<br />
1.3 V.<br />
(b) When engine runs unload, open throttle slowly, the signal<br />
of terminal 4 is changed little.<br />
(c) Open throttle quickly, the signal of terminal 4 is to about<br />
4 V, then drop to 1.5 V.<br />
(d) Turn multimeter to voltage range. Black pin to ground,<br />
red pin to terminal 2 of the IAT sensor. Check IAT signal.<br />
IAT: 0 ℃ 3.2 ~ 3.8V<br />
AN<br />
If it is not OK, check MAP/IAT sensor, harness or ECM.<br />
11A-38 ENGINE CONTROL SYSTEM -<br />
3. REMOVE MAP/IAT SENSOR CONNECTOR.<br />
(a) Disconnect MAP/IAT sensor connector.<br />
(b) Remove MAP/IAT sensor retaining bolt.<br />
Remove MAP/IAT sensor.<br />
Clear surface after removing MAP/IAT sensor.<br />
4. CHECK IAT SENSOR RESISTANCE.<br />
(a) Turn digital multimeter to Ohm range. Check resistance<br />
between terminal 2 and 3 of sensor. Using a hairdryer,<br />
blow air to sensor ( IMPORTANT:do not get too close to<br />
the sensor ). Inspect the change of the value, the value<br />
should decline.<br />
(b) If it is not OK, replace it.<br />
11A-39<br />
5.3 ~ 6.7 kΩ<br />
IAT: 10 ℃<br />
IAT: 30 ℃<br />
2.3 ~ 3.0 kΩ<br />
1.0 ~ 1.5 kΩ<br />
0.30 ~ 0.42 kΩ<br />
5. INSTALL MAP/IAT SENSOR.<br />
(a) Tighten MAP/IAT sensor retaining bolt.<br />
(b) Connect MAP/IAT sensor connector.<br />
Do not use any impact tools (such as a hammer, etc.) to<br />
knock sensor into mounting hole.<br />
11A-40 ENGINE CONTROL SYSTEM - KNOCK SENSOR<br />
KNOCK SENSOR<br />
1. PRINCIPLE OF KNOCK SENSOR.<br />
Knock sensor is one vibrating acceleration sensor that<br />
installed on the engine cylinder body, normally between<br />
cylinder 2 and cylinder 3 to facilitate the engine knock<br />
balance.<br />
By means of the vibrating frequency signal output from<br />
the knock sensor, the ECM will judge for engine knock<br />
after the ECM internal wave filter.<br />
In case of the detection of the knock signal, the ECM will<br />
reduce gradually till the elimination of the knock and then<br />
resume gradually till the knock threshold.<br />
Above steps will be repeated again and again.<br />
11A-41<br />
2. RAISE AND SUPPORT VEHICLE.<br />
3. REMOVE KS.<br />
(a) Remove 4 retaining bolts on intake manifold lower bracket<br />
Disconnect KS connector.<br />
Remove knock sensor retaining bolt.<br />
• Clear the surface after removing.<br />
• Don’t contact all kinds of liqulds. For example: oil,<br />
coolant, brake fluid.<br />
4. CHECK KS.<br />
(a) Measure the resistance according to the value in the<br />
Sensor Terminal Terminal Resistance (20 ℃ )<br />
1 2<br />
1 Ground<br />
2 Ground<br />
> 1 MΩ<br />
If the check result is not OK, replace it.<br />
11A-42 ENGINE CONTROL SYSTEM - KNOCK SENSOR<br />
5. INSTALL KNOCK SENSOR.<br />
(a) Tighten knock sensor retaining bolt.<br />
Torque: 15 ~ 25N•m<br />
• Confirm the KS correct direction.<br />
• install it by applying pressure. Any impact tool is not<br />
allowed.<br />
• The metal surface should be pressed against the cylinder<br />
body. Any type of washer is not allowed.<br />
• Don’t let the signal cable resonance. To avoid it<br />
brokn.<br />
(b) Connect knock sensor connector.<br />
6. INSTALL INTAKE MANIFOLD LOWER BRACKET.<br />
(a) Tighten 4 retaining bolts on intake manifold lower<br />
bracket.<br />
7. INSTALL THE INTAKE MANIFOLD. (Refer to “Chapter 14A intake air - intake manifold, replacement”)<br />
CKP SENSOR<br />
11A-43<br />
1. CRANKSHAFT POSITION SENSOR DESCRIPTION.<br />
(a) The 58X reference signal is produced by the Crankshaft<br />
Position (CKP) sensor. The Engine Control Module<br />
(ECM) uses the 58X reference signal to caculate engine<br />
RPM and CKP. The ECM constantly monitors the<br />
number of pulses on the 58X reference circuit and<br />
compares them with the number of MAP signal being<br />
received.<br />
11A-44 ENGINE CONTROL SYSTEM - CKP SENSOR<br />
3. REMOVE CKP.<br />
(a) Disconnect CKP connector.<br />
(b) Remove CKP sensor retaining bolt on flywheel housing .<br />
Remove knock sensor.<br />
Clear the surface after removing knock sensor.<br />
4. CHECK CKP SENSOR.<br />
(a) Turn digital multimeter to Ohm range, connect two<br />
probes to terminal 2 and 3 of sensor. Check resistance.<br />
Standard resistance: 560 Ω ± 10% (20 ℃ )<br />
(b) If the check result is not normal, replace it.<br />
11A-45<br />
5. INSTALL CKP SENSOR.<br />
• Apply a layer of preventative oil on the O-ring of the<br />
CKP sensor.<br />
• Do not use any impact tools (such as a hammer, etc.)<br />
to knock sensor into mounting hole.<br />
(a) Insert CKP sensor into the mounting hole by turning .<br />
Tighten CKP sensor retaining bolt.<br />
Connect the CKP sensor connector..<br />
6. PUT DOWN DRIVER SEAT AND LOCK IT.<br />
11A-46 ENGINE CONTROL SYSTEM - UPSTREAM OXYGEN SENSOR<br />
UPSTREAM OXYGEN SENSOR<br />
1. UPSTREAM OXYGEN SENSOR DESCRIPTION.<br />
This sensor is used to provide the excess oxygen<br />
information after the injected fuel in the cylinder has<br />
passed the full combustion in the sucked air. By means<br />
of this information, the ECM can perform the closed loop<br />
control upon the fuel quantity so that the 3 main toxic<br />
substances in the exhaust, which named Hydrocarbon<br />
(HC), Carbon Oxides (CO) and nitrogen oxides, can be<br />
converted and purified in the three-way catalytic<br />
converter.<br />
11A-47<br />
1. A/F: to be rich when<br />
acceleration<br />
2. A/F: to be lean when<br />
deceleration<br />
6. IF IT IS NOT OK, CHECK SENSOR, HARNESS AND ECM.<br />
Decelerate suddenly<br />
Accelerate suddenly<br />
Engine: 2500 RPM<br />
0.1 ~ 0.9 V<br />
11A-48 ENGINE CONTROL SYSTEM - UPSTREAM OXYGEN SENSOR<br />
3. REMOVE UPSTREAM OXYGEN SENSOR.<br />
(a) Disconnect upstream oxygen sensor connector.<br />
(b) Using wrench, remove upstream oxygen sensor .<br />
Remove the exhaust pipe after cooling completely.<br />
4. CHECK UPSTREAM OXYGEN SENSOR.<br />
(a) Turn digital multimeter to ohm range. Check resistance<br />
between terminal 3 and 4 of the sensor.<br />
Standard resistance: 9.6 ± 1.5 Ω (20 ℃ )<br />
5. INSTALL UPSTREAM OXYGEN SENSOR.<br />
Apply a layer of rust-proof oil on the thread.<br />
Install upstream oxygen sensor.<br />
Torque: 40 ~ 60 N•m<br />
Connect upstream oxygen sensor connector.<br />
6. LOWER THE VEHICLE.<br />
DOWNSTREAM OXYGEN SENSOR<br />
11A-49<br />
1. DOWNSTREAM OXYGEN SENSOR DESCRIPTION.<br />
(a) The purpose of the rear oxygen sensor is to check the<br />
oxygen concentration in the exhaust that passed threeway<br />
catalytic converter and the sensor will convert such<br />
signal to dot signal and transmit to the ECM. After the<br />
comparison of the signals of the upstream/downstream<br />
oxygen sensors, the ECM will judge if the three-way<br />
catalytic converter functions well.<br />
(b) The structure of downstream oxygen sensor is same as<br />
the upstream oxygen sensor.<br />
11A-50 ENGINE CONTROL SYSTEM - DOWNSTREAM OXYGEN SENSOR<br />
Downstream oxygen sensor<br />
• Engine: warm<br />
Engine: running<br />
About 0.1 V<br />
11A-51<br />
2. RAISE AND SUPPORT THE VEHCLE.<br />
3. REMOVE DOWNSTREAM OXYGEN SENSOR.<br />
(a) Disconnect downstream oxygen sensor connector.<br />
(b) Remove downstream oxygen sensor.<br />
4. CHECK DOWNSTREAM OXYGEN SENSOR.<br />
(a) Turn digital multimeter to ohm range, check resistance<br />
5. INSTALL DOWNSTREAM OXYGEN SENSOR.<br />
(a) Install downstream oxygen sensor.<br />
(b) Connect downstream oxygen sensor connector.<br />
11A-52 ENGINE CONTROL SYSTEM - CANISTER SOLENOID VALVE<br />
CANISTER SOLENOID VALVE<br />
1. CARBON CANISTER SOLENOID VALVE DESCRIPTION.<br />
The carbon canister solenoid valve is a kind of solenoid<br />
valve mechanism internally and contrilled by ECM. ECM<br />
will send digitalized square wave control pulse to control<br />
the open extent of the solenoid valve. The open extent of<br />
the carbon canister is different depending on the various<br />
engine operating modes. In case of the great load of<br />
engine or engine idle, the carbon canister solenoid valve<br />
doesn’t operation in order to ensure the engine power<br />
output well.<br />
11A-53<br />
5. CHECK THE ACTION OF CARBON CANISTER SOLENOID VALVE.<br />
(a) Use the “action test” function of the diagnostic apparatus.<br />
• Touch the fuel Evaporative Emission Control (EVAP) system carbon canister solenoid valve with hand.<br />
• Perform the action test of carbon canister solenoid valve with the “action test” function of the diagnostic<br />
apparatus.<br />
• The carbon canister solenoid valve should vibrate slightly. If the carbon canister solenoid valve has no<br />
slight vibration, check solenoid valve, harness and ECM.<br />
(b) Vacuum test method.<br />
• When the engine operates at the idle status, pull out the vacuum hose from the activated carbon<br />
canister and check the vacuum hose for vacuum suction. If the carbon canister solenoid valve operates<br />
normally, the solenoid valve should be closed and there should be no vacuum suction in the vacuum<br />
hose. If there is vacuum suction in the vacuum hose now, remove the socket connector from the<br />
solenoid valve. If there is voltage in the terminals of the harness socket connector in the carbon<br />
canister solenoid valve, it indicates there is a fault in ECM. If there is no voltage, it indicates the carbon<br />
canister solenoid valve is stuck in the opening position.<br />
• Press the accelerator pedal to allow the engine speed reach above 2000 RPM and check the vacuum<br />
hose for the vacuum suction. If the vacuum suction exists, it indicates the carbon canister solenoid<br />
valve operates normally. If no vacuum suction exists in the vacuum hose and the voltage is normal on<br />
the terminal of harness socket connector in the carbon canister solenoid valve, it indicates there is a<br />
fault in the carbon canister solenoid valve. If the voltage is abnormal, it indicates there is a fault in ECM<br />
or harness.<br />
11A-54 ENGINE CONTROL SYSTEM - CANISTER SOLENOID VALVE<br />
4. REMOVE CANISTER SOLENOID VALVE.<br />
(b) Remove fuel pressure regulator vaccum line.<br />
Disconnect canister solenoid valve connector.<br />
Disconnect canister solenoid valve inlet hose clips and<br />
remove the hose ( to canister).<br />
When disconnecting these hoses which used for a long time.<br />
Twist hose to be loosed first, then operate disconnection.<br />
Disconnect canister solenoid valve outlet hose clips and<br />
remove hose ( to intake manifold below throttle body ).<br />
Using screw driver, pry canister solenoid valve away from<br />
mounting bracket and remove it.<br />
11A-55<br />
5. CHECK CANISTER SOLENOID VALVE.<br />
(a) Apply battery voltage to canister solenoid valve. Sound<br />
should be heard. At this time, blow air to the inlet port:<br />
• If air passes, then the canister solenoid valve is OK. If it<br />
is not OK, replace it.<br />
• If no power applied, the solenoid should be closed. No<br />
air pass.<br />
(b) Check carbon control solenoid valve resistance.<br />
• Turn digital multimeter to Ohm range. Check resistance<br />
between terminal A and B of canister solenoid valve.<br />
Standard resistance: 19 ~ 22 Ω (20 ℃ )<br />
• If it is not OK, replace it.<br />
6. INSTALL CANISTER SOLENOID VALVE.<br />
(a) Install canister solenoid valve on mounting bracket.<br />
(b) Connect canister solenoid valve outlet hose clip (to<br />
intake manifold below throttle body).<br />
Connect canister solenoid valve inlet hose clips ( to canister<br />
).<br />
Connect canister solenoid valve connector.<br />
Connect IAC connector.<br />
Connect fuel pressure regulator vaccum line.<br />
11A-56 ENGINE CONTROL SYSTEM - CANISTER SOLENOID VALVE<br />
7. INSTALL AIR INTAKE HOSE. (Refer to “Chapter 14A intake air - intake air hose, replacement”)<br />
8. PUT DOWN DRIVER SEAT AND LOCK IT.<br />
VEHICLE SPEED SENSOR<br />
11A-57<br />
1. VEHICLE SPEED SENSOR DESCRIPTION.<br />
(a) Vehicle speed sensor is the type of hall sensor. It works<br />
together with signal wheel on output shaft. Unified meter<br />
measures digital voltage signal through it and determines<br />
the current speed of the vehicle.<br />
11A-58 ENGINE CONTROL SYSTEM - VEHICLE SPEED SENSOR<br />
3. CONNECT SCAN TOOL TO THE DATA LINK CONNECTOR (DLC) - USE THE MOST CURRENT<br />
SOFTWARE AVAILABLE.<br />
5. DRIVE THE VEHICLE, READ THE SCAN TOOL DATA STREAM: VEHICLE SPEED.<br />
6. VEHICLE SPEED: THE SAME VALUE AS THE ACTUAL VEHICLE SPEED.<br />
7. IF THE DISPLAYED VALUE IS NOT EQUAL TO THE ACTUAL VALUE, CHECK SENSOR, HAR-<br />
NESS AND ECM.<br />
8. RAISE THE VEHICLE.<br />
9. TURN THE IGNITION SWITCH ON AND NOT START ENGINE. CHECK AS FOLLOWING:<br />
Set digital multimeter to voltage range. Check voltage<br />
between terminal 2 and 3 of the sensor. It should be 12V.<br />
If it is not OK, replace it.<br />
Start engine, pull into gear. Using the oscilloscope, check<br />
the wave output of terminal 3 of sensor. If it is not OK,<br />
check harness and sensor.<br />
11A-59<br />
3. REMOVE VEHICLE SPEED SENSOR.<br />
(a) Disconnect vehicle speed sensor connector.<br />
(b) Remove vehcle speed sensor retaining bolt.<br />
Pull out vehcle speed sensor straight by slightly turning.<br />
Clear surface after removeing.<br />
4. INSTALL VEHICLE SPEED SENSOR.<br />
(a) Install vehicle speed sensor and tighten 1 mounting bolt.<br />
(b) Connect vehicle speed sensor connector.<br />
5. LOWER VEHICLE.<br />
6. CHECK AFTER INSTALLATION.<br />
(a) Start the vehicle and check vehicle speed sensor for fluid leakage and confirm that speedometer is<br />
operational.<br />
11A-60 ENGINE CONTROL SYSTEM - IGNITION CONTROL MODULE<br />
IGNITION CONTROL MODULE<br />
1. IGNITION CONTROL MODULE DESCRIPTION.<br />
Adopting group ignition technology, taking advantage of the<br />
theory that the mutual induction of the electromagnetic coils<br />
can generate high energy, controlling the switch-on/switchoff<br />
time of the primary coil, and taking advantage of the high<br />
voltage power of the secondary coil to puncture the spark<br />
plug gap so as to generate strong spark to ignite the mixed<br />
air. Since the air ionization is very great and the resistance<br />
is very low during the engine exhaust process, only low<br />
voltage power is required to puncture the spark plug gap.<br />
Therefore, this system adopts group ignition technology so<br />
as not to waste the energy.<br />
11A-61<br />
4. REMOVE IGNITION CONTROL MODULE.<br />
(a) Disconnect ignition control module connector.<br />
(b) Remove spark plug wires.<br />
Mark spark plug wires in the firing order in order to identify<br />
their positon when installing spark plug wires .<br />
Remove ignition control module retaining bolts.<br />
Remove ignition control module.<br />
5. INSTALL IGNITION CONTROL MODULE.<br />
(a) Tighten ignition control module 2 mounting bolts.<br />
Align the marks made previously and Install spark plug<br />
wire to ignition module.<br />
Connect ignition control module connector.<br />
6. INSTALL AIR INTAKE HOSE. (Refer to “Chapter 14A intake air - intake air hose, replacement”)<br />
FUEL SYSTEM<br />
FUEL SYSTEM.................................................................................12A-1<br />
PRECAUTION............................................................................ 12A-1<br />
FUEL SYSTEM PRESSURE RELEASE PROCESS ................. 12A-2<br />
DRAIN FUEL TANK PROCESS................................................. 12A-2<br />
FUEL TUBE CLEAN .................................................................. 12A-2<br />
PROBLEM SYMPTOMS TABLE................................................ 12A-3<br />
COMPONENTS ......................................................................... 12A-4<br />
FUEL TANK ASSY...........................................................................12A-6<br />
REPLACEMENT ........................................................................ 12A-6<br />
FUEL FILTER ASSY ........................................................................12A-9<br />
REPLACMENT........................................................................... 12A-9<br />
ELECTRIC FUEL PUMP ASSY .....................................................12A-10<br />
REPLACMENT......................................................................... 12A-10<br />
FUEL INJECTOR RAIL ASSY ......................................................12A-12<br />
OVERHAUL ............................................................................. 12A-12<br />
FUEL FILLER DOOR .....................................................................12A-17<br />
REPLACEMENT ...................................................................... 12A-17<br />
FUEL FILLER DOOR LOCK LATCH ASSY .................................12A-18<br />
REPLACEMENT ...................................................................... 12A-18<br />
FUEL FILLER CAP ........................................................................12A-20<br />
INSPECTION ........................................................................... 12A-20<br />
FUEL FILLING TUBE AND BREATHER TUBE ASSY .................12A-21<br />
INSPECTION ........................................................................... 12A-21<br />
ACCELERATE PEDAL ..................................................................12A-25<br />
REPLACEMENT ...................................................................... 12A-25<br />
12A<br />
FUEL - FUEL SYSTEM<br />
12A-1<br />
1. FUEL SYSTEM PRECAUTION.<br />
(a) Before working on fuel system, disconnect battery negative cable.<br />
(b) When removing the fuel hose, use a suitable container to hold the fuel.<br />
(c) Do not smoke, carry lighted tobacco or work near an open flame when working on fuel system.<br />
Equipment with ventilator at woking area can avoid personal injury.<br />
(d) Fuel in the fuel pump , railway and tubes remain under high pressure. In order to avoid personal injury,<br />
do not loosen tube connector while engine is running.<br />
(e) Keep gasoline away from rubber and leather parts.<br />
(f) Before disconncting any of the fuel system lines or fuel system components, release the fuel system<br />
pressure to prevent accidental spraying of fuel, even when the engine is not running. failure to follow<br />
this instruction may result in serious personal injury.<br />
(g) Check if there is any dirt like mud around the fuel line connector before work. And clean it away,<br />
otherwise it can damage fuel system or engine.<br />
(h) Keep cleaner away from the O-ring of tube connector. Cleaner can corrode the seal of fuel system.<br />
(i) Don’t bend or twist the fuel system tube and pipe by force.<br />
(j) Before connceting fuel system tube, be sure there is no damage, otherwise, replace it with a new tube<br />
assy.<br />
12A-2<br />
FUEL SYSTEM PRESSURE RELEASE PROCESS<br />
(a) Loosen driver seat clamp.<br />
(b) Rotate driver seat and open engine compartment cover.<br />
3. REMOVE FUEL PUMP FUSE.<br />
(a) Remove the lid of battery compartment junction box,<br />
identify the fuel pump fuse with its name labelled inside<br />
the box lid.<br />
(b) Remove the fuse with special puller or plier.<br />
4. START THE ENGINE UNTILL IT STOPS.<br />
5. START THE ENGINE AGAIN FOR 5 SECONDS, ENSURE FUEL RAIL PRESSURE RELEASE<br />
COMPLETELY.<br />
6. TURN IGNITION SWITCH OFF, RE-INSERT FUEL PUMP FUSE BACK INTO BATTERY COMPART-<br />
MENT JUNCTION BOX.<br />
DRAIN FUEL TANK PROCESS<br />
1. CHECK FUEL LEVEL ON FUEL GAUGE.<br />
2. DRAIN FUEL TANK.<br />
(a) Turn ignition switch off.<br />
(b) Insert hose of less than 22mm in diameter into fuel filler hose through fuel filler port to draw fuel in fuel<br />
filler hose.<br />
(c) Disconnect fuel filler hose from fuel tank filler neck.<br />
(d) Insert the hose into fuel tank to draw fuel through fuel tank filler neck.<br />
FUEL TUBE CLEAN<br />
1. USE FUEL TREATMENT THAT FOTON RECOMMENDS TO CLEAN FUEL SYSTEM.<br />
2. USE FUEL ADDITIVES THAT FOTON RECOMMENDS TO CLEAN FUEL SYSTEM.<br />
12A-3<br />
cause of the problem. Check each part in the order shown. If necessary, repair or replace these parts.<br />
Engine does not start<br />
1. Fuel pump (Damaged) Chapter 12A fuel - electric fuel pump assy,<br />
2. Fuel tube (Choked) Chapter 12A fuel - fuel system, precaution<br />
3. Fuel pressure regulator (Fuel<br />
pressure too low)<br />
4. Fuel tank (No fuel) Chapter 12A fuel - fuel tank assy, replacement<br />
5. Fuel pump relay(Damaged) -<br />
6. Fuel injector (Damaged) Chapter 12A fuel - fuel injector rail assy,<br />
1. Fuel tube (Obstructed) Chapter 12A fuel - fuel system, precaution<br />
2. Fuel pressure regulator (Fuel<br />
Chapter 12A fuel - fuel injector rail assy,<br />
Engine start hard<br />
3. Fuel injector (Leaking or<br />
obstructed)<br />
overhaull<br />
4. Fuel pump (Out of order) Chapter 12A fuel - electric fuel pump assy,<br />
Engine idles rough<br />
5. Fuel injector control system (Out<br />
of order)<br />
6. Fuel pressure regulator or fuel<br />
pump (Return valve damaged)<br />
1. Fuel pressure regulator (Fuel<br />
2. Fuel injector (Leaking or<br />
Chapter 04 diagnostics - engine control<br />
3. Fuel tube (Obstructed) Chapter 12A fuel - fuel system, precaution<br />
Engine loss of power<br />
3. Fuel pump (Out of order) Chapter 12A fuel - electric fuel pump assy,<br />
4. Fuel tube (Obstructed) Chapter 12A fuel - fuel system, precaution<br />
5. Fuel (Poor quality) -<br />
12A-4<br />
COMPONENTS<br />
1 Fuel Tank Assy<br />
2 Fuel Tank Rear Bracket<br />
3 Bolt, Spring Washer And Flat Washer<br />
5 Fuel Tank Retaining Belt Assy<br />
6 Fuel Tank Retaining Belt Assy<br />
7 Bolt, Spring Washer And Flat Washer<br />
4 Bolt, Spring Washer And Flat Washer<br />
12A-5<br />
1 Bolt, Spring Washer And Flat Washer<br />
2 Bolt, Spring Washer And Flat Washer<br />
3 Three Line Clip<br />
4 Canister Vent Hose Bracket<br />
5 Fuel Line Clip<br />
6 Fuel Line Clip<br />
7 Single Line Clip<br />
8 Electric Fuel Pump Assy<br />
9 Fuel Filter To Engine Fuel Line Assy<br />
10 Fuel Tank To Engine Fuel Line Assy<br />
11 Canister Vent Hose 1<br />
12 Fuel Filler Hose<br />
13 Bolt, Spring Washer And Flat Washer<br />
14 Fuel Filter<br />
15 Fuel Filter Bracket<br />
16 Nut<br />
17 Bolt, Spring Washer And Flat Washer<br />
18 Canister Vent Hose 2<br />
19 Canister Bracket<br />
20 Canister<br />
21 Fuel Filler Cap<br />
22 Fuel Filter To Engine Rear Fuel Line<br />
23 Bolt, Spring Washer And Flat Washer<br />
24 Bolt, Spring Washer And Flat Washer<br />
25 Band Clamp<br />
26 Fuel Line Clip<br />
27 Fuel Line Clip<br />
28 Dual Line Clip<br />
29 Dual Line Clip<br />
30 Locking Nut<br />
31 Steel Spring Band Clamp<br />
32 Steel Spring Band Clamp<br />
12A-6<br />
FUEL - FUEL TANK ASSY<br />
1. RELEASE FUEL PRESSUE. (Refer to “Chapter 12A fuel - fuel system, fuel system pressure<br />
2. DRAIN FUEL TANK. (Refer to “Chapter 12A fuel - fuel system, drain fuel tank process”)<br />
3. DISCONNECT BATTERY NEGATIVE CABLE.<br />
4. RAISE AND SUPPORT THE VEHICLE IN SUITABLE POSITION.<br />
5. SUPPORT FUEL TANK WITH A JACK.<br />
• The tank may have an uneven surface at the bottom so shims or something similar should be<br />
put on the lower side to keep tank stable when supporting the fuel tank with a jack.<br />
• Support the position that fuel tank retaining belt never engage<br />
6. REMOVE FUEL TANK ASSY.<br />
(a) Remove fuel tank breather pipe clamp.<br />
(b) Remove fuel tank filler tube clamp.<br />
(c) Disconnect fuel tank breather pipe and filling tube from<br />
fuel tank assy.<br />
• Disconnect fuel filler tube, check filler port rubber<br />
grommet for improper crack, damage or deterioration,<br />
replace if necessary.<br />
Remove 4 fuel tank retaining belt mounting bolts.<br />
Remove 2 fuel tank rear bracket mounting bolts.<br />
Lower the fuel tank to a suitable position.<br />
Disconnect electric fuel pump assy connector.<br />
Disconnect feed tube quick connector.<br />
Disconnect return tube quick connector.<br />
Disconnect EVAP tube quick connector.<br />
to prevent quick connector from being<br />
damaged.<br />
12A-7<br />
• Mark the fuel tube and quick connector to avoid misassembling.<br />
• Keep the connecting portion clean and avoid<br />
damage and foreign materials, cover them<br />
completely with plastic bags or something similar.<br />
Remove fuel tank assy.<br />
7. INSTALL FUEL TANK ASSY.<br />
Support fuel tank to a suitable position with jack.<br />
Connect electric fuel pump connector.<br />
Connect feed tube, return tube and EVAP tube quick<br />
Connectors.<br />
Connect fuel tube quick connectors until a click is heard,<br />
Install 2 fuel tank retaining belts and tighten 4 mounting<br />
bolts.<br />
Tighten 2 fuel tank rear bracket mounting bolts.<br />
Torque: 41 ~ 51 N•m<br />
Connect fuel tank breather tube, then tighen the clamp.<br />
Connect fuel tank filling tube, then tighen the clamp.<br />
8. LOWER THE VEHICLE.<br />
9. CONNECT BATTERY NEGATIVE CABLE.<br />
10. CHECK FUEL TUBE.<br />
12A-8<br />
When Turning ignition switch on, fuel pump will apply fuel pressure to fuel lines. Inspect if there is fuel<br />
Start engine and rev it up and check there is no fuel leakage at the fuel system tube and hose<br />
FUEL - FUEL FILTER ASSY<br />
12A-9<br />
FUEL FILTER ASSY<br />
REPLACMENT<br />
Install fuel filter and tighten the mounting band bolt.<br />
Connect both sides quick connector.<br />
12A-10<br />
FUEL - ELECTRIC FUEL PUMP ASSY<br />
ELECTRIC FUEL PUMP ASSY<br />
2. DRAIN FUEL TANK AS REQUIRED. (Refer to “Chapter 12A fuel - fuel system, drain fuel tank<br />
process”)<br />
5. REMOVE FUEL TANK. (Refer to “Chapter 12A fuel - fuel tank, replacment”)<br />
6. REMOVE ELECTRIC FUEL PUMP ASSY.<br />
(a) Loosen lock ring counterclockwise with special wrench.<br />
Remove electric fuel pump assy.<br />
Be careful not to bend float arm during removing electric<br />
fuel pump assy.<br />
7. CHECK SEALING RING OF SEALING COVER.<br />
(a) Removing sealing ring as possible as early to avoid<br />
deformation caused by contacting the fuel.<br />
(b) Check seal ring for improper crack, damage or deterioration<br />
and replace if necessary.<br />
12A-11<br />
8. INSTALL ELECTRIC FUEL PUMP ASSY.<br />
(a) Position sealing ring onto the opening of fuel tank until it<br />
seat into place.<br />
(b) Position electric fuel pump assy into fuel tank.<br />
Press installation surface of the electric fuel pump assy<br />
into place, then install lock ring and rotate the lock ring<br />
clockwise.<br />
Tighten lock ring with special wrench to specific torque.<br />
Torque: 60 ~ 70 N•m<br />
When installation, align the mark on the installation surface<br />
of the fuel pump with the corresponding mark on top surface<br />
of fuel tank .<br />
9. INSTALL FUEL TANK. (Refer to “Chapter 12A fuel - fuel tank, replacment”)<br />
10. CHECK AFTER INSTALLATION.<br />
After disconnecting fuel pump connector, connect fuel level sensor connector, turn ignition switch on.<br />
Slide fuel level sensor position manually and then check the fuel gauge’s conditions in instrument<br />
panel.<br />
connections and confirm fuel pump works normally.<br />
12A-12<br />
FUEL - FUEL INJECTOR RAIL ASSY<br />
FUEL INJECTOR RAIL ASSY<br />
3. REMOVE INTAKE AIR PIPE AND HOSE. (Refer to “Chapter 14A intake air- intake air pipe and<br />
hose, replacement”)<br />
4. REMOVE FUEL INJECTOR RAIL ASSY.<br />
(a) Disconnect 4 fuel injector connectors.<br />
Disconnect fuel pressure vaccum hose from fuel pressure<br />
regulator.<br />
Disconnect PCV hose from engine cylinder head cover.<br />
Disconnect feed tube quick connector from fuel injector<br />
rail.<br />
12A-13<br />
Disconnect return tube quick connector from fuel injector<br />
Remove 2 fuel injector rail retaining bolts.<br />
Remove fuel injector rail assy carefully.<br />
Check the O-ring locating between injectors and intake<br />
manifold is in good condition.<br />
5. CHECK FUEL PRESSURE REGULATOR.<br />
(a) Pull clip and remove fuel pressure regulator.<br />
Inspect return spring of fuel pressure regulator operation.<br />
6. REMOVE INJECTOR.<br />
(a) Remove locking clip from the slot of injector.<br />
(b) Turn slightly and pull out inject from fuel injector rail.<br />
Be sure that the O-ring locating between injector and fuel<br />
injector rail is in good condition.<br />
12A-14<br />
7. CHECK INJECTOR.<br />
(a) Use an ohmmeter to measure resistance between two<br />
terminals of injector.<br />
Resistance: 13 ~ 16 Ω<br />
(b) Check if there is any carbon deposition or dirty aroud<br />
injector nozzle, clear it away if blocked.<br />
If necessary, take injector on injector test table, check<br />
injector leakage or not.<br />
8. INSTALL INJECTOR.<br />
(a) Install new insulator to each fuel injector.<br />
• O-ring on both sides of injector are different, do not<br />
misassemble.<br />
• Apply a light coat of spindle oil or gasoline to a new<br />
o-ring, and install it to each fuel injector. Do not use<br />
engine oil or brake fluid.<br />
Install each fuel injector to fuel rail.<br />
Attempt to pull injector out to check the locking clip<br />
secured the injector in place firmly.<br />
9. INSTALL FUEL PRESSURE REGULATORS.<br />
Inspect it if fuel pressure regulator turns smoothly. If not, it means that O-ring is clamped. Reinstall it<br />
with new O-ring.<br />
12A-15<br />
10. INSTALL FUEL INJECTOR ASSY.<br />
(a) Slightly press injector rail to install injector into hole properly.<br />
(b) Tighten 2 fuel injector rail assy retaining bolts.<br />
Connect feed tube to fuel injector rail assy.<br />
are secure.<br />
Connect return tube to fuel injector rail assy.<br />
11. CONNECT 4 INJECTOR CONNECTORS.<br />
12. CONNECT VACCUM HOSE TO FUEL PRESSURE<br />
REGULATIOR.<br />
12A-16<br />
13. CONNECT VACCUM HOSE TO PCV.<br />
14. INSTALL INTAKE AIR PIPE AND HOSE. (Refer to “Chapter 14A intake air- intake air pipe and<br />
15. CHECK AFTER INSTALLATION.<br />
Turn ignition switch “ON” (with engine stopped), and check connections for leakage by applying fuel<br />
pressure to fuel lines<br />
Start engine and rev it up and check there are no fuel leakage at the fuel system tube and hose<br />
FUEL - FUEL FILLER DOOR<br />
12A-17<br />
FUEL FILLER DOOR<br />
1. REMOVE FUEL FILLER DOOR.<br />
(a) Pull fuel filler door handle.<br />
(b) Open fuel filler door.<br />
Remove 2 fuel filler door retaining bolts.<br />
Remove the clip connected to fuel filler cap from fuel filler<br />
door.<br />
Remove fuel filler door.<br />
2. INSTALL FUEL FILLER DOOR.<br />
Install 2 fuel filler door retaining bolts.<br />
Install the clip connected to fuel filler cap to fuel filler<br />
3. ADJUST FUEL FILLER DOOR.<br />
Adjust fuel filler door or 2 retaining bolts position manually<br />
if fuel filler door is not closed completely<br />
12A-18<br />
FUEL - FUEL FILLER DOOR LOCK LATCH ASSY<br />
FUEL FILLER DOOR LOCK LATCH ASSY<br />
1. REMOVE FRONT SIDE WALL GUARD BOARD. (Refer to “Chapter 88 exterior and interior trim<br />
panel - side wall guard board, replacement”)<br />
2. REMOVE LEFT FRONT SEAT LOCK ASSY.<br />
(a) Remove 2 left front seat lock assy retaining bolts.<br />
3. REMOVE FUEL FILLER DOOR LOCK LATCH ASSY.<br />
(a) Open fuel filler door.<br />
(b) Remove lock latch retaining nut.<br />
Remove lock latch assy.<br />
Disconnect fuel filler door cable.<br />
4. INSTALL FUEL FILLER DOOR LOCK LATCH ASSY.<br />
(a) Connect fuel filler door cable to lock latch assy.<br />
12A-19<br />
Position fuel filler door lock latch assy into place inside B<br />
pillar, then tighten retaining nut.<br />
5. CHECK FUEL FILLER DOOR LOCK LATCH ASSY.<br />
(a) Close fuel filler door, then pull fuel filler door handle.<br />
(b) Be sure that fuel filler door lock latch assy is operatonal.<br />
6. INSTALL LEFT FRONT SEAT LOCK ASSY.<br />
(a) Tighten 2 left front seat lock assy retaining bolts.<br />
7. INSTALL FRONT SIDE WALL GUARD BOARD. (Refer to “Chapter 88 exterior and interior trim<br />
12A-20<br />
FUEL - FUEL FILLER CAP<br />
FUEL FILLER CAP<br />
1. PULL FUEL FILLER DOOR HANDLE AND OPEN<br />
FUEL FILLER CAP.<br />
2. REMOVE FUEL FILLER CAP.<br />
(a) Rotate the fuel filler cap counterclockwise to unlock it.<br />
(b) Remove the fixing clip from the plastic ring on the fuel<br />
filler cap.<br />
(c) Remove fuel filler cap.<br />
3. INSPECT FUEL FILLER CAP ASSY.<br />
(a) Visually inspect fuel filler cap and seal ring. If deformed<br />
or damaged, replace with a new one.<br />
(b) Termly lubricate the rotating part.<br />
4. INSTALL THE FUEL FILLER CAP.<br />
(a) Install the fuel filler cap fixing clip into plastic ring.<br />
(b) Rotate the fuel filler cap clockwise until a click is heard.<br />
FUEL - FUEL FILLING TUBE AND BREATHER TUBE ASSY<br />
12A-21<br />
FUEL FILLING TUBE AND BREATHER TUBE ASSY<br />
2. REMOVE BATTERY AND BATTERY TRAY. (Refer to “Chapter 20A starting and charging - battery,<br />
replacement” )<br />
3. OPEN FUEL FILLER DOOR.<br />
4. REMOVE FUEL FILLER CAP.<br />
5. DRAIN FUEL TANK AS REQUIRED. (Refer to “Chapter 12A fuel - fuel system, drain fuel tank<br />
6. REMOVE FUEL FILLER AND BREATHER HOSES.<br />
(a) Remove 3 fuel filler port retaining bolts.<br />
Remove fuel breather hose and fuel filler hose retaining<br />
bolts that are located below battery tray.<br />
Raise and support the vehicle.<br />
Remove upper fuel breather hose bracket retaining nut.<br />
Remove the clamp between upper and lower fuel<br />
breather hoses, then disconnect breather hoses.<br />
Pull upper fuel breather hose out of the hole on sidewall<br />
of the battery compartment .<br />
12A-22<br />
Loosen fuel filler hose retaining clamp at the fuel tank<br />
side, then disconnect fuel filler hose from fuel tank filler<br />
neck.<br />
Remove fuel filler hose retaining bolt from vehicle frame.<br />
Remove upper fuel filler hose retaining bolt from vehicle<br />
frame.<br />
Remove fuel filler hose and upper fuel breather hose.<br />
Remove retaining bolt on the bracket of lower fuel<br />
breather, then pull fuel breather hose out of the hole on<br />
vehicle frame.<br />
(n)<br />
Remove retaining bolt between lower fuel breather hose<br />
bracket and side member NO.2.<br />
Remove fuel breather hose clamp at the fuel tank<br />
breather neck, then disconnect them.<br />
Pull lower fuel breather hose from the side member<br />
NO.2, then remove lower fuel breather hose.<br />
7. INSTALL FUEL FILLER AND BREATHER HOSES.<br />
Position upper fuel filler hose in place.<br />
Tighten 3 fuel filler port retaining bolts.<br />
Engage the groove of seal ring with the lip of fuel filler neck<br />
first securely when installing fuel filler hose assy.<br />
12A-23<br />
Tighten fuel filler hose and upper fuel breather hose<br />
retaining bolt below the battery tray.<br />
Connect upper and lower breather hoses, then tighten<br />
the clamp.<br />
Tighten upper breather hose retaining nut.<br />
Install fuel filler hose through the hole on side member<br />
NO.1.<br />
Connect upper and lower fuel breather hoses, then<br />
tighten retaining clamp.<br />
Tighten the retaining bolt securing breather hose bracket<br />
to side member NO.1.<br />
Install lower breather hose throuth the hole on side<br />
member NO.2.<br />
Tighten retaining bolt securing breather hose bracket to<br />
side member NO.2.<br />
Connect breather hose to fuel tank, then tighten the<br />
clamp.<br />
12A-24<br />
Tighten retaining bolt securing upper fuel filler hose to<br />
(o)<br />
Conncet fuel filler hose to fuel tank filler nect, then<br />
Tighten 1 fuel filler hose retaining bolt.<br />
8. INSTALL BATTERY AND BATTERY TRAY. (Refer to “Chapter 20A starting and charging - battery,<br />
9. CHECK AFTER INSTALLATION.<br />
(a) Fill fuel tank if necessary. Check filling is a smooth flow and no fuel leaks.<br />
10. INSTALL FUEL FILLER CAP, THEN CLOSE THE FUEL FILLER DOOR.<br />
FUEL - ACCELERATE PEDAL<br />
12A-25<br />
ACCELERATE PEDAL<br />
3. REMOVE THROTTLE CABLE.<br />
(a) Push throttle linkage wide open and hold it there to withdraw<br />
throttle cable end from the recess in throttle linkage.<br />
4. REMOVE ACCELERATE PEDAL ASSY.<br />
(a) Remove 2 accelerate pedal retaining nuts.<br />
(b) Remove accelerate pedal with throttle cable and move it<br />
aside.<br />
12A-26<br />
Release locking tab securing throttle cable to accelerate<br />
pedal, then disengage cable end from the recess in the<br />
accelerate pedal so that the cable can be removed<br />
completely.<br />
Remove accelerate pedal assy.<br />
5. INSTALL ACCELERATE PEDAL ASSY.<br />
(a) Engage throttle cabe end into the recess of accelerate<br />
pedal, then install locking tab to lock cable into place.<br />
(b) Position accelerate pedal and tighten 2 retaining nuts.<br />
6. ENGAGE THROTTLE CABLE IN THE THROTTLE<br />
MECHANISM IN THE ENGINE COMPARTMENT.<br />
7. PUT DOWN DRIVER SEAT AND LOCK THE CLAMP.<br />
8. CHECK AFTER INSTALLATION.<br />
(a) After installation, press accelerate pedal to check that the accelerator pedal operates smoothly without<br />
stuck phenomenon.<br />
FUEL FILLER CAP ..........................................................................13A-1<br />
INSPECTION ............................................................................. 13A-1<br />
CHARCOAL CANISTER..................................................................13A-2<br />
OVERHAUL ............................................................................... 13A-2<br />
CANISTER SOLENOID VALVE.......................................................13A-4<br />
OVERHAUL ............................................................................... 13A-4<br />
POSITIVE CRANKCASE VENTILATION VALVE (PCV VALVE)....13A-7<br />
OVERHAUL ............................................................................... 13A-7<br />
EMISSION CONTROL - FUEL FILLER CAP<br />
13A-1<br />
13A<br />
13A-2<br />
CHARCOAL CANISTER<br />
EMISSION CONTROL - CHARCOAL CANISTER<br />
3. REMOVE BATTERY AND BATTERY TRAY. (Refer to “Chapter 20A starting and charging - battery,<br />
4. REMOVE CHARCOAL CANISTER.<br />
(a) Loosen charcoal canister outlet hose clip and disconnect<br />
the hose (to canister solenoid ).<br />
When disconnecting these hoses which are used for a long<br />
time, twist hose first and make them loosed, then perform<br />
the disconnection.<br />
Loosen charcoal canister outlet hose clip and disconnect<br />
The end of EVAP hose connecting to fuel tank identifies<br />
with green mark.<br />
Remove charocal canister directly.<br />
5. CHECK CHAROCAL CANISTER.<br />
(a) Visually check charcoal canister for crack and damage,<br />
replace with a new one if necessary<br />
(b) Blow compressed air into inlet port (to fuel tank), feel<br />
charcoal canister outlet port (to canister solenoid) with<br />
hand and check if air flows from the outlet port.<br />
If no air flows from the outlet port, charcoal canister is<br />
blocked, replace if necessary.<br />
13A-3<br />
6. INSTALL CHARCOAL CANISTER.<br />
(a) Install the hose which connects fuel tank to charcoal<br />
canister and install clip.<br />
Install the hose which connects canister solenoid to<br />
charcoal canister and install clip.<br />
Install charcoal canister on bracket<br />
7. INSTALL BATTERY AND BATTERY TRAY. (Refer to “Chapter 20A starting and charging - battery,<br />
8. PUT DOWN THE DRIVER SEAT AND LOCK IT.<br />
13A-4<br />
EMISSION CONTROL - CANISTER SOLENOID VALVE<br />
13A-5<br />
13A-6<br />
7. INSTALL AIR INTAKE PIPE AND HOSE. (Refer to “Chapter 14A intake air - intake air pipe and<br />
EMISSION CONTROL - POSITIVE CRANKCASE VENTILATION VALVE (PCV VALVE)<br />
13A-7<br />
POSITIVE CRANKCASE VENTILATION VALVE (PCV VALVE)<br />
1. TURN IGNITION SWITCH ON.<br />
2. OPEN ENGINE COMPARTMENT COVER<br />
3. REMOVE PCV VALVE.<br />
(a) Disconnect PCV hose from engine cylinder head cover<br />
(b) Remove PCV valve.<br />
4. INSPECT PCV VALVE.<br />
(a) Disconnect PCV hose from engine cylinder head, start engine at idle speed. put finger at PCV port,<br />
check if vacuum of air intake manifold exits. if not, clean or replace with a new one.<br />
Blow air from port that connect cylinder. Air can flow out<br />
from the other port.<br />
Blow air from port that connect air intake mainfold. Air<br />
can’t flow out from the other port.<br />
13A-8<br />
5. INSTALL PCV VALVE .<br />
(a) Install PCV valve into engine cylinder head cover.<br />
(b) Connect PCV hose to PCV valve.<br />
INTAKE AIR SYSTEM......................................................................14A-1<br />
PRECAUTION............................................................................ 14A-1<br />
INTAKE AIR PIPE AND HOSE ........................................................14A-2<br />
REPLACEMENT ........................................................................ 14A-2<br />
AIR FILTER ASSY ...........................................................................14A-6<br />
REPLACEMENT ........................................................................ 14A-6<br />
INTAKE MANIFOLD................................................................. 14A-10<br />
REPLACEMENT ...................................................................... 14A-10<br />
14A<br />
INTAKE AIR SYSTEM<br />
AIR<br />
1. INTAKE AIR SYSTEM PRECAUTION.<br />
INTAKE AIR - INTAKE AIR SYSTEM<br />
14A-1<br />
Intake air must be filtered to avoid debris and dirt entering the engine. loose and damaged pipe or hose<br />
connection may cause unfiltered air to enter the engine leading to premature engine wear.<br />
The intake manifold hose connection must be reliable enough to avoid gaps and looseness, etc.<br />
Each cushion and bracket connection with intake manifold hose must be reliable. There are no cracks<br />
on the apperance or gaps in the connection portion.<br />
When using the solvent, acid or alkaline material washing, please follow the manufacturers’ advice to<br />
wear protective clothing and goggles to avoid personal injury.<br />
When dealing with corrosive work, use skin and eye protection device to reduce the possibility of<br />
personal injury.<br />
When using compressed air, wear appropriate goggles and protective mask. Both dust particles and<br />
dirt will cause injury.<br />
14A-2<br />
INTAKE AIR - INTAKE AIR PIPE AND HOSE<br />
INTAKE AIR PIPE AND HOSE<br />
1. REMOVE UPPER INTAKE AIR HOSE IN THE ENGINE<br />
COMPARTMENT.<br />
Remove intake air hose clamp on throttle body side.<br />
Remove 2 intake air pipe retaining bolt.<br />
Disconnect crankcase vent hose on intake air pipe.<br />
Remove the clamp at the end of intake air pipe.<br />
Remove upper intake air pipe and hose.<br />
14A-3<br />
2. REMOVE MIDDLE INTAKE AIR PIPE AND HOSE.<br />
(a) Remove middle intake air ripple hose clamp under the<br />
Remove middle intake air ripple hose.<br />
Remove middle intake air pipe retaining bolt by the right<br />
front wheel side.<br />
Remove the clamp connecting middle intake air pipe to<br />
bending hose.<br />
Remove middle intake air pipe.<br />
(f) Remove air filter assy. (Refer to “Chapter 14A intake air -<br />
air filter assy, replacement”)<br />
14A-4<br />
Remove the clamp securing bending hose to air filter<br />
assy, then remove the bending hose.<br />
3. INSTALL MIDDLE INTAKE AIR PIPE AND HOSE.<br />
Install bending hose to air filter outlet pipe and tightnen<br />
Install air filter assy. (Refer to “Chapter 14A intake air - air<br />
filter assy, replacement”)<br />
Positon middle intake air pipe in place, then install<br />
Tighten middle intake air pipe retaining bolt and bending<br />
hose retaining clamp.<br />
Install middle intake air ripple hose.<br />
Tighten ripple hose clamp.<br />
4. INSTALL UPPER INTAKE AIR PIPE AND HOSE IN<br />
THE ENGINE COMPARTMENT.<br />
Tighten the clamp securing intake air pipe to ripple hose.<br />
14A-5<br />
Tighten intake air hose clamp to throttle body side.<br />
Tighten 2 intake air pipe retaining bolts.<br />
Connect crankcase vent hose to intake air pipe, then<br />
tighten clamp.<br />
5. CHECK AFTER INSTALLATION.<br />
(a) After installing air filter, check all parts and parts connection again to make sure engine operates properly.<br />
14A-6<br />
INTAKE AIR - AIR FILTER ASSY<br />
AIR FILTER ASSY<br />
1. REMOVE FRONT GRILLE. (Refer to “Chapter 88 exterior and interior trim - front grille, replacement”)<br />
2. REMOVE FRONT BUMPER. (Refer to “Chapter 88 exterior and interior trim - front bumper assy,<br />
3. REMOVE AIR FILTER INTAKE AIR DUCT.<br />
Remove retaining bolt and clamp of air filter intake air<br />
duct.<br />
Remove intake air duct.<br />
4. REMOVE AIR FILTER ASSY.<br />
Remove retaining clamp securing bending hose to<br />
middle intake air pipe.<br />
14A-7<br />
Remove 3 air filter assy retaining bolts.<br />
Remove air filter together with bending hose.<br />
loosen clamp securing bending hose to air filter and<br />
remove bending hose.<br />
5. INSTALL AIR FILTER ASSY.<br />
Install bending hose to air filter assy outlet pipe, then<br />
Connect the end of benging hose which has a triangle mark<br />
to air filter when installation.<br />
14A-8<br />
Position air filter with bending hose in place.<br />
Connect bending hose to middle intake air pipe, then<br />
Tighten 3 air filter assy retaining bolts.<br />
Torque: 21 ~ 25 N.m<br />
Install air filter intake air duct retaining bolt.<br />
Tighten the clamp securing intake air duct to air filter inlet<br />
pipe.<br />
14A-9<br />
6. INSTALL FRONT BUMPER. (Refer to “Chapter 88 exterior and interior trim - front bumper assy,<br />
7. INSTALL FRONT GRILLE. (Refer to “Chapter 88 exterior and interior trim - front grille, replacement”)<br />
8. REPLACE AIR FILTER ELEMENT.<br />
Release 3 retaining clips from air filter lower cover.<br />
Open air filter lower cover and remove air filter element.<br />
Air filter element is made of paper. If necessary, clear the air<br />
filter element with high pressure air gun. Do not clean it<br />
with water.<br />
Clean or replace air filter element.<br />
Install air filter lower cover and lock the retaining clips.<br />
14A-10<br />
INTAKE MANIFOLD<br />
1. DRIAN THE COOLANT. (Refer to “Chapter 17A cooling - coolant, replacement”)<br />
4. REMOVE INTAKE AIR PIPE AND HOSE. (Refer to “Chapter 14A intake air - intake air pipe and hose,<br />
5. DISCONNECT VACCUM BOOSTER HOSE ON INTAKE<br />
MANIFOLD.<br />
6. REMOVE THROTTLE BODY. (Refer to “Chapter 11A engine control system - throttle body, overhaul”)<br />
7. DISCONNECT ENGINE COOLANT TEMPERATURE<br />
SENSOR CONNECTOR.<br />
14A-11<br />
8. DISCONNECT IGNITION COIL CONNECTOR.<br />
9. REMOVE GROUND HARNESS.<br />
10. DISCONNECT INTAKE TEMPERATURE/ PRESSURE<br />
11. DISCONNECT A/C COMPRESSOR CONNECTOR.<br />
12. DISCONNECT KS CONNECTOR.<br />
13. DISCONNECT STARTER CONTROL WIRE CONNEC-<br />
TOR.<br />
14A-12<br />
14. DISCONNECT 4 INJECTOR CONNECTORS.<br />
Position wire harness aside for easy operation。<br />
15. REMOVE FUEL INJECTOR RAIL ASSY. (Refer to “Chapter 12A fuel - fuel injector rail assy,<br />
16. REMOVE CANISTER SOLENOID VALVE. (Refer to “Chapter 11A engine control system - canister<br />
solenold valve, overhaul”)<br />
17. REMVOE INTAKE MANIFOLD LOWER BRACKET.<br />
(a) Remove 4 intake manifold lower bracket retaining bolts.<br />
18. REMOVE WATER HOSES ON INTAKE MANIFOLD<br />
SIDE.<br />
(a) Remove 4 water hoses retaining clamps.<br />
(b) Disconnect 4 water hoses.<br />
Remove 2 three-way water pipe retaining bolts.<br />
14A-13<br />
Remove three-way water pipe.<br />
Check whether there are sign of coolant leakage for cap<br />
plug and coolant sensor. If it is present, replace cup plug or<br />
coolant sensor shim.<br />
19. REMOVE INTAKE MANIFOLD ASSY.<br />
(a) Remove intake manifold retaining bolts and nuts.<br />
Remove intake manifold assy.<br />
Remove intake manifold sealing gasket.<br />
Always replace a new sealing gasket after removing intake<br />
manifold.<br />
20. INSTALL INTAKE MANIFOLD ASSY.<br />
(a) install intake manifold sealing gasket.<br />
(b) install 9 intake manifold retaining bolts and nuts.<br />
Torque: 15 ~ 18 N.m<br />
14A-14<br />
Install 4 intake manifold lower bracket retaining bolts.<br />
21. INSTALL THREE-WAY WATER PIPE.<br />
(a) Use scraper to remove all old sealant adhering to the<br />
groove on mating surface of three-way water pipe, and<br />
then apply sealant to the groove.<br />
Install 2 three-way water pipe retaining bolts.<br />
Install 4 water hoses.<br />
Tighten 4 water hose clamps.<br />
22. INSTALL FUEL INJECTOR RAIL ASSY. (Refer to “Chapter 12A fuel - fuel injector rail assy,<br />
23. INSTALL CANISTER SOLENOID VALVE. (Refer to “Chapter 11A engine control system - canister<br />
24. INSTALL THROTTLE BODY. (Refer to “Chapter 11A engine control system - throttle body, overhaul”)<br />
14A-15<br />
25. CONNECT INTAKE MANIFOLD VACCUM BOOSTER<br />
HOSE.<br />
26. CONNECT STARTER CONTROL WIRE CONNECTOR.<br />
27. CONNECT KS CONNECTOR.<br />
28. CONNECT A/C COMPRESSOR CONNECTOR.<br />
29. CONNECT ENGINE COOLANT TEMPERATURE SEN-<br />
SOR CONNECTOR.<br />
14A-16<br />
30. TIGHTEN GROUND WIRE.<br />
31. CONNECT IGNITION COIL CONNECTOR.<br />
32. CONNECT INTAKE TEMPERATURE / PRESSURE<br />
33. INSTALL INTAKE AIR PIPE AND HOSE. (Refer to “Chapter 14A intake air - intake air pipe and hose,<br />
34. CONNECT BATTERY NEGATIVE CABLE.<br />
35. FILL COOLANT TO SPECIFIED LEVEL. (Refer to “Chapter 17A cooling - coolant, replacement”)<br />
36. PUT DOWN DRIVER SEAT AND LOCK IT.<br />
37. CHECK AFTER INSTALLATION.<br />
(a) Start the vehicle, check all electrical component is functional and no gas, air and fluid leakage are<br />
found.<br />
ENGINE MECHANICAL PART ........................................................15A-1<br />
PRECAUTION............................................................................ 15A-1<br />
ENGINE ASSY .................................................................................15A-2<br />
REPLACEMENT ........................................................................ 15A-2<br />
TIMING PULLEY CASING .............................................................15A-14<br />
REPLACEMENT ...................................................................... 15A-14<br />
TIMING BELT.................................................................................15A-18<br />
COMPONENTS ....................................................................... 15A-18<br />
OVERHAUL ............................................................................. 15A-19<br />
ROCK ARM, ROCK ARM SHAFT, HYDRAULIC<br />
TAPPET & CAMSHAFT.................................................................15A-37<br />
COMPONENTS ....................................................................... 15A-37<br />
ROCK ARM, ROCK ARM SHAFT & HYDRAULIC TAPPET OVER-<br />
HAUL ....................................................................................... 15A-39<br />
CAMSHAFT OVERHAUL......................................................... 15A-49<br />
CYLINDER HEAD,VALVE .............................................................15A-51<br />
COMPONENTS ....................................................................... 15A-51<br />
CYLINDER HEAD OVERHAUL ............................................... 15A-52<br />
VALVE OVERHAUL................................................................. 15A-54<br />
PISTON & CONNECTING ROD ASSEMBLY................................15A-59<br />
COMPONENTS ....................................................................... 15A-59<br />
PISTON & CONNECTING ROD ASSEMBLY OVERHAUL..... 15A-60<br />
CRANKSHAFT, CYLINDER BLOCK & FLYWHEEL ....................15A-69<br />
COMPONENTS ....................................................................... 15A-69<br />
OVERHAUL ............................................................................. 15A-71<br />
15A<br />
ENGINE MECHANICAL - ENGINE MECHANICAL PART<br />
ENGINE MECHANICAL PART<br />
MECHANICAL<br />
1. EMGINE MECHNANICAL PART PRECAUTION.<br />
Follow the instructions of maintenance methods and regulations to adjust or maintain.<br />
15A-1<br />
(b) Before starting the engine, check the coolant level, fill or drain the coolant if necessary. Check the<br />
engine oil level, fill the engine oil if necessary.<br />
(c) Do not adjust the position of throttle valve screw. It will cause the throttle valve closed angle change<br />
and make the engine work abnormal.<br />
(d) Do not pull up the spark plug wire when the engine is running.<br />
(e) The clearance between ckp sensor and flywheel is 0.8 ~ 1.2 mm. Do not try to adjust it.<br />
(f) The fuel should use ron ≥ 93 unleaded gasoline, otherwise the catalytic converter will be damaged.<br />
(g) Use the oil as requirement, otherwise exacerbate engine wear.<br />
(h) Use the original fittings, otherwise it will damage the engine or affect the engine working condition.<br />
(i) Do not use the high pressure water cannons to wash the ecm shell.<br />
(j) The engine starting time should be less than 5s. Not more than 5 consecutive starting times. Interval<br />
time to next starting should not be less than 15 seconds.<br />
(k) Keep the normal coolant temperature 85 ~ 105 ℃ .<br />
(l) When the engine in high speed or high load, do not turn the ignition switch off. Keep the engine running<br />
in low speed for 3~5 mins that the engine radiates eventually.<br />
(m) Before opening the radiator cap, check the coolant level and must ensure the engine is cool.<br />
(n) Use the sealant scraper to clear the sundries in seal surface. Confirm seal surface flat and smooth, no<br />
oil stain there.<br />
15A-2<br />
ENGINE MECHANICAL - ENGINE ASSY<br />
1. RECOVER REFRIGERANT. (Refer to “Chapter 61 heater and air conditioner - refrigerant,<br />
2. RELEASE FUEL SYSTEM PRESSURE. (Refer to “Chapter 12A fuel - fue system, fuel system<br />
pressure release process”)<br />
4. DRAIN COOLANT. (Refer to “Chapter 17A cooling - coolant, replacement”)<br />
5. DRAIN ENGINE OIL. (Refer to “Chapter 18A lubricantion - engine oil, replacement”)<br />
6. DRAIN TRANSMISSION FLUID. (Refer to “Chapter 41 transmission - transmission assy, replacement”)<br />
7. LOWER THE VEHICLE.<br />
8. OPEN ENGINE COMPARTMENT COVER.<br />
9. DISCONNECT BATTERY NEGATIVE CABLE.<br />
10. REMOVE ASSISTANT DRIVER SEAT. (Refer to “Chapter 84 seat - driver / assistant driver seat,<br />
11. REMOVE ENGINE COMPARTMENT COVER UNDER<br />
ASSISTANT DRIVER SEAT.<br />
(a) Remove front floor covering.<br />
(b) Remove 5 engine compartment cover retaining bolts.<br />
(c) Remove engine compartment cover.<br />
12. REMOVE INTAKE AIR PIPE AND HOSE. (Refer to “Chapter 14A intake air - intake air pipe and<br />
15A-3<br />
13. LOOSEN CLAMP AND DISCONNECT ENGINE WATER<br />
OUTLET HOSE.<br />
14. LOOSEN CLAMP AND DISCONNECT WATER OUT-<br />
LET HOSE AND INLET HOSE TO FRONT HEATER.<br />
15. DISCONNECT WATER INLET HOSE TO REAR HEATER.<br />
16. REMOVE THROTTLE CABLE FROM THE THROTTLE<br />
BODY.<br />
17. REMOVE THE HOSE TO CANISTER SOLENOID VALVE.<br />
18. REMOVE FUEL RETURN TUBE.<br />
19. REMOVE FUEL FEED TUBE.<br />
After disconnecting fuel tubes, cover them completely with<br />
plastic bags or something similar to avoid damage and<br />
foreign materials.<br />
20. REMOVE VACUUM BOOSTER HOSE TO INTAKE<br />
21. REMOVE WATER OUTLET HOSE TO REAR HEATER.<br />
15A-4<br />
22. REMOVE ENGINE WATER INLET HOSE.<br />
23. REMOVE ENGINE ECM HARNESS CONNECTOR.<br />
(a) Remove the clip securing engine harness to cowl panel<br />
at engine compartment.<br />
(b) Pull rubber grommet securing engine harness out of the<br />
hole at ECM compartment sidewall.<br />
Remove ECM compartment cover, then disconnect ECM<br />
connector and the other 2 electrical connectors.<br />
Pull engine harness connectors and 2 electrical connectors<br />
through the hole of ECM compartment.<br />
24. REMOVE GENERATOR POSITIVE CABLE.<br />
25. DISCONNECT HIGH PRESSURE AND LOW PRESSURE<br />
PIPES TO COMPRESSOR.<br />
(a) Loosen 2 nuts securing high pressure and low pressure<br />
pipes to compressor, then disconnect them.<br />
Using clean cloth, block the A/C pipe and A/C compressor<br />
hole to avoid dust entering.<br />
15A-5<br />
26. RAISIE THE VEHICLE.<br />
27. REMOVE 2 FRONT WHEELS. (Refer to “Chapter 33 wheel and tire - wheel, replacement”)<br />
28. REMOVE STARTER POSITIVE CABLE.<br />
29. DISCONNECT THE GROUND CABLE TO ENGINE<br />
BLOCK.<br />
30. REMOVE LEFT FRONT SUSPENSION UNIT.<br />
(a) Separate left front shock absorber from lower control<br />
arm. (Refer to “Chapter 31 front suspension - front shock<br />
absorber, overhaul”)<br />
(b) Separate left front stabilizer bar from lower control arm.<br />
(Refer to “Chapter 31 front suspension - stalilizer bar,<br />
(c) Separate left front stabilizer bar from lower control arm<br />
ball joint seat. (Refer to “Chapter 31 front suspension -<br />
lower control arm, replacement”)<br />
(d) Separate left front steering tie rod from the steering<br />
knuckle arm. (Refer to “Chapter 52 power steering -<br />
power steering link assy, replacement”)<br />
31. REMOVE RIGHT FRONT SUSPENSION UNIT.<br />
The procedure to remove right front suspension unit is similar to the procedure above.<br />
32. REMOVE STEERING DRIVE SHAFT ASSY II.<br />
(a) Remove retaining bolts on both sides of steering drive<br />
shaft assy II.<br />
(b) Remove steering drive shaft assy II.<br />
Before disconnecting steering drive shaft assyII, mark<br />
steering drive shaft assy and steering gear output shaft for<br />
easier installation.<br />
33. REMOVE TRANSMISSION FLEXIBLE SHAFT ASSY.<br />
(a) Remove clamp NO.1 retaining bolt securing flexible shaft<br />
assy to sub-frame.<br />
15A-6<br />
Remove clamp NO.2 retaining bolt securing flexible shaft<br />
assy to sub-frame..<br />
(c) Remove locking nuts and locking clips securing<br />
transmission flexible shaft to transmission shift<br />
mechanism.<br />
34. REMOVE CLUTCH SLAVE CYLINDER.<br />
(a) Remvoe 2 retaining bolt mounting clutch slave cylinder to<br />
transmission assy.<br />
(b) Remove clutch slave cylinder.<br />
35. REMOVE CATALYTIC CONVERTER. (Refer to“Chapter 16 exhaust - exhaust pipe, replacement”)<br />
36. DISCONNECT VSS AND BACK-UP LAMP SWITCH<br />
HARNESS CONNECTORS.<br />
37. SUPPORT ENGINE SUB-FRAME AND TRANSMISSION ASSY WITH HYDRAUMATIC JACK.<br />
Lower the vehicle in suitable position and support bottom of engine sub-frame and transmission assy<br />
with hydraumatic jack securely.<br />
15A-7<br />
38. REMOVE SUB-FRAME RETAINING BOLTS.<br />
Remove 5 retaining bolts securing sub-frame right side to<br />
(b) Left side is similar to the procedure above. Remove 5<br />
retaining bolts securing sub-frame left side to vehicle<br />
Before removing sub-frame, mark the sub-frame to ensure<br />
align the reference line marked on the sub-frame with<br />
retaining bolts when installing<br />
39. SEPARATE PROPELLER SHAFT FROM TRANSMISSION ASSY. (Refer to “Chapter 34 axle and<br />
propeller shaft - prepeller shaft, overhaul”)<br />
40. REMOVE TRANSMISSION MOUNT.<br />
(a) Remove the retaining nut securing transmission mount to<br />
After supporting the rear of transmission to a suitable<br />
height with jack, pull out the retaining bolt to separate the<br />
transmission mount from the vehicle frame.<br />
41. LOWER THE JACK SLOWLY TO SEPARATE ENGINE SUB-FRAME AND TRANSMISSION ASSY<br />
FROM VEHICLE FRAME.<br />
• Verify all vacuum hoses, fuel and coolant hoses, electrical connectors between engine/<br />
transmission and vehicle are disconnected.<br />
• Lower engine about 150 mm slowly. verify all components between the engine/transmission and<br />
vehicle are disconnected again.<br />
42. SEPARATE ENGINE ASSY FROM TRANSMISSION ASSY. (Refer to “Chapter 41 transmission -<br />
transmission assy, replacement”)<br />
43. DISCONNECT HIGH PRESSURE AND LOW PRESSURE FLUID PIPES FROM POWER STEERING<br />
PUMP. (Refer to “Chapter 52 power steering - power steering link assy, replacement”)<br />
44. FIT ENGINE HOOK AND HANG ENGINE ASSY WITH A HOIST.<br />
45. REMOVE ENGINE MOUNTS ON BOTH SIDES OF<br />
ENGINE.<br />
Remove retaining nut securing left engine mount to subframe<br />
and separter them.<br />
Remove right engine mount, the procedure is similar to<br />
the left side.<br />
46. HOIST ENGINE UP AND SEPARATE ENGINE FROM SUB-FRAME.<br />
15A-8<br />
47. INSTALL ENGINE MOUNTS ON BOTH SIDES OF<br />
Aligning the engine mount bracket with engine mount<br />
stud, lower and position engine onto sub-frame.<br />
Tighten retaining nut securing left engine mount to subframe.<br />
Tighten retaining nut securing right engine mount to subframe.<br />
Torque: 78 ~ 96 N.m<br />
48. CONNECT HIGH PRESSURE AND LOW PRESSURE FLUID PIPES TO POWER STEERING PUMP.<br />
(Refer to “Chapter 52 power steering - power steering link assy, replacement”)<br />
49. CONNECT TRANSMISSION TO ENGINE ASSY. (Refer to “Chapter 41 transmission - transmission<br />
assy, replacement”)<br />
50. POSITION THE HYDRAULIC JACK SUPPORTING ENGINE SUB-FRAME AND TRANSMISSION<br />
ASSY BENEATH THE VEHCLE.<br />
51. RAISE THE HYDRAULIC JACK UNTIL THE SUB-FRAME MOUNTING PIN WAS FULLY SEATED<br />
INTO THE VEHICLE FRAME AND TARANSMISSION MOUNT IS IN RIGHT PLACE.<br />
• Lift up the hydraulic jack slowly, make sure there is no interference with vehicle during raising<br />
the engine and transmission assy.<br />
• During raising slowly, handle lower control arm, steering tie rod and shock absorber related<br />
position with vehicle avoid interference.<br />
52. INSTALL SUB-FRAME RETAINING BOLTS.<br />
(a) Install 5 retaining bolts securing sub-frame left side to<br />
Torque: 150 ~ 170 N.m<br />
(b) Install 5 retaining bolts securing sub-frame right side to<br />
Align the mark on sub-frame while installation.<br />
53. INSTALL RETAINING NUT SECURING TRANSMISSION<br />
MOUNT TO VEHICLE FRAME.<br />
Torque: 126 ~ 154 N.m<br />
15A-9<br />
54. REMOVE GENERATOR RETAINING BOLTS AND<br />
SEPARATE GENERATOR FROM BRACKET.<br />
Connect left front shock absorber to lower control arm.<br />
(Refer to “Chapter 31 front suspension - front shock<br />
Connect left front stabilizer bar to lower control arm.<br />
Connect left front stabilizer bar to lower control arm ball<br />
joint seat. (Refer to “Chapter 31 front suspension - lower<br />
control arm, replacement”)<br />
Connect left front steering tie rod to the steering knuckle<br />
arm.(Refer to “Chapter 52 power steering - power<br />
steering link assy, replacement”)<br />
55. INSTALL RIGHT FRONT SUSPENSION UNIT.<br />
56. INSTALL 2 FRONT WHEEL. (Refer to “Chapter 33 wheel and tire - wheel, replacement”)<br />
57. INSTALL STEERING DRIVE SHAFT ASSY II.<br />
(a) Install steering drive shaft assy II.<br />
(b) Tighten retaining bolts on both sides of steering drive<br />
When installing steering drive shaft assyII, make sure steering<br />
wheel is in the center and front wheel stands straight<br />
ahead of the vehicle.<br />
58. INSTALL CATALYTIC CONVERTER. (Refer to“Chapter 16A exhaust - exhaust pipe,<br />
59. CONNECT PROPELLER SHAFT TO TRANSMISSION ASSY. (Refer to “Chapter 34 axle and<br />
60. INSTALL TRANSMISSION FLEXIBLE SHAFT ASSY.<br />
(a) Install locking nuts and locking clips securing transmission<br />
flexible shaft to transmission shift mechanism.<br />
(b) Tighten 2 clamp retaining bolts securing flexible shaft<br />
15A-10<br />
61. INSTALL CLUTCH SLAVE CYLINDER.<br />
Tighten 2 clutch slave cylinder retaining bolts.<br />
62. CONNECT VSS AND BACK-UP LAMP SWITCH<br />
HARNESS CONNECTOR.<br />
63. CONNECT ENGINE WATER INLET HOSE.<br />
64. INSTALL A/C PIPES TO COMPRESSOR.<br />
(a) Tighten mounting nuts securing high pressure and low<br />
pressure pipes to compressor.<br />
Torque: 20 ~ 26 N•m<br />
Always replace O-ring with new one.<br />
65. CONNECT STARTER POSITIVE CABLE.<br />
66. CONNECT GROUND CABLE TO ENGINE BLOCK.<br />
15A-11<br />
67. CONNECT WATER OUTLET HOSE TO REAR HEATER.<br />
68. CONNECT WATER INLET HOSE TO REAR HEATER.<br />
69. INSTALL THROTTLE CABLE TO THE THROTTLE<br />
70. CONNECT CANISTER SOLENOID VALVE HOSE.<br />
71. CONNECT RETURN TUBE TO FUEL INJECTOR RAIL<br />
ASSY.<br />
72. CONNECT VACCUM BOOSTER HOSE TO INTAKE<br />
73. CONNECT FEED PIPE TO FUEL INJECTOR RAIL<br />
74. CONNECT ENGINE WATER OUTLET HOSE, THEN<br />
TIGHTEN CLAMP.<br />
75. CONNECT WATER OUTLET AND WATER INLET HOSES<br />
TO REAR HEATER, THEN TIGHTEN CLAMPS.<br />
15A-12<br />
76. CONNECT GENERATOR POSITIVE CABLE.<br />
77. INSTALL ENGINE ECM HARNESS.<br />
(a) Route the engine electrical harness throuth the mounting<br />
hole into ECM compartment.<br />
(b) Connect ECM connector and other 2 electrical connectors.<br />
Fasten the tie securing engine harness to cowl panel.<br />
Press the rubber grommet into place.<br />
78. INSTALL INTAKE AIR PIPE AND HOSE. (Refer to “Chapter 14A intake air - intake air pipe and<br />
79. ADD POWER STEERING FLUID TO SPECIFIED LEVEL. (Refer to “Chapter 52 power steering -<br />
steering fluid, replacement”)<br />
80. INSTALL ENGINE COMPARTMENT COVER UNDER<br />
(a) Tighten 5 engine compartment cover retaining bolts.<br />
(b) Cover front floor covering.<br />
15A-13<br />
81. INSTALL ASSISTANT DRIVER SEAT. (Refer to “Chapter 84 seat - driver / assistant driver seat,<br />
82. PUT DOWN DRIVER SEAT AND LOCK IT.<br />
83. FILL COOLANT. (Refer to “Chapter 17A cooling - coolant, replacement”)<br />
84. FILL ENGINE OIL. (Refer to “Chapter 18A lubricantion - engine oil, replacement”)<br />
85. FILL TRANSMISSION FLUID. (Refer to “Chapter 41 transmission - transmission assy, replacement”)<br />
86. SUPPLY REFRIGERANT. (Refer to “Chapter 61 heater and air conditioner - refrigerant, replacement”)<br />
15A-14<br />
ENGINE MECHANICAL - TIMING PULLEY CASING<br />
TIMING PULLEY CASING<br />
1. Switch off the ignition.<br />
2. Disconnect battery negative cable. (Refer to "Chapter 20. Start & charge - battery, replacement")<br />
3. Remove the ignition coil and the spark plug cable. (refere to "Chapter 19A. Ignition - ignition<br />
module, high voltage cable, spark plug, overhaul")<br />
4. Remove the retaining bolts on the front upper cover<br />
of the toothen timing belt and then the cover.<br />
5. Remove the engine accessory belt. (Refer to "Chapter 15A. Engine mechanical system - engine<br />
accessory belt, overhaul")<br />
6. Remove the retaining bolts on the front middle cover<br />
7. Remove the retaining nuts of the water pump belt<br />
pulley and then the pulley.<br />
15A-15<br />
8. Remove the retaining nuts of the crank crankshaft<br />
damper wheel and then the pulley.<br />
9. Remove the retaining bolts on the front lower cover<br />
10. Clean the interior of the toothed timing belt front cover and the impurities at the side.<br />
11. Install the front lower cover of the toothed timing belt<br />
and tighten the retaining bolts.<br />
Torque: 11N·m<br />
15A-16<br />
12. Install the crank shock absorption belt pulley and<br />
tighten the retaining bolts.<br />
Torque: 25 N·m<br />
13. Install the water pump belt pulley and tighten the<br />
retaining nuts.<br />
Torque: 14 N·m<br />
14. Install the front middle cover of the toothed timing<br />
belt and tighten the retaining bolts.<br />
15. Install the engine accessory belt. (Refer to "Chapter 15A. Engine mechanical system - engine<br />
16. Install the front upper cover of the toothed timing<br />
Torque: 18 ~ 26N·m<br />
15A-17<br />
17. Install the ignition coil and the spark plug cable. (refere to "Chapter 19A. Ignition - ignition<br />
18. Connect battery negative cable. (Refer to "Chapter 20. Start & charge - battery, replacement")<br />
15A-18<br />
ENGINE MECHANICAL - TIMING BELT<br />
1 Front Lower Cover of Timing Belt<br />
2 Front Middle Cover of Timing Belt<br />
3 Front Upper Cover of Timing Belt<br />
4 Toothed Camshaft Belt Pulley<br />
5 Harness Bracket<br />
6 Timing Belt<br />
7 Tensioner<br />
8 Tensioner Arm<br />
9 Timing Belt B Tensioner<br />
10 Balancing Shaft Belt Pulley<br />
11 Timing Belt B<br />
12 Flange<br />
13 Idler<br />
14 Crank TImming Belt Pulley B<br />
15 Crank Timing Belt Pulley Gasket<br />
16 Oil Pump Belt Pulley<br />
17 Crank TImming Belt Pulley<br />
18 Automatic Tensioner<br />
15A-19<br />
1. Disconnect negative battery cable. (Refer to "Chapter 20. Start & charge - battery, replacement")<br />
2. Remove the engine harness.<br />
3. Remove the engine accessory belt. (Refer to "Chapter 15A. Engine mechanical system - engine<br />
4. Remove the front cover of toothed engine timing belt. (Refer to "Chapter 15A. Engine<br />
mechanical system - toothed timing belt casing, replacement")<br />
5. Mark down the rotation direction of the toothed<br />
timing belt to faciliate installation.<br />
6. Turn and align the crank to the timing mark:<br />
Align the timing mark of the toothed camshaft belt pulley.<br />
15A-20<br />
Align the timing mark of the toothed oil pump belt pulley.<br />
Align the timing mark of the toothed crankshaft belt<br />
pulley.<br />
7. Use a specific tool to screw into the threaded hole,<br />
until the pin can be inserted into the locking hole on<br />
the automatic tensioner.<br />
8. Insert the pin into the locking hole on the automatic<br />
tensioner.<br />
15A-21<br />
9. Remove the retaining bolts of the automatic<br />
tensioner and then the tensioner.<br />
10. Check the automatic tensioner:<br />
(a) Check whether there is damage or leakage on the automatic tensioner and replace it if necessary.<br />
(b) Check whether there is wear or damage on the rod end and repalce it if necessary.<br />
(c) Measure the protrusion on the top of the automatic<br />
tensioner. If not qualified, replace it.<br />
Standard: 12 mm<br />
Press the rod down in 98~196N while measuring the<br />
movement. If the value is 1mm less than Item 3) or<br />
above, replace the tensioner.<br />
Standard: ≤ 1mm<br />
15A-22<br />
Hold the tensioner with vise with soft jaws. Turn the plier<br />
handles and push the tensioner rod into it. If it can be<br />
easily inserted, replace the tensioner. You shall feel<br />
certain resistance during the process.<br />
There is a protruded plug at the bottom of the automatic<br />
tensioner. Insert a flat pad between the pliers and the plug<br />
to prevent them from touching each other.<br />
11. Loose the retaining bolts of the tensioner and then<br />
the toothed timing belt.<br />
12. Remove and check the toothed timing belt. Replace it in case of any of the following damages:<br />
• Water or grease on the belt teeth will quickly reduce its useful life. Therefore, after removal,<br />
protect the belt teeth, the toothed belt pulley and the tensioner from water or grease. Do not<br />
clean these parts. In case of heavy contamination, replace it with a new one.<br />
• If any water or grease is found on the parts, check whether there is any leakage on the front<br />
cover oil seal, the crankshaft oil seal and water pump.<br />
Aged and shiny rubber on the back, showing no nail<br />
scratch.<br />
15A-23<br />
(b) Cracked or peeled canvas.<br />
(c) Cracked rubber on the back.<br />
(d) Cracked belt tooth at the bottom.<br />
(e) Cracked belt tooth on the side.<br />
Unusual tear and wear on the side of the belt. If the side<br />
of the tooth belt is as neat as cut, it is normal.<br />
Unusal tear wear of the toothed belt.<br />
Missing tooth.<br />
13. With a tool, remove the retaining bolts of the toothed<br />
camshaft belt pulley and then the pulley.<br />
14. Remove the toothed oil pump belt pulley:<br />
Remove the plug at the side of the cylinder.<br />
15A-24<br />
Insert a screwdriver to fix the left balancing shaft.<br />
Remove the toothed oil pump belt pulley nuts and then<br />
the pulley.<br />
(c) Remove the toothed oil pump belt pulley.<br />
15. Remove the toothed crank timing belt pulley:<br />
(a) Fix the flywheel with a tool.<br />
Remove the retaining bolts of crank shock absorption<br />
belt pulley and toothed crank timing belt pulley, and then<br />
the crank shock absorption belt pulley.<br />
Remove the toothed crank timing belt pulley. Use a tool<br />
in case of difficulty.<br />
15A-25<br />
16. Remove the retaining bolts of the tensioner arm and<br />
then the arm.<br />
17. Mark down the rotation direction of the toothed<br />
balancing shaft belt to faciliate installation.<br />
• Water or grease on the belt teeth will quickly reduce<br />
its useful life. Therefore, after removal, protect the<br />
belt teeth. the toothed belt pulley and the tensioner<br />
from water or grease. Do not clean these parts. In<br />
case of bad contamination, replace it with a new one.<br />
• If any water or grease is found on the parts, check<br />
whether there is any leakage on the front cover oil<br />
seal, the crankshaft oil seal and water pump.<br />
18. Align the timing mark of the toothed balancing shaft<br />
belt pulley.<br />
Align the timing mark of the toothed balancing shaft belt<br />
15A-26<br />
19. Loose the retaining bolts of the toothed balancing<br />
shaft belt tensioner and then the toothed timing belt<br />
20. Remove and check the toothed balancing shaft belt. Replace it in case of any of the following<br />
damages:<br />
Check all parts of the toothed belt carefully and replace it in case of the following damages.<br />
15A-27<br />
Cracked or peeled canvas.<br />
Cracked rubber on the back.<br />
Cracked belt tooth at the bottom.<br />
Cracked belt tooth on the side.<br />
21. Fix the toothed balancing shaft belt pulley with a<br />
tool.<br />
22. Remove the retaining bolts of the toothed balancing<br />
shaft belt pulley and then the toothed balancing<br />
shaft belt pulley and sleeve.<br />
15A-28<br />
23. Remove the toothed timing belt pulley B. Use a tool<br />
24. Install the balancing shaft sleeve.<br />
During installation, face the bevelled side towards the oil<br />
seal.<br />
25. Install the toothed crank timing belt pulley.<br />
26. Fix the toothed balancing shaft belt pulley with a tool<br />
Torque: 42 ~ 48 N·m<br />
15A-29<br />
27. Align the timing mark of the toothed balancing shaft<br />
15A-30<br />
28. Install the toothed balancing shaft belt pulley<br />
according to the rotation direction marked on the<br />
belt before disassembly. Do not allow loose part at<br />
the tension side.<br />
29. Push a finger against the toothed balancing shaft<br />
belt tensioner and impose a force along the arrow<br />
direction, while tightening the retaining bolts and<br />
fixing the tensioner.<br />
Torque: 48N·m<br />
When tightening the bolts, do not allow the shaft turning<br />
along with the toothed belt pulley, which will overly tension<br />
the belt.<br />
30. Confirm that the toothed belt pulley is aligned with<br />
the mark on the front cover. Press the center of the<br />
toothed timing belt B at the tensioner side, measured<br />
at 5 ~ 7 mm.<br />
31. Install the toothed crank timing belt pulley and the crank shock absorption belt pulley:<br />
Fix the flywheel with a tool.<br />
15A-31<br />
Install the toothed crank timing belt pulley and the crank shock absorption belt pulley.<br />
Tighten the retaining bolts of the toothed crank timing<br />
belt pulley and the crank shock absorption belt pulley.<br />
Torque of toothed crank timing belt pulley bolts:<br />
165 N·m<br />
Torque of crank shock absorption belt pulley bolts:<br />
25N·m<br />
32. Install the toothed oil pump belt pulley:<br />
Insert a screwdriver to fix the left balancing shaft. Install<br />
the toothed oil pump belt pulley and tighten the nuts.<br />
Torque: 55N·m<br />
Tighten the plug at the cylinder side.<br />
33. Install the tensioner arm and tighten the retaining<br />
nuts.<br />
Torque: 22N·m<br />
34. Install the automatic tensioner:<br />
(a) If the automatic tensioner is in a protruding position, retract it in the following steps.<br />
15A-32<br />
Hold the tensioner with a pair of pliers with soft jaws.<br />
to prevent them from directly touching each other.<br />
With the pliers, slowly push in the rod until the hole is aligned to that on the tensioner. Insert the bolt into<br />
the holes.<br />
Loose the pliers and remove the automatic tensioner.<br />
35. Install the automatic tensioner and tighten the<br />
Torque: 24N·m<br />
Before adjusting the tension of the toothed timing belt, do<br />
not remove the bolt in the locking hole of the tensioner.<br />
36. Install the retaining bolts of the toothed camshaft<br />
belt pulley with a tool.<br />
Torque: 90N·m<br />
15A-33<br />
37. Align the timing marks:<br />
15A-34<br />
38. Insert a plus screwdriver into the hole. If it goes<br />
beyond 60 mm, it means that it is aligned to the<br />
timing mark. If the distance is less than 20~25mm,<br />
turn the toothed oil pump belt pulley around once<br />
and again align it to the timing mark. Check whehter<br />
it can go beyond 60mm. Keep the screwdriver<br />
inserted until the end of the belt installation.<br />
39. Install the toothed timing blet along the direction<br />
marked before.<br />
Do not move the timing mark during the installation.<br />
40. Impose force to the tensioner along the arrow<br />
direction and temporarily tighten the retaining bolts.<br />
41. Check whether all timing marks are aligned.<br />
15A-35<br />
42. Pull out the inserted screwdriver from the cylinder<br />
body and tighten the cylinder plug.<br />
Torque: 30N·m<br />
43. Turn 1/4 round of the crank counterclockwise and then turn it clockwise, until all timing marks<br />
are realigned. If the timing marks are unable to realign, reinstall the toothed timing belt until<br />
alignment is achieved.<br />
44. Equipped the tensioner belt pulley with the sleeve<br />
and wrench in the toolkit and loose the tensioner<br />
retaining bolts.<br />
Or use a general torque wrench ranging from 0 to 3 N·m.<br />
45. Tighten the tensioner retaining bolts.<br />
Torque: 26 ~ 27N·m<br />
46. Press the toothed timing belt B tensioner by hand,<br />
along the arrow direction, while tightening the<br />
47. Turn the crank clockwise for two rounds and leave it<br />
for 15 minutes. Then check whether the retaining<br />
wire of the automatic tensioner can move freely.<br />
If not, repeat Steps 3-4 until it moves.<br />
48. Remove the retaining bolts of the automatic tensioner.<br />
15A-36<br />
49. Measure the distance between the tensioner arm and<br />
the tensioner body.<br />
Standard: 3.8 ~ 4.5mm<br />
50. Install the engine timing casing. (Refer to "Chapter 15A. Engine mechanical system - engine<br />
51. Install the engine accessory belt. (Refer to "Chapter 15A. Engine mechanical system - engine<br />
52. Reconnect the engine harness.<br />
53. Connect battery negative cable. (Refer to "Chapter 20. Start & charge - battery, replacement")<br />
ENGINE MECHANICAL - ROCK ARM, ROCK ARM SHAFT, HYDRAULIC TAPPET &<br />
ROCK ARM, ROCK ARM SHAFT, HYDRAULIC TAPPET &<br />
15A-37<br />
15A-38<br />
1 Rock Arm cover<br />
2 Rock Arm Cap Gasket<br />
3 Exhaust Rock Arm<br />
4 Intake Rock Arm<br />
5 Hydraulic Tappet<br />
6 Rock Arm Shaft Spring<br />
8 Intake Rock Arm Shaft<br />
9 Rock Arm Shaft Bolt<br />
10 O-ring<br />
11 Thrust Cap<br />
12 Camshaft<br />
13 Camshaft Oil Seal<br />
7 Exhaust Rock Arm Shaft<br />
15A-39<br />
HAUL<br />
1. Disconnect negative battery cable. (Refer to "Chapter 20: Start & Charge - Battery,<br />
Replacement")<br />
2. Remove the engine intake pipe. (Refer to "Chapter 14: Intake air - intake air pipe, replacement")<br />
3. Remove the engine accessory belt. (Refer to "Chapter 15A: Engine mechanical system - engine<br />
4. Loose the accelerator cable adjustment bolts on the<br />
throttle valve and remove the head clip and then the<br />
accelerate cable.<br />
5. Pull out the PCV valve hose on the rock arm cap.<br />
6. Remove the retaining bolts of heater pipe.<br />
15A-40<br />
7. Pull out the spark plug cable.<br />
8. Pull out the ignition coil connector.<br />
9. Unscrew the retaining bolts of the ignition coil.<br />
10. Remove the ignition coil and the spark plug cable assembly.<br />
Before disconnecting the spark plug cable on the ignition coil, mark the cable positions of different<br />
cylinders on the coil, to faciliate installation.<br />
11. Remove the retaining bolts on the front upper cover<br />
of the toothen engine timing belt and then the cover.<br />
15A-41<br />
12. Remove the retaining bolts of the rock arm cap in<br />
numeric sequence.<br />
13. Remove the rock arm cap and the rock arm cap gasket.<br />
The gasket is disposable and replace it with a new one before installation.<br />
14. Remove the oil seal.<br />
15. Remove the retaining bolts of the rock arm shaft in<br />
15A-42<br />
16. Before removing the rock arm and the rock arm shaft<br />
assembly, fix the hydraulic tappet with a tool, to<br />
prevent it from falling during the disassembly.<br />
17. Remove the rock arm shaft and the rock arm assembly.<br />
18. Remove the rock arm shaft spring and separate the rock arm from the rock arm shaft.<br />
19. Remove the hydraulic tappet.<br />
20. Check the rock arm:<br />
(a) Check the roller surface and replace the rock arm in case<br />
of any scratch or other damage.<br />
(b) Check whether the roller can rotate smoothly. If it's stuck<br />
or loose, replace the rock arm.<br />
(c) Check the inner diameter and replace the rock arm in<br />
case of any scratch or other damage.<br />
21. Check and clean the hydraulic tappet and replace it if any damage is detected:<br />
• The hydraulic tappet is a precision component. No dust or impurity is allowed on the surface.<br />
• Do not disassemble the hydraulic tappet.<br />
• Clean the hydraulic tappet with clean diesel.<br />
(a) Prepare 3 containers and almost 5L diesel. Pull enough<br />
diesel into each container so that the tappet is fully<br />
immersed. Then follow the steps below.<br />
Put the hydraulic tappet into Container A to clean its<br />
exterior.<br />
Clear the hard impurities with a nylon brush.<br />
15A-43<br />
Install a tool onto the hydraulic tappet and gently push<br />
the interior balls. Move the tappet plunger for 5-10 travels<br />
until it moves smoothly. In addition, it also eliminates the<br />
sliding resistance and the dirty grease.<br />
• As the steel ball spring is particular soft, do not exert<br />
exceesive force when pushing it with an air-release<br />
metal wire, in order to avoid damaging the hydraulic<br />
tappet.<br />
• If the slide is blocked or the mechanical unit appears<br />
to be abnormal, replace the hydraulic tappet.<br />
(d) Take the hydraulic tappet from the container. Then gently<br />
push the ball and move the tappet plunger to remove<br />
diesel from the pressure vessel.<br />
Install the tool onto the hydraulic tappet. Put it into<br />
Container B. With a tool, gently push the interior ball and<br />
move the tappet plunger for 5-10 travels, until it moves<br />
smoothly. This step cleans the pressure vessel of the<br />
hydraulic tappet.<br />
As the steel ball spring is particular soft, do not exert<br />
exceesive force when pushing it with an air-release metal<br />
wire, in order to avoid damaging the hydraulic tappet.<br />
Take the hydraulic tappet from the container. Then gently<br />
Put it into Container C. And push the interior ball with a<br />
Do not clean the hydraulic tappet in Container C. Otherwise,<br />
contamination may get into the pressure vessel full of<br />
diesel.<br />
15A-44<br />
Hold the hydraulic tappet vertically, with the tappet<br />
plunger at the top. Steady move the plunger downward<br />
up to its maximum travel. Then slowly move back the<br />
plunger. Release the ball so that the pressure vessel is<br />
full of diesel.<br />
Remove the tool.<br />
Take the hydraulic tappet from the container. Hold the<br />
hydraulic tappet vertically, with the tappet plunger at the<br />
top. Steady push the plunger and ensure it can no longer<br />
move. Compare its height to a new one.<br />
If the height is reduced, repeat Steps 7-10 and fill the<br />
hydraulic tappet with diesel. If it is still lower after these<br />
steps, replace it.<br />
Put the hydraulic acid on the tool. When the plunger is<br />
slightly lowered (0.2~0.5 mm), measure the time took for<br />
additional 1 mm.<br />
Standard: 3~20 seconds /1 mm (diesel at 15 ~ 20 ℃ )<br />
If unqualified, replace it.<br />
Install the tool onto the hydraulic tappet. Put the<br />
hydraulic tappet into Container c again and gently push<br />
down the interior balls with a tool. Hold the hydraulic<br />
tappet vertically, with the tappet plunger at the top.<br />
Steady move the plunger downward up to its maximum<br />
travel. Then slowly move back the plunger. Release the<br />
ball so that the pressure vessel is full of diesel.<br />
If the height is reduced, repeat Steps 12-14 and fill the<br />
15A-45<br />
(o) Hold the hydraulic tappet vertically to prevent diesel from<br />
flowing out. Prevent dust or impurity from contaminating<br />
the hydraulic tappet. Install it onto the engine as soon as<br />
• Insert the hydraulic tappet into the rock arm and<br />
make sure the diesel doesn't overflow. Then fix the<br />
hydraulic tappet with a tool to prevent it from falling<br />
during installation.<br />
• If the hydraulic tappet is reusable, clean it first.<br />
22. Install the rock arm onto the rock arm shaft.<br />
23. Temporarily tighten the air inlet rock arm with bolts until all rock arms no longer press the<br />
throttle valve.<br />
24. Install the rock arm shaft spring from the top and<br />
make sure it is vertical to the spark plug duct.<br />
• Install the rock arm shaft spring and then tighten the<br />
air outlet rock arm bolts.<br />
• Align the oil hole on the rock arm shaft to the<br />
cylinder body, to ensure correct installation.<br />
25. Tighten the retaining bolts of the rock arm shaft in<br />
Torque: 31N·m<br />
26. Remove the tools used to retain the hydraulic tappet.<br />
15A-46<br />
27. Ensure the notch on the rock arm shaft is located as<br />
illustrated.<br />
28. Install the oil seal.<br />
29. Install a new rock arm cap gasket.<br />
30. Install the rock arm cap.<br />
31. Tighten the retaining bolts of the rock arm cap in<br />
Torque: 4N·m<br />
15A-47<br />
32. Install the front upper cover of the toothed engine<br />
timing belt and tighten the retaining bolts.<br />
33. Install the spark plug cable to the ignition coil.<br />
Install the spark plug cable as marked.<br />
34. Install the ignition coil and tighten the retaining<br />
35. Install the ignition coil connector.<br />
36. Install the spark plug cable to the rock arm cap.<br />
15A-48<br />
37. Install the retaining bolts of heater pipe.<br />
38. Install the PCV valve hose to the rock arm cap.<br />
39. Install the accelerator cable head clip and tighten the<br />
bolts on the throttle valve.<br />
40. Install the engine accessory belt. (Refer to "Chapter 15A: Engine mechanical system - engine<br />
41. Install the engine intake pipe. (Refer to "Chapter 14: Intake air - intake air pipe, replacement")<br />
42. Connect battery negative cable. (Refer to "Chapter 20: Start & Charge - Battery, Replacement")<br />
15A-49<br />
CAMSHAFT OVERHAUL<br />
1. Remove the cylinder head. (Refer to "Chapter 15A: Engine mechanical system - cylinder head,<br />
throttle, cylinder head overhaul")<br />
2. Remove the retaining bolts of the toothed camshaft<br />
3. Remove the retaining bolts of the camshaft lock cap<br />
and then the cap.<br />
4. Pull out the camshaft.<br />
5. Check the camshaft:<br />
Check whether there is any corrosion, wear or crack on<br />
the surface of the camshaft. Replace it if any.<br />
Measure Camshaft Height<br />
Name Standard Limit<br />
Intake Cam 37.20mm 36.70mm<br />
Exhaust Cam 36.83mm 36.33mm<br />
6. Remove the camshaft oil seal.<br />
Once removed, it is necessary to replace it with a new<br />
camshaft oil seal.<br />
15A-50<br />
7. Install the camshaft.<br />
8. Apply some engine oil on the outside of the camshaft oil seal lips and the front end.<br />
9. With a tool, install a new camshaft oil seal.<br />
10. Install a new camshaft lock cap O-ring.<br />
11. Install the camshaft lock cap and tighten the<br />
Torque: 19N·m<br />
12. Install the toothed camshaft belt pulley and retaining<br />
bolts with a tool.<br />
13. Install the cylinder head. (Refer to "Chapter 15A: Engine mechanical system - cylinder head,<br />
CYLINDER HEAD,VALVE<br />
ENGINE MECHANICAL - CYLINDER HEAD,VALVE<br />
15A-51<br />
1 Valve Spring Lock<br />
2 Upper Valve Spring Retainer<br />
3 Valve Spring<br />
4 Valve Oil Seal<br />
5 Valve Spring Retainer<br />
6 Valve Guide<br />
7 Vavle Seat<br />
8 Valve<br />
9 Cylinder Head<br />
10 Cylinder Head Gasket<br />
15A-52<br />
CYLINDER HEAD OVERHAUL<br />
1. Disconnect battery negative cable. (Refer to "Chapter 20. Start & Charge - Battery,<br />
2. Drain coolant. (Refer to "Chapter 17A. Cooling - coolant, replacement")<br />
3. Remove the engine intake pipe. (Refer to "Chapter 14A. Intake air - intake air pipe, replacement")<br />
4. Remove the engine accessory belt. (Refer to "Chapter 15A: Engine mechanical system - engine<br />
5. Remove the toothed timing belt. (Refer to "Chapter 15A. Engine mechanical system - toothed<br />
timing belt, overhaul")<br />
6. Remove the rock arm and the rock arm shaft. (Refer to "Chapter 15A. Engine mechanical<br />
system - rock arm, rock arm shaft, hydraulic tappet & camshaft, rock arm, rock arm shaft &<br />
hydraulic tappet overhaul")<br />
7. Remove the retaining bolts of the cylinder head in<br />
When loosing the bolts, exert evenl and gradual torque to<br />
ensure balanced force on the cylinder head.<br />
8. Remove the cylinder head and the cylinder head gasket.<br />
9. Clean the cylinder head and check whether there is crack or serious damage. Replace it if<br />
10. Check the evenness of the cylinder head bottom with<br />
a ruler and a feeler blade. In case of excessive<br />
deformation, polish it (both cylinder head and body)<br />
or replace it.<br />
Flatness Standard: 0.03 mm<br />
Flatness Limit: 0.2mm<br />
Correction Limit: 0.2mm<br />
11. Check the height of the cylinder head and replace it if unqualified.<br />
Standard: 119.9 ~ 120.1mm<br />
12. Install a new cylinder head gasket.<br />
DANGER<br />
It is important to correctly install the cylinder gasket, with the hole aligned to that on the cylinder<br />
surface, or it may lead to serious engine damage.<br />
13. Install the cylinder head and fix it until the dowel pin is installed.<br />
15A-53<br />
14. Before installing the cylinder head bolts, ensure the<br />
length is within the standard range and replace them<br />
out of limit.<br />
Standard: 97.4mm<br />
15. Tighten the retaining bolts of the cylinder head in the<br />
following steps and numeric sequence:<br />
• Apply a proper amount of engine oil on the threaded<br />
part and gasket of the cylinder head bolts, to faciliate<br />
tightening.<br />
• In case of excess torque, loose the bolts completely<br />
and re-tighten them.<br />
(a) Tighten the retaining bolts of the cylinder head in numeric<br />
sequence.<br />
Torque: 78N·m<br />
(b) Completely loose all bolts.<br />
(c) Tighten the cylinder head bolts.<br />
Torque: 20N·m<br />
(d) Draw straight lines with paint, as marks on the bolt heads<br />
and the cylinder head.<br />
(e) Tighten the cylinder head bolts to 90° in the sequence of<br />
(f) Tighten the bolts to another 90° in the same sequence<br />
and ensure the mark on the bolt head is aligned to that<br />
on the cylinder head.<br />
16. Install the rock arm and the rock arm shaft. (Refer to "Chapter 15A. Engine mechanical system -<br />
rock arm, rock arm shaft, hydraulic tappet & camshaft, rock arm, rock arm shaft & hydraulic<br />
tappet overhaul")<br />
17. Install the toothed timing belt. (Refer to "Chapter 15A. Engine mechanical system - toothed<br />
18. Install the engine accessory belt. (Refer to "Chapter 15A. Engine mechanical system - engine<br />
19. Install the engine intake pipe. (Refer to "Chapter 14A. Intake air - intake air pipe, replacement")<br />
20. Fill the engine coolant. (Refer to "Chapter 17A. Cooling - coolant, replacement")<br />
21. Connect battery negative cable. (Refer to "Chapter 20. Start & Charge - Battery, Replacement")<br />
15A-54<br />
VALVE OVERHAUL<br />
1. Remove the cylinder head. (Refer to "Chapter 15A. Engine mechanical system - cylinder head,<br />
valve, cylinder head overhaul")<br />
Mark the removed valve, valve spring and other parts with the cylinder number and installation<br />
position. Keep them well to ease installation.<br />
2. Use a appropriate tool to remove the valve lock and<br />
then the upper valve spring retainer, the valve spring<br />
and the valve spring shim.<br />
3. Remove the valve oil seal and then the valve.<br />
The valve oil seal cannot be reused.<br />
4. Check the valve spring:<br />
Measure the free height of the valve spring. Replace it if<br />
below limit.<br />
Standard: 51.0mm<br />
Limit: 50.0mm<br />
Measure the uprightness of the central line of the spring<br />
to the bottom surface. Replace it if beyond limit.<br />
Standard: ≤ 2°<br />
Limit: 4°<br />
15A-55<br />
5. Check the valve:<br />
Check whether the working surface of the valve and the valve seat is airtight. If not, polish it with a valve<br />
polisher. The contact surface of the valve seat shall be consistent with the center of the valve working<br />
face.<br />
Check the thickness at the edge of the valve. Replace it if<br />
unqualified and polish it with a valve polisher:<br />
Thickness at<br />
Edge of Valve<br />
Intake 1.0mm 0.5mm<br />
Exhaust 1.2mm 0.7mm<br />
Check the total height of the valve. Replace it if below<br />
limit:<br />
Total Valve<br />
Height<br />
Intake 112.30mm 111.80mm<br />
Exhaust 114.11mm 113.61mm<br />
6. Check the clearance between the valve guide and the<br />
valve rod. Replace either or both of them if beyond<br />
limit, until the clearance meets the requirement:<br />
Clearance Standard Limit<br />
Intake 0.02 ~ 0.05mm 0.10mm<br />
Exhaust 0.03 ~ 0.07mm 0.15mm<br />
7. Follow the steps to replace the valve guide:<br />
Do not use a new valve guide of the same dimension as the removed one.<br />
(a) Heat the cylinder head and remove the valve seat.<br />
(b) With a tool, drive out the valve guide towards the lower surface of the cylinder head.<br />
(c) Treat the valve guide hole on the cylinder head so that the diameter meets the dimension of a larger<br />
guide:<br />
Diameter of Valve Guide Hole<br />
Larger 0.05mm<br />
Larger 0.25mm<br />
Larger 0.50mm<br />
11.05-11.068mm<br />
11.25-11.268mm<br />
11.50-11.518mm<br />
15A-56<br />
Installl a new valve guide by pressing it down the top of<br />
the cylinder head until the protrusion part meets the<br />
requirement.<br />
Standard: 14 ± 0.3mm<br />
• Press down the valve guide from the top of cylinder<br />
head.<br />
• The guides of intake valve and exhaust valve are of<br />
different lengths (intake valve: 45.5mm; exhaust<br />
valve: 50.5mm).<br />
Once installed, insert a new valve and check whether it moves freely along the axis.<br />
8. Assemble the valve and measure the protruded<br />
height of the valve rod between the end of the rod<br />
and the valve spring retainer. Replace the valve seat<br />
if unqualified:<br />
Protruded Height Standard Limit<br />
Intake 49.30mm 49.80mm<br />
Exhaust 49.30mm 49.80mm<br />
9. Finish the valve seat:<br />
(a) Before finishing the valve seat, check the clearance<br />
between the valve guide and the valve rod. Finish it after<br />
replacement if necessary.<br />
(b) Finish the width and angle of the valve seat to the rated<br />
values with a grinder.<br />
(c) Once finished, polish the valve and the valve seat<br />
together with abrasive. Then measure the protruded<br />
height of the valve rod.<br />
15A-57<br />
10. Replace the valve seat:<br />
(a) Cut part of the valve seat to replace from inside and<br />
remove it.<br />
(b) Finish the valve seat hole on the cylinder head subject to<br />
the outer diameter of the larger valve seat.<br />
Diameter of valve seat:<br />
Intake Valve<br />
Exhaust Valve<br />
Larger Valve Seat<br />
Hole<br />
Larger 0.30mm<br />
Larger 0.60mm<br />
Diameter of Valve<br />
Seat<br />
34.435 ~ 34.455mm<br />
4.735 ~ 34.755mm<br />
31.935 ~ 31.955mm<br />
32.235 ~ 32.255mm<br />
(c) Before installing the valve seat, heat the cylinder head to<br />
250 ℃ , or chill the seat in liquid nitrogen, to avoid<br />
possible blockage inside the cylinder head.<br />
(d) With a valve seat miller, finish the seat to rated width and<br />
angle.<br />
11. Install the valve as marked during removal.<br />
12. Install the valve spring washer.<br />
13. Install a new valve oil seal with a tool.<br />
14. Install the valve spring.<br />
When installing the valve spring, face the color-coded end towards the upper valve spring retainer.<br />
15. Install the upper valve spring retainer.<br />
15A-58<br />
16. With a tool, install the valve lock.<br />
17. Install the cylinder head. (Refer to "Chapter 15A. Engine mechanical system - cylinder head,<br />
ENGINE MECHANICAL - PISTON & CONNECTING ROD ASSEMBLY<br />
PISTON & CONNECTING ROD ASSEMBLY<br />
15A-59<br />
1 1st Gas Ring<br />
2 2nd Gas Ring<br />
3 Oil Ring<br />
4 Piston Pin<br />
5 Connecting Rod<br />
6 Connecting Rod Bolt<br />
7 Piston<br />
8 Piston & Connecting Rod Assembly<br />
9 Upper Connecting Rod Bearing<br />
10 Lower Connecting Rod Bearing<br />
11 Connecting Rod Cap<br />
12 Nut<br />
15A-60<br />
PISTON & CONNECTING ROD ASSEMBLY OVERHAUL<br />
1. Remove the engine assembly. (Refer to "Chapter 15A. Engine mechanical system - engine<br />
assembly, replacement")<br />
2. Remove the cylinder head. (Refer to "Chapter 15A. Engine mechanical system - cylinder head,<br />
3. Remove the oil tray. (Refer to "Chapter 18A. Lubrication - oil try, overhaul")<br />
4. Remove the engine oil strainer. (Refer to "Chapter 18. Lubrication - engine oil strainer,<br />
replacement")<br />
5. Mark the cylinder number on the larger side of the<br />
connecting rod to faciliate assembly.<br />
Put down the connecting rod, the connecting rod cap and<br />
the connecting rod bearing in the order of the cylinder<br />
numbers, to avoid confusion.<br />
6. Remove the retaining bolts of the connecting rod cap<br />
in sequence.<br />
7. Gently knock out the piston & connecting rod<br />
assembly with a wooden or plastic stick.<br />
8. Separate the connecting rod bearing.<br />
15A-61<br />
9. Remove the piston pin with a tool:<br />
Put down the piston, the piston pin and the connecting rod in the order of cylinder number, to avoid<br />
confusion.<br />
1 Push Rod<br />
2 Guide Block B<br />
3 Guide Block C<br />
4 Guide A<br />
5 Guide A<br />
6 Guide A<br />
7 Guide A<br />
8 Base<br />
Insert the push rod (special tool) into the piston from the<br />
side with arrow and attach the Guide Block C to the end<br />
of the push rod.<br />
Keep the forward mark of the piston upward and install<br />
the piston & connecting rod assembly onto the base of<br />
the piston pin installer.<br />
Press the piston pin out by force.<br />
10. Remove the 1st and 2nd gas rings and the oil ring.<br />
• Clean the carbon residue on the surface of the piston and inside the gas ring, as well as the<br />
grease inside the oil ring.<br />
• Be careful not to scratch the piston surface.<br />
15A-62<br />
11. Check whether there is damage, over wear or crack on the piston ring and replace it if any.<br />
Replace the piston and the piston ring together.<br />
12. Check the side clearance between the piston ring<br />
and the groove. If the limit is exceeded, replace the<br />
ring or both the piston and the ring.<br />
Standard: 0.02 ~ 0.06mm<br />
Limit: 0.1mm<br />
13. Insert the piston ring into the cylinder. Put it into the<br />
correct position against the piston top and measure<br />
the end clearance of the piston ring with a feeler<br />
blade.<br />
Replace the ring if the end play exceeds the limit:<br />
1st Gas<br />
Ring<br />
2nd Gas<br />
Oil Ring<br />
0.25 ~<br />
0.35mm<br />
0.40 ~<br />
0.55mm<br />
0.10 ~<br />
0.40mm<br />
Limit 0.8mm 0.8mm 1.0mm<br />
14. Check the oil clearance of the crankshaft pin with a<br />
plastigage:<br />
(a) Clear the engine oil on the connecting rod neck and<br />
bearing.<br />
(b) Cut the plastigauge into length as wide as the bearing.<br />
Lay the plastigauge across the crankshaft pin, parallel to<br />
its central axis.<br />
(c) Carefully install the connecting rod cap and tighten the<br />
nuts to its rated torque.<br />
(d) Carefully remove the connecting rod cap.<br />
15A-63<br />
Using a measuring ruler imprinted on the plastigauge<br />
package, measure the width of the widest part of the<br />
plastigauge and calculate the clearance value.<br />
Standard: 0.02 ~ 0.05mm<br />
15. Install the piston pin:<br />
Measure the following dimensions of the piston, the<br />
piston pin and the connecting rod:<br />
A: Length of piston pin in hole<br />
B: Width of pin socket<br />
C: Length of piston pin<br />
D: Width of connecting rod at smaller end<br />
Put the measurements into the following formula to<br />
calculate L. L = [(A - C) - (B - D)] / 2<br />
After inserting the push rod into the piston pin, install<br />
Guide A at the end of the push rod.<br />
Install the piston and the connecting rod with both<br />
forward marks in the same direction.<br />
Lubricate the external diameter of the piston pin with engine oil.<br />
Once assembled in Step 3, insert the push rod, piston pin and guide assembly into the piston pin hole<br />
from the side with the forward mark.<br />
15A-64<br />
Screw the Guide Block B into Guide A so that the<br />
clearance between Guide Block A and Guide Block B<br />
equals to L (L=((A-C)-(B-D)) / 2) plus 3 mm.<br />
Press the piston pin in by force. If the force is below the<br />
standard, replace the piston pin and the piston assembly,<br />
or the connecting rod.<br />
Standard: 7500 ~ 17500N<br />
16. Once installed, check whether the piston and the<br />
connecting rod move freely.<br />
15A-65<br />
17. Install the oil ring:<br />
• There is no difference between the upper and lower<br />
sides of the oil ring scraper and the main ring.<br />
• The new ring and oil ring scraper are color-coded to<br />
identify their dimensions.<br />
Dimension<br />
Larger 1.00mm<br />
Color Code<br />
N/A<br />
Red<br />
Yellow<br />
18. Install the 1st and 2nd gas rings:<br />
Install the main oil ring.<br />
Put the upper scraper in. During the installation, press<br />
one end of the scraper into the piston oil ring groove and<br />
press the remaining part into the groove with your thumb,<br />
as illustrated.<br />
Do not install the scraper with a pair of piston ring pliers,<br />
which may break the scraper.<br />
(c) Install the lower scraper in the same process of Step 2.<br />
(d) Check whether the installed ring can rotate freely.<br />
Install the 1st gas ring after the 2nd gas ring, with a pair<br />
of piston ring pliers.<br />
During installation, turn the mark upward to the top of the<br />
piston.<br />
There are identification marks at the opening of the gas<br />
ring. 1st gas ring: 1R, 2nd gas ring: 2R.<br />
The dimension marks are follows:<br />
Dimension Mark<br />
Larger 0.50 mm 50<br />
Larger 1.00 mm 100<br />
15A-66<br />
19. Adjust the opening directions of the gas rings and the oil ring:<br />
Lubricate the piston ring groove, the gas rings and the oil ring with clean engine oil.<br />
Adjust the openings of the gas rings and the oil ring to<br />
the position shown.<br />
1 Oil ring scraper opening<br />
2 Piston pin position<br />
3 Oil ring lower scraper opening<br />
Sleeve ring and 2nd gas ring<br />
opening<br />
5 1st gas ring opening<br />
6 Crankshaft belt pulley side<br />
20. Turn the crankshaft so that the crankshaft pin is at the center of the cylinder.<br />
21. Before inserting the piston & connecting rod assembly into the cylinder block, take proper<br />
threat protection on the connecting rod bolts. Be careful not to damage the crankshaft pin.<br />
22. During installation, confirm the dot (forward mark)<br />
on the top of the piston faces the side of the toothed<br />
timing belt.<br />
23. Use a proper piston ring compression tool to install<br />
the piston & connecting rod assembly.<br />
• When putting the assembly into the cylinder, be<br />
careful not to damage the crankshaft pin with the<br />
connecting rod cap bolts.<br />
• During the installation, gently press down the<br />
assembly with a wooden or plastic tool, without<br />
overly force, or it may break the piston ring or<br />
crankshaft pin.<br />
24. To replace the connecting rod bearing, choose and install it as follows:<br />
15A-67<br />
Measure the outer diameter of the crankshaft pin, identify<br />
the dimensions with different paint colors as illustrated,<br />
and group them subject to the table below.<br />
The identification mark of the connecting rod bearing is<br />
shown as followes:<br />
Crankshaft Pin<br />
Connecting Rod<br />
Bearing<br />
ID No. Dimension (mm/in) Mark<br />
I 44.995 ~ 45.000 1<br />
II 44.985 ~ 44.995 2<br />
III 44.980 ~ 44.985 3<br />
Inner diameter of connecting rod: 48.000 ~ 48.015mm<br />
If the outer diameter of the crankshaft pin is marked as "1", for example, pick up the bearing marked as<br />
"1" as well. If there is no mark on the crankshaft, measure the outer diameter of the pin and pick up a<br />
connecting rod bearing with the matching bear ("1").<br />
25. Install the connecting rod cap subject to the marks<br />
made during disassembly. If it a new connecting rod<br />
without combination mark, install the grooves of the<br />
upper bearing and the lower bearing on the both<br />
sides as illustrated.<br />
15A-68<br />
26. Measure the axial clearance of the connecting rod at<br />
the larger end with a feeler blade.<br />
Standard: 0.10 ~ 0.25mm<br />
Limit: 0.4mm<br />
27. Install the connecting rod nuts:<br />
Before the installation, if the cylinder head is already in place, remove the spark plug first and install<br />
the connecting rod cap nuts.<br />
(a) Use plastic zone torque technique on the connecting rod bolts and nuts. Check whether there is any<br />
stretch in the bolt before reuse.<br />
How to check: Tighten the nut along the thread of the bolt up to the full length. If the nut cannot be<br />
tightened smoothly, it means that the threaded part of the bolt might be stretched. Replace the bolt.<br />
(b) Lubricate the threaded part of the nuts and the surface with engine oil, before tightening the nuts.<br />
(c) Install each nut to the bolt and tighten it by hand. Then tighten the nuts alternately to install the cap<br />
(d) Tighten the nuts for the first time.<br />
(e) Make a paint mark on the head of each nut.<br />
(f) Make a paint mark on the bolt at the position 90° ~ 100°<br />
from that made on the nut in the direction of tightening.<br />
(g) Turn additional 90° ~ 100° to the nut and make sure that<br />
the paint mark on the nut and that on the bolt are in<br />
alignment.<br />
• If the nuts are tightened less than 90°, they may not<br />
hold the caps with sufficient strength. Pay attention<br />
to the angle during tightening.<br />
• If a nut is tightened exceeding 100°, completely<br />
remove all nuts and carry out the installation<br />
procedure again from Step 1.<br />
28. Install the engine oil strainer. (Refer to "Chapter 18. Lubrication - engine oil strainer,<br />
29. Install the oil tray. (Refer to "Chapter 18A. Lubrication - oil try, overhaul")<br />
30. Install the cylinder head. (Refer to "Chapter 15A. Engine mechanical system - cylinder head,<br />
31. Install the engine assembly. (Refer to "Chapter 15A. Engine mechanical system - engine<br />
ENGINE MECHANICAL - CRANKSHAFT, CYLINDER BLOCK & FLYWHEEL<br />
CRANKSHAFT, CYLINDER BLOCK & FLYWHEEL<br />
15A-69<br />
1 Cylinder Block<br />
2 Crankshaft Rear Oil Seal Cap<br />
3 Crankshaft Rear Oil Seal<br />
4 Crankshaft Thrust Bearing<br />
6 Crankshaft<br />
7 Lower Crankshaft Bearing<br />
8 Main Bearing Cap<br />
9 Main Bearing Cap Bolt<br />
5 Upper Crankshaft Bearing<br />
15A-70<br />
1 Flywheel Bolt<br />
2 Ball Bearing<br />
3 Flywheel<br />
4 Rear Cover<br />
5 Bell Housing<br />
6 Crankshaft Rear Oil Seal<br />
7 Crankshaft Rear Oil Seal Cap<br />
8 Cylinder Block<br />
15A-71<br />
3. Fix the engine cylinder block onto the flip frame for disassembly.<br />
4. Remove the oil tray. (Refer to "Chapter 18A. Lubrication - oil try, replacement")<br />
5. Remove the retaining bolts and nuts of the engine oil<br />
strainer and then the strainer.<br />
6. Remove the retaining bolts of the engine oil pump<br />
front cover and then the cover.<br />
7. Fix the flywheel with a tool.<br />
15A-72<br />
8. Remove the retaining bolts of the flywheel in<br />
numeric order and then the flywheel.<br />
9. Remove the retaining bolts then the cover.<br />
10. Remove the crankshaft rear oil seal.<br />
15A-73<br />
11. Remove the retaining bolts of the crankshaft rear oil<br />
seal cap and then the cap.<br />
12. Flip over the engine so that the oil tray faces upward.<br />
13. Remove the retaining bolts of the crankshaft main<br />
bearing cap in numeric sequence.<br />
14. Remove the crankshaft main bearing cap and disassemble the lower crankshaft bearing.<br />
15. Remove the crankshaft and measure the crankshaft<br />
oil clearance with a plastgage:<br />
Clear the oil on the surface of the crankshaft neck and<br />
inside the crankshaft.<br />
Install the crankshaft.<br />
Cut a piece of plastigage of the same width as the<br />
bearing and put it on the crankshaft neck, parallel to the<br />
latter.<br />
Carefully install the crankshaft main bearing cap and<br />
tighten the bolts to the rated toque.<br />
Torque: 25N•m+90° ~ 100°<br />
Remove the retaining bolts of the crankshaft main<br />
bearing cap and then the cap carefully.<br />
15A-74<br />
Use the scale imprinted on the plastigauge package to<br />
measure the width of the widest part of the plastigauge.<br />
Standard: 0.02 ~ 0.04mm<br />
16. Remove the crankshaft and the bearing.<br />
17. Take the engine block assembly from the flip frame<br />
and inspect:<br />
(a) Check for scratches, rust, and corrosion, visually or with<br />
flaw detecting agent. If defects are evident, correct or<br />
(b) Use a straightedge and a feeler gauge to check the block<br />
top surface for warpage. Make sure that the surface is<br />
free from gasket chips and other impurities.<br />
Standard: 0.05mm<br />
(c) If the warpage is excessive, correct within the allowable<br />
limit or replace.<br />
Grinding limit: 0.2mm<br />
Max. sum of cylinder block and cover to grind off:<br />
0.2mm<br />
Block height (new part): 284mm<br />
(d) The cylinder walls should be checked for scratch or other<br />
damage. Finish or replace it if apparent.<br />
(e) Measure the inner diameter and cylindricity of the<br />
cylinder with a cylinder bore. In case of heavy wear,<br />
finish the cylinder to a greater dimension or replace the<br />
piston and the ring with matching dimensions.<br />
Inner Diameter of Cylinder<br />
Cylindricity<br />
87mm<br />
≤ 0.01mm<br />
Choose the diameter of the larger piston subject to the<br />
maximum cylinder diameter.<br />
Mark<br />
Larger 0.50mm 0.50<br />
Larger 1.00mm 1.00<br />
15A-75<br />
Measure the outer diameter of the piston to use, in the<br />
thrust direction as shown.<br />
Follow the above measurement to calculate cylinder bore<br />
dimension:<br />
Cylinder bore dimension = Outer diameter of piston<br />
+ (clearance between piston and cylinder) - 0.02 mm<br />
(grinding volume)<br />
In case of finishing, finish four cylinders to the same<br />
dimension.<br />
(h) Finish the diameters of the cylinders to the said<br />
During finishing, to avoid possible error caused by rising<br />
temperature, perform the operations in the following order:<br />
No.2 -> No.4 -> No.1 -> No.3<br />
(i) Finish it to the final diameter (piston diameter +<br />
clearance between piston and cylinder).<br />
(j) Check the clearance between the piston and the<br />
18. Flip over the cylinder block onto the engine stand so that the oil tray faces upward.<br />
19. Pick up a suitable crankshaft bearing subject to the table below:<br />
Combination of Crankshaft Main Neck and Shaft Bore<br />
Crankshaft Main Neck<br />
Group Mark Outer Dia. (mm)<br />
Mark of Main<br />
Mark of Neck<br />
Bearing 1, 2, 4 &<br />
Bearing 3<br />
0 1 0<br />
I 0 56.994 ~ 57.000<br />
1 2 1<br />
2 3 2<br />
0 2 1<br />
II 1 56.988 ~ 56.994<br />
1 3 2<br />
2 4 3<br />
15A-76<br />
0 3 2<br />
III 2 56.982 ~ 56.988<br />
1 4 3<br />
2 5 4<br />
For example:<br />
(a) If the outer diameter mark the crankshaft neck is "0" and that of the bearing bore is “1”, choose No. 1, 2,<br />
4 or 5 bearing marked as “2” and No.3 bearing marked as “1”.<br />
If there is no mark on the crankshaft, measure the neck and pick up a matching bearing subject to the<br />
measurement.<br />
20. Install the thrust bearing as follows:<br />
(a) Install the bearing with groove at the cylinder block side.<br />
(b) Install the bearing without groove at the bearing cap side.<br />
(c) Install the crankshaft thrust bearing at the position of the<br />
No.3 main bore of the cylinder block. Lubricate the<br />
surface of the thrust bearing with some engine oil to<br />
faciliate installation.<br />
21. Install the crankshaft main bearing cap.<br />
The arrow on the cap points to the side of the toothed<br />
22. Install the crankshaft bearing cap bolts as follows:<br />
(a) Before tightening the retaining bolts of the bearing cap,<br />
measure the length of the bolts first. If beyond limit,<br />
replce them.<br />
Limit: 71.1mm<br />
(b) Lubricate the threaded part and surface of the bolts with<br />
engine oil.<br />
15A-77<br />
Tighten the retaining bolts of the crankshaft main bearing<br />
cap in numeric sequence.<br />
Mark the bolt heads with paint.<br />
Make a paint mark on the area around the bolt bearing<br />
surface at the position of 90° ~ 100° in the direction of<br />
Turn additional 90° ~ 100° to the bolts and make sure<br />
that the paint mark on the bolts and that on the cover are<br />
in alignment.<br />
hold the caps with sufficient strength. So pay<br />
attention to the angle during tightening.<br />
• If a bolt is tightened exceeding 100°, completely<br />
remove all bolts and carry out the installation<br />
23. After installation, check whether the crankshaft<br />
rotates freely as well as the axial clearance. If<br />
beyond limit, replace the bearing.<br />
Standard: 0.05 ~ 0.18mm<br />
Limit: 0.25mm<br />
15A-78<br />
24. Install the crankshaft rear oil seal with a tool.<br />
25. Install the crankshaft rear oil seal cap.<br />
• Before installation, clear the impurities on the suface of the cap without scratching the surface.<br />
• Apply the sealant (Mistubishi MD970389) or comparable alternative to the surface of the oil seal<br />
cap.<br />
• Quickly install the rear oil seal cap in 15 minutes, before the sealant is dried.<br />
• After installation, keep the sealed parts away from lubricant and coolant for around 1 hour.<br />
26. Install the rear cover and tighten the retaining bolts.<br />
27. Install the flywheel and lock it with a tool.<br />
15A-79<br />
28. Tighten the retaining bolts of the flywheel in numeric<br />
Torque: 135N·m<br />
29. Install the engine oil pump front cover and tighten<br />
the retaining bolts.<br />
30. Install the engine oil strainer and tighten the<br />
Nut torque: 19N·m<br />
Bolt torque: 19N·m<br />
31. Install the oil tray. (Refer to "Chapter 18A. Lubrication - oil try, replacement")<br />
32. Install the cylinder head. (Refer to "Chapter 15A. Engine mechanical system - cylinder head,<br />
33. Install the engine assembly. (Refer to "Chapter 15A. Engine mechanical system - engine<br />
EXHAUST SYSTEM<br />
EXHAUST PIPE ...............................................................................16A-1<br />
PRECAUTION............................................................................ 16A-1<br />
REPLACEMENT ........................................................................ 16A-2<br />
EXHAUST MANIFOLD.....................................................................16A-6<br />
REPLACEMENT ........................................................................ 16A-6<br />
36<br />
16A<br />
EXHAUST - EXHAUST PIPE<br />
16A-1<br />
EXHAUST PIPE<br />
1. BEFORE REMOVING MOUNTING RUBBER, ALWAYS APPLY A SMALL AMOUNT OF GREASE TO<br />
MOUNTING RUBBER FOR REMOVING OR INSTALLING EASILY.<br />
2. WHEN INSTALLING EXHAUST PIPE, ALWAYS USE NEW RING GASKET OTHERWISE GAS<br />
LEAKAGE WILL PRESENT.<br />
3. AFTER A LONG-TIME USED, THE EXHAUST PIPE GASKET WILL BE ADHERED TO EXHAUST<br />
PIPE. AFTER REMOVING THE MUFFLER, USE THE SCRAPER TO CLEAN THE SURFACE OF<br />
EXHAUST PIPE AND REPLACE WITH A NEW GASKET TO AVOID EXHAUST LEAKAGE.<br />
16A-2<br />
Exhaust pipe is a high temperature part. Never work around or attempt to service any parts of the<br />
exhaust system until it cools down.<br />
3. REMOVE REAR MUFFLER ASSY.<br />
Remove 2 rear muffler assy nuts.<br />
Support one end of exhaust pipe with a jack first, and then<br />
remove the other end.<br />
Remove the rear muffler mounting rubber.<br />
Remove rear muffler assy.<br />
4. INSPECT REAR MUFFLER ASSY.<br />
Tap or shake the muffler, check to make sure that broken<br />
element inside the muffler is the cause of unusual noise,<br />
if it is found, replace it.<br />
Check the appearance of muffler for corrosion holes that<br />
caused by moisture in air or from burning, If it is found,<br />
After a long-time used, the exhaust pipe gasket will be<br />
adhered to exhaust pipe. After removing the muffler, use<br />
the scraper to clean the surface of exhaust pipe and replace<br />
with a new gasket to avoid exhaust leakage.<br />
5. REMOVE FRONT MUFFLER ASSY.<br />
(a) Remove front muffler rear mounting rubber.<br />
Support one end of exhaust pipe with a jack, and then<br />
16A-3<br />
Remove 2 front muffler retaining nuts.<br />
Remove 2 support in the front of front muffler.<br />
Remove front muffler assy.<br />
6. INSPECT FRONT MUFFLER ASSY.<br />
(a) Tap or shake the muffler, check to ensure that broken<br />
(b) Check the appearance of muffler for corrosion holes that<br />
7. REMOVE MIDDLE EXHAUST PIPE.<br />
(a) loosen 2 retaining bolts fitting middle exhaust pipe to the<br />
(b) Remove the middle exhaust pipe.<br />
8. REMOVE CATALYTIC CONVERTER ASSY.<br />
(a) Disconnect front and rear oxygen sensor connectors.<br />
16A-4<br />
Remove retaining nut securing catalytic converter mounting<br />
bracket to the rear of transmission.<br />
Loosen 2 retaining nuts securing catalytic converter to<br />
exhaust manifold.<br />
Remove the catalytic converter.<br />
9. INSPECT CATALYTIC CONVERTER.<br />
(a) Tap the catalytic converter, if hear any noise, replace with a new one.<br />
(b) Using a scan tool, check the oxygen sensor signal fluctuation range. If the catalytic converter damage,<br />
oxygen sensor signal fluctuation range will become larger.<br />
• When reinstalling exhaust pipe each time, always replace ring gasket with new one.<br />
• When installing each mounting rubber, avoid twisting or unusual extension in up/down and left/<br />
right directions.<br />
10. INSTALL CATALYTIC CONVERTER ASSY.<br />
(a) Tighten 2 retaining nuts securing catalytic converter to<br />
Torque: 78 ~ 96 N•m<br />
16A-5<br />
Connect front and rear oxygen sensor connectors.<br />
Tighten retainng bolt securing catalytic converter mounting<br />
11. INSTALL MIDDLE EXHAUST PIPE.<br />
(a) Tighten 2 retaining bolts securing middle exhaust pipe to<br />
12. INSTALL FRONT MUFFLER ASSY.<br />
(a) Install 1 mounting rubber at the rear side of front muffler<br />
16A-6<br />
Install 2 support in the front of front muffler.<br />
Install 2 front muffler retaining nuts.<br />
13. INSTALL REAR MUFFLER ASSY.<br />
(a) Install rear muffler rubber support.<br />
Tighten 2 retaining bolts in the front of rear muffler.<br />
14. CHECK AFTER INSTALLATION.<br />
(a) Check clearance between exhaust pipe and rear bumper is uniform gap.<br />
(b) With engine running, check exhaust pipe joints for gas leakage and unusual noises.<br />
(c) Check to ensure that mounting bracket and mounting rubbers are installed properly stress.improper<br />
installation could result in excessive noise and vibration.<br />
EXHAUST - EXHAUST MANIFOLD<br />
16A-7<br />
Perform the operation with the exhaust system fully cooled down because the system will be hot just<br />
after engine stops.<br />
3. REMOVE CATALYTIC CONVERTER ASSY. (Refer to “Chapter 16A exhaust - exhaust pipe, replacement”)<br />
Ring gaskets are different on both sides of catalytic converter, take care not to misassemble them.<br />
4. LOWER THE VEHICLE.<br />
5. REMOVE OIL DIPSTICK PIPE.<br />
(a) Pull out oil dipstick.<br />
(b) Remove oil dipstick pipe retaining bolt.<br />
(c) Pull out oil dipstick pipe.<br />
6. REMOVE EXHAUSE MANIFOLD HEAT SHIELD.<br />
(a) Remove 4 exhause manifold heat shield retaining bolts,<br />
then take off the exhaust manifold heat shield.<br />
The exhaust manifold heat shield retaining bolts will be<br />
rusted after a long-time running. Be careful to remove these<br />
7. REMOVE EXHAUST MANIFOLD.<br />
(a) Remove 9 exhaust manifold retaining nuts.<br />
The exhaust manifold retaining nuts will be rusted after a<br />
long-time running. Use derusting spray when loosen the<br />
16A-8<br />
Remove the exhaust manifold.<br />
• Check whether parts have any damage or crack.<br />
• CHeck exhaust manifold and cylinder head surface<br />
for flatness by using a ruler and thickness gauge.<br />
Standard: 0.15 mm or less<br />
Limit value: 0.20 mm<br />
• Clean the dirt on exhaust manifold and cylinder head<br />
connect surface<br />
8. INSTALL A NEW EXHAUST MANIFOLD GASKET.<br />
If do not replace with a new gasket, use exhaust sealant to<br />
avoid exhaust leakage.<br />
9. INSTALL EXHAUST MANIFOLD.<br />
(a) Install exhaust manifold retaining nuts.<br />
• Apply rust-inhibiting lubricant on nuts for easier<br />
installation or removal next time.<br />
• Install the exhaust manifold retaining bolts diagonally.<br />
10. INSTALL EXHAUST MANIFOLD HEAT SHIELD.<br />
(a) Install 4 exhaust manifold heat shield retaining bolts.<br />
Torque: 10 ~ 14 N•m<br />
11. INSTALL OIL DIPSTICK PIPE.<br />
(a) Install oil dipstick pipe and tighten 1 retaining bolt.<br />
Replace oil dipstick pipe O-ring with a new one.<br />
(b) Insert oil dipstick completely into the dipstick pipe.<br />
16A-9<br />
12. INSTALL CATALYTIC CONVERTER ASSY. (Refer to “Chapter 16A exhaust - exhaust pipe, replacement”)<br />
13. CHECK AFTER INSTALLATION.<br />
Check to make sure exhaust manifold is installed properly between cylinder head and catalytic converter.<br />
With engine running, check exhaust manifold joints for gas leakage and unusual noises.<br />
COOLING SYSTEM<br />
COOLING SYSTEM .........................................................................17A-1<br />
PRECAUTION............................................................................ 17A-1<br />
COMPONENTS ......................................................................... 17A-2<br />
PROBLEM SYMPTOMS TABLE................................................ 17A-3<br />
ON-VEHICLE INSPECT............................................................. 17A-4<br />
COOLANT ........................................................................................17A-6<br />
REPLACEMENT ........................................................................ 17A-6<br />
RESERVIOR.....................................................................................17A-8<br />
REPLACEMENT ........................................................................ 17A-8<br />
COOLING FAN ASSY....................................................................17A-10<br />
OVERHAUL ............................................................................. 17A-10<br />
RADIATOR.....................................................................................17A-13<br />
REPLACEMENT ...................................................................... 17A-13<br />
THERMOSTAT...............................................................................17A-18<br />
OVERHAUL ............................................................................. 17A-18<br />
COOLANT PUMP...........................................................................17A-23<br />
OVERHAUL ............................................................................. 17A-23<br />
17A<br />
COOLING - COOLING SYSTEM<br />
17A-1<br />
1. COOLING SYSTEM PRECAUTION.<br />
(a) When disconnecting the cooling hose, use a suitable container to recycle the retains of coolant. If it is<br />
not to be used, dispose of them according to the regulations.<br />
(b) When disconnecting the pipes of cooling system, do not let debris go into the pipes of cooling system. It<br />
may damage the cooling system and engine.<br />
(c) When disconnecting the cooling system pipes connectors, a special plug must be used to cover the<br />
nozzle to prevent dirt and impurities.<br />
(d) Coolant is poisonous, always keep it away from children and pets. If it is not to be used, disposal them<br />
according to the regulations.<br />
(e) Do not open the radiator cap when the engine is hot. Coolant temperature should be reduced to 50 ℃<br />
(120 ℉) below, remove the radiator cap. Otherwise, the cooling liquid or vapor emitting heat may cause<br />
(f) Use foton specified coolant, do not use water instead of coolant. Water will damage the engine<br />
because of corrosion.<br />
(g) Clean radiator outside regularly, which can prevent mud and dust deposition from damaging radiator.<br />
17A-2<br />
1 Radiator Assy<br />
3 Fan Cowl<br />
4 Locking Nut<br />
5 Cooling Fan Assy<br />
6 Bolt, Spring Washer And Flat Washer<br />
8 Bolt, Spring Washer And Flat Washer<br />
9 Washer<br />
10 Nut<br />
11 Cooling Fan Bracket<br />
12 Reservoir Refilling Hose<br />
13 Reservoir Assy<br />
14 Bolt, Spring Washer And Flat Washer<br />
15 Clamp<br />
16 Radiator To Reservoir Vent Hose<br />
17 Hose Clip<br />
18 Clamp<br />
17A-3<br />
1. Coolant (Lack or leaking) Chapter 17A cooling - coolant, replacement<br />
2. Coolant (Non-standard) Chapter 17A cooling - coolant, replacement<br />
3. Thermostat (Damaged) Chapter 17A cooling - thermostat, overhaul<br />
Engine overheated<br />
4. Engine (Rough work) -<br />
5. Radiator (Poor cooling) Chapter 17A cooling - cooling system, precaution<br />
6. Cooling fan (Damaged) Chapter 17A cooling - cooling fan assy, overhaul<br />
7. Cooling system (Blocked) -<br />
1. Radiator(Damaged) Chapter 17A cooling - radiator, replacement<br />
Coolant leaking<br />
Engine noise<br />
2. Cooling system hose<br />
(Broken)<br />
3. Coolant pump(Damaged) Chapter 17A cooling - coolant pump, replacement<br />
4. Coolant reservoir(Damaged) Chapter 17A cooling - reservoir, replacement<br />
1. Cooling fan(Damaged) Chapter 17A cooling - cooling fan assy, overhaul<br />
2. Coolant pump(Damaged) Chapter 17A cooling - coolant pump, overhaul<br />
3. Cooling line -<br />
17A-4<br />
ON-VEHICLE INSPECT<br />
1. CHECK WHETHER COOLANT LEVEL IS NORMAL.<br />
2. IF COOLANT LACKS ABNORMALLY, CHECK COOLING SYSTEM FOR LEAKAGE.<br />
Never remove the reservior cap while the engine and radiator are still hot, as fluid and steam can be<br />
blown out.<br />
Fill the reservior with coolant and attach a reservior cap<br />
tester.<br />
Warm up the engine.<br />
Pump it to 110 kPa, and check that the pressure does not<br />
drop.<br />
If the pressure drops, check the hoses, reservior, radiator<br />
or water pump for leakage. If no external leakage is found,<br />
check the heater core, cylinder block and head.<br />
3. CHECK ENGINE COOLANT LEVEL IN COOLANT<br />
RESERVOIR.<br />
(a) When the engine is cool, the engine coolant level should<br />
be between the ”LOW” and ”FULL” line.<br />
4. CHECK ENGINE COOLANT QUALITY.<br />
If the coolant level too low, check for leakage and add<br />
”FOTON Long-effective coolant” or equivalent up to the<br />
”FULL” line.<br />
Do not use water instead of coolant.<br />
(a) Remove the reservior cap.<br />
(b) Place a container under the radiator to bloom the coolant from the coolant drain hole.<br />
(c) Loosen the coolant drain plug to drain the coolant and check if there is any excessive deposits of rust or<br />
scale around the radiator cap and radiator filler hole. The coolant should be free from oil. If excessively<br />
dirty, replace the coolant.<br />
(d) Tighten the drain plug and check the coolant level in the coolant reservoir. Fill the coolant if necessary.<br />
5. INSPECT FINS BLOCKAGE.<br />
(a) If fins are clogged, wash them with water or a steam cleaner and dry them with compressed air.<br />
• If the distance between the steam cleaner and core is too close, there is a possibility of<br />
damaging the fins. So keep the proper injection distance.<br />
17A-5<br />
• Be careful not to spray water directly onto electronic components.<br />
6. INSPECT COOLING FAN.<br />
(a) Disconnect the cooling fan connector.<br />
(b) Connect battery and ammeter to the connector.<br />
(c) Check that the cooling fan rotates smoothly, and check the reading on the ammeter.<br />
Temperature: 20°C<br />
Current: 8.0 ~ 12.0 A<br />
(d) Connect the cooling fan connector.<br />
(e) No abnormal noise except fan itself when the fan is rotating at a high speed.<br />
17A-6<br />
COOLING - COOLANT<br />
COOLANT<br />
17A-7<br />
17A-8<br />
COOLING - RESERVIOR<br />
RESERVIOR<br />
1. DRAIN ENGINE COOLANT. (Refer to “Chapter 17A cooling- coolant, replacement”)<br />
2. REMOVE RESERVIOR.<br />
(a) Open reservior pressure cover by turn it slowly to release<br />
the built-up pressure.<br />
Do not open the reservior cap when the engine is hot.<br />
Coolant temperature should be reduced to 50 ° C (120 ° F)<br />
below, remove the radiator cap. Otherwise, the cooling<br />
Loosen reservior vent hose clamp and disconnect vent<br />
hose.<br />
Remove reservior retaining bolt.<br />
Disconnect coolant fluid level sensor connector.<br />
Loosen reservior refilling hose clamp and disconnect<br />
reservior refilling hose.<br />
Remove reserivor.<br />
Do not lose the rubber grommet located on radiator upper<br />
support when removing reservior. If damaged, replace<br />
them.<br />
17A-9<br />
3. INSTALL RESERVIOR.<br />
Connect reservior refilling hose and tighten retaining<br />
Connect coolant fluid sensor connector.<br />
Position the lower support of reservior into rubber grommet<br />
on upper radiator frame.<br />
Tighten reservior retaining bolt.<br />
Connect reservior vent hose.<br />
(a) Fill the coolant to max level when cold, check coolant fluid level indicator is normal in instrument cluster<br />
and no coolant leakage is found.<br />
17A-10<br />
COOLING - COOLING FAN ASSY<br />
COOLING FAN ASSY<br />
2. DISCONNECT COOLING FAN ASSY CONNECTOR.<br />
3. REMOVE COOLING FAN BRACKET.<br />
(a) Remove 4 cooling fan bracket retaining bolts/nuts.<br />
(b) Remove retaining nut securing A/C pipe clamp to vehicle<br />
(c) Move A/C pipes slightly to one aside .<br />
Disengage A/C pipes from the dual line clip at the bottom of<br />
cooling fan bracket.<br />
Remove cooling fan bracket carefully.<br />
17A-11<br />
4. REMOVE COOLING FAN ASSY.<br />
Remove 6 cooling fan retaining bolts.<br />
Remove cooling fan assy from the left side under the<br />
5. INSPECT COOLING FAN.<br />
(a) Using an ohmmeter, measure the resistance between the terminals.<br />
Main cooling fan:<br />
• Resistance between white wire and brown wire:1.527±15%Ω ;<br />
• Resistance between white wire and red wire:1.2±15%Ω ;<br />
Secondary cooling fan:<br />
• Resistance between white wire and brown wire:1.562±15%Ω ;<br />
• Resistance between white wire and red wire:1.377±15%Ω ;<br />
(b) Visually inspect cooling fan blade for cracks or unusual bend.<br />
(c) Rotate cooling fan by hand, the blades should be rotated smoothly.<br />
6. INSTALL COOLING FAN ASSY.<br />
(a) Position cooling fan assy into place from under the<br />
(b) Tighten 6 cooling fan retaining bolts.<br />
Torque: 9 ~ 11 N.m<br />
7. INSTALL COOLING FAN BRACKET.<br />
(a) Positon cooling fan bracket properly in the original<br />
positon.<br />
(b) Tighten 4 bracket retaining bolts and nuts.<br />
(c) Engage A/C pipes into dual line clip at the bottom of<br />
17A-12<br />
Tighten A/C pipes clamp retaining nut.<br />
8. CONNECT COOLING FAN ASSY CONNECTORS.<br />
Start the vehicle, check cooling fan for normal operation and ensure that no unusual noise is heard<br />
when engine warms up and A/C switch is on.<br />
COOLING - RADIATOR<br />
17A-13<br />
RADIATOR<br />
(120 ° F) below, remove the reservior cap. Otherwise, the cooling liquid or vapor emitting heat may<br />
1. DRAIN ENGINE COOLANT. (Refer to “Chapter 17A cooling - coolant, replacement”)<br />
2. REMOVE RESERVIOR. (Refer to “Chapter 17A cooling - reservior, replacement”)<br />
3. REMOVE COOLING FAN ASSY. (Refer to “Chapter 17A cooling - coolant fan assy, replacement”)<br />
4. REMOVE FRONT GRILLE. (Refer to “Chapter 88 exterior and interior trim - front grille, replacement”)<br />
5. REMOVE FRONT BUMPER. (Refer to “Chapter 88 exterior and interior trim - front bumper,<br />
6. REMOVE ENGINE HOOD LOWER COVER PANEL.<br />
(a) Remove 4 engine hood lower cover panel retaining bolts.<br />
Remove 2 push pins from the back of lower cover panel.<br />
Remove engine hood lower cover panel.<br />
7. REMOVE THE FAN COWL.<br />
(a) Remove 2 retaining bolts in the upper fan cowl.<br />
(b) Remove reservior refilling hose from fan cow fixing clip.<br />
17A-14<br />
Push fan cowl upward until 2 lower support disengage<br />
from radiator lower mounting notch.<br />
Remove lower fan cowl.<br />
8. REMOVE RADIATOR UPPER AND LOWER WATER<br />
HOSES.<br />
Remove engine water outlet hose to upper radiator.<br />
Check water hose for cracks and deterioration, replace if<br />
Remove engine water inlet hose to lower radiator.<br />
9. REMOVE THE RADIATOR UPPER SUPPORT.<br />
(a) Pull out reservior vent hose from fixing clip on radiator<br />
upper support.<br />
(b) Disconnect engine hood switch connector and remove<br />
the wire harness clip from the radiator upper support.<br />
Disconnect washer motor connector.<br />
Remove 2 washer assy retaining bolts.<br />
17A-15<br />
Remove 5 radiator upper support retaining bolts.<br />
Remove radiator upper support and put it aside.<br />
Do not lose the upper mounting rubber installed on radiator<br />
upper mounting pin when removing radiator. if damaged,<br />
replace them.<br />
10. REMOVE THE RADIATOR.<br />
Remove 2 retaining bolts securing upper condenser to<br />
radiator.<br />
Remove 2 retaining bolts securing both upper air<br />
deflector to radiator.<br />
The vehicle was equipped with air deflector depend on<br />
different Model.<br />
Remove 2 retaining bolts securing lower condenser to<br />
Remove 2 retaining bolts securing both lower air<br />
Hang and hold condenser with wire after removing the bolts<br />
securing condenser to radiator to prevent the A/C pipes or<br />
condenser from damaging.<br />
Lift up and remove the radiator.<br />
Do not lose lower mounting rubbers of radiator when<br />
removing radiator and check the mounting rubbers for<br />
damage, replace them as required.<br />
17A-16<br />
11. INSTALL THE RADIATOR.<br />
Make sure lower mounting rubbers are seated onto raditaor<br />
lower support before installing radiator.<br />
Tighten 2 retaining bolts securing upper condenser to<br />
Tighten 2 retaining bolts securing both upper air deflector<br />
to radiator.<br />
The vehicle is equipped with air deflector depending on<br />
Model.<br />
Tighten 2 retaining bolts securing lower condenser to<br />
Tighten 2 retaining bolts securing both lower air deflector<br />
12. INSTALL RADIATOR UPPER AND LOWER WATER<br />
Connect engine water inlet hose to radiator.<br />
Connect engine water outlet hose to radiator.<br />
17A-17<br />
13. INSTALL THE FAN COWL.<br />
(a) Position fan cowl into place from under the vehicle.<br />
(b) Tighten 2 upper fan cowl retaining bolts.<br />
14. INSTALL THE RADIATOR UPPER SUPPORT.<br />
Positon the radiator upper support.<br />
Make sure mounting rubbers are seated onto raditaor upper<br />
support pin.<br />
(b) Tighten 5 radiator upper support retaining bolts.<br />
15. INSTALL ENGINE HOOD LOWER COVER PANEL.<br />
(a) Position engine hood lower cover panel, then install 2<br />
push pins.<br />
Tighten 4 lower cover panel retaining bolts.<br />
16. INSTALL COOLING FAN ASSY. (Refer to “Chapter 17A cooling - cooling fan, overhaul”)<br />
17. INSTALL RESERVIOR. (Refer to “Chapter 17A cooling - reservior, replacement”)<br />
18. INSTALL FRONT BUMPER. (Refer to “Chapter 88 exterior and interior trim - front bumper assy,<br />
19. INSTALL FRONT GRILLE. (Refer to “Chapter 88 exterior and interior trim - front grille, replacement”)<br />
20. FILL COOLANT. (Refer to “Chapter 17A cooling - coolant, replacement”)<br />
21. CHECK AFTER INSTALLATION.<br />
(a) After installing radiator, let engine be running until cooling fan runs at high speed. Check coolant for<br />
leakage.<br />
17A-18<br />
COOLING - THERMOSTAT<br />
2. DRAIN COOLANT. (Refer to “Chapter 17A cooling - coolant, replacement”)<br />
4. DISCONNECT BATTERY NEGATIVE CABLE.<br />
It is recommended that the battery negative cable must be disconnected, prior to thermostat removing,<br />
to avoid touching generator positive retaining nut.<br />
5. INSTALL ASSISTANT DRIVER SEAT. (Refer to “Chapter 84 seat - driver / assistant driver seat,<br />
6. REMOVE ENGINE COMPARTMENT COVER UNDER<br />
17A-19<br />
7. REMOVE ENGINE WATER INLET HOSE NO. 2.<br />
Remove engine water inlet hose NO. 2 clamp.<br />
(b) Disconnect engine water inlet hose NO. 2.<br />
8. REMOVE THERMOSTAT.<br />
Remove 2 thermostat housing retaining bolts.<br />
Remove thermostat housing.<br />
Pull out thermostat.<br />
17A-20<br />
9. INSPECT THERMOSTAT.<br />
(a) The thermostat is numbered with the valve opening<br />
temperature.<br />
Immerse the thermostat in water and gradually heat the<br />
water.<br />
Check the valve opening temperature.<br />
Valve opening temperature:<br />
80 - 84 ℃<br />
If the valve opening temperature is out of the specification,<br />
replace the thermostat.<br />
Check the valve lift.<br />
Valve lift: 8 mm or more, at 95 ℃ .<br />
• If the valve opening temperature is out of the specification, replace the thermostat.<br />
• Check that the valve is fully closed when the thermostat is at low temperature (below 77 ℃ ).<br />
• If it is not closed, replace it with a new one.<br />
10. INSTALL THERMOSTAT.<br />
Always replace with a new thermostat rubber ring when<br />
performing thermostat operation.<br />
17A-21<br />
Install thermostar and rubber ring.<br />
Make sure that rubber ring is fitting to the thermostat properly<br />
and they are fully seated.<br />
Install thermostat housing.<br />
Tighten thermostat housing retaining bolts.<br />
11. CONNECT ENGINE WATER INLET HOSE NO. 2.<br />
(a) Connect engine water inlet hose NO. 2, then tighten<br />
retaining clamp.<br />
12. CONNECT BATTERY NEGATIVE CABLE.<br />
13. FILL COOLANT. (Refer to “Chapter 17A cooling - coolant, replacement”)<br />
(a) After installing thermostat, start the engine until cooling fan runs at high speed. check coolant for<br />
17A-22<br />
15. INSTALL ENGINE COMPARTMENT COVER UNDER<br />
Tighten 5 engine compartment cover retaining bolts.<br />
Cover front floor covering.<br />
16. INSTALL ASSISTANT DRIVER SEAT. (Refer to “Chapter 84 seat - driver / assistant driver seat,<br />
17. PUT DOWN DRIVER SEAT AND LOCK IT.<br />
COOLANT PUMP<br />
COOLING - COOLANT PUMP<br />
17A-23<br />
1. DISCONNECT BATTERY NEGATIVE CABLE.<br />
3. REMOVE GENERATOR BELT. (Refer to “Chapter 20A starting and charging - generator, overhaul”)<br />
4. REMOVE COOLANT PUMP PULLEY RETAINING BOLTS.<br />
5. REMOVE ENGINE TIMING BELT HOUSING.<br />
6. REMOVE ENGINE TIMING BELT.<br />
7. REMOVE COOLANT PUMP.<br />
(a) Remove coolant pump retaining bolt.<br />
(b) Remove coolant pump.<br />
Remove coolant pump gasket.<br />
Using a scraper, clean dirt on coolant pump and engine<br />
block connect surface.<br />
Clean the dirt, do not damage coolant pump and engine<br />
8. INSPECT COOLANT PUMP.<br />
(a) Rotate coolant pump and it should turn smoothly.<br />
(b) There should be no clearance between coolant pump shaft and coolant punp bearing, and no abnormal<br />
noise when it turns.<br />
(c) No coolant leakage around coolant pump.<br />
9. INSTALL COOLANT PUMP.<br />
(a) Install coolant pump gasket. to avoid coolant leaking, use coolant pump sealant if necessary.<br />
17A-24<br />
After using the coolant pump sealant, wait for 15 minutes then fill the coolant.<br />
Install coolant pump retaining bolts.<br />
Torque: 14 N•m<br />
10. INSTALL ENGINE TIMING BELT.<br />
11. INSTALL ENGINE TIMING BELT HOUSING.<br />
12. INSTALL COOLANT PUMP PULLEY RETAINING BOLTS.<br />
13. INSTALL GENERATOR BELT. (Refer to “Chapter 20A starting and charging - generator, overhaul”)<br />
14. CONNECT BATTERY NEGATIVE CABLE.<br />
15. FILL COOLANT. (Refer to “Chapter 17A cooling - coolant, replacement”)<br />
16. CHECK AFTER INSTALLATION.<br />
(a) After replacing coolant pump, let engine be running until cooling fan runs at high speed. check coolant<br />
for leakage.<br />
LUBRICATION SYSTEM<br />
LUBRICATION SYSTEM .................................................................18A-1<br />
PRECAUTION............................................................................ 18A-1<br />
COMPONENT............................................................................ 18A-2<br />
ENGINE OIL .....................................................................................18A-4<br />
REPLACEMENT ........................................................................ 18A-4<br />
OIL FILTER ......................................................................................18A-6<br />
REPLACEMENT ........................................................................ 18A-6<br />
OIL PAN ...........................................................................................18A-8<br />
REPLACEMENT ........................................................................ 18A-8<br />
OIL PUMP ......................................................................................18A-11<br />
OVERHAUL ............................................................................. 18A-11<br />
18A<br />
LUBRICATION - LUBRICATION SYSTEM<br />
18A-1<br />
Prolonged and repeated contact with engine oil will cause the skin fat to be removed, resulting in dry<br />
skin, allergies and dermatitis. In addition, used engine oil contains potentially harmful pollutants which<br />
may cause skin cancer. Therefore, the skin must be protected in appropriate methods and with<br />
1. LUBRICATION SYSTEM PRECAUTION.<br />
(a) Avoid contacting with oil for a long time, especially the used engine oil.<br />
(b) Wear protective clothing including waterproof work gloves.<br />
(c) Avoid contaminated clothing, especially underwear containing the oil.<br />
(d) Never put rags contaminated with oil in pockets.<br />
(e) Avoid eyes contacting with oil, must wear goggles, In addition, equipment must be prepared to clean<br />
the eye. And wrapping the wound must be dealt with immediately.<br />
(f) Frequent use of soap and water can clean, especially before meals, and make sure all the oil has been<br />
removed (skin cleansers can also be used to assist with the nail brush). After cleaning, it is<br />
recommended to replace the natural skin oils cotton suet.<br />
(g) Do not use gasoline, kerosene, diesel, thinner or solvent to clean skin.<br />
(h) Before each work, apply cream to help skin cleaning after work.<br />
(i) If your skin is abnormal, consult a doctor immediately.<br />
18A-2<br />
COMPONENT<br />
1 Drain Plug<br />
2 Oil Pan Bolt<br />
3 Oil Filter<br />
4 Oil Pan<br />
5 Oil Strainer<br />
6 Oil Strainer Gasket<br />
7 Oil Pump Cover Bolt<br />
8 Engine Oil Pressure Switch<br />
9 Relief Plug<br />
10 Gasket<br />
11 Relief Spring<br />
12 Relief Plug<br />
13 Oil Filter Bracket<br />
14 Oil Filter Bracket Gasket<br />
15 Front Case Plug<br />
16 O-ring<br />
17 Front Case Inside Bolt<br />
18 Front Case<br />
19 Front Case Gasket<br />
20 Oil Pump Cover<br />
21 Oil Pump Driven Gear<br />
22 Oil Pump Drive Gear<br />
23 Front Crankshaft Oil Seal<br />
24 Balance Shaft Oil Seal<br />
18A-3<br />
25 Oil Pump Oil Seal<br />
26 Right Balance Shaft<br />
27 Left Balance Shaft<br />
28 Right Balance Shaft Front Bearing<br />
29 Right Balance Shaft Rear Bearing<br />
30 Left Balance Shaft Bearing<br />
18A-4<br />
LUBRICATION - ENGINE OIL<br />
ENGINE OIL<br />
18A-5<br />
18A-6<br />
LUBRICATION - OIL FILTER<br />
5. DRAIN ENGINE OIL .(Refer to “Chapter 18A lubrication - engine oil, replacement”)<br />
Without special circumstances, the oil filter should be replaced with engine oil, avoid oil pollution and<br />
keep engine operation.<br />
18A-7<br />
18. PUT DOWN DRIVER SEAT AND LOCK IT.<br />
18A-8<br />
LUBRICATION - OIL PAN<br />
1. OPEN ENGINE COMPARTMENT COVER.<br />
2. OPEN OIL FILLER CAP.<br />
4. DRAIN ENGINE OIL. (Refer to “Chapter 18A lubrication - engine oil, replacement”)<br />
6. PULL OIL DIPSTICK OUT.<br />
7. REMOVE OIL DIPSTICK PIPE.<br />
(a) Remove oil dipstick pipe mounting bolt.<br />
(b) Pull oil dipstick pipe out.<br />
Check O- ring at the bottom of oil dipstick pipe for damage<br />
and replace it as required.<br />
8. RAISE AND SUPPORT THR VEHICLE.<br />
9. REMOVE OIL PAN.<br />
(a) Remove 4 bolts (or nuts) securing front cover to transmission.<br />
(b) Remove the front cover.<br />
(c) Remove bolts on the backside of oil pan.<br />
18A-9<br />
Remove the bolts on the rightside of oil pan.<br />
Remove the bolts on the leftside of oil pan.<br />
Remove the bolts in the front of oil pan through the front<br />
crossmember.<br />
Insert proper tool between cylinder block and oil pan,<br />
then separate them by hammer.<br />
Never use screwdriver or chisel to remove the oil pan. It will<br />
damage the oil pan flange and cause oil leakage.<br />
10. CLEAN CONNECT SURFACE OF OIL PAN AND ENGINE BLOCK.<br />
11. APPLY A 4MM WIDE SEALANT TO THE ENTIRE<br />
CIRCUMFERENCE OF OIL PAN FLANGE.<br />
Circle the bolt hole with sealant strips around.<br />
18A-10<br />
12. INSTALL OIL PAN.<br />
(a) Position oil pan and install oil pan mounting bolts.<br />
(b) Tighten the bolt according to the number as shown.<br />
Torque: 6 ~ 7 N•m<br />
Be sure to install the oil pan quickly while the sealant is wet<br />
(within 15 minutes).After installation, keep the sealant area<br />
away from the oil for about one hour.<br />
Install front cover for transmission.<br />
13. INSTALL OIL DIPSTICK PIPE.<br />
14. LOWER VEHICLE.<br />
15. INSERT OIL DIPSTICK.<br />
16. OPEN OIL FILLER CAP AND FILL ENGINE OIL TO SPECIFIED LEVEL.<br />
17. INSTALL OIL FILLER CAP.<br />
18. PARK THE VEHICLE ON LEVEL GROUND AND START ENGINE UNTIL IT IS WARM.<br />
19. CHECK OIL PAN AND ENSURE THERE IS NO OIL LEAKAGE.<br />
20. TURN THE IGNITION SWITCH OFF AND WAIT FOR 10 MINUTES.<br />
21. PULL OIL DIPSTICK OUT AND ENSURE OIL LEVEL IS BETWEEN “MAX” MARK AND THE “MIN”<br />
22. PUT DOWN DRIVER SEAT AND LOCK IT.<br />
LUBRICATION - OIL PUMP<br />
18A-11<br />
OIL PUMP<br />
2. RAISE AND SUPPORT THR VEHICLE.<br />
3. DRAIN ENGINE OIL.(Refer to “Chapter 18A lubrication - engine oil, replacement”)<br />
4. REMOVE OIL PAN.(Refer to “Chapter 18A lubrication - oil pan, replacement”)<br />
5. OPEN ENGINE COMPARTMENT COVER.<br />
7. REMOVE OIL PRESSURE SWITCH.<br />
8. REMOVE OIL FILTER BRACKET MOUNTING BOLT AND<br />
OIL FILTER BRACKET.<br />
9. REMOVE FRONT CASE PLUG WITH SPECIAL TOOL.<br />
18A-12<br />
10. REMOVE PLUG ON THE LEFT SIDE OF CYLINDER<br />
BLOCK AND INSERT A SCREWDRIVER INTO PLUG<br />
HOLE TO LOCK BALANCE SHAFT.<br />
11. REMOVE LEFT BALANCE SHAFT BOLT INSIDE<br />
FRONT CASE PLUG.<br />
12. TAKE OUT SCREWDRIVER FROM THE INSIDE OF PLUG ON THE CYLINDER BLOCK SIDE.<br />
13. REMOVE FRONT CASE RETAINING BOLTS.<br />
14. TAKE FRONT CASE AND BALANCE SHAFT AWAY AND INSPECT IT.<br />
(a) Check oil holes for blocking and clean if necessary.<br />
(b) Check the front case for cracks and other damage. Replace cracked or damaged front case if necessary.<br />
(c) Check the oil seal lip for wear and damage. Replace oil seal if necessary.<br />
Check balance shaft front bearing section for wear,<br />
damage and seizure. If there are anything damaged with<br />
the section, replace the front case.<br />
18A-13<br />
15. REMOVE OIL PUMP COVER MOUNTING BOLTS.<br />
16. INSPECT OIL PUMP GEAR.<br />
(a) Using rules and feeler gauge, measure the gear<br />
clearance.<br />
Standard:<br />
Drive gear: 0.08 ~ 0.14 mm<br />
Dirven gear: 0.06 ~ 0.12 mm<br />
(b) Install the oil pump gear to the front case and rotate it to<br />
ensure smooth rotation with no looseness.<br />
(c) Ensure that there is no ridge wear on the contact surface<br />
between the front case and the gear surface of the oil<br />
pump cover.<br />
17. TAKE OIL PUMP DRIVE GEAR AND DRIVEN GEAR AWAY.<br />
18. REMOVE FRONT CRANKSHAFT OIL SEAL, BALANCE SHAFT OIL SEAL AND PUMP OIL SEAL.<br />
Oil seal can not be reused after removal and replace it with new one.<br />
19. USING SPECIAL TOOL, REMOVE BALANCE SHAFT<br />
FRONT BEARING FROM CYLINDER BLOCK.<br />
(a) Check balance shaft front bearing section for wear,<br />
damage and seizure, replace it as required.<br />
20. USING SPECIAL TOOL, REMOVE BALANCE SHAFT<br />
REAR BEARING FROM THE CYLINDER BLOCK.<br />
(a) Check balance shaft rear bearing section for wear,<br />
Remove balance shaft front bearing first, then remove<br />
balance shaft rear bearing .<br />
18A-14<br />
21. INSTALL LEFT BALANCE SHAFT REAR BEARING.<br />
(a) Position tools into cylinder block.<br />
(b) Apply engine oil to the outer surface of bearing and<br />
bearing hole in the cylinder block.<br />
Using special tool, install the rear bearing.<br />
The left rear bearing hasn’t oil holes.<br />
22. INSTALL RIGHT BALANCE SHAFT REAR BEARING.<br />
(a) Align the ratchet ball of the special tool with the oil hole in<br />
the rear bearing to install the bearing of the special tool.<br />
(b) Apply engine oil to the front bearing outer surface and<br />
bearing hole in the cylinder.<br />
Using special tool, install the rear bearing. Make sure<br />
that the oil hole of the bearing is aligned with the oil hole<br />
of the cylinder block.<br />
18A-15<br />
Remove rear bearing installing portion from special tool.<br />
Using special tool, install front bearing.<br />
23. INSTALL OIL PUMP DRIVE GEAR AND OIL PUMP<br />
DRIVEN GEAR.<br />
Apply engine oil generously to the gears and line up the<br />
alignment marks.Oil pump drive gear timing mark as<br />
shown in the figure.<br />
Oil pump driven gear timing mark.<br />
18A-16<br />
24. INSTALL OIL PUMP COVER AND TIGHTEN RETAINING<br />
BOLTS.<br />
25. INSTALL A NEW FRONT CASE GASKET.<br />
26. POSITION FRONT CASE AND TIGHTEN RETAINING<br />
BOLTS TEMPORARILY.<br />
27. USING SPECIAL TOOL, INSTALL OIL PUMP SEAL.<br />
28. USING SPECIAL TOOL, INSTALL BALANCE SHAFT<br />
OIL SEAL.<br />
18A-17<br />
29. USING SPECIAL TOOL, INSTALL FRONT CRANKSHAFT<br />
30. INSTALL OIL FILTER BRACKET SEAL.<br />
31. POSITION OIL FILTER BRACKET AND TIGHTEN<br />
RETAINING BOLTS TEMPORARILY.<br />
32. INSTALL OIL PRESSURE SWITCH.<br />
(a) Clean the thread portion of oil pressure switch and apply<br />
sealant to the thread portion.<br />
Using special tool, tighten the oil pressure switch.<br />
Torque: 10 N•m<br />
18A-18<br />
33. REMOVE PLUG ON THE LEFT SIDE OF CYLINDER<br />
BLOCK. INSERT A SCREWDRIVER INTO PLUG<br />
HOLE TO LOCK BALANCE SHAFT ON THE LEFT<br />
SIDE OF CYLINDER BLOCK.<br />
34. INSTALL LEFT BALANCE SHAFT MOUNTING BOLT<br />
INSIDE FRONT CASE PLUG HOLE.<br />
Torque: 37 N•m<br />
35. INSTALL PLUG ON THE CYLINDER BLOCK SIDE.<br />
Torque: 24 N•m<br />
36. TIGHTEN BOLTS ON THE FRONT CASE OF OIL<br />
PUMP.<br />
37. TIGHTEN OIL FILTER BRACKET MOUNTING BOLT.<br />
Torque: 19 N•m<br />
18A-19<br />
38. USING TOOL, INSTALL FRONT CASE PLUG.<br />
39. INSTALL ENGINE TIMING BELT.<br />
40. INSTALL OIL STRAINER RETAINING BOLTS.<br />
41. INSTALL OIL PAN. (Refer to “Chapter 18A lubrication - oil pan, replacement”)<br />
42. LOWER VEHICLE.<br />
43. FILL ENGINE OIL. (Refer to “Chapter 18A lubrication - enginge oil, replacement”)<br />
44. PUT DOWN DRIVER SEAT AND LOCK IT.<br />
IGNITION SYSTEM ............................................................................ 19-1<br />
COMPONENTS ........................................................................... 19-1<br />
IGNITION MODULE/SPARK PLUG WIRE/SPARK PLUG................ 19-2<br />
OVERHAUL ................................................................................. 19-2<br />
IGNITION - IGNITION SYSTEM<br />
19-1<br />
1 Engine Cylinder Head Cover<br />
2 Ignition Module Bracket<br />
3 Ignition Module<br />
4 Bolt<br />
5 Spark Plug<br />
6 Spark Plug Wire<br />
19-2<br />
IGNITION - IGNITION MODULE/SPARK PLUG WIRE/SPARK PLUG<br />
IGNITION MODULE/SPARK PLUG WIRE/SPARK PLUG<br />
Remove spark plug wire from ignition module in a certain<br />
Remove spark plug wire.<br />
19-3<br />
5. REMOVE IGNITION MODULE<br />
Disconnect ignition module connector.<br />
Remove 2 ignition module retaining bolts.<br />
Remove ignition module.<br />
6. REMOVE SPARK PLUG.<br />
7. INSPECT SPARK PLUG WIRE.<br />
• Check if the spark plug wire has been broken down.<br />
• Make sure the spark plug wire resistance is less than 4 KΩ.<br />
8. CHECK IGNITION MODULE.<br />
• Check if crack exists on the ignition module.<br />
• Check ignition module condition.<br />
(a) Using diagnostic tool, ensure there exists no DTC. If there exists DTC, record it. Ensure that the DTC<br />
fault is resolved even the DTC is unrelated with ignition system.<br />
(b) Pull out fuel pump relay.<br />
19-4<br />
Lightly pull out spark plug wire and remove the spark plug.<br />
Install a new spark plug to the spark plug wire, touch spark plug negative to the engine cylinder block.<br />
Start engine, check the flash over.<br />
If the flash over is weak or no flash over, replace with a new ignition module. After replacing the new<br />
ignition module, if the flash over become strong, we can ensure the ignition module has been damaged.<br />
If there is still no flash over, check the ignition circuit and inspect the spark plug.<br />
Using diagnostic tool, ensure there appears no DTC, except for the DTC record in step (b). Clear all<br />
DTCs.<br />
9. INSPECT SPARK PLUG.<br />
• Check spark plug insulator outer surface for cracks.<br />
• Check spark plug flash over for carbon deposition.<br />
• Check spark plugs for burned off or melted positive and<br />
negative electrode.<br />
• Check spark plug gap.<br />
Standard value: 1 ~ 1.1 mm<br />
10. INSTALL SPARK PLUG.<br />
11. INSTALL IGNITION MODULE.<br />
(a) Install 2 ignition module retaining bolts.<br />
12. INSTALL SPARK PLUG WIRE.<br />
(c) Connect ignition module connector.<br />
13. INSTALL INTAKE HOSE. (Refer to “Chapter 14A intake air- intake air hose, replacement”)<br />
19-5<br />
15. START ENGINE AND CONFIRM IT IS IN GOOD CONDITION.<br />
STARTING AND CHARGING SYSTEM ..........................................20A-1<br />
PRECAUTION............................................................................ 20A-1<br />
PROBLEM SYMPTOMS TABLE................................................ 20A-2<br />
GENERATOR...................................................................................20A-4<br />
COMPONENTS ......................................................................... 20A-4<br />
OVERHAUL ............................................................................... 20A-5<br />
STARTER.......................................................................................20A-12<br />
COMPONENTS ....................................................................... 20A-12<br />
OVERHAUL ............................................................................. 20A-13<br />
BATTERY.......................................................................................20A-21<br />
COMPONENTS ....................................................................... 20A-21<br />
USE AND MAINTENANCE...................................................... 20A-22<br />
INSPECTION ........................................................................... 20A-24<br />
BATTERY COMMON PROBLEMS, THE CAUSES ANALYSIS AND<br />
TROUBLESHOOTING............................................................. 20A-25<br />
REPLACEMENT ...................................................................... 20A-27<br />
20A<br />
STARTING AND CHARGING - STARTING AND CHARGING SYSTEM<br />
STARTING AND CHARGING SYSTEM<br />
AND CHARGING<br />
1. STARTING AND CHARGING SYSTEM PRECAUTION.<br />
20A-1<br />
Battery may have escaping explosive gas. in order to avoid personal injury, keep ventilated in engine<br />
room before maintaining battery. To avoid electric arc, disconnect battery negative cable first and<br />
connect the negative cable last.<br />
Battery electrolyte is very dangerous. It can damage the machine and cause serious burns. When<br />
maintaining battery, prepare neutralizers concentration soda water, wear safety eyepiece and wear<br />
protective clothing, which can avoid personal injury.<br />
When using compressed air, wear appropriate goggles and protective mask. Dust particles and dirt can<br />
cause injury.<br />
Don't tighten the electrical connectors excessively, which may damage the starter.<br />
Never short two cables of the battery, it will cause a rapid battery fever even an explosion occur. The<br />
escaping gas from battery is easily be burned by the spark, so do not use fire near battery.<br />
After the generator operation, do not try to use spark check whether the generator works. Use bulb or<br />
multimeter to perform the test. Otherwise it will damage the generator diode.<br />
Check the generator silicon rectifier devices, it is strictly forbidden to use multimeter or apply 220V<br />
directly for generator insulation check, otherwise it will make diode breakdown and damaged.<br />
20A-2<br />
Use the table below to help you find the cause of the problem. The numbers indicate the priority of<br />
the likely cause of the problem. Check each part in order. If necessary, replace these parts.<br />
1. Starter switch control circuit (Open) Check wire harness<br />
Starter out of operation<br />
2. Brush and rectifier (Poor<br />
connection)<br />
3. Starter inside circuit (Open or short)<br />
1. Battery (Low voltage)<br />
Chapter 20A starting and charging - starter,<br />
use and maintenance<br />
2. Starter wire (Poor connection) Check wire harness<br />
Starter lacks power,<br />
can not srart engine<br />
Starter keep working<br />
after engine start<br />
3. Rectifier (Surface damaged or<br />
stains)<br />
4. Brush (Wear) or Brush spring (Loss<br />
elastic force)<br />
5. Solenoid switch (Contacts ablation)<br />
6. Bearing (Wear),commutator (Wipe<br />
shell)<br />
1. Starter relay (Copper contacts bond)<br />
2. Starter commutator (Bend or break)<br />
3. Starter gear tooth surface contact<br />
(Roughening or stuck)<br />
-Chapter 20A starting and charging - starter,<br />
1. Generator connect wire (damaged) Check wire harness<br />
Generator out of operation<br />
2. Rotor winding (Open)<br />
3. Rectifier diode (Damaged)<br />
4. Brush (Poor connection)<br />
5. Regulator (Damaged)<br />
Chapter 20A starting and charging - generator,<br />
20A-3<br />
Generator lacks<br />
enough electricity<br />
1. Belt losing tensity<br />
2. Brush (Poor connection) or collector<br />
ring (Smeary)<br />
3. Regulator (Damaged)<br />
Chapter 15A engine mechanical - engine<br />
accessory belt, overhaul<br />
4. Battery lose electrolyte<br />
20A-4<br />
STARTING AND CHARGING - GENERATOR<br />
1 Generator Belt Pulley<br />
2 Rotator Component<br />
3 Rear Bearing<br />
4 Bearing Carrier<br />
5 Front Bearing<br />
6 Front Cover<br />
8 Anchor Plate<br />
9 Regulator And Brush Carriage<br />
10 Brush<br />
11 Brush Ring<br />
12 Rectifier Component<br />
13 Back Cover<br />
7 Stator Component<br />
20A-5<br />
1. TURN IGNITION SWITH OFF.<br />
4. REMOVE A/C COMPRESSOR BELT. (Refer to “Chapter 61 heater and air conditioning - A/C compressor,<br />
5. REMOVE POWER STEERING PUMP BELT. (Refer to “Chapter 52 power steering - power steering<br />
pump and fliud reservior assy, replacement”)<br />
6. REMOVE GENERAOR BELT.<br />
(a) Loosen locking bolt securing belt tensioner.<br />
(b) Loosen adjustment bracket mounting bolt.<br />
Loosen generator lower mounting nut.<br />
(d) Rotate adjustment bolt and adjust generator belt<br />
(e) Remove generator belt.<br />
Check generator belt for crack and replace it as required.<br />
20A-6<br />
7. REMOVE GENERATOR.<br />
(a) Loosen generator positive cable connecting nut.<br />
(a) Disconnect generator connector.<br />
Remove generator adjustment bolt.<br />
Remove generator lower support bolt.<br />
Remove generator.<br />
8. DISASSEMBLE GENERATOR.<br />
Using pneumatic tools, loosen generator belt pulley retaining<br />
nut.<br />
Loosen retaining bolts attaching generator front cover to<br />
stator component.<br />
Insert a screwdriver between front cover and stator then<br />
separate them.<br />
• If it is difficult to be separated, slap the front cover<br />
slightly with rubber hammer and pry it with screwdriver.<br />
• Do not insert screwdriver too deep to prevent stator<br />
component being damaged.<br />
20A-7<br />
Using a electric iron (180 ~ 250 w), remove stator. This<br />
operation should be within 4 seconds to prevent diode<br />
from heat.<br />
Loosen 4 retaining bolts from rectifier.<br />
Using a electric iron, remove rectifier from regulator.<br />
• Ensure that the heat is not transmitted from electric<br />
iron to diode for long time.<br />
• Do not let diode pin bear too much force.<br />
Remove and inspect rotor.<br />
• Check the rotor coil is conductive, and confirm that the<br />
collector rings are conductive. Measure the resistance of<br />
rotor. If the resistance is less than specified value, it<br />
means the rotor is short circuit. If it is not conductive or it<br />
is short circuit, replace the rotor assy.<br />
Specified value: 3 ~ 5 Ω<br />
• Check that rotor coil ground. Confirm that it is insulative<br />
between collector ring and core. If not, replace the rotor<br />
20A-8<br />
• Using a vernier caliper, measure the slip ring diameter.<br />
Standard: 14.2 ~ 14.4 mm<br />
Limit: 12.8 mm<br />
(h) Remove and inspect stator.<br />
• Check the stator for continuity. Confirm that the coil lead<br />
is conductive. If not, replace the stator assy.<br />
• Check the coil ground. Confirm that it is not conductive<br />
between coil and stator core. Replace the stator assy if<br />
conductive.<br />
(i) Inspect stator rectifier.<br />
• Diode group (three diodes) check: Using an ammeter to<br />
connect two ends of each diode, check if three diodes<br />
are conductive. If it is not conductive in both directions, it<br />
means the diodes are broken, and it is required to<br />
replace the rectifier assy.<br />
Get rid of welding point of brush lead, then take out the<br />
brush.<br />
20A-9<br />
If brush is so worn to reach wear limit line, replace brush.<br />
9. ASSEMBLE GENERATOR.<br />
(a) When installing new brush, weld brush lead in the<br />
condition when brush is pressed down to brush bracket<br />
as shown.<br />
Tighten 4 retaining bolts of rectifier.<br />
Weld rectifiers and stator.<br />
Before mounting rotor on rear cover, insert a steel wire<br />
into small hole on rear cap, then erect mounted rotor by<br />
brush, pull out steel wire.<br />
20A-10<br />
Install rotor.<br />
Tighten the retaining bolts attaching generator front<br />
cover to stator component.<br />
10. POSITION GENERATOR BELT PULLY. USING PNEUMATIC TOOLS, INSTALL GENERATOR BELT<br />
PULLEY RETAINING NUT.<br />
11. INSTALL GENERATOR.<br />
(a) place generator into proper position.<br />
(b) Install generator adjustment bolt and lower suppor bolt.<br />
Position adjustment bolt and lower support bolt ,but just<br />
install, do not tighten.<br />
Connect generator connector.<br />
Tighten generator positive cable connecting nut.<br />
12. INSTALL GENERATOR BELT.<br />
(a) Adjust adjustment bolt until generator belt is in proper<br />
20A-11<br />
Tighten belt tensioner locking bolt.<br />
Tighten adjustment bracket mounting bolt.<br />
Torque: 20 ~ 24 N•m<br />
Tighten nut to generator lower support bolt.<br />
13. INSTALL POWER STEERING PUMP BELT. (Refer to “Chapter 52 power steering - power steering<br />
14. INSTALL A/C COMPRESSOR BELT. (Refer to “Chapter 61 heater and air conditioning - A/C compressor,<br />
15. CONNECT BATTERY NEGATIVE CABLE.<br />
16. PUT DOWN ENGINE COMPARTMENT COVER AND LOCK IT.<br />
17. START THE VEHICLE AND CHECK GENERATOR FOR GOOD CONDITION.<br />
20A-12<br />
STARTING AND CHARGING - STARTER<br />
1 Front Bracket<br />
2 Spring<br />
3 Starter Drive Lever<br />
4 Rubber Washer<br />
5 Planetary Gear Bracket<br />
6 Solenoid Component<br />
7 Rubber Washer<br />
8 Steel Ball<br />
9 Planetary Gear<br />
11 Overdrive Clutch<br />
12 Locating Snap Ring<br />
13 Magnet Yoke Assy<br />
14 Commutator<br />
15 Brush<br />
16 Brush Bracket<br />
17 Starter Shell Bolt<br />
18 Rear Bearing<br />
19 Rear Bracket<br />
10 Internal Gear<br />
20A-13<br />
4. REMOVE STARTER.<br />
(a) Disconnect starter control wire connector.<br />
Remove starter positive cable locking nut.<br />
Remove 2 starter retaining bolts.<br />
Remove starter.<br />
5. INSPECT STARTER.<br />
(a) Pinion gap adjustment.<br />
• Disconnect the field coil wire from the M-terminal of the<br />
magnetic switch.<br />
• Connect a 12-volt battery between the S-terminal and M-<br />
terminal.<br />
This test must be performed quickly (less than 10 seconds)<br />
to prevent the coil from being burned.<br />
• When the 12-volt battery is connected between the S-<br />
terminal and M-terminal, the pinion will move out.<br />
20A-14<br />
• Check the pinion-to-stopper clearance (pinion gap) with<br />
a feeler gauge.<br />
Standard: 0.5 ~ 2.0 mm<br />
• If the pinion gap is out of specification, adjust by adding<br />
or removing gasket(s) between the magnetic switch and<br />
front bracket.<br />
(b) Magnetic switch pull-in test.<br />
• When turn ignition switch on, the pinion will move out. If<br />
the pinion moves out, the pull-in coil is good. If it doesn't,<br />
replace the magnetic switch.<br />
(c) Magnetic switch hold-in test.<br />
• Connect a 12-volt battery between the S-terminal and<br />
body.<br />
• <strong>Manual</strong>ly pull out the pinion as far as the pinion stopper<br />
• If the pinion remains out, everything is operating properly.<br />
If the pinion moves in, the hold-in circuit is open.<br />
Replace the magnetic switch.<br />
20A-15<br />
Magnetic switch return test.<br />
• Connect a 12-volt battery between the M-terminal and<br />
to prevent the coil from burning.<br />
• Pull the pinion out and release. If the pinion quickly<br />
returns to its original position, everything is operating<br />
properly. If it doesn't, replace the magnetic switch.<br />
Be careful not to get your fingers caught when pulling out<br />
the pinion.<br />
6. DISASSEMBLE STARTER.<br />
(a) Disconnect magnetic coil lead nut from magnetic switch.<br />
Remove magnetic switch retaining bolts.<br />
Remove starter shell retaining bolts.<br />
20A-16<br />
Disassemble starter as components art shown.<br />
• When removing armature, do not lose the steel ball<br />
mounted in the bearing ends.<br />
• Using a proper control sleeve, push and press the<br />
locating snap ring to the overdrive clutch side, and<br />
make it be away from the clip spring.<br />
• Remove the snap spring with snap ring pliers, then<br />
remove the locating snap ring and overdrive clutch.<br />
7. CLEAN STARTER PARTS.<br />
Do not put the parts in the detergent for cleaning. If the magnet yoke, excitation winding lead or rotor is<br />
immerged in detergent, their insulating ability will be damaged.<br />
Clean starter parts with cloth.<br />
Drive parts can not be immerged in detergent for cleaning. Before delivering out of factory, the<br />
overdrive clutch is greased. If clean it by detergent, its grease might be removed.<br />
Using a brush and dipping with detergent, clean drive parts then dry them with a cloth.<br />
8. INSPECT COMMUTATOR.<br />
(a) Support the commutator with a pair of V block and turn it<br />
to measure the runout of the surface using a dial gauge.<br />
Standard: ≤ 0.05 mm<br />
Limit: 0.1 mm<br />
Measure the diameter of the commutator.<br />
Standard: 29.4 mm<br />
Limit: 28.4 mm<br />
20A-17<br />
Measure the depth of the undercut between segments.<br />
Standard: 0.5 mm<br />
Limit: 0.2 mm<br />
9. INSPECT BRUSH AND BRUSH BRACKET.<br />
(a) Check that it is conductive between brush plate and brush bracket, if not, it is normal.<br />
(b) Check the commutator contact surface of each brush for abnormal roughness. Also check the height of<br />
the brush. Replace the brush holder if the height is lower than the limit.<br />
Limit: 7.0 mm<br />
(c) When the contact surface of the brush is rectified or the brush holder is replaced, recondition the<br />
contact surface with sandpaper wrapping around the commutator.<br />
10. INSPECT OVERDRIVE CLUTCH.<br />
(a) Make sure that the pinion can not be turned counterclockwise<br />
and can be turned clockwise freely.<br />
(b) Check the pinion for abnormal waring and damage.<br />
11. INSPECT ARMATURE COIL.<br />
(a) Set the armature in a growler.<br />
(b) While holding a thin strip of iron against the armature in<br />
parallel with its axis, turn the armature slowly. The<br />
armature is normal if the iron strip is not attracted to the<br />
armature or it does not vibrate.<br />
Clean the surface of the armature thoroughly before performing<br />
the test.<br />
Check the insulation between commutator segments and<br />
armature coils. It is normal if there is not continuity.<br />
20A-18<br />
Check continuity between a segment and another. It is<br />
normal if there is continuity.<br />
12. INSPECT MAGNETIC SWITCH.<br />
(a) Coil open circuit test.<br />
• Check that there is continuity between the M terminal<br />
and body A.<br />
• If there is no continuity, replace the magnetic switch.<br />
Contact fusion check.<br />
• Check that there is no continuity between the B terminal<br />
and M terminal.<br />
• If there is continuity, replace the magnetic switch.<br />
Switch contact check.<br />
• Push the indicated end of the magnetic switch with a<br />
strong force to close the internal contacts. Without<br />
releasing the switch end, check that there is continuity<br />
between the B terminal and M terminal.<br />
13. ASSEMBLE STARTER.<br />
(a) Using a suitable puller, pull stop ring until it gets over<br />
snap ring.<br />
20A-19<br />
Install locating snap ring and overdrive clutch.<br />
Assemble starter as components art shown.<br />
Tighten the starter shell retaining bolts.<br />
Torque: 8 ~ 10 N•m<br />
Tighten the magnetic switch retaining bolts.<br />
Connect the magnetic coil lead nut to magnetic switch.<br />
Torque: 14 ~ 16 N•m<br />
20A-20<br />
14. INSTALL STARTER.<br />
(a) Tighten 2 starter retaining bolts.<br />
Torque: 68 ~ 72 N•m<br />
Connnect and tighten starter positive cable locking nut.<br />
Torque: 18 ~ 20 N•m<br />
Connect starter control wire connector.<br />
15. LOWER THE VEHICLE.<br />
16. CONNECT BATTERY NEGATIVE CABLE.<br />
STARTING AND CHARGING - BATTERY<br />
20A-21<br />
BATTERY<br />
2 Battery Fix Frame<br />
3 Battery Fix Rod<br />
4 Mounting Nut<br />
5 Battery Tray<br />
6 Bolt And Washer<br />
20A-22<br />
USE AND MAINTENANCE<br />
1. CHARGING DEVICE.<br />
DC power supply must be used for battery charging, howerever, what is supplied by power plant is AC<br />
that it must be transformed into DC, After transform, the charging can be performed.<br />
Rectifier.<br />
Controllable silicone voltage regulation charger.<br />
2. CHARGE PRECAUTIONS.<br />
(a) Charging should choose in ventilated dry room, indoor temperature in 5 ℃ ~ 40 ℃ is advisable.<br />
(b) Battery can not be overlap shelved, also do not put them on the ground directly. It should be put on the<br />
wooden support, and cannot be set with alkaline battery or other chemicals.<br />
(c) Charging in field should be far away from fire and heat.<br />
(d) Liquid temperature should not exceed 45 ℃ and otherwise cooling measures shouldl be taken (by<br />
reducing filling current or stopping sharge or being cooled down in water tank).<br />
3. CHARGE CONNECTION.<br />
(a) The positive pole of charger is to be connected with the positive pole of battery, while the negative pole<br />
of charger should be connected with the negative pole of battery. Never connect them reversely.<br />
(b) Charge of most batteries may be determined based on the size of motor power. Connection for charge<br />
must be firm.<br />
4. CHARGING MODES.<br />
(a) Constant current charge.<br />
(b) Constant voltage charge.<br />
(c) Quick charge.<br />
5. AFTER CHARGING, USING THE BELOW METHODS, CHECK THE BATTERY CAPACITY IS<br />
RESTORED TO STANDARD.<br />
(a) Voltage method<br />
Voltage Determination Treatment<br />
above 12.5 v normal go on using<br />
11.5 ~ 12.5 v undercharge additional charge<br />
below 11.5 v over-discharge or internal failure to be further checked after charging<br />
Capacity method<br />
Capacity Tester Display Determination Treatment<br />
white zone fully charged go on using<br />
green zone normal go on using<br />
yellow zone undercharge additional charge<br />
red zone over-discharge to be further checked after charging<br />
20A-23<br />
6. USING AND MAINTENANCE OF BATTERY IN WINTER<br />
Keep the battery is to be maintained under full charge status, avoid the electrolyte from being frozen<br />
arising from drop in density, which may give rise to breakage of container, curve of pole plats, as well as<br />
smash and dropout of active substances, and other failures.<br />
Because the battery capacity reduced in winter, when start the engine in cold status, preheated the<br />
engine and each time start the engine should not more than 15 seconds, two starting interval 2 ~ 3<br />
minutes, if can not start the engine in three times, troubleshooting, then restarting.<br />
20A-24<br />
1. APPEARANCE INSPECTION.<br />
(a) Observe whether the battery appearance in good condition. Check if fixed terminal and wires are<br />
connected firmly.<br />
(b) Observe whether the battery shell and the center partition cracks, and use a wooden beat shell and<br />
center partitions respectively, listen to the sound without breaking, especially the central baffle and shell<br />
side of shell wall at the junction of four, prone to crack, should be carefully examined.<br />
(c) Through mirrors, green for fully charged, red and white says lack of electricity and no electricity. Need<br />
of the following capacity, voltage detection.<br />
2. CAPACITY TEST.<br />
(a) The excel tester is also known as the discharging tongs.<br />
It consists of a DC voltmeter of three volts and one load<br />
resistance.<br />
(b) The tips of the two tongs shall be pressed on the anode<br />
and the cathode tightly and maintain for five seconds in<br />
the measurement. Observe the terminal voltage in the<br />
state of the big load discharging and the discharging<br />
content and the starting ability can be judged correctly.<br />
(c) For the excel tester of different brands, the readings of<br />
the current and the voltage shall be read according to the<br />
regulations of the factory manual. Generally, the single<br />
voltage of the battery in good state shall be above 1.5 V<br />
and keep steady within five seconds. If the voltage drops<br />
rapidly within five minutes or the voltage of one single<br />
cell is 0.1 V lower than that of others, it indicates there<br />
are troubles in the battery and it shall be repaired.Below<br />
is the use of excel tester of discharge plan detection<br />
income cross-references.<br />
Display Zone Determination Treatment<br />
3. VOLTAGE TEST.<br />
The following table is derived using the digital multimeter test table.<br />
under 112.5 v over-discharge or internal fault to be further checked after charging<br />
20A-25<br />
TROUBLESHOOTING<br />
1. ELECTRICAL QUALITY OF ONE FULL-CHARGED BATTERY REDUCE WITHOUT USE FOR A<br />
LONG PERIOD.<br />
• Causes analysis:<br />
The full-charged battery without use will lose its electrical quality gradually and this phenomenon is<br />
known as “self-discharge”. The important cause of self-discharge is the impure materials. If there are<br />
impurities in the material of the polar plate or in the electrolyte, there will be a potential difference<br />
between the impurity and the polar plate and between the impurities. A closed “local current” is formed<br />
and would make the discharge of the battery.<br />
• Troubleshooting:<br />
For the battery which has discharged seriously, it can be discharged completely or excessively. This will<br />
enable the impurities on the polar plate into the electrolyte. Then, pour the electrolyte out and clean the<br />
battery with distilled water. Finally, inject the new electrolyte and re-charge the battery.<br />
2. BATTERY EXPLODE.<br />
The water in the electrolyte hydrolyzes into hydrogen or oxygen and a lot of bubbles are generated;<br />
there are short circuit and vulcanization troubles in the battery; the temperature increases while<br />
charging and large amount of water are evaporated. Then if the vent holes of the injection hole cover<br />
are plugged or there are a lot of gases which are unable to escape, the battery will explode when the<br />
inner pressure comes to a limit (or there are sparks).<br />
(a) The vent holes of the injection hole cover shall be cleared.<br />
(b) In order to avoid sparks, the wirings on the polar stud shall be fastened.<br />
(c) The injection hole cover shall be opened first when check with the excel tester.<br />
(d) Control the charging amount and do not over-charge in order to reduce the releasing amount of the<br />
gases. Open flames are prohibited and the ventilation shall be ensured in the charging room.<br />
3. RAPID DECREASE OF THE LIQUID LEVEL DURING THE USE PROCESS OF THE BATTERY.<br />
(a) Excessive charging current lead to evaporation of water.<br />
(b) Battery shell broken.<br />
(a) Add distilled water.<br />
(b) Repair shell, add the electrolyte.<br />
4. A YELLOW OR WHITE PASTE APPEARS ON BATTERY COVER.<br />
The yellow or white paste surrounding the battery cover and the polar stud is caused by the corrosion of<br />
the polar studs, wiring clip and the fixed frame by the sulfuric acid sprayed.<br />
In order to avoid these pastes, clean the electrolyte sprayed on the battery cover and the shell with a<br />
cloth soaked with the soda solution of 10 percents. Then wipe with water and dry with a clean cloth.<br />
The paste on the wire ends and the studs shall be wiped with the cloth soaked with soda solution. If<br />
there are oxides of poor conductivity, scrape them with a little knife and clean them. It would be best to<br />
smear a coat of Vaseline or butter on the cover after the polar studs and wiring clips are fastened.<br />
20A-26<br />
The vehicle for <strong>Foton</strong> <strong>View</strong> <strong>CS2</strong> is equipped with maintenance-free battery. If battery is bad, replace the<br />
battery as a unit. To avoid personal injury, it is strictly prohibited to disassemble the battery.<br />
Disassembly is limited to find the cause of the problem and provide information through professional<br />
testing.<br />
20A-27<br />
3. REMOVE BATTERY CABLE.<br />
(a) Open shield and disconnect battery negative cable.<br />
Disconnect the negative cable first when removal.<br />
Open shield and disconnect battery positive cable.<br />
4. REMOVE BATTERY FIX FRAME.<br />
(a) Remove battery fix rod mounting nut.<br />
(b) Remove battery fix frame.<br />
5. REMOVE BATTERY.<br />
Battery should be put up, placing battery upside down is prohibited.<br />
20A-28<br />
6. REMOVE BATTERY TRAY.<br />
(a) Loosen 3 battery tray retaining bolts.<br />
(b) Remove battery tray.<br />
7. INSTALL BATTERY TRAY.<br />
(a) Install 3 battery tray retaining bolts.<br />
Torque: 16 ~ 18 N•m<br />
8. INSTALL BATTERY.<br />
(a) Position battery.<br />
(b) Place battery fix frame and tighten fix rod mounting nut.<br />
Connect battery positive cable, tighten mounting nut and<br />
cover shield.<br />
Connect battery negative cable, tighten mounting nut<br />
and cover shield.<br />
• If terminals has sediments, remove the impurities<br />
then apply thin layer of grease to terminal.<br />
• Connect positive battery cable first when installing.<br />
A SINGLE MIRROR IS INOPERATIVE .....................................04-445<br />
ABS CONTROL IS UNREASONABLE ......................................04-119<br />
ABS MODULE CONNECTOR .....................................................04-98<br />
ABS SYSTEM IS INOPERATIVE...............................................04-122<br />
ACCELERATE PEDAL ............................................................. 12A-25<br />
AIR FILTER ASSY ...................................................................... 14A-6<br />
AIR PURIFIER LAMP IS INOPERATIVE ...................................04-283<br />
ALL FOG LAMPS ARE INOPERATIVE .....................................04-229<br />
ALL HEADLAMPS ARE INOPERATIVE ....................................04-207<br />
INOPERATIVE ...........................................................................04-295<br />
ALL POWER WINDOWS ARE INOPERATIVE .........................04-421<br />
ALL STOP LAMPS ARE INOPERATIVE ...................................04-260<br />
ANTI-LOCK BRAKE SYSTEM .....................................................04-96<br />
AUDIO SYSTEM ........................................................................04-361<br />
AUXILIARY POWER..................................................................04-374<br />
INOPERATIVE ...........................................................................04-307<br />
A/C CONTROL PANEL ILLUMINATION IS NOT INOPERA-<br />
TIVE(LIGHTING SYSTEM) ........................................................04-307<br />
A/C SYSTEM IS INOPERATIVE................................................04-153<br />
BACK - UP LAMP IS INOPERATIVE(ONE SIDE) .....................04-269<br />
BACK - UP LAMPS ARE INOPERATIVE (BOTH SIDES) .........04-271<br />
BASIC IDLE SPEED ADJUSTMENT(THROTTLE BODY) ....... 11A-23<br />
BASIC INSPECTION ...........04-150, 04-182, 04-335, 04-362, 04-418,<br />
04-440, 04-453, 04-469, 04-495<br />
BASIC PRINCIPLE(GASOLINE ENGINE CONTROL<br />
SYSTEM) .................................................................................... 11A-8<br />
BASIC SERVICE PROCEDURE..................................................04-10<br />
BATTERY.................................................................................. 20A-21<br />
IN SPECIFIED DISTANCE (DISPLAYER IS NORMAL) ............04-408<br />
CANISTER SOLENOID VALVE.....................................11A-52, 13A-4<br />
CAPTURING DATA .....................................................................04-20<br />
CENTRAL DOME LIGHT IS INOPERATIVE .............................04-278<br />
CENTRAL LOCKING CONTROLLER ASSY A..........................04-493<br />
CENTRAL LOCKING CONTROLLER ASSY A PIN...................04-417<br />
CENTRAL LOCKING CONTROLLER ASSY B..........................04-494<br />
CHECK ACCESSORY BELT(INSPECTION)...............................05-20<br />
CHECK AND CLEAN WINDSHIELD FLUME(INSPECTION)......05-16<br />
SCRIBED TORQUE(INSPECTION) ............................................05-22<br />
CHECK BRAKING SYSTEM(INSPECTION) ...............................05-30<br />
CHECK CHASSIS(INSPECTION) ...............................................05-26<br />
CHECK COOLANT LEVEL(INSPECTION)..................................05-34<br />
(INSPECTION).............................................................................05-14<br />
CHECK ENGINE COMPARTMENT PARTS(INSPECTION) .......05-17<br />
CHECK EXHAUST SYSTEM(INSPECTION) ..............................05-33<br />
CHECK HEADLIGHTS(INSPECTION) ........................................05-23<br />
CHECK PARKING BRAKE, BRAKE PEDAL(INSPECTION).......05-13<br />
CHECK SEAT BELT(INSPECTION)............................................05-11<br />
CHECK STEERING FLUID LEVEL(INSPECTION) .....................05-29<br />
CHECK SUSPENSION BALL JOINT AND DUST COVER(INSPEC-<br />
TION)........................................................................................... 05-28<br />
CHECK SUSPENSION COMPONENTS(INSPECTION) ............ 05-27<br />
CHECK THE AIRBAG(INSPECTION)......................................... 05-10<br />
CHECK THE BATTERY(INSPECTION)........................................ 05-9<br />
PLATE(INSPECTION)................................................................. 05-31<br />
(INSPECTION) .............................................................................. 05-8<br />
CHECK THE ENGINE OIL LEVEL (ISF2.8)(INSPECTION)........ 05-36<br />
CHECK THE ENGINE OIL LEVEL (4G69)(INSPECTION) ......... 05-35<br />
(INSPECTION) ............................................................................ 05-21<br />
CHECK TIMING BELT(INSPECTION) ........................................ 05-18<br />
CHECK TIRES(INSPECTION) .................................................... 05-32<br />
(INSPECTION) ............................................................................ 05-24<br />
INOPERATIVE .......................................................................... 04-305<br />
CIGARETTE LIGHTER IS INOPERATIVE................................ 04-375<br />
CKP SENSOR ...........................................................................11A-43<br />
COMPONENTS(COOLING SYSTEM) ........................................17A-2<br />
COMPONENTS(CRANKSHAFT, CYLINDER<br />
BLOCK & FLYWHEEL) .............................................................15A-69<br />
COMPONENTS(CYLINDER HEAD,VALVE).............................15A-51<br />
COMPONENTS(EXHAUST PIPE) ..............................................16A-1<br />
COMPONENTS(GENERATOR)..................................................20A-4<br />
COMPONENTS(PISTON & CONNECTING ROD<br />
ASSEMBLY) ..............................................................................15A-59<br />
COMPONENTS(ROCK ARM, ROCK ARM SHAFT, HYDRAULIC<br />
TAPPET & CAMSHAFT) ...........................................................15A-37<br />
COMPONENTS(STARTER)......................................................20A-12<br />
COMPONENTS(TIMING BELT)................................................15A-18<br />
COMPOSITION(BATTERY) ......................................................20A-21<br />
COOLANT ...................................................................................17A-6<br />
COOLANT PUMP......................................................................17A-23<br />
COOLING SYSTEM ....................................................................17A-1<br />
CRANKSHAFT, CYLINDER BLOCK & FLYWHEEL .................15A-69<br />
CYLINDER HEAD OVERHAUL(CYLINDER HEAD,VALVE) ....15A-52<br />
CYLINDER HEAD,VALVE.........................................................15A-51<br />
DATA STREAM LIST/ACTIVE TEST .......................................... 04-23<br />
DEFROSTER SYSTEM............................................................. 04-452<br />
DIAGNOSIS SWITCH ILLUMINATION IS NOT INOPERATIVE04-303<br />
DIAGNOSTIC HELP - INTERMITTENT FAULT............................ 04-8<br />
DIAGNOSTIC SYSTEM .............................................................. 04-16<br />
DIAGNOSTIC TROUBLE CODE CHART ...........04-27, 04-99, 04-129<br />
DIAGNOSTICS GASOLINE ENGINE CONTROL SYSTEM<br />
(BJ491EQ).................................................................................... 04-1<br />
(BUZZER IS NORMAL) ............................................................. 04-411<br />
INOPERATIVE .......................................................................... 04-313<br />
DOOR CONTROL SWITCH PIN ............................................... 04-415<br />
DOOR DOES NOT OPEN / CLOSE<br />
(USING THE REMOTE KEY) .................................................... 04-504<br />
DOWNSTREAM OXYGEN SENSOR........................................11A-49<br />
DTC DIAGNOSTIC...................................................................... 04-32<br />
ENGINE CONTROL MODULE (ECM) ......................................11A-15<br />
ENGINE CONTROL SYSTEM ...................................................... 04-1<br />
ENGINE COOLANT TEMPERATURE SENSOR ......................11A-18<br />
ENGINE MECHANICAL PART....................................................15A-1<br />
ENGINE OIL ................................................................................18A-4<br />
ENGINE OIL PRESSURE WARNING LIGHT NEVER /<br />
ALWAYS ON ............................................................................. 04-482<br />
ENGINE SYMPTOM DIAGNOSTIC ............................................ 04-59<br />
EXHAUST PIPE ..........................................................................16A-1<br />
FAIL-SAFE CHART ..................................................................... 04-21<br />
FRONT AIR FLOW IS INSUFFICIENT...................................... 04-163<br />
FRONT BLOWER MOTOR IS INOPERATIVE.......................... 04-157<br />
FRONT DOME LIGHT IS INOPERATIVE ................................. 04-291<br />
FRONT FOG LAMPS ARE ALWAYS ON ................................. 04-218<br />
FRONT FOG LAMPS ARE INOPERATIVE............................... 04-213<br />
FRONT POWER WINDOW LH DOES NOT CLOSE ................ 04-432<br />
FRONT POWER WINDOW LH DOES NOT OPEN .................. 04-430<br />
CONTROL SWITCH RH) .......................................................... 04-436<br />
FRONT POWER WINDOW RH IS INOPERATIVE ................... 04-427<br />
TROL SWITCH)......................................................................... 04-434<br />
FUEL FILLER CAP........................................................ 12A-20, 13A-1<br />
FUEL FILLER DOOR LOCK LATCH ASSY ..............................12A-18<br />
FUEL FILLING DOOR ...............................................................12A-17<br />
FUEL FILLING TUBE AND BREATHER TUBE ASSY..............12A-21<br />
FUEL FILTER ASSY ...................................................................12A-9<br />
FUEL LEVEL SENSOR ASSY ..................................................12A-10<br />
FUEL SYSTEM............................................................................12A-1<br />
GASOLINE ENGINE CONTROL SYSTEM ........................05-1, 11A-1<br />
GENERATOR..............................................................................20A-4<br />
TIVE........................................................................................... 04-245<br />
HAZARD WARNING LAMPS ARE ALWAYS ON ..................... 04-258<br />
LAMPS ARE NORMAL) ............................................................ 04-236<br />
TIVE........................................................................................... 04-321<br />
TIVE........................................................................................... 04-317<br />
HEATER AND AIR CONDITIONING SYSTEM ......................... 04-149<br />
HI - BEAM HEADLAMP IS INOPERATIVE (ONE SIDE)........... 04-197<br />
HIGH - MOUNTED STOP LAMP IS INOPERATIVE ................. 04-267<br />
HORN IS ALWAYS ON ............................................................. 04-389<br />
HORN IS INOPERATIVE .......................................................... 04-383<br />
HORN SYSTEM ........................................................................ 04-382<br />
HOW TO DIAGNOSTICS ANALYSE ............................................ 04-5<br />
IDLE AIR CONTROL MOTOR...................................................11A-28<br />
IGNITION CONTROL MODULE................................................11A-60<br />
IGNITION SWITCH ILLUMINATION IS INOPERATIVE............ 04-275<br />
INSPECTION................................................................................. 05-8<br />
INSPECTION(BATTERY)..........................................................20A-24<br />
INSPECTION(FUEL FILLER CAP)................................12A-20, 13A-1<br />
INSPECTION(FUEL FILLING TUBE AND BREATHER TUBE<br />
ASSY) ....................................................................................... 12A-21<br />
INSTRUMENT CLUSTER..........................................................04-461<br />
INSTRUMENT CLUSTER ILLUMINATION IS NOT<br />
INOPERATIVE...........................................................................04-300<br />
INSTRUMENT CLUSTER INFORMATION ...............................04-463<br />
TIVE ...........................................................................................04-319<br />
INTAKE AIR PIPE AND HOSE ................................................... 14A-2<br />
INTAKE AIR SYSTEM ................................................................ 14A-1<br />
INTAKE MANIFOLD ................................................................. 14A-10<br />
INTRODUCTION TO SYSTEM FUNCTION(GASOLINE ENGINE<br />
CONTROL SYSTEM) ................................................................. 11A-6<br />
LICENSE LAMP IS INOPERATIVE ...........................................04-328<br />
LIGHTING SYSTEM ..................................................................04-181<br />
LIQUID CRYSTAL DISPLAY .....................................................04-465<br />
(ONE SIDE) ..............................................................................04-204<br />
LO - BEAM HEADLAMP IS INOPERATIVE (ONE SIDE)..........04-191<br />
(BOTH SIDES)...........................................................................04-193<br />
LOCATION.......................................................... 04-4, 04-183, 04-462<br />
LOCATION(SUPPLEMENTAL RESTRAINT SYSTEM) ............04-126<br />
LUBRICATION SYSTEM ............................................................ 18A-1<br />
MAIN COMPONENTS(GASOLINE ENGINE CONTROL<br />
SYSTEM) .................................................................................. 11A-13<br />
TION(MAINTENANCE SCHEDULE) .............................................05-3<br />
MAINTENANCE SCHEDULE ........................................................05-1<br />
GAUGE......................................................................................04-479<br />
ER OR ALWAYS ON .................................................................04-476<br />
MALFUNCTION IN SPEEDOMETER........................................04-472<br />
MALFUNCTION IN TACHOMETER ..........................................04-474<br />
MIRROR ADJUSTMENT LEFT/RIGHT IS INOPERATIVE........04-450<br />
MIRROR ADJUSTMENT UP/DOWN IS INOPERATIVE ...........04-448<br />
MIRRORS ARE INOPERATIVE (BOTH SIDES) .......................04-442<br />
NO COOLING FROM FRONT A/C SYSTEM ............................04-167<br />
OIL FILTER................................................................................. 18A-6<br />
OIL PUMP................................................................................. 18A-11<br />
ON VEHICLE INSPECTION(IDLE AIR CONTROL MOTOR)... 11A-29<br />
ON VEHICLE INSPECTION(THROTTLE POSITION SENSOR<br />
(TPS)) ...................................................................................... 11A-33<br />
ON VEHICLE INSPECT(COOLING SYSTEM)........................... 17A-4<br />
ONE DOOR IS INOPERATIVE (USING THE KEY)...................04-502<br />
ON-VEHICLE INSPECTION(CANISTER SOLENOID<br />
VALVE) ..................................................................................... 11A-53<br />
ON-VEHICLE INSPECTION(DOWNSTREAM OXYGEN<br />
SENSOR).................................................................................. 11A-50<br />
ON-VEHICLE INSPECTION(MANIFOLD ABSOLUTE PRESSURE/IN-<br />
TAKE TEMPERATURE SENSOR) ........................................... 11A-37<br />
ON-VEHICLE INSPECTION(VEHICLE SPEED SENSOR)...... 11A-58<br />
ON-VEHICLE INSPECTION(UPSTREAM OXYGEN<br />
SENSOR).................................................................................. 11A-47<br />
OVERHAUL(CANISTER SOLENOID VALVE)...............11A-54, 13A-4<br />
OVERHAUL(CKP SENSOR) .................................................... 11A-44<br />
OVERHAUL(COOLANT PUMP) ............................................... 17A-23<br />
OVERHAUL(CRANKSHAFT, CYLINDER BLOCK &<br />
FLYWHEEL).............................................................................. 15A-71<br />
OVERHAUL(DOWNSTREAM OXYGEN SENSOR) ................. 11A-51<br />
OVERHAUL(ENGINE COOLANT TEMPERATURE<br />
SENSOR).................................................................................. 11A-19<br />
OVERHAUL(FUEL INJECTOR RAIL ASSY) ............................ 12A-12<br />
OVERHAUL(GENERATOR) ....................................................... 20A-5<br />
OVERHAUL(IDLE AIR CONTROL MOTOR) ............................ 11A-30<br />
OVERHAUL(IGNITION CONTROL MODULE) ......................... 11A-61<br />
OVERHAUL(MANIFOLD ABSOLUTE PRESSURE/INTAKE TEM-<br />
PERATURE SENSOR) ............................................................. 11A-38<br />
OVERHAUL(OIL PUMP)........................................................... 18A-11<br />
OVERHAUL(POSITIVE CRANKCASE VENTILATION VALVE<br />
(PCV VALVE))............................................................................ 13A-7<br />
OVERHAUL(STARTER) ........................................................... 20A-13<br />
OVERHAUL(THERMOSTAT) ................................................... 17A-18<br />
OVERHAUL(THROTTLE BODY).............................................. 11A-24<br />
OVERHAUL(THROTTLE POSITION SENSOR (TPS)) ............ 11A-34<br />
OVERHAUL(TIMING BELT) ..................................................... 15A-19<br />
OVERHAUL(VEHICLE SPEED SENSOR) ............................... 11A-59<br />
OVERHAUL(UPSTREAM OXYGEN SENSOR) ....................... 11A-48<br />
OUTSIDE MIRROR....................................................................04-439<br />
OUTSIDE MIRROR DEFROST ER IS INOPERATIVE..............04-455<br />
INOPERATIVE ...........................................................................04-315<br />
PARKING BRAKE INDICATOR LIGHT NEVER /<br />
ALWAYS ON..............................................................................04-489<br />
PISTON & CONNECTING ROD ASSEMBLY........................... 15A-59<br />
(PISTON & CONNECTING ROD ASSEMBLY) ........................ 15A-60<br />
POOR SOUND QUALITY ..........................................................04-369<br />
POSITIVE CRANKCASE VENTILATION VALVE<br />
(PCV VALVE)............................................................................. 13A-7<br />
POWER DOOR LOCKS.............................................................04-492<br />
POWER SUPPY VOLTAGE HIGH OR LOW.............................04-104<br />
POWER WINDOWS ..................................................................04-414<br />
PRE - CHECK ............................................................................04-102<br />
PRECAUTION...........04-96, 04-126, 04-149, 04-181, 04-334, 04-361,<br />
04-391, 04-414, 04-461, 04-492<br />
PRECAUTION(COOLING SYSTEM).......................................... 17A-1<br />
PRECAUTION(ENGINE MECHANICAL PART) ......................... 15A-1<br />
PRECAUTION(FUEL SYSTEM) ................................................. 12A-1<br />
PRECAUTION(GASOLINE ENGINE CONTROL SYSTEM)....... 11A-1<br />
PRECAUTION(INTAKE AIR SYSTEM) ...................................... 14A-1<br />
PRECAUTION(LUBRICATION SYSTEM) .................................. 18A-1<br />
PRECAUTION(MAINTENANCE SCHEDULE) ..............................05-1<br />
PRECAUTION(STARTING AND CHARGING SYSTEM) ........... 20A-1<br />
PRINCIPLE(CANISTER SOLENOID VALVE) .......................... 11A-52<br />
PRINCIPLE(CKP SENSOR) ..................................................... 11A-43<br />
PRINCIPLE(DOWNSTREAM OXYGEN SENSOR).................. 11A-49<br />
PRINCIPLE(ENGINE CONTROL MODULE (ECM))................. 11A-15<br />
PRINCIPLE(ENGINE COOLANT TEMPERATURE<br />
SENSOR).................................................................................. 11A-18<br />
PRINCIPLE(IDLE AIR CONTROL MOTOR)............................. 11A-28<br />
PRINCIPLE(IGNITION CONTROL MODULE).......................... 11A-60<br />
PRINCIPLE(MANIFOLD ABSOLUTE PRESSURE/INTAKE TEMPER-<br />
ATURE SENSOR)..................................................................... 11A-36<br />
PRINCIPLE(THROTTLE POSITION SENSOR (TPS)) ............. 11A-32<br />
PRINCIPLE(VEHICLE SPEED SENSOR) ................................ 11A-57<br />
PRINCIPLE(UPSTREAM OXYGEN SENSOR) ........................ 11A-46<br />
PROBLEM SYMPTOMS TABLE....... 04-101, 04-130, 04-151, 04-185,<br />
04-336, 04-363, 04-374, 04-382, 04-394, 04-419, 04-441, 04-454,<br />
04-470, 04-496<br />
PROBLEM SYMPTOMS TABLE ................................................. 04-58<br />
PROBLEM SYMPTOMS TABLE(FUEL SYSTEM)......................12A-3<br />
PROBLEM SYMPTOMS TABLE(STARTING AND CHARGING<br />
SYSTEM).....................................................................................20A-2<br />
PUMP MOTOR FAILURE.......................................................... 04-109<br />
RADIATOR ................................................................................17A-13<br />
RADIO DOES NOT WORK ....................................................... 04-364<br />
RADIO ILLUMINATION IS NOT INOPERATIVE....................... 04-309<br />
RADIO RECEPTION IS POOR ................................................. 04-368<br />
(DTC).......................................................................................... 04-18<br />
ERATIVE ................................................................................... 04-311<br />
REAR FOG LAMPS ARE ALWAYS ON.................................... 04-226<br />
REAR FOG LAMPS ARE INOPERATIVE ................................. 04-221<br />
HEATING................................................................................... 04-174<br />
(REPLACEMENT) ....................................................................... 05-38<br />
REPLACE AIR FILTER ELEMENT(REPLACEMENT) ................ 05-37<br />
REPLACE BRAKE FLUID(REPLACEMENT).............................. 05-54<br />
REPLACE COOLANT(REPLACEMENT) .................................... 05-52<br />
REPLACE ENGINE OIL (ISF2.8)(REPLACEMENT)................... 05-44<br />
REPLACE ENGINE OIL (4G69)(REPLACEMENT)..................... 05-40<br />
(REPLACEMENT) ....................................................................... 05-50<br />
(REPLACEMENT) ....................................................................... 05-51<br />
REPLACE GEARBOX LUBRICATING OIL(REPLACEMENT).... 05-56<br />
REPLACE OIL FILTER (4G69)(REPLACEMENT) ...................... 05-42<br />
(REPLACEMENT) ....................................................................... 05-57<br />
REPLACE SPARK PLUG (4G69)(REPLACEMENT) .................. 05-48<br />
REPLACEMENT.......................................................................... 05-37<br />
REPLACEMENT(ACCELERATE PEDAL) ................................12A-25<br />
REPLACEMENT(AIR FILTER ASSY) .........................................14A-6<br />
REPLACEMENT(BATTERY).....................................................20A-27<br />
REPLACEMENT(COOLANT)......................................................17A-6<br />
REPLACEMENT(ENGINE ASSY)...............................................15A-2<br />
REPLACEMENT(ENGINE OIL)...................................................18A-4<br />
REPLACEMENT(ENGINE OIL)(REPLACEMENT) ..................... 05-46<br />
REPLACEMENT(EXHAUST MANIFOLD)...................................16A-7<br />
REPLACEMENT(EXHAUST PIPE) .............................................16A-2<br />
REPLACEMENT(FUEL FILLER DOOR LOCK<br />
LATCH ASSY) ...........................................................................12A-18<br />
REPLACEMENT(FUEL FILLING DOOR)..................................12A-17<br />
REPLACEMENT(FUEL TANK ASSY).........................................12A-4<br />
REPLACEMENT(INTAKE AIR PIPE AND HOSE) ......................14A-2<br />
REPLACEMENT(INTAKE MANIFOLD).....................................14A-10<br />
REPLACEMENT(OIL FILTER) ....................................................18A-6<br />
REPLACEMENT(RADIATOR)...................................................17A-13<br />
REPLACEMENT(REPLACEMENT) ............................................ 05-57<br />
REPLACEMENT(RESERVIOR) ..................................................17A-8<br />
REPLACEMENT(TIMING PULLEY CASING) ...........................15A-14<br />
REPLACMENT(FUEL FILTER ASSY) ........................................12A-9<br />
REPLACMENT(FUEL LEVEL SENSOR ASSY) .......................12A-10<br />
RESERVIOR ...............................................................................17A-8<br />
CONNECTOR PIN .................................................................... 04-127<br />
REVERSE RADAR SYSTEM .................................................... 04-391<br />
REVERSE RADAR SYSTEM IS INOPERATIVE AT ALL ......... 04-395<br />
DISTANCE (BACK-UP LAMP IS NORMAL) ............................. 04-402<br />
REVERSE RADAR SYSTEM IS OPERATIVE BUT THERE IS NO OB-<br />
STACLE BEHIND VEHICLE...................................................... 04-405<br />
VER IS OUT OF REVERSE POSITION.................................... 04-400<br />
HAUL(ROCK ARM, ROCK ARM SHAFT, HYDRAULIC TAPPET &<br />
CAMSHAFT)..............................................................................15A-39<br />
ROCK ARM, ROCK ARM SHAFT, HYDRAULIC TAPPET & CAM-<br />
SHAFT.......................................................................................15A-37<br />
SEAT BELT WARNING LIGHT NEVER / ALWAYS ON ........... 04-485<br />
SOLENOID VALVES AND VALVES RELAY FAILURE ............ 04-105<br />
SPEAKER DOES NOT WORK.................................................. 04-370<br />
SRS WARNING LIGHT IS ALWAYS ON .................................. 04-145<br />
SRS WARNING LIGHT IS INOPERATIVE................................ 04-147<br />
STARTER..................................................................................20A-12<br />
STARTING AND CHARGING SYSTEM......................................20A-1<br />
STEP LAMP ARE INOPERATIVE............................................. 04-286<br />
STOP LAMP IS INOPERATIVE (ONE SIDE)............................ 04-265<br />
SUPPLEMENTAL RESTRAINT SYSTEM................................. 04-126<br />
SYSTEM COMPONENTS DESCRIPTION(GASOLINE ENGINE<br />
CONTROL SYSTEM) ................................................................11A-14<br />
SYSTEM DESCRIPTION ............................................. 04-392, 04-452<br />
SYSTEM OVERVIEW(GASOLINE ENGINE CONTROL<br />
SYSTEM).....................................................................................11A-2<br />
USE AND MAINTENANCE(BATTERY).................................... 20A-22<br />
Z<br />
INOPERATIVE...........................................................................04-378<br />
8101 - POWER SUPPLY VOLTAGE HIGH ...............................04-131<br />
8102 - POWER SUPPLY VOLTAGE LOW................................04-131<br />
8201 - DRIVER AIRBAG FAULT - HIGH RESISTANCE ...........04-133<br />
8202 - DRIVER AIRBAG FAULT - LOW RESISTANCE............04-133<br />
8203 - DRIVER AIRBAG CIRCUIT SHORT TO GROUND .......04-135<br />
8204 - DRIVER AIRBAG CIRCUIT SHORT TO BATTERY.......04-137<br />
RESISTANCE ............................................................................04-139<br />
GROUND ...................................................................................04-141<br />
BATTERY ..................................................................................04-143<br />
TAIL LAMPS ARE INOPERATIVE ............................................ 04-325<br />
TERMINALS OF ECM ................................................................. 04-11<br />
TERMINALS OF INSTRUMENT CLUSTER.............................. 04-466<br />
TERMINALS OF OUTSIDE MIRROR SWITCH ........................ 04-439<br />
THE FIXED SPEED ADJUSTING SCREW (SAS) ADJUST-<br />
MENT(THROTTLE BODY)........................................................11A-22<br />
(USING THE KEY) ................................................................... 04-497<br />
THERMOSTAT..........................................................................17A-18<br />
THROTTLE BODY ....................................................................11A-21<br />
THROTTLE BODY CLEANING(THROTTLE BODY) ................11A-21<br />
THROTTLE POSITION SENSOR (TPS)...................................11A-32<br />
TIMING BELT ............................................................................15A-18<br />
TIMING PULLEY CASING ........................................................15A-14<br />
TRUNK LAMP IS INOPERATIVE.............................................. 04-288<br />
LAMPS ARE NORMAL) ............................................................ 04-240<br />
TURN SIGNAL LAMPS ARE INOPERATIVE (ONE SIDE) ....... 04-254<br />
VALVE OVERHAUL(CYLINDER HEAD,VALVE) ......................15A-54<br />
WASHER PUMP IS INOPERATIVE - REAR WINDOW............ 04-358<br />
WASHER PUMP IS INOPERATIVE - WINDSHIELD ................ 04-348<br />
VEHICLE SPEED SENSOR......................................................11A-57<br />
WHEEL SPEED SENSOR CIRCUIT FAULT ............................ 04-113<br />
WHEEL SPEED SENSOR SIGNAL FAULT.............................. 04-115<br />
NOT RETRACT ......................................................................... 04-351<br />
WIDTH LAMPS IS NOT INOPERATIVE ................................... 04-323<br />
WIDTH LAMPS TAIL LAMPS AND LICENSE LAMP ARE<br />
INOPERATIVE .......................................................................... 04-330<br />
WINDOW CONTROL SWITCH LH PIN .................................... 04-416<br />
WIPER AND WASHER ............................................................. 04-334<br />
WINDSHIELD ........................................................................... 04-345<br />
WINDSHIELD ............................................................................ 04-344<br />
SHIELD...................................................................................... 04-346<br />
UPSTREAM OXYGEN SENSOR ..............................................11A-46<br />
V O L U M E 3<br />
11B ENGINE CONTROL SYSTEM 1571<br />
12B FUEL SYSTEM 1619<br />
13B EMISSION CONTROL 1671<br />
14B INTAKE AIR 1683<br />
15B ENGINE MECHANICAL 1705<br />
16B EXHAUST SYSTEM 2021<br />
17B COOLING SYSTEM 2037<br />
18B LUBRICATION SYSTEM 2067<br />
19A IGNITION SYSTEM 2093<br />
20B STARTING AND CHARGING 2105<br />
21 SUPERCHARGER 2141<br />
电 控 燃 油 喷 射 系 统 - 燃 油 管 路 10-1<br />
CONTROL SYSTEM OF ENGINE ..................................................... 11B-1<br />
Precautions ................................................................................... 11B-1<br />
BJ4JB1 Engine System Composition And Principle ................ 11B-2<br />
Table Of Fault Phenomena .......................................................... 11B-4<br />
ENGINE CONTROL SYSTEM MAINTENACNE ............................. 11B-13<br />
General Troubleshooting Procedure ........................................ 11B-13<br />
SERVICING Procedures Of Basic Inspection .......................... 11B-14<br />
General Steps For Fault Diagnosis .......................................... 11B-15<br />
REPAIR FOR SENSOR AND ACTUATOR ..................................... 11B-17<br />
Coolant Temperature Sensor .................................................... 11B-17<br />
Camshaft Position Sensor ......................................................... 11B-20<br />
Mass Air Flow Sensor ................................................................ 11B-23<br />
EGR Vacuum Adjuster ............................................................... 11B-25<br />
Preheat Controller ...................................................................... 11B-28<br />
Rail Pressure Sensor ................................................................. 11B-32<br />
Interior Pressure Control Valve ................................................ 11B-35<br />
Vehicle Speed Sensor ................................................................ 11B-37<br />
Crankshaft Position Sensor ...................................................... 11B-40<br />
Accelerator Pedal Position Sensor .......................................... 11B-42<br />
Electronic Control Module (ECU) ............................................. 11B-45<br />
11B<br />
10- 2 电 控 燃 油 喷 射 系 统 - 燃 油 管 路<br />
CONTROL SYSTEM OF ENGINE-CONTROL SYSTEM OF ENGINE<br />
11B-1<br />
CONTROL SYSTEM OF ENGINE<br />
PRECAUTIONS<br />
1. In dismantling the connector of ground wire of electric control system, firstly turn off ignition switch and<br />
disassembly the ground wire of negative pole of battery. If only electric control system will be inspected,<br />
then, it is necessary to turn off ignition switch.<br />
2. Make sure that the power supply system for vehicles have negative ground. In installing battery, pay<br />
special attention to negative pole and positive pole, which cannot be connected reversely.<br />
3. In installing or taking down ECU, operators shall make themselves grounded (contact with vehicle<br />
body). Otherwise, the physical static electricity will damage circuits of computer.<br />
4. When people enter or leave carriage, the static electricity of human body may generate high voltage.<br />
So, make sure to wear iron metal straps while carrying out service for computer operation and digital<br />
instrument or near such instrument with one end is winded to wrist and the other to vehicle body.<br />
5. For the dismantling of any oil line, firstly decompress fuel system.<br />
6. In servicing electric control system, avoid damaging electric control system due to overloading. For this,<br />
pay attention to the following points:<br />
• Do not use test lamp to check the sensors of electric control system and control unit of computer<br />
(including inspection on their terminal blocks).<br />
• In addition to special instructions in testing procedures of some vehicles, generally do not use<br />
analog multimeter to check the resistance of electric control system, but to use high impedance<br />
digital multimeter (above 10MΩ) or special detection instrument for electric control system.<br />
• On the vehicles installed with electric control system, avoid using grounding for fire test or<br />
dismantling wire for fire scrapping to inspect circuits.<br />
7. Do not use water to wash control unit of computer and other electronic device. If there is leakage for<br />
windscreen wiper, repair it timely and pay attention to protecting the control system of computer to<br />
avoid abnormal operation of circuit board, electrical elements and parts, integrated circuit and sensors<br />
due to damp.<br />
8. In general situation, do not open the computer cover, as most faults of electric control engine are faults<br />
of external equipment with a few computer faults. Even if the computer has faults, the opening of<br />
computer cover cannot solve any problems in the situation of without taking detection means<br />
(equipment to detect the oscilloscope and signal generator of computer). On the contrary, the opening<br />
of computer may lead to new faults due to improper operation. In affirming the computer faults,<br />
professional personnel shall be invited for its detection and repair.<br />
9. Do not unplug any line plug (connector) of any sensors while the engine is in operation. Otherwise,<br />
artificial fault code (a kind of pseudo code) will appear in computer, influencing the correct judgment of<br />
repair personnel for fault removal.<br />
11B-2<br />
BJ4JB1 ENGINE SYSTEM COMPOSITION AND PRINCIPLE<br />
1. Electronic Control System Composition<br />
Electronic control system comprises of fuel pump, fuel rail, injector, ECU, accelerator pedal position<br />
sensor, revolution speed sensor and some other sensors and actuators.<br />
1 High-Pressure Pump<br />
2 Interior Pressure Control Valve<br />
3 Fuel Filter<br />
4 Fuel Tank<br />
5 ECU<br />
6 Battery<br />
7 High-pressure Fuel Rail<br />
8 Fuel Rail Pressure Sensor<br />
9 Injector<br />
10 Engine Coolant Temperature Sensor<br />
11 Crankshaft Speed Sensor<br />
12 Accelerator Pedal Position Sensor<br />
13 Camshaft Speed Sensor<br />
14 Mass Air Flow Sensor<br />
15 Turbocharger<br />
16 EGR Valve<br />
17 Vacuum Pump<br />
18 Vacuum Solenoid Valve<br />
11B-3<br />
2. Electronic Control System Operational Principles<br />
ECU can figure out the amount of fuel injection, injection moment, injection frequency and injection<br />
pressure (the rail pressure when injecting) within ECU according to the driver’s demands that are the<br />
position of accelerator pedal position sensor (the signal of accelerator pressure input to ECU) and the<br />
current operational situation of the engine and the vehicle (engine speed, coolant temperature, current<br />
load and etc.). Meanwhile ECU will issue the directives to control the rail pressure within a limit and<br />
make the injector injects according to the calculation result.<br />
11B-4<br />
TABLE OF FAULT PHENOMENA<br />
The following table is helpful for troubleshooting. The serial number stands for the possible order of fault<br />
causes. According to this order, check each part and replace them if necessary.<br />
Phenomenon Possible Part Measures/References<br />
1. Cold start port (does not open)<br />
Chapter 4 Diagnosis - Electric Control<br />
System of Engine (BJ4JB1)<br />
2. Vehicle cold start relay<br />
(unconnected)<br />
Chapter 14B Engine Mechanical<br />
3. Preheat plug (invalid)<br />
System-Engine Disassembly, Disassembly<br />
EGR Controller<br />
4. Main relay (burnt down)<br />
5. Main relay fuse (burnt down)<br />
6. ECU connector (inappropriately<br />
connected)<br />
Diesel engine cannot<br />
start up or start up<br />
difficultly<br />
7. ECU (damaged)<br />
Chapter 11B Engine Control System -<br />
Sensor, Actuator Maintenance, Electronic<br />
Control Module (ECU)<br />
8. ECU(water entering) Blow ECU Dry<br />
9. ECU connector (water entering) Blow Connector Dry<br />
10. ECU (unmatched type)<br />
11. Fuel water separator (blocked)<br />
12. Sensor harness connector (become<br />
loose)<br />
13. Fuel filter (blocked)<br />
14. Fuel line (the curvature is too small<br />
or bent)<br />
Chapter 12B Fuel System - Fuel Filter (Fine<br />
Filter) And Replacement<br />
Filter) and Replacement<br />
Chapter 12B Fuel System - Fuel Lines and<br />
Replacement<br />
11B-5<br />
15. Low pressure fuel lines (interior<br />
diameter becomes small)<br />
16. Low pressure fuel lines (air flows in)<br />
17. Inlet and outlet fuel lines (reversely<br />
18. Fuel tank (run out of fuel or short of<br />
fuel)<br />
Chapter 12B Fuel System - Fuel Tank,<br />
Service<br />
19. Harness (badly connected)<br />
20. Camshaft and crankshaft sensor<br />
(incredible signal)<br />
21. Camshaft sensor clearance (quite<br />
poor)<br />
22. Camshaft sensor (absorb foreign<br />
body or damaged)<br />
Chapter 11B Engine Control Systems -<br />
Sensor, Actuator Maintenance, Camshaft<br />
Position Sensor<br />
23.Crankshaft sensor clearance (quite<br />
24. Camshaft sensor (absorb foreign<br />
25. Accelerator pedal position sensor<br />
System Of Engine (BJ4JB1)<br />
26. Air intake heater (ECU port does not<br />
open)<br />
27. Preheat device (burnt down)<br />
28. Injector (Needle valve blocked and<br />
does not work)<br />
Chapter 14B Engine Mechanical System -<br />
Engine Disassembly<br />
11B-6<br />
29. Injector solenoid valve (burnt down)<br />
30. Ignition lock (damaged)<br />
31. Battery (under voltage)<br />
Chapter 91 Vehicle Control System -<br />
Ignition Switch, Replacement<br />
Chapter 20B Start Up and Charge –<br />
Battery Assembly And Replacement<br />
32. Fuel (wrong type) Fuel Replacement<br />
1. Fuel (wrong type)<br />
2. Fuel water separator (blocked)<br />
Chapter 12B Fuel System - Fuel Filter<br />
(Fine Filter) and Replacement<br />
3. Main diesel filter (blocked)<br />
(Rough Filter)<br />
4. Low pressure fuel lines (curvature is<br />
too small or bent)<br />
Engine lack of power<br />
5. Low pressure lines (interior diameter<br />
becomes small)<br />
6. Low pressure fuel lines (air flows in)<br />
7. Low pressure fuel lines (inlet and<br />
outlet reversely connected)<br />
8. Low pressure fuel lines (connector<br />
become loose and air flows in)<br />
(Fine Filter) And Replacement<br />
9. Camshaft sensor (absorb foreign<br />
body)<br />
Chapter 12B Engine Control System -<br />
10. Camshaft sensor (wrong gap)<br />
11B-7<br />
11. Coolant temperature sensor<br />
(damaged)<br />
12. Coolant temperature sensor<br />
(connector become loose or cut off)<br />
13. Thermostat (blocked or temperature<br />
is too high)<br />
14. Accelerator pedal position sensor<br />
(wrong signal)<br />
15. Injector solenoid valve (damaged)<br />
16. Injector (cut off or connector<br />
becomes loose)<br />
17. Injector (Harness short circuits)<br />
Chapter 11B Engine Control<br />
Systems-Sensor, Actuator Maintenance,<br />
Camshaft Position Sensor<br />
1. ECU (damaged)<br />
2. ECU (interior or connector water<br />
entering)<br />
3. ECU (connector become loose)<br />
Blow Dry<br />
Engine turns off<br />
automatically<br />
4. ECU (overheating protection)<br />
5. ECU (ground wire cut off)<br />
6. ECU main relay (burnt down)<br />
7. Main relay fuse (burnt down)<br />
11B-8<br />
8. High pressure pump timing gear<br />
9. Accelerator pedal position sensor<br />
(not the regulated type)<br />
10. Rail pressure sensor (damaged)<br />
11. Rail pressure sensor (connector<br />
12. Low pressure fuel lines (aging hose<br />
and sucked flat)<br />
13.Low pressure fuel lines (too much<br />
air)<br />
14. Harness (cut off or short circuits)<br />
System-Engine Disassemble, Injector<br />
Pump Assembly and Disassembly<br />
Sensor, Actuator Maintenance, Accelerator<br />
Throttle Pedal Position Sensor<br />
Sensor, Actuator Maintenance, Rail<br />
Pressure Sensor<br />
15. Fuel ( low quality) Fuel Replacement<br />
1. Fuel (low quality) Fuel Replacement<br />
Too thick smoke of<br />
When the accelerator<br />
throttle pedal reached<br />
its highest position, the<br />
maximum speed is not<br />
obtained<br />
2. Valve (wrong clearance)<br />
3. Injector (needle valve stuck or<br />
wears out)<br />
4. ECU (program runs disorderly)<br />
1. Accelerator pedal (lines connected<br />
wrong)<br />
2. Accelerator pedal (connecting lines<br />
become loose)<br />
System-Engine Disassembly<br />
11B-9<br />
When the<br />
accelerator throttle<br />
pedal reached its<br />
highest position,<br />
the maximum<br />
speed is not<br />
3. Accelerator pedal position sensor<br />
4. Accelerator throttle pedal<br />
(non-calibrated)<br />
Chapter 11B Engine Control System - Sensor,<br />
Actuator Maintenance, Accelerator Throttle Pedal<br />
1. Accelerator throttle pedal (lines<br />
connected wrong)<br />
Chapter 4 Diagnosis - Electric Control System of<br />
Engine (BJ4JB1)<br />
2. Accelerator throttle pedal<br />
(connecting lines become loose)<br />
3. Accelerator throttle pedal position<br />
sensor (damaged)<br />
4. Rail pressure sensor (damaged)<br />
Actuator Maintenance, Rail Pressure Sensor<br />
5. Low pressure fuel lines (blocked)<br />
Lame home (speed<br />
and power<br />
decrease)<br />
6. Fuel metering unit (damaged)<br />
7. Metering valve (stuck, blocked)<br />
Actuator Maintenance, Metering Valve<br />
8. Low pressure fuel lines (blocked)<br />
9. Fuel water separator (blocked or<br />
too much water)<br />
Chapter 12B Fuel System - Fuel Filter (Fine Filter)<br />
and Replacement<br />
10. Diesel filter (blocked)<br />
Chapter 12B Fuel System - Fuel Filter (Rough<br />
Filter)<br />
11. Low pressure fuel lines (bent or<br />
curvature is too small)<br />
Chapter 12B Fuel System - Fuel Lines And<br />
12. Low pressure fuel lines (interior<br />
diameter is too small)<br />
11B-10<br />
13. Low pressure fuel lines (air flows in)<br />
14. Return pipe (blocked)<br />
Lame home (speed and<br />
power decrease)<br />
15. Inlet and outlet fuel pipes (reversely<br />
16. ECU (poor cooling)<br />
17. ECU (loose connection, heavy<br />
vibration)<br />
1. Harness (short circuit or cut off)<br />
2. ECU (supply state does<br />
nonconforming to calibrated data)<br />
Fault light is always on<br />
3. AC (line is not connected with ECU)<br />
4. Preheat relay (not connected with<br />
5. Fuel water separator (lines are not<br />
correctly connected)<br />
6. Water sensor (nonconforming to<br />
requirements of ECU)<br />
Sensor, Actuator Maintenance, Water<br />
Level Sensor<br />
Idle speed too high<br />
1. Accelerator pedal (connectors water<br />
2. AC request switch (Is always on)<br />
Chapter 61 Heater and AC-AC and<br />
Maintenance<br />
1. ECU (the calibrated data does<br />
Wrong fuel water<br />
separator signal (water<br />
nonconforming to vehicle practical<br />
status)<br />
information)<br />
2. Harness (cut off or wrong<br />
11B-11<br />
1. Fuel (wrong type) Fuel Replacement<br />
2. Fuel (contain air or water)<br />
(Fine Filter), Discharge Water<br />
Abnormal sound of<br />
deflagration<br />
3. Injector return fuel pipe fitting (fuel<br />
pore is too small)<br />
4. Injector return fuel pipe one-way<br />
valve (stuck)<br />
Chapter 12B Fuel System - Injector<br />
Overhaul<br />
5. Return fuel jack (fuel does not return<br />
smoothly)<br />
1. Accelerator throttle pedal harness<br />
(cut off)<br />
Chapter 04 Diagnose-Engine Electric<br />
Control System ( BJ4JB1)<br />
During<br />
accelerator pedal<br />
driving,<br />
2. Crankshaft and camshaft sensor<br />
(too dirty or wear out)<br />
3. ECU (poor cooling)<br />
Sensor and Actuator Maintenance<br />
Sensor, Actuator Maintenance,<br />
Electronic Control Module (ECU)<br />
4. ECU (heavy vibration during driving)<br />
1. Fuel water separator (inlet and<br />
outlet fuel pipes reversely<br />
Hand fuel pump does<br />
not work<br />
3. Fuel water separator fuel pipes (too<br />
long)<br />
4. Fuel tank pipes (blocked)<br />
5. Fuel tank pipes (bent or curvature is<br />
too small)<br />
11B-12<br />
Rail pressure is too low<br />
1. Low pressure fuel lines (blocked)<br />
2. Fuel water separator (blocked or<br />
contains too much water)<br />
3. Diesel filter (blocked)<br />
4. Low pressure fuel pipes (bent or<br />
5. Low pressure fuel pipes (interior<br />
6. Low pressure fuel pipes (air flows in)<br />
7. Fuel return pipe (blocked or does<br />
not return smoothly)<br />
8. Inlet and outlet fuel pipes (reversely<br />
CONTROL SYSTEM OF ENGINE-ENGINE CONTROL SYSTEM MAINTENACNE<br />
11B-13<br />
ENGINE CONTROL SYSTEM MAINTENACNE<br />
GENERAL TROUBLESHOOTING PROCEDURE<br />
11B-14<br />
SERVICING PROCEDURES OF BASIC INSPECTION<br />
According to diagram fswx110041, carry out fault diagnosis for electric control engine. In order to determine<br />
the nature and position of fault and avoid many necessary operations, after visual inspection on engine, carry<br />
out basic inspection according to procedures shown in diagram fswx110042. In the basic inspection, the water<br />
temperature of engine must reach normal operating temperature (about above 80℃). Meanwhile, close all<br />
attached electrical device of vehicle, such as AC). What is more, carry out inspection adjustment before<br />
cooling fan is started for operation to avoid energy consumption of fan, which will influence the accuracy of<br />
inspection.<br />
11B-15<br />
GENERAL STEPS FOR FAULT DIAGNOSIS<br />
△ Tip:<br />
• The common faults of electric control engine are as follows: difficult starting, stop at once after starting,<br />
unstable idle speed, too high idle speed, powerless travelling, poor acceleration, tempering explosion,<br />
shaking and surging, smoking and large fuel consumption.<br />
General steps for fault diagnosis of electric control engine are as follows:<br />
1. Firstly, affirm whether there are faults of engine<br />
General methods to judge the operation of engine are as follows:<br />
• The engine cannot be started or in normal operation after starting, or there is explosion of exhaust<br />
pipe and tempering of intake pipe in the operation of engine, or there is obvious abnormal<br />
phenomenon like the obvious knocking sound. Then, it can be affirmed that there are faults for<br />
engine.<br />
• See whether the warning indicator of engine (check engine) installed with electric control system is<br />
on. If the indicator is on, this shows that there are faults for the electric control system of engine.<br />
• If large changes occur to the performance of engine in a short term, it can be affirmed that there<br />
are certain faults for engine, such as the power of engine is reduced greatly and its fuel<br />
consumption is obviously increased.<br />
• If the changes occurring to performance of engine are not obvious, the following methods can<br />
used for test: let engine operate in various simulated working conditions and carefully listen to that<br />
whether there is abnormal sound for exhaust pipe and intake pipe in the operation of engine, feel<br />
the vibrating situation of engine and whether there is obvious shaking and metal knocking sound<br />
and observe the changing situation of engine speed.<br />
NOTE:<br />
Slowly depress accelerator pedal and increase the engine speed from low to high gradually. Pay<br />
attention to judging whether above said phenomenon is existent. If they are existent, this shows that<br />
there may be faults for engine. It is necessary to carry out test repeatedly to provide basis for correct<br />
judgment of fault. Depress accelerator pedal suddenly and observe whether there are above said<br />
phenomenon and the increasing rate of engine speed is ideal. If there is abnormal situation or the<br />
increasing rate of engine speed is too slow, this shows that there are faults for engine. If under the<br />
above two situations, any abnormal phenomenon of engine is not found, then, loose accelerator pedal<br />
and observe the idle speed operation situation of engine. See whether the rotating speed in idle speed<br />
is too high or unstable and whether the shaking of engine is serious or not.<br />
Through above operations, if any abnormal phenomenon is not found, this shows the normal operation of<br />
engine. If carry out careful inspection on the dynamic property, economical efficiency and exhausting situation<br />
of engine, it is necessary to use detection line or special detection instrument to carry out fault inspection and<br />
2. Secondly, determine the nature of faults<br />
If there are faults for electric control engine, firstly observe the situation of self diagnosis warning<br />
indicator (CHECKENGINE) in electric control system of engine. If the indicator is on in the operation<br />
process of engine, this shows that there are faults monitored by the self diagnosis system of electric<br />
control engine. Faults are usually related with electric control system. At this moment, through certain<br />
11B-16<br />
methods, acquire the fault code in internal storage of computer and then find out the fault causes<br />
according to fault code. If there are faults for engine indeed, warning indicator “check engine” of engine<br />
on instrument panel is not on in the operation of engine, this shows that self diagnosis system of<br />
electric control unit cannot identify such faults for engine. At this moment, according to fault<br />
phenomenon, make initial diagnosis result like the way to diagnose traditional engine and analyze the<br />
possible fault causes. According to the principles of starting from the outside to inside, from the simple<br />
to the complex, carry out deep diagnosis. Under such situation, make sure not to disassembly the<br />
electric control system casually. Only after affirming the faults of electric control system, firstly check<br />
electric control system. Otherwise, check the other parts firstly.<br />
3. Carry out visual inspection<br />
Firstly check whether plugs of wire are loose in poor contact, open circuit and short circuit. Then,<br />
observe whether there is gas leakage and oil leakage for each intake pipe, vacuum pipe and oil way<br />
and carry out further inspection again.<br />
4. Locate the failed part<br />
In order to reduce the working quantity to remove faults, the method of reducing 1/2 can be used if<br />
there is abnormal response of engine. Narrow the suspected parts in the scope of 1/2. For this, firstly<br />
affirm whether there are faults for oil way or circuit. Most faults of engine are caused by oil way or<br />
circuit. So, if there are faults for engine and you can affirm the faults of oil way or circuit definitely, 1/2<br />
working quantity can be reduced and concentrate your energy in the scope of 1/2. For this, carry out<br />
the following steps.<br />
(a). For the fault judgment of oil way or circuit, as it is easy to carry out fault diagnosis for circuit visually,<br />
start to check whether there are faults for circuit. Unplug the central high tension line of ignition system<br />
and carry out spark over test for cylinder body to affirm whether the parts of high pressure ad low<br />
pressure are normal. If spark without high voltage or spark is too weak, faults of ignition system can be<br />
affirmed. If above said inspection is normal, unplug the high tension line of distributor of spark plug and<br />
check whether there is distributed fire. If there is no such fire, then there are faults for wire from the<br />
central high tension line to live wire of distributor. If above said inspection is normal and there is<br />
distributed fire in each cylinder, then circuits are normal. So, faults are mostly caused by oil way.<br />
(b). In order to judge whether faults are caused by poor operation of individualized cylinder or all cylinders,<br />
poor operation of engine, start from the analysis and inspection on the causes for the poor operation of<br />
individualized cylinder if individualized cylinder does not operate or in poor operation. If all cylinders of<br />
engine are in operation, but their operations are not very obvious, then start from the causes for the<br />
poor operation of all cylinders of engine. So, 1/2 working quality for diagnosis can be reduced. For this,<br />
carry out the following steps: start engine and let it operate in idle speed. After reaching normal<br />
temperature, carry out discontinuous fire cutoff test between distributed fire line and observe the<br />
response situation of engine. If intermittent fire cutoff and re-firing test are carried out discontinuously<br />
for single cylinder, but the operation of engine does not have any response, then, the cylinder is poor<br />
operation. Next, analyze and inspect the causes of poor operation of single cylinder in concentration. If<br />
intermittent fire cutoff and re-firing test are carried out for each cylinder, but there is no obvious change<br />
for the operating situation of engine, then, the operating situation of each cylinder is the similar. So,<br />
start from the causes for abnormal operation of each cylinder of engine.<br />
CONTROL SYSTEM OF ENGINE-REPAIR FOR SENSOR AND ACTUATOR<br />
11B-17<br />
REPAIR FOR SENSOR AND ACTUATOR<br />
COOLANT TEMPERATURE SENSOR<br />
1. Profile<br />
2. Location<br />
It is installed under the engine’s thermostat block.<br />
3. Instructions to parts<br />
It is used in the electronic fuel injection device to detect the engine coolant temperature, send the<br />
voltage signal to electronic control module which is taken as the load signal of the engine so as to<br />
evaluate the operational situation of the engine.<br />
4. Composition and principle<br />
The operational principle of coolant temperature sensor is sealed in a thermister with a negative<br />
temperature coefficient. By the temperature sensitive characteristics of the thermister, the change of<br />
environment temperature will be converted into the change of the thermal resistance and then<br />
converted to be voltage signal which will be sent to the electronic control unit.<br />
5. Technical parameters<br />
(a). Limit data<br />
Item Value Unit<br />
Rated voltage<br />
Only 5+0.15 of the rated voltage<br />
can be operated by ECU<br />
V<br />
20 ℃ rated resistance 2.5±6% KΩ<br />
100 ℃ rated resistance 0.186±2% KΩ<br />
Operation temperature range -40~130 ℃<br />
Allowable vibration acceleration 300 m/s2<br />
11B-18<br />
6. Replacement<br />
(a). Park the vehicle on stable and flat ground.<br />
After stopping the vehicle, turn off engine and shift into neutral gear and pull up the parking brake lever.<br />
Lift the handle of bracing and locking wire of engine<br />
compartment cover up.<br />
Lift the engine compartment cover up.<br />
Discharge appropriate amount of coolant by a water drain<br />
switch until the engine is cooled down.<br />
Disconnect the connector of coolant temperature sensor.<br />
Remove the coolant temperature sensor and take it<br />
down.<br />
11B-19<br />
(g). Install and tighten the coolant temperature sensor.<br />
△Tip:<br />
The temperature sensor can be screwed into the tapped hole of<br />
thermostat block using the hexagon head on the socket with<br />
threads.<br />
(h).<br />
(i).<br />
Connect the connector of coolant temperature sensor.<br />
Add coolant.<br />
(j). Lift the engine compartment cover up to make the<br />
support bar move away from the support hole of<br />
compartment cover and clip the support bar into the slot.<br />
(k). Lower the room cover slowly and loose your hands<br />
when the room cover is about 20cm away from lock-up<br />
position and let it fall freely.<br />
When closing engine compartment cover, people cannot<br />
stand in the rotating scope to avoid the personal injury.<br />
11B-20<br />
CAMSHAFT POSITION SENSOR<br />
Position sensor PG is installed at the end of camshaft,<br />
cooperating with speed sensor and distinguishing<br />
compression TDC and exhaust TDC on No.1 cylinder.<br />
Position sensor is to detect the engine timing valve which is realized by the detection of camshaft<br />
sensor angle.<br />
Position sensor PG comprises of one Hall sensor and one signal rotor (semi-circular iron magnet). The<br />
rotation of camshaft will drive the rotation of the signal rotor installed at the end. By using Hall principles,<br />
when the signal rotor blade goes into the gap of permanent magnet circuit of Hall sensor, Hall sensor<br />
switch is in the position of “OFF” and the corresponding circuit output is high level. When the signal<br />
rotor blade goes into the gap of permanent magnet circuit of Hall sensor, Hall sensor switch is in the<br />
position of “ON” and the corresponding circuit output is low level. The corresponding rotation of the<br />
crankshaft has signal while the other one does not have it which then can distinguish the different TDC.<br />
Ambient Temperature<br />
Limit Life Expectancy<br />
-40~150℃<br />
Ambient temperature in operation is 150℃<br />
Ambient temperature without operation is 160℃<br />
1000h<br />
250h<br />
Speed range 0~4500rpm (camshaft speed)<br />
11B-21<br />
After stopping the vehicle, turn off engine and shift into neutral gear and pull up the parking brake<br />
lever.<br />
(b). Open the engine compartment cover and hold it. (Refer to Chapter 11B Engine Control System –<br />
Repair for Sensor and Actuator, Coolant Temperature Sensor).<br />
Disconnect the connector of camshaft position sensor.<br />
Remove the fixing bolts of camshaft position sensor.<br />
Take down the camshaft position sensor.<br />
Place the camshaft position sensor to mounting position.<br />
11B-22<br />
(g).<br />
Tighten the fixing bolts of camshaft position sensor.<br />
Torque: 8±0.5 N·m<br />
Connect the connector of camshaft position sensor.<br />
Close the engine compartment cover. (Refer to Chapter<br />
11B Engine Control System – Repair for Sensor and<br />
Actuator, Coolant Temperature Sensor).<br />
11B-23<br />
MASS AIR FLOW SENSOR<br />
It is installed behind the engine air filter while before the<br />
engine turbocharger inlet.<br />
3. Composition and principle<br />
Inlet mass sensor is a heat flux sensor which comprises of inlet air temperature sensor and air mass flow<br />
sensor. It is used to detect the engine inlet temperature and inlet mass flow. By reporting the detection of inlet<br />
air mass to the electronic unit and its participation in control, the control of EGR system in the closed loop can<br />
be realized.<br />
4. Technical parameters<br />
Parameters<br />
Value<br />
Minimum Standard Maximum<br />
Unit<br />
Temperature tolerance -40 120 ℃<br />
Transient temperature tolerance limit 120 130 ℃<br />
Operational voltage 7.5 14 17.0 V<br />
Pressure drop 15 hPa<br />
5. Replacement<br />
11B-24<br />
Disconnect the connector of mass air flow sensor.<br />
Remove 2 A-type worm drive hose clamps.<br />
Take down the mass air flow sensor.<br />
(f). Place the mass air flow sensor to mounting position, and<br />
install 2 A-type worm drive hose clamps.<br />
The airflow direction is required to be consistent with the<br />
arrow direction on the sensor case when installing the<br />
sensor. Otherwise, the power is limited and the system<br />
operation degrades.<br />
Connect the connector of mass air flow sensor.<br />
11B-25<br />
EGR VACUUM ADJUSTER<br />
It is installed in the engine compartment.<br />
It can control the pulse width, switching on time of EGR valve, control EGR rate, reduce NOx pollutants<br />
and optimize the emission.<br />
Operational voltage 10 12 16 V<br />
Mass air flow 30 L/h<br />
Switch on response time 1 s<br />
Switch off response time 0.2 s<br />
Operational temperature range -30 130 ℃<br />
Output resistance 14 Ω<br />
11B-26<br />
Disconnect the vacuum line of EGR vacuum adjuster.<br />
Disconnect the connector of EGR vacuum adjuster.<br />
Remove the fixing bolts of EGR vacuum adjuster.<br />
(f). Take down the EGR vacuum adjuster.<br />
Prevent contact with alkali-metal impurity and avoid<br />
invalidation due to entering the inner cavity of vacuum<br />
adjuster.<br />
11B-27<br />
Place the EGR vacuum adjuster to mounting position.<br />
Tighten the fixing bolts of EGR vacuum adjuster.<br />
Torque: 6 N·m<br />
Connect the connector of EGR vacuum adjuster.<br />
(j).<br />
(k).<br />
11B-28<br />
PREHEAT CONTROLLER<br />
(a) Preheat control unit (GCU) is controlled by electronic control unit (EDC) and it has the following<br />
functions:<br />
• By the input of the signal from ST and K port, GCU is applicable to 4, 5, or 6-cylinder engine.<br />
• Electronic control unit (EDC) control the switch signal of 4, 5 or 6 preheat plug of GSK.<br />
• Overcurrent cut off protection (electronic protection)<br />
• Preheat plug invalidity diagnose<br />
• Small volume and can be installed in the engine compartment.<br />
• High potential protection from electronic control unit (EDC).<br />
11B-29<br />
Limit data<br />
Preheat time 4 200 s<br />
Temperature tolerance of 200s maximum preheat time,<br />
the accumulated life expectancy is shorter than 1000h.<br />
Temperature tolerance of non-preheat, the<br />
accumulated life expectancy is shorter than 5000h.<br />
Temperature tolerance of non-preheat with heat load,<br />
the accumulated life expectancy is shorter than 5000h.<br />
-40 85 ℃<br />
-40 125 ℃<br />
Power supply voltage of normal operation 8 12 16 V<br />
Allowable minimum voltage at the starting up stage 6 8 V<br />
Input current at 66 port ≤1000 mA<br />
Control current at ST/K port 1 50 mA<br />
Signal current at DI port 1 10 mA<br />
Operational current at 30 port 60 180 A<br />
Operational current at G port 10 30 A<br />
Energy consumption 10 18 W<br />
Output resistance at DI port 10±5 % KΩ<br />
Preheat pressure drop of each cylinder ≤250 mV<br />
11B-30<br />
Disconnect the connector of preheat controller.<br />
Remove the fixing bolts of preheat controller.<br />
Take down the preheat controller.<br />
Place the preheat controller to mounting position.<br />
Install the fixing bolts of preheat controller.<br />
Torque: 5±1 N·m<br />
Broken torque: >7 N·m<br />
11B-31<br />
Connect the connector of preheat controller.<br />
11B-32<br />
RAIL PRESSURE SENSOR<br />
It is installed at the ends of fuel rail.<br />
It is to detect the rail pressure and offer the input signal to electronic control unit.<br />
Symbol<br />
Operational temperature T -40 130 ℃<br />
Pressure range P 0<br />
150<br />
180<br />
200<br />
MPa<br />
Operational power supply voltage Us 4.75 5.0 5.25 V<br />
Current when Us=5V Is 12 15 A<br />
Load resistance when 0.1US
11B-33<br />
Park the vehicle on stable and flat ground.<br />
Disconnect the connector of rail pressure sensor.<br />
Remove the rail pressure sensor.<br />
Take down the rail pressure sensor.<br />
Place the rail pressure sensor to mounting position.<br />
11B-34<br />
Install the rail pressure sensor and tighten.<br />
Connect the connector of rail pressure sensor.<br />
11B-35<br />
INTERIOR PRESSURE CONTROL VALVE<br />
It is installed on the fuel pump.<br />
3. Components<br />
Pressure control valve is connected to high-pressure pump by a mounting flange. In order to ensure<br />
that the gap between the high-pressure and the low-pressure section is well sealed, the pivot makes a<br />
ball valve resist against the seal gasket. Two forces act on the pivot: one is the spring force; the other is<br />
the acting force produced by electromagnet. In order to ensure lubrication and cooling, fuel must flow<br />
through the pivot.<br />
Pressure control valve comprises of two closed-loop control:<br />
• One is the electronic control loop used to set the low speed of the changing average common rail<br />
pressure.<br />
• The other is the mechanical hydraulic control loop used to compensate the quick-acting of<br />
high-frequency pressure fluctuations.<br />
11B-36<br />
Disconnect the connector of interior pressure control<br />
(d). Remove the interior pressure control valve.<br />
Remove using the inner offset wrench.<br />
Install the interior pressure control valve.<br />
Connect the connector of interior pressure control valve.<br />
11B-37<br />
It is installed at the rear end of the transmission.<br />
Vehicle speed sensor is installed on output shaft of gearbox with mechanical gears transforming to<br />
electric pulse signal. Then, use wire to send electric pulse signal to odometer with pulse frequency<br />
indicating speed and pulse counter accumulating mileage.<br />
The vehicle speed sensor is to measure the vehicle speed in the travelling of car and it is also signal<br />
output part to accumulate total travelling mileage of vehicle.<br />
4. Components and principles<br />
Closed magnetic circuit revolution speed sensor is composed of external gear, internal gear, coil and<br />
permanent magnet installed on revolving shaft. Internal and external gears have the same number of<br />
teeth. If revolving shaft is connected to the shaft for measurement to revolution together, magnetic<br />
resistance will change due to relative motion of internal and external gears. So, AC induction potential<br />
will be generated in coil. Through the potential value, the corresponding revolving speed can be<br />
worked out.<br />
5. Common faults<br />
• Vehicle speed odometer does not move.<br />
• Vehicle speed odometer does not move at times.<br />
6. Operating characteristics<br />
Rated operating voltage: 12 V<br />
Power voltage scope (Vcc): 8 V~16 V<br />
Injection current at output end (lsink): ≤25 mA<br />
Power supply current (lcc): 10 mA (max)<br />
Output low level (Vol): 0.5 V (max)<br />
Output high level (Vol): Vcc-0.5 V (min)<br />
The number of signal pulses: 8 P (pulses/round)<br />
11B-38<br />
Operating temperature: - 40 ℃~120 ℃<br />
Maximum revolving speed of sensor: 3000 r/min<br />
7. Replacement<br />
· Turn off engine, remove the key and start parking brake to make sure that the vehicle does not move when<br />
dismantling.<br />
· When pulling out the connector of harnesses, press and hold the snap rings of connector and pull them<br />
out slowly to avoid pulling the lead to result in poor contact or open circuit.<br />
Disconnect the connector of vehicle speed sensor.<br />
Remove the fixing bolts of vehicle speed sensor.<br />
Take down the vehicle speed sensor.<br />
Install the vehicle speed sensor.<br />
11B-39<br />
Tighten the fixing bolts of vehicle speed sensor.<br />
Connect the connector of vehicle speed sensor.<br />
11B-40<br />
CRANKSHAFT POSITION SENSOR<br />
It is installed on the clutch housing.<br />
It is used to check the engine speed, so, it is also known as revolving speed sensor. It is also used to<br />
check the position of top dead center of piston, so, it is also known as top dead center sensor, including<br />
checking of top dead center signal of each cylinder for ignition control and top dead center of first<br />
cylinder for sequence control of fuel injection.<br />
Crankshaft position sensor is electromagnetic sensor and 58X tooth top and tooth space pass sensor<br />
with different clearances. Sensor can induct the changes of magnetic resistance. Then, the alternating<br />
magnetic resistance will generate alternating output signal. ECM makes use of the signal to determine<br />
the revolving position and speed of crankshaft.<br />
• There is no contact or in poor contact for crankshaft position sensor.<br />
Operating clearance: 0.25~1.75 mm<br />
Coil resistance: 560 Ω<br />
11B-41<br />
Disconnect the connector of crankshaft position<br />
Remove the crankshaft position sensor and take it down.<br />
(d). Install the crankshaft position sensor and tighten.<br />
Clean the mounting position of sensor and the sensor when<br />
installing. Otherwise, the clearance between sensor and gears<br />
will be influenced to affect the signals sent to electronic control<br />
module.<br />
Torque: 7~9 N·m<br />
Connect the connector of crankshaft position sensor.<br />
11B-42<br />
ACCELERATOR PEDAL POSITION SENSOR<br />
It is installed on the accelerator pedal.<br />
Transfer the driver’s expectation of the vehicle to ECU. ECU will determine the basic demands of<br />
injection and torque according to the signal.<br />
• Operational voltage: 5 V±2%<br />
• Operational temperature: - 40~85 ℃<br />
• Signal current: maximum 20 mA<br />
• Short-circuit protection: 16 V,20 min<br />
• Output error:
11B-43<br />
Disconnect the connector of accelerator pedal position<br />
Remove the fixing screws of accelerator pedal position<br />
Take down the accelerator pedal position sensor.<br />
Install the accelerator pedal position sensor.<br />
Tighten the fixing screws of accelerator pedal position<br />
11B-44<br />
Connect the connector of accelerator pedal position<br />
11B-45<br />
ELECTRONIC CONTROL MODULE (ECU)<br />
It is installed under the driver’s seat.<br />
ECU is to receive the input signal of sensor and carry out calculation according to designed programs<br />
to generate corresponding control signal output and drive each actuator to carry out different actions.<br />
Meanwhile, make the engine operate according to specific control strategy.<br />
ECU (electronic control unit) is also known as “travelling computer” and “auto computer”. From its<br />
functions, it is special micro computer controlled for vehicle. So, it is also called special single-chip for<br />
vehicle. Like the ordinary single-chip, it is composed of microprocessor (CPU), memory (ROM and<br />
RAM), input/output interface (I/O), AD converter (A/D), shaping and driving large scale integrated<br />
circuit. Electronic control unit is to calculate process and make judgments on the input information of air<br />
flow meter and various sensors according to its memorized programs and data and then output orders<br />
to provide electric pulse signal of certain width for fuel injector to control fuel injection quantity.<br />
Electronic control unit is composed of microcomputer, input, output and control circuits.<br />
(a). Faults of power circuit.<br />
(b). Faults of output circuit.<br />
(c). Memory faults.<br />
Nominal operating voltage: DC12 V<br />
Operating voltage scope: 6.5~16 V<br />
Maximum operating current: 5 A<br />
Operating temperature: - 30 ℃~85 ℃<br />
-MEMO-<br />
After stopping the vehicle, turn off engine, place the transmission to empty gear, start parking brake<br />
system and disconnect the negative cable of battery.<br />
(b). Remove the driver’s seat (See Chapter 84 Seats - Main Driver’s Seat and Replacement).<br />
(c). Remove the connector of ECU.<br />
Lift the fixing clips for connector of ECU up, and then pull<br />
out the connector of ECU.<br />
(d). Remove the fixing bolts of ECU assembly.<br />
(e). Take down the ECU assembly.<br />
When taking down the ECU assembly, do not impact the<br />
ECU to avoid damaging the ECU.<br />
Place the ECU assembly to mounting position, install the<br />
fixing bolts and tighten.<br />
Torque: 5 N·m<br />
(g). Connect the connector of ECU.<br />
When connecting the connector of ECU, align the mounting<br />
position to avoid damaging the pins. When the ECU is<br />
inserted completely, pull up the clips to lock the connector<br />
of ECU.<br />
(h). Connect the negative cable of battery.<br />
(i). Install the main driver’s seat (See Chapter 84 Seats –<br />
MainDriver’s Seat and Replacement).<br />
模 板 00<br />
FUEL SYSTEM .................................................................................. 12B-1<br />
Overview ........................................................................................ 12B-1<br />
Precautions ................................................................................... 12B-2<br />
System Composition and Its Principles..................................... 12B-3<br />
Diagram of Components .............................................................. 12B-7<br />
FUEL INJECTOR (ELECTRONIC).................................................. 12B-13<br />
Precautions ................................................................................. 12B-13<br />
Parameter of Technical Characteristics ................................... 12B-14<br />
Service ......................................................................................... 12B-15<br />
FUEL INJECTOR (MECHANICAL)................................................. 12B-19<br />
Diagram of Components ............................................................ 12B-19<br />
Testing ......................................................................................... 12B-20<br />
Disassembly and Cleaning ........................................................ 12B-21<br />
Service ......................................................................................... 12B-23<br />
Assembly and Adjustment ........................................................ 12B-25<br />
HIGH PRESSURE FUEL RAIL ....................................................... 12B-26<br />
Overview ...................................................................................... 12B-26<br />
Replacement ............................................................................... 12B-27<br />
FUEL INJECTION PUMP (VE PUMP) ............................................ 12B-31<br />
Adjustment .................................................................................. 12B-31<br />
FUEL PIPELINE (ENGINE PART) .................................................. 12B-33<br />
Precautions ................................................................................. 12B-33<br />
Replacement ............................................................................... 12B-34<br />
FUEL TANK ..................................................................................... 12B-37<br />
Service ......................................................................................... 12B-37<br />
FUEL FILTER (COARSE FILTER) .................................................. 12B-42<br />
Replacement ............................................................................... 12B-42<br />
FUEL FILTER (FINE FILTER) ......................................................... 12B-44<br />
Drainage of Water ....................................................................... 12B-44<br />
Replacement ............................................................................... 12B-46<br />
12B<br />
FUEL-FUEL SYSTEM<br />
12B-1<br />
OVERVIEW<br />
1. Introduction<br />
4JB1 EuroⅢ diesel engine fuel system matched with Sapupika diesel engine series is electronically<br />
controlled high pressure common rail system, and 4D20 diesel engine fuel system matched with it is<br />
electronically controlled VE pump system.<br />
2. Function of fuel system<br />
Function of fuel system is to inject diesel into combustion chamber at rated time, quantity and<br />
pressure to provide necessary conditions for good combustion of diesel and automatically adjust fuel<br />
delivery according to load condition of diesel engine to ensure steady running of diesel engine.<br />
12B-2<br />
1. Safety precautions<br />
(a). Before service of fuel supply system, turn off the ignition switch first and disconnect negative terminal<br />
cable of battery. Open the fuel filler cap for short periods and screw it up.<br />
(b). When removing and installing the fuel tank, the vehicle should be stopped on a horizontal plane, and<br />
fuel in the tank should not occupy 3/4 of the gross capacity. If needed, empty the fuel tank.<br />
(c). Before the service, fix a plug-in emission hose of fuel vapor near installation port of fuel tank to empty<br />
the fuel vapor.<br />
If there is no fuel vapor emission device, you can use a centrifugal blower with over 15m 3 /h gas delivery.<br />
(d). Maintenance of the fuel tank and related accessories must be away from fire, the maintenance site<br />
should be well-ventilated and appropriate fire fighting equipment should be prepared.<br />
(e). The connection of fuel pipe and connectors should be reliable without any loosening, so as to avoid<br />
pipeline leakage.<br />
(f). Use the plastic strip assembly to fix with pipeline for each 250mm intervals in the frame, while use the<br />
tank band to fix the forepart of return pipe, so as to prevent friction with the stringer.<br />
(g). Add spiral protective sleeve at the contact part of pipeline and fuel tank, fuel tank bracket, frame to<br />
protect the pipe.<br />
(h). The pipe should be unified with the direction of harness, brake pipelines after entering the frame, and<br />
should keep the maximum distance with the harnesses and then fix.<br />
(i). Release the oil pump pressure (pressure relief) firstly when repairing the fuel system, in order to<br />
prevent the fuel injection causing the environment and human damages.<br />
(j). When starting the engine after installation of injection system, ensure the oil delivery pump and filter<br />
full of fuel. If needed, keep pressing on the start button to make it in active state.<br />
High pressure connection part of fuel system needs no deflation for the high pressure common rail<br />
will emit air automatically under high pressure. If loosen tight cap of the high pressure fuel pipeline,<br />
fuel will leak out under pressure.<br />
2. Cleaning precautions<br />
(a). Clean thoroughly the connector and its nearby before switching off it.<br />
(b). The removed parts should be put on the clean surface and covered up. Don’t use fuzzy cloth.<br />
(c). Cover or lock up the open parts if you don’t repair them immediately.<br />
(d). Only clean parts can be assembled. Take out spare parts only before assembling. Don’t use scattered<br />
parts (for instance, in the tool box).<br />
12B-3<br />
SYSTEM COMPOSITION AND ITS PRINCIPLES<br />
1. Composition of fuel system<br />
(a). Fuel system composition of 4JB1 Euro Ⅲ high pressure common rail diesel engine<br />
It consists of diesel tank, diesel pipe, diesel filter, high pressure fuel pump, fuel rail, high pressure fuel<br />
pipe and fuel injector, etc. (See the following figure)<br />
1 High pressure fuel pipe<br />
2 Diesel pipe (fuel delivery)<br />
3 high pressure fuel pump<br />
4 Diesel pipe<br />
5 Fuel filter<br />
6 Diesel pipe (fuel delivery)<br />
7 Fuel tank<br />
8 Strainer<br />
9 Fuel injector<br />
10 Diesel pipe (fuel return)<br />
11 Diesel pipe (fuel return)<br />
12 High pressure fuel rail<br />
13 High pressure fuel pipe<br />
12B-4<br />
Fuel system composition of 4D20 electronically controlled VE pump diesel engine:<br />
It consists of diesel tank, diesel pipe, oil-water separator, diesel filter, fuel injector pump assembly,<br />
high pressure fuel pipe, fuel injector, etc.<br />
1 Fuel filter<br />
2 Diesel pipe(fuel delivery)<br />
3 Fuel injector pump<br />
4 Fuel return pipe<br />
5 Fuel injector<br />
6 High pressure fuel pipe<br />
7 High idle speed solenoid valve<br />
<strong>Manual</strong> pump handle of oil-water<br />
separator<br />
9 Oil-water separator<br />
10 Fuel tank<br />
11 Diesel pipe (fuel delivery)<br />
12 Diesel pipe (Fuel return)<br />
12B-5<br />
2. Working principle of fuel system<br />
Working principle of 4JB1 Euro III high pressure common rail diesel engine.<br />
• High pressure part<br />
With continuous work of electronically controlled high pressure fuel pump, fuel is injected into the high<br />
pressure fuel rail, in which it accumulates pressure, and ECU controls the fuel pressure in the rail with fuel<br />
pump actuator in the pump. Rail pressure sensor in the rail feeds back information of rail pressure to form<br />
a closed-loop control for ECU. For high pressure fuel rail accumulates high pressure fuel at any time, ECU<br />
calculates proper fuel according to the inner rated data when it needs the injection of some vat and make<br />
the injector inject the calculated fuel according to the calculated time by controlling the magnetic solenoid<br />
valve of the fuel injector.<br />
• Low pressure part<br />
Low pressure fuel rail is divided into oil-inlet part and fuel return part. Fuel inlet means fuel is transferred<br />
from fuel tank into coarse filter, fuel filter and high pressure fuel pump. Fuel return means fuel return of fuel<br />
injector, high pressure fuel rail and electronically controlled high pressure pump connects together and<br />
fuel returns to the fuel tank.<br />
12B-6<br />
Fuel system Working principle of 4D20 electronically controlled VE pump diesel engine.<br />
Raise the diesel pressure by the work of fuel injection pump and provide high pressure fuel for combustion<br />
chamber at rated time, quantity and pressure according to the working requirements of diesel engine.<br />
from fuel tank into coarse filter, fuel filter and fuel injection pump. Fuel return means Fuel return of injector<br />
and fuel injection pump connects together and fuel returns to the fuel tank.<br />
12B-7<br />
DIAGRAM OF COMPONENTS<br />
High pressure common rail fuel system (Engine Part)<br />
12B-8<br />
1 Fuel injector<br />
2 O-ring<br />
3 Fuel injector pad<br />
Fuel injector and Fuel return pipe<br />
assembly<br />
5 High pressure clamp<br />
6 Fuel injector Fuel return rubber hose<br />
7 Fuel return T-pipe weldment<br />
8 High pressure clamp<br />
Fuel injection pump Fuel return rubber<br />
hose<br />
10 High pressure fuel pipe 1<br />
11 High pressure fuel pipe 2<br />
12 High pressure fuel pipe 3<br />
13 High pressure fuel pipe 4<br />
14 Bolt<br />
15 High pressure fuel rail<br />
High pressure fuel pipe (from fuel<br />
injection pump to fuel rail)<br />
17 Fuel rail support<br />
18 Bolt<br />
19 Nut<br />
20 Bolt<br />
21<br />
Fuel injection pump pulley pressure<br />
plate<br />
22 Woodruff key<br />
23 Fuel injection pump pulley<br />
24 Fuel injection pump flange<br />
25 Bolt<br />
26 Fuel injection pump<br />
12B-9<br />
Electric VE pump fuel system (Engine Part)<br />
12B-10<br />
1 Fuel injection pump flange seal ring<br />
2 Bolt<br />
3 Fuel injection pump gear<br />
4 Flange plate<br />
5 Fuel injection pump parts<br />
6 Bolt<br />
7 Fuel injection pump support<br />
8 Fuel injection pump rear support<br />
9 Large washer<br />
10 Bolt<br />
11 Bolt<br />
12 Idle lift valve parts<br />
13 Bolt<br />
14 High pressure fuel pipe parts 1<br />
15 High pressure fuel pipe parts 2<br />
16 High pressure fuel pipe parts 3<br />
17 High pressure fuel pipe parts 4<br />
18<br />
High pressure fuel pipe punch holder<br />
High pressure fuel pipe die holder<br />
21 Fuel injector<br />
22 O-ring<br />
23 Fuel injector pad<br />
24 Fuel injector fuel return pipe assembly<br />
25 Fuel return pipe clip<br />
26 Fuel injector Fuel return pipe<br />
27 Low pressure fuel pipe seal head<br />
12B-11<br />
Fuel system I (Body Part)<br />
1 Cross recess head screw<br />
2 Large washer<br />
3 Fuel filler cap assembly<br />
4 Spring hose clamp<br />
5 Rubber hose<br />
6 Rubber hose<br />
7 Air valve<br />
8 Nylon cable tie<br />
9 Fuel filler lower pipe<br />
10 EFI fuel hose II<br />
11 Rubber hose<br />
12 Diesel coarse filter<br />
13 Diesel settler support welding<br />
14 Rubber hose<br />
15 Fuel pipe clamp (blue)<br />
16 A-type worm drive hose clamp<br />
17 Fuel tank front pressure plate assembly<br />
18 All-metal hexagon flange lock nut<br />
19 Rubber hose<br />
20 Rubber hose<br />
21 Fuel return pipe<br />
22 Fuel delivery pipe<br />
12B-12<br />
Fuel system II (Body Part)<br />
1 High pressure clamp<br />
2 Rubber hose<br />
3 Spring washer<br />
4 Rubber hose<br />
5 Hexagon bolt<br />
6 Flat washer<br />
7 Fine filter support<br />
8 Rubber hose<br />
9 Cross recess head screw<br />
10 Large washer<br />
11 Fuel filler cap assembly<br />
12 Spring hose clamp<br />
13 Rubber hose<br />
15 Air valve<br />
16 Nylon cable tie<br />
17 Fuel filler lower pipe<br />
18 A-type worm drive hose clamp<br />
19 Fuel tank front pressure plate assembly<br />
20 Spring washer<br />
21 Type 1 hexagon nut<br />
22 Fuel filler cap assembly<br />
23 Fuel return pipe<br />
24 Fuel delivery pipe<br />
25 Fuel pipe clamp<br />
26 Fine filter<br />
FUEL-FUEL INJECTOR (ELECTRONIC)<br />
12B-13<br />
FUEL INJECTOR (ELECTRONIC)<br />
1. Replace fuel injector assembly if there is any fault of fuel injector solenoid valve. Don’t remove the<br />
valve by yourself.<br />
2. Keeping fuel injector clean is the first requisite for normal operation of solenoid valve.<br />
3. Avoid short circuit of solenoid valve binding post and the engine.<br />
4. Take out protective cap only before assembling and cover the connector up immediately after<br />
removing. Ensure there is some spared clean protective cap and clean the used protective cap with<br />
ultrasonic wave.<br />
5. Grease all the O-ring with engine oil or diesel before assembling.<br />
6. Don’t overly bend or squeeze the cable or connect with sharp ends. Avoid vibration of circuits.<br />
7. Don't use any tool when installing and removing fuel return pipe.<br />
8. Fuel injector clamp bracket: don’t take it out or bend it.<br />
9. Don’t assemble fuel return pipe without clamp bracket or the fuel will leak out.<br />
10. If clamp bracket is removed by mistake, please replace with a new one.<br />
11. Bigger bend, rotation or deformation will narrow the fuel return pipe. All these should be avoided.<br />
12. Hose part of fuel return pipe should not be removed or loosened from the fuel return plug for it cannot<br />
ensure complete assembling. If something happens as above, the whole fuel return pipe must be<br />
13. When loosening high pressure pipe nut, ensure no pressure is on the connector. If the high pressure<br />
connector is already loosened, the whole fuel injector must be replaced.<br />
14. Replace with a new bronze seal ring after each fuel injector is removed. And all the nuts that need<br />
fastening must be replaced.<br />
12B-14<br />
PARAMETER OF TECHNICAL CHARACTERISTICS<br />
Due to various types of diesel engine matched with Sapupika, the following chart of technical characteristics<br />
parameter of the 4JB1 EuroⅢ diesel engine fuel injector is just for reference, and the practical maintenance<br />
of engine should be subject to parameter of technical characteristics supported by the suppliers based on<br />
different types of engines.<br />
Parameter<br />
Minimum Typical Maximum<br />
Remark<br />
Peak current A 17.5 18 18.5<br />
Holding current A 11.5 12 12.5<br />
20~70℃ measuring<br />
resistor<br />
Ω 0.215 0.255 0.295<br />
Current on time Μs 4000 (Starting stage 300-450μs)<br />
Cold start Μs 6000<br />
Maximum 60s,frequency is lower than<br />
5Hz<br />
Pre-injection and<br />
main injection<br />
minimum interval<br />
μs 800<br />
Interval of current on time (from<br />
conclusion of pre-injection current signal<br />
to starting of main-injection current signal)<br />
Working pressure Bar 250 1450 Rail pressure<br />
Fuel return pressure<br />
(relative pressure)<br />
Bar 0.3 0.8 Relative to external pressure<br />
String leak pressure Bar 1700 1800 No current, eigenvalue<br />
nozzle opening<br />
pressure caused by<br />
combustion<br />
Bar 120 Eigenvalue, no system pressure<br />
Fuel temperature ℃ -30<br />
Fuel temperature ℃ 115<br />
In cold start condition, measurement<br />
point: fuel inlet of fuel injector<br />
working area, permitted temperature<br />
amounts to 135℃ in 15min, working time<br />
exceeding 100 hours, measurement point:<br />
fuel inlet of fuel injector<br />
Fuel return<br />
temperature<br />
℃ 125<br />
Permitted temperature amounts to 145℃<br />
in 15min, working time exceeding 100<br />
hours, measurement point: fuel outlet of<br />
fuel injector<br />
External temperature ℃ -30 120<br />
Permitted temperature amounts to 130℃<br />
hours, measurement point: solenoid valve<br />
head of fuel injector<br />
12B-15<br />
SERVICE<br />
After the engine stalls, any installation must be prohibited in 30s. For fuel is inflammable, the<br />
operating area should keep away from fire and should be equipped with ventilators when servicing<br />
the fuel system.<br />
1. Park the vehicle on steady road<br />
Switch off the engine after parking, shut down the ignition switch, change the transmission into<br />
neutral gear and start parking braking system.<br />
2. Lift engine compartment cover assembly<br />
(a). Lift engine compartment cover lock cable handle.<br />
(b). Lift engine compartment cover.<br />
Reach your hand into the front of engine compartment cover,<br />
move the lock operation handle upward when touching it, then<br />
the hood is completely open. Finally, raise the hood with efforts<br />
and find the support bar to plug it into fixed position.<br />
3. Remove fuel injector<br />
(a). Disconnect the connector of fuel injector.<br />
Don’t pull the lead directly when pulling the connector or it<br />
will cause short circuit or open circuit.<br />
12B-16<br />
(b). Switch off the connector of high pressure fuel pipe and<br />
high pressure fuel rail.<br />
Block the fuel pipe up with plug after removing, or the dirt will<br />
influence function of fuel system.<br />
(c). Switch off high pressure fuel pipe connecting between<br />
fuel injector and high pressure fuel rail.<br />
Use two wrenches to remove high pressure fuel pipe. Block the<br />
fuel pipe up with plug after removing, or the dirt will influence<br />
function of fuel system.<br />
(d). Push the fuel return pipe fixing clip to the direction of<br />
the opening and take out the fuel pipe.<br />
Don’t remove or loosen the hose part of fuel injector fuel<br />
return pipe, if something happens as the above, please<br />
replace the whole fuel return pipe.<br />
(e). Remove fuel injector pressure plate fixing bolt.<br />
(f). Take out fuel injector pressure plate.<br />
Pull the fuel injector pressure plate backward before taking it<br />
out to make the removal easier.<br />
(g). Take out the fuel injector in sequence.<br />
4. Check the fuel injector<br />
(a). Fix fuel injector on the calibration stand to control fuel<br />
pressure, voltage and current duration and determine<br />
whether the fuel injector is normal by observing the<br />
pulverization of fuel injector and amount of fuel<br />
injection.<br />
Fuel injector is precise hence non-professionals must not<br />
remove or maintain it.<br />
12B-17<br />
5. Install fuel injector<br />
(a). Assemble fuel injector and fuel injector pressure plate<br />
together.<br />
To prevent bronze washer shedding off when installing fuel<br />
injector, grease the bronze washer with some lithium-based<br />
lubricants.<br />
(b). Install fuel injectors in corresponding holes in<br />
(c). Install firmly fixing nuts of fuel injector pressure plate.<br />
Fastening of fuel injector pressure plate bolts is divided into<br />
two steps: first, rotate it for 7.5~9 N·m; then rotate it for 40~45<br />
degrees.<br />
(d). Connect the connector of each fuel return pipe and fuel<br />
injector.<br />
Directly press the connector of fuel return pipe and fuel injector<br />
onto the installation hole or clip will be stuck after being<br />
pressed down.<br />
(e). Connect high pressure fuel pipe with fuel injector and<br />
fasten the nuts.<br />
Fasten each high pressure fuel pipe in couple.<br />
(f). Connect the connector of each fuel injector.<br />
You can hear a sound of clatter when installing the connector.<br />
Slowly pull it up after installation to ensure it is installed in<br />
place.<br />
12B-18<br />
6. Close the engine compartment cover<br />
(a). Put the engine compartment cover support bar down into<br />
the clip slot.<br />
(b). Lower the compartment cover gently at the height of<br />
20cm from the lock and then drop it to fall free.<br />
Lock the compartment cover firmly for safety. Check whether<br />
the compartment cover is locked after closing it. The engine<br />
compartment cover must be flush with the vehicle’s body<br />
nearby.<br />
FUEL INJECTOR (MECHANICAL)<br />
FUEL-FUEL INJECTOR (MECHANICAL)<br />
12B-19<br />
1 Clip<br />
2 Fuel injector<br />
3 O-ring<br />
4 Fuel injector pad<br />
12B-20<br />
TESTING<br />
1. Remove fuel injector assembly<br />
(a). Removal of fuel injectors (See Chapter 15B Mechanical Part of Engine - fuel pipeline, fuel injector,<br />
removal)<br />
2. Detection of fuel injectors<br />
(a). Fix the fuel injector on the test stand and move the<br />
stand handle at the speed of 4~6 times/s. Check if<br />
there is any particle flying out, dripping backward or<br />
spraying abnormally, etc. Keep fuel injection pressure<br />
below 21.0MPa, if there is no leakage, it works well.<br />
The opening pressure is 27~28MPa, if it is abnormal,<br />
restore or replace parts of fuel injectors.<br />
3. Injection of fuel injectors<br />
(a). See the left figure of injection of fuel injectors.<br />
(b). Adjust and service it if the pulverization is abnormal.<br />
12B-21<br />
DISASSEMBLY AND CLEANING<br />
1. Clean the fuel injector<br />
(a). Brush the fuel injector’s outer surface clean in the fuel<br />
basin.<br />
Be cautious of head of pin valve. Brush it with banister<br />
2. Remove fuel injectors<br />
(a). Fasten the fuel injector on table vice placed with a<br />
copper sheet and make the nozzle upward.<br />
If the pin valve is stuck in the nozzle nut by carbon deposit,<br />
it should be dipped in the diesel oil and taken out without<br />
being tapped or pulled.<br />
3. Clean parts of fuel injectors<br />
(a). Clean nozzle fixing nut, fuel injection body, pushing rod,<br />
lock nut, adjusting screw and pressure adjusting spring<br />
with clean diesel oil or kerosene.<br />
(b). Clean the oil passage of fuel injector body with copper<br />
needle.<br />
Clean the carbon deposit outside the pin valve with<br />
banister brush or thin copper wire.<br />
12B-22<br />
Clean the oil passage of pin valve with copper needle.<br />
(f). Stretch the brass angle scraper into the pressure<br />
chamber and rotate it to scrape off the carbon deposit<br />
in the pressure chamber of pin valve.<br />
(g). Clean up the matching parts of pin valve again with<br />
clean diesel oil.<br />
Matching parts of pin valve cannot be replaced or pieced<br />
12B-23<br />
1. Check fuel injector body<br />
Ensure that the precise plate matched with matching parts of<br />
pin valve is flat and smooth without scratches. All screw<br />
threads are complete without scratches, the bearing pad is flat<br />
and all the inner holes are clean, unblocked. If it is not qualified,<br />
please replace it.<br />
2. Check fixing nuts of fuel injector nozzle<br />
Inside and outside surface are clean without scratches; the<br />
screw threads are complete without scratches; the matching<br />
parts of pin valve are clean without damage. If it is not qualified,<br />
3. Check the pushing rod<br />
The rod is upright; connection part with pin valve has no<br />
scratches. If it is not qualified, please replace it.<br />
4. Check the spring<br />
Both ends are flat with not overly abrasion, of good elasticity,<br />
and with no scratches on the surface. If it is not qualified,<br />
12B-24<br />
5. Check the pin valve<br />
Ways of checking as follows:<br />
Do sliding testing of the cleaned matching parts of pin valve to<br />
see whether it is still available. The checking method is that put<br />
the pin valve spotted with clean diesel oil into the valve body,<br />
tilt the matching parts of pin valve for 45 degrees, extract 1/3<br />
pin valve of the whole length and drop it to let it slide down<br />
slowly and smoothly by its own weight without blockage or<br />
detention. If the matching parts of pin valve are seriously<br />
defective, please replace them. As for those which are not<br />
seriously defective, such as due to the poor surface of pin<br />
valve and its body, the sliding testing fails, we can restore them<br />
by grinding.<br />
12B-25<br />
ASSEMBLY AND ADJUSTMENT<br />
1. Assemble fuel injectors<br />
(a). Fasten fuel injector body on the table vice placed with<br />
copper sheet and install the gasket, spring, pushing<br />
rod, spacer, fuel injection nozzle and fuel injector<br />
nozzle fixing nut in sequence.<br />
Fasten fuel injector nozzle fixing nut to meet the<br />
standards.<br />
2. Adjust the fuel injector<br />
(a). Fix fuel injector on the testing stand and observe the<br />
condition of fuel injection by raising the pressure.<br />
Regulate gaskets properly until the pulverization is in<br />
good condition.<br />
(b). Take out the fuel injector after adjustment, fasten it on<br />
the table vice placed with copper sheet, and fasten<br />
fuel injector nozzle nuts to meet the standards.<br />
12B-26<br />
FUEL-HIGH PRESSURE FUEL RAIL<br />
HIGH PRESSURE FUEL RAIL<br />
1. The fuel rail is integrated with rail pressure sensors. The fuel rail is for storage of high pressure fuel.<br />
Fluctuation of pressure caused by fuel supply and fuel injection of high pressure pump can be<br />
controlled in the common rail. Rail pressure sensor feeds back information of current rail pressure for<br />
ECU, with which the inner pressure control valve in the pump controls the rail pressure.<br />
2. High pressure common rail means several fuel injectors share the same high pressure rail. Rail<br />
pressure is created by high pressure pump.<br />
3. The fuel injection system eliminates mutual influence between creation of pressure and fuel injection<br />
in traditional fuel supply system. In this system, creation of injection pressure does not completely rely<br />
on rotation rate of the engine and fuel delivery and fuel stored in the high pressure fuel rail under<br />
pressure is ready to be injected at any time.<br />
4. Electronically controlled high pressure common rail diesel engine is completely controlled by ECU.<br />
ECU determines the running condition of engine according to the present rotation rate, coolant<br />
temperature, atmospheric pressure and throttle position (that is driver’s needs), etc.<br />
5. For the electronically controlled high pressure common rail system provides the ideal mixture of air<br />
and fuel, it hugely increases the whole noise of vehicle, driving comfort, dynamics and emission, etc<br />
compared with traditional diesel engine.<br />
12B-27<br />
Block the fuel pipe up with plug after removing, or the dirt will enter in.<br />
3. Remove high pressure fuel rail assembly<br />
(a). Disconnect the connector of rail pressure sensors.<br />
(b). Disconnect nuts of high pressure fuel pump and high<br />
pressure fuel pipe.<br />
Use two wrenches to remove.<br />
12B-28<br />
Disconnect nuts of high pressure fuel pipe and high<br />
pressure fuel rail.<br />
(d). Disconnect nuts of fuel injectors and high pressure fuel<br />
Remove fixing nuts of high pressure fuel rail assembly.<br />
Take out high pressure fuel rail support assembly.<br />
(g). Remove fixing bolts of high pressure fuel rail and the<br />
support.<br />
(h). Check if the high pressure fuel rail is damaged, if it is,<br />
Rail pressure sensor is fixed by hexagon surface according to<br />
specific torque and supplied with fuel rail and it cannot be<br />
replaced personally. Try to avoid touching connector of the<br />
sensor in case of damage when installing the fuel rail.<br />
4. Install high pressure fuel rail assembly<br />
(a). Install the high pressure fuel rail on the support and<br />
fasten it with fixing bolts.<br />
12B-29<br />
Install fixing bolts of high pressure fuel rail assembly.<br />
Install nuts connecting high pressure fuel pipe and high<br />
(d). Install nuts connecting fuel injector and high pressure<br />
fuel pipe.<br />
Use two wrenches to install.<br />
(e). Install nuts connecting high pressure fuel pump and<br />
high pressure fuel pipe.<br />
Connect rail pressure sensor connector.<br />
12B-30<br />
5. Close the engine compartment cover<br />
Fg<br />
FUEL INJECTION PUMP (VE PUMP)<br />
ADJUSTMENT<br />
FUEL-FUEL INJECTION PUMP (VE PUMP)<br />
12B-31<br />
1. Adjust fuel supply timing<br />
(a). Check if the notch line of fuel injection pump flange<br />
aligns with that of pump body.<br />
(b). Rotate the crankshaft and align the piston of the first<br />
cylinder with TDC position on compression stroke until<br />
the TDC reticle 1 on crankshaft pulley align with timing<br />
mark 2.<br />
Check intake valve of the first cylinder and idle stroke of<br />
exhaust valve push rod. If there is idle stroke of first<br />
cylinder intake valve and valve push rod, the piston of first<br />
valve is on the TDC position of compression stroke.<br />
Remove cone screw plug of lower plunger hole end<br />
from fuel injection pump.<br />
Install measurement instrument3 of fuel supply<br />
advance angle. Detector of the instrument should be<br />
pressed inward for about 1mm.<br />
Rotate crankshaft and adjust the dial gauge to zero<br />
when the first cylinder piston is on the 30-40 degrees<br />
position of TDC. Slowly rotate crankshaft pulley at both<br />
directions and check the reading of dial gauge.<br />
12B-32<br />
Rotate the crankshaft clockwise and check the reading<br />
on the instrument when the TDC mark of crankshaft<br />
pulley aligns with timing mark of gear cover.<br />
If fuel supply timing is incorrect, do the following steps.<br />
• Loosen fixing nuts of fuel injection pump and<br />
bracket bolts.<br />
• Adjust fuel supply advance angle.<br />
If the advance angle is too big or small, loosen bolts of<br />
high pressure fuel pump connection plate and adjust it.<br />
If the advance angle is too big, turn the high pressure<br />
fuel pump for a proper angle counter-clockwise.<br />
If the advance angle is too small, turn the high pressure<br />
fuel pump for a proper angle clockwise.<br />
Fasten the three bolts. Check the fuel supply advance<br />
angle again.<br />
Install high pressure fuel pipe of the first cylinder.<br />
FUEL-FUEL PIPELINE (ENGINE PART)<br />
12B-33<br />
FUEL PIPELINE (ENGINE PART)<br />
1. Don't use any tool when installing and removing fuel return pipe.<br />
2. Don’t assemble fuel return pipe without clamp bracket or the oil will leak out.<br />
3. Hose part of fuel return pipe should not be removed or loosened from the fuel return plug for it cannot<br />
4. When loosening nuts of high pressure fuel pipe, switch off the power and operate after 30s.<br />
5. Cover the removed fuel pipe with protective cap to prevent the dirt from entering.<br />
12B-34<br />
For fuel is inflammable, the operating area should keep away from fire and should be equipped with<br />
ventilators to decrease harm or death of personnel. Block the fuel pipe and parts pipe up with cap<br />
after removing, or the dirt will influence function of fuel system.<br />
3. Remove high pressure fuel pipe<br />
(a). Disconnect nuts of high pressure fuel pump and high<br />
12B-35<br />
(c). Disconnect nuts of fuel injectors and high pressure fuel<br />
4. Remove Fuel return fuel pipe<br />
(a). Push fuel return fuel pipe clamp to the opening<br />
direction and take it out from fuel injectors.<br />
Hose part of fuel injectors should not be removed or<br />
loosened from the fuel return plug. If something happens<br />
as above, the whole fuel return pipe must be replaced.<br />
Disconnect fuel return fuel pipe and high pressure fuel<br />
pump.<br />
5. Install fuel return fuel pipe<br />
(a). Install connectors of fuel return pipe and each fuel<br />
injector in place.<br />
12B-36<br />
Fasten the spring hose clamp of fuel return fuel pipe<br />
and high pressure fuel pump.<br />
6. Install high pressure fuel pipe<br />
(a). Install fixing nuts connecting high pressure fuel pipe<br />
and fuel rail.<br />
When installing the high pressure fuel pipe, put high pressure<br />
fuel pipe down from the lower end of intake manifold.<br />
(b). Install firmly fixing nuts connecting high pressure fuel<br />
pipe and fuel injectors.<br />
Use two wrenches when installing. Fasten each high pressure<br />
fuel pipe in couple.<br />
Install firmly fixing nuts connecting high pressure fuel<br />
pump and high pressure fuel pipe.<br />
7. Close the engine compartment cover<br />
FUEL-FUEL TANK<br />
12B-37<br />
FUEL TANK<br />
1. Exhaust fuel<br />
(a). Park the vehicle on the lifter and pull the parking braking handle to the braking position.<br />
(b). Switch off negative terminal cable of the battery.<br />
(c). Open the fuel filler cap.<br />
The switch of fuel filler cap is at the lower left of driver’s seat.<br />
Pull up the switch and the fuel filler cap will open automatically.<br />
Screw down the fuel tank cap.<br />
Lay oil drum or equivalent container down drain bolts<br />
under the fuel tank.<br />
Remove the drain bolts under the fuel tank.<br />
2. Check<br />
(a). Before removing the fuel tank, visually check whether there are leakage or leakage trace on the fuel<br />
tank, fuel tank pipeline and connector, make it for future maintenance and replacement if any.<br />
3. Remove the fuel tank<br />
(a). Remove the fixing screws of fuel tank filling pipe<br />
assembly with a screwdriver.<br />
(b). Put the bracket to the bottom of fuel tank.<br />
12B-38<br />
(c). Remove the fixing bolts of fuel tank assembly.<br />
After removing the fixing bolts of fuel tank assembly, drag it<br />
with the bracket, and lower the bracket to a proper position.<br />
Disconnect the connector of the fuel level sensor lead.<br />
(e). Loose the fixing clips of fuel inlet and outlet pipes, pull<br />
out the fuel inlet and outlet pipes.<br />
After disconnect the pipe, the pipe and the fuel inlet and<br />
outlet shall be blocked, and then mark on the fuel inlet and<br />
outlet pipes, so as to prevent wrong installation.<br />
(f). Lower the bracket to the appropriate position, and pull<br />
out the fuel tank.<br />
Disconnect all the pipes connecting with the fuel tank<br />
and check whether the pipes are aged or fractured,<br />
please replace if damaged.<br />
12B-39<br />
(h). Remove the fuel pump.<br />
• Remove the fuel pump gland with special wrench.<br />
• Remove the fuel pump.<br />
Check whether the fuel stand pipe filter has any dirt, blockage<br />
or crack, if there is any dirt or blockage, clean it up with brush<br />
and petrol and if there is any crack, please replace it.<br />
(i). Remove the fuel level sensor.<br />
When removing the fuel level sensor, move up the sensor a<br />
little, and then incline to one side to remove it, must be careful<br />
not to damage the oil level float.<br />
4. Clean the fuel tank<br />
(a). Clean the fuel tank inner part from all angles with high<br />
pressure water jet, ensure no dirt and impurities remain<br />
in the fuel tank<br />
• When cleaning, the waste water should be collected<br />
from the fuel outlet, in order to avoid environmental<br />
contamination.<br />
• The high pressure water jet can be put into the fuel<br />
tank to ensure that all parts could be cleaned.<br />
(b). Use compressed air to dry the fuel tank inner part<br />
5. Install the fuel tank assembly<br />
(a). Install the fuel level sensor.<br />
Do not damage the oil level float during installation.<br />
12B-40<br />
Install the fuel pump.<br />
• Place the fuel pump in installation position.<br />
• The fuel pump gland should be installed and<br />
fastened using special tools.<br />
Connect all the pipes connected with the fuel tank and<br />
use the flexible clip or A-type worm drive hoop to<br />
fasten.<br />
Place the fuel tank on the bracket and drag the fuel<br />
tank to the appropriate position of installation position<br />
under the car body.<br />
(e). Connect intake and outlet fuel pipes.<br />
Install according to the tag, do not install the fuel inlet and<br />
outlet pipes wrongly.<br />
(f). Connect the connector of fuel level sensor lead.<br />
When connecting the connector of fuel level sensor lead,<br />
it should sound "click", and gently pull back to ensure it<br />
installed in place.<br />
12B-41<br />
Install the fixing bolts of fuel tank.<br />
Torque: 45~55 N·m<br />
(h). Install the screws of fuel tank filling pipe assembly and<br />
(i). Refill the fuel.<br />
Check whether the fuel drain plug of the fuel tank installed<br />
in place.<br />
(j). Fasten the fuel tank cap.<br />
Clockwisely rotate the fuel tank cap until it “click”, which<br />
means the fuel tank cap has been fastened.<br />
(k). Close the fuel filler cap.<br />
12B-42<br />
FUEL-FUEL FILTER (COARSE FILTER)<br />
FUEL FILTER (COARSE FILTER)<br />
1. Remove fuel filter assembly<br />
(a). Switch off the fuel inlet hose and fuel outlet hose on the<br />
fuel filters.<br />
Check fuel inlet and outlet hoses, if there is any<br />
efflorescing, erosion or crack, please replace them.<br />
Take out the filter element with special tools of the filter.<br />
Remove the fuel filter base.<br />
2. Install fuel filter assembly<br />
(a). Install the fuel filter base.<br />
• Install firmly the fixing bolts of the fuel filter base.<br />
Torque:45~55 N·m<br />
12B-43<br />
(b). Install the filter element with special tools of the filter.<br />
When installing the fuel filter, inject proper clean fuel into<br />
the filter and grease the filter seal ring with some<br />
Hook the fuel inlet and outlet pipes with elastic clips on<br />
the inlet and outlet positions of the filter and fasten<br />
12B-44<br />
FUEL-FUEL FILTER (FINE FILTER)<br />
FUEL FILTER (FINE FILTER)<br />
DRAINAGE OF WATER<br />
When the engine fault indicator lights up, check whether there is any water in the diesel fine filter, if there is<br />
any, drain completely all the water in the drainer.<br />
3. Water drainage of diesel fine filter<br />
(a). Loosen the water drain valve of diesel fine filter.<br />
Put drainage pipe of water drain valve into a vessel before<br />
loosening the water drain valve to prevent the drained water<br />
from polluting the environment.<br />
Don't switch off the diesel fine filter water drain valve but<br />
loosen it. When the clean fuel comes out from the pipe, all<br />
the water in the fine filter is drained. Fasten the screws of<br />
water drain valve immediately.<br />
12B-45<br />
4. Close the engine compartment cover<br />
12B-46<br />
3. Remove the fuel fine filter<br />
(a). Drain the fuel in the fuel fine filter by drainage of the<br />
fuel fine filter.<br />
(b). Disconnect fuel inlet and outlet pipes of the filter.<br />
Put fuel inlet and outlet pipes into the fuel in the drainage<br />
pipeline in the vessel after switching off them. Seal it up<br />
with the cap after drainage. Check the fuel inlet and outlet<br />
hoses, if there is any efflorescing, erosion or crack, please<br />
(c). Disconnect the connector of fine filter lead.<br />
Don’t pull the lead directly when disconnecting the<br />
connector of fine filter.<br />
(d). Remove fine filter sensors.<br />
12B-47<br />
Remove the fine filter element with special tools of the<br />
filter.<br />
Remove the fine filter base.<br />
4. Install the fuel filter<br />
(b). Install the fine filter element with special tools of the<br />
Grease the filter seal ring with some engine oil to lubricate<br />
when installing the filter. If the fuel filter is screwed too<br />
firmly, it will cause the deformation of threads of screws,<br />
or the damage of the filter element or gasket or can.<br />
(c). Install the fuel fine filter sensors.<br />
(d). Connect the connector of fine filter lead.<br />
The connector of fuel fine filter lead must be installed in<br />
12B-48<br />
Hook the fuel inlet and outlet hoses of fine filter with the<br />
spring hose clamp and fasten them up.<br />
5. Drainage<br />
(a). Remove the air exhaust bolts of the fuel filter.<br />
Air exhaust of fuel pipeline must be operated after<br />
maintaining the pipelines of fuel system or replacing the<br />
(b). Operate the manual fuel pump of the filter several times<br />
for the exhaust of fuel system.<br />
Don’t overexert when operating the manual fuel pump in<br />
case of damage.<br />
Drainage is completed until the fuel appears in the<br />
exhaust hole of the filter without bubbles.<br />
12B-49<br />
驻 车 制 动 - 驻 车 制 动 系 统<br />
27-1<br />
EGR SYSTEM ·····································································13B-1<br />
Overview ········································································13B-1<br />
Working principle ····························································13B-2<br />
Diagram of Components···················································13B-3<br />
EGR PIPE ··········································································13B-4<br />
Service ···········································································13B-4<br />
EGR VALVE········································································13B-7<br />
Service ···········································································13B-7<br />
13B<br />
EMISSION CONTROL--EGR SYSTEM<br />
13B-1<br />
EGR SYSTEM<br />
1. EGR system is also called Exhaust Gas Recirculation system which mainly comprises of ECU, vacuum<br />
adjuster, EGR valve, valve position sensor, coolant temperature sensor, speed sensor, throttle position<br />
sensor, pressure maintaining valve, exhaust gas recirculation pipeline and vacuum connecting pipeline<br />
and etc. Its main functions are: make part of the exhaust gas in the exhaust pipe re-circulate into the<br />
intake manifold and mix with the fresh air to flow into the combustor so as to reduce the combustion<br />
temperature,reduce the generation of oxynitride and finally reduce the pollution of atmosphere.<br />
2. The function of EGR valve is to control the opening of vacuum valve by vacuum degree so as to control<br />
the mass of exhaust gas flow. The opening of the valve is sent back to ECU by valve position sensor. If<br />
EGR valve is seriously stuck, the engine will produce black smoke.<br />
3. When the car has driven for each 4000-5000km, check whether each nut on the exhaust connecting<br />
pipe is loose, there is any flaw or hole for the exhaust gas connecting pipe, and any damage or erosion<br />
for the gasket.<br />
13B-2<br />
WORKING PRINCIPLE<br />
EGR will prohibit the generation of NOx, CO and some other pollutants in the emission by guiding a small<br />
amount of engine exhaust gas to the intake manifold, diluting the fresh air to decrease the peak of combustion<br />
pressure and temperature. When the engine is working, throttle position sensor, speed sensor, coolant<br />
temperature sensor and etc. will input the signal of engine instant state to ECU and ECU will judge the instant<br />
operational situation according to these signals, and based on the data which has been stored in it, ECU can<br />
adjust different vacuum degree by vacuum adjuster. EGR valve will control the valve opening according to<br />
different vacuum degree. The valve opening is then sent back to ECU by the valve position sensor. During the<br />
whole operational process, each operational situation of the engine will have a perfect EGR rate (the ratio of<br />
mass of exhaust gas recirculation - mE and mass of fresh air - mA, that is, mE/mA).<br />
1 Joint of diagnostic tool<br />
2 Vacuum adjuster<br />
3 Pressure maintaining valve<br />
4 Vacuum pump<br />
5 Vacuum connecting pipe<br />
6 EGR valve<br />
7 ECU<br />
8 Coolant temperature sensor<br />
9 Speed sensor<br />
10 Throttle position sensor<br />
11 Exhaust gas connecting pipe<br />
13B-3<br />
1 Rubber plug<br />
2 Pressure maintaining valve<br />
3 Hose<br />
4 Hose<br />
5 Three-way<br />
6 Idling lift valve connecting hose<br />
7 770 hose<br />
8 EGR pipe connecting bolt<br />
9 EGR valve<br />
10 EGR pipe gasket<br />
11 EGR pipe<br />
12 Type 1 hexagon nut<br />
13 Spring washer<br />
14 Small washer<br />
15 Vacuum adjuster<br />
16 Stud<br />
17 ECU<br />
13B-4<br />
EMISSION CONTROL-EGR PIPE<br />
EGR PIPE<br />
1. Disassemble EGR pipe<br />
(a). Disassemble the nut connecting EGR pipe and intake<br />
Disassemble bolt connecting EGR pipe and EGR valve.<br />
Take down EGR pipe.<br />
2. Clean and check EGR pipe<br />
(a) Clean the sealing surface of EGR pipe and intake pipe<br />
by relieving tool.<br />
13B-5<br />
Clean the sealing surface of EGR pipe and EGR valve<br />
(c). Clean EGR pipe by vapor.<br />
When using the vapor cleaner, you shall put on safety<br />
glasses or protective mask and clothing as hot vapor may<br />
cause severe personal injury.<br />
Check whether the sealing surface of EGR pipe is<br />
perfect. There shall be no severe flaw on the sealing<br />
surface.<br />
Check whether the gasket of EGR is perfect. If there is<br />
any wear or damage, it shall be replaced.<br />
3. Install EGR pipe<br />
(a) Put the EGR pipe in the installation position.<br />
13B-6<br />
Fasten the nut connecting the EGR pipe and intake pipe.<br />
Fasten the bolt connecting the EGR pipe and EGR<br />
EGR VALVE<br />
EMISSION CONTROL-EGR VALVE<br />
13B-7<br />
1. Disassemble EGR pipe (see chapter 13B Emission control-EGR pipe, service)<br />
2. Disassemble EGR valve<br />
(a) Disassemble fixing bolt of EGR valve<br />
Take down EGR valve.<br />
3. Clean and check EGR valve<br />
(a) Clean the sealing surface of EGR valve by relieving tool.<br />
Two sealing surfaces of EGR valve shall be cleaned.<br />
Clean the dirt and debris in the EGR valve by blowing<br />
high-pressure gas.<br />
13B-8 EMISSION CONTROL-EGR VALVE<br />
Check whether the sealing surface of EGR valve is<br />
perfect. The sealing surface shall have no severe flaw.<br />
Check whether the gasket of EGR valve is perfect. If<br />
there is any wear or damage, it shall be replaced.<br />
(e). Provide EGR valve with 15Kpa vacuum degree by<br />
manual vacuum pump and EGR valve shall be able to be<br />
switched on.<br />
When no vacuum degree is provided to EGR valve, EGR<br />
valve shall be able to be switched off.<br />
4. Install EGR valve<br />
(a). Put EGR valve in the installation position.<br />
Install and fasten the fixing bolt of EGR valve.<br />
13B-9<br />
5. Install EGR pipe (see chapter 13B Emission control-EGR pipe, service)<br />
-MENO-<br />
INTAKE SYSTEM<br />
INTAKE SYSTEM .............................................................................. 14B-1<br />
Overview ........................................................................................ 14B-1<br />
Precautions ................................................................................... 14B-2<br />
Working Principle ......................................................................... 14B-3<br />
INTAKE MANIFOLD .......................................................................... 14B-4<br />
Diagram of Components .............................................................. 14B-4<br />
Service ........................................................................................... 14B-5<br />
INTAKE PIPELINE ........................................................................... 14B-12<br />
Diagram of Components ............................................................ 14B-12<br />
Replacement ............................................................................... 14B-13<br />
AIR FILTER ...................................................................................... 14B-17<br />
Service ......................................................................................... 14B-17<br />
14B<br />
INTAKE-INTAKE SYSTEM<br />
14B-1<br />
1. The intake system mainly includes air filter, intake manifold and relevant hose, which supplies pure air<br />
for each cylinder.<br />
2. The function of intake system is to evenly supply combustible mixture or pure air for each cylinder as<br />
much as possible.<br />
3. The intake manifold distributes the pure air to the inlet of each cylinder.<br />
4. The function of air filter is to filter out the impurities and dust in the air, in order to avoid accelerating<br />
the cylinder wear, and reduce the service life of engine, while the air filter could reduce the intake<br />
noise.<br />
14B-2<br />
1. Safety cautions<br />
(a). The operation should not be conducted at the road side or crowded places, the car should be parked<br />
on the flat ground if possible.<br />
(b). Ensure the parking brake lever is placed on the parking location.<br />
(c). Fix the wheel with a wedge or bunk block, wedge or bunk block should be placed in the position close<br />
to both sides of the tire, it’s preferred to fix on both sides of the rear wheels.<br />
(d). When maintaining and replacing the filter element, the car should be parked in a place without wind,<br />
dirt and dust.<br />
2. Important tips<br />
(a). The tightness of intake pipeline and air filter connection should be check frequently, any leakage<br />
should be dealt with timely, fasten the connector to avoid the abnormal wear.<br />
(b). After 4,000 ~ 5,000km drive, the exhaust pipe of the car should be checked as follows:<br />
• If any nut is loosen. Fasten the nuts of exhaust pipe with uniform force, or it may cause air<br />
• If there is any crack or perforation for exhaust pipe, and any damage or erosion for gasket.<br />
• The exhaust pipe gasket is suggested to use once only; in order to ensure the air tightness,<br />
timely replace the damaged gasket.<br />
(c). Unless replacing the filter element, do not Disassemble (or clean) the inner filter element (safe filter<br />
element) in the dual snorkel air filter.<br />
(d). When replacing the outer filter element, if the inner filter element is damaged originally, the inner filter<br />
element must be replaced.<br />
14B-3<br />
The outside air enters compressor room of turbocharger after being filtered by air filter, and enters intake<br />
manifold through intake connecting pipe after being compressed by turbocharger, then is distributed to inlet of<br />
each cylinder by intake manifold. The burned gas is discharged from exhaust manifold. The formed exhaust<br />
gas flow will impact turbine of turbocharger so that it can rotate at a high speed. The exhaust gas through<br />
turbine is finally discharged to the exterior by exhaust tail pipe. Part of exhaust gas in the exhaust manifold is<br />
discharged from EGR valve. Then this exhaust gas enters intake connecting pipe through EGR pipe, and is<br />
sent back to engine combustor for combustion again to suppress the generation of oxynitride.<br />
1 Exhaust tail pipe<br />
2 EGR pipe<br />
3 EGR valve<br />
4 Intake connecting pipe<br />
5 Intake manifold<br />
6 Exhaust manifold<br />
7 turbocharger<br />
8 Intake pipe<br />
9 Air filter<br />
14B-4<br />
INTAKE-INTAKE MANIFOLD<br />
1 Double wire clamp 66<br />
2 Intake hose 2<br />
Hexagon head bolt and spring washer<br />
4 Flange bolt<br />
5 Intake connecting pipe bracket<br />
6 Type 1 hexagon nut<br />
7 Spring washer<br />
8 Flat washer<br />
9 stud<br />
10 Intake connecting pipe<br />
11 Intake elbow gasket<br />
12 Intake manifold<br />
Hexagon head bolt, spring washer<br />
and flat washer assembly<br />
14 Harness clamp<br />
15 Intake manifold gasket<br />
14B-5<br />
1. Disassemble the intake manifold assembly<br />
(a). Disassemble the connecting bolts between EGR pipe<br />
and intake connecting pipe.<br />
Disassemble the connecting bolts between EGR pipe<br />
and EGR valve.<br />
Remove the EGR pipe.<br />
Disassemble the breather outlet hose clamp.<br />
• Remove the breather outlet hose.<br />
14B-6<br />
Disassemble the fixing bolts of turbocharger intake<br />
connecting pipe assembly bracket.<br />
Remove the turbocharger intake connecting pipe<br />
assembly.<br />
Disassemble the fixing bolts of exhaust pipe bracket.<br />
Disassemble the fixing bolts of intake connecting pipe.<br />
Remove the intake connecting pipe.<br />
Disassemble the fixing bolts of oil level gauge bracket<br />
and remove the oil level gauge assembly.<br />
Disassemble the fixing bolts of oil cooling water pipe<br />
14B-7<br />
(l).<br />
Disassemble the fixing nuts of high-pressure oil pipe<br />
and remove the high-pressure oil pipe.<br />
(m).<br />
Disassemble the fixing nuts of intake manifold.<br />
(n).<br />
Remove the intake manifold.<br />
• Remove the intake manifold gasket.<br />
2. Clean and check all the parts<br />
(a). Clean the sealing surface that combines cylinder head<br />
and intake manifold with a relieving tool and a clean<br />
cloth.<br />
Prevent the sealing materials and other impurities from<br />
entering the intake port.<br />
When cleaning the sealing surface with a relieving tool, it is<br />
preferred to plug the intake port with a clean cloth, and prevent<br />
the dirt and debris from entering the intake manifold.<br />
14B-8<br />
Clean the sealing surface that combines intake<br />
connecting pipe and intake manifold with a relieving<br />
Clean the sealing surface of intake pipe connector and<br />
the interior of intake manifold connector with a clean<br />
Check the intake connecting pipe. If there is any crack<br />
or any severe defect for sealing surface, repair or<br />
replace it with a new.<br />
Clean the sealing surface of intake manifold with a<br />
relieving tool and a clean cloth.<br />
Blow away the dirt and debris in the intake manifold<br />
with high-pressure gas.<br />
14B-9<br />
Measure the junction surface flatness of intake<br />
manifold and cylinder head with high-precision ruler<br />
and feeler (or on the plat calibration console). If the<br />
flatness exceeds technical range, the intake manifold<br />
shall be machined or replaced.<br />
3. Install the intake manifold<br />
(a). Install the intake manifold gasket.<br />
(b). Place the intake manifold to installation position.<br />
Replace a new intake manifold gasket when installing the<br />
intake manifold connector.<br />
Install and fasten the fixing bolts of intake manifold.<br />
Install and fasten the nuts of high-pressure oil pipe.<br />
Install the oil cooling water pipe and fasten the fixing<br />
bolts of oil cooling water pipe.<br />
14B-10<br />
Install the oil level gauge and fasten the fixing bolts of<br />
oil level gauge assembly.<br />
Install the intake connecting pipe and fasten the fixing<br />
bolts of intake connecting pipe.<br />
Install and fasten the fixing bolts of exhaust pipe<br />
(i). Install the turbocharger intake connecting pipe<br />
assembly and fasten the fixing bolts of turbocharger<br />
intake connecting pipe assembly.<br />
Install the breather outlet hose.<br />
Install the breather outlet hose clamp.<br />
14B-11<br />
Install the EGR pipe.<br />
Install the connecting bolts between EGR pipe and<br />
EGR valve.<br />
intake connecting pipe.<br />
14B-12<br />
INTAKE-INTAKE PIPELINE<br />
INTAKE PIPELINE<br />
3 Hexagon head bolt<br />
4 Air filter assembly<br />
Intake pipe with resonance box<br />
6 Air filter bracket 2<br />
7 Air filter bracket 1<br />
8 A-type worm drive hose clamp<br />
9 Intake connecting pipe assembly<br />
10 Air flow meter<br />
11 A-type worm drive hose clamp<br />
12 Intake bellows<br />
14B-13<br />
1. Park the car on flat and stable road<br />
Flame out the engine after parking the car, the transmission should be located in neutral, and enable<br />
the parking brake system<br />
2. Lift the engine compartment cover assembly<br />
(a). Pull up the lock line handle of engine compartment<br />
Lift the engine compartment cover.<br />
3. Disassemble the intake pipe<br />
(a). Loose the A-type worm drive hose clamp connecting<br />
between the intake rubber hose of turbocharger and<br />
turbocharger.<br />
Loose the A-type worm drive hose clamp connecting<br />
the intake bellows.<br />
14B-14<br />
(c). Remove the bolts of intake rubber hose clamp for<br />
(d). Remove the intake rubber hose of turbocharger.<br />
It is necessary to block the turbocharger outlet port with plug<br />
after removing the intake rubber hose of turbocharger to<br />
prevent the dirt from entering the engine.<br />
between the intake bellows and air flow meter.<br />
Remove the intake bellows.<br />
Disconnect the connector of air flow meter.<br />
between air flow meter and intake connecting pipe<br />
Remove the air flow meter.<br />
between intake connecting pipe assembly and air filter<br />
14B-15<br />
4. Check the intake pipeline<br />
(a). Check whether the intake bellows aged, fractured or<br />
cracked, replace the intake bellows if any.<br />
5. Install the intake pipeline<br />
(a). Install the intake connecting pipe assembly.<br />
• Fasten the A-type worm drive hose clamp<br />
connecting between the intake connecting pipe<br />
assembly and the air filter assembly.<br />
Clean the pipeline before installation.<br />
Install the air flow meter.<br />
connecting between air flow meter and intake<br />
connecting pipe assembly.<br />
(c). Install the intake bellows.<br />
connecting between intake bellows and air flow<br />
meter.<br />
(d). Install the intake rubber hose of turbocharger.<br />
• Install the A-type worm drive hose clamp<br />
connecting between intake rubber hose of<br />
turbocharger and intake bellows.<br />
14B-16<br />
turbocharger and turbocharger.<br />
Install the intake rubber hose clamp of turbocharger<br />
and fasten the bolts.<br />
Connect the connector of air flow meter.<br />
6. Cover the engine compartment cover<br />
Lower the support bar of engine compartment cover, and cover the engine compartment cover.<br />
AIR FILTER<br />
INTAKE-AIR FILTER<br />
14B-17<br />
The filter element of air filter should be cleaned for every 10,000Km drive, and the filter element of air filter<br />
should be replaced for every 20,000Km drive.<br />
1. Disassemble the intake pipe with resonance box<br />
between intake pipe with resonance box assembly and<br />
air filter device.<br />
Disassemble the fixing bolts of intake pipe with<br />
resonance box assembly.<br />
Remove the intake pipe with resonance box assembly.<br />
2. Check the dust exhausting bag<br />
(a). Press the dust exhausting bag of the air filter with hand,<br />
check whether there is any dust blew out.<br />
If any dust blew out, checking and maintenance are needed.<br />
3. Disassemble the air filter assembly<br />
(a). Lift the fixing lock catch of air filter upper cover.<br />
14B-18<br />
Remove the filter element.<br />
Remove the fixing bolts of filter bracket.<br />
(d). Disassemble the fixing bolts of the filter device.<br />
(e). Remove the filter device lower part<br />
The operation procedure for c and d is performed when the<br />
filter device is replaced as a unit.<br />
Clean the dust in the housing and dust on the cover<br />
and surface of gasket for air filter.<br />
(g). Clean the filter element.<br />
The filter element should be cleaned periodically, do not use<br />
compressed air to clean the filter element from the outside, this<br />
may cause dust entering the filter element, rotate the filter<br />
element with hands and use compressed air (below 7kg/cm2)<br />
to blow the dust on the surface inside the filter element at the<br />
same time.<br />
4. Install the air filter assembly<br />
(a). Install the fixing bolts of filter device.<br />
14B-19<br />
Install and fasten the fixing bolts of filter bracket.<br />
Install the filter element.<br />
Lock the fixing lock catch on air filter upper cover.<br />
5. Install the intake pipe with resonance box<br />
(a). Place the intake pipe with resonance box assembly to<br />
installation position.<br />
(b). Install the fixing bolts of intake pipe with resonance box<br />
Install and fasten the A-type worm drive hose clamp<br />
connecting between intake pipe with resonance box<br />
assembly and air filter device.<br />
ENGINE ASSEMBLY ......................................................................... 15B-1<br />
Overview ........................................................................................ 15B-1<br />
Precautions ................................................................................... 15B-2<br />
Diesel Engine Fault Diagnosis .................................................... 15B-3<br />
ENGINE MAINTENANCE ................................................................ 15B-63<br />
Precautions ................................................................................. 15B-63<br />
Operations ................................................................................... 15B-66<br />
Maintenance ................................................................................ 15B-70<br />
Basic Maintenance ..................................................................... 15B-74<br />
DISASSEMBLY/INSTALLATION OF COMPLETE ENGINE .......... 15B-77<br />
Precautions ................................................................................. 15B-77<br />
Disassembly Procedure ............................................................. 15B-79<br />
Installation Procedure ................................................................ 15B-84<br />
Instruction of Essentials ............................................................ 15B-90<br />
PRESERVATION OF COMPLETE ENGINE ................................... 15B-91<br />
Precautions ................................................................................. 15B-91<br />
Maintenance ................................................................................ 15B-91<br />
DISASSEMBLY OF ENGINE (4JB1) .............................................. 15B-92<br />
Instruction of Disassembly ....................................................... 15B-92<br />
Disassembly of Pipeline and Harness ..................................... 15B-93<br />
Disassembly of High and low Pressure Fuel Pipes and Fuel<br />
Injector ......................................................................................... 15B-95<br />
Disassembly of dipstick and Breather ..................................... 15B-97<br />
Disassembly of Turbocharger, Intake Manifold and Exhaust<br />
Manifolds ..................................................................................... 15B-99<br />
Disassembly of Cylinder Head Cover and Rockshaft .......... 15B-101<br />
Disassembly of Tappet and Cylinder Head ........................... 15B-103<br />
Disassembly of Thermostat Assembly and Valve ................ 15B-104<br />
Disassembly of Hook and A/C Bracket .................................. 15B-106<br />
Disassembly of starter motor and High Pressure Fuel Rail 15B-107<br />
Disassembly of oil Filter and Generator ................................ 15B-108<br />
Disassembly of fan and Crankshaft Pulley ............................ 15B-110<br />
Disassembly of Observation Chamber Cover and Water Pump<br />
Pulley Chamber Cover Assembly ............................................ 15B-111<br />
Disassembly of Pressure Plate and Timing Belt.................... 15B-112<br />
Disassembly of Injection Pump Assembly ............................. 15B-114<br />
Disassembly of Idle Pulley and Camshaft Gear ..................... 15B-115<br />
Disassembly of Clutch Components and Flywheel Assembly ...... 15B-118<br />
Disassembly of oil pan and Gear Chamber ........................... 15B-120<br />
Disassembly of Camshaft and Engine support .................... 15B-122<br />
Disassembly of oil Pump, oil Injection Pipe and Tappet ...... 15B-123<br />
Disassembly of Piston and Crankshaft.................................. 15B-125<br />
15B<br />
Assembly of Engine (4JB1)........................................................ 15B-128<br />
Instruction of Assembly ················································15B-128<br />
Installation of Crankshaft and Piston······························15B-129<br />
Installation of Tappet, oil Injection Pipe and oil Pump ······15B-137<br />
Installation of Engine support and Camshaft ···················15B-139<br />
Installation of Gear Chamber and oil Pan ························15B-141<br />
Flywheel Assembly and Clutch Components ··················15B-143<br />
Camshaft Gear and Idle Pulley ······································15B-145<br />
Installation of Injection Pump Assembly ·························15B-148<br />
Installation of Timing Belt and Pressure Plate ·················15B-149<br />
Installation of Water Pump Pulley Chamber Cover Assembly<br />
and Observation Chamber Cover .......................................... 15B-151<br />
Installation of the Crankshaft Pulley and the Fan ·············15B-152<br />
Installation of High Pressure Fuel Rail and starter motor ··15B-153<br />
Installation of Hook and A/C Bracket ······························15B-154<br />
Installation of Valve and Thermostat Assembly ···············15B-155<br />
Installation of Cylinder Head and Tappet ························15B-158<br />
Installation of Rockshaft and Cylinder Head Cover ··········15B-160<br />
Installation of Intake and exhaust MANIFOLDS and<br />
Turbocharger ······························································15B-162<br />
Installation of Breather and dipstick ·······························15B-164<br />
Installation of Fuel Injector and High & low Pressure Fuel<br />
Pipe ···········································································15B-166<br />
Generator and oil Filter ·················································15B-168<br />
Installation of Pipeline and Harness ·······························15B-170<br />
Disassembly of Engine (4D20)................................................... 15B-172<br />
Installation of Disassembly ···········································15B-172<br />
Disassembly of Heater Water Inlet/Outlet Pipe Weldment ·15B-173<br />
Disassembly of Cylinder Head Cover ·····························15B-174<br />
Disassembly of EGR Controller ·····································15B-175<br />
Disassembly of Intake and exhaust MANIFOLDS and<br />
Turbocharger ............................................................................ 15B-177<br />
Disassembly of Generator and Breather ·························15B-180<br />
Disassembly of fan, fan Pulley and Crankshaft Pulley ······15B-183<br />
Disassembly of dipstick ················································15B-185<br />
Disassembly of High & low Pressure Fuel Pipe and Fuel<br />
Injector ·······································································15B-186<br />
Disassembly of Rockshaft and Tappet ····························15B-188<br />
Disassembly of Cylinder Head ·······································15B-189<br />
Disassembly of the Water Outlet Pipe Connector, Valve and<br />
Hook ··········································································15B-190<br />
Disassembly of oil Filter and oil Radiator ·······················15B-192<br />
Disassembly of Clutch Components and Flywheel<br />
Assembly ····································································15B-194<br />
Disassembly of oil pan and oil Pump ..................................... 15B-196<br />
Disassembly of oil Seal Cover and oil Seal ........................... 15B-198<br />
Disassembly of Gear Chamber Cover, Fuel Injection Pump<br />
and Water Pump Assembly ..................................................... 15B-199<br />
Disassembly of Camshaft Gear and Crankshaft Gear.......... 15B-202<br />
Disassembly of Camshaft, Piston and Crankshaft ............... 15B-204<br />
Assembly of Engine (4D20)......................................................... 15B-208<br />
Introduction of Assembly ........................................................ 15B-208<br />
Installation of Crankshaft, Piston and Camshaft .................. 15B-209<br />
Installation of oil Seal and oil Seal Cover .............................. 15B-218<br />
Installation of Crankshaft Gear and Camshaft Gear ............. 15B-219<br />
Installation of Fuel Injection Pump and Gear Chamber<br />
Cover ··········································································15B-220<br />
Installation of oil Pump and oil Pan ....................................... 15B-222<br />
Installation of Flywheel Assembly and Clutch Components 15B-224<br />
Installation of oil Radiator and oil Filter................................. 15B-226<br />
Installation of Hook, Valve, and Water Outlet Pipe<br />
Connector .................................................................................. 15B-228<br />
Installation of Cylinder Head ................................................... 15B-231<br />
Installation of Tappet and Rockshaft ...................................... 15B-233<br />
Pipe ············································································15B-234<br />
Installation of dipstick .............................................................. 15B-236<br />
Installation of Crankshaft Pulley, fan and fan Pulley ............ 15B-237<br />
Installation of Breather and Generator .................................. 15B-238<br />
Installation of Intake and exhaust Manifolds and<br />
Turbocharger ........................................................................... 15B-241<br />
Installation of EGR Controller ................................................. 15B-244<br />
Installation of Cylinder Head Cover ....................................... 15B-246<br />
Installation of Heater Water Inlet/Outlet Pipe Weldment ...... 15B-247<br />
Cylinder Head Cover .................................................................... 15B-248<br />
Diagram of Components .......................................................... 15B-248<br />
Service ········································································15B-250<br />
Rocker Assembly ......................................................................... 15B-255<br />
Diagram of Components .......................................................... 15B-255<br />
Service ········································································15B-256<br />
Cylinder Head ............................................................................... 15B-262<br />
Diagram of Components .......................................................... 15B-262<br />
Service ········································································15B-264<br />
Valve .............................................................................................. 15B-269<br />
Overview .................................................................................... 15B-269<br />
Adjustment ................................................................................ 15B-270<br />
Service ········································································15B-273<br />
Camshaft and Tappet ................................................................... 15B-282<br />
Diagram of Components ···············································15B-282<br />
Service ·······································································15B-283<br />
Piston and Connecting Rod Assembly ..................................... 15B-292<br />
Diagram of Components ···············································15B-292<br />
Service ·······································································15B-293<br />
Crankshaft and Flywheel Assembly .......................................... 15B-301<br />
Diagram of Components ···············································15B-301<br />
Service ·······································································15B-302<br />
Cylinder Block ............................................................................. 15B-307<br />
Diagram of Components ···············································15B-307<br />
Service ·······································································15B-309<br />
ENGINE MECHANICAL PART-ENGINE ASSEMBLY<br />
15B-1<br />
ENGINE ASSEMBLY<br />
This chapter analyzes and resolves the common faults of diesel engine and provides solutions for these<br />
common faults of the diesel engines equipped on the SUP product series.<br />
During the operation of the diesel engine, due to the causes such as the wear and deformation or the<br />
improper use and technical maintenance of the parts, the technical status is gradually deteriorated in various<br />
portions of the diesel engine. When any technical index is out of the allowable limit, it indicates that the diesel<br />
engine is malfunctioned. In event of the fault of the diesel engine, the diesel engine may not continue for<br />
normal functioning if such fault is not timely and correctly resolved. This will not only lead to the reduction of<br />
power and economy, the deterioration of the operation performance, and the reduction of exhaust level, but<br />
also cause the early wear of parts.<br />
Some faults of the diesel engine, such as the air contained in the fuel system, blockage of filter, and loose<br />
drive belt, can be resolved by means of the necessary technical maintenance and adjustment. However,<br />
some faults, such as the defect of the mechanisms, can’t be resolved by means of the regular maintenance<br />
and adjustment, which include the damage of cylinder gasket, serious wear of piston ring, wear of valve cone,<br />
and excessive wear of bearing bush. Such faults shall be resolved by removing the diesel engine and<br />
repairing or replacing some parts of the diesel engine.<br />
Generally speaking, the engine fault is complex, and one fault is influenced by various reasons; when a fault<br />
happens, by no means should we disassemble the parts blindly, but we should firstly have a clear<br />
understanding of the whole condition of the car, then analyze the possible reasons according to the specific<br />
phenomena, and investigate the faults one by one in an order from easy to complicated.<br />
15B-2<br />
1. Collect all the actual condition of the fault phenomena.<br />
2. Thoroughly analyze the fault.<br />
3. Connect the fault symptom with basic engine system and parts.<br />
4. Consider whether the recent maintenance and repair measurements are related to the fault<br />
phenomena.<br />
5. Recheck once more carefully before any disassembly work.<br />
6. Judge the fault type, use the fault diagnosis table, and firstly choose the easiest problem to resolve.<br />
7. Confirm the fault cause and repair.<br />
8. After the repair, start the engine and ensure the fault cause has been thoroughly removed.<br />
15B-3<br />
DIESEL ENGINE FAULT DIAGNOSIS<br />
1. The engine cannot be started<br />
Generally, the reasons why the engine cannot be started are mainly the problems of fuel system, electric<br />
system, the compressing pressure in the cylinder, oil, fuel supply advance angle and ambient temperature.<br />
The fuel system goes wrong<br />
The details are as follows:<br />
• There is no fuel in the fuel tank or the drain switch is not turned on.<br />
• There is the air in the fuel system.<br />
• Fuel pipe or the fuel filter is blocked.<br />
• The fuel delivery pump does not supply oil or interruptedly supply oil.<br />
• The advance angle is not correct.<br />
• The fuel injection atomization is bad.<br />
• The draw bar does not return to the maximum fuel supply position.<br />
The electric system goes wrong<br />
• The circuit connection is wrong or there is a bad contact.<br />
• The power of the battery is not adequate.<br />
• The carbon brush of the starter motor and the commutator are in a bad contact.<br />
• The generator does not work.<br />
The viscosity of the oil is too high and causes the reducing of the starting speed.<br />
The ambient temperature is too low.<br />
The compressing pressure in the cylinder is low.<br />
• The cylinder liner, piston and piston ring are worn.<br />
• The valve and the valve seat do not match closely.<br />
• There is no valve clearance.<br />
• The valve stem is stuck in the conduit.<br />
• The cylinder head gasket leaks air.<br />
• The fuel injector seat hole leaks air.<br />
• Valve timing is not correct.<br />
When the engine cannot be started, firstly consider whether it is caused by misoperation or lack of<br />
maintenance.<br />
15B-4<br />
(f). Fault diagnosis and troubleshooting<br />
Check the possible causes for the difficult start or start failure of the engine one by one as per procedure<br />
below. Check in an order from easy to complicated, in order to effectively save the diagnosis time. Any cause<br />
clearly unlikely to occur through analysis may be omitted directly. This diagnosis procedure is for reference<br />
only.<br />
Step Diagnosis Description Measure<br />
Check whether the ambient<br />
temperature is too low<br />
Add hot water or adopt the preheating start<br />
No Go to Step 2<br />
Check whether the starting circuit is in<br />
a good contact<br />
Yes Go to Step 3<br />
Screw down the circuit connection screw<br />
Check whether the battery voltage is<br />
normal<br />
Yes Go to Step 4<br />
Charge the battery according to the technical<br />
requirements<br />
Check whether there is diesel in the<br />
fuel tank or whether the drain switch<br />
is not turned on<br />
Add diesel or turn on the switch<br />
No Go to Step 5<br />
Yes Go to Step 6<br />
Check whether the fuel draw bar has<br />
returned to the maximum fuel supply<br />
When the engine is started, more tension shall<br />
be added to the speed adjusting lever to make<br />
the draw bar return to the maximum fuel supply<br />
Check whether the fuel pipe or the<br />
diesel filter is blocked<br />
Clean the fuel pipe and clean or replace the<br />
diesel filter to solve the blockage problem<br />
No Go to Step 7<br />
Use the manual pump to remove the air. And<br />
Check whether there is any air in the<br />
fuel system<br />
check whether there is air leakage at each<br />
connecting pipe and solve the problem<br />
No Go to Step 8<br />
15B-5<br />
Check whether there is air leakage at the fuel<br />
inlet pipe, and whether the filter screen at the<br />
Check whether the fuel delivery pump<br />
dose not supply fuel or interruptedly<br />
supply fuel<br />
connector of the fuel inlet pipe is blocked; Check<br />
whether the fuel supply solenoid valve is open;<br />
turn on and off the switch and listen, if there is<br />
any sound of movement, the solenoid valve shall<br />
be replaced.<br />
No Go to Step 9<br />
Check whether the fuel injection<br />
atomization is bad<br />
Clean the nozzle parts, adjust the fuel injection<br />
pressure or replace the fuel injector<br />
No Go to Step 10<br />
Check whether the fuel supply<br />
Readjust the fuel supply advance angle<br />
advance angle meets the<br />
requirement<br />
No Go to Step 11<br />
Check whether the connection is<br />
correct and stable<br />
Yes Go to Step 12<br />
No Reconnect and screw down<br />
12<br />
Whether the carbon brush of the<br />
starter motor and communtator are<br />
in a bad contact<br />
Repair or replace carbon brushes and use<br />
Yes sand paper to clean the surface of the<br />
communtator and blow off.<br />
No Go to Step 13<br />
Whether the generator does not<br />
Yes Repair or replace<br />
No Go to Step 14<br />
Check whether the viscosity of the<br />
oil is too high and makes the<br />
Turn the crankshaft for several turns with the<br />
handle or add preheated oil<br />
starting speed too low<br />
No Go to Step 15<br />
15<br />
Check whether the air valve<br />
contains no clearance or the<br />
Adjust the air valve clearance according to the<br />
clearance is too small<br />
No Go to Step 16<br />
Check whether the valve stem is<br />
stuck in the conduit<br />
Yes Clean carefully with kerosene or diesel<br />
No Go to Step 17<br />
17 Check whether the air valve and the Yes Grind the air valve, and replace the damaged<br />
15B-6<br />
air valve seat do not match closely.<br />
air valve spring.<br />
No Go to Step 18<br />
Check whether the nut is screwed down;<br />
Check whether there is air leakage<br />
at the fuel injector seat hole<br />
whether the fuel injector gasket is undamaged;<br />
replace the damaged parts<br />
No Go to Step 19<br />
or blow-by phenomena at the<br />
cylinder head gasket<br />
Check whether the valve timing is<br />
incorrect<br />
Fasten according to the Torque of the cylinder<br />
head bolt; replace the cylinder head gasket<br />
No Go to Step 20<br />
Yes Adjust the timing according to the timing mark<br />
No Go to Step 21<br />
Check whether the cylinder liner,<br />
piston and piston ring are worn<br />
Replace the cylinder liner, piston and piston<br />
ring; remove the reason causing wear<br />
Check carefully according to the above steps,<br />
find out the fault position and remove timely<br />
15B-7<br />
2. Low temperature start difficulty of diesel engine<br />
(a). The diesel goes wrong<br />
When the winter comes or after we enter the severe cold region and do not choose the diesel<br />
according to the requirement, diesel becomes turbid and solidified under the condition of low<br />
(b). The lubricating oil goes wrong<br />
When the winter comes or after we enter the severe cold region and do not choose the oil according<br />
to the requirement, the viscosity of the oil is too high under the condition of low temperature, and<br />
internal friction increased, and starting resistance moment of the diesel engine increased.<br />
(c). The battery goes wrong<br />
When working at the severe cold region, and do not choose the battery according to the requirement,<br />
the battery capacity is less than 100Ah.<br />
(d). The preheating system goes wrong<br />
The electrical element fault makes the preheating system does not work, the preheat plug is<br />
unheated.<br />
15B-8<br />
(e). Fault diagnosis and troubleshooting<br />
Check the causes for the difficult start of the engine one by one as per procedure below, check in an order<br />
from easy to complicated, in order to effectively save the diagnosis time. Any cause clearly unlikely to occur<br />
through analysis may be omitted directly. This diagnosis procedure is for reference only.<br />
When the winter comes or after we enter the<br />
severe cold region, whether choose the diesel<br />
according to the requirement, the diesel<br />
becomes turbid and solidified under the condition<br />
of low temperature<br />
Choose low condensing point diesel<br />
No according to the ambient temperature<br />
in which the diesel engine works<br />
Yes Go to Step 2<br />
Choose low viscosity oil according to<br />
severe cold region, whether choose the oil<br />
according to the requirement, the viscosity of<br />
the ambient temperature in which the<br />
diesel engine works to reduce the<br />
the oil is too high under the condition of low<br />
power required for the start<br />
temperature, and internal friction increased,<br />
and starting resistance moment of the diesel<br />
engine increased<br />
Go to Step 3<br />
When working at the severe cold region,<br />
whether choose the battery according to the<br />
requirement, the battery capacity is less than<br />
100Ah<br />
Choose low temperature battery with<br />
capacity higher than 100Ah according<br />
to the ambient temperature in which<br />
the diesel engine works<br />
Check the voltage of each preheat<br />
The electrical element fault makes the<br />
preheating system does not work, whether the<br />
plug in preheating system, and judge<br />
whether it is the preheat plug fault or<br />
the circuit fault<br />
preheat plug is heated<br />
Check carefully according to the<br />
above steps; find out the fault position<br />
and remove timely<br />
15B-9<br />
3. Low engine power<br />
Low engine power means that the engine power can’t reach the design requirement so that the vehicle lacks<br />
of power, with poor color of exhaust emission, while driving under heavy load or climbing an abrupt slope.<br />
The reasons causing low engine power are mainly problems of fuel system, intake system, exhaust system,<br />
cooling system, low compressing pressure in the cylinder, abnormal oil temperature, incorrect fuel supply<br />
advance angle and low ambient temperature and so on.<br />
When the intake system goes wrong, it generally represents as: at the urgent acceleration, the engine<br />
revolution speed cannot be accelerated to the corresponding speed, and the exhaust pipe exhausts<br />
blue smoke with sharp flavor of the incomplete combustion of the diesel.<br />
• The dust in the filter element of the air filter is too much and causes blockage.<br />
• The intake pipe of the air filter is damaged.<br />
• The intake pipe is not sealed closely.<br />
When the exhaust system goes wrong, it generally represents as: at the acceleration, the exhaust<br />
pipe muffler makes abnormal sound and sometimes there is abnormal dense smoke exhausted from<br />
the exhaust port.<br />
• The exhaust pipe or muffler is damaged and causes blockage.<br />
• The turning radius of the exhaust pipe is too small or there are too many bends.<br />
• Exhaust brake has faults, and the brake valve is normally closed.<br />
When the fuel system goes wrong, it generally represents as: after the acceleration is increased, the<br />
power or revolution speed still cannot be increased, and the engine tends to flameout.<br />
• No fuel in the fuel tank or the fuel level is too low.<br />
• There is air in the fuel system.<br />
• The fuel pipe or diesel filter is blocked.<br />
• The fuel supply of the fuel injector pump is low.<br />
• The atomization of fuel injector is bad.<br />
• The fuel injection pressure is low.<br />
• Few fuel injectors are blocked.<br />
• The fuel injector pump accelerate handle is not properly adjusted.<br />
Fuel supply advance angle changes, revolution speed and performance of each gear decrease.<br />
• The fuel supply advance angle is changed.<br />
• The air valve clearance is incorrect.<br />
The abnormal oil temperature generally represents as: the oil warning light flickers or is normally on;<br />
too high or too low oil temperature will cause the oil deterioration and bad lubrication; this kind of<br />
phenomenon can be caused by problems of ambient temperature, engine cooling system or engine<br />
internal machine.<br />
• Oil filling amount cannot meet the standard.<br />
• Oil brand is not suitable for the ambient temperature.<br />
• The abnormal engine cooling system causes the too high oil temperature.<br />
• The ambient temperature is too low.<br />
15B-10<br />
Low compressing pressure in the cylinder generally represents as: phenomena of low engine power,<br />
decreased performance, air leakage, black smoke and abnormal knocking sound.<br />
• Air vale and air vale seat do not match closely.<br />
• There is no air valve clearance.<br />
Diesel engine is overheated<br />
• The temperature of air coolant is too high.<br />
• The temperature of oil is too high.<br />
• The temperature of exhaust gas is too high.<br />
Cylinder head fault: at this time, not only the power is low and the performance is decreased, but also<br />
there are phenomena of air leakage, black smoke and abnormal knocking sound.<br />
• The joint surface of cylinder head and the engine body leaks air, the cylinder head bolt is loose or<br />
the cylinder gasket is damaged.<br />
• Intake valve and exhaust valve leak air.<br />
• The fuel injector hole leaks air or the copper washer is damaged.<br />
Crank-link mechanism fault<br />
• Connecting rod small end copper sleeve is seized with piston pin.<br />
The low engine power often comes with start difficulty, they are closely related; we can take it as a<br />
reference to analyze, but we shall firstly consider whether it is caused by lack of maintenance.<br />
15B-11<br />
(j). Fault diagnosis and troubleshooting<br />
Tip:<br />
Check the possible causes for the low engine power one by one as per procedure below. Check in an order<br />
Check whether the filter element of<br />
Clean or replace the air filter element.<br />
the air filter is blocked because of<br />
dirtiness.<br />
Check whether the intake pipe of the<br />
air filter is damaged.<br />
Replace the damaged pipe and clean the dust<br />
and other things in the undamaged pipe.<br />
No Go to Step 3<br />
Check whether the intake pipe is well<br />
sealed.<br />
Fasten the pipe connector clamp according to<br />
the technical requirements<br />
Check whether the fixing bolt at the<br />
Yes Go to Step 5<br />
connector of exhaust gas pipe is fixed<br />
firmly<br />
Fasten the loose blot to specified torque.<br />
Check whether the exhaust gas pipe<br />
or the muffler is blocked.<br />
Remove the exhaust gas pipe and muffler to<br />
clean; replace the muffler if necessary.<br />
No Go to Step 6<br />
Whether the modified exhaust gas<br />
pipe caused low exhaust gas amount<br />
or too small turning radius and too<br />
many bends.<br />
Install the exhaust gas pipe according to factory<br />
design to ensure the free flowing of exhaust gas.<br />
Check whether fault happens to<br />
Remove the brake valve fault.<br />
exhaust gas brake or the brake valve<br />
is normally closed<br />
Check whether the fuel in the fuel tank<br />
is sufficient.<br />
Yes Go to Step 9<br />
Fill fuel which suits for local climate condition<br />
15B-12<br />
Loosen the oil return valve on the fuel injector<br />
pump or the air bleeding bolt on the diesel filter,<br />
Check whether there is air in the fuel<br />
pipe<br />
and use the fuel delivery pump to pump the fuel<br />
and bleed the air. Ensure there is no air in the<br />
fuel pipe and fasten the air bleeding bolt.<br />
Check whether the fuel pipe and fuel<br />
filter are blocked<br />
Clean the fuel pipe and replace the fuel filter if<br />
necessary<br />
Check whether the fuel supply of the<br />
fuel injection pump is sufficient<br />
Check, repair and replace the fuel injection<br />
No Go to Step 12<br />
Check whether the atomization of the<br />
fuel injector is bad<br />
Check the fuel injector and repair or replace the<br />
fuel injector with bad atomization<br />
pressure is low<br />
Use the adjusting hot gasket to adjust the fuel<br />
injection pressure<br />
Check whether few fuel injector is<br />
stuck<br />
Yes Repair or replace fuel injector couple<br />
advance angle is changed<br />
Yes Adjust the fuel supply advance angle<br />
clearance is correct<br />
Yes Go to Step 17<br />
No Adjust the air valve clearance<br />
17<br />
pump acceleration handle is well<br />
adjusted<br />
Adjust the acceleration handle to the maximum<br />
Yes fuel supply amount according to the requirement;<br />
check the fuel injection pump if necessary<br />
15B-13<br />
Yes Go to Step 19<br />
Check whether the oil meets the<br />
standard<br />
If the oil amount is low, add more; if the amount<br />
is too high, discharge the redundant oil and find<br />
out the reason of the redundance.<br />
Check whether the oil brand is not<br />
suitable for the ambient temperature<br />
Check whether there is any fault at the<br />
engine coolant level and the cooling<br />
system and causes too high engine<br />
Whether the too low ambient<br />
temperature made the viscosity of the<br />
oil too high and caused the bad<br />
lubrication<br />
Check whether the air valve stem is<br />
Check whether the air valve well<br />
matches with the air valve seat<br />
Replace with the oil suitable for local climate<br />
Fill the coolant to the standard level and find out<br />
Yes the reason of the high temperature and remove<br />
the fault<br />
Replace the oil suitable for the local climate<br />
Yes condition; add suitable warm-keeping<br />
components in front of the radiator<br />
No Go to Step 22<br />
No Go to Step 23<br />
Grind the air valve; replace the damaged air<br />
valve spring<br />
No Go to Step 24<br />
Check whether the fuel injector seat<br />
hole leaks air.<br />
Check whether the nut is screwed down and the<br />
fuel injector gasket is undamaged; replace the<br />
damaged parts<br />
Check there is air leakage or blow-by<br />
phenomena at the cylinder head gasket<br />
correct<br />
No Go to Step 25<br />
Fasten according to the Torque of cylinder head<br />
bolt; replace the cylinder head gasket<br />
No Go to Step 26<br />
No Go to Step 27<br />
15B-14<br />
27<br />
Check whether the cylinder liner, piston<br />
and piston ring are worn.<br />
Replace the cylinder liner, piston and piston ring;<br />
remove the reason causing wear.<br />
No Go to Step 28<br />
Check the cooling system; clean the scale; check<br />
28<br />
Check whether the coolant temperature<br />
is too high<br />
the tightness of the belt and adjust; check the<br />
thermostat<br />
No Go to Step 29<br />
Check the oil amount, add more if it is low; if the<br />
29<br />
Check whether the oil temperature is<br />
too high<br />
bearing bush or one moving member radiates,<br />
find out the radiation part and the reason, and<br />
remove it<br />
No Go to Step 30<br />
Check and revise the static fuel supply advance<br />
Check whether the exhaust<br />
temperature is too high<br />
angle, fuel injection pressure and atomization<br />
condition of the fuel injector<br />
31<br />
Check whether there is air leakage at<br />
the joint surface of cylinder head and<br />
the engine body, and whether the<br />
cylinder head bolt is loosen or the<br />
cylinder gasket is damaged.<br />
No Go to Step 31<br />
Screw down the cylinder head bolt according to<br />
Yes the specified torque or replace the cylinder<br />
gasket<br />
No Go to Step 32<br />
Disassemble and check the intake, exhaust<br />
32<br />
the intake, exhaust valves<br />
valves; grind the air valve or grind the joint<br />
surface of the air valve seat<br />
No Go to Step 33<br />
33<br />
34<br />
Check whether the air valve clearance<br />
is correct<br />
Check the air leakage of the fuel<br />
injector hole or whether the copper<br />
gasket is damaged<br />
Yes Go to Step 34<br />
Revise the air valve clearance to the specified<br />
value<br />
Remove, service, clean and replace the<br />
No Go to Step 35<br />
15B-15<br />
Remove the oil pan, check whether the<br />
35<br />
Check the seizure of the connecting<br />
rod small end copper sleeve and the<br />
piston pin<br />
connecting rod big end can conduct the axial<br />
wobble, if not, remove the connecting rod of the<br />
piston and service<br />
15B-16<br />
4. Engine sudden flameout<br />
Engine sudden flameout means that in the normal work of engine, it suddenly shuts down and cannot run<br />
again. There are two situations for engine sudden flameout: one is that it can start again after the flameout<br />
but cannot run normally, which means the fuel supply system fault; another one is that it cannot start again<br />
after the flameout, even with the starter driving it, which means the machine part fault caused by the bad<br />
internal lubrication of the engine.<br />
When a fault happens in the fuel supply system, it generally represents as after the flameout, when<br />
restart and increase the accelerator, the engine is about to start and there are a little blue smoke<br />
discharged from the exhaust gas pipe, but it stopped if the ignition switch is loosen.<br />
• The fuel in the fuel tank ran out.<br />
• The fuel filter or pipe is blocked.<br />
• The diesel contains water.<br />
The engine internal parts fault generally represents as when restart the engine after the flameout, the<br />
engine cannot run with the starter or runs very slowly.<br />
• The oil pressure is too low or too little.<br />
• Oil pump has faults.<br />
• The piston is stuck with the cylinder liner.<br />
• The connecting rod small end or connecting rod bearing bush is seized with crankshaft.<br />
• Crankshaft main bearing bush is seized.<br />
When the engine suddenly shut down, first use tool to turn the start claw to judge whether the engine<br />
can run, if it can run and runs normally, it means the fuel system goes wrong; if it can not run, it<br />
means the seizure phenomenon appears on the engine internal parts, then disassemble and check to<br />
avoid unnecessary loss.<br />
15B-17<br />
(c). Fault diagnosis and troubleshooting<br />
Check the possible causes for the engine sudden flameout one by one as per procedure below, and check in<br />
an order from easy to complicated, in order to effectively save the diagnosis time. Any cause clearly unlikely<br />
to occur through analysis may be omitted directly. This diagnosis procedure is for reference only.<br />
Check whether the fuel in the fuel<br />
tank ran out<br />
Fill the fuel and bleed the air in the fuel pipe<br />
Go to Step 2<br />
Check whether the fuel system<br />
contains air<br />
Find out the reason of air admission and remove<br />
it; bleed the air in the fuel pipe<br />
Check whether the fuel filter or the<br />
pipe is blocked<br />
Clean the fuel pipe, replace the fuel filter if<br />
No Go to Step 4<br />
Check whether the fuel contains<br />
water<br />
Drain the fuel in the fuel tank and add new fuel,<br />
or deposit the drained fuel and use it again<br />
Check whether the lack of oil caused<br />
Fill the fuel to the standard scale, use tool the<br />
the bad lubrication of the engine parts<br />
turn the start claw and start the engine after it<br />
which caused the slight damage<br />
(there is damping when use tool to<br />
turn the start claw but it can be<br />
turned)<br />
runs smoothly<br />
Go to Step 6<br />
Disassemble the oil pan and check<br />
whether the oil pump goes wrong<br />
Replace or repair the oil pump; repair the worn<br />
parts<br />
Check whether the piston is stuck<br />
with the cylinder liner<br />
Replace the damaged piston and cylinder liner<br />
and find out the reason and remove it<br />
15B-18<br />
Check whether the connecting rod<br />
small end or connecting rod bearing<br />
bush is seized with the crankshaft<br />
Replace the damaged parts, find out the reason<br />
and remove it<br />
Check whether the crankshaft main<br />
bearing bush is seized with the<br />
crankshaft<br />
Replace the main bearing bush; repair or replace<br />
the crankshaft<br />
15B-19<br />
5. Engine abnormal sound<br />
Engine abnormal sound means the obvious knocking or impact sound inside of or on the top of the engine<br />
that can be heard during the normal working. The size and the frequency of such sound increase following<br />
the increasing of the engine rotation speed. Once occurred, such sound is hard to disappear without the<br />
adoption of the remedy measure. Firstly differentiate the type of the engine abnormal sound as the impact<br />
sound arising from the abnormal detonation or from the abnormal movement of parts and then find out the<br />
root cause depending on the noise characteristic and portion of noise source in combination with the<br />
structure theory.<br />
(a). Air valve mechanism abnormal sound. It generally represents as: in the running process of the car,<br />
there is obvious abnormal sound at the upper part of the engine, and the volume and frequency of the<br />
sound will increase along with the increase of the engine revolution speed; once the sound happens,<br />
it is difficult to vanish without taking any measurements.<br />
• The viscosity of the oil is too dilute.<br />
• The air valve tappet contains no oil.<br />
• The air valve clearance is too large.<br />
• The rocker or the rockshaft is worn.<br />
• The air valve is stuck; the air valve seat is inclined or contains too much carbon deposit.<br />
(b). Fuel supply time too early or too late abnormal sound. When the fuel supply is too early, it generally<br />
represents as that it makes clear metal knocking sound form the cylinder at the urgent acceleration;<br />
while when the fuel supply is too late, it generally represents as that it makes low and deep but not<br />
clear knocking sound from the cylinder; and generally it exhausts air with dense smoke.<br />
• The fuel supply time is too early.<br />
• The fuel supply time is too late.<br />
• The fuel injector is stuck.<br />
(c). Piston and piston ring abnormal sound. It generally represents as grinding sound “Da Da Da” from the<br />
upper part of the cylinder block and the cylinder head, the sound and frequency will increase with the<br />
increase of the engine revolution speed, and it comes out with possible exhaust gas and blue smoke<br />
and decreased engine power.<br />
• The piston ring is severely worn.<br />
• The piston is severely worn.<br />
• The cylinder barrel is severely worn.<br />
• The clearance between the cylinder barrel and the piston is too large.<br />
(d). The piston pin and connecting rod small end bush match loosely. It generally represents as that the<br />
engine will make slight and blunt sound when it is running, and this kind of sound is particularly clear<br />
at the idle operation.<br />
• The connecting rod small end bush is worn.<br />
• The piston pin is worn.<br />
(e). The clearance between the piston and cylinder liner is too large. It generally represents as that a<br />
crashing sound can be heard from the outer wall of the engine when it is running, and the sound will<br />
15B-20<br />
be louder when the revolution speed increases.<br />
The air valve and piston crash abnormal sound. It generally represents as that it makes deep, uniform<br />
and rhythmed knocking sound form the upper part of the cylinder block and cylinder head.<br />
• The valve timing is incorrect.<br />
• The clearance of the air valve is too small.<br />
The transmission gear is worn, and the clearance is too large. It generally represents as that it makes<br />
abnormal sound from the gear chamber, and a crashing sound can be heard at sudden decreased<br />
speed.<br />
The wear of the connecting rod bearing bush and the main bearing bush makes the clearance too<br />
large. It generally represents as that when the engine is running, a crashing sound can be heard at<br />
the crank case and it becomes louder when the revolution speed increases.<br />
The clearance of intake valve and exhaust valve are too large. It generally represents as that a loud<br />
and rhythmed sound can be heard at the cylinder head.<br />
When the engine makes abnormal sound and fault sound, we shall not let it continue to work; after<br />
hearing the abnormal sound, we shall urgently stop the car, check and diagnose, judge the reason<br />
and position of the fault and timely remove it to avoid unnecessary loss.<br />
15B-21<br />
Check the possible causes for the sudden flameout of engine one by one as per procedure below, and check<br />
in an order from easy to complicated, in order to effectively save the diagnosis time. Any cause clearly<br />
unlikely to occur through analysis may be omitted directly. This diagnosis procedure is for reference only.<br />
Replace the lubricating oil suitable for the climate<br />
Check whether the viscosity of the oil<br />
is too dilute<br />
condition; check the engine parts damage<br />
caused by the too dilute oil and replace them<br />
Check whether the air valve tappet is<br />
severely worn because of the lack of<br />
Fill engine lubricating oil; replace the damaged<br />
air valve tappet<br />
Rumble sound can be heard at the<br />
intake or exhaust port, meaning<br />
whether the clearance of the air valve<br />
is too large<br />
Adjust all air valve clearance according to the<br />
Check whether the rocker are or<br />
rockshaft is worn<br />
Replace the damaged parts; readjust the air<br />
Clean the stuck air valve, replace the air valve<br />
Check whether the air valve is stuck,<br />
the air valve seat is inclined or<br />
contains too much carbon deposit<br />
Yes seat and grind the air valve; find out the reason<br />
of too much carbon deposit and remove it<br />
Adjust the static fuel supply advance angle,<br />
Check whether the fuel supply time is<br />
too early.<br />
check the fuel injection condition of the fuel<br />
injector, repair or replace if necessary<br />
too late<br />
8 Check whether few fuel injectors are Yes Replace or repair the damaged fuel injector<br />
15B-22<br />
stuck No Go to Step 9<br />
Check whether the piston ring is<br />
severely worn.<br />
Check whether the piston is severely<br />
worn<br />
Check whether the cylinder barrel is<br />
severely worn<br />
Check whether the too large<br />
clearance between the cylinder barrel<br />
and the piston caused the crashing<br />
sound<br />
Replace the piston ring; if necessary, replace the<br />
piston, too.<br />
Replace the damaged piston and cylinder liner;<br />
find out the reason and remove it<br />
Replace the damaged cylinder barrel; if<br />
necessary, replace the piston, too.<br />
Replace the damaged parts; if necessary,<br />
replace the whole set<br />
Replace the damaged piston and cylinder liner,<br />
find out the reason and remove it.<br />
small end bush is worn<br />
Replace the connecting rod small end bush; if<br />
necessary, replace the piston or the connecting<br />
rod<br />
16 Check whether the piston pin is worn<br />
Replace the piston pin; if necessary, replace the<br />
connecting rod small end bush<br />
15B-23<br />
Whether the clearance between the<br />
piston and cylinder liner is too large, a<br />
crashing sound can be heard at the<br />
outer wall of the engine body while<br />
running and it becomes louder when<br />
the revolution speed increases<br />
Replace the piston, or replace the cylinder liner<br />
according to the wear condition<br />
No Adjust the timing gears<br />
clearance is too small or closed<br />
Check whether the transmission<br />
gears are worn and caused too large<br />
clearance<br />
bearing bush and the main bearing<br />
bush are worn and caused the too<br />
large clearance<br />
Check the gear clearance, replace the gear<br />
Disassemble and check the bearing bush; if<br />
Yes necessary, replace and keep the required fit<br />
Whether the clearance of intake valve<br />
and exhaust valve is too large and a<br />
loud and rhythmed sound can be<br />
heard at the cylinder head<br />
Revise the air valve clearance again<br />
15B-24<br />
6. The oil pressure is abnormal<br />
Whether the oil pressure is too high or too low belongs to abnormal situation, in which the too low oil pressure<br />
is rather common. When the pressure is too low, the oil pressure alarm will flicker, meaning the oil pressure is<br />
low or there is no oil. There are many reasons causing oil pressure problems, and the driver or maintenance<br />
personnel shall treat seriously, check the reason of the fault carefully and remove the fault.<br />
The oil pressure sensor or the oil gauge is damaged.<br />
The oil level is too low.<br />
The viscosity of the oil is too dilute.<br />
• The oil brand is not suitable for the local climate condition.<br />
• The temperature of the engine is too high.<br />
• The cylinder head gasket is damaged and the coolant is mixed into the oil.<br />
• The water-blocking seal ring of the cylinder barrel is damaged, and the coolant is mixed into the<br />
oil.<br />
• The cylinder head or cylinder block is cracked and the coolant is mixed into the oil.<br />
The oil filter is blocked<br />
The clearance between the main bearing bush and the connecting rod bearing bush is too large<br />
Oil pump fault<br />
• The inner and outer rotors of the oil pump are severely worn or it leaks oil.<br />
• The oil inlet pipe of the oil pump is blocked.<br />
• The pressure regulating valve of the oil pump has a fault or the lubricating oil pipe is cracked<br />
• The oil filter gasket is installed in the reverse direction.<br />
When the oil pressure is abnormal, we shall not let the engine continue to work, we shall urgently<br />
stop the car after we find it, shut down the engine, check the reason and position of the fault and<br />
timely remove it to avoid unnecessary loss.<br />
15B-25<br />
(g). Fault diagnosis and troubleshooting<br />
Check the possible causes for the abnormal oil pressure one by one as per procedure below, and check in an<br />
order from easy to complicated, in order to effectively save the diagnosis time. Any cause clearly unlikely to<br />
occur through analysis may be omitted directly. This diagnosis procedure is for reference only.<br />
Check whether the oil pressure sensor or the oil<br />
gauge is damaged<br />
Replace the oil pressure sensor or the<br />
oil gauge<br />
2 Check whether the oil level is too low<br />
Add suitable amount of oil, and find<br />
out the reason causing the too low oil<br />
level and remove it<br />
Judge the reason causing too high or too low<br />
engine temperature and whether the oil is<br />
deteriorated influencing by the ambient<br />
Replace the oil suitable for the local<br />
climate temperature condition<br />
Check whether the cylinder head gasket is<br />
damaged and whether the damaged cylinder<br />
Replace the cylinder head gasket and<br />
the oil<br />
gasket makes the coolant mixed into the oil<br />
Check whether the water-blocking seal ring of<br />
the cylinder barrel is damaged, and whether the<br />
damaged water-blocking seal ring of the cylinder<br />
Replace the water-blocking seal ring<br />
of the cylinder barrel and replace the<br />
barrel makes the coolant mixed into the oil<br />
Check whether the cylinder head of the cylinder<br />
block is cracked and whether the cracked<br />
cylinder head of cylinder block makes the coolant<br />
mixed into the oil<br />
Replace the damaged parts and the<br />
7 Check whether the oil filter is blocked<br />
Replace the oil filter; if necessary,<br />
replace the oil<br />
15B-26<br />
Replace the main bearing bush or the<br />
The clearance between the main bearing bush<br />
and the connecting rod bearing bush is too large<br />
connecting bearing bush; if<br />
necessary, replace or repair the<br />
connecting rod or the crankshaft<br />
The oil filter gasket is installed in the reverse<br />
direction<br />
Yes Reinstall or replace<br />
10 Check whether the oil pump goes wrong<br />
Replace or repair the oil pump<br />
Check whether the inner and outer rotors of the<br />
oil pump are severely worn or leaks oil.<br />
12 The oil inlet pipe of the oil pump is blocked<br />
Dredge the oil inlet pipe of the oil<br />
pump and replace the filter screen of<br />
the oil inlet pipe<br />
Replace or repair the damaged parts<br />
The pressure regulating valve of the oil pump or<br />
the lubricating oil pipe is cracked<br />
above steps, find out the fault position<br />
15B-27<br />
7. Engine overheating or supercooling<br />
The overheating or supercooling of the engine will influence the overall performance of the engine. Engine<br />
overheating is rather common, and it generally represents as that the pointer of the coolant temperature<br />
gauge points at the red dangerous scale, the radiator is easy to boil, and vapor can be seen from the radiator<br />
when the engine cover is opened. Drivers or maintenance personnel shall treat it seriously, check the reason<br />
of the fault carefully, and remove the fault.<br />
The cooling system overheating<br />
• The water tank lacks water.<br />
• The cooling pin out of the water tank is blocked with sundries.<br />
• The scale in the water tank is too much and caused blockage and bad circulation.<br />
• The belts of the fan and water pump are too loose, causing that the output volume of the water<br />
pump and fan is too little.<br />
• The distance between the water tank and the fan is inappropriate.<br />
• The water inlet and outlet pipes are deformed and blocked.<br />
• The valve of the thermostat cannot be opened.<br />
• Water pump has faults.<br />
• The fuel supply timing is not correct.<br />
Engine supercooling<br />
• The valve of the thermostat cannot be closed.<br />
• The coolant temperature gauge does not work.<br />
The fuel injection is too late or the fuel injector leaks oil.<br />
• The timing phase is not correct.<br />
• Engine operates with overload for a long time.<br />
• In event of engine overheating, do not stop the engine or add the coolant immediately, or it will<br />
lead to personal injuries or damage of parts. In such case, release the accelerator pedal, run under<br />
unloaded condition or splash a small amount of water onto the surface of coolant tank. After the<br />
coolant in the cooling system cools down, stop the engine for checking.<br />
• Do not remove the cap of coolant tank while the engine is still hot, in order to prevent scalding.<br />
While refilling the coolant, special caution shall be taken.<br />
• If the causes for engine overheating can’t be found and resolved, contact the service station or<br />
service plant immediately, or it will lead to damage of other parts.<br />
15B-28<br />
(d). Fault diagnosis and troubleshooting<br />
Check the causes for the engine overheating or supercooling one by one as per procedure below, and check<br />
1 Check whether the engine lacks coolant<br />
Remove the reason of losing coolant<br />
and fill the coolant<br />
Clean the sundries with hairbrush and<br />
Check whether the cooling pin of the water tank<br />
is blocked because of too much dust or sundries<br />
clean the dust in the cooling pin with<br />
compressed gas<br />
Add aqueous alkali into the water tank<br />
(ten liters of water with 750 grams of<br />
Check whether the scale in the water passage is<br />
too much<br />
washing soda), run the engine for 4-8<br />
hours and drain the water, and<br />
cyclically clean the water passage<br />
with the clean water<br />
Check whether the belts of the fan and the water<br />
pump are too loose or fractured<br />
Adjust the tightness of the belts; if<br />
necessary, replace the belts<br />
Check whether the distance between the water<br />
tank and the fan is not installed properly<br />
Adjust the distance between the water<br />
tank and the fan properly<br />
Check whether the water inlet and outlet pipes<br />
(rubber hoses) are deformed<br />
Replace the deformed rubber hoses<br />
Check whether the thermostat valve does not<br />
work normally<br />
Replace the thermostat<br />
8 Check whether the water pump goes wrong<br />
Replace or repair<br />
15B-29<br />
9 Check whether the fuel supply timing is correct<br />
Yes Go to Step 10<br />
Adjust the fuel supply timing correctly<br />
Check the temperature of the coolant,<br />
Check whether the coolant temperature gauge<br />
does not work<br />
replace the coolant temperature<br />
gauge and sensor<br />
Adjust the fuel supply timing, check<br />
Check whether the fuel injection of the fuel<br />
injector is too late or the fuel injector leaks oil<br />
the fuel injector and replace if<br />
13 Check whether the timing phase is correct<br />
Yes Go to Step 14<br />
Readjust the timing phase<br />
Properly decrease the load to operate<br />
Whether the long time overloading operation of<br />
engine caused the high temperature<br />
15B-30<br />
8. The smoke color of the exhaust gas of the engine is abnormal<br />
Observing the color of the exhaust gas of the engine and judge whether the engine goes wrong is an easy<br />
and effective way. If the engine is under the normal working temperature, its exhaust gas color shall be<br />
colorless or light gray, (the so-called colorless does not mean completely colorless like the diesel engine, but<br />
colorless with slight gray) this is the normal exhaust gas color. The exhaust gas color of the diesel engine<br />
under idle operation, urgent acceleration and high speed and high loading will be darker, the abnormal<br />
exhaust gas colors generally contain: exhaust gas with blue smoke, exhaust gas with white smoke and<br />
exhaust gas with black smoke; more observation of the normal exhaust gas color at ordinary time will be<br />
helpful for having a clearly understanding of the abnormal exhaust gas color.<br />
Engine exhaust gas with blue smoke (oil entersthe cylinder)<br />
• The piston ring and the cylinder liner are worn; the piston ring is bonded or the piston ring gap<br />
• The conduit hole near the exhaust valve is worn.<br />
• The oil level in the oil pan is too high.<br />
• The piston ring is stuck or excessively worn, the elasticity is low; the piston chamfer is reversely<br />
installed and makes the oil enters the combustor.<br />
• With long time low loading operation, the clearance between the piston and cylinder liner is<br />
rather large and makes the oil enters the combustor.<br />
Engine exhaust gas with white smoke (the diesel is not completely combusted under the condition of<br />
engine supercoolling and low loading)<br />
• The fuel supply of the fuel injector is too much.<br />
• The fuel atomization is bad, and the fuel injection is too low.<br />
• The fuel supply is too late.<br />
• The cylinder compressing pressure is too low.<br />
• The diesel contains water or the cylinder contains water.<br />
• When the diesel engine is just started, no combustion in few cylinders (especially in winter)<br />
Engine exhaust gas with black smoke (uncompleted combustion)<br />
• The diesel engine works with overloading.<br />
• The diesel is not atomized well or there is an oil leakage phenomenon.<br />
• The intake pipe or the air filter is blocked.<br />
• The fuel injection quantity is too much.<br />
• The fuel supply amount of each cylinder is not equal.<br />
• The air valve clearance is not correct and the bad sealed air valve caused the air leakage of the<br />
exhaust valve.<br />
• The too small fuel supply advance angle and the too late fuel injection make part of the fuel<br />
combusted in the exhaust gas pipe.<br />
• The cylinder liner and the piston ring are severely worn.<br />
• The EGR system solenoid valve is damaged.<br />
15B-31<br />
• The EGR valve cannot be closed well.<br />
• The fuel injector is damaged.<br />
When the smoke color of the engine exhaust gas is abnormal, firstly consider whether it is caused by<br />
improper operation or lack of maintenance.<br />
Check the possible causes for the abnormal smoke color of engine exhaust gas one by one as per procedure<br />
below, and check in an order from easy to complicated, in order to effectively save the diagnosis time. Any<br />
cause clearly unlikely to occur through analysis may be omitted directly. This diagnosis procedure is for<br />
reference only.<br />
• Exhaust gas with blue smoke fault diagnosis and troubleshooting<br />
Check whether the exhaust gas with blue smoke<br />
is caused by the wear of piston and cylinder liner,<br />
the bonding of piston ring, the low elasticity or the<br />
piston ring gap alignment<br />
Repair carefully, and replace the worn<br />
parts if necessary<br />
Check whether the conduits of the intake and<br />
exhaust pipes are worn<br />
Replace the worn parts and grind the<br />
air valve<br />
Check whether the oil level in the oil pan is too<br />
Exhaust the excessive oil<br />
Check whether the piston ring is stuck or<br />
excessively worn, and whether the elasticity is<br />
Disassemble and check the piston<br />
ring, replace if necessary<br />
low<br />
Whether the long time low loading operation and<br />
the rather large clearance between the piston<br />
and cylinder liner make the oil enter the<br />
combustor<br />
Properly increase the loading or<br />
disassemble, check and repair<br />
15B-32<br />
• Diagnosis and troubleshooting of exhaust gas with white smoke.<br />
Check whether the fuel supply of the fuel<br />
injection pump is too much<br />
Adjust the fuel supply amount of the<br />
Check whether atomization and pressure of<br />
fuel injector is normal.<br />
Check and adjust pressure of the<br />
fuel injector, and replace the fuel<br />
injector when necessary.<br />
Check whether fuel supply of fuel injection<br />
pump is too late.<br />
Adjust fuel supply advance angle.<br />
Service cylinder liner, piston, piston<br />
Check whether the compressing pressure of<br />
the cylinder is too low<br />
ring , grind the air valve, and<br />
replace the worn parts when<br />
5 Check whether there is water in the diesel<br />
Replace diesel, and replace fuel<br />
Whether there is combustion in few cylinders<br />
immediately when the diesel engine starts<br />
(Especially in winter).<br />
above steps, find out the fault<br />
position and remove timely<br />
Properly increase the rotation speed<br />
and the load, and run it for more<br />
time.<br />
15B-33<br />
• Diagnosis and troubleshooting of exhaust gas with black smoke<br />
Make sure whether it is caused by overload work<br />
of the diesel engine<br />
Decrease the load.<br />
Check and adjust the fuel injector<br />
Check whether the fuel injector atomization is<br />
bad or leaks oil.<br />
pressure and replace the fuel<br />
Check whether the fuel supply of the oil pump is<br />
Yes Adjust the fuel supply advance angle.<br />
Clean the air filter and intake pipe and<br />
Check whether the intake pipe or air filter is<br />
blocked.<br />
replace the filter element when<br />
Adjust the amount of fuel supply, and<br />
Check whether the amount of fuel supply is too<br />
much.<br />
check the fuel injection pump when<br />
Yes Go to Step 7<br />
Check whether the fuel supply amount of each<br />
cylinder is equal.<br />
Adjust the amount of fuel supply in the<br />
cylinders of each injection pump and<br />
make them equal.<br />
Check whether the valve clearance is correct,<br />
and whether the valve is not sealed well and<br />
caused the air leakage of the exhaust valve<br />
Adjust the valve clearance and check<br />
the sealing cone.<br />
Check whether fuel supply advance angle is too<br />
small and whether fuel injection is too late which<br />
can makes few fuel combusted in the exhaust<br />
Yes Adjust the static fuel supply advance<br />
15B-34<br />
Check whether the cylinder liner and piston ring<br />
are seriously worn<br />
Replace the piston ring and the<br />
cylinder liner<br />
Unplug the hose between the<br />
solenoid valve and EGR valve at the<br />
Check whether the solenoid valve in ERG<br />
system is broken.<br />
ERG valve end, and if the pheromone<br />
of smoke disappears, it means the<br />
solenoid valve is broken, then replace<br />
new part<br />
11 Check whether ERG valve is not closed well.<br />
Disassemble the ERG valve and<br />
clean the carbon deposition<br />
12 Check whether the fuel injector is broken.<br />
To decide which fuel injector goes<br />
wrong using the cylinder fuel cut<br />
method, and the details are as<br />
follows.<br />
15B-35<br />
9. Fault of the fuel injection pump<br />
The fuel injection pump is the main part for the fuel supply to engine, so the problems in the fuel pump can<br />
influence the normal working of the engine directly. The faults in engine resulting from the problems of the fuel<br />
injection pump are as follows: the engine cannot get started, improper engine idling, runaway in engine and<br />
knocking of the engine. The driver should take these seriously, and the injection pump is precise unit and<br />
non-professionals cannot disassemble and adjust it.<br />
(a). The injection pump does not supply oil.<br />
• The delivery valve is worn or is lined with dirt and stains<br />
• The delivery valve spring or plunger spring is deformed or broken off.<br />
• The adjustment spring is dropped.<br />
• The adjustment arm and the shifter fork are struck.<br />
• The mandril of the delivery pump is struck.<br />
(b). The fuel injection pump does not stop supplying fueland causes runway in engine”(The engine<br />
rotation speed cannot be reduced or is not controlled by the accelerator pedal)<br />
• The oil shifting yoke is blocked.<br />
• The adjustment arm is dropped.<br />
• The shaft sleeve of governor is burned because it is not lubricated well.<br />
• The draw bar stroke is not enough.<br />
• The fly hammer components are loose.<br />
• The draw bar spring is dropped.<br />
(c). The speed governing rate is too high.<br />
• The speed governing torsional spring is deformed or worn or the stiffness is too large.<br />
• The corrector plays a part too early.<br />
(d). The fuel supply is not stable.<br />
• There is air or water in the fuel<br />
• The fuel delivery pump is broken.<br />
• The plunger spring is fractured.<br />
(e). Engine hunting<br />
• Frictional resistance in the governor is too large.<br />
• The axial clearance in camshaft is too large.<br />
• The lubricating oil is too much.<br />
(f). The rated oil amount is not enough.<br />
• The plunger and barrel assembly or the delivery valve is worn.<br />
• The corrector is adjusted improperly.<br />
• The high speed limit is incorrect.<br />
15B-36<br />
The fuel supply amount of each cylinder is not equal suddenly.<br />
• The adjustment arm is loose.<br />
• There is dirt and stains in the delivery valve and fuel nozzle.<br />
Low speed and unstability<br />
• Idle speed adjustment screw is not adjusted properly.<br />
• The low speed oil amount is not equal.<br />
15B-37<br />
(i). Fault diagnosis and troubleshooting<br />
Check the reason causing the fault of the fuel injection pump one by one according to the following steps.<br />
Check in an order from easy to complicated, in order to effectively save the diagnosis time. Any cause clearly<br />
• Fuel njection pump not pumping oil fault diagnosis and troubleshooting.<br />
Check whether the delivery valve is worn or<br />
lined with dirt and stains<br />
Replace the delivery valve or clean it.<br />
Check whether the delivery valve spring or<br />
the plunger spring is deformed or broken off.<br />
Replace the damaged components.<br />
Check whether the adjustment spring is<br />
dropped.<br />
Replace and compress the adjustment<br />
arm tightly.<br />
Check whether the adjustment arm and the<br />
shifter fork is struck<br />
Replace or repair.<br />
Check whether the mandril of the delivery<br />
pump is struck.<br />
Check carefully according to the above<br />
steps, find out the fault position and<br />
remove timely<br />
·<br />
15B-38<br />
• The diagnosis and troubleshooting of the “runway in engine”caused by continuous fuel supply of the fuel<br />
injection pump<br />
Check whether the adjustment arm or<br />
Check whether the adjustment arm is<br />
dropped. .<br />
Check whether the governor shaft<br />
sleeve is burned resulted from the<br />
improper lubrication.<br />
Check whether the draw bar stroke<br />
is too small.<br />
Check whether the fly hammer<br />
components are loose.<br />
Yes Replace or repair<br />
Replace and compress the adjustment arm<br />
tightly.<br />
Yes Adjust the draw bar stroke<br />
Yes Fasten the loose components.<br />
Check whether the draw bar circlip is<br />
Install the circlip and readjust<br />
• The diagnosis and troubleshooting of the too high speed governing rate<br />
Check whether the speed governing<br />
torsional spring is deformed or worn<br />
or the stiffness is too large.<br />
Replace the speed governing torsional spring.<br />
Check whether the oil pump corrector<br />
works too early.<br />
Readjust the corrector.<br />
15B-39<br />
• Unstable fuel supply amount diagnosis and troubleshooting.<br />
Check whether there is air or water in<br />
the fuel tank.<br />
Check whether the fuel delivery<br />
pump is damaged.<br />
Yes Bleed the air or water.<br />
Yes Replace or repair the fuel delivery pump.<br />
Check whether plunger spring is<br />
damaged or fatigue.<br />
Replace the plunger spring and check the fuel<br />
injection pump.<br />
• The diagnosis and troubleshooting of engine hunting<br />
Check whether the frictional<br />
resistance in the governor is high.<br />
Yes Repair and remove the fault.<br />
Check whether the axial clearance in<br />
camshaft is too large.<br />
Yes Readjust the axial clearance<br />
Yes Replace the speed governing torsional spring<br />
Fasten the loose components to the specified<br />
standard.<br />
Check whether the lubricating oil is<br />
too much.<br />
Add the lubricating oil according to the standard.<br />
15B-40<br />
Check whether the plunger elements<br />
or the delivery valve is worn<br />
Check whether the corrector is<br />
adjusted improperly.<br />
Replace the plunger elements or whether the<br />
delivery valve is worn<br />
Yes Readjust the corrector<br />
Check whether the high speed limit is<br />
Readjust the high speed limit screw.<br />
loose.<br />
Check whether the plunger spring is<br />
fractured.<br />
Yes Anew replace and compress it tightly.<br />
Check whether the delivery valve is<br />
worn or is lined with dirt and stains.<br />
Check whether is the position of idle<br />
speed fixing bolt is adjusted<br />
incorrectly.<br />
Renew adjust the idle speed fixing screw.<br />
fuel injection pump at a low speed is<br />
wrong<br />
Check the fuel injection pump and adjust the<br />
amount of fuel supply at a low speed.<br />
15B-41<br />
10. Coolant temperature in the cooling system of diesel engine is abnormal ,there is short of<br />
coolant and there is noise.<br />
Diesel engine overheating<br />
• The coolant level is too low (lack of liquid)<br />
• The fan belt is loose or fractured.<br />
• The thermostat valve cannot be opened.<br />
• The water pump has faults.<br />
• Fuel supply timing is not correct.<br />
• The core of radiator is blocked.<br />
Diesel engine supercooling<br />
• The thermostat valve cannot be closed completely.<br />
• The coolant temperature gauge is out of order.<br />
Frequent lack of water.<br />
• The radiator leaks.<br />
• The hose connector of radiator is loose or the hose is damaged.<br />
• The water pump leaks.<br />
• The hose connector of heater is loose or the hose is damaged.<br />
• When meet the engine overheating, you should not stop the diesel engine from working<br />
immediately or add coolant suddenly. You should decrease the accelerator and make it operate<br />
with no load. Check after flameout when the coolant temperature in the cooling system falls.<br />
• When the diesel engine is still hot, do not take down the filler cover in case of scald. Pay special<br />
attention to safety when adding the coolant.<br />
• If the overheat reason cannot be found and removed, you should contact with the service station<br />
or the service plant, or it will lead to damage of the parts.<br />
15B-42<br />
Check whether the coolant level is too<br />
low (lack of liquid)<br />
Replenish the coolant and check whether there<br />
is leakage. Repair according to the demand.<br />
Check whether the fan belt is loose or<br />
Adjust or replace the fan belt.<br />
Check whether the thermostat valve<br />
can be opened.<br />
Replace the thermostat assembly<br />
Check whether there is fault of the<br />
water pump<br />
Replace the water pump assembly.<br />
Check whether the fuel supply timing<br />
is correct.<br />
Adjust correctly the fuel supply timing.<br />
Check whether the core of radiator is<br />
Clean the radiator.<br />
can be closed completely<br />
Yes Go to Step 8<br />
Replace the thermostat.<br />
Check whether the coolant<br />
temperature gauge is out of order.<br />
Measure the coolant temperature, and replace<br />
the coolant temperature gauge.<br />
Check whether there is leakage of<br />
radiator<br />
Repair or replace the radiator<br />
Check whether the hose connector of<br />
Fastening the connectors or replace the hose.<br />
radiator is loose or the hose is<br />
11 Check whether there is leakage of Yes Replace the water pump assembly.<br />
15B-43<br />
water pump. No Go to Step 12<br />
Fastening or replace the hose.<br />
heater is loose or the hose is<br />
15B-44<br />
11. Fuel consumption of lubricating system of diesel engine is large with low pressure.<br />
Consumption of oil is too large.<br />
• Use the oil without conforming to requirements.<br />
• Gasket and oil seal are invalid, causing oil leakage.<br />
• Piston ring or ring slot is damaged.<br />
• Piston ring is clamped in stagnation.<br />
• Oil seal of valve guide pipe, valve guide pipe or valve stem are damaged.<br />
• Cylinder is worn.<br />
The pressure of oil is too low.<br />
• Safety valve is clamped in stagnation.<br />
• Screen filter of oil pump is blocked.<br />
• Driving gear and driven gear of oil pump are worn.<br />
• Oil pipe is cracked or broken or connectors are loosing.<br />
• Faults of oil pump.<br />
• Main bush or connecting rod bearing bush is worn excessively.<br />
• Oil pressure gauge is damaged.<br />
Oil cannot reach valve system.<br />
• Oil hole between cylinder block and cylinder head is blocked.<br />
• Oil hole on rockshaft is blocked.<br />
• Oil hole on the support of rockshaft is blocked.<br />
• Oil hole on rocker is blocked.<br />
If the oil pressure is too lower for lubricating system, diesel engine cannot be operated. In such<br />
situation, stop vehicle at once for inspection and Disassembly of faults.<br />
15B-45<br />
Check whether oil without<br />
conforming to requirement is used.<br />
Replace the oil of specified brand<br />
Check whether gasket and oil seal<br />
are invalid and whether there is oil<br />
Replace gasket and oil seal<br />
Check whether piston ring or ring<br />
slot is worn.<br />
Replace piston ring or piston<br />
Check whether piston ring is<br />
clamped in stagnation<br />
Check whether oil seal of valve<br />
guide pipe, valve guide pipe or<br />
valve stem are worn.<br />
Replace oil seal, valve or valve guide pipe<br />
6 Check whether cylinder is worn.<br />
Repair cylinder bore or replace cylinder liner<br />
Check whether safety valve is<br />
clamped in stagnation.<br />
Yes Replace safety valve<br />
Check whether screen filter of oil<br />
pump is blocked.<br />
Yes Clean or replace screen filter.<br />
Check whether driving gear and<br />
driven gear of oil pump are worn.<br />
Replace oil pump assembly<br />
Check whether oil pipe is cracked or<br />
broken or connectors are loosing.<br />
Repair or replace<br />
15B-46<br />
Check whether there are faults for<br />
oil pump<br />
Check whether main bush or<br />
connecting rod bearing bush is worn<br />
excessively.<br />
Check whether oil pressure gauge<br />
is damaged.<br />
Check oil hole on cylinder block and<br />
cylinder head is blocked.<br />
Check whether oil hole on rockshaft<br />
is blocked.<br />
Check whether oil hole on the<br />
support of rockshaft is blocked.<br />
Yes Replace oil pump assembly<br />
Replace main bush or connecting rod bearing<br />
bush<br />
Yes Repair or replace the oil pressure gauge.<br />
Yes Clean or repair.<br />
Clean or repair.<br />
Check whether oil hole of rocker is<br />
find out the fault position and remove faults in<br />
time<br />
15B-47<br />
12. Faults of supercharging system of diesel engine.<br />
(a). Inadequate power.<br />
• Impurities in oil are accumulated at the seal of turbine.<br />
• Oil temperature is too high and fuel supply is not adequate. Floating bearing is damaged by<br />
burning.<br />
• Oil return pipe of turbocharger is blocked or deformed to cause oil leakage from turbine and shaft<br />
end of compressor.<br />
• Gasket of turbocharger is damaged or invalid.<br />
• Rotor of turbine shaft loses balance.<br />
• Turbine blade and compressor blade are in friction and damaged.<br />
• Air filter is blocked (too dirty).<br />
• Air guide pipe of supercharging compensator is broken.<br />
• There is too much dirt for intake pipe and exhaust pipe or connecting parts have air leakage.<br />
• Turbocharger is in poor operation or damaged.<br />
(b). Fuel injection pump does not supply fuel or provide inadequate fuel.<br />
• The connection of delivery valve is poor or delivery valve is stuck.<br />
• Mebrane of supercharging compensator is damaged.<br />
(c). Fuel consumption is too large.<br />
• There is too much dirt on intake pipe and exhaust pipe or connecting parts have air leakage.<br />
• The property of turbocharger is poor.<br />
• Fuel injector is in poor operation.<br />
• Piston ring is worn.<br />
(d). Consumption of oil is too large.<br />
• Seal ring of turbocharger is worn or damaged.<br />
• There is oil leakage at impeller end of compressor.<br />
• Screws at the connecting place of intake pipe and oil return pipe are loosing and gasket is<br />
• Oil is in poor quality.<br />
(e). Abnormal sound<br />
• There is too much dirt at air channel for turbine and turbine is obviously reduced.<br />
• There is too much dirt at compressor and air channel is reduced obviously.<br />
• The wear of floating bearing is too large and friction is generated among turbine, impeller of<br />
compressor and shell.<br />
(f). Friction is generated among turbine, impeller of compressor and shell to produce vibration.<br />
• Entrance of foreign matter<br />
• The wear of floating bearing is too large.<br />
• Dynamic balance of turbine shaft is weak.<br />
15B-48<br />
• In the process to remove faults and disassemble and install diesel engine, prevent the entrance of<br />
foreign matter to intake and exhaust system strictly, as the rotor of turbocharger is rotating at a<br />
extremely high speed and the clearance between rotor and shell is very small. The entrance of no<br />
matter what kind of foreign matter to impeller will influence the operation of rotor and damage<br />
blade. If the blade is damaged, turbocharger will produce abnormal vibration and noise. At this<br />
moment, stop the vehicle for service of turbocharger.<br />
• If there is oil leakage for turbocharger, but the impeller of spindle does not touch inner shell and<br />
rotates flexibly, do not replace turbocharger casually, but to remove the fault of oil leakage for<br />
continuing use.<br />
15B-49<br />
Check whether impurities in oil are accumulated<br />
at the seal of turbine.<br />
Replace oil and repair turbocharger.<br />
Check whether the oil temperature is too high<br />
and fuel supply is adequate and whether floating<br />
bearing is damaged by burning.<br />
Check fuel supply system and repair<br />
Check whether oil return pipe of turbocharger is<br />
blocked or deformed to cause oil leakage from<br />
turbine and shaft end of compressor.<br />
Repair and replace oil return pipe.<br />
Check whether the seal ring of turbocharger is<br />
damaged or invalid.<br />
Replace seal ring.<br />
Check whether rotor of turbine shaft loses<br />
Repair and replace the rotor of turbine<br />
shaft.<br />
Check whether the turbine blade and<br />
compressor blade are in friction or damaged.<br />
7 Check whether the air filter is blocked (too dirty)<br />
Repair or replace turbine blade and<br />
compressor blade.<br />
Maintain air filter and replace filter<br />
element.<br />
Check whether the air guide pipe of<br />
supercharging compensator is broken.<br />
Service or replace air guide pipe.<br />
Check whether there is too much dirt on intake<br />
pipe and exhaust pipe or connecting parts have<br />
air leakage.<br />
Clean, service or replace intake pipe<br />
and exhaust pipe.<br />
15B-50<br />
Check whether the operation of turbocharger is<br />
good or whether it is damaged.<br />
Check whether the connection of delivery valve<br />
is poor or delivery valve is stuck.<br />
Check whether the mebrane of supercharging<br />
compensator is damaged.<br />
Check whether the turbocharger is in good<br />
operation.<br />
Yes Service or replace turbocharger.<br />
Yes Repair or replace parts<br />
Yes Repair and replace mebrane<br />
Yes Clean, adjust or replace turbocharger.<br />
14 Check whether fuel injector is in good operation.<br />
Repair or replace the fuel injector or<br />
nozzle.<br />
15 Check whether piston ring is damaged.<br />
Check or replace piston ring.<br />
worn or damaged.<br />
Yes Replace seal ring.<br />
Check whether there is oil leakage for the<br />
impeller of compressor.<br />
Yes Service<br />
Check whether the screws at the connecting<br />
place of intake pipe and oil return pipe are<br />
loosing and whether gasket is damaged.<br />
Yes Service and replace gasket.<br />
19 Whether the quality of oil is weak.<br />
Replace oil according to<br />
requirements.<br />
Whether there is too much dirt at the air channel<br />
and turbine is becoming smaller obviously.<br />
Yes Clean and replace<br />
15B-51<br />
Check whether there is too much dirt at<br />
compressor and air channel is becoming smaller<br />
obviously.<br />
Whether the wear of floating bearing is too large<br />
and whether friction is generated among turbine,<br />
impeller of compressor and shell.<br />
Check whether there is entrance of foreign<br />
matter.<br />
Yes Replace the floating bearing<br />
Service or replace turbine shaft.<br />
Check whether the dynamic balance of turbine is<br />
weak.<br />
and remove faults in time<br />
15B-52<br />
13. The capacity of battery is inadequate with difficult starting and too large self discharge.<br />
The capacity of battery is inadequate and it is difficult to start diesel engine.<br />
• The level of electrolyte is too low.<br />
• Short circuit between polar plates<br />
• Vulcanization of polar plate<br />
• Connectors of wire are in poor contact and there is too much oxide on polar column with<br />
inadequate charging.<br />
Self discharge of battery is too large.<br />
• There are impurities in electrolyte.<br />
• There is short circuit at external wire of battery.<br />
• There is electrolyte spilling out at the surface of battery to cause short circuit of passive and<br />
negative polar column.<br />
• Place metal tools or rod between positive polar column and negative polar column, causing<br />
serious short circuit.<br />
• Active substance of polar plate is at loss. Too much accumulation makes polar plate in short<br />
circuit. The damage of clapboard causes short circuit form polar plate. The warping of polar plate<br />
causes short circuit for positive and negative plates.<br />
• It is easy for the discharged gas of battery to be burnt by sparks. In service and maintenance of<br />
battery, avoid striking fire, open fire and smoking. In repair, do not let electrolyte of battery contact<br />
skin and clothes and wear goggles.<br />
• Do not make the two connecting poles of battery become short circuit. Otherwise, the battery will<br />
be heated rapidly and may cause explosion.<br />
• In order to prevent short circuit, dismantle the bond strap of battery firstly in removing and<br />
installing electrical equipment. But in changing bulb, it is only necessary to cut off related<br />
switches.<br />
• In removing battery, firstly disassemble bond strap and then disassemble positive pole line. Next,<br />
disassembly battery baffle and take battery out from the support. The order to install battery is<br />
opposite to the order of disassembly.<br />
15B-53<br />
According to requirements, add the distilled<br />
Check whether the level of electrolyte<br />
is too low.<br />
water or dilute sulfuric acid solution with its<br />
density of 1.1.<br />
Check whether there is short circuit<br />
between polar plates.<br />
Remove sediment and replace electrolyte.<br />
Check whether vulcanization occurs to<br />
polar plates.<br />
Carry out charging and discharging repeatedly to<br />
remove vulcanization.<br />
Check whether line connectors are in<br />
Fasten connection and remove oxide.<br />
good contact, there is too much oxide<br />
on pole column and whether the<br />
charging is adequate.<br />
Go to Step 5<br />
Check whether there are impurities in<br />
electrolyte.<br />
According to regulations, inject electrolyte made<br />
of chemical pure sulfuric acid and distilled water.<br />
Check whether there is short circuit for<br />
external wire of battery.<br />
Check the part of short circuit and remove faults.<br />
Use alkaline water or warm water to clean pole<br />
Check whether there is electrolyte<br />
spilling on the surface of battery to<br />
cause short circuit for negative and<br />
positive pole column.<br />
column head of battery surface and keep the<br />
outside clean. (water cannot be leaked into<br />
15B-54<br />
Whether serious short circuit is caused<br />
by placing metal tool or rods between<br />
positive pole column and negative pole<br />
column.<br />
Do not place metal tools or rods on the surface of<br />
battery.<br />
Whether the active substance of polar<br />
plate is at loss and too much<br />
accumulation causes short circuit of<br />
polar plate. Damage of clapboard also<br />
causes short circuit of polar plate.<br />
Warping of polar plate causes short<br />
circuit for positive pole plate and<br />
negative pole plate.<br />
Repair or replace the battery<br />
15B-55<br />
14. Faults of starter<br />
Starter is used to transfer the electric energy of battery to mechanical energy and generate electromagnet to<br />
drive engine to operate at regulatory rotation speed and make engine start and operate. The fault of starter is<br />
usually reflected as follows: turn on ignition switch, but starter does not operate and the starting of starter is<br />
powerless to make starter in empty operation. In starting, there is abnormal sound for driving gear and<br />
approach action of flywheel ring gear.<br />
(a). Turn of ignition switch, but starter does not operate.<br />
• The wire is in poor contact.<br />
• Battery is lack of electricity seriously or there is short circuit inside.<br />
• There is short circuit inside starter.<br />
• Bearing or bushing of starter is worn.<br />
• The line is broken for control circuit of starting switch.<br />
• Carbon brush is in poor contact with commutator.<br />
(b). Starter is powerless.<br />
• The charging of battery is not adequate.<br />
• There is short circuit for the lead of starter.<br />
• Battery terminal is corrosive or wiring clip is loosing.<br />
• There is short circuit for field winding of starter or armature winding.<br />
• The assembly of starter is too tight or there is sweeping phenomenon.<br />
• The resistance of engine is too large.<br />
• Capacity of battery is not adequate.<br />
• There is burning damage or oily dirt on the surface of commutator.<br />
• Carbon brush is worn excessively or elasticity of carbon brush is not adequate, causing its poor<br />
contact with commutator.<br />
• Main contact of electromagnetic switch is ablated, causing poor contact.<br />
• Bearing wear is serious and armature is in contact with shell.<br />
(c). Idle operation of starter.<br />
• One-way clutch is damaged.<br />
• Check whether the electromagnetic switch of starter is damaged.<br />
(d). There is abnormal sound for driving gear and approach action of flywheel ring gear.<br />
• Driving gear or flywheel ring gear is worn seriously.<br />
• Electromagnetic switch of starter is damaged.<br />
(e). Diesel engine is started, but starter is still in idle operation and sound sharp noise.<br />
• Inner copper contact disc of starter relay is in adhesion with two contacts.<br />
• Armature shaft of starter is broken or bended.<br />
• Sgraffito of gear surface is stuck.<br />
15B-56<br />
Do not exceed 15s in starting starter for operation and the time interval of two starting shall be more<br />
than 2 minutes to avoid too hot starter damaging internal parts. If it can not be started for three times<br />
continuously, check engine, fuel system, electromagnetic switch, starter, battery and wiring terminal<br />
and re-start it after removing faults. Loose the ignition switch right away once engine is started for<br />
operation and back the self meshing position of engine gear and stop operation.<br />
Fault diagnosis and troubleshooting<br />
• Diagnosis and removal for the non-operation of starter<br />
Check whether there is poor contact<br />
in connecting line.<br />
Check whether battery is lack of<br />
electricity serious or open circuit<br />
inside.<br />
Check whether the internal line of<br />
starter is broken.<br />
Whether there is short circuit for<br />
internal line of starter.<br />
Fasten the connectors of line and replace<br />
connectors if necessary.<br />
Charge the battery and replace battery if<br />
Repair of replace starter<br />
Repair or replace starter.<br />
5 Check whether fuse is broken.<br />
Check whether the bearing or<br />
bushing of starter is seriously worn.<br />
Yes Replace the fuse.<br />
Yes Repair or replace starter.<br />
Check whether the line of starting<br />
switch and control circuit is broken.<br />
Check whether the circuit is in reliable<br />
connection.<br />
Check whether carbon brush is in<br />
good contact with commutator.<br />
Adjust the spring pressure of carbon brush and<br />
clean commutator.<br />
15B-57<br />
• Diagnosis and Disassembly of powerlessness of starter<br />
Check whether battery charging is<br />
adequate.<br />
Yes Charge the battery<br />
Check whether the connectors of lead of<br />
started is in good contact or short circuit.<br />
them if necessary.<br />
Check whether the wiring terminal of<br />
battery is corrosive or wiring clip is loosing.<br />
Remove the corrosive and fasten the fixing<br />
bolt of wiring clamp.<br />
field winding or armature winding of starter.<br />
Check whether the assembly of starter is<br />
too tight or swept.<br />
Repair starter and replace the worn parts if<br />
Check whether the resistance of engine is<br />
too high.<br />
Yes Remove the resistance causes of engine.<br />
Check whether the capacity of battery is<br />
Check whether there is burning damage or<br />
oily dirt on the surface of commutator.<br />
Charge the battery according to<br />
regulations.<br />
Polish the surface of commutator or<br />
remove the oily dirt.<br />
Whether the wear of carbon brush is too<br />
much or the spring elasticity of carbon<br />
brush is inadequate, causing its poor<br />
Replace carbon brush or adjust the spring<br />
pressure of carbon brush.<br />
Check whether the main contact of<br />
electromagnetic switch is ablated to poor<br />
contact.<br />
Yes Use “0” non-metal sand paper for polishing.<br />
15B-58<br />
Check whether the bearing is worn<br />
seriously and whether the armature<br />
touches the shell.<br />
Replace the bearing<br />
remove faults in time<br />
• Diagnosis and Disassembly of idle operation of starter<br />
1 Check whether one-way clutch slips.<br />
Replace one-way clutch<br />
Replace electromagnetic switch of starter.<br />
Check whether electromagnetic switch of<br />
starter is damaged.<br />
• Diagnosis and Disassembly of abnormal sound for driving gear and approach action of flywheel ring gear<br />
Check whether driving gear or flywheel<br />
ring gear is worn seriously.<br />
Replace the worn parts<br />
Replace the electromagnetic switch of<br />
starter.<br />
15B-59<br />
• Start the diesel engine and starter continues to operate, then, carry out diagnosis and Disassembly of<br />
sharp noise.<br />
Check whether copper contact disc in<br />
starter relay is in adhesion with two<br />
contacts.<br />
Cut off power at once, check the line and<br />
repair contacts.<br />
Check whether the armature shaft of<br />
starter is broken or bended.<br />
Cut off power at once and replace starter.<br />
Cut off power at once and trim gear surface<br />
Check whether sgraffito of gear surface<br />
is stuck.<br />
15B-60<br />
15. Faults of generator<br />
(a). Generator does not generate power.<br />
• The line is in poor contact, wrong connector or broken.<br />
• The line of stator and rotor is in short circuit or broken.<br />
• The rectifying valve is damaged, causing short circuit or open circuit.<br />
• Electric brush is in poor contact, there is oily dirt for slip ring and the belt of generator is too<br />
loosing.<br />
• Regulator is damaged.<br />
(b). Charging of generator is inadequate.<br />
• The transmission belt is loose.<br />
• Carbon brush is in poor contact and there is oily dirt for slip ring.<br />
• There is too little electrolyte for battery of the vulcanization of polar plate is too serious or it is too<br />
aged.<br />
(c). Charging current is not stable.<br />
• Short circuit is to occur to rotor coil and stator coil.<br />
• Electric brush is in poor contact, spring pressure of electric brush is small and line is in poor<br />
(d). Generator produces abnormal sound.<br />
• The installation of generator is not proper and bearing is damaged.<br />
• Rectifying valve and rotor coil are in short circuit.<br />
15B-61<br />
• Diagnosis and Disassembly of the faults for no power generation of generator<br />
Check whether line is in poor contact or wrong<br />
Check and repair<br />
Check whether rotor coil and stator coil is in short<br />
Service or replace<br />
Check whether rectifying valve is damaged,<br />
causing short circuit or open circuit.<br />
Repair or replace as a unit.<br />
Check whether electric brush is in poor contact,<br />
there is oily direct for slip ring and belt of<br />
generator is too loosing.<br />
Repair or clear or adjust the tension of<br />
belt.<br />
Repair or replace regulator.<br />
5 Check whether the regulator is damaged.<br />
• Diagnosis and removal for the faults of inadequate charging of generator<br />
1 Check whether transmission belt is loose.<br />
Adjust the tension rate of belt.<br />
Check whether carbon brush is in poor contact or<br />
there is oily dirt for slip ring.<br />
Adjust and clean<br />
3 Check whether regulator is damaged.<br />
Replace regulator<br />
15B-62<br />
Supplement electrolyte to regulatory<br />
Check whether there is too little electrolyte for<br />
battery of vulcanization of polar plate is serious<br />
height. For the battery without<br />
recoverable vulcanization of polar<br />
plate, replace it.<br />
or it is too aged.<br />
• Diagnosis and removal for unstable charging current<br />
Check whether short circuit occurs to rotor coil<br />
and stator coil.<br />
Check whether electric brush is in poor contact<br />
and the spring pressure of electric brush is too<br />
small and line is in poor contact<br />
position and remove faults in time<br />
Check whether the installation of generator is<br />
proper and bearing is damaged.<br />
Check whether rectifying valve and stator<br />
coil are in short circuit.<br />
ENGINE MECHANICAL PART-ENGINE MAINTENANCE<br />
15B-63<br />
ENGINE MAINTENANCE<br />
1. General Precautions<br />
During the operation, perform the adjustments and maintenances in accordance with the<br />
maintenance methods and various regulations specified in the manual.<br />
The new engine or the engine after being serviced shall not be allowed to run with full load at high<br />
speed. The engine shall run for 45h from at a low speed with no-load to a high speed with full load,<br />
and then the engine shall run with normal load.<br />
The fuel which is used by the engine shall be precipitated for a week or be filtered by a silk before it is<br />
used.<br />
The normal coolant temperature shall be 80 ℃ -90 ℃ and the normal oil pressure shall be<br />
280-400kPa.<br />
During the process of running, if a abnormal phenomenon is found out, stop the car and check it.<br />
2. Precautions for Running and stop of Engine<br />
Gradually and equably perform the engine’s load and rotation speed and car’s running speed<br />
increasing and decreasing. Except in special circumstances, do not suddenly change the load and<br />
During the process of engine’s running and the car’s running, pay attention to whether the registration<br />
of each meter is normal or the running conditions of engine (running sound and the discharge smoke<br />
color). If the registration is abnormal, please take measures or stop running.<br />
The running coolant temperature shall be about 358K (85℃) and the oil pressure is 196~490kPa<br />
under normal circumstances.<br />
The car cannot adopt the operational approach of “accelerate-shut down-neutral position’s<br />
slide-ignite by putting the clutch into gear”.<br />
The reasons are as follows:<br />
• The engine suddenly shuts down with high speed and high temperature, the oil pump and water<br />
pump will stop working, which can not make the lubricating oil and coolant carry off the heat of the<br />
• For the ignition by putting the clutch into gear, if the speed is about 40km per hour, it indicates that<br />
the engine starts at a rotation speed of 1300r/min with large impact force, which is harmful to the<br />
Before stopping the car, the engine shall decrease the load and speed. After the car stops, the engine<br />
will run for 3-5min and then stops. The aim is to gradually and equably cool down the engine to avoid<br />
overheating the engine and damaging some parts.<br />
3. Precautions for Generator<br />
The center of the generator pulley shall be aligned with that of the drive wheel and the tension of the<br />
belt shall not be too tight or too loose, or it will impair the reliability and service life of the generator.<br />
The generator shall be in parallel connection with the battery and shall be matched with appropriate<br />
model of regulator, in which the wiring shall be secure and reliable.<br />
Both the generator and the battery shall be negative grounded (earthed), or it will burn out the<br />
generator and the regulator.<br />
15B-64<br />
Use a multi-meter, instead of using the test method of ignition to ground, to check whether the<br />
generator is generating power.<br />
Frequently remove the dust and oil sludge from the generator and maintain the good wiring.<br />
Maintain the generator at interval of 1,000h. Check the electric brush for presence of wear, clean the<br />
bearings and add an appropriate amount of lubricating oil (The amount added shall be 2/3 of the<br />
bearing chamber). No maintenance is required for the double sealed bearing.<br />
During the running of the generator, it’s absolutely prohibited to disconnect the connecting wires, in<br />
order to prevent short-circuit from burning out the silicone rectifying unit<br />
When the silicone rectifying unit is connected with the stator coil, it’s absolutely prohibited to check<br />
the insulation status of the generator with mega-meter or 200V AC, or it will lead to puncture of diode<br />
and damage<br />
4. Precautions for vacuum pump<br />
The pressure oil connects with the connector of oil inlet, the vacuum pump connects with the<br />
connector of exhaust gas and the engine body connects with the connector of oil return. Each<br />
connector shall be sealed.<br />
Check whether the pump body and pump base have crack and whether the pump core and generator<br />
spline shaft fit and the inner working face have wear and scratches. If any damage is found out, and<br />
then replace them.<br />
The blade width shall be ≥3mm, which can ensure the exhaust gas property. If any damage is found<br />
out, and then replace them.<br />
If the oil leak is found, find out the place of leaking oil and then maintain and replace it.<br />
Ensure the lubricating oil’s cleanness and proper viscosity during its use. Do not make the engine<br />
work without lubricating oil, or else it can seriously damaging the vacuum pump.<br />
5. Precautions for starter motor<br />
Before the use, check the engine and use the starter motor after it’s determined that the engine can<br />
run normally.<br />
When connecting the starter’s circuit, the copper wire sectional area for connecting electric power<br />
storage shall not be less than 25mm2 , the sectional area for connecting switch wire shall not be less<br />
than 4mm2 and the wire shall be short as much as possible. Before starting, check whether the starter<br />
circuit connection is correct, the connection is tight and whether the battery is fully charged.<br />
After the preparations, press down the electromagnetic switch, the starter’s gear meshes starter’s<br />
flywheel ring gear, and then it begins to run. Under normal circumstances, it can be started once. If it<br />
cannot be started once, after the starter’s armature and gear are completely at a standstill, it can be<br />
started for the second time, or else the starter will fiercely hit against the starter ring gear and the<br />
starter will be damaged.<br />
In cold days, pre-warm the engine, and then use it.<br />
The start time for starter shall not be more than 15s, and the interval between two times of start shall<br />
be more than 2min to avoid overheating the starter.<br />
When the starter cannot normally start for consecutive three times, please eliminate fault and then<br />
start the starter.<br />
When the starter begins to run, please immediately loosen the switch button to make starter gear<br />
return from meshing position and stop running in order to avoid damaging the starter.<br />
Frequently check whether the connection of starter’s fastening pieces are tight, whether the lead<br />
15B-65<br />
connection is tight. And eliminate the pollution, put a little vaseline to avoid corrosion.<br />
(h). Frequently check whether the wire insulation is damaged.<br />
(i). Disassemble dustproof belt at regular intervals to check whether the surface of commutator is bright<br />
and clean and whether the brush has hysteresis phenomenon and the spring pressure is normal.<br />
Clean the dust, and if the brush wears a lot, the surface of commutator singes and other faults are<br />
found out, please immediately disassemble it to make repairs and supply replacements.<br />
(j). The starter motor shall be overhauled once a year. Depending on the actual condition, the overhaul<br />
interval may be shortened or prolonged appropriately.<br />
6. Precautions for turbocharger<br />
(a). The lubrication of floating bearing of turbocharger shall use CF-4 lubricating oil. Clean the oil filter at<br />
regular intervals and replace the lubricating oil.<br />
(b). After starting diesel engine, immediately decrease the accelerator to make the diesel engine run at<br />
low speed. When the oil pressure rises, accelerate “heating of turbine”.<br />
(c). The diesel engine shall not suddenly stop with high load at high speed.<br />
(d). The new diesel engine or the diesel engine after being repaired, replaced diesel engine or the engine<br />
with cleaned turbocharger, replaced oil or with cleaned filter shall screw off the oil inlet connector of<br />
turbocharger and turn off the injection pump before start. Drive the diesel engine by starting engine for<br />
few seconds (less than 10s), screw up the diesel engine when lubricating oil spills from the oil inlet<br />
connector of turbocharger. Fill 60~100ml lubricating oil (oil) in the oil inlet of turbocharger, and then<br />
start the diesel engine.<br />
(e). Frequently check the tightness of intake pipeline and exhaust pipeline to avoid air leakage.<br />
(f). Pay attention whether the turbocharger has abnormal sound during the running of diesel engine.<br />
(g). If the diesel engine’s rotation speed is not stable during the running, turbocharger fiercely shake and<br />
the intake pipe has rumble sound, which means that the turbocharger surges, please clean the air<br />
filter element and intake pipeline.<br />
15B-66<br />
OPERATIONS<br />
1. Fuel, Oil, and Coolant<br />
Fuel<br />
User can select diesel according to local ambient temperature. In summer 0# light diesel oil is be<br />
suitable and in winter -10# light diesel oil is suitable in general area in China. In cold area, -35# and<br />
-20# light diesel can be used.<br />
• When the working temperature for diesel is low, wax material shall be separated out if using<br />
incorrect grade, then the oil line will be blocked. Therefore, the diesel with correct grade shall be<br />
determined according to ambient temperature.<br />
• Do not fill oil in the fuel tank when the diesel engine is running. If the car runs in hot weather, the<br />
fuel tank cannot be fully filled, or else the fuel will spill because of expansion. Once the fuel spills,<br />
clean it immediately.<br />
Oil<br />
Please respectively select lubricating oil with viscosity grades of 5W/50 ( used in the temperature<br />
range of -30℃~+ 40℃) and 10W/30 ( used in the temperature range of -25℃~+40℃), property<br />
grade of CD, CE or higher grade according to local atmospheric temperature. The Great Wall brand,<br />
Uniform brand and Kunlun brand are recommended. Disassemble the filter cap from the cylinder<br />
head cover and then fill oil in the engine. Disassemble the oil outlet bolts from the oil pan and then let<br />
the oil out.<br />
• After the diesel engine is supercharged by air turbine, both mechanical load and thermal load are<br />
greatly raised. The turbocharger which is a precision running component with high speed and<br />
high temperature has strict requirements for the quality of lubricating oil. Therefore, the clean oil<br />
according to required brand cannot be replaced by low grade or poor quality oil to avoid faults<br />
such as scuffing of cylinder bore, bush burning and turbocharger damaged.<br />
• The oil in the diesel engine shall not include impurities and moisture. When changing oil for<br />
technical service, the old and new oil can be mixed to use.<br />
Water coolant<br />
The water which is processed by anti-erosion and anti-corrosion can be taken as coolant in the area<br />
with temperature of more than 0℃. This kind of coolant contains the anti-erosion and restrainable<br />
type of glycol. The anti-corrosion inhibitor adopts sodium nitrite/ sodium benzoate. Anti-freezing<br />
mixed liquor shall be characterized by good cooling property and shall provide anti-corrosion<br />
protection under any ambient temperature. The specification of anti-freezing mixed liquor at least<br />
meets the requirements of BS6580 or MODAL39. When the engine is used under the ambient<br />
temperature of lower than 0℃, avoid the coolant to be frozen to make the relevant parts frost crack.<br />
The engine which adopts closed cycle coolant system can use antifreeze solution with proper<br />
condensation point or fill hot water before start according to ambient temperature. But when it stops,<br />
please immediately turn on the water.<br />
• Anti-freeze solution is poisonous, so the anti-freeze shall be stored in the original container to<br />
avoid contacting people.<br />
15B-67<br />
2. Preparation before start<br />
(a). Check whether each connection for starter is tight and whether the operating handle (accelerator and<br />
shutdown handle and etc.) are flexible.<br />
(b). Rotate the crank a few rotation to check whether the motion parts are flexible without being stopped<br />
phenomenon.<br />
(c). Check whether the oil pan and oil surface of oil pump are in upper limit position in the range of oil<br />
gauge’s scale.<br />
(d). Check whether the water tank is full and whether each water pipe connector leaks.<br />
(e). Check whether the fuel tank is full of diesel, the fuel line is unblocked and whether each oil pipe<br />
connector is sealed or has no leakage.<br />
(f). Check whether the engine accessories’ connection is dependable (fuel injection pump, diesel filter, oil<br />
filter, water pump, fan, generator and generator support, fan belt, starter, water tank and etc. )<br />
(g). Check whether each connector of electrical system is correct, tight and dependable. The battery shall<br />
be sufficient and silicon rectification generator’s negative pole shall be grounded. Pay attention that<br />
the battery wiring’s negative pole shall be grounded.<br />
3. Start diesel engine<br />
Do not start the diesel engine until the preparations before start are fulfilled. Before starting the engine, check<br />
the surrounding area of the diesel engine for the presence of any article obstructing the working of the diesel<br />
engine. Start the engine only after such article is kept away.<br />
(a). Start with normal temperature (higher than -5℃)<br />
• Shift the gearshift lever of the transmission to neutral position. ·<br />
• Put the lock switch on the position “ON”, and then pause for about 2-3 seconds and then check<br />
whether each meter display is normal. Please power up ECU. The engine shall not be directly<br />
stared without electricity.<br />
• When the fault lamp is on, stop the car immediately, and then contact the service station to treat<br />
fault and eliminate the fault code.<br />
• If the diesel engine does not start, the electric switch lock shall return “OFF” position. After the<br />
starter motor stops rotating, start the diesel engine.<br />
• ·After the diesel starts, keep the diesel engine run at idle speed. Check whether the oil pressure is<br />
normal, whether the turbocharger has no abnormal sound and vibration, the oil pressure shall be<br />
less than 0.1MPa. The supercharged and cooling diesel engine shall not run at idle speed for 5<br />
(b). Start with low temperature (lower than -5℃)<br />
• Put the gear lever of transmission in the neutral position and depress the clutch pedal to reduce<br />
starting load.<br />
• Put the lock switch in ON position, pause for 2-3 seconds at least, then check whether each meter<br />
display is normal. Please power up ECU. The engine shall not be directly stared without electricity.<br />
• When the coolant temperature is lower, the preheating indicator on the fascia is usually on, which<br />
indicates that the preheating system is working and the heater plug powers on and is preheated.<br />
After finishing preheating, the preheating indicator is off, then the operator can start diesel engine.<br />
If the operator does not start the diesel engine timely, turn off the switch lock for 20 seconds, and<br />
15B-68<br />
then repeat the above steps to preheat and start again.<br />
• When the heater plug finishes preheating and the preheating indicator is off, depress the clutch<br />
pedal, put the ignition switch in START position to start the diesel engine.<br />
• If the diesel engine does not start smoothly, the electric switch lock shall return OFF position. After<br />
the starter motor stop running, try to start the diesel engine again. When the diesel engine stops to<br />
start again, the interval time shall be more than 60 seconds.<br />
• After the diesel engine successfully starts, put the lock switch on the ON position from START<br />
• When the temperature is lower than -25℃ and there is trouble for start, let the anti-freezing and<br />
anti-corrosion solution out and then preheat the diesel engine with boiled water. Fill higher than<br />
90℃ hot water in radiator, after the water becomes cool then let the water out, fill hot water again<br />
to start and run, and then let hot water out again, finally fill anti-freezing and anti-corrosion solution<br />
again. During the period of preheating, after the diesel engine starts, the coolant’s cycle shall not<br />
pass through radiator because the thermostat valve is closed. Therefore, in order to reduce the<br />
chance of coolant’s freeze in the radiator, adopt hot water and put a radiator blind in front of the<br />
• After the diesel engine starts, keep the diesel engine running at idle speed and check whether the<br />
oil pressure is normal and turbocharger has abnormal sound and vibration. The oil pressure shall<br />
be no less than 0.1Mpa. But the supercharging and cooling diesel engine shall not run at idle<br />
speed for more than 5 minutes. When the temperature is lower than -25℃, after start the diesel<br />
engine, the diesel engine shall run with no load at low and medium speed and preheat for several<br />
minutes to “heat the engine”. In order to raise the coolant temperature as much as possible, do not<br />
turn on the heater switch when heat the engine. When the coolant and lubricating oil temperature<br />
is higher than 50℃ and each system is in normal working condition, turn on the heater switch and<br />
allow the diesel engine works with full load at the maximum rotation speed.<br />
NOTE;<br />
• The time for each start shall not exceed 15 seconds in order to protect the starter motor and<br />
battery. If one start fails, wait for at least 2min before retry. If the engine can't be started by three<br />
consecutive starts, find out and resolve the cause before retry.<br />
• When starting the diesel again, please return the lock in OFF position, else the ECU fault will<br />
happen.<br />
4. Run diesel engine<br />
When the cooling coolant temperature is higher than 50℃, the diesel engine can work with load. The<br />
outlet coolant temperature shall be higher than 80℃ when using rated power.<br />
The increasing and decreasing for engine’s load and rotation speed shall be gradually and uniformly<br />
carried on. Under general circumstance, do not suddenly increase or decrease the load.<br />
During the period of running, please pay much attention whether meter reading is normal, whether<br />
fuel, cooling system and lubrication system have leakage and pay much attention to the discharged<br />
smoke color and running sound. If there is abnormal sound, please stop the car and check it.<br />
15B-69<br />
5. Stop diesel engine running<br />
(a). Before the diesel engine stops running, please decrease load and reduce the rotation speed to idle<br />
speed and the coolant temperature shall be lower than 75℃, and then operate the shutdown handle<br />
to make the diesel engine stop running.<br />
(b). After the engine stops running, screw the ignition switch in neutral position.<br />
(c). When the ambient temperature is lower than 5℃ in winter, then the engine shall stop running after<br />
the coolant temperature is lower than 60℃. Switch on the water drain switch of engine body and<br />
water tank, let the coolant out to avoid frost crack. If the antifreeze solution is used, and then do not let<br />
the water out.<br />
15B-70<br />
MAINTENANCE<br />
1. Regular Maintenance<br />
In order to increasing the diesel engine’s service life, the following procedures shall be adopted for<br />
maintenance during the process of service.<br />
Check whether the oil level in the oil pan is in the position between two scribed lines of dipstick. Fill oil<br />
in the new engine or the engine which stops running for a long time until the oil being at the scribed<br />
line, then make the engine run at a low speed for 5-10 minutes and stop the engine diesel, and then<br />
measure the oil level height with dipstick.<br />
Check the water amount of water tank.<br />
Check the injection pump and oil level of governor, if the oil is not enough, then supplement the oil<br />
until the oil level is at specified position.<br />
Check and eliminate the phenomena of oil leak, water leakage and air leakage.<br />
Check each accessory’s tightness of engine.<br />
Check the tightness of engine’s bracket and coupling.<br />
Keep the engine clean and eliminate the greasy dirt and dust and specially keep the electric<br />
equipment dry and clean.<br />
After the new engine runs in with light load for 45 hours, please timely replace the oil (including the oil<br />
in injection pump and governor) and please clean oil filter element.<br />
Eliminate all abnormal phenomena which are founded out.<br />
2. Maintenance after running for 100 hours<br />
Replace the oil in the oil pan.<br />
Clean or replace the oil filter element.<br />
Clean or replace diesel filter element (or carry on after accumulative total 200 hours)<br />
Check the tightness of bolts of cylinder head.<br />
Check whether the value clearance is in accordance with the regulations. If necessary, please adjust<br />
it.<br />
Check the tension of fan belt. If necessary, please adjust it.<br />
Eliminate the dust on intake pipe and air filter.<br />
Check the situation of fuel injection pressure and fuel injection after accumulative 200 hours. If<br />
necessary, please clean and adjust it.<br />
(i). Check battery voltage. The electrolyte proportion shall be 1.28-1.29 (atmospheric temperature is 15℃)<br />
and shall not lower than 1.27. Check whether the electrolyte liquid level is 10-15mm higher than pole<br />
plate, or else the distilled water shall be supplemented.<br />
Replace coolant according to the water quality’s turbidity. Take out thermostat, reinstall outlet water<br />
pipe and start the engine while changing rotation speed from time to time. Wash the precipitate of<br />
cooling system with coolant’s flow velocity and then stop the engine running, open the water tank and<br />
switch on the water drain switch to let water out. Continuously inject clean water from the water tank<br />
and then start the engine to run at idle speed to make the water flow. Check water quality timely until<br />
the water is clean. Switch off each water drain switch and stop the engine running and then reinstall<br />
the thermostat.<br />
Reassemble the parts and components which are maintained in correct installation position.<br />
15B-71<br />
3. Maintenance after running 500 hours<br />
The maintenance after running 500 hours includes the procedures of maintenance after 100 hours and shall<br />
contain the following procedures too.<br />
(a). Check the fuel injection pressure of fuel injector and observe atomization quality. Clean and adjust it.<br />
(b). Check fuel injection advance angle. If necessary, please adjust it.<br />
(c). Disassemble cylinder head and eliminate carbon deposit. Check the tightness of air valve, if it is not<br />
accordance with the requirements, and then grind it.<br />
(d). Check the tightness of connecting rod bolts, main bearing bolts and flywheel bolts.<br />
(e). Re-screw up cylinder head bolts in order and adjust the valve clearance according to regulations.<br />
(See Chapter 08 Assembly of Engine)<br />
(f). Clean or replace air filter element (according to the amount of environmental dust, perform the<br />
“maintenance after 100 hours” in advance or after shorter time)<br />
(g). Replace the oil of injection pump and governor.<br />
(h). Clean the cooling system. The cleanout fluid consists of 150g caustic soda (Na OH) and 1L water.<br />
Before cleaning, let all water of cooling system out, and then fill cleanout fluid. When the coolant<br />
temperature reaches the working temperature, stop the engine, let the cleanout liquid out to avoid the<br />
water scale which floats in the cleanout fluid precipitating and then clean the cooling system with<br />
clean water.<br />
(i). Check the working situation of thermostat.<br />
(j). Check each part of electric equipment for start. Check whether the fastening pieces are tight and<br />
whether the contact of wire is tight. If there is burned mark, please replace it.<br />
(k). Check each parts of engine. If necessary, please maintain and adjust them.<br />
The user can carry out more careful maintenance according to situation in addition with the above regular<br />
4. Seal up for safekeeping<br />
(a). Thoroughly clean engine appearance.<br />
(b). The fuel system can be full of common fuel, but when the storage period expires, let the fuel out. And<br />
the fuel and the fuel’s filter element are declared worthless.<br />
(c). Run the engine until the engine is hot, and then discharge fuel. When the engine stops running, let<br />
lubricating oil of oil pan out.<br />
(d). Replace lubricating oil filter element.<br />
(e). Fill the new clean lubricating oil in the oil pan until the dipstick has full scale.<br />
(f). Fill the antifreeze solution which has anti-corrosion function in order to avoid the cooling system<br />
corrode.<br />
(g). Run the engine for a short time to cycle the engine’s lubricating oil and coolant.<br />
(h). Clean the engine’s air-pipe and seal the pipe ends.<br />
(i). Disassemble the air filter. If necessary, disassemble the connecting pipe between the air filter and<br />
intake manifold and seal the intake manifold with waterproof tape.<br />
(j). Seal the intake manifold, fuel tank’s air pipe and with waterproof tape.<br />
(k). Disconnect the battery and then store the battery after the battery is fully charged. Before storing the<br />
battery, carry out anti-corrosion treatment for battery.<br />
(l). Disassemble the transmission belt of generator and store it well.<br />
15B-72<br />
5. Running in<br />
Make the new engine running in before it is used to make each kinematic pair operate normally and to avoid<br />
abnormal wear and damaged. The experience proves that the service life of engine, economical efficiency<br />
and dependability of work are greatly determined by the situation of running in for engine at the initial<br />
operation, so please strictly carry out the maintenance regulations for running in.<br />
(a). Running in specification<br />
• Running in period:<br />
The running period is about 50 hours; the whole car can carry out running in together. The running<br />
in mileage is 1500~2500 kilometers.<br />
• The running in period’s requirements for load and speed are as follows:<br />
Mileage (kilometer) Highest load Highest speed<br />
0~200 No load —<br />
300~1000 50% rated load 70% rated speed<br />
1000~1500 75% rated load 75% rated speed<br />
1500~2000 Full load Not faster than the highest speed<br />
15B-73<br />
Running maintenance content and standard:<br />
Number Content Standard<br />
1 Replace lubricating oil of oil pan<br />
The brand shall be selected according to ambient<br />
Clean the oil pan and replace the paper oil<br />
filter element<br />
The parts and components shall be produced by<br />
formal accessory manufacturers<br />
3 Clean the air filter element<br />
4 Replace paper diesel filter element<br />
5 Check connecting rod bolt torque 155N·m<br />
6 Check cylinder head bolt torque 75N·m<br />
7 Check and adjust valve clearance<br />
8 Check fan belt tension<br />
9 Check fuel supply advance angle<br />
Cold car, Inlet valve 0.2mm<br />
Exhaust valve 0.45mm<br />
Add 45N force on vertical single belt, deflection<br />
is10 mm<br />
According to requirements of Operating Instruction<br />
<strong>Manual</strong><br />
10 Fasten the exposed bolts and nuts According to requirements<br />
Clean oil inlet filter screen of fuel delivery<br />
pump<br />
No dirt and no damage<br />
15B-74<br />
BASIC MAINTENANCE<br />
1. Determine the maintenance period<br />
Growth rate of oil consumption<br />
Suppose that the new oil consumption rate (mileage every hour or the running hours) is 100%, when<br />
the oil consumption rate reduces to 50%, and then the engine shall be maintained.<br />
Growth rate of fuel consumption<br />
Suppose that the new engine fuel consumption (mileage every hour or the running hours) is 100%,<br />
when the oil consumption rate reduces to 60%, and then the engine shall be maintained.<br />
The inside has abnormal sound<br />
There are various reasons for abnormal sound, for example, the engine has lots of wear or is<br />
overheated or the operation and maintenance are improper. So the engine shall be maintained early.<br />
2. Determine cylinder bed quality<br />
The cylinder head gasket is placed on the connection of cylinder head’s bottom and the engine body’s top<br />
surface to form air sealed chamber under the function of high strength cylinder bolt and to make burning<br />
gasses push forward the pistons work and not leakage outward. At the same time, it can carry out seal<br />
function for cycling coolant and pressure oil which leads to cylinder head and lubrication rocker mechanism.<br />
There are high requirements for cylinder gasket’s tightness and heat resistance, so the engine adopts<br />
composite plate cylinder gasket and the cylinder hole edge is sealed with steel plate. And the inside has steel<br />
wire protecting ring, and the edges of water hole and oil hole are sealed with copper sheet or are processed<br />
specially. They have good tightness and longer service life.<br />
(a). Check whether the cylinder bed has cracks and whether the water hole and oil hole are connected<br />
together. If yes, then replace the cylinder bed.<br />
(b). Measure the clearance of piston head when replacing cylinder, and the piston head clearance shall<br />
be in the range of 0.9~1.1mm.<br />
3. Adjust the valve clearance<br />
Check and adjust the valve clearance when the engine is serviced or maintained.<br />
(a). Check and screw up the nuts of valve rockshaft bracket when removing the cylinder head.<br />
(b). Rotate the crank in the dead center of the first cylinder piston, at the this moment the observation<br />
mark of flywheel housing is rightly aligned with “O” scribed line of flywheel or the “O” scribed line of<br />
crankshaft pulley is aligned with the indicator of timing gears cap.<br />
(c). Insert a thickness gauge thinness gauge into the first cylinder, exhaust valve and rocker respectively.<br />
Check and adjust the inlet valve clearance and exhaust valve clearance. The clearances are<br />
respectively 0.2 and 0.45mm when cold starting. Rotate the cranks of four cylinders 180°according to<br />
working order of 1-3-4-2 and adjust each cylinder’s valve clearance.<br />
15B-75<br />
4. Adjust the fuel supply advance angle<br />
In order to obtain the most economic fuel consumption and good running property, properly adjust fuel supply<br />
advance angle.<br />
(a). Eliminate the air of fuel system and repeatedly rotate the crank to make the injection pump full of fuel.<br />
(b). Disassemble the first cylinder’s high-pressure oil pipe and pull the accelerator operating handle in the<br />
position with maximum fuel supply amount. Rotate the crank in a clockwise direction from engine<br />
head to make the first cylinder piston is at compressed dead center.<br />
(c). Rotate the crank more than 60°in reverse direction, then slowly rotate the crank in clockwise direction<br />
and observe the oil outlet situation of outlet valve support. When the oil level begins to wave, it<br />
indicates that the first cylinder begins to supply oil. At this moment, please stop rotating the crank and<br />
check the difference between the scribed line of timing gear chamber cover and the scribed line of<br />
pulley to determine the fuel supply advance angle. If the scribed line of pulley is in front of the scribed<br />
line of timing gear chamber cover, it indicates fuel supply in advance. If the scribed line of pulley is on<br />
the back of the scribed line of timing gear chamber cover, it indicates fuel supply hysteresis. The<br />
engine’s fuel supply advance angle shall be 10°±1°.<br />
(d). If the fuel supply advance angle does not meet the requirements, loosen the bracket of injection pump<br />
and the nuts of pump end flange and adjust it by using the of pump end flange. When the pump body<br />
is close to the engine body, then the fuel supply advance angle is increased. And when the pump end<br />
body is far away the engine body, then the fuel supply advance angle is reduced. The outer edge of<br />
pump body flange rotates 1mm arc length, and the fuel supply advance angle is increased or reduced<br />
about 1°of crank angle.<br />
5. Adjust fuel injector<br />
The fuel injector is tested and adjusted on the tester of fuel injector to adjust the fuel injection pressure and to<br />
observe the atomization quality and to treat faults. When the fuel injection pressure of injector is too high or<br />
too low and the fuel injection is abnormal and the parts are damaged, the engine will appear faults, such as<br />
pouring up smoke, the power and rotation are reduced, discharging temperature rises or piston slap. The<br />
method of stop cylinder in turn can be adopted to determine the fuel injector with fault. The method is:<br />
gradually loosen the coupling nut between fuel injector and high-pressure oil pipe and stop fuel injection, at<br />
the same time observe the exhaust smoke color. If the fuel injector has fault, the exhaust will stop smoking,<br />
and the engine rotation has no change or little change. Rotate the flywheel to listen to injection sound of each<br />
cylinder one by one, when the ringing injection sound is not heard, it indicates that the fuel injector may have<br />
fault.<br />
(a). Install the fuel injector in the tester of fuel injector.<br />
(b). The gauge pressure shall be 180×10pa by manual pump. Continuously slowly press the manual<br />
pump to raise the gauge pressure to 200×10pa and to inject oil. Observe the fuel spray nozzle’s oil<br />
hole and make it has no oil drip and leakage. If after test for many times, if there is also oil drip,<br />
disassemble the injection nozzle couple to clean. After checking and grinding it, please test again.<br />
(c). Adjust the fuel injection pressure, disassemble the pressure regulating nut of fuel injector, and then<br />
unscrew or screw up the pressure regulating bolts to make the fuel injection pressure is 200×10pa.<br />
Screw the pressure regulating nut and test it again.<br />
15B-76<br />
Observe atomization quality and carry out atomization test with fuel injection speed every minute. The<br />
oil mist shall be fine mist. And the splashed oil which can be seen with naked eyes shall not be<br />
appeared, and the phenomena of uneven concentration and one side’s fuel injection shall not be<br />
appeared. And the ringing sound shall be heard when cutting off the fuel.<br />
The abnormal fuel injection is normally caused by inflexible motion of injection nozzle. Oil drip of jet<br />
orifice is caused by damaged seal surface. Oil injection branch is caused by the head carbon deposit<br />
and thermal deformation of injection nozzle.<br />
6. Adjust oil pressure<br />
(a). Loosen the lock nut.<br />
(b). Twist the pressure regulating bolts with wrench to make the oil is 280~400kpa (the oil can be higher<br />
when cold starting).<br />
(c). After adjustment, screw up the nut.<br />
7. Adjust injection pump<br />
The injection pump has already been adjusted and checked before factory. If the injection pump needs to be<br />
adjusted again, the injection pump shall be adjusted on the professional injection pump tester with standard<br />
fuel injector and standard length of high-pressure oil pipe.<br />
8. Adjust the fan pulley<br />
(a). Add 45N force on the single belt which is in the middle position of two wheels and the deflection is<br />
about 10mm.<br />
If the fan pulley is not accordance with the requirements, please adjust it with the following method.<br />
• Loosen the adjusting screw of the bracket of engine.<br />
• Pry out the generator from the outboard of engine with strength pipe and then lock the screw of bracket of<br />
generator until it is up to the standard.<br />
9. Exhausting of fuel system<br />
If the pipeline from fuel tank to fuel delivery pump has air, please exhaust it when replacing diesel filter<br />
(a). Screw the manual oil pump handle out, press up and down to supply oil for fuel system.<br />
(b). Loosen the small oil return pipe of fuel filter and exhausting bolt of injection pump and continue to<br />
supply oil with manual oil pump until the oil runs out and no bubble exhausts.<br />
(c). Screw the bolts and screws and at the same time screw the manual oil pump handle.<br />
ENGINE MECHANICAL PART-DISASSEMBLY/ASSEMBLY OF COMPLETE ENGINE<br />
15B-77<br />
DISASSEMBLY/INSTALLATION OF COMPLETE ENGINE<br />
1. Park the vehicle on the vehicle trough or the vehicle service bench.<br />
2. Shift the parking brake lever to parking position.<br />
3. Block the wheels with triangular wood or wedge. The triangular wood or the wedge shall be placed<br />
closely before and after the wheels, preferable the rear wheels.<br />
4. Switch off of ignition switch before removing the complete engine (the ignition switch shall be at OFF<br />
position) and take down the ignition lock.<br />
5. Put a warning sign “No start” in steering wheel or the driver’s seat when working under the car.<br />
6. Keep away from the fire source while removing the complete engine.<br />
7. When disconnecting each connecting pipeline of engine or assembly component, put the<br />
disconnected pipeline or assembly component in the position where has no influence on the position<br />
of removing the engine and make the corresponding mark for installation. Fix the air condition<br />
compressor, clutch slave cylinder assembly on the frame with a rope to avoid falling off and<br />
damaging.<br />
15B-78<br />
DISASSEMBLY PROCEDURE<br />
1. Open the engine hood<br />
2. Discharge the engine lubricating oil and discharge<br />
the engine coolant<br />
• When the engine temperature is higher, do not open<br />
the radiator’s pressure cap or discharge coolant. The<br />
radiator’s pressure cap can be opened when the<br />
coolant temperature reduces to lower than 50℃, or<br />
else the coolant with high temperature and erupted<br />
steam may cause personal injury.<br />
• The coolant is poisonous, so the coolant shall be<br />
stored in the original container to avoid contacting<br />
people.<br />
• When replacing coolant, waste treatment shall be<br />
carried out according to local regulations.<br />
• Whether to maintain the engine determines whether to<br />
discharge lubricating oil.<br />
3. Disconnect the battery’s positive and negative wire<br />
and disconnect the ground wire, generator and<br />
connecting wire of starter<br />
• Disassemble battery negative pole first when removing to<br />
avoid the ground producing spark and causing losses and<br />
damage.<br />
• After disconnect the battery’s negative pole, wait for 60s<br />
then disassemble other electric equipment.<br />
The battery may have explosive gas escapes. Therefore, in<br />
order to avoid damaging human body, good ventilation<br />
shall be ensured for engine compartment before<br />
maintaining battery.<br />
15B-79<br />
4. Disassemble fuel inlet pipe and fuel return pipe<br />
which connects the engine<br />
After removing the fuel pipeline, please seal it to ensure no fuel<br />
leakage takes place.<br />
• The fuel is inflammables, so it will far away from naked<br />
flame, work light and power connector and etc.<br />
• The disassembly shall be made with good ventilation<br />
to avoid damaging human body and property losses.<br />
5. Disconnect all cooling pipelines which connect<br />
with the engine. If necessary, disassemble the<br />
cooling pipeline gradually.<br />
Disassemble the engine’s inlet pipe and outlet pipe possibly to<br />
avoid blocking or damaging them when removing the complete<br />
6. Disassemble the fixing clamp of intake hose and<br />
take down the intake hose.<br />
After take down the intake hose, the intake manifold port shall<br />
be sealed.<br />
7. Disconnect the connection of heater water pipe<br />
15B-80<br />
8. Disassemble the fixing clamp of engine assembly,<br />
pull out the connector of the main harness and take<br />
down the main harness<br />
9. Disconnect the vacuum connecting pipe of EGR<br />
10. Disconnect the connection between exhaust pipe<br />
and turbocharger<br />
Disassemble the front section of pipeline of exhaust pipe<br />
possibly in order to conveniently disassemble the complete<br />
11. Remove the fan<br />
Avoid collision and damaging the fan when removing.<br />
12. Disconnect the ground wire from the transmission<br />
and at the same time remove the generator<br />
connecting lead.<br />
15B-81<br />
13. Disconnect the lead connection of starter and<br />
disassemble the starter.<br />
14. Remove the A/C compressor assembly.<br />
15. Disassemble power steering pump assembly and<br />
hang the assembly on the frame<br />
16. Remove the propeller Shaft from the transfer case<br />
and at the same time remove the propeller Shaft on<br />
the other side of transfer case (Refer to Chapter 33<br />
Propeller Shaft)<br />
17. Disconnect the lead of clutch and the connection of<br />
odometer lead<br />
15B-82<br />
18. Remove the transfer case.<br />
19. Disconnect the lead of reverse gear switch and the<br />
connection of lead of vehicle speed sensor<br />
20. Remove the shift lever (Refer to Chapter 31<br />
Transmission).<br />
21. Remove the clutch slave cylinder.<br />
Once removed, fix the clutch slave cylinder onto the<br />
crossbeam, in order to prevent the trouble of empty drainage.<br />
22. Remove the fixing bolts between the transmission<br />
and the suspension.<br />
To prevent the tilting of the engine, lift the tail of the engine with<br />
jack while removing the transmission suspension.<br />
15B-83<br />
23. Remove the fixing bolts between engine and<br />
transmission<br />
24. Remove the fixing bolts for connecting the engine<br />
suspension and the frame<br />
25. Hoist the engine steadily to lift the engine suspension from the suspension bracket and slowly<br />
move the engine to an appropriate angle. Pull the hoist to move the engine from the<br />
installation location of the frame and slowly place and fix the engine assembly onto the<br />
disassembly stand.<br />
Before removing the engine, recheck whether all connections on all sides of the engine are disconnected.<br />
15B-84<br />
INSTALLATION PROCEDURE<br />
1. Lift the engine with hoist and move the hoist to position the engine at the engine installation<br />
location.<br />
• As the engine assembly is really heavy, to prevent the occurrence of accidents, it’s preferable to perform<br />
the installation by two or more operators.<br />
• By adjusting the adjusting bolts of the hoist, slowly lower the engine in such manner that the engine<br />
suspension closes to the suspension bracket on the crossbeam and aligns with the fixing bolt holes<br />
2. Install and fasten the fixing bolts of the engine front<br />
suspension.<br />
Lift the tail of the engine with jack, in order to prevent the tilting<br />
of the engine.<br />
3. Install and fasten the fixing bolts for connecting the<br />
engine and the transmission.<br />
4. Install and fix the fixing bolts for connecting the<br />
transmission and the suspension.<br />
5. Install and fasten the clutch slave cylinder and its<br />
fixing bolts.<br />
15B-85<br />
6. Install the shift lever (Refer to Chapter 41<br />
Transmission)<br />
7. Connect the leads of reverse gear switch and<br />
vehicle speed sensor.<br />
8. Install and fasten the fixing bolts of transfer case<br />
9. Connect the leads of the transfer case and the<br />
odometer.<br />
10. Install and fasten the fixing bolts and propeller<br />
shaft (see Chapter 34 Transaxle and Propeller Shaft<br />
- Propeller Shaft Assembly, Assembly Service for<br />
Detail)<br />
15B-86<br />
11. Install power steering pump and fasten the fixing<br />
12. Install A/C compressor assembly<br />
13. Install the starter motor and connect the starter<br />
motor lead.<br />
14. Install and fasten the engine ground wire onto the<br />
transmission housing<br />
15. Install the fan.<br />
15B-87<br />
16. Connect the connection of exhaust pipe and<br />
turbocharger and fasten the connecting bolts<br />
17. Install the lead of generator on the corresponding wiring terminal or in the connector<br />
18. Connect the vacuum connecting pipe of EGR valve<br />
19. Install the clamps of engine’s main harness and<br />
plug the main harness’s connector<br />
20. Install the heater water pipe<br />
15B-88<br />
21. Install the intake hose of engine<br />
22. Install engine’s fuel inlet pipe and fuel return pipe<br />
• Fuel pipeline shall be evacuated when removing the fuel<br />
pipeline.<br />
• Make sure that there is no air in the fuel pipeline and then<br />
the engine can normally start.<br />
23. Install the cooling pipeline of engine and fasten the<br />
fixing clamps of hose.<br />
24. Fill the lubricating oil with the right amount. Make sure the lubricating oil is enough by<br />
observing the dipstick and fill the coolant until the coolant is up to standard level.<br />
25. Observe the surrounding connecting pieces of engine to make sure that the installation is firm<br />
and dependable. Make sure to put the transmission in the neutral position and then test the<br />
26. Connect the battery leads.<br />
While installing the battery leads, firstly install the positive<br />
wiring terminal and fix, seal and insulate the bolt before<br />
installing the negative wiring terminal and fixing, sealing, and<br />
insulating the bolt.<br />
15B-89<br />
27. Turn on the ignition switch, and observe the instruments to ensure that all functions are<br />
normal, and then start the engine.<br />
After the engine is started, observe the instruments to ensure that the readings of oil pressure gauge and the<br />
coolant temperature gauge are normal and enter into the vehicle trough to observe the surrounding area of<br />
the engine for the presence of water leakage, oil leakage, and gas leakage. In event of any leakage, stop the<br />
engine immediately and resolve the malfunctions.<br />
28. Cover the engine hood<br />
15B-90<br />
INSTRUCTION OF ESSENTIALS<br />
1. Disconnection and Connection Instruction of<br />
Battery Ground Wire<br />
Instruction:<br />
• Before the Disassembly of the engine, firstly disconnect the<br />
negative wire of the battery.<br />
• In order to ensure that all disassembly works of the engine<br />
are fulfilled under power cut condition.<br />
• After all operation are finished, check all again. After all is<br />
right and then connect the battery’s negative pole.<br />
2. Disassembly and Installation Instruction of Fuel<br />
Pipes<br />
• While removing the fuel pipes, it’s necessary to cover the<br />
connectors disconnected with fuel pipe caps.<br />
• The fuel is one flammable substance. While handling the<br />
fuel system, make sure to keep the cigarette, open fire,<br />
indicator lamp, electric arc equipment, and switch away<br />
from the operation area and equip with ventilation<br />
equipment in the operation area, in order to minimize the<br />
possibility of serious personal injuries or even death<br />
3. Instruction of Engine Protection Measures<br />
The presence of minor foreign materials inside the engine will<br />
often lead to engine failure for normal functioning or even lead<br />
to serious harm of the engine. Therefore, while disconnecting<br />
all connecting pipes of the engine, it’s necessary to cover all<br />
openings of the engine, in order to prevent the ingress of dirt or<br />
scrap into the engine.<br />
4. Instruction of Disassembly of Engine and Installation Mode<br />
Disassemble the complete engine from engine compartment with lifting frame when removing. And when<br />
installing, lift the complete engine with lifting frame from the top of engine compartment.<br />
ENGINE MECHANICAL PART- PRESERVATION OF COMPLETE ENGINE 15B-91<br />
PRESERVATION OF COMPLETE ENGINE<br />
1. Make the coolant of radiator, cylinder blocks and water pump exhausted.<br />
2 Disassemble the battery.<br />
3. Screw out each cylinder’s heater plug and fill 30g oil in each cylinder. Rotate the crank for 15~20<br />
times and then install the heart plug.<br />
4. Put the dehydration vaseline (heat to 100~200℃) on the contact of electric equipment, connector and<br />
some metal surface which are not painted.<br />
5. Fill lubrication in each lubricating point.<br />
6. Loosen the fan belt.<br />
7. Make the diesel of diesel tank exhausted and clean the fuel tank.<br />
8. Wrap the engine with protective materials (such as canvas, waterproof cloth and oiliness) to avoid<br />
dust.<br />
9. The room for storing engine shall be clean, warm and keep out of the sun, the indoor temperature<br />
shall not lower than 5℃ and the relative humidity is 40~70%.<br />
1. Charge the battery with 5~12A current once every month.<br />
2. Screw out the heater plug and fill 30g oil every 12 months and rotate the crank for 15~20 times to<br />
avoid inside corrosion and install the heater plug again.<br />
3. Eliminate the lubricating grease on the lubricant housings every 12 months and replace the<br />
lubricating grease.<br />
15B-92<br />
ENGINE MECHANICAL PART- DISSASSEBLY OF ENGINE<br />
DISASSEMBLY OF ENGINE (4JB1)<br />
INSTRUCTION OF DISASSEMBLY<br />
1. This section provides one complete set of procedure for disassembly of diesel engine. The<br />
disassembly mode is illustrated in both graphs and texts step by step from top to bottom and from<br />
outside to inside.<br />
2. Before removing the engine, place the engine assembly onto the disassembly stand or place it on one<br />
clean and level ground and prepare the necessary disassembly tools and professional container or<br />
environment for placement of parts.<br />
3. The disassembly environment shall be kept away as far as possible from the fire source and other<br />
objects (such as children) that impair the safety.<br />
15B-93<br />
DISASSEMBLY OF PIPELINE AND HARNESS<br />
1. Disassemble EGR pipeline<br />
(a). Disassemble two fixing bolts which connect EGR pipe<br />
and intake pipe.<br />
All bolts removed shall be centrally placed, in order to prevent<br />
loss.<br />
(b). Disassemble the fixing bolts which connect EGR pipe<br />
2. Disassemble breather pipe<br />
(a). Disassemble the connectors between breather exhaust<br />
pipe and intake pipe of turbocharger and disconnect<br />
the connector of breather intake pipe.<br />
15B-94<br />
Disassemble the connectors between breather exhaust<br />
pipe and breather and disconnect and take down the<br />
breather intake pipe.<br />
Disassemble the clamps between breather intake pipe<br />
and valve chamber cover and disconnect the connector<br />
of breather intake pipe.<br />
and breather and disconnect and take down the<br />
3. Disassemble intake pipe of turbocharger<br />
(a). Disassemble the fixing bolts of intake pipe of<br />
turbocharger, disassemble the fixing bolts which<br />
connect intake pipe of turbocharger and turbocharger<br />
and then take down the intake pipe of turbocharger.<br />
4. Disassemble intake pipe<br />
(a). Disassemble the fixing bolts between intake pipe and<br />
intake manifold and take down the intake pipe.<br />
5. Disassemble the engine’s harness<br />
(a). Disassemble the engine’s ECU harness connector<br />
from the installation position and take it down.<br />
15B-95<br />
DISASSEMBLY OF HIGH AND LOW PRESSURE FUEL PIPES AND<br />
FUEL INJECTOR<br />
The fuel is one flammable substance. While handling the fuel system, make sure to keep the cigarette,<br />
open fire, indicator lamp, electric arc equipment, and switch away from the operation area and equip<br />
with ventilation equipment in the operation area, in order to minimize the possibility of serious<br />
personal injuries or even death.<br />
1. Disassemble the high pressure fuel pipe<br />
(a). Disconnect the connection between injection pump and<br />
Disconnect the connection between injection nozzle<br />
and high pressure fuel rail.<br />
(c). Disconnect the connection between the high pressure<br />
fuel pipe and high pressure fuel rail and take down the<br />
When removing the high pressure fuel pipe, take down the high<br />
pressure fuel pipe from the lower end of intake manifold, cover<br />
the connector cover of high pressure fuel pipe and install the<br />
high pressure fuel pipe with clean plastic packing bag.<br />
2. Disassemble the low pressure oil pipe<br />
(a). Disassemble and take down the low pressure oil pipe.<br />
Push the connectors of low pressure oil pipe towards the<br />
opening position and take it down from the fuel injector.<br />
15B-96<br />
3. Disassemble the fuel injector<br />
(a). Disassemble the fixing bolts of the pressure plate of<br />
fuel injector and take down the pressure plate of fuel<br />
injector and the fuel injector.<br />
15B-97<br />
DISASSEMBLY OF DIPSTICK AND VENTILATOR<br />
1. Disassemble the dipstick<br />
(a). Disconnect the oil return pipe connectors which<br />
connect the dipstick and breather and disassemble the<br />
fixing bolts of dipstick.<br />
Take down the dipstick.<br />
2. Disassemble the breather assembly<br />
(a). Disassemble the fixing bolts of breather.<br />
Take down the breather assembly<br />
15B-98<br />
(c). Disassemble the fixing bolts of breather support.<br />
Take down the breather support.<br />
15B-99<br />
DISASSEMBLY OF TURBOCHARGER, INTAKE MANIFOLD AND<br />
EXHAUST MANIFOLDS<br />
1. Disassemble the turbocharger<br />
(a). Disassemble fuel inlet pipe and oil return pipe of<br />
(b). Disassemble heat insulating pad assembly and<br />
disassemble the fixing bolts of turbocharger.<br />
Take down the turbocharger assembly.<br />
2. Disassemble exhaust manifold<br />
(a). Disassemble the fixing bolts of exhaust manifold.<br />
15B-100<br />
Take down the exhaust manifold.<br />
3. Disassemble the intake manifold<br />
(a). Disassemble the fixing bolts of intake manifold.<br />
(b). Take down the intake manifold.<br />
After taking down the intake manifold, block the exit and<br />
entrance with sealed cap or equivalent to prevent other things<br />
from entering.<br />
15B-101<br />
DISASSEMBLY OF CYLINDER HEAD COVER AND ROCKSHAFT<br />
1. Remove the cylinder head cover.<br />
(a). Remove the fixing nuts of the cylinder head cover.<br />
All nuts removed shall be centrally placed, in order to prevent<br />
loss<br />
Take down the cylinder head cover assembly.<br />
2. Disassemble electric heater plug assembly<br />
(a). Disassemble and take down four electric heater plugs.<br />
3. Remove the rockshaft.<br />
(a). Remove the fixing bolts of the rocker assembly<br />
15B-102<br />
Remove the rockshaft assembly<br />
15B-103<br />
DISASSEMBLY OF TAPPET AND CYLINDER HEAD<br />
1. Disassemble tappet<br />
(a). Take down all valve tappets one by one from<br />
Put all tappets which are taken down together to avoid losses.<br />
2. Remove the cylinder head.<br />
(a). Remove the fixing bolts of the cylinder head<br />
Screw off the bolts of cylinder head many times according<br />
to the order on the left and assembly the bolts.<br />
(b). Remove the cylinder head assembly.<br />
This assembly is really heavy. To prevent causing serious<br />
personal injuries, make sure to ask another operator for<br />
assistance or use appropriate lifting equipment to hoist this part<br />
or assembly<br />
15B-104<br />
DISASSEMBLY OF THERMOSTAT ASSEMBLY AND VALVE<br />
1. Disassemble the thermostat assembly<br />
(a). Disassemble the fixing bolts of water pipe assembly<br />
and take down the water pipe assembly.<br />
Take down the thermostat.<br />
(c). Disassemble and take down the fixing bolts of<br />
thermostat housing assembly.<br />
2. Remove the valve.<br />
(a). Disassemble the valve lock clamp.<br />
Please wear goggles to avoid damaging persons.<br />
15B-105<br />
Disassemble the spring bottom seat of valve, valve<br />
spring and the spring upper seat of valve and<br />
disassemble the valve oil seal.<br />
Take down the valve and knock out the valve guide<br />
pipe from the bottom of cylinder head with special tools.<br />
15B-106<br />
DISASSEMBLY OF HOOK AND A/C BRACKET<br />
1. Disassemble hook<br />
(a). Disassemble the fixing bolts of hook<br />
Take down the hook<br />
2. Disassemble the A/C bracket<br />
(a). Disassemble the fixing bolts of A/C bracket and take it<br />
15B-107<br />
DISASSEMBLY OF STARTER MOTOR AND HIGH PRESSURE FUEL<br />
RAIL<br />
1. Disassemble the starter motor<br />
(a). Disassemble the fixing bolts of starter motor<br />
Take down the starter motor.<br />
2. Disassemble the high pressure fuel rail<br />
(a). Disassemble fixing bolts of high pressure fuel rail<br />
Take down the high pressure fuel rail assembly<br />
15B-108<br />
DISASSEMBLY OF OIL FILTER AND GENERATOR<br />
1. Disassemble the oil filter assembly<br />
(a). Disconnect the connection of coolant pipe of oil filter.<br />
(b). Disassemble the fixing bolts of oil filter assembly.<br />
Take down the oil filter assembly.<br />
2. Disassemble the generator<br />
(a). Disconnect the connection of vacuum pump oil inlet<br />
pipe and oil outlet pipe at the rear end of generator.<br />
15B-109<br />
(b). Disassemble the adjusting bolts of generator and<br />
release all belt tension.<br />
Take down the generator belt.<br />
Disassemble the fixing bolts at the low end of generator<br />
and take down the generator assembly.<br />
While removing the fixing bolts, pull the generator with<br />
hand to prevent the fall-off of generator due to loss of<br />
bracket from damaging the generator.<br />
15B-110<br />
DISASSEMBLY OF FAN AND CRANKSHAFT PULLEY<br />
1. Disassemble the fan<br />
(a). Disassemble the fixing bolts of fan assembly<br />
Make the studs reverse stuck with screwdriver when removing<br />
and at the same time disassemble the near nuts with wrench.<br />
Take down the fan assembly<br />
2. Disassemble the crankshaft pulley<br />
(a). Disassemble the fixing bolts of crankshaft pulley<br />
Take down the crankshaft pulley<br />
15B-111<br />
DISASSEMBLY OF OBSERVATION CHAMBER COVER AND<br />
COVER ASSEMBLY OF WATER PUMP PULLEY CHAMBER<br />
1. Disassemble the observation chamber cover<br />
(a). Disassemble the fixing bolts of observation chamber<br />
Take down the observation chamber cover.<br />
2. Disassemble the cover assembly of water pump<br />
pulley chamber<br />
(a). Disassemble the fixing bolts of cover assembly of water<br />
pump pulley chamber .<br />
loss.。<br />
Take down the cover assembly of water pump pulley<br />
chamber.<br />
15B-112<br />
DISASSEMBLY OF PRESSURE PLATE AND TIMING BELT<br />
1. Disassemble the pressure plate<br />
(a). Disassemble the fixing bolts of camshaft pulley<br />
pressure plate.<br />
Take down the camshaft pulley plate.<br />
(c). Disassemble the fixing bolts of injection pump pulley<br />
Take down the injection pump pulley pressure plate.<br />
15B-113<br />
2. Disassemble the timing belt<br />
(a). Disassemble the fixing bolts of tensioning pull rod.<br />
(b). Adjust the tightness of timing belt through tensioning<br />
pull rod through special tool and loosen the fixing bolts<br />
of the low idle pulley.<br />
Firstly screw up the fixing nuts of tensioning pull rod and then<br />
adjust the tightness of timing belt through the tensioning pull<br />
rod.<br />
Take down the timing belt.<br />
15B-114<br />
DISASSEMBLY OF INJECTION PUMP ASSEMBLY<br />
1. Disassemble the injection pump<br />
(a). Disassemble the fixing bolts of injection pump<br />
(b). Take down the injection pump pulley, injection pump<br />
flange and injection pulley.<br />
Take down the injection pump pulley, injection pump flange and<br />
injection pulley together.<br />
15B-115<br />
DISASSEMBLY OF IDLE PULLEY AND CAMSHAFT GEAR<br />
1. Disassemble the idle pulley<br />
(a). Disassemble and take down the fixing bolts of<br />
tensioning pull rod.<br />
(b). Disassemble the positioning bolts and take down the<br />
tension pulley assembly.<br />
(c). Disassemble and take down the fixing bolts of idle<br />
2. Disassemble the camshaft gear<br />
(a). Disassemble the fixing bolts of camshaft pulley.<br />
• When removing the bolts of camshaft gear, the camshaft<br />
gear will rotate. Therefore the camshaft gear can be<br />
positioned with special positioned.<br />
• The camshaft gear can be also positioned with tools like<br />
screwdriver or solid wrench according to actual situation.<br />
15B-116<br />
Take down the camshaft gear.<br />
(c). Disassemble the fixing bolts of pressure plate.<br />
Take down the pressure plate.<br />
Take down the flange of camshaft pulley.<br />
(f). Disassemble the fixing bolts of the front oil seal seat of<br />
camshaft.<br />
Before removing the front oil seal seat of camshaft, first<br />
disassemble the flat key of camshaft.<br />
15B-117<br />
Take down the front oil seal seat of camshaft.<br />
15B-118<br />
DISASSEMBLY OF CLUTCH COMPONENTS AND FLYWHEEL<br />
ASSEMBLY<br />
1. Disassemble the clutch components<br />
(a). Remove the fixing bolts of the clutch components.<br />
Disassemble the clutch friction plate and clutch<br />
2. Remove the Flywheel assembly<br />
(a). Disassemble the flywheel bolts and the flywheel bolt<br />
Take down the flywheel.<br />
15B-119<br />
Disassemble the fixing bolts of the rear joint plate. Take<br />
down the rear joint plate and pry out the rear crank oil<br />
seal with screwdriver.<br />
• All bolts removed shall be centrally placed, in order to<br />
prevent loss.<br />
• The oil seal which is disassembled cannot be used again.<br />
Please replace oil seal.<br />
15B-120<br />
DISASSEMBLY OF OIL PAN AND GEAR CHAMBER<br />
1. Remove the oil pan<br />
(a). Roll over the engine body<br />
(b). Remove the fixing bolts of oil pan.<br />
• Do not disassemble a bolt randomly. The fixing bolts of oil<br />
pan shall be crossly disassembled with the method of from<br />
the middle to both sides or from both sides to the middle.<br />
Remove the oil pan.<br />
2. Disassemble the gear chamber<br />
(a). Disassemble the fixing bolts of timing gear chamber .<br />
Take down the timing gear chamber.<br />
15B-121<br />
(c). Take down the gear chamber gasket.<br />
The gear gasket which is disassembled cannot be used again.<br />
Please replace gear chamber gasket.<br />
15B-122<br />
DISASSEMBLY OF CAMSHAFT AND ENGINE SUPPORT<br />
1. Remove the camshaft.<br />
(a). Pull out the camshaft from the installation location.<br />
Slowly rotate and pull out the camshaft.<br />
2. Remove the engine support.<br />
(a) Remove 4 fixing bolts of engine support.<br />
Take down the engine support.<br />
15B-123<br />
DISASSEMBLY OF OIL PUMP, OIL INJECTION PIPE AND TAPPET<br />
1. Disassemble the oil pump<br />
(a). Disassemble 2 fixing bolts of oil pump.<br />
Disconnect the connection of oil outlet pipe of oil pump<br />
and oil pump.<br />
Take down the oil pump.<br />
2. Disassemble the oil Injection pipe<br />
(a). Disassemble the fixing bolts of oil Injection pipe and<br />
pressure-limiting valve components.<br />
15B-124<br />
(b). Take down the oil Injection pipe assembly.<br />
Make sure that the oil Injection pipe is clean especially the<br />
nozzle shall be clean.<br />
3. Disassemble the tappet<br />
(a). Attract the tappets one by one from the installation<br />
position with high performance magnet.<br />
Put the tappets which are taken down in the clean container.<br />
15B-125<br />
DISASSEMBLY OF PISTON AND CRANKSHAFT<br />
1. Remove the piston assembly.<br />
(a) Rotate the crankshaft to position the journal of<br />
connecting rod to be removed at bottom dead center.<br />
(b). Disassemble the fixing bolts of with kilo wrench.<br />
Screw off the bolts in pairs.<br />
(c). Lightly shake and pull out the connecting rod cover.<br />
(d). Take down the connecting rod bearing bush.<br />
Pay attention not to damage the connecting rod bearing<br />
bush.<br />
(e). Eliminate the carbon deposition of piston cylinder.<br />
• Please abide by the use recommendations of the<br />
manufacturer while using the solvent, acid or alkaline<br />
material for cleaning. Please wear the goggles and<br />
protective clothing to prevent causing personal<br />
injuries.<br />
• Some solvents are flammable and toxic. Please read the<br />
manual of the manufacturer before use.<br />
15B-126<br />
(f). Push out the piston assembly<br />
Push out the piston assembly with wooden or rubber object. Do<br />
not use metallic object, in order to prevent damaging the end<br />
face of connecting rod.<br />
Remove the piston assembly from the other side.<br />
(h). Install the disassembled pistons together and put the<br />
mark number in a clean container.<br />
(i). Disassemble the pistons in other cylinders with the<br />
same method.<br />
If the piston is not used immediately, mark the number on each<br />
piston and connecting rod assembly with label and put the<br />
connecting rod and pistons in the contained to avoid being<br />
2. Remove the crankshaft assembly.<br />
(a) Loosen the bolts of main bearing cap in turn.<br />
Loosen all bolts in turn in diagonal manner, but do not remove<br />
the bolts.<br />
Remove the bolts as per disassembly sequence shown in<br />
the left figure.<br />
15B-127<br />
(b). Remove the main bearing cap and the main bearing<br />
cap bolts and arrange them in order and remove the<br />
main bearing bush.<br />
• Grasp the bolts of main bearing cap with two hands, shake<br />
the main bearing cap or knock loose with rubber hammer,<br />
and then remove the main bearing cap.<br />
• The top of each main bearing cap has marking to help the<br />
remembering.<br />
(c). Remove the crankshaft.<br />
This part is a little heavy. To prevent causing serious<br />
personal injuries, make sure to lift this part or assembly<br />
with the assistance of other operators or with appropriate<br />
lifting equipment.<br />
(d). Remove the upper bushes of the main bearing bushes.<br />
Take out each upper bearing bush and mark the number on the<br />
movable lug and write down the installation position and the<br />
front and back side.<br />
15B-128<br />
ENGINE MECHANICAL PART-ASSEMBLY OF ENGINE<br />
ASSEMBLY OF ENGINE (4JB1)<br />
INSTRUCTION OF ASSEMBLY<br />
1. This section provides one complete set of procedure for assembly of diesel engine. The assembly<br />
mode is illustrated in both graphs and texts step by step from bottom to top and from inside to outside.<br />
2. The assembly environment shall be kept away as far as possible from the fire source and other<br />
3. During the assembly, install the parts removed to the original positions, without part shortage and<br />
missing part.<br />
4. During the assembly, replace all paper gaskets and never reuse these paper gaskets.<br />
5. During the assembly, make sure that the parts installed are intact and contamination-free and ensure<br />
that every part is installed securely in place.<br />
15B-129<br />
INSTALLATION OF CRANKSHAFT AND PISTON<br />
1. Install the crankshaft.<br />
(a) Face upward the cylinder block crankcase and place<br />
steadily.<br />
Make sure that there is no foreign material within the<br />
crankcase.<br />
(b). Install the upper bearing bush of main bearing bush in<br />
the specified position.<br />
• Carefully install the upper bushes of the main bearing<br />
bushes to the specified positions in turn and ensure that the<br />
back faces of the bearing bushes are clean without any<br />
scrap. The upper bush of each main bearing bush shall be<br />
in the center position of the bearing bush groove and the top<br />
faces of all bearing bushes shall be level.<br />
• After installation, uniformly put oil with right amount or the<br />
equivalent lubricating oil on the inside of bearing pad’s<br />
arched surface.<br />
During the installation, make sure that the positioning lug<br />
is aligned with the positioning groove of the main bearing<br />
bush cylinder saddle.<br />
(c). Install the crankshaft thrust bearing in the specified<br />
In this engine, there are two thrust bearings installed at the 3rd<br />
main bearing bush of the cylinder block.<br />
During the installation of the thrust bearings, notice to<br />
face the oil grooves outward<br />
15B-130<br />
(d). Drip clean oil or equivalent lubricating oil to the inner<br />
side of the main bearing bushes.<br />
Do not drip oil to the outer side of the main bearing<br />
bushes.<br />
(e). Install the crankshaft to the specified position.<br />
N OTE:<br />
• This part is a little heavy. To prevent causing personal<br />
injuries, make sure to lift this part or assembly with the<br />
assistance of other operators or with appropriate lifting<br />
equipment.<br />
• Install the crankshaft with care, in order to prevent<br />
damaging the crankshaft main bearing, specially the<br />
thrust/main bearing journals. The damage of the<br />
crankshaft will shorten the service life of the engine.<br />
(f). After installing the crank, put the clean oil or the<br />
equivalent lubricating oil on the main bearing journals<br />
of crank.<br />
(g). Apply the oil to the lower bushes of the main bearing<br />
bushes and install onto the main bearing cap.<br />
Slide the lower bushes of the main bearing bushes from one<br />
side into the main bearing bush cap and press level the end<br />
faces.<br />
15B-131<br />
During the installation, make sure that the positioning lugs<br />
of bearing bushes are aligned with the positioning<br />
grooves of the main bearing cap.<br />
(h). Install the main bearing cap in turn.<br />
Install the main bearing cap to the original position as per<br />
markings and do not wrongly install any part.<br />
Each main bearing cap of the crankshaft is marked with<br />
identification number. Install the bearing caps in order and do<br />
not wrongly install any one.<br />
Install the main bearing caps of the crankshaft onto the<br />
main bearing block of the crankcase and ensure that the<br />
arrow of each main bearing cap points to the front<br />
direction (pulley direction).<br />
(i). Install the fixing bolts of the main bearing caps to<br />
specified installation holes in turn and fasten lightly with<br />
hand<br />
Put oil with the right amount on the head bolt of main bearing<br />
Screw up the main bearing bolts according to assigned<br />
order and torque.<br />
15B-132<br />
• Fasten the bolts to the specified torque by several times,<br />
instead of fastening by one time.<br />
• Fasten the fixing bolts of the main bearing as per specified<br />
sequence (as shown in left figure).<br />
2. Install the piston assembly.<br />
(a) Install the connecting rod bolts to the connecting rod.<br />
(b). Install the upper bush of piston connecting rod bearing<br />
• Before assembly, all parts shall be clean.<br />
• Clean the connecting rod and bearing brush with a clean<br />
and non-cottony cloth.<br />
• Make sure that the back faces and side faces of the<br />
connecting rod and connecting rod bearing are clean,<br />
without any scrap.<br />
• Do not lubricate the back face and side face of the<br />
connecting rod bearing.<br />
grooves of the connecting rod.<br />
15B-133<br />
Drip clean oil or equivalent lubricating oil to the inner<br />
side of the bearing bushes.<br />
Use clean oil to lubricate the piston ring and the piston<br />
skirt.<br />
(e). As shown in the figure, rotate and adjust the positions<br />
of the piston ring openings.<br />
Each opening of piston ring shall not align at the piston pin and<br />
other openings of piston rings. If the opening position of piston<br />
ring is not correct, then the piston ring cannot correctly be<br />
(f). Use piston ring compressor to compress the piston<br />
rings to the working position.<br />
An annular cylinder can be self made with iron sheet if without<br />
special tools.<br />
Rotate the crankshaft to position the journal of<br />
connecting rod to be installed at bottom dead center.<br />
15B-134<br />
Put a thin clean oil on the wall of cylinder block.<br />
(i). Insert the connecting rod into the cylinder bore, till the<br />
piston ring compressor comes into contact with the top<br />
of the cylinder block<br />
• Align at the arrows of the top of piston to make it point at the<br />
front of engine.<br />
• The long end of connecting rod and the gap of piston skirt<br />
shall be on the exhaust side of engine, if not, please make<br />
sure that the piston is installed on the connecting rod.<br />
The engine will be seriously damaged if not according to<br />
the above operational steps.<br />
(j). Press the piston ring compressor to the cylinder block,<br />
insert the piston into the cylinder bore through the<br />
piston ring compressor, and align with the installation<br />
position of the connecting rod.<br />
If the piston can’t move smoothly, remove the piston and<br />
check the piston rings for breakage or damage.<br />
15B-135<br />
(k). Install the lower bush of the connecting rod bearing<br />
bush onto the connecting rod bearing bush cap.<br />
connecting rod cover and connecting rod bearing are<br />
clean, without any scrap. Do not lubricate the back face<br />
and side face of the connecting rod bearing.<br />
• If not replaced with new one, install the old bearing<br />
onto the original connecting rod cover from which it’s<br />
removed.<br />
grooves of the connecting rod cover.<br />
Use clean oil to lubricate the inner side of the lower<br />
bush of the connecting rod bearing bush.<br />
Install each connecting rod cover to corresponding<br />
journal of the crankshaft.<br />
15B-136<br />
The middle portion of the connecting rod and the head of<br />
the connecting rod cap are forged with markings. During<br />
assembly, face these markings towards the front of the<br />
engine (Pulley end)<br />
(n). Install and fasten the connecting rod nuts.<br />
• Fasten the nuts many times with torque wrench with the<br />
method of angle fastening.<br />
• Check whether the piston assembly is installed correctly.<br />
• Measure the gap between the connecting rod body and the<br />
crankshaft and the protrusion amount of the piston top<br />
respectively.<br />
If the piston, crankshaft, connecting rod or cylinder block<br />
is ever changed/replaced, it’s necessary to measure the<br />
protrusion amount of the piston on the combustion face of<br />
the cylinder block.<br />
The procedure is as below:<br />
• Install micrometer on the cylinder head and reset to<br />
zero.<br />
• Move the micrometer right above the top of the piston,<br />
in order to eliminate all lateral movements.<br />
• Rotate the crankshaft to the top dead center and then<br />
rotate the crankshaft clockwise and counter-clockwise,<br />
find out the maximum reading of the micrometer, and<br />
record the measurement result.<br />
15B-137<br />
INSTALLATION OF TAPPET, OIL INJECTION PIPE AND OIL PUMP<br />
1. Install tappet<br />
(a). Put clean oil and the equivalents on the tappet and<br />
tappet holes.<br />
(b). Install eight tappets on the installation holes one by<br />
one.<br />
• Make sure that the surface is clean and has no scratches<br />
before installation.<br />
• When installing the tappets, make sure that when<br />
installation holes incline at an angle of 45°~60°, the tappet<br />
slowly slide and do not have blockade phenomenon.<br />
2. Install oil Injection pipe<br />
(a). Install the oil Injection pipe in the specified position.<br />
Make sure the oil Injection pipe is clean especially the nozzle.<br />
Install the fixing bolts of oil Injection pipe and<br />
15B-138<br />
3. Install the oil pump assembly<br />
(a). Install the oil pump assembly in the specified position.<br />
When installing, put the lubricating oil on the oil pump gear.<br />
Connect the connection between oil pump’s oil outlet<br />
pipe and engine body.<br />
Install and fasten the fixing bolts of oil pump assembly.<br />
15B-139<br />
INSTALLATION OF ENGINE SUPPORT AND CAMSHAFT<br />
1. Install the engine support.<br />
(a). Install the engine right support to the specified position.<br />
Install and fasten four fixing bolts of the engine support.<br />
Install the left support with the same method.<br />
2. Install the camshaft.<br />
(a). Apply an appropriate amount of lubricating grease or<br />
equivalent lubricant onto the inner walls of the<br />
installation bore of the rear camshaft.<br />
When installing the camshaft, the engine can be placed<br />
vertically in order to avoid sliding the tappet and the<br />
engine body shall be placed with certain angle.<br />
(b). Apply an appropriate amount of lubricating grease or<br />
equivalent lubricant onto the cam of the camshaft and<br />
the journal.<br />
Before the installation, make sure that all machined surfaces<br />
are clean without any scratch.<br />
15B-140<br />
(c). Slowly install the camshaft in the specified position.<br />
• Before installing the camshaft, make sure that the<br />
tappet inserts completely in the tappet holes. If the<br />
tappets do not insert completely, the camshaft may be<br />
damaged when installing.<br />
• Rotate the camshaft and carefully insert the camshaft<br />
into the camshaft sleeve. When each camshaft journal<br />
passes through the sleeve, slightly lower the camshaft<br />
to fix the camshaft cam into the sleeve. Rotate the<br />
camshaft to separate the cam from the restraint of the<br />
sleeve, in order to install the camshaft smoothly.<br />
15B-141<br />
INSTALLATION OF GEAR CHAMBER AND OIL PAN<br />
1. Install the gear chamber<br />
(a). Install the gasket of gear chamber<br />
The gear chamber’s gasket shall be replaced. Clean the<br />
incomplete gaskets of engine body before replacing gasket.<br />
Install the timing gear chamber in the specified<br />
(c). Install and fasten the fixing bolts of timing gear<br />
Do not excessively screw up a bolt. The fixing bolts of timing<br />
gear chamber shall be screwed up alternately and gradually.<br />
2. Install oil pan<br />
(a). Paint sealant on the front and rear ends of oil pan.<br />
15B-142<br />
Paint sealant with right amount on the contact surface between<br />
oil pan and engine body.<br />
Install the front and rear ends of oil pan on the oil pan.<br />
(c). Install the oil pan to the specified position.<br />
Clean and check the thread and the sealing surface of the<br />
drainage screw plug and replace the damaged one (if any).<br />
During the installation of oil pan, use the front and rear fixing<br />
bolts of the oil pan to help the orientation.<br />
(d). Install and fasten the fixing bolts of oil pan.<br />
Cross fasten the fixing bolts of oil pan from the middle to the<br />
sides or from the sides to the middle, instead of excessively<br />
fastening any bolt by one time.<br />
15B-143<br />
FLYWHEEL ASSEMBLY AND CLUTCH COMPONENTS<br />
1. Install the Flywheel assembly.<br />
(a). Install the rear oil seal of crank in the specified position with special oil seal installer.<br />
The crank is sealed with frame oil seal with good sealing property and thread groove.<br />
Install the rear joint plate in the specified position and<br />
install the fixing bolts of rear joint plate.<br />
Install flywheel and flywheel bolt plate in the specified<br />
(d). Install the flywheel bolt in the specified position and<br />
fasten it.<br />
• Install the flywheel at the rear end of crank with 8 bolts to<br />
ensure the dependable installation strength.<br />
• When installing flywheel bolts, paint oil on bolts and contact<br />
surface then fasten them according to diagonal.<br />
2. Install the clutch components<br />
(a). Install the clutch friction plate and clutch plate in the<br />
specified position with positioning tool.<br />
15B-144<br />
Install the fixing bolts of clutch in the specified position<br />
and fasten them.<br />
15B-145<br />
CAMSHAFT GEAR AND IDLE PULLEY<br />
When installing the gear, one shall strictly align the gear with the mark without any mistake in case of<br />
the non-start, power decrease, oil consumption increase and even the unnecessary loss which may<br />
cause the damage of distribution device parts. When the marks of gears are indistinct or wear, the<br />
gear mechanism shall be displaced as a set or be repaired in a maintenance station of Beijing <strong>Foton</strong><br />
Environment Engine Co., Ltd if necessary.<br />
1. Install the camshaft gear<br />
(a). Install the front oil seal of camshaft gear on the<br />
camshaft gear.<br />
(b). Fasten the fixing bolt of camshaft gear front oil seal<br />
seat.<br />
After installing the front oil seal seat of camshaft gear, the<br />
flat key of camshaft gear also shall be installed on the<br />
camshaft in case of omission.<br />
(c). Install the camshaft pulley flange plate on the front oil<br />
seal seat of camshaft.<br />
Install the camshaft pulley flange plate correctly and make the<br />
location pin through pin hole.<br />
Install the pressure plate onto the specified position.<br />
15B-146<br />
Fasten the bolt of pressure plate.<br />
(f). Install the camshaft gear to the specified position.<br />
When installing the camshaft gear, the groove of camshaft<br />
gear shall be aligned and the pin hole of camshaft shall be<br />
installed align with the location pin.<br />
(g). Fasten the fixing bolt of camshaft pulley.<br />
• When fastening the camshaft gear bolt, the camshaft gear<br />
will revolve with it. For this reason, one shall locate the<br />
camshaft gear with special locator instead of wrench.<br />
• According to the actual situation, one may also use tools<br />
such as screwdriver and solid wrench to locate the<br />
2. Install the idle pulley<br />
(a). Install the bolt equipped with location skirt and the<br />
timing belt transition wheel assembly together.<br />
Install the location skirt and the timing belt transition<br />
wheel assembly into the gear chamber.<br />
15B-147<br />
Fasten the location skirt bolt.<br />
Install the tensioner assembly and hexagon flange locating bolt<br />
into the gear chamber with the same method and fasten them.<br />
The tensioned shall be fastened again when installing in<br />
order to facilitate the following adjustment of belt. It<br />
means to slightly fastening it.<br />
Install the tensioning pull rod onto the gear chamber.<br />
When installing the tensioning pull rod, one shall install the<br />
internal teeth serrated lock washer, hexagon flange nut and the<br />
bolt equipped with locating rod onto the tensioning pull rod all<br />
15B-148<br />
INSTALLATION OF INJECTION PUMP ASSEMBLY<br />
1. Install the injection pump assembly<br />
(a). Install the injection pump pulley, injection pump flange<br />
and injection pump onto the gear chamber.<br />
Install the injection pump onto the gear chamber from the rear<br />
of gear chamber.<br />
The timing marks on the injection pump pulley shall be<br />
installed aligning with the timing marks on gear chamber.<br />
Fasten the fixing bolt of injection pump assembly.<br />
15B-149<br />
INSTALLATION OF TIMING BELT AND PRESSURE PLATE<br />
1. Install the timing belt<br />
(a). Install the timing belt to the specified position.<br />
(b). Adjust the tension of timing belt with special tools and<br />
When the tension of belt being adjusted to proper position, one<br />
shall just Fasten the hexagon flange locating bolt.<br />
Fasten the fixing bolt of tensioning pull rod.<br />
2. Install the pressure plate<br />
(a). Install the pressure plate of injection pump pulley.<br />
15B-150<br />
Install and fasten the fixing bolt of injection pump pulley<br />
Install the pressure plate of camshaft pulley.<br />
Install and fasten the fixing bolt of camshaft pulley<br />
15B-151<br />
INSTALLATION OF WATER PUMP PULLEY CHAMBER COVER<br />
ASSEMBLY AND OBSERVATION CHAMBER COVER<br />
1. Install the cover assembly of water pump pulley<br />
chamber<br />
(a). Install the cover assembly of water pump pulley<br />
chamber onto the gear chamber.<br />
Install and fasten the fixing bolt of water pump pulley<br />
chamber cover assembly.<br />
2. Install the observation room cover<br />
(a). Install the observation room cover to the specified<br />
Install and fasten the fixing bolt of observation room<br />
15B-152<br />
INSTALLATION OF THE CRANKSHAFT PULLEY AND THE FAN<br />
1. Install the crankshaft pulley<br />
(a). Install the crankshaft pulley to the specified position.<br />
When installing the crankshaft pulley, in order to avoid the<br />
Disassembly of crankshaft pulley due to the crankshaft pulley<br />
rotating together with it, one shall firstly secure the flywheel<br />
with flywheel locator or other equivalent objects. Meanwhile,<br />
one shall smear oil onto the bolt threads.<br />
Install and fasten the crankshaft pulley bolt.<br />
2. Install the fan<br />
(a). Install the fan assembly to the specified position.<br />
(b). Install and fasten the fixing nuts of fan assembly.<br />
Clamp the double-end strut backward with screwdriver and<br />
fasten the sideward nut with wrench.<br />
15B-153<br />
INSTALLATION OF HIGH PRESSURE FUEL RAIL AND STARTER<br />
MOTOR<br />
1. Install the high pressure fuel rail assembly<br />
(a). Install the high pressure fuel rail assembly to the<br />
specified position<br />
Install and fasten the fixing bolt of high pressure fuel<br />
rail assembly.<br />
2. Install the starter motor<br />
(a). Install the starter motor onto the rear cover plate of<br />
cylinder block.<br />
When installing the starter motor, the bolt hole of starter motor<br />
shall be aligned to the bolt hole of cylinder block rear cover<br />
Install and fasten the fixing bolt of starter motor.<br />
15B-154<br />
INSTALLATION OF HOOK AND A/C BRACKET<br />
1. Install the hook.<br />
(a). Install the hook to the specified position and ensure the<br />
alignment of it with the installation hole.<br />
Install and fasten the fixing bolt of hook.<br />
2. Install the A/C bracket<br />
(a). Install the A/C bracket to the specified position and<br />
ensure the alignment of it with the installation hole.<br />
(b). Install and fasten the fixing bolt of A/C bracket.<br />
15B-155<br />
INSTALLATION OF VALVE AND THERMOSTAT ASSEMBLY<br />
1. Install the valve assembly<br />
(a). Lubricate the valve guide pipe hole and the outer wall<br />
of valve guide pipe which are required to be replaced<br />
with lubricating oil.<br />
The lubrication for the outer wall of air guide pipe is conducted<br />
to make it installing into the cylinder head guide pipe hole.<br />
(b). Knock the valve guide pipe into the inside from the top<br />
of cylinder head with special tool.<br />
The outer surface of valve guide pipe shall be covered<br />
with oil when installing. Also, one shall install the valve<br />
guide pipe and check the height of it.<br />
(c). Lubricate all the valve guide pipe hole and the valve<br />
stem with oil.<br />
• Without the lubrication for the valve guide pipe and valve<br />
stem, the valve guide will be worn early.<br />
• Before installing the valve, one shall lubricate the valve<br />
(d). Install the valve and install the valve oil seal onto the<br />
valve guide pipe with installer for valve oil seal.<br />
• If the valve isn’t replaced, one shall install the valve at<br />
the same position of the valve disassembly.<br />
• If the cylinder head will not be applied immediately, one<br />
shall also lubricate the valve stem with assembly<br />
lubricating agent or equivalent object.<br />
• The valve oil seal shall be replaced when it is<br />
disassembled.<br />
15B-156<br />
Install the lower seat of upper valve spring, valve spring<br />
and the upper seat of valve spring.<br />
Compress the valve spring with the valve<br />
springcompressor to expose the installation position of<br />
valve lock clamp.<br />
(g). Install the upper valve lock clamp, release the valve<br />
spring and lock the valve with valve lock clamp.<br />
After assembly, one shall knock the valve spring seat with<br />
rubber hammer to ensure the correct installations of locking<br />
• If the lock clamp is installed improperly, the lock clamp<br />
will dash off when knocking the valve spring seat with<br />
plastic hammer.<br />
(h). Install all the valves with the same method.<br />
2. Install the thermostat assembly<br />
(a). Install and fasten the thermostat housing assembly and<br />
fixing bolt to the specified position.<br />
15B-157<br />
Install the thermostat.<br />
Install and fasten the outlet pipe assembly and fixing<br />
bolt.<br />
15B-158<br />
INSTALLATION OF CYLINDER HEAD COVER AND TAPPET<br />
1. Install the cylinder head assembly.<br />
(a) Lubricate the bolts with clean oil.<br />
Install the gasket of the cylinder head to the specified<br />
(c). Align the installed cylinder head with the specified<br />
or assembly.<br />
(d). Install and fasten the fixing bolts of the cylinder head<br />
Lubricate the threads and lower part of end of fixing bolt with<br />
clean oil.<br />
15B-159<br />
Fasten the fixing bolts of the cylinder head to the specified<br />
torque by several times as per sequence shown in left<br />
figure.<br />
2. Install the tappet<br />
(a). Fill clean oil into the installation position hole of each<br />
valve tappet.<br />
(b). Install the valve tappets to the specified position one by<br />
Be sure that the installation position and removing position of<br />
each valve tappet are same.<br />
15B-160<br />
INSTALLATION OF ROCKSHAFT AND CYLINDER HEAD COVER<br />
1. Install the rockshaft assembly.<br />
(a). Before installing the rocker assembly, the clean oil shall<br />
be dropped into each bowl-shape groove of tappet.<br />
(b). Install the rocker assembly to the specified position.<br />
It shall be handled with care when installing. The alignment<br />
with installation hole shall also be ensured.<br />
(c). Install the fixing bolt of rocker assembly.<br />
Temporarily, the installed bolt will not be fastened in order till<br />
the installation completion of the fixing nut of rocker assembly.<br />
(d). Adjust the clearance of valve (see Chapter 15B Valve<br />
of Engine Mechanical Part, Adjustment)<br />
2. Install the electric heater plug assembly<br />
(a). Install and fasten four electric heater plug assemblies.<br />
15B-161<br />
3. Install the cylinder head cover assembly<br />
(a). Install the cylinder hear cover assembly to the specified<br />
Install and fasten the fixing nuts of the cylinder head<br />
15B-162<br />
INSTALLATION OF INTAKE AND EXHAUST MANIFOLDS AND<br />
TURBOCHARGER<br />
1. Install the intake and exhaust manifolds<br />
(a). Install the intake manifold gasket and the intake<br />
manifold to the specified position.<br />
The gasket of intake manifold shall be replaced by a new<br />
Install and fasten the fixing bolt of intake manifold.<br />
(c). Install the exhaust manifold gasket and exhaust<br />
manifold to the specified positions.<br />
One shall remember to install the ring and heat shield fixed<br />
together with the exhaust manifold when installing the exhaust<br />
Install and fasten the fixing bolt of exhaust manifold to<br />
15B-163<br />
2. Install the turbocharger<br />
(a). Install the turbocharger assembly to the specified<br />
Install the heat shield assembly.<br />
Install the turbocharger into the oil return pipe.<br />
15B-164<br />
INSTALLATION OF BREATHER AND DIPSTICK<br />
1. Install the breather<br />
(a). Install the breather bracket to the specified position.<br />
Install and fasten the fixing bolt of breather bracket.<br />
(c). Install the breather onto the breather bracket.<br />
The breather is installed inside the starter.<br />
Install and fasten the fixing bolt of breather.<br />
15B-165<br />
2. Install the dipstick<br />
(a). Install the dipstick to the specified position.<br />
Plug the lower port of dipstick assembly in the installation hole<br />
of dipstick when installing.<br />
Install the fixing bolt of dipstick and connect the<br />
connection of dipstick and the oil return pipe of<br />
breather.<br />
15B-166<br />
INSTALLATION OF FUEL INJECTOR AND HIGH & LOW PRESSURE<br />
FUEL PIPE<br />
1. Install the fuel injector<br />
(a). Install the fuel injector and the pressure plate of fuel<br />
injector together, install them to the specified position<br />
and install the fixing bolt fastening the fuel injector<br />
In case of unnecessary troubles caused by the falling off of<br />
copper washer when installing the fuel injector, the copper<br />
washer shall be covered with a little lithium oil when installing.<br />
2. Install the low pressure fuel pipe<br />
(a). Install the low pressure fuel pipe to the specified<br />
Push the clamp of low pressure fuel pipe in the direction of<br />
openness, install it onto the fuel injector and connect the<br />
connection of low pressure fuel pipe and fuel injector.<br />
3. Install high pressure fuel pipe<br />
(a). Connect the connection of high pressure fuel pipe and<br />
fuel rail.<br />
As for the installation of high pressure fuel pipe, one shall<br />
embed the lower end of intake manifold into the high pressure<br />
fuel pipe and shall not remove the cover of high pressure fuel<br />
pipe connector early.<br />
(b). Connect the connectors of high pressure fuel pipe and<br />
fuel injector and fasten the nut.<br />
Currently, the high pressure fuel pipe can be fastened couple<br />
by couple.<br />
15B-167<br />
Install the high pressure fuel pipe between the injection<br />
pump and the high pressure fuel rail and fasten the nut.<br />
15B-168<br />
GENERATOR AND OIL FILTER<br />
1. Install the generator<br />
(a). Install the generator assembly to the specified position<br />
and install the fixing bolt fastening the lower end of<br />
generator.<br />
When installing the fixing bolt, one shall hold up the<br />
generator with a hand in case of the damage of generator<br />
caused by falling of generator due to the lack of bracing<br />
force.<br />
Adjust the position of generator and install the<br />
generator belt.<br />
(c). Install the adjusting bolt on the upper end of generator.<br />
Do not screw up the adjusting bolt of the generator too tightly<br />
when installing to facilitate the adjustment of generator belt.<br />
(d). Adjust the belt tension by adjusting the position of<br />
Press the generator belt with great force to check whether the<br />
belt is installed in place.<br />
Reference Standard: 39N. The deflection is about 10~15mm.<br />
15B-169<br />
Be sure the generator belt is installed in place and<br />
fasten the adjusting bolt of generator.<br />
Connect the oil inlet and outlet pipe of vacuum pump at<br />
the rear end of generator.<br />
2. Install the oil filter assembly.<br />
(a) Install the oil filter assembly to the specified position.<br />
Install and fasten the fixing bolts of oil filter assembly.<br />
Connect the connection of oil filter coolant pipe.<br />
15B-170<br />
INSTALLATION OF PIPELINE AND HARNESS<br />
1. Install the harness of engine<br />
(a). According to the installation position relation, the<br />
generator ECU harness shall be installed in place one<br />
by one.<br />
2. Install the intake connecting pipe<br />
(a). Install the intake connecting pipe to the specified<br />
position and fasten the fixing bolt of it.<br />
3. Install the turbo-supercharging intake pipe<br />
(a). Install and fasten the turbocharger intake connecting<br />
pipe assembly and the fixing bolts of it.<br />
4. Install the breather pipeline<br />
(a). Install and connect the intake pipe of breather.<br />
15B-171<br />
Install and connect the exhaust pipe of breather.<br />
Install the clamp connecting the exhaust pipe of<br />
breather and the intake hose of turbocharger and<br />
connect to the connector of breather intake hose.<br />
5. Install the EGR pipeline<br />
(a). Install the EGR pipe to the specified position.<br />
Install and fasten the fixing bolt connecting with the<br />
EGR pipe and exhaust pipe.<br />
Install 2 fixing nuts connecting with the EGR pipe and<br />
intake pipe.<br />
15B-172<br />
ENGINE MECHANICAL PART-DISASSEMBLY OF ENGINE<br />
DISASSEMBLY OF ENGINE (4D20)<br />
2. Before removing the engine, place the engine assembly onto the disassembly stand or place on one<br />
ENGINE MECHANICAL PART- DISASSEMBLY OF ENGINE<br />
15B-173<br />
DISASSEMBLY OF HEATER AND WATER OUTLET-INLET PIPE<br />
WELDMENT<br />
1. Disassemble the weldment of heater and water<br />
outlet-inlet pipe<br />
(a). Disassemble the fixing bolt of heater and water<br />
outlet-inlet pipe weldment.<br />
Disassemble the rubber hose connecting with the<br />
heater and water outlet-inlet pipe weldment and the<br />
thermostat.<br />
Take down the heater and water outlet-inlet pipe<br />
weldment.<br />
15B-174<br />
DISASSEMBLY OF CYLINDER HEAD COVER<br />
1. Disassemble the cylinder head cover<br />
(a). Disassemble the fixing nut of cylinder head cover.<br />
15B-175<br />
DISASSEMBLY OF EGR CONTROLLER<br />
1. Disassemble the EGR controller<br />
(a). Disconnect the connection of EGR valve vacuum<br />
Disconnect the connection of preheat controller oil inlet<br />
(c). Disassemble the fixing bolt of air compressor bracket<br />
and take down the fixing bracket of air compressor.<br />
• In order to facilitate the disassembly, the air compressor<br />
fixing bracket and EGR controller shall be taken down<br />
Before taking down the air compressor bracket, the<br />
connection between the generator and EGR controller<br />
vacuum pipeline shall also be disconnected.<br />
15B-176<br />
(d). Disassemble the fixing bolt of EGR controller and take<br />
down EGR controller.<br />
15B-177<br />
DISASSEMBLY OF INTAKE AND EXHAUST MANIFOLDS AND<br />
1. Disassemble the intake and exhaust manifolds<br />
(a). Disassemble the fixing bolt of intake and exhaust<br />
manifolds.<br />
(b). Disassemble the fixing bolt connecting with EGR valve<br />
connecting pipe weldment and the exhaust manifold.<br />
(c). Disassemble the fixing bolt connecting with EGR valve<br />
and intake manifold.<br />
Take down EGR valve connecting pipe weldment.<br />
15B-178<br />
(e). Disassemble the fixing bolt of turbocharger oil inlet pipe<br />
Disconnect the connection of turbocharger oil return<br />
rubber hose.<br />
(g). Take down the intake and exhaust manifolds and<br />
In order to facilitate the Disassembly of generator, the intake<br />
and exhaust manifolds and turbocharger shall be taken down<br />
altogether.<br />
(h). Take down the washers of intake and exhaust<br />
It is not proper to reuse the disassembled washers. They shall<br />
be replaced by new washers.<br />
Disassemble the rubber hose clamp connecting with<br />
turbocharger and intake manifold and disconnect its<br />
15B-179<br />
Take down the intake manifold assembly.<br />
2. Disassemble the turbocharger<br />
(a). Disassemble the fixing bolt of turbocharger air inlet<br />
port.<br />
(b). Disassemble the fixing bolt connecting with the<br />
turbocharger and its bracket.<br />
Take down the turbocharger and its gasket.<br />
15B-180<br />
DISASSEMBLY OF GENERATOR AND BREATHER<br />
1. Disassemble the generator assembly<br />
(a). Disassemble the fixing bolt of vacuum pump oil inlet<br />
pipe assembly.<br />
Disassemble the fixing clamp of vacuum pump oil<br />
return pipe and disconnect the connection of oil return<br />
Disassemble the adjusting bolt of generator and<br />
release the whole tension of belt.<br />
(d). Disassemble the fixing bolt of generator.<br />
• In order to prevent the direction of bolt rotating with the force<br />
when removing, one shall firstly lock the bolt and then<br />
disassemble the nut of fixing bolt.<br />
• When removing the fixing bolt, one shall hold up the<br />
generator with a hand in case of generator damages or<br />
personal injuries caused by the falling off of generator due<br />
to the lack of bracing force.<br />
15B-181<br />
Take down the generator assembly.<br />
Disassemble the fixing bolt of generator bracket and<br />
take down the bracket on generator.<br />
take down the generator lower bracket.<br />
2. Disassemble the breather<br />
(a). Disassemble the fastening clamp of lower oil return<br />
pipe of breather and disconnect the connection of lower<br />
oil pipe.<br />
(b). Disassemble the fixing bolt of breather.<br />
15B-182<br />
15B-183<br />
DISASSEMBLY OF FAN, FAN PULLEY AND CRANKSHAFT PULLEY<br />
(a). Disassemble the fixing nut of fan assembly.<br />
• When removing, the fan will rotate in the direction of force.<br />
In order to prevent this, the stud shall be clamped in a<br />
reverse direction with a screwdriver.<br />
• All nuts removed shall be centrally placed, in order to<br />
prevent loss<br />
Take down the fan pulley.<br />
Take down the fan and its pulley.<br />
(a). Disassemble the fixing bolt of crankshaft pulley.<br />
15B-184<br />
Take down the crankshaft pulley.<br />
15B-185<br />
DISASSEMBLY OF DIPSTICK<br />
(a). Disassemble the fixing bolt of dipstick bracket.<br />
Remove the dipstick<br />
15B-186<br />
DISASSEMBLY OF HIGH & LOW PRESSURE FUEL PIPE AND FUEL<br />
INJECTOR<br />
(a). Disconnect the connection with high pressure fuel pipe<br />
and fuel injector.<br />
Disconnect the connection of high pressure pipeline<br />
and high pressure oil pump.<br />
Take down the high pressure fuel pipe.<br />
Disconnect the connection with low pressure rubber<br />
15B-187<br />
Take down each low pressure rubber fuel pipe<br />
connecting to fuel injectors successively.<br />
2. Disassemble the fuel injector<br />
(a). Disassemble the fixing bolts of fuel injector pressure<br />
plate successively.<br />
Take down the fuel injector pressure plate and fuel<br />
injector successively.<br />
15B-188<br />
DISASSEMBLY OF ROCKSHAFT AND TAPPET<br />
1. Disassemble the rockshaft<br />
(a). Disassemble the fixing bolts and nuts of rockshaft.<br />
• Do not disassemble a certain bolt or nut at a time. On e shall<br />
uniformly disassemble the fixing bolts or nuts of rockshaft<br />
for several times.<br />
• All bolts and nuts removed shall be centrally placed, in order<br />
to prevent loss.<br />
Take down the rockshaft.<br />
2. Disassemble the tappet<br />
(a). Take out the tappets successively and place them<br />
centrally.<br />
15B-189<br />
DISASSEMBLY OF CYLINDER HEAD<br />
1. Disassemble the cylinder head<br />
(a). Disassemble the connecting hose clamp of oil radiator<br />
and cylinder head, disconnect the hose connection and<br />
take down the hose.<br />
Disassemble the rubber hose connecting with the water<br />
pump and thermostat.<br />
(c). Disassemble the fixing bolt of cylinder head.<br />
When removing, the cylinder head bolt shall be<br />
disassembled once a couple for several times as the<br />
sequence from middle to two sides.<br />
(d). Remove the cylinder head assembly<br />
15B-190<br />
DISASSEMBLY OF THE WATER OUTLET PIPE CONNECTOR,<br />
VALVE AND HOOK<br />
1. Remove the water outlet pipe connector.<br />
(a). Remove the fixing bolts of water outlet pipe connector.<br />
Remove the water outlet pipe connector.<br />
2. Remove the valve<br />
(a). Compress the valve spring with valve spring<br />
compressor to expose the installation location of valve<br />
lock clamp.<br />
(b). Remove the valve lock clamp<br />
To prevent causing personal injuries, please wear the<br />
goggles.<br />
15B-191<br />
(c). Remove the valve spring upper seat, valve spring, and<br />
valve spring lower seat and remove the valve oil seal.<br />
The oil seal removed can’t be reused and shall be replaced<br />
with new one.<br />
Remove the valve<br />
(e). Remove the valve guide with special disassembly tool.<br />
The valve guide removed can’t be reused. Therefore, remove<br />
the valve guide depending on the actual condition.<br />
3. Remove the hook.<br />
(a). Remove the fixing bolts of front hook.<br />
Remove the front hook.<br />
Remove the rear hook as per same method.<br />
15B-192<br />
DISASSEMBLY OF OIL FILTER AND OIL RADIATOR<br />
1. Disassemble the oil filter<br />
(a). Disassemble the connecting pipe weldment fixing bolt<br />
of oil radiator and oil filter.<br />
(b). Disassemble the fixing bolt of oil filter.<br />
Take down the oil filter.<br />
(d). Disassemble the fixing bolt connecting with the<br />
connecting pipe weldment and oil radiator.<br />
15B-193<br />
(e). Take down the O-ring of weldment and the weldment of<br />
connecting pipe.<br />
It is not proper to reuse the disassemble O-ring. It shall be<br />
replaced by a new one.<br />
(f). Disassemble the fixing bolt of oil radiator.<br />
Take down the oil radiator.<br />
15B-194<br />
1. Remove the Clutch Components.<br />
(a) Remove the fixing bolts of clutch.<br />
Remove the clutch disc and clutch cover components.<br />
2. Remove the flywheel assembly.<br />
(a). Remove the fixing bolts of clutch.<br />
(b). Remove the flywheel assembly.<br />
Caution shall be taken during the removal, as the flywheel has<br />
certain weight.<br />
15B-195<br />
(c). Remove the fixing bolts of support rear cover.<br />
Remove the support rear cover.<br />
Remove the sealing strip of rear oil seal cover.<br />
15B-196<br />
DISASSEMBLY OF OIL PAN AND OIL PUMP<br />
1. Remove the oil pan.<br />
(a). Overturn the engine body.<br />
The oil shall be completely discharged in prior of the<br />
Disassembly of oil pan.<br />
(b). Disassemble the fixing bolt of oil pan.<br />
• When removing, the fixing bolt of oil pan shall be<br />
disassembled in a crossing way as the sequence from<br />
middle to two sides and then the sequence from two sides<br />
to middle.<br />
Take down the oil pan.<br />
2. Disassemble the oil pump<br />
(a). Disassemble the fixing bolt of oil pump driving gear<br />
chamber cover.<br />
15B-197<br />
Take down the cover and take out the driving gear of oil<br />
(c). Disassemble the fixing bolt of oil pump.<br />
(d). Take out the oil pump.<br />
Take out slowly and avoid the impact.<br />
15B-198<br />
DISASSEMBLY OF OIL SEAL COVER AND OIL SEAL<br />
1. Remove the oil seal cover and oil seal.<br />
(a). Remove the fixing bolts of the oil seal cover.<br />
Remove the oil seal and the oil seal cover.<br />
Separate the oil seal from the oil seal cover.<br />
15B-199<br />
DISASSEMBLY OF GEAR CHAMBER COVER, INJECTION PUMP<br />
AND WATER PUMP ASSEMBLY<br />
1. Disassemble the gear chamber cover<br />
(a). Disassemble the fixing bolt of gear chamber cover.<br />
(b). Take down the injection pump gear chamber cover.<br />
(c). Take down the gear chamber cover and the gasket.<br />
2. Disassemble the injection pump<br />
(a). Disassemble the fixing bolt of injection pump gear.<br />
15B-200<br />
Disassemble the injection pump gear with an extractor.<br />
(c). Disassemble the fixing bolt of injection pump.<br />
(d). Disassemble the fixing bolt connecting with injection<br />
pump and injection pump bracket.<br />
• When removing, the injection pump shall be hold up with a<br />
hand in case of damage or personal injuries due to the<br />
falling of pump.<br />
(e). Take down the injection pump.<br />
Take it out carefully and avoid the impact.<br />
3. Remove the water pump components<br />
(a). Remove the fixing bolts of the water pump<br />
components.<br />
15B-201<br />
(b). Remove the water pump components and water pump<br />
gasket.<br />
It is not proper to reuse the disassembled gasket. It shall be<br />
15B-202<br />
DISASSEMBLY OF CAMSHAFT GEAR AND CRANKSHAFT GEAR<br />
1. Disassemble the camshaft gear<br />
(a). Disassemble the fixing bolt of camshaft gear.<br />
(b). Take down the camshaft gear.<br />
Do not forget to take down the woodruff key.<br />
(c). Disassemble the fixing bolt of camshaft pressure plate.<br />
Take down the pressure plate of camshaft.<br />
15B-203<br />
2. Disassemble the crankshaft gear<br />
(a). Take down the oil baffle disk.<br />
(b). Take down the crankshaft gear and the woodruff key.<br />
• Do not forget to take down the woodruff key.<br />
• All woodruff keys removed shall be centrally placed, in<br />
order to prevent loss.<br />
15B-204<br />
DISASSEMBLY OF CAMSHAFT, PISTON AND CRANKSHAFT<br />
1. Disassemble the camshaft<br />
(a). Turn over the engine body and take out the camshaft.<br />
• Take out the camshaft without influencing the tappet.<br />
• The camshaft shall be taken out by slowly revolving.<br />
(b). Take out the tappets successively.<br />
• Draw out the tappets from their installation positions<br />
successively with high performance magnet.<br />
• The tappet taken out shall be put in a clean vessel.<br />
2. Disassemble the piston assembly<br />
(a). Rotate the crankshaft to locate the journal of<br />
disassembled connecting rod on the bottom dead<br />
center.<br />
(b). Disassemble the fixing nut of connecting rod cover.<br />
Unscrew every two nuts a time.<br />
15B-205<br />
Lightly shake and pull out the connecting rod cover and<br />
remove the connecting rod bearing bush.<br />
Remove the carbon deposit from the piston cylinder.<br />
(e). Push out the piston assembly<br />
face of connecting rod<br />
(f). Remove the piston assembly from the other side.<br />
Install the piston assembly removed together, add the marking,<br />
and place into a clean container.<br />
(g). Remove the pistons of other cylinders as per same<br />
method.<br />
3. Remove the crankshaft assembly.<br />
(a). Loosen the bolts of main bearing cap in turn.<br />
15B-206<br />
(b). Take down the main bearing cap and align them in<br />
Take down the main bearing bush.<br />
(d). Lift out the crankshaft<br />
This part is a little heavy. To prevent causing serious personal<br />
(e). Remove the upper bushes of the main bearing bushes.<br />
Take out every upper bush successively and mark the cylinder<br />
number at the movable lug.<br />
15B-207<br />
(f). Take down the crankshaft thrust halfring.<br />
Take down the crankshaft thrust halfring and mark the<br />
installation position and its front and back to facilitate the<br />
correct installation when assembling.<br />
15B-208<br />
ENGINE MECHANICAL PART- ASSEMBLY OF ENGINE<br />
ASSEMBLY OF ENGINE (4D20)<br />
INTRODUCTION OF ASSEMBLY<br />
15B-209<br />
INSTALLATION OF CRANKSHAFT, PISTON AND CAMSHAFT<br />
(a). Face upward the cylinder block crankcase and place<br />
(b). Install the thrust halfring of crankshaft<br />
There are only two thrust halfrings for this engine, installing at<br />
the 4th main bearing bush of cylinder block.<br />
The oil groove shall face outward when installing the<br />
thrust halfrings.<br />
(c). Install the upper bushes of the main bearing bushes to<br />
the specified positions.<br />
bushes to the specified positions in turn and ensure that<br />
the back faces of the bearing bushes are clean without<br />
any scrap. The upper bush of each main bearing bush<br />
shall be in the center position of the bearing bush groove<br />
and the top faces of all bearing bushes shall be level<br />
• After installation, the inside of bearing bush arching<br />
surface shall be evenly covered with proper amount of oil<br />
or equivalent.<br />
15B-210<br />
(d). Drip clean oil or equivalent to the inner side of the main<br />
bearing bushes.<br />
(f). After the installation of crankshaft, drop clean oil or<br />
equivalent onto the main journal of the crankshaft and<br />
rotate the crankshaft to lubricate its surfaces.<br />
15B-211<br />
(h). Install the main bearing cap and its fixing bolts in order.<br />
• Install the main bearing cap to its original position when<br />
removing as the mark without any mistake.<br />
• There are identification numbers on main bearing cap of<br />
each crankshaft. The installation shall be conducted in order<br />
without any mistake.<br />
When placing the crankshaft main bearing cap onto the<br />
main bearing seat of crank case, the arrow on each cover<br />
shall point to the front (the direction of pulley)<br />
(i). Screw up the main bearing bolt according to some<br />
sequence and torque.<br />
• Do not screw up the bolt at one time. The bolt shall be<br />
screwed up a little and generally be fastened to the<br />
specified torque.<br />
• The main bearing bolt shall be fastened according to a<br />
certain sequence (see left diagram)<br />
15B-212<br />
(a). Install the connecting rod bolts to the connecting rod.<br />
In prior of assembly, the cylinder block and all of the parts shall<br />
be clean. The connecting rod and bearing bush shall be<br />
cleaned with a piece of clean and lint-free cloth.<br />
Make sure that the back faces and side faces of the<br />
without any scrap. Do not lubricate the back face and side<br />
face of the connecting rod bearing.<br />
Drip clean oil or equivalent oil to the inner side of the<br />
15B-213<br />
The opening of each piston ring can’t be aligned with the<br />
opening of the piston pin or other piston rings, otherwise the<br />
piston rings can’t achieve correct sealing effect.<br />
One can make a piston ring with iron sheet without any special<br />
Side overturn the cylinder block and apply one film of<br />
clean oil onto the walls of the cylinder block<br />
15B-214<br />
Insert the connecting rod into the cylinder bore, till the<br />
• Align the arrow on the top of the piston with the front of the<br />
• The longer end of the connecting rod and the notch on the<br />
piston skirt shall be at the exhaust side of the engine. If not,<br />
verify whether the piston is at the correct installation<br />
position on the connecting rod.<br />
The failure to install as per above procedure will lead to<br />
serious damage of the engine.<br />
15B-215<br />
(m). Install each connecting rod cover to corresponding<br />
The middle portion of the connecting rod and the head of the<br />
connecting rod cap are forged with markings. During assembly,<br />
face these markings towards the front of the engine (Pulley<br />
end).<br />
(n). Install the connecting rod nuts.<br />
Use torque wrench to fasten the nuts by two times as per<br />
angular fastening method.<br />
Specified Torque:<br />
(o). Check whether the piston assembly is installed<br />
correctly<br />
• Measure the gap between the connecting rod body<br />
and the crankshaft and the protrusion amount of the<br />
piston top respectively.<br />
Measure the gap between the connecting rod body and the crankshaft and the protrusion amount of the<br />
If the piston, crankshaft, connecting rod or cylinder block is ever changed/replaced, it’s necessary to<br />
measure the protrusion amount of the piston on the combustion face of the cylinder block.<br />
• Install micrometer on the cylinder head and reset to zero.<br />
• Move the micrometer right above the top of the piston, in order to eliminate all lateral movements.<br />
15B-216<br />
• Rotate the crankshaft to the top dead center and then rotate the crankshaft clockwise and<br />
counter-clockwise, find out the maximum reading of the micrometer, and record the measurement<br />
result.<br />
The volume of bulge on the top of piston<br />
3. Install the camshaft assembly<br />
(a). Install the tappet into a specified installation hole<br />
successively.<br />
When installing the camshaft, instead of being placed<br />
vertically, the engine body shall be placed at a certain<br />
angle in case of gliding downward of tappet.<br />
(c). Apply an appropriate amount of lubricating grease or<br />
(d). Rotate and install the camshaft to the specified<br />
to fix the camshaft cam into the sleeve.<br />
• Rotate the camshaft to separate the cam from the<br />
restraint of the sleeve, in order to install the camshaft<br />
smoothly.<br />
15B-217<br />
Install the camshaft pressure plate to a specified<br />
(f). Install and fasten the fixing bolt of camshaft pressure<br />
Rotate the camshaft to check whether the cam shaft can rotate<br />
freely<br />
If the camshaft can’t rotate freely, do not rotate the<br />
camshaft with force, or it will damage the camshaft sleeve.<br />
Analyze the cause and reassemble the camshaft.<br />
15B-218<br />
INSTALLATION OF OIL SEAL AND OIL SEAL COVER<br />
1. Install the oil seal and the oil seal cover.<br />
(a) Install the oil seal and the oil seal cover together.<br />
Apply oil onto the lips of the oil seal.<br />
Install the oil seal and the oil seal cover to the specified<br />
positions.<br />
(d). Install and fasten the fixing bolts of the oil seal cover.<br />
Cross fasten the bolts from the middle to the sides or from the<br />
sides to the middle, instead of excessively fastening any bolt<br />
by one time.<br />
15B-219<br />
INSTALLATION OF CRANKSHAFT GEAR AND CAMSHAFT GEAR<br />
Environment Engine Co., Ltd when necessary.<br />
1. Install the crankshaft gear<br />
(a). Install the crankshaft gear to the specified position.<br />
When installing the crankshaft gear, the woodruff key shall<br />
be installed to the specified position. Also, it shall be<br />
installed aligning with the installation mark to ensure the<br />
correctness of installation.<br />
Install the oil baffle disk to a specified position.<br />
2. Install the camshaft gear<br />
(a). Install the camshaft gear to a specified position.<br />
Before installing the camshaft gear, the woodruff key of<br />
camshaft shall be installed to the specified position.<br />
Install and fasten the fixing bolt of camshaft gear.<br />
15B-220<br />
INSTALLATION OF INJECTION PUMP AND GEAR CHAMBER<br />
1. Install the injection pump<br />
(a). Install the injection pump to the specified position<br />
The marks made when removing shall be aligned with<br />
when installing to ensure the installation correctness.<br />
(b). Install and fasten the fixing bolt of injection pump.<br />
One shall hold up the injection pump with a hand when<br />
installing in case of the damages or personal injuries caused<br />
by the falling of pump.<br />
Install and fasten the fixing bolt connecting with<br />
injection pump and its bracket.<br />
(d). Install the injection pump gear to the specified position.<br />
The installation marks shall be aligned with when installing to<br />
ensure the installation correctness.<br />
15B-221<br />
Install and fasten the fixing nut of injection pump gear.<br />
2. Install the gear chamber cover<br />
(a). Install the gear chamber gasket and gear chamber<br />
cover to the specified position.<br />
The gasket of gear chamber shall be replaced by a new one.<br />
Install and fasten the fixing bolt of gear chamber.<br />
Install the injection pump gear chamber cover to the<br />
specified position and Install and fasten the fixing bolt.<br />
15B-222<br />
INSTALLATION OF OIL PUMP AND OIL PAN<br />
1. Install the oil pump assembly.<br />
(a). Install the oil pump assembly to the specified position.<br />
(c). Install the oil pump driving gear to the specified position<br />
and install the oil pump driving gear cover.<br />
Be sure the oil pump driving gear and the oil pump propeller<br />
shaft are all installed in place.<br />
Install and fasten the fixing bolt of cover.<br />
15B-223<br />
2. Install the oil pan.<br />
(a). Install the oil pan to the specified position.<br />
• Before installation, the surface of contact position of oil pan<br />
and cylinder block are covered by sealant.<br />
• Before smearing the sealant, one shall be sure that the<br />
used sealant on the oil pan and engine block shall be<br />
cleaned up.<br />
(b). Install and fasten the fixing bolts of oil pan.<br />
• When installing the fastening bolt on oil pan, one shall<br />
lubricate each fastening bolt with oil.<br />
• Cross fasten the fixing bolts of oil pan from the middle to the<br />
15B-224<br />
INSTALLATION OF FLYWHEEL ASSEMBLY AND CLUTCH<br />
1. Install the flywheel assembly<br />
(a). Install the sealing strip of the rear oil seal cover to the<br />
specified position.<br />
Install the support rear cover to the specified position.<br />
Install and fasten the fixing bolts of the support rear<br />
(d). Install the flywheel to the specified position.<br />
One shall be careful when installing for the weight of flywheel.<br />
15B-225<br />
(e). Install and fasten the fixing bolts of flywheel.<br />
While installing the flywheel bolts, apply oil to the threads and<br />
the contact face and then fasten in diagonal manner.<br />
3. Install the Clutch Components.<br />
(a). Install the clutch disc and the clutch cover assembly<br />
with installation positioning tool to the specified<br />
Install and fasten the fixing bolts of clutch.<br />
15B-226<br />
INSTALLATION OF OIL RADIATOR AND OIL FILTER<br />
1. Install the oil radiator<br />
(a). Install the oil radiator and its gasket to the specified<br />
The oil radiator gasket shall be replaced by a new one.<br />
(b). Install the O-ring to the specified position.<br />
O-ring shall be replaced by a new one.<br />
Install and fasten the fixing bolt of oil radiator.<br />
Install the connecting pipe weldment of oil radiator and<br />
oil filter and install the fixing nut.<br />
15B-227<br />
2. Install the oil filter<br />
(a). Install the oil filter to the specified position.<br />
Apply sealant onto the oil filter installation position of the<br />
cylinder block and replace with new gasket.<br />
Install and fasten the fixing bolt f oil filter.<br />
Install and fasten the fixing bolt connecting the<br />
weldment and oil filter.<br />
15B-228<br />
INSTALLATION OF HOOK, VALVE, AND WATER OUTLET PIPE<br />
CONNECTOR<br />
1. Install the hooks.<br />
(a) Install the front hook to the specified position.<br />
Install and fasten the fixing bolts of hook.<br />
Install the rear hook in place as per same method.<br />
2. Install the valves.<br />
(a). Knock in the valve guide from the top of the cylinder<br />
head with special tool.<br />
Before the installation, apply oil to the outer surfaces of<br />
the valve guide. After the installation, check the height of<br />
the valve guide.<br />
(b). Lubricate all valve guide bores and the valve stems.<br />
Lubricate with oil, otherwise it will lead to early wear of valve<br />
guides<br />
15B-229<br />
(c). Install valve to the specified position.<br />
• If the installed valve and disassembled valve are same,<br />
the valve shall be installed on the position at which the<br />
valve is disassembled.<br />
• If the cylinder head can’t be used immediately, lubricate<br />
the valve stems with assembly lubricant or equivalent.<br />
(d). Install the valve oil seal and install the valve spring<br />
lower seat, valve spring, and valve spring upper seat.<br />
The valve spring upper seat for intake valve is different from<br />
that for exhaust valve.<br />
Replace with new valve oil seal.<br />
(e). Compress the valve spring with valve spring<br />
(f). Install the valve lock clamp and then release the valve<br />
spring to enable the valve lock clamp to lock the valve.<br />
After the assembly, knock the valve spring seat with rubber<br />
hammer to ensure the correct installation of locking plate.<br />
If the lock clamp is not installed correctly, the lock clamp<br />
will fly out while knocking the valve spring seat with<br />
plastic hammer. To minimize the possibility of the<br />
personal injuries, please wear the goggles.<br />
Install all valves as per same method.<br />
15B-230<br />
3. Install the water outlet pipe connector.<br />
(a) Install the water outlet pipe connector assembly to<br />
Install and fasten the fixing bolts of the water outlet pipe<br />
connector assembly.<br />
15B-231<br />
INSTALLATION OF CYLINDER HEAD<br />
1. Install the cylinder head<br />
(a). Install the cylinder head gasket and cylinder head to<br />
• For the heavy cylinder head, it shall be lifted with assistant<br />
and proper hoisting equipment to prevent severe personal<br />
(b). Install and fasten the fixing bolts of the cylinder head.<br />
Before the installation, lubricate the threads of the fixing bolts<br />
of cylinder head and the lower portion of the bolt head with<br />
During installation, the cylinder head bolt shall be<br />
disassembled in pairs for several times as the sequence<br />
from middle to two sides.<br />
Install the rubber hose connecting the water pump and<br />
thermostat and install the fastening clamp.<br />
Install the oil radiator and cylinder head connecting<br />
hose to the specified position.<br />
15B-232<br />
Fasten the hose clamp and ensure the fastness of<br />
15B-233<br />
INSTALLATION OF TAPPET AND ROCKSHAFT<br />
1. Install the tappet<br />
(a). Fill clean oil into the installation hole of each valve<br />
(b). Install the valve tappet to the specified position.<br />
Put the valve tappet into the installations hole as the reversed<br />
sequence of disassembly.<br />
2. Install the rockshaft<br />
(a). Install the rocker assembly to the specified position.<br />
(b). Install the fixing bolt and fixing nuts of rockshaft.<br />
Do not disassemble a certain bolt or nut at a time. One shall<br />
uniformly disassemble the fixing bolts or nuts of rockshaft for<br />
several times.<br />
15B-234<br />
(a). Install the fuel injector and its pressure plate to the<br />
Ensure the fuel injector and its pressure plate is installed in<br />
Install and fasten the fixing bolt of fuel injector pressure<br />
Install the low pressure rubber fuel pipe connecting to<br />
each fuel injector in order and fasten the clamp.<br />
Connect the connection of low pressure rubber fuel<br />
15B-235<br />
2. Install the high & low pressure fuel pipe<br />
(a). Install the high pressure fuel pipe to the specified<br />
Fasten the fixing bolt connecting the high pressure fuel<br />
pipe and high pressure oil pump.<br />
Connect the connection of high pressure fuel pipe and<br />
fuel injector and ensure the fastness of connection.<br />
15B-236<br />
INSTALLATION OF DIPSTICK<br />
1. Install the dipstick.<br />
Ensure the dipstick is installed in place.<br />
Install and fasten the fixing bolts of dipstick.<br />
15B-237<br />
INSTALLATION OF CRANKSHAFT PULLEY, FAN AND FAN PULLEY<br />
Install and fasten the fixing bolt of crankshaft pulley.<br />
2. Install the fan and its pulley<br />
(a). Install the fan and its pulley to the specified position.<br />
(b). Install and fasten the fixing bolt of fan assembly.<br />
When installing, the fan will rotate in the direction of force. In<br />
order to prevent this, the stud shall be clamped in a reverse<br />
direction with a screwdriver.<br />
15B-238<br />
INSTALLATION OF BREATHER AND GENERATOR<br />
(a). Install the breather assembly to a specified position.<br />
Connect the connection of lower oil pipe of breather<br />
and the breather and install the fastening clamp.<br />
2. Install the generator<br />
(a). Install the lower bracket of generator to the specified<br />
position and install the fixing bolt fastening the lower<br />
bracket of generator.<br />
ENGINE MECHANICAL PART- INSTALLATION OF BREATHER AND GENERATOR<br />
15B-239<br />
Install the upper bracket of generator to the specified<br />
position and install the fixing bolt fastening the upper<br />
Install the generator assembly to the specified position.<br />
(d). Install the lower fixing bolt of generator.<br />
when installing, one shall firstly lock the bolt and then<br />
• When installing the fixing bolt, one shall hold up the<br />
(e). Install the adjusting bolt of generator.<br />
The adjusting bolt shall be fastened after the fan belt is<br />
(f). Adjust the tension of belt and fasten the adjusting bolt<br />
of generator.<br />
Adjust the tension of fan belt through the generator adjusting<br />
15B-240<br />
Install the hose clamp of vacuum pump oil return pipe<br />
and connect the connection of oil return pipe.<br />
Connect the connection of vacuum pump oil inlet pipe<br />
and generator and fasten the fixing bolt.<br />
15B-241<br />
1. Install the intake and exhaust manifolds and<br />
turbocharger<br />
(a). Install the turbocharger gasket and turbocharger onto<br />
the exhaust manifold pipe.<br />
turbocharger and turbocharger bracket.<br />
Install and fasten the fixing bolt of turbocharger air inlet<br />
Install the intake manifold assembly.<br />
15B-242<br />
(e). Install the rubber hose connecting the turbocharger and<br />
intake manifold, Fasten the clamp and ensure the<br />
fastness of installation.<br />
Ensure the assembly of intake and exhaust manifolds and<br />
turbocharger is correct and secure.<br />
(f). Install the intake and exhaust manifolds gaskets to the<br />
The gaskets of intake and exhaust manifolds shall be replaced<br />
by new ones.<br />
(g). Install the intake and exhaust manifolds and<br />
turbocharger to the specified positions.<br />
In order to facilitate the installation of generator, the intake and<br />
exhaust manifolds and turbocharger shall be installed all<br />
Connect the connection of turbocharger oil return<br />
rubber hose and cylinder block.<br />
Install the turbocharger oil inlet pipe weldment to the<br />
specified position and install the fastening and fixing<br />
15B-243<br />
Install EGR valve connecting pipe weldment to the<br />
connecting pipe weldment and intake manifold.<br />
Install and fasten the intake and exhaust manifolds bolt.<br />
15B-244<br />
INSTALLATION OF EGR CONTROLLER<br />
1. Install EGR controller<br />
(a). Install EGR controller onto the fixing bracket of air<br />
compressor and install the fastening and fixing bolt.<br />
(b). Install EGR controller equipped with air compressor<br />
bracket to the specified position and install the fixing<br />
bolt which can fasten the air compressor bracket.<br />
For the convenience of disassembly, the air compressor fixing<br />
bracket and EGR controller shall be taken down all together.<br />
Connect the connection of generator and EGR<br />
controller vacuum pipeline.<br />
Connect the connection of preheat controller and the<br />
controller oil inlet pipe.<br />
15B-245<br />
Connect the connection of EGR valve vacuum pipeline.<br />
15B-246<br />
INSTALLATION OF CYLINDER HEAD COVER<br />
1. Install the cylinder head cover<br />
(a). Install the cylinder head cover to the specified position.<br />
Install and fasten the fixing nut of cylinder head cover.<br />
15B-247<br />
INSTALLATION OF HEATER AND WATER OUTLET-INLET PIPE<br />
1. Install the weldment of heater and water outlet-inlet<br />
(a). Install the weldment of heater and water outlet-inlet<br />
pipe to the specified position.<br />
Install the rubber hose connecting the weldment of<br />
heater and water outlet-inlet pipe and the thermostat.<br />
Install and fasten the fixing bolt of weldment of heater<br />
and water outlet-inlet pipe.<br />
15B-248<br />
ENGINE MECHANICAL PART-CYLINDER HEAD COVER<br />
CYLINDER HEAD COVER<br />
ENGINE MECHANICAL PART- CYLINDER HEAD COVER<br />
15B-249<br />
Anti-vibration cover plate assembly of<br />
valve chamber cover<br />
Anti-vibration pad of valve chamber<br />
cover<br />
5 Oil filler cap<br />
7 Gasket of valve chamber cover<br />
8 Gasket of valve chamber cover nut<br />
9 Fixing nut of valve chamber cover<br />
10 Crankshaft vent valve component<br />
11 Spring washer<br />
12 Cross recess head screw<br />
6 Valve chamber cover assembly<br />
15B-250<br />
During the disassembly, the parts of valve assembly shall be concentrated together and marked with<br />
identification code to return to their own origin positions when reinstalling; one shall conduct a<br />
compression test and record its result before removing the cylinder head from generator and<br />
disintegrating the valve mechanism.<br />
1. Preliminarily check the engine.<br />
(a). Clean the outside of generator with steam or high<br />
pressure gun.<br />
Hot steam may cause serious personal injuries. While<br />
using the steam cleaner, please wear the safety goggles or<br />
protective mask and wear the protective clothing<br />
Run the engine at low idle speed and check for leakage<br />
of oil or coolant between cylinder head and engine<br />
(c). Listen whether there is “chirp” sound between the<br />
cylinder head and the engine cylinder block.<br />
Fill water into the coolant tank, till the overflow pipe within the<br />
coolant tank is immersed. Then, run the engine at high idling<br />
speed, till the thermostat turns on. In such case, observe the<br />
water solvent for the presence of steam bubbles, which will<br />
determine whether there is leakage in the combustion<br />
Upon the detection of leakage, disassemble and check the<br />
cylinder head and all related parts.<br />
2. Remove the cylinder head cover assembly (Refer to Chapter 15B Engine Mechanical system –<br />
Disassembly of Engine 4JB1).<br />
15B-251<br />
3. Disassemble and service the cylinder head cover<br />
(a). Take down the oil filler cap<br />
As required, screw off the oil filler cap.<br />
(b). Dismantle the fixing bolt of anti-vibration cover plate<br />
assembly of valve chamber cover.<br />
Disassemble the anti-vibration cover plate assembly of<br />
Check the anti-vibration cover plate assembly of valve<br />
chamber cover to see whether it is damaged. If it is,<br />
please replace the damaged one.<br />
Disassemble the anti-vibration pad of valve chamber<br />
15B-252<br />
Check the anti-vibration pad of valve chamber cover to<br />
see whether it is aging, corroded or deformed. If any of<br />
those phenomena occurs, it shall be replaced by a new<br />
Disassemble the fixing bolt of crankcase vent valve<br />
component with cross screwdriver and take down the<br />
crankcase vent valve component<br />
(h). Check the oil filler cap for the presence of cracking and<br />
corrosion. If yes, replace with new one.<br />
Observe for the presence of water vapor within the oil filler cap.<br />
If yes, it indicates the ingress of coolant into the cylinder block.<br />
In such case, carefully check the cylinder gasket, cylinder head,<br />
and waterway for damage. If yes, maintain or replace the<br />
damaged parts.<br />
(i). Clean the cylinder head cover with solvent, acid or<br />
alkaline material.<br />
material for cleaning.<br />
• Please wear the goggles and protective clothing to<br />
prevent causing personal injuries.<br />
15B-253<br />
(j). Blow dry the cylinder head cover with compressed air.<br />
While using the compressed air, please ware appropriate<br />
goggles and protective mask to prevent the scraps and<br />
dirt splashed from causing personal injuries.<br />
Check the cylinder head cover for presence of damage.<br />
If yes, replace with new one.<br />
Check the gasket of cylinder head cover for aging,<br />
corrosion or deformation. If yes, replace with new one.<br />
4. Install the cylinder head cover assembly.<br />
(a). Install the crankcase vent valve component to the<br />
specified position and install the fixing bolt of crankcase<br />
vent valve component.<br />
Install the anti-vibration pad of valve chamber cover.<br />
15B-254<br />
Install the anti-vibration cover plate assembly of valve<br />
Install and fasten the fixing bolt of valve chamber cover<br />
anti-vibration cover plate assembly.<br />
Install the oil filler cap<br />
5. Install the cylinder head cover assembly (Refer to Chapter 15B Engine Mechanical system –<br />
Assembly of Engine 4JB1)<br />
ENGINE MECHANICAL PART-ROCKER ASSEMBLY<br />
15B-255<br />
ROCKER ASSEMBLY<br />
1 Rockshaft plug<br />
2 Retainer ring<br />
3 Rocker assembly<br />
4 Valve adjusting bolt<br />
5 Valve adjusting nut<br />
6 Rockshaft seat<br />
7 Small washer<br />
8 Hexagon head stud<br />
9 Rocker spring washer<br />
10 Rockshaft spring<br />
11 Rockshaft<br />
12 Rockshaft bearing bolt<br />
13 Long hexagon stud<br />
15B-256<br />
If any excessively worn or damaged part is detected during the service, perform the necessary<br />
adjustment, repair and replacement.<br />
1. Remove the rockshaft assembly (Refer to Chapter 15B Engine Mechanical system –<br />
2. Clean and Test for the electric heater plug<br />
(a). Clean the electric heater plug by washing.<br />
Test the electric heater plug as shown in left diagram.<br />
• When the electric heater plug connecting with<br />
battery, if A end emits heat, it means that the<br />
electric heater plug is working well.<br />
battery, if A end doesn’t emit heat, it means that<br />
the electric heater plug is damaged.<br />
3. Disassemble the rockshaft assembly (see Chapter 15B Engine Mechanical System –<br />
Disassembly of Engine 4JB1)<br />
4. Disassemble the rockshaft assembly.<br />
(a). Disassemble the rockshaft plug and take down the<br />
circlip at the rocker assembly end with circlip pliers.<br />
15B-257<br />
(b). Take down the rocker processing assembly and rocker<br />
When taking out the rocker processing assembly, the revolving<br />
method is a relatively easy way.<br />
Take out the rockshaft.<br />
Disassemble the adjusting nut of valve and disintegrate<br />
the rocker assembly assembly.<br />
(e). Disassemble the shaft seat and rocker assembly.<br />
• The position of each disassembled one shall be marked.<br />
• During the installing, it shall be installed at the origin<br />
position and in the origin direction when removing.<br />
3. Check the rocker assembly.<br />
(a). Clean all parts with high concentration detergent and<br />
hot water solvent.<br />
15B-258<br />
Clean off the deposits on rocker seat and rocker<br />
assembly with steel brush and mild steel wire rotary<br />
(c). Blow dry all parts with compressed air.<br />
Check the adjusting bolt and fixing nut of valve<br />
clearance to see whether there are cracks or<br />
deformation of threads. If there is one of phenomena<br />
mentioned above, it shall be replaced.<br />
Check whether the adjustable threads of valve<br />
clearance is deformed or the wear condition of bolt with<br />
fillister head. If there is one of phenomena mentioned<br />
above, it shall be replaced.<br />
Check the rocker bore for the presence of cracking or<br />
excessive wear. If yes, replace with new one.<br />
15B-259<br />
Check whether the oil holes on the rocker are blocked.<br />
If yes, clean the oil holes on the rockshaft with<br />
compressed air.<br />
(h). Measure the inside diameter of the rocker with vernier<br />
caliper or micrometer.<br />
The parameters are shown in the table below:<br />
Engine Model<br />
Specified Value mm<br />
4JB1 19.010~19.030<br />
4D20 19.010~19.030<br />
(i). Measure the external diameter with dial indicator at the<br />
position of rocker swing on the rockshaft.<br />
Specified Value: mm<br />
4JB1 18.980~19.000<br />
4D20 19.979~20.000<br />
(j). Place the rockshaft onto the V-blocks and measure the<br />
radial run-out in the middle of the rockshaft with<br />
micrometer.<br />
Note:<br />
If the radial run-out is minor, the bench press may be used<br />
to correct the radial run-out of the rockshaft. If the run-out<br />
is out of the specified range, replace the rockshaft.<br />
15B-260<br />
4. Install the rockshaft assembly.<br />
(a). Lubricate the rockshaft with clean oil.<br />
Lubricate the rocker and the inner bore of rocker seat<br />
with clean oil.<br />
Install the rocker assembly, valve adjusting bolt and<br />
adjusting nut together.<br />
(d). Install the rocker, rocker spring, rockshaft bracket into<br />
the rockshaft in the reversed sequence of disassembly.<br />
The rocker, rockshaft bracket hole and rockshaft surface shall<br />
be covered with clean oil.<br />
(e). Install the rocker retainer ring and rockshaft plug with<br />
circlip pliers.<br />
As an elastic part, the retainer ring is likely to rush out. For<br />
this reason, it is recommended to wear goggles and<br />
handle this part carefully.<br />
15B-261<br />
5. Install the rocker assembly (Refer to Chapter 15B Engine Mechanical system – Assembly of<br />
Engine 4JB1).<br />
15B-262<br />
ENGINE MECHANICAL PART-CYLINDER HEAD<br />
15B-263<br />
1 Hexagon head bolt assembly<br />
3 A/C bracket<br />
4 Bowl-Bowl-shaped tabular plug 12<br />
5 Type 1 hexagon nut<br />
6 Stud<br />
Pressure plate cushion block of fuel<br />
8 Pressure plate of fuel injector<br />
Pressure plate bolt gasket of fuel<br />
10 Pressure plate bolt<br />
11 Valve key<br />
12 Valve spring upper seat<br />
13 Valve spring<br />
14 Valve guide pipe oil seal<br />
15 Valve spring lower seat<br />
16 Intake and exhaust valve guide pipes<br />
17 Bowl-Bowl-shaped tabular plug 22<br />
18 Cylinder Head<br />
19 Cylinder head bolt<br />
20 Bowl-Bowl-shaped tabular plug 45<br />
21 Electric heater plug<br />
22 Preheat plug pad<br />
23 Rear hook of generator<br />
25 Spring washer<br />
26 Plain washer<br />
27 Stud<br />
28 Exhaust valve seat<br />
29 Exhaust valve<br />
30 Exhaust valve<br />
31 Intake valve seat<br />
32 Bowl-Bowl-shaped tabular plug 18<br />
33 Cylinder head bolt<br />
15B-264<br />
1. Remove the tappet (Refer to Chapter 15B Engine Mechanical system – Disassembly of Engine<br />
4JB1)<br />
2. Remove the cylinder head assembly (Refer to Chapter 15B Engine Mechanical system –<br />
3. Check the bolts of cylinder head.<br />
(a). Clean the bolts with diesel engine solvent.<br />
Thoroughly remove the sediment from the bolt stems and the<br />
threads with wire brush, soft wire wheel brush, or non-abrasive<br />
sand blasting.<br />
• Do not clean the bolts with alkaline or acid solvent, or it<br />
will lead to damage of bolts.<br />
(b). Visually observe the bolts of the cylinder head for<br />
corrosion and observe the threads for damage. If yes,<br />
replace with new ones.<br />
4. Disassemble the thermostat assembly (see Chapter 15B Engine Mechanical System –<br />
5. Remove the valves (see Chapter 15B Engine Mechanical System – Disassembly of Engine<br />
6. Preliminarily clean the cylinder head.<br />
(a). Clean the sealing surfaces of the cylinder head and the<br />
15B-265<br />
Clean the combustion surfaces of the cylinder block<br />
and cylinder head.<br />
7. Deep cleaning and maintenance for the cylinder<br />
head<br />
(a). Clean up the carbon deposits on the fuel injector seat<br />
with fuel injector pore brush or equivalent tools.<br />
Clean the valve retainer with brush.<br />
(c). Clean the foreign materials with compressed air<br />
(d). Immerse the cylinder head into the acid solvent tank to<br />
remove the sediments.<br />
Firstly remove the expansion plug. If necessary, clean the<br />
sediment from the coolant way.<br />
15B-266<br />
(e). After the cleaning, clean the cylinder head combustion<br />
surface with hand grinding pad or equivalent cleaning<br />
pad and solvent.<br />
manual of the manufacturer before use<br />
(f). Clean the valve seat and valve guide<br />
• While cleaning the carbon deposit, wear the goggles to<br />
prevent personal injuries.<br />
• The rotation of wire wheel will damage the valve seat.<br />
Therefore, it’s necessary to machine the new valve seat<br />
or install new valve retainer.<br />
• Poor quality wire wheel will drop wires during the<br />
working, which will lead to additional contamination.<br />
Use quality wire wheel installed onto the drill or the<br />
mould polishing machine to remove the carbon deposit<br />
from the valve guide.<br />
(g). Remove the sediment from the installation hole of the<br />
valve retainer with wire brush and solvent (The valve<br />
seat is already removed)<br />
(h). Blow dry the surfaces of cylinder head with<br />
15B-267<br />
Clean the cylinder head with hot soapy solvent and<br />
then flush the cylinder head with clean water.<br />
(j). Blow dry the cylinder head with compressed air.<br />
8. After the cleaning, recheck the cylinder head.<br />
(a). Check the cylinder head for the presence of cracking,<br />
corrosion and discoloration. If any cracking, corrosion,<br />
or discoloration detected will influence the further<br />
service, replace with new cylinder head.<br />
Pay close attention to the following areas of the cylinder<br />
head:<br />
Combustion surfaces, valve seat, and valve guide.<br />
• The cylinder head can be further used if the cracking<br />
detected does not extend to the valve seat.<br />
• If the cracking extends to the valve seat or passes through<br />
the valve seat, replace the cylinder head, otherwise such<br />
cracking will lead to fall-off of the valve retainer and further<br />
lead to damage of engine.<br />
If the cylinder head is not replaced, the cracks extending<br />
to or passing by the valve seat pore may lead to the falling<br />
off of the valve retainer and further lead to the damage of<br />
15B-268<br />
Check the valve seat for presence of cracking and<br />
ablation points. If yes, depending on the working<br />
surface and the lower limit of the valve retainer, replace<br />
the valve retainer.<br />
Check the threaded holes on the rockshaft bracket and<br />
the cylinder head to see whether the threads are<br />
damaged or deformed; if they are, the chambering or<br />
repair will be conducted if possible and be replaced<br />
when necessary.<br />
(d). Measure the length of diagonal line of the cylinder head<br />
lower surface to decide whether the housing cap is<br />
deformed.<br />
If the 2 diagonal lines are not equal, it means the cylinder<br />
head is deformed and required to be replaced.<br />
(e). Clean the oil passage and water passage on the top of<br />
the cylinder head with water gun.<br />
Carefully clean the oil passage holes and water passage<br />
holes in turn<br />
9. Install the valve assembly (Refer to Chapter 15B Engine Mechanical System– Assembly of<br />
10. Install the thermostat assembly (Refer to Chapter 15B Engine Mechanical System– Assembly<br />
of Engine 4JB1).<br />
11. Install the cylinder head assembly (Refer to Chapter 15B Engine Mechanical System–<br />
Assembly of Engine 4JB1).<br />
12. Install the tappet (Refer to Chapter 15B Engine Mechanical System– Assembly of Engine<br />
4JB1).<br />
ENGINE MECHANICAL PART- VALVE<br />
15B-269<br />
1. The valve distribution mechanism is of direct influence over the normal functioning of the engine. The<br />
valve distribution mechanism shall guarantee that the clean air can timely enter into the cylinder with<br />
maximum inflation amount during the intake stroke and the exhaust gas in the cylinder can be timely<br />
drained from the cylinder and the residual exhaust gas can be minimized as far as possible during the<br />
exhaust stroke. Meanwhile, the valves shall be tightly closed during the compression and power<br />
strokes.<br />
2. Within the valve distribution mechanism, some parts are subject to the impact of high temperature gas<br />
and the impact load and some parts are poorly lubricated. Under long-term service, these parts get<br />
worn, ablated, or deformed so that the technical performance and fit relationship are impaired to<br />
cause malfunction and failure of parts.<br />
15B-270<br />
The valve clearance plays an important role in the technical state of diesel engine, so the valve clearance<br />
shall be checked in accordance to the maintenance regulate or actual operation condition. The cold state<br />
clearance of intake valve shall be about 0.40±0.050mm, while the cold state clearance of exhaust valve shall<br />
be about 0.40±0.050mm. The adjustment methods are as follows:<br />
1. Rotate the crankshaft till the pulley scale marks of crankshaft vibration damper shall aligning<br />
with timing indicator. Currently, the 1st cylinder piston or the 4th cylinder piston locates at the<br />
dead center of compression travel.<br />
The engine is in cold state.<br />
2. Judge whether is the piston of the 1st cylinder or<br />
the piston of the 4th cylinder locating at the dead<br />
center of compression travel.<br />
Shake the exhaust valve rocker of the 1st cylinder or the 4th<br />
cylinder, if there is clearance when shaking the 1st cylinder<br />
valve rocker, it means that the 1st cylinder is locating on the<br />
dead center of compression travel; if the rocker of the 1st<br />
cylinder valve cannot shake, then one shall shake the rocker of<br />
4th cylinder valve; if there is clearance on the rocker of 4th<br />
cylinder, it means the 4th cylinder is locating at the dead center<br />
of compression travel.<br />
(a). When the 1st cylinder is at the dead center of<br />
compression travel, the valve clearance shall be<br />
checked with feeler gauge.<br />
Engine Value for Clearance of Value for Clearance of<br />
Model Intake Valve mm Exhaust Valve mm<br />
4JB1 0.4 0.4<br />
4D20 0.35 0.35<br />
15B-271<br />
(b). When the clearance of valve is too small, one shall<br />
anticlockwise rotate the adjusting bolt of valve<br />
clearance till the feeler gauge can be inserted into it<br />
and meet a little resistance.<br />
When adjusting the valve clearance and revolving the<br />
adjusting bolt of valve clearance, it is recommended to<br />
conduct the adjustment with a screwdriver and a wrench.<br />
When the valve clearance is too large, one shall<br />
clockwise rotate the adjusting bolt of valve clearance till<br />
the feeler gauge can be inserted into it and meet a little<br />
When the 1st cylinder is at the dead center of<br />
compression travel, the adjustment sequence is as<br />
shown on the left diagram: 1, 2, 3 and 6 valve<br />
clearances.<br />
Rotate the crankshaft 360°, align the crankshaft<br />
anti-vibration pulley mark with the timing indicator and<br />
adjust the other clearances of valve.<br />
When the 4th cylinder is at the top dead center in<br />
compression travel the valve clearance shall be<br />
checked by feeler gauge.<br />
When the clearance of valve is too small, one shall<br />
15B-272<br />
When the clearance of valve is too large, one shall<br />
When the 4th cylinder is at the dead center of<br />
shown on the left diagram: 4, 5, 7 and 8 valve<br />
After the valve clearance has been adjusted for two times, one<br />
shall recheck the adjusting bolt and locking nut of valve to see<br />
whether they are fastened properly and recheck the valve<br />
clearance with feeler gauge when necessary to ensure the<br />
valve clearance has already reached the specified standard.<br />
15B-273<br />
1. Disassemble the valve (see Chapter 15B Engine Mechanical System - Disassembly of Engine<br />
2. Service the valve parts.<br />
(a). Check the valve lock clamp for the presence of<br />
cracking and damage. If yes, replace with new one.<br />
(b). Measure the perpendicularity of valve spring with steel<br />
square.<br />
4JB1 ≤1.7<br />
4D20 ≤1.7<br />
If the measurement is out of the specified range, replace the<br />
valve spring.<br />
(c). Compress the spring to the installation height with<br />
spring tester and measure the tension of the<br />
compression spring<br />
Spring Height When<br />
Assembly is<br />
Completed mm<br />
Spring Tension When<br />
Completed N<br />
4JB1 38.9 272~320<br />
4D20 39 279~314<br />
15B-274<br />
If the tension measurement is below the specified limit,<br />
replace the valve spring.<br />
(d). Measure the free height of valve spring with vernier<br />
4JB1 48<br />
4D20 50<br />
If the measurement is out of the specified range, replace<br />
the valve spring.<br />
(e). Polish the valve stems with grinding pad and solvent.<br />
Visually observe the tip of the valve stems for presence<br />
of excessive wear. If yes, replace the valve.<br />
If the cylinder head and valve seat are excessively<br />
worn, replace with new ones.<br />
15B-275<br />
(h). Measure the valve thickness with steel square. If the<br />
measurement is below the specified limit, replace the<br />
valve and valve guide in pair.<br />
Specified value: mm<br />
4JB1 2.25±0.075<br />
4D20 2±0.075<br />
(i). Measure the contact conical angle of the valve seat. If<br />
the measurement is out of the specified range, replace<br />
the valve, valve guide, and valve seat in group.<br />
4JB1 Inlet valve 30°, Exhaust valve 45°<br />
4D20 Inlet valve 30°, Exhaust valve 45°<br />
(j). Measure the outside diameter of valve stems with<br />
Engine<br />
Model<br />
Specified Value for<br />
4JB1 7.946~7.961 7.921~7.936<br />
4D20 7.945~7.960 7.945~7.960<br />
Measure and record the result.<br />
15B-276<br />
(k). Measure the radial run-out of each valve cone with dial<br />
gauge and V-block.<br />
4JB1 0.02 0.02<br />
4D20 0.02 0.02<br />
This measurement is intended to guarantee the air-tightness<br />
between valve and valve seat.<br />
(l). Polish the valve seat<br />
Polish the valve seat by two steps. Firstly apply coarse<br />
polishing paste onto the valve surfaces and then apply fine<br />
polishing paste. Polish the surfaces with regular polishing<br />
method after each application of polishing paste.<br />
After the polishing, wipe away the polishing paste from the<br />
surfaces of the valve and valve seat and use red lead to<br />
perform the contact inspection. Make sure to check that<br />
the contact color belt is within the width of the valve seat,<br />
without any gap. If necessary, install the cylinder head and<br />
the valve parts and adjust the valve gap.<br />
(m). Measure the drop amount of the valve from the bottom<br />
face of the cylinder head with depth gauge or ruler. If<br />
the measurement is out of the specified range, make<br />
sure to replace the valve seat.<br />
4JB1 0.50~0.80<br />
4D20 0.55~0.85<br />
15B-277<br />
(n). Check the roughness and unevenness of the valve<br />
contact surface. If the measurement is out of the<br />
specified range, make sure to replace the valve seat.<br />
4JB1 3.2<br />
4D20 3.2<br />
3. Service the valve guide.<br />
(a). Measure the outside diameter of the valve stem and<br />
the inside diameter of valve guide with micrometer.<br />
The valve and the valve guide shall be replaced in pair. While<br />
measuring the outside diameter of the valve stems, measure<br />
the inside diameter of valve guide with micrometer and<br />
subtract the measured inside diameter of the valve guide by<br />
the measured outside diameter of the valve stem. If the above<br />
difference is out of the specified limit, replace the valve and<br />
valve guide in pair.<br />
Engine Model 4JB1 4D20<br />
Gap between intake valve and valve guide mm 0.039 ~ 0.071 0.015~0.045<br />
Gap between exhaust valve and valve guide mm 0.064~0.096 0.015~0.045<br />
15B-278<br />
If the valve guide needs to be replaced, knock out the<br />
valve guide from the bottom of the cylinder head with<br />
special tool.<br />
4. Install the valve guide. (see Chapter 15B Engine Mechanical System – Assembly of Engine<br />
5. Service the valve seat.<br />
(a). Check the valve seat for presence of wear. If yes,<br />
remove and replace the valve seat. Removal method of<br />
valve seat: Perform the arc welding at the inner side of<br />
the valve seat, cool down the valve seat, and pry out<br />
the valve seat with screwdriver.<br />
During disassembly, caution shall be taken to prevent<br />
damaging the cylinder head.<br />
6. Install the valve seat.<br />
(a). Install the valve seat.<br />
During the installation, apply force onto the accessory<br />
gradually with bench press to press the valve seat in place.<br />
Do not apply excessive force with bench press, otherwise<br />
it will lead to damage of valve seat.<br />
(b). Remove the carbon deposit from the surfaces of the<br />
valve seat and machine with valve milling tool to<br />
minimize the area of scratch and other rough surfaces,<br />
which can restore the contact width to standard value.<br />
Only machine away the scratch and rough portions and do<br />
not machine away too much.<br />
15B-279<br />
(c). Measure the drop amount of the valve from the<br />
bottom face of the cylinder head with depth gauge or<br />
ruler. If the measurement is out of the specified range<br />
7. Grind the valve seat.<br />
(a). Brush a small amount of oil or Prussian blue onto the<br />
surfaces of the valve seat<br />
Use new or repaired valve to check whether the fit between the<br />
valve and the valve seat is perfect.<br />
Install the valve<br />
Rotate leftward and rightward by 1/4 turn for several<br />
times.<br />
15B-280<br />
Remove the valve.<br />
(e). Observe the contact face with the valve seat.<br />
The valve seat shall be uniformly covered with oil or Prussian<br />
blue, which shall form a complete color belt.<br />
If the contact color belt fails to meet the requirement<br />
and is situated on the upper portion of the valve cone,<br />
repair the valve seat with 30ºand 45ºmilling tool.<br />
and is situated on the lower portion of the valve cone,<br />
repair the valve seat with 60ºand 45ºmilling tool.<br />
Apply polishing paste onto the surfaces of valve seat.<br />
15B-281<br />
Polish the valve, till the valve and valve seat achieves<br />
perfect fit.<br />
After the polishing, thoroughly clean the valve, valve<br />
seat, and valve guide.<br />
8. Install the valve (see Chapter 15B Engine Mechanical System – Assembly of Engine 4JB1)<br />
15B-282<br />
ENGINE MECHANICAL PART-CAMSHAFT AND TAPPET<br />
CAMSHAFT AND TAPPET<br />
1 Camshaft gear bolt<br />
2 Upper idler shaft pressure plate<br />
3 Timing pulley assembly of camshaft<br />
5 Camshaft front oil seal component<br />
6 Camshaft flat key<br />
7 Camshaft<br />
8 Tappet<br />
9 Tappet weldment<br />
15B-283<br />
1. Service the tappet<br />
(a). Take out the tappets in order<br />
Carefully clean off all the oil, soot and carbon deposit on<br />
the cylinder head bolt and cylinder head. The electronic<br />
metallic brush cannot be applied to the gasket.<br />
Wash and clean the tappet with hot soap-suds.<br />
(c). Blow dry the tappets with compressed air.<br />
Check the two ends of tappet to see whether they are<br />
worn, pulled or damaged with other causes.<br />
15B-284<br />
Visually check the tappet to see whether it is crooked. If<br />
it is obviously crooked, it shall be replaced directly.<br />
(f). If it is not obviously crooked or likely crooked, one shall<br />
check its straightness by rolling it on a horizontal<br />
If the tappet is crooked, replace it.<br />
2. Remove the camshaft (Refer to Chapter 15 Engine Mechanical Part – Disassembly of Engine<br />
3. Service the camshaft.<br />
(a). Clean the parts with solvent.<br />
Remove the sediment from the camshaft with wire<br />
brush and soft wire wheel brush.<br />
15B-285<br />
(c). Clean the camshaft by blowing it with compressed air.<br />
Check the bore of camshaft for the presence of<br />
cracking and blockage and check the inner side of the<br />
camshaft for the deposit of oil or oil sludge. If yes, clean<br />
and when necessary replace with new one.<br />
(e). Place the camshaft onto the V-blocks and measure the<br />
radial run-out of camshaft with micrometer. If the radial<br />
run-out is out of the specified range, replace the<br />
4JB1 0.02<br />
4D20 0.025<br />
15B-286<br />
(f). Measure the outside diameter of each camshaft journal<br />
with screw micrometer in two directions perpendicular<br />
with each other respectively. If any measurement is<br />
below the specified limit, replace the camshaft.<br />
Standard Value: mm<br />
4JB1 49.945~49.975<br />
4D20 43.897~43.910<br />
(g). Measure the height of each cam with micrometer. If the<br />
4JB1 26.2635<br />
4D20 21.8±0.03<br />
Visually check the surfaces of the camshaft for the<br />
presence of corrosive pitting, cracking or other<br />
abnormalities. If yes, replace the camshaft.<br />
15B-287<br />
4. Service on the camshaft gear<br />
(a). Clean the camshaft gear with solvent<br />
Clean off the deposits on camshaft gear with steel<br />
brush and mild steel wire rotary brush.<br />
(c). Clean the camshaft gear by blowing it with compressed<br />
air.<br />
Check the bolt hole on the camshaft gear to see<br />
whether there are cracks or corrosion. If there are,<br />
repair it or replace it when necessary.<br />
Check the gear teeth of camshaft to see whether there<br />
is corrosion or cracks. If there is, repair it or replace it<br />
15B-288<br />
(f). Use the grinding pad to remove the corrosion, burr and<br />
bulge metal from the camshaft<br />
If the corrosion, burr and bulge metal can’t be removed by the<br />
grinding pad, replace the camshaft<br />
5. Service on the front oil seal seat part of camshaft<br />
(a). Clean the front oil seal seat part of camshaft with<br />
solvent.<br />
Clean off the deposits on the front oil seal seat part of<br />
camshaft with steel brush and mild steel wire rotary<br />
Clean the front oil seal seat part of camshaft by blowing<br />
it with compressed air.<br />
Check the front oil seal seat part of camshaft and the<br />
bolt hole to see whether there is corrosion or cracks. If<br />
there is, repair it or replace it when necessary.<br />
15B-289<br />
(e). Use the grinding pad to remove the corrosion, burr and<br />
bulge metal from the camshaft timing sprocket<br />
grinding pad, replace the gear.<br />
6. Remove and service the tappets<br />
(a). Draw out the tappets from their installation positions<br />
The tappets taken out shall be put in a clean vessel.<br />
(b). Clean the tappet with solvent.<br />
(c). Blow dry the tappet with compressed air.<br />
(d). Check the tappet seat, lever handle and tappet surface<br />
for presence of wear and cracks. If yes, repair or<br />
replace when necessary.<br />
• Normal contact (increasing)<br />
• Do not continue to use in irregular contact.<br />
15B-290<br />
(e). Check the surface of tappet for cavitation.<br />
The following standards define the allowable range of the<br />
cavitation on the surface of tappet.<br />
• Single cavitation point shall not beyond 2mm.<br />
• The cavitations are not allowed to gather to one piece.<br />
• The total diameter of accumulated cavitations shall not<br />
beyond 6mm or 4% of the area of tappet gauge.<br />
• The cavitations of tappet are not lowed to exist above or<br />
under the wear surface.<br />
(f). Measure the outside diameter of the tappets with screw<br />
micrometer<br />
Measure the inner diameter of tappet hole with micrometer<br />
calipers and subtract the inner diameter value of tappet hole<br />
from the outer diameter value of tappet. If the D-value is more<br />
than the specified limiting value, it means the tappet shall be<br />
Specified outside diameter of tappet mm 12.927~12.990 12.666~12.684<br />
Specified inside diameter of tappet mm 13.000~13.018 12.7~12.718<br />
Specified limit mm 0.010~0.041 0.016~0.052<br />
7. Install the tappets<br />
(a). Cover the tappet and tappet hole with oil or equivalent.<br />
15B-291<br />
Install 8 tappets into the installation holes one by one.<br />
8. Install the camshaft assembly (see Chapter 15B Engine Mechanical System – Assembly of<br />
Engine 4JB1)<br />
15B-292<br />
ENGINE MECHANICAL PART-PISTON AND CONNECTING ROD ASSEMBLY<br />
PISTON AND CONNECTING ROD ASSEMBLY<br />
1 Top compression ring<br />
2 Second compression ring<br />
3 Coil spring oil ring<br />
4 Piston<br />
5 Piston pin<br />
6 Snap ring of piston<br />
7 Connecting rod body<br />
8 Connecting rod bearing bushing<br />
9 Connecting rod bolt<br />
10 Connecting rod bearing bush<br />
11 Connecting rod cap<br />
12 Connecting rod nut<br />
15B-293<br />
1. Remove the piston assembly (Refer to Chapter 15 Engine Mechanical Part – Disassembly of<br />
2. Disassemble the piston assembly.<br />
(a). Remove three piston rings with the special piston ring<br />
remover.<br />
Disassemble the retainer rings on both sides of piston<br />
(2 retainer rings).<br />
Punch out the piston pin with punch bar.<br />
3. Service the connecting rod bearing bush<br />
(a). Check the connecting rod bearing bush for presence of<br />
sink erosion, peeling-off, corrosion, damage of locking<br />
piece, and scratch. If yes, replace with new one.<br />
15B-294<br />
4. Service the connecting rod<br />
(a). Measure the inside diameter of the smaller end bore of<br />
the connecting rod and measure the outside diameter<br />
of the piston pin.<br />
Outside diameter of piston pin mm 30.995~31.000 27.994~28.000<br />
Inside diameter of connecting rod bore mm 34.000~34.025 30.987~31.000<br />
Inner diameter of connecting rod bushing mm 31.008~31.015 28.025~28.038<br />
Specified gap mm 0.008~0.020 0.025~0.045<br />
If the gap between the smaller end bore of the connecting rod and the piston pin is out of the specified range,<br />
replace the bush and the piston pin and when necessary replace the connecting rod.<br />
(b). Remove the bush with bar and hammer.<br />
• The hammer can be used during the installation. The oil<br />
hole of the bush shall be aligned with that of the<br />
connecting rod.<br />
• After the new bush is installed, grind the bush bore with<br />
pin bore grinding machine.<br />
(c). Clean the connecting rod with solvent.<br />
• Please wear the goggles and protective clothing to prevent<br />
causing personal injuries.<br />
15B-295<br />
(d). Clean the contact surface between the connecting rod<br />
and the connecting rod cap with nylon hairbrush.<br />
The contact surface between the connecting rod and the<br />
connecting rod cap is not a machined surface. Cautions<br />
shall be taken during the handling, in order to prevent<br />
damaging the parts.<br />
(e). Thoroughly clean the connecting rod with compressed<br />
• The pressure of the compressed air used for cleaning<br />
shall not exceed 207KPa.<br />
(f). Check the connecting rod cap for the presence of wear,<br />
cracking, burr, scratch, or wear. If yes, replace with new<br />
In event of obvious wear at any portion of the connecting<br />
rod or the connecting rod cap, replace one part as a whole<br />
(g). Check the connecting rod for the presence of wear,<br />
(h). Check the contact surface between the connecting rod<br />
and the connecting rod cap<br />
connecting rod cap is not a machined surface. Unless<br />
there is really deep wear or cracking on the surface, the<br />
contact surface can be further used, instead of being<br />
considered as damaged.<br />
15B-296<br />
(i). Check the piston pin bore of the connecting rod for<br />
damage. If yes, replace with new one.<br />
There is no oil passage to be aligned with the bush hole<br />
within the smaller end bore of the connecting rod. The<br />
bore on the bush is only used during the manufacturing.<br />
5. Service the piston pin.<br />
(a). Visually check the piston pin for presence of cracking,<br />
scratch, or other damages and when necessary<br />
replace with new one.<br />
(b). Measure the outside diameter of the piston pin with<br />
micrometer at three different positions in two different<br />
directions.<br />
4JB1 30.995~31.000<br />
4D20 27.994~28.000<br />
6. Service the piston.<br />
(a). Immerse the piston into cold cleaning fluid.<br />
Generally, immersing the piston for a whole night can loosen<br />
the carbon deposit.<br />
• Do not clean the piston with sand blasting, as the sand<br />
blasting material will embed into the aluminum and<br />
thus lead to damage of piston.<br />
• Do not clean the piston in the acid solvent tank, or it will<br />
lead to damage of piston.<br />
15B-297<br />
(b). Use the mixture from high concentration detergent and<br />
hot water to clean the piston.<br />
Do not use the wire brush, or the wire brush will damage<br />
the piston ring grooves.<br />
(c). Again clean the piston with detergent fluid or solvent<br />
and rinse the piston with clean hot water.<br />
• Do not clean the piston or connecting rod in the acid<br />
solvent tank. Otherwise it will damage the piston and<br />
(d). Blow dry the piston with compressed air.<br />
Check the skirt, pin bore, head, and ring grooves of the<br />
piston for presence of damage and wear. If yes, replace<br />
15B-298<br />
Measure the piston outer diameter with screw<br />
micrometer at other positions of piston assembly.<br />
Group 1<br />
value:<br />
mm<br />
Group 2<br />
Group 3<br />
Group 4<br />
Group 5<br />
Group 6<br />
Group 7<br />
Group 8<br />
4JB1<br />
93.025~9<br />
3.034<br />
93.015~9<br />
3.024<br />
93.005~9<br />
3.014<br />
92.995~9<br />
3.004<br />
92.985~9<br />
2.994<br />
92.975~9<br />
2.984<br />
92.965~9<br />
2.974<br />
92.955~9<br />
2.964<br />
4D20<br />
85.930~8<br />
5.940<br />
85.940~8<br />
5.950<br />
85.950~8<br />
5.960<br />
- - - - -<br />
(g). Insert the piston pin into the piston pin seat bore and<br />
rotate.<br />
If the piston pin rotates smoothly without any gap, it indicates<br />
that the gap is normal. If there is a gap or the rough rotation can<br />
be felt, the gap needs to be measured. If the gap measured is<br />
out of the specified range, replace both the piston and the<br />
piston pin.<br />
4JB1 0.002~0.015<br />
4D20 -0.05~0.018<br />
(h). Install the piston ring into the cylinder sleeve and<br />
measure the opening gap with feeler gauge.<br />
It may use the piston head to push the piston rings in the<br />
direction perpendicular to the cylinder walls to the minimum<br />
bore diameter position of the cylinder sleeve.<br />
15B-299<br />
(i). Measure the gap between the piston ring grooves and<br />
the piston rings with feeler gauge<br />
If the gap between the piston ring grooves and the piston rings<br />
is out of the specified range, replace the piston rings. If the<br />
new piston rings installed still can’t meet the specified gap,<br />
replace the piston.<br />
The piston rings shall be replaced in set<br />
Standard gap between 1st piston ring and piston ring groove mm 0.090~0.125 0.06~0.10<br />
Standard gap between 2nd piston ring and piston ring groove mm 0.050~0.085 0.04~0.08<br />
Standard gap between oil ring and piston ring groove mm 0.030~0.070 0.02~0.06<br />
7. Check the piston rings<br />
(a). Check the abrasive wear of the piston rings<br />
If the frontal black grinding painting of the piston rings is<br />
reduced or even becomes invisible sometimes, it indicates that<br />
the abrasive wear occurs in the middle ring. Generally, it can<br />
be considered as the complete wear of the ring surface. The<br />
reduced painting generally will keep sharp the bottom edge of<br />
the middle ring. In addition, the central longitudinal wear on the<br />
top ring indicates the occurrence of the abrasive wear.<br />
The following causes may lead to abrasive wear:<br />
• Suction of grinding material.<br />
• Incomplete cleaning during previous services.<br />
• Particles embedded in the cylinder bore.<br />
• Prolonged oil drainage interval so that the soot content in<br />
the oil becomes high.<br />
• Wear and scratch.<br />
(b). Check the oil ring for blocking<br />
The phenomenon of oil ring blocking is caused by the deposits<br />
existing in oil ring groove.<br />
The oil ring blocking may be caused by the following reasons:<br />
• The operating temperature of engine is relatively low;<br />
long-time idling or the fault of cooling system.<br />
• The replacement interval of oil is extended.<br />
• The grade of applied oil is improper.<br />
• The quality of oil is poor.<br />
15B-300<br />
The oil return blocking of oil ring limits the return of oil, make the area of piston ring full of oil and<br />
cause the defect in terms of oil control.<br />
8. Install the piston assembly (Refer to Chapter 15 Engine Mechanical Part – Assembly of Engine<br />
ENGINE MECHANICAL PART-CRANKSHAFT AND FLYWHEEL ASSEMBLY<br />
15B-301<br />
CRANKSHAFT AND FLYWHEEL ASSEMBLY<br />
1 Crankshaft pulley bolt<br />
2 Crankshaft pulley<br />
3 Crankshaft timing pulley<br />
4 Crankshaft flat key<br />
5 Crankshaft<br />
6 Rolling bearing 6203-Z<br />
7 Flywheel ring gear<br />
8 Pin<br />
9 Flywheel<br />
10 Cylindrical pin<br />
11 Flywheel bolt plate<br />
12 Flywheel bolt<br />
15B-302<br />
1. Remove the flywheel (Refer to Chapter 15 Engine Mechanical Part – Disassembly of Engine<br />
2. Service the flywheel.<br />
(a). Visually check the working surfaces of the flywheel. In<br />
event of any wear, grooving, or gear ring wear, repair<br />
and, when necessary, replace with new one.<br />
Visually check the flywheel gear teeth. If the gear teeth<br />
are worn or broken, please repair them. If necessary,<br />
please replace them.<br />
3. Preliminarily measure the axial gap of the<br />
crankshaft.<br />
(a). Measure the axial gap of crankshaft with micrometer<br />
and magnetic base.<br />
Standard value mm<br />
4JB1 0.040~0.201<br />
4D20 0.14~0.25<br />
The sizes of the thrust bearing and the crankshaft journal<br />
determine the size of the axial gap.<br />
4. Remove the main bearing bush and crankshaft (Refer to Chapter 15 Engine Mechanical Part –<br />
15B-303<br />
5. Service the main bearing bush and the main<br />
bearing cap<br />
(a). Clean the parts such as main bearing caps with steam<br />
or hot soapy solvent.<br />
The hot steam may cause serious personal injury. So wear<br />
safety goggles or protective mask and protective clothing<br />
when using steam to clean things.<br />
(b). Blow dry the parts with compressed air.<br />
(c). Check whether all main bearing caps and main bearing<br />
cap bolts have scratches or overheating phenomenon.<br />
If the main bearing cap is damaged, replace the cylinder<br />
block.<br />
(d). Check whether the main bearing bush have cracks,<br />
scratches or overheating phenomenon.<br />
If the main bearing bush is damaged, replace the complete<br />
set of main bearing bush.<br />
(e). Check the mating surface of the bearing bush seat for<br />
presence of scratch and burr.<br />
In event of scratch or burr, grind with grinding pad. If the<br />
scratch or burr can’t be removed by the grinding pad or<br />
equivalent, replace the bearing.<br />
15B-304<br />
Check the rear main bearing cap to make sure the<br />
annular location pin is installed.<br />
6. Service the crankshaft.<br />
(a). Clean the crank with hot suds.<br />
Clean the oil holes with non-metallic hard brush.<br />
(c). Blow dry the crankshaft with compressed air<br />
Make sure that the water drips are blown out from the threaded<br />
holes and oil passage on each end of the crankshaft.<br />
Please wear proper goggles and protective mask when<br />
using compressed air to avoid the splashing chips and dirt<br />
causing personal injury.<br />
(d). Check whether the screw threads on both ends of<br />
crank are damaged. If they are damaged, please<br />
replace the crank.<br />
The threads of crank shall not need dressing, or else the<br />
engine will be seriously damaged.<br />
15B-305<br />
Visually check whether the middle of crank arm, crank<br />
arm and the top end of connecting rod journal have<br />
scratches or cracks. If they have, please replace them.<br />
Measure multiple points on the same cross section of<br />
the crankshaft with outside diameter micrometer.<br />
Specified outside diameter of crankshaft main journal mm 69.917~69.932 70.904~70.920<br />
Specified inside diameter of crankshaft main bearing bush mm 69.838~69.899 69.811~69.859<br />
Specified gap mm 0.033~0.079 0.061~0.093<br />
The main journal of the crankshaft is to be fitted with the bore of main bearing bush. While measuring the<br />
outside diameter of the crankshaft main journal, measure the inside diameter of the main bearing bush bore<br />
with micrometer as well. If the difference between two measurements is out of the specified range, replace<br />
the main bearing bush in pair.<br />
15B-306<br />
(g). Place the crankshaft onto the V-blocks, rotate the<br />
crankshaft slowly, and measure the radial run-out. If the<br />
radial run-out of the crankshaft is out of the specified<br />
range, replace or correct by cold pressing the crankshaft.<br />
4JB1 0.03<br />
(h). Correct the crankshaft.<br />
To correct the bending of the crankshaft, knock the<br />
non-machined surfaces of the crank arm to deform the crank<br />
so that the axis of the crankshaft is displaced to fulfill the<br />
correction.<br />
7. Install the crankshaft (Refer to Chapter 15 Engine Mechanical Part – Assembly of Engine 4JB1)<br />
8. Measure the axial gap of the crankshaft.<br />
determine the size of the axial gap<br />
9. Install the flywheel (Refer to Chapter 15 Engine Mechanical Part – Assembly of Engine 4JB1)<br />
ENGINE MECHANICAL PART-CYLINDER BLOCK<br />
15B-307<br />
15B-308<br />
1 Front bush of crankshaft<br />
2 Middle and rear bush of crankshaft<br />
3 Cylindrical pin<br />
4 Blocked oil passage<br />
5 Fuel supply connector of vacuum pump<br />
6 Hexagon head bolt and spring washer<br />
8 Water inlet pipe weldment<br />
9 Water inlet pipe gasket<br />
Cylinder block and cylinder head’s<br />
location pin<br />
11 Cylinder liner<br />
12 aluminum plug<br />
13 Bowl-Bowl-shaped tabular plug 36<br />
14 Bowl-shaped tabular plug 18<br />
15 Bowl-shaped tabular plug 38<br />
16 Bowl-shaped tabular plug 56<br />
17 Cylinder head gasket<br />
18 Hexagon bolt with location pin<br />
19 Back plate of cylinder block<br />
20 Flat washer<br />
21 Heavy spring washer<br />
22 Nut M10×1.25<br />
23 Cylindrical pin<br />
24 Fixing bolts of rear joint plate<br />
25 Rear oil seal of crankshaft<br />
26 Bowl-shaped tabular plug 36<br />
27 Bowl-shaped tabular plug 16<br />
28 Bowl-shaped tabular plug 32<br />
29 Harness clamp<br />
Hexagon head bolt, spring washer and<br />
flat washer assembly<br />
31 Bowl-shaped tabular plug 45<br />
32 Water drainage plug screw<br />
33 Plug screw gasket<br />
34 oil pressure sensor plug<br />
35 Oil pressure sensor head<br />
36 Oil Injection pipe weldment<br />
37 Red copper gasket<br />
38 Pressure-limiting valve components<br />
39 Crankshaft upper bearing bush<br />
40 Crankshaft low bearing bush<br />
41 The fifth main bearing cap<br />
42<br />
The first, second and fourth<br />
bearing caps<br />
43 The third main bearing cap<br />
44 Thrust bearing<br />
45 Main bearing bolts<br />
46<br />
47<br />
main<br />
48 Cylinder block<br />
15B-309<br />
1. Disassemble the cylinder block (See Chapter 15B Engine Mechanical System - Disassembly of<br />
Engine)<br />
2. Remove the cylinder gasket.<br />
(a). Remove the cylinder head gasket<br />
The gasket which is disassembled cannot be used again.<br />
Please replace the gasket.<br />
(b). Measure the bore diameter of the cylinder sleeve with<br />
inside diameter micrometer in two or more different<br />
directions and record each measurement result.<br />
Specified value mm<br />
4JB1 93.020~93.061<br />
4D20 86.000~86.030<br />
If the measurement results are out of the specified range, bore<br />
the cylinder or replace the cylinder block.<br />
For measuring the external diameter of cylinder liner and<br />
cylinder hole diameter, it can be effective to measure the<br />
smooth surface of top and bottom section.<br />
(c). Disassemble cylinder liner.<br />
Install the cylinder-liner dismantling gear in the cylinder liner.<br />
Check whether the base of cylinder-liner dismantling gear is<br />
firmly connected with the bottom edge of cylinder liner and then<br />
slowly rotate the dismantling bearing hand wheel<br />
counterclockwise to pull the cylinder liner out.<br />
15B-310<br />
3. Service the cylinder block.<br />
(a). Put the cylinder block in the cleaning tank to clean.<br />
• Clean with solvent that will not damage the camshaft<br />
sleeve.<br />
• Please abide by the operation instructions of the<br />
manufacturer for the operations of the cleaning tank.<br />
• Please abide by the instructions of the solvent<br />
manufacturers while using the solvent.<br />
(b). Thoroughly clean the cylinder block with steam and<br />
then blow dry the cylinder block with compressed air.<br />
• To minimize the damage of the engine, make sure to<br />
remove all scraps from the threaded holes and the oil<br />
passage.<br />
• If the cylinder block will not be used immediately, apply<br />
one film of protective oil for anti-rusting protection and<br />
cover the cylinder block to guard against the<br />
contamination of dirt to the oil.<br />
(c). After the cleaning, recheck the cylinder block for<br />
presence of cracking, corrosion, and discoloration and<br />
check the camshaft bore for presence of scratch, wear,<br />
and excessive wear.<br />
If the bore is damaged to beyond the allowable range, replace<br />
the cylinder block<br />
15B-311<br />
(d). Measure the length for four sides and diagonal lines of<br />
If the degree of damage for hole exceeds the allowable limit,<br />
replace the cylinder block. If the dimension of cylinder block<br />
does not be changed, then the cam bush can be still used.<br />
(e). Measure the lengths for four sides and diagonal lines of<br />
If the measurement results are out of the specified range,<br />
replace the cylinder block.<br />
(f). Measure the surface levelness of the cylinder block with<br />
ruler and feeler gauge.<br />
Planeness:0.06,Depth of Parallelism:0.06<br />
Planeness:0.05,Depth of Parallelism:0.08<br />
repair the cylinder block and when necessary replace the<br />
Visually check whether the cylinder head gasket is<br />
damaged or has cracks. If the gasket if damaged or<br />
has cracks please replace it.<br />
15B-312<br />
Visually check the gasket of the cylinder head for<br />
presence of cracking and damage. If yes, replace the<br />
After taking down all accessories of cylinder block,<br />
clean the oil passage and water passage of cylinder<br />
block with water syringe.<br />
4. Install cylinder liner<br />
(a). Install cylinder liner with special tools.<br />
• Before installation, thoroughly clean the surface of cylinder<br />
liner and cylinder hole with new kerosene or diesel and blow<br />
dry the surface of cylinder liner and cylinder hole.<br />
• Eliminate all other things carefully on the cylinder liner and<br />
cylinder hole before installing cylinder liner.<br />
5. Install the cylinder block (Refer to Chapter 15 Engine Mechanical Part – Assembly of Engine<br />
491EQ1 and 491EQ3).<br />
EXHAUST SYSTEM ............................................................................... 16B-1<br />
Overview ............................................................................................ 16B-1<br />
Precautions ....................................................................................... 16B-2<br />
Working Principle ............................................................................. 16B-3<br />
EXHAUST MANIFOLD ........................................................................... 16B-4<br />
Diagram of Components (Exhaust System) ................................... 16B-4<br />
Service ............................................................................................... 16B-5<br />
EXHAUST PIPE ..................................................................................... 16B-9<br />
Diagram of Components .................................................................. 16B-9<br />
Removal and Installation ................................................................ 16B-10<br />
16B<br />
EXHAUST-EXHAUST SYSTEM<br />
16B-1<br />
1. Exhaust system consists of the exhaust manifold, muffler and exhaust manifold welding assembly,<br />
and other related lug bracket, in order to reduce the exhaust noise and exhaust energy.<br />
2. The exhaust manifold is an important component collecting the exhausts of engine cylinders and<br />
discharging.<br />
3. The function of muffler is to reduce the exhaust noise through gradually decreasing the exhaust<br />
pressure and exhaust pressure pulsation.<br />
4. The working principle of muffler is that the exhaust gas flows to the expansion chamber and<br />
resonance chamber through the porous tube, and the exhaust gas continually changes the flow<br />
direction during this process, gradually decreases and relieves the exhaust pressure and exhaust<br />
pressure pulsation, consumes the energy and ultimately reduce the exhaust noise.<br />
16B-2<br />
(a). Ensure the parking brake lever is placed on the parking location.<br />
(b). Fix the wheel with a wedge or corner block, wedge or corner block should be placed in the position<br />
close to both sides of the tire, it’s preferred to fix on both sides of the rear wheels.<br />
(c). If operates under the car, the engine should and ignition switch should be turned off..<br />
(a). Ensure the engine turned off when repairing the exhaust system, the maintenance work should only<br />
be conducted after the exhaust system completely cooled.<br />
(b). The exhaust pipeline should be checked frequently, any leaks should be dealt with immediately,<br />
tighten the connectors to avoid unnecessary losses.<br />
(c). After 4,000 ~ 5,000km drive, the exhaust pipe of the vehicle should be checked in the following<br />
aspects:<br />
• Whether any bolts and nuts are loosen. To tighten the bolts and nuts of exhaust pipe with uniform<br />
force, fastening the bolts in diagonal, or it may cause air leaks.<br />
• Whether there are any exhaust pipe cracks and perforations, and any damage or erosion for<br />
• The exhaust pipe gasket is suggested to be used once only; in order to ensure the tightness of<br />
exhaust system, timely replace the damaged gasket.<br />
16B-3<br />
each cylinder by intake manifold. The burned gas drains from exhaust manifold. The formed exhaust gas flow<br />
will impact turbine of turbocharger so that it can rotate at a high speed. The exhaust gas through turbine<br />
finally drains to the exterior by rear exhaust pipe. Part of exhaust gas in the exhaust manifold drains from<br />
EGR valve. Then this exhaust gas enters intake connecting pipe through EGR pipe, and is sent back to<br />
engine combustor for combustion again to suppress the generation of oxynitride.<br />
1 Rear exhaust pipe<br />
7 Turbocharger<br />
16B-4<br />
EXHAUST-EXHAUST MANIFOLD<br />
DIAGRAM OF COMPONENTS (EXHAUST SYSTEM)<br />
1 Exhaust manifold gasket component<br />
2 Exhaust manifold<br />
Hexagon head bolt and flat washer<br />
4 Heat insulation plate assemblyⅡ<br />
5 Flat washer<br />
6 Spring washer<br />
7 Bolt<br />
8 Booster bracket bolt<br />
9 Heat insulation plateⅠ<br />
10 Exhaust manifold bracket<br />
11 Flat washer<br />
12 Heavy spring washer<br />
13 Hexagon head bolt<br />
16B-5<br />
1. Remove the turbocharger assembly (Refer to Chapter 21 Booster System - Booster, Service).<br />
2. Remove the EGR valve assembly (Refer to Chapter 22 EGR System - EGR Valve, Service)<br />
3. Remove the heat insulation plate assemblyⅡ<br />
(a). Dismantle 2 fixing bolts of heat insulation plate<br />
assembly II.<br />
• Remove the heat insulation assembly II.<br />
4. Remove the turbocharger bracket<br />
(a). Dismantle 2 fixing bolts of turbocharger bracket.<br />
• Remove the turbocharger bracket.<br />
• Remove the heat insulation plate I.<br />
5. Remove the exhaust manifold bracket<br />
(a). Remove the fixing bolts of exhaust manifold bracket.<br />
• Remove the exhaust manifold bracket.<br />
6. Remove the exhaust manifold<br />
(a). Remove the fixing bolts of exhaust manifold.<br />
•Remove the exhaust manifold.<br />
16B-6<br />
7. Check and clean the exhaust manifold<br />
(a). Clean the sealing surface that combines exhaust<br />
manifold and turbocharger with a scraper knife and a<br />
clean cloth.<br />
Please prevent foreign matters from entering into the<br />
exhaust port<br />
Clean the sealing surface that combines exhaust<br />
manifold and cylinder head with a scraper knife<br />
and a clean cloth.<br />
Clean the carbon deposit on the sealing surface of<br />
exhaust manifold with a crocus cloth.<br />
(d). Clean the exhaust manifold with vapor.<br />
When cleaning the exhaust manifold with vapor, wear the<br />
protective goggles, protective masks and protective<br />
clothing to avoid personnel injury.<br />
Dry the exhaust manifold with compressed air.<br />
16B-7<br />
Check whether the sealing surface of exhaust manifold<br />
and turbocharger exists cracks and other damages. If<br />
severe damages exist, replace the exhaust manifold.<br />
and cylinder head exists cracks or other damages. If<br />
Check the flatness of exhaust manifold installation<br />
surface with a precision scale and a feeler gauge. If<br />
the unevenness exceeds technical scope, the exhaust<br />
manifold shall be machined or replace it with a new one.<br />
8. Install the exhaust manifold assembly<br />
(a). Place the exhaust manifold in the installation position the<br />
fixing bolts on it and fasten.<br />
The slinger ring and heat insulation plate set with exhaust<br />
manifold together shall be installed when installing the exhaust<br />
(b). Place the exhaust manifold bracket in the<br />
installation position the fixing bolts on it and fasten.<br />
16B-8<br />
Place the heat insulation plate Ⅰ and turbocharger<br />
bracket in the installation position the fixing bolts on it<br />
and fasten.<br />
Place the heat insulation plate assembly Ⅱ in the<br />
installation position 2 fixing bolts on it and fasten.<br />
9. Install the EGR valve assembly (Refer to Chapter 22 EGR System - EGR Valve, Service)<br />
10. Install the turbocharger assembly (Refer to Chapter 21 Booster System - Booster, Service)<br />
EXHAUST-EXHAUST PIPE<br />
16B-9<br />
1 Exhaust pipe gasket assembly<br />
2 Front exhaust pipe welding<br />
4 Spring washer<br />
6 Gasket<br />
7 Hexagon head bolt<br />
8 Hoop support plate<br />
9 Middle exhaust pipe assembly<br />
10 second connection rubber<br />
11 Muffler front gasket<br />
12 Hexagon head bolt<br />
13 Flat washer<br />
14 Spring washer<br />
15 Type 1 hexagon nut<br />
16 Muffler assembly<br />
17 Rear exhaust pipe assembly<br />
18 Exhaust pipe third bracket<br />
19 third connection rubber<br />
20 Hexagon head bolt<br />
21 Large washer<br />
22 Hoop<br />
23 Fourth connection rubber<br />
16B-10<br />
REMOVAL AND INSTALLATION<br />
As the exhaust pipe is relatively heavy, certain protective measures should be taken during the disassembly,<br />
it is preferred to be operated by two persons.<br />
1. Preparations<br />
Drive the car into the inspection pit or onto the car lift.<br />
Turn off the engine after stopping the car, disconnect the battery negative, place the transmission in<br />
neutral position, and turn on the parking brake system. Operate only after the exhaust system fully<br />
cooled.<br />
2. Disassemble the exhaust system assembly<br />
(a). Remove the connection nuts of front exhaust pipe<br />
welding and engine.<br />
• Remove the exhaust pipe gasket assembly.<br />
Remove the connecting bolts between front exhaust pipe<br />
welding and middle exhaust pipe assembly.<br />
• Remove the gasket.<br />
Remove the fixing bolts of hoop support plate.<br />
• Remove the front exhaust pipe welding.<br />
(d). Remove the connecting bolts between middle exhaust<br />
pipe assembly and muffler assembly.<br />
• Remove the muffler front gasket.<br />
Support the muffler assembly with safety bench to avoid falling;<br />
otherwise it may cause personal injury.<br />
16B-11<br />
Remove the second connection rubber between<br />
middle exhaust pipe assembly and frame.<br />
• Take out the second connection rubber.<br />
• Remove the middle exhaust pipe assembly.<br />
(f). Remove the connecting bolts between muffler<br />
assembly and rear exhaust pipe assembly.<br />
• Remove the muffler assembly.<br />
Remove the fixing bolts of exhaust pipe third bracket.<br />
Remove the fourth connection rubber of rear exhaust<br />
• Remove the rear exhaust pipe assembly.<br />
16B-12<br />
3. Check the exhaust system<br />
(a). Check whether there are too many gray or carbon<br />
particles inside the muffler, it should be cleaned if<br />
any.<br />
Cleaning method:<br />
• Purge the muffler assembly with compressed air until<br />
there is no heavy smoke emitted.<br />
Wear masks and goggles before cleaning, to avoid injury.<br />
(b). Check whether there are too much gray or carbon<br />
particle inside the front, middle and rear exhaust<br />
pipe assembly; if any, please remove and clean it.<br />
The cleaning method is the same as the previous step<br />
4. Install the exhaust system assembly<br />
(a). Place the rear exhaust pipe assembly and fourth<br />
connection rubber in the installation position, and<br />
install the connection rubber to the frame.<br />
Install the fixing bolts of the exhaust pipe third bracket.<br />
(c). Place the muffler assembly in the installation position;<br />
connect the bolts between the muffler assembly and<br />
rear exhaust pipe and fasten.<br />
Replace the gasket assembly of exhaust pipe.<br />
16B-13<br />
Place the middle exhaust pipe assembly and second<br />
connection rubber in the installation position, and install<br />
the second connection rubber to the frame.<br />
(e). Connect the bolts between the middle exhaust pipe<br />
assembly and muffler assembly and fasten.<br />
Replace the front gasket of muffler.<br />
(f). Place the front exhaust pipe welding in the installation<br />
position, connect the bolts of hoop support plate and<br />
(g). Connect the bolts between front exhaust pipe welding<br />
and middle exhaust pipe assembly and fasten.<br />
The gasket shall be replaced.<br />
(h). Fasten the connection nuts of front exhaust pipe<br />
The exhaust pipe gasket assembly shall be replaced.<br />
COOLING SYSTEM........................................................................... 17B-1<br />
Overview ............................................................................................. 17B-1<br />
Precautions ........................................................................................ 17B-2<br />
Working Principle .............................................................................. 17B-3<br />
Diagram of Components ................................................................... 17B-4<br />
THERMOSTAT ................................................................................... 17B-7<br />
Service ................................................................................................ 17B-7<br />
TRANSMISSION BELT ................................................................... 17B-11<br />
Service .............................................................................................. 17B-11<br />
PULLEY AND FAN .......................................................................... 17B-14<br />
Service .............................................................................................. 17B-14<br />
WATER PUMP ................................................................................. 17B-16<br />
Service .............................................................................................. 17B-16<br />
OIL COOLER ................................................................................... 17B-19<br />
Service .............................................................................................. 17B-19<br />
EXPANSION TANK ......................................................................... 17B-21<br />
Replacement ..................................................................................... 17B-21<br />
COOLING PIPELINE ....................................................................... 17B-23<br />
Replacement ..................................................................................... 17B-23<br />
RADIATOR ....................................................................................... 17B-25<br />
Replacement ..................................................................................... 17B-25<br />
17B<br />
COOLING-COOLING SYSTEM 17B-1<br />
1. The main functions for cooling system are to timely radiate some heat which is absorbed by heated<br />
parts to ensure that the engine works under the condition of the most appropriate temperature.<br />
2. The thermostat controls temperature of engine coolant. When coolant temperature is lower than<br />
engine functioning temperature, the engine coolant reflows the inlet of water pump through the<br />
bypass to make the coolant temperature is the same with engine functioning temperature. When the<br />
engine coolant temperature is the same with the functioning temperature, the thermostat opens and<br />
the bypass is closed, which makes engine coolant flow into the radiator to make the coolant<br />
temperature is the same with the functioning temperature.<br />
3. The centrifugal water pump consists of impeller, water pump housing, bearing and water seal. The<br />
water pump is driven by crank pulley and fan belt. When water seal is damaged and the dripping<br />
phenomenon is very serious, the water seal shall be replaced. Do not allow to block the outlet when<br />
water leakage, or else the water will enter the bearing to make the bearing quickly wear down. If there<br />
is abnormal noise in the bearing during running, then the bearing shall be considered to be replaced.<br />
4. The fan is induced draught plastic fan. The tensioning degree of fan belt shall be checked regularly<br />
according to the requirements of “technical maintenance” and the fan belt shall be adjusted. The<br />
adjustment shall be carried out manually with a force of 70~80N to press the belt between the fan and<br />
generator pulley. The proper pressing distance is the range of 7~8mm (for new belt is 6~7mm).<br />
5. Silicon oil fan clutch takes silicon oil as medium and makes use of silicon oil’s high viscosity to<br />
transmit the torque. The separation and joint of fun clutch are automatically controlled by temperature<br />
detector when making use of the atmosphere temperature on the back of radiator.<br />
Temperature-sensing elements are thermometal coiled spring temperature sensors. When the<br />
temperature of air which is flowing through the radiator increases, thermal deformations of<br />
thermometal temperature sensors occur and the valve plate shaft is forced to rotate to open the oil<br />
supply hole on the driven plate. The silicon oil that stored between the driven plate and the front cover<br />
flows into the operating cavity between the drive plate and driven plate and the clutch engages, fan<br />
speed increases. The opening of oil supply hole shall be larger with higher air temperature and the<br />
fan speed is higher; however, when the temperature of air which is flowing through the radiator<br />
reduces, thermometal temperature sensors shall be reinstated, valve plate close the oil supply hole.<br />
With the effect of centrifugal force, silicon oil returns to oil chamber from the operating cavity through<br />
oil return hole. The clutch disengages and fan speed reduces to a very low one.<br />
6. The drain screw is for the drain of the engine’s coolant in coolant change.<br />
7. Oil cooler is used for oil cooling in order to maintain the oil temperature in proper rang for better<br />
engine performance and longer service life of the engine. In the case of oil in engine coolant, carry out<br />
service for oil cooler immediately.<br />
8. The radiator is pressure water tank which is the device sending out the coolant heat to the<br />
atmosphere. The functions of radiator: enlarge radiating area and accelerating the water cooling.<br />
9. The expansion tank is to reduce the losses of coolant of cooling system.<br />
10. Two water level scales on the surface of expansion tank express limiting altitude on the liquid surface<br />
17B-2 COOLING-COOLING SYSTEM<br />
1. Safety precaution<br />
(a). Make sure to place the parking brake handle in the parking position.<br />
(b). Fasten the wheel with corner blocks or wedge and the corner blocks or wedge shall be placed on two<br />
sides of wheel. And the two sides of rear wheel shall be fixed better.<br />
(c). The engine shall be shut down and the switch of ignition lock shall be shut down when working at the<br />
bottom of the car.<br />
(a). When disconnecting the cooling system pipeline, do not make the coolant overflow. If it cannot be<br />
continuously used, it shall be abandoned according to the regulations.<br />
(b). When disconnecting the cooling system pipeline, do not make the chips enter the cooling system<br />
pipeline, because the chips which enter the cooling system pipeline will damage the cooling system<br />
and engine.<br />
(c). The coolant is poisonous and if it cannot be continuously used, dispose of the coolant according to<br />
the regulations.<br />
(d). When maintaining the cooling system, pay attention to coolant temperature. If the temperature is too<br />
high, the operation shall be carried on after the coolant temperature is lower.<br />
(e). Reasonably use antifreeze solution. The antifreeze solution is poisonous and can irritate to the skin<br />
and inner organs. Do not suck the antifreeze solution when using it. Clean hands if the hands touch<br />
the antifreeze solution and timely wash the eyes if the antifreeze solution enters eyes.<br />
COOLING-COOLING SYSTEM 17B-3<br />
When the temperature of engine coolant is higher than the nominal temperature of thermostat, coolant flows<br />
out through engine water outlet and gets into the radiator through open thermostat then it flows through oil<br />
cooler and gets into the water pump through the water inlet of the pump to complete internal circulation in<br />
engine body. However, when the temperature of engine coolant is lower than the nominal temperature of<br />
thermostat, because the thermostat is closed and bypass is open, the coolant flows into the water inlet of<br />
water pump through bypass pipe to complete internal circulation in engine body. Part of coolant in engine<br />
body may flow into heater through heater water inlet pipe and then get into water pump water inlet through<br />
heater water return pipe, finally it shall return to engine body for internal circulation.<br />
1 Radiator<br />
2 Oil cooler<br />
3 Oil filter<br />
4 Heater water outlet pipe<br />
5 Fan heater<br />
6 Heater water inlet pipe<br />
7 Expansion tank<br />
8 Thermostat<br />
9 Engine water outlet pipe<br />
10 Bypass pipe<br />
11 Water pump<br />
17B-4 COOLING-COOLING SYSTEM<br />
(Thermostat)<br />
1 Plug<br />
2 Copper backing<br />
3 Screw plug<br />
5 Water outlet pipe<br />
6 Thermostat<br />
7 Water outlet pipe gasket<br />
8 Housing gasket<br />
9 Harness clamp<br />
10 Short circle pipe joint<br />
11 Heating pipe clamp<br />
12 Bypass hose<br />
13 Hexagon tapered screw plug<br />
14 Thermostat housing<br />
15 Heater water inlet pipe<br />
16 Heater water pipe<br />
Water outlet rubber hose at thermostat<br />
end<br />
Water return rubber hose at thermostat<br />
19 Machine cooler steel pipe welding part<br />
21 Heater opening cap<br />
(Fan and water pump pulley chamber cover assembly)<br />
COOLING-COOLING SYSTEM 17B-5<br />
1 Fan component<br />
2 Silicon oil clutch component<br />
3 Type 1 hexagon nut<br />
7 Water pump pulley<br />
8 Fan belt<br />
9 Water pump O ring<br />
Water pump pulley chamber cover<br />
12 Spring washer<br />
16 Bolt<br />
17 Bolt<br />
18 Harness clamp<br />
17B-6 COOLING-COOLING SYSTEM<br />
(Radiator)<br />
1 Radiator assembly<br />
2 Spring hose clamp<br />
3 Connecting hose<br />
4 Nylon cable tie<br />
5 Engine water inlet hose<br />
6 Type A worm drive hose clamp<br />
Hexagon head bolt, Spring washer and<br />
Flat washer assembly<br />
8 Engine water outlet hose<br />
11 Expansion tank assembly<br />
12 Protective fan housing assembly<br />
COOLING-THERMOSTAT<br />
17B-7<br />
1. Thermostat Dismantle<br />
(a). Dismantle fixing bolts of thermostat cap, take down<br />
bolts and Harness clamp.<br />
(b). Take down thermostat cap.<br />
Take down thermostat cap and housing gasket at the same<br />
Take out the thermostat.<br />
2. Checking and Cleaning<br />
(a). Check the appearance of thermostat for damage.<br />
• Check for the existence of crack, embedded scrap,<br />
loss of one-way valve, ball seat damage and other<br />
damages.<br />
• In the case of discovery of damage, replace the<br />
17B-8<br />
Shovel the remained gasket at the contact surface<br />
between the thermostat housing and thermostat cap.<br />
Clean the installation surface of thermostat housing.<br />
Check the installation surface of thermostat housing for<br />
crack and damage.<br />
• In the case of discovery of crack and scars,<br />
replace the thermostat housing.<br />
3. Measure<br />
(a). If the thermostat is considered to have fault, measure<br />
thermostat temperature of turning on the thermostat,<br />
and place thermostat and a thermometer with 100℃ of<br />
measuring range into a water container.<br />
Do not make thermostat or thermometer contact the<br />
container.<br />
17B-9<br />
(b). Heat the water and check the thermostat according to<br />
• Heat the water in the container to the temperature<br />
which is higher than nominal working temperature<br />
of thermostat and then the thermostat will<br />
automatically turn on.<br />
• If the thermostat cannot automatically turn on<br />
when the temperature for water in the container is<br />
higher than the nominal working temperature, it<br />
indicates that the thermostat is damaged or the<br />
model is not right and then the thermostat shall be<br />
Thermostat is marked with nominal working temperature.<br />
4. Install thermostat<br />
(a). Apply sealant on the installation surface of thermostat<br />
housing.<br />
(b). Replace with a new gasket.<br />
No matter whether the gasket is damaged, please replace<br />
the gasket.<br />
Install thermostat.<br />
17B-10<br />
(d). Install the thermostat cap.<br />
Sealant shall be applied on the installation surface of<br />
thermostat cap.<br />
Screw on fixing bolts and Harness clamps for<br />
thermostat cap and tighten them.<br />
TRANSMISSION BELT<br />
COOLING-TRANSMISSION BELT<br />
17B-11<br />
1. Dismantle fan and silicon oil clutch<br />
(a). Dismantle the nuts on the flange of silicon oil clutch.<br />
(b). Slowly take down fan and silicon oil clutch.<br />
The fan and silicon oil clutch which are not separated can be<br />
taken down.<br />
2. Dismantle fan pulley and fan belt<br />
(a). Loosen the generator bracket and dismantle the fan<br />
belt pulley and fan belt.<br />
3. Check belt appearance<br />
(a). Carefully check each part of belt. If there are the<br />
following damages, please replace the pulley.<br />
• The rubber on the back is ageing and light-reflective,<br />
in the case of nail scratching, there is no scratch and<br />
the rubber is inelastic.<br />
17B-12<br />
• There is crack of the rubber on the back.<br />
• There is crack on toothed bottom.<br />
4. Install fan pulley and fan belt<br />
(a). Place the fan belt to installation position and install the<br />
After belt installation, check the belt tension firstly and then<br />
adjust the position of generator for proper belt tension.<br />
5. Check and adjust belt tension<br />
(a). Press down the belt between water pump and<br />
generator pulley with hands to check the belt<br />
deflection.<br />
Press down the belt with 70~80N of force and the belt<br />
deflection shall be 7~8mm (the new belt deflection shall be<br />
6~7mm)<br />
Unscrew fixing bolts of generator bracket; adjust belt<br />
tension by changing the position of generator. After that,<br />
check the belt deflection. Tighten fixing bolts of bracket<br />
until proper belt tension has been reached.<br />
17B-13<br />
6. Install fan and silicon oil clutch<br />
(a). Place the fan and silicon oil clutch in the installation<br />
(b). Tighten all nuts for studs.<br />
Rotate the fan and check whether the installation is correct.<br />
17B-14<br />
COOLING-PULLEY AND FAN<br />
PULLEY AND FAN<br />
1. Dismantle the fan and silicon oil clutch (refer to Chapter 17B Cooling-Drive Belt, Dismantle)<br />
2. Separate the fan and silicon oil clutch<br />
(a). Dismantle the fixing bolts on the fan.<br />
Push down the silicon oil clutch backward slowly to<br />
separate the fan and silicon oil clutch.<br />
3. Cleaning the pulley<br />
(a). Clean the pulley with solvent.<br />
In cleaning with solvents, acid or alkali materials please<br />
follow the instructions of the manufacturer. Wear safety<br />
goggles and protective clothing to avoid personal injury.<br />
Check the bolt hole and its surrounding area of fan<br />
pulley for crack and check damage in the contact<br />
surface with drive belt.<br />
• Fan belt in the case of discovery of pulley damage,<br />
the fan belt shall be checked, too.<br />
17B-15<br />
4. Check the fan<br />
(a). Check whether there is crack or incomplete<br />
phenomenon in cooling fan.<br />
• In the case of crack or incomplete phenomenon,<br />
please replace the fan.<br />
5. Assemble the fan and silicon oil clutch<br />
(a). Align the fan bolt holes with corresponding bolt holes of<br />
the silicon oil clutch and tighten all nuts of the fan.<br />
17B-16<br />
COOLING-WATER PUMP<br />
WATER PUMP<br />
1. Preliminary check<br />
(a). Clean external water pump of generator with steam or<br />
hydraulic giant.<br />
Wear safety goggles and protective mask and protective<br />
clothing when using the steam to clean. The hot steam is<br />
possible to lead to serious personal injury.<br />
(b). Make the engine run at low idle speed to check<br />
whether the water pump leaks.<br />
2. Dismantle the water pump assembly<br />
(a). Dismantle the fixing bolts of crank position sensor and<br />
take down the sensor.<br />
Dismantle the fixing bolts of crank pulley and take down<br />
Dismantle the fixing bolts of sight hole and take down<br />
the sight-hole cover.<br />
17B-17<br />
(d). Dismantle all remained fixing bolts on water pump<br />
pulley chamber cover.<br />
There is a fixing bolt on the rear housing of crank pulley.<br />
Take down the water pump pulley chamber cover<br />
3. Clean and continuously check<br />
(a). Clean the water pump pulley chamber cover assembly.<br />
with solvent.<br />
Please keep to the manufacturer’s suggestions for use<br />
when using solvent, acid or basic materials. Wear goggles<br />
and protective clothing to avoid personal injury.<br />
(b). Dry the water pump pulley chamber cover assembly.<br />
with compressed air.<br />
Wear proper goggles and protective mask to avoid flying<br />
chips and dirt to avoid personal injury.<br />
Check the water pump pulley chamber cover assembly<br />
for crack. In the case of obvious damage, replace the<br />
water pump pulley chamber cover assembly.<br />
17B-18<br />
Check the water pump impeller for pitting and crack. In<br />
the case of obvious damage, replace the water pump<br />
pulley chamber cover assembly.<br />
4. Install the water pump assembly<br />
(a). Place the water pump pulley chamber cover assembly.<br />
To installation position, put on bolts and tighten.<br />
Place the sight-hole cover to installation position, put<br />
on bolts and tighten.<br />
Place the crank pulley to installation position, put on<br />
bolts and tighten.<br />
Place the crank position sensor to installation position,<br />
put on bolts and tighten.<br />
COOLING-OIL COOLER<br />
17B-19<br />
OIL COOLER<br />
1. Dismantle the oil cooler.<br />
(a). Drain the coolant.<br />
(b). Disconnect the water inlet and outlet pipes of oil cooler.<br />
Dismantle center bolts of oil cooler and take down the<br />
oil cooler.<br />
2. Check the oil cooler<br />
(a). Plug the water outlet pipe of the oil cooler, connect the<br />
water inlet pipe with inflator and put them into water<br />
basin with the oil cooler submerged in the water<br />
In the case of bubbles appearing in the water basin, replace<br />
with a new oil cooler.<br />
3. Install the oil cooler<br />
(a). Place the oil cooler to installation position and tighten<br />
its center bolts.<br />
17B-20<br />
Connect the water inlet and outlet pipes of the oil<br />
cooler.<br />
COOLING-EXPANSION TANK<br />
17B-21<br />
EXPANSION TANK<br />
1. Dismantle expansion tank<br />
(a). Disconnect the connection between radiator and<br />
connecting hose.<br />
Loosen Nylon cable tie and lock iron sheet on the<br />
Disconnect the connection between expansion tank<br />
and connecting hose.<br />
Dismantle the fixing bolts of expansion tank assembly.<br />
Take down the expansion tank assembly.<br />
2. Check whether there is crack and leakage phenomenon, if yes, then replace it.<br />
17B-22<br />
3. Install the expansion tank<br />
(a). Place the expansion tank in the correct installation<br />
(b). Install and fasten the fixing bolts of expansion tank.<br />
Correctly connect the connecting hose and expansion<br />
Correctly connect the connecting hose and radiator.<br />
(e). Fill the antifreeze solution to the suitable height.<br />
In antifreeze solution filling, it is preferable to place a flared<br />
vessel under the opening of expansion tank.<br />
User can choose different marks of antifreeze solution<br />
according to the local atmosphere temperature.<br />
(f). Fasten the water outlet hose of expansion tank with<br />
nylon cable tie and lock iron sheet.<br />
After finishing installation, start the engine, and then observe<br />
the liquid level height in the expansion tank when the water<br />
temperature in the engine rises to 80℃. If the coolant is<br />
insufficient, then add the coolant according to the scale of<br />
expansion tank.<br />
COOLING-COOLING PIPELINE<br />
17B-23<br />
COOLING PIPELINE<br />
1. Open the front cabin cover<br />
2. Place coolant<br />
(a). Dismantle the drainage bolt of radiator and drain the<br />
coolant of cooling pipeline empty and place the<br />
container under the radiator to storage antifreeze<br />
coolant.<br />
Do not dismantle cooling pipeline and drain the coolant when<br />
the engine water temperature is higher than 50℃ to avoid<br />
scald and engine part damage.<br />
Screw off the cover of radiator and shorten the<br />
drainage time.<br />
3. Dismantle cooling hose<br />
(a). Screw off A-type worm drive hose clamp which<br />
connects radiator water inlet hose and water inlet or<br />
water outlet hose and water outlet.<br />
Screw off A-type worm drive hose clamp which<br />
connects radiator water inlet hose and engine water<br />
outlet or water outlet hose and engine water inlet.<br />
• Take down the radiator water inlet and outlet<br />
hoses.<br />
17B-24<br />
4. Check cooling hose<br />
(a). Check whether the cooling hose has crack or<br />
expansion, if yes, and then replace the cooling hose<br />
5. Install cooling pipeline<br />
(a). Install the radiator water outlet hose in the engine water<br />
inlet and install the radiator water inlet hose in engine<br />
water outlet, and fasten the A-type worm drive hose<br />
Install the radiator water outlet hose in the water outlet<br />
and install the water inlet hose in water inlet, and fasten<br />
the A-type worm drive hose clamp.<br />
Install and fasten the drainage bolts and seal washer in<br />
the drainage hole which is at the bottom of radiator.<br />
(d). Fill the antifreeze coolant in the proper position and<br />
screw on the cover of radiator.<br />
COOLING-RADIATOR<br />
17B-25<br />
1. Dismantle the radiator assembly<br />
(a). Dismantle the drainage bolts on the radiator and drain<br />
coolant in the radiator and cooling pipeline. Place a<br />
container at the bottom of radiator to storage antifreeze<br />
Screw out the cover of radiator and shorten the<br />
drainage time in order to be conveniently dismantled.<br />
Disconnect the connection between the radiator and<br />
expansion tank and radiator connecting pipe assembly.<br />
17B-26<br />
Dismantle the connecting bolt between radiator and fan<br />
shroud.<br />
Dismantle the fixing bolts of radiator.<br />
Take down radiator assembly.<br />
2. Clean and detect radiator<br />
(a). Block up other water outlets of radiator. Fill certain<br />
pressure water in the radiator and make sure that each<br />
part of radiator has no leakage.<br />
In the case of leakage for radiator, please timely service or<br />
If there are foreign matters on the radiator, the heat<br />
radiating ability for the cooling system will be reduced.<br />
Check whether the radiating fin is blocked off. If it is<br />
blocked off, clean the radiator surface with compressed<br />
air or with not high water pressure.<br />
Thoroughly clean the inner radiator with water.<br />
17B-27<br />
3. Install radiator assembly<br />
(a). Place the radiator in the correct installation position.<br />
(b). Install and fasten the fixing bolts on both sides of<br />
Install and fasten the connecting bolts between radiator<br />
and fan shroud.<br />
A-type worm drive hose clamp.<br />
Connect the radiator and expansion tank to the radiator<br />
drainage hole which is at the bottom of radiator.<br />
17B-28<br />
(g). Fill the antifreeze coolant in the proper position and<br />
润 滑 系 统 - 润 滑 系 统 16B-1<br />
LUBRICATION SYSTEM .......................................................................... 18B-1<br />
Overview ............................................................................................... 18B-1<br />
Flow Process Diagram ........................................................................ 18B-3<br />
Diagram of Components I ................................................................... 18B-4<br />
Diagram of Components II .................................................................. 18B-5<br />
Measurement ........................................................................................ 18B-6<br />
Discharge .............................................................................................. 18B-8<br />
Checking ............................................................................................... 18B-9<br />
Injection .............................................................................................. 18B-10<br />
OIL DIPSTICK ......................................................................................... 18B-12<br />
Service ................................................................................................ 18B-12<br />
OIL PAN ................................................................................................... 18B-14<br />
Service ................................................................................................ 18B-14<br />
OIL PUMP ................................................................................................ 18B-17<br />
Service ................................................................................................ 18B-17<br />
OIL FILTER .............................................................................................. 18B-22<br />
Service ................................................................................................ 18B-22<br />
18B<br />
18B-1<br />
1. The lubrication system consists of oil suction filter, oil pump, oil filter, oil dipstick and pipelines.<br />
2. Because of different operation conditions of engine moving parts, the required lubrication strengths are<br />
also different, so are the applied lubrication methods. There are three types of lubrication methods:<br />
pressure lubrication, splash lubrication and gravity lubrication.<br />
• With the pressure lubrication method, the lubrication oil will be send to each friction surface forcibly<br />
by oil pump. Generally, the part which is bearing heavy load in operation or with high kinematic<br />
velocity, such as crankshaft main bearing and wheel bearing etc., shall adopt this pressure<br />
lubrication method. Moreover, as for the parts such as valve rocker arm shaft and others, the<br />
pressure lubrication method shall be adopted because the light bearing load and its mounting<br />
position on the cylinder head.<br />
• With the splash lubrication method, the lubrication is carried out by oil mist formed by the lubrication<br />
oil thrown out by rod journal and main journal and the lubrication oil thrown out by special oil jet.<br />
Generally, the parts which are bearing light load or with low kinematic velocity, such as cam running<br />
surface, tappet etc., shall adopt the splash lubrication method. In addition, although the working<br />
load of cylinder wall is heavy, it is not advised to apply excessive lubrication oil in case of oil flowing<br />
to the combustion chamber and the working deterioration of engine. For this reason, the cylinder<br />
wall shall be lubricated with splash lubrication method.<br />
• The gravity lubrication method carries out the lubrication with the gravitational flow of lubrication oil<br />
itself, for example, the lubrication for air rod and push rod along rocker arm is carried out by swaying<br />
the rocker arm with the gravity of lubrication oil.<br />
3. Passing through the oil suction filter, the oil stored in oil pan will be sucked into oil pump by means of oil<br />
inlet pipe and carried to oil filter after pressurization. The filtered oil can access to the main oil gallery of<br />
engine block by three ways:<br />
• One way passing by the main bearing, crankshaft oil hole and reaching the connecting rod bearing.<br />
• One way passing by the camshaft bush, eccentric oil groove of cam journal and interruptedly<br />
supplying oil to the rocker arm shaft bush.<br />
• One way passing by the bearing of correct timing idle gear.<br />
4. The scientific name of oil is lubrication oil which plays an significant role in normal operation of engine.<br />
Lubrication action: lubricate the surface of moving part, reduce the frictional resistance and abrasion<br />
and decrease the power consumption of engine.<br />
Cleanup action: the oil will constantly circulate in lubrication system, clean the friction surface and take<br />
away abrasive dust and other foreign matters.<br />
Cooling action: the oil will constantly circulate in lubrication system, take away the fricative heat of parts<br />
and carry out the cooling performance.<br />
Sealing action: there will be an oil film between each two moving parts. This is helpful to increase their<br />
leak proofness and avoid air leakage or oil leakage.<br />
Anti-corrosion action: there will be an oil film on the surface of part to protect the part’s surface and<br />
avoid corrosion and rusting.<br />
Hydraulic pressure action: the lubrication oil can be used as hydraulic oil, such as hydraulic tappet, to<br />
carry out the function of hydraulic pressure.<br />
18B-2<br />
Damping and buffer action: there will be an oil film on the surface of moving part to absorb the impact,<br />
reduce small vibration, attenuate the shock and realize the buffer action.<br />
18B-3<br />
FLOW PROCESS DIAGRAM<br />
18B-4<br />
DIAGRAM OF COMPONENTS I<br />
1 Spin-on filter element and seal ring<br />
2 Oil filter seal ring<br />
3 Oil filter seat component<br />
4 Flat washer<br />
5 Spring washer<br />
6 Hexagon head bolt<br />
7 Oil cooler component<br />
combination<br />
9 Connection hose<br />
10 Oil cooler outlet hose<br />
11 Oil cooler inlet hose<br />
12 Oil pump part<br />
flat washer combination<br />
14 Seal ring<br />
15 Oil pump outlet pipe component<br />
18B-5<br />
DIAGRAM OF COMPONENTS II<br />
Hexagon head bolt, spring washer and flat<br />
washer combination<br />
2 Oil drain plug<br />
3 Sealing gasket<br />
4 Small oil pan<br />
5 Oil pan gasket<br />
and flat washer combination<br />
7 Aluminum oil pan assembly<br />
9 Aluminum oil pan rear gasket<br />
10 Aluminum oil pan front gasket<br />
18B-6<br />
MEASUREMENT<br />
Measure the oil level in the oil pan to see whether it is between two scale marks of oil dipstick.<br />
• When measuring, the automobile shall be parked at the level position and the engine shall be<br />
stopped. One shall pull out the oil dipstick when the oil level is static, wipe out the oil on oil dipstick<br />
with clean cotton cloth, plug the oil dipstick into oil pan again till the end of dipstick and then pull<br />
out the oil dipstick to check the oil level.<br />
• When the filled oil of new gasoline engine or the one which is not used for a long time reaches the<br />
upper scale mark, one shall park the automobile after running for 5-10min at low speed and<br />
remeasure the oil level with oil dipstick.<br />
1. Check the oil level<br />
(a). Park the automobile on the road with level surface and turn<br />
off the engine.<br />
• If the automobile service time is not long, the engine<br />
shall be started to run for a few minutes.<br />
• Turn off the engine, wait at least 5min and then check<br />
the oil level.<br />
Open the automobile engine hood.<br />
Take out the oil dipstick.<br />
18B-7<br />
(d). Check the oil level<br />
There are upper and lower scale marks on oil dipstick in order to<br />
facilitate checking the oil level. The oil level shall not be lower<br />
than the lower scale mark in case of that the oil pump cannot<br />
suck up oil. The oil is also not appropriate to be higher than the<br />
upper scale mark in case of the impact of crank of crankshaft<br />
to oil surface leading to excessive oil mist and splash oil drop in<br />
crank case and serious carbon deposit on the top of piston and<br />
combustion chamber walls. Meanwhile, there are some faults<br />
such like that the piston ring is stuck by coking, the diesel engine<br />
generates smokes and oil seal leakage and the increase of oil<br />
consumption. For these reasons, besides paying attention to the<br />
oil pressure, one shall also check the oil level before driving or<br />
for every 300~500Km running distance of automobile.<br />
Besides paying attention to the oil pressure while operation,<br />
one shall also check the oil level before driving.<br />
18B-8<br />
DISCHARGE<br />
1. Dismantle the engine assembly. (Refer to Chapter 15A Engine Mechanical Part - Disassembly of<br />
Engine.)<br />
2. Dismantle the oil drain bolt<br />
• Do not reuse the disassembled bolt gasket and please<br />
replace it with a new one.<br />
Before discharging the oil, the engine shall continue<br />
running till the oil temperature reaching approximate 80°C<br />
to ensure that all oil and suspended dirt are discharged.<br />
3. Discharge the oil in oil pan<br />
• One shall prevent his/her skin from contacting the hot oil<br />
when discharging oil in order to avoid scalding.<br />
• One shall properly handle the used oil to protect the<br />
environment.<br />
4. Lubrication oil drain bolt<br />
When placing the lubrication oil drain bolt, the clean oil is<br />
required.<br />
5. Install and fasten the oil drain bolt<br />
Whenever the oil drain bolt is dissembled, the oil drain bolt<br />
washer shall be replaced by a new one.<br />
18B-9<br />
CHECKING<br />
1. Check the oil drain bolt on oil pan to see whether it<br />
is loose. If it is loose, the bolt shall be screwed up.<br />
2. Check the threads of oil drain bolt to see whether it<br />
is damaged. If it is damaged, the bolt shall be<br />
3. Check the threads of oil drain bolt to see whether it<br />
is damaged. If it is damaged, the bolt shall be tapped<br />
or the hole shall be expanded and maintained.<br />
4. Check the fixing bolt on oil pan to see whether it is<br />
loose. If it is loose, the bolt shall be screwed up or<br />
be replaced when necessary.<br />
18B-10<br />
INJECTION<br />
1. Unscrew the oil filler cap<br />
(a). Take down the oil filler cap.<br />
The oil filler shall be cleaned by wiping prior to taking down the<br />
oil filler cap to avoid access of foreign matters.<br />
2. Change oil<br />
When using for a long time, not only foreign matter or dust will exist in oil, but some unburned fuel oil will also<br />
mix with oil to reduce the oil density. Moreover, there will be eroded parts due to oil deterioration when bringing<br />
in part of exhaust gas with acid anhydride etc. For this reason, when used for a period, the oil shall be<br />
discharged completely and changed with fresh oil.<br />
Replace it every 5,000Km.<br />
• Use the diesel oil of grade CF-4 or above that conforms to the Q/SH038.202-1997 specification for<br />
the Great Wall Oil Company.<br />
• Select the oil according to ambient temperature when using.<br />
18B-11<br />
3. Fill the oil<br />
If the oil quantity of oil pan is unknown, the filled oil shall reach to<br />
the minimum volume of oil pan. Then one shall conduct the<br />
filling several times and fill a certain amount of oil each time till<br />
the oil level reaching the upper oil level mark on oil dipstick.<br />
Record the filling amount for knowing the oil volume when the<br />
next time replacement of oil.<br />
• Do not fill till overflow in case of air inflation of oil or the<br />
loss of oil pressure.<br />
• The filled oil shall not be mixed with moisture and<br />
foreign matters.<br />
• It is prohibited to use the mixture of oils with different<br />
brands and manufacturers.<br />
4. Screw up the oil filler cap<br />
(a). Install the oil filler cap.<br />
As for every time of oil change, the diesel engine shall run with<br />
no load for a short period to ensure sufficient oil providing to the<br />
lubrication system and its parts which require the oil supply.<br />
Meanwhile, one shall also check the oil leakage phenomena of<br />
oil drain bolt, fuel filter and surrounding parts.<br />
(b) Check the oil level.<br />
such like that the piston ring is stuck by coking, the gasoline<br />
engine generates smokes and oil seal leakage and the increase<br />
of oil consumption. For these reasons, besides paying attention<br />
to the oil pressure, one shall also check the oil level before<br />
driving or for every 300~500Km running distance of automobile.<br />
18B-12<br />
LUBRICATION - OIL DIPSTICK<br />
OIL DIPSTICK<br />
1. Service the oil dipstick<br />
(a). Clean the ambient dusts of oil dipstick with compressed<br />
Disengage the connection of oil dipstick pipe and engine<br />
Dismantle the oil dipstick pipe upper bracket fixing bolt.<br />
Dismantle the oil dipstick pipe lower bracket fixing bolt.<br />
18B-13<br />
Take out the oil dipstick assembly.<br />
Install the oil dipstick assembly onto the specified<br />
Install the oil dipstick pipe lower bracket fixing bolt.<br />
Install the oil dipstick pipe upper bracket fixing bolt.<br />
Connect the connection of oil dipstick pipe and engine<br />
18B-14<br />
The oil in oil pan shall be ensured to be discharged completely before dismantling the oil pan.<br />
1. Dismantle the oil pan<br />
(a). Turn over the engine body.<br />
(b). Dismantle the fixing bolt of oil pan.<br />
2. Disassemble the oil pan assembly<br />
(a). Disassemble the small oil pan fixing bolt.<br />
(b). Take down the small oil pan and small oil pan gasket.<br />
Do not reuse the removed oil pan gasket and please replace it<br />
with a new one.<br />
18B-15<br />
3. Clean and check the oil pan.<br />
(a). Scrape all the remaining sealing materials on the oil pan<br />
and cylinder block, and clean the oil pan with vapor, dry<br />
the oil pan with compressed air.<br />
No.5 and No.7 machine oil (light spindle oil) can also be used<br />
when the oil pan is cleaned, and never use gasoline or kerosene<br />
to clean.<br />
• Please wear safety glasses or protective mask and<br />
protective clothing to avoid serious personal injuries<br />
caused by hot vapor.<br />
• When using the compressed air, please wear proper<br />
safety glasses and protective mask to avoid personal<br />
injuries caused by splash scraps and dirt.<br />
(b). Check the oil pan to see whether it can still be used.<br />
• The oil pan is used to store the oil and dissipate the heat of oil.<br />
Dints and cracks are not allowed on oil pan.<br />
• When the cracks are not serious, the oil pan can still be<br />
reused instead of being replaced.<br />
4. Install the oil pan assembly<br />
(a). Install the small oil pan and gasket to designated<br />
Install and fasten the small oil pan fixing bolt.<br />
18B-16<br />
Install the oil pan assembly to a designated position.<br />
Install and fasten the fixing bolts of oil pan.<br />
Overturn and adjust the engine block.<br />
18B-17<br />
1. Dismantle the oil pan assembly. (Refer to Chapter 18B Lubrication-Oil Pan, Service.)<br />
2. Dismantle the oil pump assembly<br />
(a). Dismantle 2 fixing bolts of oil pump.<br />
Disconnect the connection of oil pump outlet pipe and oil<br />
Take down the oil pump and oil pump outlet pipe.<br />
3. Disassemble the oil pump<br />
(a). File the rivet point of pinion stopper pin.<br />
18B-18<br />
Drift the pinion out with a pivot-end drift pin.<br />
Take down the pinion.<br />
Dismantle the fixing bolt of oil pump cover and take<br />
down the oil pump cover.<br />
Put the mark on the rotor to confirm the correct direction<br />
when assembling and dismantle the rotor.<br />
4. Service for the oil pump<br />
(a). Check the clearance between rotor and oil pump cover<br />
with a feeler gauge. If there is severe wear, replace the<br />
inside and outside rotors or the oil pump assembly.<br />
Standard value: 0.06 mm<br />
Limit value: 0.15 mm<br />
18B-19<br />
Check the clearance between rotor and oil pump with a<br />
feeler gauge. If there is severe wear, replace the oil<br />
pump assembly.<br />
Standard value: 0.14 mm<br />
Check the clearance of main drive shaft and pump oil.<br />
• Check the main drive shaft external diameter with<br />
screw micrometer.<br />
• Measure the internal diameter of pump body with<br />
internal dial indicator.<br />
• The oil pump assembly shall be replaced if the<br />
clearance between main drive shaft and oil pump<br />
body exceeds the specified limit value.<br />
Standard value: 0.04 mm<br />
Check whether the oil pump cover and strainer are<br />
broken or blocked and replace them when necessary.<br />
5. Assemble the oil pump<br />
(a). Install the rotor.<br />
Install the rotor corresponding to the mark put previously.<br />
18B-20<br />
Install the oil pump cover to designated position, and<br />
install and fasten the oil pump cover fixing bolt.<br />
Install the pinion to designated position and install the<br />
pinion drift pin.<br />
6. Test the oil pump<br />
(a). When reassembling the oil pump, the oil pump shall be<br />
put into the clean oil pan and rotate the pump shaft<br />
clockwise till the oil flowing out from oil outlet of oil pump.<br />
One shall block the oil outlet with a hand and continue to<br />
rotate the pump shaft. If the rotational resistance<br />
increases, the operation condition is normal.<br />
The oil pump pressure can be measured with oil<br />
pressure gauge if necessary.<br />
7. Install the oil pump assembly<br />
(a). Install the oil pump and oil pump outlet pipe to<br />
designated position.<br />
18B-21<br />
Connect the connection of oil pump outlet pipe and oil<br />
Install and fasten 2 fixing bolts of oil pump.<br />
8. Install the oil pan assembly. (Refer to Chapter 18B Lubrication-Oil Pan, Service.)<br />
18B-22<br />
1. Dismantle the oil filter assembly<br />
(a). Disconnect the connection of oil cooler inlet and outlet<br />
hoses and oil cooler.<br />
One shall place a vessel under the oil filter when disassembling<br />
to receive the spilled oil.<br />
Dismantle the fixing bolt of oil filter assembly.<br />
(c). Take down the oil filter assembly and oil filter washer.<br />
Do not reuse the removed oil filler washer.<br />
2. Disassemble the oil filter assembly<br />
(a). Dismantle the oil cooler fixing bolt with special tools and<br />
take down the oil cooler.<br />
One shall place a clean vessel under the filter to receive the<br />
spilled oil.<br />
18B-23<br />
(b). Dismantle the oil filter element with special tools in the<br />
counterclockwise direction.<br />
One shall place a clean vessel under the filter when dismantling<br />
the filter element to receive the spilled oil.<br />
Spin-on filter element is a disposable part that can’t be<br />
reused.<br />
3. Check the oil filter seat<br />
(a). Check and clean the oil filter seat and ensure the fitness<br />
of new oil filter element.<br />
4. Assemble the oil filter assembly<br />
(a). Apply a thin layer of oil on the surface of O-ring, and<br />
screw up the new filter element to the filter seat until the<br />
resistance is felt.<br />
(b). Rotate in the clockwise direction to install the oil filter<br />
element with special tools.<br />
Rotate it by 3/4 circle clockwise.<br />
• Spin-on filter element is a disposable part that can’t be<br />
• When the oil filter is disassembled and installed, it must<br />
be noticed that do not damage the rubber seal ring to<br />
prevent impacting the sealing performance and resulting<br />
in oil leak.<br />
18B-24<br />
(c). Install the oil cooler to designated position and install the<br />
oil cooler fixing nut with special tools.<br />
Apply a thin layer of oil to the surface of O-ring.<br />
5. Install the oil filter assembly<br />
(a). Install the oil filler assembly and filter washer to the<br />
washer in designated position.<br />
Apply clean oil to the new oil filter washer before installing.<br />
Install and fasten the fixing bolt of oil filter assembly.<br />
Connect the connection of oil cooler inlet and outlet<br />
IGNITION SYSTEM ................................................................................... 19-1<br />
Overview ............................................................................................... 19-1<br />
Precautions .......................................................................................... 19-2<br />
Check on Board ................................................................................... 19-3<br />
SPARK PLUG ............................................................................................ 19-4<br />
Detection .............................................................................................. 19-4<br />
Service .................................................................................................. 19-5<br />
HIGH TENSION WIRE .............................................................................. 19-8<br />
Service .................................................................................................. 19-8<br />
IGNITION COIL ......................................................................................... 19-9<br />
Service .................................................................................................. 19-9<br />
CRANKSHAFT POSITION SENSOR ..................................................... 19-10<br />
Service ................................................................................................ 19-10<br />
In order to generate high-voltage electric sparks regularly, the gasoline engine is equipped with special<br />
ignition device, engine ignition system. Making the engine work by igniting combustible gas mixture, the<br />
ignition system can duly, accurately and reliably generate electric spark in cylinder under any working<br />
condition or service condition of engine. Generally, the ignition system consists of battery, ignition switch,<br />
ignition coil, spark plug and fuse.<br />
1. When the engine is started and working, do not touch the ignition coil and high tension wire in<br />
case of high-voltage electric shock.<br />
2. When conducting the high-voltage trial ignition, it recommends that the high tension wire<br />
shall be clamped with insulation rubber clamp. Do not directly touch the high tension wire<br />
with hands in case of electric shock and the damage of ignition system high tension circuit.<br />
During the trial ignition, one shall firstly plug a high tension wire into a standby spark plug,<br />
then ground the spark plug and observe the spark-over situation between electrodes of spark<br />
plug.<br />
3. When inspecting the service condition of each cylinder with the method of cut-out cylinder by<br />
cylinder, the high tension wire of cut-out cylinder shall be grounded by short-circuit method<br />
instead of open-circuit method.<br />
4. Ignition timing exerts a tremendous influence on engine functioning. For this reason, when<br />
the engine is in bad service or disassembled, one shall pay attention to check the ignition<br />
timing.<br />
5. While the spot welding operation on board, the ground wire of battery shall be disassembled.<br />
6. If the wire of ignition system (including the disassembly and connection of test instruments) is<br />
required to be disassembled or connected, the ignition switch shall be shut off primarily.<br />
7. While cleaning the engine, the ignition switch shall be shut off primarily.<br />
8. If the high tension wire is required to be unplugged, one shall pull the connecting part (such<br />
as the connecting sleeve of spark plug) instead of pulling the wire.<br />
CHECK ON BOARD<br />
1. Check the ignition coil<br />
(a). Turn off the ignition switch and unplug the terminal<br />
wiring harness connectors and high tension wires from<br />
ignition coil kit.<br />
(b). Respectively measure the resistance between B<br />
terminal and A & C terminals of 3-terminal- connector<br />
on the ignition coil kit with ohmmeter (primary coil<br />
resistance).<br />
Primary resistance value: 0.52±0.05 Ω<br />
The ignition coil kit shall be replaced if the resistance of ignition<br />
coil is out of the specified range.<br />
(c). Measure the resistance between high-voltage output<br />
terminals of Cylinder 2 & Cylinder 3 and Cylinder 1 &<br />
Cylinder 4.<br />
Secondary resistance value: 9840±980 Ω<br />
2. Spark over test.<br />
If the engine can rotate but not be started, one shall conduct the spark over test for it. The procedure<br />
is: unplug the high tension wire from the spark plug and assemble an ignition alignment tester onto<br />
the high tension wire. Connect the clamp of tester onto the bolt or support of engine, rotate the engine<br />
and observe the spark over situation at the end of tester. If there is no ignition alignment tester, one<br />
shall hold the high tension wire end with insulating tool, keep the end terminal 6mm distant from the<br />
proper ground position, revolve the engine and observe the spark over situation at the end of tester. If<br />
there are continuous and uniform blue sparks, one shall check or replace the spark plug; if no spark or<br />
the spark is weak or intermittent, one shall check the ignition coil kit (intermediate terminal) to see<br />
whether it gets sufficient battery voltage and check ignition high tension wire, ignition coil and ignition<br />
IGNITION - SPARK PLUG<br />
SPARK PLUG<br />
DETECTION<br />
1. Detect the spark plug<br />
Method of automobile check<br />
● Method of touch: Start the engine, make it idling and touch the ceramic insulating part of spark plug.<br />
If the temperature increases to a very high level and at a fast speed, the spark plug is working<br />
normally, otherwise, it is abnormal.<br />
● Method of short circuit: Start the engine, make it idling and short out the spark plug with<br />
screwdriver cylinder by cylinder and listen to the revolving speed and sound variation of engine. If<br />
the variation of revolving speed and sound is obvious, the spark plug is working normally,<br />
otherwise, it is abnormal.<br />
● Method of spark-over: Screw off the spark plug and put it on the cylinder block. Conduct the trial<br />
ignition with high tension wire, if no spark or the spark is weak, it means the spark plug has a fault<br />
of current leakage or it does not work.<br />
Method of observing color<br />
● Disassemble the spark plug and observe it, the color of russet or rust means the spark plug is<br />
normal; if it seems like oil stains, it must be the clearance maladjustment of spark plug, excessive<br />
gasoline, short circuit or open circuit; if it is smoky black, the selection for soft plug or hard plug<br />
must be wrong, or there’s a high concentration of gas mixture and the engine oil will go upward; if<br />
there are deposits between the top and electrode, especially if they are oily deposits, it means the<br />
oily smoke is unrelated with spark plug, and if they are black deposits, it means spark plug is<br />
accumulated by carbon deposits and bypassed, and if they are grey deposits, it means the ignition<br />
miss due to addition agent covering electrode. If the ablation is serious, such as scars on the top,<br />
black rupture pattern and melt of electrode, it means the spark plug is damaged.<br />
The following issues shall be noted for the disassembly or installation of spark plug.<br />
(a). Before dismantling the spark plug, one shall gently pull out the connector of each cylinder instead of<br />
pulling the high tension wire with great force to avoid damaging the high tension wire or the<br />
connection terminals of spark plug which is likely to be damaged.<br />
(b). As for the disassembly of spark plug, one shall firstly blow off the dirt around spark plug with a thin<br />
hose in case of dirt falling into the cylinder after screwing off the spark plug.<br />
(c). One shall disassemble the spark plug when the engine is cooled. One shall not shake the spark plug<br />
with great force during operation to avoid damaging the sealing property of spark plug.<br />
(d). During installation, the threads, electrodes and sealing gasket of spark plug shall be cleaned, dried<br />
and without oil stains in case of current leakage, air leakage, spark weakening and other faults.<br />
(e). When screwing in the spark plug, the bolt shall be screwed in by 1/2 of its total length with hands and<br />
then fastened by a jack lever. If the bolt cannot be screwed in smoothly, one shall quit the operation<br />
and check the spark plug to see whether it is aligned with screw or whether there are foreign matters<br />
in threads. One shall not aimlessly apply force on it and fasten it to avoid damaging screw hole or<br />
cylinder head.<br />
(f). If a flat-seat-type spark plug is selected, it shall be equipped with a sealing gasket, of which the<br />
quantity shall be adequate. Carbon deposit is likely to exist if the sealing deposit is excessive, while<br />
for sealing’s sake, no-sealing–gasket is not permitted. If a conical-seat-type spark plug is selected, no<br />
sealing gasket shall be equipped.<br />
(g). The spark plug shall be screwed up as required, because loose spark plug will lead to air leakage,<br />
while the excessively tight spark plug will also lead to air leakage due to elasticity lack.<br />
1. Disassemble the spark plug<br />
(a). Disassemble the spark plug with special tools.<br />
When the spark plug hole is opened, please prevent foreign matters from entering the combustion<br />
2. Service the spark plug<br />
(a). Check the edge of electrodes of spark plug and replace<br />
the spark plug if it is worn.<br />
19-6<br />
(b). Check the gap between central electrode and<br />
grounding electrode with a spark plug gap gauge to see<br />
whether it is within the specified range.<br />
Electrode gap of spark plug: 1.1±0.1 mm<br />
Please use special gauge for spark plug to measure the spark<br />
plug gap.<br />
1: Spark plug gap gauge<br />
2: Grounding electrode<br />
3: Central electrode<br />
Check the insulator to see whether there are flaws or<br />
the damages of terminal corrosion or threads. If there<br />
are, replace the spark plug.<br />
If there are moist carbons, one shall dry it and clean it<br />
with cleaning agent specially applied to spark plug.<br />
3. Adjust the spark plug gap<br />
(a). Put the grounding electrode into the gap part of spark<br />
plug gap gauge and bend the grounding electrode to<br />
adjust the gap.<br />
When bending the grounding electrode, the gap gauge of<br />
spark plug shall not touch the insulator in order to ensure<br />
the insulator shall not be ruptured. Also, one shall not pull<br />
or knock the central electrode.<br />
4: Insulator<br />
5: Before adjustment<br />
19-7<br />
4. Assemble the spark plug<br />
(a). Assemble the spark plug with special tools.<br />
Torque: 20~30 N·m<br />
19-8<br />
IGNITION-HIGH-TENSION WIRE<br />
HIGH TENSION WIRE<br />
1. Disassemble the high tension wire<br />
The engine shall be shut off in prior of dismantling the high tension wire.<br />
2. Detect the high tension wire with multimeter.<br />
(a). Measure the resistance of high tension wire with an<br />
multimeter, if it is not within the specified range, replace<br />
the high tension wire.<br />
3. Assemble the high tension wire<br />
(a). Plug the connector of high tension wire and spark plug into the spark plug and ensure its security.<br />
(b). Insert the connector of high tension wire and ignition coil into the ignition coil and ensure its security.<br />
IGNITION - CRANKSHAFT POSITION SENSOR<br />
19-9<br />
IGNITION COIL<br />
(a). Turn off the ignition switch and unplug the terminal wire<br />
harness connectors and high tension wires from the<br />
(b). Disassemble the fixing bolt of ignition coil and take<br />
down the ignition coil.<br />
(c). Respectively measure the resistance between B<br />
(d). Measure the resistance between high-voltage output<br />
2. Assemble the ignition coil<br />
(a). Assemble the ignition coil to the mounting position and<br />
tighten the fixing bolt.<br />
Torque: 10~15 N·m<br />
(b). Connect the high tension wires to the ignition coil.<br />
(c). Assemble the terminal harness connectors of ignition<br />
coil in place.<br />
19-10<br />
IGNITION-HIGH-CRANKSHAFT POSITION SENSOR<br />
1. Service the crankshaft position sensor<br />
(a). Detect for the voltage between two terminals. One shall<br />
test the voltages between each two of terminals A, B,<br />
and C, 3 terminals of sensor with voltage grade of<br />
multimeter. When the ignition switch is “ON”, the<br />
voltage value between A-C terminals is about 8V; the<br />
voltage value between B-C terminals will vary in the<br />
range of 0.3-5V when the engine is running. And its<br />
value varies like pulse: the maximum voltage is 5V, and<br />
the minimum one is 0.3V. If the actual results are not in<br />
accordance with the results, the crankshaft position<br />
sensor shall be replaced.<br />
A: Signal+ B: Signal- C: Screening Layer<br />
电 器 系 统 - 发 电 机 14-<br />
GENERATOR ......................................................................................... 20B-1<br />
Overview ............................................................................................ 20B-1<br />
Diagram of Components .................................................................. 20B-2<br />
Testing Generator ............................................................................. 20B-3<br />
Disassembly and Installation of Generator .................................... 20B-6<br />
STARTER ............................................................................................. 20B-10<br />
Overview .......................................................................................... 20B-10<br />
Diagram of Components ................................................................. 20B-11<br />
Testing Starter ................................................................................. 20B-12<br />
Disassembly and Installation of Starter ........................................ 20B-15<br />
BATTERY ASSEMBLY ......................................................................... 20B-17<br />
Overview .......................................................................................... 20B-17<br />
Structure .......................................................................................... 20B-18<br />
Working Principle ........................................................................... 20B-22<br />
Working Characteristics ................................................................. 20B-23<br />
Precautions ..................................................................................... 20B-24<br />
Common Faults and Troubleshooting for Battery ....................... 20B-25<br />
Diagram of Components ................................................................ 20B-28<br />
Replacement .................................................................................... 20B-29<br />
USE OF MAINTENANCE FREE BATTERY ........................................ 20B-32<br />
Checking of Technical Condition .................................................. 20B-32<br />
Charge The Maintenance Free Battery ......................................... 20B-33<br />
20B<br />
20B-1<br />
Generator is the main power supply for electric equipment of automobiles. During the period of automobile<br />
normal operation, generator powers the other electric equipment for starter, and also charges the battery.<br />
Please pay much attention to the following problems for the use and maintenance of alternator.<br />
1. The bonding of battery shall be in accordance with the polarity of alternator. The bonding shall be<br />
negative or else the battery will discharge through diode of silicon rectifier to burn up the diode.<br />
2. The method of make the output terminal of generator’s grounded (ground) cannot be used to check<br />
whether the generator generate electricity.<br />
3. When the generator runs at a high speed, do not dismantle the main electric equipment of battery to<br />
avoid producing overvoltage and damaging the diode, adjuster or other electric equipment.<br />
4. Inspect whether the wiring between the generator and battery is fixed and dependable.<br />
5. Inspect the tension of generator belt to judge whether it is in accordance with the ex-factory<br />
regulations. If the belt is too loose, the battery will undercharge; if the belt is too tight, the belt and<br />
generator bearing will be easily damaged.<br />
6. Once the generator is found out to work abnormally, check it timely, find out and remove the fault.<br />
7. Maintain the generator regularly. Generally speaking, check and inspect the generator’s electric brush,<br />
rectifier element, adjuster, bearing and other vulnerable elements one time after the generator runs<br />
for 750h or after the automobile travels for 30000Km.<br />
20B-2<br />
1 Belt tension arm<br />
2 Generator fastening bolt washer<br />
3 Heavy spring washer<br />
4 Hexagon head bolt<br />
5 Generator component<br />
6 Connector bolt<br />
7 Vacuum pump inlet tube assembly<br />
8 Copper washer<br />
9 Vacuum pump return tube<br />
10 Return tube clip<br />
11 Nut<br />
16 Generator bracket<br />
17 Generator fastening bolt<br />
18 Hexagon head bolt<br />
20B-3<br />
TESTING GENERATOR<br />
1. Checking generator’s output direct voltage<br />
(a). Start the generator and make the generator run at idle<br />
(b). Measure the voltages on both terminal s of storage with<br />
digital multimeter. The voltage registration shall be<br />
between 13 V and 15V (the detailed registration shall<br />
be set according to the set value of adjuster). When the<br />
generator rotate speed rises, the output direct voltage<br />
of generator basically<br />
2. AC component test of generator’s output voltage<br />
Adjust the digital multimeter to the AC voltage and connect it on the positive and negative poles of battery and<br />
measure the generator’s output AC voltage (normal value shall be ≤0.4V).<br />
The specific steps are as follows:<br />
(a). Start the generator and make the generator run at 2000rpm.<br />
(b). Turn on the headlamp and apply certain load for the generator.<br />
Adjust the digital multimeter to the AC voltage and<br />
connect it with the positive and negative poles and read<br />
the AC voltage value. If the voltage is ≤0.4V, it indicates<br />
that the rectifier of generator works normally. If the<br />
voltage is not in the range of ≤0.4V, it indicates that the<br />
rectifier of generator has fault.<br />
3. Checking the charging system voltage drop<br />
The voltage drop test is mainly for checking whether the wiring between generator and battery is in good<br />
The specific methods are as follows:<br />
(a). Start the generator and make it runs at 2000rpm of the rotate speed.<br />
(c). Adjust the digital multimeter to the AC voltage and measure the voltage drop between the generator’s<br />
output terminal and battery’s positive pole. The normal value is ≤0.4V. If the value is higher than<br />
0.4V, it indicates that the resistance of the wire connection point is too high.<br />
The following is only the schematic diagram.<br />
20B-4<br />
(d). Adjust the digital multimeter to the direct voltage and measure the voltage drop between the<br />
generator casing and battery’s negative pole. The normal value is ≤0.3V. If the value is higher than<br />
0.3V, it indicates that the wire connection becomes loose and the resistance of connection point is too<br />
high.<br />
The following is only the schematic diagram<br />
20B-5<br />
4. Checking single machine of generator<br />
(a). Measure whether the generator’s guide terminal is<br />
conductive with ohmmeter.<br />
Respectively insert ohmmeter hand in two needles of the<br />
generator’s guide terminal. If the display value on the<br />
ohmmeter is infinite, it indicates that the wire harness inside<br />
the generator disconnects, the generator is damaged and shall<br />
be replaced. If the display value on the ohmmeter is minimum,<br />
it indicates that the wire harness of generator is in good<br />
condition.<br />
(b). No-load test<br />
Disconnect the switch K, rapidly rise generator’s rotate speed,<br />
make the battery’s positive wire contact the wiring terminal of<br />
generator of magnetic field for the excitation of generator.<br />
When the generator voltage is 18V, the rotate speed of<br />
generator is 1000rpm.<br />
The generator shall run flexibly when it is moved by hands<br />
and there shall be no hysteresis and scraping phenomena.<br />
1: Magnetic field 2:Armature 3: Neutral point<br />
(c). Load test<br />
• Adjust the load resistance of circuit to the maximum.<br />
• When the alternator voltage is 28 V for the load test,<br />
the switch shall be switched on to make the<br />
generator output the current outward.<br />
• Gradually reduce the load resistance to increase the<br />
output current and raise the rotate speed to make<br />
the generator voltage keep 28V.<br />
Output current/A Voltage of electric machine/V Generator speed/(rpm)<br />
20B-6<br />
DISASSEMBLY AND INSTALLATION OF GENERATOR<br />
1. Turn off the ignition switch when the car stops stably.<br />
2. Disconnect the lead of battery pole<br />
(a). Disconnect the negative terminal of battery.<br />
Disconnect the vacuum pump inlet and outlet tubes<br />
behind generator and the generator connector.<br />
Loosen the adjusting bolt above generator.<br />
Release the whole belt tension and remove the belt.<br />
20B-7<br />
(e). Remove the generator fixing bolt.<br />
Remove the generator fixing bolt with two wrenches together.<br />
Remove the adjusting bolt above and the generator.<br />
3. Disassemble generator assembly<br />
(a). Remove the vacuum pump fixing bolt.<br />
Remove the vacuum pump.<br />
4. Install generator assembly<br />
(a). Place the vacuum pump to generator installation<br />
20B-8<br />
Install and tighten the vacuum pump fixing bolt.<br />
5. Install generator assembly<br />
(a). Place the repaired generator to engine bracket.<br />
(b). Install the upper adjusting bolt.<br />
The upper adjusting bolt is not tightened to install and adjust<br />
Install the generator fixing bolt.<br />
Adjust the generator position, install the generator belt<br />
and adjust the drive belt tension.<br />
(e). Install the adjusting bolt above generator.<br />
Do not tighten the adjusting bolt above generator excessively<br />
to adjust generator belt.<br />
20B-9<br />
Firmly press the generator belt and check if the belt is<br />
Reference standard: force of 39 N and deflection of<br />
approximately 10 ~ 15 mm<br />
Confirm the generator belt is installed in place and<br />
tighten the generator adjusting bolt.<br />
Torque: 19 N·m<br />
Connect the vacuum pump inlet and outlet tubes<br />
Connect the battery.<br />
20B-10<br />
The starter mainly consists of three components: DC series motor, driving mechanism for one -way clutch<br />
and battery switch. The three components can smoothly finish the start of engine by organic combination and<br />
cooperative work.<br />
The detailed working process is as follows:<br />
Connect the starting ignition → starting relay has electricity → solenoid switch electrifies →produce<br />
electromagnetic tension → Push off the isolator through shifting fork to mesh it with the flywheel; at the same<br />
time, transfer the battery’s electric energy to the motor → wheel gear isolator rotates → produce the<br />
electromagnetic torque to start the engine.<br />
20B-11<br />
1 1 type hexagon nut<br />
2 Spring washer<br />
3 Flat washer<br />
4 Starter motor<br />
5 Hexagon head bolt<br />
20B-12<br />
TESTING STARTER<br />
1. Testing voltage drop of starting system<br />
Testing voltage drop is mainly to check the connection condition of lead wire of main circuit for starter. Adjust<br />
the digital multimeter in the direct voltage, measure it according to the following diagram. Each part’s<br />
measured voltage value shall be ≤0.2V. if the measured voltage value of one part is >0.2V, it indicates that<br />
the wiring of the part has problem.<br />
2. Testing starter<br />
Judge the starter’s performance and technical condition by no-load test, brake test and performance test of<br />
solenoid switch.<br />
(a). No-load test<br />
Connect the circuit to observe whether the starter runs normally. Connect the ampere meter in series<br />
with the circuit. Read the current value and the current value shall not be >90A.<br />
Idling time of starter shall not be more than 1 min.<br />
20B-13<br />
Brake (locked) test<br />
The brake test shall be performed on the starter’s test station. Check whether the inner circuit of<br />
starter has fault with the method of measuring torque which is produced when braking and consumed<br />
current. And also check whether the meshing gear can slip. When performing the brake test, the<br />
starter shall be proved by no-load test to be in good condition. The test method is as follows.<br />
• Clamp the starter on the brake fixture of universal<br />
test stand and clamp three gears of pinion gear with<br />
clamp splice which is on the brake connecting rod.<br />
• Connect the wiring of test stand and starter.<br />
1: Starter<br />
20B-14<br />
• Press down the button SB on the universal test<br />
stand (press the button tight and then loosen it), the<br />
starter is braked. Rapidly read the voltage value and<br />
current value respectively from the voltmeter’s dial<br />
and ampere meter’s dial and then read the torque<br />
value from the weight beam. Compare the voltage<br />
value, current value and torque value with the<br />
standard value to analysis and judge whether the<br />
starter has fault.<br />
The time of processing circuit shall be not more than 5s. If<br />
it shall be tested again, the battery shall have a rest for 1~<br />
2min to avoid reducing the service life of battery.<br />
3. Performance test of solenoid switch<br />
(a). Remove the wiring between M terminal and motor.<br />
(b). Connect the battery’s negative pole with the starter housing and connect the positive pole with S<br />
terminal. At this moment, although the coil is kept to be electrified, the electromagnetic force is too<br />
small and the armature cannot move.<br />
(c). Connect the negative pole and M terminal to hear that the solenoid switch making pick-up sound and<br />
the driving gear is pushed out.<br />
(d). Move away the negative pole from M terminal, the solenoid switch keeps pick-up, and the resistance<br />
between two electric shocks of solenoid switch is “0”<br />
20B-15<br />
DISASSEMBLY AND INSTALLATION OF STARTER<br />
1. Disassemble starter assembly<br />
(a). Disconnect the battery.<br />
Disconnect each lead wire of starter’s wiring terminal<br />
Disassemble the fixing bolts of starter.<br />
Take down the starter.<br />
20B-16<br />
2. Install starter assembly<br />
(a). Install the starter in the corresponding position<br />
Install and fasten the fixing bolts of starter.<br />
Torque: 81 N·m<br />
Connect each connecting lead wire of starter’s wiring<br />
STARTING AND CHARGING - BATTERY ASSEMBLY<br />
20B-17<br />
BATTERY ASSEMBLY<br />
Battery, a device of converting the chemical energy into electric energy, is a reversible direct-current power<br />
supply with low voltage and is referred as “battery”. The maintenance free battery is a battery which cannot<br />
be maintained during the service period under the specified service conditions. For lead battery for<br />
automobile, the maintenance free battery is a battery which cannot be added distilled water during the service<br />
period.<br />
Functions of battery:<br />
1. When start the engine, power the main power supply equipment, such as starter, ignition system and<br />
so on.<br />
2. When there is too much electric equipment or when the electricity consumption is more than the<br />
starter’s capacity of electric power supply, the battery will assist the starter to power the electric<br />
3. The battery can stabilize the voltage. The battery is considered to be a big capacitor which can absorb<br />
the momentary overvoltage in the circuit and can protect electric equipment.<br />
4. When the storage electricity of battery is insufficient and the generator’s load is less, the battery can<br />
convert the generator’s electric energy as chemical energy to be stored (it means charging)<br />
5. The battery is considered as a capacitor with big capacity. When the generator speed and load<br />
change, the battery can keep the system voltage of automobile electric equipment relatively stable. At<br />
the same time, the battery can absorb momentary overvoltage which is produced by generator to<br />
protect the automobile electric elements from being damaged. Therefore, the generator cannot be run<br />
when it is without the battery.<br />
20B-18<br />
STRUCTURE<br />
The automobile type of SUP series adopts lead battery. The battery of 12V consists of 6 unit cell battery in<br />
series. The nominal for each unit cell of battery is 2V, and it is 2.1 V when the battery is filled.<br />
The lead battery consists of battery plate, battery plate group, and separator, acid electrolyte liquid and<br />
1 Battery housing<br />
2 Battery electrolyte liquid<br />
3 Battery plate and plate group<br />
4 Battery separator<br />
20B-19<br />
1. Plate and plate group<br />
The battery plate is divided into positive plate and negative plate. The positive plate and negative plate take<br />
the comb rack which is poured by lead-antimony alloy as the skeleton. Fill the active material on the comb<br />
rack to manufacture the plate<br />
The plate frame consists of comb rack which is the attachment<br />
of active material.<br />
The active material is filled on the comb rack. The active<br />
material on the positive plate is nigger-brown lead dioxide<br />
(PbO 2 ) and the active material on the negative plate is spongy<br />
caesious pure lead (Pb)<br />
There are two kinds of comb rack which are adopted by the<br />
battery: one is the common type as shown in the left diagram.<br />
The other is radiative type as shown in the right diagram.<br />
The radiative type comb rack, which is characterized by high<br />
output current, low internal resistance, and is used in the<br />
new-type battery.<br />
20B-20<br />
In order to increase the capacity of battery, each unit cell<br />
battery has multiple positive and negative plates to form plate<br />
group, as shown in the left diagram.<br />
Reason:<br />
Each positive plate is located between negative plates to<br />
equally charge and discharge both terminals of positive plate.<br />
2. Separator<br />
Functions of separator:<br />
The insulating separator shall be installed between the<br />
battery’s positive and negative poles to avoid the short circuit<br />
of plates.<br />
• The separator is characterized by porosity, which is convenient for electrolyte to freely permeate.<br />
• The separator is made by adopts acid resistance and alkali resistance woodiness, microfoam rubber,<br />
micropore plastic and impregnated resin paper material.<br />
• The micropore plastic separator is made in bags and is tightly wrapped on the external of positive plate to<br />
avoid falling off the active material.<br />
3. Acid electrolyte<br />
The electrolyte is the sulfate water solution which is allocated by certain proportion of sulfate (H 2 SO 4 ) and<br />
distilled water (H 2 O) .<br />
The density is 1.24~1.31g/m 3<br />
The electrolyte density has great influence on the capacity and service life of battery. The big density can<br />
raise the capacity of battery and can reduce the possibility of freeze; when the viscosity increases, the fluidity<br />
becomes poor to make the capacity of battery reduce and to make the corrosiveness strengthen, as a result,<br />
the service life of plate and separator is reduced.<br />
20B-21<br />
4. Housing<br />
The housing adopts acid resistance, heat resistance and aseismatic hard rubber or polypropylene plastic to<br />
make overall structure. The housing is divided into 6 unit cells which are not connected with each other.<br />
The housing bottom has the raised rid which supports the plate group and make the active materials drop in<br />
the groove from the plate to avoid short circuit of plate.<br />
20B-22<br />
The battery is an electrochemical power source and the charging and discharging process is a kind of<br />
reversible chemical reaction.<br />
1. Establish electromotive force<br />
(a). On the positive plate, PbO 2 and sulfate produce lead<br />
ion (Pb 4+ ) ascending and descending on the positive<br />
plate with positive charge to make the positive plate<br />
has about 2V positive potential.<br />
(b). On the negative plate, the lead ionization contains lead<br />
ion(Pb 2+ ) and electron (2e) , the two electrons leave on<br />
the negative plate to make the negative plate has about<br />
–0.1V negative potential.<br />
2. Discharge battery<br />
The electrolyte can be diluted and water increases when<br />
chemical reaction with load is processed.<br />
(a). The positive and negative plates can produce lead<br />
sulfate (PbSO 4 ) to increase water in the electrolyte.<br />
(b). When the discharge is processed, the electrolyte<br />
density will be reduced.<br />
3. Charge battery<br />
The two electrons return the negative pole from the positive<br />
pole with the function of external power to form the charging<br />
current flowing from the positive plate to the negative plate.<br />
(a). The lead sulfate on the plate revert to lead oxide and<br />
lead and the water in electrolyze reverts to sulfate.<br />
(b). The sulfate in electrolyze increases and the electrolyze<br />
density increases when charge is processed.<br />
20B-23<br />
WORKING CHARACTERISTICS<br />
1. Internal resistance of battery<br />
The internal resistance reflects the load capacity of battery. The lower the battery is, the higher the<br />
output current is. The internal resistance includes plate resistance, separator resistance and<br />
electrolyte resistance.<br />
The plate resistance is very low when it is fully charged. But when the battery’s discharge degree<br />
increases and the lead sulfate which is covered on the plate surface increases, the plate resistance<br />
increases too. The separator resistance is determined by the separator’s material, thickness and<br />
porosity. The micropore plastic separator’s resistance is lower in the common separator.<br />
The electrolyze resistance is related to electrolyze temperature and density. When the temperature<br />
falls, the electrolyze viscosity increases and the penetrating power drops, which makes that the<br />
resistance increases. When the electrolyze density is too high or too low, the resistance will increase.<br />
2. Discharging characteristic of battery<br />
(a). The discharging characteristic of battery means that<br />
the changing law of battery terminal’s voltage Uf and<br />
electrolyze density P 25 ℃with the discharging time<br />
changing during constant current discharging.<br />
3. Charging characteristic of battery<br />
(a). The charging characteristic of battery means the<br />
changing law of battery’s charge voltage and<br />
electrolyze density P 25 ℃ with the charging time<br />
changing during constant current charging.<br />
20B-24<br />
1. The selection of battery shall have the same capacity with that of the automobile.<br />
2. Keep the vent plug in tightened state to avoid spilling the acid resistance liquor.<br />
3. When the battery need to charge again, the supplemental current is 11A. When the battery is fully<br />
charged it has the following phenomena (do not allow being overcharged):<br />
Phenomenon 1: the voltage and electrolyze density shall not have obvious change within continuous<br />
2h.<br />
Phenomenon 2: the inner battery produces strong bubble and electrolyze has “ebullition”<br />
4. The battery is not allowed to be stored for a long time. If the battery shall be stored, then the battery<br />
shall be charged every three months (the supplement current is 11A and the voltage is 18 V).<br />
5. Electrolyze of battery contains sulfate which seriously damages the skin, eye and clothes. Prevent<br />
electrolyze from spilling when moving electrolyze. When the accident happens, the following methods<br />
can be properly adopted:<br />
(a). Immediately wash the external which is infected.<br />
(b). If the electrolyze enters the mouth, immediately rinse the mouth and drink lots of water or milk<br />
then go to see a doctor.<br />
Precautions for maintenance:<br />
1. Do not make two wiring terminals of battery short circuit, or else the battery will rapidly become hot<br />
even may burst. In addition, the gas which is dissipated from the battery will be easily to be lighted by<br />
sparks. Therefore, do not use naked flame near the battery.<br />
2. When disassembling and installing the electric equipment, first disassemble the ground wire of<br />
battery in order to avoid short circuit. When replacing bulb, turn off all relevant switches.<br />
3. When disassembling battery, disassemble the ground wire, then disassemble positive wire and then<br />
disassemble the battery baffle. Take out the battery from the rack. The installation of battery is in the<br />
reverse order of disassembly.<br />
20B-25<br />
COMMON FAULTS AND TROUBLESHOOTING FOR BATTERY<br />
Phenomenon 1: Housing broken<br />
Housing broken is the most serious destructive fault during the use of battery. After the housing is broken,<br />
electrolyze in the battery will leak and run off. If the housing is interval damage, the adjacent unit cell will be<br />
short circuit together to make the terminal voltage drop obviously so that the battery cannot properly work.<br />
Causes:<br />
1. Improper use and maintenance. For example, the fixed frame is too tight.<br />
2. Rubber anti-vibration pad is too tight or is not installed.<br />
3. The automobile fiercely vibrates and impacts during the driving.<br />
4. The external force hits the battery housing.<br />
5. Air vent on the plug screw is blocked.<br />
6. In winter then electrolyze density is too low or the temperature is too low or it freezes.<br />
Treatment:<br />
1. After the housing is broken, immediately disassemble the battery from the automobile. The battery<br />
shall be considered to be repaired or discarded as useless according to the condition.<br />
Phenomenon 2: Plate vulcanizing<br />
The battery is undercharge or cannot be charged for a long time after discharging, there is gradually a layer of<br />
white coarse grain lead sulfate on the plate. This lead sulfate cannot be transferred into lead dioxide in<br />
normal charge. This phenomenon is called “lead sulfate hardening” which is called “vulcanization” for short.<br />
The electrical conductivity of this kind of lead sulfate is very bad, which makes the battery’s internal<br />
resistance increase; when the volume increase, the pore space of active material is blocked and the<br />
electrolyze is blocked to permeate. Then the effective active material on the plate is reduced, and the<br />
discharge capacity is reduced, and the battery cannot provide enough start current, as a result, the engine<br />
cannot be started.<br />
1. When the battery is undercharge for a long time or is not charged timely after being discharged, some<br />
lead sulfate on the plate will be dissolved in electrolyze. The higher the temperature is, the bigger the<br />
solubility is. But when the temperature reduces, the solubility is smaller, and the lead sulfate will<br />
separate out again and crystallize again on the plate and form vulcanization.<br />
2. Electrolyze liquid level is not checked for a long time. The liquid level is too low, which makes the<br />
exposed liquid level on the upper of plate contact with the air and produce strong oxidation.<br />
3. The battery is overcharged for a long time or the low current is deeply discharged, which makes the<br />
active material’s long hole in the deep of plate produce lead sulfate so it cannot be easily to recover<br />
when charging.<br />
4. The new battery is not thoroughly charged and the active material does not get full recovery.<br />
5. Electrolyze density is a little higher, the composition is not very pure and external temperature<br />
changes fiercely.<br />
1. When the plate is slightly vulcanization, the low current is used.<br />
2. Do not use the method of charging for a long time. Eliminate the vulcanization with the method of<br />
eliminating vulcanization and charge when the vulcanization is serious.<br />
20B-26<br />
3. When the vulcanization is too serious, please abandon it.<br />
Phenomenon 3: Internal short circuit<br />
Internal short circuit means that battery’s positive and negative plates directly contacts or the plates are<br />
lapped by other electric conduction.<br />
1. The separator is damaged to make the positive and negative poles directly contact.<br />
2. The active material deposits a lot and contacts the below of plate group.<br />
3. The plate group bends.<br />
4. The conductive material falls off in the battery to make the positive and negative plate group internal<br />
short circuit.<br />
1. Replace the damaged separator, eliminate deposited active material and check or replace the bended<br />
plate group.<br />
Phenomenon 4: A lot of active materials come off<br />
When the battery is used, the active materials on the positive plate will gradually come off. It is because when<br />
charging or discharging, the volume of active material will continuously change, then it is easily to come off. If<br />
the battery is improperly used, a large number of active materials will come off, which makes the positive<br />
plate is prematurely damaged.<br />
1. The charging current of battery is too high and electrolyze temperature is too high, which makes<br />
active materials expand, floppy and easy to come off.<br />
2. The battery usually are overcharged, so a lot of gas emits from plate pore space which builds up<br />
pressure in the plate pore space, as a result, the active materials come off.<br />
3. The plate is so bended and deformed.<br />
4. Electrolyte freezes in winter.<br />
5. The vibration and bumping for automobile’s driving.<br />
1. For lead battery whose plate active materials come off, when there is little deposit, the battery can be<br />
continuously used after eliminating the deposit.<br />
2. When there is much deposit, please timely replace the plate and electrolyte.<br />
Phenomenon 5: Positive plate grid’s corrosion<br />
The positive plate will be rotted by oxide etch when the battery is used.<br />
1. The active material lead dioxide on the positive plate is a membrane which cannot compactly and<br />
completely cover the grid, so the grid will be corroded when charging.<br />
2. The acids or organic salt which have corrosion function for positive plate grid are mixed in electrolyte.<br />
3. The battery usually is overcharged.<br />
4. Electrolyze density and temperature are too high.<br />
1. For the battery with lighter corrosion, if there are impurities in electrolyte, pour out the electrolyte,<br />
clean the inner with distilled water again and again, add standard electrolyte and then the battery can<br />
be used after charging.<br />
2. For the battery with serious corrosion, if the electrolyte density is too high, adjust the density to the<br />
20B-27<br />
specified value, and then the battery can be continuously used even if it is not charged.<br />
3. For the battery with serious corrosion, if grid is broken and active materials come off in bulk, and then<br />
replace the plate.<br />
Phenomenon 6: Plate bending<br />
Plate bending appears on the positive plate and seldom appears on the negative plate. If plate bending<br />
occasionally appears on the negative plate, it is because the positive plate is excessively bended to make the<br />
negative plate bend.<br />
1. The plate quality is not good, which is because the filling lead paste is not uneven when<br />
manufacturing.<br />
2. The battery usually discharge with large current (for example, usually use the starter), because each<br />
part’s current density on the plate surface is different, the volumes of active materials change<br />
differently.<br />
3. The battery is overcharged. The lead sulfate which is produced in the deep of plate cannot recover<br />
when charging to expand the inner plate and to bend the plate.<br />
1. Take down and correct the bended plate group.<br />
Phenomenon 7: Polarity reversal of unit cell battery<br />
The battery with 6 unit cells, if there is one single battery has polarity reversal, and then the voltage is not 12V<br />
rather than 8V.<br />
1. The main reason for single battery’s polarity reversal is that the single battery is not found out fault<br />
timely (for example, plate’s short circuit, active materials’ falling off). When the battery discharges, the<br />
single battery will discharge to zero, then when the battery continuously discharges, other single<br />
batteries’ discharging current will charge it, so polarity reversal happens.<br />
1. Please replace the plate for single battery with polarity reversal.<br />
Phenomenon 8: Self-discharge<br />
The battery which is fully charged will lose electric quantity when it is not used. This phenomenon is called<br />
“self-discharged”.<br />
1. The plate materials are not pure and the electrolyte is impure.<br />
2. There is electrolyte on the cover of battery and the electrolyte can conduct the positive and negative<br />
piles.<br />
3. The battery is placed for a long time and sulfate sinks, which make the upper and lower of the plate<br />
produce potential difference.<br />
1. For the battery with little self-discharge, normally discharge the battery, pour out electrolyte, clean it<br />
with distilled water repeatedly, and then inject the new electrolyte. As a result, the battery can be used<br />
after it is fully charged.<br />
2. The battery with serious self-discharge shall be disassembled to be serviced or shall be replaced.<br />
20B-28<br />
2 1 type hexagon nut<br />
3 Pull rod assembly<br />
4 Battery rack assembly<br />
5 Hold-down strip assembly<br />
6 Pull rod assembly<br />
20B-29<br />
1. Stop the automobile on the even pavement, turn off the ignition switch and power supply main<br />
(a). Open dust cover of lead of battery pole.<br />
Screw off the fixing bolts of lead of battery pole, rock<br />
the pole around then take out the lead.<br />
3. Take out the battery<br />
(a). Screw off the fixed nuts from the battery clamp with<br />
wrench.<br />
(b). Take down the clamping plate of battery and take out<br />
the battery upward.<br />
Check the usability of battery with checking tools. If the<br />
battery cannot be used, please replace it.<br />
20B-30<br />
4. Install the full-charged or the new battery<br />
5. Install the fixed mount of battery<br />
(a). Place the battery in the tray of battery.<br />
Confirm directions of battery’s positive and negative poles and<br />
pole to compare the directions with the directions of<br />
disassembling and to avoid installing the positive and negative<br />
poles reversed to damage the circuit and components.<br />
Install the fixed pull rod and clamping plate of battery.<br />
Screw up the clamping plate nuts.<br />
6. Install the lead wire of pole for battery<br />
(a). Connect the lead of battery pole on the pole.<br />
20B-31<br />
(b). Screw up the fixing bolts of the lead of battery pole and<br />
fix the dust cover.<br />
When installing the lead of battery pole, first install the<br />
positive terminal and then install the negative terminal.<br />
20B-32<br />
STARTING AND CHARGING - USE OF MAINTENANCE FREE BATTERY<br />
USE OF MAINTENANCE FREE BATTERY<br />
CHECKING OF TECHNICAL CONDITION<br />
1. Usually keep the external clean when using the maintenance free battery.<br />
2. Usually check the color of electrolyte densimeter indicator inside.<br />
If the electrolyte densimeter indicator is black, take down the battery from the automobile for additional<br />
charge. If the electrolyte densimeter indicator is yellow, check whether the storage housing has crack or is<br />
damaged and whether electrolyte is leaked.<br />
3. Before replacing the battery, pay much attention to check whether there is fault for charging<br />
4. Load test for battery is to inspect the load capacity.<br />
Respectively connect two poles for battery on the carbon pole of carbon pile, add 300A of load current<br />
15s.<br />
Close the load, stop for 15s to wait for voltage recovery.<br />
Set the load of carbon pile as the load trial value specified on the label of battery.<br />
Apply load to test for 15s, read the voltage value of battery and judge whether the battery is good.<br />
Close the load.<br />
20B-33<br />
CHARGE THE MAINTENANCE FREE BATTERY<br />
Additional charging<br />
1. If the automobile is not used for a long time or there is fault in the charging system, and if the load<br />
voltage of battery is lower than 10V and the load voltage is lower than 12.4 V, the battery is in need of<br />
charging.<br />
2. The charging method for maintenance free battery is the same with that of the common battery. And<br />
the additional charge adopts constant current charge.<br />
3. For the first stage of charging, charge the battery with 10% current of battery capacity and the<br />
charging current is 6A. When each battery voltage is 16A, and then the second stage of charging<br />
begins.<br />
4. For the second stage of charging, charge the battery with x0.045 current of battery capacity. When<br />
each battery voltage is 16V, and then continue charging the battery for about 3~5h.<br />
5. If the electrolyze temperature is higher than 40℃ when charging, stop charging, reduce the current or<br />
carry on physical cooling. When the temperature is 45℃, please stop charging.<br />
6. Keep the battery in good ventilation when charging. Keep away from naked flame and inflammables.<br />
7. The standard of full charging: the charging indicator is green.<br />
Quick charging<br />
1. Quick charging is only used as emergency measure when the automobile cannot start. If the time<br />
allows, use the common charger.<br />
2. The current for quick charging is 3/10 of battery capacity.<br />
3. The time for quick charging is not more than 2h.<br />
SUPERCHARGER<br />
SUPERCHARGING SYSTEM .............................................................. 21-1<br />
Overview ........................................................................................... 21-1<br />
Working Principle ............................................................................ 21-2<br />
Diagram of Components ................................................................. 21-4<br />
TURBOCHARGER ............................................................................... 21-5<br />
Service .............................................................................................. 21-5<br />
SUPERCHARGING SYSTEM-SUPERCHARGING SYSTEM<br />
21-1<br />
SUPERCHARGING SYSTEM<br />
1. This engine is equipped with an exhaust turbocharger. The exhaust turbine of turbocharger is<br />
assembled on the same shaft with gas compressor, driving by the exhaust gas exhausted by engine<br />
and driving the gas compressor to compress the air sucked into the air filter to increase the air density<br />
in cylinder, the air inflow, air supply of fuel for injection pump and the output of engine.<br />
2. The turbocharger consists of turbine, radial-flow compressor, middle casing, rotor assembly, bypass<br />
valve etc. The turbine and gas compressor shall be respectively installed on both ends of shaft and<br />
own their own cast casings. The shaft is installed in the middle casing and supported by the middle<br />
casing.<br />
3. The turbine part mainly consists of turbine casing and single stage radial-flow turbine. They form an<br />
energy converter. When the exhaust gas exhausted from the diesel engine blows to turbine impeller<br />
in a fixed direction after entering the nozzle through turbine casing, the heat energy and pressure<br />
energy of exhaust gas will turn to kinetic energy and rotate the turbine at a high speed.<br />
4. The intermediate is an intermediate support which supports the rotor assembly, fixed turbine casing<br />
and compressor casing. It is also a lubricating oil tank which can lubricate and cool the floating<br />
bearing rotor.<br />
5. The gas compressor mainly consists of centrifugal-flow compressor impeller, diffuser and gas<br />
compressor casing. Passing by the air filter, the air will be sucked into the compressor impeller<br />
revolving at a high speed which will increase the air velocity and the pressure. The air will then passes<br />
diffuser and compressor casing to transform the kinetic energy of air current to pressure energy which<br />
will enter the cylinder through diesel engine intake pipe after increasing and cause the increase of air<br />
density in the cylinder of diesel engine.<br />
6. Air evacuation valve and air release valve are used to ensure the best coordination performance of<br />
the diesel engine in the range of low and intermediate speed and the turbocharger. This best<br />
performance can facilitate the diesel engine in terms of gaining sufficient air, being corresponding with<br />
the increasing of fuel supply amount, enlarging the low speed torque, improving the fuel consumption<br />
and evacuating or releasing the air in high speed range (a part of exhaust gas can directly enter into<br />
the exhaust pipe without passing turbine) to avoid the excessive combustion pressure in cylinder due<br />
to the over speed of turbocharger rotor and the excessive supercharging pressure and mechanical<br />
load aggravation of diesel engine etc. The open and close of air evacuation and release valve is<br />
automatically controlled by supercharging pressure. When the supercharging pressure reaches or<br />
exceeds the specified value, the diaphragm will be against the left spring force, move to the left with<br />
linkage push rod, and push the rocker arm to rotate around the pin roll, make the air release valve<br />
open, realize the exhaust bypass deflation and raise the turbocharger speed.<br />
21-2<br />
The heat and exhaust gas under a certain pressure exhausted from engine will enter the nozzle diaphragm in<br />
turbine casing from exhaust manifold. The area of nozzle diaphragm will generally shrink. For the reason, the<br />
pressure and temperature of exhaust gas will drop, the speed and kinetic energy will increase and the<br />
exhaust gas flow will impact the turbine in the specified direction to make it rotate at a high speed. Then the<br />
turbine will drive the centrifugal-flow compressor impeller on same shaft to rotate at the same speed with<br />
turbine, and the air passed through air filter will be sucked into compressor casing. The compressor impeller<br />
rotating at a high speed will toss the air to edge of impeller, increase the speed and pressure of air and make<br />
it entering into diffuser. Because of the form of diffuser: a small inlet and a large outlet, the airflow velocity will<br />
drop and the pressure will increase. The pressure of air current will continue increasing by passing through<br />
the ring form compressor casing (with cross sections of all sizes). The compressed air will enter the cylinder<br />
by passing the intake pipe of engine. By this way, the air inflow of engine will increase, and the output of<br />
engine will also increase. Passing the turbine, the exhaust gas will finally be injected to the atmosphere.<br />
21-3<br />
1 Exhaust pipe<br />
2 Shaft<br />
3 Nozzle Diaphragm<br />
4 Turbine<br />
5 Turbine casing<br />
6 Bearing<br />
7 Diffuser<br />
8 Compressor impeller<br />
9 Ring-form gas compressor casing<br />
10 Intake pipe<br />
21-4<br />
1 Tail pipe of turbocharger<br />
2 Stud<br />
Nut washer assembly of<br />
and exhaust pipe<br />
4 Bracket bolt of turbocharger<br />
5 Large washer<br />
6 Tail pipe bracket<br />
7 Combination nut<br />
8 Connecting stud of tail pipe<br />
9 Tail pipe gasket of turbocharger<br />
10 Turbocharger components<br />
11 Connecting bolt of turbocharger<br />
intake pipe<br />
Exhaust pipe-connector gasket of<br />
13 Exhaust pipe nut<br />
14 Jointing stud of turbocharger<br />
15 Flange gasket of oil return pipe<br />
17 Oil return pipe of turbocharger<br />
18 Heating water pipe clamp<br />
19 Oil return rubber hose of turbocharger<br />
Insulation jacketing of turbocharger oil<br />
return hose<br />
21 B-type worm drive hose clamp<br />
Turbocharger intake connecting pipe<br />
24 Oil inlet bolt A<br />
25 Copper washer<br />
26 Oil inlet pipe weldment of turbocharger<br />
27 Oil inlet bolt B<br />
28 Copper washer<br />
SUPERCHARGING SYSTEM-TURBOCHARGER<br />
21-5<br />
1. Disassemble the turbocharger assembly from the<br />
(a). Disassemble the connecting bolt of the EGR pipe and<br />
the intake connecting pipe assembly of turbocharger.<br />
Disassemble the connecting bolt of the EGR pipe and<br />
Take down the EGR pipe.<br />
Disassemble the vent hose clamp of breather.<br />
● Take down the vent hose of breather.<br />
21-6<br />
Disassemble the bracket fixing bolt of turbocharger<br />
Disassemble the A-type worm drive hose clamp<br />
connected to turbocharger and its intake connecting<br />
● Take down the intake connecting pipe assembly of<br />
Disassemble the fixing bolt of intake connecting pipe.<br />
(h). Disassemble the bracket fixing bolt of intake<br />
Disassemble the clamps of intake connecting pipe and<br />
connecting rubber hose of turbocharger.<br />
● Take down the intake connecting pipe of engine.<br />
21-7<br />
Disassemble the oil inlet bolt A of oil inlet pipe<br />
weldment of turbocharger.<br />
Disassemble the oil inlet bolt B of oil inlet pipe<br />
Take down the oil inlet pipe weldment of turbocharger.<br />
Disassemble the oil return pipe spring hose clamp of<br />
(n). Disassemble the fixing bolt of turbocharger.<br />
(o). Take down the turbocharger from engine.<br />
Disassemble the turbocharger assembly from engine. Do<br />
not lift the turbocharger with linkage push rod.<br />
2. Disassemble the turbocharger assembly<br />
The turbocharger is a precise machine which will revolve at a high speed. The turbocharger assembly<br />
shall not be disassembled casually except for necessary situation.<br />
21-8<br />
Disassemble the connecting bolt of turbocharger oil<br />
return pipe and turbocharger components and take<br />
down the oil return pipe.<br />
Disassemble the bolt connecting with turbocharger tail<br />
pipe and turbocharger components.<br />
(c). Disassemble the turbocharger tail pipe.<br />
Take down the tail pipe gasket of turbocharger.<br />
Disassemble the bleed-air pipe.<br />
Take out the linkage push rod circlip with pliers.<br />
21-9<br />
Loosen the fixing bolt of linkage push rod with wrench.<br />
Take down the regulator device of air release valve.<br />
(h). Take down the fixing bolt connecting the compressor<br />
casing and intermediate.<br />
Disassemble the fixing bolt connecting the impeller casing and<br />
intermediate, disassemble the impeller casing and<br />
intermediate and take out the rotor assembly and two<br />
impellers.<br />
One shall not impact the impeller during disassembly. If<br />
the impeller is impacted and deformed, it shall not<br />
continue to be used after alignment.<br />
3. Clean and check the turbocharger assembly<br />
(a). Clean the turbine casing with vapor.<br />
Clean the compressor casing and two impellers with vapor.<br />
When using the vapor cleaner, one shall ware safety glasses or<br />
protective mask and protective clothing in case of serious<br />
personal injuries caused by hot vapor. If the impeller is<br />
impacted and deformed, it shall not continue to be used after<br />
21-10<br />
Check the tail pipe gasket of turbocharger to see<br />
whether it is abraded. If it is, the washer shall be<br />
(c). Measure the axial clearance of impeller shaft with dial<br />
indicator.<br />
Standard Value: 0.06~0.09 mm<br />
Limiting Value: 0.11 mm<br />
Alternately apply the force of 0.12N on the end of compressor<br />
impeller and the end of turbine impeller.<br />
Measure the clearance between impeller shaft and<br />
Standard Value: 0.11~0.18 mm<br />
Limiting Value: 0.215 mm<br />
(e). Check the radical clearance of rotor.<br />
Minimum Clearance: ≥0.1 mm<br />
Depress the compressor impeller with a hand in radical<br />
direction and measure the minimum clearance between<br />
compressor impeller and compressor casing. If the measured<br />
value is smaller than the required minimum clearance value,<br />
the floating bearing shall be replaced.<br />
21-11<br />
(f). Check the axial clearance of rotor.<br />
Axial clearance value: 0.1 mm<br />
Limiting value: ≤0.25 mm<br />
One can fix the magnetic base onto the discharge flange facing<br />
of turbine casing, contact the dial indicator with the end face of<br />
turbine rotor shaft and push or pull the turbine rotor along axial<br />
direction. The measured D-value is the axial clearance value. If<br />
the axial clearance value of compressor is higher than the<br />
applied limiting value, the assembly shall be disassembled and<br />
the wore-out parts shall be replaced. Before determining and<br />
eliminating the causes of turbocharger damage, one shall not<br />
replace the turbocharger.<br />
4. Assemble the turbocharger assembly<br />
(a). Install the impeller and rotor assembly with special<br />
tools.<br />
(b). Put the turbine casing and compressor casing on the<br />
installation position and screw up the fixing bolt.<br />
Put the air release valve regulator device onto the<br />
Install the fixing bolt of linkage push rod.<br />
21-12<br />
(e). Install the linkage push rod circlip.<br />
One shall not adjust the length of linkage push rod<br />
installing the air release valve regulator. As for the<br />
adjustment, one shall refer to the related delivery<br />
information.<br />
Install the bleed-air pipe.<br />
(g). Put the turbocharger tail pipe onto the installation<br />
position of turbocharger components.<br />
Do not forget to install the turbocharger tail pipe gasket when<br />
installing the turbocharger tail pipe.<br />
Install and fasten the connecting bolt of turbocharger<br />
tail pipe and turbocharger components.<br />
5. Install the turbocharger assembly on the engine.<br />
(a). Put the turbocharger assembly onto the installation<br />
position and fasten its fixing bolt.<br />
21-13<br />
Install the oil return pipe spring hose clamp of<br />
Put the oil inlet pipe weldment of compressor into the<br />
Install and fasten the oil inlet bolt B of turbocharger oil<br />
inlet pipe weldment.<br />
Install and fasten the oil inlet bolt A of turbocharger oil<br />
Put the intake connecting pipe of engine on the<br />
● Fasten the clamps of engine intake connecting pipe<br />
and turbocharger connecting rubber hose.<br />
Install and fasten the fixing bolt of intake connecting<br />
pipe bracket.<br />
21-14<br />
(i). Put the intake connecting pipe assembly of<br />
turbocharger onto the installation position.<br />
● Fasten the A-type worm drive hose clamp<br />
connecting with turbocharger intake connecting pipe<br />
assembly and turbocharger.<br />
Install and fasten the fixing bolt of turbocharger intake<br />
Fasten the vent hose clamp of breather.<br />
Put the EGR pipe into the installation position<br />
21-15<br />
Install and fasten the connecting bolt between EGR<br />
pipe and EGR valve.<br />
pipe and intake connecting pipe assembly of<br />
V O L U M E 4<br />
11C ENGINE CONTROL SYSTEM 2161<br />
12C FUEL SYSTEM 2173<br />
13C EMISSION CONTROL 2195<br />
14C INTAKE AIR 2201<br />
15C ENGINE MECHANICAL PART 2209<br />
16C EXHAUST SYSTEM 2235<br />
17C COOLING SYSTEM 2243<br />
18C LUBRICATION SYSTEM 2263<br />
20C STARTING AND CHARGING 2273<br />
DIESEL ENGINE CONTROL SYSTEM............................................11C-1<br />
PRECAUTION............................................................................11C-1<br />
ENGINE CONTROL MODULE (ECM) .............................................11C-2<br />
PRINCIPLE ................................................................................11C-2<br />
REPLACEMENT ........................................................................11C-3<br />
ACCELEARTOR PEDAL POSITION SENSOR...............................11C-5<br />
PRINCIPLE ................................................................................11C-5<br />
INSPECTION ON VEHICLE ......................................................11C-6<br />
OVERHAUL ...............................................................................11C-7<br />
VEHICLE SPEED SENSOR.............................................................11C-8<br />
PRINCIPLE ................................................................................11C-8<br />
OVERHAUL ...............................................................................11C-9<br />
11C<br />
ENGINE CONTROL SYSTEM - DIESEL ENGINE CONTROL SYSTEM<br />
DIESEL ENGINE CONTROL SYSTEM<br />
11C-1<br />
1. DIESEL ENGINE CONTROL SYSTEM PRECAUTION.<br />
This will prevent injuring person and vehicle damage.<br />
The ignition and illumination switches must be shut off before removing or installing the battery negative<br />
cable (the semiconductor maybe damage without doing that).<br />
sealing face is level and smooth and no greasy dirt on it before installation. Don’t forget to remove the<br />
sealant on the mounting hole, the threaded hole and the thread.<br />
(d) Paint some sealant evenly on the prescribed diameters to surround the mounting hole. The sealant not<br />
hardened yet can be scraped away. Install it in place when the sealant is wet (within 15 minutes). Take<br />
care not to stick the sealant to the place where it's not desired during installation. Wait the sealant to be<br />
very hardened (1 hour or so) after installation. Don’t apply oil on the painted parts or wet or start the<br />
engine during this time.<br />
(e) Tighten the straining bolts with prescribed torque during installing the sensors, actuators or other parts.<br />
Ensure the diesel engine is always in clean and complete state. Clean or wipe up the parts to ensure<br />
the clean parts and the assembly quality before removing and assembling the parts. The complicated<br />
adjustment and maintenance should be taken indoors to avoid the diesel engine being polluted by the<br />
(f) When installing and handling sensors, handle them gently to avoid damage, any impact or falling may<br />
cause severe damage.<br />
(g) Don’t test the system electrical signal by use of a fine needle to pierce the harness.<br />
(h) Take a visual inspection to check if the sensing element at the head of sensor is damaged or color<br />
changed; Replace it if it's damaged or the color is severe changed.<br />
11C-2<br />
ENGINE CONTROL SYSTEM - ENGINE CONTROL MODULE (ECM)<br />
1. ENGINE CONTROL MODULE DESCRIPTION.<br />
(a) ECM is the electric control engine control center with the<br />
micro processor as the core that having sensor signal<br />
input interface and the executor drive circuit. The ECM<br />
(b) ECM has self protection function, it may result the<br />
after replacement of ECM, therefore we may deem as<br />
the ECM trouble. in fact, the ECM doesn’t get damaged<br />
but just enters into self protection mode. ECM will<br />
resume normal after flashing programming or “active” on<br />
factory.<br />
11C-3<br />
(a) Pull assistant driver seat forward.<br />
(b) Lift the covering behind assistant driver seat , then<br />
loosen ECM locking knob .<br />
Remove 2 ECM electrical connectors.<br />
Remove ECU.<br />
11C-4<br />
4. INSTALL ECU.<br />
Tighten 4 ECU mounting bolts.<br />
Connect ECU connector.<br />
Pull ECU connector upward, comfirm that it is installed in<br />
Install ECU cover and tighten locking knob.<br />
Cover the covering and push assistant driver seat back<br />
to the original position.<br />
ENGINE CONTROL SYSTEM - ACCELEARTOR PEDAL POSITION SENSOR<br />
11C-5<br />
ACCELEARTOR PEDAL POSITION SENSOR<br />
1. ACCELERATOR PEDAL POSITION SENSOR.<br />
(a) The electric accelerator pedal position sensor (APPS) is<br />
mounted on the pedal bracket. it is 2 three-line types of<br />
potentiometer sensor. The ECU applies a 5 V reference<br />
voltage to the sensor.<br />
(b) The sensor slide indicator connects with the accelerator<br />
and rotates following the shaft. When the accelerator<br />
pedal changes, the position of the slide indicator will also<br />
change on the carbon film resistance, at such moment<br />
the resistance output will also change, which reflects the<br />
open extent of the accelerator indirectly.<br />
11C-6<br />
INSPECTION ON VEHICLE<br />
APPS<br />
• Engine turn off<br />
APPS1<br />
APPS2<br />
• Key ON (the throttle is<br />
closed): 0.899 V<br />
fully open): 3.548 V<br />
closed): 0.572 V<br />
fully open): 1.608 V<br />
6. IF IT IS NOT OK, CHECK APPS, HARNESS OR ECU.<br />
11C-7<br />
2. REMOVE APPS.<br />
(a) Disconnect APPS connector.<br />
(b) Loosen 3 APPS mounting nuts.<br />
3. CHECK APPS RESISTANCE.<br />
(a) Using the analogue multimeter, measure the continuity of<br />
the APPS resistance.<br />
(b) The pins of the multimeter connect to terminal 4 and 3 of<br />
APPS respectively. Turn the shaft of the APPS. The<br />
value changes linearly varied with the opening of the<br />
acceperator. When connecting to terminal 2 and 4, the<br />
value is opposite.<br />
(c) Check the resistance of the APPS.<br />
Resistance<br />
(3) - (4)<br />
(2) - (4)<br />
(5) - (6)<br />
(1) - (6)<br />
Turn the shaft of the<br />
APPS. The value changes<br />
linearly varied with the<br />
opening of the accelerator<br />
The resistance value is continuity.<br />
If the ckeck result is not OK, replace it.<br />
4. INSTALL APPS.<br />
(a) Tighten 3 APPS retaining bolts.<br />
(b) Connect APPS connector.<br />
11C-8<br />
ENGINE CONTROL SYSTEM - VEHICLE SPEED SENSOR<br />
Vehicle speed sensor is the type of hall sensor. It works<br />
together with signal wheel on output shaft. ECM detects<br />
digital voltage signal through it and determines the current<br />
speed of the vehicle.<br />
11C-9<br />
Clear surface after removing.<br />
(a) Install vehicle speed sensor and tighten mounting bolt.<br />
Do not allow any impact tools (such as a hammer, etc.) to<br />
6. CHECK AFTER INSTALATION.<br />
under normal operation.<br />
FUEL SYSTEM.................................................................................12C-1<br />
PRECAUTION............................................................................12C-1<br />
FUEL SYSTEM PRESSURE RELEASE PROCESS .................12C-2<br />
FUEL SYSTEM BLEEDING.......................................................12C-2<br />
DRAIN FUEL TANK PROCESS.................................................12C-2<br />
FUEL TUBE CLEAN ..................................................................12C-3<br />
COMPONENTS .........................................................................12C-4<br />
FUEL TANK ASSY...........................................................................12C-6<br />
REPLACEMENT ........................................................................12C-6<br />
DIESEL FILTER ASSY.....................................................................12C-9<br />
REPLACEMENT ........................................................................12C-9<br />
FUEL LEVEL SENSOR AND BRACKET ASSY............................12C-10<br />
REPLACMENT.........................................................................12C-10<br />
FUEL FILLER DOOR .....................................................................12C-12<br />
REPLACEMENT ......................................................................12C-12<br />
FUEL FILLER DOOR LOCK LATCH ASSY .................................12C-13<br />
REPLACEMENT ......................................................................12C-13<br />
FUEL FILLER CAP ........................................................................12C-15<br />
INSPECTION ...........................................................................12C-15<br />
FUEL FILLING TUBE AND BREATHER TUBE ASSY .................12C-16<br />
INSPECTION ...........................................................................12C-16<br />
ELECTRONIC ACCELERATOR PEDAL......................................12C-20<br />
REPLACEMENT ......................................................................12C-20<br />
12C<br />
12C-1<br />
(a) Before working on fuel system, disconnect battery negative cable if necessary.<br />
(b) When removing the fuel hose, use a suitable container to hold the diesel.<br />
(d) Fuel in the VE dispensing pump and tubes remain under high pressure. In order to avoid personal<br />
injury, do not loosen tube connector while engine is runing.<br />
(e) Keep diesel away from rubber and leather parts.<br />
(f) Diesel injection equipment is designed to very precise tolerances and fine clearances. To prevent fuel<br />
system damage, it is essential that absolute cleanliness is oberved when working with these<br />
components. Always install fuel system caps to any open orifices or tubes.<br />
(g) Before disconncting any of the fuel system tubes or fuel system components, relieve the fuel system<br />
pressure to prevent accidental spraying of fuel, even when the engine is not running. Failure to follow<br />
(h) Check if there is any dirt like mud around the fuel tube connector before this work. And clean dirt away,<br />
(i) Keep cleaner away from the O-ring of tube connecter. Cleaner can harm seal of fuel system.<br />
(j) Don’t bend or twist the fuel system tube and pipe by force.<br />
(k) Before connceting fuel system tube, be sure there is no damage to tube connector. If there is damage,<br />
crack or dirt on surface. replace it with a new tube assy.<br />
(l) Wearing eyeshield equipment is needed when working on fuel system compoments. Failure to follow<br />
this instruction may result in personal injury.<br />
(m) The metal parts like zn, cu, mn are easily dissolved in diesel. coking may appears in fuel injector which<br />
reduces the injected diesel to cylinder. So the matal parts above should not be used in high-pressure<br />
common rail fuel system.<br />
(n) It is essential to keep fuel system clean. especially it can not contain any impurity, such as corrosion,<br />
welding spatter. Otherwise, these impurity can block fuel tube, engine shut down suddenly. The<br />
common rail parts are even damaged.<br />
12C-2<br />
• Fuel pressure in fuel pump, high pressure fuel pipe and fuel rail is high enough to cause serious<br />
injury to the skin.<br />
• Don't loosen any pipe joint when engine is running. waiting for at least 10 minutes after engine<br />
is off. when oil pressure dropps to a lower level, loosen the high pressure fuel system pipe joint.<br />
2. BEFORE REPAIRING FUEL SYSTEM, LOOSEN THE<br />
LOCKING NUT ON FUEL RAIL TO RELEASE FUEL<br />
PRESSURE.<br />
3. WHEN REMOVING LOCKING NUT, LEAVE YOU<br />
HAND FAR AWAY FROM THE CONNECTING JOINT.<br />
Fuel will spurt from the pipe joint to the engine block side<br />
along the groove in fuel rail.<br />
4. TIGHTEN FUEL RAIL LOCKING NUT.<br />
FUEL SYSTEM BLEEDING<br />
• When servicing or replacing feed / high-pressure fuel system parts, fuel system will still<br />
preserve a certain amount of air. Press manual pump to bleed air for fuel system.<br />
• It is not necessary to bleed air before starting the engine. When cranking engine, mechanical<br />
fuel pump applies fuel to fuel system.<br />
1. FUEL SYSTEM BLEEDING. (Refer to CUMMINS ISF<br />
SERIES ENGINE SERVICE MANUAL )<br />
12C-3<br />
12C-4<br />
12C-5<br />
3 Dual Line Clip<br />
4 Fuel Filler Cap Assy<br />
5 Bolt, Spring Washer And Flat Washer<br />
7 Guide Pin<br />
8 Fuel Level Sensor And Bracket Assy<br />
9 Dual Line Clip<br />
10 Bolt, Spring Washer And Flat Washer<br />
11 Return Line<br />
12 Fuel Tank To Diesel Filter Fuel Line<br />
14 Fuel Filler Hose Assy<br />
15 Diesel Filter Assy<br />
16 Diesel Filter To Engine Fuel Line<br />
17 Diesel Filter Bracket<br />
18 Guide Pin<br />
12C-6<br />
1. RELEASE FUEL PRESSUE. (Refer to “Chapter 12B fuel - fuel system, fuel system pressure<br />
2. DRAIN FUEL TANK. (Refer to “Chapter 12B fuel - fuel system, drain fuel tank process”)<br />
(c) Disconnect fuel tank breather pipe and filling tube.<br />
Lower the fuel tank to a suitiable position.<br />
12C-7<br />
12C-8<br />
(a) When Turning ignition switch on, fuel pump will apply fuel pressure to fuel lines. inspect if there is fuel<br />
(b) Start engine and rev it up and check there is no fuel leakage at the fuel system tube and hose<br />
FUEL - DIESEL FILTER ASSY<br />
12C-9<br />
DIESEL FILTER ASSY<br />
12C-10<br />
FUEL - FUEL LEVEL SENSOR AND BRACKET ASSY<br />
FUEL LEVEL SENSOR AND BRACKET ASSY<br />
1. RELEASE FUEL PRESSURE. (Refer to “Chapter 12B fuel - fuel system, fuel system pressure<br />
2. DRAIN FUEL TANK AS REQUIRED. (Refer to “Chapter 12B fuel - fuel system, drain fuel tank<br />
5. REMOVE FUEL TANK. (Refer to “Chapter 12B fuel - fuel tank, replacment”)<br />
6. REMOVE FUEL LEVEL SENSOR AND BRACKET<br />
Remove fuel level sensor and bracket assy.<br />
Be careful not to bend float arm during removing fuel level<br />
sensor and bracket assy.<br />
(b) Check sealing ring for improper crack, damage or deterioration<br />
12C-11<br />
8. INSTALL FUEL LEVEL SENSOR AND BRACKET<br />
Place sealing ring into place on the opening of fuel tank.<br />
Position fuel level sensor and bracket assy into fuel tank.<br />
Press installation surface of fuel level sensor and bracket<br />
assy into place, then install lock ring and rotate the lock<br />
ring clockwise.<br />
9. INSTALL FUEL TANK. (Refer to “Chapter 12B fuel - fuel tank assy, replacment”)<br />
After disconnecting fuel level sensor and bracket connector, connect fuel level sensor and bracket<br />
connector, turn ignition switch on. Slide fuel level sensor and bracket position manually and then check<br />
the fuel gauge’s conditions in instrument panel.<br />
connections and confirm fuel level sensor is functional.<br />
12C-12<br />
(a) Install 2 fuel filler door retaining bolts.<br />
(b) Install the clip connected to fuel filler cap to fuel filler<br />
12C-13<br />
1. REMOVE LEFT B LOWER PANEL. (Refer to “Chapter 88 inner and outer trim panel - left panel,<br />
(a) Remvoe 2 left front seat lock assy retaining bolts.<br />
Take out lock latch assy.<br />
Remove fuel filler door cable.<br />
(a) Install fuel filler door cable to lock latch assy.<br />
12C-14<br />
7. INSTALL LEFT FRONT B PILLAR LOWER PANEL. (Refer to “Chapter 88 inner and outer trim<br />
panel - left panel, replacement”)<br />
12C-15<br />
Visually inspect fuel filler cap and seal ring. If deformed<br />
Termly lubricate the rotating part.<br />
12C-16<br />
2. REMOVE BATTERY AND BATTERY TRAY. (Refer to “Chapter 20B starting and charging - battery,<br />
5. DRAIN FUEL TANK AS REQUIRED. (Refer to “Chapter 12B fuel - fuel system, drain fuel tank<br />
12C-17<br />
12C-18<br />
12C-19<br />
8. INSTALL BATTERY AND BATTERY TRAY. (Refer to “Chapter 20B starting and charging - battery,<br />
12C-20<br />
FUEL - ELECTRONIC ACCELERATOR PEDAL<br />
ELECTRONIC ACCELERATOR PEDAL<br />
2. REMOVE ELECTRONIC ACCELERATOR PEDAL.<br />
Disconnect electronic accelerator pedal harness connector.<br />
Remove 3 electronic accelerator pedal retaining nuts.<br />
3. INSTALL ELECTRONIC ACCELERATOR PEDAL.<br />
(a) Install 3 electronic accelerator pedal retaining nuts.<br />
(b) Connect electronic accelerator pedal harness connector.<br />
(a) After installation, depress accelerator pedal to check that the accelerator pedal operates smoothly<br />
without stuck phenomenon.<br />
FUEL FILLER CAP ..........................................................................13C-1<br />
INSPECTION .............................................................................13C-1<br />
EGR VALVE .....................................................................................13C-2<br />
REPLACEMENT ........................................................................13C-2<br />
DIESEL OXIDATION CATALYST....................................................13C-3<br />
COMPONENTS .........................................................................13C-3<br />
REPLACEMENT ........................................................................13C-4<br />
13C<br />
13C-1<br />
(a) Install the fuel filler cap fixing clip into ring.<br />
13C-2<br />
EMISSION CONTROL - EGR VALVE<br />
1. EGR VALVE DESCRIPTION.<br />
EGR valve is located on the top of exhaust manifold<br />
which was actuated by the electric motor controlled by<br />
ECM. EGR valve is an lift valve designed to control EGR<br />
flow to EGR cooler .<br />
EGR motor can not be repaired, if damaged, the entire EGR<br />
valve must be replaced as a unit.<br />
2. REPLACE EGR VALVE. ( Refer to CUMMINS ISF SERIAL ENGINE SERVICE MANUAL)<br />
EMISSION CONTROL - DIESEL OXIDATION CATALYST<br />
DIESEL OXIDATION CATALYST<br />
13C-3<br />
1 Diesel Oxidation Catalyst (DOC)<br />
2 DOC upper bracket<br />
3 bolt<br />
5 bolt<br />
6 bolt<br />
7 DOC front grasket<br />
4 bolt<br />
13C-4<br />
3. REMOVE FRONT EXHAUST PIPE. (Refer to “Chapter 16B exhaust - exhaust pipe, replacement”)<br />
4. ISF 2.8 USES DIESEL OXIDATION CATALYST (DOC)<br />
TO REDUCE HC AND CO2 EMISSION.<br />
5. REPLACE DIESEL OXIDATION CATALYST. ( Refer to CUMMINS ISF SERIAL ENGINE SERVICE<br />
MANUAL )<br />
Post - processing system of diesel oxidation catalyst core are made by brittle materials. DO not drop<br />
or impact post-processing system side, because this conditon will result in serious damage for postprocessing<br />
diesel oxidation catalyst core .<br />
6. INSTALL DIESEL OXIDATION CATALYST. ( Refer to CUMMINS ISF SERIAL ENGINE SERVICE<br />
INTAKE AIR SYSTEM......................................................................14C-1<br />
PRECAUTION............................................................................14C-1<br />
COMPONENTS .........................................................................14C-2<br />
INTAKE AIR PIPE AND HOSE ........................................................14C-4<br />
REPLACEMENT ........................................................................14C-4<br />
AIR FILTER ASSY ...........................................................................14C-7<br />
REPLACEMENT ........................................................................14C-7<br />
INTERCOOLER INTAKE AIR PIPE...............................................14C-11<br />
REPLACEMENT ......................................................................14C-11<br />
14C<br />
14C-1<br />
14C-2<br />
1 Spring Clamp<br />
2 Intercooler Intake Air Hose<br />
3 Intercooler Rear Ripple Hose<br />
4 Intercooler Rigid Clamp<br />
5 Intercooler Inlet Rigid Pipe<br />
6 Intercooler Outlet Rigid Pipe<br />
7 Intercooler Assy<br />
9 Bolt, Spring Washer And Flat Washer<br />
11 Bolt, Spring Washer And Flat Washer<br />
14C-3<br />
1 Band Clamp<br />
2 Middle Intake Air Pipe<br />
4 Bending Hose<br />
5 Mass Air Flow Sensor<br />
6 Screw<br />
7 Air Filter Assy<br />
11 Washer<br />
12 Band Clamp<br />
13 Intake Air Duct<br />
14 Band Clamp<br />
15 Turbocharger Intake Air Ripple Hose<br />
8 Air Filter Assy Bracket<br />
14C-4<br />
2. REMOVE ASSISTANT DRIVER SEAT. (Refer to “Chapter 84 seat - driver / assistant driver seat,<br />
3. REMOVE ENGINE COMPARTMENT COVER UNDER<br />
(a) Remove 5 engine compartment cover retaining bolts.<br />
(b) Remove engine compartment cover.<br />
4. REMOVE TURBOCHARGER INTAKE AIR RIPPLE<br />
(a) Remove band clamps on both sides of turbocharger<br />
intake air ripple hose.<br />
(b) Remove turbocharger intake air ripple hose.<br />
14C-5<br />
5. REMOVE MIDDLE INTAKE AIR PIPE.<br />
(a) Remove 2 middle intake air pipe retaining bolts.<br />
(b) Remove retaining clamp on middle intake air pipe side.<br />
(c) Remove middle intake air pipe.<br />
6. REMOVE BENDING HOSE.<br />
(a) Remove air filter assy. (Refer to “Chapter 14B instake air<br />
- air filter assy, replacement”)<br />
Remove retaining clamp securing bending hose to air<br />
filter assy.<br />
Remove bending hose.<br />
7. INSTALL BENDING HOSE.<br />
(a) Connect bending hose to air filter assy outlet pipe, then<br />
tighten the retaining clamp.<br />
Connect one end of benging hose with triangle mark to air<br />
filter when installation.<br />
(b) Install air filter assy. (Refer to “Chapter 14B instake air -<br />
14C-6<br />
8. INSTALL MIDDLE INTAKE AIR PIPE.<br />
Position middle intake air pipe.<br />
Connect middle intake air pipe to bending hose and<br />
tighten retaining.<br />
Tighten 2 retaining bolts securing middle intake air pipe<br />
to body frame.<br />
9. INSTALL TURBOCHARGER INTAKE AIR RIPPLE HOSE.<br />
(a) Position turbocharger intake air ripple hose.<br />
(b) Tighten band clamps on both sides of turbocharger<br />
(a) After installing air intake pipe and hose, check all parts and parts connection and start the engine to<br />
make sure engine operates properly.<br />
11. INSTALL ENGINE COMPARTMENT COVER UNDER<br />
12. INSTALL ASSISTANT DRIVER SEAT. (Refer to “Chapter 84 seat - driver / assistant driver seat,<br />
13. PUT DOWN DRIVER SEAT AND LOCK IT.<br />
14C-7<br />
(a) Remove retaining bolt and clamp for air filter intake air<br />
(b) Remove intake air duct.<br />
(a) Remove retaining clamp securing bending hose to<br />
14C-8<br />
Disconnect mass air flow sensor connector, then remove<br />
air filter together with bending hose.<br />
Disconnect air filter and bending hose, remvoe air filter<br />
(b) Position air filter with bending hose, then connect MAF<br />
connector.<br />
14C-9<br />
Tighten clamp securing bending hose to middle intake air<br />
6. INSTALL INTAKE AIR DUCT.<br />
(a) Tighten the clamp securing intake air duct to air filter inlet<br />
14C-10<br />
7. INSTALL FRONT BUMPER. (Refer to “Chapter 88 exterior and interior trim - front bumper assy,<br />
8. INSTALL FRONT GRILLE. (Refer to “Chapter 88 exterior and interior trim - front grille, replacement”)<br />
9. REPLACE AIR FILTER ELEMENT.<br />
• The clean intake air has a great effect on diesel engine. Do not operate the engine without<br />
installing the air filter element.<br />
• Air filter element blocking will cause oil leakage from turbocharger. Therefore, the maintenance<br />
or replacement of air filter element must be performed periodically.<br />
INTAKE AIR - INTERCOOLER INTAKE AIR PIPE<br />
14C-11<br />
INTERCOOLER INTAKE AIR PIPE<br />
3. REMOVE INTERCOOLER ASSY.<br />
(a) Remove retaining spring clamp securing intercooler inlet<br />
pipe to intercooler intake air hose.<br />
Remove retaining spring clamp securing intercooler outlet<br />
pipe to intercooler rear ripple hose.<br />
Remove 4 intercooler assy retaining spring bolts.<br />
Separate intercooler from intake air hose and rear ripple<br />
Remove intercooler assy.<br />
14C-12<br />
4. INSTALL INTECOOLER ASSY.<br />
Positon intercooler assy and connect intercooler inlet<br />
and outlet pipe to intake air hose and rear ripple hose,<br />
then tighten 2 retaining band clamp.<br />
Tighten 4 intercooler assy retaining bolts.<br />
5. REMOVE INTERCOOLER INTAKE AIR RIGID PIPE.<br />
(a) Remove retaining clamp securing intercooler inlet rigid<br />
pipe to intake air hose.<br />
Remove retaining bolt securing underbody intercooler<br />
inlet rigid pipe.<br />
Remove spring clamp, disconnect intercooler inlet rigid<br />
pipe from intake air hose.<br />
Remove 4 intercooler assy retaining bolts.<br />
14C-13<br />
Remove intercooler inlet rigid pipe.<br />
6. INSTALL INTERCOOLER INLET RIGID PIPE.<br />
Connect intercooler inlet rigid pipe to intake air hose on<br />
turbocharger side.<br />
Tighten retaining clamp.<br />
Tighten intercooler inlet rigid pipe retaining bolt.<br />
Tighten retaining clamp securing intercooler inlet rigid<br />
Install intercooler assy. (Refer to “Chapter 14B intake air<br />
- intercooler intake air pipe, replacement”)<br />
14C-14<br />
7. REMOVE INTERCOOLER OUTLET RIGID PIPE.<br />
Remove retaining clamp securing intercooler outlet rigid<br />
pipe to rear ripple hose.<br />
outlet rigid pipe.<br />
Loosen retaining bolts on both sides of steering drive<br />
shaft assy II, then remove the bolt on steering gear side<br />
as shown in the figure.<br />
Separate steering drive shaft assy II from steering gear<br />
Remove retaining clamp, disconnect intercooler outlet<br />
rigid pipe from rear ripple hose.<br />
Remove 4 intercooler assy retainng bolts..<br />
14C-15<br />
Remove intercooler outlet rigid pipe.<br />
8. INSTALL INTERCOOLER OUTLET RIGID PIPE.<br />
Connect intercooler outlet rigid pipe to rear ripple hose<br />
on throttle actuator side.<br />
Tighten intercooler outlet rigid pipe retaining bolt from<br />
the vehicle beneath.<br />
Connect steering drive shaft assyII to steering gear<br />
output shaft, then tighten both bolts.<br />
Align marks when installing steering drive shaft assyII.<br />
14C-16<br />
Connect intercooler outlet rigid pipe to rear ripple hose,<br />
then tighten retaining clamp.<br />
(a) After installing intercooler intake air pipe, check all parts and parts connection and start the engine to<br />
10. INSTALL FRONT BUMPER. (Refer to “Chapter 88 exterior and interior trim - front bumper assy,<br />
11. INSTALL FRONT GRILLE. (Refer to “Chapter 88 exterior and interior trim - front grille, replacement”)<br />
ENGINE MECHANICAL PART ........................................................15C-1<br />
PRECAUTION............................................................................15C-1<br />
ENGINE ASSY .................................................................................15C-2<br />
REPLACEMENT ........................................................................15C-2<br />
ENGINE ACCESSORY BELT........................................................15C-12<br />
OVERHAUL .............................................................................15C-12<br />
15C<br />
15C-1<br />
(a) Follow the instructions of maintenance methods and regulations to adjust or maintain.<br />
(b) Before starting the engine, check the coolant level, fill or drain the coolant if necessary. check the<br />
(c) The clearance between ckp sensor and flywheel is 0.5 ~ 1.5 mm. Do not try to adjust it.<br />
(d) Use the oil as requirement. otherwise exacerbate engine wear.<br />
(e) Use the original fittings, otherwise it will damage the engine or affect the engine working condition.<br />
(f) Do not use the high pressure water cannons wash the ecm shell.<br />
(g) The engine starting time should be less than 5s. Not more than 5 consecutive starting times. The<br />
interval time to next starting should not be less than 15 seconds.<br />
(h) Keep the normal coolant temperature 85 ~ 105 ℃ .<br />
(i) When the engine in high speed or high load, do not turn the ignition switch off. Keep the engine running<br />
in low speed for 3~5 mins, so that the engine radiates eventually.<br />
(j) Before opening the radiator cap, ensure the engine is cool.<br />
(k) Use the sealant scraper to clear the sundrise in seal surface. Confirm seal surface flat and smooth, no<br />
pollution and foreign bodies.<br />
(l) Disassembly sequence should be generally from inner to outer, assembly to parts. In order to improve<br />
the efficiency and ensure the assembly and disassembly correct, pay attention to checking and making<br />
mark. Removed parts should be cleaned and inspected. The parts can be reused according to the<br />
classification. Precision parts should be separated with general parts. Put them in clean containers.<br />
(m) Assembly sequence should be from inside to outside, parts to components, components to assembly.<br />
Pay attention to the size, location, clearance, torque, etc. When assembling, avoid the missing,<br />
mistaking, scratching and foreign parts into machine. Assemble bolts, nuts with suitable wrench,<br />
uniform properly. Use anti-losseness device correctly. According to regulations, appropriately use split<br />
cotters, spring washer, thrust washers, etc. In addition, in the assembly process, must pay attention to<br />
the marks to ensure the good position.<br />
(n) Ensure the diesel engine always in the state of complete cleaness. Before removing or assembling,<br />
parts should be cleaned to ensure clean and high quality assembly. More complicated adjustment and<br />
maintenance should be done indoor to prevent diesel engine internal parts from environmental<br />
pollution.<br />
(o) Pay attention to the security when repairing or dismantling. Improper tool or engine starting suddenly<br />
will result in injury.<br />
15C-2<br />
2. RECOVER REFRIGERANT. (Refer to “Chapter 61 heater and air conditioner - refrigerant,<br />
3. RELEASE FUEL SYSTEM PRESSURE. (Refer to “Chapter 12B fuel - fue system, fuel system<br />
4. RAISE AND SUPPORT THE VEHICLE.<br />
5. DRAIN COOLANT. (Refer to “Chapter 17B cooling - coolant, replacement”)<br />
6. DRAIN ENGINE OIL. (Refer to “Chapter 18B lubricantion - engine oil, replacement”)<br />
7. DRAIN TRANSMISSION FLUID. (Refer to “Chapter 41 transmission - transmission assy, replacement”)<br />
9. OPEN ENGINE COMPARTMENT COVER.<br />
10. DISCONNECT BATTERY NEGATIVE CABLE.<br />
11. REMOVE ASSISTANT DRIVER SEAT. (Refer to “Chapter 84 seat - driver / assistant driver seat,<br />
12. REMOVE ENGINE COMPARTMENT COVER UNDER<br />
15C-3<br />
13. DISCONNECT GENERATOR POSITIVE CABLE.<br />
14. DISCONNECT GENERATOR CONNECTOR.<br />
15. REMOVE TURBOCHARGER INTAKE AIR RIPPLE HOSE. (Refer to “Chapter 14B intake air -<br />
intake air pipe and hose, replacement”)<br />
16. REMOVE MASS AIR FLOW SENSOR CONNECTOR. (Refer to “Chapter 14B intake air - air filter<br />
17. REMOVE INTERCOOLER OUTLET STEEL PIPE. (Refer to “Chapter 14B intake air - intercooler<br />
intake air pipe, replacement”)<br />
18. REMOVE A/C PIPE FROM COMPRESSOR.<br />
(a) Remove the retaining bolt securing high pressure and<br />
low pressure pipes to compressor.<br />
19. REMOVE AIR INTAKE PIPE.<br />
(a) Disconnect ECM wire harness connectors and additonal<br />
one electrical connector in the ECM compartment.<br />
(b) Pull engine wire harness and ECM rubber grommet out<br />
of the hole on the sidewall of ECM compartment.<br />
20. REMOVE GROUND CABLE MOUNTED ON ENGINE<br />
THROTTLE ACTUATOR.<br />
21. DISCONNECT VACUUM BOOSTER HOSE FROM<br />
INAKE MANIFOLD.<br />
15C-4<br />
22. DISCONNECT ENGINE WIRE HARNESS CONNEC-<br />
TORS THROUGH THE HOLE ON THE SIDEWALL OF<br />
BATTERY COMPARTMENT FROM BATTERY COM-<br />
PARTMENT FUSE BOX CONNECTOR RECEPTACLE.<br />
23. DISCONNECT ENGINE WATER OUTLET HOSE.<br />
24. DISCONNECT ENGINE BLEEDING HOSE.<br />
25. REMOVE POWER STEERING FLUID RESERVIOR<br />
FROM THE BRACKET. (Refer to “Chapter 52 power<br />
steering - power steering pump with fluid reservior,<br />
26. REMOVE INTERCOOLER INLET STEEL PIPE. (Refer to “Chapter 14B intake air - intercooler<br />
27. RAISE AND SUPPORT THE VEHICLE.<br />
28. REMOVE FRONT WHEELS. (Refer to “Chapter 33 wheel and tire - wheel, replacement”)<br />
30. REMOVE RIGHT FRONT SUSPENSION UNIT.<br />
29. REMOVE LEFT FRONT SUSPENSION UNIT.<br />
15C-5<br />
31. REMOVE STEERING DRIVE SHAFT ASSY II.<br />
32. DISCONNECT ENGINE WATER INLET HOSE.<br />
33. DISCONNECT ENGINE FUEL DELIVERY LINE FROM<br />
DIESEL FILTER ASSY.<br />
34. DISCONNECT FUEL RETURN TUBE.<br />
35. REMOVE STARTER POSITIVE CABLE.<br />
36. REMOVE TRANSMISSION FLEXIBLE SHAFT ASSY. (Refer to “Chapter 41 transmission -<br />
37. REMOVE CLUTCH SLAVE CYLINDER. (Refer to “Chapter 42 clutch - clutch slave cylinder,<br />
38. REMOVE FRONT EXHAUST PIPE. (Refer to “Chapter 16B exhaust - exhaust pipe, replacement”)<br />
39. DISCONNECT VSS AND BACK-UP LAMP SWITCH HARNESS CONNECTORS. (Refer to “Chapter<br />
41 transmission - transmission assy, replacement”)<br />
40. SUPPORT ENGINE SUB-FRAME AND TRANSMISSION ASSY WITH HYDRAUMATIC JACK.<br />
15C-6<br />
41. REMOVE SUB-FRAME RETAINING BOLTS.<br />
Remove 5 retaining bolts from right side of sub-frame.<br />
The left is similar as the above, remove 5 retaining bolts<br />
from left side of sub-frame.<br />
retaining bolts when installing.<br />
42. SEPARATE PROPELLER SHAFT FROM TRANSMISSION ASSY. (Refer to “Chapter 34 axle and<br />
43. REMOVE TRANSMISSION MOUNT.<br />
height with jack, pull the retaining bolt for separating the<br />
44. LOWER THE JACK SLOWLY TO SEPARATE ENGINE SUB-FRAME AND TRANSMISSION ASSY<br />
transmission and vehicle are disconnected before lowering engine sub-frame and transmission<br />
45. SEPARATE ENGINE ASSY FROM TRANSMISSION ASSY. (Refer to “Chapter 41 transmission -<br />
46. DISCONNECT HIGH PRESSURE AND LOW PRESSURE FLUID PIPES FROM POWER STEERING<br />
47. FIT ENGINE HOOK AND HANG ENGINE ASSY WITH A HOIST<br />
48. REMOVE ENGINE MOUNTS LOCATED ON BOTH SIDES OF ENGINE.<br />
49. HOIST ENGINE UP AND SEPARATE ENGINE FROM SUB-FRAME.<br />
50. INSTALL BOTH ENGINE MOUNTS ON ENGINE.<br />
51. CONNECT HIGH PRESSURE AND LOW PRESSURE FLUID PIPES TO POWER STEERING PUMP.<br />
52. INSTALL TRANSMISSION ASSY ONTO ENGINE. (Refer to “Chapter 41 transmission -<br />
53. PLACE THE HYDRAULIC JACK SUPPORTING ENGINE SUB-FRAME AND TRANSMISSION ASSY<br />
UNDER THE VEHCLE.<br />
54. RAISE THE HYDRAULIC JACK UNTIL THE SUB-FRAME RETAINING GUDIES ARE FULLY<br />
SEATED INTO THE VEHICLE FRAME AND TRANSMISSION MOUNT IS POSITIONED IN PLACE<br />
PROPERLY.<br />
15C-7<br />
55. INSTALL SUB-FRAME RETAINING BOLTS.<br />
Install 5 retaining bolts securing sub-frame right side to<br />
The left is similar as the above, install 5 retaining bolts<br />
securing sub-frame left side to vehicle frame.<br />
56. INSTALL RETAINING NUT SECURING TRANSMISSION<br />
57. REMOVE GENERATOR RETAINING BOLTS AND<br />
58. INSTALL RIGHT FRONT SUSPENSION UNIT.<br />
59. INSTALL FRONT WHEEL. (Refer to “Chapter 33 wheel and tire - wheel, replacement”)<br />
15C-8<br />
60. INSTALL STEERING DRIVE SHAFT ASSY II.<br />
When installing steering drive shaft assy II, make sure<br />
steering wheel is in the center and front wheel stands<br />
straight ahead of the vehicle.<br />
61. INSTALL TRANSMISSION FLEXIBLE SHAFT ASSY. (Refer to “Chapter 41 transmission -<br />
62. INSTALL CLUTCH SLAVE CYLINDER. (Refer to “Chapter 42 clutch - clutch slave cylinder,<br />
63. INSTALL FRONT EXHAUST PIPE. (Refer to“Chapter 16B exhaust - exhaust pipe, replacement”)<br />
64. CONNECT PROPELLER SHAFT TO TRANSMISSION ASSY. (Refer to “Chapter 34 axle and<br />
65. CONNECT VSS AND BACK-UP LAMP SWITCH HARNESS CONNECTOR. (Refer to “Chapter 41<br />
transmission - transmission assy, replacement”)<br />
66. CONNECT ENGINE WATER INLET HOSE.<br />
67. INSTALL INTERCOOLER INLET STEEL PIPE. (Refer to “Chapter 14B intake air - intercooler<br />
68. INSTALL INTERCOOLER OUTLET STEEL PIPE. (Refer to “Chapter 14B intake air - intercooler<br />
69. CONNECT ENGINE FUEL DELIVERY LINE TO DIESEL<br />
FILTER ASSY.<br />
70. CONNECT FUEL RUTURN TUBE.<br />
71. CONNECT STARTER POSITIVE CABLE.<br />
72. LOWER THE VEHICLE.<br />
15C-9<br />
73. CONNECT ENGINE WATER OUTLET HOSE AND<br />
74. CONNECT ENGINE BLEEDING HOSE AND TIGHTEN<br />
CLAMP.<br />
75. INSTALL POWER STEERING FLUID RESERVIOR TO<br />
THE BRACKET. (Refer to “Chapter 52 power steering<br />
- power steering pump with fluid reservior,<br />
76. CONNECT WATER INLET AND WATER OUTLET<br />
HOSE TO FRONT HEATER, THEN TIGHTERN THE<br />
CLAMPS.<br />
77. INSTALL A/C PIPES TO COMPRESSOR.<br />
(a) Install the retaining bolt securing high pressure and low<br />
Torque: 40 ~ 45 N•m<br />
Always install O-ring with new one.<br />
78. INSTALL MASS AIR FLOW SENSOR CONNECTOR. (Refer to “Chapter 14B intake air - air filter<br />
79. INSTALL TURBOCHARGER INTAKE AIR RIPPLE HOSE. (Refer to “Chapter 14B intake air - intake<br />
air pipe and hose, replacement”)<br />
80. CONNECT GERERATOR CONNECTOR AND TIGHTEN<br />
GENERATOR POSITIVE CABLE RETAINING NUT.<br />
15C-10<br />
81. INSTALL ENGINE WIRE HARNESS.<br />
(a) Connect engine ECM harness connectors and additional<br />
one electrical connector through the hole on the sidewall<br />
of engine compartment.<br />
(b) Press the rubber grommet into place.<br />
82. INSTALL GROUND CABLE TO THE THROTTLE<br />
ACTUACTOR SIDE.<br />
83. CONNECT VACUUM BOOSTER HOSE TO INTAKE<br />
84. CONNECT ENGINE WIRE HARNESS TO BATTERY COM-<br />
85. INSTALL ENGINE COMPARTMENT COVER UNDER<br />
86. INSTALL ASSISTANT DRIVER SEAT. (Refer to “Chapter 84 seat - driver / assistant driver seat,<br />
87. PUT DOWN DRIVER SEAT AND LOCK IT.<br />
88. FILL COOLANT. (Refer to “Chapter 17B cooling - coolant, replacement”)<br />
15C-11<br />
89. FILL ENGINE OIL. (Refer to “Chapter 18B lubricantion - engine oil, replacement”)<br />
90. ADD POWER STEERING FLUID TO SPECIFIED LEVEL. (Refer to “Chapter 52 power steering -<br />
91. FILL TRANSMISSION FLUID. (Refer to “Chapter 41 transmission - transmission assy, replacement”)<br />
92. SUPPLY REFRIGERANT. (Refer to “Chapter 61 heater and air conditioner - refrigerant, replacement”)<br />
15C-12<br />
ENGINE MECHANICAL - ENGINE ACCESSORY BELT<br />
ENGINE ACCESSORY BELT<br />
2. Open the engine hood.<br />
3. Wait until the engine cools down.<br />
4. Drain the coolant. (Refer to "Chapter 17B. Cooling - coolant, replacement")<br />
5. Unscrew the clip screw and pull out the engine water<br />
outlet hose.<br />
6. With the toolkit, turn the accessory belt tensioner<br />
bolt clockwise, until the accessory belt is completely<br />
7. Remove and examine the accessory belt. Replace it in case of any of the following damages:<br />
• Water or grease on the belt will quickly reduce its service life. Therefore, after removal, protect the belt,<br />
the belt pulley and the tensioner from water or grease. Do not wash these parts. In case of heavy<br />
contamination, replace it with a new one.<br />
• If any water or grease is found on these parts, check whether there is fluid leakage in the engine.<br />
(a) Aged and shiny rubber on the back, showing no nail<br />
15C-13<br />
Unusal tear wear of the belt.<br />
8. Put the accessory belt around all the belt pulley,<br />
tensioner and idler, except for the generator belt<br />
pulley. With the toolkit, turn the tensioner bolts<br />
clockwise, so that the accessory belt wraps around<br />
the generator belt pulley. Loose the tensioner.<br />
After the installation of the accessory belt, check whether it<br />
is properly installed around each pulleys. If any malposition<br />
between the belt and the pulley, turn the tensioner nuts with<br />
the toolkit and slightely loosen the accessory belt, before<br />
further adjustment.<br />
15C-14<br />
9. Install the engine water outlet hose and tighten the<br />
clip screw.\<br />
10. Fill up the coolant. (Refer to "Chapter 17B. Cooling - coolant, replacement")<br />
11. Restore the engine hood.<br />
EXHAUST PIPE ...............................................................................16C-1<br />
COMPONENTS .........................................................................16C-1<br />
PRECAUTION............................................................................16C-2<br />
REPLACEMENT ........................................................................16C-3<br />
16C<br />
16C-1<br />
1 Rubber Support<br />
2 Rear Muffler Assy<br />
3 Nut<br />
4 Spring Washer<br />
5 Exhaust Piper Seal Gasket<br />
7 Front Muffler Assy<br />
8 Front Exhaust Pipe Assy<br />
9 Front Rubber Support<br />
16C-2<br />
16C-3<br />
3. REMOVE REAR MUFFLER ASSY.PRECAUTION<br />
4. CHECK REAR MUFFLER ASSY.<br />
(a) Tap or shake the muffler, check to make sure that broken<br />
(a) Remove front muffler rear mounting rubber<br />
16C-4<br />
7. REMOVE FRONT EXHAUST PIPE ASSY.<br />
(a) Remove front exhaust pipe mounting rubber.<br />
(b) Remove 2 retaining bolts securing front exhaust pipe to<br />
diesel oxidation catalyst.<br />
8. REMVOE DIESEL OXIDATION CATALYST. (Refer to CUMMINS ISF SERIES ENGINE SERVICE<br />
MANUAL)<br />
9. INSTALL DIESEL OXIDATION CATALYST. (Refer to CUMMINS ISF SERIES ENGINE SERVICE<br />
• When installing heat shield, avoid large gaps or interference between heat shield and each<br />
exhaust pipes.<br />
16C-5<br />
10. INSTALL FRONT EXHAUST PIPE ASSY.<br />
(a) Install front exhaust pipe rubber support.<br />
(b) Tighten 2 retaining bolts securing front exhaust pipe to<br />
Torque: 45 ~ 55 N•m<br />
11. INSTALL FRONT MUFFLER ASSY.<br />
Install 1 mounting rubber at the rear side of front muffler<br />
12. INSTALL REAR MUFFLER ASSY.<br />
(a) Install rear muffler mounting rubber.<br />
16C-6<br />
COOLING SYSTEM .........................................................................17C-1<br />
PRECAUTION............................................................................17C-1<br />
COMPONENTS .........................................................................17C-2<br />
PROBLEM SYMPTOMS TABLE................................................17C-4<br />
ON-VEHICLE INSPECT.............................................................17C-5<br />
COOLANT ........................................................................................17C-7<br />
REPLACEMENT ........................................................................17C-7<br />
RESERVIOR.....................................................................................17C-9<br />
REPLACEMENT ........................................................................17C-9<br />
COOLING FAN ASSY....................................................................17C-11<br />
OVERHAUL .............................................................................17C-11<br />
RADIATOR.....................................................................................17C-14<br />
REPLACEMENT ......................................................................17C-14<br />
17C<br />
17C-1<br />
(f) Use foton specified coolant, do not use water instead of coolant. Water will damage the engine because<br />
of corrosion.<br />
17C-2<br />
17C-3<br />
2 Hose Clamp<br />
3 Engine Inlet Hose No. 2<br />
5 Engine Inlet Pipe<br />
6 Engine Inlet Hose<br />
7 Hose Clamp<br />
8 Engine Outlet Hose No. 2<br />
9 Engine Outlet Pipe<br />
10 Engine Outlet Hose<br />
11 Hose Clamp<br />
18 Single Line Clip<br />
19 Engine Bleeding Hose<br />
20 Single Line Clip<br />
21 Clamp<br />
22 Hose Clamp<br />
17C-4<br />
1. Coolant (Lack or leaking) Chapter 17B cooling - coolant, replacement<br />
2. Coolant (Non-standard) Chapter 17B cooling - coolant, replacement<br />
3. Thermostat (Damaged) Chapter 17B cooling - thermostat, overhaul<br />
5. Radiator (Poor cooling) Chapter 17B cooling - cooling system, precaution<br />
6. Cooling fan (Damaged) Chapter 17B cooling - cooling fan, overhaul<br />
1. Radiator(Damaged) Chapter 17B cooling - radiator, replacement<br />
2. Cooling system hose(Blocked) -<br />
3. Coolant pump(Damaged) Chapter 17B cooling - coolant pump, replacement<br />
4. Coolant reservoir(Damaged) Chapter 17B cooling - coolant, replacement<br />
Engine room noise<br />
1. Cooling fan(Damaged) Chapter 17B cooling - cooling fan assy, overhaul<br />
2. Cooling line -<br />
17C-5<br />
blown out under pressure.<br />
17C-6<br />
• Be careful not to spary water directly onto electronic components.<br />
17C-7<br />
17C-8<br />
17C-9<br />
1. DRAIN ENGINE COOLANT. (Refer to “Chapter 17B cooling - coolant, replacement”)<br />
(a) Open reservior cover by turn it slowly to release the<br />
Remove reservior vent hose clamp and disconnect vent<br />
Remove reservior refilling hose clamp and disconnect<br />
17C-10<br />
Locate the lower support of reservior into rubber sleeve<br />
17C-11<br />
(a) Remove 4 cooling fan bracket retaining bolts and nuts.<br />
(b) Remove retaining nut securing A/C pipe clamp.<br />
17C-12<br />
(b) Resistance between white wire and red wire:1.377±15%Ω ;<br />
(c) Visually inspect cooling fan blade for cracks or unusual bend.<br />
(d) Rotate cooling fan by hand, the blades should be rotated smoothly.<br />
17C-13<br />
Tighten A/C pipe clamp retaining nut.<br />
17C-14<br />
2. REMOVE RESERVIOR.(Refer to “Chapter 17B cooling - reservior, replacement”)<br />
3. REMOVE COOLING FAN ASSY. (Refer to “Chapter 17B cooling- cooling fan assy, replacement”)<br />
4. REMOVE FRONT GRILLE. (Refer to “Chapter 88 exterior amd interior trim - front grille, replacement”)<br />
5. REMOVE FRONT BUMPER. (Refer to “Chapter 88 exterior amd interior trim - front bumper,<br />
(b) Pull out reservior refilling hose from fan cow fixing clip.<br />
17C-15<br />
Pull out reservior vent hose from fixing clip on radiator<br />
Disconnect engine hood switch connector and remove<br />
17C-16<br />
17C-17<br />
(a) Connect engine water inlet hose to radiator.<br />
17C-18<br />
16. INSTALL COOLING FAN ASSY. (Refer to “Chapter 17B cooling - cooling fan, overhaul”)<br />
17. INSTALL RESERVIOR. (Refer to “Chapter 17B cooling - reservior, replacement”)<br />
20. FILL COOLANT. (Refer to “Chapter 17B cooling - coolant, replacement”)<br />
(a) After installing radiator, let engine be running until cooling fan runs at high speed. check coolant for<br />
LUBRICATION SYSTEM .................................................................18C-1<br />
PRECAUTION............................................................................18C-1<br />
ENGINE OIL .....................................................................................18C-2<br />
REPLACEMENT ........................................................................18C-2<br />
OIL FILTER ......................................................................................18C-4<br />
REPLACEMENT ........................................................................18C-4<br />
OIL PAN ...........................................................................................18C-6<br />
REPLACEMENT ........................................................................18C-6<br />
OIL PUMP ........................................................................................18C-7<br />
REPLACEMENT ........................................................................18C-7<br />
18C<br />
18C-1<br />
skin, allergies and dermatitis. In addition, used engine oil contains potentially harmful pollutants may<br />
cause skin cancer. Therefore, the skin must be protected in appropriate methods and with cleaning<br />
Avoid contacting with oil for a long time, especially the used engine oil.<br />
Wear protective clothing, including waterproof work gloves.<br />
Avoid contaminated clothing, especially underwear containing the oil.<br />
Never put rags contaminated with oil in pockets.<br />
Avoid eyes contact with oil, must wear goggles, In addition, equipment must be prepared to clean the<br />
eyes and wrapping the wound must be dealt with immediately.<br />
Frequent use of soap and water can clean, especially before meals, and make sure all the oil have<br />
been removed (skin cleansers can also be used to assist with the nail brush). After cleaning, it is<br />
Do not use gasoline, kerosene, diesel, thinner or solvent to clean skin.<br />
Before each work, apply cream to help skin cleaning after work.<br />
If your skin is abnormal, consult a doctor immediately.<br />
18C-2<br />
4. OPEN ENGINE COMPARTMENT COVER.<br />
5. OPEN OIL FILLER CAP.<br />
6. LIFT THE VEHICLE.<br />
7. REMOVE OIL DRAIN PLUG.<br />
8. USING A SPECIAL CONTAINER, COLLECT OR DISPOSE USED OIL AS REQUIRED.<br />
9. REPLACE A NEW DRAIN PLUG GASKET AND TIGHTEN<br />
10. LOWER VEHICLE.<br />
11. FILL ENGINE OIL.<br />
12. INSTALL OIL FILLER CAP.<br />
18C-3<br />
13. PARK THE VEHICLE ON LEVEL GROUND AND START ENGINE UNTIL IT IS WARM.<br />
14. CHECK OIL FILTER OR OTHER PART AND ENSURE THERE IS NO OIL LEAKAGE.<br />
15. TURN IGNITION SWITCH OFF.<br />
16. AFTER 8 ~ 10 MINUTES, PULL OUT OIL DIPSTICK TO<br />
18C-4<br />
Without special circumstances, the oil filter should be<br />
replaced with engine oil to avoid oil pollution and keep<br />
engine normal operation.<br />
18C-5<br />
19. PUT DOWN DRIVER SEAT AND LOCK IT.<br />
18C-6<br />
1. OPEN OIL FILLER CAP.<br />
3. REMOVE OIL DRAIN PLUG.<br />
Be careful, the engine oil may be hot.<br />
4. USING A SPECIAL CONTAINER, COLLECT OR DISPOSE USED OIL AS REQUIRED.<br />
5. REMOVE OIL PAN. ( Refer to CUMMINS ENGINE ISF SERIAL SERVICE MANUAL )<br />
6. CLEAN SURFACE BETWEEN LADDER FRAME AND ENGINE BLOCK.<br />
7. INSTALL OIL PAN. ( Refer to CUMMINS ENGINE ISF SERIAL SERVICE MANUAL )<br />
8. TIGHTEN DRAIN PLUG.<br />
9. LOWER VEHICLE AND FILL ENGINE OIL TO SPECIFIED LEVEL.<br />
18C-7<br />
1. ISF 2.8 ENGINE USES INNER GEAR TYPE OIL PUMP WHICH IS LOCATED INSIDE FRONT GEAR<br />
CHAMBER COVER AND DRIVED BY CRANKSHAFT DIRECTLY.<br />
2. REPLACE OIL PUMP.(Refer to CUMMINS ENGINE ISF SERIAL SERVICE MANUAL )<br />
STARTING AND CHARGING SYSTEM ..........................................20C-1<br />
PRECAUTION............................................................................20C-1<br />
PROBLEM SYMPTOMS TABLE................................................20C-2<br />
GENERATOR...................................................................................20C-4<br />
OVERHAUL ...............................................................................20C-4<br />
STARTER.......................................................................................20C-10<br />
COMPONENTS .......................................................................20C-10<br />
OVERHAUL .............................................................................20C-11<br />
BATTERY.......................................................................................20C-18<br />
COMPONENTS .......................................................................20C-18<br />
USE AND MAINTENANCE......................................................20C-19<br />
INSPECTION ...........................................................................20C-21<br />
TROUBLESHOOTING.............................................................20C-22<br />
REPLACEMENT ......................................................................20C-24<br />
20C<br />
20C-1<br />
(a) Battery may have escaping explosive gas. in order to avoid personal injury, keep ventilated in engine<br />
(b) Battery electrolyte is very dangerous. It can damage the machine and cause serious burns. When<br />
(c) When using compressed air, wear appropriate goggles and protective mask. Dust particles and dirt can<br />
(d) Don't tighten the electrical connectors excessively, which may damage the starter.<br />
(e) Never short two cables of the battery, it will cause a rapid battery fever even an explosion occur. The<br />
(f) After the generator operation, do not try to use spark check whether the generator works. Use bulb or<br />
(g) Check the generator silicon rectifier devices, it is strictly forbidden to use multimeter or apply 220V<br />
20C-2<br />
Chapter 20B starting and charging - starter,<br />
4. Brush (Wear) or Brush spring<br />
(Loss elastic force)<br />
1. Bearing (Wear) Chapter 20B starting and charging - starter,<br />
after engine start.<br />
2. Starter relay (Copper contacts<br />
bond)<br />
3. Starter commutator (Bend or break)<br />
4. Starter gear tooth surface contact<br />
1. Generator connect wire Check wire harness<br />
Chapter 20B starting and charging - generator,<br />
20C-3<br />
2. Brush (Poor connection) or Collector<br />
Chapter 15B engine mechanical - engine<br />
4. Battery lose electrolyte or battery<br />
plate (Damaged)<br />
20C-4<br />
4. REMOVE ASSISTANT DRIVER SEAT. (Refer to “Chapter 84 driver / assistant driver seat - replacement”)<br />
5. REMOVE ENGINE COMPARTMENT COVER UNDER<br />
ASSISTANT DRIVER SEAT .<br />
(a) Open front surfacing on engine compartment cover.<br />
(b) Remove 5 engine compartment cover mounting bolts.<br />
(c) Remove engine compartment cover under assistant<br />
driver seat.<br />
6. REMOVE ENGINE BELT. (Refer to CUMMINS ENGINE ISF SERIAL SERVICE MANUAL)<br />
7. REMOVE GENERATOR. (Refer to CUMMINS ENGINE ISF SERIAL SERVICE MANUAL)<br />
(a) Using pneumatic tools, loosen generator belt pulley retaining<br />
20C-5<br />
20C-6<br />
20C-7<br />
20C-8<br />
11. INSTALL GENERATOR.(Refer to CUMMINS ENGINE ISF SERIAL SERVICE MANUAL)<br />
12. INSTALL GENERATOR BELT.(Refer to CUMMINS ENGINE ISF SERIAL SERVICE MANUAL)<br />
13. CONNECT BATTERY NEGATIVE CABLE.<br />
20C-9<br />
14. INSTALL ENGINE COMPARTMENT COVER UNDER<br />
(a) Place engine compart cover in proper position.<br />
(b) Tighten 5 engine compartment cover mounting bolts.<br />
15. INSTALL ASSISTANT DRIVER SEAT.(Refer to “Chapter 84 driver / assistant driver seat - replacement”)<br />
16. PUT DOWN DRIVER SEAT AND LOCK IT.<br />
20C-10<br />
20C-11<br />
4. REMOVE STARTER. (Refer to 《CUMMINS ENGINE ISF SERIAL SERVICE MANUAL》 )<br />
5. INSPECT STARTER<br />
20C-12<br />
Magnetic switch hold-in test.<br />
20C-13<br />
20C-14<br />
20C-15<br />
(b) Contact fusion check.<br />
20C-16<br />
20C-17<br />
14. INSTALL STARTER. (Refer to CUMMINS ENGINE ISF SERIAL SERVICE MANUAL)<br />
20C-18<br />
20C-19<br />
(a) Rectifier.<br />
(b) Controllable silicone voltage regulation charger.<br />
2. CHARGE PRECAUTIONS<br />
20C-20<br />
20C-21<br />
20C-22<br />
20C-23<br />
20C-24<br />
20C-25<br />
8. INSTALL BATTERY .<br />
V O L U M E 5<br />
31-32 SUSPENSION SYSTEM 2303<br />
33 TYRE AND WHEEL 2341<br />
34 AXLE AND PROPELLER SHAFT 2353<br />
35-36 BRAKING SYSTEMS 2407<br />
41 TRANSMISSION 2467<br />
42 CLUTCH 2545<br />
51 STEERING COLUMN 2567<br />
52 POWER STEERING 2591<br />
61 HEATER AND AIR CONDITIONING 2627<br />
62 SUPPLEMENTAL RESTRAINT SYSTEM 2715<br />
63 SEAT BELT 2735<br />
64 LIGHTING 2759<br />
65 WIPER AND WASHER 2789<br />
66 AUDIO SYSTEM 2811<br />
71 WIRING 2827<br />
81 COMMUNICATION SYSTEM 3221<br />
82 WINDSHIELDS, MIRRORS & GLASS 3237<br />
83 INSTRUMENT PANEL 3261<br />
84 SEATS 3279<br />
85 DOOR LOCKS 3305<br />
86 SLIDING ROOF 3327<br />
87 DOORS AND ENGINE HOOD 3337<br />
88 EXTERIOR AND INTERIOR TRIM 3359<br />
91 VEHICLE CONTROL SYSTEM 3397<br />
SUSPENSION SYSTEM<br />
FRONT SUSPENSION............................................................. 31-1<br />
FRONT WHEEL ALIGNMENT ................................................... 31-08<br />
FRONT SHOCK ABSORBER.................................................... 31-10<br />
TORSION BAR........................................................................... 31-12<br />
UPPER CONTROL ARM............................................................ 31-15<br />
LOWER CONTROL ARM........................................................... 31-18<br />
STABILIZER BAR...................................................................... 31-20<br />
STRUT ROD............................................................................... 31-23<br />
REAR SUSPENSION ............................................................... 32-1<br />
REAR SHOCK ABSORBER .......................................................... 32-4<br />
REAR LEAF SPRING ASSY.......................................................... 32-6<br />
FRONT SUSPENSION....................................................................... 31-1<br />
PRECAUTION.............................................................................. 31-1<br />
PROBLEM SYMPTOMS TABLE.................................................. 31-2<br />
ROAD TEST ................................................................................ 31-4<br />
COMPONENTS ........................................................................... 31-5<br />
ON-VEHICLE INSPECTION ........................................................ 31-7<br />
FRONT WHEEL ALIGNMENT ........................................................... 31-8<br />
ADJUSTMENT............................................................................. 31-8<br />
FRONT SHOCK ABSORBER.......................................................... 31-10<br />
OVERHAUL ............................................................................... 31-10<br />
TORSION BAR................................................................................. 31-12<br />
REPLACEMENT ........................................................................ 31-12<br />
UPPER CONTROL ARM.................................................................. 31-15<br />
REPLACEMENT ........................................................................ 31-15<br />
LOWER CONTROL ARM................................................................. 31-18<br />
REPLACEMENT ........................................................................ 31-18<br />
STABILIZER BAR............................................................................ 31-20<br />
REPLACEMENT ........................................................................ 31-20<br />
STRUT ROD..................................................................................... 31-23<br />
OVERHAUL ............................................................................... 31-23<br />
SUSPENSION<br />
1. FRONT SUSPENSION PRECAUTION<br />
FRONT SUSPENSION - FRONT SUSPENSION<br />
31-1<br />
When installing rubber parts, the tires must be on the ground in no-load condition at final tightening.<br />
Lubricating oil will shorten the life of rubber liner. Must clean the spilled lubricating oill.<br />
After installing the suspension parts, check wheel alignment. If necessary, adjust it.<br />
Lock nut is not reusable. Use new one at every installation. When replacing new parts, do not clean the<br />
lubrication oil on the lock nut before tightening it.<br />
31-2<br />
Use the table below to help you find the cause of the problem. The numbers indicate the priority of the<br />
likely cause of the problem. Check each part in order. If necessary, replace these parts<br />
1. Lubrication oil (Excess) -<br />
Shock absorber<br />
oil leakage<br />
2. Seals (Failure or damaged) -<br />
3. Shock absorber (Failure) Chapter 31 front suspension - front shock absorber,<br />
Pulling to one side<br />
1. Tire (Worn or improperly inflated)<br />
2. Wheel alignment (Incorrect)<br />
3. Steering linkage (Loose or worn)<br />
4. Hub bearing (Worn)<br />
5. Steering gear (Maladjusted or<br />
damaged)<br />
6. Suspension parts (Worn)<br />
Chapter 33 wheel and tire - wheel and tire assy, onvehicle<br />
inspection<br />
Chapter 31 front suspension - front wheel alignment,<br />
adjustment<br />
Chapter 51 steering column - steering column assy,<br />
Chapter 51 steering column - steering propeller<br />
shaft assy, overhaul<br />
Chapter 34 axle and propeller shaft - front wheel<br />
hub, overhaul<br />
Chapter 52 power steering - steering box, overhaul<br />
Chapter 31 front suspension - front suspension, onvehicle<br />
1. Vehicle (Overloaded) -<br />
Bottoming<br />
Sways/tilt<br />
2. Shock absorber (Worn or<br />
2. Steering linkage (Loose or worn)<br />
3. Stabilizer bar (Bent or broken)<br />
4. Shock absorber (Worn or<br />
Chapter 31 front suspension - front shock absorber,<br />
Chapter 31 Rear suspension - Rear shock absorber,<br />
Chapter 33 wheel and tire - wheel and tire assy,<br />
Chapter 31 front suspension - stabilizer bar,<br />
31-3<br />
2. Wheel (Out of balance)<br />
3. Shock absorber (Worn or<br />
4. Wheel alignment (Incorrect)<br />
Front wheel<br />
shimmy<br />
5. Ball joint (Worn or damaged)<br />
Chapter 31 front suspension - upper control arm,<br />
Chapter 31 front suspension - lower control arm,<br />
6. Hub bearing (Worn)<br />
Chapter 34 axle and propeller shaft - hub and<br />
steering knuckle, on-vehicle inspection<br />
7. Steering linkage (Loose or worn)<br />
8. Steering gear (Maladjusted or<br />
1. Wheel alignment (Incorrect)<br />
Abnomal tire wear<br />
2. Tire (Worn or improperly inflated)<br />
3. Wheel (Out of balance)<br />
Chapter 33 wheel and tire - wheel and tire assy, on<br />
vehicle inspection<br />
4. Shock absorber (Worn or damaged)<br />
31-4<br />
ROAD TEST<br />
This is a flow chart for vehicle pull.<br />
31-5<br />
1 Front Shock Absorber Assy<br />
3 Flat Washer<br />
4 Lower Damping Block Assy<br />
5 Bolt<br />
6 Lower Control Arm Assy RH<br />
7 Flat Washer<br />
8 Bolt<br />
9 Stabilizer Bar Mounting Bracket RH<br />
11 Sping Washer<br />
12 M10 Nut M10<br />
13 Lower Control Arm Camshaft Assy<br />
14 Nut<br />
15 Lower Control Arm Cam<br />
16 Flat Washer<br />
17 1 Style-Nut<br />
18 Front Stabilizer Bar Assy<br />
19 Bolt<br />
20 Stabilizer Bar Mounting Bracket LH<br />
21 Nut<br />
22 Upper Damping Block Assy<br />
23 Bolt<br />
24 Sping Washer<br />
25 2 Style-Nut<br />
26 Strut Rod Assy<br />
31-6<br />
1 Torsion Bar RH<br />
5 Sping Washer<br />
2 Short Mounting Bolt of Torsion Bar Seat<br />
3 Long Mounting Bolt of Torsion Bar Seat<br />
6 Flat Washer<br />
7 Upper Control Arm Assy<br />
31-7<br />
1. CHECK TIRES FOR WEAR AND INFLATION PRESSURE.<br />
For vehicles equipped with 195R15C-106R tires, the front tire pressure is 350 kPa and rear tire pressure is 400<br />
kPa. The allowable variation is ±5 kPa. The maximum of the same axle tires pressure shall not exceed 10 kPa.<br />
2. CHECK TIRES FOR RADIAL RUNOUT ERROR. The quantity of wheel sway is less than 1.2 mm.<br />
3. CHECK FRONT WHEEL BEARING FOR LOOSENESS.<br />
4. CHECK FRONT SUSPENSION PARTS FOR LOOSENESS AND DAMAGE.<br />
5. CHECK STEERING ROD FOR LOOSENESS.<br />
6. CHECK EVERY BALL JOINT FOR TOO LOOSENESS.<br />
7. PERFORM A STANDARD FLEXIBILITY TEST AND CHECK IF SHOCK ABSORBER WORKS NORMALLY<br />
8. MEASURE HEIGHT OF UNLOADED VEHICLE.<br />
(a) Park the vehicle onto an inspection platform and bounce the vehicle to set the suspension system.<br />
Bounce the front bumper for 5~10 times, then keep the bumper in free state. Measure ground<br />
clearance at bumper center. Repeat the steps for another time. The difference between two<br />
measurements should be no more than 10 mm.<br />
(b) For vehicles equipped with 195R15C-106R tires, measure the ground clearance at front center point of<br />
lower arm adjusting bolt (also use a self-made measurable tool to measure height in pit). If the<br />
measured value is not within specified value, adjust the torsion mounting bolt to meet the specified<br />
31-8<br />
FRONT SUSPENSION - FRONT WHEEL ALIGNMENT<br />
1. INSPECT TIRE. (Refer to “Chapter 33 wheel and tire - wheel and tire assy, on-vehicle<br />
inspection”)<br />
2. MEASURE HEIGHT OF WHEELS.<br />
For vehicles equipped with 195R15C-106R tires, measure the ground clearance at front center point of<br />
• Before inspecting the wheel alignment, adjust the vehicle height to meet the specified value and<br />
maintain steering wheel center.<br />
• If the vehicle height is not within the specified value, try to adjust it by pushing down or lifting<br />
the body.<br />
3. INSPECT TOE-IN.<br />
Toe-in (total): 2 ± 2mm (8′ ± 8′)<br />
If toe-in value is out of the specification, adjust toe-in by the left<br />
and right tie rods.<br />
4. ADJUST TOE-IN.<br />
(a) Loosen tie rod lock nut.<br />
(b) Turn the outer tie rod RH/LH by an equal amount to<br />
adjust the toe-in within the specified value.<br />
Measure the length of the left and right tie rod, and make<br />
them in the same length. Length difference between the<br />
right and left tie rod: 3.0 mm or less.<br />
(c) Tighten the tie rod lock nut.<br />
Torque: 40 ~ 50 N·m<br />
5. INSPECT FRONT WHEEL CAMBER, KINGPIN INCLINATION<br />
AND KINGPIN CASTER.<br />
Front wheel camber, kingpin inclination and kingpin caster:<br />
Front Wheel<br />
Camber<br />
Kingpin Inclination<br />
Kingpin Caster<br />
-0°20′±45′ (Difference between left and<br />
right < 30′)<br />
13°05′±45′(Difference between left and<br />
2°35′±45′(Difference between left and<br />
31-9<br />
If the kingpin caster is out of the specified value, adjust it by turing<br />
the strut rod nut.<br />
The range of adjusting bolt from the initial position can be<br />
no more than 3 thread. Rotating one revolution is equal to a<br />
change of approx 30′ in kingpin caster.<br />
6. ADJUST CAMBER.<br />
(a) Adjust the front camber by rotating cam. Each scale of<br />
cam means a 18′ change in camber. It is not allowed to<br />
rotate cam from the center line over 4.5 scales.<br />
31-10<br />
FRONT SUSPENSION - FRONT SHOCK ABSORBER<br />
FRONT SHOCK ABSORBER<br />
1. REMOVE FRONT WHEEL LH ASSY. (Refer to “chapter 33 wheel and tire - front wheel and tire,<br />
2. REMOVE FRONT SHOCK ABSORBER LH.<br />
(a) Remove 1 mounting nuts attaching the front shock<br />
absorber LH to frame.<br />
(b) Remove the mounting bolt attaching front shock<br />
absorber LH to the lower control arm.<br />
(c) Take out the front shock absorber LH.<br />
3. CHECK SHOCK ABSORBER FOR OIL LEAKAGE.<br />
(a) Check shock absorber for oil leakage.if the oil leaks from the shock absorber, replace it with a new one.<br />
4. CHECK SHOCK ABSORBER CONNECTING PARTS.<br />
(a) Check the shock absorber connecting rod, bushing or other connecting parts for damage. If there is any<br />
damage, replace it with a new one.<br />
5. CHECK SHOCK ABSORBER EFFICIENCY.<br />
(a) Compress and extend the shock absorber rod for 2~3 times and then check that there is no abnormal<br />
resistance or unusual noise during operation. If there is any abnormality, replace the shock absorber<br />
31-11<br />
6. INSTALL FRONT SHOCK ABSORBER LH.<br />
Place the shock absorber,tighten the mounting bolt<br />
attaching the shock absorber to the lower control arm.<br />
Be sure to use new nut bolt.<br />
Torque: 80 ~ 100 N•m<br />
Tighten 1 nut attaching front shock absorber LH to frame.<br />
Be sure to use new nut.<br />
Torque: 25 ~ 35 N•m<br />
7. INSPECT AFTER INSTALLATION.<br />
(a) After the vehicle is assembled, drive it on a bad road for a distance about 10 KM and park it, then touch<br />
the surfaces of the two shock absorbers with hands. If difference in temperature of the two shock<br />
absorbers is large, correspondingly, difference in resistance of them is also large and the absorber with<br />
a low temperature has small resistance. If the temperature of the two shock absorbers doesn’t exceed<br />
air temperature, it indicates that the shock absorbers have no resistance and disabled. It is necessary<br />
to replace with a new one.<br />
(b) When the vehicle is running slowly and given an emergent brake, if the vehicle has an excessive<br />
vibration, it indicates that there is a fault on shock absorber. Disassemble and erect the shock absorber,<br />
keep the lower part jointing ring clamping the vise, pull and press the shock absorber rod for several<br />
times. It should have stable resistance,the pull-up (restoration) resistance should be no less than pulldown<br />
resistance. If the resistance is unstable or there is no resistance, the shock absorber may lack of<br />
oil or the valve part is damaged. It is necessary to replace it with a new shock absorber.<br />
(c) The shock absorber may produce noise during use, this is because the shock absorber is crashed with<br />
spring, frame or shaft, rubber washer is damaged or fallen off, and dust wrapper is deformed and oil is<br />
insufficient. It is necessary to find out the root of the fault and replace it.<br />
(d) If it is impossible to conduct a test, we can take some experiential measures to check it: let an iron bar<br />
passing through the lower hoisting ring, step the two ends with feet, hold the hoisting ring and pull up<br />
and down for 2-4 times with hands. If there is large resistance when pulling up and almost no resistance<br />
when pulling down, stretching resistance is restored compared with resistance before repair, and you<br />
don’t feel no-running status, it indicates that the shock absorber is in normal condition.<br />
8. REMOVE AND INSTALL FRONT SHOCK ABSORBER RH.<br />
Remove and install the Front RH side by the same procedures as the Front LH side.<br />
31-12<br />
FRONT SUSPENSION - TORSION BAR<br />
TORSION BAR<br />
1. REMOVE THE FUEL TANK. (Refer to “Chapter 12A fuel - fuel tank assy, replacement”)or(Refer to<br />
“Chapter 12B fuel - fuel tank assy, replacement”)<br />
It is necesary to remove the fuel tank only before removing the torsion bar LH.<br />
2. REMOVE TORSION BAR ASSY LH.<br />
As the illustration shows, measure the length of the<br />
extension bolt end A.<br />
When adjusting the vehicle hight, value A will serve as<br />
reference. At the end of the torsion bar, there are left and<br />
right indicator. Do not install it to opposite direction.<br />
Remove the locking nut and adjustment nut of the torsion<br />
bar LH.<br />
31-13<br />
Remove 2 mounting bolt attaching the torsion bar to the<br />
upper control arm.<br />
Pull out the torsion bar backward.<br />
3. INSTALL TORSION BAR ASSY LH.<br />
Place the torsion bar LH,tighten 2 mounting bolt attaching<br />
the torsion bar to the upper control arm.<br />
扭 矩 :Torque: 110 ~ 120 N•m<br />
Tighten the locking nut and adjustment nut of the torsion<br />
• Tighten adjustment nut of torsion bar LH.<br />
• Tighten locking nut .the length of the extension bolt end<br />
must be the same as the measure value A.<br />
Torque: 120 ~ 130 N•m<br />
31-14<br />
4. INSPECT VEHICLE HEIGHT. IF THE HEIGHT IS OUT OF STANDARD, USE TORSION BAR<br />
ADJUSTING NUT TO ADJUST.<br />
5. REMOVE AND INSTALL TORSION BAR ASSY RH.<br />
Remove and install the RH side by the same procedures as the LH side.<br />
Be careful not to be scalded by hot exhaust pipe.<br />
FRONT SUSPENSION - UPPER CONTROL ARM<br />
31-15<br />
UPPER CONTROL ARM<br />
1. REMOVE FRONT WHEEL ASSY LH. (Refer to “Chapter 33 wheel and tire - front wheel and tire,<br />
2. REMOVE FRONT DISC BRAKE LH. (Refer to “Chapter 35 brake - front disc brake, overhaul”)<br />
3. REMOVE TORSION BAR LH. (Refer to Chapter 31 front suspension - torsion bar, replacement”)<br />
It is not necessary to poll out the torsion bar LH and remove the fuel tank.<br />
4. REMOVE UPPER CONTROL ARM LH.<br />
Remove mounting bracket mounting bolt of front wheel<br />
speed sensor cable.<br />
Remove the cotter pin located at slotted nut.<br />
Removed cotter pin must not be use again.<br />
Removed the slotted nut attaching upper control arm ball<br />
pin to steering knuckle.<br />
Remove 3 bolts attaching upper control arm to frame.<br />
31-16<br />
Take out the upper control arm assy.<br />
5. INSTALL UPPER CONTROL ARM ASSY LH.<br />
(a) Place upper control arm,tighten 3 bolts attaching upper<br />
control arm to frame.<br />
Torque: 170 ~ 200 N•m<br />
Tighten the slotted nut attaching upper control arm ball<br />
Torque: 105 ~ 125 N•m<br />
Install the cotter pin located at slotted nut.<br />
New cotter pin must be used.<br />
Place the mounting bracket of wheel speed sensor<br />
cable,Tighten mounting bolt.<br />
6. INSTALL TORSION BAR LH. (Refer to chapter 31 front suspension - torsion bar, replacement”)<br />
7. INSTALL FRONT DISC BRAKE LH. (Refer to “Chapter 35 brake - front disc brake, overhaul”)<br />
8. INSTALL FRONT WHEEL ASSY LH. (Refer to “Chapter 33 wheel and tire - front wheel and tire,<br />
31-17<br />
9. REMOVE AND INSTALL UPPER CONTROL ARM RH.<br />
10. INSPECT AND ADJUST FRONT WHEEL ALIGNMENT. (Refer to “Chapter 31 front suspension -<br />
front wheel alignment, adjustment”)<br />
31-18<br />
FRONT SUSPENSION - LOWER CONTROL ARM<br />
LOWER CONTROL ARM<br />
3. REMOVE LOWER CONTROL ARM ASSY LH.<br />
(a) Remove bumper block assy.<br />
(b) Remove the mounting bolt attaching atabilizer bar link LH<br />
to lower control arm.<br />
(c) Remove the mounting bolt attaching shock absorber to<br />
lower contrlo bar.<br />
Remove 4 nuts and bolts attaching ball joint seat to lower<br />
control arm.<br />
4 blots including 2 strut rod mounting nuts and bolts.<br />
(e) Remove the mounting nut attaching lower control arm to<br />
subframe.<br />
Take out the lower control arm assy LH carefully.<br />
4. INSTALL LOWER CONTROL ARM ASSY LH.<br />
(a) Place lower control arm.<br />
(b) Tighten the mounting nut attaching lower control arm to<br />
Torque: 180 ~ 220 N•m<br />
(c) Tighten the mounting bolt attaching strud rod and ball<br />
joint seat to lower contrlo arm.<br />
Torque: 100 ~ 120 N•m<br />
(d) Tighten the mounting bolt attaching ball joint seat to<br />
lower control arm.<br />
31-19<br />
Tighten the mounting bolt attaching shock absorber to<br />
TIghten the mounting bolt attaching stabilizer bar link to<br />
Place the lower pumper block assy,tighten 2 mounting<br />
nut at the bottom.<br />
Totque: 40~ 60 N•m<br />
5. INSTALL FRONT DISC BRAKE LH. (Refer to “Chapter 35 brake - front disc brake, overhaul”)<br />
6. INSTALL FRONT WHEEL ASSY LH. (Refer to “Chapter 33 wheel and tire - front wheel and tire,<br />
7. REMOVE AND INSTALL LOWER CONTROL ARM RH.<br />
8. INSPECT AND ADJUST FRONT WHEEL ALIGNMENT. (Refer to “Chapter 31 front suspension -<br />
31-20<br />
FRONT SUSPENSION - STABILIZER BAR<br />
STABILIZER BAR<br />
1. REMOVE STABILIZER BAR.<br />
(a) Remove the mounting bolt attaching stabilizer bar link<br />
ball joint LH to stabilizer bar.<br />
(b) Remove the mounting bolt attaching stabilizer bar link<br />
ball joint RH to stabilizer bar.<br />
Remove 2 mounting bolt attaching stabilizer bar bracket<br />
LH to frame.<br />
RH to frame.<br />
31-21<br />
Take down stabilizer bar carefully.<br />
2. INSPECT STABILIZER BAR BUSHING.<br />
Inspect the stabilizer bar bushing for ageing. If there is any ageing, replace the bushing with new one.<br />
3. INSTALL STABILIZER BAR.<br />
(a) Place stabilizer bar.<br />
(b) Tighten 2 mounting bolt attaching stabilizer bar bracket<br />
Torque: 40 ~ 50 N•m<br />
(c) Tighten 2 mounting bolt attaching stabilizer bar bracket<br />
31-22<br />
Tighten the mounting bolt attaching stabilizer bar link ball<br />
joint LH to stabilizer bar.<br />
joint RH to stabilizer bar.<br />
4. INSPECT AND ADJUST FRONT WHEEL ALIGNMENT. (Refer to “Chapter 31 front suspension -<br />
FRONT SUSPENSION - STRUT ROD<br />
31-23<br />
STRUT ROD<br />
1. REMOVE STRUT ROD LH.<br />
(a) Remove the nut attaching the strut rod LH to the<br />
Using a wrench, lock the head of bolts attaching the strut<br />
rod LH to the lower control arm LH.<br />
Remove the mounting nut attaching the strut rod LH to<br />
the lower control arm LH.<br />
Take out the the strut rod LH.<br />
2. CHECK THE RUBBER BUSHING OF THE STRUT ROD FOR DAMAGE.<br />
31-24<br />
3. INSTALL STRUT ROD LH.<br />
(a) Place strut rod,and install rubber bushing and baffle plate<br />
to strut rod.<br />
(b) Using a wrench,lock the head of bolts attaching the strut<br />
rod to the lower contrlo arm.<br />
Tighten the nut attaching the strut rod to the lower control<br />
arm.<br />
Tighten connecting mounting nut attaching the strut rod<br />
to the subframe.<br />
Torque: 115 ~ 135 N•m<br />
4. REMOVE AND INSTALL STRUT ROD RH.<br />
Remove the RH side by the procedure as the same procedure as the LH side.<br />
5. INSPECT AND ADJUST FRONT WHEEL ALIGNMENT. (Refer to “Chapter 31 front suspension -<br />
REAR SUSPENSION ......................................................................... 32-1<br />
PROBLEM SYMPTOMS TABLE.................................................. 32-1<br />
COMPONENTS ........................................................................... 32-2<br />
ON-VEHICLE INSPECTION ........................................................ 32-3<br />
REAR SHOCK ABSORBER .............................................................. 32-4<br />
OVERHAUL ................................................................................. 32-4<br />
REAR LEAF SPRING ASSY.............................................................. 32-6<br />
OVERHAUL ................................................................................. 32-6<br />
REAR SUSPENSION - REAR SUSPENSION<br />
32-1<br />
likely cause of the problem. Check each part in order. If necessary, replace these parts.<br />
Shock absorber oil leakage<br />
3. Shock absorber (Failure) Chapter 32 rear suspension - rear shock<br />
absorber, overhaul<br />
1. Shock absorber (Failure) Chapter 32 rear suspension - rear shock<br />
Suspension noise<br />
2. Leaf spring (Worn or damaged) Chapter 32 rear suspension - rear leaf<br />
spring, overhaul<br />
3. Bushing (Worn or damaged) Chapter 32 rear suspension - rear leaf<br />
4. Shock absorber and leaf spring<br />
mounting bolt (Loosen or<br />
Chapter 32 rear suspension - rear shock<br />
Abnomal rear tire wear,<br />
vehicle deviation<br />
1. Leaf spring pin (Over worn) Chapter 32 rear suspension - rear leaf<br />
2. U-bolt (Worn or damaged) Chapter 32 rear suspension - rear leaf<br />
3. Leaf spring (Elastic decline or<br />
stiffness inconsistent)<br />
Chapter 32 rear suspension - rear leaf<br />
4. Leaf spring (Broken) Chapter 32 rear suspension - rear leaf<br />
1. Tire (Worn or improperly<br />
inflated)<br />
Chapter 33 wheel and tire - wheel and tire<br />
assy, on-vehicle inspection<br />
2. Wheel (Out of balance) Chapter 33 wheel and tire - wheel and tire<br />
assy, adjustment<br />
32-2<br />
1 Rear Leaf Spring Assy<br />
Leaf Spring Shackle Outer Plate Welded<br />
Assy<br />
3 Leaf Spring Shackle Inner Bushing<br />
4 Leaf Spring Shackle Inner Plate<br />
5 Spring Washer<br />
6 Leaf Spring Pin Nut<br />
7 Rear Damping Block Assy<br />
8 Spring Washer<br />
10 U-bolt<br />
11 Leaf Spring Mounting Plate Welded Assy<br />
12 Rear Shock Absorber Assy<br />
13 Spring Washer<br />
15 Leaf Spring Pin Shaft<br />
16 Spring Washer<br />
9 Bolt<br />
32-3<br />
1. ON-VEHICLE INSPECTION<br />
(a) Check shock absorber for oil leakage.<br />
(b) Check shock absorber ring rubber bushing for aging, cracking, deforming. Replace it if necessary.<br />
(c) Leaf spring shackle bushing, every leaf spring pin should be replaced frequently.<br />
(d) Check U-bolt for cracking, flaw, thread for damage. replace it if necessary.<br />
(e) U-bolt should be tightened in uniform cross tightened method and step by step tight U-bolt to specified<br />
value. Tighten the U-bolts again when the leaf spring laminating closely with the car full loaded. In some<br />
cases that leaf springs can not be compacted because of the bolts and nuts being rusted. Replace it<br />
with the new U-bolts and nuts if necessary.<br />
(f) For slide-type leaf spring, a layer of lubricating grease should be applied between the leaf spring and<br />
shackle bracket to reduce the wear and tear of the slide-type leaf spring.<br />
32-4<br />
REAR SUSPENSION - REAR SHOCK ABSORBER<br />
REAR SHOCK ABSORBER<br />
1. REMOVE SHOCK ABSORBER RL.<br />
(a) Remove the lower mounting bolt for the shock absorber<br />
RL.<br />
Remove the upper mounting bolt for the shock absorber<br />
Take out the shock absorber RL with caution.<br />
2. CHECK SHOCK ABSORBER FOR OIL LEAKAGE.<br />
(a) Check the shock absorber for oil leakage,If the oil leaks from the shock absorber, replace it with a new<br />
3. CHECK SHOCK ABSORBER CONNECTING PARTS.<br />
(a) Check the shock absorber connecting rod ,rubber bushing or others for damage,replace it with a new<br />
one if necessary.<br />
4. CHECK SHOCK ABSORBER EFFICIENCY.<br />
(a) Compress and extend the shock absorber rod and then check that there is no abnormal resistance or<br />
unusual noise during operation. If there is any abnormality, replace the shock absorber with a new one.<br />
5. INSTALL SHOCK ABSORBER RL.<br />
(a) Place shock absorber RL.<br />
(b) Tighten the upper mounting bolt for the shock absorber<br />
Torqre: 55 ~ 65 N·m<br />
32-5<br />
Tighten the lower mounting bolt for the shock absorber<br />
Torqre: 60 ~ 80 N·m<br />
6. REMOVE AND INSTALL REAR SHOCK ABSORBER RH.<br />
Remove and install the REAR RH side by the same procedures as the REAR LH side.<br />
(a) After installation,drive it on a bad road for a distance about 10 KM and park it, then touch the surfaces<br />
of the two shock absorbers with hands. If difference in temperature of the two shock absorbers is large,<br />
correspondingly, difference in resistance of them is also large and the absorber with a low temperature<br />
has small resistance. If the temperature of the two shock absorbers doesn’t exceed air temperature, it<br />
indicates that the shock absorbers have no resistance and disabled. It is necessary to replace with a<br />
new one.<br />
insufficient. It is necessary to find out the root of the fault and repair it.<br />
32-6<br />
REAR SUSPENSION - REAR LEAF SPRING ASSY<br />
REAR LEAF SPRING ASSY<br />
1. REMOVE REAR SHOCK ABSORBER LH. (Refer to “Chapter 32 rear suspension - rear shock<br />
2. REMOVE REAR LEAF SPRING ASSY LH.<br />
Using proper jacks, withstand the center of the rear leaf spring.<br />
Remove bolts for the Parking Brake cable fixed shelf.<br />
Remove 4 U-bolts and nuts.<br />
Before removing the nuts,suport the rear axle with lifting<br />
jack.<br />
Lowering the jack which holds the leaf spring slowly,remove<br />
the U-bolts and rear leaf spring anchor plate.Check U-<br />
bolts,if there are any damaages such as deformation and<br />
flaw ,replace it in time.<br />
Remove the mounting nut which install the front leaf<br />
spring axis pin to the frame.<br />
Remove upper mounting nut of leaf spring shackle pin.<br />
32-7<br />
Remove lower mounting nut of leaf spring shackle pin.<br />
Remove shackle inner&outer plates and shackle pin.<br />
Remove rear leaf spring LH with caution.<br />
3. CHECK LEAF SPRING FOR AGING, FLAW AND SERIOUS RUSTING. IF THERE IS ANY ONE,<br />
REPLACE IT WITH A NEW ASSEMBLY.<br />
4. CHECK SHACKLE BUSHING OF LEAFING SPRING FOR WEARING,AGING ,DAMAGE.IF THERE<br />
IS ANY ONE ,REPLACE IT WITH A NEW ONE.<br />
5. CHECK LEAF SPRING ARCH HEIGHT, H = 128 ± 5 mm,Replace new leaf spring if necessary.<br />
• The defference value of left and right sagitta should not be more than 5 mm, or it will cause<br />
body sway.<br />
• The new spring leaf must be as same as the other side (both leaf springs ara “+”or”-”at the<br />
same time).<br />
6. INSTALL REAR LEAF SPING ASSY LH.<br />
Install shackle inner&outer plates and shackle pin.<br />
Tighten upper mounting nut of leaf spring shackle pin.<br />
Torque: 105 ~ 125 N·m<br />
Tighten lower mounting nut of leaf spring shackle pin.<br />
32-8<br />
Tighten the mounting nut which install the front leaf<br />
Torque: 110 ~ 120 N·m<br />
Lift the center of rear leaf spring LH with jack<br />
slowly, make U-bolts cross the rear leaf spring boltholes<br />
and tighten the nuts with hand.<br />
Tighten the U-bolt nuts.<br />
Torque: 85~ 105 N·m<br />
Tighten bolts for the Parking Brake cable fixed shelf.<br />
Move the jack and lifting jack.<br />
7. INSTALL REAR SHOCK ABSORBER LH. (Refer to “Chapter 32 rear suspension - rear shock<br />
absorber, overhaul”).<br />
8. TIGHTEN U-BOLTS NUTS AGAIN AFTER DRIVING 3 ~ 5 KM.<br />
9. REMOVE AND INATALL REAR LEAF SPRING ASSY RH.<br />
TYRE AND WHEEL<br />
TIRE AND WHEEL ASSY .................................................................. 33-1<br />
PRECAUTION.............................................................................. 33-1<br />
COMPONENTS ........................................................................... 33-2<br />
PROBLEM SYMPTOMS TABLE.................................................. 33-3<br />
ON-VEHICLE INSPECTION ........................................................ 33-4<br />
ADJUSTMENT............................................................................. 33-7<br />
FRONT WHEEL AND TIRE................................................................ 33-8<br />
REPLACEMENT .......................................................................... 33-8<br />
REAR WHEEL AND TIRE.................................................................. 33-9<br />
REPLACEMENT .......................................................................... 33-9<br />
TIRE AND WHEEL ASSY<br />
WHEEL AND TIRE<br />
1. TIRE AND WHEEL ASSY PRECAUTION<br />
WHEEL AND TIRE - TIRE AND WHEEL ASSY<br />
Use special tools to remove the tires. Do not remove them by huge hammers or sharp tools.<br />
33-1<br />
Do not use tires with different types, sizes, tread patterns, pressure and load index on the same axle.<br />
Please pay attention to the mark of rolling direction when installing directional tread pattern tires.<br />
Must swap each tire once after runing 5000 ~ 6000 km, make each tire wear well evenly.<br />
After swaping tires, reset proper inflation pressure according to the tire position.<br />
Operate inflation according to this manual’s specification, and measure tire pressure at cold state by<br />
tire gauge. Before inflating, check the tire valve whether matching valve core flatly and then clean the<br />
dirt. Inflating air is not allowed to contain water and oil. After inflating, tighten the tire valve core, and<br />
check the tire leakage.<br />
Check inflation pressure according to the standard service data. The tire pressure must be within the<br />
specified value.<br />
Regularly check front wheel toe-in to avoid unnecessary increased resistance of running, fuel<br />
consumption and excessive tire wear.<br />
33-2<br />
1 Tire<br />
2 Wheel Rim<br />
3 Tubeless Tire Valve<br />
4 Wheel Hub Nut<br />
5 Axle Cover<br />
33-3<br />
Symptom Suspect Area Suspect Area<br />
1. Wheel toe-in (Improper value)<br />
Chapter 31 front suspension - front wheel<br />
alignment, adjustment<br />
2. Tire ( Improperly inflated) Chapter 33 wheel and tire - wheel and tire<br />
3. Wheel (Out of balance) Chapter 33 wheel and tire - wheel and tire<br />
4. Steering system (Distortion) Chapter 51 steering system - steering box,<br />
1. Front wheel (Different tire<br />
pressure)<br />
Front wheel swing or vibration<br />
3. Shock absorber (Wear or fault) Chapter 31 front suspension - front shock<br />
4. Steering system (Over Wear)<br />
Chapter 51 steering system - steering box,<br />
Uncomfortableness when<br />
running<br />
1. Tire (Exceed specified pressure) Chapter 33 wheel and tire - wheel and tire<br />
2. Shock absorber (Failure)<br />
Chapter 31 front suspension - front shock<br />
3. Coil Spring (Failure) Chapter 31 front suspension - torsion bar,<br />
spring assy, overhaul<br />
Front wheel side slipping<br />
1. Wheel toe-in (It is not within<br />
specified value)<br />
2. Tire (Inflating pressure is not<br />
within specified value)<br />
33-4<br />
1. MEASURE TIRE TREAD DEPTH.<br />
Depth ≥ 1.6 mm<br />
If the tire tread depth is less than 1.6 mm, replace it with a new one.<br />
Replace a pair of tires at the both wheel side.<br />
2. CHECK TIRES ABNORMAL WEAR.<br />
(a) Visually inspect the tires shoulder wear. If the tire wears,<br />
measure the inflation pressure. Inflate and swap the<br />
wheel if tire pressure is lower or overload.<br />
Visually inspect the wear tires at center. If the tire wears,<br />
release extra pressure and swap the wheel assy.<br />
33-5<br />
Visually inspect the tire inner edge (shoulder) wear. The<br />
inner Edge (shoulder) wear is usually caused by excessive<br />
toe-out and/or excessive negative camber, suspension<br />
parts loose. Avoid turning at high speed. Swap the wheel<br />
assy after adjustment.<br />
Visually inspect the tire outer edge (shoulder ) wear. The<br />
outer edge (shoulder) wear is usually caused by excessive<br />
toe-in and/or excessive positive camber, suspension parts<br />
loose. Avoid turning at high spped. Swap the wheel assy<br />
after adjustment.<br />
Visually inspect the tire feathering wear that occurs along<br />
both inside and outside shoulder ribs. This kind of wear<br />
is usually caused by abnomal toe-in. Check/adjust the<br />
wheel alignment and Swap the wheel assy.<br />
33-6<br />
Visually inspect the tire corrugate wear. This kind of wear<br />
is caused by improper inflation pressure, wheel out of<br />
balance, hub bearing loose or worn and rim deformation.<br />
Swap the wheel assy after adjustment.<br />
3. MEASURE COLD TIRE INFLATION PRESSURE.<br />
Tire Specification Front wheel Rear wheel Spare tire<br />
195R15C-106R 350 kPa 400 kPa 420 kPa<br />
If tire size or inflation pressure doesn’t match standard service data, adjust or replace it with a new wheel as<br />
4. INSPECT TIRE CROWN, TIRE SHOULDER, TIRE EDGE.<br />
Replace the tire with a new one, if bent, cut, cracked, dented, deformation and abrasion exists.<br />
5. INSPECT TIRE VALVE.<br />
If air leaks from tire valve, replace it with a new one.<br />
6. INSPECT RIM.<br />
Replace the rim with a new one If it is found deformation, corrosion and crack.<br />
7. INSPECT WHELL NUTS.<br />
Check the tightening torque one by one according to the standard service data.<br />
33-7<br />
1. TIRE SWAP.<br />
Illustration arrow shows the driving direction o.<br />
Illustration A is cross swap every tire with spare tire.<br />
Illustration B is cross swap every tire without spare tire.<br />
2. WHEEL ASSEMBLY OF THE DYNAMIC BALANCE.<br />
Clean dirt, stones and used balance weights from measured<br />
wheel.<br />
Measure tire pressure and inflate as recommended.<br />
Select the match cone based on size of rim center hole<br />
to tighten by fast nut.<br />
Turn on the balance tester power.<br />
Measure rim width.<br />
Measure tire diameter.<br />
Measure the distance between the rim edge and the<br />
balance tester.<br />
Pull off wheel protect cover and then start test.<br />
After test completed, fix balance weights based on<br />
measurement result.<br />
Repeat aforementioned procedure, adjust till the data to<br />
match specification.<br />
Demount wheel assy.<br />
3. FRONT WHEEL TOE-IN. (Refer to Chapter 31 front suspention - front wheel alignment ,<br />
adjustment )<br />
4. TIRE REPAIR SHOULD BE PERFORMED IN COMPLIANCE WITH LOCAL REGULATIONS.<br />
33-8<br />
WHEEL AND TIRE - FRONT WHEEL AND TIRE<br />
FRONT WHEEL AND TIRE<br />
1. LIFT VEHICLE.<br />
2. REMOVE LH FRONT WHEEL.<br />
Remove 6 hub nuts of LH front wheel.<br />
Undo all front hub nuts diagonally.<br />
Remove LH front wheel.<br />
3. INSTALL LH FRONT WHEEL.<br />
Replace LH front wheel.<br />
Tighten 6 hub nuts of LH front wheel.<br />
Toque: 100 ~ 120 N·m<br />
Tighten all front hub nuts diagonally.<br />
4. REMOVE AND INSTALL RH FRONT WHEEL.<br />
Remove and install the wheel FRONT RH by the same procedures as the LH front wheel.<br />
WHEEL AND TIRE - REAR WHEEL AND TIRE<br />
33-9<br />
REAR WHEEL AND TIRE<br />
2. APPLY PARKING BRAKE.<br />
3. REMOVE LH REAR WHEEL.<br />
(a) Remove 6 hub nuts of LH rear wheel.<br />
Loosen all front wheel nuts diagonally.<br />
Remove LH rear wheel.<br />
4. INSTALL LH REAR WHEEL.<br />
Replace LH rear wheel.<br />
Tighten 6 hub nuts of LH rear wheel.<br />
Torque: 100 ~ 120 N·m<br />
5. REMOVE AND INSTALL RH REAR WHEEL.<br />
Remove and install the RH rear wheel by the same procedures as the LH rear wheel.<br />
6. LOWER VEHICLE.<br />
PROPELLER SHAFT ASSY .............................................................. 34-1<br />
PRECAUTION.............................................................................. 34-1<br />
PROBLEM SYMPTOMS TABLE.................................................. 34-2<br />
COMPONENTS ........................................................................... 34-3<br />
INSPECTION ............................................................................... 34-4<br />
OVERHAUL ................................................................................. 34-5<br />
U-JOINT ............................................................................................. 34-8<br />
OVERHAUL ................................................................................. 34-8<br />
CENTER SUPPORT BEARING ....................................................... 34-12<br />
OVERHAUL ............................................................................... 34-12<br />
AXLE HUB AND STEERING KNUCKLE......................................... 34-16<br />
PROBLEM SYMPTOMS TABLE................................................ 34-16<br />
ON-VEHICLE INSPECTION ...................................................... 34-18<br />
FRONT HUB..................................................................................... 34-20<br />
OVERHAUL ............................................................................... 34-20<br />
REAR AXLE HUB ............................................................................ 34-24<br />
OVERHAUL ............................................................................... 34-24<br />
STEERING KNUCKLE..................................................................... 34-28<br />
OVERHAUL ............................................................................... 34-28<br />
REAR AXLE ..................................................................................... 34-34<br />
PRECAUTION............................................................................ 34-34<br />
PROBLEM SYMPTOMS TABLE................................................ 34-36<br />
ON-VEHICLE INSPECTION ...................................................... 34-37<br />
FINAL DRIVE OIL ............................................................................ 34-40<br />
REPLACEMENT ........................................................................ 34-40<br />
AXLE SHAFT ASSY......................................................................... 34-43<br />
OVERHAUL ............................................................................... 34-43<br />
REAR AXLE HOUSING WELDING ASSY....................................... 34-44<br />
OVERHAUL ............................................................................... 34-44<br />
DRIVE PINION ................................................................................. 34-50<br />
INSPECTION ............................................................................. 34-50<br />
AXLE AND PROPELLER SHAFT - PROPELLER SHAFT ASSY<br />
PROPELLER SHAFT ASSY<br />
34-1<br />
1. PROPELLER SHAFT ASSY PRECAUTION<br />
(a) Do not disassemble the propeller shaft assy unless absolutely necessary.<br />
(b) If disassembly of propeller shaft assy is required, be sure to clean all separated parts before assembly.<br />
(c) After disassembling of propeller shaft assy, be sure to check all separated parts one by one and<br />
perform repairing or replacing when necessary.<br />
34-2<br />
1. Propeller shaft assy (Loose)<br />
Chapter 34 axle and propeller shaft - propeller<br />
2. Lubrication (Insufficient) -<br />
Abnormal noise of<br />
propeller shaft assy<br />
Propeller shaft assy<br />
vibration<br />
3. U-joint (Worn or damaged)<br />
4. Center support bearing (Worn or<br />
5. Slip spline (Worn)<br />
2. U-joint yoke (Incorrect installation)<br />
3. Propeller shaft assy (Bent or<br />
twisted)<br />
4. Propeller shaft assy (Unbalanced)<br />
5. Center support bearing rubber<br />
grommet (Aging or damaged)<br />
6. Center suppor bearing (Worn or<br />
Chapter 34 axle and propeller shaft - U-joint,<br />
Chapter 34 axle and propeller shaft - center<br />
support bearing, overhaul<br />
shaft assy, inspection<br />
Center support<br />
bearing overheat<br />
1. Center support with rubber<br />
grommet (Incorrect installation)<br />
3. Oil seal (Too tight)<br />
34-3<br />
1 Propeller Shaft Assy<br />
Bolt , Spring Washer and Flat Washer<br />
Set<br />
5 Propeller Shaft Nut<br />
3 Propeller Shaft Bolt<br />
34-4<br />
1. INSPECT VIBRATION OF POWERTRAIN.<br />
(a) Check front wheels for dynamic balance. (Refer to “Chapter 33 wheel and tire - wheel and tire assy,<br />
adjustment”)<br />
(b) Check rear wheels for dynamic balance. (Refer to “Chapter 33 wheel and tire - wheel and tire assy,<br />
(c) Perform the road test. Check the powertrain for vibration when vehicle is moving or stops.<br />
2. INSPECT PROPELLER SHAFT ASSY DIAMETER RUNOUT.<br />
(a) Using V-block and dial indicator, measure the diameter<br />
runout of propeller shaft assy.<br />
Limit: ≤ 0.5 mm<br />
If the diameter runout is out of the specification, correct the<br />
propeller shaft assy using press machine. If the diameter runout<br />
is still out of the specification after correction, replace with a new<br />
propeller shaft assy. (Chapter 34 axle and propeller shaft -<br />
propeller shaft assy, overhaul)<br />
3. INSPECT PROPELLER SHAFT ASSY DYNAMIC BALANCE.<br />
(a) Using dynamic balancer, check the propeller shaft assy.<br />
Dynamic unbalance: ≤ 20 g.cm ( 3200 r/min)<br />
If the dynamic unbalance is out of the specification, weld balance<br />
weight at the corresponding position on the both ends of propeller<br />
shaft assy.<br />
• It is no more than 3 balance weight at each end if welding.<br />
• Perform step (a) again to check whether dynamic<br />
unbalance is within the specification.<br />
4. INSPECT SLIP SPLINE CLEARANCE.<br />
(a) Using feeler gauge, measure the tangential clearance<br />
between sleeve yoke and spline on transmission output<br />
Standard: 0.15 mm<br />
Limit: 0.3 mm<br />
If the clearance is out of the specification, replace with a new<br />
propeller shaft assy. (Refer to “Chapter 34 axle and propeller<br />
shaft - propeller shaft assy, overhaul”)<br />
34-5<br />
1. PRECAUTION. (Refer to “Chapter 34 axle and propeller shaft - propeller shaft assy, precaution”)<br />
2. REMOVE PROPELLER SHAFT ASSY.<br />
(a) Mark on the front propeller shaft U-joint and transmission<br />
dust-proof cover.<br />
Make sure the marks are clear.<br />
Mark on the rear propeller shaft U-joint and final drive<br />
flange.<br />
Remove the 4 sets of nuts and bolts attaching propeller<br />
shaft to final drive flange.<br />
Discard the removed nuts and bolts.<br />
Lower the propeller shaft and set it aside.<br />
When performing this operation, another operator who holds the<br />
propeller shaft up is required.<br />
34-6<br />
Remove the 2 bolts fixing center suport bearing bracket.<br />
• Discard the removed bolts.<br />
• When performing this operation, another operator who<br />
holds the propeller shaft up is required.<br />
Lower the center support with rubber grommet.<br />
Pull out the sleeve yoke from transmission dust-proof<br />
cover and remove the propeller shaft assy.<br />
Be sure to save the propeller assy carefully.<br />
3. INSPECT PROPELLER SHAFT ASSY. (Refer to “Chapter 34 axle and propeller shaft - propeller<br />
shaft assy, inspection”)<br />
4. INSPECT U-JOINT. (Refer to “Chapter 34 axle and propeller shaft - U-joint, overhaul”)<br />
5. INSTALL PROPELLER SHAFT ASSY.<br />
(a) Insert the sleeve yoke into transmission dust-proof cover<br />
according to the marks.<br />
• Before assembly, internal and external spline should<br />
be applied with car general lithium grease.<br />
• Be sure to perform this operation according to the<br />
marks.<br />
34-7<br />
Position the center support with rubber grommet properly<br />
Tighten the 2 bolts fixing center suport bearing bracket.<br />
Torque: 60 ~ 70 N•m.<br />
• Be sure to use new bolts.<br />
Position the propeller shaft properly according to the marks.<br />
• Align the marks by rotating the pinion flange when<br />
Install the 4 sets of nuts and bolts attaching propeller<br />
Torque: 70 ~ 79 N·m<br />
Be sure to use new nuts and bolts.<br />
34-8<br />
AXLE AND PROPELLER SHAFT - U-JOINT<br />
2. REMOVE PROPELLER SHAFT ASSY. (Refer to “Chapter 34 axle and propeller shaft - propeller<br />
shaft assy, overhaul”)<br />
3. DISASSEMBLE MIDDLE U-JOINT OF PROPELLER<br />
SHAFT ASSY.<br />
(a) Mark on the end yoke, cross spider and tube yoke.<br />
Using snap ring pliers, remove the 4 snap rings.<br />
Discard the removed snap rings.<br />
Using copper rod and hammer, remove the round<br />
Do not hammer the round bearing and do not clamp the<br />
propeller shaft with vice directly.<br />
34-9<br />
Remove the 4 round bearings and the 4 dust-proof<br />
covers.<br />
Discard the removed dust-proof cover.<br />
(e) Remove the cross spider.<br />
(f) Separate the end yoke from tube yoke.<br />
4. DISASSEMBLE FRONT U-JOINT OF PROPELLER SHAFT ASSY.<br />
Disassemble the front U-joint by the same procedures as the middle U-joint.<br />
5. DISASSEMBLE REAR U-JOINT OF PROPELLER SHAFT ASSY.<br />
Disassemble the rear U-joint by the same procedures as the middle U-joint.<br />
6. INSPECT CROSS SPIDER.<br />
(a) Check the cross spider for wear and tear.<br />
Cross spider doesn’t need maintenance, has no grease mouth, and should be rotated flexibly.<br />
(b) Using the micrometer caliper, measure the cross spider<br />
journal.<br />
Standard: 16.3 mm<br />
Limit: 16.248 mm<br />
If the cross spider is excessively worn, replace with a new part.<br />
(c) Using the dial indicator, measure the clearance between<br />
round bearing and yoke.<br />
Clearance: 0 mm (Interference fit)<br />
If clearance exits, replace with new round bearing and yoke.<br />
Insert the round bearing into yoke. Measure the clearance<br />
by shaking bearing along radial direction lightly.<br />
34-10<br />
(d) Using the vice and the dial indicator, measure the radial<br />
clearance between round bearing and cross spider.<br />
Radial clearance: 0.01 ~ 0.055 mm<br />
If the radial clearance is out of the specification, replace with<br />
new round bearing and cross spider.<br />
Wrap the cross spider with rag to prevent the spider that is<br />
clamped by vice from being damaged.<br />
Hitch the cross spider with round bearing. Measure the<br />
radial clearance by shaking bearing along radial direction<br />
lightly.<br />
(e) Using dial indicator, measure the axial clearance<br />
between round bearing and cross spider.<br />
Axial clearance: 0.01 ~ 0.055 mm<br />
If the axial clearance is out of the specification, replace with new<br />
round bearing and cross spider.<br />
axialclearance by shaking bearing along axial direction<br />
7. ASSEMBLE MIDDLE U-JOINT OF PROPELLER SHAFT ASSY.<br />
(a) Apply the grease on the mating surfaces of cross spider and round bearing.<br />
Grease: lithium base grease No.2<br />
• Only apply the grease on the mating surface of cross spider and round bearing.<br />
• If the applying grease is excessive, it will cause problem for further operations.<br />
(b) Position the end yoke and tube yoke properly according<br />
to the marks.<br />
(c) Install the 4 round bearings and the 4 dust-proof covers<br />
at ouside of yoke.<br />
(d) Install the cross spider at inside of yoke.<br />
(e) Using the copper rod and the hammer, install the 4 round<br />
bearings and the 4 dust-proof covers properly.<br />
• Be sure to use new dust-proof covers.<br />
34-11<br />
Using snap ring pliers, install the 4 snap rings.<br />
Be sure to use new snap rings.<br />
8. ASSEMBLE FRONT U-JOINT OF PROPELLER SHAFT ASSY.<br />
Reassemble the front U-joint by the same procedures as the middle U-joint.<br />
9. ASSEMBLE REAR U-JOINT OF PROPELLER SHAFT ASSY.<br />
Reassemble the rear U-joint by the same procedures as the middle U-joint.<br />
10. INSTALL PROPELLER SHAFT ASSY. (Refer to “Chapter 34 axle and propeller shaft - propeller<br />
34-12<br />
AXLE AND PROPELLER SHAFT - CENTER SUPPORT BEARING<br />
3. DISASSEMBLE MIDDLE U-JOINT OF PROPELLER SHAFT ASSY. (Refer to “Chapter 34 axle and<br />
propeller shaft - U-joint, overhaul”)<br />
4. REMOVE END YOKE.<br />
(a) Remove the nut.<br />
Discard the removed nut.<br />
Remove the flat washer.<br />
Mark on the end yoke and spline.<br />
• Make sure the marks are clear.<br />
• Make sure the yoke direction of U-joint is consistent.<br />
Using a puller, remove the end yoke.<br />
34-13<br />
5. REMOVE CENTER SUPPORT WITH RUBBER GROMMET<br />
Do not damage the rubber grommet.<br />
6. REMOVE CENTER SUPPORT BEARING.<br />
(a) Using a puller, remove the center support bearing assy.<br />
Remove the 2 oil seals on both side.<br />
Discard the removed oil seals.<br />
Using hammer and copper rod, remove the center<br />
support bearing from bearing cup.<br />
7. INSPECT CENTER SUPPORT BEARING.<br />
(a) Check whether the center support bearing can be rotated freely.<br />
(b) Check whether the center support bearing is worn excessively.<br />
(c) If any fault is found, replace with a new part.<br />
8. INSTALL CENTER SUPPORT BEARING ASSY.<br />
(a) Apply the grease on the center support bearing and bearing cup.<br />
34-14<br />
Using hammer and copper rod, install the center support<br />
bearing to bearing cup.<br />
Apply the grease on the oil seal lip.<br />
Be sure to use new oil seals.<br />
Install the 2 oil seals on both side.<br />
Install the center support bearing assy with hammer and<br />
copper rod.<br />
9. INSTALL CENTER SUPPORT WITH RUBBER GROMMET<br />
Do not damage the rubber grommet during operation.<br />
10. INSTALL END YOKE.<br />
(a) Position the end yoke properly according to the marks.<br />
34-15<br />
Install the flat washer.<br />
Tighten the nut.<br />
Be sure to use a new nut.<br />
11. INSPECT CENTER SUPPORT BEARING.<br />
(a) Check whether the center support with rubber grommet can be rotated freely without deviation when<br />
rotating it by hands.<br />
(b) Replace with new center support bearing, bearing cup and support with rubber grommet assy if<br />
12. ASSEMBLE MIDDLE U-JOINT OF PROPELLER SHAFT ASSY. (Refer to “Chapter 34 axle and<br />
13. INSTALL PROPELLER SHAFT ASSY. (Refer to “Chapter 34 axle and propeller shaft - propeller<br />
34-16<br />
AXLE AND PROPELLER SHAFT - AXLE HUB AND STEERING KNUCKLE<br />
AXLE HUB AND STEERING KNUCKLE<br />
See the table below to help you find the cause of the problem. The numbers indicate the priority of the likely<br />
Wandering / Pulling<br />
1. Tire type (Incorrect)<br />
2. Tire (Worn)<br />
3. Tire pressure (Incorrect)<br />
5. Axle hub bearing (Worn)<br />
6. Front shock absorber<br />
(Damaged)<br />
7. Suspension (Loose or<br />
Chapter 34 axle and propeller shaft - axle hub and<br />
8. Steering tie rod (Loose or worn) Chapter 52 power steering - steering box, overhaul<br />
Wheel vibration<br />
9. Stabilizer bar (Bent or fractured)<br />
1. Wheel (Unbalanced or worn<br />
excessively)<br />
2. Axle hub bearing (Worn)<br />
4. B-joint (Worn)<br />
Chapter 32 rear suspension - rear shock absorber,<br />
Chapter 34 axle and propeller shaft - steering<br />
knuckle, overhaul<br />
5. Steering tie rod (Loose or worn) Chapter 52 power steering - steering box, overhaul<br />
6. Steering box (Damaged) Chapter 52 power steering - steering box, overhaul<br />
34-17<br />
1. Power steering fluid level (Low)<br />
2. Steering knuckle (Worn)<br />
Chapter 52 power steering - power steering system,<br />
on-vehicle inspection<br />
Chapter 52 power steering - steering<br />
fluid,replacement<br />
Abnormal noise<br />
3. Steering propeller shaft (Worn)<br />
4. Power steering pump (Worn or<br />
Chapter 52 power steering - power steering pump<br />
5. Steering box (Damaged) Chapter 52 power steering - steering box, overhaul<br />
34-18<br />
1. INSPECT FRONT AXLE HUB BEARING.<br />
Remove the front wheel assy. (Refer to “Chapter 33 wheel and tire - front wheel and tire, replacement”)<br />
Remove the front disk brake caliper assy. (Refer to “Chapter 35 brake - front brake, overhaul”)<br />
Open the lock-edge, loosen retaining snap ring.<br />
Be sure to take care to operate,don’t destroy retaining snap<br />
ring.<br />
Use special tool to loosen retaining snap ring.<br />
(d) Remove oil seal.<br />
Discard the removed oil seal.<br />
(e) Using dial indicator, measure the back lash around the<br />
center of front axle hub.<br />
Back lash: ≤ 0.2 mm<br />
If the back lash is out of the specification, replace with new front<br />
axle hub bearings.<br />
• Measure the back lash by shaking the front axle hub<br />
along the axial direction lightly.<br />
• When performing the measurment, make the dial<br />
indicator be close to the center of axle hub.<br />
(f) Using dial indicator, measure the deviation at the edge of<br />
front axle hub.<br />
Deviation: ≤ 0.2 mm<br />
If the deviation is out of the specification, replace with a new<br />
• Measure the deviation by rotating the front axle hub<br />
slowly.<br />
• When performing the measurement, make the dial<br />
indicator be close to the edge of axle hub.<br />
34-19<br />
Install oil seal.<br />
Be sure to use new oil seal.<br />
(h) Tighten retaining snap ring of hub bearing,lock the retaining<br />
Don’t destroy the retaining snap ring<br />
(i) Install the front disk brake.. (Refer to “Chapter 35 brake -<br />
front brake, overhaul”)<br />
(j) Install the front wheel assy. (Refer to “Chapter 33 wheel<br />
and tire - front wheel and tire, replacement”)<br />
2. INSPECT REAR AXLE HUB BEARING.<br />
Check rear axle hub bearing when removed.<br />
34-20<br />
AXLE AND PROPELLER SHAFT - FRONT HUB<br />
FRONT HUB<br />
1. REMOVE THE FRONT WHEEL ASSY LH. (Refer to “Chapter 33 wheel and tire - front wheel and<br />
tire, replacement”)<br />
2. REMOVE THE FRONT DISK BRAKE CALIPER ASSY LH. (Refer to “Chapter 35 brake - front<br />
brake, overhaul”)<br />
3. REMOVE FRONT HUB LH.<br />
(a) Open the lock-edge, loosen retaining snap ring.<br />
Be sure to take care to operate, don’t destroy retaining<br />
Remove tone wheel.<br />
34-21<br />
Remove internal hub bearing and oil seal of front hub,<br />
wash and inspect internal hub bearing, if necessary,<br />
Discard the removed internal bearing oil seal.<br />
(d) Remove retaining plate.<br />
(e) Remove external hub bearing, wash and inspect it, if<br />
necessary, replace it.<br />
Rear axle hub LH and axle shaft is an assy.<br />
4. INSTALL FRONT HUB LH.<br />
(a) Apply grease on steering knuckle LH.<br />
• Be sure to use Alvania - RL3 grease.<br />
• Apply the grease to the entire surface of steering knuckle LH.<br />
Install external bearing.<br />
Fill the grease into the bearings for more than 1/2.<br />
(c) Install retaining plate.<br />
(d) Apply grease to inside of retaining plate.<br />
• The total amount of grease is 14 ~ 16 gram.<br />
(e) Install external bearing.<br />
34-22<br />
(f) Fill the grease into the bearings for more than 1/2.<br />
LH along the axial direction lightly.<br />
indicator be close the center of axle hub.<br />
(h) Install tone wheel.<br />
Tighten retaining snap ring of hub bearing.<br />
Don’t destroy retaining snap ring.<br />
Install the front disk brake caliper assy LH. (Refer to<br />
“Chapter 35 brake - front brake, overhaul”)<br />
34-23<br />
(k) Using dial indicator, measure the deviation at the edge of<br />
front axle hub LH.<br />
LH slowly.<br />
indicator close to the edge of axle hub.<br />
(l) Rotate the front axle hub LH by 2 ~ 3 turns.<br />
(m) Using spring scale, measure the primal rotating force of<br />
Primal rotating force: 5 N·m<br />
If the primal rotating force is out of the specification, adjust the<br />
front axle hub nut.<br />
5. Install the front wheel assy LH. (Refer to “Chapter 33 wheel and tire - front wheel and tire,<br />
6. REMOVE AND INSTALL FRONT AXLE HUB RH.<br />
34-24<br />
AXLE AND PROPELLER SHAFT - REAR AXLE HUB<br />
1. Remove the rear wheel and tire assy LH. (Refer to “Chapter 33 wheel and tire - rear wheel and<br />
2. REMOVE REAR BARE LH.(Refer to “Chapter 35 brake - rear brake, overhaul”)<br />
3. REMOVE REAR HUB WITH AXLE SHAFT ASSY LH.<br />
(a) Remove 2 mounting bolts attaching cable of parking<br />
brake operation rear assy LH to brake backing plate.<br />
Remove bolts from the front of the brake backing plate.<br />
Remove tubing joint nut of rear brake LH, take out oil<br />
tube of rear brake LH.<br />
Undo bolt, remove wheel speed sensor.<br />
Remove 4 nuts.<br />
34-25<br />
Remove rear axle hub with axle shaft LH and rear brake<br />
backing plateLH.<br />
4. INSTALL REAR AXLE HUB WITH AXLE SHAFT ASSY<br />
LH.<br />
(a) Using dial indicator, measure the back lash around the<br />
center of rear axle hub LH.<br />
If the back lash is out of the specification, replace with new rear<br />
• Measure the back lash by shaking the rear axle hub<br />
Insert the rear wheel hub and axle shaft into the rear axle<br />
Apply No. 2 lithium base grease on six convex platform<br />
plane of brake backing plate, don’t pollute working surface<br />
of brake drum and brake shoes.<br />
Tighten 4 mounting nuts.<br />
Toque: 65 ~ 80 N·m6<br />
(d) Using dial indicator, measure the deviation at the edge of<br />
rear axle hub LH.<br />
• Measure the deviation by rotating the rear axle hub<br />
34-26<br />
Position rear wheel speed sensor LH, tighten mounting<br />
Connect rear brake fluid tube to rear wheel brake cylinder<br />
LH, tighten the tubing joint nut.<br />
Torque:21 ~ 24 N·m<br />
Position the cable of parking brake operation rear assy<br />
LH to brake backing plate,tighten 2 mounting bolts.<br />
Install bolts from the front of the brake backing plate.<br />
5. INSTALL REAR BRAKE LH. (Refer to “Chapter 35 brake - rear brake, overhaul”)<br />
6. MEASURE THE PRIMAL ROTATING FORCE.<br />
(a) Rotate the rear axle hub LH by 2 ~ 3 turns.<br />
(b) Using spring scale, measure the primal rotating force of<br />
7. INSTALL THE REAR WHEEL ASSY LH. (Refer to “Chapter 33 wheel and tire - rear wheel and tire,<br />
34-27<br />
8. BRAKE SYSTEM REFILLING AND BLEEDING. (Refet to “Chapter 35 braking system - brake fluid,<br />
bleeding”)<br />
9. REMOVE AND INSTALL REAR AXLE HUB RH.<br />
34-28<br />
AXLE AND PROPELLER SHAFT - STEERING KNUCKLE<br />
2. REMOVE THE FRONT BRAKE DISK WITH AXLE HUB ASSY LH. (Refer to “Chapter 35 brake -<br />
3. REMOE FRONT WHEEL SPEED SENSOR LH AND<br />
BRACKET.<br />
4. REMOVE STEERING KNUCKLE LH.<br />
(a) Separate the steering tie rod B-joint LH from the steering<br />
knuckle arm LH.<br />
• Remove the cotter pin.<br />
Discard the removed cotter pin.<br />
• Remove the slotted nut.<br />
Discard the removed slotted nut.<br />
• Set the steering tie rod LH aside.<br />
(b) Remove the lower control arm B-joint LH.<br />
34-29<br />
• Loosen the 4 sets of bolts and nuts.<br />
Discard the removed bolts and nuts.<br />
• Using hammer and copper rod, remove the lower control<br />
arm B-joint LH.<br />
34-30<br />
Separate the steering knuckle LH from the upper control<br />
• Loosen the slotted nut.<br />
• Using hammer and copper rod, remove the steering<br />
knuckle LH.<br />
5. INSPECT B-JOINT.<br />
(a) Check the contact area between steering tie rod B-joint<br />
and steering knuckle arm.<br />
• Apply red lead evenly to the steering tie rod B-joint shaft<br />
and hole of steering knuckle arm.<br />
• Insert the steering tie rod B-joint shaft into the hole of<br />
steering knuckle arm, then pull it out again. Check the<br />
contact area.<br />
Standard: red area ≤ 3/4 shaft length,evenly<br />
34-31<br />
If any problem is found, replace with a new steering box and<br />
steering knuckle arm. (Refer to “Chapter 52 power steering -<br />
steering box, overhaul”)<br />
(b) Check the contact area between lower control arm B-<br />
joint and steering knuckle.<br />
• Apply red lead evenly to the lower control arm B-joint<br />
shaft and hole of steering knuckle.<br />
• Insert the lower control arm B-joint shaft into the hole of<br />
steering knuckle, then pull it out again. Check the contact<br />
area.<br />
If any problem is found, replace with a new lower control arm B-<br />
joint and steering knuckle. (Refer to “Chapter 31 front<br />
suspension - lower control arm, replacement”)<br />
(c) Check the contact area between upper control arm B-<br />
• Apply red lead evenly to the upper control arm B-joint<br />
• Insert the upper control arm B-joint shaft into the hole of<br />
If any problem is found, replace with a new lower control arm B -<br />
suspension - upper control arm, replacement”)<br />
6. INSTALL STEERING KNUCKLE LH.<br />
(a) Install the upper control arm B-joint LH.<br />
• Using hammer and copper rod, position the steering<br />
knuckle LH properly.<br />
• Tighten the slotted nut.<br />
Torque: 110 ~ 115 N·m<br />
Be sure to use a new slotted nut.<br />
34-32<br />
• Install the cotter pin.<br />
Be sure to use a new cotter pin.<br />
(b) Install the lower control arm B-joint LH.<br />
• Using hammer and cooper rod, position the lower control<br />
arm B-joint LH properly.<br />
Align the holes of B-joint and lower control arm LH.<br />
• Tighten the 2 sets of bolts and nuts fixing lower B-joint<br />
with lower control arm .<br />
Be sure to use new bolts and nuts.<br />
and lower control arm and strut rod.<br />
• Tighten the slotted nut fixing lower B-joint and steering<br />
knuckle.<br />
34-33<br />
Connect the steering tie rod LH to the steering knuckle<br />
arm LH.<br />
• Insert the steering tie rod B-joint LH into the hole in<br />
steering knuckle arm LH.<br />
Torque: 84 ~ 100 N·m<br />
7. INSTALL FRONT WHEEL SPEED SENSOR LH AND<br />
9. INSTALL FRONT WHEEL ASSY LH. (Refer to “Chapter 33 wheel and tire - front wheel and tire,<br />
10. REMOVE AND INSTALL STEERING KNUCKLE RH.<br />
11. INSPECT FRONT WHEEL ANGLE. (Refer to “Chapter 31 front suspension - front wheel<br />
alignment, adjustment”)<br />
34-34<br />
AXLE AND PROPELLER SHAFT - REAR AXLE<br />
1. PRECAUTION ON MAITAINING FINAL DRIVE OIL.<br />
(a) Be sure to use the specified final drive oil.<br />
Final drive oil:<br />
Type Grade Viscosity Capacity<br />
Gear oil for weight-load<br />
GL - 5 SAE 80W/90 2.5 L<br />
(b) Be sure to replace the final drive oil regularly. (Refer to “Chapter 34 axle and propeller shaft - final drive<br />
oil, replacement”)<br />
• Replace with new final drive oil during the primal Level 2 maintenance.<br />
• Replace with new final drive oil in the primal 40000 Km or 24 months.<br />
• Replace with new final drive oil in the primal 80000 Km or 48 months. Then repeat this operation in<br />
each following 50000 Km.<br />
(c) Check regularly, at least every 4 times for Level 2 maitenance:<br />
• Check the final drive oil for discolouration, thinning, etc.<br />
If any fault is found, replace with new final drive oil. (Refer to “Chapter 34 axle and propeller shaft - final<br />
drive oil, replacement”)<br />
2. PRECAUTION ON MAINTAINING FINAL DRIVE ASSY.<br />
(a) Be sure to check the vent plug regularly. Clean it when<br />
• Remove and clean the vent plug during each level1<br />
• The stuck vent plug may raise the oil pressure inside<br />
the final drive assy, even cause leakage.<br />
• Wash vent plug, check the final drive oil level<br />
simultaneously.<br />
(b) Disassemble and clean the final drive assy during the<br />
Level 3 maintenance. Then assemble the final drive assy<br />
according to the specification.<br />
(c) Check the rear brake shoe and brake drum regularly for<br />
wear and tear. (Refer to “Chapter 35 brake - rear brake,<br />
on-vehilce inspection”)<br />
3. SERVICING PRECAUTION ON FINAL DRIVE ASSY.<br />
(a) Be sure to replace the mating parts as a set.<br />
34-35<br />
(b) Discard all removed rubber parts (O-rings, oil seal, grommet, etc. ).<br />
(c) With the method of visual check, red lead, etc., check all parts carefully for faults below:<br />
Uneven wear Eccentric wear Scratch Crack<br />
Deformation Bend Bend Rusting<br />
Discolouration<br />
Invalidation or weakness<br />
(Spring)<br />
Abnormal noise (Bearing)<br />
Deterioration (Brake<br />
shoes)<br />
When assembling the final drive assy, make sure all parts are clean without oil fouling and metal scrap.<br />
Without special introduction, apply the final drive oil on the parts for lubrication before performing<br />
Type Type Viscosity Capacity<br />
4. PRECAUTION ON VEHICLE DRIVING.<br />
(a) Never overload when driving vehicle.<br />
(b) Never release the clutch pedal too quickly when vehicle driving.<br />
Releasing the clutch pedal too quickly will strick the gear and cause damage.<br />
34-36<br />
Symptom Suspect area Reference<br />
Continuous<br />
knocking<br />
(Turning)<br />
(At high speed)<br />
(Accelerating)<br />
Intermittent<br />
(Running)<br />
(Final drive)<br />
主 减 速 器 过 热<br />
Overheat<br />
1. Side pinion thrust washer (Worn)<br />
2. Side pinion (Worn)<br />
1. Drive pinion, crown gear<br />
(Excessive back lash or worn)<br />
2. Drive pinion, crown gear<br />
(Undersize back lash)<br />
1. Axle shaft spline (Excessive back<br />
lash or worn)<br />
3. Final drive assy (Impurity entry)<br />
1. Vent plug (Jam)<br />
2. Final drive oil level (High)<br />
3. Bolts (Loose or worn)<br />
4. Final drive housing (Crack or<br />
fracture)<br />
1. Final drive oil level (Low)<br />
3. Differential bearing (Too tight)<br />
assy, overhaul<br />
assy, inspection and adjustment<br />
Chapter 34 axle and propeller shaft - axle shaft<br />
Chapter 34 axle and propeller shaft - final drive oil,<br />
Chapter 34 axle and propeller shaft - rear axle,<br />
precaution<br />
Chapter 34 axle and propeller shaft - final drive, onvehicle<br />
Chapter 34 axle and propeller shaft - drive pinion,<br />
4. Rear brake (Stuck) Chapter 35 brake - rear brake, overhaull<br />
34-37<br />
1. INSPECT DRIVE AXLE BASH LASH.<br />
(a) Park the vehicle on level road with parking brake applied.<br />
(b) Move transmission to neutral position and fully apply the parking brake.<br />
(c) Lift rear wheels off the ground with jack or lift.<br />
(d) Separate the propeller shaft assy from pinion flange.<br />
• Mark on the rear propeller shaft U-joint and pinion flange.<br />
Make the marks are clear.<br />
• Remove the 4 sets of nuts and bolts.<br />
• Lower the propeller shaft and set it aside.<br />
Support the propeller shaft with a bracket.<br />
(e) Measure the drive axle back lash.<br />
• Rotate counterclockwise the pinion flange by hand until it<br />
becomes hard to rotate.<br />
• Mark on the final drive housing and pinion flange.<br />
34-38<br />
• Rotate clockwise the pinion flange by hand until it<br />
• The distance between the 2 marks is the drive axle back<br />
lash.<br />
(f) Connect the propeller shaft to pinion flange.<br />
• Position the propeller shaft properly according to the<br />
• Tighten the 4 sets of nuts and bolts.<br />
2. CHECK FINAL DRIVE OIL LEVEL.<br />
(a) Using a wrench, remove the filler plug.<br />
Check the distance between the filler hole of final drive<br />
and final drive oil level.<br />
• Higher and lower final drive oil level can cause<br />
problem.<br />
• Fill or drain the final drive oil when necessary. (Refer<br />
to “Chapter 34 axle and propeller shaft - final drive<br />
34-39<br />
Using a wrench, install the filler plug.<br />
Torque: 15 ~ 25 N·m<br />
3. CHECK FINAL DRIVE HOUSING.<br />
(a) Check the final drive housing for crack, leakage, etc. Replace it when necessary.<br />
34-40<br />
AXLE AND PROPELLER SHAFT - FINAL DRIVE OIL<br />
FINAL DRIVE OIL<br />
Toque: 50 ~ 55 N·m<br />
34-41<br />
3. FILL FINAL DRIVE OIL.<br />
Fill the final drive oil.<br />
Check final drive oil level.<br />
• Higher and lower gear oil level can cause problem.<br />
Toque: 15 ~ 25 N·m<br />
34-42<br />
Install the vent plug.<br />
AXLE SHAFT ASSY<br />
AXLE AND PROPELLER SHAFT - AXLE SHAFT ASSY<br />
34-43<br />
1. REMOVE AXLE SHAFT ASSY LH.<br />
(a) Remove the rear wheel assy LH. (Refer to “Chapter 33 wheel and tire - rear wheel and tire,<br />
(b) Remove the rear brake LH. (Refer to “Chapter 35 brake - rear brake, overhaul”)<br />
(c) Remove rear axle hub LH.(Refer to “Chapter 34 axle and propeller shaft - rear axle hub,<br />
overhaul”)<br />
Rear axle hub LH and axle shaft is a assy.<br />
2. INSPECTION AXLE SHAFT ASSY.<br />
runout of the axle shaft assy and flange end face runout.<br />
Diameter runout: ≤ 0.3 mm<br />
End face runout: ≤ 0.1 mm<br />
If the diameter runout and end face runout are out of the<br />
specification,correct the axle shaft assy. Replace the new one if<br />
(b) Using magnetic testing method, inspect axle shaft<br />
whether there is crack.<br />
(c) Check the axle shaft splines for fracture, worn an<br />
If any fault is detected, replace with a new axle shaft assy.<br />
3. INSTALL REAR AXLE HUB LH.(Refer to “Chapter 34 axle and propeller shaft - rear axle hub,<br />
4. REMOVE AND INSTALL AXLE SHAFT ASSY RH.<br />
5. BRAKE FLUID REFILL AND BLEEDING. (Refer to “Chapter 35 brake system - brake fluid,<br />
34-44<br />
AXLE AND PROPELLER SHAFT - REAR AXLE HOUSING WELDING ASSY<br />
REAR AXLE HOUSING WELDING ASSY<br />
3. REMOVE REAR WHEEL ASSYS. (Refer to “Chapter 33 wheel and tire - rear wheel and tire,<br />
4. REMOVE REAR BRAKES. (Refer to “Chapter 35 brake - rear brake, overhaul”)<br />
5. DRAIN FINAL DRIVE OIL. (Rrefer to “Chapter 34 axle propeller shaft - final drive oil,<br />
6. REMOVE REAR BRAKE TUBES ,PARKING CABLE<br />
AND WHEEL SPEED SENSOR.<br />
Before removing rear brake tubes, operate brake bleeding<br />
firstly.<br />
(a) Remove 2 bolts attaching cable of parking brake rear<br />
assy LH to brake backing plate, remove cable bracket<br />
mounting bolts and set the cable aside.<br />
Remove 2 bolts attaching cable of parking brake rear<br />
assy RH to brake backing plate, remove cable bracket<br />
Remove brake tubing joint nut LH of rear axle, wheel<br />
speed sensor mounting bolt and mounting bracket LH of<br />
brake tube and wheel speed sensor.<br />
34-45<br />
Remove brake tubing joint nut RH of rear axle, wheel<br />
Remove mounting bolt of upper brake tube and tubing<br />
joint nuts LH .<br />
Remove mounting bolts of brake tubes and wheel speed<br />
sensor cable brackets that are located at the top and<br />
center(LH and RH) of rear axle.<br />
Take down and place brake tubes, wheel speed sensors<br />
and brackets aside.<br />
Make sure to prevent the brake tubes from deformation.<br />
7. REMOVE AXLE HUB ASSYS LH AND RH. (Refer to “Chapter 34 axle and propeller shaft - rear<br />
axle hub, overhaul”)<br />
8. REMOVE AXLE SHAFT ASSY LH AND RH.(Refer to “Chapter 34 axle and propeller shaft - axle<br />
9. REMOVE MAIN DIFFERENTIAL.<br />
(a) Separate the propeller shaft assy from pinion flange.<br />
34-46<br />
Remove nuts and the final drive assy.<br />
10. REMOVE REAR SUSPENSION. (Refer to “Chapter 32 rear suspension - rear leaf spring assy,<br />
Support the propeller shaft with a bracket before removing.<br />
11. REMOVE THE REAR AXLE WELDING HOUSING<br />
12. INSPECT THE REAR HOUSING ASSY.<br />
(a) Check rear axle welding housing for surface crack and oil leakage, replace it if nessary.<br />
34-47<br />
13. INSTALL REAR AXLE WELDING HOUSING ASSY.<br />
(a) Support the housing to correct position with a bracket.<br />
14. INSTALL REAR SUSPENSION. (Refer to “Chapter 32 rear suspension - rear leaf spring assy,<br />
15. INSTALL MAIN DIFFERENTIAL.<br />
(a) Position the final drive assy, tighten 10 mounting nuts.<br />
Toque: 27 ~ 32 N•m<br />
Install the propeller shaft properly according to the<br />
Tighten the 4 set of nuts and bolts.<br />
Toque: 70 ~ 79 N•m<br />
Remove lifting and supporting devices.<br />
16. INSTALL AXLE SHAFT ASSY LH AND RH.(Refer to “Chapter 34 axle and propeller shaft - axle<br />
17. INSTALL AXLE HUB ASSYS LH AND RH. (Refer to “Chapter 34 axle and propeller shaft - rear<br />
34-48<br />
18. INSTALL REAR BRAKE TUBES ,PARKING CABLE<br />
Position brake tubes, wheel speed sensor cables and<br />
brackets.Tighten mounting bolts of brake tubes and<br />
wheel speed sensor cable brackets that are located at<br />
the top and center(LH and RH) of rear axle.<br />
Tighten mounting bolt of upper brake tube and tubing<br />
joint nuts LH.<br />
Tighten brake tubing joint nut RH of rear axle, wheel<br />
speed sensor mounting bolt and install mounting bracket<br />
LH of brake tube and wheel speed sensor.<br />
Torque: 21 ~ 24 N•m<br />
Tighten brake tubing joint nut LH of rear axle, wheel<br />
Tighten 2 bolts attaching cable of parking brake rear assy<br />
RH to brake backing plate.Tighten cable bracket mounting<br />
34-49<br />
(f) Tighten 2 bolts attaching cable of parking brake rear<br />
assy LH to brake backing plate.Tighten cable bracket<br />
mounting bolts.<br />
19. INTALL THE REAR BRAKE. (Refer to “Chapter 35 brake - rear brake, overhaul”)<br />
20. INSTALL REAR WHEEL ASSYS. (Refer to “Chapter 33 wheel and tire - rear wheel and tire,<br />
21. FILL THE FINAL DRIVE OIL. (refer to “Chapter 34 axle and propeller shaft - final drive oil,<br />
22. FILL BRAKE FLUID. (Refer to “Chapter 35 brake system - brake fluid, bleeding”)<br />
23. CONNECT BATTERY NEGATIVE CABLE.<br />
34-50<br />
AXLE AND PROPELLER SHAFT - DRIVE PINION<br />
1. INSPECT PINION FLANGE.<br />
(a) Using dial indicator, measure the pinion flange back lash.<br />
Back lash: ≤ 0.1 mm<br />
If the back lash is out of the specification, replace with new<br />
pinion inner and outer bearing and collapsible spacer. (Refer to<br />
“Chapter 34 axle and propeller shaft - drive pinion, overhaul”)<br />
(b) Using dial indicator, measure the pinion flange deviation.<br />
Deviation: ≤ 0.1 mm<br />
pinion flange. (Refer to “Chapter 34 axle and propeller shaft -<br />
drive pinion, overhaul”)<br />
2. INSPECT PRELOAD.<br />
(a) Open the lock plate.<br />
(b) Loosen the pinion nut.<br />
34-51<br />
Tighten the pinion nut.<br />
Torque: 196 N·m<br />
Using a torque wrench, measure the primal rotating force<br />
of drive pinion.<br />
Primal rotating force: 1.3 ~ 2.2 N·m<br />
Never loosen the pinion nut to reduce the primal rotating<br />
force of drive pinion.<br />
• If the primal rotating force is more than the specification,<br />
replace with a new collapsible spacer. (Refer to “Chapter<br />
34 axle and propeller shaft - drive pinion, overhaul”)<br />
• If the primal rotating force is less than the specification,<br />
perform the following operations.<br />
Tighten the pinion nut further.<br />
Torque (Increment): 13 N·m<br />
Torque (Maximum): 343 N·m<br />
of drive pinion again.<br />
• If the primal rotating force is still less than the<br />
specification, repeat step (e) ~ (f) until the primal<br />
rotating force is within the specification.<br />
specification when the pinion nut retaining torque<br />
exceeds the maximum, replace with a new collapsible<br />
spacer. (Refer to “Chapter 34 axle and propeller shaft<br />
- drive pinion, overhaul”)<br />
34-52<br />
Fold the lock plate up.<br />
BRAKING SYSTEMS<br />
BRAKE SYSTEM ....................................................................... 35-1<br />
PROBLEM SYMPTOMS TABLE ................................................ 35-02<br />
BRAKE FLUID............................................................................. 35-04<br />
BRAKE PEDAL........................................................................... 35-06<br />
CYLINDER ASSY........................................................................ 35-14<br />
VACUUM BOOSTER LINE ......................................................... 35-18<br />
FRONT BRAKE........................................................................... 35-20<br />
REAR BRAKE............................................................................. 35-26<br />
ABS ACTUATOR ........................................................................ 35-37<br />
WHEEL SPEED SENSOR........................................................... 35-40<br />
PARKING BRAKE...................................................................... 36-1<br />
PROBLEM SYMPTOMS TABLE................................................... 36-1<br />
FRONT PARKING BRAKE OPERATION ASSY........................... 36-4<br />
REAR PARKING BRAKE OPERATION ASSY ............................. 36-8<br />
BRAKE SYSTEM ............................................................................... 35-1<br />
PRECAUTION.............................................................................. 35-1<br />
PROBLEM SYMPTOMS TABLE ....................................................... 35-2<br />
BRAKE FLUID.................................................................................... 35-4<br />
BLEEDING................................................................................... 35-4<br />
BRAKE PEDAL.................................................................................. 35-6<br />
COMPONENTS ........................................................................... 35-6<br />
ADJUSTMENT............................................................................. 35-7<br />
REPLACEMENT .......................................................................... 35-9<br />
VACUUM BOOSTER WITH BRAKE MASTER<br />
CYLINDER ASSY............................................................................. 35-14<br />
OVERHAUL ............................................................................... 35-14<br />
VACUUM BOOSTER LINE .............................................................. 35-18<br />
REPLACEMENT ........................................................................ 35-18<br />
FRONT BRAKE................................................................................ 35-20<br />
OVERHAUL ............................................................................... 35-20<br />
REAR BRAKE.................................................................................. 35-26<br />
ON-VEHICLE INSPECTION ...................................................... 35-26<br />
OVERHAUL ............................................................................... 35-27<br />
ABS ACTUATOR ............................................................................. 35-37<br />
REPLACEMENT ........................................................................ 35-37<br />
WHEEL SPEED SENSOR................................................................ 35-40<br />
REPLACEMENT ........................................................................ 35-40<br />
BRAKE SYSTEM<br />
BRAKE - BRAKE SYSTEM<br />
35-1<br />
1. BRAKE PRECAUTION<br />
(a) Care must be taken to replace each part properly, because it could affect the performance of the brake<br />
system and result in a driving hazard, replace with the parts which have the same part number or<br />
equivalent.<br />
(b) It is very important to keep parts and the area clean when repairing the brake system.<br />
(c) To avoid spreading brake dust, do not clean any brake components with sand paper, dry brush and<br />
compressed air. Only use a water dampende towel to clean brake components.<br />
(d) When removing or installing brake lines, use the pipeline nut wrench.<br />
(e) Always tighten brake lines when installing.<br />
35-2<br />
BRAKE - PROBLEM SYMPTOMS TABLE<br />
1. Brake fluid (Lacking) Chapter 35 brake - brake fluid, bleeding<br />
2. Brake system (Leaking) -<br />
Low pedal or spongy<br />
pedal<br />
3. Brake pad (Worn) Chapter 35 brake - front brake, overhaul<br />
4. Brake master cylinder assy<br />
(Failure)<br />
Chapter 35 brake - vacuum booster with brake<br />
master cylinder assy, overhaul<br />
5. Brake system (Air in system) Chapter 35 brake - brake fluid, bleeding<br />
6. Brake caliper (Failure) Chapter 35 brake - front brake, overhaul<br />
1. Brake tube(Block) -<br />
2. Brake cylinder (Sticking) Chapter 35 brake - rear brake, overhaul<br />
Brake drag<br />
3. Brake caliper (Sticking) Chapter 35 brake - front brake, overhaul<br />
4. Axle hub bearing (Loose)<br />
Chapter 34 axle and propeller shaft - axle hub<br />
and steering knuckle, on vehicle inspection<br />
5. Brake pedal free play (Out of<br />
adjustment)<br />
1. Tire (Improperly inflated)<br />
Chapter 35 brake - brake pedal, adjustment<br />
on vehicle inspection<br />
2. Brake shoe (Oily) -<br />
3. Brake shoe (Worn) Chapter 35 brake - rear brake, overhaul<br />
4. Brake pad (Oily) -<br />
Pull to one side<br />
5. Brake pad (Worn) Chapter 35 brake - front brake, overhaul<br />
6. Brake disk (Warped) Chapter 35 brake - front brake, overhaul<br />
7. Brake drum (Warped) Chapter 35 brake - rear brake, overhaul<br />
8. Brake caliper (Brake force<br />
unequal)<br />
9. Brake cylinder (Brake force<br />
Chapter 35 brake - front brake, overhaul<br />
Chapter 35 brake - rear brake, overhaul<br />
1. Brake pad (Worn) Chapter 35 brake - front brake, overhaul<br />
2. Brake caliper (Bolt loose) Chapter 35 brake - front brake, overhaul<br />
Braking instability<br />
3. Brake caliper mounting (Bolt<br />
4. Brake caliper (Sticking) Chapter 35 brake - front brake, overhaul<br />
5. Brake cylinder (Sticking) Chapter 35 brake - rear brake, overhaul<br />
35-3<br />
Lack of braking force<br />
2. Brake shoe (Worn) Chapter 35 brake - rear brake, overhaul<br />
3. Brake lines (Air in system) Chapter 35 brake - brake fluid, bleeding<br />
35-4<br />
BRAKE - BRAKE FLUID<br />
BRAKE FLUID<br />
BLEEDING<br />
If any work is done on the brake system or if air in the brake lines is suspected, bleed the air from the<br />
system.<br />
Brake fluid: DOT3 or DOT4 brake fluid<br />
35-5<br />
35-6<br />
BRAKE - BRAKE PEDAL<br />
1 Flat Pin<br />
2 Cotter Pin<br />
5 Nut<br />
3 Brake Pedal Assy<br />
35-7<br />
1. INSPECT BRAKE PEDAL HEIGHT.<br />
(a) Inspect the height between brake pedal and floor.<br />
Specification: 148 mm<br />
2. ADJUST BRAKE PEDAL HEIGHT.<br />
(a) Remove the stop lamp switch. (Refer to “Chapter 35 brake - brake pedal, replacement”)<br />
(b) Disconnect the push rod from the brake pedal. (Refer to “Chapter 35 brake - brake pedal,<br />
Loosen the lock nut, then adjust the brake pedal by<br />
truning the push rod clevis. Tighten the lock nut after<br />
adjusting.<br />
(d) Connect the push rod to the brake pedal. (Refer to<br />
“Chapter 35 brake - brake pedal, replacement”)<br />
(e) Install stop lamp switch. (Refer to “Chapter 35 brake -<br />
brake pedal, replacement”)<br />
(f) Push the brake pedal down about 5 ~ 10 mm and turn<br />
the stop lamp switch in the position where the stop lamp<br />
goes off, then tighten the lock nut.<br />
(g) After installation, check that stop lamp comes on when<br />
depressing the brake pedal about 5 ~ 10 mm.<br />
35-8<br />
3. INSPECT BRAKE PEDAL FREE PLAY.<br />
(a) Stop the engine and depress the brake pedal several<br />
times until there is no more vacuum left in the vacuum<br />
booster.<br />
(b) Depress the brake pedal until the pedal resistance<br />
begins to be felt, then inspect the brake pedal free play L.<br />
(c) Measure the brake pedal free play.<br />
Specification: 5 ~ 10 mm<br />
35-9<br />
2. REMOVE THE DASHBOARD(Refer to “Chapter 83 instrument panel - dashboard, replacement”)<br />
3. REMOVE STOP LAMP SWITCH.<br />
(a) Disconnect the connector from stop lamp switch.<br />
(b) Loosen the lock nut from stop lamp switch.<br />
(c) Remove the stop lamp switch.<br />
4. DISCONNECT THE CONNECTION BETWEEN PUSH<br />
ROD CLEVIS AND BRAKE PEDAL.<br />
Remove the cotter pin and flat pin, then disconnect the<br />
push rod clevis from brake pedal.<br />
35-10<br />
5. REMOVE BRAKE PEDAL AND BRACKET.<br />
(a) Remove 4 mounting bolts of bracket and 4 lock nuts of<br />
(b) Tack down the brake pedal and bracket.<br />
6. REMOVE BRAKE PEDAL.<br />
(a) Loosen the return spring.<br />
The return spring is under great pressure. To avoid injury,<br />
use caution when removing the return spring.<br />
(b) Remove the lower mounting bolt attaching pedal to<br />
(c) Remove the upper mounting bolt attaching pedal to<br />
35-11<br />
Remove the brake pedal.<br />
7. INSTALL BRAKE PEDAL.<br />
Position the brake pedal.<br />
Tighten mounting bolts attaching the pedal to bracket.<br />
Install return spring and shaft sleeve, tighten return<br />
spring bolts.<br />
35-12<br />
8. INSTALL BRAKE PEDAL AND BRACKET.<br />
(a) Position brake pedal and bracket.<br />
(b) Tighten 4 mounting bolts of bracket.<br />
Diagonally tighten 4 bolts.<br />
(c) Tighten 4 lock nuts of bracket.<br />
9. CONNECT PUSH ROD CLEVIS TO BRAKE PEDAL.<br />
(a) Install the cotter pin roll and flat pin.<br />
Make sure to use new cotter pin.<br />
35-13<br />
10. INSTALL STOP LAMP SWITCH.<br />
(a) Install the stop lamp switch and tighten the lock nut of<br />
stop lamp switch.<br />
(b) Connect the connector to stop lamp switch.<br />
Adjust the distance between stop lamp switch and brake<br />
pedal. (Refer to “Chapter 35 brake - brake pedal,<br />
11. INSPECT AND ADJUST BRAKE PEDAL HEIGHT. (Refer to “Chapter 35 brake - brake pedal,<br />
12. INSPECT BRAKE PEDAL FREE PLAY. (Refer to “Chapter 35 brake - brake pedal, adjustment”)<br />
35-14<br />
BRAKE - VACUUM BOOSTER WITH BRAKE MASTER CYLINDER ASSY<br />
VACUUM BOOSTER WITH BRAKE MASTER CYLINDER<br />
2. DRAIN BRAKE FLUID COMPLETELY.<br />
3. REMOVE WASHER ASSY.(Refer to “Chapter 65 wiper and washer - wssher assy, replacement”)<br />
4. REMOVE VACUUM BOOSTER WITH BRAKE<br />
MASTER CYLINDER ASSY.<br />
(a) Disconnect the connector of Brake liquid level sensor,<br />
and remove the sensor wire from bracket.<br />
(b) Remove the brake fluid hosepipe from clutch master<br />
(c) Remove brake tubing joint nuts,and remove brake tubes.<br />
(d) Pull out the vaccum booster pipe.<br />
Remoe 4 mounting lock nuts of vaccum booster and<br />
brake master sylinder assy.<br />
35-15<br />
Remove vaccum booster with brake master sylinder assy<br />
and fluid reservior.<br />
5. DISASSEMBLE VACCUM BOOSTER WITH BRAKE<br />
MASTER SYLINDER ASSY AND FLUID RESERVIOR.<br />
Remove 2 mounting nuts of brake master sylinder.<br />
Disassemble vaccum booster and brake master cylinder.<br />
Pull out mounting clip of brake fluid reservior.<br />
Separate brake fluid reservior and brake master cylinder.<br />
Brake masrer cylinder and fluid reservior can be removed<br />
independently when brake fluid is drained completly.<br />
35-16<br />
6. CHECK BRAKE MASTER CYLINDER.<br />
(a) Check the cylinder and seal ring for damage.<br />
7. ASSEMBLE VACCUM BOOSTER WITH BRAKE<br />
(a) Position brake fluid reservior.<br />
(b) Insert the mountiong clip.<br />
Connect vaccum booster and brake master cylinder.<br />
Tighten 2 mounting nuts.<br />
8. INSTALL VACCUM BOOSTER WITH BRAKE MASTER<br />
SYLINDER ASSY.<br />
(a) Position vaccum booster with brake master cylinder<br />
(b) Tighten 4 lock nuts of vaccum booster with brake master<br />
cylinder assy.<br />
(c) Install the cotter pin and flat pin, then connect the push<br />
rod clevis to brake pedal.<br />
35-17<br />
Connect vaccum booster pipe.<br />
Position brake tubes and tighten tubing joint nuts.<br />
Connect the brake fluid hosepipe which connect to clutch<br />
master cylinder and tighten the clamp.<br />
Connect the connector of Brake liquid level sensor,and<br />
fix the sensor wire to bracket.<br />
9. INSTALL WASHER ASSY. (Refer to “Chapter 65 wiper and washer - wssher assy, replacement”)<br />
10. FILL THE FLUID RESERVOIR WITH BRAKE FLUID.<br />
11. BLEED BRAKE MASTER CYLINDER ASSY. (Refer to “Chapter 35 brake - brake fluid, bleeding”)<br />
12. BLEED BRAKE LINES. (Refer to “Chapter 35 brake - brake fluid, bleeding”)<br />
13. INSPECT AND ADJUST BRAKE PEDAL HEIGHT. (Refer to “Chapter 35 brake - brake pedal,<br />
14. INSPECT AND ADJUST BRAKE PEDAL FREE PLAY. (Refer to “Chapter 35 brake - brake pedal,<br />
15. CHECK FLUID LEVEL IN BRAKE FLUID RESERVOIR.<br />
16. CHECK BRAKE FLUID FOR LEAKING.<br />
17. CONNECT BATTERY NEGATIVE CABLE.<br />
35-18<br />
BRAKE - VACUUM BOOSTER LINE<br />
VACUUM BOOSTER LINE<br />
1. REMOVE WASHER ASSY.(Refer to “Chapter 65 wiper and washer - wssher assy, replacement”)<br />
2. REMOVE VACCUM BOOSTER PIPE.<br />
(a) Pull out the vaccum booster pipe from brake vaccum<br />
(b) Loosen clamp,disconnect vaccum booster from clutch<br />
vaccum booster.<br />
Loosen clamp,disconnect vaccum booster from intake<br />
mainfold of engine.<br />
Along the pipeline end, loosen all fixed clamp.<br />
Remove vaccum booster pipe.<br />
Vaccum booster pipe is made up of two pipes,each one can<br />
be replaced independently.<br />
35-19<br />
3. INSTLL VACCUM BOOSTER PIPE.<br />
(a) Position vaccum booster pipe.<br />
(b) Connect vaccum booster pipe to brake vaccum booster.<br />
(c) Connect vaccum booster pipe to clutch vaccum<br />
booster,and tighten clamp screw.<br />
Connect vaccum booster pipe to intake mainfold of<br />
engine,and tighten clamp screw.<br />
(e) Along the pipeline end, fix all clamp.<br />
4. INSTALL WASHER ASSY. (Refer to “Chapter 65 wiper and washer - wssher assy, replacement”)<br />
35-20<br />
BRAKE - FRONT BRAKE<br />
1. REMOVE FRONT WHEEL LH. (Refer to “Chapter 33 wheel and tire - front wheel and tire,<br />
3. REMOVE FRONT DISK BRAKE CALIPER ASSY LH.<br />
(a) Remove screw and disconnect brake tube from front disk<br />
brake caliper assy LH.<br />
(b) Remove the 2 mounting bolts and front disk brake caliper<br />
assy LH.<br />
4. CHECK FRONT DISK BRAKE CALIPER ASSY FOR LEAKING,RUSTING AND SCORING,<br />
REPLACE IF NECESSARY.<br />
5. REMOVE FRONT BRAKE PAD ASSY LH.<br />
(a) Remove outer brake pad assy LH.<br />
35-21<br />
Remove inner brake pad assy LH.<br />
6. INSPECT BRAKE PAD THICKNESS.<br />
(a) Measure the brake pad thickness.<br />
Specification: 16 mm ~ 16.1 mm<br />
Limit: 8 mm<br />
7. REMOVE FRONT DISK BRAKE CALIPER MOUNTING<br />
(a) Remove the 2 bolts and front disk brake caliper mounting.<br />
35-22<br />
8. INSPCTE DISK THICKNESS.<br />
(a) Measure the disk thickness.<br />
Specification: 28 ± 0.1 mm<br />
(b) Measure the disk thickness difference.<br />
The thickness difference of the plane in the same<br />
circle ≤ 0.01mm<br />
9. INSPECT FRONT DISK RUNOUT.<br />
(a) Temporarily fasten the front disk with knuckle bolts.<br />
(b) Measure the disk runout at the position where is 10 mm<br />
away from the outer edge of the disk.<br />
Ultimate value: 0.03 mm<br />
(c) If the disk runout is the maximum value or is outside the<br />
maximum value, inspect the clearance of axle hub and<br />
axle hub runout. If the clearance of axle hub and axle<br />
hub runout is nomal, adjust the disk runout or grind it on<br />
a “On-vehical” brake lathe.<br />
10. REMOVE FRONT DISK LH.<br />
(a) Remove 4 mounting bolts.<br />
(b) Remove front disk with front axle hub.<br />
35-23<br />
Remove 6 mounting bolts.<br />
Remove disk.<br />
11. INSTALL FRONT DISK LH.<br />
Select the installation position which the front disk has the<br />
minimum runout.<br />
(a) Install front disk to front axle hub,tighten 6 bolts.<br />
Torque: 50 ~ 70 N•m<br />
Checked the inner bearing, replace with a new axle hub if<br />
necessary. (Refer to “Chapter 34 axle and propeller shaft -<br />
Postion front disk with front axle hub and hub bearing,Tighten<br />
4 mounting bolts.<br />
Torque: 85 ~ 120 N•m<br />
35-24<br />
12. INSTALL FRONT DISK BRAKE CALIPER MOUNTING<br />
(a) Install front disk brake caliper mounting and tighten 2<br />
Torque: 30 ~ 35 N•m<br />
13. INSTALL FRONT BRAKE PAD ASSY.<br />
Install inner brake pad assy.<br />
• Replace the anti-squeal shim when replacing the<br />
brake pad.<br />
• Keep the friction surface of brake pad and front disk<br />
away from oil and grease.<br />
Install outer brake pad assy LH.<br />
35-25<br />
14. INSTALL FRONT DISK BRAKE CALIPER LH.<br />
Using a suitable tool, push the brake cylinder piston back.<br />
Install the front disk brake caliper assy LH and tighten<br />
the 2 nuts.<br />
Torque: 90 ~ 110 N•m<br />
Install brake tube and tighten plug.<br />
15. REMOVE AND INSTALL FRONT BRAKE RH.<br />
16. FILL THE FLUID RESERVOIR WITH BRAKE FLUID.<br />
17. BLEED BRAKE MASTER CYLINDER ASSY. (Refer to “Chapter 35 brake - brake fluid, bleeding”)<br />
18. BLEED BRAKE LINES. (Refer to “Chapter 35 brake - brake fluid, bleeding”)<br />
19. CHECK FLUID LEVEL IN BRAKE FLUID RESERVOIR.<br />
20. CHECK BRAKE FLUID FOR LEAKING.<br />
21. INSATLL FRONT WHEEL LH. (Refer to “Chapter 33 wheel and tire - front wheel and tire,<br />
35-26<br />
BRAKE - REAR BRAKE<br />
1. CHECK BRAKE SHOE THICKNESS.<br />
(a) Remove the brake lining inspection hole plug and check<br />
the brake shoe thickness through the brake lining<br />
inspection hole.<br />
35-27<br />
1. RELEASE PARKING BRAKE.<br />
2. REMOVE REAR WHEEL LH. (Refer to “Chapter 33 wheel and tire - rear wheel and tire,<br />
3. DRAIN BRAKE FLUID COMPLETELY.<br />
4. REMOVE REAR BRAKE DRUM AND WASHER LH.<br />
5. REMOVE ADJUSTMENT SHEET AND TENSION<br />
SPRING FOR PARKING BRAKE .<br />
(a) Loosen tension spring of parking brake adjustment<br />
sheet.<br />
Remove adjustment sheet and tension spring for parking<br />
brake.<br />
6. LOOSEN BRAKE SHOE TENSION SPRING FROM<br />
LEADING SHOE .<br />
The parking brake tension spring is under great pressure.<br />
To avoid injury, use caution when removing the parking<br />
brake tension spring.<br />
35-28<br />
7. REMOVE LOWER TENSION SPRING ,RETAINING<br />
PLATE AND RETURN SPRING.<br />
Loosen lower tension spring from RH side.<br />
Loosen lower tension spring and retaining plate from LH<br />
side.<br />
Remove lower tension spring and retaining plate.<br />
Remove return spring.<br />
8. REMOVE LEADING SHOE.<br />
(a) Remove the leading shoe hold spring.<br />
The leading shoe hold spring is under great pressure. To<br />
avoid injury, use caution when removing the leading shoe<br />
hold spring.<br />
35-29<br />
Remove the leading shoe.<br />
9. INSPECT BRAKE SHOE THICKNESS.<br />
Specification: 5 mm<br />
Ultimate value: 1.5 mm<br />
If the thickness is at the ultimate thickness or less, or if it<br />
appears severe uneven wear, replace with a new brake<br />
shoe.<br />
10. REMOVE TRAILING SHOE.<br />
(a) Remove the trailing shoe hold spring.<br />
The trailing shoe hold spring is under great pressure. To<br />
avoid injury, use caution when removing the trailing shoe<br />
Remove the parking brake cable.<br />
35-30<br />
Remove the trailing shoe.<br />
Remove parking brake shoe strut set and tension spring.<br />
11. REMOVE REAR BRAKE AUTOMATIC ADJUSTING<br />
LEVER AND PARKING BRAKE SHOE LEVER.<br />
Remove the C-washer.<br />
Remove the rear brake automatic adjusting lever.<br />
Remove parking brake shoe lever.<br />
35-31<br />
12. INSPECT BRAKE SHOE THICKNESS.<br />
13. INSPECT REAR BRAKE DRUM INSIDE DIAMETER.<br />
Ultimate value: 254 ~ 254.2 mm<br />
If the inside diameter is outside ultimate value, replace with<br />
a new rear brake drum.<br />
14. INSPECT REAR BRAKE DRUM AND BRAKE SHOE<br />
FOR PROPER CONTACT.<br />
Apply chalk to the inside of the rear brake drum, then<br />
grind brake shoe on the surface of the drum. If the<br />
contact between the rear brake drum and the brake shoe<br />
is improper, repair brake shoe by a brake shoe grinder or<br />
replace the rear brake drum.<br />
15. REMOVE REAR WHEEL BRAKE CYLINDER ASSY<br />
(a) Loosen tubing joint nut and disconnect the brake fluid<br />
tube from rear wheel brake cylinder.<br />
Remove the bleeder plug.<br />
35-32<br />
Remove the 2 bolts from rear wheel brake cylinder.<br />
Remove rear wheel brake cylinder.<br />
16. INSTALL REAR WHEEL BRAKE CYLINDER ASSY LH.<br />
(a) Install the 2 bolts to rear wheel brake cylinder.<br />
Install the bleeder plug.<br />
Connect the brake fluid tube to rear wheel brake cylinder<br />
and tighten the tubing joint nut.<br />
35-33<br />
17. INSTALL REAR BRAKE AUTOMATIC ADJUSTING<br />
Install the rear brake automatic adjusting lever.<br />
Install the parking brake shoe lever.<br />
Install the C-washer.<br />
18. INSTALL TRAILING SHOE.<br />
(a) Install parking brake shoe strut set and tension spring to<br />
trailing shoes.<br />
(b) Connect the parking brake cable to parking brake shoe<br />
(c) Position the trailing shoe, install the trailing shoe hold<br />
spring.<br />
Apply No. 2 lithium base grease on contact surface of<br />
trailing shoe and wheel brake cylinder when installing<br />
trailing shoe,Don’t pollut the working surface of brake drum<br />
and shoe .<br />
avoid injury, use caution when installing the trailing shoe<br />
19. INSTALL LEADING SHOE.<br />
(a) Install parking brake tension spring to leading shoe.<br />
To avoid injury, use caution when installing the parking<br />
(b) Install leading shoe to wheel brake cylinder,and install<br />
parking brake shoe strut set to leading by rotating<br />
leading shoe.<br />
(c) Position the leading shoe,Install the leading shoe hold<br />
leading shoe and wheel brake cylinder when installling<br />
leading shoe,Don’t pollut the working surface of brake<br />
drum and shoe .<br />
35-34<br />
avoid injury, use caution when installing the leading shoe<br />
20. INSTALL RETURN SPRING AND LOWER TENSION<br />
SPRING , RETAINING PLATE .<br />
(a) Install return spring.<br />
The brake shoe return spring is under great pressure. To<br />
Install retaining plate and lower tension spring.<br />
The lower tension spring is under pressure. To avoid injury,<br />
use caution when installing the leading shoe hold spring.<br />
21. INSTALL ADJUSTMENT SHEET AND TENSION SPRING<br />
FOR PARKING BRAKE.<br />
(a) Install adjustment sheet for parking brake.<br />
(b) Install tension spring of adjustment sheet.<br />
The tension spring of adjustment sheet is under pressure.<br />
To avoid injury, use caution when installing the leading<br />
shoe hold spring.<br />
35-35<br />
22. INSPECT BRAKE SHOES AND REAR BRAKE DRUM<br />
INSTALLATION.<br />
Check that each part is installed properly.<br />
Measure the inside diameter of rear brake drum and the<br />
diameter of brake shoes. Inspect the clearance between<br />
rear brake drum and brake shoes.<br />
Specification: 0.5 mm<br />
There should be no oil or grease adhering to the friction<br />
surface between brake shoe and rear brake drum.<br />
23. ADJUST CLEARANCE BETWEEN REAR BRAKE<br />
DRUM AND BRAKE SHOES.<br />
Remove the hole plug behind brake backing plate.<br />
Adjust the clearance between brake shoes and rear<br />
brake drum.<br />
24. INSTALL REAR BRAKE DRUM AND WASHER LH.<br />
35-36<br />
25. FILL BRAKE FLUID INTO RESERVIOR.<br />
26. BLEED BRAKE MASTER CYLINDER ASSY. (Refer to “Chapter 35 brake - brake fluid, bleeding”)<br />
27. BLEED BRAKE LINE. (Refer to “Chapter 35 brake - brake fluid, bleeding”)<br />
28. CHECK FLUID LEVEL IN BRAKE FLUID RESERVOIR. (Refer to “Chapter 35 brake - brake fluid,<br />
29. CHECK BRAKE FLUID FOR LEAKING.<br />
30. INSTALL REAR WHEEL LH. (Refer to “Chapter 33 wheel and tire - rear wheel and tire,<br />
31. REMOVE AND INSTALL REAR BRAKE DRUM RH.<br />
BRAKE - ABS ACTUATOR<br />
35-37<br />
ABS ACTUATOR<br />
3. REMOVE FRONT BUMPER ASSY.(Refer to “Chapter 88 exterior and interior trim - front bumper,<br />
4. REMOVE ABS ACTUATOR ASSY.<br />
(a) Disconnect the connect from ABS actuator.<br />
Remove 6 brake tubes from ABS actuator.<br />
Make marks on the ABS actuator connecting fluid tube assy<br />
in order to install them properly.<br />
(c) Remove 2 mounting bolts of ABS actuator.<br />
35-38<br />
Remove ABS actuator.<br />
Don’t destroy rubber washer of core pin at the bottom of<br />
actuator and mounting nuts.<br />
5. INSTALL ABS ACTUATOR.<br />
(a) Position ABS actuator.<br />
(b) Tighten 2 mounting nuts of ABS actuator.<br />
(c) Connect the ABS connecting fluid tubes to ABS actuator<br />
as the marks show, and tighten tubing joint nuts.<br />
Connect the connector to ABS actuator.<br />
6. INSTALL FRONT BUMPER ASSY.(Refer to “Chapter 88 exterior and interior trim - front bumper,<br />
7. CONNECT BATTERY NEGATIVE CABLE<br />
8. FILL THE FLUID RESERVOIR WITH BRAKE FLUID.<br />
9. BLEED BRAKE MASTER CYLINDER ASSY. (Refer to “Chapter 35 brake - brake fluid, bleeding”)<br />
10. BLEED BRAKE LINE. (Refer to “Chapter 35 brake - brake fluid, bleeding”)<br />
35-39<br />
11. CHECK FLUID LEVEL IN BRAKE FLUID RESERVOIR. (Refer to “Chapter 35 brake - brake fluid,<br />
12. CHECK BRAKE FLUID FOR LEAKAGE.<br />
13. INSPECT ABS ACTUATOT BY SCAN TOOL. (Refer to “Chapter 04 diagnostics - anti-lock brake<br />
system, pre-check”)<br />
35-40<br />
BRAKE - WHEEL SPEED SENSOR<br />
WHEEL SPEED SENSOR<br />
2. REMOVE FRONT WHEEL SPEED SENSOR LH.<br />
(a) Remove mounting bolts of front wheel speed sensor LH.<br />
(b) Disconnect the connector of wheel speed sensor LH.<br />
(c) Remove the clamp of front wheel speed sensor wire LH.<br />
(d) Remove front wheel speed sensor LH.<br />
3. REMOVE REAR WHEEL SPEED SENSOR LH.<br />
(a) Remove mounting bolts of rear wheel speed sensor LH.<br />
Disconnect the connector of rear wheel speed sensor<br />
Remove the clamp of rear wheel speed sensor wire LH.<br />
Remove rear wheel speed sensor LH.<br />
35-41<br />
4. INSTALL REAR WHEEL SPEED SENSOR LH.<br />
Install rear wheel speed sensor LH and tighten mounting<br />
Connect the connector of rear wheel speed sensor LH.<br />
Install the clamp and wire of rear wheel speed sensor<br />
5. INSTALL FRONT WHEEL SPEED SENSOR LH.<br />
Install front wheel speed sensor LH,tighten mounting<br />
Connect the connector of front wheel speed sensor LH.<br />
Install the clamp and wire of front wheel speed sensor<br />
6. REMOVE AND INSTALL FRONT WHEEL SPEED SENSOR RH.<br />
Remove and Install the RH side by the same procedures as the LH side.<br />
7. REMOVE AND INSTALL REAR WHEEL SPEED SENSOR RH.<br />
8. CONNECT BATTERY NEGATIVE CABLE.<br />
9. INSPECT WHEEL SPEED SENSOR SIGNAL.<br />
PARKING BRAKE SYSTEM.............................................................. 36-1<br />
PROBLEM SYMPTOMS TABLE.................................................. 36-1<br />
ADJUSTMENT............................................................................. 36-2<br />
COMPONENTS ........................................................................... 36-3<br />
FRONT PARKING BRAKE OPERATION ASSY............................... 36-4<br />
REPLACEMENT .......................................................................... 36-4<br />
REAR PARKING BRAKE OPERATION ASSY ................................. 36-8<br />
REPLACEMENT .......................................................................... 36-8<br />
PARKING BRAKE - PARKING BRAKE SYSTEM<br />
36-1<br />
PARKING BRAKE SYSTEM<br />
1. Parking Brake cable(Sticking) -<br />
2. Brake shoe clearance (Out of<br />
3. Return spring (Damaged)<br />
4. Parking brake tension spring<br />
Chapter 36 parking brake - parking brake system,adjustment<br />
Chapter 36 parking brake - front parking brake<br />
operation assy, replacement<br />
5. Parking brake return spring<br />
36-2<br />
1. REMOVE REAR WHEEL LH. (Refer to “Chapter 33 wheel and tire - rear wheel and tire,<br />
2. INSPECT BRAKE SHOES AND REAR BRAKE DRUM INSTALLATION. (Refer to “Chapter 35 brake<br />
- rear brake, overhaul”)<br />
3. ADJUST SINGLE CLEARANCE BETWEEN REAR BRAKE DRUM AND BRAKE SHOES. (Refer to<br />
“Chapter 35 brake - rear brake, overhaul”)<br />
4. INSTALL REAR WHEEL LH. (Refer to “Chapter 33 wheel and tire - rear wheel and tire,<br />
5. ADJUST BOTH CLEARANCE BETWEEN REAR<br />
BRAKE DRUM AND BRAKE SHOES.<br />
(a) Adjust both clearance between rear brake drum and<br />
brake shoes at the same time by adjustment screw at the<br />
parking brake rocker arm with bracket assy,until both<br />
clearance pass muster.<br />
36-3<br />
Parking Brake Operation Handle With<br />
Cable Assy<br />
6 Clamp<br />
7 Cable Bracket<br />
Parking Brake Rocker Arm With Bracket<br />
36-4<br />
PARKING BRAKE - FRONT PARKING BRAKE OPERATION ASSY<br />
FRONT PARKING BRAKE OPERATION ASSY<br />
2. REMOVE PARKING BRAKE SHIELD ASSY. (Refer to “Chapter 83 instrument panel - dashboard,<br />
3. REMOVE PARKING BRAKE SWITCH.<br />
(a) Disconnect the connector from parking brake switch.<br />
(b) Remove the parking brake switch.<br />
4. REMOVE PARKING BRAKE OPERATION HANDLE<br />
WITH CABLE ASSY.<br />
Remove 2 upper mounting bolts.<br />
Remove 2 lower mounting nuts<br />
Remove 2 lower mounting bolts LH.<br />
36-5<br />
Disconnect cable of parking brake operation handle<br />
with cable assy from parking brake rocker arm with<br />
bracket assy.<br />
Along the end of front parking brake operation assy,<br />
remove all clamps, remove the clamp between front<br />
parking brake cable and frame and the clamp between<br />
front parking brake and the other cables.<br />
Remove parking brake operation handle with cable<br />
5. REMOVE PARKING BRAKE ROCKER ARM WITH<br />
BRACKET ASSY.<br />
(a) Disconnect cable of parking brake operation handle<br />
(b) Remove return spring.<br />
Disconnect cable of rear parking brake operation assy<br />
LH/RH from parking brake rocker arm with bracket<br />
Remove 2 mounting bolts fitting parking brake rocker<br />
arm with bracket assy to frame.<br />
Remove parking brake rocker arm with bracket assy.<br />
6. INSTALL PARKING BRAKE ROCKER ARM WITH<br />
Position parking brake rocker arm with bracket assy,<br />
tighten 2 mounting bolts.<br />
Connect cable of rear parking brake operation assy LH<br />
to parking brake rocker arm with bracket assy.<br />
36-6<br />
Install return spring.<br />
Connect cable of parking brake operation handle with<br />
cable assy to parking brake rocker arm with bracket<br />
7. INSTALL ARKING BRAKE OPERATION HANDLE WITH<br />
CABLE ASSY.<br />
(a) Position parking brake operation handle with cable assy<br />
and tighten 2 lower mounting bolts LH.<br />
Tighten 2 lower mounting nuts.<br />
(c) Tighten 2 upper mounting bolts.<br />
36-7<br />
install the clamp between front parking brake cable and<br />
frame and the clamp between front parking brake and<br />
the other cables.<br />
8. INSTALL PARKING BRAKE SWITCH.<br />
(a) Install parking brake switch.<br />
(b) Connect the connector to parking brake switch.<br />
9. INSTALL PARKING BRAKE SHIELD ASSY. (Refer to “Chapter 83 instrument panel - dashboard,<br />
10. CONNECT BATTERY NEGATIVE CABLE.<br />
36-8<br />
PARKING BRAKE - REAR PARKING BRAKE OPERATION ASSY<br />
REAR PARKING BRAKE OPERATION ASSY<br />
2. REMOVE REAR BRAKE LH. (Refer to “Chapter 35 barake - rear brake, overhaul”)<br />
3. REMOVE REAR PARKING BRAKE OPERATION ASSY LH.<br />
Disconnect the connecting between rear parking brake operation assy LH and rear brake actuator<br />
lever. (Refer to” Chapter 35 brake - rear brake, overhaul”)<br />
Remove 2 bolts fitting rear parking brake operation assy<br />
LH to brake backing plate.<br />
Remove bolts from the front of brake backing plate.<br />
Disconnect rear parking brake operation assy LH from<br />
parking brake rocker arm with bracket assy.<br />
all brackets.<br />
Remove rear parking brake operation assy LH.<br />
4. INSTALL REAR PARKING BRAKE OPERATION ASSY<br />
(a) Install 2 mounting bolts fitting rear parking brake operation<br />
assy LH to brake backing plate.<br />
Install bolts from the front of brake backing plate.<br />
36-9<br />
Connect rear parking brake operation assy LH to parking<br />
brake rocker arm with bracket assy.<br />
Connect rear parking brake operation assy LH to all<br />
brackets.<br />
Connect rear parking brake operation assy LH to rear<br />
brake actuator lever. (Refer to” Chapter 35 brake - rear<br />
5. INSTALL REAR BRAKE LH. (Refer to “Chapter 35 barake - rear brake, overhaul”)<br />
6. INSTALL REAR WHEEL LH. (Refer to “Chapter 33 wheel and tire - rear wheel and tire,<br />
7. REMOVE AND INSTALL REAR PARKING BRAKE OPERATION ASSY RH.<br />
ABS ACTUATOR .........................................................................35-37<br />
ADJUSTMENT(BRAKE PEDAL)....................................................35-7<br />
ADJUSTMENT(FRONT WHEEL ALIGNMENT) ............................31-8<br />
ADJUSTMENT(PARKING BRAKE SYSTEM) ...............................36-2<br />
AIR FILTER ASSY ...................................................................... 14C-7<br />
AXLE SHAFT ASSY.....................................................................34-43<br />
BATTERY.................................................................................. 20C-18<br />
BLEEDING(BRAKE FLUID) ...........................................................35-4<br />
BRAKE FLUID................................................................................35-4<br />
BRAKE PEDAL ..............................................................................35-6<br />
BRAKE SYSTEM ...........................................................................35-1<br />
CENTER SUPPORT BEARING...................................................34-12<br />
COMPONENTS(BRAKE PEDAL) ..................................................35-6<br />
COMPONENTS(COOLING SYSTEM)........................................ 17C-2<br />
COMPONENTS(EXHAUST PIPE).............................................. 16C-1<br />
COMPONENTS(FUEL SYSTEM) ............................................... 12C-4<br />
COMPONENTS(INTAKE AIR SYSTEM) .................................... 14C-2<br />
COMPONENTS(REAR SUSPENSION) ........................................32-2<br />
COMPONENTS(STARTER) ..................................................... 20C-10<br />
COMPOSITION(BATTERY)...................................................... 20C-18<br />
COOLANT................................................................................... 17C-7<br />
COOLING SYSTEM.................................................................... 17C-1<br />
DIESEL ENGINE CONTROL SYSTEM ...................................... 11C-1<br />
DRIVE PINION.............................................................................34-50<br />
ELECTRONIC ACCELERATOR PEDAL .................................. 12C-20<br />
ENGINE ACCESSORY BELT................................................... 15C-12<br />
ENGINE CONTROL MODULE (ECM) ........................................ 11C-2<br />
ENGINE MECHANICAL PART ................................................... 15C-1<br />
ENGINE OIL................................................................................ 18C-2<br />
FRONT BRAKE............................................................................35-20<br />
FRONT PARKING BRAKE OPERATION ASSY............................36-4<br />
FRONT SUSPENSION ..................................................................31-1<br />
FRONT WHEEL ALIGNMENT .......................................................31-8<br />
FRONT WHEEL AND TIRE ...........................................................33-8<br />
FUEL FILLER CAP ....................................................... 12C-15, 13C-1<br />
FUEL FILLER DOOR ................................................................ 12C-12<br />
FUEL FILLER DOOR LOCK LATCH ASSY.............................. 12C-13<br />
FUEL FILLING TUBE AND BREATHER TUBE ASSY ............. 12C-16<br />
FUEL LEVEL SENSOR AND BRACKET ASSY ....................... 12C-10<br />
FUEL SYSTEM ........................................................................... 12C-1<br />
GENERATOR..............................................................................20C-4<br />
INSPECTION(BATTERY)..........................................................20C-21<br />
INSPECTION(DRIVE PINION).................................................... 34-50<br />
INSPECTION(FUEL FILLER CAP) ...............................12C-15, 13C-1<br />
INSPECTION(FUEL FILLING TUBE AND BREATHER<br />
TUBE ASSY) .............................................................................12C-16<br />
INSPECTION(PROPELLER SHAFT ASSY) ................................. 34-4<br />
INTAKE AIR PIPE AND HOSE....................................................14C-4<br />
INTAKE AIR SYSTEM.................................................................14C-1<br />
INTERCOOLER INTAKE AIR PIPE ..........................................14C-11<br />
LUBRICATION SYSTEM.............................................................18C-1<br />
OIL FILTER .................................................................................18C-4<br />
OIL PAN ......................................................................................18C-6<br />
OIL PUMP ...................................................................................18C-7<br />
ON VEHICLE INSPECT(COOLING SYSTEM) ...........................17C-5<br />
ON-VEHICLE INSPECTION(FRONT SUSPENSION) .................. 31-7<br />
ON-VEHICLE INSPECTION(REAR BRAKE) .............................. 35-26<br />
ON-VEHICLE INSPECTION(REAR SUSPENSION)..................... 32-3<br />
ON-VEHICLE INSPECTION(TIRE AND WHEEL ASSY) .............. 33-4<br />
OVERHAUL(AXLE SHAFT ASSY).............................................. 34-43<br />
OVERHAUL(CENTER SUPPORT BEARING) ............................ 34-12<br />
OVERHAUL(ENGINE ACCESSORY BELT) .............................15C-12<br />
OVERHAUL(FRONT BRAKE)..................................................... 35-20<br />
OVERHAUL(GENERATOR)........................................................20C-4<br />
OVERHAUL(OIL PUMP) .............................................................18C-7<br />
OVERHAUL(REAR BRAKE) ....................................................... 35-27<br />
OVERHAUL(REAR LEAF SPRING ASSY) ................................... 32-6<br />
OVERHAUL(REAR SHOCK ABSORBER).................................... 32-4<br />
OVERHAUL(STARTER)............................................................20C-11<br />
OVERHAUL(VACUUM BOOSTER WITH BRAKE MASTER CYLIN-<br />
DER ASSY) ................................................................................. 35-14<br />
PARKING BRAKE SYSTEM ......................................................... 36-1<br />
PRECAUTION(BRAKE SYSTEM)................................................. 35-1<br />
PRECAUTION(COOLING SYSTEM) ..........................................17C-1<br />
PRECAUTION(DIESEL ENGINE CONTROL SYSTEM).............11C-1<br />
PRECAUTION(ENGINE MECHANICAL PART)..........................15C-1<br />
PRECAUTION(FRONT SUSPENSION)........................................ 31-1<br />
PRECAUTION(FUEL SYSTEM)..................................................12C-1<br />
PRECAUTION(INTAKE AIR SYSTEM).......................................14C-1<br />
PRECAUTION(LUBRICATION SYSTEM)...................................18C-1<br />
PRECAUTION(PROPELLER SHAFT ASSY)................................ 34-1<br />
PRECAUTION(STARTING AND CHARGING SYSTEM)............20C-1<br />
PRINCIPLE(VEHICLE SPEED SENSOR) ..................................11C-8<br />
PROBLEM SYMPTOMS TABLE ................................................... 35-2<br />
PROBLEM SYMPTOMS TABLE(PARKING BRAKE SYSTEM) ... 36-1<br />
PROBLEM SYMPTOMS TABLE(REAR SUSPENSION) .............. 32-1<br />
PROBLEM SYMPTOMS TABLE(STARTING AND CHARGING SYS-<br />
TEM)............................................................................................20C-2<br />
PROBLEM SYMPTOMS TABLE(TIRE AND WHEEL ASSY) ....... 33-3<br />
PROPELLER SHAFT ASSY.......................................................... 34-1<br />
RADIATOR ................................................................................17C-14<br />
REAR BRAKE ............................................................................. 35-26<br />
REAR LEAF SPRING ASSY ......................................................... 32-6<br />
REAR SHOCK ABSORBER.......................................................... 32-4<br />
REAR SUSPENSION .................................................................... 32-1<br />
REPLACEMENT(ABS ACTUATOR) ........................................... 35-37<br />
REPLACEMENT(AIR FILTER ASSY) .........................................14C-7<br />
REPLACEMENT(BATTERY).....................................................20C-24<br />
REPLACEMENT(BRAKE PEDAL) ................................................ 35-9<br />
REPLACEMENT(COOLANT)......................................................17C-7<br />
REPLACEMENT(ELECTRONIC ACCELERATOR PEDAL) .....12C-20<br />
REPLACEMENT(ENGINE ASSY)...............................................15C-2<br />
REPLACEMENT(ENGINE OIL)...................................................18C-2<br />
REPLACEMENT(EXHAUST PIPE) .................................16C-2, 16C-3<br />
REPLACEMENT(FRONT PARKING BRAKE<br />
OPERATION ASSY)...................................................................... 36-4<br />
REPLACEMENT(FRONT WHEEL AND TIRE) ............................. 33-8<br />
LATCH ASSY) ...........................................................................12C-13<br />
REPLACEMENT(FUEL FILLING DOOR)..................................12C-12<br />
REPLACEMENT(FUEL LEVEL SENSOR AND BRACKET<br />
ASSY)........................................................................................12C-10<br />
REPLACEMENT(INTAKE AIR PIPE AND HOSE) ......................14C-4<br />
REPLACEMENT(INTERCOOLER INTAKE AIR PIPE) .............14C-11<br />
REPLACEMENT(OIL FILTER) ....................................................18C-4<br />
REPLACEMENT(OIL PAN) .........................................................18C-6<br />
REPLACEMENT(RADIATOR)...................................................17C-14<br />
REPLACEMENT(RESERVIOR) ..................................................17C-9<br />
REPLACEMENT(VACUUM BOOSTER LINE) ............................ 35-18<br />
REPLACEMENT(WHEEL SPEED SENSOR) ............................. 35-40<br />
RESERVIOR ...............................................................................17C-9<br />
STARTER..................................................................................20C-10<br />
STARTING AND CHARGING SYSTEM......................................20C-1<br />
TIRE AND WHEEL ASSY ............................................................. 33-1<br />
ASSY........................................................................................... 35-14<br />
VEHICLE SPEED SENSOR........................................................11C-8<br />
WHEEL SPEED SENSOR .......................................................... 35-40<br />
USE AND MAINTENANCE(BATTERY) ....................................20C-19<br />
TRANSMISSION OPERATION MECHANISM ASSY ........................ 41-1<br />
COMPONENTS ........................................................................... 41-1<br />
REPLACEMENT .......................................................................... 41-3<br />
TRANSMISSION ASSY(YANCHENGZHONGMA ZM001)................ 41-8<br />
DIAGRAM OF COMPONENTS.................................................... 41-8<br />
REPLACEMENT ........................................................................ 41-10<br />
DISASSEMBLY AND ASSEMBLY............................................. 41-15<br />
CLUTCH CASE ................................................................................ 41-39<br />
DIAGRAM OF COMPONENTS.................................................. 41-39<br />
SERVICE ................................................................................... 41-40<br />
REAR PART ASSEMBLY................................................................ 41-43<br />
DIAGRAM OF COMPONENTS.................................................. 41-43<br />
SERVICE ................................................................................... 41-44<br />
FORK SHAFT ASSEMBLY.............................................................. 41-48<br />
DIAGRAM OF COMPONENTS.................................................. 41-48<br />
SERVICE ................................................................................... 41-49<br />
INPUT SHAFT ASSEMBLY ............................................................. 41-51<br />
DIAGRAM OF COMPONENTS.................................................. 41-51<br />
SERVICE ................................................................................... 41-52<br />
OUTPUT SHAFT ASSEMBLY ......................................................... 41-54<br />
DIAGRAM OF COMPONENTS.................................................. 41-54<br />
SERVICE ................................................................................... 41-55<br />
COUNTER SHAFT ASSEMBLY ...................................................... 41-62<br />
DIAGRAM OF COMPONENTS.................................................. 41-62<br />
SERVICE ................................................................................... 41-63<br />
REVERSE SHAFT ASSEMBLY....................................................... 41-67<br />
DIAGRAM OF COMPONENTS.................................................. 41-67<br />
SERVICE ................................................................................... 41-68<br />
SERVICE FOR OTHER IMPORTANT COMPONENTS OF TRANS-<br />
MISSION.................................................................................... 41-70<br />
TRANSMISSION ASSY(TANGSHANAIXIN) ................................... 41-73<br />
REPLACEMENT ........................................................................ 41-73<br />
41<br />
TRANSMISSION - TRANSMISSION OPERATION MECHANISM ASSY<br />
TRANSMISSION OPERATION MECHANISM ASSY<br />
41-1<br />
1 Shifting Control Lever Ball Assy<br />
2 Dust Cover<br />
3 Big Washer<br />
4 Bolt And Spring Washer Set<br />
5 Operation Mechanism Assy<br />
41-2<br />
1 Flexible Shaft Assy<br />
2 Flexible Shaft Bracket Assy No.1<br />
Bolt,spring Washer And Flat Washer<br />
6 Flexible Shaft Bracket Assy No.2<br />
7 Flexible Shaft Bracket Assy No.3<br />
41-3<br />
1. STOP THE ENGINE AND PARK THE VEHICLE ON LEVEL GROUND WITH PARKING BRAKE.<br />
2. REMOVE TRANSMISSION SHIFTING CONTROL LEVER<br />
BALL ASSY AND DUST COVER.<br />
Using plastic ripping bar,pry off retaining trim frame of<br />
transmission Shifting Control Lever dust cover.<br />
Don’t destroy dust cover.<br />
Remove shifting control lever ball assy by turning it<br />
counterclockwise, and remove dust cover.<br />
3. REMOVE DASHBOAD. (Refer to “Chapter 83 instrument panel - darshboad, replacement”)<br />
4. REMOVE TRANSMISSION OPERATION MECHANISM<br />
ASSY AND CABLES.<br />
Disconnect flexible shaft of gear shifting cable from<br />
transmission operation mechanism assy, then remove<br />
cable clamp from transmission operation mechanism<br />
Disconnect flexible shaft gear selecting cable from<br />
41-4<br />
Remove 4 mounting bolts of transmission operation<br />
mechanism assy.<br />
Remove transmission operation mechanism assy.<br />
Remove 2 bolts fitting cables to lower body.<br />
41-5<br />
Remove cotter pin,disconnect flexible shaft of gear<br />
shifting cable and flexible shaft of gear selecting cable<br />
from transmission assy.<br />
(g) Remove cables from brackets located at transmission<br />
Along the end of cables,remove 1 cable clamp located at<br />
the bottom of body and 2 clamps located at subframe.<br />
Remove gear shifting cable and gear selecting cable<br />
5. INSTALL TRANSMISSION OPERATION MECHANISM<br />
(a) Position cables.<br />
(b) Connect flexible shaft of gear shifting cable and flexible<br />
shaft of gear selecting cable to transmission assy.<br />
(c) Install cables to bracket located at transmission assy.<br />
Tighten 2 bolts fitting cables to lower body.<br />
41-6<br />
Along the end of cables, install 1 cable clamp located at<br />
Position transmission operation mechanism assy.<br />
Tighten 4 mounting bolts.<br />
(h) Install gear selecting cable clamp to transmission<br />
operation mechanism assy,then connect flexible shaft of<br />
gear selecting cable to transmission operation<br />
• Make sure that the transmission operation mechanism<br />
is in neutral position before connecting the flexible<br />
shaft to it, or adjust it.<br />
• Apply lithium base grease NO.3 to joint of transmission<br />
operation michanism assy and flexible shaft of cable.<br />
(i) Install gear shifting cable clamp to transmission<br />
gear shifting cable to transmission operation mechanism<br />
shaft to it,or adjust it.<br />
6. INSTALL DASHBOAD. (Refer to “Chapter 83 instrument panel - darshboad, replacement”)<br />
41-7<br />
7. INSTALL TRANSMISSION SHIFTING CONTROL LEVER<br />
Install dust cover, turn shifting control lever ball clockwise<br />
in order to install it.<br />
Install retaining trim frame of dust cover.<br />
Don’t detroy dust cover.<br />
8. INSPECT TRANSMISSION OPERATION MECHANIZE ASSY FOR SMOOTH SHIFTING, NO<br />
STICKING AND LOOSENING.<br />
41-8<br />
TRANSMISSION - TRANSMISSION ASSY(YANCHENGZHONGMA ZM001)<br />
TRANSMISSION ASSY(YANCHENGZHONGMA ZM001)<br />
41-9<br />
1 Ball head washer<br />
2 Control lever cover assembly<br />
3 Locating pin<br />
4 Breather plug<br />
5 Shift extension bar assembly<br />
6 Dust cover<br />
7 Shift lever spring cover<br />
8 Shift lever spring<br />
9 Sealing washer<br />
10 Positioning mechanism assembly<br />
11 Odometer driven gear assembly<br />
12 Oil guiding groove<br />
13 Shift block<br />
14 Locating bolt of shift block<br />
15 Steel ball<br />
16 Self-locking spring<br />
17 Plug<br />
18 Oil storage box<br />
19 Stopper pin<br />
20 Shift shaft<br />
21 Shift fork, lock and pin assembly<br />
22 Shift lever<br />
23 Odometer drive pinion retainer ring<br />
24 Odometer drive pinion<br />
25 Stopper<br />
26 Stopper spring<br />
27 Stopper shaft<br />
28 Intermediate plate assembly<br />
29 Case<br />
30 Hexagon head plug<br />
31 Sealing washer<br />
32 Reverse switch assembly<br />
33 Hexagon head screw plug<br />
34 Front cover oil seal<br />
35 Front cover<br />
36 Bowl-shaped expansion plug<br />
37 Clutch release fork assembly<br />
38 Clutch release fork shield<br />
39 Clutch case<br />
40 Clutch release fork stud<br />
41 Release bearing assembly<br />
41-10<br />
1. STOP THE ENGINE. PARK VEHICLE ON LEVELGROUND WITH PARKING BRAKE AND SHIFT IN<br />
NEUTRAL POSITION.<br />
3. LIFT VEHICLE.<br />
4. REMOVE DRAIN PLUG BY DOWNSIDE AND DRAIN<br />
5. DISCONNECT TRANSMISSION ASSY FROM OTHER<br />
PARTS,THEN REMOVE TRANSMISSION ASSY.<br />
(a) Remove crankshaft position sensor located at the top of<br />
transimission.<br />
Be careful not to be scalded by exhaust pipe.<br />
Remove vehicle speed sensor located at the left of<br />
transmission.<br />
41-11<br />
Remove the back-up lamp switch located at the right of<br />
Remove the clutch slave cylinder assy. (Refer to “Chapter<br />
42 clutch - clutch slave cylinder assy, replacement”)<br />
Remove back nuts,disconnect flexible shaft of gear<br />
Remove 2 mounting bolts of cable bracket and cable<br />
bracket located at transmission case.<br />
Remove 2 mounting bolts and 2 nut bolts of transmission<br />
front cover and transmission front cover.<br />
Remove starter. (Refer to “Chapter 20A starting and<br />
charging - starter, overhaul”)<br />
Remove propeller shaft assy. (Refer to “Chapter 34 axle<br />
and propeller shaft - propeller shaft assy, overhaul”)<br />
41-12<br />
Remove 4 nuts and disconnect the transmission from<br />
lifting lug.<br />
• Use jack to support transmission assy and engine<br />
before operation.<br />
• Be careful not to be scalded by exhaust pipe.<br />
Remove 5 bolts and disconnect transmission assy from<br />
engine. Remove the transmission assy.<br />
There are five bolts,one is used for retaining air condition<br />
pipe, another one which isn’t installed temporarily is used<br />
for retaining gear shifting cable bracket.<br />
6. INSTALL TRANSMISSION ASSY, AND CONNECT OTHER<br />
PARTS TO TRANSMISSION ASSY.<br />
Support the transmission assy by jack and shift in one of<br />
forward gears. Rotate the input shaft and align with the<br />
spline of clutch disk at the same time. Then insert the<br />
input shaft completely and shift in neutral position.<br />
Adopt protective measures to prevent from injuring when<br />
supporting by jack.<br />
(b) Install bolts with hand to connect transmission to engine.<br />
Support the transmission assy by jack and connect the<br />
transmission assy to lifting lug. Install 4 bolts with hand.<br />
(d) Tighten 4 nuts of lifting lug.<br />
Torque:41 ~ 51N•m<br />
41-13<br />
Tighten bolts to connect transmission assy to engine.<br />
Torque: 42.2 ~ 53.9 N•m<br />
Diagonally tighten all bolts in order to install closely.<br />
Install propeller shaft assy. (Refer to “Chapter 34 axle<br />
Install starter. (Refer to “Chapter 20A starting and<br />
Position transmission font cover,tighten 2 mounting bolts<br />
and 2 nut bolts.<br />
Torque: 7.8 ~ 9.8 N•m<br />
Position cable bracket located at transmission case and<br />
Tighten the through bolt which is used to connect transmission<br />
to engine to 42.2 ~ 53.9 N•m.<br />
(j) Position flexible shaft of gear shifting cable and flexible<br />
shaft of gear selecting cable,then tighten mounting nuts.<br />
Make sure the shift rocker arm in neutral before installation.<br />
Torque: 22 ~ 28 N•m<br />
Remove jack.<br />
Install the clutch slave cylinder assy. (Refer to “Chapter<br />
42 clutch - clutch slave cylinder assy,replacement”)<br />
Install the back-up lamp switch located at the right of<br />
41-14<br />
Install vehicle speed sensor located at the left of<br />
Install vehicle speed sensor located at the top of<br />
7. REMOVE FILLER PLUG AND FILL TRANSMISSION<br />
10. TRANSMISSION RUNNING - IN TEST.<br />
(a) Keep the rotate speed around 1500 r/min; keep the fluid temperature upper 15 centidegree; without<br />
load; keep transmission run more than 15 min in neutral position; keep transmission run more than 20<br />
min in other positions.<br />
(b) Inspect the transmission for smooth shifting.<br />
(c) Check there is no fricative and clash during running-in test.<br />
(d) Check there is no leakage around trasmission.<br />
(e) Drain out transmission fluid and clean inside of transmission after running-in test. Fill transmission fluid.<br />
41-15<br />
DISASSEMBLY AND ASSEMBLY<br />
1. Place the transmission assembly on the<br />
disassembling table, and shift the transmission in<br />
neutral<br />
Before disassembling the transmission assembly, drain the<br />
lubricating oil inside, and disassemble the transmission after<br />
cleaning the surface.<br />
2. Dismantle the clutch case assembly<br />
(a) Pull out the clutch release fork outward slightly, make the<br />
clutch release fork leave the release bearing locating<br />
snap spring.<br />
(b) Push the clutch release fork outward for a certain<br />
distance, which makes it released from the clutch<br />
release fork spherical support pillar.<br />
(c) Remove the clutch release fork and fork dustproof cover;<br />
remove the separate bearing from input shaft gland.<br />
Dismantle the fixing bolts connecting the clutch case and<br />
transmission case.<br />
When dismantling, evenly loose the fixing bolts along the<br />
diagonal direction, and avoid omitted dismantlement.<br />
Remove the clutch case assembly.<br />
If the clutch case tightly connects with the transmission case,<br />
knock the proper part of clutch case with rubber hammer, so as<br />
to remove the clutch case.<br />
41-16<br />
3. Dismantle the front cover assembly<br />
(a) Dismantle the fixing bolts on the transmission front cover.<br />
Remove the front cover assembly.<br />
If the front cover assembly tightly connects with the transmission<br />
case, knock the proper part of front cover with rubber hammer,<br />
so as to remove the clutch case.<br />
4. Dismantle the variable speed control cover assembly<br />
(a) Dismantle the locating mechanism components of gear<br />
selecting lever and gear shifting lever, and remove the<br />
sealing washer.<br />
The locating mechanism components of gear selecting lever and<br />
gear shifting lever should be two symmetrical components,<br />
dismantle the two simultaneously as much as possible to<br />
facilitate the dismantling of the following components.<br />
Dismantle the fixing bolts of variable speed control cover<br />
and rear part assembly.。<br />
41-17<br />
Remove the variable speed control cover assembly.<br />
5. Dismantle the transmission rear part assembly<br />
Dismantle the locating bolts of shift lever.<br />
Dismantle the stopper spring plug, remove the stopper<br />
spring and steel balls of fifth gear fork shaft with the bar<br />
magnet.<br />
Dismantle the fixing bolts of odometer driven gear<br />
41-18<br />
Remove the odometer driven gear assembly.<br />
Dismantle the fixing bolts of rear case assembly<br />
diagonal direction, and avoid deforming the case.<br />
Remove the transmission rear case assembly.<br />
Firstly, slowly remove a certain distance until the rear case<br />
assembly released from the locating pin and the shift lever could<br />
be seen, reverse the rear case assembly, make the shift lever<br />
leave the groove of shift fork shaft, and then remove the rear<br />
case assembly.。<br />
6. Dismantle the transmission front case assembly<br />
(a) Remove the input shaft and counter shaft front bearing<br />
stop ringwith calipers.<br />
41-19<br />
Remove the transmission case assembly towards the<br />
direction of input shaft end.<br />
Slightly knock the transmission case with rubber hammer if<br />
necessary, so as to separate the bearing from the case.。<br />
7. Dismantle the odometer drive pinion<br />
(a) Dismantle the outer retainer ring of odometer drive pinion<br />
with calipers.<br />
Remove the odometer drive pinion; dismantle the inner<br />
retainer ring of odometer drive pinion.<br />
8. Dismantle the control part of the intermediate plate<br />
(a) Dismantle each locating bolt of fork shaft with Allen<br />
wrench, remove the spring and steel ball with magnet<br />
one by one.<br />
41-20<br />
Dismantle each fork, lock and pin assembly, elastic<br />
cylindrical pin, locating screws of first and second shift<br />
fork, clamping retainer ring.<br />
When dismantling the shift fork, lock, pin and elastic cylindrical<br />
pin, the available punch could be less than Φ5 (such as Φ4. 5),<br />
the pin should be struck out from the other side of the figure.<br />
When dismantling the fork shaft retainer ring or elastic cylindrical<br />
pin assembly, avoid vigorous knocking, which may cause the<br />
fork shaft bent or damaged.<br />
(c) Rotate the fifth gear shift shaft and pull out it, and remove<br />
the fifth gear shift fork, interlocking ball of fifth reverse<br />
fork shaft.<br />
Pull out fifth reverse lead block fork shaft and remove the<br />
fifth reverse shift lead block.<br />
Remove the interlock ball inside the intermediate plate<br />
assembly with the bar magnet, dismantle the reverse<br />
shift shaft and reverse shift block rocker assembly, and<br />
after dismantling the reverse shift shaft, remove the<br />
interlock pin.<br />
41-21<br />
Remove the interlock pin, dismantle the shift shafts of<br />
first and second gears, remove the interlock pin inside<br />
the intermediate plate assembly with the bar magnet.<br />
Pull out the short interlock pin; dismantle the shift shafts<br />
of third and fourth gears.<br />
Remove the shift forks of first and second gears, and<br />
shift forks of third and fourth gears upward.<br />
9. Dismantle the moving part of intermediate plate<br />
(a) Dismantle the retainer ring of fifth gear synchronous<br />
bevel on the rear end of fifth counter shaft with calipers.<br />
41-22<br />
Remove the fifth gear synchronous bevel gear of the<br />
counter shaft.<br />
Dismantle the fifth gear synchronizer and fifth gear input<br />
gear assembly of the counter shaft.<br />
Remove the fifth gear needle bearing, fifth gear thrust<br />
washer and locking ball (Φ6. 35) of the counter shaft.<br />
Dismantle the retainer ring of output shaft fifth gear, and<br />
remove the fifth gear. Dismantle the fixing bolts of output<br />
shaft rear bearing backing plate with Allen wrench and<br />
remove the output shaft rear bearing backing plate.<br />
41-23<br />
Dismantle the fixing bolts of the reverse gear rocker arm<br />
bracket group.<br />
Remove the reverse gear rocker arm bracket group.<br />
Dismantle the fixing bolts of reverse gear idler shaft<br />
pressing plate with wrench and remove the reverse gear<br />
idler shaft pressing plate.<br />
Pull out the reverse gear idler assembly and the reverse<br />
gear idler shaft.<br />
41-24<br />
Dismantle the rear bearing stop rings of the output shaft<br />
and counter shaft with calipers.<br />
Dismantle the rear bearing of counter shaft with bearing<br />
puller.<br />
(l) Dismantle the counter shaft assembly from the<br />
intermediate plate assembly.<br />
Pull out the input shaft assembly (the roller pin inside the<br />
shaft should not missed), and the gear ring of third and<br />
fourth gears synchronizer.<br />
41-25<br />
Pull out the output shaft assembly, finish part of the<br />
assembly disassembly.<br />
10. Install the moving part of the intermediate plate<br />
Vertically fix the intermediate plate assembly on the<br />
working table, hold one end of the output shaft assembly,<br />
knock the intermediate plate assembly with rubber<br />
hammer at the same time, and install the output shaft<br />
assembly into intermediate plate assembly.<br />
Install the output shaft rear bearing stop ringwith snap<br />
ring plier.<br />
The stop ringshould be stuck with the intermediate plate<br />
assembly, and avoid the excessive axial clearance of output<br />
Press mount the input shaft bearing onto the input shaft;<br />
install the input shaft retainer ring with snap ring plier.<br />
41-26<br />
Coat the lithium base grease in the input shaft needle<br />
bearing hole, install the needle into the input shaft needle<br />
bearing hole, install the third and fourth gear<br />
synchronizer gear ring onto the input shaft.<br />
The input shaft has totally 13 needle bearings, avoid any<br />
omission.<br />
Install input shaft onto the output shaft, and install the<br />
three grooves of synchronizer ring corresponding with<br />
the three slide blocks on the synchronizer.<br />
Rotate the input shaft for several circles after installation, and<br />
check whether it smooth and with proper clearance, if any<br />
abnormal, pull out the input shaft and check whether the needle<br />
bearings are working well.<br />
Install the counter shaft into the intermediate plate<br />
assembly and hold the counter shaft, install the counter<br />
shaft rear bearing.<br />
The bearing ring groove should be installed outward and avoid<br />
reversely installing.<br />
Install the count shaft rear bearing stop ringwith snap<br />
assembly, and avoid the excessive clearance damaging other<br />
parts.<br />
41-27<br />
Install the reverse gear idler assembly and the reverse<br />
Rotate the idler shaft and make the pressing plate<br />
corresponding with the idler shaft groove, and make the<br />
pressing plate holes corresponding with the fixing bolt<br />
holes of intermediate plate assembly, install the<br />
connecting bolts of screw locking glue smeared idler<br />
shaft locking tab and fasten to specified torque.<br />
Torque: 15~20 N·m<br />
Install the two hollow locating pins to the intermediate<br />
plate assembly, and install the upper rocker arm bracket.<br />
Smear appropriate screw locking glue on the fixing bolts<br />
of rocker arm bracket assembly, install the intermediate<br />
plate assembly from the other side and fasten.<br />
Torque: 17~22 N·m<br />
41-28<br />
Smear the screw locking glue on the connecting bolts of<br />
output shaft rear bearing, install the rear bearing<br />
pressing plate with torque socket wrench and fasten the<br />
screws.<br />
Torque: 17~22 N·<br />
Install fifth gear shaft retainer ring and output shaft fifth<br />
gear.<br />
Install the locking ball and fifth gear thrust washer.<br />
After smearing the gear oil on counter shaft fifth gear<br />
needle bearing, install in onto counter shaft.<br />
(p)<br />
Install counter shaft fifth gear input gear and fifth gear<br />
synchronizer assembly.<br />
Because the input gear needle bearing of counter shaft fifth gear<br />
is semicircle bearing, avoid falling and omission when installing<br />
the gear.<br />
41-29<br />
(q)<br />
Cover the conical surface of fifth gear coupling gear with<br />
synchronizer gear ring, install the fifth gear coupling gear,<br />
align the synchronizer ring groove with the synchronizer<br />
slide block and install.<br />
(r)<br />
Select a fifth gear synchronizer retainer ring which may<br />
minimizes the axial clearance, install the fifth gear<br />
synchronizer retainer ring with calipers.<br />
(s)<br />
Measure the axial clearance of counter shaft fifth gear<br />
with feeler.<br />
Standard clearance: 0. 1~0. 3 mm<br />
Maximum clearance: 0. 3 mm<br />
11. Install the control part of the intermediate plate<br />
(a) Install the shift fork of first and second gears, and third<br />
and fourth gears.<br />
(b) Install the intermediate plate assembly and shift fork into<br />
the shift shaft of third and fourth gears.<br />
41-30<br />
Knock the elastic cylindrical pin assembly into the third<br />
and fourth gear shift fork with punch and hammer (the<br />
opening direction of elastic cylindrical pin should be<br />
towards the fork shaft axis).<br />
Avoid vigorous knocking when installing the fork shaft retainer<br />
ring or elastic cylindrical pin assembly, so as to prevent fork<br />
shaft bent or damaged, and the fork shaft retainer ring or elastic<br />
cylindrical pin assembly could also be installed in place by pliers.<br />
Smear the interlock pin with grease, and install it on the<br />
first and second gear shift shaft.<br />
Install the short interlock pin into the intermediate plate<br />
with the bar magnet, install the first and second gear shift<br />
shaft into first and second gear shift fork and<br />
Install the fixing bolts of first and second gear shift, fasten<br />
Torque: 13~17 N·m<br />
Smear the screw locking glue on the fixing bolts.<br />
41-31<br />
Install the reverse block, reverse lever and two E-rings<br />
on the reverse gear rocker arm, the reverse arm open<br />
end should be installed on the reverse gear rocker arm<br />
Smear the grease on the interlock pin, and install it on<br />
reverse shift shaft.<br />
Install the interlock pin into intermediate plate assembly<br />
with the bar magnet, and install the reverse shift shaft<br />
into reverse lever and intermediate plate assembly.<br />
Knock the elastic cylindrical pin assembly into the<br />
reverse shift fork with punch and hammer (the opening<br />
direction of elastic cylindrical pin should be towards the<br />
fork shaft axis).<br />
cylindrical pin assembly could also be installed in place by<br />
pliers.。<br />
Install the lock ball into the fifth reverse gear lead block<br />
with the bar magnet, and install the fifth gear shift shaft.<br />
Install the interlock ball into the intermediate plate<br />
assembly with the bar magnet, install the fifth gear shift<br />
shaft into the intermediate plate assembly.<br />
41-32<br />
Install fifth gear shift fork.<br />
Knock the elastic cylindrical pin assembly into the fifth<br />
gear shift fork one by one with punch and hammer (the<br />
Install the fifth reverse shift shaft into the fifth reverse<br />
shift block and intermediate plate assembly.<br />
reverse shift block with punch and hammer (the opening<br />
41-33<br />
Knock the shift shaft retainer ring with steel bar or<br />
hammer.<br />
(r) Install the gear locating ball and spring (4 balls and 4<br />
springs) into the intermediate plate assembly.<br />
Install the short spring (fifth gear) into the bottom of intermediate<br />
plate assembly, smear the screw locking glue on each hexagon<br />
socket head bolts, fasten the plug to specified torque with Allen<br />
12. Install the odometer drive pinion<br />
(a) Install the retainer ring in odometer drive pinion in place<br />
with calipers, put in the locking ball of odometer drive<br />
pinion, and install the odometer drive pinion.。<br />
Install the retainer ring in odometer drive pinion in place<br />
41-34<br />
13. Install transmission case<br />
(a) Evenly smear the antioxidant sealant on the contacting<br />
surface of transmission front case and intermediate plate<br />
Install the transmission case on the intermediate plate<br />
assembly, and ensure the shift fork shaft aligning with the<br />
object lead hole. Knock the hard part of the front case<br />
with rubber hammer if necessary, which could make it<br />
install in place.<br />
Install 2 stop rings on the input shaft bearing and counter<br />
shaft front bearing with snap ring plier.<br />
14. Install the case assembly, shift shaft and shift block<br />
(a) Install the components inside the rear case before the<br />
assembly, such as limiting mechanism, oil guiding<br />
groove, and evenly smear antioxidant sealant on the<br />
contacting surface of rear case and intermediate plate<br />
When installing the rear case, align the select and shift lever with<br />
select and shift lever shaft with hands and install in place, do not<br />
fasten the fixing bolts of select and shift gear right now. Insert<br />
the select and shift lever arm into the third and fourth gear fork<br />
shaft groove, align the fifth reverse shift shaft with the rear case<br />
installation hole, and push the rear case.<br />
41-35<br />
Install and fasten the fixing bolts on rear case.<br />
Torque: 30~45 N·m<br />
Vertically install the driven gear assembly of odometer.<br />
nstall the fixing bolt of odometer driven gear assembly<br />
and fasten to specified torque.<br />
Install the fifth reverse guide block locating ball, self<br />
locking spring and smear appropriate screw locking glue<br />
on the threads of the hexagon socket head bolts and<br />
41-36<br />
Smear appropriate screw locking glue on the threads of<br />
shift block locating bolt, install and fasten the shift block<br />
fixing bolt.<br />
15. After assembling the transmission front and rear housing, the followings should be checked.<br />
(a) Check whether the input shaft and output shaft could rotate flexibly.<br />
(b) Check whether each gear is clear and reliable, and whether there is reverse lock function.<br />
16. Install the left locating mechanism components.<br />
(a) Install the seal washer on the locating mechanism<br />
Distinguish the left one and right one when installing, the left<br />
locating mechanism components have smaller elastic force<br />
(look the input shaft from the transmission output shaft).<br />
(b) Fasten the locating mechanism components.<br />
Torque: 30~50 N·<br />
17. Install the transmission control lever cover<br />
(a) Smear appropriate antioxidant sealant on the contacting<br />
surface of transmission control lever cover and rear<br />
case.<br />
Install the fixing bolts of transmission control lever cover<br />
41-37<br />
18. Install the transmission front bearing cover<br />
Install the oil seal into the front bearing cover.<br />
Evenly smear the antioxidant sealant on the contacting<br />
surface of transmission front bearing cover and front<br />
case, and install the front bearing cover.<br />
Smear appropriate sealant on the threads of hexagon<br />
head bolt.<br />
Install the bolts and fasten to specified torque.<br />
19. Install the clutch cover<br />
(a) Align and install the clutch case location hole to the<br />
Install the fixing bolt of clutch case and fasten to<br />
When fastening the bolts, diagonally fasten the bolts in several<br />
times as much as possible, and avoid the case deformation or<br />
case damage caused by unevenly forced bolts.<br />
(c) Install the studof clutch release fork and fasten to<br />
41-38<br />
Install the clutch release fork, fork housing and release<br />
20. Install the reverse switch, filling plug, drain plug<br />
Torque: 30~50 N·m<br />
21. Finish the disassembly and assembly of transmission assembly<br />
CLUTCH CASE<br />
TRANSMISSION - CLUTCH CASE<br />
41-39<br />
1 Clutch release fork housing<br />
2 Clutch release fork assembly<br />
4 Clutch release fork stud<br />
5 Release bearing subassembly<br />
3 Clutch case<br />
41-40<br />
1. Dismantle the clutch case assembly<br />
(a) Unlock the spring fastener connecting the clutch release<br />
bearing and the clutch release fork.<br />
release fork support pillar.<br />
(c) Remove the clutch release bearing; remove the clutch<br />
release fork from the clutch case. This could avoid<br />
dismantling the dust cover of clutch release fork.<br />
Dismantle the coupling bolts connecting the clutch case<br />
and the transmission case.<br />
If the clutch case is tightly connected with the transmission case,<br />
the rubber hammer could be used for knocking the clutch case,<br />
Dismantle the clutch release fork support pillar.<br />
41-41<br />
Dismantle the clutch release fork housing<br />
The clutch housing is soft gelatinous material, avoid using sharp<br />
knives when dismantling<br />
2. Install the clutch case assembly<br />
(a) Install the clutch release fork housing.<br />
Install the clutch release fork stud and fasten to specified<br />
torque.<br />
Align and install the location hole of clutch case to<br />
41-42<br />
Install the clutch case fixing bolt and fasten to specified<br />
When installing, fasten the bolts evenly along the diagonal<br />
direction for several times, and avoid housing deformation<br />
during fastening.<br />
3. Finish the service of clutch case<br />
REAR PART ASSEMBLY<br />
TRANSMISSION - REAR PART ASSEMBLY<br />
41-43<br />
5 Sealing washer<br />
6 Locating mechanism components<br />
7 Odometer driven gear assembly<br />
8 Steel ball<br />
9 Self-locking spring<br />
10 Plug<br />
15 Stopper pin<br />
16 Shift shaft<br />
17 Shift fork, lock and pin assembly<br />
18 Shift lever<br />
19 Stopper block<br />
20 Stopper spring<br />
21 Stopper shaft<br />
11 Oil storage box<br />
41-44<br />
1. Dismantle the transmission rear part assembly.<br />
(a) Pull out the gear selecting shaft and gear shifting shaft,<br />
and remove the gear shifting block assembly.<br />
Dismantle the fixing bolt of oil guiding groove.<br />
Remove the oil guiding groove.<br />
Dismantle the fixing bolts of oil storage box and remove<br />
the oil storage box.<br />
41-45<br />
Dismantle the plug cover bolts of elastic cylindrical pin<br />
with Allen wrench, and dismantle the elastic cylindrical<br />
pin with proper drift pin.<br />
Pull out the reverse limit assembly.<br />
Strike out the shift fork, lock and pin assembly with<br />
hammer and drift pin, dismantle the shift shaft and shift<br />
Strike out the reverse limit pin with hammer and drift pin,<br />
and dismantle the stopper block, stopper spring and<br />
stopper shaft.<br />
41-46<br />
Check the wearing value of shift block; replace it if the<br />
requirements are not satisfied.<br />
Check the wearing of shift lever head; replace it if the<br />
2. Assemble the transmission rear part assembly<br />
(a) Assemble the stopper block, stopper spring and stopper<br />
shaft, install the stopper pin in place with copper bar.<br />
(b) Install the reverse limit assembly in place.<br />
Install the plug cover bolts of elastic cylindrical pin in<br />
place with Allen wrench.<br />
41-47<br />
of oil storage box, install the oil storage box and fasten<br />
the fixing bolts to specified torque.<br />
Torque: 5~10 N·m<br />
Smear appropriate screw locking glue oil on the bolts of<br />
guiding groove, install the oil guiding groove, and fasten<br />
the fixing bolt to specified torque.<br />
3. After assembling the rear case or transmission case, the followings should be checked<br />
(a) Check whether the rotations of input shaft and output shaft are flexible.<br />
4. Finish the service of transmission rear part assembly<br />
41-48<br />
FORK SHAFT ASSEMBLY<br />
TRANSMISSION - FORK SHAFT ASSEMBLY<br />
1 Elastic cylindrical pin<br />
2 Fifth gear shift fork<br />
3 Shift fork, lock and pin assembly<br />
4 Fifth reverse gear shift guide block<br />
5 Clamping ring<br />
6 Short interlock pin<br />
7 First and second gear shift shaft<br />
8 Interlock guide pillar<br />
9 Fifth reverse shift shaft<br />
10 Third and fourth gear shift shaft<br />
11 Interlock pin<br />
12 Reverse gear shift fork shaft<br />
13 Steel ball<br />
14 Fifth gear shift fork shaft<br />
15 Stopper spring screw plug<br />
16 Stopper spring<br />
17 Intermediate plate<br />
18 First and second gear shift fork<br />
19 Third and fourth gear shift fork<br />
20 Reverse gear shift lever<br />
Locating screw of first and second gear<br />
shift fork<br />
22 Reverse gear shift block<br />
Reverse gear rocker arm bracket<br />
24 Reverse gear rocker arm<br />
25 Split washer<br />
41-49<br />
During the motion, the car jump to neutral, different to engage a gear, out of gear etc. it may be caused by:<br />
• The fork axis circular groove excessively worn, the interlock pin excessively worn, the spring generated<br />
elastic deformation.<br />
• The fork working surface is excessively worn.<br />
Due to these reasons, the following checks should be performed to the components of fork shaft assembly.<br />
1. Check the free length of the self locking spring<br />
Standard value: 31. 6 mm<br />
Limitation value: 30. 1 mm<br />
2. Check the wearing of locking ball.<br />
3. Check the fork head thickness of fork<br />
Standard value: 10. 00 mm<br />
Limitation value: 9. 00 mm<br />
4. Check the wearing of the connection between<br />
moving shaft and intermediate plate assembly<br />
41-50<br />
5. Replace the damaged parts in time after checking.<br />
6. Finish the service of fork shaft assembly<br />
INPUT SHAFT ASSEMBLY<br />
TRANSMISSION - INPUT SHAFT ASSEMBLY<br />
41-51<br />
1 Bearing shaft retainer ring<br />
2 Bearing stop ring<br />
4 Input shaft assembly<br />
5 Needle bearing<br />
3 Bearing<br />
41-52<br />
1. Dissemble the input shaft assembly<br />
(a) Remove the needle bearings inside the input shaft one<br />
by one, and place them in the proper places to avoid<br />
missing.<br />
Disassemble the snap ring inside the input shaft bearing<br />
Pull out the input shaft bearing with bearing extractor.<br />
2. Check the radial runout of input shaft bearing<br />
Reference value of limitation: 0. 2 mm<br />
41-53<br />
3. Check the input shaft<br />
(a) Check whether the shaft diameter of input shaft end worn<br />
with vernier caliper; please replace the input shaft if<br />
worn.<br />
(b) Check whether the input shaft spline damaged; please<br />
replace the input shaft if damaged.<br />
4. Assemble the input shaft assembly<br />
(a) Punch the input shaft bearing onto the input shaft, install<br />
the input shaft retainer ring with snap ring plier.<br />
Smear appropriate lithium base grease in the input shaft<br />
needle bearing, install the needle into the input shaft, and<br />
then install the third and fourth gear synchronizer gear<br />
(c) Install the input shaft into output shaft, align the<br />
synchronizer ring trislot with the synchronizer block<br />
andinstall.<br />
5. Ensure the flexible rotation after installation.<br />
6. Finish the service of input shaft assembly<br />
41-54<br />
OUTPUT SHAFT ASSEMBLY<br />
TRANSMISSION - OUTPUT SHAFT ASSEMBLY<br />
1 Fifth gear shaft retainer ring<br />
2 Fifth gear<br />
3 Output shaft rear bearing baffle plate<br />
4 Output shaft rear bearing stop ring<br />
5 Output shaft rear bearing<br />
6 Intermediate plate<br />
7 Steel ball<br />
8 Output shaft<br />
9 First gear<br />
10 First gear bushing<br />
11 First gear needle bearing<br />
12 First-second gear synchronizer ring<br />
First-second gear synchronizer spring<br />
spreader ring<br />
First-second gear synchronizer gear<br />
hub<br />
First-second gear synchronizer slide<br />
block<br />
sleeve<br />
17 Second gear needle bearing<br />
18 Second gear assembly<br />
19 Third gear needle bearing<br />
20 Third gear assembly<br />
Third-fourth gear synchronizer gear<br />
ring<br />
Third-fourth-fifth gear synchronizer<br />
spring spreader ring<br />
Third-fourth gear synchronizer slide<br />
26 Third-fourth gear hub retainer ring<br />
41-55<br />
1. Take out output shaft assembly from connecting<br />
Take out the shaft and avoid damage of gears.<br />
2. Disassembling output shaft assembly<br />
(a) Fix the output shaft on the connecting plate.<br />
(b) Disassemble the third-fourth gear hub retainer ring with<br />
Take out third-fourth gear synchronizer.<br />
Take out third gear assembly.<br />
41-56<br />
Take out third gear needle bearing.<br />
Fix the output shaft upside down on the connecting plate.<br />
Take out first speed gear.<br />
Take out first speed gear needle bearing and first speed<br />
gear bushing.<br />
Take out first-second gear synchronizer assembly.<br />
41-57<br />
Take out second gear and second gear needle bearing.<br />
3. Check on critical components on output shaft<br />
According to Table of Fault Phenomena and analysis of possible damaged part, it needs to service certain part<br />
as below:<br />
Use dial indicator to check radial runout of second shaft.<br />
Maximum: 0.1mm<br />
Check the diameter of gear hole by bore dial indicator.<br />
Reference wear maximum: 0.12mm<br />
Other gears need to be checked with same way.<br />
41-58<br />
Check the gears and replace new one if there’s<br />
excessive wear or snaggletooth.<br />
Use thickness gauge to check the space between<br />
synchronizer hub and synchronizer stopping plate.<br />
Reference Maximum: 0.09~0.31 mm<br />
Check the space between synchronizer geared teeth and<br />
engaging teeth.<br />
Standard value: 1. 0~1. 6 mm<br />
Limit value: 0. 8 mm<br />
Check the radial runout of output shaft rear bearing.<br />
Reference Maximum: 0. 2mm<br />
41-59<br />
4. Assemble the output shaft assembly<br />
When assembling, it’s necessary to dip lubrication oil on each<br />
part in order to protect and assemble the parts easily.<br />
(a) Fix the output shaft upside on the connecting plate and<br />
assemble second gear assembly and second gear<br />
needle bearing<br />
Assemble first-second gear synchronizer according to<br />
pictures.<br />
The direction of first-second gear synchronizer is opposite to the<br />
direction of output shaft. The side with fork groove should toward<br />
to connecting plate. Two spring spreader ring should be<br />
staggered to each other.<br />
Fix first-second gear synchronizer assembly and firstsecond<br />
gear synchronizer geared ring.<br />
Dip lubrication oil on first speed gear bearing bush and<br />
locking ball (Φ6.35) and assemble them on output shaft,<br />
then assemble first speed needle bearing.<br />
41-60<br />
Install first speed gear.<br />
Assemble third gear needle bearing.<br />
Assemble third gear assembly.<br />
Assemble third-fourth gear synchronizer and third-fourth<br />
The side with 45° terrace of third -fourth gear synchronizer gear<br />
hub should toward to input shaft. The side with big chamfer of<br />
third -fourth gear synchronizer sleeve should toward to input<br />
shaft. Two spring spreader rings should be staggered to each<br />
other.<br />
41-61<br />
Fix third -fourth gear hub retainer ring with pliers.<br />
Check axial clearance of each gears to see if it’s within<br />
Axial clearance: 0. 1~0. 25 mm<br />
5. Check the flexibility of input shaft and output shaft<br />
6. Accomplish the process of servicing on output shaft<br />
41-62<br />
TRANSMISSION - COUNTER SHAFT ASSEMBLY<br />
COUNTER SHAFT ASSEMBLY<br />
Fifth gear synchronizer gear hub<br />
retainer ring<br />
2 Fifth gear connection gear<br />
Third, fourth and fifth gear synchronizer<br />
gear ring<br />
Fifth gear synchronizer meshing gear<br />
6 Counter shaft fifth gear assembly<br />
7 Fifth gear synchronizer slide block<br />
8 Middle fifth gear needle bearing<br />
10 Counter shaft rear shaft retainer ring<br />
11 Counter shaft rear bearing<br />
12 Intermediate plate<br />
14 Counter shaft<br />
15 Counter shaft connecting gear<br />
16 Counter shaft front bearing<br />
17 Counter shaft front bearing stop ring<br />
Counter shaft front bearing shaft<br />
9 Fifth gear thrust washer<br />
41-63<br />
1. Dismantle the counter shaft assembly<br />
Dismantle the counter shaft front bearing snap ring with<br />
calipers.<br />
Press out the counter shaft front bearing with pressure<br />
Bearing extractor could be used for dismantling the bearing.<br />
Check the counter shaft front bearing radial runout.<br />
41-64<br />
(d) Press out the counter shaft connecting gear with<br />
pressure bracket.<br />
2. Check on critical components on counter shaft<br />
Use dial indicator to check radial runout of counter shaft.<br />
Maximum: 0. 1mm<br />
Reference wear maximum: 0. 12mm<br />
Other gears need to be checked with same way<br />
41-65<br />
excessive wear or snaggletooth<br />
Reference Maximum: 0. 09~0. 31 mm<br />
3. Assemble the counter shaft assembly<br />
(a) Press the counter shaft connecting gear in place with<br />
41-66<br />
Press the counter shaft front bearing in place with<br />
Install the counter shaft front bearing snap ring in place<br />
4. Check whether the counter shaft operate flexibly after installation.<br />
5. Finish the service for counter shaft assembly<br />
REVERSE SHAFT ASSEMBLY<br />
TRANSMISSION - REVERSE SHAFT ASSEMBLY<br />
41-67<br />
1 Reverse gear idler shaft pressing plate<br />
2 Reverse gear idler shaft<br />
3 Reverse idler assembly<br />
4 Intermediate plate<br />
41-68<br />
1. Dismantle the reverse shaft assembly<br />
(a) Dismantle the fixing bolts of reverse gear idler shaft<br />
pressing plate and remove the pressing plate of reverse<br />
Rotate and pull out the reverse gear idler assembly and<br />
the reverse gear idler shaft.<br />
2. Check the parts of reverse shaft<br />
According to Table of Fault Phenomena and analysis of possible damaged part, it need to service certain part<br />
Use vernier caliper to check whether the gear bushing<br />
bore worn, replace the gear bushing if any worn.<br />
Check whether there is gear tooth worn, fatigue and<br />
spalling, corrosion and spots, broken and etc. , please<br />
replace the reverse gear if any.<br />
41-69<br />
Check whether the reverse shaft parts worn, replace it if<br />
seriously worn.<br />
3. Install the reverse gear idler shaft<br />
(a) Install the reverse gear idler shaft assembly and the<br />
reverse gear idler shaft.<br />
(b) Rotate the idler shaft to make the pressing plate<br />
pressing plate holes align with the intermediate plate<br />
assembly fixing bolt hole. Install the idler shaft locking<br />
plate smeared screw locking glue and fasten to specified<br />
4. Finish the service for reverse shaft<br />
41-70<br />
SERVICE FOR OTHER IMPORTANT COMPONENTS OF TRANSMIS-<br />
SION<br />
According to Table of Fault Phenomena and analysis of possible damaged part, it’s needed to service certain<br />
part as below:<br />
1. Service for the front case<br />
(a) Check the flatness of front case and intermediate plate<br />
assembly contacting surface with steel ruler or feeler,<br />
replace timely if could not meet the requirements, so as<br />
to prevent transmission oil leakage.<br />
When checking, please check with the steel ruler or feeler at<br />
different directions and measure for several times, in order to<br />
obtain an accurate value.<br />
2. Service for the front cover<br />
(a) Check the flatness of front cover and front case<br />
contacting surface with steel ruler or feeler, replace<br />
timely if could not meet the requirements, so as to<br />
prevent transmission oil leakage.<br />
Check the wearing extent of the front cover core<br />
diameter with the vernier caliper, repair or replace timely<br />
if could not meet the requirements.<br />
41-71<br />
3. Service for the rear case<br />
(a) Check the flatness of rear case and transmission control<br />
lever cover with steel ruler or feeler, replace timely if<br />
could not meet the requirements, so as to prevent<br />
transmission oil leakage.<br />
(b) Check the flatness of check rear case and<br />
intermediateplate assembly with steel ruler or feeler,<br />
4. Service for the intermediate plate assembly<br />
(a) Check the flatness of intermediate plate assembly with<br />
steel ruler or feeler, replace timely if could not meet the<br />
requirements, so as to prevent transmission oil leakage.<br />
41-72<br />
Check the wearing extent of the connecting holes on<br />
intermediate plate assembly shafts with the vernier<br />
caliper, repair or replace timely if could not meet the<br />
5. Service for the variable speed control cover<br />
(a) Check the wearing extent of the core diameter of variable<br />
speed control cover with the vernier caliper, repair or<br />
replace timely if could not meet the requirements.<br />
6. Service for the clutch case<br />
(a) Check the flatness of clutch case and front case<br />
TRANSMISSION - TRANSMISSION ASSY(TANGSHANAIXIN)<br />
41-73<br />
TRANSMISSION ASSY(TANGSHANAIXIN)<br />
4. REMOVE LOWER DRAIN PLUG RH AND DRAIN<br />
TRANSMISSION FLUID COMPLETELY. TIGHTEN<br />
Torque: 29.8 ~ 44.6 N•m<br />
(a) Remove vehicle speed sensor located at the right of<br />
(b) Remove the back-up lamp switch located at the upper of<br />
transmission RH.<br />
Remove nuts,disconnect flexible shaft of gear shifting<br />
cable and flexible shaft of gear selecting cable from<br />
(d) Remove 2 mounting bolts of cable bracket and cable<br />
Remove the clutch slave cylinder assy. (Refer to<br />
“Chapter 42 clutch - clutch slave cylinder assy,<br />
Remove starter.(Refer to “Chapter 20B starting and<br />
41-74<br />
Remove 10 bolts and disconnect transmission assy from<br />
2 bolts that is used for retaining starter include in these 10<br />
removed bolts.<br />
6. INSTALL TRANSMISSION ASSY, AND CONNECT<br />
OTHER PARTS TO TRANSMISSION ASSY.<br />
(b) Install 10 bolts with hand to connect transmission and<br />
Two bolts that are used for retaining starter are not installed<br />
temporarily.<br />
41-75<br />
M6 X 1.25<br />
M10 X 1.25<br />
Torque<br />
78 ~ 96 N•m<br />
45 ~ 55 N•m<br />
(f) Install propeller shaft assy. (Refer to “Chapter 34 axle<br />
(g) Install starter. (Refer to “Chapter 20B starting and<br />
(h) Remove jack.<br />
(i) Install the clutch slave cylinder assy. (Refer to “Chapter<br />
Position flexible shaft of gear shifting cable and flexible<br />
41-76<br />
Install the back-up lamp switch located at the upper of<br />
Remove vehicle speed sensor located at the right of<br />
7. FILL TRANSMISSION FLUID AND TIGNTEN FILLER<br />
75W/90 for 2.4 L.<br />
• Parking the vehicle on the levelground when checking<br />
fluid level. The fluid level must be with in 5 mm from<br />
the lowest position of the filler plug.<br />
CLUTCH SYSTEM ............................................................................. 42-1<br />
PRECAUTION.............................................................................. 42-1<br />
PROBLEM SYMPTOMS TABLE.................................................. 42-2<br />
CLUTCH FLUID.................................................................................. 42-3<br />
BLEEDING................................................................................... 42-3<br />
CLUTCH PEDAL................................................................................ 42-4<br />
COMPONENTS ........................................................................... 42-4<br />
ADJUSTMENT............................................................................. 42-5<br />
REPLACEMENT .......................................................................... 42-6<br />
VACUUM BOOSTER WITH CLUTCH MASTER<br />
CYLINDER ASSY............................................................................... 42-8<br />
REPLACEMENT .......................................................................... 42-8<br />
CLUTCH SLAVE CYLINDER........................................................... 42-11<br />
REPLACEMENT ........................................................................ 42-11<br />
CLUTCH SUB - ASSY...................................................................... 42-13<br />
COMPONENTS ......................................................................... 42-13<br />
OVERHAUL ............................................................................... 42-14<br />
CLUTCH - CLUTCH SYSTEM<br />
42-1<br />
CLUTCH SYSTEM<br />
1. CLUTCH SYSTEM PRECAUTION.<br />
(a) To avoid spreading clutch dust, do not clean any clutch components with sand paper, dry brush or<br />
compressed air. Only use a water dampened towel to clean clutch components.<br />
42-2<br />
1. Clutch pedal free play(Out of<br />
Chapter 42 clutch - clutch pedal, adjustment<br />
2. clutch driven disk (Worn) Chapter 42 clutch - clutch subassy, overhaul<br />
Clutch slips<br />
3. Flywheel ( Warped) Chapter 42 clutch - clutch subassy, overhaul<br />
4. Clutch pressure plate with<br />
cover assy (Warped)<br />
Chapter 42 clutch - clutch subassy, overhaul<br />
5. Diaphragm spring (Failure) Chapter 42 clutch - clutch subassy, overhaul<br />
1. Clutch pedal free play (Out of<br />
2. Diaphragm spring (Failure) Chapter 42 clutch - clutch subassy, overhaul<br />
3. Clutch master cylinder<br />
(Leaking)<br />
Chapter 42 clutch - vacuum booster with<br />
clutch master cylinder assy, replacement<br />
Clutch does not disengage<br />
4. Clutch slave cylinder (Leaking)<br />
Chapter 42 clutch - clutch slave cylinder assy,<br />
5. Clutch line (Air in line) Chapter 42 clutch - clutch fluid, bleeding<br />
6. clutch driven disk (Worn) Chapter 42 clutch - clutch subassy, overhaul<br />
7. Clutch pressure plate with<br />
8. Clutch release bearing (Worn) Chapter 42 clutch - clutch subassy, overhaul<br />
9. Clutch release fork (Worn) Chapter 42 clutch - clutch subassy, overhaul<br />
1. Torsion spring (Fracture) Chapter 42 clutch - clutch subassy, overhaul<br />
Clutch noisy<br />
2. Clutch driven disk(Worn) Chapter 42 clutch - clutch subassy, overhaul<br />
3. Clutch release bearing (Loose) Chapter 42 clutch - clutch subassy, overhaul<br />
4. Clutch pedal (Warped) Chapter 42 clutch - clutch pedal, replaecment<br />
1. Clutch driven disk (Worn or<br />
warped)<br />
2. Flywheel (Worn) Chapter 42 clutch - clutch subassy, overhaul<br />
Clutch chatters<br />
3. Clutch pressure plate with<br />
cover assy(Worn)<br />
4. Torsion spring (Fracture or<br />
5. Diaphragm spring (Warped) Chapter 42 clutch - clutch subassy, overhaul<br />
6. Engine mount (Loose) -<br />
CLUTCH - CLUTCH FLUID<br />
42-3<br />
CLUTCH FLUID<br />
1. FILL THE FLUID RESERVOIR WITH CLUTCH FLUID.<br />
Clutch fluid: DOT3 or DOT4 brake fluid<br />
Clutch fluid will damage painted surfaces and irritate skin. If<br />
clutch fluid is spilled on any painted surfaces or skin, wash<br />
2. BLEED CLUTCH SLAVE CYLINDER ASSY.<br />
(a) Connect a hose to the bleeder plug.<br />
(b) Depress the clutch pedal several times, then loosen the<br />
bleeder plug with the pedal held down.<br />
(c) When clutch fluid stops flowing, tighten the bleeder plug,<br />
then release the clutch pedal.<br />
(d) Repeat steps (b) and (c) until all the air in the system has<br />
been bled out.<br />
3. CHECK FLUID LEVEL IN FLUID RESERVOIR.<br />
(a) Check the fluid level and fill the fluid reservoir with clutch<br />
42-4<br />
CLUTCH - CLUTCH PEDAL<br />
1 Clutch Pedal Assy<br />
2 Flat Pin<br />
3 Cotter Pin<br />
42-5<br />
1. INSPECT CLUTCH PEDAL HEIGHT.<br />
(a) Inspect the height H between the clutch pedal and floor.<br />
Specification: 165 mm<br />
2. ADJUST CLUTCH PEDAL HEIGHT.<br />
(a) Loosen the lock nut and turn the stop bolt until the height<br />
is correct. Tighten the lock nut.<br />
Torque: 17 ~ 21 N•m<br />
3. INSPECT CLUTCH PEDAL FREE PLAY AND PUSH<br />
ROD PLAY.<br />
(a) Depress the clutch pedal until the pedal resistance<br />
begins to be felt. Inspect the clutch pedal free play L1.<br />
(b) Gently depress the pedal until the pedal resistance<br />
begins to increase a little. Inspect push rod play L2.<br />
4. ADJUST CLUTCH PEDAL FREE PLAY AND PUSH<br />
(a) Loosen the lock nut and turn the push rod until the clutch<br />
pedal free play and push rod play are correct, and then<br />
tighten the lock nut.<br />
(b) After adjusting the pedal free play, inspect the clutch<br />
pedal height.<br />
42-6<br />
2. REMOVE SREERING LOWER COVER. (Refer to “Chapter 83 instrument panel - darshboad,<br />
3. REMOVE ALARM CONTROLLER. (Refer to “Chapter 85 door locks - alarm controller,<br />
4. REMOVE FLAT PIN OF CLUTCH MASTER CYLINDER<br />
PUSH ROD.<br />
(a) Remove cotter pin of clutch master cylinder push rod.<br />
Discard removed cotter pin.<br />
(b) Remove flat pin of clutch master cylinder push rod.<br />
5. REMOVE CLUTCH SWITCH.<br />
(a) Disconnect the connector of clutch switch.<br />
(b) Loosen nut,and remove clutch switch.<br />
6. REMOVE CLUTCH PEDAL AND BRACKET.<br />
(a) Remove 2 nuts of bracket in cab.<br />
(b) Remove mounting bolt of bracket located at the top of<br />
cab.<br />
(c) Remove clutch pedal and bracket.<br />
42-7<br />
7. INSTALL CLUTCH PEDAL AND BRACKET.<br />
(a) Position clutch pedal and bracket, tighten 2 mounting<br />
nuts of bracket in cab.<br />
(b) Tighten mounting bolt of bracker located at the top of the<br />
8. INSTALL CLUTCH SWITCH.<br />
(a) Position clutch switch.<br />
(b) Tighten lower mounting nut.<br />
(c) Connect the connector.<br />
9. INSTALL FLAT PIN OF CLUTCH MASTER CYLINDER<br />
Install flat pin of clutch master cylinder push rod.<br />
Install cotter pin of clutch master cylinder push rod.<br />
10. INSTALL ALARM CONTROLLER. (Refer to “Chapter 85 door locks - alarm controller,<br />
11. INSTALL SREERING LOWER COVER. (Refer to “Chapter 83 instrument panel - darshboad,<br />
12. INSPECT AND ADJUST THE CLUTCH PEDAL HEIGHT. (Refer to “Chapter 42 clutch - clutch<br />
pedal, adjustment”)<br />
13. INSPECT AND ADJUST THE CLUTCH PEDAL FREE PLAY AND PUSH ROD PLAY. (Refer to<br />
“Chapter 42 clutch - clutch pedal, adjustment”)<br />
42-8<br />
CLUTCH - VACUUM BOOSTER WITH CLUTCH MASTER CYLINDER ASSY<br />
VACUUM BOOSTER WITH CLUTCH MASTER CYLINDER<br />
4. REMOVE WASHER ASSY. (Refer to “Chapter 65 wiper and washer - washer assy, replacement”)<br />
5. DRAIN CLUTCH FLUID COMPLETELY.<br />
Clutch fluid will damage painted surfaces and irritate skin. If clutch fluid is spilled on any painted<br />
surfaces or skin, wash it off immediately with water.<br />
6. REMOVE VACUUM BOOSTER WITH CLUTCH MASTER<br />
CYLINDER ASSY.<br />
(a) Loosen the clamp,then disconnect the hose from vacuum<br />
(b) Loosen the clamp,then disconnect the hose from fluid<br />
reservoir.<br />
Loosen the tube joint nut and disconnect the tube from<br />
the clutch master cylinder.<br />
Remove the cotter pin and flat pin of vacuum booster<br />
with clutch master cylinder assy push rod.<br />
(e) Remove 2 mounting nuts of vacuum booster with clutch<br />
42-9<br />
Remove vacuum booster with clutch master cylinder<br />
7. DISASSEMBLE VACCUM BOOSTER WITH CLUTCH<br />
MASTER SYLINDER ASSY.<br />
Loosen the 2 retaining nut connect vacuum booster and<br />
clutch master cylinder.<br />
Disassemble vaccum booster and clutch master cylinder.<br />
Clutch master cylinder can be replaced independently.<br />
8. ASSEMBLE VACCUM BOOSTER WITH CLUTCH<br />
MASTER SYLINDER ASSY<br />
Assemble vaccum booster and clutch master sylinder.<br />
9. INSTALL VACUUM BOOSTER WITH CLUTCH MASTER<br />
Position vacuum booster with clutch master cylinder assy<br />
and tighten 2 mounting nuts.<br />
Install the cotter pin and flat pin of vacuum booster with<br />
clutch master cylinder assy push rod.<br />
42-10<br />
Install the clutch master cylinder tube and tighten the<br />
tube joint nut.<br />
Install hose to fluid reservoir, and install clamp.<br />
Install hose to vacuum booster,and install clamp.<br />
10. FILL THE FLUID RESERVOIR WITH CLUTCH FLUID,THEN BLEED AIR FROM CLUTCH SYSTEM.<br />
(Refer to “Chapter 42 clutch - clutch fluid, bleeding”)<br />
11. INSPECT AND ADJUST THE CLUTCH PEDAL HEIGHT. (Refer to “Chapter 42 clutch - clutch<br />
12. CHECK FLUID LEVEL IN CLUTCH FLUID RESERVOIR. (Refer to “Chapter 42 clutch - clutch fluid,<br />
13. INSTALL WASHER ASSY. (Refer to “Chapter 65 wiper and washer - washer assy, replacement”)<br />
14. INSTALL ALARM CONTROLLER. (Refer to “Chapter 85 door locks - alarm controller,<br />
15. INSTALL SREERING LOWER COVER. (Refer to “Chapter 83 instrument panel - darshboad,<br />
CLUTCH - CLUTCH SLAVE CYLINDER<br />
42-11<br />
CLUTCH SLAVE CYLINDER<br />
1. DRAIN CLUTCH FLUID COMPLETELY.<br />
2. REMOVE CLUTCH SLAVE CYLINDER ASSY.<br />
(a) Loosen the screw, then disconnect the hose from clutch<br />
slave cylinder.<br />
Remove 2 bolts from the clutch slave cylinder.<br />
Remove the clutch slave cylinder.<br />
3. INSTALL CLUTCH SLAVE CYLINDER ASSY.<br />
(a) Install clutch slave cylinder and tighten 2 bolts .<br />
42-12<br />
Connect the hose to the clutch slave cylinder and tighten<br />
the screw.<br />
Be sure to use a new washer.<br />
4. FILL THE FLUID RESERVOIR WITH CLUTCH FLUID,THEN BLEED AIR FROM CLUTCH SYSTEM.<br />
5. CHECK FLUID LEVEL IN CLUTCH FLUID RESERVOIR. (Refer to “Chapter 42 clutch - clutch fluid,<br />
CLUTCH SUB - ASSY<br />
CLUTCH - CLUTCH SUB - ASSY<br />
42-13<br />
1 Bolt<br />
2 Spring Washer<br />
Clutch Pressure Plate With Cover<br />
5 Driven Disk Assy<br />
6 Locating Pin<br />
42-14<br />
1. REMOVE TRANSMISSION ASSY. (Refer to “Chapter 41 transmission (YANCHENGZHONGMA<br />
ZM001) - transmission assy, replacement”,“Chapter 41 transmission (TANGSHANAIXIN) -<br />
2. REMOVE CLUTCH RELEASE BEARING AND CLUTCH<br />
RELEASE FORK.<br />
Remove clutch release bearing hub clip.<br />
Remove clutch release bearing.<br />
Remove clutch release fork.<br />
3. REMOVE CLUTCH RELEASE FORK DUST BOOT.<br />
42-15<br />
4. REMOVE CLUTCH PRESSURE PLATE WITH COVER<br />
Make sure the marks on the clutch pressure plate with<br />
cover assy align with the one on the flywheel.<br />
Diagonally loosen each bolt one turn at a time until<br />
spring tension is released. Then remove 6 bolts.<br />
Remove clutch pressure plate with cover assy.<br />
Do not drop the clutch driven disk assy.<br />
5. REMOVE CLUTCH DRIVEN DISK ASSY.<br />
Keep the clutch driven disk away from oil and grease.<br />
6. INSPECT CLUTCH DREVEN DISK ASSY.<br />
(a) Measure the rivet head depth with a vernier caliper.<br />
Replace the clutch dreven disk assy if necessary.<br />
42-16<br />
Measure the runout of the clutch dreven disk assy with a<br />
dial indicator.<br />
Check the surface of the disk for loose rivets, uneven<br />
contact or adhesion of oil or grease. Replace with a new<br />
part if necessary.<br />
Check the torsion spring for clearance and wear. Replace<br />
with a new part if necessary.<br />
7. INSPECT CLUTCH PRESSURE PLATE WITH COVER<br />
Measure the depth and width of diaphragm spring for<br />
wear with a vernier caliper.<br />
Measure the height of the diaphragm spring. Replace the<br />
clutch pressure plate with cover assy if necessary.<br />
Inspect the surface of the clutch pressure plate with<br />
cover assy for wear and cracks. Replace clutch pressure<br />
plate with cover assy if necessary.<br />
Inspect the strap plate rivets for looseness. Replace the<br />
8. INSPECT FLYWHEEL.<br />
(a) Measure the runout of flywheel with a dial indicator.<br />
Replace with a new part if necessary.<br />
42-17<br />
9. INSPECT CLUTCH RELEASE BEARING.<br />
(a) Inspect the clutch release bearing for wear, noise or<br />
improper rotation. Inspect the friction surface between<br />
the clutch release bearing and the diaphragm spring for<br />
wear.<br />
The bearing is permanently lubricated and requires no<br />
cleaning or lubrication.<br />
• Inspect the inside and outside surface for wear or<br />
damage. Replace with new part if necessary.<br />
• Inspect the friction surface of clutch release bearing<br />
and release fork for wear. Replace with new part if<br />
10. INSPECT CLUTCH RELEASE FORK.<br />
(a) Inspect the position of the clutch release fork as shown<br />
by arrows for wear and shape change. Replace if<br />
11. INSTALL CLUTCH DRIVEN DISK ASSY.<br />
(a) Install the clutch driven disk assy with a special tool.<br />
Take care not to install the clutch driven disk assy in the<br />
wrong direction.<br />
(b) Apply 2 lithium grease to spline of cltch driven disk, don’t<br />
pollute other parts of driven disk and pressure plate .<br />
42-18<br />
12. INSTALL CLUTCH PRESSURE PLATE WITH COVER<br />
Install the clutch pressure plate with cover assy with a<br />
Diagonally tighten all 6 bolts of clutch ressure plate with<br />
cover assy.<br />
13. INSPECT AND ADJUST CLUTCH PRESSURE PLATE WITH COVER ASSY.<br />
(a) Inspect the height of the diaphragm spring after installation. Adjust the tip of the diaphragm spring if<br />
14. INSTALL CLUTCH RELEASE FORK DUST BOOT.<br />
42-19<br />
15. INSTALL CLUTCH RELEASE BEARING AND CLUTCH<br />
Apply grease to the release fork in the areas indicated by<br />
the arrows.<br />
Lubricating grease: Mitsubishi pure lubricating<br />
grease NO. 0101011 or same product.<br />
Install clutch release fork.<br />
Install the clutch release fork to the release fork support.<br />
(c) Install clutch release bearing.<br />
Apply grease to the friction surface between the clutch<br />
release bearing and the release fork before installation.<br />
(d) Install clutch release bearing hub clip.<br />
16. INSTALL TRANSMISSION ASSY. (Refer to “Chapter 41 transmission (YANCHENGZHONGMA<br />
ZM001) - transmission assy, replacement”,“Chapter 41 transmission (TANGSHANAIXIN)-<br />
STEERING SYSTEM.......................................................................... 51-1<br />
PRECAUTION.............................................................................. 51-1<br />
PROBLEM SYMPTOMS TABLE.................................................. 51-2<br />
COMPONENTS ........................................................................... 51-5<br />
ON-VEHICLE INSPECTION ........................................................ 51-6<br />
STEERING WHEEL ASSY................................................................. 51-7<br />
ADJUSTMENT............................................................................. 51-7<br />
OVERHAUL ................................................................................. 51-8<br />
COMBINATION SWITCH ASSY ...................................................... 51-12<br />
COMPONENTS ......................................................................... 51-12<br />
REPLACEMENT ........................................................................ 51-13<br />
STEERING COLUMN ASSY............................................................ 51-16<br />
OVERHAUL ............................................................................... 51-16<br />
STEERING PROPELLER SHAFT ASSY......................................... 51-19<br />
REPLACEMENT ........................................................................ 51-19<br />
51<br />
STEERING SYSTEM<br />
COLUMN<br />
STEERING COLUMN - STEERING SYSTEM<br />
51-1<br />
1. STEERING SYSTEM PRECAUTION.<br />
(a) Take care when replacing parts, always comply with the instructions of this manual.<br />
(b) Incorret replacement may affect the performance of the steering system and result in traffic accident.<br />
2. PRECAUTIONS ON SRS SYSTEM.<br />
(a) Some vehicles are equipped with SRS (Supplemental Restraint Sysem) such as the driver airbag.<br />
(b) Failure to carry out service operation in the correct sequence could cause the SRS to unexpectedly<br />
deploy during servicing, even a serious accident.<br />
(c) Before servicing (including removal or installation of parts, inspection or replacement), be sure<br />
to read the precaution for the supplemental restraint system. (Refer to “Chapter 62 supplemental<br />
restraint system - supplemental restraint system, precaution”)<br />
51-2<br />
1. Front axle (Overloaded) -<br />
2. Tire (Insufficient pressure)<br />
3. Power steering fluid (Low)<br />
Chapter 33 tire and wheel - tire and wheel, onvehicle<br />
Chapter 52 power steering - steering fluid,<br />
4. Steering fluid reservior (Filter jammed) -<br />
Steering heavily<br />
5. Hydraulic circuit (Leaking)<br />
6. Steering pump belt (Loose or skid)<br />
7. Front wheel alignment (Incorrect)<br />
8. Steering knuckle (Worn)<br />
9. Steering knuckle arm (Worn)<br />
10. Ball joint (Worn)<br />
11.Steering column (Bent)<br />
12.Steering propeller shaft (Deformed)<br />
13.Power steering pump (Worn or<br />
14.Steering box (Damaged)<br />
15.Power steering line assy (Jammed)<br />
Chapter 52 power steering - steering box,overhaul<br />
Chapter 52 power steering - power steering<br />
system, on-vehicle inspection<br />
Chapter 51 steering column - steering column<br />
shaft assy, overhual<br />
pump, replacement<br />
Chapter 52 power steering - steering box,<br />
overhual<br />
line assy, replacement<br />
51-3<br />
1. Power steering fluid (Low)<br />
2. Tire (Different pressure)<br />
3. Steering knuckle (Loose or worn)<br />
instability<br />
4. Steering knuckle arm (Loose or worn)<br />
5. Steering column (Loose or worn)<br />
6. Steering propeller shaft (U-joint loose or<br />
worn)<br />
7. Steering box (Loose or damaged)<br />
1. Tire (Insufficient pressure)<br />
2. Steering pump belt (Loose or skid)<br />
3. Hydraulic circuit (Invading air)<br />
4. Return hose (Curving or jammed)<br />
assy, overhual<br />
bleeding<br />
Poor return<br />
5. Front wheel alignment (Incorrect)<br />
6. Steering column (Bent)<br />
7. Steering propeller shaft (Deformed)<br />
8. Power steering pump (Worn or<br />
9. Steering box (Damaged)<br />
51-4<br />
Excessive<br />
steering wheel<br />
free play<br />
1. Steering wheel (Worn)<br />
2. Steering propeller shaft (loose or worn)<br />
3. Steering knuckle (Worn)<br />
4. Ball joint (Worn)<br />
5. Front hub bearing (Worn)<br />
6. Steering box (Loose or damaged)<br />
Chapter 51 steering column - steering wheel<br />
Chapter 34 axle and propeller shaft - axle hub,<br />
2. Steering fluid reservior (Filter jam) -<br />
Steering not<br />
smooth<br />
4. Steering knuckle (Worn)<br />
5. Steering propeller shaft (Worn)<br />
6. Power steering pump (Worn or<br />
7. Steering Box (Damaged)<br />
8. Power steering line assy (Jam)<br />
2. Hydraulic circuit (Invading air)<br />
3. Steering column (Worn)<br />
4. Steering propeller shaft (Worn)<br />
5. Steering box (Worn or damaged)<br />
51-5<br />
1 Nut<br />
2 Steering Wheel Assy<br />
3 Steering Column Assy<br />
6 Steering Propeller Shaft Assy I<br />
8 Screw<br />
9 Cloumn Base Frame Assy<br />
10 Bolt, Spring Washer<br />
12 Steering Propeller Shaft Assy II<br />
13 Steering Retarder Assy<br />
7 Steering Propeller Shaft Protection Cover<br />
51-6<br />
1. CHECK STEERING WHEEL FREE PLAY.<br />
(a) Stop the vehicle.<br />
(b) Turn the steering wheel to its straight position and face the<br />
tires straight ahead.<br />
(c) Turn the steering wheel gently left and right, check the<br />
steering wheel free play.<br />
Free play: ± 10 °<br />
If the free play is out of the specification, then:<br />
• Inspect interrelated parts. (Refer to ”Chapter 51 steering<br />
column - steering system, problem symptoms table”)<br />
• Inspect the maximum front wheel steering angle, adjust it if<br />
necessary. (Refer to “Chapter 31 front suspension - front<br />
wheel alignment, adjustment”)<br />
2. CHECK THE VEHICLE DEVIATION.<br />
(a) Drive straightly the vehicle and along the center line of the road at 50Km/h speed.<br />
(b) Release the steering wheel and continue traveling straightly for 100 m.<br />
(c) Measure the offset.<br />
Offset LH: < Half Car Body<br />
Offset RH: < Half Car Body<br />
If the checking value is out of specification, there is fault on the off track for this vehicle.<br />
STEERING COLUMN - STEERING WHEEL ASSY<br />
51-7<br />
STEERING WHEEL ASSY<br />
1. STEERING WHEEL UP-DOWN ADJUSTMENT.<br />
(a) Pull the handle down to position as shown.<br />
Adjust the steering wheel up and down.<br />
Adjustable distance: 27 mm<br />
• Be sure to adjust the steering wheel towards your<br />
chest, instead of the head or neck.<br />
• Simultaneously adjust the driver seat. make sure the<br />
distance between steering wheel and your chest.<br />
(Refer to “Chapter 84 seat - Driver / assistant driver<br />
seat, adjustment”)<br />
• Do not perform this operation when the vehicle is<br />
running.<br />
(c) Release the handle.<br />
Make sure the steering wheel is locked completely without<br />
51-8<br />
1. PRECAUTION. (Refer to “Chapter 51 steering column - steering system, precaution”)<br />
2. DISCONNECT BATTERY NEGATIVE CABLE. (Refer to “Chapter 20 starting and charging -<br />
battery, replacement”)<br />
3. DISCONNECT BATTERY POSITIVE CABLE. (Refer to “Chapter 20 starting and charging - battery,<br />
4. REMOVE DRIVER AIRBAG ASSY.<br />
(a) Turn the steering wheel to its straight position and face the<br />
Using a inner hex spanner, loosen 2 bolts at the bottom<br />
of steering wheel.<br />
Turn the driver airbag assy over.<br />
Disconnect the driver airbag connector.<br />
• Do not drag the clock spring wire harness.<br />
• Do not disassemble the driver airbag assy.<br />
• Driver airbag assy should be stored with the top<br />
surface upward. Also, do not put any things on top<br />
surface of driver airbag assy.<br />
51-9<br />
5. REMOVE STEERING WHEEL ASSY.<br />
(a) Disconnect the driver airbag connector.<br />
(b) Loosen the nut.<br />
Store it carefully to prevent it from being missing.<br />
Mark on the steering wheel and steering column assy.<br />
(d) Pull out the steering wheel from the steering column.<br />
6. INSPECT STEERING WHEEL ASSY.<br />
(a) Check the steering wheel for warp, micro-cracks or fracture.<br />
(b) Check the spline for deformation or damaged above 2 teeth. If any fault is detected, replace it with a<br />
new steering wheel.<br />
7. INSTALL STEERING WHEEL ASSY.<br />
(a) Align the marks on the steering wheel assy and steering<br />
column assy.<br />
(b) Install the steering wheel to steering column.<br />
• Be sure to perform this procedure according to the<br />
• Make sure the tires face ahead straightly.<br />
51-10<br />
(c) Tighten the nut.<br />
(d) Connect the clock spring wire harness connector.<br />
8. INSPECT STEERING WHEEL TURNING FORCE.<br />
(a) Using a spring scales, pull the steering wheel rim tangentially,<br />
measure the steering wheel turning force (engine stopped).<br />
Steering wheel turning force (engine stopped): < 300 N<br />
If steering wheel turning force exceeds the maximum, inspect<br />
interrelated parts. (Refer to “Chapter 51 steering column -<br />
steering system, problem symptoms table”)<br />
For measurment, turn the steering wheel to both sides in<br />
the range of 80°.<br />
9. INSTALL DRIVER AIRBAG ASSY.<br />
(a) Connect the driver airbag connector.<br />
WANING<br />
• Never use the airbag parts removed from another<br />
vehicle. When replacing, use a new one.<br />
• If the driver airbag assy has been dropped, or there<br />
are cracks, dents or any faults in the case or connector,<br />
replace the driver airbag assy with a new one.<br />
• Do not drag the clock spring wire harness. Make<br />
sure the wire harness does not interfere with parts<br />
around.<br />
If hear a “click”, the connector is connected completely.<br />
Install the driver airbag assy to steering wheel.<br />
51-11<br />
• There should be no interference between the driver<br />
airbag assy and steering wheel.<br />
• The clearance should be uniform all the way around<br />
when the driver airbag assy is installed on the<br />
steering wheel.<br />
Using a inner hex spanner, tighten 2 bolts at the bottom<br />
10. CONNECT BATTERY POSITIVE CABLE.(Refer to “Chapter 20 starting and charging - battery,<br />
11. CONNECT BATTERY NEGETIVE CABLE. (Refer to “Chapter 20 starting and charging - battery,<br />
12. INSPECT SRS WARNING LIGHT.<br />
51-12<br />
STEERING COLUMN - COMBINATION SWITCH ASSY<br />
COMBINATION SWITCH ASSY<br />
1 Light Switch Assy<br />
2 Wiper Switch Assy<br />
3 Combination Switch Upper Cover<br />
5 Ignition Switch Assy<br />
6 Combination Switch Lower Cover<br />
7 Screw<br />
4 Ignition Switch Keyring Assy<br />
51-13<br />
4. REMOVE DRIVER AIRBAG ASSY. (Refer to “Chapter 51 steering column - steering wheel assy,<br />
5. REMOVE STEERING WHEEL ASSY. (Refer to “Chapter 51 steering column - steering wheel assy,<br />
6. REMOVE COMBINATION SWITCH ASSY.<br />
(a) Loosen 2 screws.<br />
Remove combination switch upper and lower cover.<br />
Disconnect the front combination lamp switch connector.<br />
Remove the front combination lamp switch.<br />
51-14<br />
Disconnect the wiper and washer switch connector.<br />
Remove the wiper and washer switch.<br />
7. INSTALL COMBINATION SWITCH ASSY.<br />
(a) Install the wiper and washer switch.<br />
(b) Connect the wiper and washer switch connector.<br />
Install the front combination lamp switch.<br />
Connect the front combination lamp switch connector.<br />
Install combination switch upper and lower cover.<br />
Make sure the covers are positioned properly.<br />
Tighten 2 screws.<br />
51-15<br />
8. INSTALL STEERING WHEEL ASSY. (Refer to “Chapter 51 steering column - steering wheel assy,<br />
9. INSTALL DRIVER AIRBAG ASSY. (Refer to “Chapter 51 steering column - steering wheel assy,<br />
10. CONNECT BATTERY POSITIVE CABLE. (Refer to “Chapter 20 starting and charging - battery,<br />
11. CONNECT BATTERY NEGATIVE CABLE. (Refer to “Chapter 20 starting and charging - battery,<br />
12. INSPECT COMBINATION SWITCH ASSY FUNCTION.<br />
51-16<br />
STEERING COLUMN - STEERING COLUMN ASSY<br />
STEERING COLUMN ASSY<br />
3. DISCONNECT BATTERY POSITIVE CABLE.<br />
6. REMOVE CLOCK SPRING. (Refer to “Chapter 62 supplemental restraint system - clock spring,<br />
7. REMOVE COMBINATION SWITCH ASSY. (Refer to “Chapter 51 steering column - combination<br />
switch assy, replacement”)<br />
8. REMOVE STEERING COLUMN LOWER COVER.<br />
(a) Remove store content box.<br />
(b) Remove the steering column lower cover.<br />
(c) Remove the steering shaft cover.<br />
9. REMOVE IGNITION SWITCH ASSY. (Refer to “Chapter 91 vehicle control system - removal&installation and<br />
disassembly&reassembly”)<br />
10. REMOVE STEERING COLUMN ASSY.<br />
(a) Mark on the steering column and steering propeller shaft<br />
I.<br />
Remove the bolt.<br />
51-17<br />
Pull the steering propeller shaft I down from the steering<br />
Remove 3 bolts.<br />
Remove 2 harness clips.<br />
Remove the steering column assy.<br />
• When storage, cover the splines with gum cap or soft cloth<br />
on the both sides to prevent damage.<br />
• Be sure to store the steering column carefully, especially<br />
the splines.<br />
11. INSPECT STEERING COLUMN ASSY.<br />
(a) Check the spline shaft.<br />
• Check for rusting, crack and fracture.<br />
• Check for deformation or damage for more than 2 teeth.<br />
• If any fault is detected, replace with a new steering column assy.<br />
12. INSTALL STEERING COLUMN ASSY.<br />
(a) Positon the steering column assy properly.<br />
(b) Tighten 3 nuts.<br />
Torque: 29 ~ 35 N·m<br />
(c) Install 2 harness clips.<br />
Install the steering propeller shaft to the steering column<br />
assy according to the marks.<br />
Be sure to perform this operation according to the marks.<br />
51-18<br />
(e) Tighten the bolt.<br />
13. INSTALL IGNITION SWITCH ASSY. (Refer to “Chapter 91 vehicle control system - removal&installation<br />
and disassembly&reassembly”)<br />
14. INSTALL STEERING COLUMN LOWER COVER.<br />
(a) Install the steering column lower cover.<br />
(b) Install the steering propeller shaft cover.<br />
15. INSTALL CLOCK SPRING. (Refer to “Chapter 62 supplemental restraint system - clock spring,<br />
16. INSTALL STEERING WHEEL ASSY. (Refer to “Chapter 51 steering column - steering wheel assy,<br />
17. INSTALL DRIVER AIRBAG ASSY. (Refer to “Chapter 51 steering column - steering wheel assy,<br />
18. CONNECT BATTERY POSITIVE CABLE. (Refer to “Chapter 20 starting and charging - battery,<br />
19. CONNECT BATTERY NEGATIVE CABLE. (Refer to “Chapter 20 starting and charging - battery,<br />
20. INSPECT SRS WARNING LIGHT.<br />
STEERING COLUMN - STEERING PROPELLER SHAFT ASSY<br />
51-19<br />
STEERING PROPELLER SHAFT ASSY<br />
1. REMOVE THE STEERING COLUMN ASSY.(Refer to “Chapter 51 steering column - steering wheel assy,<br />
2. REMOVE STEERING PROPELLER SHAFT I ASSY.<br />
Mark on the steering propeller shaft I and the steering<br />
retarder.<br />
Pull the steering propeller shaft I up.<br />
Disconnect from the steering retarder.<br />
Be sure to store the steering propeller shaft carefully to<br />
prevent damage, expecially the splines.<br />
3. REMOVE STEERING PROPELLER SHAFT COVER ASSY.<br />
(a) Loosen 4 mounting nuts.<br />
(b) Remove steering propeller shaft cover assy.<br />
4. REMOVE STEERING RETARD ASSY.<br />
(a) Loosen 3 mounting bolts.<br />
(b) Remove steering retard support.<br />
51-20<br />
Remove steering retard assy mounting bolts.<br />
Loosn the steering propeller shaft II upper bolt.<br />
Remove the steering retard assy.<br />
prevent damage, expecially the splines, do not turn the<br />
steering drive shaft.<br />
5. REMOVE STEERING PROPELLER SHAFT II ASSY.<br />
(a) Remove the bolt.<br />
(b) Disconnect the steering propeller shaft II and steering<br />
gear assy.<br />
(c) Mark on the steering column and the steering propeller<br />
6. INSPECT THE STEERING COLUMN ASSY.<br />
(a) Check the steering column assy for bend.<br />
Replace with a new steering propeller shaft if necessary.<br />
(b) Inspect the splines, splined sleeves and U-joint yoke.<br />
• Check for warp, micro-cracks or fracture.<br />
If any fault is detected, replace with a new steering propeller shaft assy.<br />
(c) Inspect the steering propeller shaft U-joint.<br />
• Check whether the U-joint rolls smoothly.<br />
• Check bearing seals and cover failure.<br />
• Check universal joint cross shaft journal indentation, flaking, eccentric wear and cracks.<br />
• Check universal joint smooth rotation.<br />
Replace with a new steering propeller shaft when necessary.<br />
• Measure the clearance between the cross shaft necks and bearings.<br />
Clearance: ≤ 0.2 mm<br />
If the clearance exceeds the manximum, replace with a new steering propeller shaft.<br />
51-21<br />
7. INSTALL THE SEERING PROPELLER SHAFT II ASSY.<br />
Install the steering propeller shaft II to the steering gear<br />
assy to the marks.<br />
Tighten the bolt.<br />
8. INSTALL STEERING RETARD ASSY.<br />
(a) Install the steering propeller shaft II to the steering retard<br />
(b) Tighten 1 bolt.<br />
Tighen 2 steering retard assy mounting bolts.<br />
Tighten 3 steering retard assy cover bolts.<br />
9. INSTALL STEERING PROPELLER SHAFT COVER ASSY.<br />
(a) Tighten 4 steering propeller shaft mounting bolts.<br />
51-22<br />
10. INSTALL STEERING PROPELLER SHAFT I.<br />
and the steering retard according to the marks.<br />
11. INSTALL THE STEERING COLUMN ASSY.(Refer to “Chapter 51 steering column - steering wheel<br />
assy, overhaul”)<br />
POWER STEERING SYSTEM ........................................................... 52-1<br />
PRECAUTION.............................................................................. 52-1<br />
PROBLEM SYMPTOMS TABLE.................................................. 52-2<br />
COMPONENTS ........................................................................... 52-5<br />
ON-VEHICLE INSPECTION ........................................................ 52-7<br />
STEERING FLUID............................................................................ 52-13<br />
REPLACEMENT ........................................................................ 52-13<br />
BLEEDING AND PURIFYING.................................................... 52-15<br />
POWER STEERING PUMP WITH FLUID RESERVIOR ASSY....... 52-17<br />
REPLACEMENT ........................................................................ 52-17<br />
POWER STEERING LINE ASSY..................................................... 52-22<br />
REPLACEMENT ........................................................................ 52-22<br />
STEERING GEAR ASSY ................................................................. 52-28<br />
OVERHAUL ............................................................................... 52-28<br />
STEERING FLUID RESERVIOR...................................................... 52-33<br />
REPLACEMENT ........................................................................ 52-33<br />
52<br />
POWER STEERING -<br />
POWER STEERING SYSTEM<br />
STEERING<br />
52-1<br />
1. PRECAUTION ON POWER STEERING SYSTEM.<br />
(b) Incorrect replacement may affect the performance of the steering system and result in driving<br />
dangerously.<br />
2. PRECAUTION ON MAINTAINING THE POWER STEERING SYSTEM.<br />
(a) Be sure to use the specified steering fluid.<br />
Steering fluid: ATF- Ⅲ<br />
(b) Replace the steering fluid and clean the fluid reservior filter in the primal 2500 Km for a new steering<br />
gear assy. Then repeat these two operations in each following 5000 Km or 1 year. (Refer to “Chapter 52<br />
power steering - steering fluid, replacement”)<br />
(c) Check the steering fluid level and whether the fluid goes bad or exist excessive impurities every month.<br />
(Refer to “Chapter 52 power steering - power steering system, on-vehicle inspection”)<br />
(d) Regularly check at least each 5000 Km.<br />
• Check for loose.<br />
• Check steering system operation.<br />
52-2 POWER STEERING - POWER STEERING SYSTEM<br />
1. Overloaded -<br />
3. Power steering fluid level (Low)<br />
5. Hydraulic Circuit (Leaking)<br />
6. Steering Pump (Loose or skid)<br />
10. B-joint (Worn)<br />
11. Steering column (Bent)<br />
12. Steering propeller shaft (Deformed)<br />
13. Power steering pump (Worn or<br />
14. Steering gear assy (Damaged)<br />
15. Power steering line assy (Jammed)<br />
Chapter 52 power steering - steering gear<br />
Chapter 31 front suspension - lower control<br />
arm, replacement<br />
Chapter 51 steering column - steering<br />
propeller shaft assy, overhaul<br />
52-3<br />
Steering instability(Can<br />
not keep<br />
straight lane)<br />
steering gear assy<br />
overheat<br />
(It exceeds the<br />
enviromental<br />
temperature more<br />
than 65 ℃ )<br />
3. Steering knuckle (Loosen or worn)<br />
4. Steering knuckle arm (Loosen or worn)<br />
6. Steering propeller shaft (U-joint loose<br />
or worn)<br />
7. steering gear assy (Loose or<br />
1. Overload -<br />
2. Operation (Incorrect)<br />
(Residence more than 4 seconds at the<br />
limit position on both sides)<br />
3. Power steering pump (Exsessive flow)<br />
4. Power steering line assy (Deformed or<br />
jammed)<br />
3. Hydraulic cicuit (Invading air)<br />
bleeding and purifying<br />
assy, inspection<br />
9. steering gear assy (Damaged)<br />
52-4 POWER STEERING - POWER STEERING SYSTEM<br />
2. Steering propeller shaft (U-joint loose<br />
6. steering gear assy (Loose or<br />
2. Steering fluid reservior (Filter jammed) -<br />
7. steering gear assy (Damaged)<br />
8. Power steering line assy (Jammed)<br />
pump, overhaul<br />
2. Hydraulic circuit (Invading air) Chapter 52 power steering - steering fluid,<br />
Steering irregularity<br />
3. Steering column (Worn) Chapter 51 steering column - steering column<br />
4. Steering propeller shaft (Worn) Chapter 51 steering column - steering<br />
5. steering gear assy (Worn or damaged)<br />
52-5<br />
GASOLINE VEHICLES(4G69)<br />
1 Split Pin<br />
2 Slotted Nut<br />
3 Steering Gear Assy<br />
4 Flat Washer<br />
7 Bolt, Spring Washer<br />
9 Tensioner With Bracket Assy.<br />
11 Clamp<br />
12 Flat Washer<br />
14 Washer<br />
15 Bolt<br />
16 Ribbed Belt<br />
17 High-pressure Line Assy<br />
18 Low-pressure Line Assy<br />
19 Steering Propeller Shaft Assy<br />
Power Steering Pump With Fluid Reservior<br />
20 Engine Crankshaft Belt Pulley<br />
52-6 POWER STEERING - POWER STEERING SYSTEM<br />
DIESEL VEHICLES (ISF2.8)<br />
1 Bolt, Spring Washer<br />
High-pressure And Low-pressure Line<br />
3 Ribbed Belt<br />
4 Nut<br />
5 Copper Washer<br />
6 Copper Washer<br />
9 Fluid Reservior<br />
11 Clip<br />
13 Pipeline<br />
14 Clip<br />
15 Socket<br />
17 Nut<br />
18 Bolt, Spring Washer<br />
19 Steering Pump Bracket Assy<br />
21 Belt Pulley<br />
22 Tensioner With Bracket Assy<br />
23 Bolt, Spring Washer<br />
12 Power Steering Pump<br />
52-7<br />
2. CHECK STEERING FLUID LEVEL.<br />
(a) Park the vehicle on a flat road.<br />
1. INSPECT DRIVE BELT.<br />
(a) Visual check for exsessive wear, etc.<br />
If any fault is found, replace the drive belt.<br />
Cracks on the rib side of a belt are considered acceptable. If<br />
the missing chunks from the ribs are found on the belt, it<br />
should be replaced.<br />
(b) Check the deflection.<br />
• Apply a force of 98 N to push the middle of the drive belt<br />
and adjust deflection if necessary.<br />
Deflection (Gasoline vehicle) : 5.5 ~ 8.5 mm<br />
Deflection (Diesel vehicle) : 5.5 ~ 8.5 mm<br />
Make sure the engine is stopped before performing this<br />
(b) Check the steering fluid level.<br />
• Fill the steering fluid if necessary. (Refer to “Chapter 52<br />
Steering fluid: ATF - Ⅲ<br />
• Make sure the egnine is stopped.<br />
• Check that the fluid level is within the COLD range, if<br />
the fluid is cold.<br />
• Check that the fluid level is within the HOT range, if<br />
the fluid is hot.<br />
Start the engine and run it at idle.<br />
Turn the steering wheel fully to the right and left several<br />
times to get fluid temperature high.<br />
Fluid temperature: - 40 ~ 120 ℃<br />
52-8 POWER STEERING - POWER STEERING SYSTEM<br />
Make sure the time when steering wheel stays at full lock<br />
position will not exceed 4 seconds, otherwise it will damage<br />
the power steering pump.<br />
Check fluid for foam and emulsification.<br />
If foam or emulsification is identified, bleed the power<br />
steering sysytem. (Refer to “Chapter 52 power steering -<br />
steering fluid, bleeding”)<br />
With the engine idling, check the steering fluid level in<br />
the fluid reservior.<br />
Check that the fluid level is within the HOT range, if the fluid<br />
is hot.<br />
(g) Stop the engine.<br />
(h) Wait a few minutes, check the steering fluid level in the<br />
fluid reservior again.<br />
(i) Then check steering fluid level .<br />
Steering fluid level difference: ≤ 5 mm<br />
If the difference is out of the specification, bleed the power<br />
steering system. (Refer to “Chapter 52 power steering - steering<br />
fluid, bleeding and purifying”)<br />
Check the steering fluid level finally and fill the steering<br />
52-9<br />
3. CHECK STEERING FLUID PRESSURE.<br />
Gasoline vehicles (4G69)<br />
(a) Separate the high-pressure tube from power steering pump.<br />
Be sure to keep it clean and prevent dirt entry<br />
Diesel vehicles (ISF2.8)<br />
Separate the high-pressure tube from power steering pump.<br />
Be sure to keep tube clean and prevent dirt entry.<br />
Gasoline vehicles.<br />
Diesel vehicles.<br />
(b) Connect the special tool as shown in the illustration..<br />
SPECIAL TOOL:<br />
• Be sure to keep it clean and prevent dirt entry.<br />
• Check that the valve of the SST is in “OPEN” position.<br />
Connect the SST by the same procedures as the gasoline<br />
vehicles, although look different.<br />
(c) Bleed the power steering system. (Refer to “Chapter 52<br />
power steering - steering fluid, bleed and purifying”)<br />
(d) Start the engine and run it at idle.<br />
52-10 POWER STEERING - POWER STEERING SYSTEM<br />
Lift front wheels off the ground with jack or lift.<br />
(f) With the engine idling, close the valve of the special tool.<br />
(g) Observe the reading on the special tool.<br />
(h) The max pressure of steering system is (10±0.5)MPa.<br />
• Do not close the valve for more than 4 seconds.<br />
• Do not let the fluid temperature become too high.<br />
With the engine idling, open the valve of the SST.<br />
Measure the fluid pressure when engine is running at<br />
1000 rpm and 3000 rpm.<br />
Do not turn the steering wheel.<br />
With the engine idling and the valve fully opened, turn<br />
the steering wheel to full lock position.<br />
Observe the reading on the SST.<br />
The max pressure of steering system is (10±0.5)MPa.<br />
Disconnect the SST<br />
52-11<br />
(o) Connect the high-pressure tube to power steering pump.<br />
Be sure to keep it clean and prevent dirt entry.<br />
Diesel vehicles. (ISF2.8)<br />
Connect the high-pressure tube to power steering pump<br />
(q) Bleed the power steering system. (Refer to “Chapter 52<br />
power steering - steering fluid, bleeding and purifying”)。<br />
4. INSPECT STEERING WHEEL TURNING FORCE.<br />
Turn the steering wheel to its straight position and face the<br />
Remove the driver airbag assy. (Refer to “Chapter 51 steering<br />
column - steering wheel assy, overhaul”)<br />
Using a torque wrench, measure the steering wheel turning<br />
force (engine idling)<br />
Steering wheel turning force (engine stop): < 300 N<br />
Take the tire type, pressure and contact surface into your<br />
consideration before diagnosis.<br />
52-12 POWER STEERING - POWER STEERING SYSTEM<br />
Tighten the steering wheel lock nut.<br />
Install the driver airbag assy. (Refer to “Chapter 51 steering<br />
5. CHECK THE OFF TRACK.<br />
(a) Driving straightly (50Km/h) along the center line of the road.<br />
(c) Measure the offset in 100 m distance.<br />
Offset LH: < Half car body<br />
Offset RH: < Half car body<br />
If the measurement value is out of the specification, there is fault on the off track for this vehicle.<br />
52-13<br />
1. PRECAUTION. (Refer to “Chapter 52 power steering - power steering system, precaution”)<br />
2. DRAIN STEERING FLUID.<br />
(a) Lift front wheels off the ground with jack or lift.<br />
(b) Remove the steering fluid reservior cap when turning it<br />
counterclockwise.<br />
Loosen the clamp and separate the low- pressure hose<br />
from steering gear assy.<br />
Drain the steering fluid.<br />
times until steering fluid is drained fully.<br />
• Do not perform this operation for more than 10 seconds.<br />
• Make sure the time when steering wheel stays at full<br />
lock position will not exceed 4 seconds, otherwise it<br />
will damage the power steering pump.<br />
3. FILL STEERING FLUID.<br />
(a) Connect the low-pressure hose to steering gear assy<br />
and tighten the clamp.<br />
52-14 POWER STEERING - STEERING FLUID<br />
Fill the steering fluid.<br />
Volumn: 1.2 L<br />
times until the fluid will not be emulsifiable and the level<br />
will no longer drop down.<br />
Check the steering fluid level and fill the steering fluid if<br />
necessary. (Refer to “Chapter 52 power steering - power<br />
steering system, on-vehicle inspection”)<br />
Install and turn clockwise the reservior cap..<br />
Stop the engine.<br />
Lower the vehicle.<br />
52-15<br />
BLEEDING AND PURIFYING<br />
1. PRECAUTION. (Refer to “Chapter 52 power steering - power steering system”)<br />
2. BLEED POWER STEERING SYSTEM.<br />
Turn counterclockwise and remove the steering fluid<br />
reservior cap.<br />
(c) Turn the steering wheel fully to the right and left several<br />
(e) Turn the steering wheel.<br />
• Turn the steering wheel to left full lock position for 2 ~ 3<br />
seconds, then turn to the opposite full lock position for 2<br />
~ 3 seconds.<br />
• Repeat the previous procedure several times.<br />
(f) Stop the engine.<br />
Check for foam or emulcification.If foam or emulsification<br />
is identified, Turn the steering wheel fully to the right and<br />
left several times until the fluid will not be emulsifiable<br />
and the level will no longer drop down.<br />
If the system has to be bled twice becauce of foam or<br />
emulcification, check for fluid leakage in the system.<br />
52-16 POWER STEERING - STEERING FLUID<br />
Install and turn clockwise the reservior cap.<br />
(j) Stop the engine.<br />
(k) Lower the vehicle.<br />
3. PURIFY POWER STEERING SYSTEM.<br />
(b) Start the engine and run it at idle.<br />
(c) Turn the steering wheel fully to the right and left several times.<br />
Make sure the time when steering wheel stays at full lock position will not exceed 4 seconds, otherwise it will<br />
damage the power steering pump.<br />
(d) Check for abnormal noise.<br />
If abnormal noise is identified, bleed the power steering system. (Refer to “Chapter 52 power steering -<br />
steering fluid, bleeding and purifying”)<br />
(e) Turn the steering wheel fully to the right and left several times until the noise disappears.<br />
(g) Lower the vehicle.<br />
(h) Check for jam and dirt in the steering fluid reservior filter.<br />
Clean or replace the filter if necessary.<br />
POWER STEERING PUMP WITH FLUID<br />
RESERVIOR ASSY<br />
POWER STEERING PUMP WITH FLUID RESERVIOR ASSY<br />
GASOLINE VEHICLE (4G69)<br />
52-17<br />
• Generally, treat the power steering pump with fluid reservior assy as a whole. Do not separate<br />
the fluid reservior from the power steering pump unless absolutely necessary.<br />
• Do not disassemble the power steering pump because of its high precision.<br />
• If damaged, replace the new steering oil pump assy.<br />
2. DRAIN FLUID. (Refer to “Chapter 52 power steering - steering fluid, replacement”)<br />
3. SEPARATE POWER STEERING LINE ASSY.<br />
(a) Separate the high-pressure tube from the power steering<br />
(b) Separate the low-pressure hose from the steering fluid<br />
reservior.<br />
4. REMOVE DRIVE BELT.<br />
(a) Loosen the retaining bolt from the tensioner.<br />
Adjust the tensioner adjusting bolt to loosen the drive<br />
52-18 POWER STEERING -<br />
(c) Remove the drive belt (ribbed belt).<br />
5. REMOVE POWER STEERING PUMP WITH FLUID<br />
RESERVIOR ASSY.<br />
Remove the pulley nut.<br />
Remove the power steering pump pulley.<br />
Remove 2 bolts and 1 nut.<br />
Remove the power steering pump with fluid reservior<br />
52-19<br />
6. INSTALL POWER STEERING PUMP WITH FLUID<br />
(a) Position the power steering pump with fluid reservior<br />
assy properly.<br />
Install the power steering pump pulley temporarily, check<br />
whether the pump pulley is on the same plane with the<br />
engine crankshaft pulley and tensioner .<br />
Tighten 2 bolts and 1 nut.<br />
Install the power steering pump pulley.<br />
Make sure the power steering pump pulley is on the same<br />
plane with the engine crankshaft pulley and tensioner.<br />
Install the pulley nut.<br />
7. INSTALL DRIVE BELT.<br />
(a) Install the drive belt (ribbed belt).<br />
52-20 POWER STEERING -<br />
(b) Tighten the adjusting bolt, tension steering oil pump belt.<br />
(c) Apply a force of 98 N to middle of the drive belt and<br />
check the deflection. Adjust the tensioner adjusting bolt if<br />
Deflection : ≤ 5 mm<br />
Be sure to make sure the egnine is stopped before<br />
performing this operation<br />
Tighten the retaining nut to the tensioner.<br />
8. CONNECT THE HIGH-PRESSURE TUBE.<br />
(a) Connect the high-pressure tube to power steering pump.<br />
Torque: 40 ~ 45 N·m<br />
(b) Connect the low-pressure hose to fluid reservior and<br />
tighten the clamp.<br />
9. FILL FLUID. (Refer to “Chapter 52 power steering - steering fluid,replacement”)<br />
52-21<br />
1. REMOVE DIESEL VEHICLES THE POWER STEERING BUMP WITH FLUID RESERVIOR ASSY.<br />
(Refer to 《COMMINS ISF SERVICES ENGINE MANUAL,SECTION 9- drive)<br />
52-22 POWER STEERING - POWER STEERING LINE ASSY<br />
POWER STEERING LINE ASSY<br />
3. REMOVE POWER STEERING LINE ASSY.<br />
(a) Loosen 2 power steering line assy retaining bolts.<br />
Separate the power steering line assy:Steering pump<br />
• Separate the high-pressure tube from the power<br />
steering pump.<br />
• Loosen the clamp and separate the low-pressure<br />
hose from the steering fluid reservior.<br />
(c) Separate the power steering line assy from the steering<br />
• Separate the high-pressure tube from the steering<br />
hose from the steering gear assy.<br />
Remove the power steering line assy.<br />
Loosen 3 bolts to separate the high-pressure line assy<br />
from the low-pressure line assy.<br />
52-23<br />
4. INSTALL POWER STEERING LINE ASSY.<br />
(a) Tighten 3 bolts attaching the hig-pressure line assy to the<br />
low-pressure line assy.<br />
(b) Position the power steering line assy properly.<br />
Connect the power steering line assy to the power<br />
steering pump and the steering fluid reservior.<br />
• Connect the high-pressure tube to power steering<br />
• Connect the low-pressure hose to fluid reservior and<br />
Connect the power steering line assy to the steering gear<br />
• Connect the hig-pressure tube to the steering gear<br />
• Connect the low-pressure hose to the steering gear<br />
assy and tighten the clamp.<br />
52-24 POWER STEERING - POWER STEERING LINE ASSY<br />
Tighten 1 bolts attaching power steering line assy to<br />
power steering line assy.<br />
5. FILL FLUID. (Refer to “Chapter 52 power steering - steering fluid, replacement”)<br />
52-25<br />
(a) Loosen 1 power steering line assy retaining bolts.<br />
Disconnect the power steering line from power steering<br />
pump side.<br />
Separate the high-pressure tube from the power steering<br />
Loosen the clamp and separate the low-pressure hose<br />
from the steering fluid reservior.<br />
Separate the power steering line assy from the steering<br />
52-26 POWER STEERING - POWER STEERING LINE ASSY<br />
Connect the power steering line assy:Steering pump<br />
Tighten the clamp and connect the low-pressure hose<br />
52-27<br />
Tighten 1 bolt attaching power steering line assy to<br />
6. BLEED POWER STEERING SYSTEM.(Refer to “Chapter 52 power steering - steering fluid, bleeding<br />
and purifying”)<br />
52-28 POWER STEERING - STEERING GEAR ASSY<br />
STEERING GEAR ASSY<br />
3. TURN STEERING WHEEL STRAIGHTLY.<br />
tires to straight ahead.<br />
4. SEPARATE STEERING TIE ROD FROM STEERING<br />
KNUCKLE.<br />
Separate the steering tie rod LH from the steering knuckle<br />
Remove the split pin.<br />
Loosen the slotted nut.<br />
Do not reuse the removed split pin.<br />
Remove the left side steering gear rod ball and socket<br />
joints from the knuckle arm.<br />
Separate the steering tie rod RH from the steering knuckle<br />
RH.<br />
Separate the RH side by the same procedures as the LH<br />
52-29<br />
5. SEPARATE POWER STEERING LINE ASSY FROM<br />
STEERING GEAR ASSY.<br />
(a) Separate the high-pressure tube from the steering gear<br />
(b) Loosen the clamp and separate the low- pressure hose<br />
from the steering gear assy..<br />
Loosen 1 retaining bolt from power steering line assy.<br />
6. SEPARATE STEERING PROPELLER SHAFT FROM<br />
(a) Mark on the steering propeller shaft and the steering<br />
(b) Loosen the bolt.<br />
(c) Pull the steering propeller shaft up from the steering gear<br />
7. REMOVE STEERING GEAR ASSY.<br />
(a) Remove 4 bolts.<br />
52-30 POWER STEERING - STEERING GEAR ASSY<br />
Remove the steering gear assy.<br />
Take care because the steering gear assy is quite heavy.<br />
8. INSPECT STEERING GEAR ASSY.<br />
(a) Check the steering gear assy for crack by magnetic testing.<br />
If any fault is detected, replace with a new steering gear assy.<br />
(b) Check the contact area between steering tie rod B-joint<br />
steeering knuckle arm, then pull it out again. Check the<br />
Standard: red area ≤ 3/4 shaft length<br />
The red area is out of specification, replace with a new steering<br />
gear assy and steering knuckle arm. (Refer to “Chapter 52 power<br />
steering - steering gear assy, overhaul”, “Chapter 34 axle and<br />
propeller shaft - steering knuckle, overhaul”)<br />
9. INSTALL STEERING GEAR ASSY.<br />
(a) Position the steering gear assy properly.<br />
Tighten 4 bolts.<br />
Torque: 108 ~ 125 N•m<br />
52-31<br />
10. CONNECT STEERING PROPELLER SHAFT TO STEERING<br />
GEAR ASSY.<br />
(a) Install the steering propeller shaft to the steering gear<br />
(b) Tighten the bolt.<br />
Torque: 29 ~ 35 N•m<br />
11. CONNECT POWER STEERING LINE ASSY TO STEERING GEAR ASSY.<br />
Connect the high-pressure tube to steering gear assy<br />
(b) Connect the low-pressure hose to steering gear assy<br />
(c) Tighten 1 bolt attaching power steering line assy to the<br />
steering gear assy.<br />
Make sure the line assy does not be bended.<br />
12. CONNECT STEERING TIE ROD TO STEERING KNUCKLE.<br />
(a) Connect the steering tie rod LH to the steering knuckle LH.<br />
(b) Insert the steering tie rod LH B-joint shaft into the<br />
steering knuckle arm LH hole.<br />
52-32 POWER STEERING - STEERING GEAR ASSY<br />
Tighten the slotted nut.<br />
Install the cotter pin.<br />
Torque: 84 ~ 100 N•m<br />
Connect the steering gear trolley ball and socket joints<br />
Connect the RH side by the same procedures as the LH<br />
13. FILL FLUID. (Refer to “Chapter 52 power steering - power steering system, replacement”)<br />
14. INSPECT AND ADJUST FRONT WHEEL ALIGNMENT. (Refer to “Chapter 31 front suspension -<br />
STEERING FLUID RESERVIOR<br />
52-33<br />
3. REMOVE STEERING FLUID RESERVIOR.<br />
(a) Loosen clip and separate the steering low pressure hose<br />
(b) Remove the steering fluid reservior from the support.<br />
4. INSTALL STEERING FLUID RESERVIOR.<br />
(a) Position the steering fluid reservior to the support.<br />
(b) Connect the steering low- pressure hose.<br />
(c) Tighten 2 clips.<br />
6. BLEED THE POWER STEERING SYSTEM. (Refer To “chapter 52 Power Steering - Steering Fluid,<br />
Bleeding and purifying”)<br />
7. PRECAUTION. (Refer to “Chapter 52 power steering - power steering system, precaution”)<br />
HEATER AND AIR CONDITIONING SYSTEM................................. 61-1<br />
PRECAUTION.............................................................................. 61-1<br />
PROBLEM SYMPTOMS TABLE.................................................. 61-3<br />
ON-VEHICLE INSPECTION ........................................................ 61-7<br />
REFRIGERANT.................................................................................. 61-8<br />
ON-VEHICLE INSPECTION ........................................................ 61-8<br />
REPLACEMENT ........................................................................ 61-14<br />
COMPRESSOR OIL......................................................................... 61-17<br />
INSPECTION ............................................................................. 61-17<br />
REPLACEMENT ........................................................................ 61-18<br />
MULTI-MEDIA AND A/C CONTROLLER ASSY ............................. 61-19<br />
REPLACEMENT ........................................................................ 61-19<br />
REAR HEATER BLOWER CONTROL SWITCH............................. 61-21<br />
REPLACEMENT ........................................................................ 61-21<br />
REAR A/C BLOWER SWITCH ........................................................ 61-23<br />
REPLACEMENT ........................................................................ 61-23<br />
FRONT HEATER CORE .................................................................. 61-25<br />
REPLACEMENT ........................................................................ 61-25<br />
REAR HEATER CORE..................................................................... 61-35<br />
REPLACEMENT ........................................................................ 61-35<br />
FRONT EVAPORATOR CORE....................................................... 61-39<br />
REPLACEMENT ........................................................................ 61-39<br />
TOP EVAPORATOR CORE............................................................. 61-42<br />
REPLACEMENT ........................................................................ 61-42<br />
FRONT EVAPORATOR THERMISTOR .......................................... 61-46<br />
REPLACEMENT ........................................................................ 61-46<br />
TOP EVAPORATOR TEMPERATURE SENSOR............................ 61-47<br />
REPLACEMENT ........................................................................ 61-47<br />
FRONT EXPANSION VALVE .......................................................... 61-49<br />
REPLACEMENT ........................................................................ 61-49<br />
REAR EXPANSION VALVE............................................................. 61-50<br />
REPLACEMENT ........................................................................ 61-50<br />
FRONT A/C BLOWER ..................................................................... 61-52<br />
OVERHAUL ............................................................................... 61-52<br />
REAR A/C BLOWER........................................................................ 61-53<br />
OVERHAUL ............................................................................... 61-53<br />
REAR HEATER BLOWER............................................................... 61-55<br />
OVERHAUL ............................................................................... 61-55<br />
FRONT BLOWER CONTROL MODULE ......................................... 61-56<br />
REPLACEMENT ........................................................................ 61-56<br />
REAR HEATER BLOWER RESISTOR............................................ 61-57<br />
REPLACEMENT ........................................................................ 61-57<br />
TOP EVAPORATOR BLOWER RESISTOR.................................... 61-59<br />
REPLACEMENT ........................................................................ 61-59<br />
FRONT A/C VENT DUCT................................................................. 61-60<br />
REPLACEMENT ........................................................................ 61-60<br />
REAR A/C VENT DUCT................................................................... 61-62<br />
REPLACEMENT ........................................................................ 61-62<br />
RECIRCULATION DOOR MOTOR.................................................. 61-63<br />
REPLACEMENT ........................................................................ 61-63<br />
61<br />
BLEND DOOR MOTOR ................................................................... 61-65<br />
REPLACEMENT ........................................................................ 61-65<br />
MODE DOOR MOTOR ..................................................................... 61-67<br />
REPLACEMENT ........................................................................ 61-67<br />
FRONT A/C FILTER......................................................................... 61-69<br />
REPLACEMENT ........................................................................ 61-69<br />
REAR A/C FILTER SCREEN ........................................................... 61-71<br />
REPLACEMENT ........................................................................ 61-71<br />
A/C PRESSURE SWITCH................................................................ 61-72<br />
REPLACEMENT ........................................................................ 61-72<br />
REAR A/C SHUT-OFF SOLENOID VALVE..................................... 61-73<br />
REPLACEMENT ........................................................................ 61-73<br />
REAR HEATER SOLENOID VALVE ............................................... 61-75<br />
REPLACEMENT ........................................................................ 61-75<br />
COOLING FAN ASSY ...................................................................... 61-77<br />
REPLACEMENT ........................................................................ 61-77<br />
COMPRESSOR(4G69)..................................................................... 61-78<br />
OVERHAUL ............................................................................... 61-78<br />
COMPRESSOR(ISF2.8) ................................................................... 61-80<br />
OVERHAUL ............................................................................... 61-80<br />
CONDENSER ................................................................................... 61-83<br />
OVERHAUL ............................................................................... 61-83<br />
A/C RECEIVER DRIER FILTER ELEMENT .................................... 61-85<br />
REPLACEMENT ........................................................................ 61-85<br />
HEATER AND AIR CONDITIONING -<br />
AND AIR CONDITIONING<br />
1. HEATER AND AIR CONDITIONING PRECAUTION.<br />
(a) Expressions of ignition switch.<br />
61-1<br />
(b) Power off.<br />
• Before removing or installing any electrical devices, please disconnect the negative cable to prevent<br />
For the vehicle equipped with the power door locks, before disconnecting the negative battery cable,<br />
do not leave the key in the vehicle and avoid the door to be locked.<br />
• Make sure ignition switch is OFF if no specific instructions.<br />
(c) When disconnecting negative battery cable, memory of the audio system will be erased.<br />
When work is finished, reset the audio systems as they were before. ( Refer to “Audio system owner<br />
manual”)<br />
Do not handle refrigerant in an enclosed area or near<br />
the flame.<br />
Do not do welding operation to the parts filled with<br />
refrigerant.<br />
Always wear eye protection glasses.<br />
(g) Be careful not to get liquid refrigerant in your eyes or on<br />
your skin.<br />
If liquid refrigerant gets in your eyes or on your skin:<br />
• Wash the area with cool water.<br />
Do not rub your eyes or skin.<br />
• Apply clean petroleum jelly to the skin.<br />
• Go to a physician or hospital immediately for professional<br />
treatment.<br />
61-2 HEATER AND AIR CONDITIONING -<br />
Never heat container or expose it to naked flame.<br />
Be careful not to drop container and not to apply physical<br />
shocks to it.<br />
Do not operate compressor without enough refrigerant in<br />
refrigerant system.<br />
If there is no enough refrigerant in the refrigerant system,<br />
oil lubrication will be insufficient and compressor will be<br />
burned out. So take care to avoid this condition.<br />
Do not open high pressure manifold valve while<br />
compressor is operating.<br />
If the high pressure valves opened, refrigerant flows in<br />
the reverse direction and could cause the charging<br />
cylinder to rupture. So only open and close the lower<br />
pressure valve.<br />
(l) Be careful not to overcharge system with refrigerant.<br />
If refrigerant is overcharged, it causes problems such as insufficient cooling, poor fuel economy, engine<br />
overheating, etc.<br />
(m) When removing refrigerant components from a vehicle, immediately cap (seal) the component to<br />
minimize the entry of moisture from the atmosphere.<br />
(n) When installing refrigerant components to a vehicle, do not remove the caps (unseal) until just before<br />
connecting the components. Connect all refrigerant loop components as quickly as possible to<br />
minimize the entry of moisture into the system.<br />
(o) Only use the specified compressor oil from a sealed container. Immediatedly reseal containers of<br />
compressor oil. Without proper sealing, compressor oil will become moisture saturated and should not<br />
be used.<br />
(p) Avoid breathing A/C refrigerant and compressor oil vapor or mist. Exposure may irritate eyes, nose and<br />
throat. Remove R-134a from the A/C system using certified service equipment meeting requirements of<br />
R-134a recycling equipment. If accidental system discharge occurs, ventilate work area before<br />
resuming service. Additional health and safety information may be available from refrigerant and<br />
compressor oil manufacturers.<br />
(q) Do not allow compressor oil to contact with styrofoam parts. Otherwise, damage may occurr.<br />
(r) Do not store or heat refrigerant containers above 52 ℃ .<br />
(s) Do not intentionally drop, puncture, or incinerate refrigerant containers.<br />
(t) Do not do pressure test or leakage test R-134a service equipment and/or vehicle air conditioning<br />
systems with compressed air during repairing. Some mixtures of air and R-134a have been proved to<br />
be combustible at high pressure. These mixtures, if ignited, may cause injury or property damage.<br />
Additional health and safety information may be available from refrigerant manufacturers.<br />
61-3<br />
1. COOLING SYSTEM DOES NOT FUNCTION.<br />
1. Fuse (Burned) -<br />
2. Belt (Loose) -<br />
3. A/C clutch (Damaged) -<br />
4. A/C cut relay (Damaged) -<br />
Air flow normal,<br />
compressor not<br />
5. Multi-media and A/C controller<br />
assy (Damaged)<br />
6. A/C pressure switch (Damaged)<br />
8. A/C clutch relay (Damaged) -<br />
9. A/C relay (Damaged) -<br />
10.ECM (Damaged) -<br />
11.Harness (Open or short) -<br />
Chapter 61 heater and air conditioning - multi-media<br />
and A/C controller assy, replacement<br />
Chapter 61 heater and air conditioning - A/C<br />
pressure switch, replacement<br />
Chapter 61 heater and air conditioning - front<br />
evaporator thermistor, replacement<br />
12.Compressor (Damaged)<br />
Chapter 61 heater and air conditioning -compressor,<br />
Front blower inoperative<br />
Top blower inoperative<br />
1. Fuse (Damaged) -<br />
2. Harness (Open or short) -<br />
3. Multi-media and A/C controller<br />
5. Front blower motor (Damaged)<br />
Chapter 61 heater and air conditioning - front blower<br />
control module, replacement<br />
Chapter 61 heater and air conditioning - front A/C<br />
blower, replacement<br />
1. Top evaporator blower resistor Chapter 61 heater and air conditioning - top<br />
evaporator blower resistor, replacement<br />
2. Rear A/C blower<br />
Chapter 61 heater and air conditioning - rear A/C<br />
Cooling insufficient<br />
(air flow normal,<br />
compressor work)<br />
3. Rear A/C blower switch<br />
1. Refrigerant (Leaking)<br />
2. Compressor (Damaged)<br />
blower switch, replacement<br />
Chapter 61 heater and air conditioning - refrigerant,<br />
61-4 HEATER AND AIR CONDITIONING -<br />
2. COOLING SPORADIC.<br />
1. Harness (Poor contact) -<br />
2. Relay (Poor contact) -<br />
Air flow sporadic<br />
4. Multi-media and A/C controller<br />
5. Front blower control module<br />
6. Vent duct (Blocked)<br />
blower switch, replacemrnt<br />
Chapter 61 heater and air conditioning - vent duct,<br />
1. Belt (Slipping) Chapter 61 heater and air conditioning -compressor,<br />
Compressor work<br />
sporadic<br />
2. A/C clutch (Slipping)<br />
4. A/C pressure switch (Damaged)<br />
5. Compressor (Damaged)<br />
6. Harness (Poor contact) -<br />
Blower and<br />
compressor<br />
normal, but cooling<br />
1. Front evaporator thermistor<br />
(Loose)<br />
2. System block intermittently -<br />
3. COOLING INSUFFICIENT.<br />
Air abnormal<br />
61-5<br />
abnormal<br />
Pressure low on<br />
both low and high<br />
pressure sides<br />
1. A/C clutch (Slipping) Chapter 61 heater and air conditioning -compressor,<br />
2. Belt (Slipping)<br />
3. Harness (Poor contact) -<br />
4. Compressor (Damaged)<br />
2. Evaporator (Frosting)<br />
Pressure high on<br />
1. Refrigerant (Redundancy)<br />
2. Air mixed in refrigerant system<br />
3. Condenser (Surface filth<br />
blocked)<br />
4. Expansion valve (filth blocked)<br />
Chapter 61 heater and air conditioning - condenser,<br />
expansion valve, replacement<br />
Pressure too high<br />
on low pressure<br />
side,<br />
Pressure too low<br />
on high pressure<br />
Others<br />
1. Compressor (Damaged)<br />
2. Condenser (Blocked)<br />
3. Pipeline between compressor<br />
and reciever tank (Blocked)<br />
1. Temperature control knob<br />
2. Blend door motor (Damaged)<br />
4. COOLING SYSTEM BIG NOISE.<br />
1. Belt (Loose) Chapter 61 heater and air conditioning -compressor,<br />
2. Compressor bracket (Damaged) -<br />
System outer noise<br />
3. Compressor (Damaged)<br />
4. Compressor oil (Less than<br />
specification)<br />
5. A/C clutch (Slipping)<br />
Chapter 61 heater and air conditioning -compressor<br />
oil, replacement<br />
61-6 HEATER AND AIR CONDITIONING -<br />
System inner noise<br />
1. Refrigerant (Incorrect)<br />
(Slipping)<br />
5. NO HEATING OR HEATING INSUFFICIENT.<br />
1. Rear heater motor (Damaged)<br />
Chapter 61 heater and air conditioning - rear heater<br />
blower, overhaul<br />
2. Blower relay (Damaged) -<br />
No heating<br />
3. Blend door motor (Damaged)<br />
5. Rear heater solenoid valve<br />
(Damage)<br />
Chapter 61 heater and air conditioning - blend door<br />
motor, replacement<br />
and A/C controller assyr, replacemrnt<br />
1. Coolant (Insufficient) -<br />
Heating insufficient<br />
2. Front heater core (Deformation)<br />
3. Rear heater core (Deformation)<br />
4. Heater hose (Fouling or air in<br />
hose)<br />
5. Rear heater solenoid<br />
valve(Damage)<br />
6. Blend door motor (Damaged)<br />
Chapter 61 heater and air conditioning - front heater<br />
core, replacemrnt<br />
61-7<br />
1. COMPRESSOR ASSY WITH CLUTCH.<br />
(a) Connect the positive pole from the battery to cable and negative lead to the body ground.<br />
(b) Check the clutch energized or not.<br />
If operation is not as specified, replace the compressor assy.<br />
2. HEATER CORE.<br />
Add coolant to heater core and then check for leakage.<br />
3. A/C PIPE.<br />
Water immersion: With dry nitrogen pipe inside, high-pressure pipe is 3.5 MPa and low-pressure is 1.67 MPa.<br />
Immerse them in the water for 5 minutes to see whether there is bubble on the surface.<br />
4. EVAPORATOR.<br />
Water immersion: Pump 1.67 MPa pressure into the evaporator, then immerse it in the water for 5 minutes to<br />
see whether there is bubble on the surface.<br />
5. CONDENSER.<br />
Water immersion: Pump 3.5 MPa pressure into the condenser, then immerse it in the water for 3 minutes to<br />
61-8 HEATER AND AIR CONDITIONING - REFRIGERANT<br />
1. INSPECT REFRIGERANT PRESSURE WITH MANIFOLD GAUGE SET.<br />
(a) This is a method in which the trouble is located by using a manifold gauge set. Read the manifold<br />
gauge pressure when these conditions are established.<br />
Test conditions:<br />
• Temperature at the air inlet is 30 ~ 35 ℃ .<br />
• Engine running at 1500 RPM.<br />
• Blower switch at “HI” position.<br />
• Temperature control switch at “COOL” position<br />
• A/C switch ON.<br />
• Full open doors.<br />
These gauge indications are shown when the refrigerant system has been opened and the refrigerant<br />
charged without vacuum purging.<br />
• Normally function refrigerant system.<br />
Gauge reading:<br />
Low pressure side: 0.15 ~ 0.25 MPa<br />
High pressure side: 1.37 ~ 2.37 MPa<br />
• Moisture present in refrigerant system (Condition: Periodically cools and then fails to cool)<br />
Symptom Probable Cause Diagnosis Remedy<br />
During operation,<br />
pressure on low pressure<br />
side sometimes becomes<br />
a vacuum and sometimes<br />
normal.<br />
Moisture in refrigerating<br />
system freezes at<br />
expansion valve orifice<br />
causing a temporary stop<br />
of cycle. However, when it<br />
melts, normal state is<br />
restored.<br />
1. Reciever tank in<br />
oversaturated state<br />
2. Moisture in<br />
refrigerating system<br />
freezes at expansion<br />
valve orifice and<br />
blocks circulation of<br />
1. Replace condenser<br />
2. Remove moisture in<br />
cycle by repeatedly<br />
evacuating air<br />
3. Supply proper amount<br />
of new refrigerant<br />
61-9<br />
• Insufficient cooling (Condition: Cooling system does not function effectively.)<br />
Pressure low on both low<br />
and high pressure sides<br />
Insufficient cooling<br />
performance<br />
Gas leakage in<br />
refrigeration system<br />
Insufficient refrigerant<br />
Refrigerant leakage<br />
• Poor circulation of refrigerant (Condition: Cooling system does not function effectively.)<br />
1. Check for gas leakage<br />
and repair if necessary<br />
2. Supply proper amount<br />
3. If indicated pressure<br />
value is closed to 0<br />
when connecting to<br />
gauge, create the<br />
vacuum after<br />
inspecting and<br />
repairing location of<br />
leak<br />
Frost on pipe from<br />
condenser to unit<br />
Refrigerant flow<br />
obstructed by dirt in<br />
reciever tank<br />
Reciever tank clogged<br />
Replace reciever tank<br />
61-10 HEATER AND AIR CONDITIONING - REFRIGERANT<br />
• Refrigerant does not circulate (Condition: Cooling functions intermittently.)<br />
Vacuum indicated on low<br />
pressure side, very low<br />
pressure indicated on<br />
high pressure side<br />
Frost or dew seen on pipe<br />
before and after reciever<br />
tank or expansion valve<br />
1. Refrigerant flow<br />
obstructed by moisture<br />
or dirt in refrigerant<br />
2. Refrigerant flow<br />
obstructed by gas<br />
leaked from expansion<br />
Refrigerant not circulate<br />
1. Check expansion<br />
2. Clean out dirt in<br />
expansion valve by air<br />
blowing<br />
3. Replace condenser<br />
4. Evacuate air and<br />
supply proper amount<br />
of new refrigerants<br />
5. For gas leakage from<br />
expansion valve,<br />
replace expansion<br />
• Refrigerant overcharged or insufficient cooling of condenser (Condition: Cooling system does not<br />
function effectively.)<br />
Pressure too high on both<br />
low and high pressure<br />
sides<br />
1. Unable to develop<br />
sufficient performance<br />
due to excessive use<br />
of refrigeration system<br />
2. Insufficient cooling of<br />
condenser<br />
1. Excessive refrigerant<br />
in cycle<br />
2. Condnser cooling<br />
insufficient condenser<br />
fins<br />
3. Clogged at cooling fan<br />
1. Clean condenser<br />
2. Check cooling fan with<br />
cooling fan<br />
dooroperation<br />
3. If 1 and 2 are in normal<br />
state, check refrigerant<br />
and supply proper<br />
amount of refrigerant.<br />
61-11<br />
• Air present in refrigeration system (Condition: Cooling system does not function.)<br />
The low pressure pipe<br />
overheated<br />
Air entered in refrigeration<br />
1. Air present in<br />
2. Insufficient vacuum<br />
purging<br />
• Expansion valve trouble (Condition: Refrigerant functions insufficient.)<br />
1. Check compressor oil<br />
to see if it is dirty or<br />
insufficient<br />
2. Vacuumize and supply<br />
new refrigerant<br />
Frost or large amount of<br />
dew on pipe of low<br />
pressure side<br />
Trouble in expansion<br />
in low pressure pipe<br />
2. Expansion valve<br />
opened too wide<br />
Check and replace<br />
expansion valve<br />
61-12 HEATER AND AIR CONDITIONING - REFRIGERANT<br />
• Compressor failure (Condition: Refrigerant is not effective.)<br />
Pressure too high on low<br />
Pressure too low on high<br />
Internal leakage in<br />
1. Compressor failure<br />
2. Leakage from<br />
damaged valve or<br />
broken sliding parts<br />
Gauge reading (Reference)<br />
1 Blower LO Zone 2 Blower HI Zone<br />
2. LEAKAGE DETECTION WITH SOAP SOLUTION.<br />
For a large amount of leakage on refrigerant pipe connection, leakage can be detected by spraying<br />
soap liquid around the connection with a sprayer to check whether any bubble appears. This is a simple<br />
and convenient method for leakage detection, but it is unable to detect minor leakage.<br />
3. LEAKAGE DETECTION WITH NON-SELECTIVE DETECTOR.<br />
This detector can detect leakage of all kinds of liquid and gas regardless of chemical composition of the<br />
detected material. It has advantages of easy using, stable performance and low cost, etc., but it cannot<br />
be used for area detection of leakage.<br />
61-13<br />
4. LEAKAGE DETECTION WITH HALOGEN LEAKAGE DETECTOR.<br />
(a) It equipped with special sensor which can detect air compounds containing a small amount of fluorine,<br />
chlorine, bromine and iodine without interference of other materials. The great advantage of this<br />
instrument is its high sensitivity which can reduce error. Its minimum detection limit is less than 5g per<br />
year for area detection of leakage and 1.5g per year for leak-point detection (for leak-point, which leaks<br />
1.5g per year).<br />
5. LEAKAGE DETECTION WITH SPECIAL ELECTRONIC LEAKAGE DETECTOR.<br />
(a) This instrument is complicated and expensive which can detect certain compounds without interference<br />
of other materials. R-134a, a kind of special electronic leakage detector with high sensitivity and<br />
selectivity, can not only detect leak-point correctly, but also can identify whether refrigerant is R-134a<br />
type. Because it has high sensitivity, pay attention to pollution around the instrument when using it,<br />
otherwise, it may cause error report.<br />
6. LEAKAGE DETECTION WITH FLUORESCENT DYE.<br />
(a) Fluorescent dye can produce fluorescence under the irradiation of ultraviolet light. Therefore, if add this<br />
kind of dye to compressor oil or refrigerant, the leak-point can be detected through irradiating outer part<br />
of the system when the system has a leakage.<br />
61-14 HEATER AND AIR CONDITIONING - REFRIGERANT<br />
1. DISCHARGE REFRIGERANT FROM REFRIGERATION SYSTEM.<br />
(a) Turn the A/C switch ON.<br />
(b) Operate the compressor at the engine RPM 1000 for 5 to 6 minutes to circulate the refrigerant and<br />
collect compressor oil remaining in each component into the compressor as many as possible.<br />
(c) Stop the engine.<br />
Recover the refrigerant.<br />
Do not release the refrigerant into the air.<br />
2. PUMP VACUUM.<br />
Connect high pressure and low pressure gauge hoses to<br />
maintenance valve on compressor, and connect central<br />
hose to vacuum pump.<br />
Open high and low pressure valves of manifold pressure<br />
gauge, and then open the vacuum pump valve.<br />
(c) Start the vacuum pump. Keep vacuumizing for at least 20<br />
minutes to make vacuum value below -760 mmHg. Shut<br />
manual valves at both high and low pressure sides and<br />
stop vacuumizing to detect leakage.<br />
3. INSPECT LEAKAGE OF REFRIGERANT.<br />
(a) Shut valves, the gauge value shall not increase within 5 minutes. If the value increases, repair where<br />
leaks, then pump vacuum again.<br />
4. SUPPLY REFRIGERANT.<br />
(a) If there is no leakage, connect central filling hose of manifold pressure gauge with refrigerant tank.<br />
(b) Loosen the nut of manifold pressure gauge central hose, and retighten it until white gas refrigerant<br />
flows out and a “fizz” sound is heard, which indicates that air in central hose is exhausted.<br />
Open high pressure manual valve, and turn refrigerant tank<br />
upside down to SUPPLYliquid refrigerant into refrigeration<br />
system. Do not start air conditioning system at this moment<br />
to avoid back flow. Add at least 200g of refrigerant each<br />
61-15<br />
Shut high pressure manual valve and open low pressure<br />
manual valve to allow gas refrigerant to enter refrigeration<br />
system. Start the engine. The refrigerant entering from low<br />
pressure manual valve must be gasified because liquid<br />
refrigerant will cause liquid impact in compressor and<br />
damage the unit.<br />
(e) Add refrigerant according to the specified amount of the<br />
A/C system. If there is no specified amount, observe the<br />
high and low pressure gauges and the peephole of the<br />
refrigerant flow state (clear, sparkling, turbidity) to<br />
estimate the adding time.<br />
Specified value:<br />
Front and rear A/C:850 + 0/- 25 g<br />
Front A/C:700 ± 25 g<br />
When estimating refrigerant adding amount, set the<br />
basic conditions:<br />
• Radiator water temperature: maintain stable state<br />
• A/C switch: ON<br />
• Temperature regulator: adjust inner circulation air<br />
temperature to 25 ~ 30 ℃<br />
• Fan swtich: HI position<br />
• Change inner and outer air: Inner circulation<br />
• Door: full open<br />
• Window: full open<br />
• Estimate the adding amount<br />
(f) After finishing the adding process, turn the HVAC switch<br />
to OFF and wait to balance pressure condition, reopen<br />
the A/C switch to ON and begin to judge.<br />
Sparkling condition: gas and liquid refrigerant mixed<br />
state with bubble.<br />
Clear conditon: it is clear condition when all refrigerant is<br />
liquid.<br />
Turbidity condition: when the oil and refrigerant separae<br />
with each other, it shows thin ivory.<br />
Sparkling and turbidity condition: gas refrigerant and<br />
separated oil mixing state, it shows thin ivory and<br />
sparkling<br />
61-16 HEATER AND AIR CONDITIONING - REFRIGERANT<br />
Refrigerant Adding Amount<br />
Peephole Condition (After Turn<br />
On The HVAC Switch About 1<br />
Minute )<br />
High Side Pressure<br />
Suitable<br />
1.8 ~ 2.5 MPa<br />
> 2.5 MPa<br />
Insufficient<br />
1.2 MPa<br />
Above peephole conditions are visible general condition. When it is hard to judge the peephole<br />
condition due to the reasons such as external condition, it must be confirmed to inspect the pressure<br />
variation of the high pressure side (excessive adding when pressure sharply up).<br />
When adding refrigerant, pay attention to refrigerant condition variation in peephole and high side<br />
pressure variation in the pressure gauge.<br />
Shut low pressure manual valve and remove maintenance valve, then cap the valve quickly to avoid<br />
gas leakage.<br />
5. WARM UP ENGINE.<br />
6. CHECK REFRIGERANT FOR LEAKAGE. (Refer to “Chapter 61 heater and air conditioning -<br />
refrigerant, on-vehicle inspection”)<br />
COMPRESSOR OIL<br />
61-17<br />
1. CORRELATION METHOD:<br />
Take fresh compressor oil into test tube as the standard oil and also take old compressor oil into test<br />
tube, then compare the two tubes. If the color of the old compressor oil is light yellow or orange, it can<br />
be used. If it turns to bronzing turbid liquid, it can not be used.<br />
2. PAPER METHOD:<br />
Drip a drop of compressor oil on a clean white paper. After a while, check the color of the oil. If the color<br />
is light and uniform, which shows it is no impurity and can be used. If the center of the oil has black<br />
spot, which shows the oil is metamorphous and can not be used.<br />
61-18 HEATER AND AIR CONDITIONING - COMPRESSOR OIL<br />
1. RECOVER REFRIGERANT. (Refer to “Chapter 61 heater and air conditioning - refrigerant,<br />
2. DRAIN OUT COMPRESSOR OIL.<br />
(a) Remove the compressor. (Refer to “Chapter 61 heater and air conditioning - compressor, overhaul”)<br />
(b) Pour out the oil from the compressor.<br />
3. SUPPLYCOMPRESSOR OIL.<br />
(a) Install the compressor. (Refer to “Chapter 61 heater and air conditioning - compressor, overhaul”)<br />
(b) SUPPLYthe oil into the compressor as the specified value.<br />
Specified value: 180 mL<br />
• Generally, it is no need to add oil to new A/C system, because new compressor has the whole amount<br />
of the oil for the system (14% ~ 18% amount of the refrigerant ). If the A/C system has more than two<br />
times repairment or other causes the lack of compressor oil, it is need to add compressor oil. After<br />
replacing the A/C system, add compressor oil as necessary.<br />
Part Name<br />
Amount of oil<br />
Compressor -<br />
Evaporator<br />
Reciever tank<br />
5 ~ 10 ml<br />
Condenser<br />
Pipe<br />
No leakage -<br />
4. SUPPLY REFRIGERANT. (Refer to “Chapter 61 heater and air conditioning - refrigerant, replacement”)<br />
MULTI-MEDIA AND A/C CONTROLLER<br />
MULTI-MEDIA AND A/C CONTROLLER ASSY<br />
61-19<br />
2. REMOVE FRAME BEZEL OF MULTI-MEDIA AND A/C<br />
CONTROLLER ASSY.<br />
Pry frame bezel out with prying tool, be careful not to<br />
scratch frame bezel and dashboard.<br />
3. REMOVE MULTI-MEDIA AND A/C CONTROLLER<br />
Remove 4 mounting screws securing multi-media and A/C<br />
controller assy into the centre opening of dashboard.<br />
Pull multi-media and A/C controller assy out far enough<br />
to disconnect antenna cable, multi-media wire harness<br />
connectors and A/C controller wire harness connectors.<br />
Remove GPS antenna attached to the top of multi-media<br />
and A/C controller assy.<br />
Remove multi-media and A/C controller assy.<br />
61-20 HEATER AND AIR CONDITIONING -<br />
4. INSTALL MULTI-MEDIA AND A/C CONTROLLER ASSY.<br />
(a) Attach GPS antenna to the top surface of multi-media<br />
and A/C controller assy and fit the GPS connector into<br />
corresponding socket.<br />
(b) Place multi-media and A/C controller assy to the centre<br />
opening of dashboard and connect wire harness<br />
connectors to multi-media and A/C controller connector<br />
receptacle.<br />
Install multi-media and A/C controller assy into place,<br />
then tighten 4 mounting screws.<br />
Install the frame bezel and press it into place.<br />
6. INSPECT MULTI-MEDIA AND A/C CONTROLLER ASSY AND RESET RADIO STATIONS.<br />
7. CHECK TO ENSURE THAT MULTI-MEDIA AND A/C CONTROLLER ASSY WORKS PROPERLY.<br />
REAR HEATER BLOWER CONTROL<br />
SWITCH<br />
REAR HEATER BLOWER CONTROL SWITCH<br />
61-21<br />
2. REMOVE FRONT SIDE WALL GUARD BOARD. (Refer to “Chapter 88 inner/outer trim panel - left<br />
panel, replacement”)<br />
3. REMOVE REAR HEATER BLOWER SWITCH.<br />
(a) Pull out rear heater blower switch cap.<br />
Disconnect rear heater blower switch connector.<br />
Remove 2 rear heater blower switch bracket retaining<br />
screws from the back of front side wall guard board.<br />
Seperate rear heater blower switch from rear heater<br />
blower switch bracket.<br />
Remove rear heater blower switch.<br />
61-22 HEATER AND AIR CONDITIONING -<br />
4. INSTALL REAR HEATER BLOWER SWITCH.<br />
(a) Install rear heater blower switch until it snaps into<br />
bracket, then position them on rear of front side wall<br />
guard board.<br />
(b) Tighten 2 retaining screws.<br />
(c) Connect rear heater blower switch connector.<br />
Install rear heater blower switch cap.<br />
5. INSTALL FRONT SIDE WALL GUARD BOARD. (Refer to “Chapter 88 inner/outer trim panel - left<br />
(a) Turn rear heater blower switch on, confirm blower switch is functional in all positons.<br />
REAR A/C BLOWER SWITCH<br />
61-23<br />
2. REMOVE REAR A/C BLOWER SWITCH.<br />
(a) Pry up rear A/C blower switch control panel along its<br />
edge.<br />
(b) Disconnect rear A/C blower switch connector from the<br />
back of rear A/C blower switch control panel.<br />
Pull rear A/C blower switch cap out, then seperate rear<br />
A/C blower switch from rear A/C blower switch control<br />
3. INSTALL REAR A/C BLOWER SWITCH.<br />
(a) Position rear A/C blower switch on rear A/C blower<br />
switch control panel, and snap it into place.<br />
Connect the wire harness connector which extends from<br />
the mounting opening of roof panel to connector<br />
receptacle of the rear A/C blower switch integrated on<br />
rear of A/C blower switch control panel.<br />
61-24 HEATER AND AIR CONDITIONING - REAR A/C BLOWER SWITCH<br />
Position rear A/C blower switch control panel onto the<br />
opening of the roof panel and press it into place, then<br />
plug the blower switch cap.<br />
FRONT HEATER CORE<br />
61-25<br />
3. RECOVER REFRIGERANT. (Refer to “Chapter 61 heater and air conditioning - refrigerant,<br />
4. REMOVE DASHBOARD. (Refer to “Chapter 83 instrument panel - dashboard, replacement”)<br />
5. REMOVE FRONT DASHBOARD BEAM ASSY AND<br />
INSTRUMENT PANEL WIRE HARNESS.<br />
(a) Remove 5 dashboard stay retaining bolts.<br />
Remove 2 retaining bolts securing hand brake bracket to<br />
dashboard assy.<br />
Disconnect 5 electrical connectors from the left and<br />
lower side of the driver side junction box.<br />
Loosen power connecting nut in driver side junction box.<br />
Release the tab on top of driver side junction box to<br />
remove it from the dashboard beam assy.<br />
Disconnect 5 electrical connectors from the rear and<br />
right side of driver side junction box.<br />
61-26 HEATER AND AIR CONDITIONING - FRONT HEATER CORE<br />
Remove 3 retaining bolts mounting steering column to<br />
dashboard beam assy.<br />
Remove 1 retaining bolt securing clutch pedal bracket to<br />
Remove 2 retaining bolts securing A/C unit assy to dashboardb<br />
beam assy.<br />
Remove 1 retaining bolt securing A/C unit assy to dashboard<br />
Disconnect recirculation door motor connector.<br />
Remove 2 electrical wire harness ties at the bottom of<br />
the A/C unit assy.<br />
61-27<br />
Remove 1 electrical harness tie on one side of the ac<br />
Disconnect evaporator temperature sensor connector.<br />
Disconnect blend door motor connector.<br />
Disconnect blower control module connector.<br />
Disconnect mode door connector.<br />
Loosen 2 retaining bolts securing dashboard beam assy<br />
to left A pillar.<br />
to right A pillar.<br />
61-28 HEATER AND AIR CONDITIONING - FRONT HEATER CORE<br />
(t)<br />
(u)<br />
Remove front windshield lower trim cover and front wiper<br />
motor assy. (Refer to “Chapter 65 wiper and washer<br />
system - wiper link with motor assy, replacement”)<br />
Remove 2 bolts located in dedicated holes below the<br />
wiper motor that secure dashboard beam assy to front<br />
dash panel.<br />
(v)<br />
Remove dashboard beam and wire harness.<br />
Remove dashboard beam out of the vehicle carefully, do<br />
not scratch the trim panel and relevant component inside<br />
the vehicle.<br />
6. REMOVE A/C ASSY.<br />
(a) Remove the bolt securing high and low pressure pipes to<br />
evaporator core, then separate them<br />
(b) Remove clamps and separate inlet and outlet hoses from<br />
front heater core.<br />
Disconnect drain hose from A/C unit assy.<br />
61-29<br />
Remove 2 retaining bolts mounting the bottom of A/C<br />
unit assy to the body.<br />
(e) Remove A/C unit assy.<br />
Do not drag or damage relevant component while removing<br />
the A/C unit assy from the inside of the vehicle.<br />
7. REMOVE HEATER CORE.<br />
(a) Remove 3 heater core cover retaining screws.<br />
(b) Slide heater core.<br />
8. CHECK HEATER CORE.<br />
Check heater core for dust contamination and coolant<br />
leaks, if necessary, clean or replace it.<br />
9. INSTALL HEATER CORE.<br />
(a) Insert heater core into heater unit assy carefully.<br />
(b) Position heater core cover and tightern 3 retaining<br />
61-30 HEATER AND AIR CONDITIONING - FRONT HEATER CORE<br />
10. INSTALL A/C UNIT ASSY.<br />
(a) Position A/C unit assy in vehicle until it is located in place<br />
(b) Tighten 2 retaining bolts at the bottom of A/C unit assy.<br />
Connect drain hose to the A/C unit assy.<br />
Position high and low pressure pipes in place, then<br />
tighten 1 mounting bolt.<br />
Always use a new O-ring for high-pressure and low-pressure<br />
pipes before installing A/C pipes.<br />
Attach inlet and outlet hoses to the front heater core,<br />
then tighten 2 clamps.<br />
11. INSTALL DASHBOARD BEAM ASSY AND WIRE HARNESS.<br />
(a) Position dashboard into vehicle.<br />
Position dashboard beam in vehicle, do not scratch interior trim panel and related part or drag wire<br />
harness hard.<br />
61-31<br />
Tighten 2 retaining bolts mounting dashboard beam assy<br />
to front dash panel in the holes on dash panel.<br />
Tighten 2 retaining bolts mounting A/C unit assy to dashboard<br />
61-32 HEATER AND AIR CONDITIONING - FRONT HEATER CORE<br />
Tighten 3 retaining bolts mounting steering column to<br />
Tighten 1 retaining bolt securing clutch pedal bracket to<br />
Tighten 3 retaining bolts securing steering column to<br />
Connect evaporator temperature sensor connector.<br />
Connect blend door motor connector.<br />
Connect blower and blower control module connectors.<br />
Fasten 1 electrical wiring harness tie to one side of the A/C<br />
Fasten 2 electrical wire harness ties to the bottom of A/C<br />
Connect recirculation door motor connector.<br />
61-33<br />
Connect 5 electrical wire harness connectors to the back<br />
and right side of the driver side junction box.<br />
Fix the driver side junction box in place.<br />
Connect 5 electrical wire harness connectors on one<br />
side and bottom of the driver side junction box.<br />
Tighten power connecting nut located on lower driver<br />
side junction box.<br />
Tighten 2 retaining bolts mounting hand brake bracket to<br />
Tighten 5 dashboard stay retaining bolts.<br />
61-34 HEATER AND AIR CONDITIONING - FRONT HEATER CORE<br />
12. INSTALL DASHBOARD. (Refer to “Chapter 83 instrument panel - dashboard, replacement”)<br />
13. INSTALL FRONT WINDSHIELD LOWER TRIM COVER AND FRONT WIPER MOTOR ASSY. (Refer<br />
to “Chapter 65 wiper and washer system - wiper link with motor assy, replacement”)<br />
REAR HEATER CORE<br />
61-35<br />
4. REMOVE REAR HEATER ASSY.<br />
(a) Loosen water inlet and outlet hoses clamps.<br />
(b) Separate inlet and outlet hoses from rear heater pipes<br />
extending to the vehicle beneath through the floor.<br />
Disconnect rear heater assy connector.<br />
Remove 1 retaining screw in the front of rear heater assy.<br />
Remove 2 retaining screws on the back of rear heater<br />
Remove rear heater assy.<br />
5. REMOVE REAR HEATER CORE.<br />
(a) Remove 2 heater core upper cover retaining screws.<br />
61-36 HEATER AND AIR CONDITIONING - REAR HEATER CORE<br />
Remove 3 blower cover retaining screws and 1 inlet and<br />
outlet pipes retaining screw on one side of heater assy.<br />
Remove blower upper cover.<br />
Disconnect blower connector.<br />
Remove 3 blower retaining screws.<br />
Remove blower.<br />
Slide rear heater core.<br />
61-37<br />
6. CHECK REAR HEATER CORE.<br />
Check rear heater core for dust contamination and coolant<br />
leakage, if necessary ,clean or replace it.<br />
7. ASSEMBLE REAR HEATER ASSY.<br />
(a) Place rear heater core into rear heater assy.<br />
Position blower and then tighten 3 retaining screws.<br />
Connect blower connector.<br />
Install blower cover.<br />
Tighten 3 blower cover retaining screws and 1 screw on<br />
one side of the inlet and outlet pipes.<br />
61-38 HEATER AND AIR CONDITIONING - REAR HEATER CORE<br />
Install 2 blower upper cover retaining screws.<br />
8. INSTALL REAR HEATER ASSY.<br />
(a) Position rear heater assy under the passenger seat.<br />
(b) Tighten 2 retaining screws on the back of rear heater<br />
(c) Tighten 1 retaing screw in the front of rear heater assy .<br />
(d) Connect rear heater assy connector.<br />
Attach inlet and outlet hoses to rear heater core under<br />
9. FILL COOLANT. (Refer to “Chapter 17A cooling - coolant, replacement”)<br />
(a) Start the engine until it is warm, confirm rear heater is functional and no coolant leaks.<br />
FRONT EVAPORATOR CORE<br />
61-39<br />
3. RECOVER REFERGRIATANT. (Refer to “Chapter 61 heater and air conditioning - refrigerant,<br />
5. REMOVE DASHBOARD BEAM ASSY AND DASHBOARD WIRE HARNESS. (Refer to “Chapter 61<br />
heater and air conditioning - front heater core, replacement”)<br />
6. REMOVE A/C UNIT ASSY. (Refer to “Chapter 61 heater and air conditioning - front heater core,<br />
7. REMOVE FRONT HEATER CORE. (Refer to “Chapter 61 heater and air conditioning - front heater<br />
core, replacement”)<br />
8. REMOVE BLOWER ASSY.<br />
(a) Remove 3 blower assy retaining screws.<br />
Remove 2 blower assy retaining screws.<br />
Remove blower assy.<br />
9. REMOVE HEATER ASSY.<br />
(a) Remove 5 heater assy retaining screws.<br />
(b) Remove heater assy.<br />
61-40 HEATER AND AIR CONDITIONING - FRONT EVAPORATOR CORE<br />
10. REMOVE EVAPORATOR CORE.<br />
(a) Remove 9 evaporator core retaining screws.<br />
(b) Remove Front Evaporator Thermistor. (refer to “Chapter<br />
61 heater and air conditioning - front evaporator thermistor,<br />
replacement “)<br />
(c) Remove evaporator core.<br />
11. CHECK EVAPORATOR CORE.<br />
Check evaporator core for dust contamination and<br />
refrigerant leakage, if necessary, clean or replace it.<br />
12. INSTALL EVAPORATOR CORE.<br />
(a) Position evaporator core into evaporator assy .<br />
(b) Tighten 9 retaining screws.<br />
13. INSTALL FRONT EVAPORATOR THERMISTOR. (Refer to “Chapter 61 heater and air conditioning -<br />
front evaporator thermistor, replacement”)<br />
14. INSTALL HEATER ASSY.<br />
(a) Position heater assy into place.<br />
(b) Tighten 5 heater assy retaining screws<br />
61-41<br />
15. INSTALL BLOWER ASSY.<br />
(a) Position blower assy.<br />
(b) Tighten 3 blower assy retaining screws.<br />
Tighten 2 blower assy retaining screw.<br />
16. INSTALL A/C ASSY. (Refer to “Chapter 61 heater and air conditioning - front heater core,<br />
17. INSTALL DASHBOARD BEAM ASSY. (Refer to “Chapter 61 heater and air conditioning - front<br />
heater core, replacement”)<br />
18. INSTALL DASHBOARD. (Refer to “Chapter 83 instrument panel - dashboard, replacement”)<br />
19. FILL COOLANT. (Refer to “Chapter 17A cooling - coolant, replacement”)<br />
20. SUPPLY REFERGENANT. (Refer to “Chapter 61 heater and air conditioning - refrigerant,<br />
Start the vehicle and turn A/C switch on, check that A/C system is functional and no refrigerant leaks.<br />
61-42 HEATER AND AIR CONDITIONING - TOP EVAPORATOR CORE<br />
TOP EVAPORATOR CORE<br />
2. RECOVER REFRIGERANT. (Refer to “Chapter 61 heater and air conditioning - refrigerant, replacement”)<br />
3. REMOVE ROOF PANEL. (Refer to “Chapter 88 exterior and interior - roof panel, replacement”)<br />
4. REMOVE TOP EVAPORATOR ASSY.<br />
Remove high-pressure and low-pressure pipes on top<br />
evaporator.<br />
Disconnect right drain hose.<br />
Disconnect top evaporator assy connector.<br />
Disconnect left drain hose.<br />
Remove 2 retaining bolts in the front of top evaporator<br />
Remove 3 retaining bolts in the back of top evaporator<br />
Remove top evaporator assy.<br />
61-43<br />
5. REMOVE TOP EVAPORATOR CORE.<br />
Remove 19 top evaporator assy housing retaining screws.<br />
Remove top evaporator assy upper housing.<br />
Remove 1 retaining screw from the clamp securing highpressure<br />
and low-pressure pipes to lower housing.<br />
Remove top evaporator core.<br />
6. REMOVE TOP EVAPORATOR TEMPERATURE SENSOR AND FILTER SCREEN.<br />
7. CHECK TOP EVAPORATOR CORE.<br />
8. INSTALL TOP EVAPORATOR TEMPERATURE SENSOR. (Refer to “Chapter 61 heater and air<br />
conditioning - top evaporator temperature sensor, replacement”)<br />
61-44 HEATER AND AIR CONDITIONING - TOP EVAPORATOR CORE<br />
9. INSTALL TOP EVAPORATOR CORE.<br />
Position top evaporator core into top evaporator housing<br />
Tighten retaining screws on clamp securing high-pressue<br />
Install top evaporator assy upper housing, then tighten<br />
19 retaining screws.<br />
Position top evaporator on mounting bracket of roof.<br />
Tighten 5 top evaporator assy retaining bolts.<br />
61-45<br />
Replace O-ring for top evaporator high-pressure and<br />
lower-pressure pipes, then tighten high-pressure and<br />
low-pressure pipes nut.<br />
Connect right drain hose.<br />
Connect top evaporator assy wire harness connector.<br />
Connect left drain hose.<br />
10. SUPPLY REFRIGERRANT. (Refer to “Chapter 61 heater and air conditioning - refrigerant, replacement”)<br />
11. INSTALL ROOF PANEL. (Refer to “Chapter 88 exterior and interior - roof panel, replacement”)<br />
12. CHECK AFTER INSTALLATION.<br />
(a) Start the vehicle and turn A/C switch on, check that A/C system is functional and no refrigerant leaks.<br />
61-46 HEATER AND AIR CONDITIONING - FRONT EVAPORATOR THERMISTOR<br />
FRONT EVAPORATOR THERMISTOR<br />
1. DISCONNECT BATTERY NEGATIVE CABLE .<br />
2. REMOVE DASHBOARD. (Refer to “Chapter 83 instrument panel - dashboard, replacement”)<br />
3. RECOVER REFRIGERANT. (Refer to “Chapter 61 heater and air conditioning - refrigerant, replacement”)<br />
4. REMOVE FRONT A/C ASSY.(Refer to “Chapter 61 heater and air conditioning - front heater core,<br />
5. REMOVE FRONT EVAPORATOR THERMISTOR.<br />
(a) Remove blower assy and heater assy.(refer to )<br />
Remove front evaporator thermistor carefully.<br />
6. INSTALL FRONT EVAPORATOR THERMISTOR.<br />
Position front evaporator thermistor on original position,<br />
and run out thermistor wire along the slot on evaporator<br />
Install front evaporator thermistor carefully to avoid<br />
damage to the thermistor.<br />
7. ASSEMBLE A/C ASSY. (Refer to “Chapter 61 heater and air conditioning - front heater core,<br />
8. SUPPLY REFRIGERANT. (Refer to “Chapter 61 heater and air conditioning - refrigerant,<br />
9. INSTALL DASHBOARD. (Refer to “Chapter 83 instrument panel - dashboard, replacement”)<br />
TOP EVAPORATOR TEMPERATURE<br />
TOP EVAPORATOR TEMPERATURE SENSOR<br />
61-47<br />
2. REMOVE TOP EVAPORATOR CORE. (Refer to “Chapter 61 heater and air conditioning - top<br />
evaporator core, replacement”)<br />
3. REMOVE TOP EVAPORATOR TEMPERATURE SENSOR.<br />
Disconnect top evaporator temperature sensor connector.<br />
Pry out top evaporator temperature sensor clamp.<br />
61-48 HEATER AND AIR CONDITIONING -<br />
Remove top evaporator temperature sensor.<br />
4. INSTALL TOP EVAPORATOR TEMPERATURE SENSOR.<br />
(a) Position front evaporator temperature sensor on original<br />
position and remove sensor wire along the slot on evaporator<br />
Install evaporator temperature sensor carefully and avoid<br />
damage to sensor element.<br />
5. INSTALL TOP EVAPORATOR ASSY. (Refer to “Chapter 61 heater and air conditioning - top evaporator<br />
6. SUPPLY REFRIGERANT. (Refer to “Chapter 61 heater and air conditioning - refrigerant,<br />
FRONT EXPANSION VALVE<br />
61-49<br />
2. OPEN ENGINE HOOD.<br />
4. REMOVE FRONT EXPANSION VALVE.<br />
(a) Remove 1 retaining bolt securing front A/C high-pressure<br />
and low-pressure pipes to expansion valve.<br />
Remove 2 bolts securing expansion valve to evaporator<br />
core<br />
Remove expansion valve.<br />
5. INSTALL EXPANSION VALVE.<br />
(a) Install expansion valve to evaporator core.<br />
(b) Tighten 2 retaining bolts.<br />
Always use new O-ring and lubricate it with compressor oil.<br />
Install high-pressure and low-pressure pipes to expansion<br />
valve, then tighten retaining bolt.<br />
61-50 HEATER AND AIR CONDITIONING - REAR EXPANSION VALVE<br />
REAR EXPANSION VALVE<br />
2. RECOVER REFRIGERANT. (Refer to “Chapter 61 heater and air conditioning - refrigerant,<br />
4. REMOVE REAR EXPANSION VALVE.<br />
(a) Disconnect rear A/C shut off solenoid.<br />
(b) Remove retaining bolt securing rear A/C high-pressure<br />
Remove high-pressure and low-pressure pipes and shut<br />
off solenoid valve.<br />
Remove 2 rear expansion valve retaining bolts.<br />
Remove rear expansion valve.<br />
5. INSTALL REAR A/C EXPANSION VALVE.<br />
Install rear A/C expansion valve to rear A/C pipes.<br />
Always use new O-ring and lubricate it with compressor oil<br />
Tighten 2 retaining bolts.<br />
61-51<br />
Install rear A/C high-pressure and low-pressure pipes<br />
below rear A/C expansion valve, then tighten retaining<br />
Connect rear A/C shut off solenoid valve connector.<br />
Connect high-pressure and low-pressure pipes to rear A/C<br />
pipes assy, then tighten nut to standard torque.<br />
Torque: 12 ~ 15 N.m<br />
Torque: 20 ~ 26 N.m<br />
61-52 HEATER AND AIR CONDITIONING - FRONT A/C BLOWER<br />
FRONT A/C BLOWER<br />
2. REMOVE FRONT A/C BLOWER.<br />
Disconnect front A/C blower connector from behind the<br />
glove box.<br />
3. CHECK BLOWER.<br />
(a) Rotate the blade of the blower by hand, no stuck phenomenon<br />
is found.<br />
(b) Visually inspect blade of the blower, no abnormal wear<br />
is present.<br />
4. INSTALL FRONT A/C BLOWER..<br />
(a) Place front A/C blower into blower unit and tighten 3<br />
retaining screws.<br />
(b) Connect blower connector.<br />
(a) Turn front A/C switch on, confirm that blower works normally and no noise is heard.<br />
REAR A/C BLOWER<br />
61-53<br />
2. REMOVE ROOF PANEL. (Refer to “Chapter 88 exterior and interior - roof panel, replacement”)<br />
3. REMOVE LEFT TOP BLOWER.<br />
(a) Remove 3 blower cover retaining screws.<br />
(b) Remove blower cover.<br />
Remove 3 blower retaining screws in top evaporator<br />
Remove blower and disconncet blower connector.<br />
4. REMOVE RIGHT TOP BLOWER.<br />
The precedure to remove right top blower is similar to the precedure above.<br />
5. CHECK BLOWER.<br />
(b) Visually inspect blade of the blower, no abnormal wear is<br />
present.<br />
6. INSTALL LEFT BLOWER.<br />
(a) Position blower into top evaporator housing in place.<br />
(b) Tighten 3 retaining screws.<br />
(c) Connect blower connector to the back of blower.<br />
61-54 HEATER AND AIR CONDITIONING - REAR A/C BLOWER<br />
Install blower cover and tighten 3 retaining screws.<br />
7. INSTALL RIGHT BLOWER.<br />
The precedure to install right blower is similar to the precedure above.<br />
(a) Turn top evaporator blower switch on, check blower works normally and no abnormal noise is heard.<br />
9. INSTALL ROOF PANEL. (Refer to “Chapter 88 exterior and interior - roof panel, replacement”)<br />
REAR HEATER BLOWER<br />
61-55<br />
2. REMOVE REAR HEATER CORE. (Refer to “Chapter 61 heater and air conditioning - rear heater<br />
3. REMOVE REAR HEATER BLOWER. (Refer to “Chapter 61 heater and air conditioning - rear<br />
4. CHECK BLOWER.<br />
5. INSTALL REAR HEATER BLOWER. (Refer to “Chapter 61 heater and air conditioning - rear<br />
6. INSTALL REAR HEATER CORE (Refer to “Chapter 61 heater and air conditioning - rear heater<br />
7. CHECK AFTER INSTALLATION.<br />
(a) Turn rear heater blower switch on, check blower works normally and no abnormal noise is heard.<br />
61-56 HEATER AND AIR CONDITIONING - FRONT BLOWER CONTROL MODULE<br />
FRONT BLOWER CONTROL MODULE<br />
2. REMOVE FRONT BLOWER CONTROL MODULE.<br />
Disconnect front blower control module connector under<br />
the glove box.<br />
Remove 2 front blower control module retaining screws.<br />
Remove front blower control module.<br />
3. INSTALL FRONT BLOWER CONTROL MODULE.<br />
(a) Insert front blower control module into blower housing.<br />
(b) Tighten front blower control module retaining screws.<br />
(c) Connect front blower control module connector.<br />
(a) Turn front blower switch on, check front blower is operational in all positions.<br />
REAR HEATER BLOWER RESISTOR<br />
61-57<br />
2. REMOVE REAR HEATER BLOWER RESISTOR.<br />
(a) Remove 3 rear heater blower resistor upper cover<br />
Disconnect rear heater blower resistor connector.<br />
Remove 2 rear heater blower resistor retaining screws.<br />
Remove rear heater blower resistor.<br />
3. INSTALL REAR HEATER BLOWER RESISTOR.<br />
(a) Install rear heater blower resistor.<br />
61-58 HEATER AND AIR CONDITIONING - REAR HEATER BLOWER RESISTOR<br />
Install blower resistor upper cover.<br />
Tighten 3 retaining screws.<br />
(a) Turn rear heater blower switch on, check rear heater blower is operational in all positions.<br />
TOP EVAPORATOR BLOWER<br />
RESISTOR<br />
TOP EVAPORATOR BLOWER RESISTOR<br />
61-59<br />
3. REMOVE TOP EVAPORATOR BLOWER RESISTOR.<br />
(a) Disconnect blower resistor connector.<br />
(b) Remove blower resistor retaining screw.<br />
Remove blower resistor.<br />
4. INSTALL TOP EVAPORATOR BLOWER RESISTOR.<br />
(a) Insert blower resistor into top evaporator housing.<br />
(b) Tighten 1 retaining screw.<br />
(c) Connect blower resistor connector.<br />
(a) Turn top evaporator blower switch on, check top evaporator blower is operational in all positions.<br />
6. INSTALL ROOF PANEL. (Refer to “Chapter 88 exterior and interior - roof panel, replacement”)<br />
61-60 HEATER AND AIR CONDITIONING - FRONT A/C VENT DUCT<br />
FRONT A/C VENT DUCT<br />
1. INSTRUMENT PANEL VENT DUCT.<br />
(a) Remove instrument panel. (Refer to “Chapter 83<br />
instrument panel - dashboard, replacement”)<br />
A/C front and side vent duct are an integral part of<br />
instrument panel and can not be serviced or replaced<br />
separately.<br />
2. INSTALL DASHBOARD VENT DUCT. (Refer to “Chapter 83 instrument panel - dashboard,<br />
3. REMOVE LEFT FOOT DUCT.<br />
(a) Remove dashboard. (Refer to “Chapter 83 instrument panel - dashboard, replacement”)<br />
(b) Remove 4 transmission operation mechanism retaining bolts. (Refer to “Chapter 41 transmission - transmission<br />
operation mechanism assy, replacement”)<br />
Remove 3 left foot duct mounting bolts and disengage<br />
the pawls.<br />
Remove left foot duct.<br />
4. INSTALL LEFT FOOT DUCT.<br />
(a) Position left foot duct to front A/C assy and engage the<br />
pawls.<br />
(b) Tighten 3 retaining bolts.<br />
Install 4 transmission operation mechanism retaining<br />
bolts. (Refer to “Chapter 41 transmission - transmission<br />
Install dashboard. (Refer to “Chapter 83 instrument panel<br />
- dashboard, replacement”)l<br />
61-61<br />
5. REMOVE RIGHT FOOT DUCT.<br />
(a) Remove glove box to get access to right foot duct.<br />
(b) Disengage the pawl.<br />
(c) Remove right foot duct.<br />
6. INSTALL RIGHT VENT DUCT.<br />
(a) Engage right vent duct with front A/C assy.<br />
(b) Install glove box.<br />
(a) Turn front blower switch on, check rear heater blower is operational in all positions.<br />
61-62 HEATER AND AIR CONDITIONING - REAR A/C VENT DUCT<br />
REAR A/C VENT DUCT<br />
1. REMOVE REAR A/C VENT DUCT.<br />
(a) Remove roof panel. (Refer to “Chapter 88 exterior and<br />
interior - roof panel, replacement”)<br />
Rear A/C vent duct is an integral part of roof panel and can<br />
not be serviced separately.<br />
2. INSTALL REAR A/C VENT DUCT.<br />
(a) Install roof panel. (Refer to “Chapter 88 exterior and interior - roof panel, replacement”)<br />
RECIRCULATION DOOR MOTOR<br />
61-63<br />
2. REMOVE GLOVE BOX.<br />
(a) Pull glove box upward to disengage the pawl on its lower<br />
side from the latch on dashboard.<br />
(b) Remove glove box.<br />
3. REMOVE REVERSE RADAR CONTROL UNIT.<br />
(a) Disconnect reverse radar control unit connector and<br />
remove retaining bolt.<br />
(b) Remove reverse radar control unit.<br />
4. REMOVE RECIRCULATION DOOR MOTOR.<br />
(a) Disconnect recirculation door motor connector and<br />
remove 3 retaining screws.<br />
Remove recirculation door motor.<br />
61-64 HEATER AND AIR CONDITIONING - RECIRCULATION DOOR MOTOR<br />
5. INSTALL RECIRCULATION DOOR MOTOR.<br />
(a) Position recirculation door motor.<br />
(b) Tighten 3 recirculation door motor retaining screws and<br />
connect the connector.<br />
6. INSTALL REVERSE RADAR CONTROL UNIT.<br />
(a) Tighten 1 reverse radar control unit retaining bolt.<br />
(b) Connect reverse radar control unit connector.<br />
7. INSTALL GLOVE BOX.<br />
(a) Position glove box with its pawl and latch on dashboard<br />
aligned.<br />
(a) Install glove box into place.<br />
(a) Turn A/C switch on, confirm that recirculation door motor works normally.<br />
BLEND DOOR MOTOR<br />
61-65<br />
3. DRAIN COOLANT. (Refer to “Chapter 17A cooling - coolant, replacement”)<br />
4. RECOVER REFRIGERANT. (Refer to “Chapter 61 heater and air conditioning - refrigerant,<br />
5. REMOVE DASHBOARD. (Refer to “Chapter 83 instrument panel - dashboard, replacement”)<br />
6. REMOVE FRONT A/C ASSY. (Refer to “Chapter 61 heater and air conditioning - front heater<br />
7. REMOVE BLEND DOOR MOTOR.<br />
(a) Disassemble front A/C assy. (Refer to “Chapter 61 heater<br />
and air conditioning - front evaporator core, replacement”)<br />
(b) Remove 3 blend door motor retaining screws.<br />
Remove blend door motor.<br />
61-66 HEATER AND AIR CONDITIONING - BLEND DOOR MOTOR<br />
8. INSTALL BLNED DOOR MOTOR.<br />
Tighten 3 blend door motor retaining screws.<br />
Assemble front A/C assy. (Refer to “Chapter 61 heater<br />
9. INSTALL A/C ASSY. (REFER TO “CHAPTER 61 HEATER AND AIR CONDITIONING - FRONT<br />
HEATER CORE, REPLACEMENT”)<br />
10. INSTALL DASHBOARD. (Refer to “Chapter 83 instrument panel - dashboard, replacement”)<br />
11. CONNECT BATTERY NEGATIVE CABLE.<br />
12. FILL COOLANT. (Refer to “Chapter 17A cooling - coolant, replacement”)<br />
13. SUPPLY REFRIGERANT. (Refer to “Chapter 61 heater and air conditioning - refrigerant,<br />
(a) Turn A/C switch on, confirm blend door motor works normally.<br />
MODE DOOR MOTOR<br />
61-67<br />
3. REMOVE DASHBOARD. (Refer to “Chapter 83 instrument panel - dashboard, replacement”)<br />
BEFORE REMOVING DASHBOARD, ENSURE THE VENT BUTTON ON A/C CONTROLLER IS SELECTED<br />
AND AIR COMES OUT FROM THE CENTER ONLY.<br />
4. REMOVE MODE DOOR MOTOR.<br />
(a) Remove 3 mode door motor retaining screws.<br />
Remove mode door motor.<br />
5. INSTALL MODE DOOR MOTOR.<br />
(a) Tighten 3 mode door motor retainng screws.<br />
When installation, ensure the upper ventilator door in A/C<br />
assy is in a position where air comes out only from the<br />
61-68 HEATER AND AIR CONDITIONING - MODE DOOR MOTOR<br />
6. INSTALL DASHBOARD. (Refer to “Chapter 83 instrument panel - dashboard, replacement”)<br />
7. CONNECT BATTERY NEGATIVE CABLE.<br />
(a) Turn A/C switch on, confirm that mode door motor works normally.<br />
FRONT A/C FILTER<br />
61-69<br />
1. REMOVE GLOVE BOX.<br />
2. REMOVE A/C FILTER COVER.<br />
(a) Release locking tab on both sides of filter cover, then<br />
remove cover.<br />
3. SLIDE A/C FILTER.<br />
4. INSTALL A/C FILTER.<br />
Install A/C filter according to arrow direction marked on one<br />
61-70 HEATER AND AIR CONDITIONING - FRONT A/C FILTER<br />
5. INSTALL A/C FILTER COVER AND SNAP IT INTO<br />
PLACE.<br />
6. INSTALL GLOVE BOX.<br />
REAR A/C FILTER SCREEN<br />
61-71<br />
1. REMOVE ROOF PANEL. (Refer to “Chapter 88 exterior and interior - roof panel, replacement”)<br />
3. REMOVE TOP EVAPORATOR. (Refer to “Chapter 61 heater and air conditioning - top evaporator<br />
4. REMOVE REAR A/C FILTER SCREEN.<br />
(a) Remove top evaporator. (Refer to “Chapter 61 heater<br />
and air conditioning - top evaporator core, replacement”)<br />
(b) Remove adhesive tape, then remove filter screen.<br />
Replace filter screen or clean filter screen with water, then<br />
dry it with compressor air.<br />
5. INSTALL REAR A/C FILTER SCREEN.<br />
(a) Secure filter screen to the top A/C evaporator with adhesive tape.<br />
6. INSTALL TOP EVAPORATOR ASSY. (Refer to “Chapter 61 heater and air conditioning - top evaporator<br />
7. SUPPLY REFRIGERANT. (Refer to “Chapter 61 heater and air conditioning - refrigerant,<br />
8. INSTALL ROOF PANEL. (Refer to “Chapter 88 exterior and interior - roof panel, replacement”)<br />
61-72 HEATER AND AIR CONDITIONING - A/C PRESSURE SWITCH<br />
A/C PRESSURE SWITCH<br />
3. REMOVE FRONT GRILLE. (Refer to “Chapter 88 exterior amd interior trim - front grille, replacement”)<br />
4. REMOVE FRONT BUMPER. (Refer to “Chapter 88 exterior amd interior trim - front bumper assy,<br />
5. REMOVE A/C PRESSURE SWITCH .<br />
(a) Disconnect A/C pressure switch connector.<br />
Remove A/C pressure switch with suitable wrench.<br />
6. INSTALL A/C PRESSURE SWITCH.<br />
Always use new O-ring and apply compressor oil to it.<br />
Tighten A/C pressure switch to specified torque.<br />
Torque: 20 ~ 26 N·m<br />
(a) Turn A/C switch on, check that electronic fan speed is varied with the pressure in A/C line, then comfirm<br />
A/C pressure switch is functional.<br />
9. INSTALL FRONT BUMPER. (Refer to “Chapter 88 exterior amd interior trim - front bumper assy,<br />
10. INSTALL FRONT GRILLE.(Refer to “Chapter 88 exterior amd interior trim - front grille, replacement”)<br />
REAR A/C SHUT-OFF SOLENOID<br />
REAR A/C SHUT-OFF SOLENOID VALVE<br />
61-73<br />
3. REMOVE REAR A/C SHUT OFF SOLENOID VALVE.<br />
(a) Open engine ECM compartment cover behind assistant<br />
(b) Disconnect rear A/C shut off solenoid valve connector.<br />
Remove high pressure pipe above the rear A/C shut off<br />
solenoid valve.<br />
Remove A/C pipe locking nut under the vehicle.<br />
Remove rear A/C pipe and rear A/C shut off solenoid<br />
Separate rear A/C shut off solenoid valve from high<br />
pressure pipe.<br />
Remove shut off solenoid valve.<br />
4. INSTALL REAR A/C SHUT OFF SOLENOID VALVE.<br />
(a) Connect rear A/C shut off solenoid valve to upper highpressure<br />
pipe. then tighten the union nut to standard<br />
(b) Connect rear A/C pipes assy to lower high-pressure<br />
pipe, then tighten the connection nut to standard torque.<br />
Install the rear A/C shut off solenoid valve according to the<br />
arrow direction marked on it.<br />
61-74 HEATER AND AIR CONDITIONING -<br />
Connect rear A/C shut off solenoid connector.<br />
5. SUPPLY REFRIGERANT. (Refer to “Chapter 61 heater and air conditioning - refrigerant,<br />
(a) Start the vehicle and turn A/C switch on, check that rear A/C system is functional and no refrigerant<br />
leakage was present.<br />
REAR HEATER SOLENOID VALVE<br />
61-75<br />
3. REMOVE REAR HEATER SOLENOID VALVE.<br />
(a) Disconnect rear heater solenoid valve connector.<br />
Remove 2 clamps on both sides of heater hose, then<br />
separate them from rear heater solenoid valve.<br />
Remove 2 rear heater solenoid valve retaining screws.<br />
Remove rear heater solenoid valve.<br />
61-76 HEATER AND AIR CONDITIONING - REAR HEATER SOLENOID VALVE<br />
4. INSTALL REAR HEATER SOLENOID VALVE.<br />
(a) Position rear heater solenoid valve, then tighten 2<br />
Note the water flow direction and do not reverse direction<br />
when installation.<br />
Attach heater hoses to solenoid valve, then tighten<br />
clamps.<br />
Connect rear heater solenoid valve connector.<br />
(a) Fill coolant, start engine until it is warm, check both sides of solenoid valve for coolant leaks.<br />
(b) Turn rear blower switch on, confirm that rear heater is functional.<br />
61-77<br />
1. REMOVE COOLING FAN ASSY. (Refer to “Chapter 17 cooling - cooling fan assy, replacement”)<br />
2. DISASSEMBLE COOLING FAN ASSY.<br />
(a) Remove 3 cooling fan locking nuts.<br />
Remove retaining nut mounting fan blade to fan motor.<br />
3. ASSEMBLE COOLING FAN ASSY.<br />
(a) Tighten retaining nut mounting fan blade to fan motor.<br />
Tighten 3 cooling fan locking nuts.<br />
4. INSTALL COOLING FAN ASSY. (Refer to “Chapter 17 cooling - cooling fan assy, replacement”)<br />
61-78 HEATER AND AIR CONDITIONING - COMPRESSOR(4G69)<br />
COMPRESSOR(4G69)<br />
4. REMOVE COMPRESSORE BELT.<br />
(a) Loosen idler locking nut.<br />
(b) loosen idler adjustment bolt by turning it counterclockwise.<br />
(c) Remove compressor belt.<br />
5. REMOVE COMPRESSOR ASSY.<br />
Disconnect compressor connector.<br />
Loosen 2 retaining nuts mounting high-pressure and lowpressure<br />
pipes to compressor.<br />
Separate high-pressure and low-pressure pipes from<br />
compressor.<br />
Remove 4 compressor retaining bolts.<br />
Reomve compressor assy.<br />
6. CHECK COMPRESSOR OIL.<br />
(a) If replace the compressor with a new one, remove the refrigerant gas from the service valve, drain the<br />
following amount of oil from the new compressor before installing.<br />
Oil capacity inside new compressor - remaining oil amount in the removed compressor = oil<br />
amount to be drained out when replacing.<br />
61-79<br />
• When checking the compressor oil level, observe the precautions on the compressor removal/<br />
installation.<br />
• Compressor oil will remain in the pipes of the vehicle. If a new compressor is installed without<br />
draining out some oil inside, too much oil will affect heat exchange in the refrigerant cycle and<br />
cause refrigerant failure.<br />
• If the remaining oil in the removed compressor is too little in volume, oil leakage checking is<br />
• Be sure to use the right compressor oil.<br />
7. INSTALL COMPRESSOR ASSY.<br />
(a) Position the compressor properly, then tighten 4 retaining<br />
(b) Install high-pressure and low-pressure pipes, then<br />
tighten 2 retaining nuts.<br />
• Check compressor for specified oil level.<br />
• Always use new O-rings and sufficiently apply<br />
compressor oil to them.<br />
(c) Connect compressor connector.<br />
8. Connect the connector.<br />
(a) Install compressor belt.<br />
(b) Rotate adjustment bolt clockwise to keep compressor<br />
belt in proper tensiton.<br />
(c) Tighten idler locking nut.<br />
9. SUPPLY REFRIGERANT. (Refer to “Chapter 61 heater and air conditioning - refrigerant,<br />
(a) Start engine until it is warm, then turn A/C switch on, check compressor works normally and no refrigerant<br />
leaks.<br />
61-80 HEATER AND AIR CONDITIONING - COMPRESSOR(ISF2.8)<br />
COMPRESSOR(ISF2.8)<br />
(b) Turn over driver seat and open engine compartment<br />
It is recommended that the battery negative cable must be disconnected, prior to compressor<br />
removing, to avoid touching generator positive retaining nut.<br />
5. REMOVE ASSISTANT DRIVER SEAT. (Refer to “Chapter 84 seat - drive / assistant driver seat,<br />
6. OPEN ENGINE COMPARTMENT COVER UNDER<br />
(a) Open front floor covering.<br />
(b) Remove 5 retaining bolts.<br />
7. REMOVE INTAKE CORRUGATED HOSE TO TURBO<br />
CHARGER.<br />
(a) Remove band clamps from both sides of intake ripple<br />
(b) Remove intake ripple hose.<br />
8. DISCONNECT COMPRESSOR CONNECTOR.<br />
61-81<br />
9. REMOVE HIGH PRESSURE AND LOW PRESSURE<br />
PIPES ON COMPRESSOR SIDE.<br />
(a) Remove retaining bolt mounting high pressure and low<br />
Cover the inlet and outlet holes on compressor and the<br />
opening of high pressure and low pressure pipes with a<br />
clean cloth to avoid dust entering.<br />
10. REMOVE ENGINE BELT. (Refer to CUMMINS ISF SERIAL ENGINE SERVICE MANUAL)<br />
11. REMOVE COMPRESSOR ASSY. (Refer to CUMMINS ISF SERIAL ENGINE SERVICE MANUAL)<br />
12. CHECK COMPRESSOR OIL.<br />
13. INSTALL COMPRESSOR ASSY. (Refer to CUMMINS ISF SERIAL ENGINE SERVICE MANUAL)<br />
14. INSTALL COMPRESSOR ASSY.<br />
(a) Install high pressure and low pressure pipes to compressor.<br />
Torque: 40 ~ 45 N.m<br />
Always use a new O - ring to A/C pipes.<br />
15. CONNECT COMPRESSOR CONNECTOR.<br />
61-82 HEATER AND AIR CONDITIONING - COMPRESSOR(ISF2.8)<br />
16. INSTALL INTAKE RIPPLE HOSE TO TURBOCHARGER.<br />
Position intake ripple hose to turbocharger.<br />
Tighten the band clamp on both sides of intake ripple<br />
17. INSTALL ENGINE BELT. (Refer to CUMMINS ISF SERIAL ENGINE SERVICE MANUAL)<br />
18. INSTALL BATTERY NEGATIVE CABLE.<br />
19. SUPPLYREFRIGERANT. (Refer to “Chapter 61 heater and air conditioning - refrigerant,<br />
20. CHECK REFRIGERANT FOR LEAKAGE. (Refer to “Chapter 61 heater and air conditioning -<br />
21. INSTALL ENGINE COMPARTMENT COVER UNDER<br />
Cover surfacing to front floor.<br />
22. INSTALL ASSISTANT DRIVER SEAT. (Refer to “Chapter 84 seat - drive / assistant driver seat,<br />
23. PUT DOWN DRIVER SEAT AND LOCK IT.<br />
CONDENSER<br />
61-83<br />
1. REMOVE FRONT GRILLE. (Refer to “Chapter 88 exterior amd interior trim - front grille, replacement”)<br />
2. REMOVE FRONT BUMPER. (Refer to “Chapter 88 exterior amd interior trim - front bumper assy,<br />
4. REMOVE CONDENSER.<br />
(a) Loosen A/C high pressure and low pressure pipes retaining<br />
(b) Disconnect high pressure and low pressure pipes from<br />
condenser.<br />
Loosen 4 retaining bolts mounting condenser to radiator.<br />
Remove the condenser with caution.<br />
The condenser is a heat exchanger. It has many vulnerable<br />
parts (especially the heat sink) in structure and material.<br />
When removing and installing, pay attention not to<br />
dropping, colliding or scraping.<br />
5. INSTALL CONDENSER.<br />
(a) Position condenser on radiator.<br />
(b) Tighten 4 retaining bolts securing condenser to radiator.<br />
Add 20 ml compressor oil to condenser when replacing<br />
with a new condenser.<br />
61-84 HEATER AND AIR CONDITIONING - CONDENSER<br />
Install high pressure pipe to condensser, then tighten the<br />
retaining bolt.<br />
Install low pressure pipe to condensser, then tighten the<br />
Always use new O - rings and apply compressor oil to them<br />
before installing high pressure and low pressure pipes.<br />
6. SUPPLY REFRIGERANT. (Refer to “Chapter 61 heater and air conditioning - refrigerant, replacement”)<br />
7. WARM UP ENGINE.<br />
8. CHECK REFRIGERANT FOR LEAKAGE. (Refer to “Chapter 61 heater and air conditioning -<br />
A/C RECEIVER DRIER FILTER<br />
ELEMENT<br />
A/C RECEIVER DRIER FILTER ELEMENT<br />
61-85<br />
3. REMOVE CONDENSER. (Refer to “Chapter 61 heater and air conditioning - condenser, replacement”)<br />
4. REMOVE A/C RECEIVER DRIER FILTER ELEMENT.<br />
(a) Remove locking bolt from the bottom of A/C receiver<br />
drier with special wrench.<br />
Remove filter element, filter screen and locking bolt.<br />
Always use new O - ring and apply compressor oil to it<br />
before installing filter element and filter screen.<br />
5. INSTALL A/C RECEIVER DRIER FILTER ELEMENT.<br />
(a) Install new filter element and filter screen.<br />
(a) Tighten locking bolt.<br />
Torque: 30 - 35 N.m<br />
6. INSTALL CONDENSER.(Refer to “Chapter 61 heater and air conditioning - condenser,<br />
7. SUPPLY REFRIGERANT. (Refer to “Chapter 61 heater and air conditioning - refrigerant, replacement”)<br />
8. CHECK AFTER INSTALLATION .<br />
(a) Turn A/C switch on, check that A/C system works normally and no refrigerant leaks.<br />
SUPPLEMENTAL RESTRAINT SYSTEM ......................................... 62-1<br />
PRECAUTION.............................................................................. 62-1<br />
SYSTEM PRINCIPLES................................................................ 62-2<br />
SYSTEM PERFORMANCE ......................................................... 62-3<br />
ON-VEHICLE INSPECTION ........................................................ 62-4<br />
HORN SWITCH ASSY ....................................................................... 62-6<br />
REPLACEMENT .......................................................................... 62-6<br />
DISPOSAL ................................................................................... 62-9<br />
CLOCK SPRING .............................................................................. 62-13<br />
REPLACEMENT ........................................................................ 62-13<br />
RCM.................................................................................................. 62-16<br />
REPLACEMENT ........................................................................ 62-16<br />
62<br />
SUPPLEMENTAL RESTRAINT SYSTEM - SUPPLEMENTAL RESTRAINT SYSTEM<br />
62-1<br />
RESTRAINT SYSTEM<br />
• Some vehicles are equipped with SRS (Supplemental Restraint System), which contains a driver<br />
airbag. Failure to carry out service operations in the correct sequence could cause the SRS to<br />
unexpectedly deploy during servicing. It may lead to a serious accident. Furthermore, if a<br />
mistake is made in servicing the SRS, it is possible that the SRS may fail to operate when<br />
required. Before servicing (including removal or installation of parts, inspection or<br />
replacement), be sure to read the following items carefully, then follow the correct procedures<br />
described in the service manual.<br />
• Operation must be started 90 seconds after the ignition switch is turned to the “LOCK” position<br />
and the negative (-) cable and positive (+) cable are disconnected from the battery. (The SRS is<br />
equipped with a back-up power source. If operation is started within 90 seconds after<br />
disconnecting the battery negative (-) cable and positive (+) cable, the SRS may deploy.)<br />
• Do not expose the horn switch assy (with driver airbag) directly to hot air or flames.<br />
• Malfunction symptoms of the SRS are difficult to confirm, so the DTCs become the most<br />
important source of information when troubleshooting. When troubleshooting the SRS, always<br />
inspect the DTCs before disconnecting the battery.<br />
• Even in case of a minor collision that the SRS does not deploy, the horn switch assy should be<br />
inspected. (Refer to “Chapter 62 supplemental restraint system - horn switch assy, replacement”,<br />
“Chapter 62 supplemental restraint system - RCM, replacement”)<br />
• Before repairing, remove the RCM first if shocks may be applied to it during repairs.<br />
• Never use SRS related parts from another vehicle. Be sure to replace them with new parts when<br />
• Do not disassemble and repair the horn switch assy.<br />
• If the horn switch assy has been dropped, or there are cracks, dents or other faults, replace it<br />
• Use a multimeter with high impedance (10 kΩ/V minimum) for troubleshooting of the SRS electrical<br />
circuits.<br />
• Information labels are attached to the SRS components. Be sure to follow the instructions on<br />
the labels when performing operations.<br />
• After repairing on the SRS system, perform the inspection of airbag warning light. (Refer to<br />
“Chapter 04 diagnostics - supplemental restraint system, precheck”, “Chapter 04 diagnostics -<br />
supplemental restraint system, SRS warning light is always on”, “Chapter 04 diagnostics -<br />
supplemental restraint system, SRS warning light is inoperative”)<br />
• When the negative (-) cable is disconnected from the battery, the memory of the clock and audio<br />
system will be cleared. So before repairing, record the necessary data of the clock and audio<br />
system. After repairing, reset the clock and audio system. Never use a back-up power supply<br />
from another battery to avoid erasing the memory in each memory system. The back-up power<br />
supply will supply power to the SRS system. It could cause the SRS to unexpectedly deploy<br />
during servicing.<br />
62-2<br />
SYSTEM PRINCIPLES<br />
1. SYSTEM STRUCTURE.<br />
(a) The SRS system contains steering wheel assy, driver airbag, airbag wire harness, clock spring and<br />
RCM.<br />
2. SYSTEM SELF-CHECK.<br />
(a) After turning the ignition switch to the “ON” position to start the SRS, the RCM will perform self-check<br />
by the preset programme.<br />
• If the airbag warning light goes out 4 seconds after lighting up, it means that the system is normal and<br />
has passed the self-check. then the RCM enters monitoring status.<br />
• If the airbag warning light does not light up,flashes or stays on, it means that the system is abnormal<br />
and fail to pass the self-check.<br />
System temperature: - 35 ~ 85 ℃<br />
System volt: 12 ± 3 V<br />
3. SYSTEM PRINCIPLES.<br />
(a) When driving normally (including all kinds of road condition and interference), the RCM will not output<br />
the ignition signal. The drive airbag is nonoperative.<br />
(b) When the vehicle is involved in a serious frontal impact, the RCM will output the ignition signal timely to<br />
deploy the driver airbag.<br />
(c) The deployed airbag absorbs the driver’s part energy in the collision to reduce the possible injuries.<br />
• The SRS airbag just provides a further protection besides the seat belt.<br />
• To achieve the perfect protection, the driver must fasten the seat belt correctly and keep a good<br />
posture.<br />
• The technical parameters of airbag and RCM is matched each other. Never use airbag or RCM<br />
components of other brands with this product together.<br />
• It’s forbidden to maintenance in unauthorized dealer or by non-professional operators.<br />
• Never use a multimeter to measure the resistance of airbag. to prevent airbag deployed unexpectedlly.<br />
62-3<br />
SYSTEM PERFORMANCE<br />
1. AIRBAG.<br />
(a) Fuzzy state (or critical condition)<br />
• If the vehicle frontal collision strength, lower than the vehicle 23 ± 1 Km/h speed driving straight frontal<br />
walls can not be moved and will not be deformed collision strength (perpendicular to the vehicle direction),<br />
the airbag will be operative timely.<br />
• If the vehicle frontal collision strength, more than the vehicle 23 ± 1 Km/h speed driving straight frontal<br />
• If the strength of the frontal impact is within the strength of impact against unmovable and underformable<br />
walls (perpendicular to the driving direction) when driving in straight line at the speed between 13±<br />
1 Km/h and 23 ± 1 Km/h, the system will be in fuzzy control state, which is normal weather or not the<br />
airbags are deployed.<br />
(b) When a collision described below, the airbag must be deployed timely to protect the driver. In addition,<br />
the relevant laws and regulations should be complied with.<br />
(c) If the vehicle by the impact from the side or the rear, or vehicles overturning, or not by the positive<br />
impact from, the airbag will not expand in the design.<br />
(d) If the vehicle suffers a serious collision which is from the bottom, the airbag will be deployed possibly.<br />
62-4<br />
1. INSPECT HORN SWITCH ASSY (VEHICLE DOES NOT SUFFER A COLLISION).<br />
(a) Check the diagnostic system. (Refer to “Chapter 04 diagnostics - supplemental restraint system,<br />
precheck”)<br />
(b) Visual check.<br />
• Check for cuts, micro-cracks or marked discoloration on the horn switch assy surface and in<br />
the grooved portion.<br />
• Make sure there is no interference between the horn switch assy and steering wheel.<br />
• Make sure the clearance between the horn switch assy and steering wheel is uniform.<br />
• If any fault is found, replace with a new part if necessary. (Refer to “Chapter 62 supplemental<br />
restraint system, horn switch assy, replacement”, “Chapter 51 steering column - steering wheel<br />
2. INSPECT HORN SWITCH ASSY (VEHICLE SUFFERS A COLLISION BUT AIRBAG IS NOT<br />
DEPLOYED).<br />
(a) Check the diagnostic system.<br />
(b) Remove the horn switch assy. (Refer to “Chapter 62 supplemental restraint system, horn switch assy,<br />
(c) Visual check.<br />
• Check for cuts, micro-cracks or marked discoloration on<br />
the horn switch assy surface and in the grooved portion.<br />
• Check for cuts and cracks in wire harness and chipping<br />
in connectors.<br />
• Check for deformation on the steering wheel assy.<br />
• Check whether the clock spring is damaged.<br />
If any fault is found, replace with a new part if necessary. (Refer<br />
to “Chapter 62 supplemental restraint system, horn switch assy,<br />
replacement”, ”Chapter 62 supplemental restraint system - clock<br />
spring, replacement”, “Chapter 51 steering column - steering<br />
wheel assy, replacement”)<br />
(d) Install the horn switch assy. (Refer to “Chapter 62<br />
supplemental restraint system - horn switch assy,<br />
• Make sure there is no interference between the horn<br />
switch assy and steering wheel.<br />
• Make sure the clearance between the horn switch<br />
assy and steering wheel is uniform.<br />
62-5<br />
If any fault is found, replace with a new part for necessary.<br />
(Refer to “Chapter 62 supplemental restraint system, horn<br />
switch assy, replacement”, “Chapter 51 steering column -<br />
steering wheel assy, replacement”)<br />
3. INSPECT HORN SWITCH ASSY. (VEHICLE SUFFERS A COLLISION AND AIRBAG IS NOT DEPLOYED)<br />
(b) Replace the horn switch assy, clock spring, SRS wire harness and RCM with new parts. (Refer to<br />
“Chapter 62 supplemental restraint system - horn switch assy, replacement”, “ Chapter 62<br />
supplemental restraint system - clock spring, replacement”, “Chapter 62 supplemental restraint system<br />
- RCM, replacement”)<br />
If the airbag is deployed, be sure to replace all of the horn switch assy, clock spring, SRS wire harness<br />
and RCM together.<br />
4. INSPECT RCM .(VEHICLE DOES NOT SUFFER A COLLISION)<br />
5. INSPECT RCM. (VEHICLE SUFFERS A COLLISION BUT AIRBAG IS NOT DEPLOYED)<br />
6. INSPECT RCM .(VEHICLE SUFFERS A COLLISION AND AIRBAG IS DEPLOYED)<br />
“Chapter 62 supplemental restraint system - horn switch assy, replacement”, “Chapter 62 supplemental<br />
restraint system - clock spring, replacement”, “Chapter 62 supplemental restraint system - RCM,<br />
62-6<br />
SUPPLEMENTAL RESTRAINT SYSTEM - HORN SWITCH ASSY<br />
1. PRECAUTION. (Refer to “Chapter 62 supplemental restraint system - supplemental restraint<br />
system, precaution”)<br />
4. REMOVE HORN SWITCH ASSY.<br />
(a) Turn the steering wheel to its straight position and face<br />
the tires straight ahead.<br />
Using a hex spanner, loosen 2 inner hex bolts at the<br />
bottom of the steering wheel.<br />
Turn the horn switch assy over.<br />
Disconnect the horn switch wire harness connector.<br />
Remove the horn switch assy.<br />
62-7<br />
• Do not disassemble the horn switch assy.<br />
• When removing the horn switch assy or handling a<br />
new horn switch assy, it should be placed with the<br />
pad top surface upward. Placing it with the pad top<br />
surface downward may lead to a serious accident if<br />
the airbag accidently inflates. Also, do not place<br />
horn switch assy on top of one another.<br />
5. INSPECT HORN SWITCH ASSY.<br />
(a) Visually check for cuts, micro-cracks and marked discolouration on the horn switch assy top surface<br />
and in the grooved portion.<br />
62-8<br />
6. INSTALL HORN SWITCH ASSY.<br />
(a) Connect the horn switch wire harness connector.<br />
• Never use SRS parts from another vehicle. Be sure to<br />
replace them with new parts when replacing.<br />
• If the horn switch assy has been dropped, or there<br />
are cracks, dents or other faults, be sure to replace it<br />
• Do not drag the clock spring wire harness and make<br />
sure there is no interference between wire harness<br />
and parts around.<br />
If you hear a clicking sound, the connector is connected<br />
(b) Position the horn switch assy properly.<br />
Using a hex spanner, tighten 2 inner hex bolts at the<br />
Torque: 5~7 N·m<br />
7. CONNECT BATTERY POSITIVE CABLE.(Refer to “Chapter 20 starting and charging - battery,replacement”)<br />
8. CONNECT BATTERY NEGATIVE CABLE.(Refer to “Chapter 20 starting and charging - battery,replacement”)<br />
9. INSPECT SRS WARNING LIGHT<br />
62-9<br />
DISPOSAL<br />
• Never dispose of the horn switch assy with an undeployed airbag.<br />
• The airbag produces a sizable exploding sound when being deployed. So be sure to perform the<br />
operations outdoor where it will not create a nuisance to nearby residents.<br />
• When deploying the airbag, be sure to use the<br />
specified SST (SRS Airbag Deployment Tool) and<br />
perform the operations in a place away from<br />
electrical noise.<br />
• When deploying a airbag, be sure to perform the<br />
operation at least 10 m away from horn switch assy.<br />
• The horn switch assy is very hot when the airbag is<br />
depoyed. So leave it at least 30 minutes after<br />
deployment.<br />
• Use gloves and goggles when handling a horn<br />
switch assy with the deployed airbag.<br />
• Do not apply water, etc. to a horn switch assy with<br />
the deployed airbag.<br />
• Be sure to wash your hands with water after<br />
completing the operation.<br />
When disposing of the horn switch assy, be sure to follow the correct procedures described below to<br />
deploy the airbag.<br />
62-10<br />
1. CHECK FUNCTION OF SST.<br />
(a) Prepare a battery for the power supply to deploy the<br />
airbag.<br />
(b) Connect the SST to the battery.<br />
Do not connect the yellow connector which will be<br />
connected to the airbag.<br />
Press the SST activation switch, check whether the<br />
illumination lights up.<br />
Standard: Light up<br />
If the illumination lights up when the activation switch is<br />
not pressed, SST malfunction is probable. Never use this<br />
SST.<br />
Disconnect the SST from the battery.<br />
2. DISPOSE OF HORN SWITCH ASSY.<br />
• When disposing of the horn switch assy (with airbag), never use the customers’ vehicle to<br />
• Be sure to follow the procedures described below when deploying the airbag.<br />
(a) Prepare a battery for the power supply to deploy the airbag.<br />
(b) Remove the horn switch assy. (Refer to “Chapter 62 supplemental restraint system - horn switch assy,<br />
Tighten 2 bolts to the 2 bolt holes of the horn switch assy.<br />
• Tighten the bolts by hands until the bolts become<br />
hard to turn.<br />
• Do not tighten the bolts too much.<br />
• The bolts should be long enough.<br />
Connect the SST to the horn switch assy.<br />
62-11<br />
Prepare a steel rim with tire and place it level.<br />
Separately tie the left and right sides of the horn switch<br />
assy to the steel rim through the hub nut holes.<br />
• Be sure to tie down the horn switch assy with the<br />
pad surface upward.<br />
• Make sure the horn switch assy is tied down tightly.<br />
• To avoid damaging the SST connector and wire<br />
harness, secure some slack for the SST wire harness<br />
inside the steel rim.<br />
Connect the SST to the battery.<br />
Move the SST at least 10 m away from the horn switch<br />
Cover the horn switch assy with a carton or tires.<br />
• Make sure the horn switch assy is covered<br />
• Weight the carton down with at least 20 Kg.<br />
• Place at least 3 tires. In addition, always use the<br />
redundant tires which may be marked by the airbag<br />
Press the activation switch to deploy the airbag.<br />
Make sure nobody is within 10 m away from the horn switch<br />
The airbag is deployed simultaneously when the LED of the<br />
SST activation switch lights up.<br />
62-12<br />
Remove the horn switch assy from the steel rim.<br />
Put the horn switch assy in a plastic bag and tie the end<br />
tightly. Dispose of it in the same way as other general<br />
parts disposal.<br />
SUPPLEMENTAL RESTRAINT SYSTEM - CLOCK SPRING<br />
62-13<br />
CLOCK SPRING<br />
4. REMOVE HORN SWITCH ASSY. (Refer to “Chapter 51 steering column - steering wheel assy,<br />
6. REMOVE COMBINATION SWITCH COVER. (Refer to “Chapter 51 steering column - combination<br />
7. REMOVE CLOCK SPRING.<br />
(a) Disconnect 2 connectors:<br />
Remove the clock spring with 3 clips.<br />
8. INSTALL CLOCK SPRING.<br />
(a) Install the clock spring with 3 clips.<br />
62-14<br />
Connect 2 connectors:<br />
9. CENTER CLOCK SPRING.<br />
(a) Make sure the ignition switch is in the “LOCK” position.<br />
(b) Make sure the battery positive and negative cables are<br />
disconnected.<br />
Do not start the operation within 90 seconds after<br />
diconnecting the cables.<br />
There is an information label on the clock spring. Follow<br />
the instructions on the label.<br />
(c) Rotate the cable counterclockwise by hands until it<br />
becomes hard to turn.<br />
Rotate the cable clockwise about 3 turns to align the<br />
The cable will rotate above 3 turns to either left or right off<br />
the center.<br />
For a new clock spring:<br />
• It is located at the center position by clip.<br />
• Do not forget to remove the clip after installing a new<br />
clock spring.<br />
62-15<br />
10. INSTALL COMBINATION SWITCH UPPER COVER. (Refer to “Chapter 51 steering column - combination<br />
11. INSTALL STEERING WHEEL ASSY. (Refer to “Chapter 51 steering column - steering wheel assy,<br />
12. INSTALL HORN SWITCH ASSY. (Refer to “Chapter 51 steering column - steering wheel assy,<br />
13. CONNECT BATTERY POSITIVE CABLE. (If airbag is equipped, refer to “Chapter 20 starting and<br />
charging - battery, replacement”)<br />
14. CONNECT BATTERY NEGATIVE CABLE. (Refer to “Chapter 20 starting and charging - battery,<br />
15. INSPECT SRS WARNING LIGHT.<br />
62-16<br />
SUPPLEMENTAL RESTRAINT SYSTEM - RCM<br />
4. REMOVE INSTRUMENT CENTER COVER.<br />
(a) Loosen 3 screws and 2 bolts to remove the instrument<br />
center cover.<br />
The instrument cover is on the front carpet assy which is in<br />
front of the middle platform assy and under the dashboard<br />
ashtray assy.<br />
5. REMOVE RCM.<br />
(b) Make sure the battery positive and negative cables are disconnected.<br />
• Do not start the operation within 90 seconds after diconnecting the cables.<br />
• Never strike the RCM when it is energized.<br />
Disconnect the RCM wire harness connector.<br />
Loosen 3 bolts and remove the RCM.<br />
6. INSTALL RCM.<br />
62-17<br />
(c) Position the RCM properly.<br />
(d) Tighten 3 bolts by the sequence shown in the illustration.<br />
Torque: 8 ~ 10 N·m<br />
Position the RCM along the direction shown in the<br />
information label.<br />
Connect the RCM wire harness connector.<br />
7. INSTALL INSTRUMENT CENTER COVER.<br />
Tighten 3 screws and 2 bolts to install the instrument<br />
8. CONNECT BATTERY POSITIVE CABLE. (Refer to “Chapter 20 starting and charging - battery,<br />
9. CONNECT BATTERY NEGATIVE CABLE. (Refer to “Chapter 20 starting and charging - battery,<br />
10. INSPECT SRS WARNING LIGHT.<br />
SEAT BELT SYSTEM ........................................................................ 63-1<br />
PRECAUTION.............................................................................. 63-1<br />
SEAT BELT WARNING SYSTEM...................................................... 63-2<br />
PROBLEM SYMPTOMS TABLE.................................................. 63-2<br />
INSPECTION ............................................................................... 63-3<br />
DRIVER / ASSISTANT DRIVER SEAT BELT ................................... 63-4<br />
COMPONENTS ........................................................................... 63-4<br />
PASSENGER SEAT BELT ................................................................ 63-5<br />
COMPONENTS ........................................................................... 63-5<br />
SEAT BELT CATCH ASSY................................................................ 63-9<br />
REPLACEMENT .......................................................................... 63-9<br />
RETRACTOR ASSY......................................................................... 63-15<br />
OVERHAUL ............................................................................... 63-15<br />
63<br />
SEAT BELT - SEAT BELT SYSTEM<br />
63-1<br />
SEAT BELT SYSTEM<br />
BELT<br />
• Once any fault is found in the system, be sure to replace the parts (including belt, retractor, lock<br />
catch & latch, bolt and nut).<br />
• The seat belt which is not used in a collision should also be inspected and replaced if found any<br />
damage or working improperly.<br />
63-2<br />
SEAT BELT - SEAT BELT WARNING SYSTEM<br />
SEAT BELT WARNING SYSTEM<br />
Use the table below to help you find the cause of the problem. The numbers indicate the prioity of the likely<br />
1. Fuse (Burnt) -<br />
Seat belt warning light does not<br />
light up<br />
2.Intument cluster (Damaged)<br />
3.Electric lock catch assy (Damaged)<br />
Chapter 83 instrument panel-instrument<br />
cluster, replacement<br />
Chapter 63 seat belt - seat belt<br />
warning system, inspection<br />
4. Wire harness (Open or short) -<br />
63-3<br />
1. INSPECT ELECTRIC LOCK CATCH ASSY.<br />
(a) Check the resistance.<br />
Driver seat belt<br />
latch plate<br />
Terminal<br />
Pull out 1-2 < 2Ω<br />
Insert 1-2 > 1MΩ<br />
63-4<br />
SEAT BELT - DRIVER / ASSISTANT DRIVER SEAT BELT<br />
DRIVER / ASSISTANT DRIVER SEAT BELT<br />
1 Driver Seat Belt With Retractor Assy<br />
2 Webbing Lock Catch Assy<br />
3 Electric Lock Catch Assy<br />
Assistant Driver Seat Belt With Retractor<br />
SEAT BELT - PASSENGER SEAT BELT<br />
63-5<br />
PASSENGER SEAT BELT<br />
LEFT PASSENGER SEATS (2+2+2+2)<br />
1 Belt With Latch Plate Assy<br />
2 Dual Webbing Catch Assy<br />
Belt With Latch Plate And Webbing Catch<br />
63-6<br />
RIGHT PASSENGER SEATS (1+1+1)<br />
1 Seat Belt With Retractor 2 Webbing Catch Assy<br />
63-7<br />
LEFT PASSENGER SEATS (3+3)<br />
1 Belt With Latch Plate Assy 2 Dual Lock Catch Assy<br />
63-8<br />
RIGHT PASSENGER SEATS (1+1+2)<br />
1 Belt With retractor Assy<br />
2 Webbing Catch Assy<br />
3 Dual Lock Catch Assy<br />
Belt With Latch Plate And Lock Catch<br />
SEAT BELT - SEAT BELT CATCH ASSY<br />
63-9<br />
SEAT BELT CATCH ASSY<br />
1. REMOVE ELECTRIC LOCK CATCH ASSY.<br />
Remove the driver seat assy. (Refer to “ Chapter 84 seat - driver / assistant driver seat, removal &<br />
installation and disassembly & reassembly”)<br />
Loosen the screw of the seat side tirm cover.<br />
Remove the reclining adjuster trim cover electric lock<br />
catch side by the sequence shown in the illustration.<br />
• Move the trim cover backward to separate 2 slots.<br />
• Pull outward and remove the trim cover.<br />
Loosen completely the bolt attaching the electric lock<br />
catch to the driver seat reclining adjuster.<br />
63-10<br />
Remove the electric lock catch assy.<br />
Pull out the electric lock catch wire harness through the<br />
aperture between cushion pad and reclining adjuster.<br />
Be careful. Do not damage the electric lock catch wire harness<br />
2. REMOVE LOCK CATCH ASSY.<br />
• Remove the lock catch assy by the same procedures as the electric lock catch assy.<br />
• Remove the lock catch assy in step (e).<br />
• Skip step (f).<br />
3. REMOVE LEFT REAR PASSENGER SEAT WEBBING<br />
CATCH ASSY.<br />
(a) Turn over the left coner of the middle seat cushion.<br />
(c) Remove the webbing catch assy.<br />
63-11<br />
4. REMOVE THE MIDDLE REAR SEAT WEBBING CATCH.<br />
Remove seat cushion regulating handle.<br />
Loosen retaining screw.<br />
Remove the reclining adjuster trim cover.<br />
Loosen webbing catch retaining bolt.<br />
Remove webbing catch assy.<br />
5. REMOVE RIGHT REAR SEAT WEBBING CATCH ASSY.<br />
Remove the right rear seat webbing catch assy by the same procedures as the middle rear seat<br />
webbing catch assy<br />
63-12<br />
6. INSTALL ELECTRIC LOCK CATCH ASSY.<br />
Put the electric lock catch wire harness connector<br />
through the aperture between cushion pad and reclining<br />
Position the electric lock catch assy properly.<br />
Torque: 50 ~ 55 N·m<br />
Install the reclining adjuster trim cover electric lock catch<br />
sie by the sequence shown in the illustration.<br />
• Push the trim cover inward to align the slots.<br />
• Move the trim cover forward to position it properly.<br />
Tighten the screw.<br />
7. INSTALL LOCK CATCH ASSY.<br />
• Install the lock catch assy by the same procedures as the electric lock catch assy.<br />
• Position the lock catch assy properly in step (b).<br />
63-13<br />
• Skip step (a).<br />
8. INSTALL THE LEFT REAR PASSENGER SEAT WEBBING<br />
CATCH.<br />
Position the webbing catch assy.<br />
Position the seat cushion.<br />
9. INSTALL THE MIDDLE REAR PASSENGER SEAT<br />
WEBBING CATCH.<br />
(a) Position the webbing catch assy.<br />
Install the webbing catch side trim.<br />
63-14<br />
Insert seat cushion regulating handle.<br />
10. INSTALL RIGHT REAR SEAT WEBBING CATCH ASSY.<br />
Install the right rear seat webbing catch assy by the same procedures as the middle rear seat webbing<br />
catch assy.<br />
SEAT BELT - RETRACTOR ASSY<br />
63-15<br />
RETRACTOR ASSY<br />
1. REMOVE DRIVER SEAT BELT WITH RETRACTOR<br />
Turn up the trim cover, loosen the bolt.<br />
Remove the lower belt retaining bolt.<br />
(c) Remove front quarter panel guard board.(Refer to “Chapter 88<br />
exterior and interior trim - quarter panel guard board,<br />
Loosen the bolt.<br />
Remove the driver seat belt retractor assy.<br />
Never disassemble the retractor.<br />
2. REMOVE ASSISTANT DRIVER SEAT BELT WITH RETRACTOR ASSY.<br />
Remove the assistant driver seat belt with retractor by the same procedures as the driver seat belt with<br />
retractor assy.<br />
63-16<br />
3. INSPECT RETRACTOR.<br />
(a) Check whether the seat belt is locked when tilting the<br />
retractor.<br />
• Within 15° of tilt in all the directions, check that the<br />
seat belt should not be locked.<br />
• Over 45° of tilt in all the directions, check that the<br />
seat belt should be locked.<br />
If the operation is out of the specification, replace with a new<br />
driver / assistant driver seat belt with retractor assy. (Refer to<br />
“Chapter 63 seat belt - retractor assy, overhaul”)<br />
4. REMOVE LEFT REAR PASSENGER SEAT BELT WITH RETRACTOR ASSY.<br />
(a) Remove left rear passenger seat assy. (Refer to “Chapter 84 seat - driver / assistant driver seat,<br />
remove & installion and disassembly & reassemlby”)<br />
Remove seat belt with retractor assy trim cover.<br />
Loosen retractor retaining bolt, remove retractor assy.<br />
Loosen belt lower retaining bolt.<br />
Be careful not to lose gasket.<br />
Remove the belt upper retaining bolt.<br />
Remove seat belt with retractor assy.<br />
63-17<br />
5. REMOVE MIDDLE REAR PASSENGER SEAT BELT<br />
WITH RETRACTOR ASSY.<br />
Remove retractor housing.<br />
Remove the retractor retaining bolt.<br />
Remove 4 belt retaining screws.<br />
63-18<br />
Turn over the middle rear seat cushion.<br />
Loosen belt bolt.<br />
6. REMOVE RIGHT REAR ASSISTANT DRIVER SEAT BELT WITH RETRACTOR ASSY.<br />
Remove the right rear assistant driver seat belt with retractor by the same procedures as the left rear<br />
assistant driver seat belt with retractor assy.<br />
7. INSTALL DRIVER SEAT BELT RETRACTOR ASSY.<br />
(a) Position the driver seat belt retractor assy.<br />
(c) Install front quarter panel guard board.(Refer to “Chapter 88<br />
exterior and interior trim - quarter panelquarter panel guard<br />
board, replacement”)<br />
Make sure the seat belt is flat, do not kink or winding.<br />
Install belt lower retaining bolt.<br />
63-19<br />
Torque:50 ~ 55 N·m<br />
Install the trim cover.<br />
8. INSTALL ASSISTANT DRIVER SEAT BELT WITH RETRACTOR ASSY.<br />
Install the assistant driver seat belt with retractor by the same procedures as the driver seat belt with<br />
9. INSTALL LEFT REAR PASSENGER SEAT BELT WITH<br />
RETRACTOR ASSY.<br />
(a) Position the belt upper retaining bolt.<br />
(b) Tighten the belt upper retaining bolt<br />
(c) Install the trim cover.<br />
Tighten belt lower retaining bolt.<br />
Position the retractor.<br />
Tighten the retractor retaining bolt.<br />
Install belt retractor trim cover.<br />
63-20<br />
10. INSTALL MIDDLE REAR SEAT RETRACTOR.<br />
(a) Turn over the middle rear seat cushion.<br />
(b) Tighten the belt bottom retaining bolt.<br />
Install seat cushion.<br />
Tighten 4 belt retaining screws.<br />
Position the seat belt with retractor.<br />
Tighten seat belt with retractor retaining bolt.<br />
63-21<br />
Position the belt retractor housing.<br />
Install the belt retractor housing.<br />
11. INSTALL RIGHT REAR SEAT BELT WITH RETRACTOR ASSY.<br />
Install the right rear passenger belt with retractor by the same procedures as the left rear passenger<br />
belt with retractor assy.<br />
12. Inspect driver / assistant driver seat belt with retractor assy.<br />
(a) Check belt locking operation.<br />
• The belt should be locked when being dragged quickly.<br />
(b) Check children protection operation.<br />
• After extracting the belt out of the retractor completely, the retractor enters LOCK mode. In this mode,<br />
the belt only can be contracted.<br />
• When the belt contracts fully, the retractor will recover to NORMAL mode from LOCK mode.<br />
This function is used for the children protector applied to the vehicle.<br />
If the operation is out of the specification, replace with a new driver / assistant driver seat belt with retractor<br />
assy. (Refer to “Chapter 63 seat belt - retractor assy, overhaul”)<br />
LIGHTING SYSTEM........................................................................... 64-1<br />
PRECAUTION.............................................................................. 64-1<br />
FRONT COMBINATION LAMP ASSY............................................... 64-2<br />
COMPONENTS ........................................................................... 64-2<br />
REPLACEMENT .......................................................................... 64-3<br />
ADJUSTMENT............................................................................. 64-7<br />
FRONT FOG LAMP ASSY................................................................. 64-8<br />
REPLACEMENT .......................................................................... 64-8<br />
REAR COMBINATION LAMP ASSY............................................... 64-10<br />
COMPONENTS ......................................................................... 64-10<br />
REPLACEMENT ........................................................................ 64-11<br />
LICENCE LAMP ASSY .................................................................... 64-14<br />
REPLACEMENT ........................................................................ 64-14<br />
HIGH-MOUNTED STOP LAMP ASSY............................................. 64-16<br />
REPLACEMENT ........................................................................ 64-16<br />
FRONT DOME LIGHT ASSY ........................................................... 64-17<br />
REPLACEMENT ........................................................................ 64-17<br />
MIDDLE DOME LIGHT ASSY.......................................................... 64-19<br />
REPLACEMENT ........................................................................ 64-19<br />
REAR DOME LIGHT ASSY ............................................................. 64-22<br />
REPLACEMENT ........................................................................ 64-22<br />
STEP LAMP ASSY........................................................................... 64-25<br />
REPLACEMENT ........................................................................ 64-25<br />
COMBINATION SWITCH ASSY ...................................................... 64-27<br />
REPLACEMENT ........................................................................ 64-27<br />
64<br />
1. LIGHTING SYSTEM PRECAUTION.<br />
LIGHTING - LIGHTING SYSTEM<br />
64-1<br />
Even if a thin film of oil is left on the surface of the halogen lamp, its service life will be shortened because<br />
the lamp will be burned at a higher temperature.<br />
Handle any halogen lamp with great care. Dropping, hitting or damaging the bulb in any way may result<br />
in exploding and scattering because the internal pressure is high.<br />
Always use a bulb of the same wattage for replacement. Be sure not to touch the bulb immediately.<br />
Reinstall the socket firmly after bulb replacement. The lens may become cloudy or the light cavity may<br />
be filled with water through the gaps around the socket.<br />
64-2<br />
LIGHTING - FRONT COMBINATION LAMP ASSY<br />
FRONT COMBINATION LAMP ASSY<br />
6 Support Holder<br />
7 Support Holder<br />
64-3<br />
2. REMOVE FRONT COMBINATION LAMP ASSY LH.<br />
(a) Remove the front grille. (Refer to “Chapter 88 exterior and interior trim - front grille, replacement”)<br />
(b) Remove the front bumper assy. (Refer to “Chapter 88 exterior and interior trim - front bumper assy,<br />
Loosen 3 screws.<br />
Disconnect the 3 connectors and remove front combination<br />
lamp assy LH.<br />
3. REMOVE FRONT COMBINATION LAMP ASSY RH.<br />
Remove the RH side by the same procedures as the LH side.<br />
4. REMOVE HEADLAMP BULB LH.<br />
(a) Remove the cap .<br />
64-4<br />
Remove the steel wire.<br />
Remove the headlamp bulb.<br />
5. REMOVE HEADLAMP BULB RH.<br />
6. REMOVE LAMPLET BULB LH.<br />
Remove the lamp socket.<br />
Remove the lamplet bulb.<br />
7. REMOVE LAMPLET BULB RH.<br />
Remove the RH side by the same procedures as the LH side<br />
64-5<br />
8. REMOVE SIDE TURN SIGNAL LAMP BULB.<br />
Side turn signal lamp bulb is LED (Light emitting diode) it can not be replaced without the lamp socket.<br />
9. INSTALL HEADLAMP BULB LH<br />
Install the headlamp bulb, Tighten the steel wire.<br />
Install the cap.<br />
10. INSTALL HEADLAMP BULB RH.<br />
Install the RH side by the same procedures as the LH side<br />
11. INSTALL LAMPLET BULB LH.<br />
Install the lamplet bulb.<br />
Install the lamp socket.<br />
12. INSTALL LAMPLET BULB RH.<br />
64-6<br />
13. INSTALL FRONT COMBINATION LAMP ASSY LH.<br />
(a) Connect the 3 connectors to front combination lamp assy<br />
(b) Install the front combination lamp LH and tighten the 3<br />
(c) Install the front bumper assy. (Refer to “Chapter 88<br />
exterior and interior trim - front bumper assy,<br />
(d) Install the front grille. (Refer to “Chapter 88 exterior and<br />
interior trim - front grille, replacement”)<br />
14. INSTALL FRONT COMBINATION LAMP ASSY RH.<br />
Install the RH side by the same procedures as the LH side.<br />
64-7<br />
1. ADJUST THE HEADLAMP AIMING.<br />
(a) Park the vehicle in the following conditions.<br />
• The area around the headlight is not deformed.<br />
• The vehicle is parked on a level surface.<br />
• Tire inflation pressure is in the specified value. (Refer to “Chapter 33 tire and wheel - tire and wheel<br />
system, on-vehicle inspection,”)<br />
• A driver is in the driver’s seat or let something weighs 73 Kg on the seat of the vehicle; the vehicle is<br />
ready for driving. (with a tank full)<br />
(b) Check the headlamp aiming.<br />
• Park the vehicle at the flat field and make the lens surface<br />
of the headlamps be 10m away from the screen.The<br />
curtain or flat wall can be used as the screen.<br />
• Turn the headlamps on.<br />
• Check that the headlamps properly strike the position<br />
A and B shows the position of the headlamps; H shows the<br />
height of the headlamps; L1 and L2 shows the distance<br />
between the center of headlamps and the center of the<br />
• Adjust the headlamps if necessary.<br />
Adjust the adjusting screws to adjust the headlamp aiming<br />
to be within the specified range.<br />
64-8<br />
LIGHTING - FRONT FOG LAMP ASSY<br />
FRONT FOG LAMP ASSY<br />
2. REMOVE FRONT FOG LAMP ASSY LH.<br />
(a) Remove the front bumper assy. (Refer to “Chapter 88 exterior and interior trim - front bumper assy,<br />
Disconnect the connectors from the front fog lamp assy.<br />
Loosen 3 nuts and remove the front fog lamp assy LH.<br />
3. REMOVE FRONT FOG LAMP BULB LH.<br />
(a) Remove the cap.<br />
(b) Remove the steel wire.<br />
(c) Remove the front fog lamp bulb<br />
4. REMOVE FRONT FOG LAMP ASSY RH.<br />
64-9<br />
5. INSTALL FRONT FOG LAMP BULB LH.<br />
(a) Install the front fog lamp bulb.<br />
(b) Install the steel wire.<br />
(c) Install the cap.<br />
6. INSTALL FRONT FOG LAMP ASSY LH.<br />
(a) Install the front fog lamp assy and tighten 3 nuts.<br />
Connect the connectors to front fog lamp assy.<br />
Install the front bumper assy. (Refer to “Chapter 88 exterior and interior trim - front bumper assy,<br />
7. INSTALL FRONT FOG LAMP ASSY RH.<br />
64-10<br />
LIGHTING - REAR COMBINATION LAMP ASSY<br />
REAR COMBINATION LAMP ASSY<br />
1 Rear Combination Lamp Assy LH<br />
2 Support Holder<br />
3 Bolt<br />
4 Support Holder<br />
5 High-mounted Stop Lamp Assy<br />
7 License Plate Lamp Assy<br />
9 Rear Combination Lamp Assy RH<br />
10 Sealing Gasket LH<br />
11 Sealing Gasket RH<br />
6 Nut<br />
64-11<br />
2. REMOVE REAR COMBINATION LAMP ASSY LH.<br />
(a) Remove the 3 bolts.<br />
Disconnect the connector and remove rear combination<br />
3. REMOVE BULBS OF REAR COMBINATION LAMP ASSY<br />
(a) Remove the lamp sockets.<br />
Remove the bulbs.<br />
64-12<br />
4. REMOVE REAR COMBINATION LAMP ASSY RH.<br />
5. INSTALL BULBS OF REAR COMBINATION LAMP<br />
ASSY LH.<br />
Install the bulbs.<br />
Install lamp sockets.<br />
6. INSTALLE REAR COMBINATION LAMP ASSY LH.<br />
(a) Connect the connector to rear combination lamp assy<br />
Install the rear combination lamp assy LH and tighten the<br />
3 bolts.<br />
64-13<br />
7. INSTALL REAR COMBINATION LAMP ASSY RH.<br />
64-14<br />
LIGHTING - LICENCE LAMP ASSY<br />
LICENCE LAMP ASSY<br />
2. REMOVE LICENCE LAMP ASSY LH.<br />
(a) Remove 2 screws of licence lamp assy LH.<br />
Remove the lampshade.<br />
Disconnect the connector.<br />
Remove the bulb of licence lamp.<br />
3. REMOVE LICENCE LAMP ASSY RH.<br />
4. INSTALL LICENCE LAMP ASSY LH.<br />
(a) Install the bulb of licence lamp.<br />
64-15<br />
Install the lampshade.<br />
Connect the connector.<br />
5. INSTALL LICENCE LAMP ASSY RH.<br />
6. CONNECT BATTERY NEGATIVE CABLE.<br />
64-16<br />
LIGHTING - HIGH-MOUNTED STOP LAMP ASSY<br />
HIGH-MOUNTED STOP LAMP ASSY<br />
2. REMOVE HIGH-MOUNTED STOP LAMP ASSY.<br />
Remove the rear hatch upper guard board. (Refer to<br />
“Chapter 88 exterior and interior trim - vehicle door inner<br />
guard board, replacement”)<br />
Loosen 2 screws.<br />
Remove the high-mounted stop lamp assy.<br />
3. INSTALL HIGH-MOUNTED STOP LAMP ASSY.<br />
(b) Connect the connector .<br />
4. CONNECT THE BATTERY NEGATIVE GABLE.<br />
LIGHTING - FRONT DOME LIGHT ASSY<br />
64-17<br />
FRONT DOME LIGHT ASSY<br />
2. REMOVE FRONT DOME LIGHT BULB.<br />
Be carefully, do not damage interior trim.<br />
Remove the front dome light.<br />
Remove the front dome light bulb.<br />
3. INSTALL FRONT DOME LIGHT.<br />
(a) Position the front dome light bulb.<br />
64-18<br />
4. CONNECT BATTERY NEGATIVE CABLE.<br />
LIGHTING - MIDDLE DOME LIGHT ASSY<br />
64-19<br />
MIDDLE DOME LIGHT ASSY<br />
2. REMOVE MIDDLE DOME LIGHT ASSY.<br />
Loosen 2 screws<br />
Remove the middle dome light assy.<br />
3. INSTALL MIDDLE DOME LIGHT ASSY.<br />
(a) Connect the connector.<br />
64-20<br />
Tighten 2 screws<br />
4. REMOVE MIDDLE DOME LIGHT BULB.<br />
Turn up the leaf spring.<br />
Remove the dome light.<br />
Be carefully, do not damage the light.<br />
5. INSTALL MIDDLE DOME LIGHT BULB.<br />
(a) Turn up the leaf spring.<br />
(b) Install the dome light.<br />
64-21<br />
64-22<br />
LIGHTING - REAR DOME LIGHT ASSY<br />
REAR DOME LIGHT ASSY<br />
2. REMOVE REAR DOME LIGHT ASSY.<br />
Hold on both side, remove the cover of air purifier.<br />
Loosen 8 screws and 2 bolts.<br />
Disconnect 3 connectors.<br />
Remove rear dome light socket.<br />
64-23<br />
Remove rear dome light bulb.<br />
3. INSTALL REAR DOME LIGHT BULB.<br />
Position the rear dome light bulb.<br />
Connect 3 connectors<br />
Tighten 8 screws and 2 bolts.<br />
64-24<br />
Install the cover of air purifier.<br />
LIGHTING - STEP LAMP ASSY<br />
64-25<br />
STEP LAMP ASSY<br />
2. REMOVE STEP LAMP ASSY.<br />
Use a screwdriver to remove step lamp assy.<br />
Remove the step lamp assy.<br />
3. INSTALL STEP LAMP ASSY.<br />
Install step lamp assy.<br />
64-26<br />
4. REMOVE STEP LAMP BULB.<br />
Remove the step lamp lampshade.<br />
Remove the step lamp bulb.<br />
Be careful do not damage the step lamp.<br />
5. INSTALL STEP LAMP BULB.<br />
(a) Install the step lamp bulb.<br />
(b) Install the step lamp lampshade.<br />
LIGHTING - COMBINATION SWITCH ASSY<br />
64-27<br />
2. REMOVE COMBINATION SWITCH ASSY.<br />
(a) Remove the steering wheel assy. (Refer to “Chapter 51 steering column - steering wheel assy,<br />
Loosen the 2 screws.<br />
Remove the upper and lower cover.<br />
Disconnect combination switch connector.<br />
Remove combination switch assy.<br />
3. INSTALL COMBINATION SWITCH ASSY.<br />
(a) Position the combination switch.<br />
(b) Connect the combination switch connector.<br />
Install the upper and lower cover.<br />
Tighten the 2 screws.<br />
(e) Install the steering wheel assy. (Refer to “Chapter 51<br />
steering column - steering wheel assy, overhaul”)<br />
64-28<br />
WIPER AND WASHER SYSTEM....................................................... 65-1<br />
PRECAUTION.............................................................................. 65-1<br />
PROBLEM SYMPTOMS TABLE.................................................. 65-2<br />
COMPONENTS ........................................................................... 65-4<br />
WIPER ASSY ..................................................................................... 65-5<br />
REPLACEMENT .......................................................................... 65-5<br />
WIPER LINK WITH MOTOR ASSY ................................................... 65-9<br />
REPLACEMENT .......................................................................... 65-9<br />
WIPER BLADE WITH BRACKET ASSY ......................................... 65-13<br />
REPLACEMENT ........................................................................ 65-13<br />
WASHER NOZZLE........................................................................... 65-15<br />
INSPECTION ............................................................................. 65-15<br />
ADJUSTMENT........................................................................... 65-16<br />
WASHER ASSY ............................................................................... 65-17<br />
REPLACEMENT ........................................................................ 65-17<br />
WASHER PUMP ASSY.................................................................... 65-19<br />
REPLACEMENT ........................................................................ 65-19<br />
65<br />
WIPER AND WASHER - WIPER AND WASHER SYSTEM<br />
WIPER AND WASHER SYSTEM<br />
AND WASHER<br />
1. PRECAUTION ON WASHER FLUID.<br />
(a) Usually use ordinary washer fluid for window glass.<br />
(b) Sometimes use water instead of the washer fluid temporarily.<br />
(c) Be sure to fill correct washer fluid in low temperature area.<br />
(d) Never use the coolant for engine or other substitutes to prevent damage on body paint.<br />
65-1<br />
65-2<br />
Wipers do not operate<br />
2. Wiper switches (Damaged)<br />
3. Wiper motor (Damaged)<br />
combination switch assy,<br />
wiper motor assy, replacement<br />
Front wipers do not operate in LO<br />
or HI<br />
1. Front wiper switch (Damaged)<br />
2. Front wiper motor (Damaged)<br />
3. Wire harness (Open or short) -<br />
Front wipers do not operate in<br />
INT<br />
2. Solid state timer (Damaged) -<br />
3. Front wiper motor (Damaged)<br />
Rear wiper does not operate<br />
1. Rear wiper and washer switch<br />
2. Wire harness (Open or short) -<br />
Wiper arms do not stop automatically<br />
or not in correct position<br />
(Wiper switch turned off)<br />
1. Wiper arms (Installed incorrectly)<br />
2. Wiper motor (Damaged)<br />
wiper assy, replacement<br />
1. Worm (Rusty or unlubricated)<br />
2. Wiper link (Worn or deformed)<br />
3. Wiper blade assy (Aging or<br />
cracked)<br />
wiper link assy, replacement<br />
wiper blade with bracket assy,<br />
65-3<br />
Wiper less effective<br />
1. Front and rear windshield (Be<br />
soiled by oil or wax)<br />
2. Washer fluid (Poor quality) -<br />
3. Wiper blade assy (Incorrect type) -<br />
4. Wiper blade assy (Aging or<br />
5. Wiper arms (Deformed or<br />
Washers do not operate<br />
6. Wiper arms (Spring force<br />
declined)<br />
2. Rear wiper and washer switch<br />
3. Washer motor with pump assy<br />
1. Washer fluid (Low) -<br />
2. Washer fluid (Frozen) -<br />
Washer fluid does not spray or<br />
spray powerlessly<br />
Incorrect point where washer fluid<br />
spray on front / rear windshield<br />
3. Washer fluid hose (Curving or<br />
jam)<br />
4. Washer nozzle (Blocking)<br />
5. Washer motor with pump assy<br />
1. Washer nozzle (Adjustment<br />
required)<br />
washer nozzle, inspection<br />
washer nozzle, adjustment<br />
65-4<br />
VEHICLE WITH REAR WIPER ASSY<br />
1 Front Wiper Assy RH<br />
2 Front Wiper Assy LH<br />
4 Washer<br />
5 Front Link With Motor Assy<br />
6 Front Washer Assy<br />
8 Washer<br />
9 Rear Washer Assy<br />
10 Rear Wiper Assy<br />
12 Rear Link With Motor Assy<br />
WIPER AND WASHER - WIPER ASSY<br />
65-5<br />
WIPER ASSY<br />
1. REMOVE FRONT WIPER ASSY LH.<br />
(a) Remove the front wiper arm cap.<br />
Do not perform this operation when the windshield is dry to prevent<br />
scoring.<br />
Loosen the nut and remove the spring washer.<br />
Remove the front wiper assy LH.<br />
Upturn the front wiper arm LH before performing this operation.<br />
2. REMOVE FRONT WIPER ASSY RH.<br />
65-6<br />
3. REMOVE REAR WIPER ASSY.<br />
(a) Remove the rear wiper arm cap.<br />
Loosen the nut<br />
Remove the rear wiper assy.<br />
Upturn the rear wiper arm before performing this procedure.<br />
4. INSTALL FRONT WIPER ASSY LH.<br />
(a) Scrape off the spline part of the wiper arm with a round<br />
file or equivalent.<br />
(b) Clean the wiper pivot spline with the wire brush.<br />
Position the front wiper assy LH properly.<br />
Install the spring washer and tighten the nut.<br />
Torque:6 ~ 8 N·m<br />
• The front wiper blade assy LH should be located<br />
along lower edge of the windshield.<br />
• Upturn the front wiper arm LH before performing this<br />
procedure.<br />
65-7<br />
Install the front wiper arm cap.<br />
• Turn the front wiper arm LH down after performing<br />
this procedure.<br />
• Make sure the front wiper blade assy LH is located<br />
along lower edge of the rear windshield.<br />
(f) Check the automatic stop position of front wiper assy LH.<br />
• Set the front wiper switch to the “INT / LO / HI” position to<br />
activate the front wiper assy.<br />
Do not perform this operation when the windshield is dry to<br />
prevent scoring.<br />
• Set the front wiper switch to the “OFF” position to stop<br />
the front wiper assy at the automatic stop position.<br />
• Check whether the front wiper blade assy LH is located<br />
5. INSTALL FRONT WIPER ASSY RH.<br />
6. INSTALL REAR WIPER ASSY.<br />
(a) Scrape off the serration part of the wiper arm with a<br />
round file or equivalent.<br />
(b) Clean the wiper pivot serration with the wire brush.<br />
Position the rear wiper assy properly.<br />
• The rear wiper blade assy should be located along<br />
the lower edge of the rear window.<br />
• Turn the rear wiper arm up before performing this<br />
65-8<br />
Install the rear wiper arm cap.<br />
• Turn the rear wiper arm down after performing this<br />
• Make sure the rear wiper blade assy is located along<br />
lower edge of the rear window.<br />
Check the automatic position of rear wiper assy.<br />
• Set the rear wiper switch to the “INT/ON” position to<br />
activate the rear wiper assy.<br />
Do not perform this operation when the rear window is dry<br />
to prevent scoring.<br />
• Set the rear wiper switch to the “OFF” position to<br />
stop the rear wiper assy at the automatic stop<br />
• Check whether the rear wiper blade assy is located<br />
along lower edge of the rear window.<br />
WIPER AND WASHER - WIPER LINK WITH MOTOR ASSY<br />
WIPER LINK WITH MOTOR ASSY<br />
1. STOP WIPER ASSY AT AUTOMATIC STOP POSITION.<br />
(a) Stop the front wiper assy at the automatic stop position.<br />
• Set the front wiper switch to the “INT / LO / HI” position to activate the front wiper assy.<br />
65-9<br />
Do not perform this operation when the windshield is dry in order to prevent the windshield from<br />
• Set the front wiper switch to the “OFF” position to stop the front wiper assy at the automatic stop<br />
(b) Stop the rear wiper assy at the automatic stop position.<br />
• Set the rear wiper switch to the “INT / ON” position to activate the rear wiper assy.<br />
Do not perform this operation when the rear window is dry in order to prevent the windshield from<br />
• Set the rear wiper switch to the “OFF” position to stop the rear wiper assy at the automatic stop<br />
3. REMOVE FRONT WIPER LINK WITH MOTOR ASSY.<br />
(a) Open the engine hood and support it with the hood rod.<br />
Remove windshield lower trim cover side rubber strip.<br />
Loosen retaining buckles.<br />
Remove windshield lower trim cover.<br />
65-10<br />
Disconnect front wiper motor connector.<br />
Loosen 2 wiper link bolts.<br />
Remove front wiper link with motor assy.<br />
4. REMOVE REAR WIPER MOTOR WITH LINK ASSY.<br />
(a) Remove the rear wiper assy. (Refer to “Chapter 65 wiper and washer - wiper assy, replacement”)<br />
Remove the rear wiper arm shaft seal.<br />
Remove the nut.<br />
Disconnect the rear wiper motor with link assy connector.<br />
65-11<br />
Loosen 3 bolts.<br />
Remove rear wiper motor with link assy.<br />
Store the rear wiper motor with link assy carefully. Do not<br />
rotate the rocker arm of rear wiper motor with link assy.<br />
5. INSTALL FRONT WIPER LINK WITH MOTOR ASSY.<br />
(a) Tighten front wiper link with motor 2 bolts.<br />
(b) Connect motor connector.<br />
Position the windshield lower trim cover.<br />
Install clips and windshield lower trim cover.<br />
Install windshield lower trim side rubber strip.<br />
Be sure change new clips.<br />
6. INSTALL REAR WIPER MOTOR WITH LINK ASSY.<br />
(a) Position the rear wiper motor with link assy properly.<br />
(b) Tighten 3 bolts.<br />
Connect the rear wiper motor with link assy connector.<br />
65-12<br />
Install the rear hatch upper guard board. (Refer to<br />
Install the rear wiper arm shaft seal.<br />
Install the rear wiper assy. (Refer to “Chapter 65 wiper<br />
and washer - wiper assy, replacement”)<br />
7. CONNECT BATTERY NEGATIVE CABLE. (Refer to “Chapter 20 starting and charging - battery,<br />
replacement”).<br />
8. CHECK AUTOMATIC STOP POSITION OF WIPER ASSY.<br />
(a) Check automatic stop position of the front wiper assy LH.<br />
• Check whether the front wiper blade assy LH is located along lower edge of the windshield.<br />
(b) Check the automatic position of rear wiper assy.<br />
• Check whether the rear wiper blade assy is located along lower edge of the rear window.<br />
WIPER AND WASHER - WIPER BLADE WITH BRACKET ASSY<br />
65-13<br />
WIPER BLADE WITH BRACKET ASSY<br />
1. REMOVE FRONT WIPER BLADE WITH BRACKET ASSY LH.<br />
(a) Upturn the front wiper blade bracket assy LH.<br />
Press the latch plate.<br />
(c) Remove the front wiper blade with bracket assy LH.<br />
2. REMOVE FRONT WIPER BLADE WITH BRACKET ASSY RH.<br />
3. REMOVE REAR WIPER BLADE WITH BRACKET ASSY.<br />
Remove the rear side by the same procedures as the front side.<br />
4. INSTALL FRONT WIPER BLADE WITH BRACKET<br />
(a) Position the front wiper blade with bracket assy LH.<br />
(b) Turn the front wiper blade bracket assy LH down.<br />
65-14<br />
Install the front wiper blade with bracket assy LH.<br />
If hear a “click”, the front wiper blade assy is connected to<br />
the front wiper link assy completely.<br />
Turn the front wiper blade with brackte assy LH down.<br />
5. INSTALL FRONT WIPER BLADE WITH BRACKET ASSY RH.<br />
6. INSTALL REAR WIPER BLADE WITH BRACKET ASSY.<br />
Install the rear side by the same procedures as the front side.<br />
WIPER AND WASHER - WASHER NOZZLE<br />
65-15<br />
WASHER NOZZLE<br />
1. INSPECT WASHER NOZZLE.<br />
(a) Set the front washer switch to the “ON” position. Check the point which the washer fluid sprays on<br />
windshield is in the range shown in the illustration.<br />
Set the rear wiper and washer switch and check the point which the washer fluid spray on rear window<br />
is in the range shown in the illustration.<br />
65-16<br />
1. ADJUST WASHER NOZZLE.<br />
(a) Check the point which the washer fluid sprays on windshield and rear window. (Refer to “Chapter 65<br />
wiper and washer - washer nozzle, inspection”)<br />
(b) Insert a needle or equivalent into the nozzle to adjust until the point which the washer fluid sprays on<br />
windshield and rear window is within the range specified.<br />
WIPER AND WASHER - WASHER ASSY<br />
65-17<br />
WASHER ASSY<br />
1. REMOVE WASHER ASSY.<br />
(b) Disconnect washer pump connector and water pipe.<br />
Remove the washer assy.<br />
2. INSTALL WASHER ASSY.<br />
Position the washer assy.<br />
65-18<br />
Connect washer pump connector and water pipe.<br />
Tighten 2 screws, install the washer assy.<br />
WIPER AND WASHER - WASHER PUMP ASSY<br />
65-19<br />
WASHER PUMP ASSY<br />
1. REMOVE WASHER PUMP ASSY.<br />
(a) Disconnect washer pump connector.<br />
(b) Remove washer assy.(Refer to “Chapter 65 wiper and<br />
washer - washer assy, replacement”)<br />
(c) Disconnect washer pump pipe.<br />
(d) Remove washer pump.<br />
Do not reuse the seal ring again.<br />
2. INSTALL WASHER PUMP ASSY.<br />
(a) Replacement the seal ring.<br />
(b) Position the washer pump.<br />
Connect washer pump pipe.<br />
Install washer assy.(Refer to “Chapter 65 wiper and<br />
65-20<br />
Connect the washer pump connector.<br />
AUDIO SYSTEM................................................................................. 66-1<br />
COMPONENTS ........................................................................... 66-1<br />
MULTI-MEDIA AND AIR-CONDITON CONTROLLER ASSY ........... 66-2<br />
REPLACEMENT .......................................................................... 66-2<br />
FRONT SPEAKER ASSY .................................................................. 66-4<br />
REPLACEMENT .......................................................................... 66-4<br />
MIDDLE SPEAKER ASSY................................................................. 66-6<br />
REPLACEMENT .......................................................................... 66-6<br />
REAR SPERKER ASSY..................................................................... 66-8<br />
REPLACEMENT .......................................................................... 66-8<br />
TELESCOPIC ANTENNA ASSY...................................................... 66-10<br />
REPLACEMENT ........................................................................ 66-10<br />
ELECTRIC DEVICE ACCESSORIES .............................................. 66-12<br />
REPLACEMENT ........................................................................ 66-12<br />
66<br />
AUDIO SYSTEM - AUDIO SYSTEM<br />
66-1<br />
1 Telescopic Antenna Mounting Bolt<br />
2 Telescopic Antenna Assy<br />
3 Telescopic Antenna Clamp<br />
4 Water Pipe Inner Rubber Block<br />
Multi-media and Air-condition Controller<br />
7 Spring Washer<br />
8 Flat Washer<br />
9 Screw and Big Washer Set<br />
10 Front Speaker Assy<br />
11 Screw and Flat Washer Set<br />
12 Plastic Nut<br />
13 Speaker Assy RR<br />
14 Speaker Assy RL<br />
66-2<br />
AUDIO SYSTEM - MULTI-MEDIA AND AIR-CONDITON CONTROLLER ASSY<br />
MULTI-MEDIA AND AIR-CONDITON CONTROLLER ASSY<br />
2. REMOVE EXTERIOR FRAME OF MULTI-MEDIA AND<br />
AIR-CONDITION CONTROLLER ASSY.<br />
Pry out the frame with plastic trim stick, be careful not damage<br />
exterior frame and panel.<br />
3. REMOVE MULTI-MEDIA AND AIR-CONDITION CON-<br />
TROLLER ASSY.<br />
Remove 4 mounting screws of Multi-media and aircondition<br />
controller assy.<br />
Take out Multi-media and air-condition assy,disconnect<br />
connector of Multi-media and air-condition controller assy<br />
with telescopic antenna,power supply,signal wire,aircondition<br />
wire.<br />
Remove GPS antenna.<br />
Remove Multi-media and air-condition controller assy.<br />
66-3<br />
4. INSTALL MULTI-MEDIA AND AIR-CONDITION CONTROLLER<br />
Install GPS antenna.<br />
Reconnect connector of multi-media and air-condition<br />
controller assy with telescopic antenna, power supply,<br />
signal wire, air-condition wire.<br />
Replace multi-media and air-condition controller assy, tighten<br />
4 mounting screws of multi-media and air-condition controller<br />
5. INSTALL EXTER-FRAME OF MULTI-MEDIA AND AIR-<br />
CONDITION CONTROLLER ASSY.<br />
6. RECONNECT BATTERY NEGATIVE CABLE.<br />
7. INSPECT MULTI-MEDIA AND AIR-CONDITION CONTROLLER ASSY, RESET THE STATIONS.<br />
8. INSPECT MULTI-MEDIA AND AIR-CONDITION CONTROLLER ASSY FOR ITS PROPER<br />
OPERATION.<br />
66-4<br />
AUDIO SYSTEM - FRONT SPEAKER ASSY<br />
FRONT SPEAKER ASSY<br />
2. REMOVE FRONT DOOR INNER GUARD PLATE ASSY LH. (Refer to “Chapter 88 exterior and<br />
interior trim - vehicle door inner guard board, replacement”)<br />
3. REMOVE FRONT SPEAKER ASSY LH.<br />
(a) Remove the 3 screws from front speaker assy LH.<br />
Take down the front speaker assy LH and disconnect the<br />
Remove the front speaker assy LH.<br />
4. INSTALL FRONT SPEAKER ASSY LH.<br />
(a) Reconnect conector of front speaker LH.<br />
66-5<br />
Position front sperker LH, tighten 3 mounting screws.<br />
5. INSTALL FRONT DOOR INNER GUARD PLATE ASSY LH. (Refer to “Chapter 88 exterior and<br />
7. INSPECT FRONT SPEAKER ASSY LH FOR ITS PROPER OPERATION.<br />
8. REMOVE AND INSTALL FRONT SPEAKER ASSY RH.<br />
66-6<br />
AUDIO SYSTEM - MIDDLE SPEAKER ASSY<br />
MIDDLE SPEAKER ASSY<br />
2. REMOVE ROOF GUARD BOARD.(Refer to “Chapter 88 exterior and interior trim - roof guard<br />
board inner trim, replacement”)<br />
3. Remove middle speaker assy LH.<br />
(a) Remove 2 mounting screws of middle speaker LH.<br />
Take down middle speaker assy LH, disconnect connector<br />
of middle speaker LH.<br />
Remove the middle speaker assy LH.<br />
4. INSTALL MIDDLE SPEAKER ASSY LH.<br />
(a) reconnect the connector of middle speaker assy LH.<br />
66-7<br />
Position middle speaker assy LH, tighten 2 mounting<br />
5. INSTALL ROOF GUARD BOARD.(Refer to “Chapter 88 exterior and interior trim - roof guard<br />
7. INSPECT MIDDLE SPEAKER ASSY LH FOR ITS PROPER OPERATION.<br />
8. REMOVE AND INSTALL MIDDLE SPEAKER ASSY RH.<br />
66-8<br />
AUDIO SYSTEM - REAR SPERKER ASSY<br />
REAR SPERKER ASSY<br />
2. REMOVE SIDE WALL REAR LOWER GUARD BOARD LH. (Refer to “Chapter 88 exterior and<br />
interior trim - side wall guard board, replacement”)<br />
3. REMOVE REAR SPEAKER ASSY LH.<br />
(a) Remove 3 screws from rear speaker assy LH.<br />
Take down rear speaker assy LH, disconnect the<br />
connector of rear speaker assy LH.<br />
Remove the rear speaker assy LH.<br />
4. NSTALL REAR SPEAKER ASSY LH.<br />
(a) Reconnect the connector of the rear speaker assy LH.<br />
66-9<br />
Position the rear speaker assy LH,Tighten 3 mounting<br />
5. INSTALL SIDE WALL REAR LOWER GUARD BOARD LH. (Refer to “Chapter 88 exterior and<br />
7. INSPECT REAR SPEAKER ASSY LH FOR ITS PROPER OPERATION.<br />
8. REMOVE AND INSTALL REAR SPEAKER RH.<br />
66-10<br />
AUDIO SYSTEM - TELESCOPIC ANTENNA ASSY<br />
TELESCOPIC ANTENNA ASSY<br />
2. REMOVE MULTI-MEDIA AND AIR-CONDITION CONTROLLER ASSY.(Refer to “Chapter 66 audio<br />
system - Multi-media and Air-condition controller assy, replacement”)<br />
3. REMOVE DASHBOARD. (Refer to“Chapter 88 instrument panel-dashboard,replacement)<br />
4. REMOVE TELESCOPIC ANTENNA ASSY.<br />
(a) Release 7 retaining clips of telescopic antenna.<br />
Remove 2 mounting bolts of telescopic antenna, pull out<br />
the telescopic antenna.<br />
Telescopic antenna should prevent from break when you<br />
pull out it.<br />
5. INSTALL TELESCOPIC ANTENNA ASSY.<br />
(a) Insert telescopic antenna from outside, replace it, tighten<br />
2 mounting bolt of external telescopic antenna.<br />
66-11<br />
Engage 7 retaining clips of telescopic antenna.<br />
6. INSTALL DASHBOARD. (Refer to“Chapter 88 instrument panel-dashboard,replacement)<br />
7. INSTALL MULTI-MEDIA AND AIR-CONDITION CONTROLLER ASSY. (Refer to “Chapter 66 audio<br />
66-12<br />
AUDIO SYSTEM - ELECTRIC DEVICE ACCESSORIES<br />
ELECTRIC DEVICE ACCESSORIES<br />
2. REMOVE CIGARETTE LIGHTER ASSY.<br />
(a) Pull out cigarette lighter connector.<br />
Pull out cigarette lighter body from dash board by using<br />
Disconnect cigarette lighter connector.<br />
Remove cigarette lighter assy.<br />
66-13<br />
3. REMOVE 12 V POWER SOCKET ASSY.<br />
Loosen rear retaining ring.<br />
Disconnect connector of power suply line.<br />
Remove 12V power socket assy.<br />
4. INSTALL 12 V POWER SOCKET ASSY.<br />
Reconnect connector of power suply line.<br />
Position12V power socket assy, tighten rear retaining<br />
66-14<br />
5. INSTALL CIGARETTE LIGHTER ASSY.<br />
Make sure that conduction aperture has already install to<br />
the dash board.<br />
Install cigarette lighter to conduction aperture.<br />
Install the cigarette lighter.<br />
6. INSTALL CIGARETTE LIGHTER.<br />
7. INSPECT ELECTRIC DEVICE ACCESSORIES FOR ITS PROPER OPERATION.<br />
WIRING<br />
HOW TO USE THIS MANUAL........................................................... 71-1<br />
INTRODUCTION.......................................................................... 71-1<br />
SYSTEM WIRING DIAGRAM SECTION EXAMPLE ................... 71-2<br />
POWER SOURCE SECTION EXAMPLE .................................... 71-5<br />
CONNECTOR VIEWS SECTION EXAMPLE .............................. 71-6<br />
GLOSSARY OF TERMS AND SYMBOLS................................... 71-7<br />
FUSE AND RELAY LOCATIONS ................................................ 71-9<br />
WIRING DIAGRAM .......................................................................... 71-18<br />
POWER SOURCE ..................................................................... 71-18<br />
ENGINE CONTROL SYSTEM................................................... 71-24<br />
STARTING SYSTEM ................................................................. 71-37<br />
CHARGING SYSTEM................................................................ 71-39<br />
ANTI-LOCK BRAKE CONTROL SYSTEM ................................ 71-41<br />
HEATER AND CONDITIONING CONTROL SYSTEM.............. 71-44<br />
LIGHT SYSTEM......................................................................... 71-52<br />
WIPER AND WASHER.............................................................. 71-77<br />
MULTIMEDIA SYSTEM ............................................................. 71-80<br />
POWER SOCKET...................................................................... 71-83<br />
COMMUNICATION SYSTEM .................................................... 71-85<br />
POWER MIRROR...................................................................... 71-90<br />
WINDOW DEFROSTER ............................................................ 71-93<br />
INSTRUMENT CLUSTER.......................................................... 71-96<br />
ANTI-THEIF SYSTEM.............................................................. 71-103<br />
SLIDING ROOF ....................................................................... 71-108<br />
RESTRAINT CONTROL SYSTEM .......................................... 71-110<br />
CONNECTOR VIEWS .................................................................... 71-112<br />
A - CHASSIS & FRAME WIRE HARNESS ............................ 71-112<br />
B - BATTERY WIRE HARNESS .............................................. 71-125<br />
C - FRONT BUMPER WIRE HARNESS.................................. 71-126<br />
D - FRONT DOOR LH WIRE HARNESS................................. 71-127<br />
E - ENGINE WIRE HARNESS................................................. 71-130<br />
F - ROOF WIRE HARNESS 1.................................................. 71-142<br />
G - ROOF WIRE HARNESS 2................................................. 71-146<br />
H - FRONT DOOR RH WIRE HARNESS ................................ 71-148<br />
I - INSTRUMENT PANEL WIRE HARNESS............................ 71-150<br />
J - REAR HATCH WIRE HARNESS........................................ 71-166<br />
K - REAR HATCH TRANSITION WIRE HARNESS................. 71-168<br />
L - REAR EVAPORATOR WIRE HARNESS ........................... 71-169<br />
M - DIAGNOSIS WIRE HARNESS .......................................... 71-170<br />
N - STEP LAMP WIRE HARNESS .......................................... 71-171<br />
O - DRIVER SEAT BELT WIRE HARNESS ............................ 71-172<br />
P - REAR HEATER WIRE HARNESS ..................................... 71-173<br />
Q - REAR BUMPER TRANSITION WIRE HARNESS ............. 71-174<br />
R - REAR BUMPER WIRE HARNESS .................................... 71-175<br />
S - REAR DEFROST RH WIRE HARNESS ............................ 71-176<br />
T - REAR DEFROST LH WIRE HARNESS ............................. 71-177<br />
U - HIGH-MOUNTED STOP LAMP WIRE HARNESS........... 71-178<br />
V - FRONT WIRE HARNESS................................................. 71-179<br />
X - PREHEATING WIRE HARNESS ....................................... 71-185<br />
71<br />
WIRE HARNESS & CONNECTOR LOCATION VIEWS................ 71-186<br />
C - FRONT BUMPER WIRE HARNESS.................................. 71-186<br />
V - FRONT WIRE HARNESS .................................................. 71-186<br />
D - FRONT DOOR LH WIRE HARNESS................................. 71-188<br />
H - FRONT DOOR RH WIRE HARNESS ................................ 71-189<br />
A - CHASSIS & FRAME WIRE HARNESS .............................. 71-190<br />
E - ENGINE WIRE HARNESS ................................................. 71-193<br />
I - INSTRUMENT PANEL WIRE HARNESS............................ 71-196<br />
M - DIAGNOSIS WIRE HARNESS .......................................... 71-196<br />
B - BATTERY WIRE HARNESS .............................................. 71-199<br />
O - DRIVER SEAT BELT WIRE HARNESS ............................ 71-199<br />
P - REAR HEATER WIRE HARNESS ..................................... 71-199<br />
X - PREHEATING WIRE HARNESS ....................................... 71-199<br />
F - ROOF WIRE HARNESS 1.................................................. 71-201<br />
L - REAR EVAPORATOR WIRE HARNESS ........................... 71-202<br />
N - STEP LAMP WIRE HARNESS .......................................... 71-203<br />
G - ROOF WIRE HARNESS 2 ................................................. 71-204<br />
J - REAR HATCH WIRE HARNESS ........................................ 71-204<br />
K - REAR HATCH TRANSITION WIRE HARNESS................. 71-204<br />
Q - REAR BUMPER TRANSITION WIRE HARNESS ............. 71-204<br />
R - REAR BUMPER WIRE HARNESS .................................... 71-204<br />
S - REAR DEFROST RH WIRE HARNESS ............................ 71-204<br />
T - REAR DEFROST LH WIRE HARNESS ............................. 71-204<br />
U - HIGH-MOUNTED STOP LAMP WIRE HARNESS............. 71-204<br />
WIRING - HOW TO USE THIS MANUAL<br />
71-1<br />
This manual provides information on the electrical circuits installed on vehicles by dividing them into electrical<br />
systems. The actual wiring of each system wiring diagram is shown from the point where the power source is<br />
received from the battery to each ground point. (All wiring diagrams are shown with the switches in the OFF<br />
position.)<br />
When troubleshooting any problem, firstly, make sure you understand the operation of the circuit where the<br />
problem was detected (see System Wiring Diagram Section). Secondly, understand the power source supplying<br />
to that circuit (see Power Source Section). Finally, understand the direction of current flow (see System<br />
Description).<br />
When the circuit operation is understood, begin troubleshooting of the suspected circuit to find out the cause.<br />
(Based on relays, controllers, accessory, inlines, sensors, actuators, switches, ground points, connection location<br />
of each system wiring diagram and wire harness location.)<br />
71-2<br />
SYSTEM WIRING DIAGRAM SECTION EXAMPLE<br />
*The system wiring diagram shown here is an EXAMPLE ONLY. It is different to the actual circuit<br />
shown in the SYSTEM WIRING DIAGRAM SECTION.<br />
71-3<br />
No. Name Description<br />
1 System Title Distinguish between different systems and functions, easy to query.<br />
Indicates the<br />
wire color<br />
Wire colors are indicated by an alphabetical code,easy to query.<br />
The first letter indicates the basic wire color and the second letter indicates<br />
the color of the stripe.<br />
R (Red)<br />
L-B (Blue and Black)<br />
component name<br />
component number<br />
Name of electrical component, easy to query.<br />
An electrical component can only have one name.<br />
Number of electrical component, easy to query.<br />
An electrical component has one or more numbers.<br />
Female and male connectors have different numbering rules.<br />
The two examples below are viewed from terminal side when connectors are<br />
unplugged.<br />
Female - Numbered in order from upper right to lower left.<br />
Indicates the pin number<br />
of<br />
connector<br />
Male - Numbered in order from upper left to lower right.<br />
This rules also applied to inline connector number.<br />
6 Indicates a ground point<br />
The first letter of the code for each ground point(s) indicates the component’s<br />
Indicates related<br />
Indicates inline<br />
connector number<br />
Indicate that other system(s) associated with this system.<br />
A group of inline has two connector numbers, one is the female and the other<br />
is the male.<br />
Male:<br />
gender<br />
Female:<br />
71-4<br />
10 System Description Describe the current flows and how the system works.<br />
11 Service Hints Describe the component's value and principle. Refer in the service process.<br />
12 Parts Location Indicate the wire harness showing the parts location on the vehicle.<br />
13 Inline Indicate the inline two parts gender and the connected wire harness types.<br />
14 Ground Points Indicate the ground location of each wire harness.<br />
71-5<br />
POWER SOURCE SECTION EXAMPLE<br />
The “POWER SOURCE” section describes how the current flows and each part power feed conditions. In the<br />
POWER SOURCE wiring diagram, the conditions when battery power is supplied to each system are explained.<br />
Since all system wiring diagrams start from the power source, the power source system must be fully<br />
understood.<br />
71-6<br />
CONNECTOR VIEWS SECTION EXAMPLE<br />
*The connector views shown here is an EXAMPLE ONLY. It is different to the actual connector views<br />
shown in the CONNECTOR VIEWS SECTION.<br />
1 Connector Face Indicate connector face and pin order.<br />
2 Component Name<br />
3 Component Number<br />
4 Connector Information Indicate pin number, wire color and function.<br />
71-7<br />
GLOSSARY OF TERMS AND SYMBOLS<br />
Stores chemical energy and converts it into electrical energy.<br />
Provides DC current for the auto’s various electrical circuits.<br />
GROUND<br />
The point at which wiring attaches to the body, thereby providing a<br />
return path for an electrical circuit. Without a ground, current cannot<br />
flow.<br />
FUSIBLE LINK<br />
FUSE<br />
In high amperage circuits, a heavy gauge wire burns when it is overloaded<br />
to protect the connected components.<br />
A thin metal strip burns when too much current flows through it,<br />
thereby it can stop current flow and protect a circuit from damage.<br />
COIL<br />
When the magnetic field engenders fluctuations, the coil circuit is<br />
induced electromotive force.<br />
SOLENOID<br />
An electromagnetic coil which forms a magnetic field when current<br />
flows, to move a plunger, etc.<br />
SINGLE FILAMENT<br />
LAMPS<br />
Current flow causes a headlight filament to heat up and emit light. A<br />
headlight may have either a single filament or double filaments.<br />
DOUBLE FILAMENT<br />
A power unit which converts electrical energy into mechanical<br />
energy, especially rotary motion.<br />
SPEED MOTOR<br />
INLINE<br />
Indicate the connector joining wire harness and wire harness.<br />
DIODE<br />
A semiconductor which allows current flow in only one direction.<br />
LED (LIGHT EMITTING DIODE)<br />
Upon current flow, these diodes emit light without producing the<br />
heat of a comparable light.<br />
71-8<br />
HORN<br />
An electric device which sounds a loud audible signal.<br />
THERMISTOR SENSOR<br />
A resistor which varies its resistance with temperature.<br />
TAPPED RESISTOR<br />
SLIDE RHEOSTAT<br />
An electrical component with a fixed resistance, placed in a circuit to<br />
reduce voltage to a specific value.<br />
A resistor which supplies two or more different non-adjustable<br />
resistance values.<br />
A controllable resistor with a variable rate of resistance. Also called<br />
a potentiometer or rheostat.<br />
POWER SOCKET (CIGARETTE LIGHTER)<br />
An electric resistance heating element.<br />
MANUAL SWITCH<br />
Opens and closes circuits, stops or allows current flow.<br />
IGNITION SWITCH<br />
A key operated switch with several positions which allows various<br />
HEATER<br />
RELAY(4Pin)<br />
RELAY<br />
Basically, an electrically operated switch which may be normally<br />
closed or open. Current flow through a small coil to create a magnetic<br />
field which either opens or closes an attached switch.<br />
RELAY(5Pin)<br />
71-9<br />
FUSE AND RELAY LOCATIONS<br />
POSITIVE JUNCTION BOX<br />
No. Amps Function<br />
F1 60A Instrument Panel Fusible Link<br />
F2 120A Charge Fusible Link<br />
F4 60A Battery Fusible Link<br />
F5 50A Engine Room Fusible Link<br />
F3 120A Pre-heat Fusible Link<br />
71-10<br />
BATTERY COMPARTMENT JUNCTION BOX LOCATION<br />
F9 30A AM2 Fusible Link F10 40A ABS Pump Fusible Link<br />
71-11<br />
F2 7.5A Start Fuse<br />
F3 5A ABS IG Fuse<br />
F4 15A Accessory Fuse<br />
F5 15A Fuel Pump/Diesel Filter Fuse<br />
F6 30A ECM Main Fuse<br />
F7 10A Diagnosis Fuse<br />
F8 25A ABS Valve Fuse<br />
R1<br />
R2<br />
Fuel Pump/Diesel Filter Heating Relay<br />
Starter Relay<br />
71-12<br />
ENGINE ROOM JUNCTION BOX LOCATION<br />
F1 30A Low-speed Fan Fusible Link F2 30A High-speed Fan Fusible Link<br />
71-13<br />
F7 15A Stop Lamp Fuse<br />
F11 15A Injector Fuse<br />
F12 15A Ignition Coil Fuse<br />
\\\RELAY<br />
Low-speed Fan 1 Relay<br />
R5<br />
High-speed Fan 2 Relay<br />
R3<br />
Low-speed Fan 2 Relay<br />
R6<br />
Main Relay<br />
R4<br />
High-speed Fan 1 Relay<br />
71-14<br />
CO - PILOT SIDE JUNCTION BOX LOCATION<br />
F6 30A Rear A/C Fusible Link F13 30A Front Blower Fusible Link<br />
71-15<br />
F8 15A Rear Heater Fuse<br />
F9 10A Airbag Fuse<br />
F10 7.5A Outside Mirror Defrost Fuse<br />
F11 25A Rear Defroster Fuse<br />
Compressor Relay<br />
R7<br />
Water Valve Relay<br />
Rear A/C Relay<br />
R8<br />
A/C Cut Off Relay<br />
Outside Mirror Defrost Relay<br />
R9<br />
Front Blower Relay<br />
Rear Heater Relay<br />
R10<br />
Rear Defroster Relay<br />
71-16<br />
DRIVER SIDE JUNCTION BOX LOCATION<br />
F28 20A AM1 Fusible Link<br />
F30 40A IG2 Fusible Link<br />
F29 20A Power Window Fusible Link<br />
71-17<br />
F1 15A A/C Fuse<br />
F2 5A ECU IG Fuse<br />
F3 15A Power Fuse<br />
F4 10A Back-up Lamp Fuse<br />
F7 15A Sliding Roof Fuse<br />
F8 10A Rear Wiper Fuse<br />
F9 10A Turn Signal Fuse<br />
F10 15A Cigarette Lighter Fuse<br />
F11 15A Front Wiper Fuse<br />
F14 7.5A Lo-beam RH Fuse<br />
F15 7.5A Lo-beam LH Fuse<br />
F16 7.5A Radio ACC Fuse<br />
F17 7.5A Instrument IG Fuse<br />
F18 7.5A Lamplet Fuse<br />
F19 7.5A Switch Lighting Fuse<br />
F20 10A Hi-beam RH Fuse<br />
F21 10A Hi-beam LH Fuse<br />
F22 20A Headlamp Fuse<br />
F23 10A Rear Fog Lamp Fuse<br />
F24 10A Central Locking Fuse<br />
F25 7.5A A/C Controller Fuse<br />
F26 15A Front Fog Lamp Fuse<br />
F27 15A Horn Fuse<br />
F32 10A Radio/Outside Mirror Fuse<br />
F33 10A Instrument Cluster Fuse<br />
F34 10A Dome Light Fuse<br />
F35 15A Hazard Warning Fuse<br />
Rear Wiper Relay<br />
Front Fog Lamp Relay<br />
IG2 Relay<br />
Horn Relay<br />
Hi-beam Relay<br />
Rear Fog Lamp Relay<br />
Lo-beam Relay<br />
Lamplet Relay<br />
71-18<br />
POWER SOURCE<br />
WIRING - WIRING DIAGRAM<br />
71-19<br />
71-20<br />
71-21<br />
71-22<br />
71-23<br />
Service Hints<br />
• I009 Ignition Switch<br />
AM1 - ACC: Closed with the ignition switch at ACC/ON position.<br />
AM1 - IG1: Closed with the ignition switch at ON/ST position.<br />
AM2 - IG2: Closed with the ignition switch at ON/ST position.<br />
AM2 - ST2: Closed with the ignition switch at ST position.<br />
Parts Location<br />
Code Wire Harness Code Wire Harness<br />
A017 Chassis & Frame Wire Harness I009 Instrument Panel Wire Harness<br />
B001<br />
Battery Wire Harness<br />
Connector Joining Wire Harness and Wire Harness<br />
Code Code Wire Harness (Connector Location)<br />
A101<br />
A102<br />
A104<br />
A106<br />
A111<br />
I110<br />
I104<br />
I106<br />
I111<br />
E101<br />
I109<br />
M101<br />
Chassis & Frame Wire Harness & Instrument Panel Wire Harness<br />
(Under the Driver Side Junction Box)<br />
(Right Side of the Driver Side Junction Box)<br />
Chassis & Frame Wire Harness & Engine Wire Harness<br />
(Manhole After the Co-pilot Seat)<br />
(Under the Right Side of the Instrument Panel)<br />
Instrument Panel Wire Harness & Diagnosis Wire Harness<br />
(Under the Left Side of the Central Instrument Panel)<br />
Ground Points<br />
Code Ground Points Location Code Ground Points Location<br />
B201 Engine Block Side B202 Car Body Side of the Battery Compartment<br />
71-24<br />
ENGINE CONTROL SYSTEM - WITH 4G69 ENGINE<br />
71-25<br />
71-26<br />
71-27<br />
71-28<br />
System Description<br />
Engine control system of 4G69 engine is based on Engine Control Module (ECM) of Delphi MT20U2 as the<br />
center system. The engine control system mainly consists of sensor signal input, engine control module (ECM)<br />
and executive control.<br />
• Sensor Signal Input<br />
Manifold Absolute Pressure/Intake Air Temperature (MAP/IAT) Sensor<br />
Manifold absolute pressure/intake air temperature (MAP/IAT) sensor integrates functions of manifold absolute<br />
pressure sensor with those of intake air temperature sensor, while achieving the functions of feedback<br />
manifold absolute pressure and intake air temperature.<br />
Manifold absolute pressure sensor measures engine inhaled air volume, which is a critical element that forms<br />
method of speed-density type air flow measurement. The sensor directly senses manifold absolute pressure<br />
state inside the engine intake manifold. The engine control module (ECM) takes this reference signal as the<br />
basis to adjust the basic fuel supply sprayed into the engine.<br />
Intake air temperature sensor uses NTC (negative temperature coefficient) thermistor sensor, with which the<br />
engine control module (ECM) measures the air temperature in the engine cylinder and modifies the engine<br />
fuel supply.<br />
Engine Coolant Temperature Sensor<br />
Engine coolant temperature sensor is used for detecting engine operating temperature. The engine control<br />
module (ECM) provides the optimum control solution for the engine according to different temperatures.<br />
Engine coolant temperature sensor uses NTC thermistor sensor, with engine coolant temperature rising and<br />
resistance value decreasing.<br />
Crankshaft Position Sensor<br />
As magnetoelectric sensor, crankshaft position sensor works with gear ring of crankshaft. The sensor detects<br />
the change of reluctance while the crankshaft rotates and alternating reluctance generates alternating output<br />
signal. The notch positions on the gear ring correspond to top dead center (TDC) in the engine. The engine<br />
control module (ECM) uses this signal to determine the rotation position and speed of the crankshaft.<br />
Knock sensor is a vibration acceleration sensor, equipped at the engine knock induction-sensitive parts and<br />
used for sensing the knock generated by the engine. The engine control module (ECM) uses knock intensity<br />
detected by the knock sensor to modify ignition advance angle and achieve the effective control of the knock,<br />
so as to optimize engine power performance, fuel economy and reduce emissions.<br />
Throttle position sensor consists of carbon film resistor and sliding pointer driven by throttle shaft. When the<br />
throttle opening changes, the signal that the sensor feeds back to the engine control module (ECM) also<br />
varies. The control module determines real-time engine load and dynamic change condition based on the<br />
sensor signal value and its rate of change.<br />
Upstream (Downstream) Oxygen Sensor<br />
Oxygen sensor is an important symbolic component of closed loop fuel control system. With its adjustment<br />
and keeping the desired air-fuel ratio, the three-way catalytic converter can<br />
achieve the best conversion efficiency. The zirconium oxide in oxygen sensor is heated (> 300 ℃ ) for<br />
activation. The sensor changes the output voltage according to the presence or absence of oxygen in the<br />
exhaust and determines the oxygen content in the exhaust. If the oxygen content in the exhaust is increased,<br />
output voltage of oxygen sensor will be decreased; on the other hand, the output voltage will be increased,<br />
thus providing feedback of the actual air-fuel ratio conditions for the engine control module (ECM). Usually,<br />
when the sensor has the theoretical air-fuel ratio (14.6:1), it will result in dramatic change of voltage amplitude,<br />
helping the engine control module (ECM) to accurately determine the air-fuel ratio.<br />
Odometer Sensor<br />
Odometer sensor is Hall effect sensor, working with signal wheel on the transmission output shaft. The engine<br />
control module (ECM) measures digital voltage signal through the sensor. In order to determine the current<br />
vehicle speed.<br />
71-29<br />
• Executive Control<br />
Fuel injection Control<br />
The system uses the speed density method to make multi-point sequential injection, i.e., each engine cycle<br />
implements accurate fuel supply through main pulse width and amended pulse width, which has closed-loop<br />
control and self-learning function.<br />
Oil pump is single-stage electric turbine pump, and its operation is controlled by the engine control module<br />
(ECM) through the pump relay. When ignition switch is turned on, the pump will run for 1.5 seconds. If the<br />
crankshaft position signal is not received, the pump will stop running. If the crankshaft position signal is<br />
detected, the oil pump starts to work. Upon loss of crankshaft position signal, the pump will stop running.<br />
Mounting Position: in the fuel tank.<br />
Fuel injector is a ball valve device with solenoid switch. The coil in injector is controlled grounded by the<br />
engine control module (ECM) to produce magnetic force and pull up spool. The fuel is ejected from the pilot<br />
hole in the form of mist. The main factors affecting changes in fuel injection pulse width include air-fuel ratio,<br />
manifold absolute pressure, intake air temperature, closed loop feedback correction, acceleration<br />
concentration, deceleration cutoff, self-learning and correction.<br />
Ignition Control<br />
The system uses grouping ignition. Ignition coil is divided into two groups, each group providing the ignition<br />
energy for two cylinder spark plugs with 360-degree crankshaft angle difference.<br />
Idle Control<br />
The system uses the idle air control, achieving high-precision idle speed control.<br />
The idle stepping motor controls circulation area of throttle body bypass air duct to adjust control volume in the<br />
engine. The engine control module (ECM) controls the amount of movement (forward / backward) for the<br />
stepping motor through the digital square wave signal.<br />
Canister Solenoid Valve Control<br />
The engine control module (ECM) controls volume of gasoline vapor in intake manifold flowing from canister<br />
through the canister solenoid valve control. The opening of canister solenoid valve is determined by the<br />
engine control module (ECM) according to the duty cycle signal based on the state of engine.<br />
Fan Control<br />
The engine control module (ECM) monitors the level of coolant temperature and whether the air-conditioning<br />
works properly to determine the operating state of each fan.<br />
• Malfunciton Diagnosis Function<br />
When the system comes into operation, the engine control module (ECM) controls the operation of all parts of<br />
the system and conducts detection in real time. Once the system or parts have faults, the system will switch on<br />
the malfunction indicator light (MIL) to remind drivers of repair in time. When the system is in failure, the<br />
engine control module (ECM) will start backup emergency control program.<br />
• E010 Engine Coolant Temperature Sensor<br />
1 - Ground: Approx. 5 volts<br />
1 - 2: Approx. 29 KΩ (-20 ℃ )<br />
Approx. 9 KΩ (0 ℃ )<br />
Approx. 3 KΩ (20 ℃ )<br />
Approx. 0.3 KΩ (80 ℃ )<br />
• E015 Idle Speed Control Valve<br />
1 - 2: Approx. 53 Ω<br />
3 - 4: Approx. 53 Ω<br />
• E002 Fuel Injector 1, E003 Fuel Injector 2, E004 Fuel Injector 3, E005 Fuel Injector 4<br />
1 - Ground: Approx. 12 volts<br />
• E009 Throttle Position Sensor<br />
2 - Ground: Approx. 5 volts<br />
71-30<br />
• E007 Upstream Oxygen Sensor, A019 Downstream Oxygen Sensor<br />
• E006 Manifold Absolute Pressure/Intake Air Temperature (MAP/IAT) Sensor<br />
4 - Ground: Approx. 5 volts<br />
A001 Chassis & Frame Wire Harness E006 Engine Wire Harness<br />
A002 Chassis & Frame Wire Harness E007 Engine Wire Harness<br />
A004 Chassis & Frame Wire Harness E009 Engine Wire Harness<br />
A006 Chassis & Frame Wire Harness E010 Engine Wire Harness<br />
A014 Chassis & Frame Wire Harness E011 Engine Wire Harness<br />
A019 Chassis & Frame Wire Harness E015 Engine Wire Harness<br />
A022 Chassis & Frame Wire Harness E016 Engine Wire Harness<br />
A105 Chassis & Frame Wire Harness E017 Engine Wire Harness<br />
A106 Chassis & Frame Wire Harness I002 Instrument Panel Wire Harness<br />
E001 Engine Wire Harness I003 Instrument Panel Wire Harness<br />
E002 Engine Wire Harness I011 Instrument Panel Wire Harness<br />
E003 Engine Wire Harness I020 Instrument Panel Wire Harness<br />
E004 Engine Wire Harness M002 Data Link Connector<br />
E005 Engine Wire Harness V107 Front Wire Harness<br />
A107<br />
I102<br />
E102<br />
V102<br />
(Right Side of the Driver side Junction Box)<br />
Instrument Panel Wire Harness & Front Wire Harness<br />
(Left Side of the Driver side Junction Box)<br />
71-31<br />
Instrument Panel Wire Harness & Data Link Connector<br />
(Under the Left Side of the CentralInstrument Panel)<br />
A202<br />
Left Front Wheel Cover Plate Side<br />
Plates<br />
I201<br />
Left Side of the Instrument Panel<br />
A203<br />
Right Front Wheel Cover Plate Side<br />
I205<br />
Central of the Instrument Panel<br />
71-32<br />
ENGINE CONTROL SYSTEM - WITH ISF2.8 ENGINE<br />
71-33<br />
71-34<br />
71-35<br />
Engine control system of ISF2.8 engine is based on Engine Control Module (ECM) of Bosch CM2220 as the<br />
Mounting Position: on the flywheel housing perpendicular to the crankshaft position.<br />
A001 Chassis & Frame Wire Harness E026 Engine Wire Harness<br />
A002 Chassis & Frame Wire Harness E027 Engine Wire Harness<br />
A004 Chassis & Frame Wire Harness E028 Engine Wire Harness<br />
A006 Chassis & Frame Wire Harness E029 Engine Wire Harness<br />
A015 Chassis & Frame Wire Harness E030 Engine Wire Harness<br />
A016 Chassis & Frame Wire Harness E031 Engine Wire Harness<br />
A025 Chassis & Frame Wire Harness E032 Engine Wire Harness<br />
A030 Chassis & Frame Wire Harness E033 Engine Wire Harness<br />
A031 Chassis & Frame Wire Harness E035 Engine Wire Harness<br />
A033 Chassis & Frame Wire Harness E034 Engine Wire Harness<br />
A034 Chassis & Frame Wire Harness E036 Engine Wire Harness<br />
A035 Chassis & Frame Wire Harness I001 Instrument Panel Wire Harness<br />
71-36<br />
A036 Chassis & Frame Wire Harness I002 Instrument Panel Wire Harness<br />
E018 Engine Wire Harness I003 Instrument Panel Wire Harness<br />
E019 Engine Wire Harness I019 Instrument Panel Wire Harness<br />
E020 Engine Wire Harness M001 Data Link Connector<br />
E021 Engine Wire Harness M002 Data Link Connector<br />
E022 Engine Wire Harness V017 Front Wire Harness<br />
E023 Engine Wire Harness X001 Pre-heater Wire Harness<br />
E024 Engine Wire Harness X002 Pre-heater Wire Harness<br />
E025 Engine Wire Harness X003 Pre-heater Wire Harness<br />
A113<br />
B003<br />
Chassis & Frame Wire Harness & Battery Wire Harness<br />
(Battery Compartment)<br />
B202<br />
Car Body Side of the Battery<br />
Compartment<br />
71-37<br />
STARTING SYSTEM<br />
71-38<br />
• Starting System<br />
a. When ignition switch is turned to ST, the current flows through battery fusible link positive in junction box, to<br />
AM2 fusible link in battery compartment junction box, through the AM2 fusible box. The current flows from pin<br />
ST2 of ignition switch through starter fuse and accessory fuse in battery compartment junction box to pin 85 of<br />
starter relay, and through coil to ground at pin 86 of starter relay. Coil then creates a magnetic field, and switch<br />
is activated.<br />
b. The current flows through AM2 fusible link, through starter relay, to solenoid switch of starter. Solenoid<br />
switch creates a magnetic field, and starter is activated.<br />
c. The current flows through the terminal of starter, to starter motor, and to crank the engine.<br />
AM2 – IG2: Closed with the ignition switch at ON/ST position.<br />
AM2 – ST2: Closed with the ignition switch at ST position.<br />
B001 Battery Wire Harness E014 Engine Wire Harness<br />
B002 Battery Wire Harness I009 Instrument Panel Wire Harness<br />
B101<br />
Code<br />
Ground Points Location<br />
Left Front Wheel Cover Plate Side Plates<br />
71-39<br />
CHARGING SYSTEM<br />
71-40<br />
• Charging System<br />
a. 4G69 engine: When ignition switch is turned to ON/ST, the current flows output from ignition switch to ignition<br />
fuse in engine room junction box, through the fuse, to IG terminal of generator connector A018.<br />
b. When ignition switch is ON/ST, the current flows output from ignition switch, to instrument panel fuse in<br />
driver side junction box, through the fuse, to pin A20 of instrument cluster. The current flows through charging<br />
warning light of instrument cluster, from pin B25 of instrument cluster, to pin L of generator connector A018, to<br />
field winding of generator. Field winding creates a magnetic field. Rotation of the excited field coil generates<br />
AC voltage in the stator. The alternation current is rectified through diodes to DC voltage, to pin 1 of generator<br />
connector A017, to charge fusible link and charge a battery, at the same time, supply electrical energy to other<br />
electrical devices.<br />
• A018 Generator<br />
1 - Ground:12 volts with the ignition switch at ON position and engine not running.<br />
A002 Chassis & Frame Wire Harness I002 Instrument Panel Wire Harness<br />
A017 Chassis & Frame Wire Harness I003 Instrument Panel Wire Harness<br />
A018<br />
Chassis & Frame Wire Harness<br />
71-41<br />
ANTI-LOCK BRAKE CONTROL SYSTEM<br />
71-42<br />
ABS control system uses vehicle speed sensor to detect vehicle speed and transmits the speed signal to the<br />
control module. The control module controls wheel slipping rate by repeatedly increasing or decreasing the<br />
wheel brake pressure according to the input vehicle speed, keep the wheels rotating. The system enables the<br />
vehicle in braking state to prevent the wheels locking and have the steering capability, guaranteeing stability in<br />
the braking direction and preventing side-slipping and deviation.<br />
• Power Input<br />
The current flows through battery fusible link in positive junction box to ABS valve fuse and ABS pump fusible<br />
link in battery compartment junction box, to pin 1 and 25 of ABS module. System is then powered.<br />
• Ignition signal<br />
When ignition switch is ON/ST, current flows through ABS IG fuse in driver side junction box, to pin 20 of ABS<br />
module and ABS system getss ignition signal.<br />
• Speed Signal<br />
Speed sensor provide the alternating signal to the ABS module. The signal from 4 sensors: front wheel speed<br />
sensor LH, front wheel speed sensor RH, rear wheel speed sensor LH and rear wheel speed sensor RH.<br />
• Brake Signal<br />
a. 4G69 engine: The current flows through battery fusible link in positive junction box, to ECM main fuse in battery<br />
compartment junction box, to stop lamp fuse in engine room junction box, to pin 2 of stop lamp switch.<br />
When the brake pedal is depressed, the current flows from pin 1 of stop lamp switch, to pin 30 of ABS module,<br />
and provide the brake signal to the ABS module.<br />
b. ISF2.8 engine: The current flows through engine room fusible link in positive junction box, to stop lamp fuse<br />
in engine room junction box, to pin 2 of stop lamp switch. When the brake pedal is depressed, the current<br />
flows from pin 1 of stop lamp switch, to pin 30 of ABS module, and provide the brake signal to the ABS<br />
• Malfunction Diagnosis Function<br />
When the system comes into operation, ABS module detects the operation of all parts of the system. Once the<br />
system or parts have faults, the system will switch on the ABS warning light to remind drivers of repair in time.<br />
• A025 Stop Lamp Switch<br />
1 - 2:Closed when the brake pedal depressed.<br />
A009 Chassis & Frame Wire Harness A025 Chassis & Frame Wire Harness<br />
A010 Chassis & Frame Wire Harness I002 Instrument Panel Wire Harness<br />
A011 Chassis & Frame Wire Harness I003 Instrument Panel Wire Harness<br />
A012 Chassis & Frame Wire Harness M002 Diagnosis Wire Harness<br />
A013<br />
71-43<br />
A201<br />
71-44<br />
HEATER AND CONDITIONING CONTROL SYSTEM<br />
FRONT AND REAR AIR CONDITIONING CONTROL SYSTEM<br />
71-45<br />
71-46<br />
71-47<br />
• Ignition Switch At On/st, A/C System Power Supply<br />
a. When ignition switch is turned to ON/ST, current flows through A/C fuse in driver side junction box, to pin 30<br />
of A/C cut off relay, through the relay, battery output from the pin 87a of cut off relay, to pin 10 of A/C controller,<br />
pin 85 of front blower relay, pin 30 and 85 of compressor relay (ISF2,8 engine) and pin 2 of rear blower forward<br />
switch, then A/C system getss the operation power.<br />
b. When ignition switch is turned to ON/ST, current flows through ignition fuse in engine room junction box, to<br />
pin 86 of main relay, pass the the pin 85 of main relay, to pin 10 of the ECM module, the ECM module control<br />
the main relay working. When the pin 85 of main relay is controlled by ECM to connect the ground, coil then<br />
creates a magnetic field, and switch is activated. The current flows through battery fusible link in positive junction<br />
box, to main fuse in battery cmpartment junction box, to main relay, through the relay, to injector fuse, pass<br />
the fuse and connect the pin 85 of compressor relay (4G69 engine).<br />
• Ignition Switch At St, A/C System Power Supply<br />
When ignition switch is turned to ST, current flows through starter fuse in battery compartment junction box, to<br />
pin 85 of A/C cut off relay, through the coil to pin 86 and connect the groud. Coil then creates a magnetic field,<br />
and switch is open, cut off the power of A/C system to sure the starter motor have more power to crank the<br />
• Front A/C Control<br />
a. blower control: current flows from the pin 87a of A/C relay, to pin 86 of front blower relay, through coil of<br />
relay, output from the pin 86 of relay to pin 8 of A/C control panel; A/C control panel make the coil of relay to<br />
connect the ground, coil creates a magnetic field, and switch is closed. Current outputs from the pin 30 of A/C<br />
relay, to pin 1 of the front blower, through the pin 2 of the blower, to pin 4 of blower control module. A/C control<br />
panel control the front blower by controlling the blower control module.<br />
b. A/C clutch control: Working inquire signal of the front A/C system outputs from pin 9 of A/C control<br />
panel, to pin 1 of triple pressure switch, the signal through switch and connect to engine ECM. If the<br />
pressure of refrigerant in A/C pipe meet the specification as design, ECM will control the A/C relay<br />
coil to connect the ground.Coil then creates a magnetic field, and switch is activated. Current flows into A/C<br />
clutch solenoid and A/C compressor clutch engage and front A/C system begin to work<br />
c. servo motor (internal & external circulation) control: Current flows from pin 6 of A/C control panel, to pin 6<br />
of circulation motor, outputs from pin 5 of circulation motor, to pin 7 of A/C control panel. Motor is working, the<br />
front A/C system is internal circulation mode, on the contrary, system is external circulation mode.<br />
d. servo motor (temperature) control: Current flows from pin 5 and 4 of A/C control panel, to pin 5 and 6 of<br />
servo motor to control the motor operation. The current flows through the potentiometer in servo motor and<br />
return to A/C control panel from pin 3 and 1 of servo motor to pin 26 and 27 of A/C control panel. The signal<br />
current outputs from pin 2 of motor, to pin 23 of A/C control panel, feedback the position signal of servo<br />
motor(step motor).<br />
e. servo motor (mode) control: Current flows from pin 1 and 3 of A/C control panel, to pin 5 and 6 of servo<br />
motor to control the motor operation. The current flows through the potentiometer in servo motor and return to<br />
A/C control panel from pin 3 and 1 of servo motor to pin 26 and 27 of A/C control panel. The signal current outputs<br />
from pin 2 of motor, to pin 24 of A/C control panel, feedback the position signal of servo motor(step<br />
motor).<br />
f. Current flows from pin 29 of A/C control panel, to pin 1 of evaporator thermistor, through thermister, outputs<br />
from pin 2 of thermister, to pin 33 of A/C control panel. The A/C sustem getsss the temperature Info of evaporator.<br />
• Rear A/C Blower Control<br />
Press the switch of rear blower, current flows pin 2 of switch and outputs from pin 5 of switch, through pin 85 of<br />
rear A/C relay; Coil then creates a magnetic field, and switch is activated. Current flows from A/C cut off relay<br />
and outputs from pin 30 of rear A/C relay, to pin 1 of rear left blower and pin 1 of rear right blower, through the<br />
blowers, to pin1 of blower resistor and outputs:<br />
a. blower at lower speed: Current flows from pin 2 of right and left blower, to pin 1 of blower resistor, through<br />
resistor, outputs from pin 3 of blower resistor, to pin 4 of top evaporator blower switch, through switch, connect<br />
the ground at pin 3 of switch.<br />
b. blower at middle speed: Current flows from pin 2 of right and left blower, to pin 1 of blower resistor, through<br />
resistor, outputs from pin 2 of blower resistor, to pin 5 of top evaporator blower switch, through switch, connect<br />
c. blower at higher speed: Current flows from pin 2 of right and left blower, to pin 1 of blower resistor, through<br />
resistor, outputs from pin 4 of blower resistor, to pin 6 of top evaporator blower switch, through switch, connect<br />
71-48<br />
• Rear A/C Solenoid Control<br />
Press the button of rear A/C in A/C control panel, switch on the rear blower forward switch and top evaporator<br />
blower switch. The signal of rear A/C request outputs from pin 2 of top evaporator blower switch, to pin 36 of<br />
A/C control panel; Rear A/C relay coil creates a magnetic field, and switch is activated, blowers are working;<br />
The power of rear A/C solenoid outputs from pin 87 of A/C control panel, to pin 1 of rear A/C solenoid, through<br />
solenoid, to pin 1 of A/C control panel and conrtol panel control the operation of rear A/C soleniod.<br />
• A/C Cut Off Relay<br />
30 - 87a:Open with the ignition switch at ST position.<br />
• Rear A/C Relay<br />
30 - 87:Closed when rear A/C system is working.<br />
• compressor Relay<br />
30 - 87:Closed when fron A/C system is working.<br />
A028 Chassis & Frame Wire Harness I026 Instrument Panel Wire Harness<br />
A036 Chassis & Frame Wire Harness I027 Instrument Panel Wire Harness<br />
E001 Engine Wire Harness L001 Rear Evaporator Wire Harness<br />
E013 Engine Wire Harness L002 Rear Evaporator Wire Harness<br />
I020 Instrument Panel Wire Harness L003 Rear Evaporator Wire Harness<br />
I021 Instrument Panel Wire Harness L004 Rear Evaporator Wire Harness<br />
I022 Instrument Panel Wire Harness L005 Rear Evaporator Wire Harness<br />
I023 Instrument Panel Wire Harness N003 Step Lamp Wire Harness<br />
I024 Instrument Panel Wire Harness V017 Front Wire Harness<br />
I025<br />
Instrument Panel Wire Harness<br />
A108<br />
N101<br />
Chassis & Frame Wire Harness & Step Lamp Wire Harness<br />
(Under the B-Pillar RH)<br />
71-49<br />
A112<br />
E103<br />
F101<br />
I107<br />
Roof Wire Harness 1 & Instrument Panel Wire Harness<br />
(Above the Left Side of the Instrument Panel)<br />
F106<br />
L101<br />
Roof Wire Harness 1 & Rear Evaporator Wire Harness<br />
(in Front Roof)<br />
(Left Side of the Driver Side Junction Box)<br />
A202 Left Front Wheel Cover Plate Side Plate I204 Central of the Instrument Panel<br />
71-50<br />
REAR HEATER CONTROL<br />
71-51<br />
• Rear Blower Forward Switch control<br />
When ignition switch is turned to ON/ST, current flows through pin 30 of A/C cut off relay in co-pilot side junction<br />
box, through the relay, to pin 87a of cut off relay and outputs:<br />
a. to pin 30 of water valve relay.<br />
b. to pin 2 of rear blower forward switch, press the switch, the current flows from pin 5 of switch to 85 pin of<br />
water valve relay and pin 85 of rear heater relay.<br />
• Rear Heater Blower Operation<br />
When switch on the rear blower forward switch and rear heater blower switch, the rear heater relay is at operating<br />
status; Current flows through charge fusible link and instrument panel fusible link in positive junction box,<br />
to rear heater fuse in co-pilot side junction box, to rear heater relay, coil then creates magnetic field, and switch<br />
is activated, current flows through relay to pin 2 of rear heater blower, the speed of blower is controlled by<br />
resistor:<br />
a. Current outputs from pin 4 of rear heater blower, to pin 4 of rear heater blower switch, through the switch,<br />
connect to the ground at the pin 1 of switch. Blower is at higher speed.<br />
b. Current outputs from pin 1 of rear heater blower, to pin 5 of rear heater blower switch, through the switch,<br />
connect to the ground at the pin 1 of switch. Blower is at middle speed.<br />
c. Current outputs from pin 3 of rear heater blower, to pin 6 of rear heater blower switch, through the switch,<br />
• Water valve operation<br />
When switch on the rear blower forward switch and rear heater blower switch, water valve is at operating status;<br />
Current flows through coil and creates magnetic field, and switch is activated, current flows through relay<br />
to pin 1 of rear heater water valve and connect to ground at pin 2 of valve, water valve is working.<br />
A007 Chassis & Frame Wire Harness P001 Rear Heater Wire Harness<br />
I023 Instrument Panel Wire Harness P002 Rear Heater Wire Harness<br />
A109<br />
P101<br />
Chassis & Frame Wire Harness & Rear Heater Wire Harness<br />
(At the Left Side of the Chassis)<br />
A202 Left Front Wheel Cover Plate Side Plates I201 Left Side of the Instrument Panel<br />
A204 Right Front Wheel Cover Plate Side Plates I203 Left Side of the Instrument Panel<br />
71-52<br />
LIGHT SYSTEM<br />
HEADLAMP<br />
71-53<br />
• Headlamp (Low Beam)<br />
The current flows through charge and instrument panel fusible link, to pin 85 of lo-beam relay, through coil of<br />
relay, and then to pin 8 of combination switch. When the combination switch is set headlamp (Low Beam)<br />
position, the current output from pin 11 of combination switch to connect the ground. The coil of relay creates a<br />
magnetic field, and switch is activated. The current flows through switch of relay, to lo-beam fuse (LH) and lobeam<br />
fuse (RH) in dirver side junction box, and pass then to pin 3 of left lamp and pin 3 of right headlamp and<br />
through light of headlamp (Low Beam). The power is ground at pin 1 of left and right headlamp. This enables<br />
headlamp (Low Beam) to operate.<br />
• Headlamp (High Beam)<br />
The current flows through charge and instrument panel fusible link, to headlamp fuse in driver side junction<br />
box, to pin 85 and pin 30 of hi-beam relay, through coil of relay, and then to pin 9 of combination switch. When<br />
the combination switch is set headlamp (High Beam) position, the current output from pin 11 of combination<br />
switch to connect the ground. The coil of relay creates a magnetic field, and switch is activated. The current<br />
flows through switch of relay, to hi-beam fuse (LH) and hi-beam fuse (RH) in driver side junction box, and pass<br />
then to pin 2 of headlamp LH and pin2 of headlamp RH, and through light of headlamp (High Beam). The<br />
power is ground at pin 1 of left and right headlamp. This enables headlamp (High Beam) to operate.<br />
• High Beam Indicator<br />
When the combination switch is set headlamp (High Beam) position, the current flows through hi-beam (LH),<br />
to instrument cluster, and through high beam indicator. This enables high beam indicator to operate.<br />
• Flash to Pass<br />
the combination switch is set flash to pass position, the current output from pin 11 of combination switch to<br />
connect the ground. The coil of relay creates a magnetic field, and switch is activated. The current flows<br />
through switch of relay, to hi-beam fuse (LH) and hi-beam fuse (RH) in driver side junction box, and pass then<br />
to pin 2 of headlamp LH and pin2 of headlamp RH, and through light of headlamp (High Beam). The power is<br />
ground at pin 1 of left and right headlamp. This enables flash to pass to operate.<br />
• Headlamp Adjusting<br />
When low beam lamp is under working condition, current through right low beam lamp fuse, to pin 1 of front<br />
left/right adjusting motor, to supply power for adjusting motor. Pin 2 of front left/right adjusting motor connect to<br />
the pin 4 and pin 5 of the adjusting switch, adjusting motor control the adjusting motor.<br />
• I012 Combination Switch (Light Control)<br />
8 - 9:Closed with the combination switch at Headlamp position ( Low Beam).<br />
9 - 11:Closed with the combination switch at Headlamp position (High Beam and Flash to Pass).<br />
9 - 11:Closed with the combination switch at Flash to Pass position.<br />
I004 Instrument Panel Wire Harness V003 Front Wire Harness<br />
I012 Instrument Panel Wire Harness V005 Front Wire Harness<br />
V001 Front Wire Harness V006 Front Wire Harness<br />
71-54<br />
71-55<br />
I201 Left Side of the Instrument Panel V201 Left Side of the Longitudinal Beam Flank<br />
I202 Left Side of the Instrument Panel V203 Right Side of the Longitudinal Beam<br />
71-56<br />
LAMPLET<br />
71-57<br />
• Width Light<br />
The current flows through charge and instrument panel fusible link in positive junction box, to pin 85 of lamplet<br />
relay in driver side junction box, pass the coil of relay and then to pin 13 of combination switch. When the<br />
combination switch is set lamplet light or headlamp (Low Beam/High Beam) position, the current flows output<br />
pin 10 of combination switch to connect the ground. The coil of lamplet relay creates a magnetic field, and<br />
switch is activated. The current flows through switch of relay, and through the lamplet fuse in driver side<br />
junction box, to pin 2 of front position lamp LH and pin 2 of front position lamp RH. The power is ground at pin<br />
1 of front position lamp LH and pin 1 of front position lamp RH. This enables width light to operate.<br />
• Tail Light<br />
junction box, to pin 1 of front combination lamp LH and pin 1 of front combination lamp RH. The power is<br />
ground at pin 2 of front combination lamp LH and pin 2 of front combination lamp RH. This enables tail light to<br />
operate.<br />
• License Light<br />
junction box, to pin 1 of license light. The power is ground at pin 2 of license light. This enables license light to<br />
13 - 10:Closed with the combination switch at Headlamp and lamplet position.<br />
F006 Roof Wire Harness 1 J004 Rear Hatch Wire Harness<br />
G001 Roof Wire Harness 2 V002 Front Wire Harness<br />
I012 Instrument Panel Wire Harness V007 Front Wire Harness<br />
F103<br />
G103<br />
G101<br />
K101<br />
Roof Wire Harness 1 & Roof Wire Harness 2<br />
(Left Side of the Top Cap Rear Beam)<br />
Roof Wire Harness 2 & Rear Hatch Transition Wire Harness<br />
(Right Side of the Top Cap Rear Beam)<br />
71-58<br />
J101<br />
K102<br />
Rear Hatch Wire Harness & Rear Hatch Transition Wire Harness<br />
(Under the Right Side of the Rear Hatch)<br />
F201 Rear Inner Panel of the Left Gusset J201 Under the Right Side of the Right Door<br />
G201 Rear Inner Panel of the Right Gusset V201 Left Side of the Longitudinal Beam Flank<br />
I201 Left Side of the Instrument Panel V203 Right Side of the Longitudinal Beam<br />
71-59<br />
STOP LAMP<br />
71-60<br />
• 4G69 Engine<br />
The current flows through battery fusible link in positive junction box, to ECM main fuse in battery compartment<br />
junction box, to stop lamp fuse in engine room junction box, to pin 2 of stop lamp switch. The stop lamp<br />
switch is closed with the brake pedal depressed. The current then flows from pin 1 of stop lamp switch to pin 3<br />
of rear combination lamp LH, pin 3 of rear combination lamp RH and pin 2 of high-mounted stop lamp. The<br />
power is ground at pin 2 of rear combination lamp LH, pin 2 of rear combination lamp RH and pin 1 of highmounted<br />
stop lamp. This enables stop lamp and high-mounted stop lamp to operate.<br />
• ISF 2.8 Engine<br />
The current flows through engine room fusible link in positive junction box, to stop lamp fuse in engine room<br />
junction box, to pin 2 of stop lamp switch. The stop lamp switch is closed with the brake pedal depressed. The<br />
current then flows from pin 1 of stop lamp switch to pin 3 of rear combination lamp LH, pin 3 of rear<br />
combination lamp RH and pin 2 of high-mounted stop lamp. The power is ground at pin 2 of rear combination<br />
lamp LH, pin 2 of rear combination lamp RH and pin 1 of high-mounted stop lamp. This enables stop lamp and<br />
high-mounted stop lamp to operate.<br />
1 - 2:Closed with the brake pedal depressed.<br />
A025 Chassis & Frame Wire Harness G001 Roof Wire Harness 2<br />
F006 Roof Wire Harness 1 U002 High-mounted Stop Lamp Wire Harness<br />
F105<br />
U101<br />
Roof Wire Harness 1 & High-mounted Stop Lamp Wire Harness<br />
F201 Rear Inner Panel of the Left Gusset G201 Rear Inner Panel of the Right Gusset<br />
71-61<br />
BACK-UP LAMP<br />
71-62<br />
When ignition switch is ON/ST, the current flows throug back-up lamp fuse in driver side junction box, to pin 1<br />
of back-up lamp switch. The current flows from pin 2 of back-up lamp switch, and then to the circuit as follows:<br />
a. The current pass through pin 6 of rear combination lamp LH, and ground at pin 2 of rear combination lamp<br />
LH. This enables rear back-up lamp LH to operate.<br />
b. The current pass through pin 6 of rear combination lamp RH, and ground at pin 2 of rear combination lamp<br />
RH. This enables rear back-up lamp RH to operate.<br />
c. The current pass through the reverse radar control unit. Reverse radar control unit is then powered.<br />
d. The current pass through the multimedia system. Multimedia system is then powered.<br />
• A021 Back-up Lamp Switch<br />
1 – 2: Closed with the shift lever in “R” position.<br />
A021 Chassis & Frame Wire Harness F006 Roof Wire Harness 1<br />
G001 Roof Wire Harness 2<br />
F201 Rear Inner Panel of the Left Gusset I201 Left Side of the Instrument Panel<br />
G201<br />
Rear Inner Panel of the Right Gusset<br />
71-63<br />
TURN SIGNAL AND HAZARD WARNING LAMPS<br />
71-64<br />
• Turn Signal Lamp Working Condition<br />
Current flows through hazard waring fuse in driver side junction box, to pin 1 of flasher, to supply power for<br />
flasher.<br />
When ignition switch is ON/ST, the current flows through turn signal fuse in driver side junction box, to pin 6 of<br />
combination switch. When operating the combination switch, the current flow output from pin 7 and pin 5 of<br />
combination switch, to pin 12 and pin 5 of flasher, vehicle turning lamp is under working condition.<br />
• Turn Signal Lamp LH<br />
When the combination switch is in Left Turn position, the current flows output from pin 9 and pin 4 of flasher,<br />
the circuit as follows:<br />
a. The current flows through pin 2 of front turn signal lamp LH, and ground at pin 1 of front turn signal lamp LH.<br />
This enables front turn signal lamp LH to operate.<br />
b. The current flows through pin 4 of rear combination lamp LH, and ground at pin 2 of rear combination lamp<br />
LH. This enables rear turn signal lamp LH to operate.<br />
c. The current flows to pin A32 of instrument cluster and ground at pin B30 of instrument cluster. This enables<br />
left turn signal/hazard indicator to operate.<br />
• Turn Signal Lamp RH<br />
When the combination switch is in Right Turn position, the current flows output from pin 10 and pin 2 of flasher,<br />
a. The current flows to pin 2 of front turn signal lamp RH, and ground at pin 1 of front turn signal lamp RH. This<br />
enables front turn signal lamp RH to operate.<br />
b. The current flows through pin 4 of rear combination lamp RH, and ground at pin 2 of rear combination lamp<br />
RH. This enables rear turn signal lamp RH to operate.<br />
c. The current flows to pin B32 of instrument cluster and ground at pin B30 of instrument cluster. This enables<br />
right turn signal/hazard indicator to operate.<br />
• Hazard Warning Lamp<br />
When hazard warning switch is pressed, the signal flows from pin 8 of hazard warning switch, to pin 7 of<br />
flasher. Flasher is working condition; The current flows output from pin 4 , 2, 9, 10 of flasher.<br />
Power from pin 9 and pin 4 of flasher:<br />
Power from pin 10 and pin 2 of flasher:<br />
• I006 Hazard Warning Switch<br />
7 - 10:Closed with the hazard warning switch released.<br />
7 - 8:Closed with the hazard warning switch pressed.<br />
4 - 5 - 6:Closed with the hazard warning switch pressed.<br />
• I012 Combination Switch<br />
5 - 6:Closed with the combination switch at Left Turn position.<br />
6 - 7:Closed with the combination switch at Right Turn position.<br />
71-65<br />
F006 Roof Wire Harness 1 I012 Instrument Panel Wire Harness<br />
G001 Roof Wire Harness 2 I034 Instrument Panel Wire Harness<br />
I002 Instrument Panel Wire Harness I039 Instrument Panel Wire Harness<br />
I003 Instrument Panel Wire Harness I040 Instrument Panel Wire Harness<br />
V008 Front Wire Harness V004 Front Wire Harness<br />
I006<br />
F201 Rear Inner Panel of the Left Gusset V201 Left Side of the Longitudinal Beam Flank<br />
G201 Rear Inner Panel of the Right Gusset V203 Right Side of the Longitudinal Beam<br />
71-66<br />
FOG LAMP<br />
71-67<br />
• Front Fog Lamp<br />
Operation requirement: Always turn on lamplet or headlamp.<br />
relay, pass the coil of relay and then to pin 13 of combination switch. When the combination switch is set lamplet<br />
or headlamp (Low Beam/High Beam) position, the current flows output pin 10 of combination switch to<br />
through switch of relay, from the pin 87 of relay to front fog relay coil, to pin 2 of ombination switch. When front<br />
fog lamp switch is closed, the current flows output from pin 4 of combination switch to connect the ground. The<br />
coil of front fog lamp relay creates a magnetic field, and switch is activated. The current flows through fog lamp<br />
fuse in driver side junction box, to front fog lamp relay, and through switch of front fog lamp relay, to pin 1 of<br />
front fog lamp LH and pin 1 of front fog lamp RH, the power is ground at pin 2 of front fog lamp LH and pin 2 of<br />
front fog lamp RH. This enables front fog lamp LH and front fog lamp RH to operate.<br />
• Rear Fog Lamp<br />
The current flows through charge and instrument panel fusible link in positive junction box, to rear fog lamp<br />
fuse in driver side junction box, to rear fog lamp relay. When front low beam lamp work and rear fog lamp<br />
switch is closed, the current flows output from pin 4 of combination switch to connect the ground. The coil of<br />
rear fog lamp relay creates a magnetic field, and switch is activated. The current flows through rear lamp fuse<br />
in driver side junction box, to rear fog lamp relay, and through switch of rear fog lamp relay, to pin 5 of rear<br />
combination lamp LH and pin 5 of rear combination lamp RH, the power is ground at pin 2 of rear combination<br />
lamp LH and pin 2 of rear combination lamp RH. This enables rear fog lamp LH and rear fog lamp RH to operate.<br />
• Fog Lamp indicator<br />
a. Front fog lamp indicator: When front fog lamp is woring, the current flows to pin A7 of instrument cluster and<br />
ground at pin B30 of instrument cluster. This enables front fog lamp indicator to operate.<br />
b. Rear fog lamp indicator: When rear fog lamp is working, the current flows to pin B21 of instrument cluster<br />
and ground at pin B30 of instrument cluster. This enables rear fog lamp indicator to operate.<br />
10 - 13:Closed with the combination switch at Lamplet and Headlamp position<br />
C001 Front Bumper Wire Harness I002 Instrument Panel Wire Harness<br />
C002 Front Bumper Wire Harness I003 Instrument Panel Wire Harness<br />
C101<br />
V110<br />
Front Bumper Wire Harness & Front Wire Harness<br />
(Left Front Combination Lamps Positioning Plate Side)<br />
71-68<br />
Instrument Panel Wire Harness & Roof Wire Harness 1<br />
G201 Rear Inner Panel of the Right Gusset V202 Left Side of the Longitudinal Beam<br />
71-69<br />
INTERIOR LAMPS<br />
71-70<br />
71-71<br />
• Front Dome Light<br />
The current flows through charge and instrument panel fusible link in positive junction box, to dome light fuse<br />
in driver side junction box, to pin 1 and 2 of front dome light. Front dome light is working condition.<br />
a. Press front dome light switch, and the power is ground by the switch. This enables front dome light to<br />
b. Dome light switch is at DOOR postion; If any front door is not closed, the front door ajar switch will turn to<br />
ON. The current flows from pin 4 of front dome lamp, to front door ajar switch. The power is ground by ajar the<br />
switch. This enables front dome light to operate.<br />
• central dome Light<br />
in driver side junction box, to pin 1 of central dome light. central dome light is working condition.<br />
a. When central dome light is at ON position; The current flows from pin 3 (high equipped) or 2 (low equipped)<br />
of central dome light, to pin 5 of central dome light switch, press the switch, and the power is ground by the pin<br />
2 of switch. This enables central dome light to operate.<br />
b. When central dome light is at DOOR position (high equipped); If sliding door is not closed, the door ajar<br />
switch will turn to ON. The current flows from pin 2 of central dome lamp, to door ajar switch. The power is<br />
ground by ajar the switch. This enables central dome light to operate.<br />
• Step lamp<br />
in driver side junction box, to pin 1 of step light and output from pin 2 of step light; If sliding door is not closed,<br />
the door ajar switch will turn to ON. The current flows from pin 2 of step light, to door ajar switch. The power is<br />
ground by ajar the switch. This enables step light to operate.<br />
• Ignition Switch Illumination<br />
in driver side junction box, to pin 1 of ignition switch illumination; The current outputs from the pin 2 of ignition<br />
switch illumination, to pin B1 of central locking controller, the central locking controller control the ignition<br />
switch illumination to operation.<br />
• Trunk lamp<br />
in driver side junction box, to pin 1 of trunk lamp and output from pin 2 of trunk lamp; If rear hatch door is not<br />
closed, the door ajar switch will turn to ON. The current flows from pin 2 of trunk lamp, to door ajar switch. The<br />
power is ground by ajar the switch. This enables trunk lamp to operate.<br />
• Door open Indicatior<br />
If any door is not closed, the door ajar switch will turn to ON. The ground signal input pin A15 and A30 of<br />
instrument cluster and this enables indicatior to operate.<br />
A008 Chassis & Frame Wire Harness I008 Instrument Panel Wire Harness<br />
A024 Chassis & Frame Wire Harness I010 Instrument Panel Wire Harness<br />
A029 Chassis & Frame Wire Harness I018 Instrument Panel Wire Harness<br />
F001 Roof Wire Harness 1 I036 Instrument Panel Wire Harness<br />
F004 Roof Wire Harness 1 I037 Instrument Panel Wire Harness<br />
F007 Roof Wire Harness 1 J001 Rear Hatch Wire Harness<br />
G003 Roof Wire Harness 2 J003 Rear Hatch Wire Harness<br />
I002 Instrument Panel Wire Harness N002 Step Lamp Wire Harness<br />
71-72<br />
I203<br />
71-73<br />
ILLUMINATION<br />
71-74<br />
71-75<br />
The current flows from charge and instrument panel fusible link, to pin 85 of lamplet relay, through the coil of<br />
tail light relay, and then to pin 13 of combination switch. When the combination switch is set lampet or<br />
headlamp (Low Beam/High Beam) position, the current flows output pin 10 of combination switch to connect<br />
the ground. The coil of lamplet relay creates a magnetic field, and switch is activated. The current flows<br />
through switch of relay and through the lamplet and switch light fuse in driver side junction box and the system<br />
getsss the power to operation.<br />
• Instrument Cluster Illumination<br />
When the combination switch is set lamplet or headlamp position, the current flows output lamplet fuse in<br />
driver side junction box, to pin A6 of instrument cluster. This enables instrument cluster illumination to operate.<br />
• Hazard Warning Switch Illumination<br />
driver side junction box, to pin 2 of hazard warning switch, to pin 3 of hazard warning switch, the power is<br />
ground at pin 3 of hazard warning switch. This enables hazard warning switch illumination to operate.<br />
• Headlamp Dimmer Switch Illumination<br />
When the combination switch is set lamplet or headlamp position, the current flows output switch light fuse in<br />
driver side junction box, to pin 3 of headlamp dimmer switch illumination, to pin 6 of headlamp dimmer switch<br />
illumination, the power is ground at pin 6 of headlamp dimmer switch illumination. This enables headlamp<br />
dimmer switch illumination to operate.<br />
• Instrument Dimmer Switch Illumination<br />
driver side junction box, to pin 3 of instrument dimmer switch illumination, to pin 6 of instrument dimmer<br />
switch illumination, the power is ground at pin 6 of instrument dimmer switch illumination. This enables<br />
instrument dimmer switch illumination to operate.<br />
• Rear Window Defroster Switch Illumination<br />
driver side junction box, to pin 3 of rear window defroster switch illumination, to pin 1 of rear window defroster<br />
switch illumination, the power is ground at pin 1 of rear window defroster switch illumination. This enables<br />
rear window defroster switch illumination to operate.<br />
• Outside Mirror Defroster Switch Illumination<br />
driver side junction box, to pin 3 of outside mirror defroster switch illumination, to pin 1 of outside mirror<br />
defroster switch illumination, the power is ground at pin 1 of outside mirror defroster switch illumination.<br />
This enables outside mirror defroster switch illumination to operate.<br />
• Rear Blower Forward Switch Illumination<br />
driver side junction box, to pin 3 of rear blower forward switch illumination, to pin 1 of rear blower forward<br />
switch illumination, the power is ground at pin 1 of rear blower forward switch illumination. This enables<br />
rear blower forward switch illumination to operate.<br />
• Dome Light Switch Illumination<br />
driver side junction box, to pin 3 of dome light switch illumination, to pin 1 of dome light switch illumination,<br />
the power is ground at pin 1 of dome light switch illumination. This enables dome light switch illumination<br />
to operate.<br />
• Cigarette Lighter Illumination<br />
driver side junction box, to pin 3 of cigarette lighter illumination, to pin 1 of cigarette lighter illumination,<br />
the power is ground at pin 1 of cigarette lighter illumination. This enables cigarette lighter illumination to<br />
• Radio Illumination<br />
driver side junction box, to pin A3 of radio illumination, to pin A8 of radio illumination, the power is ground<br />
at pin A8 of radio illumination. This enables radio illumination to operate.<br />
71-76<br />
• A/C Control Panel llumination<br />
driver side junction box, to pin 32 of A/C control panel llumination, to pin 20 of A/C control panel<br />
llumination, the power is ground at pin 20 of A/C control panel llumination. This enables A/C control<br />
panel llumination to operate.<br />
• Diagnosis Switch llumination<br />
driver side junction box, to pin 3 of diagnosis switch llumination, to pin 1 of diagnosis switch llumination,<br />
the power is ground at pin 1 of diagnosis switch llumination. This enables diagnosis switch llumination to<br />
10 - 13:Closed with the combination switch at Lamplet or Headlamp position.<br />
I002 Instrument Panel Wire Harness I018 Instrument Panel Wire Harness<br />
I004 Instrument Panel Wire Harness I019 Instrument Panel Wire Harness<br />
I005 Instrument Panel Wire Harness I020 Instrument Panel Wire Harness<br />
I006 Instrument Panel Wire Harness I021 Instrument Panel Wire Harness<br />
I012 Instrument Panel Wire Harness I023 Instrument Panel Wire Harness<br />
I016 Instrument Panel Wire Harness I031 Instrument Panel Wire Harness<br />
I017 Instrument Panel Wire Harness I033 Instrument Panel Wire Harness<br />
I201 Left Side of the Instrument Panel I204 Central of the Instrument Panel<br />
I202 Left Side of the Instrument Panel I205 Central of the Instrument Panel<br />
71-77<br />
71-78<br />
When ignition switch is ON/ST, the current flows through front wiper fuse and rear wiper fuse in driver side<br />
junction box. System is then powered.<br />
• Front Wiper Switch LO<br />
When the front wiper switch of combination switch is in LO position, the current flows from front wiper fuse, to<br />
pin 8 of combination switch, and output from pin 7 of combination switch, to pin 1 of front wiper motor, and<br />
through wiper motor to ground. This enables front wiper to operate at low speed.<br />
• Front Wiper Switch MIST<br />
• Front Wiper Switch HI<br />
When the front wiper switch of combination switch is in HI position, the current flows from front wiper fuse, to<br />
pin 8 of combination switch, and output from pin 9 of combination switch, to pin 4 of front wiper motor, and<br />
through wiper motor to ground. This enables front wiper to operate at high speed.<br />
• Front Wiper Switch INT<br />
When the front wiper switch of combination switch is set INT, The intermittent current flows from pin 7 of<br />
combination switch, to front wiper motor. This enables front wiper to operate in the intermittent mode.<br />
• Front Washer switch ON<br />
When the front washer switch is in ON position, the current flows output from pin 2 of front washer pump, and<br />
through the front washer pump, output from pin 1 of front washer pump, to pin 4 of combination switch, and<br />
ground at pin 5 of combination switch. This enables front washer to function.<br />
• Rear Wiper Switch ON<br />
The current flows output from rear wiper fuse, to pin 85 and 87 of rear wiper relay, and then output from pin 30<br />
of rear wiper relay. When the rear wiper switch is in ON position, the current flows into pin 2 of combination<br />
switch, and then to ground at pin 5 of combination switch; The current flows into coil of rear wiper relay. The<br />
coil of relay creates a magnetic field, and switch is activated. The current flows through switch of relay, from<br />
the pin 30 of relay, to pin 4 of rear wiper motor, and through the rear wiper motor, to ground at pin 3 of rear<br />
wiper motor. This enables rear wiper to operation.<br />
• Rear Washer Switch ON<br />
When the rear wiper switch is in ON position, the current flows from rear wiper fuse, to pin 2 of rear washer<br />
pump, and output from pin 1 of rear washer pump, to pin 3 of combination switch, and ground at pin 5 of<br />
combination switch. This enables rear washer to operation.<br />
I013 Instrument Panel Wire Harness V010 Front Wire Harness<br />
U001 High-mounted Stop Lamp Wire Harness V011 Front Wire Harness<br />
V009<br />
Front Wire Harness<br />
F102<br />
I108<br />
71-79<br />
I101<br />
V101<br />
F201 Rear Inner Panel of the Left Gusset I202 Left Side of the Instrument Panel<br />
I201 Left Side of the Instrument Panel V202 Left Side of the Longitudinal Beam<br />
71-80<br />
71-81<br />
• I031 Radio<br />
A4 - Ground Points:Approx.12 V with the ignition switch at ACC/ON position.<br />
A7 - Ground Points:Approx. 12 V<br />
• D001 Front Speaker LH<br />
1 - 2:Approx. 4 Ω<br />
• H001 Front Speaker RH<br />
• F005 Rear Speaker LH<br />
• G002 Rear Speaker RH<br />
A026 Chassis & Frame Wire Harness I029 Instrument Panel Wire Harness<br />
D001 Front Door LH Wire Harness I030 Instrument Panel Wire Harness<br />
F005 Roof Wire Harness 1 I031 Instrument Panel Wire Harness<br />
G002 Roof Wire Harness 2 I032 Instrument Panel Wire Harness<br />
H001 Front Door RH Wire Harness J005 Rear Hatch Wire Harness<br />
D103<br />
F104<br />
H103<br />
V106<br />
G102<br />
V109<br />
Front Door LH Wire Harness & Front Wire Harness<br />
(Under the Left Side of the Door Flame)<br />
Front Door RH Wire Harness & Front Wire Harness<br />
(Under the Right Side of the Door Flame)<br />
71-82<br />
G201 Rear Inner Panel of the Right Gusset I205 Central of the Instrument Panel<br />
71-83<br />
POWER SOCKET<br />
71-84<br />
• Cigarette Lighter<br />
When ignition switch is ACC/ON, the current flows through cigarette lighter fuse in driver side junction box, pin<br />
2 of cigarette lighter. When pressing the cigarette lighter, the current flows output from pin 1 of cigarette lighter,<br />
and ground at pin 1 of cigarette lighter. This enables cigarette lighter to operate.<br />
• 12V Power Output Socket<br />
When ignition switch is ON/ST, the current flows through cigarette lighter fuse in driver side junction box, pin 2<br />
of power output socket. When pressing the power output socket, the current flows output from pin 1 of power<br />
output socket, and ground at pin 1 of power output socket. This enables power output socket to operate.<br />
I015 Instrument Panel Wire Harness I033 Instrument Panel Wire Harness<br />
I201 Left Side of the Instrument Panel I203 Left Side of the Instrument Panel<br />
71-85<br />
COMMUNICATION SYSTEM<br />
71-86<br />
• horn control<br />
The current flows through charge and instrument panel fusible link in positive junction box, to horn fuse in<br />
driver side junction box, to pin 85 of horn relay, and through the coil of horn relay, and then to the circuit as<br />
follows:<br />
a. High equipped: Current flows from 2 pin of clock spring, to horn switch, when pressing the horn switch, the<br />
power is ground by switch. The coil of horn relay creates a magnetic field, and switch is activated. The current<br />
then flows through switch of horn relay, to pin 1 of horn, and to ground at pin 2 of horn. This enables horn to<br />
b. low equipped: Current flows to horn switch, when pressing the horn switch, the power is ground by switch.<br />
The coil of horn relay creates a magnetic field, and switch is activated. The current then flows through switch<br />
of horn relay, to pin 1 of horn, and to ground at pin 2 of horn. This enables horn to operate.<br />
• Horn of Anti-thief System<br />
Pin 86 of horn relay is controlled by pin B4 of central locking controller to coonect the ground; When pin 86 of<br />
relay to connect the ground, The coil of horn relay creates a magnetic field, and switch is activated. The<br />
current then flows through switch of horn relay, to pin 1 of horn, and to ground at pin 2 of horn. This enables<br />
horn to operate.<br />
I008 Instrument Panel Wire Harness V013 Front Wire Harness<br />
I014 Instrument Panel Wire Harness V014 Front Wire Harness<br />
I038<br />
V202<br />
Left Side of the Longitudinal Beam<br />
71-87<br />
71-88<br />
When ignition switch is ON/ST, the current flows through back-up lamp fuse in driver side junction box, to pin 2<br />
of back-up lamp switch. When shift lever in “R” position, the current flows from pin 1 of back-up lamp switch to<br />
pin 1 of reverse radar control unit. The reverse radar control system is then powered.<br />
• Reverse Radar Sensor LH<br />
The current outputs from pin 7 of reverse radar control unit, to pin 1 of reverse radar sensor LH, and through<br />
the sensor, output from pin 2 of reverse radar sensor LH, to pin 11 of reverse radar control unit, this detects the<br />
obstacle in rear left side.<br />
• Reverse Radar Central Sensor LH<br />
The current outputs from pin 8 of reverse radar control unit, to pin 1 of reverse radar central sensor LH, and<br />
through the sensor, output from pin 2 of reverse radar central sensor LH, to pin 11 of reverse radar control unit,<br />
this detects the obstacle in rear left central side.<br />
• Reverse Radar Central Sensor RH<br />
The current outputs from pin 4 of reverse radar control unit, to pin 1 of reverse radar central sensor RH, and<br />
through the sensor, output from pin 2 of reverse radar central sensor RH, to pin 11 of reverse radar control<br />
unit, this detects the obstacle in rear right central side.<br />
• Reverse Radar Sensor RH<br />
The current outputs from pin 15 of reverse radar control unit, to pin 1 of reverse radar sensor RH, and through<br />
the sensor, output from pin 2 of reverse radar sensor RH, to pin 11 of reverse radar control unit, this detects<br />
the obstacle in rear right side.<br />
1 - 2:Closed with the shift lever in “R” position.<br />
A021 Chassis & Frame Wire Harness R001 Rear Bumper Wire Harness<br />
A026 Chassis & Frame Wire Harness R002 Rear Bumper Wire Harness<br />
I002 Instrument Panel Wire Harness R003 Rear Bumper Wire Harness<br />
I028 Instrument Panel Wire Harness R004 Rear Bumper Wire Harness<br />
A103<br />
A110<br />
I105<br />
Q102<br />
Chassis & Frame Wire Harness & Rear Bumper Transition Wire Harness<br />
(Left Rear Side of the Car Body)<br />
71-89<br />
Q101<br />
R101<br />
Rear Bumper Transition Wire Harness & Rear Bumper Wire Harness<br />
(Left Side of the Rear Bumper)<br />
71-90<br />
POWER MIRROR<br />
71-91<br />
When ignition switch is ACC/ON, the current flows through radio ACC fuse in driver side junction box, to pin 4<br />
of outside mirror switch. System is then powered.<br />
• Outside Mirror LH (Up/Down)<br />
The current flows from pin 4 of electric outside mirror switch and output from pin 7 of electric outside mirror<br />
switch, to pin 6 of outside mirror LH, through motor, the current flows from pin 4 of outside mirror LH, to pin 5<br />
of electric outside mirror switch, and ground at pin 6 of electric outside mirror switch. This enables outside<br />
mirror LH to go up.<br />
The current flows from pin 4 of electric outside mirror switch and output from pin 5 of electric outside mirror<br />
switch, to pin 4 of outside mirror LH, through motor, the current flows from pin 6 of outside mirror LH, to pin 7<br />
mirror LH to go down.<br />
• Outside Mirror RH (Up/Down)<br />
The current flows from pin 4 of electric outside mirror switch and output from pin 8 of electric outside mirror<br />
switch, to pin 6 of outside mirror RH, through motor, the current flows from pin 4 of outside mirror RH, to pin 5<br />
mirror RH to go up.<br />
switch, to pin 4 of outside mirror RH, through motor, the current flows from pin 6 of outside mirror RH, to pin 8<br />
mirror RH to go down.<br />
• Outside Mirror LH (Left/Right)<br />
TThe current flows from pin 4 of electric outside mirror switch and output from pin 5 of electric outside mirror<br />
switch, to pin 4 of outside mirror LH, through motor, the current flows from pin 5 of outside mirror LH, to pin 1<br />
mirror LH to turn to left.<br />
The current flows from pin 4 of electric outside mirror switch and output from pin 1 of electric outside mirror<br />
switch, to pin 5 of outside mirror LH, through motor, the current flows from pin 4 of outside mirror LH, to pin 5<br />
mirror LH to turn to right.<br />
• Outside Mirror RH (Left/Right)<br />
switch, to pin 4 of outside mirror RH, through motor, the current flows from pin 5 of outside mirror RH, to pin 3<br />
mirror RH to turn to left.<br />
The current flows from pin 4 of electric outside mirror switch and output from pin 3 of electric outside mirror<br />
switch, to pin 5 of outside mirror RH, through motor, the current flows from pin 4 of outside mirror RH, to pin 5<br />
mirror RH to turn to right.<br />
D003 Front Door LH Wire Harness H003 Front Door RH Wire Harness<br />
D004<br />
Front Door LH Wire Harness<br />
D101<br />
D102<br />
V104<br />
V105<br />
71-92<br />
V107<br />
H101<br />
Front Wire Harness & Front Door RH Wire Harness<br />
71-93<br />
WINDOW DEFROSTER<br />
71-94<br />
• Rear Window Defrost<br />
When ignition switch is ON/ST, the current flows through outside mirror defrost fuse in co-pilot side junction<br />
box, to pin 2 of rear window defroster switch, when press the switch, pin 5 and pin 2 of rear window defroster<br />
switch connected, the current flows to pin 85 of rear defroster relay, through the coil in rear defroster relay, and<br />
output from pin 86 of rear defroster relay. The coil of rear defroster relay creates a magnetic field, and switch is<br />
activated. The current flows through switch of rear defroster relay, to pin 1 of rear window defrost grid and<br />
ground. This enables rear window defroster to operate.<br />
• Outside Mirror Defrost<br />
box, to pin 2 of outside mirror defroster switch, when press the switch, pin 5 and pin 2 of outside mirror<br />
defroster switch connected, the current flows to pin 85 of outside mirror defroster relay, through the coil in outside<br />
mirror defroster relay, and output from pin 86 of outside mirror defroster relay. The coil of outside mirror<br />
defroster relay creates a magnetic field, and switch is activated. The current flows from outside mirror defrost<br />
fuse, through switch of outside mirror defroster relay, to pin 1 of outside mirror defrost grid and ground at pin 2<br />
of grid. This enables outside mirror defroster to operate.<br />
• I016 Rear Window Defrost Switch<br />
2 - 5:Closed with the rear window defrost switch in operation.<br />
• I017 Outside mirror Defrost Switch<br />
2 - 5:Closed with the outside mirror defrost switch in operation.<br />
D003 Front Door LH Wire Harness I017 Instrument Panel Wire Harness<br />
H003 Front Door RH Wire Harness S001 Rear Defrost RH Wire Harness<br />
I016 Instrument Panel Wire Harness T001 Rear Defrost LH Wire Harness<br />
71-95<br />
S101<br />
U103<br />
Rear Defrost RH Wire Harness & High-mounted Stop Lamp Wire Harness<br />
(Above the Right Side of the Rear Hatch)<br />
T101<br />
U102<br />
Rear Defrost LH Wire Harness & High-mounted Stop Lamp Wire Harness<br />
(Above the Left Side of the Rear Hatch)<br />
A201 Left Front Wheel Cover Plate Side Plates V202 Left Side of the Longitudinal Beam<br />
71-96<br />
71-97<br />
71-98<br />
71-99<br />
71-100<br />
• instrument cluster power<br />
a. ISF 2.8 engine: When ignition switch is ON/ST, the current flows through instrument IG fuse in driver side<br />
junction box, to pin A1 and A20 of instrument cluster. System is then powered.<br />
b. 4G69 engine: The instrument cluster IG power of circuit as follows: When ignition switch is ON/ST, the current<br />
flows through instrument IG fuse in driver side junction box, to pin A20 of instrument cluster. System is<br />
then powered. When ignition switch is ON/ST, current flows through main relay and output from pin 87 of relay,<br />
to pin A1 of intrument cluster. System is then powered.<br />
• Engine Coolant Fluid Level Warning Light<br />
The current flows through engine coolant fluid level warning light in instrument cluster, and output from pin B7<br />
of instrument cluster, to pin 2 of engine coolant level sensor, and ground at pin 1 of engine coolant level<br />
sensor. This enables engine coolant fluid level warning light to operate.<br />
• Engine Coolant Temperature Indicator<br />
The current flows from pin B16 of instrument cluster, to pin 1 of engine coolant temperature sensor, and<br />
ground at pin 2 of engine coolant temperature sensor (ISF2.8) or itself (4G69). This enables engine coolant<br />
fluid temperature indicator to operate.<br />
• Engine Oil Pressure Warning Light<br />
The current flows through engine oil pressure warning light in instrument cluster, and output from pin B22 of<br />
instrument cluster, to pin 1 of engine oil pressure switch, and then to ground. This enables engine oil pressure<br />
warning light to operate.<br />
• Low Fuel Indicator and Warning Light<br />
The current flows through low fuel warning light in instrument cluster, and output from pin A23 of instrument<br />
cluster, to pin 3 of fuel level sensor, and then ground at pin 2 of level sensor. This checks the fuel leveland<br />
shows the fuel level in instrument cluster, if the fuel is less, the warning light will be activated.<br />
• ABS Warning Light<br />
The current flows into pin A20 of instrument cluster, through ABS warning light in instrument cluster, and<br />
output from pin B20 of instrument cluster, to 15 of ABS module. If ABS system is fault, this enables ABS<br />
• EBD Warning Light<br />
The current flows into pin A20 of instrument cluster, through EBD warning light in instrument cluster, and<br />
output from pin B24 of instrument cluster, to 14 of ABS module. If ABS system is fault, this enables EBD<br />
• Charging Warning Light<br />
The current flows into pin A20 of instrument cluster, through charging warning light in instrument cluster, and<br />
output from pin B25 of instrument cluster, to pin 1 of generator. This identifies if the generator operates or not.<br />
• Safe Belt Indicator<br />
The current flows into pin A20 of instrument cluster, through safe belt indicator in instrument cluster, and<br />
output from pin A31of instrument cluster, to pin 1 of driver seat belt warning switch. If driver do not fasten the<br />
safe belt, switch will close, this enables safe belt indicator to operate.<br />
• Buzzer of Safe Belt<br />
The current flows through buzzer in instrument cluster, and output from pin B9 of instrument cluster, to pin 1 of<br />
driver seat belt warning switch. If driver do not fasten the safe belt, switch will close, this enables buzzer to<br />
• Air Bag System Warning Light<br />
The current flows into pin A20 of instrument cluster, through warning light in instrument cluster, and output<br />
from pin B27 of instrument cluster, to pin 7 of RCM. If Air bag system is fault, this enables air bag system<br />
warning light to operate<br />
• Parking Indicator<br />
The current flows into pin A20 of instrument cluster, through indicator in instrument cluster, and output from pin<br />
B6 of instrument cluster, to pin 1 of parking brake switch. Through switch to ground, this enables parking indicator<br />
to operate<br />
• Brake Warning Light<br />
The current flows into pin A20 of instrument cluster, through brake warning light in instrument cluster, and<br />
output pin B28 of instrument cluster, to pin 1 of brake fluid level sensor, and ground at pin 2 of brake fluid level<br />
sensor. This checks the brake fluid level.<br />
71-101<br />
• Lamplet indicator<br />
The current flows into pin A6 of instrument cluster, through indicator in instrument cluster, and output pin B30<br />
of instrument cluster to ground. If lamplet or interior lamp work, the indicator will be activated.<br />
• Enging Pre-heating indicator<br />
ISF2.8 engine: The current flows into pin A1 of instrument cluster, through indicator in instrument cluster, and<br />
output pin A27 of instrument cluster, to pin 35 of ECM. If pre-heating system is working, the indicator will be<br />
activated.<br />
• Malfunction Indicator<br />
The current flows into pin A1 of instrument cluster, through malfunction indicator in instrument cluster, and<br />
output from pin B23 of instrument cluster, to pin 19 of ECM (4G69) or 22 of ECM (ISF2.8). If engine control<br />
system fault exist, this enables malfunction indicator to operate.<br />
• Maintenance Indicator<br />
The current flows into pin A1 of instrument cluster, through indicator in instrument cluster, and output from pin<br />
A28 of instrument cluster, to pin 12 of ECM (4G69) or 36 of ECM (ISF2.8). If engine need to service, this<br />
enables indicator to operate.<br />
• Engine Stop Indicator<br />
ISF 2.8 engine: The current flows into pin A20 of instrument cluster, through indicator in instrument cluster,<br />
and output from pin A24 of instrument cluster, to pin 49 of ECM. ECM control the stop indicator.<br />
• Vacuum Warning Light<br />
ISF 2.8 engine: The current flows from pin A26 of instrument cluster, through indicator in instrument cluster, to<br />
pin 1 of vacuum warning switch. Through the switch to connect ground, this enables the warning light to operate.<br />
A009 Chassis & Frame Wire Harness E012 Engine Wire Harness<br />
A018 Chassis & Frame Wire Harness E036 Engine Wire Harness<br />
A020 Chassis & Frame Wire Harness E037 Engine Wire Harness<br />
A022 Chassis & Frame Wire Harness I002 Instrument Panel Wire Harness<br />
A023 Chassis & Frame Wire Harness I003 Instrument Panel Wire Harness<br />
A026 Chassis & Frame Wire Harness I005 Instrument Panel Wire Harness<br />
A027 Chassis & Frame Wire Harness O001 Driver Seat Belt Wire Harness<br />
A032 Chassis & Frame Wire Harness V012 Front Wire Harness<br />
A036 Chassis & Frame Wire Harness V016 Front Wire Harness<br />
E001<br />
Engine Wire Harness<br />
71-102<br />
A105<br />
O101<br />
Chassis & Frame Wire Harness & Driver Seat Belt Wire Harness<br />
(Above the B-Pillar LH)<br />
A202 Left Front Wheel Cover Plate Side Plates I203 Left Side of the Instrument Panel<br />
A204 Right Front Wheel Cover Plate Side Plates V202 Left Side of the Longitudinal Beam<br />
71-103<br />
ANTI-THEIF SYSTEM<br />
71-104<br />
71-105<br />
The current flows through charge and instrument panel fusible link in positive junction box, to driver side junction<br />
box and circuit as follows:<br />
a. Through the central locking fuse, to pin B3 of central locking controller, system getsss the power of central<br />
locking.<br />
b. Through power window fusible link, to pin A8 of central locking controller, system getsss the power of electrical<br />
window.<br />
c. Through power window fusible link, to pin 12 of door control switch, switch is then powered.<br />
• Key Lock Signal<br />
a. When key lock switch is LOCK position, the current flows output from pin A6 of central locking controller, to<br />
pin 9 of front door lock actuator assembly LH and through the key lock switch, to ground at pin 7 of front door<br />
lock actuator assembly LH. This enables closed with door of all with mechanical operate.<br />
b. When key lock switch is OPEN position, the current flows output from pin A7 of central locking controller, to<br />
pin 10 of front door lock actuator assembly LH, and through the key lock switch, to ground at pin 7 of front door<br />
lock actuator assembly LH. This enables opened with door of all with mechanical operate.<br />
• Status of Front Door LH<br />
Current flows from pin B2 of central locking controller, to pin 1 of front door LH switch, through switch to<br />
ground, system getss the signal of front door status.<br />
• Status of Hood<br />
Current flows from pin B6 of central locking controller, to pin 1 of hood switch, through 2 pin of switch to<br />
ground, system getss the signal of hood status.<br />
• Collision Signal<br />
Signal is from pin 30 of restraint control module, to pin A11 of central locking controller. System getssgetss the<br />
Info of collision.<br />
• vehicle speed signal<br />
Signal is from pin A9 of instrumen cluster, to pin A17 of central locking controller. When the vehicle speed<br />
attach the value as design, system will lock all door that unlocked before.<br />
• Key Insert signal<br />
Current flows from pin B8 of central locking controller, to pin 3 of key insert switch, through the switch and<br />
ground at pin 4 of switch. System getss the key insert signal.<br />
• Door control switch<br />
Pin 1 and 2 of door control switch connect the pin A15 and A16 of central locking controller, through this<br />
connection, the controller getsss the signal that control the door window and lock from door control swith.<br />
• Door Actuator Control<br />
a. Front door LH unlock: The current flows output from pin A3 of central locking controller, to pin 1 of front door<br />
lock actuator assembly LH, and through the motor in front door lock actuator assembly LH, output from pin 4 of<br />
front door lock actuator assembly LH, to pin A2 of central locking controller. This enables front door LH open.<br />
On the contrary, the front door LH is closed.<br />
b. Front door RH unlock: The current flows output from pin A3 of central locking controller, to pin 1 of front door<br />
lock actuator assembly RH, and through the motor in front door lock actuator assembly RH, output from pin 4<br />
of front door lock actuator assembly RH, to pin A2 of central locking controller. This enables front door RH<br />
open. On the contrary, the front door RH is closed.<br />
c. Sliding door unlock: The current flows output from pin A3 of central locking controller, to pin 2 of sliding door<br />
lock actuator assembly, and through the motor in sliding door lock actuator assembly, output from pin 4 of sliding<br />
door lock actuator assembly, to pin A2 of central locking controller. This enables sliding door open. On the<br />
contrary, the sliding door is closed.<br />
d. Rear hatch unlock: The current flows output from pin A3 of central locking controller, to pin 2 of rear hatch<br />
lock actuator assembly, and through the motor in door lock actuator assembly, output from pin 4 of lock<br />
actuator assembly, to pin A2 of central locking controller. This enables rear hatch open. On the contrary, the<br />
rear hatch is closed.<br />
• Power Window Control<br />
a. Power window LH up: The current flows output from pin A5 of central locking controller, to pin 1 of power<br />
window LH, and through the motor, output from pin 2 of power window LH, to pin A4 of central locking<br />
controller. This enables power window LH up. On the contrary, power window LH is down.<br />
b. Power window RH up: The current flows output from pin A7 of central locking controller, to pin 1 of power<br />
window RH, and through the motor, output from pin 2 of power window RH, to pin A6 of central locking<br />
controller. This enables power window RH up. On the contrary, power window RH is down.<br />
71-106<br />
A008 Chassis & Frame Wire Harness I002 Instrument Panel Wire Harness<br />
A027 Chassis & Frame Wire Harness I007 Instrument Panel Wire Harness<br />
D002 Front Door LH Wire Harness I008 Instrument Panel Wire Harness<br />
D005 Front Door LH Wire Harness I010 Instrument Panel Wire Harness<br />
D006 Front Door LH Wire Harness I011 Instrument Panel Wire Harness<br />
H002 Front Door RH Wire Harness J002 Rear Hatch Wire Harness<br />
H004 Front Door RH Wire Harness N001 Step Lamp Wire Harness<br />
H005 Front Door RH Wire Harness V015 Front Wire Harness<br />
H102<br />
V108<br />
71-107<br />
I103<br />
V103<br />
I202 Left Side of the Instrument Panel V202 Left Side of the Longitudinal Beam<br />
71-108<br />
71-109<br />
• System power<br />
a. When ignition switch is ACC: The current flows through cigarette lighter fuse in driver side junction box, pin<br />
4 of sliding roof ECU and pin 2 of sliding roof switch. Then system is powered.<br />
b. When ignition switch is ON/ST: The current flows through sliding roof fuse in driver side junction box, pin 1<br />
of sliding roof ECU and pin 3 of sliding roof switch. Then system is powered.<br />
• System Control<br />
ECU getss the operation signal from the switch and control the motor to operate. All operation is accordance<br />
with user want.<br />
F002 Roof Wire Harness 1 F003 Roof Wire Harness 1<br />
71-110<br />
RESTRAINT CONTROL SYSTEM<br />
71-111<br />
When a car collides with an obstacle, it will quickly open an airbag filled with air, so that the occupants can<br />
throw themselves on the airbag when moving due to inertia, thereby easing the impact on occupants and<br />
absorbing collision energy to reduce personal injuries.<br />
When ignition switch is ON/ST, the current flows through airbag fuse in co-pilot side junction box, to pin 5 of<br />
restraint control module. System is then powered<br />
• Deployment of Airbag<br />
When vehicle is in a frontal collision exceeding a specified level, the current flows from pin 10 of restraint<br />
control module, to pin 3 of clock spring, to driver airbag. Current then flows from driver airbag, to pin 4 of clock<br />
spring, and back to pin 11 of restraint control module. Driver airbag is then activated.<br />
When vehicle is in a frontal collision exceeding a specified level, the current flows from pin 13 of restraint<br />
control module, to pin 1 of passenger airbag. Current then flows from pin 2 of passenger airbag, and back to<br />
pin 14 of restraint control module. Passenger airbag is then activated.<br />
• All Door Unlock<br />
When vehicle is in a frontal collision exceeding a specified level, the current flows from pin 30 of restraint<br />
control module, to pin A11 of central locking controller. Central locking controller getss the sginal of collision<br />
and unlock the all door.<br />
When the system comes into operation, restraint control module detects the operation of all parts of the<br />
system. Once the system or parts have faults, the system will switch on the SRS warning light to remind<br />
drivers of repair in time.<br />
A027 Chassis & Frame Wire Harness I014 Instrument Panel Wire Harness<br />
I002 Instrument Panel Wire Harness I035 Instrument Panel Wire Harness<br />
I003 Instrument Panel Wire Harness M002 Diagnosis Wire Harness<br />
I007<br />
A205<br />
Left Side of the Airbag Module<br />
71-112<br />
WIRING - CONNECTOR VIEWS<br />
CONNECTOR VIEWS<br />
A - CHASSIS & FRAME WIRE HARNESS<br />
A004 to Positive Junction Box A<br />
Code Color Function Qualifier<br />
1 W<br />
2 W-G<br />
Battery Compartment<br />
Junction Box Power<br />
Input<br />
Engine Room<br />
A007 Rear Heater Blower Switch<br />
1 W-B<br />
2 P<br />
3 W-B<br />
Rear Heater Air Flow<br />
Switch Ground<br />
Switch Input<br />
4 B Rear Heater Motor H<br />
A005 to Positive Junction Box C<br />
5 W Rear Heater Motor M<br />
6 L Rear Heater Motor L<br />
1 R-B Generator Output B+<br />
A008 Front Door Lamp Switch LH<br />
A006 to Positive Junction Box D<br />
1 W-L Switch Input<br />
to Positive Junction<br />
Box D Power Input<br />
71-113<br />
A009 ABS Module<br />
Code Color Function Qualifier Code Color Function Qualifier<br />
ABS Motor Power<br />
2 - - 21 - -<br />
3 Y-R<br />
EBD Warning Lamp<br />
Signal Output<br />
Front Right Wheel<br />
Speed Sensor-<br />
5 - - 24 - -<br />
6 R-L Data Link Connector k 25 R-W<br />
ABS Solenoid Valve<br />
Power Input<br />
7 - - 26 - -<br />
8 W<br />
Front Left Wheel<br />
27 Y-G<br />
ABS Fault Light<br />
9 - - 28 R-W ABS-IG Input<br />
10 - - 29 LG<br />
Rear Right Wheel<br />
11 - - 30 G-W Brake Signal Input<br />
12 - - 31 Y-W<br />
Rear Left Wheel<br />
Speed Sensor+<br />
13 W-B Ground 32 - -<br />
14 - - 33 - -<br />
15 - - 34 - -<br />
18 L-G<br />
38 W-B Ground<br />
71-114<br />
A010 Front Wheel Speed Sensor LH<br />
2 B<br />
A013 Rear Wheel Speed Sensor RH<br />
1 LG<br />
A011 Front Wheel Speed Sensor RH<br />
1 L<br />
2 G<br />
A014 Acceleration Sensor<br />
1 Br-R<br />
2 Br-G<br />
3 SB<br />
Acceleration Sensor<br />
Signal-<br />
Signal+<br />
Power+<br />
A012 Rear Wheel Speed Sensor LH<br />
1 L-G<br />
2 Y-W<br />
A015 Secondary Fan Motor<br />
1 W Secondary Fan+<br />
2 Y<br />
Secondary Fan Low<br />
Speed+<br />
Secondary Fan<br />
71-115<br />
A016 Main Fan Motor<br />
1 R-W Fan High Speed+<br />
2 R-B Fan Low Speed+<br />
3 W-B Main Fan Ground<br />
A019 Downstream Oxygen Sensor<br />
1 B<br />
2 O<br />
Downstream Oxygen<br />
3 Y-B<br />
4 G<br />
Heating<br />
Sensor+<br />
A017 Generator B+<br />
A020 Odometer Sensor<br />
1 R-B Sensor Power<br />
A018 Generator Excitation (Gasoline)<br />
1 P-L Generator Excitation<br />
2 L IG End<br />
2 W-B<br />
3 W-G<br />
Vehicle Speed Signal<br />
Output<br />
A021 Back-up Lamp Switch (Gasoline)<br />
A018 Generator (Diesel)<br />
2 P-L Generator Excitation<br />
1 W-L<br />
2 B-Y<br />
Back-up Lamp Power<br />
Reverse Power<br />
71-116<br />
A021 Back-up Lamp Switch (Diesel)<br />
A024 Front Door Lamp Switch RH<br />
1 R-W Front Door Lamp+<br />
A025 Stop Lamp Switch<br />
A022 Fuel Sensor/Fuel Pump<br />
1 Br<br />
Fuel Pump Relay Pin<br />
Fuel Pump,Fuel<br />
Sensor Ground<br />
1 G-W Brake Power Output<br />
2 W-R<br />
3 L-Y<br />
Stop Lamp Power<br />
Engine ECM Brake<br />
Switch Output<br />
4 W-B SW RET<br />
3 V Fuel Sensor+ Input<br />
4 W-B Ground<br />
A026 Parking Brake Switch<br />
A023 Engine Oil Pressure Sensor<br />
1 Y Parking Brake Switch<br />
1 L-Y<br />
Engine Oil Pressure<br />
Warning Light<br />
71-117<br />
A027 Restraint control module (RCM)<br />
1 - - 16 - -<br />
2 - - 17 - -<br />
3 - - 18 - -<br />
4 - - 19 - -<br />
5 B-O Airbag Power Input 20 - -<br />
6 W-B Airbag Ground 21 - -<br />
7 B-Y<br />
Airbag Warning Lamp<br />
8 - - 23 - -<br />
9 R-L Airbag K 24 - -<br />
10 Y<br />
11 Y-B<br />
Airbag Drive Low-side<br />
Interface ACU<br />
Airbag Drive Highside<br />
12 - - 27 - -<br />
13 G-B<br />
14 G-R<br />
High-side<br />
Low-side<br />
15 - - 30 Y<br />
Collision Signal<br />
71-118<br />
A028 Front Blower<br />
1 R-W Front Blower+<br />
A032 Vacuum Level Alarm Switch (Diesel)<br />
1 B -<br />
2 G-W Front Blower-<br />
A029 Front Door Lamp Diode LH<br />
2 W-L Diode-<br />
A033 Data Link Connector 120 Resistance<br />
1 G-B -<br />
2 G-O -<br />
A030 Diesel Filter Heater (Diesel)<br />
1 Br -<br />
2 W-B -<br />
A034 Clutch Switch (Diesel)<br />
3 W-B -<br />
4 L-B -<br />
A031 Preheating Relay Coil (Diesel)<br />
1 L-Y -<br />
2 L-B -<br />
71-119<br />
A035 Electronic Throttle (Diesel)<br />
3 W -<br />
2 L-G -<br />
4 Y -<br />
5 W-R -<br />
6 Y-G -<br />
A036 ECM (Diesel)<br />
E1<br />
W-R<br />
Engine ECU Power<br />
E30 - -<br />
E2 W-B Engine ECU Ground E31 - -<br />
E3<br />
E32 - -<br />
E4 W-B Engine ECU Ground E33 W-B<br />
High-speed Fan<br />
Control Input Pin 86<br />
E5<br />
E34<br />
B-W<br />
Low-speed Fan<br />
Control Feedback Pin<br />
86<br />
E6 W-B Engine ECU Ground E35 G-Y<br />
Preheat Indication<br />
E7 - - E36 Br Engine Maintenance<br />
E8 - - E37 - -<br />
E9 V-W Speed Output E38 - -<br />
E10<br />
B-Y<br />
Diagnosis Switch<br />
E39 L-B Clutch Control Output<br />
71-120<br />
E11<br />
R-W<br />
Medium Pressure<br />
Switch + Output<br />
E40 - -<br />
E12 - - E41 B-G ECU-IG<br />
E13 - - E42 Y-G Throttle Sensor 2+<br />
E14 G-B CAN-H E43 W-R Throttle Sensor 2<br />
E15 G-O CAN-L E44 L-G Throttle Sensor 1<br />
E16 - - E45 - -<br />
E17 - - E46 L-B<br />
Preheating Relay Coil<br />
E18 - - E47 R-Y Fan Low-speed Diode<br />
E19 - - E48 L<br />
A/C Low Level<br />
Approval Output<br />
E20 - - E49 Y-W Engine Stop Light<br />
E21<br />
L-Y<br />
E50 - -<br />
E22 L-W MILL Light E51 - -<br />
E23 - - E52 L-Y<br />
Engine ECU Brake<br />
E24 - - E53 - -<br />
E25 - - E54 - -<br />
E26 - - E55 Y Throttle Sensor 2-<br />
E27 Y-B A/C Request Input E56 B Throttle Sensor 1-<br />
E28 L Vehicle Speed Input E57 W Throttle Sensor 1+<br />
E29 W-B SW RET E58 - -<br />
A101 to Instrument Panel Wire Harness A<br />
5 L -<br />
1 B-W -<br />
2 B -<br />
6 Y -<br />
7 V -<br />
8 Y-B -<br />
9 Y-R -<br />
10 Y-G -<br />
11 W-G -<br />
71-121<br />
12 V-W -<br />
13 P-L -<br />
14 R-W -<br />
15 L-W -<br />
16 Y-W -<br />
17 L-Y -<br />
18 Y-G -<br />
19 Br -<br />
20 G-Y -<br />
A102 to Instrument Panel Wire Harness B<br />
11 G-W -<br />
13 W-L -<br />
14 R-Y -<br />
15 W-L -<br />
16 B-Y -<br />
17 R -<br />
18 G -<br />
21 W-L -<br />
21 R-B -<br />
22 R-B -<br />
4G69 Left<br />
ISF2.8<br />
Left Hand<br />
A103 to Instrument Panel Wire Harness C<br />
1 Y-B -<br />
2 Y -<br />
1 R-B<br />
2 B-G<br />
3 R-W<br />
4 R<br />
5 G-B -<br />
6 R -<br />
7 W-B -<br />
9 W-L -<br />
10 R-L -<br />
3 G-L -<br />
4 Br-L -<br />
5 B-Y -<br />
7 Y-L -<br />
8 B -<br />
9 G-B -<br />
10 G-R -<br />
12 B -<br />
14 B -<br />
15 R-G -<br />
71-122<br />
16 R-B -<br />
17 R-W -<br />
18 R-L -<br />
A106 to Engine Wire Harness 1 (Gasoline)<br />
6 R-W -<br />
7 Y -<br />
8 W-B -<br />
9 L -<br />
10 R -<br />
11 L -<br />
12 W-L -<br />
A104 to Instrument Panel Wire Harness D<br />
1 R -<br />
13 G-B -<br />
15 V-W -<br />
16 L -<br />
A105 to Driver Seat Belt Warning Wire<br />
Harness Assy<br />
A107 to Engine Wire Harness 2 (Gasoline)<br />
2 Br-R -<br />
3 Br-G -<br />
4 SB -<br />
5 G -<br />
2 L-W -<br />
3 Y-G -<br />
5 Y-B -<br />
9 R-L -<br />
10 B -<br />
11 Y-B -<br />
12 O -<br />
14 B-G -<br />
71-123<br />
15 G-W -<br />
16 G -<br />
A108 to Step Lamp Wire Harness<br />
1 G -<br />
2 L -<br />
3 R -<br />
5 R -<br />
6 Gr -<br />
7 R-Y -<br />
A110 to Rear Bumper Transition Wire<br />
Harness<br />
1 R-G -<br />
2 R-B -<br />
3 R-L -<br />
4 R-W -<br />
5 B -<br />
A109 to Rear Heater Wire Harness<br />
1 W -<br />
3 L -<br />
4 B -<br />
5 W-B -<br />
6 W-L -<br />
71-124<br />
A112 to Engine Wire Harness A (Diesel)<br />
A111 to Instrument Panel Wire Harness E<br />
2 Gr -<br />
5 R-B -<br />
6 Gr-R -<br />
7 G-W -<br />
2 G-B -<br />
6 L-Y -<br />
10 G -<br />
11 LG -<br />
12 L -<br />
A113 to Battery Wire Harness B (Diesel)<br />
1 W-B -<br />
2 R -<br />
71-125<br />
B - BATTERY WIRE HARNESS<br />
B001 Starter<br />
B R -<br />
B101 to Chassis & Frame Wire Harness B<br />
B002 Starter Excitation<br />
71-126<br />
C - FRONT BUMPER WIRE HARNESS<br />
C001 Front Fog Lamp LH<br />
1 LG Fog Lamp Power<br />
2 W-B Ground<br />
C101 to Front Wire Harness<br />
C002 Front Fog Lamp RH<br />
4 LG -<br />
6 LG -<br />
71-127<br />
D - FRONT DOOR LH WIRE HARNESS<br />
D001 Front Speaker LH<br />
1 V<br />
Front Left Speaker<br />
2 P Front Left Speaker-<br />
D004 Electric Outside Mirror Switch<br />
1 L-R<br />
Left Outside Mirror<br />
Left And Right Adjust<br />
Right Outside Mirror<br />
Left and Right Adjust<br />
D002 Power Window Motor LH<br />
4 G-R<br />
Outside Mirror Switch<br />
5 R-Y Outside Mirror-<br />
6 W-B Ground<br />
Driver Side Window<br />
Up Input<br />
Down Input<br />
8 R-L<br />
Left Outside Mirror Up<br />
And Down Adjust<br />
Up And Down Adjust<br />
output<br />
D003 Outside Mirror Assy LH<br />
3 B<br />
Outside Mirror Assy<br />
LH Ground<br />
Defroster Power Input<br />
4 R-Y Left Outside Mirror-<br />
5 L-R<br />
6 R<br />
D005 Door Control Switch<br />
1 L-B<br />
2 L<br />
4 P-L<br />
5 L-G<br />
Left Side Door Assy<br />
Control Switch Input<br />
Right Side Window<br />
Control Switch Output<br />
71-128<br />
6 W-B<br />
Door Control Switch<br />
9 G-R<br />
Lamplet Control<br />
12 W-L<br />
D101 to Front Wire Harness A<br />
2 L-R -<br />
3 L-Y -<br />
4 G-R -<br />
6 L-O -<br />
8 R-L -<br />
D006 Front Door Lock Assy LH<br />
1 G<br />
Front Left Door Lock<br />
Unlock Input<br />
Latch Input<br />
7 W-B<br />
Front Door Lock Assy<br />
9 L-O Key Lock Output<br />
10 L-R Key Unlock Output<br />
D102 to Front Wire Harness B<br />
1 L-B -<br />
2 L-Y -<br />
3 P-L -<br />
4 W-L -<br />
6 L -<br />
7 G-R -<br />
8 L-G -<br />
71-129<br />
D103 to Front Wire Harness C<br />
2 P -<br />
5 V -<br />
6 G -<br />
71-130<br />
E - ENGINE WIRE HARNESS<br />
E001 ECM<br />
1 L Ignition Coil 42 Br-Y<br />
Idle Speed Control B<br />
Low<br />
2 B Ground 43 - -<br />
3 B Ground 44 G-W Main Relay Control<br />
4 G Ignition Coil 45 - -<br />
5 - - 46 - -<br />
6 L-W Injector A- 47 W<br />
7 L-P Injector C- 48 O<br />
8 L-V Injector B- 49 W-R<br />
Upstream Oxygen<br />
Sensor Signal+<br />
Coolant Temperature<br />
9 G<br />
10 L<br />
Fuel Pump Relay<br />
ECU Control<br />
Air Conditioning Low<br />
Level Approval Output<br />
50 - -<br />
51 L Vehicle Speed Input<br />
11 P<br />
Sensor-<br />
52 W-B<br />
12 Br Engine Maintenance 53 - -<br />
13 - - 54 L-Y Air Pressure MAP<br />
14 - - 55 - -<br />
15 - - 56 - -<br />
16 - - 57 - -<br />
17 W-B<br />
Control<br />
58 B-W Knock Sensor<br />
18 V-W Vehicle Speed 59 Br-G Acceleration Sensor+<br />
19 L-W MIL 60 - -<br />
20 G-Br<br />
Idle Speed Control A<br />
High<br />
61 - -<br />
71-131<br />
21 G-Y<br />
62 - -<br />
22 - - 63 - -<br />
23 Y-B<br />
Sensor Heating-<br />
64 W-Y<br />
Canister Solenoid<br />
Valve-<br />
24 L-R<br />
65 Y<br />
Starter Excitation<br />
Power Output<br />
25 L-O Injector D- 66 SB<br />
Intake Air<br />
Temperature<br />
Power 2<br />
26 R-W<br />
27 V-G<br />
Switch<br />
67 W-L ECU Power<br />
68 B-G ECU-IG<br />
28 - - 69 - -<br />
29 - - 70 SB<br />
Power<br />
30 O<br />
71 L-W Air Temperature<br />
31 - - 72 - -<br />
32 - - 73 B<br />
33 - - 74 Br-R<br />
Upstream And<br />
Throttle Position Sen-<br />
sor-<br />
34 - - 75 R-L ECU-K Line<br />
35 - - 76 Br-R<br />
36 - - 77 - -<br />
37 O-V Knock Sensor 78 - -<br />
38 - - 79 Y-B AC Request<br />
39 - - 80 - -<br />
40 - - 81 - -<br />
41 Y-P<br />
71-132<br />
E002 Injector A<br />
1 G Injector+<br />
2 L-W Injector A-<br />
E006 Mainfold Absolute Pressure/Intake Air<br />
Temperature Sensor<br />
1 L-Y Air Pressure MAP<br />
2 SB<br />
3 L-W Air Temperature<br />
E003 Injector B<br />
2 L-V Injector B-<br />
4 Br-R<br />
E007 Upstream Oxygen Sensor<br />
E004 Injector C<br />
2 L-P Injector C-<br />
2 W<br />
3 L-R<br />
Sensor Signal-<br />
E005 Injector D<br />
2 L-O Injector D-<br />
E008 Crankshaft Position Sensor<br />
1 O<br />
71-133<br />
3 - Ground<br />
E012 Engine Coolant Temperature Sense<br />
Plug<br />
1 Y-G<br />
Water Temperature<br />
Gauge Sensor<br />
E009 Throttle Position Sensor<br />
1 SB<br />
2 Br-R<br />
3 V-G<br />
Throttle Position<br />
E013 Compressor<br />
1 G-B<br />
Compressor Excitation<br />
E010 Engine Coolant Temperature Sensor<br />
E014 Starter Coil<br />
Starter Excitation Output<br />
E015 Idle Air Control Valve<br />
E011 Knock Sensor<br />
1 O-V Knock Sensor<br />
2 B-W Knock Sensor<br />
1 Br-Y<br />
2 Y-P<br />
71-134<br />
3 G-Y<br />
4 G-Br<br />
E017 Ignition Coil<br />
1 G Ignition Coil<br />
2 L Ignition coil+<br />
3 L Ignition Coil<br />
E016 Canister Solenoid Valve<br />
1 W-Y Canister Valve-<br />
2 G Canister Valve+<br />
E018 Engine Electronic Control Module<br />
1 P<br />
Cylinder 3 Fuel<br />
Injector Solenoid<br />
Valve Drive Signal<br />
49 B<br />
Cylinder 1 Fuel<br />
Valve Drive Circuit<br />
Cylinder 2 Fuel<br />
50 P<br />
3 - - 51 - -<br />
4 - - 52 - -<br />
5 P EGR Valve Motor+ 53 P<br />
Intake Throttle<br />
Actuator Motor-<br />
6 - - 54 - -<br />
7 - - 55 - -<br />
71-135<br />
8 - - 56 - -<br />
9 - - 57 - -<br />
10 - - 58 - -<br />
11 - - 59 - -<br />
12 - - 60 - -<br />
13 R<br />
Engine Crankshaft<br />
Position 5V power<br />
14 B<br />
Position Circuit<br />
62 L<br />
Engine Camshaft<br />
Position Signal<br />
15 G<br />
SAE J1939 Data<br />
Communication<br />
Interface+<br />
63 B<br />
Circuit<br />
Interface-<br />
64 B<br />
Atmospheric Pressure<br />
17 - - 65 B<br />
18 - - 66 B<br />
19 - - 67 B<br />
20 - - 68 B<br />
21 - - 69 L<br />
22 - - 70 L<br />
Intake Manifold<br />
Pressure/<br />
Temperature Circuit<br />
EGR Valve Position<br />
Actuator Position<br />
Fuel Rail Pressure<br />
Signal<br />
Pressure Signal<br />
23 L<br />
Temperature Signal<br />
71 - -<br />
24 - - 72 L<br />
25 B<br />
73 B<br />
26 B<br />
74 P<br />
Cylinder 4 Fuel<br />
27 - - 75 - -<br />
28 - - 76 - -<br />
71-136<br />
29 P EGR Valve Motor- 77 P<br />
Actuator Motor+<br />
30 - - 78 - -<br />
31 B<br />
Fuel Pump Actuator<br />
79 - -<br />
32 P<br />
80 R<br />
Air Mass Flow 12V<br />
33 - - 81 - -<br />
34 - - 82 - -<br />
35 - - 83 - -<br />
36 - - 84 - -<br />
37 L<br />
38 L<br />
85 - -<br />
86 L Air Mass Flow Signal<br />
39 - - 87 R<br />
40 B Air Mass Flow Circuit 88 R<br />
41 - - 89 R<br />
42 - - 90 R<br />
Position Sensor 5V<br />
power<br />
5V Power<br />
Intake manifold<br />
Temperature 5V<br />
43 B<br />
Engine Coolant<br />
91 R<br />
Actuator Position 5V<br />
44 B<br />
Fuel Moisture Content<br />
92 R<br />
Fuel Rail Pressure 5V<br />
45 - - 93 - -<br />
46 L<br />
94 - -<br />
47 L<br />
95 L<br />
48 - - 96 L<br />
71-137<br />
E019 Crankshaft Position Sensor<br />
1 R 5V Signal<br />
2 B Circuit<br />
3 L Signal<br />
E022 Intake manifold Pressure/<br />
1 L Pressure Signal<br />
2 R 5V Power<br />
3 L Temperature Signal<br />
4 B Circuit<br />
E020 Camshaft Position Sensor<br />
1 R 5V Power<br />
E023 Atmospheric Pressure Sensor<br />
E021 Fuel Rail Pressure Sensor<br />
1 B Circuit<br />
2 L Signal<br />
3 R 5V Power<br />
E024 Engine Coolant Temperature Sensor<br />
71-138<br />
E025 Fuel Moisture Content Sensor<br />
1 L Sensor Signal<br />
2 B Sensor Circuit<br />
E028 SAE J1939 Data Communication<br />
Interface<br />
Data Communication<br />
E026 Engine Oil Pressure Switch<br />
E029 Injector 1<br />
1 B Drive Circuit<br />
2 P Drive Signal<br />
E027 Fuel Pump Actuator<br />
1 P Signal<br />
E030 Injector 2<br />
71-139<br />
E031 Injector 3<br />
E034 Intake Throttle Actuator<br />
E032 Injector 4<br />
5 P<br />
E035 EGR Valve<br />
E033 Air Mass Flow Sensor<br />
1 L Signal<br />
2 B 12V Power<br />
3 R Circuit<br />
1 P EGR Valve Motor-<br />
2 P EGR Valve Motor+<br />
3 L<br />
4 B<br />
5 R<br />
71-140<br />
E101 to Chassis Wire Harness 1<br />
E036 Engine Oil Pressure Switch (IC)<br />
1 L-Y Signal<br />
8 W-B<br />
9 L<br />
10 R<br />
11 L Ignition Coil+<br />
12 W-L ECU Power<br />
Compressor<br />
Excitation<br />
E037 Engine Coolant Temperature Sensor<br />
(IC)<br />
15 V-W Vehicle Speed<br />
16 L Vehicle Speed Input<br />
1 Y-G Signal Input<br />
2 W-B Signal Output<br />
E102 to Chassis Wire Harness 2<br />
1 Br Engine Maintenance<br />
2 L-W MILL<br />
3 Y-G<br />
5 Y-B AC Request<br />
6 R-W<br />
3 Br-G Acceleration Sensor+<br />
4 SB<br />
5 G<br />
Sensor Power<br />
Injector,Oxygen<br />
Sensor,Canister<br />
Solenoid Valve+<br />
9 R-L ECU-K Line<br />
7 Y<br />
10 B<br />
71-141<br />
12 O<br />
14 B-G ECU-IG<br />
15 G-W Main Relay Control<br />
E103 to Chassis Wire Harness A (Diesel)<br />
71-142<br />
F - ROOF WIRE HARNESS 1<br />
F003 Sliding Roof Control Switch<br />
F001 Front Dome Light<br />
2 R<br />
Front Dome Light<br />
Central Dome Light<br />
3 W-B Ground<br />
2 R-B<br />
3 R<br />
Sliding Roof ACC<br />
Sliding Roof Switch<br />
4 G Sliding Roof Switch<br />
5 W-B<br />
4 R-W Front Dome Light-<br />
F004 Central Dome Light (High Equipped)<br />
F002 Sliding Roof ECU<br />
Sliding Roof ECU<br />
2 G Sliding Roof Switch<br />
Trunk Lighting Power<br />
2 R-Y Central Dome Light-<br />
3 Y<br />
Dome Light Power<br />
4 R-B<br />
to Power Sliding Roof<br />
ECU-<br />
Sliding Roof ECU-<br />
ACC Input<br />
5 Y<br />
Sliding Roof Control<br />
F004 Central Dome Light (Low Equipped)<br />
1 R Lighting Power Input<br />
2 Y Power Output<br />
1 Y Sliding Roof Switch<br />
71-143<br />
F005 Rear Speaker LH<br />
1 Y<br />
Rear Left Speaker<br />
2 B Rear Left Speaker-<br />
F007 Air Purifier<br />
F006 Rear Combination Lamp LH<br />
1 V-W Rear Left Lamplet+<br />
Rear Left Combination<br />
Lamp Ground<br />
3 G-W Rear Left Stop Lamp+<br />
4 G-Y<br />
5 R-Y<br />
6 B-Y<br />
Rear Left Turn Signal<br />
Rear Left FogLamp<br />
Rear Left Back-up<br />
Lamp+<br />
F101 to Instrument Panel Wire Harness A<br />
1 V-W -<br />
2 G-W -<br />
3 Br -<br />
4 Y-W -<br />
7 L -<br />
9 R -<br />
10 R-W -<br />
12 R-Y -<br />
13 R-B -<br />
15 G-B -<br />
16 G-Y -<br />
Illumination Power<br />
2 R-Y Dome Light-<br />
71-144<br />
F103 to Roof Wire Harness 2A<br />
9 R-Y -<br />
F102 to Instrument Panel Wire Harness B<br />
1 Y -<br />
10 V-W -<br />
11 R -<br />
12 G -<br />
4 R-B -<br />
6 W -<br />
7 R -<br />
8 G-W -<br />
9 G-O -<br />
11 Br -<br />
12 G-Y -<br />
13 B -<br />
F104 to Roof Wire Harness 2B<br />
4 R -<br />
5 W -<br />
6 G-W -<br />
1 G-W -<br />
4 G-B -<br />
6 R-Y -<br />
8 B-Y -<br />
F105 to High-mounted Stop Lamp Wire<br />
3 G-Y -<br />
8 Br -<br />
71-145<br />
F106 to Rear Evaporator Wire Harness<br />
3 Y-W -<br />
4 Br -<br />
71-146<br />
G - ROOF WIRE HARNESS 2<br />
G001 Rear Combination Lamp RH<br />
1 V-W Rear Right Lamplet+<br />
G101 to Roof Wire Harness 1A<br />
3 G-W<br />
4 G-B<br />
Rear Right<br />
Combination Lamp<br />
Rear Right Stop<br />
Rear Right Turn<br />
Signal Power Input<br />
Rear Right Fog Lamp<br />
Rear Right Back-up<br />
G002 Rear Speaker RH<br />
Rear Right Speaker<br />
2 R Rear Right Speaker-<br />
G102 to Roof Wire Harness 1B<br />
G003 Sliding Door Ajar Switch RH<br />
1 R-Y<br />
Right Middle Door<br />
Lamp Power Input<br />
71-147<br />
G103 to Rear Hatch Transition Wire<br />
2 V-W -<br />
4 B-Y -<br />
6 R-B -<br />
7 G -<br />
8 R -<br />
10 G-W -<br />
71-148<br />
H - FRONT DOOR RH WIRE HARNESS<br />
H001 Front Speaker RH<br />
H004 Window Control Switch RH<br />
Front Right Speaker<br />
2 L-G Front Right Speaker-<br />
3 P-L<br />
4 L-Y<br />
H002 Power Window Motor RH<br />
1 G-R<br />
2 R-L<br />
Co-pilot Side Window<br />
H005 Front Door Lock Assy RH<br />
Front Right Door Lock<br />
H003 Outside Mirror Assy RH<br />
4 R-Y Right Outside Mirror-<br />
5 L-Y<br />
6 R-L<br />
71-149<br />
H101 to Front Wire Harness A<br />
4 R-L -<br />
H103 to Front Wire Harness C<br />
3 G-R -<br />
5 L-G -<br />
6 R-L -<br />
H102 to Front Wire Harness B<br />
4 P-Y -<br />
71-150<br />
I - INSTRUMENT PANEL WIRE HARNESS<br />
I002 Instrument Cluster A<br />
A26<br />
Vacuum Level Alarm<br />
+ Input<br />
A1 W-L Instrument Power<br />
A27 G-Y Preheat Indicator<br />
A28 Br Engine Maintenance<br />
A30<br />
Front Door Open<br />
Indicator<br />
A31 B-W Seat Belt Warning<br />
A32 G-Y Left Turn Indicator<br />
A6 V-W Lamplet Signal Input<br />
A7<br />
LG<br />
Front Fog Lamp<br />
A9 W-L Vehicle Speed Output<br />
A10 L-B Vehicle Speed Output<br />
A13<br />
W-G<br />
A14 B Lighting PWM Signal<br />
A15 W-R Door Open Indicator<br />
A16<br />
Instrument Power<br />
A19 W-B Instrument A Ground<br />
A20 R-B Instrument IG Ground<br />
A24 Y-W Engine Stop Light<br />
I003 Instrument Cluster B<br />
B6<br />
Y<br />
B7 V-W<br />
Instrument Parking<br />
Brake Light<br />
Coolant Level Sensor<br />
+ Output<br />
B9<br />
Seat Belt Alarm +<br />
B10 V-W Speed Input<br />
71-151<br />
B16<br />
Y-G<br />
B20<br />
B21<br />
R-Y<br />
Signal Input<br />
Rear Fog Lamp<br />
I004 Headlamp Dimmer Switch<br />
3 G<br />
4 LG<br />
5 Br<br />
Headlamp Dimmer<br />
Lighting<br />
to Front Left<br />
Headlamp Adjustment<br />
Motor<br />
to Front Right<br />
B22<br />
B23<br />
B24<br />
B25<br />
L-W<br />
Y-R<br />
P-L<br />
Engine Failure<br />
Warning Input<br />
EBD Warning Light<br />
Instrument Charging<br />
Indicator Input<br />
B27<br />
B28 R-W<br />
Brake Fluid Sensor +<br />
B30 W-B Instrument B Ground<br />
B31 R-G High Beam Indicator<br />
I005 Instrument Dimmer Switch<br />
Instrument Dimmer<br />
Switch Lamplet<br />
5 B Lighting PWM Signal<br />
B32 G-B Right Turn Indicator<br />
I006 Hazard Warning Switch<br />
to Front Right Low<br />
Beam Fuse<br />
Hazard Warning<br />
Switch Lighting<br />
Instructions<br />
71-152<br />
7 W-B Ground<br />
I007 Central Locking Controller Assy A<br />
Left Door Assy<br />
Switch(Clock) Output<br />
A17 W-L Vehicle Speed Signal<br />
A18 R-B Ignition Switch<br />
8 G-R Switch Signal Output<br />
I008 Central Locking Controller Assy B<br />
A1 W-B Ground<br />
A2 R Lock Output<br />
A3 G Unlock Output<br />
A4<br />
A5<br />
Down Output<br />
Up Output<br />
B1<br />
B2<br />
B3<br />
W-L<br />
Ignition Switch<br />
Illumination Control<br />
Front Left Door Open<br />
Central Locking Spare<br />
B4 G-R Horn<br />
O-L<br />
to Engine Hood<br />
A6<br />
R-L<br />
B7<br />
V-W<br />
Lamplet Forget to<br />
Turn Off Hints<br />
A8<br />
G-R<br />
Window Control<br />
A9 L-O Key Lock Input<br />
A10 L-R Key Unlock Input<br />
B8 O-B Key Detection Switch<br />
B9 - -<br />
B10 W-B Ground<br />
A11 Y Collision Signal Input<br />
A12 G-Y Left Turn Light Signal<br />
G-B<br />
Right Turn Light<br />
A14 R Door Lamp Indicator<br />
A15<br />
L-B<br />
Switch(Data) Output<br />
71-153<br />
I009 Ignition Switch<br />
Ignition Switch AM1<br />
2 R IG1 Power Output<br />
3 R ACC Output<br />
5 R-B<br />
Start Control Power<br />
Ignition Switch AM2<br />
6 L Ignition Switch IG2<br />
I010 Ignition Switch Illumination<br />
I012 Combination Switch (Light)<br />
2 B-W<br />
4 W-B Light Switch Ground<br />
5 G-V Left Turn Switch<br />
6 Y-B Turn Signal Switch<br />
7 G-W Right Turn Switch<br />
8 W-R to Low Beam Relay<br />
9 L-R to High Beam Relay<br />
10 W-B Light Switch Ground<br />
11 W-B Light Switch Ground<br />
13 G-R<br />
Lamplet Relay Control<br />
2 W-R to Central Lock Unit<br />
I013 Combination Switch (Wiper)<br />
I011 Key Insert Switch<br />
3 O-B Switch Input<br />
4 W-B Switch Ground<br />
2 W Rear Wiper<br />
3 P<br />
Rear Washing Motor<br />
4 Y-W Front Washing Motor-<br />
5 W-B Wiper Switch Ground<br />
6 Y<br />
Wiper Intermittent<br />
71-154<br />
7 L-W<br />
8 G-R<br />
9 L-R<br />
Wiper Low Speed<br />
Wiper Switch Power<br />
Wiper High Speed<br />
I016 Rear Window Defroster Switch<br />
2 Y-L<br />
Rear Window<br />
Defroster Switch<br />
I014 Clock Spring<br />
2 G-R Horn Switch<br />
5 Br-L<br />
4 Y-B<br />
I017 Outside Mirror Defroster Switch<br />
I015 12V Power Output Socket<br />
1 W-B Ground<br />
2 R-Y 12V Power Output<br />
5 G-L<br />
Defroster Control<br />
71-155<br />
I020 A/C Control Panel A<br />
I018 Dome Light Switch<br />
Dome Light Switch<br />
Illumination<br />
6 R Indicator Power Input<br />
1 Gr<br />
2 L-B<br />
Rear AC Solenoid<br />
Valve-Input<br />
Servo Motor (Mode)<br />
Defrost<br />
Blowing Face<br />
Warm Damper<br />
5 L-R Cold Damper Control<br />
6 G-W Internal Circulation<br />
7 G External Circulation<br />
8 G<br />
Blower Relay Control<br />
9 G-B AC Request Output<br />
10 R-B AC IG Power<br />
I019 Diagnosis Switch<br />
1 W-B Switch Ground<br />
2 W-B Switch -<br />
3 G Illumination Power<br />
5 B-Y Switch Input<br />
6 R-B Switch Power<br />
18 W-B Ground<br />
19 R-G<br />
Front Air Conditioning<br />
Controller Battery<br />
20 W-B Ground<br />
71-156<br />
I022 Servo Motor (Temperature)<br />
I021 A/C Control Panel B<br />
21 Y-W<br />
Rear Temperature<br />
23 L-O<br />
24 L-G<br />
Mix Damper<br />
Feedback<br />
Mode Feedback<br />
Servo Motor<br />
(Mode)/<br />
(Temperature) 5V<br />
2 L-O<br />
(Temperature)<br />
Internal Temperature<br />
6 L<br />
27 W-B<br />
28 Y-G Front Blower-<br />
29 V<br />
Front Evaporator<br />
Temperature Sensor+<br />
30 - -<br />
31 - -<br />
32 G<br />
Controller Back<br />
33 Br Temperature Sensor-<br />
35 Y Blower Feedback<br />
I023 Rear Blower Forward Switch<br />
Rear Blower Forward<br />
Switch Power Input<br />
5 Gr-R<br />
Solenoid Valve Power<br />
36 LG<br />
Rear AC Switch<br />
Request Output<br />
71-157<br />
I024 Servo Motor (Mode)<br />
2 L-G<br />
I026 Front Evaporator Thermistor<br />
2 Br Temperature Sensor-<br />
5V Output<br />
5 L-B<br />
6 L-Y<br />
I027 Servo Motor (Internal & External<br />
Circulation)<br />
I025 Blower Control Module<br />
5 G External Circulation<br />
2 Y Blower Feedback<br />
3 Y-G Blower Control<br />
4 G-W Front Blower-<br />
I028 Reverse Radar Control Unit<br />
1 B-R Reverse Power Input<br />
2 G-R<br />
3 W-L<br />
Front Right Reverse<br />
Radar Sensor Output<br />
Reverse Radar<br />
Sensor Power Input<br />
71-158<br />
4 R-W<br />
Central Right Sensor<br />
6 L-B Vehicle Speed Signal<br />
7 R-G<br />
8 R-B<br />
Sensor LH Output<br />
Central Left Sensor<br />
9 Y Parking Signal<br />
10 G-O<br />
Front Left Reverse<br />
I030 CD Player-C2<br />
1 B-Y Reverse Detection<br />
2 Y Parking Signal<br />
11 B<br />
15 R-L<br />
Sensor RH Output<br />
16 W-B Ground<br />
I031 Radio A<br />
A1 - -<br />
A3 G Radio illumination<br />
A4 G-R Radio ACC Input<br />
I029 CD Player-C1<br />
1 G-W VIDEO GND Input<br />
2 G-O VIDEO+ Output<br />
A6 - -<br />
A7 R Radio Power Input<br />
A8 W-B Ground<br />
71-159<br />
I032 Radio B<br />
B2 R Rear Right Speaker-<br />
B4 L-G Front Right Speaker-<br />
B5<br />
B6 P Front Left Speaker-<br />
B8 B Rear Left Speaker-<br />
I034 Flasher<br />
1 B-Y Power<br />
2 G-B<br />
Rear Right Turning<br />
Lamp Power<br />
4 R-Y<br />
5 G-V<br />
Front Left Turning<br />
Left Turning Signal<br />
7 G-R<br />
Hazard Warning/Turn<br />
8 W-B Ground<br />
9 G-Y<br />
Rear Left Turning<br />
10 R-L<br />
Front Right Turning<br />
12 G-W<br />
Right Turning Signal<br />
I033 Cigarette Lighter<br />
Cigarette Lighter<br />
I035 Passenger Airbag Assy<br />
71-160<br />
I039 Right Turn Signal Lamp Diode<br />
I036 Right Side Sliding Door Lamp Diode<br />
1 W-R<br />
2 R-Y<br />
Diode - Door Open<br />
Indicator Output<br />
I040 Left Turn Signal Lamp Diode<br />
I037 Rear Hatch Lamp Switch Diode<br />
1 G-Y<br />
Rear Hatch Lamp<br />
Indicate Output<br />
I101 to Front Wire Harness A<br />
I038 Horn Switch<br />
1 G-R Signal Output<br />
5 P -<br />
6 G-Y -<br />
7 G-O -<br />
71-161<br />
8 G-R -<br />
9 B -<br />
10 O-L -<br />
17 G-R -<br />
18 B -<br />
20 G-R -<br />
22 L-O -<br />
23 L-R -<br />
24 L -<br />
25 L-B -<br />
26 G -<br />
27 R -<br />
I102 to Front Wire Harness B<br />
7 L-G -<br />
8 V-W -<br />
9 R-W -<br />
11 G-B -<br />
14 LG -<br />
15 W-B -<br />
16 Y-B -<br />
17 R-L -<br />
18 R-Y -<br />
19 R-B -<br />
20 R-G -<br />
21 G-B -<br />
22 L-B -<br />
23 G-R -<br />
24 L-W -<br />
25 L-R -<br />
26 Y -<br />
27 Y-W -<br />
1 LG -<br />
2 Br -<br />
3 B -<br />
I103 to Front Wire Harness C<br />
71-162<br />
I104 to Chassis & Frame Wire Harness A<br />
5 G-R -<br />
21 R-B<br />
(LH)<br />
I105 to Chassis & Frame Wire Harness C<br />
71-163<br />
I106 to Chassis & Frame Wire Harness B<br />
1 R-B -<br />
2 B-G -<br />
3 R-W -<br />
19 G-O -<br />
20 G-B -<br />
I107 to Roof Wire Harness Assy 1A<br />
I108 to Roof Wire Harness Assy 1B<br />
71-164<br />
I110 to Data Link Connector<br />
5 R-L -<br />
6 G-O -<br />
7 G-B -<br />
I109 to Chassis & Frame Wire Harness E<br />
71-165<br />
I111 to Chassis & Frame Wire Harness D<br />
71-166<br />
J - REAR HATCH WIRE HARNESS<br />
J001 Rear Hatch Lock Assy-Switch<br />
J004 License Lamp<br />
Rear Hatch/Trunk<br />
Lights Power Input<br />
Rear Hatch Lock<br />
1 V-W Power<br />
J005 Camera<br />
J002 Rear Hatch Lock Assy-Motor<br />
Rear Hatch Latch<br />
Rear Hatch Unlocking<br />
1 W-B Camera Ground<br />
2 B-Y Camera Power Input<br />
3 G-W Video Output<br />
4 G-O Video Input<br />
J003 Trunk Lamp<br />
Trunk Lamp Power<br />
71-167<br />
J101 to Rear Hatch Transition Wire Harness<br />
1 B-Y -<br />
3 V-W -<br />
5 G-W -<br />
8 G -<br />
9 R-B -<br />
10 W-B -<br />
71-168<br />
K - REAR HATCH TRANSITION WIRE HARNESS<br />
K101 to Roof Wire Harness 2<br />
K102 to Rear Hatch Wire Harness<br />
71-169<br />
L - REAR EVAPORATOR WIRE HARNESS<br />
L001 Left Blower<br />
1 R +<br />
L004 Temperature Sensor<br />
1 B-W Ground<br />
2 W Sensor+<br />
L002 Right Blower<br />
1 L +<br />
L005 Top Evaporator Blower Switch<br />
1 B Ground<br />
2 R-B A/C signal<br />
3 B Ground<br />
4 L-G L Position<br />
5 L-R M Position<br />
6 R-B H Position<br />
L003 Blower Resistor<br />
1 L-W to Blower-<br />
2 L-R M Position<br />
3 L-G L Position<br />
4 R-B H Position<br />
L101 to Roof Wire Harness 1<br />
4 B-W -<br />
71-170<br />
M - DIAGNOSIS WIRE HARNESS<br />
M001 Data Link Connector Resistance<br />
1 G-B CAN-H<br />
2 G-O CAN-L<br />
M101 to Instrument Panel Wire Harness<br />
M002 Data Link Connector<br />
5 W-B Ground<br />
6 G-B CAN-H<br />
7 R-L<br />
Data Link Connector<br />
K<br />
14 G-O CAN-L<br />
16 W-L Power Input<br />
71-171<br />
N - STEP LAMP WIRE HARNESS<br />
N001 Right Side Sliding Door Lock Assy<br />
Right Side Sliding<br />
Door Unlocking Input<br />
Door Locking Input<br />
N101 to Chassis & Frame Wire Harness<br />
N002 Step Lamp<br />
Step Lamp Power<br />
Right Sliding Door<br />
Light Switch Output<br />
N003 Rear A/C Solenoid Valve<br />
2 Gr<br />
Rear A/C Solenoid<br />
Valve Power Input<br />
Valve Output<br />
71-172<br />
O - DRIVER SEAT BELT WIRE HARNESS<br />
O001 Driver Seat Belt Warning Switch<br />
O101 to Chassis & Frame Wire Harness<br />
71-173<br />
P - REAR HEATER WIRE HARNESS<br />
P001 Rear Heater Solenoid Valve<br />
P002 Rear Heater Motor<br />
1 W Rear Heater Motor M<br />
P101 to Chassis & Frame Wire Harness<br />
Rear Heater Motor+<br />
3 L Rear Heater Motor L<br />
71-174<br />
Q - REAR BUMPER TRANSITION WIRE HARNESS<br />
Q101 to Rear Bumper Wire Harness<br />
1 R-W -<br />
2 R-L -<br />
3 R-B -<br />
4 R-G -<br />
Q102 to Chassis & Frame Wire Harness<br />
71-175<br />
R - REAR BUMPER WIRE HARNESS<br />
R001 Reverse Radar Sensor LH<br />
R004 Reverse Radar Sensor RH<br />
1 R-G<br />
Reverse Radar Sensor<br />
LH Input<br />
1 R-L<br />
Sensor RH Input<br />
Sensor RH Ground<br />
R002 Reverse Radar Central Sensor LH<br />
Reverse Radar Central<br />
Left Sensor Input<br />
R101 to Rear Bumper Transition Wire<br />
R003 Reverse Radar Central Sensor RH<br />
1 R-W<br />
Right Sensor<br />
71-176<br />
S - REAR DEFROST RH WIRE HARNESS<br />
S001 Rear Defrost Heating Wire RH<br />
Rear Right Defrost<br />
S101 to High-mounted Stop Lamp Wire<br />
71-177<br />
T - REAR DEFROST LH WIRE HARNESS<br />
T001 Rear Defrost Heating Wire LH<br />
T101 to High-mounted Stop Lamp Wire<br />
71-178<br />
U - HIGH-MOUNTED STOP LAMP WIRE HARNESS<br />
U101 to Roof Wire Harness 1<br />
U001 Rear Wiper<br />
1 Br Rear Wiper Return<br />
2 G-Y<br />
Rear Wiper Power<br />
Relay to The Rear<br />
Wiper Power Output<br />
U102 to Rear Defrost LH Wire Harness<br />
U002 High-mounted Stop Lamp<br />
2 G-W<br />
High-mounted Stop<br />
Lamp-<br />
U103 to Rear Defrost RH Wire Harness<br />
71-179<br />
V - FRONT WIRE HARNESS<br />
V001 Left Headlight Dimming Motor<br />
V004 Front Turn Signal Lamp LH<br />
1 G-B Motor Power<br />
2 LG<br />
Left Headlamp<br />
Adjusting Signal<br />
Dimming Motor<br />
Front Turn Signal<br />
Lamp LH Ground<br />
Lamp LH Power Input<br />
V005 Right Headlight Dimming Motor<br />
V002 Front Position Lamp LH<br />
2 Br<br />
Right Headlamp<br />
2 V-W<br />
Front Left Position<br />
Right headlamp<br />
V003 Headlamp LH<br />
2 R-G Front Left High Beam<br />
3 R-B Front Left Low Beam<br />
V006 Headlamp RH<br />
Front Right High<br />
Beam<br />
3 G-B<br />
Front Right Low<br />
71-180<br />
V007 Front Position Lamp RH<br />
V010 Front Washing Reservoir Motor<br />
1 Y-W Front Washing Motor-<br />
2 V-W Front Position Lamp+<br />
Front Washing<br />
Motor+<br />
V008 Front Turn Signal Lamp RH<br />
V011 Windshield Wiper Assy<br />
Lamp RH Ground<br />
Lamp RH Power Input<br />
1 L-W<br />
Front Wiper Lowspeed<br />
2 G-R Front Wiper+<br />
V009 Rear Washing Reservoir Motor<br />
4 L-R<br />
Front Wiper<br />
Intermittent Input<br />
Front Wiper Highspeed<br />
Windshield Wiper<br />
Assy Ground<br />
V012 Brake Fluid Level Sensor<br />
Brake Fluid Level<br />
Sensor + Input<br />
71-181<br />
V013 Bass Horn<br />
1 B Horn+<br />
V016 Coolant Level Sensor<br />
2 V-B<br />
V014 Alt Horn<br />
V017 Triple Pressure Switch<br />
1 G-B AV Request Input<br />
Switch-<br />
Switch+ Input<br />
4 Y-B AV Request Output<br />
V015 Engine Hood Switch<br />
1 O-L<br />
Engine Hood Switch<br />
V101 to Instrument Panel Wire Harness<br />
assy A<br />
71-182<br />
V102 to Instrument Panel Wire Harness<br />
assy B<br />
4 V -<br />
71-183<br />
V103 to Instrument Panel Wire Harness<br />
assy C<br />
V105 to Driver Door Wire Harness Assy B<br />
V104 to Driver Door Wire Harness Assy A<br />
V106 to Driver Door Wire Harness Assy C<br />
71-184<br />
V107 to Co-Driver Door Wire Harness Assy<br />
V109 to Co-Driver Door Wire Harness Assy<br />
V110 to Front Bumper Wire Harness Assy<br />
V108 to Co-Driver Door Wire Harness Assy<br />
4 P-L -<br />
2 G-R -<br />
3 G-O -<br />
71-185<br />
X - PREHEATING WIRE HARNESS<br />
X001 Pre-heater<br />
1 B Pre-heater+<br />
X003 Pre-heater Relay B<br />
1 R Pre-heater Relay B<br />
X002 Pre-heater Relay L<br />
1 B Pre-heater Relay L<br />
71-186<br />
WIRING - WIRE HARNESS & CONNECTOR LOCATION VIEWS<br />
WIRE HARNESS & CONNECTOR LOCATION VIEWS<br />
C Front Bumper Wire Harness - Connector<br />
C001 Front Fog Lamp LH C002 Front Fog Lamp RH<br />
C Front Bumper Wire Harness- Inline<br />
71-187<br />
V Front Wire Harness - Connector<br />
00<br />
V001<br />
Left Headlight Dimming Motor<br />
V010<br />
Front Washing Reservoir Motor<br />
V002<br />
V003<br />
Front Position Lamp LH<br />
Headlamp LH<br />
V011<br />
V012<br />
Windshield Wiper Assy<br />
Brake Fluid Level Sensor<br />
V004<br />
V005<br />
Front Turn Signal Lamp LH<br />
Right Headlight Dimming Motor<br />
V013<br />
V014<br />
Bass Horn<br />
Alt Horn<br />
V015<br />
V007<br />
Front Position Lamp RH<br />
V016<br />
Coolant level Sensor<br />
V008<br />
Front Turn Signal Lamp RH<br />
V017<br />
Triple Pressure Switch<br />
Rear Washing Reservoir Motor<br />
V Front Wire Harness - Inline<br />
to Instrument Panel Wire Harness assy A<br />
to Driver Door Wire Harness Assy C<br />
to Instrument Panel Wire Harness assy B<br />
to Co-Driver Door Wire Harness Assy A<br />
to Instrument Panel Wire Harness assy C<br />
to Co-Driver Door Wire Harness Assy B<br />
to Driver Door Wire Harness Assy A<br />
to Co-Driver Door Wire Harness Assy C<br />
to Driver Door Wire Harness Assy B<br />
to Front Bumper Wire Harness Assy<br />
V Front Wire Harness - Ground<br />
V201<br />
Front Wire Harness Left Side Ground<br />
V203<br />
Front Wire Harness Right Side Ground<br />
Front Wire Harness Central Ground<br />
71-188<br />
D Front Door LH Wire Harness - Connector<br />
D001<br />
Front Speaker LH<br />
Electric Outside Mirror Switch<br />
D002<br />
Power Window Motor LH<br />
D005<br />
D003<br />
Outside Mirror Assy LH<br />
D006<br />
Front Door Lock Assy LH<br />
D Front Door LH Wire Harness - Inline<br />
to Front Wire Harness A<br />
to Front Wire Harness C<br />
to Front Wire Harness B<br />
71-189<br />
H Front Door RH Wire Harness - Connector<br />
H001<br />
Front Speaker RH<br />
H004<br />
Window Control Switch RH<br />
H002<br />
Power Window Motor RH<br />
H005<br />
Front Door Lock Assy RH<br />
H003<br />
Outside Mirror Assy RH<br />
H Front Door RH Wire Harness - Inline<br />
71-190<br />
A Chassis & Frame Wire Harness - Connector<br />
A004<br />
to Positive Junction Box A<br />
A025<br />
Stop Lamp Switch<br />
A005<br />
to Positive Junction Box C<br />
A026<br />
Parking Brake Switch<br />
A006<br />
to Positive Junction Box D<br />
A027<br />
Restraint control module (RCM)<br />
A010<br />
Front Wheel Speed Sensor LH<br />
A028<br />
Front Blower<br />
A011<br />
Front Wheel Speed Sensor RH<br />
A029<br />
Front Door Lamp Diode LH<br />
A014<br />
A031<br />
Preheating Relay Coil (Diesel)<br />
A015<br />
Secondary Fan Motor<br />
A032<br />
Vacuum Level Alarm Switch (Diesel)<br />
A016<br />
Main Fan Motor<br />
A034<br />
Clutch Switch<br />
Generator Excitation<br />
A035<br />
Electronic Throttle<br />
A023<br />
Engine Oil Pressure Sensor<br />
71-191<br />
A Chassis & Frame Wire Harness - Inline<br />
to Instrument Panel Wire Harness B<br />
to Rear Heater Wire Harness<br />
to Instrument Panel Wire Harness C<br />
to Instrument Panel Wire Harness D<br />
to Engine Wire Harness A (Diesel)<br />
to Driver Seat Belt Warning Wire Harness<br />
to Engine Wire Harness 1 (Gasoline)<br />
to Battery Wire Harness B (Diesel)<br />
A Chassis & Frame Wire Harness - Ground<br />
Airbag Ground<br />
71-192<br />
A007<br />
Rear Heater Blower Switch<br />
A008<br />
Front Door Lamp Switch LH<br />
A009<br />
ABS Module<br />
A021<br />
A022<br />
A024<br />
A030<br />
A033<br />
A036<br />
Back-up Lamp Switch<br />
Fuel Sensor/Fuel Pump<br />
Front Door Lamp Switch RH<br />
Diesel Filter Heater (Diesel)<br />
Data Link Connector 120 Resistance<br />
ECM (Diesel)<br />
A020<br />
to Instrument Panel Wire Harness A<br />
to Step Lamp Wire Harness<br />
to Engine Wire Harness 2 (Gasoline)<br />
to Rear Bumper Transition Wire Harness<br />
Engine Room Left Side/ABS Ground<br />
A204<br />
Engine Room Right Side Ground<br />
Engine Room Left Side Ground<br />
Electronic Fan Ground<br />
71-193<br />
ENGINE 4G69<br />
E Engine Wire Harness - Connector<br />
E010<br />
E002<br />
Injector A<br />
E011<br />
E003<br />
Injector B<br />
E012<br />
Engine Coolant Temperature Sense Plug<br />
E004<br />
Injector C<br />
E013<br />
E005<br />
Injector D<br />
E014<br />
Starter Coil<br />
E006<br />
E007<br />
E008<br />
Mainfold Absolute Pressure/Intake Air<br />
Upstream Oxygen Sensor<br />
E015<br />
E016<br />
E017<br />
Idle Air Control Valve<br />
Canister Solenoid Valve<br />
Ignition Coil<br />
E009<br />
E Engine Wire Harness - Inline<br />
E101 to Chassis Wire Harness 1 E102 to Chassis Wire Harness 2<br />
71-194<br />
E Engine Wire Harness - Ground<br />
E201 Ground (Near the Thermostat)<br />
71-195<br />
ENGINE ISF2.8<br />
E018<br />
E019<br />
E020<br />
E021<br />
E022<br />
E023<br />
E024<br />
E025<br />
Engine Electronic Control Module<br />
Fuel Rail Pressure Sensor<br />
Intake manifold Pressure/Temperature<br />
Atmospheric Pressure Sensor<br />
Fuel Moisture Content Sensor<br />
E028<br />
SAE J1939 Data Communication<br />
E033<br />
E034<br />
E035<br />
E036<br />
Air Mass Flow Sensor<br />
Intake Throttle Actuator<br />
EGR Valve<br />
Engine Oil Pressure Switch (IC)<br />
E026<br />
E027<br />
E037<br />
to Chassis Wire Harness A (Diesel)<br />
71-196<br />
I Instrument Panel Wire Harness - Connector<br />
Instrument Cluster A<br />
I019<br />
Instrument Cluster B<br />
I020<br />
A/C Control Panel A<br />
I004<br />
Headlamp Dimmer Switch<br />
I021<br />
A/C Control Panel B<br />
I005<br />
Instrument Dimmer Switch<br />
I022<br />
Servo Motor (Temperature)<br />
Hazard Warning Switch<br />
I023<br />
Rear Blower Forward Switch<br />
Central Locking Controller Assy A<br />
I024<br />
I008<br />
Central Locking Controller Assy B<br />
Blower Control Module<br />
I012<br />
Combination Switch (Light)<br />
I026<br />
Front Evaporator Thermistor<br />
I013<br />
I014<br />
I015<br />
I016<br />
I017<br />
I018<br />
Combination Switch (Wiper)<br />
Clock Spring<br />
12V Power Output Socket<br />
Rear Window Defroster Switch<br />
Outside Mirror Defroster Switch<br />
I027<br />
I028<br />
I029<br />
I030<br />
I031<br />
Servo Motor (Internal & External<br />
Reverse Radar Control Unit<br />
CD Player-C1<br />
CD Player-C2<br />
Radio A<br />
71-197<br />
I032<br />
Radio B<br />
I035<br />
Passenger Airbag Assy<br />
I033<br />
Horn Switch<br />
I Instrument Panel Wire Harness - Inline<br />
to Roof Wire Harness Assy 1A<br />
to Chassis & Frame Wire Harness E<br />
to Roof Wire Harness Assy 1B<br />
M Diagnosis Wire Harness - Connector<br />
M001 Data Link Connector Resistance M002 Data Link Connector<br />
M Diagnosis Wire Harness - Inline<br />
to Instrument Panel Wire Harness<br />
69<br />
71-198<br />
I009<br />
I036<br />
Right Side Sliding Door Lamp Diode<br />
I010<br />
Ignition Switch Illumination<br />
I037<br />
Rear Hatch Lamp Switch Diode<br />
I011<br />
Key Insert Switch<br />
I039<br />
Right Turn Signal Lamp Diode<br />
I034<br />
Flasher<br />
I040<br />
Left Turn Signal Lamp Diode<br />
to Chassis & Frame Wire Harness C<br />
to Chassis & Frame Wire Harness B<br />
to Data Link Connector<br />
to Chassis & Frame Wire Harness A<br />
to Chassis & Frame Wire Harness D<br />
I Instrument Panel Wire Harness - Ground<br />
I201 Instrument Panel Signal Ground<br />
I202 Instrument Panel Power Ground<br />
I204<br />
Instrument Panel Power Ground<br />
A/C System Ground<br />
Radio/Data Link Connector Ground<br />
71-199<br />
B Battery Wire Harness - Connector<br />
B001 Starter B002 Starter Excitation<br />
B Battery Wire Harness - Inline<br />
B Battery Wire Harness - Ground<br />
B201 Engine Ground in Engine Room B202 Body Ground (Battery Side)<br />
O Driver Seat Belt Wire Harness - Connector<br />
O001<br />
Driver Seat Belt Warning Switch<br />
71-200<br />
O Driver Seat Belt Wire Harness - Inline<br />
to Chassis & Frame Wire Harness<br />
P Rear Heater Wire Harness - Connector<br />
P001 Rear Heater Solenoid Valve P002 Rear Heater Motor<br />
P Rear Heater Wire Harness - Inline<br />
X Preheating Wire Harness - Connector<br />
X001<br />
Pre-heater<br />
X003<br />
Pre-heater Relay B<br />
X002<br />
Pre-heater Relay L<br />
71-201<br />
F Roof Wire Harness 1 - Connector<br />
F001<br />
F004<br />
Central Dome light (Low Equipped)<br />
F002<br />
F005<br />
Rear Speaker LH<br />
F003<br />
Sliding Roof Control Switch<br />
F006<br />
Rear Combination Lamp LH<br />
Central Dome light (High Equipped)<br />
F007<br />
Air Purifier<br />
F Roof Wire Harness 1 - Inline<br />
to Roof Wire Harness 2A<br />
to High-mounted Stop Lamp Wire<br />
to Rear Evaporator Wire Harness<br />
to Roof Wire Harness 2B<br />
F Roof Wire Harness 1 - Ground<br />
F201<br />
Roof Wire Harness Rear Left Department<br />
71-202<br />
L Rear Evaporator Wire Harness - Connector<br />
L001<br />
Left Blower<br />
L004<br />
L002<br />
Right Blower<br />
L005<br />
Top Evaporator Blower Switch<br />
L003<br />
Blower Resistor<br />
L Rear Evaporator Wire Harness - Inline<br />
71-203<br />
N Step Lamp Wire Harness - Connector<br />
N001<br />
Right Side Sliding Door Lock Assy<br />
N003<br />
Rear A/C Solenoid Valve<br />
N002<br />
Step Lamp<br />
N Step Lamp Wire Harness - Inline<br />
71-204<br />
G Roof Wire Harness 2 - Connector<br />
G001<br />
Rear Combination Lamp RH<br />
G003<br />
Sliding Door Ajar Switch RH<br />
G002<br />
Rear Speaker RH<br />
G Roof Wire Harness 2 - Inline<br />
to Roof Wire Harness 1A<br />
to Rear Hatch Transition Wire Harness<br />
to Roof Wire Harness 1B<br />
71-205<br />
G Roof Wire Harness 2 - Ground<br />
Roof Rear Right Department Ground<br />
J Rear Hatch Wire Harness - Connector<br />
J001<br />
J002<br />
Rear Hatch Lock Assy-Switch<br />
Rear Hatch Lock Assy-Motor<br />
J004<br />
J005<br />
License Lamp<br />
J003<br />
Trunk Lamp<br />
J Rear Hatch Wire Harness - Inline<br />
J Rear Hatch Wire Harness - Ground<br />
J201<br />
Rear Hatch Internal Ground<br />
Q Rear Bumper Transition Wire Harness - Inline<br />
Q101 to Rear Bumper Wire Harness Q102 to Chassis & Frame Wire Harness<br />
R Rear Bumper Wire Harness - Connector<br />
R001<br />
Reverse Radar Sensor LH<br />
R003<br />
Reverse Radar Central Sensor RH<br />
R002<br />
Reverse Radar Central Sensor LH<br />
R004<br />
Reverse Radar Sensor RH<br />
R Rear Bumper Wire Harness - Inline<br />
S Rear Defrost RH Wire Harness - Connector<br />
S001<br />
Rear Defrost Heating Wire RH<br />
S Rear Defrost RH Wire Harness - Inline<br />
to High-mounted Stop Lamp Wire Harness<br />
T Rear Defrost LH Wire Harness - Connector<br />
T001<br />
Rear Defrost Heating Wire LH<br />
71-206<br />
T Rear Defrost LH Wire Harness - Inline<br />
U High-mounted Stop Lamp Wire Harness - Connector<br />
U001 Rear Wiper U002 High-mounted Stop Lamp<br />
U High-mounted Stop Lamp Wire Harness - Inline<br />
to Rear Defrost RH Wire Harness<br />
to Rear Defrost LH Wire Harness<br />
WIRING(RHD)<br />
WIRING DIAGRAM .......................................................................... 71-19<br />
POWER SOURCE ..................................................................... 71-19<br />
ENGINE CONTROL SYSTEM................................................... 71-23<br />
STARTING SYSTEM ................................................................. 71-35<br />
CHARGING SYSTEM................................................................ 71-37<br />
ANTI-LOCK BRAKE CONTROL SYSTEM ................................ 71-39<br />
HEATER AND CONDITIONING CONTROL SYSTEM.............. 71-42<br />
LIGHT SYSTEM......................................................................... 71-49<br />
WIPER AND WASHER.............................................................. 71-73<br />
MULTIMEDIA SYSTEM ............................................................. 71-76<br />
POWER SOCKET...................................................................... 71-79<br />
COMMUNICATION SYSTEM .................................................... 71-81<br />
POWER MIRROR...................................................................... 71-85<br />
WINDOW DEFROSTER ............................................................ 71-88<br />
INSTRUMENT CLUSTER.......................................................... 71-90<br />
ANTI-THEIF SYSTEM................................................................ 71-97<br />
RESTRAINT CONTROL SYSTEM .......................................... 71-102<br />
CONNECTOR VIEWS .................................................................... 71-104<br />
B - BATTERY WIRE HARNESS .............................................. 71-104<br />
C - FRONT BUMPER WIRE HARNESS.................................. 71-105<br />
D - FRONT DOOR LH WIRE HARNESS................................. 71-106<br />
E - ENGINE WIRE HARNESS................................................. 71-108<br />
F - ROOF WIRE HARNESS 1.................................................. 71-119<br />
G - ROOF WIRE HARNESS 2................................................. 71-122<br />
H - FRONT DOOR RH WIRE HARNESS ................................ 71-124<br />
J - REAR HATCH WIRE HARNESS........................................ 71-127<br />
K - REAR HATCH TRANSITION WIRE HARNESS................. 71-129<br />
M - DIAGNOSIS WIRE HARNESS .......................................... 71-130<br />
P - REAR HEATER WIRE HARNESS ..................................... 71-131<br />
Q - REAR BUMPER TRANSITION WIRE HARNESS ............. 71-132<br />
R - REAR BUMPER WIRE HARNESS .................................... 71-133<br />
U - HIGH-MOUNTED STOP LAMP WIRE HARNESS........... 71-134<br />
V - FRONT WIRE HARNESS................................................. 71-135<br />
X - PREHEATING WIRE HARNESS ....................................... 71-141<br />
Z - Main Wire Harness ............................................................. 71-142<br />
WIRE HARNESS & CONNECTOR LOCATION VIEWS................ 71-166<br />
C - FRONT BUMPER WIRE HARNESS.................................. 71-166<br />
V - FRONT WIRE HARNESS .................................................. 71-166<br />
D - FRONT DOOR LH WIRE HARNESS................................. 71-168<br />
H - FRONT DOOR RH WIRE HARNESS ................................ 71-169<br />
Z - MAIN WIRE HARNESS(CHASSIS & FRAME SECTION) 71-170<br />
E - ENGINE WIRE HARNESS................................................. 71-172<br />
Z - MAIN WIRE HARNESS(INSTRUMENT PANEL<br />
SECTION) ............................................ 71-175<br />
M - DIAGNOSIS WIRE HARNESS .......................................... 71-175<br />
B - BATTERY WIRE HARNESS .............................................. 71-179<br />
P - REAR HEATER WIRE HARNESS ..................................... 71-179<br />
X - PREHEATING WIRE HARNESS ....................................... 71-179<br />
F - ROOF WIRE HARNESS 1.................................................. 71-181<br />
G - ROOF WIRE HARNESS 2 ................................................. 71-182<br />
J - REAR HATCH WIRE HARNESS ........................................ 71-182<br />
K - REAR HATCH TRANSITION WIRE HARNESS................. 71-182<br />
Q - REAR BUMPER TRANSITION WIRE HARNESS ............. 71-182<br />
R - REAR BUMPER WIRE HARNESS .................................... 71-182<br />
U - HIGH-MOUNTED STOP LAMP WIRE HARNESS............. 71-182<br />
WIRING(RHD) - HOW TO USE THIS MANUAL<br />
F6 30A ECU Main Fuse<br />
F19 40A IG2 Fusible Link<br />
F20 20A Power Window Fusible Link<br />
F21 20A AM1 Fusible Link<br />
F25 30A Rear A/C Fusible Link<br />
F27 30A Front Blower Fusible Link<br />
F2 7.5A Radio Fuse<br />
F3 7.5A A/C Controller Fuse<br />
F5 10A Instrument Cluster Fuse<br />
F7 10A Rear Fog Lamp Fuse<br />
F9 15A Horn Fuse<br />
F11 15A Front Fog Lamp Fuse<br />
F12 15A Hazard Warning Fuse<br />
F13 10A Dome Light Fuse<br />
F14 20A Headlamp Fuse<br />
F15 20A Central Locking Fuse<br />
F17 15A Rear Heater Fuse<br />
F28 7.5A Small Lamp Fuse<br />
F29 7.5A Switch Lighting Fuse<br />
F30 10A Left High Beam Fuse<br />
F31 10A Right High Beam Fuse<br />
F32 7.5A left Low Beam Fuse<br />
F33 7.5A Right Low Beam Fuse<br />
F34 10A Radio/Outside Mirror Fuse<br />
F35 15A Cigarette Lighter Fuse<br />
F36 7.5A Instrument IG Fuse<br />
F37 15A Front Wiper Fuse<br />
F43 10A Turn Signal Fuse<br />
F44 10A Rear Wiper Fuse<br />
F46 10A Airbag Fuse<br />
F48 10A Back-up Lamp Fuse<br />
F49 15A Power Fuse<br />
F50 5A ECU IG Fuse<br />
F51 15A A/C Fuse<br />
F52 7.5A Outside Mirror Defrost Fuse<br />
R14<br />
Low Beam Relay<br />
R16<br />
R18<br />
R19<br />
R20<br />
R21<br />
High Beam Relay<br />
R22<br />
R11<br />
WIRING(RHD) - WIRING DIAGRAM<br />
• Z015 Ignition Switch<br />
B001 Battery Wire Harness Z050 Main Wire Harness<br />
Z015 Main Wire Harness Z051 Main Wire Harness<br />
Z049 Main Wire Harness Z074 Main Wire Harness<br />
Z111<br />
Z113<br />
Main Wire Harness & Engine Wire Harness<br />
(Manhole After the Driver Seat)<br />
Main Wire Harness & Diagnosis Wire Harness<br />
(Under the Right Bottom Side of the Instrument Panel)<br />
Z203<br />
Instrument Panel Signal Ground<br />
E001 Engine Wire Harness E002 Engine Wire Harness<br />
E003 Engine Wire Harness E004 Engine Wire Harness<br />
E005 Engine Wire Harness E006 Engine Wire Harness<br />
E007 Engine Wire Harness E008 Engine Wire Harness<br />
E009 Engine Wire Harness E010 Engine Wire Harness<br />
E011 Engine Wire Harness E015 Engine Wire Harness<br />
E016 Engine Wire Harness E017 Engine Wire Harness<br />
M002 Diagnosis Wire Harness V031 Front Wire Harness<br />
Z002 Main Wire Harness Z003 Main Wire Harness<br />
Z023 Main Wire Harness Z043 Main Wire Harness<br />
Z048 Main Wire Harness Z050 Main Wire Harness<br />
Z051 Main Wire Harness Z063 Main Wire Harness<br />
Z064 Main Wire Harness Z065 Main Wire Harness<br />
Z067 Main Wire Harness Z076 Main Wire Harness<br />
Z077<br />
Main Wire Harness<br />
Z101<br />
Z112<br />
V112<br />
Engine Wire Harness & Main Wire Harness<br />
Diagnosis Wire Harness & Main Wire Harness<br />
Main Wire Harness & Front Wire Harness<br />
(Right Side of the Instrument Panel)<br />
E201 Ground (Near the Thermostat) Z203 Instrument Panel Signal Ground<br />
Z204 Radio/Data Link Connector Ground Z208 Vehicle Frame Left Side Ground<br />
Z209<br />
E038 Engine Wire Harness E039 Engine Wire Harness<br />
E040 Engine Wire Harness E041 Engine Wire Harness<br />
E042 Engine Wire Harness E043 Engine Wire Harness<br />
E044 Engine Wire Harness E045 Engine Wire Harness<br />
E046 Engine Wire Harness E047 Engine Wire Harness<br />
E048 Engine Wire Harness E049 Engine Wire Harness<br />
E050 Engine Wire Harness E051 Engine Wire Harness<br />
E052 Engine Wire Harness E053 Engine Wire Harness<br />
E054 Engine Wire Harness E055 Engine Wire Harness<br />
E056 Engine Wire Harness M001 Diagnosis Wire Harness<br />
X001 Preheating Wire Harness X002 Preheating Wire Harness<br />
X003 Preheating Wire Harness Z001 Main Wire Harness<br />
Z006 Main Wire Harness Z029 Main Wire Harness<br />
Z037 Main Wire Harness Z043 Main Wire Harness<br />
Z051 Main Wire Harness Z053 Main Wire Harness<br />
Z054 Main Wire Harness Z063 Main Wire Harness<br />
Z068 Main Wire Harness Z072 Main Wire Harness<br />
Z107<br />
Battery Wire Harness & Main Wire Harness<br />
(Car Body Side of the Battery Compartment)<br />
B201 Engine Ground in Engine Room Z208 Vehicle Frame Left Side Ground<br />
B001 Battery Wire Harness B002 Battery Wire Harness<br />
E014 Engine Wire Harness Z015 Main Wire Harness<br />
Main Wire Harness & Battery Wire Harness<br />
Z208<br />
Vehicle Frame Left Side Ground<br />
b. When ignition switch is ON/ST, the current flows output from ignition switch, to instrument panel fuse in copilot<br />
side junction box, through the fuse, to pin A20 of instrument cluster. The current flows through charging<br />
warning light of instrument cluster, from pin B25 of instrument cluster, to pin L of generator connector Z066, to<br />
connector Z074, to charge fusible link and charge a battery, at the same time, supply electrical energy to other<br />
• Z066,Z074 Generator<br />
Z043 Main Wire Harness Z049 Main Wire Harness<br />
Z063 Main Wire Harness Z066 Main Wire Harness<br />
Z074<br />
• Ignition Signal<br />
When ignition switch is ON/ST, current flows through ABS IG fuse in co-pilot side junction box, to pin 28 of<br />
ABS module and ABS system getss ignition signal.<br />
system or parts have faults, the system will switch on the ABS warning light and the EBD warning light to<br />
remind drivers of repair in time.<br />
• Z006 Stop Lamp Switch<br />
M002 Diagnosis Wire Harness Z002 Main Wire Harness<br />
Z003 Main Wire Harness Z006 Main Wire Harness<br />
Z043 Main Wire Harness Z048 Main Wire Harness<br />
Z050 Main Wire Harness Z058 Main Wire Harness<br />
Z059 Main Wire Harness Z060 Main Wire Harness<br />
Z061 Main Wire Harness Z062 Main Wire Harness<br />
Z063<br />
(Under the Right Bottom Side of the Instrument Panel<br />
Z207<br />
ABS Ground<br />
• Ignition Switch At On/St, A/C System Power Supply<br />
a. When ignition switch is turned to ON/ST, current flows through A/C fuse in co-pilot side junction box, to pin<br />
30 of A/C cut off relay, through the relay, battery output from the pin 87a of cut off relay, to pin 10 of A/C controller,<br />
pin 85 of front blower relay, pin 30 and 85 of compressor relay and pin 2 of rear blower forward switch,<br />
then A/C system getss the operation power.<br />
a. blower control: current flows from the pin 87a of A/C relay, to pin 85 of front blower relay, through coil of<br />
relay, output from the pin 86 of relay to pin 8 of A/C control panel A; A/C control panel make the coil of relay to<br />
b. A/C clutch control: Working inquire signal of the front A/C system outputs from pin 9 of A/C control panel, to<br />
pin 1 of triple pressure switch, the signal through switch and connect to engine ECM. If the pressure of refrigerant<br />
in A/C pipe meet the specification as design, ECM will control the A/C relay coil to connect the<br />
ground.Coil then creates a magnetic field, and switch is activated. Current flows into A/C clutch solenoid and<br />
A/C compressor clutch engage and front A/C system begin to work.<br />
c. servo motor (internal & external circulation) control: Current flows from pin 6 of A/C control panel A, to pin<br />
5 of circulation motor, outputs from pin 6 of circulation motor, to pin 7 of A/C control panel A. Motor is working,<br />
the front A/C system is internal circulation mode, on the contrary, system is external circulation mode.<br />
d. servo motor (temperature) control: Current flows from pin 5 and 4 of A/C control panel A, to pin 5 and 6 of<br />
return to A/C control panel from pin 3 and 1 of servo motor to pin 26 and 27 of A/C control panel B. The signal<br />
current outputs from pin 2 of motor, to pin 23 of A/C control panel B, feedback the position signal of servo<br />
e. servo motor (mode) control: Current flows from pin 2 and 3 of A/C control panel, to pin 5 and 6 of servo<br />
A/C control panel from pin 3 and 1 of servo motor to pin 26 and 27 of A/C control panel B. The signal current<br />
outputs from pin 2 of motor, to pin 24 of A/C control panel B, feedback the position signal of servo motor(step<br />
f. Current flows from pin 29 of A/C control panel B, to pin 1 of evaporator thermistor, through thermister, outputs<br />
from pin 2 of thermister, to pin 33 of A/C control panel B. The A/C sustem getsss the temperature Info of<br />
• Compressor Relay<br />
E001 Engine Wire Harness E013 Engine Wire Harness<br />
F008 Roof Wire Harness 1 V031 Front Wire Harness<br />
Z017 Main Wire Harness Z019 Main Wire Harness<br />
Z020 Main Wire Harness Z021 Main Wire Harness<br />
Z022 Main Wire Harness Z023 Main Wire Harness<br />
Z038 Main Wire Harness Z039 Main Wire Harness<br />
Z041 Main Wire Harness Z043 Main Wire Harness<br />
Z051 Main Wire Harness Z069 Main Wire Harness<br />
Z072<br />
F107<br />
Z108<br />
Z103<br />
Engine Wire Harnes & Main Wire Harness<br />
Roof Wire Harness 1 & Main Wire Harness<br />
(Left Side of the Instrument Panel)<br />
Z203 Instrument Panel Signal Ground Z204 Radio/Data Link Connector Ground<br />
Z205<br />
P001 Rear Heater Wire Harness P002 Rear Heater Wire Harness<br />
Z022 Main Wire Harness Z043 Main Wire Harness<br />
Z047 Main Wire Harness Z048 Main Wire Harness<br />
Z051 Main Wire Harness Main Wire Harness<br />
Z109<br />
Main Wire Harness & Rear Heater Wire Harnesss<br />
(Left Side of the Chassis)<br />
Z202 Instrument Panel Power Ground Z204 Radio/Data Link Connector Ground<br />
Z205 A/C System Ground Z210 Engine Room Right Side Ground<br />
The current flows through charge and instrument panel fusible link, to pin 86 and 87 of lo-beam relay in copilot<br />
side junction box, through coil of relay, and then to pin 10 of combination switch. When the combination<br />
switch is set headlamp (Low Beam) position, the current output from pin 7 of combination switch to connect<br />
the ground. The coil of relay creates a magnetic field, and switch is activated. The current flows through switch<br />
of relay, to lo-beam fuse (LH) and lo-beam fuse (RH) in dirver side junction box, and pass then to pin 3 of left<br />
lamp and pin 3 of right headlamp and through light of headlamp (Low Beam). The power is ground at pin 1 of<br />
left and right headlamp. This enables headlamp (Low Beam) to operate.<br />
The current flows through charge and instrument panel fusible link, to headlamp fuse in co-pilot side junction<br />
the combination switch is set headlamp (High Beam) position, the current output from pin 7 of combination<br />
flows through switch of relay, to hi-beam fuse (LH) and hi-beam fuse (RH) in co-pilot side junction box, and<br />
pass then to pin 2 of headlamp LH and pin2 of headlamp RH, and through light of headlamp (High Beam).<br />
The power is ground at pin 1 of left and right headlamp. This enables headlamp (High Beam) to operate.<br />
the combination switch is set flash to pass position, the current output from pin 7 of combination switch to connect<br />
the ground. The coil of relay creates a magnetic field, and switch is activated. The current flows through<br />
switch of relay, to hi-beam fuse (LH) and hi-beam fuse (RH) in co-pilot side junction box, and pass then to pin<br />
2 of headlamp LH and pin2 of headlamp RH, and through light of headlamp (High Beam). The power is<br />
• Z011 Combination Switch (Light Control)<br />
10 - 7:Closed with the combination switch at Headlamp position ( Low Beam).<br />
9 - 7:Closed with the combination switch at Headlamp position (High Beam and Flash to Pass).<br />
V018 Front Wire Harness V020 Front Wire Harness<br />
V023 Front Wire Harness Z011 Main Wire Harness<br />
Z033 Main Wire Harness Z043 Main Wire Harness<br />
Z051<br />
Z105<br />
V111<br />
V205 Front Wire Harness Left Side Ground V206 Front Wire Harness Right Side Ground<br />
Z201 Instrument Panel Power Ground Z203 Instrument Panel Signal Ground<br />
The current flows through charge and instrument panel fusible link in positive junction box, to pin 85 and 87 of<br />
lamplet relay in co-pilot side junction box, pass the coil of relay and then to pin 5 of combination switch. When<br />
the combination switch is set lamplet light or headlamp (Low Beam/High Beam) position, the current flows<br />
output pin 8 of combination switch to connect the ground. The coil of lamplet relay creates a magnetic field,<br />
and switch is activated. The current flows through switch of relay, and through the lamplet fuse in co-pilot side<br />
5 - 8:Closed with the combination switch at Headlamp and lamplet position.<br />
F012 Roof Wire Harness 1 G004 Roof Wire Harness 2<br />
J004 Rear Hatch Wire Harness V019 Front Wire Harness<br />
V024 Front Wire Harness Z011 Main Wire Harness<br />
Z043 Main Wire Harness Z051 Main Wire Harness<br />
G104<br />
G105<br />
F109<br />
Roof Wire Harness 2 & Roof Wire Harness 1<br />
(Top Cap of the Rear Beam Left Side)<br />
(Top Cap of the Rear Beam Right Side)<br />
Main Wire Harness & Roof Wire Harness 1<br />
F202<br />
G202<br />
Roof Wire Harness Rear Right Department<br />
J201 Rear Hatch Internal Ground V205 Front Wire Harness Left Side Ground<br />
V206 Front Wire Harness Right Side Ground Z203 Instrument Panel Signal Ground<br />
2 - 1:Closed with the brake pedal depressed.<br />
U002 High-mounted Stop Lamp Wire Harness Z006 Main Wire Harness<br />
F111<br />
Groundt<br />
When ignition switch is ON/ST, the current flows throug back-up lamp fuse in co-pilot side junction box, to pin<br />
1 of back-up lamp switch. The current flows from pin 2 of back-up lamp switch, and then to the circuit as<br />
• Z056 Back-up Lamp Switch<br />
Z056<br />
Instrument Panel Signal Groundt<br />
Current flows through hazard waring fuse in co-pilot side junction box, to pin 1 of flasher, to supply power for<br />
When ignition switch is ON/ST, the current flows through turn signal fuse in co-pilot side junction box, to pin 12<br />
of combination switch. When operating the combination switch, the current flow output from pin 11 and pin 13<br />
of combination switch, to pin 5 and pin 12 of flasher, vehicle turning lamp is under working condition.<br />
When the combination switch is in Left Turn position, the current flows output from pin 4 and pin 9 of flasher,<br />
When the combination switch is in Right Turn position, the current flows output from pin 2 and pin 10 of flasher,<br />
flasher. Flasher is working condition; The current flows output from pin 2 , 4, 9, 10 of flasher.<br />
Power from pin 4 and pin 9 of flasher:<br />
Power from pin 2 and pin 10 of flasher:<br />
• Z034 Hazard Warning Switch<br />
• Z011 Combination Switch<br />
12 - 11:Closed with the combination switch at Left Turn position.<br />
12 - 13:Closed with the combination switch at Right Turn position.<br />
V021 Front Wire Harness V025 Front Wire Harness<br />
Z007 Main Wire Harness Z011 Main Wire Harness<br />
Z034 Main Wire Harness Z035 Main Wire Harness<br />
Z036 Main Wire Harness Z043 Main Wire Harness<br />
Z202 Instrument Panel Power Ground Z203 Instrument Panel Signal Ground<br />
relay, pass the coil of relay and then to pin 5 of combination switch. When the combination switch is set lamplet<br />
or headlamp (Low Beam/High Beam) position, the current flows output pin 8 of combination switch to connect<br />
switch of relay, from the pin 30 of relay to front fog relay coil, to pin 3 of ombination switch. When front fog lamp<br />
switch is closed, the current flows output from pin 1 of combination switch to connect the ground. The coil of<br />
front fog lamp relay creates a magnetic field, and switch is activated. The current flows through fog lamp fuse<br />
in co-pilot side junction box, to front fog lamp relay, and through switch of front fog lamp relay, to pin 1 of front<br />
fog lamp LH and pin 1 of front fog lamp RH, the power is ground at pin 2 of front fog lamp LH and pin 2 of front<br />
fog lamp RH. This enables front fog lamp LH and front fog lamp RH to operate.<br />
fuse in co-pilot side junction box, to rear fog lamp relay. When front low beam lamp work and rear fog lamp<br />
in co-pilot side junction box, to rear fog lamp relay, and through switch of rear fog lamp relay, to pin 5 of rear<br />
8 - 1:Closed with the combination switch at Lamplet and Headlamp position<br />
C001 Front Bumper Wire Harness C002 Front Bumper Wire Harness<br />
Z011 Main Wire Harness Z043 Main Wire Harness<br />
V120<br />
Front Wire Harness & Front Bumper Wire Harness<br />
V204 Front Wire Harness Central Ground Z203 Instrument Panel Signal Ground<br />
in co-pilot side junction box, to pin 1 and 2 of front dome light. Front dome light is working condition.<br />
a. Press front dome light switch, and the power is ground by the pin 3 of switch. This enables front dome light<br />
in co-pilot side junction box, to pin 1 of central dome light. central dome light is working condition.<br />
in co-pilot side junction box, to pin 1 of step light and output from pin 2 of step light; If sliding door is not closed,<br />
in co-pilot side junction box, to pin 1 of ignition switch illumination; The current outputs from the pin 2 of ignition<br />
in co-pilot side junction box, to pin 1 of trunk lamp and output from pin 2 of trunk lamp; If rear hatch door is not<br />
F009 Roof Wire Harness 1 F010 Roof Wire Harness 1<br />
F011 Roof Wire Harness 1 F014 Roof Wire Harness 1<br />
J001 Rear Hatch Wire Harness J003 Rear Hatch Wire Harness<br />
Z003 Main Wire Harness Z004 Main Wire Harness<br />
Z005 Main Wire Harness Z008 Main Wire Harness<br />
Z014 Main Wire Harness Z031 Main Wire Harness<br />
Z043 Main Wire Harness Z046 Main Wire Harness<br />
Z051 Main Wire Harness Z055 Main Wire Harness<br />
Z071 Main Wire Harness Z073 Main Wire Harness<br />
G106<br />
tail light relay, and then to pin 5 of combination switch. When the combination switch is set lampet or headlamp<br />
(Low Beam/High Beam) position, the current flows output pin 8 of combination switch to connect the ground.<br />
The coil of lamplet relay creates a magnetic field, and switch is activated. The current flows through the pin 87<br />
of lamplet relay and through the lamplet and switch light fuse in co-pilot side junction box and the system<br />
When the combination switch is set lamplet or headlamp position, the current flows output lamplet fuse in copilot<br />
side junction box, to pin A6 of instrument cluster. This enables instrument cluster illumination to operate.<br />
side junction box, to pin 2 of hazard warning switch, to pin 3 of hazard warning switch, the power is<br />
co-pilot side junction box, to pin 3 of headlamp dimmer switch illumination, to pin 6 of headlamp dimmer<br />
switch illumination, the power is ground at pin 6 of headlamp dimmer switch illumination. This enables<br />
headlamp dimmer switch illumination to operate.<br />
co-pilot side junction box, to pin 3 of instrument dimmer switch illumination, to pin 6 of instrument dimmer<br />
co-pilot side junction box, to pin 3 of rear window defroster switch illumination, to pin 1 of rear window<br />
defroster switch illumination, the power is ground at pin 1 of rear window defroster switch illumination. This<br />
enables rear window defroster switch illumination to operate.<br />
co-pilot side junction box, to pin 3 of outside mirror defroster switch illumination, to pin 1 of outside mirror<br />
co-pilot side junction box, to pin 3 of rear blower forward switch illumination, to pin 1 of rear blower<br />
forward switch illumination, the power is ground at pin 1 of rear blower forward switch illumination. This<br />
enables rear blower forward switch illumination to operate.<br />
co-pilot side junction box, to pin 3 of dome light switch illumination, to pin 1 of dome light switch<br />
illumination, the power is ground at pin 1 of dome light switch illumination. This enables dome light switch<br />
illumination to operate.<br />
co-pilot side junction box, to pin 3 of cigarette lighter illumination, to pin 1 of cigarette lighter illumination,<br />
co-pilot side junction box, to pin A3 of radio illumination, to pin A8 of radio illumination, the power is ground<br />
co-pilot side junction box, to pin 32 of A/C control panel llumination, to pin 20 of A/C control panel<br />
co-pilot side junction box, to pin 3 of diagnosis switch llumination, to pin 1 of diagnosis switch llumination,<br />
5 - 8:Closed with the combination switch at Lamplet or Headlamp position.<br />
Z003 Main Wire Harness Z011 Main Wire Harness<br />
Z017 Main Wire Harness Z022 Main Wire Harness<br />
Z023 Main Wire Harness Z024 Main Wire Harness<br />
Z025 Main Wire Harness Z029 Main Wire Harness<br />
Z030 Main Wire Harness Z031 Main Wire Harness<br />
Z032 Main Wire Harness Z033 Main Wire Harness<br />
Z034 Main Wire Harness Z043 Main Wire Harness<br />
Z201 Instrument Panel Power Ground Z202 Instrument Panel Power Ground<br />
When ignition switch is ON/ST, the current flows through front wiper fuse and rear wiper fuse in co-pilot side<br />
pin 3 of combination switch, and output from pin 4 of combination switch, to pin 1 of front wiper motor, and<br />
pin 3 of combination switch, and output from pin 2 of combination switch, to pin 4 of front wiper motor, and<br />
When the front wiper switch of combination switch is set INT, The intermittent current flows from pin 5 of<br />
through the front washer pump, output from pin 1 of front washer pump, to pin 7 of combination switch, and<br />
The current flows output from rear wiper fuse, to pin 86 and 87 of rear wiper relay, and then output from pin 30<br />
of rear wiper relay. When the rear wiper switch is in ON position, the current flows into pin 9 of combination<br />
switch, and then to ground at pin 6 of combination switch; The current flows into coil of rear wiper relay. The<br />
pump, and output from pin 1 of rear washer pump, to pin 8 of combination switch, and ground at pin 6 of<br />
U001 High-mounted Stop Lamp Wire Harness V028 Front Wire Harness<br />
V029 Front Wire Harness V030 Front Wire Harness<br />
Z013 Main Wire Harness Z043 Main Wire Harness<br />
F108<br />
Z106<br />
V204<br />
• Z025 Radio A, Z026 Radio B<br />
• D011 Front Speaker LH<br />
• H006 Front Speaker RH<br />
• F013 Rear Speaker LH<br />
• G005 Rear Speaker RH<br />
D011 Front Door LH Wire Harness F013 Roof Wire Harness 1<br />
G005 Roof Wire Harness 2 H006 Front Door RH Wire Harness<br />
J003 Rear Hatch Wire Harness Z025 Main Wire Harness<br />
Z026 Main Wire Harness Z027 Main Wire Harness<br />
Z028 Main Wire Harness Z043 Main Wire Harness<br />
Z045 Main Wire Harness Z051 Main Wire Harness<br />
F110<br />
V116<br />
V119<br />
D106<br />
H106<br />
Rear Hatch Transition Wire Harness & Rear Hatch Wire Harness<br />
Front Wire Harness & Front Door LH Wire Harness<br />
Z204<br />
• Z030 Cigarette Lighter<br />
When ignition switch is ACC/ON, the current flows through cigarette lighter fuse in co-pilot side junction box,<br />
pin 2 of cigarette lighter. When pressing the cigarette lighter, the current flows output from pin 1 of cigarette<br />
lighter, and ground at pin 1 of cigarette lighter. This enables cigarette lighter to operate.<br />
• Z018 12V Power Output Socket<br />
When ignition switch is ON/ST, the current flows through cigarette lighter fuse in co-pilot side junction box, pin<br />
2 of power output socket. When pressing the power output socket, the current flows output from pin 1 of<br />
power output socket, and ground at pin 1 of power output socket. This enables power output socket to<br />
Z018 Main Wire Harness Z030 Main Wire Harness<br />
Z202<br />
• Horn Control<br />
The current flows through charge and instrument panel fusible link in positive junction box, to horn fuse in copilot<br />
side junction box, to pin 85 of horn relay, and through the coil of horn relay, and then to the circuit as<br />
Current flows from 2 pin of clock spring, to horn switch, when pressing the horn switch, the power is ground by<br />
switch. The coil of horn relay creates a magnetic field, and switch is activated. The current then flows through<br />
switch of horn relay, to pin 1 of horn, and to ground at pin 2 of horn. This enables horn to operate.<br />
Pin 86 of horn relay is controlled by pin 4 of central locking controller to coonect the ground; When pin 86 of<br />
V026 Front Wire Harness V027 Front Wire Harness<br />
Z008 Main Wire Harness Z012 Main Wire Harness<br />
When ignition switch is ON/ST, the current flows through back-up lamp fuse in co-pilot side junction box, to pin<br />
1 of back-up lamp switch. When shift lever in “R” position, the current flows from pin 2 of back-up lamp switch<br />
to pin 1 of reverse radar control unit. The reverse radar control system is then powered.<br />
R001 Rear Bumper Wire Harness R002 Rear Bumper Wire Harness<br />
R003 Rear Bumper Wire Harness R004 Rear Bumper Wire Harness<br />
Z003 Main Wire Harness Z042 Main Wire Harness<br />
Z043 Main Wire Harness Z045 Main Wire Harness<br />
Z051 Main Wire Harness Z056 Main Wire Harness<br />
Z110<br />
Main Wire Harness & Rear Bumper Transition Wire Harness<br />
(Left Side Of the Rear Bumper)<br />
Z203 Instrument Panel Signal Ground Z205 A/C System Ground<br />
When ignition switch is ACC/ON, the current flows through radio ACC fuse in co-pilot side junction box, to pin<br />
4 of outside mirror switch. System is then powered.<br />
D008 Front Door LH Wire Harness H008 Front Door RH Wire Harness<br />
H009 Front Door RH Wire Harness Z043 Main Wire Harness<br />
D104<br />
V117<br />
V114<br />
H104<br />
V118<br />
H105<br />
defroster switch connected, the current output from pin5, then flows to pin 85 of outside mirror defroster<br />
relay,and ground at pin 86. Then through the coil in outside mirror defroster relay pin30, and output from pin 87<br />
of outside mirror defroster relay. The coil of outside mirror defroster relay creates a magnetic field, and switch<br />
is activated. The current flows from outside mirror defrost fuse, through switch of outside mirror defroster relay,<br />
to pin 3 of outside mirror defrost grid and ground at pin 2 of grid. This enables outside mirror defroster to<br />
• Z024 Outside mirror Defrost Switch<br />
Z024 Main Wire Harness Z043 Main Wire Harness<br />
Z102<br />
V113<br />
a. When ignition switch is ON/ST, the current flows through instrument IG fuse in co-pilot side junction box, to<br />
pin A1 and A20 of the instrument cluster. System is then powered.<br />
b.The current flows through charge and instrument panel fusible link in positive junction box, to co-pilot side<br />
junction box and then to pin A16 of instrument cluster. System is then powered.<br />
The current flows through engine coolant fluid level warning light in instrument cluster, and output from pin B16<br />
of instrument cluster, to pin 1 of engine coolant temperature sensor, and ground at pin 2 of engine coolant<br />
temperature sensor (ISF2.8) or itself (4G69). This enables engine coolant fluid level warning light to operate.<br />
output from pin B20 of instrument cluster, to 27 of ABS module. If ABS system is fault, this enables ABS<br />
output from pin B24 of instrument cluster, to 3 of ABS module. If ABS system is fault, this enables EBD<br />
output from pin A31 of instrument cluster, to pin 1 of driver seat belt warning switch and ground at pin 2. If<br />
driver do not fasten the safe belt, switch will close, this enables safe belt indicator to operate.<br />
driver seat belt warning switch and ground at pin 2. If driver do not fasten the safe belt, switch will close, this<br />
enables buzzer to operate.<br />
• Brake Fluid Warning Light<br />
E001 Engine Wire Harness E012 Engine Wire Harness<br />
E036 Engine Wire Harness E037 Engine Wire Harness<br />
V032 Front Wire Harness V033 Front Wire Harness<br />
Z032 Main Wire Harness Z043 Main Wire Harness<br />
Z044 Main Wire Harness Z045 Main Wire Harness<br />
Z051 Main Wire Harness Z057 Main Wire Harness<br />
Z062 Main Wire Harness Z066 Main Wire Harness<br />
Z067 Main Wire Harness Z070 Main Wire Harness<br />
Z072 Main Wire Harness Z078 Main Wire Harness<br />
Z210<br />
• System Power<br />
The current flows through charge and instrument panel fusible link in positive junction box, to co-pilot side<br />
junction box and circuit as follows:<br />
a. When key lock switch is LOCK position, the current flows output from pin A9 of central locking controller, to<br />
pin 9 of front door lock actuator assembly RH and through the key lock switch, to ground at pin 7 of front door<br />
lock actuator assembly RH. This enables closed with door of all with mechanical operate.<br />
b. When key lock switch is OPEN position, the current flows output from pin A10 of central locking controller,<br />
to pin 10 of front door lock actuator assembly RH, and through the key lock switch, to ground at pin 7 of front<br />
door lock actuator assembly RH. This enables opened with door of all with mechanical operate.<br />
• Status of Front Door RH<br />
Current flows from pin B2 of central locking controller, to pin 1 of front door RH switch, through switch to<br />
Signal is from pin 30 of restraint control module, to pin B8 of central locking controller. System getssgetss the<br />
lock actuator assembly, and through the motor in door lock actuator assembly, output from pin 1 of lock<br />
a. Power window LH up: The current flows output from pin A7 of central locking controller, to pin 1 of power<br />
window LH, and through the motor, output from pin 2 of power window LH, to pin A6 of central locking<br />
b. Power window RH up: The current flows output from pin A5 of central locking controller, to pin 1 of power<br />
window RH, and through the motor, output from pin 2 of power window RH, to pin A4 of central locking<br />
D007 Front Door LH Wire Harness D009 Front Door LH Wire Harness<br />
D010 Front Door LH Wire Harness H007 Front Door RH Wire Harness<br />
H010 Front Door RH Wire Harness H011 Front Door RH Wire Harness<br />
J002 Rear Hatch Wire Harness V034 Front Wire Harness<br />
Z003 Main Wire Harness Z008 Main Wire Harness<br />
Z009 Main Wire Harness Z010 Main Wire Harness<br />
Z014 Main Wire Harness Z043 Main Wire Harness<br />
Z044 Main Wire Harness Z051 Main Wire Harness<br />
Z052 Main Wire Harness Z071 Main Wire Harness<br />
V115<br />
D105<br />
(Right Side of the Instrument Panel )<br />
V204 Front Wire Harness Central Ground Z201 Instrument Panel Power Ground<br />
When vehicle is in a frontal collision exceeding a specified level, the current flows from pin 11 of restraint<br />
control module, to pin 4 of clock spring, to driver airbag. Current then flows from driver airbag, to pin 3 of clock<br />
spring, and back to pin 10 of restraint control module. Driver airbag is then activated.<br />
Z003 Main Wire Harness Z009 Main Wire Harness<br />
Z012 Main Wire Harness Z040 Main Wire Harness<br />
Z043 Main Wire Harness Z044 Main Wire Harness<br />
M010<br />
Z203 Instrument Panel Signal Ground Z206 Airbag Ground<br />
WIRING(RHD) - CONNECTOR VIEWS<br />
B101 to Main Wire Harness<br />
D009 Window Control Switch LH<br />
Left Side Window<br />
D007 Power Window Motor LH<br />
1 G-R SIde Window Up<br />
2 R-L Side Window Down<br />
D010 Front Door Lock Assy LH<br />
D008 Outside Mirror Assy LH<br />
Front Left Door<br />
Unlock<br />
4 R Front Left Door Lock<br />
D011 Front Speaker LH<br />
Power +t<br />
2 P Front Left Speaker -<br />
D104 to Front Wire Harness A<br />
3 L-R -<br />
D106 to Front Wire Harness C<br />
D105 to Front Wire Harness B<br />
3 L-YL -<br />
49 R-G<br />
Injector -<br />
2 R-W<br />
50 R-Y<br />
5 B EGR Valve Motor+ 53 B<br />
13 R Sensor + 61 - -<br />
14 B Sensor - 62 Y-Br<br />
15 R CAN + 63 B Sensor -<br />
16 B CAN - 64 B<br />
Sensor -<br />
17 - - 65 B Sensor -<br />
18 - - 66 B Sensor -<br />
19 - - 67 B Sensor -<br />
21 - - 69 Y-Br<br />
23 P-B<br />
24 - - 72 Y-Br<br />
25 W-V<br />
73 W-L<br />
26 R-L<br />
74 W-Y<br />
29 B EGR Valve Motor - 77 B<br />
31 B Inlet Metering Valve - 79 - -<br />
32 B Inlet Metering Valve + 80 B Sensor +<br />
37 Y-Br<br />
38 Y-Br<br />
86 B Air Mass Flow Signal<br />
39 - - 87 R Sensor +<br />
40 B Sensor - 88 R<br />
Sensor +<br />
41 - - 89 R Sensor +<br />
42 - - 90 B Sensor +<br />
91 B Sensor +<br />
46 W-Y<br />
+<br />
47 W-Y<br />
95 B<br />
48 - - 96 B<br />
E039 Inlet Metering Valve<br />
1 B Inlet Metering Valve +<br />
2 B Inlet Metering Valve -<br />
E040 Coolant Temperature Sensor<br />
1 B Sensor -<br />
2 W-Y Sensor +<br />
E041 Water in Fuel Sensor<br />
1 W-Y<br />
E044 Accuumulator Pressure Sensor<br />
2 Y-Br Pressure Signal<br />
3 R Sensor -<br />
E042 Oil Pressure Switch<br />
1 Y-Br Pressure Signal<br />
E045 Ambient Air Pressure Sensor<br />
1 R Sensor +<br />
2 B Sensor -<br />
3 Y-Br Pressure Signal<br />
E043 CAN Datalink<br />
1 R CAN +<br />
2 B CAN -<br />
E046 Intake Manifold Press/Temp Sensor<br />
Presure Signal<br />
2 R Sensor +<br />
3 P-B<br />
Intake Manifold Air<br />
4 B Sensor -<br />
E047 Camshaft Position Sensor<br />
E050 Injector 2<br />
1 R-L Injector 2 -<br />
2 R-W Injector 2 +<br />
3 Y-Br<br />
E051 Injector 3<br />
E048 Crankshaft Position Sensor<br />
1 W-V Injector 3 -<br />
2 W-L Injector 3 +<br />
E052 Injector 4<br />
1 W-L Injector 4 -<br />
2 W-Y Injector 4 +<br />
E049 Injector 1<br />
1 R-G Injector 1 -<br />
2 R-Y Injector 1 +<br />
E053 Air Mass Flow Sensor<br />
1 B Signal<br />
2 B Sensor +<br />
3 B Sensor -<br />
E056 CAN Resistor<br />
1 R Resistor +<br />
2 B Resistor -<br />
E054 Intake Throttle Actuator<br />
4 B Sensor +<br />
5 B<br />
E055 EGR Valve<br />
1 B EGR Control Valve -<br />
2 B EGR Control Valve +<br />
5 B Sensor +<br />
E101 to Main Wire Harness 1<br />
E102 to Main Wire Harness 2<br />
E103 to Main Wire Harness A (Diesel)<br />
F008 Rear Evaporator Module<br />
2 L Power Input<br />
3 Y-W<br />
4 Br Temperature Sensor -<br />
5 L Power Input<br />
6 Lg<br />
Rear Evaporator Air<br />
Flow Switch Power<br />
F010 Central Dome Light (High Equipped)<br />
F010 Central Dome Light (Low Equipped)<br />
F009 Front Dome Light<br />
F011 Air Purifier<br />
F012 Rear Combination Lamp LH<br />
F107 to Main Wire Harness A<br />
F013 Rear Speaker LH<br />
F014 Sliding Door Ajar Switch LH<br />
1 V-W Switch Signal Output<br />
F108 to Main Wire Harness B<br />
F110 to Roof Wire Harness 2B<br />
F109 to Roof Wire Harness 2A<br />
F111 to High-mounted Stop Lamp Wire<br />
G104 to Roof Wire Harness 1A<br />
G004 Rear Combination Lamp RH<br />
G105 to Roof Wire Harness 1B<br />
G005 Rear Speaker RH<br />
G106 to Rear Hatch Transition Wire<br />
H006 Front Speaker RH<br />
D009 Electric Outside Mirror Switch<br />
H007 Power Window Motor RH<br />
1 R Side Window Up<br />
2 L Side Window Down<br />
H008 Outside Mirror Assy RH<br />
D010 Door Control Switch<br />
Right Side Door Assy<br />
H104 to Front Wire Harness A<br />
H011 Front Door Lock Assy RH<br />
1 G Front Right Door Lock<br />
Front Right Door<br />
9 L-O Key Lock<br />
10 L-R Key Unlock<br />
H105 to Front Wire Harness B<br />
H106 to Front Wire Harness C<br />
P101 to Main Wire Harness<br />
Q102 to Main Wire Harness<br />
V018 Left Headlight Dimming Motor<br />
V021 Front Turn Signal Lamp LH<br />
V022 Headlamp RH<br />
V019 Front Position Lamp LH<br />
V020 Headlamp LH<br />
V023 Right Headlight Dimming Motor<br />
1 G-R Motor Power<br />
V027 Alt Horn<br />
V024 Front Position Lamp RH<br />
V028 Front Washing Reservoir Motor<br />
V025 Front Turn Signal Lamp RH<br />
V029 Rear Washing Reservoir Motor<br />
1 P Washing Motor -<br />
2 G-Y Washing Motor +<br />
V026 Bass Horn<br />
V030 Windshield Wiper Assy<br />
3 G-R Power<br />
V034 Engine Hood Switch<br />
V031 Triple Pressure Switch<br />
V111 to Main Wire Harness A<br />
2 LG -<br />
3 P -<br />
V032 Vacuum Warning Switch<br />
1 B Switch + Input<br />
7 R-G -<br />
8 G-B -<br />
9 L-B -<br />
10 L-Y -<br />
12 R-L -<br />
V033 Brake Fluid Level Sensor<br />
13 R-Y -<br />
14 V-W -<br />
15 G-R -<br />
16 LG -<br />
17 P -<br />
18 G-Y -<br />
19 Y-W -<br />
21 G-R -<br />
22 R-L -<br />
23 R -<br />
24 G -<br />
V113 toMain Wire Harness D<br />
2 G -<br />
7 L-R -<br />
V112 to Main Wire Harness C<br />
8 O-L -<br />
9 G-R -<br />
1 G-R -<br />
2 R-W -<br />
4 W-B -<br />
5 R-W -<br />
6 L-W -<br />
8 L-R -<br />
9 Y-B -<br />
10 G-B -<br />
12 L-G -<br />
V114 to Front Door LH Wire Harness A<br />
V115 to Front Door LH Wire Harness B<br />
V117 to Front Door RH Wire Harness A<br />
V116 to Front Door LH Wire Harness C<br />
V118 to Front Door RH Wire Harness B<br />
V119 to Front Door RH Wire Harness C<br />
V120 to Front Bumper Wire Harness<br />
Z - Main Wire Harness<br />
Z002 Instrument Cluster B<br />
Z001 Electronic Throttle<br />
1 B Throttle Sensor 1 -<br />
2 L-G Throttle Sensor 1<br />
3 W Throttle Sensor 1+<br />
4 Y Throttle Sensor 2 -<br />
5 W-R Throttle Sensor 2<br />
6 Y-G Throttle Sensor 2 +<br />
B7 - -<br />
B10 V-W Speed Output<br />
Z003 Instrument Cluster A<br />
A1 R-B Instrument IG Power<br />
A8 L Vehicle Speed Input<br />
Z004 Rear Hatch Lamp Switch Diode<br />
Door Open Indicator<br />
A16 R Instrument Power<br />
A20 R-B Instrument IG Power<br />
Z005 Left Side Sliding Door Lamp Diode<br />
Z006 Stop Lamp Switch<br />
4 W-B Switch -<br />
Z008 Central Locking Controller Assy B<br />
Open Signal Output<br />
Z007 Flasher<br />
Z009 Central Locking Controller Assy A<br />
Z011 Combination Switch (Light)<br />
3 B-W<br />
5 G-R<br />
Door Assy<br />
A18 R-B IG Power<br />
6 W to Day light Relay<br />
10 W-R to Low Beam Relay<br />
11 G-V Left Turn Switch<br />
12 B-R Turn Light Power<br />
13 G-W Right Turn Switch<br />
Z010 Key Insert Switch<br />
Z012 Clock Spring<br />
Z013 Combination Switch (Wiper)<br />
2 L-R<br />
3 G-R<br />
4 L-W<br />
Z015 Ignition Switch<br />
7 Y-W Front Washer Motor -<br />
8 P Rear Washer Motor -<br />
9 W Rear Wiper<br />
Z017 A/C Control Panel B<br />
Z014 Ignition Switch Illumination<br />
Z020 Blower Control Module<br />
Z021 Servo Motor (Temperature)<br />
Z018 12V Power Output Socket<br />
5 L<br />
Z019 Front Blower<br />
6 L-R Cold Damper Control<br />
Z023 A/C Control Panel A<br />
Z022 Rear Blower Forward Switch<br />
Z024 Outside Mirror Defroster Switch<br />
Z026 Radio B<br />
Z025 Radio A<br />
Z027 CD Player-C2<br />
Z028 CD Player-C1<br />
Z031 Dome Light Switch<br />
Z029 Diagnosis Switch<br />
Z032 Instrument Dimmer Switch<br />
Z030 Cigarette Lighter<br />
Z033 Headlamp Dimmer Switch<br />
1 G-B Power<br />
Front Left Headlamp<br />
Adjustment<br />
Front Right<br />
Z034 Hazard Warning Switch<br />
Z036 Turn Signal Lamp Diode LH<br />
Z037 Clutch Switch<br />
3 W-B Clutch Switch<br />
4 L-B Switch Control Output<br />
Z035 Turn Signal Lamp Diode RH<br />
Z038 Servo Motor (Mode)<br />
6 L-B<br />
Z041 Servo Motor (Internal & External<br />
Z039 Front Evaporator Thermistor<br />
5 G-W Internal Circulation<br />
6 G External Circulation<br />
Z042 Reverse Radar Control Unit<br />
Z040 Passenger Airbag Assy<br />
Z044 Restraint control module (RCM)<br />
Z045 Parking Brake Switch<br />
Z047 Rear Heater Blower Switch<br />
Z046 Front Left Door Lamp Switch<br />
Door Open signal<br />
Z049 to Positive Junction Box C<br />
Z050 to Positive Junction Box A<br />
Z053 Diesel Filter Heater<br />
1 Br Power<br />
Z054 Preheating Relay Coil<br />
Z051 to Positive Junction Box D<br />
1 L-Y Coil Output<br />
2 L-B Coil Input<br />
Z055 Step Lamp<br />
Z052 Left Side Sliding Door Lock Assy<br />
1 R Step Lamp Power<br />
2 R-Y Door Control Output<br />
2 G Unlock<br />
4 R Lock<br />
Z056 Back-up Lamp Switch (Gasoline)<br />
Z056 Back-up Lamp Switch (Diesel)<br />
Z059 Front Wheel Speed Sensor LH<br />
Z057 Odometer Sensor<br />
Z060 Rear Wheel Speed Sensor RH<br />
Z061 Rear Wheel Speed Sensor LH<br />
Z058 Front Wheel Speed Sensor RH<br />
Z062 ABS ECU<br />
Z064 Secondary Fan Motor<br />
Z066 Generator (Diesel)<br />
Z067 Fuel Sensor/Fuel Pump<br />
Z065 Main Fan Motor<br />
1 Br Fuel Pump Power<br />
3 V Fuel Sensor Signal<br />
Z068 Data Link Connector 120 Resistance<br />
Z066 Generator Excitation (Gasoline)<br />
1 L IG End<br />
Z069 Rear A/C Solenoid Valve<br />
Z070 Driver Seat Belt Warning Switch<br />
1 B-W Switch Signal Output<br />
A008 Front Door Lamp Switch RH<br />
Z072 ECM (Diesel)<br />
E28 L Vehicle Speed Signal E57 W Throttle Sensor 1+<br />
Z073 Front Door Lamp Diode RH<br />
1 R-W Diode +<br />
2 W-L Diode -<br />
Z077 Acceleration Sensor<br />
Z074 Generator B+<br />
Z078 Engine Oil Pressure Sitch<br />
Z076 Downstream Oxygen Sensor<br />
Z101 to Front Wire Harness C<br />
Z103 to Roof Wire Harness 1A<br />
Z102 to Front Wire Harness D<br />
Z105 to Front Wire Harness A<br />
Z106 to Roof Wire Harness 1B<br />
11 Br<br />
12 G-Y<br />
Z107 to Battery Wire Harness B<br />
Z108 to Engine Wire Harness A<br />
Z109 to Rear Heater Wire Harness<br />
Z111 to Engine Wire Harness 1<br />
Z110 to Rear Bumper Transition Wire<br />
Z112 to Engine Wire Harness 2<br />
Z113 to Data Link Connector<br />
WIRING(RHD) - WIRE HARNESS & CONNECTOR LOCATION VIEWS<br />
V018<br />
V027<br />
V019<br />
V020<br />
V028<br />
V029<br />
V021<br />
V030<br />
V031<br />
V023<br />
V032<br />
Vacuum Warning Switch<br />
V024<br />
V033<br />
V025<br />
V034<br />
V026<br />
to Main Wire Harness A<br />
to Front Door LH Wire Harness C<br />
to Main Wire Harness C<br />
to Front Door RH Wire Harness A<br />
to Main Wire Harness D<br />
tto Front Door RH Wire Harness B<br />
to Front Door LH Wire Harness A<br />
to Front Door RH Wire Harness C<br />
to Front Door LH Wire Harness B<br />
to Front Bumper Wire Harness<br />
V206<br />
V205<br />
D007<br />
D010<br />
D008<br />
D011<br />
D009<br />
Window Control Switch LH<br />
H006<br />
H009<br />
H007<br />
H010<br />
H008<br />
H011<br />
Z - MAIN WIRE HARNESS(CHASSIS & FRAME SECTION)<br />
Z Main Wire Harness - Connector<br />
Z049<br />
Z064<br />
Z050<br />
Z065<br />
Z066<br />
Z054<br />
Preheating Relay Coil(Diesel)<br />
Z069<br />
Z058<br />
Z059<br />
Z078<br />
Z Main Wire Harness - Inline<br />
to Battery Wire Harness B(Diesel)<br />
to Engine Wire Harness A<br />
to Engine Wire Harness 1(Gasoline)<br />
Z046<br />
Z047<br />
Z052<br />
Z053<br />
Z055<br />
Z057<br />
Z060<br />
Z061<br />
Front Left Door Lamp Switch<br />
Left Side Sliding Door Lock Assy<br />
Diesel Filter Heater<br />
Rear Wheel Speed Sensor RH<br />
Rear Wheel Speed Sensor LH<br />
Z062<br />
ABS ECU<br />
Z067<br />
Z071 Front Door Lamp Switch RH<br />
Z112 to Engine Wire Harness 2(Gasoline) Z110 to Rear Bumper Transition Wire Harness<br />
Z Main Wire Harness - Ground<br />
E101 to Main Wire Harness 1 E102 to Main Wire Harness 2<br />
71-Wiring.fm<br />
E038<br />
E039<br />
E040<br />
E041<br />
E042<br />
E043<br />
E044<br />
E045<br />
Inlet Metering Valve<br />
Coolant Temperature Sensor<br />
Water in Fuel Sensor<br />
Oil Pressure Switch<br />
CAN Datalink<br />
Accuumulator Pressure Sensor<br />
Ambient Air Pressure Sensor<br />
E047<br />
E048<br />
E053<br />
E054<br />
E055<br />
E056<br />
CAN Resistor<br />
to Main Wire Harness A (Diesel)<br />
Z - MAIN WIRE HARNESS(INSTRUMENT PANEL SECTION)<br />
Z006<br />
Z008<br />
Z009<br />
Z010<br />
Z015<br />
Z017<br />
Z023<br />
Z033<br />
Z034<br />
Z036<br />
Turn Signal Lamp Diode LH<br />
Z038<br />
Z101 to Front Wire Harness C Z102 to Front Wire Harness D<br />
Z201 Instrument Panel Power Ground Z204 Radio/Data Link Connector Ground<br />
to Main Wire Harness<br />
Z001<br />
Z022<br />
Z024<br />
Z004<br />
Z025<br />
Z005<br />
Left Side Sliding Door Lamp Diode<br />
Z026<br />
Z007<br />
Z027<br />
Z011<br />
Z028<br />
Z012<br />
Z029<br />
Z013<br />
Z014<br />
Z018<br />
Z019<br />
Z020<br />
Z021<br />
Z030<br />
Z031<br />
Z032<br />
Z037<br />
Z039<br />
Z040<br />
Z041<br />
Z042<br />
Z044<br />
Z045<br />
Restraint control module(RCM)<br />
Z206<br />
P001<br />
P002<br />
Rear Heater Solenoid Valve<br />
Rear Heater Motor<br />
F008<br />
Rear Evaporator Module<br />
F012<br />
F009<br />
F013<br />
F010<br />
Central Dome light<br />
F014<br />
Sliding Door Ajar Switch LH<br />
F011<br />
to Main Wire Harness B<br />
G004 Rear Combination Lamp RH G005 Rear Speaker RH<br />
Q101 to Rear Bumper Wire Harness Q102 to Main Wire Harness<br />
HORN ................................................................................................. 81-1<br />
PROBLEM SYMPTOMS TABLE.................................................. 81-1<br />
COMPONENTS ........................................................................... 81-2<br />
REPLACEMENT .......................................................................... 81-3<br />
MULTI-MEDIA AND AIR-CONDITON CONTROLER ASSY ............. 81-4<br />
COMPONENTS ........................................................................... 81-4<br />
REPLACEMENT .......................................................................... 81-5<br />
REVERSE RADAR............................................................................. 81-7<br />
PROBLEM SYMPTOMS TABLE.................................................. 81-7<br />
COMPONENTS ........................................................................... 81-8<br />
REPLACEMENT .......................................................................... 81-9<br />
ASTERN IMAGE .............................................................................. 81-11<br />
REPLACEMENT ........................................................................ 81-11<br />
81<br />
COMMUNICATION SYSTEM - HORN<br />
81-1<br />
1. Horn (Damaged)<br />
2. Horn switch (Damaged)<br />
3. Harness (Damaged) -<br />
1. Horn switch (Damaged)<br />
Chapter 51 steering column - combination<br />
switch assy, replacement<br />
2. Harness (Damaged) -<br />
3. Horn (Damaged) Chapter 81 communication system - horn,<br />
4. Center Door Lock Controller<br />
81-2<br />
1 Alt Horn<br />
2 Bass Horn<br />
5 Horn Transition Bracket Assy2<br />
3 Horn Transition Bracket Assy1<br />
81-3<br />
1. REMOVE FRONT BUMPER. (Refer to “Chapter 88 exterior and interior trim - front bumper,<br />
replacememt”)<br />
2. REMOVE HORN.<br />
(a) Disconnect the horn connector.<br />
Remove the horn retaining bolt.<br />
Remove the horn.<br />
3. INSTALL HORN.<br />
(a) Tighten the horn retaining bolt.<br />
Connect the horn connector.<br />
4. INSTALL FRONT BUMPER. (Refer to “Chapter 88 exterior and interior trim - front bumper,<br />
5. CHECK HORN OPERATION AFTER INSTALLATION.<br />
Check horn volume and quality is normal or not.<br />
MULTI-MEDIA AND AIR-CONDITON CONTROLER ASSY<br />
Multi-Media And Air-Conditon controler<br />
5 Flat Washer<br />
3 Screw<br />
COMMUNICATION SYSTEM - MULTI-MEDIA AND AIR-CONDITON CONTROLER ASSY<br />
81-5<br />
1. REMOVE MULTI-MEDIA AND AIR-CONDITION CON-<br />
TROLER ASSY.<br />
(a) Pry-out the edge of multi-media and air-condition controler<br />
assy with a screwdriver, and then put out.<br />
Dip a cloth into screwdriver to prevent damage to exterior<br />
frame and panel.<br />
Loosen 4 multi-media and air-conditon controler retaining<br />
Disconnect 4 connectors.<br />
Remove multi-media and air-conditon controler assy.<br />
2. INSTALL MULTI-MEDIA AND AIR-CONDITION ASSY.<br />
(a) Connect 4 connectors.<br />
81-6<br />
Tighten 4 retaining screws.<br />
Install exterior frame of multi-media and air-condition<br />
controler assy.<br />
3. CHECK MULTI-MEDIA AND AIR-CONDITION CONTROLER ASSY OPERATION AFTER INSTAL-<br />
LATION.<br />
(a) Display resolution for 800X480.<br />
(b) Multi-media and air-condition controler assy button work normal.<br />
(c) No obvious noise and image fuzzy when useing.<br />
REVERSE RADAR<br />
COMMUNICATION SYSTEM - REVERSE RADAR<br />
81-7<br />
1. Buzzer (Damaged)<br />
Chapter 81 communication system -<br />
reverse radar, replacement<br />
There is no chime within<br />
specified distance<br />
Chime sounds when the<br />
vehicle<br />
is out of specified distance<br />
2. Harness between sensor and<br />
controller (Damaged)<br />
3. Controller (Damaged)<br />
1. Sensor (Incorrect installation)<br />
2. Sensor (Damaged)<br />
81-8<br />
1 Reverse Radar Sensor Assy<br />
2 Reverse Radar Sensor Assy<br />
3 Reverse Radar Controller Assy<br />
81-9<br />
REVERSE RADAR SENSOR ASSY<br />
1. REMOVE REAR BUMPER. (Refer to “Chapter 88 exterior and interior trim - rear bumper, replacement”)<br />
2. REMOVE REVERSE RADAR SENSOR ASSY.<br />
(a) Disconnect the reverse radar sensor connector.<br />
(b) Separate both side of the reverse radar externa bush,<br />
release the reverse radar from the inside of the rear<br />
bumper.<br />
• Do not damage the painted surface of rear bumper.<br />
• Do not damage the reverse radar externa bush.<br />
3. INSTALL REVERSE RADAR SENSOR ASSY.<br />
(a) Position the reverse radar externa bush assy.<br />
Position the reverse radar sensor assy.<br />
81-10<br />
Connect the reverse radar sensor connector.<br />
4. INSTALL REAR BUMPER. (Refer to “Chapter 88 exterior and interior trim - rear bumper, replacement”)<br />
81-11<br />
REVERSE RADAR CONTROL UNIT<br />
1. REMOVE GLOVE BOX.(Refer to “Chapter 83 Instrument Panel - glove box, replacememt”)<br />
2. REMOVE REVERSE RADAR CONTROL UNIT.<br />
(a) Disconnect the reverse radar control unit connector.<br />
Loosen reverse radar control unit screws.<br />
Remove reverse radar control unit.<br />
3. INSTALL REVERSE RADAR CONTROL UNIT.<br />
(a) Tighten reverse radar control unit screws.<br />
Connect the reverse radar control unit connector.<br />
4. INSTALL GLOVE BOX.(Refer to “Chapter 83 Instrument Panel - glove box, replacememt”)<br />
81-12<br />
COMMUNICATION SYSTEM - ASTERN IMAGE<br />
ASTERN IMAGE<br />
1. REMOVE REAR HATCH UPPER GUARD BOARD.(Refer to “Chapter 88 exterior and interior trim<br />
- vehicle door inner guard board, replacememt”)<br />
2. REMOVE ASTERN IMAGE.<br />
(a) Loosen 4 rear hatch outside handle retaining screws.<br />
Pry-out both side buckle of the outside handle.<br />
• Be carefull not to damage body paint.<br />
• Be carefull not to damage rear hatch outside handle.<br />
(c) Turn up the outside handle.<br />
Disconnect the astern image connector.<br />
Loosen 2 astern image retaining screws.<br />
Remove astern image.<br />
81-13<br />
3. INSTALL ASTERN IMAGE<br />
(a) Position the astern image and tighten 2 retaining screws.<br />
Connect astern image connector.<br />
Position the rear hatch outside handle and then retaining<br />
both side buckle.<br />
Tighten 4 retaining screws and install rear hatch outside<br />
handle.<br />
4. INSTALL REAR HATCH UPPER GUARD BOARD.(Refer to “Chapter 88 exterior and interior trim<br />
WINDSHIELDS, MIRRORS & GLASS<br />
WINDOW GLASS............................................................................... 82-1<br />
COMPONENTS ........................................................................... 82-1<br />
POWER WINDOW.............................................................................. 82-2<br />
INSPECTION ............................................................................... 82-2<br />
REPLACEMENT .......................................................................... 82-3<br />
WINDSHIELD ..................................................................................... 82-7<br />
REPLACEMENT .......................................................................... 82-7<br />
REAR WINDOW GLASS.................................................................. 82-12<br />
REPLACEMENT ........................................................................ 82-12<br />
SIDE WINDOW GLASS ................................................................... 82-15<br />
REPLACEMENT ........................................................................ 82-15<br />
OUTSIDE MIRROR .......................................................................... 82-17<br />
REPLACEMENT ........................................................................ 82-17<br />
82<br />
WINDSHIELD/WINDOWGLASS/REAR<br />
VIEW MIRROR -<br />
WINDOW GLASS<br />
WINDSHIELD/WINDOWGLASS/REAR VIEW MIRROR<br />
1 Windshield<br />
2 Rear Window Glass<br />
3 Power Window LH<br />
4 Front Glass LH<br />
5 Middle Glass LH<br />
6 Rear Glass LH<br />
7 Power Window RH<br />
8 Slip Door Glass<br />
9 Middle Glass RH<br />
10 Rear Glass RH<br />
82-1<br />
82-2<br />
POWER WINDOW<br />
Inspect the RH side by the same procedures as the LH side.<br />
1. CHECK POWER WINDOW LIFT FOR DEFORMATION.<br />
(a) If there is any deformation, replace it with a new one.<br />
2. CHECK ROLLER FOR WEAR AND DEFORMATION.<br />
(a) Check roller for wear and deformation.<br />
(b) If there are any wear and deformation, replace the power window lift with a new one.<br />
82-3<br />
Replace the RH side by the same procedures as the LH side<br />
2. REMOVE FRONT DOOR CONTROLLER COVER.<br />
(a) Remove 2 retaining screws of the front door controller<br />
(b) Using a screwdriver, pry up the front door controller<br />
Be careful not to damager interior trim.<br />
Disconnect front door controller connector LH.<br />
3. REMOVE FRONT DOOR LOCK INNER HANDLE<br />
Remove the retaining screw.<br />
82-4<br />
4. REMOVE FRONT DOOR INNER GUARD PLATE ASSY<br />
Using a screwdriver, pry the front door inner triangle<br />
plate LH.<br />
Be careful, not to damager interior trim.<br />
5. REMOVE FRONT DOOR INNER GUARD PLATE.<br />
(a) Using a screwdriver, pry the front door inner guard plate<br />
6. REMOVE FRONT POWER WINDOW LIFT LH.<br />
(a) Loosen retaining screw, remove inner guard.<br />
(b) Disconnect the connector of the front door lock LH.<br />
Connect front door controller connector, lower the glass<br />
to a proper position.<br />
The position you can see 2 window glass motor retaining<br />
Loosen 2 retaining bolts of the power window LH.<br />
Carefully take out the glass.<br />
82-5<br />
Turn the ignition switch OFF and disconnect the front<br />
door controller connectors<br />
Remove retaining bolts of the front power window lift LH.<br />
Disconnect front power window lift connector.<br />
Take out the power window lift assy.<br />
7. INSTALL FRONT POWER WINDOW LIFT LH ASSY.<br />
(a) Position the front power window lift LH assy.<br />
(b) Tighten the retaining screw of the front power window lift<br />
LH assy.<br />
Torque: 6.5 ~ 8.5 N·m<br />
(c) Connect front power window lift connector.<br />
Position the power window glass carefully.<br />
Tighten 2 retaining screws of power window LH.<br />
Install front door inner guard LH.<br />
82-6<br />
8. INSTALL FRONT DOOR INNER GUARD PLATE ASSY.<br />
(a) Install front door inner guard plate assy.<br />
Always use new clips when installing the guard plate<br />
9. INSTALL FRONT DOOR INNER TRIANGLE PLATE<br />
Install front door inner triangle plate LH.<br />
10. INSTALL FRONT DOOR LOCK INNER HANDLE ASSY<br />
Install the retaining screw.<br />
11. INSTALL FRONT DOOR CONTROLLER COVER LH.<br />
Connect connectors.<br />
Position the front door controller cover properly.<br />
Install 2 retaining screws of the front door conreoller LH.<br />
82-7<br />
1. REMOVE ENGINE HOOD. (Refer to “Chapter 87 engine hood and doors - engine hood, replacement”)<br />
2. REMOVE FRONT WIPER ARM ASSY. (Refer to “Chapter 65 wiper and washer - wiper assy,<br />
3. REMOVE WINDSHIELD LOWER TRIM. (Refer to “Chapter 65 wiper and washer - front wiper link<br />
4. REMOVE REAR VIEW MIRROR ASSY. (Refer to “Chapter 82 windshield - rear view mirror,<br />
5. REMOVE A PILLAR UPPER INNER GUARD BOARD. (Refer to “Chapter 88 exterior and interior<br />
trim - side wall guard board, replacement”)<br />
6. REMOVE FRONT WINDSHIELD.<br />
(a) Using a special tool, remove the windshield moulding.<br />
Mark the windshield and body position as shown in the<br />
illustration.<br />
It is no need to mark if the windshield is not resued.<br />
Insert the piano wire between the body and the glass.<br />
Attach wooden blocks to both ends of the piano wire.<br />
Pull the piano wire around the glass and cut off the sealant.<br />
• To prevent vehicle paint damage, use adhesive tape<br />
on painted surfaces during windshield removal.<br />
• Place a plastic cover between the piano wire and the<br />
instrument panel to prevent the instrument panel<br />
from being scuffed when removing the glass.<br />
82-8<br />
Using 2 suckers, remove the windshield.<br />
Remove the front windshield glass.<br />
• Be carefully not to drop off the windshield.<br />
• Leave as much sealant as possible on the body<br />
when removing the front windshield.<br />
7. CLEAN WINDSHIELD.<br />
(a) Remove the sealant on the windshield with a knife.<br />
Do not damage the windshield.<br />
(b) Clean the windshield outer circle with cleaning solvent.<br />
• Do not touch the glass surface after cleaning.<br />
• Even if you use new windshield, you should also<br />
clean the windshield with cleaning solvent.<br />
8. CLEAN BODY SURFACE.<br />
(a) Remove the rough harden sealant left on the body with a<br />
knife and clean with a rag soaked with cleaning slovent.<br />
• Do not damage the body.<br />
• Even if the entire sealant has been cleared, you<br />
should also clean the body surface.<br />
Cut the sealant with the knife around the glass frame.<br />
Leave 2 mm in thickness of sealant.<br />
Do not completely cut curing sealant without necessary. Do<br />
not damage the surface of the body paint. If the paint is<br />
damaged, brush paint or antirusting paint on the damaged<br />
surface<br />
Clean the windshield primer with the alcohol.<br />
82-9<br />
Apply a layer of primer at the outside of the windshield.<br />
• Do not touch the contact surface by hand after<br />
applying the primer.<br />
• Do not brush body primer on the windshield.<br />
• Do not touch water, dust or rarity on the brushing<br />
82-10<br />
9. INSTALL WINDSHIELD.<br />
(a) Position the windshield preperly.<br />
• Position the windshield properly with sucker as shown in<br />
the illustration.<br />
• Check and ensure the contact surface of the windshield<br />
edge is flat.<br />
• Align the reference marks on the glass and the body.<br />
Reaction type polyurethane black primer with a brush in<br />
a mounting surface of the windshield.<br />
• Do not apply too much primer.<br />
• Dry the primer coat for 5 minutes or more.<br />
• Do not save the opened primer for later use.<br />
• Wipe the excess primer off with a clean rag before it<br />
dries.<br />
(c) Apply the polyurethane black glass sealant with sealer<br />
gun in a defined area.<br />
• Wipe the excess sealant off with a clean rag before it<br />
(d) Position the windshield preperly.<br />
• Before installation, torn off the paper of the double-sided<br />
adhesive on the windshield.<br />
• Using a sucker, position the glass so that the reference<br />
marks are aligned.Press it in gently along the rim.<br />
• Lightly press the glass front surface for close contact.<br />
• Using a scraper, remove any excess or protruding<br />
• Fasten the glass with rubber tape before the sealant has<br />
hardened.<br />
• Remove the rubber tape after 4 hours later.<br />
• Check that the stoppers are attached to the body<br />
• Check the clearance between the body and glass.<br />
82-11<br />
10. INSPECT FOR LEAKAGE AND REPAIR .<br />
(a) Perform the leakage test after the hardening period.<br />
(b) Seal any leaks with the porper sealant.<br />
(c) Remove the tape.<br />
11. INSTALL FRONT WIPER ARM ASSY. (Refer to “Chapter 65 wiper and washer - wiper assy,<br />
12. INSTALL WINDSHIELD LOWER TRIM. (Refer to “Chapter 65 wiper and washer - front wiper link<br />
13. INSTALL ENGINE HOOD. (Refer to “Chapter 87 engine hood and doors - engine hood,<br />
14. INSTALL REAR VIEW MIRROR ASSY. (Refer to “Chapter 82 windshield - rear view mirror,<br />
82-12<br />
REAR WINDOW GLASS<br />
1. REMOVE REAR WIPER ARM ASSY. (Refer to “Chapter 88 exterior and interior trim - spoiler<br />
2. REMOVE REAR WINDOW DEFROST WIRING CONNECTOR.<br />
3. REMOVE REAR WINDOW GLASS BY THE SAME PROCEDURES AS FRONT WINDSHIELD.<br />
4. CUT THE SEALANT WITH THE KNIFE AROUND THE GLASS BRACKET. LEAVE 2 MM IN THICKNESS OF<br />
SEALANT.<br />
Do not completely cut curing sealant without necessary. Do not damage the surface of the body paint.<br />
If the paint is damaged, brush paint or antirusting paint on the damaged surface.<br />
5. REMOVE THE ROUGH HARDEN SEALANT LEFT ON THE BODY WITH A KNIFE AND CLEAN WITH A RAG<br />
SOAKED WITH CLEANING SLOVENT.<br />
6. POSITION THE REAR WINDOWSHIEDL, MARK THE REAR<br />
WINDOW AND BODY POSITION AS SHOWN IN THE<br />
ILLUSTRATION.<br />
7. APPLY A LAYER OF PRIMER AT THE INSIDE OF THE<br />
REAR WINDOW GLASS INSERTION STRIP.<br />
• Do not brush body primer on the rear windowglass.<br />
8. APPLY THE SEALANT AROUND THE WINDOW GLASS.<br />
82-13<br />
Apply sealant within 5 minutes after applying the primer.<br />
9. APPLY THE PRIMER ON THE GLASS INSTALLING<br />
SURFACE. AFTER 10 MINUTES INSTALL REAR<br />
WINDOW GLASS.<br />
10. USING SPEICAL TOOLS, INSTALL THE REAR<br />
WINDSHIELD ON THE MOUNTING FRAME.<br />
11. USING A SCRAPER, REMOVE ANY EXCESS OR<br />
PROTRUDING SEALANT.<br />
12. AFTER FOUR HOUR, PERFORM THE TEST FOR REAR<br />
WINDOW WATER LEAKAGE.<br />
82-14<br />
13. FOUND LEAKING, COATED WITH A SEALANT AFTER THE LEAKING PARTS DRY.<br />
• After installing rear window glass, wait one hour or more to let sealant hardened.<br />
• After installing rear window glass, place the vehicle on a flat ground for more than four hours. If<br />
need to run the car this moment, slowly drive the car in eight hours.<br />
• When all the windows are closed, do not close the door furiously.<br />
• After installing rear window glass, do not be over-load in two to three days. (As drive in<br />
irregular, uneven road.)<br />
SIDE WINDOW GLASS<br />
82-15<br />
1. REMOVE SIDE WALL INNER GUARD BOARD. (Refer to “Chapter 88 exterior and interior trim -<br />
side wall inner guard board, replacement”)<br />
2. REMOVE SIDE WINDOW GLASS BY THE SAME PROCEDURES AS WINDSHIELD.<br />
3. CUT THE SEALANT WITH THE KNIFE AROUND THE GLASS FRAME. LEAVE 2mm IN<br />
THICKNESS OF SEALANT.<br />
4. REMOVE THE ROUGH HARDEN SEALANT PORTIONS ON THE BODY WITH A KNIFE AND CLEAN WITH A<br />
RAG SOAKED WITH CLEANING SLOVENT.<br />
5. MARK THE SIDE WINDOW AND BODY POSITION AS<br />
SHOWN IN THE ILLUSTRATION.<br />
6. STICK RUBBER FENDER AROUND THE GLASS TO AVOID SEALANT SPILLED WHEN INSTALLING.<br />
7. INSTALL SIDE WINDOW GLASS TRIM STRIP WITHOUT ANY CLEARENCE.<br />
8. APPLY A LAYER OF PRIMER AT THE OUTSIDE OF THE<br />
SIDE WINDOW GLASS INSERTION STRIP.<br />
applying the primer<br />
9. APPLY THE SEALANT AROUND THE WINDOW GLASS.<br />
82-16<br />
10. APPLY THE PRIMER ON THE SIDE BOARD WIDOW-<br />
GLASS FRAME. AFTER 10 MINUTES INSTALL SIDE<br />
11. USING SPECIAL TOOLS, POSITION THE GLASS SO<br />
THAT THE REFERENCE MARKS ARE ALIGNED.<br />
12. USING A SCRAPER, REMOVE ANY EXCESS OR<br />
13. AFTER FOUR HOURS, PERFORM THE TEST FOR<br />
REAR WINDOW WATER LEAKAGE.<br />
14. FOUND LEAKING, COATED WITH A SEALANT AFTER THE LEAKING PARTS DRY.<br />
• After installing side window glass, wait one hour or more to let sealant hardened.<br />
• After installing side window glass, place the vehicle on a flat ground for more than four hours. If<br />
• After installing side window glass, do not be over-load in two to three days. (As drive in<br />
82-17<br />
1. REMOVE FRONT DOOR INNER GUARD BOARD LH.<br />
(Refer to “Chapter 88 exterior and interior trim -<br />
vehicle door inner guard board, replacement”).<br />
(a) Remove front door inner guard board LH.<br />
2. REMOVE OUTSIDE MIRROR LH.<br />
Disconnect connector.<br />
Loosen 3 retaining nuts.<br />
Remove the outside mirror LH.<br />
3. DISMASSEMBLE OUTSIDE MIRROR LH.<br />
(a) Remove 3 bolts from the mirror base<br />
(b) Remove the mirror body.<br />
82-18<br />
Disconnect the connector of the mirror heating.<br />
Remove the mirror.<br />
• Adjust the outside mirror to limit position, then pry<br />
out the mirror from the back of the outside mirror.<br />
• Be careful when disconnect the connector of the<br />
outside mirror.<br />
Loosen 3 retaining screws of the mirror motor.<br />
Disconnect the connector of the mirror motor.<br />
4. REMOVE THE OUTSIDE MIRROR CONTROLLER.<br />
(a) Loosen 2 front door controller cover.<br />
(b) Remove the front door controller cover.<br />
Disconnect the connector of the front door controller<br />
switch.<br />
82-19<br />
Remove the outside mirror control switch from the bottom<br />
of the controller cover.<br />
5. INSTALL THE OUTSIDE MIRROR CONTROLLER.<br />
(a) Connect the front door controller switch connector.<br />
(b) Install the front door controller switch.<br />
Position the front door controller switch connector.<br />
Tighten 2 retaining screws.<br />
6. ASSEMBLE MIRROR.<br />
(a) Connect the harness of the mirror motor.<br />
Connect the connector of the mirror heating.<br />
Install the outside mirror.<br />
82-20<br />
Tighten 3 bolts from the mirror base.<br />
7. INSTALL OUTSIDE MIRROR ASSY.<br />
Tighten 3 retaining nuts.<br />
8. INSTALL FRONT DOOR INNER GUARD BOARD LH.<br />
9. REMOVE INSIDE REAR VIEW MIRROR.<br />
(a) Remove inside rear view mirror cover.<br />
(b) Extraction the inside rear view mirror from the base.<br />
82-21<br />
10. INSTALL INSIDE REAR VIEW MIRROR.<br />
(a) Install inside rear view mirror.<br />
(b) Install inside rear view mirror cover.<br />
11. REMOVE REAR LOWER VIEW MIRROR.<br />
(a) Use a screwdriver, pry out rear view mirror cover from the<br />
base.<br />
Remove 4 retaining screws from the rear lower view<br />
mirror.<br />
Remove the rear lower view mirror.<br />
12. INSTALL REAR LOWER VIEW MIRROR.<br />
(a) Tighten 4 retaining screws of rear lower view mirror.<br />
Install the rear lower view mirror cover.<br />
INSTRUMENT PANEL<br />
INSTRUMENT CLUSTER .................................................................. 83-1<br />
PRECAUTION.............................................................................. 83-1<br />
COMPONENTS ........................................................................... 83-2<br />
REPLACEMENT .......................................................................... 83-3<br />
DASHBOARD..................................................................................... 83-5<br />
PRECAUTION.............................................................................. 83-5<br />
COMPONENTS ........................................................................... 83-6<br />
REPLACEMENT .......................................................................... 83-7<br />
MIDDLE PLATFORM................................................................. 83-15<br />
REPLACEMENT ........................................................................ 83-15<br />
83<br />
INSTRUMENT PANEL -<br />
83-1<br />
PANEL<br />
(a) Before removing or installing any electrical devices,please disconnect the battery negative cable first<br />
to avoid device damage or personal injury.<br />
(b) Make sure ingition switch is OFF if no specific instructions.<br />
83-2 INSTRUMENT PANEL - INSTRUMENT CLUSTER<br />
1 Instrument Cluster Assy<br />
2 Screw<br />
4 Oil Pressure Switch<br />
5 Coolant Sensor<br />
3 Odometer Sensor<br />
83-3<br />
2. ADJUST STEERING WHEEL TO THE LOWEST POSITION.<br />
3. REMOVE INSTRUMENT CLUSTER COVER ASSY.<br />
(a) Remove 2 instrument cluster cover mounting screws.<br />
(b) Using trim stick, pry out instrument cluster cover from the<br />
dashboard.<br />
(c) Pull instrument cluster cover out far enough to<br />
disconnect dimming switch connector on the left side of<br />
instrument cluster cover.<br />
Disconnect hazard warning switch connector on the<br />
right side of instrument cluster cover.<br />
Disconnect headlight height adjusting switch connector<br />
on the right side of instrument cluster cover.<br />
Remove instrument cluster cover.<br />
Care not to scratch the dashboard and take instrument<br />
cluster cover out from the right side of steering wheel.<br />
83-4 INSTRUMENT PANEL - INSTRUMENT CLUSTER<br />
4. REMOVE INSTRUMENT CLUSTER ASSY.<br />
Remove 2 mounting bolts at the bottom of instrument<br />
cluster.<br />
Pull instrument cluster out.<br />
Turn instrument cluster over and disconnect 2 instrument<br />
cluster connectors.<br />
Remove instrument cluster through the space between<br />
steering wheel and dashboard.<br />
Take instrument cluster out from the right side of steering<br />
wheel, be careful not to scratch the dashboard and instrument<br />
5. INSTALL INSTRUMENT CLUSTER ASSY.<br />
(a) Connect 2 instrument cluster connectors.<br />
Position instrument cluster assy and fix instrument<br />
cluster into proper place.<br />
Tighten 2 instrument cluster mounting screws.<br />
6. INSTALL INSTRUMENT CLUSTER COVER ASSY.<br />
(a) Connect connectors at either side of instrument cluster<br />
(b) Place instrument cluster cover inside and fix it into place.<br />
(c) Tighten 2 mounting screws.<br />
DASHBOARD<br />
83-5<br />
1. WHEN REMOVING INSTRUMENT PANEL, THE MEMORY OF THE AUDIO SYSTEM WILL BE<br />
LOST.<br />
It is recommended that reset the audio systems when work is finished.<br />
(a) Before removing or installing any electrical devices, please disconnect the battery negative cable to<br />
83-6 INSTRUMENT PANEL - DASHBOARD<br />
1 Dashboard Body Assy<br />
3 Center Lower Panel Bracket<br />
4 Screw<br />
5 Instrument Cluster Cover<br />
6 Tapping Screw<br />
7 Center Panel Assy<br />
8 Center Control Panel<br />
9 Steering Column Lower Cover<br />
10 Parking Brake Shield Assy<br />
11 Glove Box Assy<br />
12 Left Defost Vent Assy<br />
13 Right Defost Vent Assy<br />
14 Right Outlet Vent Panel Assy<br />
15 Center Lower Panel Assy<br />
16 Screw base<br />
83-7<br />
1. PLACE TEH VEHICLE ON LEVEL GROUND OR LIFTER AND FACE TIRES STRAIGHT AHEAD.<br />
When disconnecting or connecting the battery cables, please turn off the ignition switch first and<br />
lighting switch and loosen the cable nut completely. Do not pry up the cable when peforming these<br />
operations。<br />
4. REMOVE STEERING WHEEL ASSY. (Refer to “Chapter 51 steering column - steering wheel assy,<br />
5. REMOVE STEERING COLUMN LOWER COVER.<br />
6. REMOVE COMBINATION SWITCH UPPER AND LOWER COVER.<br />
8. REMOVE INSTRUMENT CLUSTER ASSY. (Refer to “Chapter 83 instrument panel - instrument<br />
cluster , replacement”)<br />
9. REMOVE MULTI-MEDIA AND A/C CONTROLLER. (Refer to “Chapter 61 heater and air conditioner<br />
- multi-media and A/C controller assy , replacement”)<br />
10. REMOVE CENTER SWITCH PANEL.<br />
(a) Remove 4 center switch panel mounting screws.<br />
(b) Pull center switch panel out.<br />
Disconnect 4 electrical connectors from the rear.<br />
Remove centre switch panel.<br />
11. REMOVE CIGARETTE LIGHTER.<br />
(a) Disconnect connector from the back of cigarette lighter.<br />
(b) Remove cigarette lighter. (Refer to “Chapter 66 audio<br />
system - electric device accessories , replacement”)<br />
83-8 INSTRUMENT PANEL - DASHBOARD<br />
12. REMOVE ASHTRAY.<br />
(a) Depress release latch, pull ashtray out.<br />
13. REMOVE TRANSMISSION SHIFTING CONTROL LEVER BALL ASSY AND DUST COVER. (Refer<br />
to “Chapter 41 transmission - transmission operation mechanism assy, replacement”)<br />
14. REMOVE BOTH SIDE DEFOST VENT.<br />
(a) Using trim stick, pry up left defost vent assy.<br />
(b) The procedure to remove right defost vent assy is similar<br />
to the left side.<br />
15. REMOVE OUTLET VENT PANEL.<br />
(a) Using trim stick, along the edge pry outlet vent panel out.<br />
(b) Remove outlet vent panel.<br />
16. REMOVE GLOVE BOX ASSY.<br />
83-9<br />
17. REMOVE CENTRE LOWER PANEL ASSY.<br />
(a) Remove 5 mounting screws on both and top side of the<br />
centre lower panel.<br />
18. REMOVE PARKING BRAKE SHIELD.<br />
(a) Using trim stick, pry up parking brake shield along its<br />
19. REMOVE CENTRE PANEL ASSY.<br />
(a) Remove 3 centre panel mounting screws.<br />
(b) Using trim stick, pry up centre panel.<br />
20. REMOVE 12V POWER OUTLET SOCKET.<br />
(a) Disconnect 12V power outlet connect from the inside of<br />
(b) Remove 12V power outlet socket from dashboard. (Refer<br />
to “Chapter 66 audio system - electric device accessories<br />
, replacement”)<br />
21. REMOVE DIAGNOSTIC SOCKET.<br />
(a) Loosen 2 diagnostic socket mounting screws.<br />
(b) Remove diagnostic socket from the dashboard.<br />
83-10 INSTRUMENT PANEL - DASHBOARD<br />
22. REMOVE ENGINE HOOD AND FUEL FILLER DOOR<br />
HANDLE.<br />
Remove engine hood handle from dashboard.<br />
Remove fuel filler door handle from dashboard.<br />
23. REMOVE BOTH A-PILLAR HANDLES AND A PILLAR UPPER GUARD BOARDS. (Refer to<br />
“Chapter 88 exterior and interior - roof panel, replacement”)<br />
24. REMOVE DASHBOARD ASSY.<br />
Remove 11 mounting bolts/screws as shown.<br />
Remove instrument cluster carefully.<br />
Because there are many harnesses in the instrument panel,<br />
when removing the instrument panel, be careful not to hook<br />
the harness, so as not to damage the harness.<br />
25. INSTALL DASHBOARD ASSY.<br />
83-11<br />
Position the dashboard body properly.<br />
Put the inside harness in order and wait for using when<br />
installing dashboard accessories.<br />
Tighten 11 mounting bolts/screws.<br />
26. INSTALL CENTRE PANEL ASSY.<br />
(a) Place centre panel into dashboard properly.<br />
(b) Tighten 3 mounting screws.<br />
27. INSTALL OUTLET VENT PANEL ASSY.<br />
(a) Position outlet vent panel and press outlet vent panel<br />
evenly into place.<br />
28. INSTALL INSTRUMENT CLUSTER AND COVER. (Refer to “Chapter 83 instrument panel -<br />
instrument cluster , replacement”)<br />
29. INSTALL TRANSMISSION SHIFTING CONTROL LEVER BALL ASSY AND DUST COVER. (Refer<br />
83-12 INSTRUMENT PANEL - DASHBOARD<br />
30. INSTALL CIGARETTE LIGTHTER.<br />
(a) Install cigarette lighter, and connect the connector to the<br />
back of cigarette lighter.<br />
31. INSTALL CENTRE SWITCH PANEL.<br />
(a) Connect centre switch panel connector.<br />
Tighten 4 centre switch panel mounting screws.<br />
32. INSTALL MULTI-MEDIA AND A/C CONTROLLER ASSY. (Refer to “Chapter 61 heater and air conditioner<br />
- multi-media and A/C controller assy, replacement”)<br />
33. INSTALL 12V POWER OUTLET SOCKET.<br />
(a) Install 12V power outlet socket. (Refer to “Chapter 66<br />
audio system - electric device accessories , replacement”)<br />
(b) Connect 12V power outlet socket connector.<br />
83-13<br />
34. INSTALL GLOVE BOX ASSY.<br />
35. INSTALL PARKING BRAKE SHIELD ASSY.<br />
(a) Position parking brake shield, then press it on dashboard<br />
into place.<br />
36. INSTALL CENTRE LOWER PANEL ASSY.<br />
(a) Position centre lower panel assy, then tighten 5 mounting<br />
screws on both and top side.<br />
37. INSTALL ENGINE HOOD AND FUEL FILLER DOOR<br />
(a) Install engine hood and fuel filler door handle into place.<br />
(b) Pull engine hood and fuel filler door handle to confirm it is<br />
working properly.<br />
38. INSTALL BOTH A-PILLAR HANDLES AND A PILLAR UPPER GUARD BOARDS. (Refer to<br />
39. REMOVE COMBINATION SWITCH ASSY. (Refer to “Chapter 51 steering column - combination<br />
40. REMOVE STEERING WHEEL ASSY. (Refer to “Chapter 51 steering column - steering wheel assy,<br />
41. REMOVE STEERING COLUMN LOWER COVER. (Refer to “Chapter 51 steering column - steering<br />
column assy, overhaul”)<br />
42. CONNECT BATTERY NEGATIVE CABEL.<br />
83-14 INSTRUMENT PANEL - DASHBOARD<br />
43. CHECK AFTER INSTALLATION.<br />
(a) Check electrical switches on instrument panel are functional and combination switch works normally.<br />
83-15<br />
MIDDLE PLATFORM<br />
1. REMOVE MIDDLE PLATFORM ASSY.<br />
(a) Open centre glove box lid, remove rubber pad NO.1, and<br />
then remove 2 internal retaining bolts.<br />
(b) Remove cup holder rubber pad and then remove 2<br />
internal retaining bolts.<br />
(c) Remove centre glove box rubber pad NO.2 and then<br />
remove 2 interal retaining bolts.<br />
(d) Remove middle platform assy.<br />
2. INSTALL MIDDLE PLATFORM ASSY.<br />
(a) Position the middle platform assy properly.<br />
(b) Tighten all bolts inside glove box and cup holder.<br />
(c) Cover glove box and cup holder rubber pads.<br />
(d) Close glove box lid.<br />
SEATS<br />
SEATS................................................................................................ 84-1<br />
PRECAUTION.............................................................................. 84-1<br />
DRIVER / ASSISTANT DRIVER SEAT.............................................. 84-2<br />
COMPONENTS ........................................................................... 84-2<br />
ADJUSTMENT............................................................................. 84-3<br />
REMOVAL & INSTALLATION AND<br />
DISASSEMBLY & ASSEMLBY.................................................... 84-7<br />
PASSENGER SEAT......................................................................... 84-15<br />
REPLACEMENT ........................................................................ 84-15<br />
PASSENGER SEAT......................................................................... 84-20<br />
COMPONENTS ......................................................................... 84-20<br />
84<br />
SEAT - SEAT<br />
84-1<br />
• Never adjust the seat when vehicle is moving.<br />
• After adjusting the seat position fore-and-aft, be sure to attempt to slide the seat with track<br />
handle released and make sure the seat is locked completely.<br />
• After adjusting the angle of backrest, be sure to attempt to recline the backrest backward and<br />
make sure the backrest is locked completely.<br />
• Never move the vehicle before all pasengers sitting down properly.<br />
• When vehicle is moving, make sure the backrest is locked completely. Be sure to wear seat belt<br />
correctly and lean the backrest. Never sit on a folding seat or in the trunk.<br />
• Do not stand and ambulate when vehicle is moving.<br />
• Never place objects under the seat. Otherwise it will affect the performance of seat adjuster,<br />
even cause the seat slide unexpectedly.<br />
84-2<br />
SEAT - DRIVER / ASSISTANT DRIVER SEAT<br />
DRIVER / ASSISTANT DRIVER SEAT<br />
1 Driver Seat Assy 2 Assistant Driver Seat Assy<br />
84-3<br />
1. PRECAUTION. (Refer to “Chapter 84 seat - seat, precaution”)<br />
2. PRECAUTION ON DRIVER SEAT ADJUSTMENT.<br />
Slide the driver seat backward as much as possible on the premise that the driver can push the pedal<br />
comfortably.<br />
If necessary, adjust the angle of driver seat backrest to keep the distance between steering wheel and<br />
your chest above 250 mm.<br />
Adjust the steering wheel towards your chest, instead of the head or neck. (Refer to “Chapter 51<br />
steering column - steering wheel assy, adjustment”)<br />
3. ADJUST HEADREST HEIGHT.<br />
(a) Press the lock button and hold it.<br />
Move the headrest up or down to the comfortable position.<br />
Release the lock button.<br />
84-4<br />
Attempt to move the headrest up and down to make sure<br />
the headrest is locked completely.<br />
If hear a “click”, the headrest is locked completely.<br />
4. ADJUST FORE AND AFTER POSITION.<br />
Pull the handle up and hold it.<br />
Slide the seat forward or rearward to the comfortable position.<br />
Release the handle.<br />
Attempt to slide the seat forward and rearward to make<br />
sure the seat is locked completely.<br />
If hear a “click”, the seat is locked completely.<br />
84-5<br />
5. ADJUST BACKREST RECLINING.<br />
(a) Pull the reclining adjuster handle up.<br />
Recline the backrest forward or rearward to the comfortable<br />
84-6<br />
Release the reclining adjuster handle.<br />
Attempt to recline the backrest forward and rearward to<br />
The backrest can not be moved if it locked completely.<br />
84-7<br />
REMOVAL & INSTALLATION AND DISASSEMBLY & ASSEMLBY<br />
1. DISCONNECT BATTERY NEGATIVE CABLE. (Refer to “Chapter 20 starting and charging- battery,<br />
2. REMOVE DRIVER SEAT ASSY.<br />
(a) Slide the driver seat assy to the back end.<br />
Loosen the 2 bolts.<br />
Slide the driver seat assy to the front end.<br />
• Turn over the driver seat assy backward carefully and<br />
• Do not drag the electric lock catch wire harness.<br />
• Do not move the tracks to prevent malposition.<br />
84-8<br />
Disconnect the electric lock catch wire harness connector.<br />
Using a screwdriver, pry the electric lock catch wire harness<br />
connector from the driver seat.<br />
If the connector is broken, replace the electric lock catch<br />
assy. (Refer to “Chapter 63 seat belt - lock catch assy,<br />
Remove the driver seat assy.<br />
3. REMOVE ASSISTANT DRIVER SEAT ASSY.<br />
Care must be taken because the seat assy is quite heavy.<br />
• Do not score the surfaces of parts around.<br />
• Do not move the tracks when storing to prevent malposition.<br />
• Remove the assistant driver seat assy by the same procedures as the driver seat assy.<br />
• Skip step (e) and (f).<br />
4. DISASSEMBLE DRIVER SEAT ASSY.<br />
(a) Pull out the reclining adjuster handle cover.<br />
84-9<br />
Loosen the screw.<br />
Remove the reclining adjuster trim cover handle side by<br />
the sequence shown in the illustration.<br />
• Move the trim cover backward first.<br />
• Then pull the trim cover outward.<br />
• Move forward and remove the trim cover.<br />
• Then pull outward and remove the trim cover.<br />
84-10<br />
Loosen the bolt attaching the electric lock catch to the<br />
driver seat reclining adjuster.<br />
hole between cushion pad and reclining adjuster.<br />
Be careful not to damage the electric lock catch wire harness<br />
Turn the clips.<br />
(j) Turn the cushion pad, remove the clips.<br />
(k) Remove the cushion pad.<br />
Replace the clips with a new one.<br />
Loosen 4 retaining screws.<br />
Remove the driver seat bottom plate.<br />
84-11<br />
Loosen 4 retaining bolts.<br />
Remove the rail block.<br />
5. DISASSEMBLE THE ASSISTANT DRIVER SEAT ASSY.<br />
• Disassemble the assistant driver seat assy by the same procedures as the driver seat assy.<br />
• Step (g), remove lock catch assy.<br />
• Skip step (h).<br />
6. ASSEMBLE DRIVER SEAT ASSY.<br />
(a) Position the rail block.<br />
(b) Tighten 4 retaining bolts.<br />
Install driver seat bottom plate.<br />
Position the cushion pad properly.<br />
Install clips.<br />
84-12<br />
Put the electric lock catch wire harness connector through the<br />
Install the electric lock catch side reclining adjuster trim<br />
cover and screw.<br />
side by the sequence shown in the illustration.<br />
84-13<br />
Install the reclining adjuster handle cover.<br />
7. ASSEMBLE ASSISTANT DRIVER SEAT ASSY.<br />
• Assemble the assistant driver seat assy by the same procedures as the driver seat assy.<br />
• Position the lock catch assy properly in step (k).<br />
• Skip step (j).<br />
8. INSTALL DRIVER SEAT ASSY.<br />
(a) Position the driver seat assy.<br />
Care must be taken because the driver seat assy is quite heavy.<br />
Install the electric lock catch wire harness connector to<br />
mounting hole on the driver seat.<br />
Connect the electric lock catch wire harness connector.<br />
• Do not score surfaces of parts around<br />
If the connector is broken, replace with a new one. (Refer to<br />
“Chapter 63 seat belt - lock catch assy, replacement”)<br />
84-14<br />
Tighten 2 bolts.<br />
• Make sure the driver seat assy is at the back end.<br />
• Move the seat assy carefully and slowly then position it on<br />
the top of the base welding assy.<br />
• Do not move the sliding tracks to prevent malposition.<br />
9. INSTALL ASSISTANT DRIVER SEAT ASSY.<br />
• Install the assistant driver seat assy by the same procedures as the driver seat assy.<br />
• Skip step (b) and (c).<br />
10. CONNECT BATTERY NEGATIVE CABLE. (Refer to “Chapter 20 starting and charging - battery,<br />
11. ADJUST DRIVER / ASSISTANT DRIVER SEAT ASSY. (Refer to “Chapter 84 seat- driver / assistant<br />
driver seat, adjustment”)<br />
SEAT - PASSENGER SEAT<br />
84-15<br />
PASSENGER SEAT<br />
1. REMOVE PASSENGER SEAT ASSY.<br />
(a) Loosen 4 seat trim cover clips.<br />
(b) Remove the side trim cover.<br />
Remove 4 retaining bolts and 2 nuts.<br />
Remove passenger seat assy LH.<br />
• Do not lost screw washer.<br />
• Care must be taken because the seat assy is quite<br />
heavy.<br />
2. REMOVE THE THIRD/FOURTH/FIFTH ROW PASSENGER SEAT ASSY LH.<br />
Remove the third/fourth/fifth row passenger seat assy by the same procedures as the second row passenger<br />
seat assy.<br />
3. REMOVE THE PASSENGER SEAT ASSY RH.<br />
(a) Loosen 4 seat trim cover clasps.<br />
(b) Remove the seat trim cover.<br />
Remove 3 retaining bolts and 1 nut.<br />
Remove passenger seat assy RH.<br />
84-16<br />
4. REMOVE THE THIRD/FOURTH/FIFTH ROW PASSENGER SEAT ASSY RH.<br />
5. DISASSEMBLE THE PASSENGER SEAT ASSY RH.<br />
(a) Pry up the clasp from the each side of the seat.<br />
Pry up the clasp from the right side first, otherwise the seat<br />
will be damaged.<br />
(b) Remove the cushion.<br />
Remove reclining adjuster.<br />
Remove reclining coil spring device.<br />
Loosen 2 handle retaining screws.<br />
Remove the handle.<br />
Remove the seat rear trim cover.<br />
84-17<br />
Press the lock button and remove the headrest.<br />
Make the zipper open.<br />
Remove the backrest.<br />
6. ASSEMBLE THE PASSENGER SEAT ASSY RH.<br />
(a) Position the seat backrest.<br />
(b) Make the zipper close.<br />
Install the headrest.<br />
Position the seat rear trim cover.<br />
Tighten 2 handle retaining screws.<br />
Install the handle.<br />
84-18<br />
Tighten 4 retaining bolts.<br />
Install reclining coil spring device.<br />
Install reclining adjuster.<br />
Position the cushion.<br />
Install seat retaining clips.<br />
Install passenger seat assy RH.<br />
7. DISASSEMBLE THE PASSENGER SEAT ASSY LH.<br />
Disassemble the passenger seat assy LH by the same procedures as the passenger seat assy RH.<br />
8. INSTALL PASSENGER SEAT ASSY LH.<br />
Tighten 4 retaining bolts and 2 nuts.<br />
84-19<br />
Position the seat trim cover.<br />
Install 4 seat trim cover retaining clips.<br />
9. INSTALL THE THIRD/FOURTH/FIFTH ROW PASSENGER SEAT ASSY LH.<br />
Install the third/fourth/fifth row passenger seat assy LH by the same procedures as the second row<br />
passenger seat assy LH.<br />
10. INSTALL PASSENGER SEAT ASSY LH.<br />
(a) Tighten 3 retaining bolts and 1 nuts.<br />
Install the seat trim cover.<br />
11. INSTALL THE THIRD/FOURTH/FIFTH ROW PASSENGER SEAT ASSY RH<br />
Install the third/fourth/fifth row passenger seat assy RH by the same procedures as the second row<br />
passenger seat assy RH.<br />
84-20<br />
PASSEBGER SEAT LH<br />
1 Seat Assy<br />
3 Clips<br />
2 Seat Trim Cover<br />
84-21<br />
84-22<br />
PASSEBGER SEAT RH<br />
1 Seat Assy1 2 Seat Assy2<br />
84-23<br />
2 Clips<br />
3 Seat trim Cover<br />
FRONT DOOR LOCKS ...................................................................... 85-1<br />
COMPONENTS ........................................................................... 85-1<br />
REPLACEMENT .......................................................................... 85-2<br />
SLIDING DOOR LOCKS.................................................................... 85-7<br />
COMPONENTS ........................................................................... 85-7<br />
REPLACEMENT .......................................................................... 85-8<br />
REAR HATCH LOCK....................................................................... 85-12<br />
COMPONENTS ......................................................................... 85-12<br />
REPLACEMENT ........................................................................ 85-13<br />
ENGINE HOOD LOCK ..................................................................... 85-17<br />
COMPONENTS ......................................................................... 85-17<br />
REPLACEMENT ........................................................................ 85-18<br />
ALARM CONTROLLER................................................................... 85-19<br />
REPLACEMENT ........................................................................ 85-19<br />
85<br />
FRONT DOOR LOCKS<br />
DOOR LOCKS - FRONT DOOR LOCKS<br />
85-1<br />
1 Outside Handle Assy<br />
2 Lock Catch Assy<br />
3 Inner Handle Assy<br />
4 Lock Block<br />
85-2<br />
• When disconnecting or connecting the battery cable, first turn off the ignition switch and<br />
lighting switch and completely loosen the cable nut. Do not pry up the cable when peforming<br />
these operation.<br />
• For the vehicle equipped with the power door locks, before disconnecting the battery negative<br />
cable, do not leave the key in the vehicle to avoid the door being locked.<br />
3. REMOVE FRONT DOOR CONTROLLER COVER LH.<br />
(a) Remove 2 retaining screws of the front door conreoller<br />
(b) Using a screwdriver, pry up the front door controller cover.<br />
Disconnect 2 connectors.<br />
4. REMOVE FRONT DOOR LOCK INNER HANDLE ASSY LH.<br />
(a) Remove 1 retaining screw.<br />
85-3<br />
5. REMOVE FRONT DOOR INNER GUARD PLATE ASSY<br />
Using a screwdriver, pry out the front door inner triangle<br />
Using a screwdriver, pry out the front door inner guard<br />
plate assy LH.<br />
6. REMOVE FRONT DOOR LOCK LH.<br />
7. REMOVE FRONT POWER WINDOW LIFT LH. (Refer to “Chapter 82 windshied/window glass/<br />
outside mirror , replacement”)<br />
8. REMOVE FRONT DOOR LOCK LH.<br />
(a) Disconnect the front door lock actuator LH connector.<br />
Remove retaining screws cover from the front door outer<br />
handle LH.<br />
85-4<br />
Remove retaining screws from the front door outer<br />
handle LH<br />
Remove front door outer handle carefully.<br />
Remove 1 retaining screw front door lock body LH<br />
Remove front door lock cylinder.<br />
Disconnect the front door lock connecting rods from the<br />
front door lock body LH.<br />
Do not damage the connecting rods plastic clamp.<br />
Remove 3 retaining screws from the front door actuator<br />
Remove the front door actuator LH.<br />
9. INSTALL FRONT DOOR LOCK LH.<br />
(a) Install front power window lift LH. (Refer to “Chapter 82<br />
windshied/window glass/outside mirror , replacement”)<br />
(b) Position the front door lock actuator properly.<br />
(c) Tighten 3 front door actuator LH retaining screws.<br />
Install front door outer handle assy.<br />
Connect the front door lock connecting rods from the<br />
85-5<br />
Connect the front door lock actuator LH connectors.<br />
10. INSTALL FRONT DOOR INNER GUARD PLATE ASSY<br />
Slap it by hand until all clips lock into position.<br />
Always use the new clips when installing the guard plate.<br />
Position the front door inner triangle plate LH properly<br />
and slap it by hand until all clips lock into position.<br />
11. INSTALL FRONT DOOR LOCK INNER HANDLE ASSY<br />
Install 1 retaining screw.<br />
12. INSTALL FRONT DOOR CONTROLLER COVER LH.<br />
(a) Connect 2 connectors.<br />
85-6<br />
14. INSPECT FRONT DOOR LOCK.<br />
• For the vehicle equipped with the power door locks, when inspecting front door LH lock and<br />
unlock, both the slidind door and the front door RH should be activated simultaneously.<br />
SLIDING DOOR LOCKS<br />
DOOR LOCKS - SLIDING DOOR LOCKS<br />
85-7<br />
1 Screw<br />
Sliding Door Electric Control Concave<br />
Limiting Device<br />
3 Lower Damping Block<br />
4 Sliding Door Welding Assy<br />
5 Sliding Door Concave Limiting Device<br />
6 Sliding Door Convex Limiting Device<br />
7 Sliding Door Glass Assy<br />
8 Sliding Door Lock Assy<br />
9 Sliding Door Lower Guard Board<br />
10 Sliding Door Middle Guard Board<br />
11 Sliding Door Upper Guard Board<br />
Sliding Door Electric Control Convex<br />
85-8<br />
For the vehicle equipped with the power door locks, before disconnecting the battery negative cable,<br />
do not leave the key in the vehicle to avoid the door being locked.<br />
3. REMOVE SLIDING DOOR LOWER GUARD BOARD ASSY<br />
Remove 2 sliding door inner handle retaining screws.<br />
Remove the sliding door lower guard board assy.<br />
Remove the water-proof film.<br />
Disconnect the sliding door inner handle connecting rod.<br />
Loosen the sliding door inner handle screws.<br />
Remove sliding door inner handle.<br />
85-9<br />
4. REMOVE SLIDING DOOR LOCK ACTUATOR.<br />
(a) Disconnect the sliding door lock actuator connector.<br />
Disconnect the connecting rods from the sliding door<br />
lock actuator.<br />
Remove 5 retaining bolts from the sliding door lock<br />
actuator.<br />
Remove the sliding door lock actuator.<br />
5. REMOVE SLIDING DOOR LOCK ASSY.<br />
(a) Disconnect the sliding door lock connecting rods.<br />
Loosen 3 retaining screws from the sliding door lock.<br />
Remove the sliding door lock.<br />
85-10<br />
6. INSTALL SLIDING DOOR LOCK.<br />
(a) Position the sliding door lock properly.<br />
(b) Tighten 3 sliding door lock retaining screws.<br />
(c) Connect the connecting rods to the sliding door.<br />
7. INSTALL SLIDING DOOR LOCK ACTUATOR.<br />
(a) Position the sliding door lock actuator properly.<br />
(b) Tighten 5 sliding door lock actuator retaining bolts.<br />
Connect the sliding door lock actuator connector.<br />
Connect the connecting rods to the sliding door lock actuator.<br />
(e) Connect the connecting rod to the sliding door inner handle .<br />
Install the sliding door inner handle.<br />
85-11<br />
8. INSTALL SLIDING DOOR GUARD BOARD ASSY.<br />
Install the water-proof film.<br />
Install sliding door lower guard board assy.<br />
Tighten the sliding door inner handle screws.<br />
10. INSPECT SLIDING DOOR LOCK/UNLOCK WITH KEY.<br />
85-12<br />
REAR HATCH LOCK<br />
DOOR LOCKS - REAR HATCH LOCK<br />
1 Rear Hatch License Plate Lamp Shield<br />
2 Rear Hatch Upper Gaurd Board<br />
4 Rear Hatch Lock Catch<br />
5 Rear Hatch Lower Gaurd Board<br />
3 Rear Hatch Lock<br />
85-13<br />
2. REMOVE REAR HATCH LOCK ASSY.<br />
(a) Remove 3 rear hatch lock retaining screw.<br />
(b) Remove rear hatch lock assy.<br />
3. REMOVE REAR HATCH LOWER GUARD BOARD ASSY.<br />
(a) Remove rear hatch inner handle retaining screw.<br />
Remove rear hatch lower guard board.<br />
4. REMOVE REAR HATCH LOCK ACTUATOR ASSY.<br />
(a) Disconnect the rear hatch lock actuator connector.<br />
85-14<br />
Disconnect the rear hatch lock actuator connecting rods.<br />
Loosen the rear hatch lock actuator 3 retaining bolts.<br />
Remove the rear hatch lock actuator.<br />
5. REMOVE REAR HATCH LOCK CYLINDER ASSY.<br />
(a) Disconnect the rear hatch lock cylinder connecting rod.<br />
(b) Loosen 2 rear hatch lock cylinder retaining bolts.<br />
(c) Remove the rear hatch lock cylinder assy.<br />
6. REMOVE REAR HATCH INNER HANDLE LOCK .<br />
(a) Disonnect the rear hatch inner handle lock connecting<br />
(b) Remove 3 rear hatch inner handle lock retaining screws.<br />
(c) Remove the rear hatch inner handle lock.<br />
7. INSTALL REAR HATCH INNER HANDLE LOCK .<br />
(a) Install 3 rear hatch inner handle lock retaining screws.<br />
(b) Connect the rear hatch inner handle lock connecting rod.<br />
85-15<br />
8. INSTALL REAR HATCH LOCK CYLINDER ASSY.<br />
(a) Position the rear hatch lock cylinder assy.<br />
(b) Install rear hatch lock cylinder connecting rod.<br />
(c) Tighten 2 rear hatch lock cylinder retaining screws.<br />
9. INSTALL REAR HATCH LOCK ACTUATOR ASSY.<br />
(a) Position the rear hatch lock actuator assy properly.<br />
(b) Tighten 3 rear hatch lock actuator retaining bolts.<br />
Connect the rear hatch lock actuator connecting rods.<br />
Connect the rear hatch lock actuator connector.<br />
10. INSTALL REAR HATCH LOWER GUARD BOARD ASSY.<br />
Install the rear hatch lower guard board.<br />
85-16<br />
Install the rear hatch lower inner handle screw.<br />
11. INSTALL REAR HATCH LOCK BLOCK.<br />
(a) Position the rear hatch lock block.<br />
(b) Tighten 3 rear hatch lock block retaining bolts.<br />
12. INSPECT REAR HATCH LOCK.<br />
ENGINE HOOD LOCK<br />
DOOR LOCKS - ENGINE HOOD LOCK<br />
85-17<br />
1 Engine Hood Buffer Block<br />
2 Engine Hood Lock Assy<br />
4 Engine Hood Support Bar<br />
5 Engine Hood Support Bar Clip<br />
3 Engine Hood Assy<br />
85-18<br />
2. REMOVE FRONT GRILLE.(Refer to “Chapter 82 exterior and interior trim front grille , replacement”)<br />
3. REMOVE ENGINE HOOD LOCK ASSY.<br />
(a) Remove 3 retaining bolts from the engine hood lock.<br />
(b) Remove the engine hood lock.<br />
Disconnect the engine hood lock cable.<br />
4. INSTALL ENGINE HOOD LOCK ASSY.<br />
(a) Connect the engine hood lock cable.<br />
Position the engine hood lock properly.<br />
Install 3 retaining bolts to the engine hood lock.<br />
5. INSTALL FRONT GRILLE.(Refer to “Chapter 82 exterior and interior trim front grille , replacement”)<br />
DOOR LOCKS - ALARM CONTROLLER<br />
85-19<br />
ALARM CONTROLLER<br />
2. REMOVE STEERING WHEEL LOWER TRIM COVER.<br />
3. REMOVE ALARM CONTROLLER ASSY.<br />
(a) Disconnect the alarm controller connector.<br />
Loosen 2 alarm controller retaining bolts.<br />
Remove alarm controller.<br />
4. INSTALL ALARM CONTROLLER ASSY.<br />
(a) Tighten 2 alarm controller retaining bolts.<br />
Connect the alarm controller connector.<br />
5. INSTALL STEERING WHEEL LOWER TRIM COVER.<br />
SLIDING ROOF ASSY ....................................................................... 86-1<br />
PROBLEM SYMPTOMS TABLE.................................................. 86-1<br />
COMPONENTS ........................................................................... 86-2<br />
OVERHAUL ................................................................................. 86-3<br />
SLIDING ROOF ASSY<br />
SLIDING ROOF - SLIDING ROOF ASSY<br />
Symptom Suspect Reference<br />
86-1<br />
1. Sliding rail (Insufficient lubrication) Chapter 86 sliding roof - sliding roof assy, overhaul<br />
Abnormal<br />
working<br />
2. Sliding rail (Dusty) Chapter 86 sliding roof - sliding roof assy, overhaul<br />
3. Sliding roof control switch (Failure) Chapter 86 sliding roof - sliding roof assy, overhaul<br />
Sliding roof<br />
assy leakage<br />
4. Sliding roof control switch (Damage) Chapter 86 sliding roof - sliding roof assy, overhaul<br />
1. Sliding roof weatherstrip (Aging) Chapter 86 sliding roof - sliding roof assy, overhaul<br />
2. Sliding roof weatherstrip (Improper<br />
installation)<br />
Chapter 86 sliding roof - sliding roof assy, overhaul<br />
3. Sliding roof assy (Improper installation) Chapter 86 sliding roof - sliding roof assy, overhaul<br />
4. Sliding roof assy (Maladjusted) Chapter 86 sliding roof - sliding roof assy, overhaul<br />
86-2<br />
1 Front Sliding Roof<br />
2 Front Ceiling Insulation Felt<br />
4 Front Sliding Roof Switch Panel<br />
5 Front Sliding Roof Switch<br />
3 Front Ceiling Trim Cover<br />
86-3<br />
2. REMOVE SLIDING ROOF CONTROL SWITCH.<br />
(a) Remove the sliding roof control switch carefully.<br />
Be careful, do not damage the interior.<br />
Disconnect the connector and remove the sliding roof<br />
control switch.<br />
3. REMOVE SLIDING ROOF WEATHERSTRIP.<br />
Remove the sliding roof weatherstrip slowly.<br />
4. REMOVE ROOF GUARD BOARD. (Refer to "Chapter 88 exterior and interior trim - roof guard<br />
board, replacement")<br />
5. REMOVE SLIDING ROOF CONTROL MOTOR.<br />
(a) Disconnect the connector of the sliding roof control<br />
motor.<br />
86-4<br />
Remove 2 bolts and sliding roof control motor.<br />
6. REMOVE SLIDING ROOF CONTROLLER.<br />
(a) Disconnect the connector of the sliding roof controller.<br />
Loosen 2 controller retaining screws.<br />
Remove the sliding roof controller.<br />
7. REMOVE THE SLIDING ROOF ASSY.<br />
(a) Loosen 4 sliding roof visor retaining screws.<br />
(b) Remove sliding roof visor assy.<br />
r<br />
Loosen 12 sliding roof retaining cover retaining screws.<br />
86-5<br />
Raise the sliding roof glass and guide assy gently.<br />
Rotation and remove the sliding roof assy.<br />
8. INSPECT SLIDING RAIL. CLEAN UP AND LUBRICATE THE SLIDING ROOF RAIL IF NECESSARY.<br />
9. INSPECT SLIDING ROOF CONTROL MOTOR.<br />
(a) Check the sliding roof control motor operates smoothly. If it isn’t operating smoothly, replace the sliding<br />
roof control motor with a new part.<br />
10. INSPECT SLIDING ROOF CONTROL SWITCH.<br />
(a) Gently press the ”open” then release the button, the sliding roof should be completely opened.<br />
(b) Gently press the ”close” then release the button, the sliding roof should be completely closed.<br />
(c) Press and hold down the ”open” then the sliding roof will operate untill you release the button.<br />
(d) Press and hold down the ”close” then the sliding roof will operate untill you release the button.<br />
11. INSTALL SLIDING ROOF ASSY.<br />
(a) Position the sliding roof assy.<br />
(b) Install the sliding roof retaining cover.<br />
(c) Tighten 12 sliding roof retaining cover retaining screws.<br />
Torque:9 ~ 11 N·m<br />
(d) Position the sliding roof visor.<br />
(e) Tighten the sliding roof visor retaining screws.<br />
86-6<br />
12. INSTALL SLIDING ROOF CONTROL MOTOR.<br />
(a) Install the sliding roof control motor and tighten 2 bolts.<br />
Install the connector of the sliding roof control motor.<br />
13. INSTALL SLIDING ROOF CONTROLLER.<br />
(a) Tighten 2 controller retaining screws.<br />
Connect the connector of the sliding roof controller.<br />
14. INSTALL ROOF GUARD BOARD. (Refer to "Chapter 88 exterior and interior trim - roof guard<br />
86-7<br />
15. INSTALL THE SLIDING ROOF WEATHERSTRIP.<br />
The weatherstrip has a direct influence on the body sealing<br />
performance. Inspect the weatherstrip from aging, cracking<br />
and damage before installing them. Replace with new<br />
weatherstrip if necessary.<br />
16. INSTALL THE SLIDING ROOF CONTROL SWITCH.<br />
(a) Connect the connector and install the sliding roof control<br />
18. INSPECT WHETHER SLIDING ROOF CONTROL MOTOR OPERATES SMOOTHLY OR NOT.<br />
19. INSPECT WHETHER SLIDNG ROOF ASSY IS INSTALLED PROPERLY OR NOT.<br />
20. INSPECT FOR LEAKAGE.<br />
(a) Inspect the sliding roof for leakage after operating the sliding roof many times. Readjust the position of<br />
the sliding roof assy if necessary. (Refer to “Chapter 86 sliding roof - sliding roof system, overhaul”)<br />
DOORS & ENGINE HOOD<br />
ENGINE HOOD .................................................................................. 87-1<br />
ADJUSTMENT............................................................................. 87-1<br />
REPLACEMENT .......................................................................... 87-3<br />
FRONT DOOR.................................................................................... 87-4<br />
COMPONENTS ........................................................................... 87-4<br />
ADJUSTMENT............................................................................. 87-5<br />
REPLANCEMENT........................................................................ 87-7<br />
SLIDING DOOR.................................................................................. 87-9<br />
COMPONENTS ........................................................................... 87-9<br />
ADJUSTMENT........................................................................... 87-10<br />
REPLACEMENT ........................................................................ 87-13<br />
REAR HATCH .................................................................................. 87-15<br />
COMPONENTS ......................................................................... 87-15<br />
ADJUSTMENT........................................................................... 87-16<br />
REPLACEMENT ........................................................................ 87-18<br />
DOORS - ENGINE HOOD<br />
87-1<br />
ENGINE HOOD<br />
1. INSPECT HOOD.<br />
(a) Check that the clearance is within the specified value.<br />
Hood -Fender Clearance<br />
Hood-Headlamp Clearance<br />
4.0 mm<br />
4.5 mm<br />
2. ADJUST HOOD.<br />
(a) Asjust the engine hood horizontally.<br />
• Loosen the hood side hinge bolts.<br />
• Move the hood to adjust the clearance within the specified<br />
Specified Value: 4.0 mm<br />
• After adjusting, tighten the hood side hinge bolts.<br />
Torque: 28 ~ 32 N·m<br />
87-2<br />
Adjust the hood by turning the rubber damper.<br />
• Adjust the rubber damper so as to align the hood<br />
with the fender.<br />
Turn the rubber to let it move up and down.<br />
87-3<br />
1. REMOVE ENGINE HOOD.<br />
Remove 2 retaining bolts from the engine hood hinge LH.<br />
Remove 2 retaining bolts from the engine hood hinge<br />
Remove engine hood.<br />
Be careful, the engine hood is too heavy, pay attention to<br />
prevent contact with the windshield lift under.<br />
2. INSTALL ENGINE HOOD.<br />
(a) Tighten 2 retaining bolts to the engine hood hinge LH.<br />
Torque: 28 ~ 32 N·m.<br />
Tighten 2 retaining bolts to the engine hood hinge RH.<br />
3. ADJUST ENGINE HOOD.(Refer to “Chapter 87 engine hood and doors - engine hood, adjustment”)<br />
87-4<br />
DOORS - FRONT DOOR<br />
1 Front Door Glass Assy LH<br />
2 Front Door Adjustment Assy<br />
10 Front Door Power Lift Assy<br />
11 Front Door Glass Sealing Strip LH<br />
3 Front Door Glass Guide Slot Assy LH<br />
4 Front Door Sealing Strip LH<br />
5 Front Door Cylinder Assy<br />
6 Front Door Inner Triangle Plate LH<br />
7 Left Fender Plug Strip Assy<br />
8 Front Door Glass Inner Weather Bar LH<br />
12 Maintenance Panel II<br />
13 Front Door Controller Cover LH<br />
14 Front Door Inner Guard Board LH<br />
15 Screw<br />
16 Screw<br />
17 Front Door Lock Assy LH<br />
9 Front Door Glass Outer Weather Bar LH<br />
87-5<br />
Adjust the RH side by the same procedures as the LH side<br />
1. INSPECT FRONT DOOR LH.<br />
Front Door- Fender<br />
Front Door- Quarter Panel<br />
5.5mm<br />
5.0mm<br />
2. ADJUST FRONT DOOR LH.<br />
(a) Adjust the door vertically and horizontally by loosening<br />
the body side hinge bolts.<br />
(b) After adjusting, tighten the body hinge bolts.<br />
87-6<br />
Adjust the striker position by slightly loosening the striker<br />
mounting screws .<br />
After adjusting, tighten the striker mounting screws.<br />
87-7<br />
REPLANCEMENT<br />
1. REMOVE THE FRONT BUMPER.(Refer to“Chapter 88 interior and exterior trim- front bumper,<br />
replacement)<br />
2. REMOVE FRONT DOOR ASSY.<br />
Disconnect front door connector from the front bumper<br />
Remove retaining bolts from the front door limiting device<br />
Remove 4 retaining bolts from the front door hinge LH.<br />
Remove the front door assy.<br />
Use new parts when installing.<br />
3. REMOVE FRONT DOOR HINGE RH.<br />
4. INSTALL FRONT DOOR HINGE LH.<br />
(a) Position the front door LH properly. After adjusting the<br />
front door clearance, tighten 4 retaining bolts to the front<br />
door hinge LH.<br />
87-8<br />
Install front door limiting device LH.<br />
Connect front door connector from front bumper bracket.<br />
5. ADJUST FRONT DOOR LH.(Refer to “Chapter 87 engine hood and doors - front door, adjustment”)<br />
6. INSTALL THE FRONT BUMPER.(Refer to“Chapter 88 interior and exterior trim- front bumper,<br />
7. CONNECT THE BATTERY NEGATIVE CABLE.<br />
8. INSTALL THE RRONT DOOR RH.<br />
DOORS - SLIDING DOOR<br />
87-9<br />
1 Sliding Door Upper Inner Guard Board RH<br />
Sliding Door Middle Inner Guard Board<br />
3 Sliding Door Glass Assy RH<br />
4 Sliding Door Slide Weatherstrip RH<br />
5 Sliding Door Slide Cover<br />
6 Sliding Door Glass Weatherstrip RH<br />
7 Sliding Door Weatherstrip<br />
8 Sliding Door Waterproof<br />
10 Screw<br />
Sliding Door Lower Slideway Bracket<br />
Assy RH<br />
11 Sliding Door Lock Assy RH<br />
12 Sliding Door Lower Inner Guard Board<br />
87-10<br />
1. INSPECT SLIDING DOOR.<br />
Front Of Sliding Door<br />
Rear Of Sliding Door<br />
87-11<br />
Upper Of Sliding Door<br />
Lower Of Sliding Door<br />
2. ADJUST SLIDING DOOR.<br />
(a) Loosen the sliding door upper bracket nut.<br />
(b) Adjust the sliding door position.<br />
Loosen the sliding door lower bracket bolts.<br />
Adjust the door vertically.<br />
After adjusting, tighten the sliding door bracket bolts.<br />
6.5 ~ 8.5 N·m(small bolts)<br />
87-12<br />
Adjust the middle convex limiting device by slightly loosening<br />
the middle convex limiting device mounting screws<br />
and hitting the middle convex limiting device with a plastic<br />
Adjust the lock catch by slightly loosening the lock catch<br />
mounting bolts and hitting the lock catch with a plastic<br />
Adjust the middle concave limiting device by slightly<br />
loosening the middle concave limiting device mounting<br />
bolts and hitting the middle concave limiting device with a<br />
After adjusting, tighten those bolts and screws.<br />
87-13<br />
1. REMOVE SLIDING DOOR RH.<br />
(a) Remove 3 mounting bolts from the sliding door lower<br />
Remove 2 mounting bolts from the sliding door middle<br />
Remove 2 mounting nut from the sliding door upper<br />
Slid out the sliding door.<br />
Remove the sliding door.<br />
2. INSTALL SLIDING DOOR RH.<br />
(a) Tighten mounting nut to upper bracket.<br />
87-14<br />
Install 2 mounting bolts from the sliding door middle<br />
Install 3 mounting bolts from the sliding door lower<br />
3. ADJUST SLIDING DOOR RH. (Refer to “Chapter 87 engine hood and doors - sliding door,<br />
DOORS - REAR HATCH<br />
87-15<br />
1 License Plate Lamp Shield<br />
7 Nut<br />
2 Rear Hatch Upper Guard Board Assy<br />
3 Gas Prop Assy LH<br />
4 Clip<br />
5 Gas Prop Assy RH<br />
6 Gas Prop Adjustment Assembly<br />
8 Rear Window Glass Assy<br />
9 Rear Hatch Sealing Strip<br />
10 Rear Hatch lower Guard Board Assy<br />
11 Rear Hatch Waterproof Film<br />
12 Rear Hatch Lock Assy<br />
87-16<br />
1. INSPECT REAR HATCH..<br />
Check that the clearance is within the specified value.<br />
Rear Hatch - Quarter Panel<br />
Rear Hatch - Rear Bumper<br />
87-17<br />
2. ADJUST REAR HATCH.<br />
(a) Adjust the lock catch and limiting device by slightly<br />
loosening the lock catch and limiting device mounting<br />
(b) After adjusting, tighten the lock catch mounting bolts<br />
Loosen the rear hatch hinge mounting bolts to adjust the<br />
rear hatch position.<br />
After adjusting, tighten the rear hatch hinge mounting<br />
87-18<br />
1. REMOVE ROOF PANEL ASSY. (Refer to “Chapter 8 Interior and Exterior - Roof panel assy,<br />
2. REMOVE GAS PROP ASSY RH.<br />
Disconnect the rear washer hose and the connector.<br />
Remove 2 upper mounting bolts from the gas prop assy<br />
Remove 2 lower mounting bolts from the gas prop assy<br />
Remove gas prop.<br />
• Do not disassemble it or throw it into fire.<br />
• Using a drill, make a hole in the gas prop to<br />
discharge the gas inside.<br />
3. REMOVE GAS PROP LH.<br />
Remove the LH side by the same procedures as the RH side.<br />
4. REMOVE REAR HATCH HINGE.<br />
(a) Hold the rear hatch and remove rear hatch hinge<br />
mounting bolts LH.<br />
Remove rear hatch hinge mounting bolts RH.<br />
Remove rear hatch.<br />
87-19<br />
5. INSTALL REAR HATCH.<br />
(a) Tighten 4 rear hatch hinge mounting bolts.<br />
Position the gas prop properly and tighten the snap ring.<br />
Connect the rear hatch connector.<br />
Connect the rear washer hose.<br />
6. INSTALL ROOF PANEL ASSY. (Refer to “Chapter 8 Interior and Exterior - Roof panel assy,<br />
7. ADJUST REAR HATCH. (Refer to “Chapter 87 engine hood and doors - rear hatch, adjustment”)<br />
FRONT GRILLE ................................................................................. 88-1<br />
COMPONENTS ........................................................................... 88-1<br />
REPLACEMENT .......................................................................... 88-2<br />
FRONT BUMPER ASSY .................................................................... 88-3<br />
COMPONENTS ........................................................................... 88-3<br />
REPLACEMENT .......................................................................... 88-4<br />
WHEEL MUDGUARD......................................................................... 88-7<br />
REPLACEMENT .......................................................................... 88-7<br />
REAR BUMPER ASSY .................................................................... 88-10<br />
COMPONENTS ......................................................................... 88-10<br />
REPLACEMENT ........................................................................ 88-11<br />
SUN VISOR ASSY ........................................................................... 88-13<br />
COMPONENTS ......................................................................... 88-13<br />
REPLACEMENT ........................................................................ 88-14<br />
STEP BOARD .................................................................................. 88-15<br />
COMPONENTS ......................................................................... 88-15<br />
REPLACEMENT ........................................................................ 88-16<br />
VEHICLE DOOR INNER GUARD BOARD...................................... 88-18<br />
REPLACEMENT ........................................................................ 88-18<br />
QUARTER PANEL GUARD BOARD............................................... 88-23<br />
REPLACEMENT ........................................................................ 88-23<br />
FLOOR DECORATIVE PARTS........................................................ 88-27<br />
COMPONENTS ......................................................................... 88-27<br />
REPLACEMENT ........................................................................ 88-28<br />
ROOF PANEL .................................................................................. 88-31<br />
COMPONENTS ......................................................................... 88-31<br />
REPLACEMENT ........................................................................ 88-32<br />
88<br />
FRONT GRILLE<br />
EXTERIOR AND INTERIOR TRIM - FRONT GRILLE<br />
88-1<br />
1 Front Grille 2 Bolt<br />
88-2<br />
1. REMOVE FRONT GRILLE.<br />
(a) Remove 2 front grille screws.<br />
Pull out front grille, remove 9 clips.<br />
Remove front grille.<br />
2. INSTALL FRONT GRILLE.<br />
(a) Position the front grille, install 9 clips.<br />
Install 2 screws.<br />
FRONT BUMPER ASSY<br />
EXTERIOR AND INTERIOR TRIM - FRONT BUMPER ASSY<br />
88-3<br />
2 Clip<br />
3 Front Grille<br />
4 Front Bumper<br />
5 Front Bumper Support LH<br />
7 Front Bumper Support RH<br />
88-4<br />
2. REMOVE FRONT GRILLE. (Refer to “Chapter 88 exterior and interior - front grille, replacement”)<br />
3. REMOVE FRONT BUMPER ASSY.<br />
(a) Disconnect the front fog lamper connector.<br />
Remove 2 bolts from front bumper assy by upside.<br />
(c) Loosen 3 screws from front bumper assy .<br />
Remove 3 bolts from front bumper assy by downside.<br />
88-5<br />
(e) Remove the both side front step board cover .<br />
Remove the clip RH.<br />
Remove the clip LH.<br />
Remove the front bumper assy.<br />
4. INSTALL FRONT BUMPER ASSY.<br />
(i) Position the front fog lamps assy.<br />
(j) Tighten front step board cover retaining screw RH.<br />
Tighten front step board cover retaining screw LH.<br />
Tighten 3 bolts from front bumper assy by downside.<br />
88-6<br />
Tighten 3 bolts from front bumper assy by upside.<br />
Tighten 3 screws from front bumper assy.<br />
Connect the connectors to front fog lamps.<br />
5. INSTALL FRONT GRILLE. (Refer to “Chapter 88 exterior and interior trim - front grille, replacement”)<br />
EXTERIOR AND INTERIOR TRIM - WHEEL MUDGUARD<br />
88-7<br />
WHEEL MUDGUARD<br />
1. REMOVE FRONT WHEEL MUDGUARD LH.<br />
(a) Remove 3 screws and front wheel mudguard LH.<br />
2. REMOVE FRONT WHEEL MUDGUARD RH.<br />
3. REMOVE REAR WHEEL MUDGUARD LH.<br />
(a) Remove 4 screws and rear wheel mudguard LH.<br />
4. REMOVE REAR WHEEL MUDGUARD RH.<br />
5. REMOVE ENGINE MUDGUARD LH.<br />
(a) Loosen 4 clips, remove the engine mudguard LH.<br />
6. REMOVE ENGINE MUDGUARD RH.<br />
88-8<br />
7. REMOVE FRONT WHEEL FRONT MUDGUARD LH.<br />
Loosen 3 clips, remove the front wheel front mudguard<br />
8. INSTALL FRONT WHEEL FRONT MUDGUARD LH.<br />
Tighten 3 clips, install the front wheel front mudguard LH.<br />
9. INSALL ENGINE MUDGUARD LH.<br />
Tighten 4 clips, install the engine mudguard LH.<br />
10. INSTALL ENGINE MUDGUARD RH.<br />
11. INSTALL FRONT WHEEL MUDGUARD LH.<br />
Install the front wheel mudguard LH and install 3 screws.<br />
12. INSTALL FRONT WHEEL MUDGUARD RH.<br />
Intsall the RH side by the same procedures as the LH side.<br />
88-9<br />
13. INSTALL REAR WHEEL MUDGUARD LH.<br />
(a) Install the rear wheel mudguard LH and install 4 screws.<br />
14. INSTALL REAR WHEEL MUDGUARD RH.<br />
88-10<br />
REAR BUMPER ASSY<br />
EXTERIOR AND INTERIOR TRIM - REAR BUMPER ASSY<br />
1 Wheel mudguard Clip<br />
2 Wheel mudguard Clip Cover<br />
3 Clip<br />
5 Rear Bumper Support RH<br />
6 Rear Bumper Support LH<br />
7 Rear Bumper Body Assy<br />
8 Rear Bumper Support Clip<br />
9 Rear Bumper Lower Side Support<br />
88-11<br />
1. REMOVE REAR BUMPER ASSY.<br />
(a) Remove 6 bolts from rear bumper assy by upside.<br />
Remove 4 clips from rear bumper assy by downside.<br />
Pull out the rear bumper slowly.<br />
Be careful, not to damage the rear bumper.<br />
Disconnect the reverse radar connector.<br />
Remove the rear bumper assy.<br />
2. INSTALL REAR BUMPER ASSY.<br />
(a) Connect the reversing radar connector.<br />
(b) Position the rear bumper and install the clips.<br />
88-12<br />
Install 6 bolts from rear bumper assy by upside.<br />
Install 4 clips from rear bumper assy by downside.<br />
SUN VISOR ASSY<br />
EXTERIOR AND INTERIOR TRIM - SUN VISOR ASSY<br />
88-13<br />
1 Sun Visor Assy RH<br />
2 Sun Visor Assy LH<br />
88-14<br />
1. REMOVE SUN VISOR ASSY LH.<br />
(a) Remove 2 bolts from the hook.<br />
(b) Remove 2 bolts from sun visor assy.<br />
(c) Remove sun visor assy.<br />
2. REMOVE SUN VISOR ASSY RH.<br />
3. INSTALL SUN VISOR ASSY LH.<br />
(a) Position the sun visor assy, install the hook.<br />
(b) Install 2 bolts to sun visor assy.<br />
(c) Install sun visor assy.<br />
4. INSTALL SUN VISOR ASSY RH.<br />
STEP BOARD<br />
EXTERIOR AND INTERIOR TRIM - STEP BOARD<br />
88-15<br />
1 Step Board LH<br />
2 Step Board RH<br />
5 Jack Cover<br />
6 Sliding Door Step Board Assy<br />
88-16<br />
1. REMOVE FRONT STEP BOARD COVER ASSY LH.<br />
(a) Remove 2 upside clips from the step board LH.<br />
Change new clip, when installation.<br />
Remove 2 downside clips from the step board LH<br />
Remove the step board LH.<br />
2. REMOVE STEP BOARD COVER RH.<br />
3. REMOVE SLIDING DOOR STEP BOARD COVER<br />
ASSY RH.<br />
(a) Loosen 11 covers and screws.<br />
Disconnect the step lamp connector.<br />
Remove the sliding door step board cover RH.<br />
88-17<br />
4. INSTALL STEP BOARD LH.<br />
(a) Position the step board LH.<br />
(b) Install 2 upside clips to step board LH.<br />
Install 2 downside clips to step board LH.<br />
5. INSTALL FRONT STEP BOARD COVER ASSY RH.<br />
6. INSTALL SLIDING DOOR STEP BOARD COVER ASSY<br />
(a) Connect the step lamp connector<br />
(a) Position the sliding door step board cover<br />
Install 11 covers and screws.<br />
88-18<br />
EXTERIOR AND INTERIOR TRIM - VEHICLE DOOR INNER GUARD BOARD<br />
VEHICLE DOOR INNER GUARD BOARD<br />
1. REMOVE FRONT DOOR INNER GUARD PLATE ASSY<br />
Remove the clip from front door inner triangle plate LH.<br />
Remove the front door inner triangle plate LH.<br />
Loosen 2 screws to remove the front door controller<br />
cover LH.<br />
Disconnect 2 front door controller cover connectors.<br />
Remove front door controller cover.<br />
Remove the screw of front door lock inner handle assy<br />
Remove 2 door lock connecting rods, then remove front<br />
inner handle LH.<br />
88-19<br />
Disengage 13 clips, remove the front door inner guard<br />
Change new clips when installation.<br />
2. REMOVE FRONT DOOR INNER GUARD PLATE ASSY RH.<br />
3. REMOVE SLIDING DOOR UPSIDE INNER GUARD<br />
BOARD.<br />
Disengage 13 clips and remove the sliding door upside<br />
inner guard board.<br />
4. REMOVE SLIDING DOOR MIDDLE GUARD BOARD.<br />
(a) Disengage 3 clips and remove the sliding door middler<br />
5. REMOVE SLIDING DOOR DOWNSIDE INNER GUARD<br />
(a) Remove 2 sliding door lock retaining scerws.<br />
88-20<br />
Disengage 18 clips and remove the sliding door downside<br />
6. REMOVE REAR HATCH UPPER GUARD BOARD.<br />
(a) Disengage 17 clips and remove the rear hatch upper<br />
Be carful not to damage the rear hatch upper guard board.<br />
7. REMOVE REAR HATCH LOWER GUARD BOARD.<br />
(b) Remove blot of rear hatch handle, remove the rear hatch<br />
Disengage 12 clips and remove the rear hatch upper<br />
Be carful not to damage the rear hatch lower guard board.<br />
8. INSTALL FRONT DOOR INNER GUARD PLATE ASSY<br />
(a) Install the front door lock inner handle assy LH with the<br />
screw.<br />
88-21<br />
Install 2 door lock connecting rods, then install front inner<br />
Install the door lock inner handle assy LH with the screw.<br />
Connect the connector of the front door controller cover<br />
Position the front door controller cover LH.<br />
Install the front door inner triangle plate LH.<br />
9. INSTALL FRONT DOOR INNER GUARD PLATE ASSY RH.<br />
10. INSTALL SLIDING DOOR LOWER GUARD BOARD.<br />
Install the sliding door lower guard board with 13 clips.<br />
88-22<br />
11. INSTALL SLIDING DOOR MIDDLER GUARD BOARD<br />
Install the sliding door middler guard board with 3 clips.<br />
12. INSTALL SLIDING DOOR UPPER GUARD BOARD<br />
Install the sliding door upper guard board with 18 clips.<br />
13. INSTALL REAR HATCH UPPER GUARD BOARD<br />
Install the rear hatch upper guard board with 17 clips.<br />
14. INSTALL REAR HATCH LOWER GUARD BOARD<br />
(a) Install the sliding door lower guard board with 12 clips.<br />
(b) Install the rear hatch handle bolt.<br />
EXTERIOR AND INTERIOR TRIM - QUARTER PANEL GUARD BOARD<br />
QUARTER PANEL GUARD BOARD<br />
1. CONNECT BATTERY NEGATIVE CABLE.<br />
88-23<br />
2. REMOVE REAR QUARTER PANEL GUARD BOARD<br />
Remove passengers seat assy.<br />
Remove driver seat meshbelt with retractor assy.(Refer to<br />
“Chapter 63 seat belt-anchor adjuster assy, replacement”)<br />
Disengage 17 clips and remove the rear quarter panel<br />
guard board LH.<br />
3. REMOVE REAR QUARTER PANEL GUARD BOARD RH.<br />
4. REMOVE MIDDLE QUARTER PANEL GUARD BOARD<br />
Loosen the retaining screw.<br />
Remove passenger seat meshbelt with retractor assy.<br />
(Refer to “Chapter 63 seat belt -anchor adjuster assy,<br />
Disengage 6 clips and remove the middle quarter panel<br />
5. REMOVE MIDDLE QUARTER PANEL GUARD BOARD RH.<br />
6. REMOVE FRONT QUARTER PANEL GUARD BOARD<br />
7. REMOVE FRONT QUARTER PANEL GUARD BOARD RH.<br />
(a) Pull out front and sliding door sealing strip RH.<br />
(b) Loosen 2 retaining screwsm, remove B pillar handle.<br />
(c) Remove assistant driver seat belt lower bolt.<br />
(d) Disengage 17 clips and remove the front quarter panel guard board LH.<br />
Remove driver seat meshbelt with retractor assy. (Refer<br />
to “Chapter 63 seat belt -anchor adjuster assy,<br />
Remove driver seat assy.<br />
Disengage 17 clips and remove the front quarter panel<br />
Remove engine compartment cover.<br />
Remove front quarter panel guard board LH.<br />
88-24<br />
8. REMOVE B PILLAR UPPER GUARD BOARD LH.<br />
(a) Remove driver seat belt upper bolt.<br />
(b) Pull out front door sealing strip.<br />
(c) Remove the engine compartment cover support point.<br />
(d) Disengage 3 clips and remove B pillar upper guard board<br />
9. REMOVE B PILLAR UPPER GUARD BOARD RH.<br />
• Remove the RH side by the same procedures as the LH side.<br />
10. REMOVE OTHER SIDE PILLAR INNER GUARD BOARD.<br />
• Remove other side pillar inner guard board by the same procedures as the LH side.<br />
• Skip step (c)and(d).<br />
• Add step“ Remove side pillar inner guard board screw”.<br />
11. REMOVE A PILLAR UPPER GUARD BOARD LH.<br />
(a) Pull out front door sealing strip.<br />
(b) Use a screwdriver to remove the bolt covers of A pillar<br />
(c) Remove 2 bolts.<br />
Remove A pillar handle.<br />
Remove A pillar guard board.<br />
12. REMOVE A PILLAR UPPER GUARD BOARD RH.<br />
88-25<br />
13. INSTALL FRONT QUARTER PANEL GUARD BOARD<br />
Install 17 clips and install the front quarter panel guard<br />
board LH.<br />
Install driver seat belt upper bolt.<br />
Install engine compartment cover.<br />
14. INSTALL FRONT QUARTER PANEL GUARD BOARD RH.<br />
(a) Install 6 clips and install the front quarter panel guard board RH<br />
(b) Tighten 2 retaining screwsm, install B pillar handle.<br />
(c) Install front and sliding door sealing strip RH.<br />
15. INSTALL MIDDLE QUARTER PANEL GUARD BOARD<br />
Install 6 clips and install the middle quarter panel guard<br />
Install passenger seat meshbelt with retractor assy.<br />
16. INSTALL MIDDLE QUARTER PANEL GUARD BOARD RH.<br />
17. INSTALL REAR QUARTER PANEL GUARD BOARD<br />
Install 17 clips and install the rear quarter panel guard<br />
Install rear hatch sealing strip<br />
18. INSTALL REAR QUARTER PANEL GUARD BOARD RH.<br />
88-26<br />
19. INSTALL B PILLAR UPPER GUARD BOARD LH.<br />
(a) Install 3 clips and install B pillar upper guard board LH.<br />
(b) Remove the engine compartment cover support point.<br />
(c) Install upper driver seat belt retaining bolt.<br />
(d) Install rear hatch sealing strip<br />
20. INSTALL B PILLAR UPPER GUARD BOARD RH.<br />
21.<br />
• Install other side pillar inner guard board by the same procedures as the LH side.<br />
• Add step“ Tighten side pillar inner guard board screw”.<br />
22. INSTALL A PILLAR UPPER GUARD BOARD LH.<br />
(a) Install 3 clips and install A pillar upper guard board LH.<br />
Position the A pillar handle, install 2 bolts.<br />
Install the bolt covers of A pillar handle.<br />
Install the front door sealing strip.<br />
23. INSTALL A PILLAR UPPER GUARD BOARD RH.<br />
EXTERIOR AND INTERIOR TRIM - FLOOR DECORATIVE PARTS<br />
FLOOR DECORATIVE PARTS<br />
88-27<br />
1 Stop Plate<br />
2 Front Floor Covering<br />
3 Stop Plate Cover LH<br />
4 Stop Plate Cover RH<br />
5 Assisant Driver Step Board Trim Strip<br />
6 Engine Compartment Covering<br />
7 Driver Step Board Trim Strip<br />
8 Engine Compartment Cover Holder Belt<br />
9 Screw<br />
10 Air Filter Cover Switch Assy<br />
11 Screw<br />
12 Clip<br />
13 Screw<br />
15 Sliding Door Lower Trim Strip<br />
16 Sliding Door Step Board Covering<br />
17 Sliding Door Upper Trim Strip<br />
18 Wheel Casing Carpet LH<br />
19 Rear Hatch Floor Trim Strip<br />
20 Wheel Casing Carpet RH<br />
21 Rear Floor Covering<br />
22 Engine Rear Stop Plate Covering<br />
23 Clip<br />
24 Screw<br />
25 Clip<br />
88-28<br />
1. REMOVE ENGIEN COMPARTMENT COVER.<br />
Remove driver seat assy.(Refer to “Chapter 84 seat - driver/assisant driver seat, removal & installation<br />
and disassembly &reassemlby)<br />
Remove middle platform.(Refer to “Chapter 83 instrument panel - middle platform, replacement”)<br />
Remove driver step board trim strip, remove the driver side covering.<br />
Remove the quarter panel front lower guard board cover,<br />
remove the nut.<br />
Loosen 3 retaining bolt.<br />
Remove engine compartment cover assy.<br />
2. REMOVE ENGIEN COMPARTMENT COVER UNDER ASSISTANT DRIVER SEAT.<br />
• Remove engine compartment cover under assistant driver seat by the same procedures as the<br />
engine compartment cover.<br />
• Skip step (d)<br />
3. REMOVE FRONT FLOOR COVERING.<br />
(a) Remove driver and assistant driver seat assy.(Refer to “Chapter 84 seat-driver/assistant driver seat<br />
,removal & installation and disassembly &reassemlby”)<br />
(b) Remove middle platform.(Refer to “Chapter 83 instrument panel - middle platform, replacement”)<br />
Remove driver step board trim strip.<br />
Remove front floor covering.<br />
4. REMOVE ENGINE REAR STOP PLATE COVERING.<br />
(a) Remove 9 engine rear stop plate covering retaining clips.<br />
(b) Remove engine rear stop plate covering.<br />
88-29<br />
5. REMOVE REAR FLOOR COVERING.<br />
(a) Remove passenger seat.(Refer to “Chapter 84 seat- passenger seat,replacement”)<br />
(b) Remove quarter panel guard board.(Refer to “Chapter 88 exterior and interior trim-quarter panel guard<br />
board,replacement”)<br />
(c) Remove rear hatch floor trim strip.<br />
(d) Remove rear floor covering.<br />
6. INSTALL ENGINE COMPARTMENT COVER.<br />
(a) Tighten 3 retaining bolts.<br />
(b) Tighten the nut, install the engine comparement cover.<br />
Install driver step board trim strip, install assistant driver<br />
covering.<br />
7. INSTALL ENGINE COMPARTMENT COVER UNDER ASSISTANT DRIVER SEAT.<br />
• Install engine compartment cover under assistant driver seat by the same procedures as the<br />
8. INSTALL FRONT FLOOR COVERING.<br />
(a) Position the front floor covering.<br />
Install driver step board trim strip.<br />
Install middle platform. (Refer to “Chapter 83 instrument<br />
panel - middle platform, replacement”)<br />
Install driver and assistant driver seat assy.(Refer to “Chapter<br />
84 seat-driver/assistant driver seat ,removal & installation and<br />
disassembly &reassemlby”)<br />
88-30<br />
9. INSTALL ENGINE REAR STOP PLATE COVERING.<br />
(a) Position the engine rear stop plate covering.<br />
(b) Install 9 retaining clips.<br />
10. INSTALL REAR FLOOR COVERING.<br />
(a) Position the rear floor covering.<br />
(b) Install rear hatch floor trim strip.<br />
11. INSTALL QUARTER PANEL GUARD BOARD LH.(Refer to “Chapter 88 exterior and interior trim -<br />
quarter panel guard board, replacement”)<br />
12. INSTALL PASSENGER SEAT. (Refer to “Chapter 84 seat - passenger seat, replacement”)<br />
ROOF PANEL<br />
EXTERIOR AND INTERIOR TRIM - ROOF PANEL<br />
88-31<br />
2 Front Insulating Felt<br />
3 Front Trim Cover<br />
6 Front Visor LH<br />
7 Front Visor RH<br />
10 Rear Insulating Felt<br />
11 Rear Trim Cover<br />
12 Bolt<br />
88-32<br />
2. REMOVE MIDDLE INDOOR LAMP ASSY. (Refer to“Chapter 64 lighting - middle indoor lamp<br />
assy,replacement”)<br />
3. REMOVE PASSENGER SEAT BELT UPPER REAINING BOLT.(Refer to “Chapter 63 belt -<br />
Retractor Assy,Replacement.”)<br />
4. REMOVE UPPER GUARD BOARD.(Refer to “Chapter 88 Exterior and interior trim - quarter panel<br />
5. REMOVE SLIDING ROOF SEALING STRIP.<br />
6. REMOVE REAR AIR PURIFIER ASSY.<br />
(a) Pass on both side, remove air purifier cover.<br />
Remove air filter.<br />
88-33<br />
Remove the air purifier.<br />
7. INSTALL REAR AIR PURIFIER ASSY<br />
Position the air filter.<br />
88-34<br />
Install air purifier cover..<br />
8. REMOVE REAR ROOF GUARD BOARD ASSY.<br />
(a) Disconnect the sealing strip of rear hatch.<br />
(b) Disengage 30 clips.<br />
(c) Remove the roof guard board assy.<br />
• Be careful, the roof guard board assy is too heavy.<br />
• Be careful, do not damage the interior trim.<br />
• Be sure change new clips when installation.<br />
9. REMOVE FRONT ROOF GUARD BOARD ASSY.<br />
(a) Remove 2 safety hammer retaining screws.<br />
Pry out air conditioning control switch.<br />
Disconnect the air conditioning control switch connector.<br />
Remove the air conditioning control switch.<br />
Remove the front visors.<br />
Remove front indoor lamp assy.<br />
88-35<br />
Remove the front handle.<br />
Disengage 6 clips.<br />
Remove the front roof guard board assy.<br />
Be sure change new clips when installation.<br />
10. INSTALL FRONT ROOF GUARD BOARD ASSY.<br />
(a) Install 6 clips and intsll front roof guard board.<br />
Install the front handle.<br />
Install the front visors.<br />
Install front indoor lamp assy.<br />
88-36<br />
Connect the air conditioning control switch connector.<br />
Install 2 safety hammer retaining screws.<br />
11. INSTALL FRONT ROOF GUARD BOARD ASSY.<br />
(a) Install 30 clips and intsll rear roof guard board.<br />
(b) Install rear hatch sealing strip.<br />
12. INSALL UPPER GUARD BOARD.(Refer to “Chapter 88 Exterior and interior trim - quarter panel<br />
13. INSTALL MIDDLE INDOOR LAMP ASSY. (Refer to“Chapter 64 lighting - middle indoor lamp<br />
14. INSTALL REAR INDOOR LAMP ASSY. (Refer to“Chapter 64 lighting - rear indoor lamp<br />
15. INSTALL SLIDING ROOF SEALING STRIP.<br />
16. INSTALL PASSENGER SEAT BELT UPPER REAINING BOLT.(Refer to “Chapter 63 belt -<br />
17. CONNECT BATTERY NEGATIVE CABLE<br />
IGNITION SWITCH ASSY.................................................................. 91-1<br />
INSPECTION ............................................................................... 91-1<br />
DISASSEMBLY & ASSEMBLY.................................................... 91-2<br />
91<br />
VEHICLE CONTROL SYSTEM - IGNITION SWITCH ASSY<br />
91-1<br />
1. INSPECT IGNITION SWITCH ASSY.<br />
(a) Test the resistance and the continuity of all pins using the<br />
following table.<br />
Switch position Terminal Specified condition<br />
LOCK AM1 - ACC - IG1 - AM2 - IG2 - ST ≥ 1 MΩ<br />
ACC AM1 - ACC < 2 Ω<br />
ON AM1 - ACC - IG1, AM2 - IG2 < 2 Ω<br />
START AM1 - IG1 , AM2 - IG2 - ST < 2 Ω<br />
If the resistance is out of the specification, replace the ignition switch assy. (Refer to “Chapter 91<br />
vehicle control system - ignition switch assy, removal & installation and disassembly & assembly”)<br />
91-2<br />
REMOVAL & INSTALLATION AND DISASSEMBLY & ASSEMBLY<br />
3. REMOVE STEERING WHEEL ASSY. (Refer to “Chapter 51 steering column - steering wheel assy,<br />
4. REMOVE STEERING COLUMN PANEL.<br />
5. REMOVE CLOCKSPRING. (Refer to “Chapter 62 Supplemental Restraint System - clock spring,<br />
8. REMOVE IGNITION SWITCH HARNESS.<br />
(a) Disconnect ignition switch connector.<br />
(b) Disconnect ignition key switch connector.<br />
(c) Disconnect ignition switch illumination light connector.<br />
Using prying tool remove 2 harness ties.<br />
9. REMOVE STEERING COLUMN.<br />
(a) Remove 3 steering column retaining bolts as shown in<br />
the figure.<br />
It is recommended to remove steering column for easier<br />
91-3<br />
10. REMOVE IGNITION SWITCH ILLUMINATION LIGHT.<br />
(a) Pry out lock slot on both sides of illumination light as<br />
(b) Remove illumination light.<br />
11. REMOVE IGNITION SWITCH ASSY.<br />
(a) Remove 2 ignition switch anti-theft bolts.<br />
Using special chisel, cut out a groove on top surface of<br />
anti-theft bolts, then remove them.<br />
(b) Remove ignition switch assy.<br />
12. DISASSEMBLE IGNITION SWITCH ASSY.<br />
Insert the ignition key, then turn the ignition switch to the<br />
“ACC” position.<br />
Using a stick, press the lock latch of ignition switch.<br />
Pull out the ignition switch body.<br />
91-4<br />
Remove 2 screws.<br />
Remove the ignition switch connector.<br />
13. ASSEMBLE IGNITION SWITCH ASSY.<br />
Install the ignition switch connector.<br />
Insert and turn it to align the key sets.<br />
91-5<br />
Install the ignition switch body.<br />
If hear a “click”, the ignition switch is installed properly.<br />
Align the lock slot on the steering column assy and the latch<br />
block on the ignition switch assy.<br />
The ignition switch lock latch will extrude only when the<br />
ignition key is pulled out.<br />
(f) Position the ignition switch assy properly, then tighten 2<br />
anti-theft bolts with a suitable tool.<br />
After installation, using a special tool, strike the top surface<br />
of anti-theft bolts where there is a groove into a flat surface.<br />
14. INSTALL IGNITION SWITCH ILLUMINATION LIGHT.<br />
(a) Press the illumination light until lock slots snap in place<br />
91-6<br />
15. INSTALL STEERING COLUMN ASSY.<br />
Position steering column, then tighten 3 retaining bolts.<br />
16. CONNECT IGNITION SWITCH HARNESS CONNECTOR.<br />
17. INSTALL STEERING COLUMN PANEL. (Refer to “Chapter 51 steering column - steering column<br />
18. INSTALL COMBINATION SWITCH ASSY. (Refer to “Chapter 51 steering column - combination<br />
19. INSTALL CLOCKSPRING. (Refer to “Chapter 62 Supplemental Restraint System - clock spring,<br />
20. INSTALL COMBINATION SWITCH UPPER AND LOWER COVER.<br />
21. INSTALL STEERING WHEEL ASSY. (Refer to “Chapter 51 steering column - steering wheel assy,<br />
22. CONNECT BATTERY NEGATIVE CABLE.<br />
23. CHECK AFTER INSTALLATION.<br />
(a) Insert ignition key into ignition lock cylinder and switch the ignition key in the ACC ,ON and LOCK<br />
positions so that confirm ignition switch works normally .<br />
A - CHASSIS & FRAME WIRE HARNESS(CONNECTOR<br />
VIEWS) ........................................................................ 71-112, 71-104<br />
A - CHASSIS & FRAME WIRE HARNESS(WIRE HARNESS & CON-<br />
NECTOR LOCATION VIEWS)...................................................71-190<br />
ADJUSTMENT(CLUTCH PEDAL) .................................................42-5<br />
ADJUSTMENT(DRIVER / ASSISTANT DRIVER SEAT) ...............84-3<br />
ADJUSTMENT(ENGINE HOOD) ...................................................87-1<br />
ADJUSTMENT(FRONT COMBINATION LAMP ASSY) ................64-7<br />
ADJUSTMENT(REAR HATCH) ...................................................87-16<br />
ADJUSTMENT(SLIDING DOOR) ................................................87-10<br />
ADJUSTMENT(STEERING WHEEL ASSY)..................................51-7<br />
ADJUSTMENT(WASHER NOZZLE)............................................65-16<br />
ANTI-LOCK BRAKE CONTROL SYSTEM(WIRING<br />
DIAGRAM) ....................................................................... 71-41, 71-39<br />
ANTI-THEIF SYSTEM(WIRING DIAGRAM) .................. 71-103, 71-97<br />
AUDIO SYSTEM ............................................................................66-1<br />
A/C RECEIVER DRIER FILTER ELEMENT ................................61-85<br />
B - BATTERY WIRE HARNESS(CONNECTOR<br />
VIEWS) ........................................................................ 71-125, 71-104<br />
B - BATTERY WIRE HARNESS(WIRE HARNESS & CONNECTOR<br />
LOCATION VIEWS) ..................................................... 71-199, 71-179<br />
BLEEDING(CLUTCH FLUID).........................................................42-3<br />
C - FRONT BUMPER WIRE HARNESS(CONNECTOR<br />
VIEWS) ........................................................................ 71-126, 71-105<br />
C - FRONT BUMPER WIRE HARNESS(WIRE HARNESS & CON-<br />
NECTOR LOCATION VIEWS)..................................... 71-186, 71-166<br />
CHARGING SYSTEM(WIRING DIAGRAM) .................... 71-39, 71-37<br />
CLOCK SPRING ..........................................................................62-13<br />
CLUTCH FLUID .............................................................................42-3<br />
CLUTCH PEDAL............................................................................42-4<br />
CLUTCH SLAVE CYLINDER.......................................................42-11<br />
CLUTCH SUB - ASSY .................................................................42-13<br />
CLUTCH SYSTEM.........................................................................42-1<br />
COMBINATION SWITCH ASSY ...................................... 51-12, 64-27<br />
COMMUNICATION SYSTEM(WIRING DIAGRAM)......... 71-85, 71-81<br />
COMPONENTS(AUDIO SYSTEM)................................................66-1<br />
COMPONENTS(CLUTCH PEDAL)................................................42-4<br />
COMPONENTS(CLUTCH SUB - ASSY) .....................................42-13<br />
COMPONENTS(COMBINATION SWITCH ASSY)......................51-12<br />
COMPONENTS(DASHBOARD) ....................................................83-6<br />
COMPONENTS(DRIVER / ASSISTANT DRIVER SEAT BELT) ...63-4<br />
COMPONENTS(DRIVER / ASSISTANT DRIVER SEAT) .............84-2<br />
COMPONENTS(FLOOR DECORATIVE PARTS) .......................88-27<br />
COMPONENTS(FRONT BUMPER ASSY)....................................88-3<br />
COMPONENTS(FRONT COMBINATION LAMP ASSY)...............64-2<br />
COMPONENTS(FRONT DOOR LOCKS)......................................85-1<br />
COMPONENTS(FRONT DOOR)...................................................87-4<br />
COMPONENTS(FRONT GRILLE).................................................88-1<br />
COMPONENTS(INSTRUMENT CLUSTER)..................................83-2<br />
COMPONENTS(PASSENGER SEAT BELT) ................................63-5<br />
COMPONENTS(POWER STEERING SYSTEM) ..........................52-5<br />
COMPONENTS(REAR BUMPER ASSY) ....................................88-10<br />
COMPONENTS(REAR COMBINATION LAMP ASSY) ...............64-10<br />
COMPONENTS(REAR HATCH LOCK) ...................................... 85-12<br />
COMPONENTS(REAR HATCH) ................................................. 87-15<br />
COMPONENTS(ROOF PANEL) ................................................. 88-31<br />
COMPONENTS(SLIDING DOOR LOCKS) ................................... 85-7<br />
COMPONENTS(SLIDING DOOR) ................................................ 87-9<br />
COMPONENTS(SLIDING ROOF ASSY) ...................................... 86-2<br />
COMPONENTS(STEERING SYSTEM) ........................................ 51-5<br />
COMPONENTS(STEP BOARD) ................................................. 88-15<br />
COMPONENTS(SUN VISOR ASSY) .......................................... 88-13<br />
COMPONENTS(TRANSMISSION OPERATION MECHANISM<br />
ASSY)............................................................................................ 41-1<br />
COMPONENTS(WIPER AND WASHER SYSTEM) ..................... 65-4<br />
COMPRESSOR OIL.................................................................... 61-17<br />
COMPRESSOR(ISF2.8).............................................................. 61-80<br />
COMPRESSOR(4G69) ............................................................... 61-78<br />
CONDENSER.............................................................................. 61-83<br />
CONNECTOR VIEWS.................................................. 71-112, 71-104<br />
(HOW TO USE THIS MANUAL).................................................... 71-6<br />
D - FRONT DOOR LH WIRE HARNESS(CONNECTOR<br />
VIEWS)......................................................................... 71-127, 71-106<br />
D - FRONT DOOR LH WIRE HARNESS(WIRE HARNESS & CON-<br />
NECTOR LOCATION VIEWS) ..................................... 71-188, 71-168<br />
DASHBOARD................................................................................ 83-5<br />
DRIVER / ASSISTANT DRIVER SEAT ......................................... 84-2<br />
DRIVER / ASSISTANT DRIVER SEAT BELT ............................... 63-4<br />
(CONNECTOR VIEWS) ............................................... 71-130, 71-108<br />
E - ENGINE WIRE HARNESS(WIRE HARNESS & CONNECTOR<br />
LOCATION VIEWS) ..................................................... 71-193, 71-172<br />
ELECTRIC DEVICE ACCESSORIES ......................................... 66-12<br />
ENGINE HOOD ............................................................................. 87-1<br />
(CONNECTOR VIEWS) ............................................... 71-142, 71-119<br />
F - ROOF WIRE HARNESS 1(WIRE HARNESS & CONNECTOR<br />
LOCATION VIEWS) ..................................................... 71-201, 71-181<br />
FLOOR DECORATIVE PARTS................................................... 88-27<br />
FRONT BUMPER ASSY ............................................................... 88-3<br />
FRONT COMBINATION LAMP ASSY .......................................... 64-2<br />
FRONT DOME LIGHT ASSY ...................................................... 64-17<br />
FRONT DOOR .............................................................................. 87-4<br />
FRONT DOOR LOCKS ................................................................. 85-1<br />
FRONT GRILLE ............................................................................ 88-1<br />
FRONT HEATER CORE ............................................................. 61-25<br />
FRONT SPEAKER ASSY.............................................................. 66-4<br />
FUSE AND RELAY LOCATIONS(HOW TO USE<br />
THIS MANUAL) ............................................................................. 71-9<br />
(CONNECTOR VIEWS) ............................................... 71-146, 71-122<br />
G - ROOF WIRE HARNESS 2(WIRE HARNESS & CONNECTOR<br />
LOCATION VIEWS) ..................................................... 71-204, 71-182<br />
GLOSSARY OF TERMS AND SYMBOLS(HOW TO USE THIS<br />
MANUAL) ...................................................................................... 71-7<br />
(CONNECTOR VIEWS) ............................................... 71-148, 71-124<br />
H - FRONT DOOR RH WIRE HARNESS(WIRE HARNESS &<br />
CONNECTOR LOCATION VIEWS) ............................. 71-189, 71-169<br />
HEATER AND AIR CONDITIONING SYSTEM ............................. 61-1<br />
(WIRING DIAGRAM) ........................................................ 71-44, 71-42<br />
HIGH-MOUNTED STOP LAMP ASSY ........................................ 64-16<br />
HORN SWITCH ASSY .................................................................. 62-6<br />
HOW TO USE THIS MANUAL ...................................................... 71-1<br />
I - INSTRUMENT PANEL WIRE HARNESS(WIRE HARNESS &<br />
CONNECTOR LOCATION VIEWS) .......................................... 71-196<br />
J - REAR HATCH WIRE HARNESS(WIRE HARNESS &<br />
CONNECTOR LOCATION VIEWS) ............................. 71-204, 71-182<br />
IGNITION SWITCH ASSY............................................................. 91-1<br />
INSPECTION(COMPRESSOR OIL) ........................................... 61-17<br />
INSPECTION(IGNITION SWITCH ASSY) .................................... 91-1<br />
INSPECTION(POWER WINDOW)................................................ 82-2<br />
INSPECTION(WASHER NOZZLE) ............................................. 65-15<br />
INSTRUMENT CLUSTER ............................................................. 83-1<br />
INSTRUMENT CLUSTER(WIRING DIAGRAM)............... 71-96, 71-90<br />
INTRODUCTION(HOW TO USE THIS MANUAL) ........................ 71-1<br />
K - REAR HATCH TRANSITION WIRE HARNESS(WIRE HARNESS<br />
& CONNECTOR LOCATION VIEWS).......................... 71-204, 71-182<br />
L - REAR EVAPORATOR WIRE HARNESS(WIRE HARNESS &<br />
CONNECTOR LOCATION VIEWS) ............................. 71-202, 71-181<br />
LICENCE LAMP ASSY................................................................ 64-14<br />
LIGHT SYSTEM(WIRING DIAGRAM).............................. 71-52, 71-49<br />
LIGHTING SYSTEM...................................................................... 64-1<br />
M - DIAGNOSIS WIRE HARNESS(WIRE HARNESS & CONNECTOR<br />
LOCATION VIEWS) ..................................................... 71-196, 71-175<br />
MIDDLE PLATFORM .................................................................. 83-15<br />
MIDDLE SPEAKER ASSY ............................................................ 66-6<br />
MULTI-MEDIA AND AIR-CONDITON CONTROLLER ASSY ....... 66-2<br />
MULTI-MEDIA AND A/C CONTROLLER ASSY ......................... 61-19<br />
MULTIMEDIA SYSTEM(WIRING DIAGRAM) .................. 71-80, 71-76<br />
N - STEP LAMP WIRE HARNESS(WIRE HARNESS & CONNECTOR<br />
LOCATION VIEWS) ..................................................... 71-203, 71-181<br />
O - DRIVER SEAT BELT WIRE HARNESS(CONNECTOR<br />
VIEWS)...................................................................................... 71-172<br />
O - DRIVER SEAT BELT WIRE HARNESS(WIRE HARNESS & CON-<br />
NECTOR LOCATION VIEWS) .................................................. 71-199<br />
ON-VEHICLE INSPECTION(HEATER AND AIR CONDITIONING<br />
SYSTEM) .......................................................................................61-7<br />
ON-VEHICLE INSPECTION(REFRIGERANT)..............................61-8<br />
ON-VEHICLE INSPECTION(STEERING SYSTEM) .....................51-6<br />
ON-VEHICLE INSPECTION(SUPPLEMENTAL RESTRAINT<br />
SYSTEM) .......................................................................................62-4<br />
OVERHAUL(CLUTCH SUB - ASSY) ...........................................42-14<br />
OVERHAUL(COMPRESSOR(ISF2.8))........................................61-80<br />
OVERHAUL(COMPRESSOR(4G69))..........................................61-78<br />
OVERHAUL(CONDENSER)........................................................61-83<br />
OVERHAUL(RETRACTOR ASSY)..............................................63-15<br />
OVERHAUL(STEERING COLUMN ASSY) .................................51-16<br />
OVERHAUL(STEERING GEAR ASSY).......................................52-28<br />
OVERHAUL(STEERING PROPELLER SHAFT ASSY) ..............51-19<br />
OVERHAUL(STEERING WHEEL ASSY) ......................................51-8<br />
OUTSIDE MIRROR .....................................................................82-17<br />
(CONNECTOR VIEWS)................................................71-173, 71-131<br />
P - REAR HEATER WIRE HARNESS(WIRE HARNESS &<br />
CONNECTOR LOCATION VIEWS)..............................71-199, 71-179<br />
PASSENGER SEAT ....................................................................84-15<br />
PASSENGER SEAT BELT ............................................................63-5<br />
POWER MIRROR(WIRING DIAGRAM) ...........................71-90, 71-85<br />
POWER SOCKET(WIRING DIAGRAM) ...........................71-83, 71-79<br />
POWER SOURCE SECTION EXAMPLE(HOW TO USE THIS<br />
MANUAL).......................................................................................71-5<br />
POWER SOURCE(WIRING DIAGRAM) ..........................71-18, 71-19<br />
POWER STEERING LINE ASSY ................................................52-22<br />
RESERVIOR ASSY .....................................................................52-17<br />
POWER STEERING SYSTEM ......................................................52-1<br />
POWER WINDOW.........................................................................82-2<br />
PRECAUTION(CLUTCH SYSTEM)...............................................42-1<br />
PRECAUTION(DASHBOARD) ......................................................83-5<br />
PRECAUTION(HEATER AND AIR CONDITIONING<br />
SYSTEM) .......................................................................................61-1<br />
PRECAUTION(INSTRUMENT CLUSTER)....................................83-1<br />
PRECAUTION(LIGHTING SYSTEM) ............................................64-1<br />
PRECAUTION(POWER STEERING SYSTEM) ............................52-1<br />
PRECAUTION(SEAT BELT SYSTEM)..........................................63-1<br />
PRECAUTION(SEAT)....................................................................84-1<br />
PRECAUTION(SUPPLEMENTAL RESTRAINT SYSTEM) ...........62-1<br />
PRECAUTION(WIPER AND WASHER SYSTEM) ........................65-1<br />
PROBLEM SYMPTOMS TABLE(CLUTCH SYSTEM)...................42-2<br />
CONDITIONING SYSTEM) ...........................................................61-3<br />
PROBLEM SYMPTOMS TABLE(POWER STEERING<br />
SYSTEM) .......................................................................................52-2<br />
PROBLEM SYMPTOMS TABLE(SLIDING ROOF ASSY).............86-1<br />
PROBLEM SYMPTOMS TABLE(STEERING SYSTEM)......51-1, 51-2<br />
PROBLEM SYMPTOMS TABLE(WIPER AND WASHER<br />
SYSTEM) .......................................................................................65-2<br />
Q<br />
Q - REAR BUMPER TRANSITION WIRE HARNESS(CONNECTOR<br />
VIEWS) .........................................................................71-174, 71-132<br />
Q - REAR BUMPER TRANSITION WIRE HARNESS(WIRE<br />
HARNESS & CONNECTOR LOCATION VIEWS)........71-204, 71-182<br />
QUARTER PANEL GUARD BOARD...........................................88-23<br />
R - REAR BUMPER WIRE HARNESS(CONNECTOR<br />
VIEWS) .........................................................................71-175, 71-133<br />
R - REAR BUMPER WIRE HARNESS(WIRE HARNESS & CONNEC-<br />
TOR LOCATION VIEWS) ............................................ 71-204, 71-182<br />
RCM .............................................................................................62-16<br />
REAR BUMPER ASSY ................................................................88-10<br />
REAR COMBINATION LAMP ASSY ...........................................64-10<br />
REAR HATCH..............................................................................87-15<br />
REAR HATCH LOCK ...................................................................85-12<br />
REAR HEATER CORE ................................................................61-35<br />
REAR SPERKER ASSY ................................................................66-8<br />
REAR WINDOW GLASS .............................................................82-12<br />
REFRIGERANT .............................................................................61-8<br />
REMOVAL & INSTALLATION AND DISASSEMBLY & REASSEM-<br />
BLY(IGNITION SWITCH ASSY) ....................................................91-2<br />
REMOVAL & INSTALLATION AND DISASSEMBLY & REASSEML-<br />
BY((DRIVER / ASSISTANT DRIVER SEAT)) ................................84-7<br />
REMOVAL & INSTALLATION(PASSENGER SEAT) ..................84-15<br />
REPLACEMENT(A/C RECEIVER DRIER FILTER<br />
ELEMENT) ...................................................................................61-85<br />
REPLACEMENT(CLOCK SPRING).............................................62-13<br />
REPLACEMENT(CLUTCH PEDAL) ..............................................42-6<br />
REPLACEMENT(CLUTCH SLAVE CYLINDER) .........................42-11<br />
REPLACEMENT(COMBINATION SWITCH ASSY)......... 51-13, 64-27<br />
REPLACEMENT(COMPRESSOR OIL) .......................................61-18<br />
REPLACEMENT(DASHBOARD) ...................................................83-7<br />
REPLACEMENT(ELECTRIC DEVICE ACCESSORIES).............66-12<br />
REPLACEMENT(ENGINE HOOD) ................................................87-3<br />
REPLACEMENT(FLOOR DECORATIVE PARTS) ......................88-28<br />
REPLACEMENT(FRONT BUMPER ASSY) ..................................88-4<br />
REPLACEMENT(FRONT DOME LIGHT ASSY) .........................64-17<br />
REPLACEMENT(FRONT DOOR LOCKS) ....................................85-2<br />
REPLACEMENT(FRONT GRILLE)................................................88-2<br />
REPLACEMENT(FRONT HEATER CORE) ................................61-25<br />
REPLACEMENT(FRONT SPEAKER ASSY).................................66-4<br />
REPLACEMENT(HIGH-MOUNTED STOP LAMP ASSY) ...........64-16<br />
REPLACEMENT(HORN SWITCH ASSY) .....................................62-6<br />
REPLACEMENT(INSTRUMENT CLUSTER) ................................83-3<br />
REPLACEMENT(LICENCE LAMP ASSY)...................................64-14<br />
REPLACEMENT(MIDDLE PLATFORM)......................................83-15<br />
REPLACEMENT(MIDDLE SPEAKER ASSY)................................66-6<br />
REPLACEMENT(MULTI-MEDIA AND AIR-CONDITON CONTROL-<br />
LER ASSY) ....................................................................................66-2<br />
REPLACEMENT(MULTI-MEDIA AND A/C CONTROLLER<br />
ASSY) ..........................................................................................61-19<br />
REPLACEMENT(OUTSIDE MIRROR) ........................................82-17<br />
REPLACEMENT(POWER STEERING LINE ASSY) ...................52-22<br />
REPLACEMENT(POWER STEERING PUMP WITH FLUID RESER-<br />
VIOR ASSY).................................................................................52-17<br />
REPLACEMENT(POWER WINDOW) ...........................................82-3<br />
REPLACEMENT(QUARTER PANEL GUARD BOARD)..............88-23<br />
REPLACEMENT(RCM)................................................................62-16<br />
REPLACEMENT(REAR BUMPER ASSY)...................................88-11<br />
REPLACEMENT(REAR COMBINATION LAMP ASSY) ..............64-11<br />
REPLACEMENT(REAR HATCH LOCK)......................................85-13<br />
REPLACEMENT(REAR HATCH) ................................................87-18<br />
REPLACEMENT(REAR HEATER CORE)...................................61-35<br />
REPLACEMENT(REAR SPERKER ASSY) ...................................66-8<br />
REPLACEMENT(REAR WINDOW GLASS) ................................82-12<br />
REPLACEMENT(REFRIGERANT) ..............................................61-14<br />
REPLACEMENT(ROOF PANEL).................................................88-32<br />
REPLACEMENT(SEAT BELT CATCH ASSY) ..............................63-9<br />
REPLACEMENT(SIDE WINDOW GLASS)..................................82-15<br />
REPLACEMENT(SLIDING DOOR LOCKS) ..................................85-8<br />
REPLACEMENT(SLIDING DOOR)..............................................87-13<br />
REPLACEMENT(STEERING FLUID) ..........................................52-13<br />
REPLACEMENT(STEP BOARD).................................................88-16<br />
REPLACEMENT(SUN VISOR ASSY) .........................................88-14<br />
REPLACEMENT(TELESCOPIC ANTENNA ASSY) ....................66-10<br />
REPLACEMENT(TRANSMISSION ASSY<br />
(TANGSHANAIXIN)) ....................................................................41-73<br />
(YANCHENGZHONGMA ZM001)) .............................................. 41-10<br />
REPLACEMENT(TRANSMISSION OPERATION MECHANISM<br />
ASSY)............................................................................................ 41-3<br />
REPLACEMENT(VACUUM BOOSTER WITH CLUTCH<br />
MASTER CYLINDER ASSY)......................................................... 42-8<br />
REPLACEMENT(VEHICLE DOOR INNER GUARD BOARD) .... 88-18<br />
REPLACEMENT(WHEEL MUDGUARD) ...................................... 88-7<br />
REPLACEMENT(WINDSHIELD)................................................... 82-7<br />
REPLACEMENT(WIPER ASSY)................................................... 65-5<br />
REPLACEMENT(WIPER BLADE WITH BRACKET ASSY)........ 65-13<br />
REPLACEMENT(WIPER LINK WITH MOTOR ASSY) ................. 65-9<br />
RETRACTOR ASSY.................................................................... 63-15<br />
ROOF PANEL ............................................................................. 88-31<br />
S - REAR DEFROST RH WIRE HARNESS(CONNECTOR<br />
VIEWS)...................................................................................... 71-176<br />
S - REAR DEFROST RH WIRE HARNESS(WIRE HARNESS &<br />
CONNECTOR LOCATION VIEWS) .......................................... 71-204<br />
SEAT ............................................................................................. 84-1<br />
SEAT BELT CATCH ASSY ........................................................... 63-9<br />
SEAT BELT SYSTEM ................................................................... 63-1<br />
SIDE WINDOW GLASS .............................................................. 82-15<br />
SLIDING DOOR ............................................................................ 87-9<br />
SLIDING DOOR LOCKS ............................................................... 85-7<br />
SLIDING ROOF ASSY .................................................................. 86-1<br />
STARTING SYSTEM(WIRING DIAGRAM) ...................... 71-37, 71-35<br />
STEERING COLUMN ASSY ....................................................... 51-16<br />
STEERING GEAR ASSY ............................................................ 52-28<br />
STEERING PROPELLER SHAFT ASSY .................................... 51-19<br />
STEERING WHEEL ASSY............................................................ 51-7<br />
STEP BOARD ............................................................................. 88-15<br />
SUN VISOR ASSY ...................................................................... 88-13<br />
SUPPLEMENTAL RESTRAINT SYSTEM..................................... 62-1<br />
SYSTEM PERFORMANCE(SUPPLEMENTAL RESTRAINT<br />
SYSTEM)....................................................................................... 62-3<br />
SYSTEM PRINCIPLES(SUPPLEMENTAL RESTRAINT<br />
SYSTEM)....................................................................................... 62-2<br />
SYSTEM WIRING DIAGRAM SECTION EXAMPLE(HOW TO<br />
USE THIS MANUAL)..................................................................... 71-2<br />
T - REAR DEFROST LH WIRE HARNESS(CONNECT<br />
VIEWS)...................................................................................... 71-177<br />
T - REAR DEFROST LH WIRE HARNESS(WIRE HARNESS & CON-<br />
NECTOR LOCATION VIEWS) .................................................. 71-204<br />
TELESCOPIC ANTENNA ASSY ................................................. 66-10<br />
TRANSMISSION ASSY(TANGSHANAIXIN)............................... 41-73<br />
TRANSMISSION ASSY(YANCHENGZHONGMA ZM001) ........... 41-8<br />
TRANSMISSION OPERATION MECHANISM ASSY ................... 41-1<br />
V - FRONT WIRE HARNESS(CONNECT VIEWS) ...... 71-179, 71-135<br />
V - FRONT WIRE HARNESS(WIRE HARNESS & CONNECTOR<br />
LOCATION VIEWS) ..................................................... 71-186, 71-166<br />
U - HIGH-MOUNTED STOP LAMP WIRE HARNESS(CONNECT<br />
VIEWS)......................................................................... 71-178, 71-134<br />
U - HIGH-MOUNTED STOP LAMP WIRE HARNESS(WIRE HAR-<br />
NESS & CONNECTOR LOCATION VIEWS) ............... 71-204, 71-182<br />
ASSY ............................................................................................. 42-8<br />
WASHER NOZZLE...................................................................... 65-15<br />
VEHICLE DOOR INNER GUARD BOARD ................................. 88-18<br />
VEHICLE WITH REAR WIPER ASSY(COMPONENTS) .............. 65-4<br />
WHEEL MUDGUARD.................................................................... 88-7<br />
WINDOW DEFROSTER(WIRING DIAGRAM) ................. 71-93, 71-88<br />
WINDSHIELD ................................................................................ 82-7<br />
WIPER AND WASHER SYSTEM.................................................. 65-1<br />
WIPER AND WASHER(WIRING DIAGRAM)................... 71-77, 71-73<br />
WIPER ASSY ................................................................................ 65-5<br />
WIPER BLADE WITH BRACKET ASSY ..................................... 65-13<br />
WIPER LINK WITH MOTOR ASSY............................................... 65-9<br />
WIRE HARNESS & CONNECTOR LOCATION<br />
VIEWS.......................................................................... 71-186, 71-166<br />
WIRING DIAGRAM .......................................................... 71-18, 71-19<br />
X<br />
X - PREHEATING WIRE HARNESS(WIRE HARNESS & CONNEC-<br />
TOR LOCATION VIEWS)............................................. 71-199, 71-179<br />
- More documents
- Recommendations
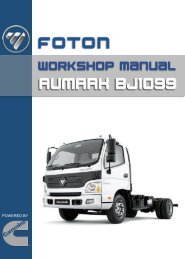
POWERED BY WCRKSHCP manuaL
- Page 3: VOLUME 1 FOTON WORKSHOP MANUAL - VI
- Page 7 and 8: INTRODUCTION HOW TO USE THIS MANUAL
- Page 9 and 10: HOW TO USE THIS MANUAL INTRODUCTION
- Page 11 and 12: INTRODUCTION - HOW TO USE THIS MANU
- Page 13 and 14: INTRODUCTION - HOW TO USE THIS MANU
- Page 15 and 16: INTRODUCTION - IDENTIFICATION INFOR
- Page 17 and 18: INTRODUCTION - REPAIR INSTRUCTION 0
- Page 19 and 20: INTRODUCTION - REPAIR INSTRUCTION 0
- Page 21 and 22: INTRODUCTION - REPAIR INSTRUCTION 0
- Page 23 and 24: INTRODUCTION - REPAIR INSTRUCTION 0
- Page 25 and 26: INTRODUCTION - REPAIR INSTRUCTION 0
- Page 27 and 28: INTRODUCTION - HOW TO TROUBLESHOOT
- Page 29 and 30: INTRODUCTION - HOW TO TROUBLESHOOT
- Page 31 and 32: INTRODUCTION - HOW TO TROUBLESHOOT
- Page 33 and 34: INTRODUCTION - HOW TO TROUBLESHOOT
- Page 35 and 36: INTRODUCTION - HOW TO TROUBLESHOOT
- Page 37 and 38: INTRODUCTION - HOW TO TROUBLESHOOT
- Page 39 and 40: INTRODUCTION - HOW TO TROUBLESHOOT
- Page 41 and 42: INTRODUCTION - TERMS 01-33 TERMS AB
- Page 43 and 44: PREPARATION DIAGNOSTICS............
- Page 45 and 46: PREPARATION - DIAGNOSTICS 02-1 DIAG
- Page 47 and 48: ENGINE CONTROL SYSTEM PREPARATION R
- Page 49 and 50: EMISSION CONTROL PREPARATION RECOMM
- Page 51 and 52: PREPARATION - ENGINE MECHANICAL 02-
PREPARATION - ENGINE MECHANICAL 02-
PREPARATION - COOLING 02-11 COOLING
PREPARATION - LUBRICATION 02-13 SSM
PREPARATION - FRONT SUSPENSION 02-1
PREPARATION - TIRE AND WHEEL 02-17
PREPARATION - AXLE AND PROPELLER SH
PREPARATION - BRAKE 02-21 BRAKE PRE
PREPARATION - TRANSMISSION 02-23 TR
PREPARATION - CLUTCH 02-25 CLUTCH P
POWER STEERING PREPARATION RECOMMEN
PREPARATION - HEATER AND AIR CONDIT
WIPER AND WASHER PREPARATION RECOMM
PREPARATION - INSTRUMENT PANEL/INST
DOOR LOCKS PREPARATION RECOMMENDED
VEHICLE CONTROL SYSTEM PREPARATION
SERVICE SPECIFICATIONS SPECIFIED TO
SERVICE SPECIFICATIONS - SPECIFIED
SERVICE SPECIFICATIONS - ENGINE CON
EMISSION CONTROL TORQUE SPECIFICATI
SERVICE SPECIFICATIONS - ENGINE MEC
SERVICE SPECIFICATIONS - EXHAUST 03
SERVICE SPECIFICATIONS - LUBRICATIO
SERVICE SPECIFICATIONS - STARTING A
FRONT SUSPENSION SERVICE DATA FRONT
TIRE AND WHEEL SERVICE DATA TIRE PR
SERVICE SPECIFICATIONS - AXLE AND P
SERVICE SPECIFICATIONS - BRAKE 03-2
TRANSMISSION SERVICE DATA Transmiss
SERVICE SPECIFICATIONS - CLUTCH 03-
POWER STEERING SERVICE DATA VEHICLE
SERVICE SPECIFICATIONS - HEATER AND
SERVICE SPECIFICATIONS - LIGHTING 0
SERVICE SPECIFICATIONS - SEAT 03-35
SERVICE SPECIFICATIONS - EXTERIOR A
DIAGNOSTICS ENGINE CONTROL SYSTEM..
NOT INOPERATIVE ...................
REAR WINDOW DEFROSTER IS INOPERATIV
ENGINE CONTROL SYSTEM DIAGNOSTICS P
DIAGNOSTICS - ENGINE CONTROL SYSTEM
DIAGNOSTICS - ANTI - LOCK BRAKE SYS
DIAGNOSTICS - SUPPLEMENTAL RESTRAIN
DIAGNOSTICS - HEATER AND AIR CONDIT
DIAGNOSTICS - LIGHTING SYSTEM 04-20
DIAGNOSTICS - LIGHTING SYSTEM 04-21
DIAGNOSTICS - LIGHTING SYSTEM 04-22
DIAGNOSTICS - LIGHTING SYSTEM 04-23
DIAGNOSTICS - LIGHTING SYSTEM 04-24
DIAGNOSTICS - LIGHTING SYSTEM 04-25
DIAGNOSTICS - LIGHTING SYSTEM 04-26
DIAGNOSTICS - LIGHTING SYSTEM 04-27
DIAGNOSTICS - LIGHTING SYSTEM 04-28
DIAGNOSTICS - LIGHTING SYSTEM 04-29
DIAGNOSTICS - LIGHTING SYSTEM 04-30
DIAGNOSTICS - LIGHTING SYSTEM 04-31
DIAGNOSTICS - LIGHTING SYSTEM 04-32
DIAGNOSTICS - LIGHTING SYSTEM 04-33
DIAGNOSTICS - LIGHTING SYSTEM 04-34
DIAGNOSTICS - LIGHTING SYSTEM 04-35
DIAGNOSTICS - WIPER AND WASHER 04-3
DIAGNOSTICS - AUDIO SYSTEM 04-393 L
DIAGNOSTICS - AUDIO SYSTEM 04-395 P
DIAGNOSTICS - AUDIO SYSTEM 04-397 I
DIAGNOSTICS - AUDIO SYSTEM 04-399 5
DIAGNOSTICS - AUDIO SYSTEM 04-401 P
DIAGNOSTICS - AUDIO SYSTEM 04-403 I
DIAGNOSTICS - AUDIO SYSTEM 04-405 6
DIAGNOSTICS - AUXILIARY POWER 04-40
DIAGNOSTICS - AUXILIARY POWER 04-41
HORN SYSTEM LOCATION DIAGNOSTICS -
DIAGNOSTICS - HORN SYSTEM 04-417 HO
DIAGNOSTICS - HORN SYSTEM 04-419 3.
DIAGNOSTICS - HORN SYSTEM 04-421 8.
DIAGNOSTICS - HORN SYSTEM 04-423 IN
DIAGNOSTICS - REVERSE RADAR SYSTEM
DIAGNOSTICS - POWER WINDOWS 04-449
DIAGNOSTICS - POWER WINDOWS 04-451
DIAGNOSTICS - POWER WINDOWS 04-453
DIAGNOSTICS - POWER WINDOWS 04-455
DIAGNOSTICS - POWER WINDOWS 04-457
DIAGNOSTICS - POWER WINDOWS 04-459
DIAGNOSTICS - POWER WINDOWS 04-461
DIAGNOSTICS - POWER WINDOWS 04-463
DIAGNOSTICS - POWER WINDOWS 04-465
DIAGNOSTICS - POWER WINDOWS 04-467
DIAGNOSTICS - POWER WINDOWS 04-469
DIAGNOSTICS - POWER WINDOWS 04-471
OUTSIDE MIRROR LOCATION DIAGNOSTICS
DIAGNOSTICS - OUTSIDE MIRROR 04-475
DIAGNOSTICS - OUTSIDE MIRROR 04-477
DIAGNOSTICS - OUTSIDE MIRROR 04-479
DIAGNOSTICS - OUTSIDE MIRROR 04-481
DIAGNOSTICS - OUTSIDE MIRROR 04-483
DIAGNOSTICS - OUTSIDE MIRROR 04-485
DEFROSTER SYSTEM LOCATION DIAGNOSTI
DIAGNOSTICS - DEFROSTER SYSTEM 04-4
DIAGNOSTICS - DEFROSTER SYSTEM 04-5
DIAGNOSTICS - INSTRUMENT CLUSTER 04
DIAGNOSTICS - POWER DOOR LOCKS 04-5
DIAGNOSTICS - SLIDING ROOF SYSTEM 0
A ABBREVIATIONS USED IN THIS MANUAL
PROBLEM SYMPTOMS TABLE(SUPPLEMENTAL
WORKSHOP MANUAL - VIEW CS2 / C2 V O
DIAGNOSTICS(RHD) ENGINE CONTROL SYS
CIGARETTE LIGHTER ILLUMINATION IS N
MALFUCTION IN ENGINE COOLANT TEMPER
ENGINE CONTROL SYSTEM DIAGNOSTICS(R
DIAGNOSTICS(RHD) - ENGINE CONTROL S
DIAGNOSTICS(RHD) - ANTI-LOCK BRAKE
DIAGNOSTICS(RHD) - SUPPLEMENTAL RES
DIAGNOSTICS(RHD) - HEATER AND AIR C
LIGHTING SYSTEM PRECAUTION DIAGNOST
DIAGNOSTICS(RHD) - LIGHTING SYSTEM
DIAGNOSTICS(RHD) - WIPER AND WASHER
DIAGNOSTICS(RHD) - AUDIO SYSTEM 04-
DIAGNOSTICS(RHD) - AUXILIARY POWER
DIAGNOSTICS(RHD) - HORN SYSTEM 04-3
REVERSE RADAR SYSTEM PRECAUTION DIA
DIAGNOSTICS(RHD) - REVERSE RADAR SY
DIAGNOSTICS(RHD) - POWER WINDOWS 04
DIAGNOSTICS(RHD) - OUTSIDE MIRROR 0
DIAGNOSTICS(RHD) - OUTSIDE MIRROR D
DIAGNOSTICS(RHD) - INSTRUMENT CLUST
DIAGNOSTICS(RHD) - POWER DOOR LOCKS
VEHICLE MAINTENANCE MAINTENANCE SCH
VEHICLE MAINTENANCE - MAINTENANCE S
CHECK THE BATTERY VEHICLE MAINTENAN
CHECK SEAT BELT VEHICLE MAINTENANCE
VEHICLE MAINTENANCE - INSPECTION 05
VEHICLE MAINTENANCE - (g) (h) INSPE
VEHICLE MAINTENANCE - REPLACEMENT 0
VEHICLE MAINTENANCE - 14. TURN IGNI
ENGINE CONTROL SYSTEM GASOLINE ENGI
ENGINE CONTROL SYSTEM - GASOLINE EN
ENGINE CONTROL SYSTEM - 3. ECM CONT
ENGINE CONTROL SYSTEM - 3. CONTROL
MAIN COMPONENTS ENGINE CONTROL SYST
ENGINE CONTROL SYSTEM - ENGINE CONT
ENGINE CONTROL SYSTEM - (g) ENGINE
OVERHAUL ENGINE CONTROL SYSTEM - 1.
ENGINE CONTROL SYSTEM - THROTTLE BO
ENGINE CONTROL SYSTEM - IDLE AIR CO
ENGINE CONTROL SYSTEM - THROTTLE PO
ENGINE CONTROL SYSTEM - ON-VEHICLE
ENGINE CONTROL SYSTEM - MANIFOLD AB
ENGINE CONTROL SYSTEM - KNOCK SENSO
CKP SENSOR PRINCIPLE ENGINE CONTROL
ENGINE CONTROL SYSTEM - CKP SENSOR
ENGINE CONTROL SYSTEM - DOWNSTREAM
ENGINE CONTROL SYSTEM - CANISTER SO
ENGINE CONTROL SYSTEM - VEHICLE SPE
ENGINE CONTROL SYSTEM - IGNITION CO
FUEL SYSTEM FUEL SYSTEM............
FUEL SYSTEM PRECAUTION FUEL - FUEL
FUEL - FUEL SYSTEM 12A-3 PROBLEM SY
FUEL - FUEL SYSTEM 12A-5 12A 12A 12
FUEL - FUEL TANK ASSY 12A-7 • Mar
FUEL - FUEL FILTER ASSY 12A-9 FUEL
FUEL - ELECTRIC FUEL PUMP ASSY 12A-
FUEL - FUEL INJECTOR RAIL ASSY 12A-
FUEL - FUEL FILLER DOOR 12A-17 FUEL
FUEL - FUEL FILLER DOOR LOCK LATCH
FUEL - FUEL FILLING TUBE AND BREATH
FUEL - ACCELERATE PEDAL 12A-25 ACCE
EMISSION CONTROL FUEL FILLER CAP ..
EMISSION CONTROL - FUEL FILLER CAP
EMISSION CONTROL - CHARCOAL CANISTE
EMISSION CONTROL - CANISTER SOLENOI
EMISSION CONTROL - POSITIVE CRANKCA
INTAKE AIR INTAKE AIR SYSTEM.......
INTAKE AIR SYSTEM AIR PRECAUTION 1.
INTAKE AIR - INTAKE AIR PIPE AND HO
INTAKE AIR - AIR FILTER ASSY 14A-7
INTAKE AIR - AIR FILTER ASSY 14A-9
INTAKE AIR - AIR FILTER ASSY 14A-11
INTAKE AIR - AIR FILTER ASSY 14A-13
INTAKE AIR - AIR FILTER ASSY 14A-15
ENGINE MECHANICAL ENGINE MECHANICAL
ENGINE MECHANICAL - ENGINE MECHANIC
ENGINE MECHANICAL - ENGINE ASSY 15A
ENGINE MECHANICAL - TIMING PULLEY C
ENGINE MECHANICAL - TIMING BELT 15A
ENGINE MECHANICAL - ROCK ARM, ROCK
CYLINDER HEAD,VALVE COMPONENTS ENGI
ENGINE MECHANICAL - CYLINDER HEAD,V
ENGINE MECHANICAL - PISTON & CONNEC
ENGINE MECHANICAL - CRANKSHAFT, CYL
EXHAUST SYSTEM EXHAUST PIPE .......
EXHAUST - EXHAUST PIPE 16A-1 EXHAUS
EXHAUST - EXHAUST PIPE 16A-3 (b) (c
EXHAUST - EXHAUST PIPE 16A-5 (b) Co
EXHAUST - EXHAUST MANIFOLD 16A-7 EX
EXHAUST - EXHAUST MANIFOLD 16A-9 12
COOLING SYSTEM COOLING SYSTEM .....
COOLING SYSTEM PRECAUTION COOLING -
COOLING - COOLING SYSTEM 17A-3 PROB
COOLING - COOLING SYSTEM 17A-5 •
COOLING - COOLANT 17A-7 (c) Push th
COOLING - RESERVIOR 17A-9 3. INSTAL
COOLING - COOLING FAN ASSY 17A-11 4
COOLING - RADIATOR 17A-13 RADIATOR
COOLING - RADIATOR 17A-15 (e) Remov
COOLING - RADIATOR 17A-17 13. INSTA
COOLING - THERMOSTAT 17A-19 7. REMO
COOLING - THERMOSTAT 17A-21 (a) Ins
COOLANT PUMP OVERHAUL COOLING - COO
LUBRICATION SYSTEM LUBRICATION SYST
LUBRICATION SYSTEM PRECAUTION LUBRI
LUBRICATION - LUBRICATION SYSTEM 18
LUBRICATION - ENGINE OIL 18A-5 7. R
LUBRICATION - OIL FILTER 18A-7 9. T
LUBRICATION - OIL PAN 18A-9 (d) Rem
LUBRICATION - OIL PUMP 18A-11 OIL P
LUBRICATION - OIL PUMP 18A-13 15. R
LUBRICATION - OIL PUMP 18A-15 (d) R
LUBRICATION - OIL PUMP 18A-17 29. U
LUBRICATION - OIL PUMP 18A-19 38. U
IGNITION SYSTEM IGNITION SYSTEM ...
IGNITION SYSTEM COMPONENTS IGNITION
IGNITION - IGNITION MODULE/SPARK PL
STARTING AND CHARGING STARTING AND
STARTING AND CHARGING - STARTING AN
STARTING AND CHARGING - GENERATOR 2
STARTING AND CHARGING - STARTER 20A
STARTING AND CHARGING - BATTERY 20A
A A SINGLE MIRROR IS INOPERATIVE ..
OVERHAUL(CANISTER SOLENOID VALVE)..
电 控 燃 油 喷 射 系 统 -
CONTROL SYSTEM OF ENGINE-CONTROL SY
CONTROL SYSTEM OF ENGINE-ENGINE CON
CONTROL SYSTEM OF ENGINE-REPAIR FOR
模 板 00 FUEL SYSTEM FUEL SYSTEM
FUEL-FUEL SYSTEM 12B-1 FUEL SYSTEM
FUEL-FUEL SYSTEM 12B-3 SYSTEM COMPO
FUEL-FUEL SYSTEM 12B-5 2. Working p
FUEL-FUEL SYSTEM 12B-7 DIAGRAM OF C
FUEL-FUEL SYSTEM 12B-9 Electric VE
FUEL-FUEL SYSTEM 12B-11 Fuel system
FUEL-FUEL INJECTOR (ELECTRONIC) 12B
FUEL INJECTOR (MECHANICAL) DIAGRAM
FUEL-FUEL INJECTOR (MECHANICAL) 12B
FUEL-HIGH PRESSURE FUEL RAIL 12B-27
FUEL-HIGH PRESSURE FUEL RAIL 12B-29
FUEL INJECTION PUMP (VE PUMP) ADJUS
FUEL-FUEL PIPELINE (ENGINE PART) 12
FUEL-FUEL TANK 12B-37 FUEL TANK SER
FUEL-FUEL TANK 12B-39 (h). Remove t
FUEL-FUEL TANK 12B-41 (g). Install
FUEL-FUEL FILTER (COARSE FILTER) 12
FUEL-FUEL FILTER (FINE FILTER) 12B-
驻 车 制 动 - 驻 车 制 动
EMISSION CONTROL--EGR SYSTEM 13B-1
EMISSION CONTROL--EGR SYSTEM 13B-3
EMISSION CONTROL-EGR PIPE 13B-5 (b)
EGR VALVE SERVICE EMISSION CONTROL-
EMISSION CONTROL-EGR VALVE 13B-9 5.
1 INTAKE SYSTEM INTAKE SYSTEM .....
INTAKE-INTAKE SYSTEM 14B-1 INTAKE S
INTAKE-INTAKE SYSTEM 14B-3 WORKING
INTAKE-INTAKE MANIFOLD 14B-5 SERVIC
INTAKE-INTAKE MANIFOLD 14B-7 (l). D
INTAKE-INTAKE MANIFOLD 14B-9 (g). M
INTAKE-INTAKE MANIFOLD 14B-11 (l).
INTAKE-INTAKE PIPELINE 14B-13 REPLA
INTAKE-INTAKE PIPELINE 14B-15 4. Ch
AIR FILTER SERVICE △ Tip: INTAKE-
INTAKE-AIR FILTER 14B-19 (b). (c).
ENGINE MECHANICAL PART ENGINE ASSEM
Disassembly of oil pan and oil Pump
ENGINE MECHANICAL PART-ENGINE ASSEM
ENGINE MECHANICAL PART-ENGINE MAINT
ENGINE MECHANICAL PART-DISASSEMBLY/
ENGINE MECHANICAL PART- PRESERVATIO
ENGINE MECHANICAL PART- DISSASSEBLY
ENGINE MECHANICAL PART-ASSEMBLY OF
ENGINE MECHANICAL PART- DISASSEMBLY
ENGINE MECHANICAL PART- ASSEMBLY OF
ENGINE MECHANICAL PART- INSTALLATIO
ENGINE MECHANICAL PART- CYLINDER HE
ENGINE MECHANICAL PART-ROCKER ASSEM
ENGINE MECHANICAL PART-CYLINDER HEA
ENGINE MECHANICAL PART- VALVE 15B-2
ENGINE MECHANICAL PART-CAMSHAFT AND
ENGINE MECHANICAL PART-PISTON AND C
ENGINE MECHANICAL PART-CRANKSHAFT A
ENGINE MECHANICAL PART-CYLINDER BLO
1 EXHAUST SYSTEM EXHAUST SYSTEM ...
EXHAUST-EXHAUST SYSTEM 16B-1 EXHAUS
EXHAUST-EXHAUST SYSTEM 16B-3 WORKIN
EXHAUST-EXHAUST MANIFOLD 16B-5 SERV
EXHAUST-EXHAUST MANIFOLD 16B-7 (f).
EXHAUST PIPE DIAGRAM OF COMPONENTS
EXHAUST-EXHAUST PIPE 16B-11 (e). Re
EXHAUST-EXHAUST PIPE 16B-13 (d). Pl
COOLING SYSTEM COOLING SYSTEM......
COOLING-COOLING SYSTEM 17B-1 COOLIN
COOLING-COOLING SYSTEM 17B-3 WORKIN
(Fan and water pump pulley chamber
COOLING-THERMOSTAT 17B-7 THERMOSTAT
COOLING-THERMOSTAT 17B-9 (b). Heat
TRANSMISSION BELT SERVICE COOLING-T
COOLING-TRANSMISSION BELT 17B-13 6.
COOLING-PULLEY AND FAN 17B-15 4. Ch
COOLING-WATER PUMP 17B-17 (d). Dism
COOLING-OIL COOLER 17B-19 OIL COOLE
COOLING-EXPANSION TANK 17B-21 EXPAN
COOLING-COOLING PIPELINE 17B-23 COO
COOLING-RADIATOR 17B-25 RADIATOR RE
COOLING-RADIATOR 17B-27 3. Install
润 滑 系 统 - 润 滑 系 统 1
LUBRICATION - OIL DIPSTICK 18B-13 (
LUBRICATION - OIL PAN 18B-15 3. Cle
LUBRICATION - OIL PUMP 18B-17 OIL P
LUBRICATION - OIL PUMP 18B-19 (b).
LUBRICATION - OIL PUMP 18B-21 (b).
LUBRICATION - OIL FILTER 18B-23 (b)
IGNITION - IGNITION SYSTEM 19-1 IGN
IGNITION - IGNITION SYSTEM 19-3 CHE
IGNITION - SPARK PLUG 19-5 SERVICE
IGNITION - SPARK PLUG 19-7 4. Assem
IGNITION - CRANKSHAFT POSITION SENS
电 器 系 统 - 发 电 机 14- S
STARTING AND CHARGING - STARTER 20B
STARTING AND CHARGING - BATTERY ASS
STARTING AND CHARGING - USE OF MAIN
SUPERCHARGER SUPERCHARGING SYSTEM .
SUPERCHARGING SYSTEM-SUPERCHARGING
SUPERCHARGING SYSTEM-TURBOCHARGER 2
ENGINE CONTROL SYSTEM DIESEL ENGINE
ENGINE CONTROL SYSTEM - DIESEL ENGI
ENGINE CONTROL SYSTEM - ACCELEARTOR
FUEL - FUEL SYSTEM 12C-3 FUEL TUBE
FUEL - FUEL SYSTEM 12C-5 12C 1 Bolt
FUEL - FUEL TANK ASSY 12C-7 (g) (h)
FUEL - DIESEL FILTER ASSY 12C-9 DIE
FUEL - FUEL LEVEL SENSOR AND BRACKE
FUEL - FUEL FILLER CAP 12C-15 FUEL
EMISSION CONTROL - DIESEL OXIDATION
INTAKE AIR - INTAKE AIR SYSTEM 14C-
INTAKE AIR - AIR FILTER ASSY 14C-7
INTAKE AIR - AIR FILTER ASSY 14C-9
INTAKE AIR - INTERCOOLER INTAKE AIR
ENGINE MECHANICAL - ENGINE ASSY 15C
ENGINE MECHANICAL - ENGINE ACCESSOR
EXHAUST PIPE COMPONENTS EXHAUST - E
EXHAUST - EXHAUST PIPE 16C-3 REPLAC
EXHAUST - EXHAUST PIPE 16C-5 10. IN
COOLING SYSTEM COOLING PRECAUTION C
COOLING - COOLING SYSTEM 17C-3 17C
COOLING - COOLING SYSTEM 17C-5 ON-V
COOLING - COOLANT 17C-7 COOLANT REP
COOLING - RESERVIOR 17C-9 RESERVIOR
COOLING - COOLING FAN ASSY 17C-11 C
COOLING - COOLING FAN ASSY 17C-13 (
COOLING - RADIATOR 17C-15 (c) (d) P
COOLING - RADIATOR 17C-17 11. INSTA
LUBRICATION - ENGINE OIL 18C-3 13.
LUBRICATION - OIL FILTER 18C-5 10.
LUBRICATION - OIL PUMP 18C-7 OIL PU
STARTING AND CHARGING - STARTER 20C
STARTING AND CHARGING - BATTERY 20C
SUSPENSION SYSTEM FRONT SUSPENSION.
FRONT SUSPENSION FRONT SUSPENSION..
FRONT SUSPENSION SUSPENSION PRECAUT
FRONT SUSPENSION - FRONT SUSPENSION
FRONT SUSPENSION - FRONT WHEEL ALIG
FRONT SUSPENSION - FRONT SHOCK ABSO
FRONT SUSPENSION - TORSION BAR 31-1
FRONT SUSPENSION - UPPER CONTROL AR
FRONT SUSPENSION - LOWER CONTROL AR
FRONT SUSPENSION - STABILIZER BAR 3
FRONT SUSPENSION - STRUT ROD 31-23
REAR SUSPENSION REAR SUSPENSION ...
REAR SUSPENSION - REAR SUSPENSION 3
REAR SUSPENSION - REAR SHOCK ABSORB
REAR SUSPENSION - REAR LEAF SPRING
TYRE AND WHEEL TIRE AND WHEEL ASSY
TIRE AND WHEEL ASSY WHEEL AND TIRE
WHEEL AND TIRE - TIRE AND WHEEL ASS
WHEEL AND TIRE - REAR WHEEL AND TIR
AXLE AND PROPELLER SHAFT PROPELLER
AXLE AND PROPELLER SHAFT - PROPELLE
AXLE AND PROPELLER SHAFT - U-JOINT
AXLE AND PROPELLER SHAFT - CENTER S
AXLE AND PROPELLER SHAFT - AXLE HUB
AXLE AND PROPELLER SHAFT - FRONT HU
AXLE AND PROPELLER SHAFT - REAR AXL
AXLE AND PROPELLER SHAFT - STEERING
AXLE AND PROPELLER SHAFT - FINAL DR
AXLE SHAFT ASSY OVERHAUL AXLE AND P
AXLE AND PROPELLER SHAFT - DRIVE PI
BRAKING SYSTEMS BRAKE SYSTEM ......
BRAKE BRAKE SYSTEM ................
BRAKE SYSTEM PRECAUTION BRAKE - BRA
BRAKE - PROBLEM SYMPTOMS TABLE 35-3
BRAKE - BRAKE FLUID 35-5 3. BLEED B
BRAKE - BRAKE PEDAL 35-7 ADJUSTMENT
BRAKE - BRAKE PEDAL 35-9 REPLACEMEN
BRAKE - BRAKE PEDAL 35-11 (d) Remov
BRAKE - BRAKE PEDAL 35-13 10. INSTA
BRAKE - VACUUM BOOSTER WITH BRAKE M
BRAKE - VACUUM BOOSTER LINE 35-19 3
BRAKE - FRONT BRAKE 35-21 (b) Remov
BRAKE - FRONT BRAKE 35-23 (c) Remov
BRAKE - FRONT BRAKE 35-25 14. INSTA
BRAKE - REAR BRAKE 35-27 OVERHAUL 1
BRAKE - REAR BRAKE 35-29 (b) Remove
BRAKE - REAR BRAKE 35-31 12. INSPEC
BRAKE - REAR BRAKE 35-33 17. INSTAL
BRAKE - REAR BRAKE 35-35 22. INSPEC
BRAKE - ABS ACTUATOR 35-37 ABS ACTU
BRAKE - ABS ACTUATOR 35-39 11. CHEC
BRAKE - WHEEL SPEED SENSOR 35-41 4.
PARKING BRAKE PARKING BRAKE SYSTEM.
PARKING BRAKE - PARKING BRAKE SYSTE
PARKING BRAKE - FRONT PARKING BRAKE
PARKING BRAKE - REAR PARKING BRAKE
PROBLEM SYMPTOMS TABLE(STARTING AND
TRANSMISSION TRANSMISSION OPERATION
TRANSMISSION - TRANSMISSION OPERATI
TRANSMISSION - TRANSMISSION ASSY(YA
CLUTCH CASE DIAGRAM OF COMPONENTS T
TRANSMISSION - CLUTCH CASE 41-41 (g
REAR PART ASSEMBLY DIAGRAM OF COMPO
TRANSMISSION - REAR PART ASSEMBLY 4
TRANSMISSION - FORK SHAFT ASSEMBLY
INPUT SHAFT ASSEMBLY DIAGRAM OF COM
TRANSMISSION - INPUT SHAFT ASSEMBLY
TRANSMISSION - OUTPUT SHAFT ASSEMBL
TRANSMISSION - COUNTER SHAFT ASSEMB
REVERSE SHAFT ASSEMBLY DIAGRAM OF C
TRANSMISSION - REVERSE SHAFT ASSEMB
TRANSMISSION - TRANSMISSION ASSY(TA
CLUTCH CLUTCH SYSTEM ..............
CLUTCH - CLUTCH SYSTEM 42-1 CLUTCH
CLUTCH - CLUTCH FLUID 42-3 CLUTCH F
CLUTCH - CLUTCH PEDAL 42-5 ADJUSTME
CLUTCH - CLUTCH PEDAL 42-7 7. INSTA
CLUTCH - VACUUM BOOSTER WITH CLUTCH
CLUTCH - CLUTCH SLAVE CYLINDER 42-1
CLUTCH SUB - ASSY COMPONENTS CLUTCH
CLUTCH - CLUTCH SUB - ASSY 42-15 4.
CLUTCH - CLUTCH SUB - ASSY 42-17 9.
CLUTCH - CLUTCH SUB - ASSY 42-19 15
STEERING COLUMN STEERING SYSTEM....
STEERING SYSTEM COLUMN PRECAUTION S
STEERING COLUMN - STEERING SYSTEM 5
STEERING COLUMN - STEERING WHEEL AS
STEERING COLUMN - COMBINATION SWITC
STEERING COLUMN - STEERING COLUMN A
STEERING COLUMN - STEERING PROPELLE
POWER STEERING POWER STEERING SYSTE
POWER STEERING - POWER STEERING SYS
POWER STEERING - ON-VEHICLE INSPECT
POWER STEERING - STEERING FLUID 52-
POWER STEERING - POWER STEERING PUM
POWER STEERING - DIESEL VEHICLES (I
POWER STEERING - POWER STEERING LIN
POWER STEERING - STEERING GEAR ASSY
POWER STEERING - STEERING FLUID RES
HEATER AND AIR CONDITIONING HEATER
HEATER AND AIR CONDITIONING - HEATE
HEATER AND AIR CONDITIONING - ON-VE
HEATER AND AIR CONDITIONING - REFRI
HEATER AND AIR CONDITIONING - COMPR
HEATER AND AIR CONDITIONING - MULTI
HEATER AND AIR CONDITIONING - REAR
HEATER AND AIR CONDITIONING - FRONT
HEATER AND AIR CONDITIONING - (n) F
HEATER AND AIR CONDITIONING - TOP E
HEATER AND AIR CONDITIONING - RECIR
HEATER AND AIR CONDITIONING - BLEND
HEATER AND AIR CONDITIONING - MODE
HEATER AND AIR CONDITIONING - COOLI
HEATER AND AIR CONDITIONING - CONDE
HEATER AND AIR CONDITIONING - A/C R
SUPPLEMENTAL RESTRAINT SYSTEM SUPPL
SUPPLEMENTAL RESTRAINT SYSTEM - SUP
SUPPLEMENTAL RESTRAINT SYSTEM - HOR
SUPPLEMENTAL RESTRAINT SYSTEM - CLO
SUPPLEMENTAL RESTRAINT SYSTEM - RCM
SEAT BELT SEAT BELT SYSTEM ........
SEAT BELT - SEAT BELT SYSTEM 63-1 S
SEAT BELT - SEAT BELT WARNING SYSTE
SEAT BELT - PASSENGER SEAT BELT 63-
SEAT BELT - SEAT BELT CATCH ASSY 63
SEAT BELT - RETRACTOR ASSY 63-15 RE
SEAT BELT - RETRACTOR ASSY 63-17 5.
SEAT BELT - RETRACTOR ASSY 63-19 (e
SEAT BELT - RETRACTOR ASSY 63-21 (g
LIGHTING LIGHTING SYSTEM...........
LIGHTING SYSTEM PRECAUTION 1. LIGHT
LIGHTING - FRONT COMBINATION LAMP A
LIGHTING - FRONT FOG LAMP ASSY 64-9
LIGHTING - REAR COMBINATION LAMP AS
LIGHTING - LICENCE LAMP ASSY 64-15
LIGHTING - FRONT DOME LIGHT ASSY 64
LIGHTING - MIDDLE DOME LIGHT ASSY 6
LIGHTING - REAR DOME LIGHT ASSY 64-
LIGHTING - STEP LAMP ASSY 64-25 STE
LIGHTING - COMBINATION SWITCH ASSY
WIPER AND WASHER WIPER AND WASHER S
WIPER AND WASHER - WIPER AND WASHER
WIPER AND WASHER - WIPER ASSY 65-5
WIPER AND WASHER - WIPER ASSY 65-7
WIPER AND WASHER - WIPER LINK WITH
WIPER AND WASHER - WIPER BLADE WITH
WIPER AND WASHER - WASHER NOZZLE 65
WIPER AND WASHER - WASHER ASSY 65-1
WIPER AND WASHER - WASHER PUMP ASSY
AUDIO SYSTEM AUDIO SYSTEM..........
AUDIO SYSTEM SYSTEM COMPONENTS AUDI
AUDIO SYSTEM - MULTI-MEDIA AND AIR-
AUDIO SYSTEM - FRONT SPEAKER ASSY 6
AUDIO SYSTEM - MIDDLE SPEAKER ASSY
AUDIO SYSTEM - REAR SPERKER ASSY 66
AUDIO SYSTEM - TELESCOPIC ANTENNA A
AUDIO SYSTEM - ELECTRIC DEVICE ACCE
WIRING HOW TO USE THIS MANUAL......
WIRING - HOW TO USE THIS MANUAL 71-
WIRING - WIRING DIAGRAM 71-19 71 71
WIRING - WIRING DIAGRAM 71-21 71 71
WIRING - WIRING DIAGRAM 71-23 Servi
WIRING - WIRING DIAGRAM 71-25 71 71
WIRING - WIRING DIAGRAM 71-27 71 71
WIRING - WIRING DIAGRAM 71-29 • E
WIRING - WIRING DIAGRAM 71-31 I110
WIRING - WIRING DIAGRAM 71-33 71 71
WIRING - WIRING DIAGRAM 71-35 Syste
WIRING - WIRING DIAGRAM 71-37 START
WIRING - WIRING DIAGRAM 71-39 CHARG
WIRING - WIRING DIAGRAM 71-41 ANTI-
WIRING - WIRING DIAGRAM 71-43 I110
WIRING - WIRING DIAGRAM 71-45 71 71
WIRING - WIRING DIAGRAM 71-47 Syste
WIRING - WIRING DIAGRAM 71-49 Code
WIRING - WIRING DIAGRAM 71-51 Syste
WIRING - WIRING DIAGRAM 71-53 Syste
WIRING - WIRING DIAGRAM 71-55 Groun
WIRING - WIRING DIAGRAM 71-57 Syste
WIRING - WIRING DIAGRAM 71-59 STOP
WIRING - WIRING DIAGRAM 71-61 BACK-
WIRING - WIRING DIAGRAM 71-63 TURN
WIRING - WIRING DIAGRAM 71-65 F006
WIRING - WIRING DIAGRAM 71-67 Syste
WIRING - WIRING DIAGRAM 71-69 INTER
WIRING - WIRING DIAGRAM 71-71 Syste
WIRING - WIRING DIAGRAM 71-73 ILLUM
WIRING - WIRING DIAGRAM 71-75 Syste
WIRING - WIRING DIAGRAM 71-77 WIPER
WIRING - WIRING DIAGRAM 71-79 Code
WIRING - WIRING DIAGRAM 71-81 Servi
WIRING - WIRING DIAGRAM 71-83 POWER
WIRING - WIRING DIAGRAM 71-85 COMMU
WIRING - WIRING DIAGRAM 71-87 REVER
WIRING - WIRING DIAGRAM 71-89 Code
WIRING - WIRING DIAGRAM 71-91 Syste
WIRING - WIRING DIAGRAM 71-93 WINDO
WIRING - WIRING DIAGRAM 71-95 Code
WIRING - WIRING DIAGRAM 71-97 71 71
WIRING - WIRING DIAGRAM 71-99 71 71
WIRING - WIRING DIAGRAM 71-101 •
WIRING - WIRING DIAGRAM 71-103 ANTI
WIRING - WIRING DIAGRAM 71-105 Syst
WIRING - WIRING DIAGRAM 71-107 Code
WIRING - WIRING DIAGRAM 71-109 Syst
WIRING - WIRING DIAGRAM 71-111 Syst
WIRING - CONNECTOR VIEWS 71-113 71
WIRING - CONNECTOR VIEWS 71-115 71
WIRING - CONNECTOR VIEWS 71-117 71
WIRING - CONNECTOR VIEWS 71-119 A03
WIRING - CONNECTOR VIEWS 71-121 A10
WIRING - CONNECTOR VIEWS 71-123 A10
WIRING - CONNECTOR VIEWS 71-125 B -
WIRING - CONNECTOR VIEWS 71-127 D -
WIRING - CONNECTOR VIEWS 71-129 71
WIRING - CONNECTOR VIEWS 71-131 E00
WIRING - CONNECTOR VIEWS 71-133 E00
WIRING - CONNECTOR VIEWS 71-135 E01
WIRING - CONNECTOR VIEWS 71-137 71
WIRING - CONNECTOR VIEWS 71-139 71
WIRING - CONNECTOR VIEWS 71-141 E10
WIRING - CONNECTOR VIEWS 71-143 F00
WIRING - CONNECTOR VIEWS 71-145 71
WIRING - CONNECTOR VIEWS 71-147 71
WIRING - CONNECTOR VIEWS 71-149 71
WIRING - CONNECTOR VIEWS 71-151 B15
WIRING - CONNECTOR VIEWS 71-153 I00
WIRING - CONNECTOR VIEWS 71-155 I01
WIRING - CONNECTOR VIEWS 71-157 71
WIRING - CONNECTOR VIEWS 71-159 71
WIRING - CONNECTOR VIEWS 71-161 I10
WIRING - CONNECTOR VIEWS 71-163 71
WIRING - CONNECTOR VIEWS 71-165 71
WIRING - CONNECTOR VIEWS 71-167 71
WIRING - CONNECTOR VIEWS 71-169 L -
WIRING - CONNECTOR VIEWS 71-171 N -
WIRING - CONNECTOR VIEWS 71-173 P -
WIRING - CONNECTOR VIEWS 71-175 R -
WIRING - CONNECTOR VIEWS 71-177 T -
WIRING - CONNECTOR VIEWS 71-179 V -
WIRING - CONNECTOR VIEWS 71-181 71
WIRING - CONNECTOR VIEWS 71-183 71
WIRING - CONNECTOR VIEWS 71-185 X -
WIRING - WIRE HARNESS & CONNECTOR L
WIRING(RHD) HOW TO USE THIS MANUAL.
WIRING(RHD) - HOW TO USE THIS MANUA
WIRING DIAGRAM POWER SOURCE WIRING(
WIRING(RHD) - WIRING DIAGRAM 71-21
WIRING(RHD) - WIRING DIAGRAM 71-23
WIRING(RHD) - WIRING DIAGRAM 71-25
WIRING(RHD) - WIRING DIAGRAM 71-27
WIRING(RHD) - WIRING DIAGRAM 71-29
WIRING(RHD) - WIRING DIAGRAM 71-31
WIRING(RHD) - WIRING DIAGRAM 71-33
WIRING(RHD) - WIRING DIAGRAM 71-35
WIRING(RHD) - WIRING DIAGRAM 71-37
WIRING(RHD) - WIRING DIAGRAM 71-39
WIRING(RHD) - WIRING DIAGRAM 71-41
WIRING(RHD) - WIRING DIAGRAM 71-43
WIRING(RHD) - WIRING DIAGRAM 71-45
WIRING(RHD) - WIRING DIAGRAM 71-47
WIRING(RHD) - WIRING DIAGRAM 71-49
WIRING(RHD) - WIRING DIAGRAM 71-51
WIRING(RHD) - WIRING DIAGRAM 71-53
WIRING(RHD) - WIRING DIAGRAM 71-55
WIRING(RHD) - WIRING DIAGRAM 71-57
WIRING(RHD) - WIRING DIAGRAM 71-59
WIRING(RHD) - WIRING DIAGRAM 71-61
WIRING(RHD) - WIRING DIAGRAM 71-63
WIRING(RHD) - WIRING DIAGRAM 71-65
WIRING(RHD) - WIRING DIAGRAM 71-67
WIRING(RHD) - WIRING DIAGRAM 71-69
WIRING(RHD) - WIRING DIAGRAM 71-71
WIRING(RHD) - WIRING DIAGRAM 71-73
WIRING(RHD) - WIRING DIAGRAM 71-75
WIRING(RHD) - WIRING DIAGRAM 71-77
WIRING(RHD) - WIRING DIAGRAM 71-79
WIRING(RHD) - WIRING DIAGRAM 71-81
WIRING(RHD) - WIRING DIAGRAM 71-83
WIRING(RHD) - WIRING DIAGRAM 71-85
WIRING(RHD) - WIRING DIAGRAM 71-87
WIRING(RHD) - WIRING DIAGRAM 71-89
WIRING(RHD) - WIRING DIAGRAM 71-91
WIRING(RHD) - WIRING DIAGRAM 71-93
WIRING(RHD) - WIRING DIAGRAM 71-95
WIRING(RHD) - WIRING DIAGRAM 71-97
WIRING(RHD) - WIRING DIAGRAM 71-99
WIRING(RHD) - WIRING DIAGRAM 71-101
WIRING(RHD) - WIRING DIAGRAM 71-103
WIRING(RHD) - CONNECTOR VIEWS 71-10
WIRING(RHD) - CONNECTOR VIEWS 71-11
WIRING(RHD) - CONNECTOR VIEWS 71-12
WIRING(RHD) - CONNECTOR VIEWS 71-13
WIRING(RHD) - CONNECTOR VIEWS 71-14
WIRING(RHD) - CONNECTOR VIEWS 71-15
WIRING(RHD) - CONNECTOR VIEWS 71-16
WIRING(RHD) - WIRE HARNESS & CONNEC
COMMUNICATION SYSTEM HORN .........
COMMUNICATION SYSTEM - HORN 81-1 HO
COMMUNICATION SYSTEM - HORN 81-3 RE
COMMUNICATION SYSTEM - MULTI-MEDIA
REVERSE RADAR PROBLEM SYMPTOMS TABL
COMMUNICATION SYSTEM - REVERSE RADA
COMMUNICATION SYSTEM - ASTERN IMAGE
WINDSHIELDS, MIRRORS & GLASS WINDOW
WINDSHIELD/WINDOWGLASS/REAR VIEW MI
INSTRUMENT PANEL INSTRUMENT CLUSTER
INSTRUMENT PANEL - INSTRUMENT CLUST
INSTRUMENT PANEL - DASHBOARD 83-5 D
INSTRUMENT PANEL - DASHBOARD 83-7 R
INSTRUMENT PANEL - DASHBOARD 83-9 1
INSTRUMENT PANEL - DASHBOARD 83-11
INSTRUMENT PANEL - DASHBOARD 83-13
INSTRUMENT PANEL - DASHBOARD 83-15
SEATS SEATS........................
SEAT - SEAT 84-1 SEATS PRECAUTION W
SEAT - DRIVER / ASSISTANT DRIVER SE
SEAT - PASSENGER SEAT 84-15 PASSENG
SEAT - PASSENGER SEAT 84-17 (j) Pre
SEAT - PASSENGER SEAT 84-19 (b) (c)
SEAT - PASSENGER SEAT 84-21 PASSEBG
SEAT - PASSENGER SEAT 84-23 PASSEBG
DOOR LOCKS FRONT DOOR LOCKS .......
FRONT DOOR LOCKS DOOR LOCKS COMPONE
DOOR LOCKS - FRONT DOOR LOCKS 85-3
DOOR LOCKS - FRONT DOOR LOCKS 85-5
SLIDING DOOR LOCKS COMPONENTS DOOR
DOOR LOCKS - SLIDING DOOR LOCKS 85-
DOOR LOCKS - REAR HATCH LOCK 85-13
DOOR LOCKS - REAR HATCH LOCK 85-15
ENGINE HOOD LOCK COMPONENTS DOOR LO
DOOR LOCKS - ALARM CONTROLLER 85-19
SLIDING ROOF SLIDING ROOF ASSY ....
SLIDING ROOF ASSY SLIDING ROOF PROB
SLIDING ROOF - SLIDING ROOF ASSY 86
DOORS & ENGINE HOOD ENGINE HOOD ...
DOORS - ENGINE HOOD 87-1 ENGINE HOO
DOORS - ENGINE HOOD 87-3 REPLACEMEN
DOORS - FRONT DOOR 87-5 ADJUSTMENT
DOORS - FRONT DOOR 87-7 REPLANCEMEN
SLIDING DOOR COMPONENTS DOORS - SLI
DOORS - SLIDING DOOR 87-11 87 87 Up
DOORS - SLIDING DOOR 87-13 REPLACEM
REAR HATCH COMPONENTS DOORS - REAR
DOORS - REAR HATCH 87-17 2. ADJUST
DOORS - REAR HATCH 87-19 5. INSTALL
EXTERIOR AND INTERIOR TRIM FRONT GR
FRONT GRILLE EXTERIOR AND INTERIOR
FRONT BUMPER ASSY COMPONENTS EXTERI
EXTERIOR AND INTERIOR TRIM - FRONT
EXTERIOR AND INTERIOR TRIM - WHEEL
EXTERIOR AND INTERIOR TRIM - REAR B
SUN VISOR ASSY COMPONENTS EXTERIOR
STEP BOARD COMPONENTS EXTERIOR AND
EXTERIOR AND INTERIOR TRIM - STEP B
EXTERIOR AND INTERIOR TRIM - VEHICL
EXTERIOR AND INTERIOR TRIM - QUARTE
EXTERIOR AND INTERIOR TRIM - FLOOR
ROOF PANEL COMPONENTS EXTERIOR AND
EXTERIOR AND INTERIOR TRIM - ROOF P
VEHICLE CONTROL SYSTEM IGNITION SWI
VEHICLE CONTROL SYSTEM - IGNITION S
INDEX (ORGNIZED ALPHABETICALLY) A A
R - REAR BUMPER WIRE HARNESS(WIRE H
Extended embed settings
Inappropriate
You have already flagged this document. Thank you, for helping us keep this platform clean. The editors will have a look at it as soon as possible.
Delete template?
Are you sure you want to delete your template?
DOWNLOAD ePAPER
This ePaper is currently not available for download. You can find similar magazines on this topic below under ‘Recommendations’.
Save as template?

- Help & Support
- tuxbrain.com
- ooomacros.org
- nubuntu.org
- Terms of service
- Privacy policy
- Cookie policy
- Cookie settings

Choose your language
Main languages
Further languages
- Bahasa Indonesia
Performing this action will revert the following features to their default settings:
Hooray! Your file is uploaded and ready to be published.
Saved successfully!
Ooh no, something went wrong!
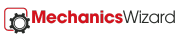
Peugeot Traveller Dashboard Warning Lights Meaning
Navigating through the sea of dashboard lights on your Peugeot Traveller can sometimes feel like cracking a secret code. From the moment you turn the key, a symphony of lights illuminates your dashboard, each with its unique message and level of urgency. But what do they all mean?
Among these, the indicator lights play a crucial role, serving as the vehicle’s way of communicating vital information to you. Whether it’s a gentle reminder to buckle up or a stern warning about engine trouble, each dashboard light carries its significance.
However, interpreting these dashboard symbols can be a manageable task. With a little knowledge and attention to detail, you can master the language of your Peugeot Traveller’s dashboard lights, ensuring a safer and smoother driving experience. So, buckle up, and let’s dive into the world of dashboard enlightenment!
Hybrid Service Alert Warning Light
The appearance of a wrench intertwined with a lightning bolt (or zig-zag pattern) on your dashboard is a clear indicator that the hybrid system of your Peugeot Traveller requires attention. Various elements could trigger this alert, from the vehicle’s mileage and age to the system identifying a potential malfunction. To address this issue promptly and accurately, it is highly recommended to seek the expertise of a mechanic specializing in Peugeot Traveller vehicles, as they possess the necessary skills and knowledge to handle the intricate nature of hybrid systems.
Power Steering Alert
Observing a red steering wheel icon accompanied by an exclamation point on your dashboard typically signals a problem with the electric power-assisted steering system of your Peugeot Traveller. In such a scenario, it is advisable to safely pull over, turn off the vehicle entirely, and then restart it. If the warning light persists upon restarting the vehicle, it is crucial to contact a skilled mechanic or visit a Peugeot Traveller dealership for professional assistance.
Security/Anti-Theft Alert
A solitary red dot illuminating your dashboard’s instrument cluster may indicate a malfunction within the security or anti-theft system, potentially affecting components like the immobilizer or alarm system (if installed). If this light remains active while driving, it is a clear sign of an issue requiring inspection and resolution by a certified mechanic.
Airbag Alert
The visual cue of a passenger encircled by a large, illuminated red circle on your dashboard is your vehicle’s way of alerting you to a potential problem with one or more airbags in your Peugeot Traveller. Addressing this issue promptly is vital, and it is recommended to take the vehicle to a qualified mechanic or an authorized Peugeot Traveller dealership.
Seat Belt Reminder
An image of a passenger restrained by a belt, set against a red light on your dashboard, serves as a reminder to ensure all passengers have securely fastened their seat belts. This feature operates through a weight-detection system in the seats, meaning items like shopping bags or luggage could also trigger the alert. Additionally, an auditory warning is typically activated once the vehicle is in motion.
Transmission Oil Overheat Alert
A red warning light on your dashboard resembling a thermometer inside a wavy circle (or possibly flower petals) indicates an overheating issue with your transmission oil. This could stem from aged oil that is no longer performing effectively or from your Peugeot Traveller ‘s transmission being subjected to excessive strain. It is imperative to pull over at the earliest opportunity to let the oil cool down before continuing your journey. Should the issue persist, professional help from a trained mechanic or a Peugeot Traveller dealership is recommended.
Engine Temperature Alert
A red backlight illuminating a series of waves with a floating thermometer above them on your dashboard is a critical alert from your Peugeot Traveller, warning that the engine temperature is excessively high. The waves symbolize the engine’s coolant, typically monitored for temperature. Potential causes for this issue range from overworking the engine to a leak or other malfunction. Immediate action is required:
- Allow the engine to cool.
- Seek assistance from a Peugeot Traveller dealership or a trained mechanic if the problem is unresolved.
Oil Temperature Alert
When an oil can icon accompanied by a floating thermometer appears on your dashboard, it is a clear signal from your Peugeot Traveller that the engine oil is excessively hot. This warning is particularly prevalent in performance-oriented models, which are designed to endure rigorous driving conditions. The overheating could be attributed to vigorous acceleration or, in more severe cases, an oil loss. Given that this is a red warning light, it is imperative to pull over immediately and allow the engine to cool down. If the issue persists, seeking assistance from a professional mechanic is advisable.
Brake System Alert
The appearance of the brake warning light may vary depending on the region where your Peugeot Traveller was purchased. Generally, the brake warning is displayed as the word “BRAKE,” but in Canada, it may be represented by an exclamation point encircled by brake pads. The latter can be misleading as it also resembles the handbrake symbol found in many vehicles. Regardless of the region or the specific icon displayed, a red brake warning light necessitates an immediate response: pull over and halt the vehicle. The issue could range from fluid pressure anomalies to malfunctions in brake assistance programs. It is crucial to seek professional help from a Peugeot Traveller dealership or an independent garage when this warning light is illuminated.
Charging System Alert
A red warning light shaped like a battery (or possibly a Lego brick), with a positive and a negative symbol on opposite sides, indicates a charging system malfunction. If this light illuminates your dashboard, it means the battery is not receiving a charge from the engine. Given the severity of this issue, as indicated by the red light, it is essential to stop driving and pull over as soon as possible. Common causes include a malfunctioning alternator or loose wires connecting to the battery. Continuing to drive with a potentially depleted battery could lead to a loss of critical vehicle systems, posing a severe risk. In such cases, it is advisable to seek immediate assistance from an independent mechanic or a Peugeot Traveller dealership.
Oil Pressure Alert
The red warning light in the shape of Aladdin’s lamp, standing alone, signals low oil pressure in the engine. This could be due to a rapid oil leak from beneath the engine or oil being burned inside the engine and expelled through the exhaust. As this is a critical alert, it is not recommended to continue driving until the light goes off. Operating the vehicle with the low oil pressure light on can cause damage to the engine due to inadequate lubrication, potentially leading to overheating and excessive wear.
Master Warning Light
A triangular warning symbol with a central exclamation mark is a universal indicator of a significant vehicle fault. If this warning light briefly illuminates, it could signal that the vehicle momentarily lost traction, prompting an automatic correction. However, if the light remains on after restarting the vehicle, it is crucial to seek assistance from a Peugeot Traveller dealership or a qualified mechanic.
Adaptive Cruise Control Alert
A warning light featuring a speedometer and a car, accompanied by an exclamation mark, pertains to a potential fault in the adaptive cruise control system. Alternatively, this alert may be displayed using “ACC” in a yellow or red hue. This system relies on radars and cameras to monitor the traffic ahead and adjust the vehicle’s speed accordingly. If this warning light activates, attempt restarting the vehicle to see if the issue resolves. If the problem persists, professional assistance from a trained mechanic or a Peugeot Traveller dealership is recommended.
Lane Sense Alert
A warning light resembling a car veering across broken or solid lines is your vehicle’s way of indicating a potential lane departure. An auditory signal may accompany this alert, and it functions properly only when the vehicle’s camera or other technology can detect lane markings. Certain Peugeot Traveller models are equipped with advanced features that enable the vehicle to autonomously adjust steering to ensure the vehicle remains centered within its current lane.
Forward Collision Detection Disabled
When a warning light on your dashboard depicts two cars with a star (symbolizing a collision) above the word “OFF,” it indicates that the forward collision detection system is deactivated. Unless you have intentionally turned off this system, it is advisable to consult with a trained mechanic or visit a Peugeot Traveller dealership to resolve this issue and reactivate this crucial safety feature.
Forward Collision Detection Alert
A warning light showing two cars nearby, with one car marked by an exclamation point and an arrow, pertains to the forward collision detection system. This system alerts you to a potential collision risk, initiating adjustments to the brakes, suspension, and seatbelts to mitigate the threat. If this warning light remains on continuously, it is crucial to seek assistance from a trained mechanic or a Peugeot Traveller dealership.
Key-Fob Detection Indicator
The image of a key surrounded by waves on your dashboard indicates that the vehicle’s key fob has been detected, signifying that the car is ready to be started, especially if it is equipped with a keyless system. If this indicator fails to appear when the key fob is inside the car, the fob’s battery may be depleted.
A conspicuous warning light featuring the letters “ABS” encircled by a ring and accompanied by a representation of brake pads serves to alert you of a malfunction in the ABS (Anti-lock Braking System). While the vehicle’s standard braking functionality might remain unaffected, it is essential to address this issue promptly by seeking the expertise of a trained mechanic or visiting a Peugeot Traveller dealership.
Stability/Traction Control Deactivated
Like the stability (or traction) control warning symbol, this version includes the word “OFF” to indicate that the system is currently disabled. Deactivating stability control typically requires more than an accidental button press; it usually necessitates holding down a button for several seconds. If you have not intentionally turned off this system, the vehicle may be experiencing a malfunction, necessitating a visit to a trained mechanic for a thorough inspection and resolution.
Stability Control Alert
When the stability control system activates, you may notice an orange or yellow warning light on your dashboard, depicting a car with swirls beneath it. This is typically accompanied by an auditory alert, signaling that the vehicle has intervened to regain traction. If the light remains illuminated despite no apparent traction issues, this could indicate a malfunction within the system of your Peugeot Traveller. In such cases, it is advisable to seek assistance from a trained mechanic or an authorized Peugeot Traveller dealership, especially if the warning light persists.
Low Fuel Indicator Warning Light
An orange or yellow light shaped like an old-fashioned fuel pump signals that your vehicle is running low on fuel. Should this light continue to illuminate even after refueling, consult with a trained mechanic or visit your dealership to address any potential issues.
Low Washer Fluid Warning
A warning light resembling a windshield (or an open book) with a water fountain in the middle is your vehicle’s way of informing you that the washer fluid is running low. Refilling is typically straightforward, with the refill cap under the hood marked with a similar symbol. If the light does not extinguish after topping up and waiting a few minutes, professional assistance is recommended.
Loose Gas Cap Warning
A warning light showing a car with a segment removed and a screw hovering nearby indicates that the gas cap may be loose. After ensuring that the gas cap is securely fastened, if the light remains on, a mechanic should inspect the vehicle for potential issues. A loose gas cap or a leak in the system can cause pressure irregularities in modern engines, particularly diesel-powered ones, potentially leading to erratic engine behavior.
Check Engine Light Alert
The check engine light is a multifaceted warning that can signal anything from a minor issue to a significant problem with your Peugeot Traveller. The symbol may appear as an engine outline, with or without text inside. Upon noticing this light, it is recommended to pull over and restart the engine, as transient fluctuations can sometimes trigger the alert unnecessarily. A flashing light, as opposed to a steady one, indicates a severe issue that necessitates immediate attention, and the vehicle should be turned off as quickly as safely possible. Utilizing an OBD2 reader to retrieve a fault code is a common diagnostic step, which can be done by a mechanic or yourself with an affordable reader.
Hybrid Power Limitation Alert
A yellow or orange light featuring a turtle inside a circle is an alert from your Peugeot Traveller indicating that the hybrid system is low on power. This could result from depleted batteries due to extensive use or, more concerning, damage to the batteries themselves. Suppose you notice this warning light staying on longer than usual. In that case, it is advisable to have the hybrid system of your vehicle thoroughly tested to ensure everything is functioning as it should.
Electronic Throttle Control Alert
A warning light depicting a lightning bolt (zig-zag) situated between two curved lines signals a potential issue with the electronic throttle control system in your Peugeot Traveller. The first course of action to try to resolve this issue is to pull over and restart the vehicle safely. If the problem persists, it is crucial to consult with a trained mechanic to ensure safe and optimal vehicle performance.
Tire Pressure Alert
Most Peugeot Traveller vehicles today have a tire pressure monitoring system, represented by an orange light on the dashboard’s instrument cluster. This light illuminates when the tire pressure drops, signaling the need for immediate attention. A flashing indicator suggests a rapid decrease in pressure, necessitating an urgent response to pull over and address the issue. The loss of tire pressure could stem from various factors, including a puncture, wear and tear around the rim, or sudden temperature changes. Neglecting to maintain proper tire pressure can lead to dangerous driving conditions, impacting both braking and handling, with the worst-case scenario being a tire burst at high speeds. You must inflate the tires or seek professional assistance from a tire shop or a Peugeot Traveller service center.
Auto Stop-Start Alert
An illuminated circle featuring an arrow and the letter “A” in the center, or possibly an exclamation mark, indicates a malfunction within the auto stop-start system of your vehicle. While the car might still function normally, it is advisable to restart the vehicle to see if the issue is resolved. If the warning light remains, professional assistance should be sought. However, it’s important to note that the vehicle’s overall performance may be fine, apart from losing this specific fuel economy feature.
Cruise Control Indicator
A green warning light showing a speedometer with an arrow pointing towards it indicates that the cruise control system is activated. Depending on the Model, this symbol may also appear in yellow, accompanied by an icon of a car shape next to it, signifying the system’s active status.
High Beam Indicator
The vehicle’s high beam lights are on when a blue (or sometimes yellow) semi-circle with straight lines emanating from the side is displayed. These lights provide a stronger and more focused beam of light, aiding visibility, particularly during nighttime driving. However, it is essential (and a legal requirement in some regions) to deactivate the high beams when approaching other road users to prevent glare. The high beams are typically controlled using a forward and backward motion on the light stalk behind the steering wheel.
Fog Lamp Indicator
A warning light resembling a semi-circle adjacent to a series of wavy lines indicates that your fog lamps are active. These additional lights enhance visibility in foggy conditions when you have your main lights turned on. To deactivate the fog lamps, you can use the control located near your steering wheel and lights.
Hybrid Ready Indicator
On the dashboard of a Peugeot Traveller, a green box containing the word “READY” signals that the hybrid system is fully charged and ready for operation. This means the batteries have enough charge to power the motors, allowing the vehicle to run in electric mode.
Brake Pad Warning Light
An illuminated yellow brake disc symbol, accompanied by an exclamation mark, warns that your brake pads may be wearing thin. This feature is increasingly common in modern vehicles, providing drivers ample time to address the issue before the brake pads become dangerously thin.
Engine Coolant Warning
A warning light displaying waves with a floating thermometer, set against a red background, indicates the engine is overheating. The waves represent the engine’s coolant, crucial for maintaining an optimal temperature. Causes for this overheating can vary, ranging from excessive engine strain to a leak or other malfunction. In such cases, it is imperative to pull over, allow the engine to cool, and seek professional assistance from a trained mechanic or a Peugeot Traveller service center.
Powertrain/Drivetrain Warning
The powertrain or drivetrain of your Peugeot Traveller encompasses the mechanical components responsible for transmitting power from the engine to the wheels. This includes the transmission, clutch, differentials, axles, and potentially other driving aids. Suppose a warning light related to the powertrain or drivetrain illuminates and remains on after restarting the vehicle. In that case, it is crucial to address this issue promptly as it could indicate a severe problem, potentially making driving unsafe.
Heads Up Display Warning Light
A warning light on your Peugeot Traveller ‘s dashboard resembling a caterpillar or a long tube with flashing lines may be related to the heads-up display system. If no corresponding error message appears on the separate heads-up display unit, this could indicate a system malfunction. In such cases, it is advisable to consult with a Peugeot Traveller mechanic or visit a dealership to conduct diagnostics and resolve the issue.
Electronic Parking Brake Alert
Modern Peugeot Traveller models have transitioned to an electronic parking brake, typically engaged via a button rather than the traditional handbrake lever near the gear shifter. This system may be represented by a yellow warning light displaying a “P” enclosed within it. If the system encounters a fault, a red warning light featuring brake pads surrounding a circle with a lightning bolt inside will appear. Given that an electronic system provides less tactile feedback compared to a mechanical handbrake, this warning is crucial. Operating the vehicle with this warning light could be hazardous, and it is strongly recommended to seek assistance from a Peugeot Traveller dealership.
Blind Spot Monitoring System Deactivated
A warning light showing two side-by-side cars with a radar effect between them, accompanied by the word “OFF” above, indicates that the blind spot monitoring system is turned off. The blind spot is the area outside of a driver’s immediate line of sight, and this system aids in detecting vehicles within that area. If you did not manually deactivate this system and the warning persists after restarting the car, it is advisable to consult with a trained mechanic.
Hood Open Alert
The hood ajar warning is a critical alert that should not be ignored. Ensure that the hood of your Peugeot Traveller is securely closed by opening it fully and then closing it firmly to engage the locking mechanism. Driving with an unsecured hood is extremely dangerous, as it could open while the vehicle is in motion, obstructing your view and causing severe damage.
Trunk Open Warning Light
A car silhouette with an open trunk flap on the right-hand side indicates that the trunk of your vehicle is not properly closed. Ensure that the trunk is securely shut before driving, as ignoring this warning could lead to more severe alerts, including auditory alarms. If the trunk appears closed yet the warning persists, there may be an issue with the sensor, necessitating professional inspection.
Engine Air Filter Alert
A clogged engine air filter can hinder performance and fuel efficiency, and it is essential to replace it promptly. Some Peugeot Traveller models are equipped with sensors that detect when the air filter is blocked, providing a warning before it becomes a significant issue. This warning is represented on the dashboard by a series of circles with a gust of wind flowing through them. Replacing the air filter is a relatively simple and affordable maintenance task.
Water in Fuel Warning Light
In most diesel engines, the fuel filters are designed to separate and remove any traces of water from the fuel to prevent damage to the engine. If water can bypass this system, you may see a warning light on your dashboard, usually as a fuel pump next to water droplets or rain. Water in the fuel can cause severe damage to the engine, so it’s crucial to address this issue promptly. You should refer to your car’s owner’s manual, which will provide detailed instructions on resolving this issue if this warning light appears.
Glow Plug Warning
For diesel engines, a glow plug is a crucial component that aids in starting the engine, especially in cold conditions. The glow plug warning light usually represented as a coiled wire or string in yellow, illuminates briefly when you turn on the ignition, indicating that the glow plug is warming up. This light should disappear quickly, signaling that the glow plug has reached the necessary temperature. If the light remains illuminated, it indicates a potential issue with the glow plug, and you should seek assistance from a Peugeot Traveller mechanic.
Service Reminder
Some Peugeot Traveller models have a service reminder feature triggered after a specific number of miles or months since the last service. This reminder is typically displayed as a spanner with an exclamation mark passing through it on the dashboard. While this is usually just a friendly reminder and not an indication of a malfunction, it’s advisable to schedule a service soon to maintain your vehicle in optimal condition.
Brake Override Warning
Engaging the brake and accelerator pedals simultaneously can cause damage to the vehicle and increase the risk of an accident. Some vehicles feature a warning light on the dashboard to alert the driver when both pedals are being pressed simultaneously, urging them to adjust their driving for safety reasons. In some models, the vehicle may even intervene to resolve the issue. If this warning light is flashing, it indicates a malfunction in the system, necessitating immediate attention from a professional.
Adblue Warning
Adblue® is an additive in some modern diesel engines to reduce emissions and pollution. When the Adblue® level is low, a warning light will appear on the dashboard, displaying the word “Adblue” or an image of an emptying bottle. If the Adblue® reservoir can run empty, the engine may not start. Adblue® fluid is readily available at various retailers, including fuel and service stations, and can be easily replenished by the vehicle owner.
Headlight/Taillight Malfunction Indicator
Modern Peugeot Traveller vehicles may be equipped with a convenient warning system designed to alert you when a headlight or taillight is not functioning properly. Since a burnt-out light can be challenging to detect from the driver’s seat, this feature is invaluable for maintaining safe driving conditions. The warning typically appears as an illuminated light bulb encircled by two smaller semi-circles on your dashboard. Addressing this issue promptly ensures optimal visibility and compliance with traffic regulations.
Immobilizer System Alert
The immobilizer is a vital security feature in your car, designed to thwart potential car thieves by preventing the engine from starting without the proper key. It achieves this by cutting off the fuel pump’s power supply. The system operates by detecting your car’s authorized key inside the vehicle, thereby enabling the engine to start. If an issue arises with the immobilizer, your car may fail to start, and you will see a warning icon resembling a car with a large key inside of it on your dashboard. In such a case, it is advisable to seek assistance from a trained Peugeot Traveller mechanic to diagnose and resolve the issue.
Air Suspension Alert
Some car models, particularly those capable of off-road driving, have an air suspension system that allows the driver to adjust the vehicle’s height. While innovative, this system has numerous components and relies on piping prone to damage. A warning light depicting the outline of a car with arrows pointing up and down indicates a potential issue with the air suspension system. Given that driving with a faulty air suspension can be hazardous, it is crucial to consult with a trained mechanic as soon as possible.
Automatic Transmission Fault Indicator
An automatic transmission enhances the driving experience by simplifying gear changes, but it is also a complex component that can be expensive to repair if problems arise. A warning light resembling a cog with an exclamation mark indicates a potential fault in the gearbox. Addressing this issue promptly is imperative, and it may be advisable only to drive or at least push the vehicle too hard until a professional has resolved the issue.
Oil Service Reminder
A yellow oil symbol on your dashboard generally signals that it’s time for an oil service, indicating either a need for an oil change or a drop in oil levels. Some modern vehicles provide explicit dashboard messages such as “oil service required” or “oil change required.” To resolve this issue, schedule an oil change and consider replacing the oil filter simultaneously to remove any lingering contaminants from the system. While topping off the oil levels may provide a temporary solution, it is not a substitute for a proper oil service.
Leave a Reply Cancel reply
Your email address will not be published. Required fields are marked *
Save my name, email, and website in this browser for the next time I comment.

IMAGES
VIDEO
COMMENTS
There are 25+ possible lights that may illuminate for a variety of reasons. While this guide is helpful, please refer to your owner’s manual after reading through this list.
Foton. Foton Grator Dashboard Warning Lights (All Models 2014 to 2024) Foton Toano Dashboard Warning Lights (All Models 2015 to 2024) Foton Thunder Dashboard Warning Lights (All Models 2012 to 2024) Foton …
If the light does not go out when vehicle speed<br /> is greater than 7km/h, it indicates an ABS<br /> malfunction or indicator light line failure.<br /> Indicator light line failure or ABS control unit<br /> malfunction<br /> 04<br /> Tip:<br /> …
Welcome to the ultimate guide to all dashboard symbols, warning lights, errors and faults for the 2014 to 2024 Foton Grator. This will assist in troubleshooting, diagnosing and solving common …
powerful random data flow help function. Select read data flow function menu in engine system, enter<br />. The data can be used to simulate the vehicle conditions as the failure occurs. It also can help<br />. determine the cause of …
Peugeot Traveller warning lights & dashboard symbols explained for the years 2016 through to 2024. Find out what the dashboard symbols mean for your make, model and year of car.
This article will give you a quick explanation for every warning, alert, and indicator light on the dashboard, 113 to be exact. We’ll break them down into sections, and include images to help you compare them to the …
Navigating through the sea of dashboard lights on your Peugeot Traveller can sometimes feel like cracking a secret code. From the moment you turn the key, a Skip to content